Open Access
ARTICLE
Research on Stick-Slip Vibration Suppression Method of Drill String Based on Machine Learning Optimization
School of Petroleum Engineering, Chongqing University of Science and Technology, Chongqing, 401331, China
* Corresponding Author: Jian Wei. Email:
Sound & Vibration 2023, 57, 97-117. https://doi.org/10.32604/sv.2023.043734
Received 10 July 2023; Accepted 08 September 2023; Issue published 14 December 2023
Abstract
During the drilling process, stick-slip vibration of the drill string is mainly caused by the nonlinear friction generated by the contact between the drill bit and the rock. To eliminate the fatigue wear of downhole drilling tools caused by stick-slip vibrations, the Fractional-Order Proportional-Integral-Derivative (FOPID) controller is used to suppress stick-slip vibrations in the drill string. Although the FOPID controller can effectively suppress the drill string stick-slip vibration, its structure is flexible and parameter setting is complicated, so it needs to use the corresponding machine learning algorithm for parameter optimization. Based on the principle of torsional vibration, a simplified model of multi-degree-of-freedom drill string is established and its block diagram is designed. The continuous nonlinear friction generated by cutting rock is described by the LuGre friction model. The adaptive learning strategy of genetic algorithm (GA), particle swarm optimization (PSO) and particle swarm optimization improved (IPSO) by arithmetic optimization (AOA) is used to optimize and adjust the controller parameters, and the drill string stick-slip vibration is suppressed to the greatest extent. The results show that: When slight drill string stick-slip vibration occurs, the FOPID controller optimized by machine learning algorithm has a good effect on suppressing drill string stick-slip vibration. However, the FOPID controller cannot get the drill string system which has fallen into serious stick-slip vibration (stuck pipe) out of trouble, and the machine learning algorithm is required to mark a large amount of data on adjacent Wells to train the model. Set a reasonable range of drilling parameters (weight on bit/drive torque) in advance to avoid severe stick-slip vibration (stuck pipe) in the drill string system.Graphic Abstract
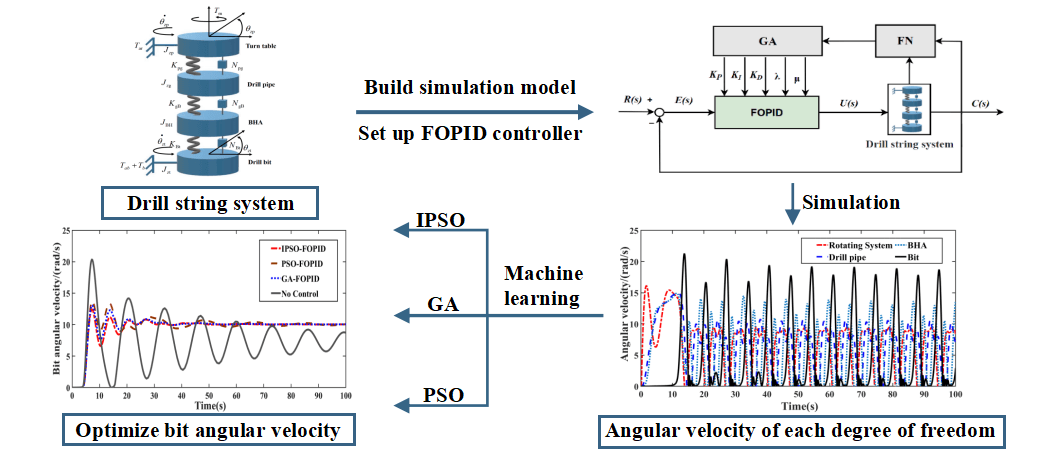
Keywords
Cite This Article
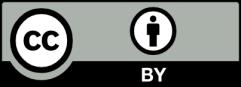
This work is licensed under a Creative Commons Attribution 4.0 International License , which permits unrestricted use, distribution, and reproduction in any medium, provided the original work is properly cited.