Open Access
ARTICLE
Computational Analysis of Surface and Subsurface Initiated Fatigue Crack Growth due to Contact Loading
1 University of Maribor, Faculty of Education
2 University of Maribor, Faculty of Mechanical Engineering
Structural Durability & Health Monitoring 2005, 1(3), 215-224. https://doi.org/10.3970/sdhm.2005.001.215
Abstract
A computational model for simulation of surface and subsurface initiated fatigue crack growth due to contact loading is presented. The model is based on fracture mechanics theory where the required materials properties are obtained from common fatigue tests. For computational simulations an equivalent model of two contacting cylinders is used instead of simulating the actual contact of mechanical elements. The discretised model with the initial crack on or under the surface is then subjected to normal contact pressure, which takes into account the elasto-hydro-dynamic (EHD) lubrication conditions, and tangential loading due to friction between contacting surfaces. The model considers also the moving contact of mechanical elements and for the surface initiated crack also the fluid trapped in the crack. The virtual crack extension method, implemented in the finite element method is then used for simulating the fatigue crack growth from the initial crack up to the formation of the surface pit. The numerical results correspond well with available experimental data. The described model can be used for simulation of pitting phenomenon of contacting mechanical elements like gears, bearings, wheels, etc.Keywords
Cite This Article
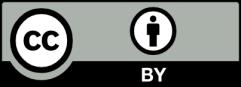
This work is licensed under a Creative Commons Attribution 4.0 International License , which permits unrestricted use, distribution, and reproduction in any medium, provided the original work is properly cited.