Open Access
ARTICLE
Dynamic Interaction Analysis of Coupled Axial-Torsional-Lateral Mechanical Vibrations in Rotary Drilling Systems
1 Applied Automation Laboratory, Faculty of Hydrocarbons and Chemistry, University of Boumerdes, Boumerdes, 35000, Algeria
2 Institute of Electrical and Electronic Engineering (IGEE), University of Boumerdes, Boumerdes, 35000, Algeria
3 Laboratory of the Electrification of Industrial Enterprises, University of Boumerdes, Boumerdes, 35000, Algeria
4 Electrical Engineering Department, Mohamed Boudiaf University of M’sila, M’sila, 28000, Algeria
5 Department of Civil and Environmental Engineering, King Fahd University of Petroleum & Minerals, Dhahran, 31261, Saudi Arabia
6 Interdisciplinary Research Center for Construction and Building Materials, King Fahd University of Petroleum & Minerals (KFUPM), Dhahran, 31261, Saudi Arabia
* Corresponding Authors: Sabrina Meddah. Email: ; Kong Fah Tee. Email:
,
Structural Durability & Health Monitoring 2025, 19(1), 77-103. https://doi.org/10.32604/sdhm.2024.053541
Received 03 May 2024; Accepted 13 August 2024; Issue published 15 November 2024
Abstract
Maintaining the integrity and longevity of structures is essential in many industries, such as aerospace, nuclear, and petroleum. To achieve the cost-effectiveness of large-scale systems in petroleum drilling, a strong emphasis on structural durability and monitoring is required. This study focuses on the mechanical vibrations that occur in rotary drilling systems, which have a substantial impact on the structural integrity of drilling equipment. The study specifically investigates axial, torsional, and lateral vibrations, which might lead to negative consequences such as bit-bounce, chaotic whirling, and high-frequency stick-slip. These events not only hinder the efficiency of drilling but also lead to exhaustion and harm to the system’s components since they are difficult to be detected and controlled in real time. The study investigates the dynamic interactions of these vibrations, specifically in their high-frequency modes, using field data obtained from measurement while drilling. The findings have demonstrated the effect of strong coupling between the high-frequency modes of these vibrations on drilling system performance. The obtained results highlight the importance of considering the interconnected impacts of these vibrations when designing and implementing robust control systems. Therefore, integrating these components can increase the durability of drill bits and drill strings, as well as improve the ability to monitor and detect damage. Moreover, by exploiting these findings, the assessment of structural resilience in rotary drilling systems can be enhanced. Furthermore, the study demonstrates the capacity of structural health monitoring to improve the quality, dependability, and efficiency of rotary drilling systems in the petroleum industry.Keywords
Cite This Article
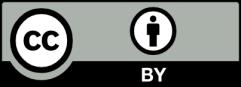
This work is licensed under a Creative Commons Attribution 4.0 International License , which permits unrestricted use, distribution, and reproduction in any medium, provided the original work is properly cited.