Open Access
REVIEW
Review of Artificial Neural Networks for Wind Turbine Fatigue Prediction
Windstorm Impact, Science and Engineering (WISE) Research Lab, Louisiana State University, Baton Rouge, LA 70803, USA
* Corresponding Author: Aly Mousaad Aly. Email:
Structural Durability & Health Monitoring 2024, 18(6), 707-737. https://doi.org/10.32604/sdhm.2024.054731
Received 01 February 2024; Accepted 07 June 2024; Issue published 20 September 2024
Abstract
Wind turbines have emerged as a prominent renewable energy source globally. Efficient monitoring and detection methods are crucial to enhance their operational effectiveness, particularly in identifying fatigue-related issues. This review focuses on leveraging artificial neural networks (ANNs) for wind turbine monitoring and fatigue detection, aiming to provide a valuable reference for researchers in this domain and related areas. Employing various ANN techniques, including General Regression Neural Network (GRNN), Support Vector Machine (SVM), Cuckoo Search Neural Network (CSNN), Backpropagation Neural Network (BPNN), Particle Swarm Optimization Artificial Neural Network (PSO-ANN), Convolutional Neural Network (CNN), and nonlinear autoregressive networks with exogenous inputs (NARX), we investigate the impact of average wind speed on stress transfer function and fatigue damage in wind turbine structures. Our findings indicate significant precision levels exhibited by GRNN and SVM, making them suitable for practical implementation. CSNN demonstrates superiority over BPNN and PSO-ANN in predicting blade fatigue life, showcasing enhanced accuracy, computational speed, precision, and convergence rate towards the global minimum. Furthermore, CNN and NARX models display exceptional accuracy in classification tasks. These results underscore the potential of ANNs in addressing challenges in wind turbine monitoring and fatigue detection. However, it’s important to acknowledge limitations such as data availability and model complexity. Future research should explore integrating real-time data and advanced optimization techniques to improve prediction accuracy and applicability in real-world scenarios. In summary, this review contributes to advancing the understanding of ANNs’ efficacy in wind turbine monitoring and fatigue detection, offering insights and methodologies that can inform future research and practical applications in renewable energy systems.Keywords
The world demand for renewable energy resources has recently increased significantly due to the shortage of conventional energy sources and their adverse effects on the environment and climate. The current severe shortage of energy and degradation of the environment have compelled individuals and authorities around the globe to explore promising sources of alternative energy [1]. There are many sources for generating renewable energy, and one of them is wind energy, which is the most common due to its abundance and simplicity in generating power. Wind energy is an alternative source demonstrating the benefits of being sustainable, environmentally friendly, and clean [2–4]. Because of this, wind energy has attracted significant interest as a form of plentiful, environmentally friendly renewable energy resources and has recently seen unparalleled growth in development [1]. With just 2000 offshore wind megawatts (MW) constructed at the end of 2009, wind energy has been acknowledged as one of the primary renewable energy sources. Its progress has primarily involved the development of onshore wind farms [5]. Up till recently, onshore installations have accounted for the majority of the utilization of wind energy. Compared to other renewable energies, wind energy has a higher technological sophistication and higher availability of wind resources, which account for this selective progress [5]. Hence, we can witness a vast orientation of the developed countries to harness wind energy for power generation, as it all started with one wind turbine in 1887 to produce electricity in Scotland, and now it is more than 70,800 in the U.S. only. Even though wind turbines have shown numerous expansions, they are still significantly vulnerable to physical damage [6].
Fatigue occurs when a material under stress weakens with time, especially cyclic stresses [7]. Cycling loading and fatigue can cause cracks to spread even at nominal maximum stress levels substantially lower than the material’s ultimate stress limit, which can ultimately cause the structure to fracture [7].
During the operational phase of a wind turbine, most of its components experience fluctuating mechanical stresses due to the variation in wind speed. Consequently, this process results in gradual deterioration of individual components, ultimately culminating in a failure. The initiation of this process occurs at the micro-scale as a result of irreversible alterations in the microstructure. Over time, it progresses and eventually becomes evident as a defect, ultimately causing the loss of functioning in a specific component [8]. Understanding the process of component degradation over time is of significant importance, as it allows for the estimation of the remaining usable life of the component before the loss of its functionality. To enhance the operational longevity of a wind turbine, it is vital to understand the utilized lifespan, often referred to as cumulative damage. However, it should be noted that the cumulative damage in wind turbines directly correlates with the fatigue load they endure [9].
If fatigue loads are continuously monitored while wind turbines are in operation, an up-to-date evaluation of lifetime consumption concerning design criteria may be feasible [10]. To avoid fatigue as much as possible and improve the wind energy production process, many mechanisms could be used to predict fatigue, including the ANN (artificial neural network).
ANN is a set of interconnected units or nodes, as seen in Figs. 1 and 2. More accurately, it combines many simple processing units running in parallel, each capable of learning from its environment and storing that knowledge in its connections [11]. ANN provides obvious benefits over conventional data processing techniques when handling fuzzy, random, and nonlinear data [12]. Remembering that all artificial neural network methods exhibit optimal performance when dealing with nonlinear dependencies between the inputs and outputs is crucial. ANNs can model and identify linear relationships. However, it is worth noting that in some instances, the outcomes obtained through ANNs may be inferior to those achieved using more straightforward basic statistical procedures [13].
Figure 1: An illustration depicting the architecture of an artificial neural network (ANN). The ANN is composed of multiple layers, including an input layer, one or more hidden layers, and an output layer
Figure 2: Artificial neural network architecture, as (a) represents the input values (i), (b), (d), (f) represent the weighted connections (w), (c) and (e) represent the processing neurons, (g) represents the output values (o)
Within a neural network, individual nodes engage in basic computations, while connections facilitate the transmission of signals between nodes. These connections are characterized by numerical values referred to as “Connection Weight”, which signify the degree to which a signal is either amplified or attenuated by the connection [14]. The artificial neuron is designed to replicate the functionality of a real neuron, specifically by receiving multiple impulses from nearby neurons and processing them according to a predetermined and straightforward method [13].
There are many types of ANN methods. In this paper, we investigated the literature for its uses in the prediction of wind turbine fatigues, and the paper aims to make it a reference for researchers in this field or any related field.
The paper is structured as follows. Section 2 introduces an overview of wind turbine fatigue. The fundamentals of artificial neural networks are presented in Section 3, which provides a comprehensive review of the essential aspects of ANNs, including their basic principles, the learning process, and their specific application in the context of wind energy systems. A previous study on wind turbine fatigue is investigated in Section 4, which comprehensively examines the current research literature. The application of ANNs in wind turbine fatigue prediction is illustrated in Section 5, which includes an extensive review of the application of ANN in fatigue prediction. Section 6 presents a previous case study where ANNs had been applied in investigating wind turbine fatigue, in addition to a simulation that we conducted based on the literature. The current limitations and challenges in using ANNs for wind turbine fatigue prediction are presented in Section 7, and valuable perspectives for future research and development in this field are provided. A summary of the main findings and the significance of ANNs in advancing the understanding of wind turbine fatigue is presented in Section 8.
2 An Overview of Wind Turbine Fatigue
Wind turbine fatigue is the term used to describe the accumulated and gradual degradation that develops over time in the structural elements of a wind turbine structure due to cyclic loads brought on by wind-induced forces and operational circumstances. Fatigue is essential to consider while designing and operating wind turbines since it can significantly affect the structure’s durability and viability over time for these sustainable energy systems. Pacheco et al. in 2022 [15] addressed multiple issues evaluating wind turbine tower fatigue. Wind gusts, turbulence, and the blades’ continual rotation, which subjects the tower to cyclic loads, are just a few of the variables that can cause fatigue in wind turbine structures. The following are some crucial aspects of how fatigue affects the health and durability of wind turbine structures:
1. Reduced Structural Life: The wind turbine structure’s estimated life may be reduced due to fatigue [16]. The wind turbine’s structural elements develop cracks over time due to cyclic loads; if these cracks are not effectively handled, they may eventually collapse the structure [16].
2. Maintenance Costs: To identify and reduce fatigue-induced damage, periodic checks and upkeep are necessary [17]. The total effectiveness of the wind turbine may be impacted by these time- and money-consuming upkeep tasks [17].
3. Safety Concerns: The safety of operating wind turbines may be affected by fatigue-related degradation. Fatigue-related structural failures can cause disastrous incidents, such as the tower collapsing, which puts both the surrounding environment and the workforce in danger [18].
4. Financial Implications: Operators of wind farms may suffer economic losses due to wind turbine outages and repair expenses related to fatigue-induced damage. To reduce these financial risks, efficient fatigue evaluations and handling techniques are crucial [16,19–22].
5. Design Considerations: Towers for wind turbines must be designed considering fatigue risks. Enhancing the tower’s resilience to fatigue requires careful design considerations, including materials choice, element sizing, and structural strengthening [23,24].
The recognition and handling of fatigue-related difficulties in wind energy structure depends on several interconnected factors, such as wind loads, cyclic loads, and material qualities. Wind turbine towers are particularly susceptible to these factors.
Due to its turbulent and dynamic properties, the wind force, which exerts variable and cyclic stresses on tower structures, is the primary external source that causes fatigue. Wind-induced forces cause variable strains to be placed on tower parts, which results in cyclic loading patterns. These forces are affected by multiple factors, such as wind speed, gustiness, direction, and turbulence intensity. Wind loads must be precisely characterized and modeled to be evaluated for their impact on fatigue life.
Furthermore, cyclic loading is the essential mechanism underlying the onset and spread of fatigue damage within wind turbine towers. It is driven by noises brought on by the wind and the constant rotation of turbine blades, which create stress fluctuations and, over time, accumulate fatigue damage [25,26]. Understanding and reducing the impacts of cyclic loading requires strategies involving load tracking, stress evaluation, and fatigue assessment [27].
Additionally, it turns out that the inherent material characteristics of tower components have a crucial role in determining how they respond to cyclic loads and, consequently, how susceptible they are to fatigue [28]. Significant influence is exerted by ductility, fracture toughness, yield strength, and fatigue strength. A wise material choice strengthens the ability to withstand fatigue-induced damage by reflecting improved fatigue strength and fracture toughness [28]. It is crucial to understand that material qualities might vary depending on the environment, temperature swings, and over some time, underlining the necessity for careful material specification and selection [28].
An investigation of processing techniques for fatigue assessment is conducted. These solutions combine techniques created to consider the critical role of material properties, capture the intricate components of wind loading, and forecast the complicated impacts of cyclic loading [15]. The research emphasizes the importance of developing a comprehensive strategy for managing fatigue that considers the complex interactions between different causing elements [15].
Improved computational techniques, sensing technology, and materials science must be integrated to successfully traverse the difficulties caused by fatigue in wind turbine structures. This integration is the basis for establishing reliable and practical techniques for handling and evaluating fatigue. Moreover, continuing research projects and industry collaboration activities are crucial for improving our understanding of these complex elements, ultimately improving the dependability and long-term viability of wind energy structures.
Table 1 summarizes different methods for wind turbine fatigue assessment, as it provides a comprehensive overview and comparison of various methods used for assessing fatigue in wind turbines.
3 Artificial Neural Networks (ANNs): Fundamentals
Artificial neural networks (ANNs) are computational modeling methods recently developed and have gained widespread adoption in many fields for simulating challenging real-world issues [39]. ANNs could be described as thickly coupled adaptive basic processing units capable of executing enormously concurrently high-performance computations for data processing and knowledge representation [40,41]. Even though ANNs are blatant representations of their biological counterparts, the ultimate objective of ANNs is not to mimic the functioning of biological systems but rather to employ what is known about how biological networks work to address complicated issues. The extraordinary information processing traits of biological systems, such as nonlinear behavior, significant parallelism, durability, error and failure tolerance, learning, capability to cope with inaccurate and ambiguous input, and the ability for generalization, make ANNs attractive [42]. Such features make artificial models advantageous because (i) nonlinearity provides for an improved fit to the data, (ii) Noise-insensitivity allows for precise forecasting even in the presence of faulty measurements and questionable data, (iii) High parallelism ensures quick processing and hardware fault tolerance, (iv) As the environment changes, the system can adapt by updating (modifying) its internal structure, and (v) Generalization permits the model to be used with unlearned data. The primary goal of ANN-based computing, often known as “neurocomputing”, is to create mathematical formulas that allow ANNs to emulate the data processing and information acquisition processes seen in the human brain. Although ANN models possess an empirical nature, they can yield highly accurate answers for issues that are either precisely or imprecisely defined. Additionally, they are adept at handling phenomena that can only be comprehended using experimental data and observations conducted in real-world settings [43].
Artificial intelligence is distinctive in its predominant application for data analysis, notably advocated by social science and art scholars, and its utility in science and engineering [44]. ANNs have been extensively used in various domains, including business, education, economics, and everyday life. ANNs have demonstrated their applicability in multiple domains, including optimization methods [45], intrusion detection [46,47] and data analysis [48–50]. Numerous scholars have utilized machine learning (ML) methodologies to address classification challenges [51,52]. Artificial neural networks (ANNs) have demonstrated a high level of proficiency in identifying trends and patterns within datasets [53]. Consequently, they are well-suited for fulfilling forecasting and prediction requirements [53].
Within artificial systems, learning is commonly understood as the iterative process by which the system’s internal representation is modified in direct reaction to external inputs, enabling the system to execute a designated task effectively. Learning encompasses the alteration of the network architecture, encompassing modifications of link weights, the creation or removal of connecting links, and the adjustment of firing rules for individual neurons [41]. ANN learning occurs through iterative steps, wherein the network is exposed to training instances, resembling the process through which humans acquire knowledge through experiential learning. An ANN system is considered to have acquired knowledge when it can effectively process imprecise, fuzzy, turbulent, and probabilistic information without significantly compromising the quality of its responses. Additionally, a well-trained ANN system should be capable of using the knowledge gained from specific tasks to solve unfamiliar problems, thereby exhibiting the capacity to generalize its learning.
The forecasting process involves utilizing ANNs to analyze a time series dataset that represents a specific phenomenon inside a particular situation. This analysis entails training the ANN using samples from the dataset, enabling it to learn the patterns and relationships within the data. Once trained, the ANN can be applied to additional scenarios to anticipate or forecast the phenomenon’s behavior at future times [39].
3.3 ANNs Applications in Wind Energy Systems
3.3.1 Forecasting and Predictions
The accurate estimation of wind energy generation is a multifaceted undertaking that holds significant importance in facilitating optimal decision-making for various stakeholders, including energy providers, participants in the wind energy market, wind farm proprietors and operators, and maintenance teams. One possible approach to mitigating overproduction among energy suppliers is incorporating energy storage systems or synchronizing the projected wind energy production with the anticipated demand [54]. Additionally, generators can implement strategies for optimizing the electricity market offers [55,56]. Furthermore, maintenance tasks can be scheduled based on predictive models [57,58], among other potential strategies.
The utilization of ANNs has proven effective when understanding physical processes that are limited or highly intricate, such as predicting wind patterns [59], which is mainly attributed to the inherent complexity and nonlinearity of wind behavior, making accurate wind forecasting challenging. Hence, the primary benefit of artificial neural networks (ANNs) is their ability to effectively capture intricate nonlinear relationships utilizing pattern recognition [60]. This characteristic renders them well-suited for application in the domain of wind forecasting.
Most of the literature studies for wind speed forecasting using ANN are focused on concise and short-term wind speed prediction because these predictions are beneficial and helpful for controlling the wind turbine and avoiding any kind of fatigue [61], such as wind turbine blade fracture. Some other research that has been considered for forecasting very short-term wind speed is 1-The new approach developed by Riahy et al. in 2008 [62] for predicting short-term wind speed, combining the linear prediction model with waveform filtering. Still, according to the published results, the suggested approach is fast and practical for online use. However, it is not sufficiently precise [62]. 2-By using wavelet-based networks and particle swarm optimization, Safavieh et al. in 2007 [63] suggested a newly developed integrated approach to forecast very short-term wind speed. Although the mentioned hybrid model is effective, the optimization technique takes up much CPU time. Hence, it is not suitable for online applications [63].
Kani et al. in 2011 [64] proposed a new approach to forecast the very short-term wind speed using ANN. Two ANNs are utilized in this proposed approach. Ten real-world wind speed data are used from t to (t−10) as input variables for the first ANN (ANN-1), which is mainly used for forecasting and detecting the short-term trend in wind speed signal [64]. Transition probabilities for the forecasted values, the other four indices, and the primary forecasts are provided as input variables to a second ANN (ANN-2) following the first prediction using ANN-1 [64].
Silva et al. [65] forecasted the wind speed by using the RBF (radial basis function) instead of the MLP (multilayer perceptron) because it is more efficient, and they proved that by designing an experiment that shows the difference between RBF and MLP [65].
Kulkarni et al. [66] after using the ANN to forecast the wind speed in the long-term, they observed that current deep neural network techniques like NARX (nonlinear autoregressive networks with exogenous inputs) and LSTM (long short-term memory) are comparable. However, LSTM turns out to be more adaptable to changes in cell state while being effective in training time. It also gives better results than NARX for more extended multistep forecasts [66].
Many proposed hybrid models in the literature gave better results than single ANN methods for forecasting wind speed in the short term. As a result, the literature suggested that hybridizing the ANNs is better than using a single ANN method for the wind speed predictions in the concise term [61]. Furthermore, the use of ANN for wind speed prediction was not limited to short and concise terms; scientists used it in medium-term wind speed prediction by developing specific algorithms using ANN [61].
Babbar et al. [67] used LASSO (Least Absolute Shrinkage and Selection Operator) and BNN (Bayesian Neural Network) to forecast medium-term wind speed. The data has been collected using the NWP (Numerical Weather Prediction) model, which typically predicts weather characteristics. The primary goal of wind speed prediction was to eliminate differences between expected and actual wind speed using BNN. MAPE (Mean Absolute Percentage Error) and NMAE (Normalized Mean Absolute Error) are performance indicators used to evaluate precision. The outcome demonstrates that, in contrast to LASSO, which did not offer acceptable accuracy at any hour, BNN has done very well and has obtained high precision for 6 to 72 h ahead of forecasting by estimation predicting [67].
Even after extensive studies utilizing various machine learning techniques, it is still possible to enhance wind speed prediction. Prospectively, a wide variety of algorithms for improving the accuracy of predictions are available in machine learning techniques. First, BNN has a more extended forecasting range for long-term wind speed predictions. Second, a combination of several linear and nonlinear models may also be used to forecast wind speed [67]. Studies have been done in the last ten years on merging forecasting methods, and BNN is seen as a potential for the ensemble method. However, a small gap in achieving high precision has been seen due to the limited data set. At the same time, López et al. [68] suggested an approach for forecasting the wind speed using ANN. This approach accurately estimates the average wind speed over the year with only a 3% error. In this approach, they used a multilayer perceptron neural network that was trained using the Bayesian regularization process and has one hidden layer with 15 neurons [68].
The aerodynamic configuration of wind turbines plays a crucial role in optimizing their efficiency and, as a result, enhancing the overall effectiveness of wind energy systems. ANNs are utilized in the design field because they can consider several aerodynamic elements, such as lift coefficient, drag coefficient, Reynolds number, angle of attack, and viscosity [69].
Sun et al. [70] focused on the crucial matter of wake impact in wind power generation. The wake effect refers to the phenomenon when wind turbines located downstream encounter a decrease in wind velocity due to the turbulence caused by upstream wind turbines [71]. To minimize the effects and improve power production, the researchers suggest a novel method that integrates artificial neural networks with experimental data on wind patterns. They specifically created an artificial neural network wake-power model to forecast the power generated by wind turbines accurately. The model considers wind velocities, directions, and yaw angles. The model is validated using experimental data from an active wind farm [72]. The findings illustrate that the ANN-wake-power model accurately predicts power generation while ensuring computational efficiency [70]. The accuracy of the ANN-wake-power model depends on the presence of an adequate amount of data during the training phase. Having sufficient data coverage is essential for attaining accurate predictions. The model considers wind speeds, directions, and yaw angles to accurately represent the intricate interactions inside wind farms, resulting in enhanced power estimation [73]. The model’s computational efficiency renders it suitable for real-world applications, mainly when prompt evaluations are crucial.
3.3.3 Fault Detection and Diagnosis
There are numerous approaches to identifying faults in wind turbines through CM (condition monitoring) techniques, commonly referred to as FDD (fault detection and diagnosis) when accompanied by diagnostic capabilities. Numerous scholarly articles have examined various strategies in the field, such as FDD using CMS (condition monitoring systems) [74], FDD for maintenance management [75], pattern recognition for FDD [76], and FDD based on ANNs. Most techniques utilize ANNs to discern patterns within SCADA (supervisory control and data acquisition) signals, which may serve as potential indicators of fault events [77]. Various models exist to evaluate a system’s entirety and identify any outliers that may be present [78]. Nevertheless, most algorithms and models are designed to assess distinct elements, including but not limited to gearbox and bearings, generator, power electronics, electric controls, rotor blades, and hydraulic controls, and the decrease of false-alarm rates.
Research has provided evidence to support the notion that Artificial Neural Networks (ANNs) exhibit a high level of resilience when employed in control tasks. Due to this rationale, they are extensively utilized in diverse systems. For example, ANN controllers have been developed and used in various applications such as flight control, robot manipulators, maritime dynamic positioning systems, induction motors, product storage, and regulating multiple parameters in wind turbines [79].
Navarette et al. [80] investigated the crucial field of wind energy systems, specifically focusing on wind turbine pitch control. Optimizing the power generation of wind turbines is essential due to their direct connection to the electrical grid [81]. The difficulty lies in obtaining the most efficient power production throughout a broad spectrum of wind velocities while considering the inherent unpredictability of wind patterns [82]. Conventional control methods frequently encounter challenges in dealing with variable and unpredictable wind conditions [82,83]. To tackle this issue, Navarette et al. [80] present expert control systems, a new method that relies on human expertise and experience. These systems accurately predict and simulate the control reactions for several possible events, thereby replicating the expertise of specialists in the sector. The expert system improves decision-making in power generation by integrating many variables, increasing efficiency. The aim is to simulate the conditions of various wind turbines, ultimately aiding in developing wind energy technology [80].
4 Previous Studies on Wind Turbine Fatigue
This section explores the profound significance of mechanical fatigue analysis within the wind turbine structural design framework. Wind turbines experience a significant number of load cycles throughout their operating lifespans, which necessitates the inclusion of mechanical fatigue analysis as a crucial measure to ensure the structural stability of these renewable energy systems [84,85]. The main aim of this analysis is to quantitatively assess the potential structural damage that may arise at various positions within the wind turbine structure. The precision of fatigue assessments guarantees wind turbine production units’ enduring reliability and safety [84,86].
The operational lifespan of a wind turbine can be characterized as a series of distinct structural states, including periods of inactivity, regular output, idle operation, and several other operating circumstances. These states exhibit complex interconnections with diverse environmental loading conditions, distinguished by factors such as average wind speed, wave direction, and other relevant parameters. The parameters are evaluated within certain intervals, varying from brief intervals of around 10 min to longer durations lasting several hours. The choice of time interval depends on the particular operational scenario being analyzed.
To effectively address the complexity of these circumstances, it is vital to undertake a sequence of numerical studies referred to as DLC (design load cases). Each DLC corresponds to a distinct set of environmental conditions and reflects a distinctive situation in which the wind turbine structure may experience the accumulation of damage. Of particular significance is DLC 1.2, which focuses on calculating the damage incurred during normal production states. The DLC poses a considerable industrial challenge due to the multitude of possible loading situations that the structure may experience in such circumstances [84,87].
The procedure of estimating short-term damage d for each of these parameter combinations is complicated. The process proceeds by producing stochastic time trajectories using the relevant environmental parameters. The structural stress responses are consequently calculated using computationally complex numerical algorithms developed explicitly for conducting multiphysics simulations. Those responses are subjected to analysis employing ‘rain flow cycle counting techniques’ to estimate the extent of short-term damage [88]. The Miner cumulative model is utilized to compute short-term damage, a procedure that requires a significant amount of time [89]. In several scenarios, the computational duration necessary for conducting these simulations is equivalent to or beyond the duration of the simulated period.
A probabilistic methodology assesses the enduring damage encountered by a particular location on the wind turbine framework. This process entails the development of an integrated estimation of short-term damage by assigning probabilities to each feasible combination of environmental elements. In assessing wind turbine structural integrity over a long-term period, the likelihood analysis for each parameter combination is significantly influenced by the utilization of real-time on-site measurements, such as midocean data [84]. Although this estimating technique is generally considered conservative, it has limitations. The process requires a significant amount of precise short-term damage assessments, which may result in a combinatorial increase in the number of simulation requests needed. Engineers may need to perform a substantial number of simulations, perhaps reaching hundreds of thousands, to obtain just one estimation of the long-term damage per the comprehensive grid outlined in the established standards. The substantial computational requirement can lead to extended computation periods, even using high-performance computing resources [84].
In recent research investigations, several approaches have been suggested to handle the computational problems and mitigate evaluation timeframes. A frequently utilized technique in the industrial sector is the aggregation of environmental factors, generally called “lumping”. This approach aims to decrease the number of simulations necessary for conducting a comprehensive assessment of damages, hence rendering the process more feasible and efficient [90,91]. Although this approach efficiently analyzes one location, it may face challenges when dealing with many structural locations, which could result in inaccurate damage predictions [90]. Moreover, the aggregation of environmental factors may not sufficiently include the uncertainties inherent in models, which hold significant importance within wind turbine structural analysis [92,93].
Reduced model techniques have been extensively utilized in offshore mechanical engineering and precisely tailored to analyze wind turbine structures [94–96]. Various strategies have been developed to minimize simulation times, including spectral approaches [97–99], simplified time-domain analysis [100], and decoupled simulation approaches [101]. These techniques have demonstrated the ability to substantially reduce the time required for simulations. However, including linearization artifacts can have a detrimental effect on the accuracy and reliability of the findings.
An alternative method for mitigating simulation costs is minimizing the number of simulator invocations. Zwick et al. [102] suggested the utilization of regression models as a means to forecast the structural damage reactions d for unsimulated combinations of environmental elements. This approach’s calibration of statistical models depends on a limited number of model observations [102]. Although this methodology has the potential to yield acceptable levels of prediction accuracy, it is crucial to note that the selection of the limited set of model observations highly influences its performance, which highlights the significance of proper calibration to obtain reliable results.
The fatigue evaluation in wind turbine structures encompasses a multifaceted interaction among environmental factors, structural conditions, and comprehensive computational modeling. The field faces considerable difficulty balancing the precision requirement and the computational resources necessary for such analyses. Engineers have devised multiple techniques to optimize the process, each exhibiting distinct advantages and drawbacks, to guarantee the continued dependability and safety of these crucial renewable energy resources.
5 Application of ANNs in Wind Turbine Fatigue Prediction
Detecting fatigue damage in wind turbine blades ensures safe and efficient operation. While traditional methods exist, Artificial Neural Networks (ANNs) have emerged as a promising alternative due to their ability to learn complex relationships from data.
As for the traditional methods, such as attaching physical sensors to the wind turbine blade to measure stresses, relying on SCADA (Supervisory Control and Data Acquisition) systems, or using finite element analysis models, there are limitations as the use of physical sensors or SCADA systems might not capture the complete picture of fatigue damage throughout the blade. In contrast, the FEA models have high costs and are time-consuming [103]. On the other hand, ANNs can learn complex relationships between various data sources, and by learning from historical data, ANNs can potentially achieve higher accuracy in fatigue damage detection compared to traditional methods. Also, ANNs can potentially identify fatigue damage at earlier stages before it becomes critical, allowing for preventive maintenance [103]. In this paper, we investigated the fatigue in wind turbine components as follows:
5.1 Wind Turbine Structure Fatigue Prediction
One of the areas that the literature investigates is wind turbine fatigue reduction. A wind-induced stress transfer function changes by the nonlinearity of turbine reactions to various mean wind speeds, and numerous simulations handling thousands of environmental factors are needed to obtain the stress transfer function from time simulations in fatigue analysis [104]. Additionally, this requires a lot of time to complete, which could take a couple of days to complete the process. To minimize the required number of simulations, Kim et al. [104] used ANN models to account for the impact of mean wind speed on the fatigue analysis results. Whereas the stress transfer function, the stress spectrum, and the fatigue damage are potential outputs of the ANN models, the mean wind speed and frequency are supposed to represent the inputs. Significantly, using ANN models indicates that computational efficiency can be increased while retaining a maximum error range of 35% and reducing the number of simulations needed from 41 to 7 [104]. A thorough overview of ANN model development highlights the significance of sampling techniques in improving model performance. It suggests including crucial wind speeds, such as cut-in, cut-out, and rated wind speeds [104]. Furthermore, the superposition model concept, which focuses on correction factors close to stress spectrum peaks, can improve predicted outcomes without adding more sample data or neurons to the hidden layer. Although it is observed that the effect of lowly fluctuating resonant motion on fatigue damage in floating wind turbine systems is negligible, its inclusion in ANN models research is recommended, suggesting directions for further investigation [104].
Yin et al. [105] studied a big data-driven multi-objective prediction system for predicting wind farm power production and structural fatigue. The average power production of the wind farm and the equivalent thrust of turbines were used as the response variables in the prediction system. In contrast, the wind conditions, control settings, and turbine characteristics were used as the predictor factors. Five distinct data mining methods, including the GRNN (General Regression Neural Network), the RF (Random Forest), the SVM (Support Vector Machine), and the GBR (Gradient Boosting), were then used to build the prediction models. A wind farm simulation platform, FLORIS (FLOw Redirection and Induction in Steady State) created by the National Renewable Energy Laboratory (NREL) and the Delft University of Technology, has been used to evaluate the aforementioned data-driven machine learning algorithms. Based on the most recent version of FLORIS, the five methods’ prediction performances were compared and assessed. According to their results, all of these approaches can achieve a relative accuracy of 99% or higher, which is sufficient for practical applications [105]. The GRNN and SVM show the highest levels of accuracy, with the GRNN having the highest accuracy and performance when making predictions about thrust. The GRNN is the most efficient in terms of computational performance [105].
Luna et al. [106] focused on predicting wind turbine tower fatigue, and they suggest using the NARX due its capability to predict nonlinear time series as it uses historical data from expected or actual time series. He et al. [107] proposed a data-driven technique for predicting fatigue load and power to evaluate the structural performance of wind turbines precisely and effectively under yaw control. The power yield and fatigue loads at crucial turbine elements are computed under realistic yaw angles while considering wake impacts. Then, input-output mappings are created using a support vector regression (SVR) model that has been trained. Based on comparison evaluation and effectiveness assessment, they discovered that the suggested prediction technique can return very high regression coefficients with a minor deviation, confirming its preciseness and resilience [107].
5.2 Wind Turbine Blades Fatigue Prediction
Yilmaz et al. [108] used the MLP (Multilayer Perceptron) and RBF (Radial Basis Function) in their study to control the wind turbine pitch angle and avoid any possible fatigue that could occur in the wind turbine blades. Their study focused on controlling the blade pitch angle at wind speeds above 14 m/s. One hidden layer has been used in both approaches (MLP & RBF). Two input neurons, five hidden neurons, and one output neuron used in MLP. Three input neurons, ten hidden neurons, and one output neuron used in RBF. Per their results, if there is no control for the pitch angle, the generator won’t be able to generate power because there will be no overspeed prevention [108]. Also, compared to the common PID (Proportional Integral Derivative) controller, the MLP and RBF showed better results in controlling and generating power [108].
Ziane et al. [109] used ANN to predict the fatigue life of the wind turbine blades, as shown in Fig. 3, by proposing the following hybrid neural network models: BPNN (Backpropagation Neural Network), PSO-ANN (Particle Swarm Optimization Artificial Neural Network), and CSNN (Cuckoo Search Neural Network). Based on the results, it was observed that the CSNN outperforms the BPNN and PSO-ANN in terms of prediction due to its ease of use when applying mathematical models, and due to its capability to change weights without determining a gradient [109]. Also, CSNN showed better fatigue life predictions, faster computation, higher precision, and most importantly a high convergence rate toward the actual global minimum [109]. The advantages of CSNN that make it preferable to use over BPNN and PSO-ANN are that it explores the search space more effectively, potentially leading to better convergence and avoiding local optima [109,110]. CSNN is robust to noisy data and can handle complex, nonlinear relationships between input features and fatigue life. CSNN efficiently adjusts the synaptic weights of the neural network, improving prediction accuracy while minimizing computational resources [109,110].
Figure 3: Fatigues in wind turbine blades, as (a) shows a wind turbine with broken blades, (b) and (c) show a wind turbine that experienced failure in the trailing edge. Please note that (b) reprinted from Composites Part B: Engineering, Vol. 176, Raman et al., “Numerical simulation of a resistant structural bonding in wind-turbine blade through the use of composite cord stitching”, Copyright (2024), with permission from Elsevier [111], and (a) and (c) reprinted with permission from reference [112]
The limitations of CSNN are as follows: 1-It requires tuning of hyperparameters for optimal performance, because poorly chosen parameters may lead to suboptimal results [109,110]. 2-CSNN performance can be sensitive to the initial population of solutions, as different initializations may yield varying results. 3-CSNN may not perform as well as other algorithms regarding local exploitation around promising regions [109,110].
Li et al. [113] used the Back Propagation (BP) neural network and Radial Basis Function (RBF) neural network for icing conditions prediction of the wind turbine blades. For predicting the blade icing mass, the neural networks trained by the usage of data sets showing a positive correlation between blade icing mass and natural. Per their findings, the BP neural network is more accurate than RBF in detecting the blade icing mass [113].
Abdallah et al. [114] created a machine learning (ML) method to statistically combine the fatigue load on the wind turbine blade from numerous concurrent simulators, considering the varying fidelity, complexity, and underlying assumptions to create a “most likely” fatigue load and thereby decrease the model-form uncertainty. To derive a map of probability, they developed clusters of simulator outputs as a function of wind speed, and they utilized bootstrap aggregations to obtain an aggregated estimate of the damage equivalent fatigue of the blade root bending moment [114].
For early damage identification utilizing vibration analysis measures Dervilis et al. [115] employed ML (Machine Learning) nonlinear neural network techniques such as auto-associative neural network (AANN) and radial basis function (RBF). The primary purpose was to improve the structural health monitoring of the wind turbine blade and assist with preventing catastrophic failure.
According to Malik et al. [116] the primary causes of a blade imbalance, as shown in Table 2, include mistakes made during manufacturing or construction, icing conditions, deterioration brought on by aging, or wear and fatigue in the wind turbine. Equipment shifts and wears to varied degrees over time due to imbalance on the blades and rotating shaft. Various factors, including control system errors and extreme wind shear, contribute to aerodynamic asymmetry. One blade pitch angle differs slightly from the other two due to a control system malfunction, which will cause aerodynamic asymmetry in the wind turbine. Malik et al. [116] used PNN (probabilistic neural network) to analyze the wind turbine defects caused by imbalance conditions. The simulated results demonstrate that the PNN has a greater diagnosis accuracy than other ANN approaches and requires less training and testing time, and it performs better than conventional approaches [116].
5.3 Wind Turbine Gearbox Fatigue Prediction
Due to their capability to transmit a relatively high load from blades while offering a high gear ratio (necessary for the generator to produce electrical energy efficiently), considerable power planetary gearboxes became widespread components of wind turbine drivetrains [117]. In this category of rotating machinery, gearboxes are at the top of the drivetrain components that are most prone to damage [117]. A single malfunction typically causes total gear damage, necessitating the replacement of the entire gearbox because a planetary gearbox distributes the load amongst multiple meshes while in operation [117]. Vibration analysis is one of the methods for evaluating the extent of damage to planetary gearboxes. Still, it is more difficult for such planetary gearboxes because wind turbines inherently operate in nonstationary circumstances with varying speeds and loads [117]. Strączkiewicz et al. [117] used methodology that considers the fluctuation of vibration signal characteristics under the effects of rapidly changing speed and load. The ANN algorithms trained at the machine typical operation. The provided value of a feature is compared to the value estimated using the taught net for each following unclassified observation. A linear regression is used, and the b parameter, also known as the error term, is observed to reduce the impact of changing conditions [117].
Chen et al. [118] used the CNN (Convolutional Neural Network) for fatigue prediction in the wind turbine gearbox, and the CNN was trained by using experimental vibration data that was processed by using standard deviation, skewness, and kurtosis in the time domain, and FFT (Fast Fourier Transform) and RMS (Root Mean Squared) in the frequency domain. Based on the results, they found that for over 20 test cases, the CNN model classification rate is better than that of SVM as it is more accurate. The CNN model had an accuracy range of 91.4% to 98.9%, whereas the SVM (Support Vector Machine) model ranged from 55.9% to 70.2% [118]. In contrast, Janssens et al. [119] used a CNN model to classify faults, as the CNN model is applied to raw frequency spectrum vibration data from bearings experiment rigs. The results showed that CNN has a higher classification accuracy than the conventional feature extraction methods, with an accuracy of 94% [119]. Based on that, we can see that Convolutional Neural Networks (CNNs) have proven to be highly efficient in predicting fatigue in spinning machinery, such as wind turbines [120–122]. The imported original vibration signals can be automatically and effectively analyzed to capture fatigue features and determine their condition using several CNN models [122]. This can be done by acquiring features directly from the one-dimensional raw vibration signals without manual feature extraction [123]. Using CNNs in this domain has yielded exceptional accuracy in recognizing and classifying fatigues [120,124].
Simani et al. [125] used NARX for fault diagnosis. NARX before comparing it with other methods like the GSKV (Gaussian kernel support vector machine), UDC (up-down counters), and GFM (general failure model), it was trained using data from routine and defective wind turbine simulators. When evaluated on nine failures, neural network estimates outperformed other methods, with just a 1.12-s delay between the incidence of the failure and its detection [125]. Additionally, it was shown that this method had significantly lower false alarm and missed fault rates than other methods. Based on that, we can tell that NARX is a type of recurrent neural network that has proven effective in predicting future values in time-series data. Within the domain of wind turbine monitoring, these models can predict future conditions of the turbine by analyzing its previous performance. This capability can detect and prevent fatigue early [125].
A wind turbine gearbox test rig experimental vibration data was gathered under fault-induced conditions by Jiang et al. [126]. To diagnose the faults in these data, the MSCNN (Multi-Scale Convolutional Neural Network) approach was used, and the results of this analysis were compared to those of conventional CNN and other techniques. Based on the results, the proposed MSCNN outperformed the different approaches, averaging 98.53%; the most significant average was 84.31% in fault classification and feature learning [126].
This section presents a study conducted by Yilmaz et al. [108] that aimed to evaluate the ability and efficiency of pitch controllers in controlling wind speeds within the optimal range for fatigue prediction purposes in the wind turbine blades. Additionally, we conducted a simulation by using MLP (Multilayer Perceptron) and RBF (Radial Basis Function) neural networks to validate the approach employed by Yilmaz et al. [108].
Yilmaz et al. [108] examined the adaptability of pitch controllers to varying conditions and assessed their effectiveness in regulating wind speeds over the optimal range. The parameters of the simulated wind turbine are derived from an actual turbine and its associated generating equipment. Therefore, the suggested controllers can be readily adjusted for utilization in real-time applications and may effectively operate in conjunction with actual wind turbines. The training of the proposed controllers is conducted using MLP and RBF neural networks. According to the computer simulations’ findings, the pitch angle of turbine blades can be adjusted to achieve optimal values for the Cp (performance coefficient) and TSR (tip speed ratio). The reference model is constructed based on the aerodynamic calculations for the wind turbine. The primary objective of the turbine controller is to regulate the speed through the use of pitch control. The pitch control remains inactive when wind speeds do not exceed 14 m/s, as the turbine fails to achieve its maximum power output. This means the study does not consider wind speeds below 14 m/s. Therefore, the neural network controllers described in this study effectively imposed the necessary limitations during the aforementioned wind speeds. The proposed controllers effectively tracked the reference signal despite the volatile nature of the applied wind speeds. When comparing the two neuro-controllers, it is seen that although the amount of errors between them is not significantly different, the RBF controller exhibits a shorter settling time than the MLP. Furthermore, in the case of MLP, it has been shown that small-magnitude oscillations are present in the lower frequency range after a change in wind speed [108]. The presence of oscillations delayed the controller’s ability to accurately track the reference signal. Two intelligent controllers are presented for blade pitch position controlling beyond the rated wind speed. Both controllers yielded satisfactory outcomes. However, the controller based on RBF yielded more efficient results than MLP [108].
Based on Yilmaz et al.’s study [108], we have conducted a simulation for Louisiana offshore wind speed data using MLP and RBF neural networks to ensure the proposed model reliability, as shown in Figs. 4 and 5. Furthermore, the Louisiana offshore wind speed map is shown in Fig. 6. Also, the wind speed time histories are illustrated in Fig. 7, and the wind speed labels are described in Table 3. The neural network structures used are depicted in Fig. 8 and Table 4. The 5 MW NREL wind turbine has been used as a reference in this study, and Table 5 illustrates its properties [127].
Figure 4: ANN model for controlling pitch angle in the wind turbine. Please note that the metrological tower photo was reprinted with permission from reference [128] John fitzburn, CC BY-SA 3.0 <https://creativecommons.org/licenses/by-sa/3.0, accessed on 13/04/2024>, via Wikimedia Commons
Figure 5: MATLAB simulation flowchart for fatigue prediction
Figure 6: Louisiana offshore wind speed map at 90 m. Please note that the map was reprinted with permission from DOE/NREL, reference [129]
Figure 7: Wind speed data time histories generated by using Weibull distribution. x-axis, time (s), and y-axis, velocity (m/s)
Figure 8: ANN model components, as (a) represents the Multilayer perceptron model components with two inputs, five hidden neurons, and one output, while (b) represents the Radial basis function model components, with two inputs, 16 hidden neurons, and one output, noting that we used the sigmoid activation function in the Multilayer perceptron, and gaussian activation function in the Radial basis function
Figure 9: Total error vs. learning rate
Based on Sudhamshu et al. 2016, we have used a starting value of pitch angle equal to 5 degrees as an optimum value to build our simulation [131]. Based on the simulation results, the changes in the performance coefficient, the tip speed ratio, and the pitch angle of both methods are depicted in Figs. 10 and 11. Additionally, Fig. 10 shows that the performance coefficient significantly decreased when the wind turbine was exposed to high speeds, which indicates that the turbine performance was horrible during that period. Thus, there will be a significant impact on the output power, as it will be significantly decreased. Moreover, Fig. 11 shows that the pitch angle increases at specific periods when the wind speed is too high to minimize the amount of energy captured by the wind turbine, therefore preventing the turbine blades from spinning too fast and potentially damaging the turbine or its components, as increasing the pitch angle will slow and brake the turbine. By comparing the results of both methods, it can be concluded that both produce equivalent performance coefficients and tip speed ratios, indicating comparable performance in the context. Please note that Fig. 12 shows the fitting curve between the predicted and the target values of the pitch angle.
Figure 10: Changes of performance coefficient and tip speed ratio for both multi-layer perceptron (MLP) and radial basis function (RBF) methods, as (a) and (b) represent the performance coefficients for MLP and RBF, respectively, while (c) and (d) represent the tip speed ratio for MLP and RBF, respectively. Noting that the wind speed labels are explained in Table 3
Figure 11: Changes in pitch angle based on the multilayer perceptron (MLP) method
Figure 12: Scatter plot, as (a) represents the predicted values of pitch angle by using MLP, and (b) represents the predicted values of pitch angle by using RBF
Furthermore, both MLP and RBF are effective. They can identify the underlying patterns in the data and generate reasonably accurate predictions because their performance coefficients lie within a comparable range. The equations that are used to get the target values for training our ANN model are as follows:
CP=(0.44−0.167θ)×sin(π(λ−3)15−0.3λ)−0.00184(λ−3)θ (1)
θ=CP−0.44sin(π(λ−3)15−0.3λ)(−0.167sin(π(λ−3)15−0.3λ)−0.00184λ−5.52×10−3) (2)
λ=ωtRV (3)
Noting that CP represents the performance coefficient, λ represents the tip speed ratio, θ represents the pitch angle, R, ωt , and V represents the rotor radius, the rotational speed, and the wind speed, respectively [132,133].
For the ANN model, the training of the ANN algorithms and calculations in the neurons and layers will be done by using an input-output equation (Eq. (4)), and the following procedures will be followed in the training of the ANN algorithms:
The first step is initializing all weights at random. The output vector and error propagation terms are calculated in the second step. In the third step, the weights will be updated by using Eq. (7). After that, the total error will be calculated by using Eq. (8). Finally, the last step is repeating step 2 to continue iterating the calculation until the overall error is less than the required error [108].
y(k)p=sgm(k)p[∑Nk−1i=1W(k−1)ip. y(k−1)i−β(k)p] (4)
(p=1,2,…Nk; k=1,2,…M)
As W(k−1)ip is the connection weight between the ith neuron in the (k−1) th layer and pth neuron in the kth layer, while y(k)p is the output of the pth neuron in the kth layer, and sgm(k)p is the sigmoid activation function of the pth neuron in the kth layer, and β(k)p is the threshold of the pth neuron in the kth layer.
The sigmoid activation function is represented in Eq. (5), while the gaussian activation function is represented in Eq. (6) as following:
sgm(x)=11+exp(−x) (5)
f(x)=e−x2 (6)
W(k−1)ip(t+1)=W(k−1)ip(t)+αl∑n=1δ(k)npy(k−1)ni (7)
where t is the iteration number and alpha is the learning rate
ε=∑ln=1∑NMj=1(y(M)nj−y′(M)nj)2 (8)
TI=σVVmean (9)
σV represents the wind speed standard deviation, and Vmean represents the mean wind speed.
7 Challenges and Future Directions
The application of Artificial Neural Networks (ANNs) in investigating wind turbine fatigue poses several significant challenges and offers potential avenues for future research and development. Firstly, the accuracy of short-term wind speed prediction using ANNs remains a concern, particularly in real-time scenarios, necessitating improved precision and computational efficacy. Additionally, while hybrid ANN models have shown promise in forecasting wind speed, further enhancements are needed, including exploring hybridization approaches and integrating data to increase precision and resilience.
Expanding the use of ANNs to encompass medium-term wind speed forecasts represents a significant development opportunity but requires tailored models to achieve advancements in accuracy. Predicting wind turbine structure fatigue with ANNs faces challenges in reducing processing time and training, indicating a need for more efficient models to predict fatigue damage while minimizing computational costs precisely.
Furthermore, while ANNs have shown potential in predicting blade fatigue, incorporating advanced optimization methods or data-driven techniques could improve prediction accuracy and computational efficiency. Gearbox fatigue prediction in wind turbines presents distinct challenges due to fluctuating wind conditions, suggesting advanced ANN models and feature extraction techniques tailored for non-stationary conditions are needed.
To enhance the training process and efficiency of ANNs in wind turbine fatigue prediction, researchers are encouraged to explore the integration of advanced optimization techniques such as genetic algorithms, particle swarm optimization, or reinforcement learning. These efforts could significantly improve the precision and effectiveness of ANNs in this domain.
The results of this paper shed light on the significance of using artificial neural networks in wind turbine fatigue prediction as they can be trained by using historical data, analyzing vibration patterns, or using other sensor data to predict the fatigue in wind turbine components, allowing for proactive maintenance, reducing downtime and improving operational efficiency, which will result in extending the lifespan of the wind turbine and reducing maintenance cost. ANNs have proven valuable in wind turbine monitoring and fatigue detection. ANN models are widely used for short- and long-term wind speed forecasts, with hybrid models surpassing single ANN methods in performance. Modern deep neural network approaches, such as NARX and LSTM, are practical for long-term wind speed predictions. ANN models have been used to examine the impact of mean wind speed on stress transfer function and fatigue damage in wind turbine structures. Various data mining techniques, such as GRNN, RF, SVM, GBR, and RN, have been developed for wind farm power generation and structural fatigue prediction. ANN models have also been used to monitor wind turbine blades and detect early damage. ANN models have shown considerable potential in accurately forecasting wind speed, detecting wear in wind turbine components, and identifying early damage. However, there is a lack of research on predicting long-term and medium-term wind speeds using ANN. Additional research is needed to increase the precision and efficacy of current methods to prevent catastrophic failures and improve structural health monitoring of wind turbine blades. Merging vibration analysis approaches with ANN models could enhance the precision and dependability of diagnosing gearbox faults in wind turbines.
Acknowledgement: The authors acknowledge the U.S. Department of Energy (DOE), National Renewable Energy Laboratory (NREL), and Alliance for Sustainable Energy, LLC (Alliance) for the use of Figure 6, which was reproduced from the following NREL document [Schwartz M, Heimiller D, Haymes S, Musial W. Assessment of Offshore Wind Energy Resources for the United States. Technical Report, NREL/TP-500-45889, June 2010. Available from: https://www.nrel.gov/docs/fy10osti/45889.pdf [Accessed on July 4th, 2024]].
Funding Statement: Author Aly Mousaad Aly received funding from the Louisiana Board of Regents through the Industrial Ties Research Subprogram (ITRS) (Award Number: LEQSF (2022-25)-RD-B-02). The author (Aly) also acknowledges support from the LSU Institute for Energy Innovation [Research for Energy Innovation 2023-I (Phase I)]. The opinions expressed in this work solely represent those of the authors and do not necessarily reflect the views of the sponsoring entities.
Author Contributions: The authors confirm their contribution to the paper as follows: Husam AlShannaq: Writing, Methodology, Investigation, Data curation, Analysis, and interpretation of results. Aly Mousaad Aly: Conceptualization, Writing, Supervision, Methodology, Funding acquisition. All authors reviewed the results and approved the final version of the manuscript.
Availability of Data and Materials: The data utilized in this review paper were primarily drawn from previously published research studies. Specific datasets or raw data used in this review are not directly available for access. However, all references cited in this paper are provided to enable interested readers to access the sources for further examination.
Ethics Approval: Not applicable.
Conflicts of Interest: The authors declare that they have no conflicts of interest to report regarding the present study.
References
1. Sun X, Huang D, Wu G. The current state of offshore wind energy technology development. Energy. 2012;41(1):298–312. doi:10.1016/j.energy.2012.02.054. [Google Scholar] [CrossRef]
2. Sheng S, O’Connor R. Chapter 15–reliability of wind turbines. In: Letcher TM, editor. Wind Energy Engineering. Cambridge, MA: Academic Press; 2017. p. 299–327. doi:10.1016/B978-0-12-809451-8.00015-1. [Google Scholar] [CrossRef]
3. Kamal M, Rahman MM. Advances in fatigue life modeling: a review. Renew Sustain Energ Rev. 2018;82:940–9. doi:10.1016/j.rser.2017.09.047. [Google Scholar] [CrossRef]
4. Liao D, Zhu SP, Qian G. Multiaxial fatigue analysis of notched components using combined critical plane and critical distance approach. Int J Mech Sci. 2019;160(10):38–50. doi:10.1016/j.ijmecsci.2019.06.027. [Google Scholar] [CrossRef]
5. Esteban MD, Diez JJ, López JS, Negro V. Why offshore wind energy? Renew Energy. 2011;36(2):444–50. doi:10.1016/j.renene.2010.07.009. [Google Scholar] [CrossRef]
6. Mutharasan A, Chandrasekar P. Fault detection and power quality analysis of wind turbine system using integrated systems. Int J Power Electron Drive Syst. 2022;13:576–85. [Google Scholar]
7. Lee YL, Pan J, Hathaway R, Barkey M. Fatigue testing and analysis: theory and practice. Oxford, UK: Butterworth-Heinemann; 2005. vol. 13. [Google Scholar]
8. Chen B, Matthews PC, Tavner PJ. Automated on-line fault prognosis for wind turbine pitch systems using supervisory control and data acquisition. IET Renew Power Gener. 2015;9:503–13. doi:10.1049/rpg2.v9.5. [Google Scholar] [CrossRef]
9. Njiri JG, Beganovic N, Do MH, Söffker D. Consideration of lifetime and fatigue load in wind turbine control. Renew Energy. 2019;131(2):818–28. doi:10.1016/j.renene.2018.07.109. [Google Scholar] [CrossRef]
10. Vera-Tudela L, Kühn M. Analysing wind turbine fatigue load prediction: the impact of wind farm flow conditions. Renew Energy. 2017;107(1):352–60. doi:10.1016/j.renene.2017.01.065. [Google Scholar] [CrossRef]
11. Haykin S. Neural networks: a comprehensive foundation. Saddle River, NJ: Prentice Hall PTR; 1999. [Google Scholar]
12. Gao L, Liu Y, Hu H. An experimental investigation of dynamic ice accretion process on a wind turbine airfoil model considering various icing conditions. Int J Heat Mass Transf. 2019;133:930–9. doi:10.1016/j.ijheatmasstransfer.2018.12.181. [Google Scholar] [CrossRef]
13. Zupan J. Introduction to artificial neural network (ANN) methods: what they are and how to use them. Acta Chim Slov. 1994;41:327. [Google Scholar]
14. Dongare AD, Kharde RR, Kachare AD. Introduction to artificial neural network. Int J Eng Innov Technol (IJEIT). 2012;2:189–94. [Google Scholar]
15. Pacheco J, Pimenta F, Pereira S, Cunha A, Magalhães F. Fatigue assessment of wind turbine towers: review of processing strategies with illustrative case study. Energies. 2022;15(13):4782. doi:10.3390/en15134782. [Google Scholar] [CrossRef]
16. Pollino M, Huckelbridge A. In-situ measurements of fatigue demands on a wind turbine support structure. IEEE Energytech, 2012;67:1–5. doi:10.1109/EnergyTech.2012.6304680. [Google Scholar] [CrossRef]
17. Hübler C, Weijtjens W, Rolfes R, Devriendt C. Reliability analysis of fatigue damage extrapolations of wind turbines using offshore strain measurements. J Phys: Conf Ser. 2018;1037(3):032035. doi:10.1088/1742-6596/1037/3/032035. [Google Scholar] [CrossRef]
18. AS DNV. Fatigue design of offshore steel structures. Rev. 2005;126. [Google Scholar]
19. Rebelo C, Veljkovic M, Matos R, Silva L. Structural monitoring of a wind turbine steel tower–Part II: monitoring results. Wind & Struct. 2012;15:301–11. doi:10.12989/was.2012.15.4.301. [Google Scholar] [CrossRef]
20. Botz M, Oberlaender S, Raith M, Grosse CU. Monitoring of wind turbine structures with concrete-steel hybrid-tower design. In: Proceedings of the 8th European Workshop on Structural Health Monitoring (EWSHM); 2016; Bilbao, Spain. p. 5–8. [Google Scholar]
21. Weijtens W, Noppe N, Verbelen T, Iliopoulos A, Devriendt C. Offshore wind turbine foundation monitoring, extrapolating fatigue measurements from fleet leaders to the entire wind farm. J Phys: Conf Ser. 2016; 753(9):092018. doi:10.1088/1742-6596/753/9/092018. [Google Scholar] [CrossRef]
22. Loraux CT. Long-term monitoring of existing wind turbine towers and fatigue performance of UHPFRC under compressive stresses. Lausanne, EPFL; 2018. doi:10.5075/epfl-thesis-8404. [Google Scholar] [CrossRef]
23. Wedel-Heinen J, Ronold K, Madsen P. Revision of DNV design standard for offshore wind turbine structures. 2007;5:433–439. doi:10.1115/OMAE2007-29118. [Google Scholar] [CrossRef]
24. Veljkovic M, Feldmann M, Naumes J, Pak D, Simões L, Rebelo C. Wind turbine tower design, erection and maintenance. In: Wind Energy Systems. Amsterdam, The Netherlands: Elsevier; 2011. p. 274–300. [Google Scholar]
25. Milne I, Ritchie RO, Karihaloo BL. Comprehensive structural integrity: cyclic loading and fatigue. Amsterdam, The Netherlands: Elsevier; 2003. vol. 4. [Google Scholar]
26. Nikitas G, Vimalan NJ, Bhattacharya S. An innovative cyclic loading device to study long term performance of offshore wind turbines. Soil Dyn Earthq Eng. 2016;82:154–60. doi:10.1016/j.soildyn.2015.12.008. [Google Scholar] [CrossRef]
27. Veers PS, Winterstein SR. Application of measured loads to wind turbine fatigue and reliability analysis. J Sol Energy Eng. 1998 Nov;120(4):233–9. doi:10.1115/1.2888125. [Google Scholar] [CrossRef]
28. Rashedi A, Sridhar I, Tseng KJ. Multi-objective material selection for wind turbine blade and tower: ashby’s approach. Mater Des. 2012;37:521–32. doi:10.1016/j.matdes.2011.12.048. [Google Scholar] [CrossRef]
29. Veldkamp D. A probabilistic evaluation of wind turbine fatigue design rules. Wind Energy. 2008;11:655–72. doi:10.1002/we.v11:6. [Google Scholar] [CrossRef]
30. Niu XP, Wang RZ, Liao D, Zhu SP, Zhang XC, Keshtegar B. Probabilistic modeling of uncertainties in fatigue reliability analysis of turbine bladed disks. Int J Fatigue. 2021;142:105912. doi:10.1016/j.ijfatigue.2020.105912. [Google Scholar] [CrossRef]
31. Liu X, Lu C, Liang S, Godbole A, Chen Y. Vibration-induced aerodynamic loads on large horizontal axis wind turbine blades. Appl Energy. 2017;185:1109–19. doi:10.1016/j.apenergy.2015.11.080. [Google Scholar] [CrossRef]
32. Musial WD, Butterfield C. Using partial safety factors in wind turbine design and testing. Golden, CO, USA: National Renewable Energy Lab. (NREL); 1997. [Google Scholar]
33. Carta JA, Ramirez P, Velazquez S. A review of wind speed probability distributions used in wind energy analysis: case studies in the Canary Islands. Renew Sustain Energ Rev. 2009;13:933–55. doi:10.1016/j.rser.2008.05.005. [Google Scholar] [CrossRef]
34. Shi H, Dong Z, Xiao N, Huang Q. Wind speed distributions used in wind energy assessment: a review. Front Energy Res. 2021;9:769920. doi:10.3389/fenrg.2021.769920. [Google Scholar] [CrossRef]
35. Tarp-Johansen NJ. Examples of fatigue lifetime and reliability evaluation of larger wind turbine components. Denmark: N. p.; 2003. Available from: https://www.osti.gov/etdeweb/servlets/purl/20387443. [Accessed on 2024]. [Google Scholar]
36. Hu W, Choi K, Gaul N, Hardee E. Reliability analysis of wind turbine blades for fatigue life under wind load uncertainty. In: 12th AIAA Aviation Technology, Integration, and Operations (ATIO) Conference and 14th AIAA/ISSMO Multidisciplinary Analysis and Optimization Conference; 2012. p. 5601. [Google Scholar]
37. Li H, Cho H, Sugiyama H, Choi KK, Gaul NJ. Reliability-based design optimization of wind turbine drivetrain with integrated multibody gear dynamics simulation considering wind load uncertainty. Struct Multidiscipl Optim. 2017;56:183–201. doi:10.1007/s00158-017-1693-5. [Google Scholar] [CrossRef]
38. Toft HS, Svenningsen L, Sørensen JD, Moser W, Thøgersen ML. Uncertainty in wind climate parameters and their influence on wind turbine fatigue loads. Renew Energy. 2016;90:352–61. doi:10.1016/j.renene.2016.01.010. [Google Scholar] [CrossRef]
39. Basheer IA, Hajmeer M. Artificial neural networks: fundamentals, computing, design, and application. J Microbiol Methods. 2000;43:3–31. doi:10.1016/S0167-7012(00)00201-3. [Google Scholar] [PubMed] [CrossRef]
40. Hecht-Nielsen R. On the algebraic structure of feedforward network weight spaces. In: Advanced Neural Computers. Amsterdam, The Netherlands: Elsevier; 1990. p. 129–35. [Google Scholar]
41. Schalkoff RJ. Artificial neural networks. New York City, NY: McGraw-Hill; 1997. [Google Scholar]
42. Jain AK, Mao J, Mohiuddin KM. Artificial neural networks: a tutorial. Computer. 1996;29(3):31–44. [Google Scholar]
43. Mahanta J. Introduction to neural networks, advantages and applications; 2017. Available from: https://towardsdatascience.com/introduction-to-neural-networksadvantages-and-applications-96851bd1a207. [Accessed on 2024]. [Google Scholar]
44. Haykin S, Network N. A comprehensive foundation. Neural Netw. 2004;2:41. [Google Scholar]
45. Haykin S. Kalman filtering and neural networks. Hoboken, NJ: John Wiley & Sons; 2004. [Google Scholar]
46. Yu W, He H, Zhang N. Advances in neural networks-ISNN 2009. In: 6th International Symposium on Neural Networks, ISNN 2009; 2009 May 26–29; Wuhan, China. vol. 5552. [Google Scholar]
47. Fan W, Bouguila N, Ziou D. Variational learning for finite Dirichlet mixture models and applications. IEEE Trans Neural Netw Learn Syst. 2012;23(5):762–74. doi:10.1109/TNNLS.2012.2190298. [Google Scholar] [PubMed] [CrossRef]
48. Saravanan KS, Sasithra. Review on classification based on artificial neural networks. Int J Ambient Syst Appl. 2014;2(4):11–8. doi:10.5121/ijasa.2014.2402. [Google Scholar] [CrossRef]
49. Martínez-Porchas M, Villalpando-Canchola E, Vargas-Albores F. Significant loss of sensitivity and specificity in the taxonomic classification occurs when short 16S rRNA gene sequences are used. Heliyon. 2016;2:2–10. [Google Scholar]
50. Abid F, Hamami L. A survey of neural network based automated systems for human chromosome classification. Artif Intell Rev. 2018;49(1):41–56. doi:10.1007/s10462-016-9515-5. [Google Scholar] [CrossRef]
51. Das K, Behera RN. A survey on machine learning: concept, algorithms and applications. Int J Innov Res Comput Commun Eng. 2017;5:1301–9. [Google Scholar]
52. Boutaba R, Salahuddin MA, Limam N, Ayoubi S, Shahriar N, Estrada-Solano F, et al. A comprehensive survey on machine learning for networking: evolution, applications and research opportunities. J Internet Serv Appl. 2018;9:1–99. [Google Scholar]
53. Ogwueleka FN, Misra S, Colomo-Palacios R, Fernandez L. Neural network and classification approach in identifying customer behavior in the banking sector: a case study of an international bank. Hum Factors Ergon Manuf & Serv Ind. 2015;25:28–42. [Google Scholar]
54. Kim JH, Powell WB. Optimal energy commitments with storage and intermittent supply. Oper Res. 2011;59:1347–60. doi:10.1287/opre.1110.0971. [Google Scholar] [CrossRef]
55. Zugno M, Conejo AJ. A robust optimization approach to energy and reserve dispatch in electricity markets. Eur J Oper Res. 2015;247:659–71. doi:10.1016/j.ejor.2015.05.081. [Google Scholar] [CrossRef]
56. Napoli C, Pappalardo G, Tina GM, Tramontana E. Cooperative strategy for optimal management of smart grids by wavelet RNNs and cloud computing. IEEE Trans Neural Netw Learn Syst. 2015;27(8):1672–85. doi:10.1109/TNNLS.2015.2480709. [Google Scholar] [PubMed] [CrossRef]
57. Gómez CQM, García FPM, Arcos AJ, Cheng L, Kogia M, Mohimi A, et al. A heuristic method for detecting and locating faults employing electromagnetic acoustic transducers. Eksploatacja i Niezawodność. 2017;19(4):493–500. doi:10.17531/ein.2017.4.1. [Google Scholar] [CrossRef]
58. Muñoz CQG, Marquez FPG, Lev B, Arcos A. New pipe notch detection and location method for short distances employing ultrasonic guided waves. Acta Acust United Acust. 2017;103(5):772–81. doi:10.3813/AAA.919106. [Google Scholar] [CrossRef]
59. Olaofe ZO. A 5-day wind speed & power forecasts using a layer recurrent neural network (LRNN). Sustain Energy Technol Assess. 2014;6(2):1–24. doi:10.1016/j.seta.2013.12.001. [Google Scholar] [CrossRef]
60. Wilkinson M, Darnell B, van Delft T, Harman K. Comparison of methods for wind turbine condition monitoring with SCADA data. IET Renew Power Gener. 2014;8(4):390–7. doi:10.1049/iet-rpg.2013.0318. [Google Scholar] [CrossRef]
61. Marugán AP, Márquez FPG, Perez JMP, Ruiz-Hernández D. A survey of artificial neural network in wind energy systems. Appl Energy. 2018;228:1822–36. doi:10.1016/j.apenergy.2018.07.084. [Google Scholar] [CrossRef]
62. Riahy GH, Abedi M. Short term wind speed forecasting for wind turbine applications using linear prediction method. Renew Energy. 2008;33:35–41. doi:10.1016/j.renene.2007.01.014. [Google Scholar] [CrossRef]
63. Safavieh E, Ardakani AJ, Laviani AK, Pourmousavi SA, Hosseinian SH, Abedi M. A new integrated approach for very short-term wind speed prediction using wavelet networks and PSO. In: Proceedings of the International Conference on Power Systems; 2007; Kaohsiung, Taiwan. [Google Scholar]
64. Kani SAP, Ardehali MM. Very short-term wind speed prediction: a new artificial neural network-Markov chain model. Energy Convers Manag. 2011;52:738–45. doi:10.1016/j.enconman.2010.07.053. [Google Scholar] [CrossRef]
65. Silva GX, Fonte PM, Quadrado JC. Radial basis function networks for wind speed prediction. In: Proceedings of the 5th WSEAS International Conference on Artificial Intelligence, Knowledge Engineering and Data Bases; 2006; Madrid, Spain. p. 286–90. [Google Scholar]
66. Kulkarni PA, Dhoble AS, Padole PM. Deep neural network-based wind speed forecasting and fatigue analysis of a large composite wind turbine blade. Proc Inst Mech Eng C J Mech Eng Sci. 2019;233:2794–812. doi:10.1177/0954406218797972. [Google Scholar] [CrossRef]
67. Babbar SM, Lau CY. Medium term wind speed forecasting using combination of linear and nonlinear models. Solid State Technol. 2020;63:874–82. [Google Scholar]
68. López P, Velo R, Maseda F. Effect of direction on wind speed estimation in complex terrain using neural networks. Renew Energy. 2008;33(10):2266–72. doi:10.1016/j.renene.2007.12.020. [Google Scholar] [CrossRef]
69. Casás VD, Pena FL, Duro RJ, Lamas A. Automatic aerodynamic design of a wind turbine through evolutionary techniques. In: 2005 IEEE Intelligent Data Acquisition and Advanced Computing Systems: Technology and Applications; 2005; Sofia, Bulgaria, IEEE. p. 454–9. [Google Scholar]
70. Sun H, Qiu C, Lu L, Gao X, Chen J, Yang H. Wind turbine power modelling and optimization using artificial neural network with wind field experimental data. Appl Energy. 2020;280(6):115880. doi:10.1016/j.apenergy.2020.115880. [Google Scholar] [CrossRef]
71. Sun H, Gao X, Yang H. A review of full-scale wind-field measurements of the wind-turbine wake effect and a measurement of the wake-interaction effect. Renew Sustain Energ Rev. 2020;132(1):110042. doi:10.1016/j.rser.2020.110042. [Google Scholar] [CrossRef]
72. Sun H, Gao X, Yang H. Validations of three-dimensional wake models with the wind field measurements in complex terrain. Energy. 2019;189(3):116213. doi:10.1016/j.energy.2019.116213. [Google Scholar] [CrossRef]
73. Sun H, Gao X, Yang H. Investigation into offshore wind farm repowering optimization in Hong Kong. Int J Low Carbon Technol. 2019;14(2):302–11. doi:10.1093/ijlct/ctz016. [Google Scholar] [CrossRef]
74. Lu B, Li Y, Wu X, Yang Z. A review of recent advances in wind turbine condition monitoring and fault diagnosis. In: 2009 IEEE power electronics and machines in wind applications; 2009; Lincoln, Nebraska. p. 1–7. [Google Scholar]
75. Kusiak A, Li W. The prediction and diagnosis of wind turbine faults. Renew Energy. 2011;36:16–23. doi:10.1016/j.renene.2010.05.014. [Google Scholar] [CrossRef]
76. Márquez FPG, Muñoz JMC. A pattern recognition and data analysis method for maintenance management. Int J Syst Sci. 2012;43:1014–28. doi:10.1080/00207720903045809. [Google Scholar] [CrossRef]
77. Jiménez AA, Muñoz CQG, Márquez FPG. Machine learning and neural network for maintenance management. In: Proceedings of the Eleventh International Conference on Management Science and Engineering Management 11; 2018; Kanazawa, Japan; Springer. p. 1377–88. [Google Scholar]
78. Catmull S. Self-organising map based condition monitoring of wind turbines; In: Proceedings of the European Wind Energy Association (EWEA) Annual Conference; 2011 Mar. 14–17; Brussels, Belgium. [Google Scholar]
79. Hong C-M, Cheng F-S, Chen C-H. Optimal control for variable-speed wind generation systems using general regression neural network. Int J Elec Power & Energy Syst. 2014;60:14–23. doi:10.1016/j.ijepes.2014.02.015. [Google Scholar] [CrossRef]
80. Navarrete EC, Perea MT, Correa JCJ, Serrano RVC, Moreno GJR. Expert control systems implemented in a pitch control of wind turbine: a review. IEEE Access. 2019;7:13241–59. doi:10.1109/Access.6287639. [Google Scholar] [CrossRef]
81. Menezes E, Araújo A, Bouchonneau N. A review on wind turbine control and its associated methods. J Clean Prod. 2017;174:945–953. doi:10.1016/j.jclepro.2017.10.297. [Google Scholar] [CrossRef]
82. Jiao X, Meng W, Yang Q, Fu L, Chen Q. Adaptive continuous neural pitch angle control for variable-speed wind turbines. Asian J Control. 2019;21:1966–79. doi:10.1002/asjc.v21.4. [Google Scholar] [CrossRef]
83. Chamorro HR, Riaño I, Gerndt R, Zelinka I, Gonzalez-Longatt F, Sood VK. Synthetic inertia control based on fuzzy adaptive differential evolution. Int J Elec Power & Energy Syst. 2019;105(1):803–13. doi:10.1016/j.ijepes.2018.09.009. [Google Scholar] [CrossRef]
84. Huchet Q, Mattrand C, Beaurepaire P, Relun N, Gayton N. AK-DA: an efficient method for the fatigue assessment of wind turbine structures. Wind Energy. 2019;22:638–52. doi:10.1002/we.v22.5. [Google Scholar] [CrossRef]
85. Moynihan B, Liberatore S, Moaveni B, Khan U. Fatigue life analysis of main shaft bearings in wind turbines using strain measurements collected on blades. In: Dynamics of civil structures. Berlin, Germany: Springer; 2021. vol. 2, p. 185–92. [Google Scholar]
86. Mazetto BM, Ritto TG. Uncertainty and global sensitivity analysis of wind turbines fatigue in non-ideal conditions. J Vib Eng Technol. 2022;10:2391–402. doi:10.1007/s42417-022-00632-7. [Google Scholar] [CrossRef]
87. Galinos C, Larsen TJ, Madsen HA, Paulsen US. Vertical axis wind turbine design load cases investigation and comparison with horizontal axis wind turbine. Energy Proc. 2016;94:319–28. doi:10.1016/j.egypro.2016.09.190. [Google Scholar] [CrossRef]
88. Amzallag C, Gerey JP, Robert JL, Bahuaud J. Standardization of the rainflow counting method for fatigue analysis. Int J Fatigue. 1994;16:287–93. doi:10.1016/0142-1123(94)90343-3. [Google Scholar] [CrossRef]
89. Sutherland HJ. On the fatigue analysis of wind turbines. USA: US Department of Energy (US); 1999. [Google Scholar]
90. Kühn MJ. Dynamics and design optimisation of offshore wind energy conversion systems. The Netherlands: DUWIND, Delft University Wind Energy Research Institute Delft; 2001. [Google Scholar]
91. Katsikogiannis G, Sørum SH, Bachynski EE, Amdahl J. Environmental lumping for efficient fatigue assessment of large-diameter monopile wind turbines. Mar Struct. 2021;77:102939. doi:10.1016/j.marstruc.2021.102939. [Google Scholar] [CrossRef]
92. Passon P, Branner K. Condensation of long-term wave climates for the fatigue design of hydrodynamically sensitive offshore wind turbine support structures. Ships Offshore Struct. 2016;11:142–66. doi:10.1080/17445302.2014.967994. [Google Scholar] [CrossRef]
93. Damgaard M, Andersen LV, Ibsen LB, Toft HS, Sørensen JD. A probabilistic analysis of the dynamic response of monopile foundations: soil variability and its consequences. Probab Eng Mech. 2015;41:46–59. doi:10.1016/j.probengmech.2015.05.001. [Google Scholar] [CrossRef]
94. de Oliveira ÉL, Pesce CP, Mendes B, Orsino RMM, Franzini GR. A Reduced-order mathematical model for the current-induced motion of a floating offshore wind turbine. In: International Conference on Offshore Mechanics and Arctic Engineering; 2021; American Society of Mechanical Engineers. vol. 84768, p. V001T01A004. [Google Scholar]
95. Lui HFS, Wolf WR. Construction of reduced-order models for fluid flows using deep feedforward neural networks. J Fluid Mech. 2019;872:963–94. doi:10.1017/jfm.2019.358. [Google Scholar] [CrossRef]
96. Reddy SB, Magee AR, Jaiman RK, Liu J, Xu W, Choudhary A, et al. Reduced order model for unsteady fluid flows via recurrent neural networks. In: International Conference on Offshore Mechanics and Arctic Engineering; 2019; American Society of Mechanical Engineers. vol. 58776, p. V002T08A007. [Google Scholar]
97. Yeter B, Garbatov Y, Soares CG. Evaluation of fatigue damage model predictions for fixed offshore wind turbine support structures. Int J Fatigue. 2016;87(3):71–80. doi:10.1016/j.ijfatigue.2016.01.007. [Google Scholar] [CrossRef]
98. Ragan P, Manuel L. Comparing estimates of wind turbine fatigue loads using time-domain and spectral methods. Wind Eng. 2007;31(2):83–99. doi:10.1260/030952407781494494. [Google Scholar] [CrossRef]
99. Tibaldi C, Henriksen LC, Hansen MH, Bak C. Wind turbine fatigue damage evaluation based on a linear model and a spectral method. Wind Energy. 2016;19(7):1289–306. doi:10.1002/we.1898. [Google Scholar] [CrossRef]
100. Schløer S, Garcia Castillo L, Fejerskov M, Stroescu E, Bredmose H. A model for quick load analysis for monopile-type offshore wind turbine substructures. Wind Energy Sci. 2018;3(1):57–73. doi:10.5194/wes-3-57-2018. [Google Scholar] [CrossRef]
101. Schafhirt S, Verkaik N, Salman Y, Muskulus M. Ultra-fast analysis of offshore wind turbine support structures using impulse based substructuring and massively parallel processors. In: ISOPE International Ocean and Polar Engineering Conference; 2015; Kona, HI, USA. p. ISOPE-I. [Google Scholar]
102. Zwick D, Muskulus M. Simplified fatigue load assessment in offshore wind turbine structural analysis. Wind Energy. 2016;19(2):265–78. doi:10.1002/we.1831. [Google Scholar] [CrossRef]
103. Owolabi OI, Madushele N, Adedeji PA, Olatunji OO. FEM and ANN approaches to wind turbine gearbox monitoring and diagnosis: a mini review. J Reliab Intell Environ. 2023;9(4):399–419. doi:10.1007/s40860-022-00183-4. [Google Scholar] [CrossRef]
104. Kim HJ, Jang BS, Park CK, Bae YH. Fatigue analysis of floating wind turbine support structure applying modified stress transfer function by artificial neural network. Ocean Eng. 2018;149:113–26. doi:10.1016/j.oceaneng.2017.12.009. [Google Scholar] [CrossRef]
105. Yin X, Zhao X. Big data driven multi-objective predictions for offshore wind farm based on machine learning algorithms. Energy. 2019;186(1):115704. doi:10.1016/j.energy.2019.07.034. [Google Scholar] [CrossRef]
106. Luna J, Falkenberg O, Gros S, Schild A. Wind turbine fatigue reduction based on economic-tracking NMPC with direct ANN fatigue estimation. Renew Energy. 2020;147:1632–41. doi:10.1016/j.renene.2019.09.092. [Google Scholar] [CrossRef]
107. He R, Yang H, Sun S, Lu L, Sun H, Gao X. A machine learning-based fatigue loads and power prediction method for wind turbines under yaw control. Appl Energy. 2022;326(4):120013. doi:10.1016/j.apenergy.2022.120013. [Google Scholar] [CrossRef]
108. Yilmaz AS, Özer Z. Pitch angle control in wind turbines above the rated wind speed by multi-layer perceptron and radial basis function neural networks. Expert Syst Appl. 2009;36(6):9767–75. doi:10.1016/j.eswa.2009.02.014. [Google Scholar] [CrossRef]
109. Ziane K, Ilinca A, Karganroudi SS, Dimitrova M. Neural network optimization algorithms to predict wind turbine blade fatigue life under variable hygrothermal conditions. Eng. 2021;2(3):278–95. doi:10.3390/eng2030018. [Google Scholar] [CrossRef]
110. Shiralkar S, Bahulekar A, Jawade S. The cuckoo search algorithm: a review. Int Res J Eng Technol. 2022;9:1238–46. [Google Scholar]
111. Raman V, Drissi-Habti M. Numerical simulation of a resistant structural bonding in wind-turbine blade through the use of composite cord stitching. Compos B Eng. 2019;176:107094. doi:10.1016/j.compositesb.2019.107094. [Google Scholar] [CrossRef]
112. Mishnaevsky Jr L. Root causes and mechanisms of failure of wind turbine blades: overview. Materials. 2022;15:2959. doi:10.3390/ma15092959. [Google Scholar] [PubMed] [CrossRef]
113. Li F, Cui H, Su H, Iderchuluun, Ma Z, Zhu Y. Icing condition prediction of wind turbine blade by using artificial neural network based on modal frequency. Cold Reg Sci Technol. 2022;194(1):103467. doi:10.1016/j.coldregions.2021.103467. [Google Scholar] [CrossRef]
114. Abdallah I, Tatsis K, Chatzi E. Fatigue assessment of a wind turbine blade when output from multiple aero-elastic simulators are available. Procedia Eng. 2017;199:3170–5. doi:10.1016/j.proeng.2017.09.509. [Google Scholar] [CrossRef]
115. Dervilis N, Choi M, Antoniadou I, Farinholt KM, Taylor SG, Barthorpe RJ, et al. Machine learning applications for a wind turbine blade under continuous fatigue loading. In: Key engineering materials. Trans Tech Publications, Ltd.; 2014. vol. 588, p. 166–74. [Google Scholar]
116. Malik H, Mishra S. Application of probabilistic neural network in fault diagnosis of wind turbine using FAST, TurbSim and Simulink. Procedia Comput Sci. 2015;58(2):186–93. doi:10.1016/j.procs.2015.08.052. [Google Scholar] [CrossRef]
117. Strączkiewicz M, Barszcz T. Application of artificial neural network for damage detection in planetary gearbox of wind turbine. Shock Vib. 2016;2016(4):1–12. doi:10.1155/2016/4086324. [Google Scholar] [CrossRef]
118. Chen Z, Li C, Sanchez RV. Gearbox fault identification and classification with convolutional neural networks. Shock Vib. 2015;2015(2):1–10. doi:10.1155/2015/390134. [Google Scholar] [CrossRef]
119. Janssens O, Slavkovikj V, Vervisch B, Stockman K, Loccufier M, Verstockt S, et al. Convolutional neural network based fault detection for rotating machinery. J Sound Vib. 2016;377(6):331–45. doi:10.1016/j.jsv.2016.05.027. [Google Scholar] [CrossRef]
120. Li G, Chen Y, Wang W, Liu R, Gu F. A convolutional neural network for rotating machinery fault diagnosis based on fast independent component analysis. In: International Conference on Maintenance Engineering; 2020; Zhuhai, China; Springer. p. 700–8. [Google Scholar]
121. Ma S, Cai W, Liu W, Shang Z, Liu G. A lighted deep convolutional neural network based fault diagnosis of rotating machinery. Sensors. 2019;19(10):2381. doi:10.3390/s19102381. [Google Scholar] [PubMed] [CrossRef]
122. Wang MH, Lu SD, Hsieh CC, Hung CC. Fault detection of wind turbine blades using multi-channel CNN. Sustainability. 2022;14(3):1781. doi:10.3390/su14031781. [Google Scholar] [CrossRef]
123. Wang Y, Zhou J, Zheng L, Gogu C. An end-to-end fault diagnostics method based on convolutional neural network for rotating machinery with multiple case studies. J Intell Manuf. 2022;33(3):809–30. doi:10.1007/s10845-020-01671-1. [Google Scholar] [CrossRef]
124. Jing L, Zhao M, Li P, Xu X. A convolutional neural network based feature learning and fault diagnosis method for the condition monitoring of gearbox. Measurement. 2017;111(6):1–10. doi:10.1016/j.measurement.2017.07.017. [Google Scholar] [CrossRef]
125. Simani S, Turhan C. Fault diagnosis of a wind turbine simulated model via neural networks. IFAC-PapersOnLine. 2018;51(24):381–8. doi:10.1016/j.ifacol.2018.09.605. [Google Scholar] [CrossRef]
126. Jiang G, He H, Yan J, Xie P. Multiscale convolutional neural networks for fault diagnosis of wind turbine gearbox. IEEE Trans Ind Electron. 2018;66(4):3196–207. doi:10.1109/TIE.2018.2844805. [Google Scholar] [CrossRef]
127. Jonkman J, Butterfield S, Musial W, Scott G. Definition of a 5-MW reference wind turbine for offshore system development. Golden, CO, USA: National Renewable Energy Lab. (NREL); 2009. [Google Scholar]
128. Contributors WC. File:Jaslovske Bohunice meteorological tower.JPG. Wikimedia Commons; n.d. Available from: https://commons.wikimedia.org/w/index.php?title=File:Jaslovske_Bohunice_meteorological_tower.JPG&oldid=814200756. [Accessed 2023]. [Google Scholar]
129. NREL. Louisiana offshore 90-meter wind map and wind resource potential; 2011. Available from: https://www.nrel.gov/docs/fy10osti/45889.pdf. [Accessed on 2024]. [Google Scholar]
130. Barthelmie RJ, Frandsen ST, Nielsen MN, Pryor SC, Rethore P, Jørgensen HE. Modelling and measurements of power losses and turbulence intensity in wind turbine wakes at Middelgrunden offshore wind farm. Wind Energy: An Int J Progress Appl Wind Power Convers Technol. 2007;10(6):517–28. doi:10.1002/we.238. [Google Scholar] [CrossRef]
131. Sudhamshu AR, Pandey MC, Sunil N, N.S. S, Mugundhan V, Velamati RK. Numerical study of effect of pitch angle on performance characteristics of a HAWT. Eng Sci Technol Int J. 2016;19(1):632–41. doi:10.1016/j.jestch.2015.09.010. [Google Scholar] [CrossRef]
132. Abdin ES, Xu W. Control design and dynamic performance analysis of a wind turbine-induction generator unit. IEEE Trans Energy Convers. 2000;15(1):91–96. doi:10.1109/60.849122. [Google Scholar] [CrossRef]
133. Heier S. Grid integration of wind energy: onshore and offshore conversion systems. Hoboken, NJ: John Wiley & Sons; 2014. [Google Scholar]
Cite This Article
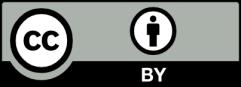
This work is licensed under a Creative Commons Attribution 4.0 International License , which permits unrestricted use, distribution, and reproduction in any medium, provided the original work is properly cited.