Open Access
ARTICLE
Surface Defect Detection and Evaluation Method of Large Wind Turbine Blades Based on an Improved Deeplabv3+ Deep Learning Model
1 Institution of Earthquake Protection and Disaster Mitigation, Lanzhou University of Technology, Lanzhou, 730050, China
2 International Research Base on Seismic Mitigation and Isolation of GANSU Province, Lanzhou University of Technology, Lanzhou, 730050, China
3 Disaster Prevention and Mitigation Engineering Research Center of Western Civil Engineering, Lanzhou University of Technology, Lanzhou, 730050, China
* Corresponding Author: Wanrun Li. Email:
(This article belongs to the Special Issue: Advanced Computer Vision Methods and Related Technologies in Structural Health Monitoring)
Structural Durability & Health Monitoring 2024, 18(5), 553-575. https://doi.org/10.32604/sdhm.2024.050751
Received 16 February 2024; Accepted 22 April 2024; Issue published 19 July 2024
Abstract
The accumulation of defects on wind turbine blade surfaces can lead to irreversible damage, impacting the aerodynamic performance of the blades. To address the challenge of detecting and quantifying surface defects on wind turbine blades, a blade surface defect detection and quantification method based on an improved Deeplabv3+ deep learning model is proposed. Firstly, an improved method for wind turbine blade surface defect detection, utilizing Mobilenetv2 as the backbone feature extraction network, is proposed based on an original Deeplabv3+ deep learning model to address the issue of limited robustness. Secondly, through integrating the concept of pre-trained weights from transfer learning and implementing a freeze training strategy, significant improvements have been made to enhance both the training speed and model training accuracy of this deep learning model. Finally, based on segmented blade surface defect images, a method for quantifying blade defects is proposed. This method combines image stitching algorithms to achieve overall quantification and risk assessment of the entire blade. Test results show that the improved Deeplabv3+ deep learning model reduces training time by approximately 43.03% compared to the original model, while achieving mAP and MIoU values of 96.87% and 96.93%, respectively. Moreover, it demonstrates robustness in detecting different surface defects on blades across different backgrounds. The application of a blade surface defect quantification method enables the precise quantification of different defects and facilitates the assessment of risk levels associated with defect measurements across the entire blade. This method enables non-contact, long-distance, high-precision detection and quantification of surface defects on the blades, providing a reference for assessing surface defects on wind turbine blades.Graphic Abstract
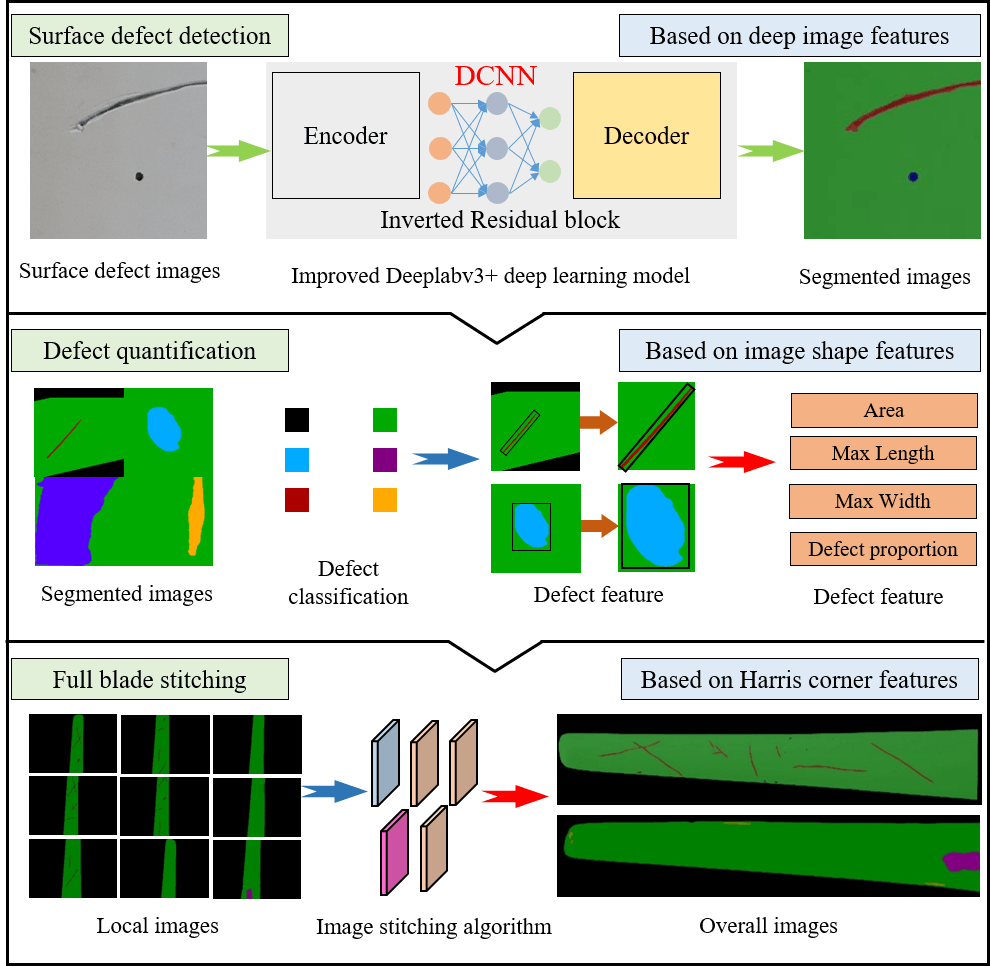
Keywords
Cite This Article
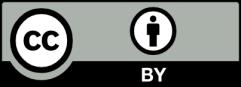
This work is licensed under a Creative Commons Attribution 4.0 International License , which permits unrestricted use, distribution, and reproduction in any medium, provided the original work is properly cited.