Open Access
ARTICLE
Reinforcement Effect of Recycled CFRP on Cement-Based Composites: With a Comparison to Commercial Carbon Fiber Powder
Research Center for Wind Engineering and Engineering Vibration, Guangzhou University, Guangzhou, 510006, China
* Corresponding Author: Zhifang Zhang. Email:
Structural Durability & Health Monitoring 2024, 18(4), 409-423. https://doi.org/10.32604/sdhm.2024.048597
Received 12 December 2023; Accepted 26 February 2024; Issue published 05 June 2024
Abstract
In this paper, recycled carbon fiber reinforced polymer (CFRP) mixture (CFRP-M, including recycled carbon fiber and powder) and refined recycled CFRP fiber (CFRP-F, mostly recycled carbon fiber) were added to cement to study the influence of addition on the flexural strength, compressive strength, and fluidity of cement-based materials. The recycled CFRP were prepared by mechanically processing the prepreg scraps generated during the manufacture of CFRP products. For comparison, commercial carbon fiber powder was also added in cement and the performance was compared to that of addition of recycled CFRP. The hydration products and strengthening mechanism of cement-based materials were analyzed by Fourier Transform Infrared Spectroscopy (FTIR) and Scanning Electron Microscope (SEM). The results show that the recycled CFRP has limited impact on the compressive strength but has an obvious improvement in the flexural strength of cement-based composites. Notably, CFRP-F is superior to CFRP-M in the reinforcement of cement-based materials. When the mass content of CFRP-F is 5%, the fluidity is 100 mm, and the flexural strength of specimens can be increased by up to 43.55%. Through XRD, FTIR, and SEM analysis, it is found that the main mechanism of recycled CFRP reinforced cement-based materials is the “bridging effect” induced by fibers and can prevent or delay the development of cracks. The recycled CFRP has no influence on the hydration process and will not introduce any new hydration products. Current research not only provides a theoretical basis for the design and use of recycled CFRP to reinforce cement-based composites but also offers a solution to relieve environmental pressure and improve resource utilization.Keywords
Carbon fiber reinforced polymer (CFRP) is widely used in aerospace, construction, transportation, and other fields due to its excellent properties. However, during the manufacturing process or at the end of its service life, a large amount of CFRP waste is produced. Traditional treatment methods such as landfills and incineration may cause environmental concerns and waste resources. Extensive studies have shown that adding a suitable amount of fiber, such as carbon fiber, glass fiber, or PVA, to the cement matrix can effectively enhance its mechanical properties. Specifically, the addition of fibers can improve the properties of cementitious composites [1], such as compressive strength [2], flexural strength [3], durability [4], shrinkage, and flexural toughness [5].
Carbon fiber reinforced composites (CFRP) possess exceptional characteristics such as high strength, lightweight, highly effective load-bearing capacity, good corrosion resistance, high-temperature tolerance, and ease of molding. These remarkable advantages have made CFRP widely used in aerospace, construction, transportation, wind power generation, and more engineering fields [6]. However, with the expanding use of CFRP, a large amount of CFRP waste is generated [7], and it is urgent to find ways to recycle the originally expensive carbon fiber for reuse from such waste [8]. Data shows that a total of about 8,500 aircraft worldwide are expected to be decommissioned by 2025. According to the American Wind Power Association forecast [9], by 2035, more than 700,000 tons of turbine blades for wind power will be phased out, and by 2055, this number is expected to reach 2.7 million tons. Therefore, a significant number of CFRP components will reach the end of their operational lifespan in the coming decade [10]. The traditional methods to handle the CFRP waste, such as incineration or landfill, will lead to substantial economic losses, and result in environmental issues including but not limited to air, groundwater, and soil pollution, as well as occupying a large area of land for waste disposal [11].
A feasible solution is to incorporate recycled CFRP into cement-based materials to investigate whether it can provide comparable reinforcement as commercial carbon fiber or carbon fiber powder, as the main constitute of CFRP is carbon fiber. If recycled CFRP is appropriately treated and utilized to enhance cement-based materials, it not only facilitates waste resource recycling but also potentially improves the performance of cementitious composite materials [12]. It has been shown that the addition of appropriate amounts of recycled carbon fiber reinforced polymer (CFRP) has a significant effect on the properties of cementitious materials. Nguyen et al. [13] cut the prepreg waste into fiber bundles of about 20 mm in length and cured them in an oven at 150°C for 24 h. The results showed that the maximum increase in compressive and flexural strength was 13% and 20%, respectively, and the cracking caused by shrinkage could be effectively reduced. Wang et al. [14] used 1 mol/L NaOH solution to treat recycled carbon fiber with residual thermoset epoxy resin on its surface, before its use in cementitious mortar. The results showed that the mechanical properties of the samples were improved and the maximum reduction of drying shrinkage was 26.7%. Akbar et al. [15] added the milled recycled carbon into the cement, and the results show that the flexural and compressive strengths of cement were increased by 82% and 47%, and the degree of hydration and chemically bounded water has increased by 6.64% and 1.59%.
In this paper, CFRP prepreg scraps from the factory production process were mechanically recycled into a CFRP mixture and then added to cementitious materials. The CFRP prepreg used is a prepreg waste generated during the production process when it is cut to fit the design, and its main component is carbon fiber. Since it is not involved in the hot compression molding of the composite material, the properties of the carbon fibers in the CFRP prepreg scraps are close to those of the original carbon fibers. Furthermore, it is a consistent and abundant source of industrial waste found in all composite manufacturing facilities. There is a large amount of powder in the recycled CFRP mixture, so the powder was also characterized and studied by comparison to those of commercial carbon powder. The effect of recycled CFRP on flexural strength, compressive strength, and fluidity of recycled CFRP on cement-based materials was evaluated by specimen testing. The hydration products of cement were further analyzed by Fourier transform infrared spectroscopy (FTIR) and scanning electron microscopy (SEM). The reinforcement effect of recycled CFRP was also compared to that of commercial carbon fiber powder on the cement-based composites. The findings in the present study are crucial in establishing a theoretical basis for the potential widespread application of recycled CFRP reinforced cement-based composites in engineering fields. The study of recycled CFRP reinforced cementitious composites will benefit both environmental protection and resource utilization.
The cement used in the current experiment is PO.42.5R ordinary Portland cement, sourced from the Shijing brand in Guangzhou, China. Recycled CFRP with a length of approximately 6 mm is obtained by mechanical treatment on the original CFRP prepreg scraps (Fig. 1) directly transported from the manufacturing factory. The initial recycled CFRP is a mixture of long carbon fibers and carbon fiber powder, which is referred to as CFRP-M in this study. The powder in the recycled CFRP mixture was removed by screening to obtain the recycled CFRP fibers, which are referred to as CFRP-F in this paper. Therefore, there are two kinds of recycled CFRP materials used in the current experiment, CFRP-M and CFRP-F (Fig. 2). For comparison, a commercial carbon fiber powder (CP, Fig. 3) which was often used in addition to cement was also studied in this experiment. The composition and particle size of CP are similar to those of powders in CFRP-M. The features of commercial CP are summarized in Table 1 (data provided by Nanjing Weida Composite Materials Co., Ltd., Nanjing, China).
Figure 1: Original recycled CFRP prepreg scraps from CFRP product manufacturing factory
Figure 2: Recycled CFRP
Figure 3: Commercial carbon fiber powder
Figs. 4 and 5 show the SEM images illustrating the morphology of the powder and CP in CFRP-M, respectively. A comparison of these images reveals that the powder in CFRP-M is mainly composed of carbon fiber powder, and mixed with a small amount of lumps, which may be the exfoliated resin component in the recycled CFRP materials. In contrast, when compared to the commercial carbon fiber powder, the length of most carbon fiber in CFRP-M is around 100 μm, while the length of the most carbon fibers in CP is less than 50 μm.
Figure 4: SEM images of morphology of carbon fiber powder in CFRP-M
Figure 5: SEM images of morphology of commercial carbon fiber powder
The results of the specific gravity characterization for the fibers and powder in the recycled CFRP-M are shown in Fig. 6. Ms represents the mass of the recycled fibers in the CFRP mixture, while Mv stands for the mass of the recycled CFRP-M. From the figure, it can be seen that when the mass of CFRP-M reaches 150 g and above, the specific gravity of the mass of recycled CFRP-F obtained tends to stabilize at around 0.75. It can be inferred that the specific gravity of the mass of CFRP-F in the recycled CFRP mixture is about 0.75, and that of the recycled carbon powder is about 0.25.
Figure 6: Mass proportion of CFRP fiber in recycled CFRP mixture
The XRD test results of the recycled CFRP powder and the commercial carbon fiber powder CP are shown in Fig. 7, where RCP and CP represent the recycled CFRP powder and the commercial carbon fiber powder, respectively. The XRD peak intensity indicates that the chemical composition of the recycled CFRP powder is basically the same as that of the commercial carbon fiber powder. A comparison of the images of the two powders shows that the image of the recycled CFRP powder is rougher than that of the CP, indicating that it contains more amorphous substances such as epoxy resin.
Figure 7: X-ray diffraction patterns of RCP and CP
The particle size distribution of recycled carbon powder (RCP) and commercial carbon powder (CP) is shown in Fig. 8. Compared with CP, the powder in RCP is much larger, and the particle size is mainly in the range of 10–100 μm, but more than 60% of the particle size distribution is around 10 μm.
Figure 8: (a) Average size distribution, and (b) cumulative size distribution of RCP and CP
The results of the water absorption of the three materials, namely CFRP-M, CFRP-F, and CP, are shown in Fig. 9. It can be found that the water absorption rate of recycled CFRP-M (380%) is marginally higher than that of recycled CFRP-F (350%). In contrast, CP demonstrates the lowest water absorption rate, standing at 260%.
Figure 9: Water absorption rate of recycled CFRP-M, CFRP-F, and commercial carbon powder CP
2.2 Sample Preparation and Testing Equipment
The water-cement ratio of the specimens was fixed at 0.45 to ensure the same degree of hydration of cement, and a total of 21 groups of specimens were prepared with the mass fraction of recycled CFRP ranging from 0% to 6% increased by 1%. The two types of recycled CFRP used in the experiment were CFRP-F and CFRP-M. A commercial carbon fiber powder (CP) was also added to the cement-based materials for comparison. The mass fraction of CP varies from 0% to 6%, increasing in the increments of 1%. Although the good water absorption capability of recycled CFRP will lead to a large amount of water reduced during the mixing of cement, however, the recycled CFRP with water absorbed can gradually release water during the hydration process of cement, which plays a key role in internal curing and can improve the internal relative humidity of cement [16].
The flexural and compressive specimens were made according to the “Test Methods for Strength of Cement Mortar” GB/T17617-1999, China. The weighed CFRP-M, CFRP-F, and CP were mixed with cement by a cement mixer for about 1 min, and then water was slowly added and stirred for 1 min. The prepared mixture was poured into a mold (40 mm * 40 mm * 160 mm) and vibrated to eliminate bubbles. Due to the good dispersion of recycled CFRP fibers, it is not easy to agglomerate in the cement paste, so the homogeneity of the specimen is high. After 24 h, it was taken out from the mold and put into the standard curing box until it was taken out during the test. The compressive and flexural strengths of the specimens were tested at 7 d, 28 d, and 120 d using an electronic universal testing machine manufactured by Instron, USA. The flexural strength was tested on 40 mm * 40 mm * 160 mm specimens. The loading rates are set to 50 N/s. After the flexural strength test was completed, the original specimen was separated into two pieces of the specimen (about half and half), and these specimens were then used to test the compressive strength, the loading rates were set to 2500 N/s.
The cement fluidity test was conducted following “Test Methods for Water Requirement, Setting Time and Stability of Standard Cement Paste” (GB/T1346-2011). The average diameter of the mixture in two vertical directions was measured. The particle size analysis of the recycled CFRP powder was carried out using a Malvern MS2000 laser particle size analyzer from the UK. X-ray diffraction (XRD) testing of the recycled CFRP powder was performed using a Rigaku Ultima VI X-ray diffractometer from Japan. The target material employed for the experiment was a copper target, and the scanning angle was ranged from 2θ = 5° to 2θ = 80°, and the scanning speed was set at 2°/min. The samples were ground and filtered through 200 mesh net and then dried before being analyzed using a Bruker TENSOR II+ Hyperion2000 infrared spectrometer. Besides, the crushed sample fragments were dried and gold sprayed, and the fiber reinforcement mechanism was analyzed by a Phenom Nano benchtop scanning electron microscope (Fenner, Netherlands).
The flexural strength of specimens was measured at 7 days, 28 days, and 120 days of age. The results are compared in Fig. 10. Remarkable enhancement of flexural strength is seen for cement matrix reinforced by CFRP-M and CFRP-F. The flexural strength gradually increases with the increasing amount (<5%) of recycled CFRP added to the cement. The enhancement is the best when the added dosage reaches 5%. Compared with the plain cement matrix, at the age of 7 days, 28 days and 120 days, the samples added with 5% CFRP-M has increased by 34.41%, 37.26%, and 26.63%, and the samples added with 5% CFRP-F has increased by 43.55%, 42.01%, and 23.23%. When the recycled CFRP content exceeds 5%, the flexural strength begins to decrease. The reason is if the recycled CFRP are used in excessive amounts, this will lead to uneven distribution of recycled CFRP in the cement, and the cement-based composites will have poor bonding surfaces and the load transfer effect is reduced [17]. Besides, a large number of air bubbles would be introduced in the processing of samples which can lead to the formation of a large number of pores and voids in the sample [18], thus affecting the overall flexural strength. With the proper amount of recycled CFRP, as the main component of recycled CFRP is carbon fiber which has high tensile modulus and tensile strength, the carbon fibers can form a stable grid structure inside the cement. The fiber bridging can inhibit the generation and diffusion of cracks in cement [19], and reduce the tip stress. When the cement is pulled, the friction resistance caused by pulling recycled CFRP out of the concrete under tension is large. The added recycled FRP fibers can consume more external energy and delay the concrete tensile failure [20], thereby can significantly improve the flexural strength of the samples [21] and prolong the life of the specimen [22]. In addition, the recycled CFRP can absorb and contain the water during the mixture, and then the water can be released gradually during curing, which can improve the internal relative humidity of cement and finally maximize the hydration degree of cement [23].
Figure 10: Flexural strength of specimens after 7 days, 28 days, and 120 days
The flexural strength of the sample mixed with commercial carbon powder CP is lower than that of plain cement. The flexural strength decreases with the increase of CP content in concrete. When the content is 6%, the flexural strength of the sample has decreased by 13.71%, compared to the plain cement. It can be inferred that when the CP content continues to increase, the flexural strength of the sample will be further reduced. The flexural strength values of 7 days, 28 days, and 120 days samples have shown the same trend. This might be explained by the literature of Li et al. [24], in which it was found that after the added carbon powder is high, the surface of the particles will absorb more water, which has a great impact on the hydration process, resulting in a reduction in the strength of the specimen. Wu et al. [25] showed that the incorporation of untreated commercial short-cut carbon fibers into the cement matrix does not result in effective fiber bridging, as it requires a certain fiber length to enhance the mechanical properties of cement. However, with a length of only 10 μm, CP cannot form a stable network structure in the matrix. This also provides insight into why the incorporation of commercial carbon fiber powder into cement decreases the mechanical properties of cement. Since the particle size and composition of the powder in CP and CFRP-M are similar, this further explains why CFRP-F has a better enhancement on the cement matrix. This also provides insight into why the incorporation of commercial carbon fiber powder into cement decreases the mechanical properties of cement. Since the particle size and composition of the powder in CP and CFRP-M are similar, this further explains why CFRP-F has a better enhancement on the cement matrix than CFRP-M.
As shown in Fig. 11, after compression, the brittle failure of the cement test block without recycled CFRP (Fig. 11a) occurred, and the cement peels off from the surface, and finally formed a shape similar to an up-side-down pyramid. The cement around the test block with 6% recycled CFRP (Fig. 11b) only shows a tendency to peel off but does not really happen, and its surface only has a small number of cracks. The reason may be due to the constraint of recycled CFRP fibers on cement and the bridging effect on initial cracks [26]. The compression testing was conducted on specimens at 7 days, 28 days, and 120 days of age. The results are compared in Fig. 12. The addition of recycled CFRP can slightly enhance the compressive strength of cement. Similar to the trend of flexural strength, the compressive strength increases with the increasing amount (<0.5%) of recycled CFRP added to concrete. The enhancement was best when the content was 5%, compared with the plain cement matrix at 7 days, 28 days, and 120 days, the samples added with 5% CFRP-M has increased by 23.69%, 9.77%, and 5.11%, and the samples added with 5% CFRP-F has increased by 24.53%, 9.19% and 5.71%. Compared with flexural strength, the enhancement of recycled CFRP on the compressive strength of the cement matrix is not significant, especially after 28 days of curing, the enhancement is less than 10%. This phenomenon can be attributed to the occurrence of compressive failure within the colloid between particles, resulting in lower strength during the early stages of curing. The bonding force between the carbon fiber in the recycled CFRP and the cement naturally increase. Consequently, the contribution of the fiber reinforcement becomes less prominent over time. As for the samples mixed with CP, the compressive strength is higher than that of plain cement samples. At the curing age of 7 days, 28 days, and 120 days, the compressive strength increased by 7.53%, 6.09%, and 3.82%, respectively. This improvement can be attributed to the ability of CP to effectively fill the voids within the cement matrix. By filling these voids, CP enhances the compactness and density of the cement [27], ultimately leading to an increase in compressive strength.
Figure 11: Compressive failure mode of cement test block (a) without adding CFRP; (b) with adding 6%
Figure 12: Compressive strength of specimens after 7 days, 28 days, and 120 days
From Fig. 13, it can be seen that under the same dosage, CFRP-F has less effect on cement matrix fluidity. When the content of two recycled CFRP products (CFRP-F and CFRP-M) is less than 5%, the fluidity of cement matrix is good, and the slump is above 10 cm. When the content of the two CFRP recycles reached 6%, the slump was reduced to only 8 cm, indicating the loss of fluidity. In contrast, commercial carbon powder CP has less effect on the fluidity of cement. Even when the content reaches 6%, the slump of cement is still above 10 cm, indicating that the cement still has good fluidity. In summary, when the content of CFRP-M, CFRP-F, and CP is 6%, the fluidity of cement decreases by 29.63%, 24.44%, and 25.18%, respectively. All three substances contribute to a reduction in the fluidity of the cement matrix. This can be attributed to the water absorption properties of carbon fiber and CP present in recycled CFRP. As the content of these materials increases, they absorb more free water within the cement due to a constant water-cement ratio. Consequently, the thickness of the water layer between particles in the cement slurry decreases, leading to increased friction between particles [28]. In addition, fibers are more likely to form a stable network structure in the cement [29]. This network structure within the cement paste primarily originates from various forces, such as the van der Waals forces and flocculation interactions among cement particles [30], which, in turn, lead to a decrease in fluidity [31]. Similar conclusions were reported by Wong et al. [32] and Shahbazi et al. [27] regarding the impact of this internal network structure on the fluidity of cement paste [33].
Figure 13: Effect of various admixtures on fluidity of cement paste
The effect of recycled CFRP on the hydration reaction of cement was analyzed by observing the FTIR spectra of the plain cement specimens and the samples mixed with recycled CFRP and CP. From the comparison of Figs. 14 and 15, it is concluded that, compared to plain cement, the hydration products of the samples mixed with recycled CFRP and CP have the same absorption peak at the same position, indicating that the incorporation of these two substances does not change the types of hydration products. Therefore, it can be inferred that the incorporation of recycled CFRP and CP will not affect the hydration process of the cement matrix. In more detail, the absorption peak at 3644 cm−1 appear to be due to the O-H stretching of the portlandite (Ca (OH)2) phase [34]. The absorption peak at 1652~1643 cm−1 is the in-plane bending vibration peak of bound water H-O-H in hydration product [35]. The absorption peak of asymmetric Si-O stretching vibration in Ettringite appears at 1200 cm−1 [36]. Due to the carbonation of CO2 in the atmosphere, the cement forms calcium carbonate with an absorption peak at 1488 cm−1. The absorption peak at 960 cm−1 may be formed by unhydrated C2S. Further, the above several admixtures will not produce chemical composition of cement matrix. In summary, the analysis of FTIR spectra indicates that the incorporation of recycled CFRP and CP does not alter the type of hydration products formed during the cement hydration process. The observed absorption peaks correspond to the typical components of cement hydration, and the admixtures do not introduce any additional chemical compositions into the cement matrix.
Figure 14: FTIR spectra of plain cement and cement with recycled CFRP at 7 d and 28 d
Figure 15: FTIR spectra of plain cement and cement with CP at 7 d and 28 d
Fig. 11 shows the effect of recycled CFRP fiber bundles on the development of microcracks. In Fig. 16a, it is evident that microcracks initially form along the weaker hydration products of the cement. However, when encountering the recycled CFRP fiber bundles, the microcracks change their direction and propagate along the interface of the recycled CFRP fibers. This suggests that the presence of the CFRP fibers influences the path and direction of microcrack development. In Fig. 16b, the effect of a single carbon fiber, separated from the recycled CFRP, on microcrack development is displayed. The cracks initiate from the top and progress downwards, eventually branching into two at the carbon fiber interface. Notably, the width of the two separated cracks is significantly narrower, indicating that the original cracks tend to propagate towards the carbon fiber interface. This phenomenon can be attributed to the redistribution of fracture energy, which influences the direction in which the cracks propagate. In summary, the observations from Fig. 16 demonstrate that the introduction of recycled CFRP fiber bundles alters the path of microcrack formation, leading the cracks to develop along the interface of the CFRP fibers. Additionally, the presence of individual carbon fibers affects the width and direction of crack propagation, indicating the redistribution of fracture energy within the materials.
Figure 16: Microcrack development in cement composites
A large number of dendritic C-S-H can be clearly seen on the surface of recycled CFRP after hydration for 4 h, indicating that the surface of recycled CFRP is suitable for the nucleation and growth of C-S-H (Fig. 17a). The hydroxyl groups on the recycled CFRP are also capable of forming hydrogen bonds with calcium silicate hydrate (C-S-H) gel or cement hydration products, which can be explained by the presence of some carboxylic and hydroxyl groups in the polymeric coatings on the surfaces of recycled, which could react with calcium ions (Ca2+) and generate ionic bonds [37]. After hydration for 7 h, it can be seen that the surface of recycled CFRP is completely covered by the hydration products of cement, and rod-like ettringite can also be observed in the field of view (Fig. 17b), which indicates that recycled CFRP has no effect on the hydration reaction of cement, and the bonding strength between recycled CFRP and cement is good.
Figure 17: Microstructure of recycled CFRP
Fig. 17c reveals the presence of residual epoxy resin within the fiber bundle, while the outer surface appears smooth. This observation suggests that the primary failure mode of the fiber is predominantly pull-out failure. During the pull-out process, the outer edge of the fiber bundle undergoes scraping, leading to the shedding of the epoxy resin. When the sample experiences a fracture, the bonding force between the fiber and the matrix creates a bridging effect that impedes crack propagation. As the sample reaches its maximum load-bearing capacity, the fiber on the fracture surface disengages from the bonding force and slips out. This pull-out mechanism consumes a significant amount of energy, contributing to the actual load-bearing capacity and toughness of the material [38].
The current experimental investigation aims to understand the effect of recycled CFRP with different dosages added as reinforcement in cement-based materials. For comparison, the effect of the carbon powder in the recycled CFRP mixture was compared to the results of the commercial carbon powder. Different additional amounts of recycled CFRP were investigated, and the flowability, compressive, and flexural strength of the cementitious materials were evaluated. In addition, the reinforcement mechanism of recycled CFRP in cement-based materials and hydration products was analyzed by SEM and FTIR.
(1) The addition of CFRP-M or CFRP-F into the cement has improved the flexural and compressive strength, the effect of flexural strength enhancement is more obvious, and the reinforcement effect is most obvious when the amount of recycled CFRP is 5%, reaching 43.55% and 42.01% at the age of 7 d and 28 d, respectively. With the additional amount of recycled CFRP increased from 0% to 6%, the enhancement of the mechanical properties of cement-based materials is more obvious in the early stage. The flexural strength of adding 5% CFRP-M and CFRP-F at 7 days has increased by 34.41% and 43.55%, respectively, which is close to the increase rate of that at 28 days. At 120 days, the increase rate from plain cement to cement with 5% recycled CFRP has reduced to 26.63% and 23.23%. Similarly, from 0% to the best performance of 5% addition of recycled CFRP, the improvement rates of CFRP-M and CFRP-F on compressive strength at 7d were 23.69% and 24.53%, respectively, but at 28 days and 120 days, the improvement rates have decreased to be less than 10%.
(2) The fluidity of the cement matrix is negatively influenced by the content of CFRP-M and CFRP-F. Specifically, CFRP-M has a greater negative impact on fluidity. However, when the addition amount is below 5%, the cement paste can still maintain good fluidity with a slump value >10 cm. If the content of the two recycled CFRP parameters exceeds 5%, the cement matrix will experience a severe loss of fluidity.
(3) Through FTIR analysis, it was found that both CFRP-M and CFRP-F will not affect the chemical properties of the cement matrix and will not affect the hydration process. SEM analysis showed that the interface bonding performance between the cement matrix and the recycled CFRP is good, which makes the recycled CFRP fiber play a better bridging role in the cement matrix. This bridging effect is the primary reason for the enhancement of mechanical properties.
(4) With the increase of the addition of CP in cement, the flexural strength of cement-based materials was decreased, and the compressive strength was slightly improved. When the CP content is 6%, the fluidity of the matrix decreases by 25.18%. At the age of 7 d, the flexural strength of the matrix has decreased by 13.71%, and the compressive strength has increased by 7.53%. It was found by FTIR analysis that commercial carbon powder does not influence the hydration products or the hydration process of the cement matrix.
In summary, recycled CFRP obtained by mechanical processing of CFRP prepreg scraps generated during the manufacturing of CFRP products can be added to cement to enhance the flexural and compressive properties. The recycled CFRP does not have a chemical reaction with the cement, and the bridging effect is the main mechanism behind why the added recycled CFRP can increase the mechanical properties. When the amount of added recycled CFRP is less than 5%, no obvious effect on the flowability of cement was observed. Therefore, the CFRP prepreg scraps generated in the manufacturing process of CFRP products can be processed and added to cement to create recycled CFRP-reinforced cement, which has the advantage of low cost and stable performance. Durability investigation is to be further studied to better evaluate the life cycle of recycled CFRP-reinforced cement and concrete.
Acknowledgement: The authors thank Associate Professor Xiaowei Ouyang for his support in the equipment arrangement and the useful suggestions in the research.
Funding Statement: The research has been supported by the 111 Project (Grant No. D21021), the Key Discipline of Materials Science and Engineering, the Bureau of Education of Guangzhou (Grant No. 202255464), and the Municipal Science and Technology Planning Project of Guangzhou (Grant No. 20212200004).
Author Contributions: The authors confirm contribution to the paper as follows: methodology, testing, formal analysis, writing-original draft: Hantao Huang; conception, supervision, funding, writing-review and editing: Zhifang Zhang; data collection, testing, formal analysis: Zhenhua Wu; methodology, analysis, interpretation of results: Yao Liu. All authors reviewed the results and approved the final version of the manuscript.
Availability of Data and Materials: Some or all data, models, or codes that support the findings of this study are available from the corresponding author upon reasonable request.
Conflicts of Interest: The authors declare that they have no conflicts of interest to report regarding the present study.
References
1. Beroll, P., Schmalzl, S., Volkmer, D. (2020). Influence of surface-modification, length and volume fraction of carbon short fibers on the mechanical properties of calcium aluminate cement systems. Materials Today Communications, 25, 101704. [Google Scholar]
2. García, D., Vegas, I., Cacho, I. (2014). Mechanical recycling of GFRP waste as short-fiber reinforcements in microconcrete. Construction and Building Materials, 64, 293–300. [Google Scholar]
3. Li, H., Schamel, E., Liebscher, M., Zhang, Y., Fan, Q. (2023). Recycled carbon fibers in cement-based composites: Influence of epoxide matrix depolymerization degree on interfacial interactions. Journal of Cleaner Production, 411, 137235. [Google Scholar]
4. Wei, J., Ma, S., Thomas, D. G. (2016). Correlation between hydration of cement and durability of natural fiber-reinforced cement composites. Corrosion Science, 106, 1–15. [Google Scholar]
5. Rangelov, M., Nassiri, S., Haselbach, L., Englund, K. (2016). Using carbon fiber composites for reinforcing pervious concrete. Construction and Building Materials, 126, 875–885. [Google Scholar]
6. Liu, B., Zhang, X., Ye, J., Liu, X., Deng, Z. (2022). Mechanical properties of hybrid fiber reinforced coral concrete. Case Studies in Construction Materials, 16, e00865. https://doi.org/10.1016/j.cscm.2021.e00865 [Google Scholar] [CrossRef]
7. Naqvi, S. R., Prabhakara, H. M., Bramer, E. A., Dierkes, W., Akkerman, R. et al. (2018). A critical review on recycling of end-of-life carbon fiber/glass fiber reinforced composites waste using pyrolysis towards a circular economy. Resources, Conservation and Recycling, 136, 118–129. [Google Scholar]
8. Chin, K. Y., Shiue, A., Wu, Y. J., Chang, S., Li, Y. et al. (2022). Studies on recycling silane controllable recovered carbon fiber from waste CFRP. Sustainability, 14(2), 700. [Google Scholar]
9. Bank, L., Arias, F. (2016). Assessment of present/future decommissioned wind blade fiber-reinforced composite material in the United States. New York, NY, USA: Department of Civil Engineering, City College of New York. [Google Scholar]
10. Liu, P., Barlow, C. (2017). Wind turbine blade waste in 2050. Waste Management, 62, 229–240 [Google Scholar] [PubMed]
11. Xiong, C., Li, Q., Lan, T., Li, H., Long, W. et al. (2021). Sustainable use of recycled carbon fiber reinforced polymer and crumb rubber in concrete: Mechanical properties and ecological evaluation. Journal of Cleaner Production, 279, 123624. [Google Scholar]
12. Correia, J., Almeida, N., Figueira, J. (2011). Recycling of FRP composites: Reusing fine GFRP waste in concrete mixtures. Journal of Cleaner Production, 19(15), 1745–1753. [Google Scholar]
13. Nguyen, H., Carvelli, V., Fujii, T., Okubo, K. (2016). Cement mortar reinforced with reclaimed carbon fibres, CFRP waste, or prepreg carbon waste. Construction and Building Materials, 126, 321–331. [Google Scholar]
14. Wang, Y., Zhang, S., Li, G., Shi, X. (2019). Effects of alkali-treated recycled carbon fiber on the strength and free drying shrinkage of cementitious mortar. Journal of Cleaner Production, 228, 1187–1195. [Google Scholar]
15. Akbar, A., Kodur, V., Liew, K. (2021). Microstructural changes and mechanical performance of cement composites reinforced with recycled carbon fibers. Cement & Concrete Composites, 121, 104069. [Google Scholar]
16. Guo, A., Sun, Z., Satyavolu, J. (2022). Impact of modified kenaf fibers on shrinkage and cracking of cement pastes. Construction and Building Materials, 264, 120230. [Google Scholar]
17. Natali, A., Manzi, S., Bignozzi, M. (2021). Novel fiber-reinforced composite materials based on sustainable geopolymer matrix. Procedia Engineering, 21, 1124–1131. [Google Scholar]
18. Zhu, W., Hu, X., Zhang, J., Li, T., Chen, Z. et al. (2021). Experimental study on mechanical properties of a novel micro-steel fiber reinforced magnesium phosphate cement-based concrete. Frontiers of Structural and Civil Engineering, 15(4), 1047–1057. [Google Scholar]
19. Li, H., Liebscher, M., Ranjbarian, M., Hempel, S., Tzounis, L. et al. (2019). Electrochemical modification of carbon fiber yarns in cementitious pore solution for an enhanced interaction towards concrete matrices. Applied Surface Science, 487, 52–58. [Google Scholar]
20. Gao, Y., Wang, B., Liu, C., Hui, D., Xu, Q. (2022). Experimental study on basic mechanical properties of recycled steel fiber reinforced concrete. Reviews on Advanced Materials Science, 61(1), 417–429. [Google Scholar]
21. Shi, Z., Sun, G., Pang, J. (2023). Research progress on the influence of varying fiber contents on mechanical properties of recycled concrete. Structural Durability & Health Monitoring, 17(3), 239–255. https://doi.org/10.32604/sdhm.2023.022816 [Google Scholar] [CrossRef]
22. Gopinath, S., Ramachandra, M., Iyer, N. (2013). Experimental investigations on the glass fabrics for confinement of concrete specimens. Structural Durability & Health Monitoring, 9(1), 1–20. https://doi.org/10.32604/sdhm.2013.009.001 [Google Scholar] [CrossRef]
23. Wei, Y., Guo, W., Liang, S. (2018). Chloride ingress in internally cured concrete under complex solution. Journal of Materials in Civil Engineering, 30(4), 04018037. [Google Scholar]
24. Li, S., Chen, Y., Guo, Y., Wang, R. (2022). Analysis of piezoresistance characteristics of cement mortar mixed with carbon fiber powder. Science Technology and Engineering, 22(20), 8828–8833 (In Chinese). [Google Scholar]
25. Wu, Z., Sha, J., Xu, H., Guo, F. (2016). Research progress on toughening of magnesium phosphate cement. Materials Reports, 30(S1), 454–457 (In Chinese). [Google Scholar]
26. Özalp, F., Yilmaz, H. D., Akcay, B. (2022). Mechanical properties and impact resistance of concrete composites with hybrid steel fibers. Frontiers of Structural and Civil Engineering, 16(5), 615–623. [Google Scholar]
27. Shahbazi, R., Korayem, A., Razmjou, A., Duan, W., Wang, C. et al. (2020). Integrally hydrophobic cementitious composites made with waste amorphous carbon powder. Construction and Building Materials, 233, 117238. [Google Scholar]
28. Jun, H., Seo, D., Lim, D., Park, J., Heo, G. (2023). Effect of carbon and steel fibers on the strength properties and electrical conductivity of fiber-reinforced cement mortar. Applied Sciences, 13(6), 3522. [Google Scholar]
29. Heo, G., Park, J., Song, K., Park, J., Jun, H. (2022). Mechanical properties of SiO2-coated carbon fiber-reinforced mortar composites with different fiber lengths and fiber volume fractions. Advances in Civil Engineering, 2020, 1–12. [Google Scholar]
30. Cao, M., Xu, L., Zhang, C. (2018). Rheological and mechanical properties of hybrid fiber reinforced cement mortar. Construction and Building Materials, 171, 736–742. [Google Scholar]
31. Dehghani, A., Aslani, F. (2020). The effect of shape memory alloy, steel, and carbon fibres on fresh, mechanical, and electrical properties of self-compacting cementitious composites. Cement and Concrete Composites, 112, 103659. [Google Scholar]
32. Wong, H. S., Barakat, R., Alhilali, A., Saleh, M. (2015). Hydrophobic concrete using waste paper sludge ash. Cement and Concrete Research, 70, 9–20. [Google Scholar]
33. Zhang, K., Pan, L., Li, J., Lin, C. (2021). What is the mechanism of the fiber effect on the rheological behavior of cement paste with polycarboxylate superplasticizer? Construction and Building Materials, 281, 122542. [Google Scholar]
34. Ylmén, R., Jäglid, U., Steenari, B., Panas, I. (2009). Early hydration and setting of Portland cement monitored by IR, SEM and Vicat techniques. Cement and Concrete Research, 39(5), 433–439. [Google Scholar]
35. Yu, P., Kirkpatrick, R., Poe, B., McMillan, P., Cong, X. (2004). Structure of calcium silicate hydrate (C-S-HNear-, mid-, and far-infrared spectroscopy. Journal of the American Ceramic Society, 82(3), 742–748. [Google Scholar]
36. García Lodeiro, I., Macphee, D., Palomo, A., Fernández-Jiménez, A. (2009). Effect of alkalis on fresh C-S-H gels. FTIR analysis. Cement and Concrete Research, 39(3), 147–153. [Google Scholar]
37. Li, H., Liebscher, M., Micusik, M., Yang, J., Sun, B. (2022). Role of pH value on electrophoretic deposition of nano-silica onto carbon fibers for a tailored bond behavior with cementitious matrices. Applied Surface Science, 600, 154000. [Google Scholar]
38. Dey, V., Kachala, R., Bonakdar, A., Mobasher, B. (2015). Mechanical properties of micro and sub-micron wollastonite fibers in cementitious composites. Construction and Building Materials, 82, 351–359. [Google Scholar]
Cite This Article
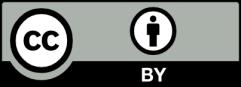
This work is licensed under a Creative Commons Attribution 4.0 International License , which permits unrestricted use, distribution, and reproduction in any medium, provided the original work is properly cited.