Open Access
ARTICLE
Response Spectrum Analysis of 7-story Assembled Frame Structure with Energy Dissipation System
School of Civil and Transportation Engineering, Henan University of Urban Construction, Pingdingshan, 467000, China
* Corresponding Author: Yi Wang. Email:
Structural Durability & Health Monitoring 2023, 17(2), 159-173. https://doi.org/10.32604/sdhm.2023.09601
Received 20 December 2019; Accepted 13 January 2020; Issue published 09 May 2023
Abstract
Viscoelastic damper is an effective passive damping device, which can reduce the seismic response of the structure by increasing the damping and dissipating the vibration energy of structures. It has a wide application prospect in actual structural vibration control because of simple device and economical material. In view of the poor seismic behaviors of assembled frame structure connections, various energy dissipation devices are proposed to improve the seismic performance. The finite element numerical analysis method is adopted to analyze relevant energy dissipation structural parameters. The response spectrum of a 7-story assembled frame structure combined the ordinary steel support, ordinary viscoelastic damper, and viscoelastic damper with displacement amplification device is analyzed. The analysis results show that the mechanical behavior of assembled frame structure with ordinary steel supports are not significantly different from those without energy dissipation devices. The assembled frame structure with viscoelastic damper has better seismic performance and energy dissipation, especially for the viscoelastic damper with displacement amplification devices. The maximum value of inter-story displacement angle decreases by 32.24%; the maximum floor displacement decreases by 31.91%, and the base shear decreases by 13.62% compared with the assembled frame structures without energy dissipation devices. The results show that the seismic fortification ability of the structure is significantly improved, and the overall structure is more uniformly stressed. The damping structure with viscoelastic damper mainly reduces the dynamic response of the structure by increasing the damping coefficient, rather than by changing the natural vibration period of the structure. This paper provides an effective theoretical basis and reference for improving the energy dissipation system and the seismic performance of assembled frame structures.Keywords
Assembled frame structures have attracted the attention of many scholars in the early 20th century because of its fast construction speed and low production cost. Since the 1950s, aerospace and mechanical systems have been using additional damping provided by viscoelastic damper materials to control excessive vibrations. Similar efforts have not been made for the civil engineering structures until the early 1970s. By the 1960s, assembled frame structure had been initially established in Britain, France and the Soviet Union [1,2]. China began to vigorously develop assembly buildings in 2015 and issued a series of relevant measures. With the support and promotion of national policies, the development of assembly buildings has entered the “fast lane”. The document of General Office of the State Council clearly pointed out that it would take a decade to increase the proportion of assembly buildings from 5% to 30% [3]. Assembled frame structures has the advantages of economic and environmental protection, rapid construction speed and quality assurance. The development of assembled structure system is an inevitable choice to construction industrialization. Due to the poor reliability of fabricated structure connections, it is often difficult to meet the requirements of seismic design. According to the seismic damage investigation of frame structures, the connection of concrete frame is the weak link of assembled buildings. The formation of plastic hinges consumes energy with its own damage, which is not only easy to cause local failure, but also overall collapse [4–9].
According to incomplete statistics, the rural buildings account for more than 50% of the total construction in China. However, there are few researches on the structure technology system applicable to the assembled frame structures. The seismic performance of assembled frame structures is relatively poor, which may cause a large number of human casualties and economic loss in the earthquake [10]. In recent years, scholars have paid more and more attention to the seismic performance of assembled frame structures [11–15]. However, the research on the seismic performance of assembled concrete frame structures mainly focuses on the strength, stiffness, ductility of connections, while the structural damping control technology is rarely used. The structural performance cannot meet the seismic requirements, which seriously restricts the development and promotion of assembled structure. The shortage of traditional seismic methods has led to continuous emergence and improvement of various new damping technologies. One of them is the structural damping control technology and energy dissipation and damping technology [16–18]. The structural damping control technology can change or adjust the dynamic characteristics of the structure with measures to reduce and reasonably control the dynamic response of the structure under earthquake. There are many classification methods for structural vibration control. According to whether external energy input is needed, the structural vibration control can be divided into active control, semi-active control, passive control, hybrid control and intelligent control. Among them, passive control is widely concerned because of its simple structure, low cost and easy maintenance. Passive control can be divided into base isolation technology, energy dissipation technology and energy absorption technology. Energy dissipating devices, such as dampers, can be installed at the connections or shear walls of the structure. The hysteretic deformation caused by the energy dissipating device can absorb or dissipate the energy input into the structure to reduce the seismic response of the structure. The researches mainly focus on the theoretical analysis, design method and experiment of the insulation and damping devices. A variety of energy dissipation systems, such as friction dampers, metallic dampers, viscoelastic dampers and viscous dampers, have been developed [19–22].
Viscoelastic damper mainly relies on the energy dissipation characteristics of viscoelastic damping materials to increase damping and reduce the dynamic response of the structure [23]. Viscoelastic damper is an effective energy dissipation device that is widely used in the design of building structure. Most dampers can give full play to their energy dissipation capacity in the case of large displacement [24–26]. However, due to the small relative displacement and rotation angle of the beam-column connection, the energy dissipation capacity of dampers installed in this position cannot be fully developed. To this end, a viscoelastic damper with displacement amplification device and a new energy dissipation system is proposed. Based on the principle of Lever, the small displacement and rotation angle generated by the structure are amplified by amplification device, which could be used for energy dissipation and damping of the structure under small displacement. Different from the general energy dissipating devices, the damper can be directly installed in the structure for energy dissipating and damping without other supporting members. The viscoelastic damper is not only suitable for cast-in-place beam column joints, but also for assembled frame structures.
The response spectrum of a 7-story assembled frame structure combined the ordinary steel support, ordinary viscoelastic damper and viscoelastic damper with the displacement amplification device is analyzed. The energy dissipation advantage of lever-based viscoelastic damper is quantitatively analyzed, and the results show that the energy dissipation effect of the viscoelastic damper with displacement amplification device is very obvious. The deformation and stress distribution of the whole assembled frame structure are more uniform.
2 Energy Dissipation Technology
Traditional seismic design method in China is based on the principle of ensuring personal safety and probability theory. The three-level fortification requirements of “small earthquake is not bad; medium earthquake is repairable and large earthquake is not collapsed” are put forward. This traditional seismic method is based on the elastic-plastic deformation of components and absorption of seismic energy, aiming is mainly to properly control the rigidity of the structure and make the structural members enter an inelastic state in the earthquake. This requires the structure have a large ductility, so that the structure “cracks but not falls”. This traditional design method is often effective, but still with many problems. To improve the seismic performance of buildings, designers usually adopt the method of increasing the cross-section of components and adding more reinforcement. However, this will greatly increase construction costs. In recent years, energy dissipation design has developed gradually to overcome the defects of traditional seismic design methods. Structural energy dissipation design refers to the installation of energy dissipation device in the structure to provide additional damping through its local deformation to reduce the dynamic response of the structure under earthquakes, consume the seismic energy of the upper structure, and meet seismic requirements. The damping forces or plastic deformations generated by various damping components are used to attenuate the seismic response of the structure. It is a significant improvement over traditional seismic structures that rely on structural plastic deformation and connection energy consumption.
Energy dissipation technology is to install energy dissipaters to increase the inner damping of the structure. Viscoelastic dampers have been installed in some high-rise buildings to reduce vibrations caused by wind load because of their ability to absorb a lot of energy and cost-effectiveness. It is feasible to apply the energy dissipation technology to building structures, and it has been widely used in assembled frame structure. In existing devices, viscoelastic dampers have been shown to provide added damping to structures to dissipate energy generated by the strong ground motion. It has been demonstrated that wind-induced sway of high-rise building can be considerably reduced by adding viscoelastic dampers to the structure. Viscoelastic damper is usually made of viscoelastic layer bonded with steel plate, which is directly sheared to dissipate dynamic input energy [27–32]. When they are added to the structure, although they can effectively attenuate the seismic response of the structure, their proper design for maximum efficiency must take into account important factors, such as excitation frequencies and working environmental temperature. To accurately describe the relationship between stress and strain of viscoelastic dampers various calculation models, such as equivalent stiffness and damping model, Kelvin model, and Maxwell model are put forward. Equivalent stiffness and damping model is suitable for small strain cases and has been widely used due to its relatively simple calculation. The relationship between the force, velocity and displacement of the energy dissipater can be expressed as follows:
Fd=cd˙X+KdXFd=cd˙X+KdX (1)
Cd=G′′Aωt (2)
Kd=G′At (3)
η = G′′G′= tgδ (4)
Ed=nπγ20G′′At (5)
where:
Fd is the force provided by the damper;
Cd is the equivalent damping coefficient of the viscoelastic damper;
Kd is the stiffness of the viscoelastic damper;
˙X is the relative velocity of the damper;
X is the displacement of the damper;
G′ is the storage shear modulus, which represents the stiffness performance of the material;
G′′ is the loss shear modulus, indicating the damping capacity of the material;
ω is the vibration frequency of the structure;
η is the loss factor, which is the main index to measure the dissipative vibration energy of damping materials;
Ed is the energy consumption of each hysteresis loop;
A is the shear area of the viscoelastic layer;
t is the thickness of the viscoelastic layer;
n is the number of layers of viscoelastic material;
γ0 is the shear strain of viscoelastic material.
The shear modulus and geometry size of viscoelastic damper are important parameters affecting the effect of viscoelastic damping materials. Viscoelastic damping material is a kind of polymer material with two characteristics of viscous liquid and elastic solid, which has the function of energy dissipation and vibration absorption. The shear storage modulus and loss factor of viscoelastic damping materials will decrease with the increase of ambient temperature and the decrease of frequency. The influence of load cycle on the dynamic characteristics of viscoelastic damping materials is relatively small. The main factors affecting the mechanical properties of viscoelastic materials are deformation frequency, environmental temperature and strain amplitude.
Viscoelastic dampers are usually composed of viscoelastic damping materials and restrained steel plates, which dissipate energy mainly through the shear deformation of viscoelastic materials. The storage stiffness, equivalent damping and energy dissipation capacity of viscoelastic dampers are directly related to the mechanical properties of viscoelastic materials. Viscoelastic dampers have high sensitivity. As long as the structure starts to vibrate under small disturbance, the damper will dissipate energy immediately. Even under small elastic vibration, it can increase the damping and reduce the dynamic response of the structure. In this way, viscoelastic damper can be used for seismic and wind-induced control of the structure. The problem of how to match the initial stiffness of other dampers with the lateral stiffness of the structure is avoided [33,34].
In recent years, the application of energy dissipation and damping technology in assembly buildings has become a hot spot. Concrete frame connections are the weak link of assembled frame structures. The energy consumption mode of plastic hinges is not only easy to damage the connection, but also difficult to repair after an earthquake. Especially for the assembled cast-in-place integral concrete frame structure, the narrow working space greatly increases the difficulty of stirrup binding and concrete pouring, and the construction quality is difficult to guarantee. An energy dissipation system for assembled frame structures is presented. The rotation-driven damper connected by assembled beam and column makes full use of the interlayer displacement and plays the role of viscoelastic dampers.
2.2 Energy Dissipation System of Assembled Frame Structure
Energy dissipation system can be divided into four types: (1) energy dissipation support; (2) energy dissipation shear wall; (3) energy dissipation node; (4) energy dissipation connection. The damper of energy dissipater is usually installed supports, beam-column joints, frame and shear wall joints, so that the mechanical performance of assembly buildings can be effectively improved. According to the damage of assembled structures in earthquakes, the energy dissipation and damping technology is applied to the assembled frame structure. First, the energy dissipation device is placed at the beam-column and column-foot connections of the assembled frame structure. Then, an energy dissipation system composed of energy dissipation devices and assembled frame structures is proposed. The energy dissipation system can meet the requirements of strong shear and weak bending, as well as strong joints and weak components. According to different energy dissipation characteristics, three kinds of energy dissipation devices (ordinary steel support, ordinary viscoelastic damper and viscoelastic damper with displacement amplification device) are arranged at different weak connections of the assembled frame structure respectively, as shown in Fig. 1. To explore the possibility of the new connection in practice, the energy dissipation device is completely placed in a 7-story assembled frame structure.
Figure 1: The energy dissipation system
Viscoelastic damper cannot only improves the stiffness of the joint, but also reduce the horizontal displacement of the structure. Aiming to the shortcomings of existing dampers, a viscoelastic damper based on Lever is proposed. It can amplify the small displacement of the structure according to different proportions of the rod axis, and finally convert it into the energy dissipation displacement of the damper. The energy dissipation capacity of the damper can be fully utilized by amplifying the displacement or rotation angle of the structure. At the same time, the external dimension of the damper is relatively small, which can be installed at the beam-column joints of the structure. The damper does not affect the internal space of the building, and has great significance and practical value in the project. When the viscoelastic damper with displacement amplification device are adopted, the horizontal displacement generated by the structure is transmitted to the displacement amplification device through the connection plates in an earthquake. Through the amplification of the horizontal relative displacement, the shear deformation of the damper increases and absorb more seismic energy. In this way, the seismic response of the assembled connections is reduced to protect the beam-column connections, and the overall stability of the structure is improved. The displacement amplification mechanism is connected with the upper layer of the structure and the movable steel plate of the viscoelastic damper. The relative velocity of movable steel plates can be increased by amplifying the small interlayer displacement of the structure and transferring it to the movable steel plate of the viscoelastic damper. Meanwhile, the damping force of the damper and the energy dissipation of the viscoelastic damper are also improved.
3 Performance Analysis of Energy Dissipation System
The object is based on a 7-story assembled frame structure. To compare the performance of different energy dissipation devices, four structure systems under different working conditions are established ① Assembled frame structure without energy dissipation devices; ② Assembled frame structure with ordinary steel supports in the middle and bottom layers; ③ Assembled frame structure with ordinary viscoelastic dampers in the middle and bottom layers; ④ Assembled frame structure with viscoelastic damper and displacement amplification device in the middle and bottom layers. The performance parameters of ordinary steel supports are shown in Table 1.
The finite element models of the above four structure systems all use three-dimensional bar elements to simulate the assembed beams and columns. The shell element is used to simulate the floors. Since the connection between slabs and beams in assembled structure is weaker than that of cast-in-place slab, the 70% reduction factor of slab is considered in modeling. The elastic modulus, rigidity and strength of the material are taken according to the Code for design of concrete structures (GB50010–2010) [35]. PMM and M3 plastic hinges are arranged at the ends of the assembled columns respectively to simulate the nonlinear stress characteristics of the components. All cross-section reinforcement of the four models are from the automatic design results of SAP2000, and the reinforcement results are analyzed and verified in PKPM to ensure that the structural reinforcements ratio meets the requirements of the Code for design of concrete structures (GB50010–2010). The main components of the structure are C35 concrete; the concrete unit weight is 26 kN/m3, and the masonry unit weight is 22 kN/m3. The performance parameters of concrete are shown in Table 2 and all indicators meet the specification requiremets.
The storey height is 3 meters, and the total height of the structural model is 21 meters. According to the Load code for design of building structure (GB50009–2012) [36], the standard value of roof live loads is 2.5 kN/m2, and the additional dead load of 2 kN/m2 is considered. The combination coefficient is 1.2 for dead load and 1.4 for live load. In addition, the load of beam and wall is applied as 16 kN/m. To meet the limit of axial compression ratio, the column section is designed as 600 mm × 600 mm, and the beam section is designed as 500 mm × 300 mm. The thickness of the floor slab is 100 mm. Q235 restrained steel plate is used as the core shear plate of the ordinary viscoelastic damper and viscoelastic damper with the displacement amplification devices. The steel plate is an elastic-plastic material, and it is treated as a linear elastic material in modeling considering its actual working state. It has an elastic modulus of 200 GPa and a Poisson ratio of 0.3. The parameters of the viscoelastic damper are shown in Table 3. The failure type of the bonding surface is peel failure, meeting the actual engineering requirements.
Rubber material is the core component of the viscoelastic damper. As a polymer nonlinear material, rubber materials have the characteristics of high elasticity and large deformation, which can meet a wide range of application requirements, especially in engineering applications. In addition to excellent softness, wear resistance, insulation and barrier, rubber materials also have super elasticity and viscoelasticity. When it is loaded slowly, its stress-strain curve is nonlinear. When it is loaded dynamically, its mechanical properties are closely related to the loading rate, amplitude, time and temperature. Its main performance is as follows: (1) Under the same strain, the stress increases with the increase of loading rate; (2) The behavior of stress relaxation is related to the strain and the steady equilibrium value of relaxation is different under different strains; (3) In dynamic cyclic loading, the size of hysteresis loop is closely related to the loading rate [37]. In this paper, the rubber material is considered as an isotropic and incompressible hyper elastic body, and it is modeled as a Nonlinear plastic element is used to simulate the viscoelastic damper in SAP2000. After the design parameters of the damper are determined, it is necessary to determine the damping coefficient, yield force, post-yield stiffness ratio and initial stiffness of the nonlinear plastic element. The specific design parameters are shown in Table 4. The working temperature is normal. When installing viscoelastic dampers, the rigidity of the structure should be balanced as much as and the dampers should be installed symmetrically in the structure. For convenient computation, the following basic assumptions are used in the structural model: (1) Floor slabs and infilled walls have no influence on the rigidity of the structure, and the weight of the floor slab and the loads it bears are directly loaded on the beams around it in a denser manner; (2) Beam-column connections are rigid; (3) The influence of temperature on the energy dissipation effect of viscoelastic dampers is not considered in the analysis.
The selected example is located in Huiji District, Zhengzhou, China. The seismic precautionary intensity is 7 degrees and the design basic acceleration of ground motion is 0.15 g. The design earthquake is classified as Class II, the construction site is classified as Class II, and the design characteristic period of ground motion is 0.35 s. Due to the coupling between the structural damping and other modes, CQC method is adopted for mode combination, and the total damping ratio of the structure is 0.05. The energy dissipation devices should be installed on the diagonal of the two columns with the largest relative displacement between the structural layers to better play the damping effect.
The seismic responses of the above four structural systems are calculated by the modal analysis response spectrum method. According to the actual seismic action, the response of the structural system is calculated by static analysis. On this basis, seismic analysis is carried out. The parameters such as period, inter-story displacement angle, floor displacement and base shear are obtained. Finally, the results of four structural systems are compared and analyzed. To study the control effect of the damper, the vibration periods of the first six modes are shown in Table 5.
Model analysis is a basic method to study the dynamic performance of structures. This is the premise of dynamic time history analysis. The general modal decomposition response spectrum method and direct integration method of dynamic time-history analysis need to analyze the natural vibration of the structure, so as to obtain the natural vibration mode and period of the structure. It can be seen from Table 5 that the first vibration mode is mainly X-direction translation, with a period of 1.518 s. The second vibration mode is mainly Y-direction translation, with a period of 1.389 s. The third vibration mode is mainly Z-direction translation, with a period of 1.364 s. This indicates that the X-direction stiffness of the structure is weaker than Y-direction stiffness. From the longitudinal comparison, it can be seen that the former three vibration periods are not significant. This shows that the stiffness of the structure in X, Y and Z directions increases due to energy dissipation devices, especially for Model ③ and Model ④, indicating that the viscoelastic damper is better than ordinary steel support. However, after the third vibration mode, the difference suddenly becomes large, indicating that the influence of the high-order vibration mode on the structure is very small and can be ignored. The fifth vibration period of Model ④ is only 0.315 s. From the horizontal comparison, it can be seen that compared with Model ①, the frequencies of Model ②, Model ③ and Model ④ increase and the periods are shortened. The results show that the structural rigidity increases and the dynamic performance of the structure changes with the addition of energy dissipation devices, especially for Model ④. However, according to the data of vibration period reduction, the vibration period decreases small. The first, second and third vibration periods of Model ④ decrease by 0.290, 0.321 and 0.438 s at most, indicating that the addition of viscoelastic dampers has little effect on the structural stiffness. The seismic response acceleration of the structure will not be greatly increased under the installation of viscoelastic dampers. It can be known that the damping structure with viscoelastic dampers is mainly used to reduce the dynamic response of the structure under earthquake by increasing the damping coefficient of the structure, rather than by changing the natural vibration period of the structure.
The period ratios of the first six vibration modes is shown in Table 6. The ratio of the third order vibration period is 0.899, meeting the requirements of the code. This indicates that the lateral vibration of the structure (Y-direction), the direction of the smaller size of the building plane has a greater effect on the structure. When analyzing the input seismic wave, the input direction of the seismic wave should also be the lateral direction of the structure. The periods from Model ① to Model ④ decreases gradually, so does the period ratios of the structure. However, the sixth order period ratio has little change. The model with energy dissipation devices has better energy dissipation capacity, especially for Model ③ and Model ④. Viscoelastic dampers have good energy consumption effect. This is because as the stiffness of the structure increases, the distribution is more uniform, and the torsional amplitude of the structure also decreases.
The maximum floor displacement of the four structural systems is shown in Table 7 and the variation comparison are shown in Fig. 2. It can be seen from Fig. 2 that the viscoelastic damping structure has excellent energy dissipation and damping effect under seismic wave. The curves of Models ③ and ④ are similar and more average than that of Model ①. The slope of the curve is larger than that of Models ① and ②, which is more conducive to the seismic performance of all structural members in each floor of the assembled frame structure. The damping effect of viscoelastic damper is better than that of ordinary steel support, which is consistent with the previous analysis. It can be seen from Table 7 that the maximum floor displacements of Model ①, Model ②, Model ③ and Model ④ are 36.29 mm, 34.74 mm, 24.82 mm and 24.71 mm, respectively. The maximum floor displacement of Models ③ and ④ is smaller than that of Models ① and ②. Compared with the original structure without energy dissipation devices, the ordinary steel support structure can be reduced by 7.68% at most, and the viscoelastic damping structure of Models ③ and ④ can be reduced by 32.51% and 32.40%, respectively. The damping effect of viscoelastic dampers is obviously higher than that of ordinary steel support. The energy dissipation and damping effect of viscoelastic dampers in an earthquake can effectively reduce the internal force of structural members for protection. The results show that viscoelastic damper has excellent energy dissipation and damping performance, especially for the viscoelastic dampers with displacement amplification devices.
Figure 2: Maximal floor displacement
The maximum inter-story displacement angle of the four structural systems is shown in Table 8 that of frame structure limited by the specification is 1/550 [38]. It can be seen that the maximum inter-story displacement angle of the original assembled frame structure is 1/540, which does not meet the specification requirements. The deformation curves of inter-story displacement angle is shown in Fig. 3. It can be seen that the inter-story displacement angle has an obvious inflection point on the second floor, and the inter-story displacement mainly occurs in the middle and lower floors (the second third and fourth floors). According to the energy dissipation principle of viscoelastic dampers, it is necessary to install the dampers in the floor with larger inter-story displacement. It is recommended to install the viscoelastic dampers mainly in the middle and lower layers of the frame structure. The maximum inter-story displacement angle of Model ② reduces from 1/540 to 1/585, which meets the limit value required by the specification. However, the effect of ordinary steel support is limited, and the maximum inter-story displacement angle decreases by 8.23%. When the energy dissipation device adopts viscoelastic dampers, the maximum inter-story displacement angle of the structure reduces about 1/752 and 1/798, meeting the specification requirements. The maximum inter-story displacement angle reduces greatly, and Models ③ and ④ decrease by 30.2% and 34.22%, respectively.
Figure 3: Inter-story displacement angle
Through the analysis of response spectrum, the inter-story shear force of the four models can be obtained as shown in Fig. 4, and the results are shown in Table 9. The inter-story displacement angle and the maximal floor displacement of Model ③ and Model ④ is smaller and more average than that of Models ① and ②, which is far less than the specification limits. Viscoelastic damper has better damping effect than the ordinary steel support. Compared with the former, viscoelastic dampers based on lever principle have obvious energy dissipation effect, which is more conducive to the seismic performance of all structural components. The base shear force of Model ①, Model ②, Model ③ and Model ④ is 3895.12 kN, 3684.12 kN, 3585.79 kN and 3364.48 kN, respectively. Compared with Model ①, the base shear of Model ②, ③ and ④ decreases by 5.42%, 7.94% and 13.62%, respectively. The reduction of inter-story force is more favorable for the overall structure to resist transverse and seismic loads. The stress distribution of each component will be more uniform, and the shear failure of vertical bearing members is avoided. It can be seen that the effect of ordinary steel support on improving the mechanical performance of assembled structure is very limited. In contrast, the excellent damping and energy dissipation of viscoelastic dampers can obviously improve the mechanical performance of assembled frame structures.
Figure 4: Inter-story shear force
The response spectrum of a 7-story assembled frame structure combined the ordinary steel support, ordinary viscoelastic damper, and viscoelastic damper with displacement amplification devices is analyzed. According to an actual seismic action, the response of the structure system is calculated by static analysis. On this basis, the seismic analysis is carried out. The results show that this method is simple and can be used in anti-seismic design. The following conclusions can be obtained:
(1) The dynamic performance of the structure changes with the addition of energy dissipation devices. The assembled frame structure with viscoelastic dampers is mainly used to reduce the dynamic response of the structure in earthquakes by increasing the damping coefficient of the structure, rather than by changing the natural vibration period of it. The seismic response acceleration of the assembled frame structure will not be greatly increased under the installation of viscoelastic damper.
(2) The direction with the smaller size of the building plane has a greater effect on the structure. Therefore, when analyzing the input seismic wave, the input direction of seismic wave should also be the lateral direction of the structure.
(3) The model with viscoelastic dampers has good energy dissipation. This is because as the stiffness of the structure increases, the distribution is more uniform and the torsional amplitude of the structure also decreases.
(4) Viscoelastic damping structures have excellent energy dissipation and damping effects in earthquake, especially for the viscoelastic dampers with displacement amplification devices. The maximum floor displacement of viscoelastic damped structures is obviously smaller than that of the original structure without energy dissipation devices. Ordinary steel support structure can be reduced by 7.68% at most, and the viscoelastic damping structure can be reduced by about 32.51% and 32.40%, respectively. Viscoelastic damper has excellent energy dissipation and damping, especially for the viscoelastic dampers with displacement amplification devices.
(5) The inter-story displacement angle has an obvious inflection point on the second floor. Therefore, it is recommended to install viscoelastic dampers in the middle and lower floors. The inter-story displacement angle of ordinary steel support structure can be reduced by 8.23% at most, and the viscoelastic damping structure can be reduced by 30.2% and 34.22%. The viscoelastic damper has better damping effect than the ordinary steel support. Compared with the former, the viscoelastic damper based on lever principle has obvious energy dissipation effect, which is more conducive to the seismic performance of all structural components.
(6) The stress distribution of each component will be more uniform, and the shear failure of vertical bearing members is avoided. The base shear force of ordinary steel support structure can be reduced by 5.42% compared with original non-energy dissipation device structure. However, the viscoelastic damping structure can be reduced by 7.94% and 13.62%, respectively. The effect of ordinary steel support on improving the mechanical performance of assembled structure is very limited. In contrast, the excellent damping and energy dissipation capacity of viscoelastic dampers can obviously improve the mechanical performance of assembled frame structures.
(7) The damping force and energy dissipation of the viscoelastic dampers with displacement amplification devices are obviously higher than that of traditional viscoelastic dampers. The mechanical properties of the damper is obviously related to the displacement amplitude. The energy consumption of viscoelastic dampers can be increased by using the displacement amplifier, which can reduce the energy consumption and the dynamic response of the structure.
(8) The energy dissipation system has good energy dissipation, which can effectively reduce the seismic response of the structure. A new viscoelastic damper with displacement amplification device is proposed, which is a feasible design method of assembled frame structures. The results of this paper provide an effective theoretical basis and reference for improving the energy dissipation system and the seismic performance of assembled frame structures.
Funding Statement: This work was supported by Foundation of Henan Educational Committee (20A560004, J. Z.); Foundation of Henan Science and Technology Project (182102311086, Y. W.); Foundation for University Key Teacher (YCJQNGGJS201901, J. Z., YCJXSJSDTR201801, Y. W., Henan University of Urban Construction).
Conflicts of Interest: The authors declare that they have no conflicts of interest to report regarding the present study.
References
1. Ghotb, M. R., Toopchi-Nezhad, H. (2019). A feasibility study on pre-compressed partially bonded viscoelastic dampers. Engineering Structures, 201, 1–11. https://doi.org/10.1016/j.engstruct.2019.109796 [Google Scholar] [CrossRef]
2. Waseem, S. (2019). Viscoelastic material as energy dissipater viscoelastic damper for building structures to mitigate the seismic vibration. Civil and Environmental Engineering Reports, 29(2), 41–49. https://doi.org/10.2478/ceer-2019-0015 [Google Scholar] [CrossRef]
3. Liu, R., Zhang, J., Wang, Y., Huang, C., Guo, Z. (2019). Development background and current situation of China’s prefabricated buildings. Housing and Real Estate, 11(32), 32–47. [Google Scholar]
4. Kotaro, M., Daisuke, K., Iwao, Y., Atsushi, M. (2018). Model-based installation of viscoelastic damper support for reduction of residual vibration. International Journal of Automation Technology, 12(5), 650–657. https://doi.org/10.20965/ijat.2018.p0650 [Google Scholar] [CrossRef]
5. Parth, D. J., Digesh, D. J., Paresh, V. P. (2016). Enhancing progressive collapse resistance of RC building using viscoelastic dampers. International Journal of Research in Engineering and Technology, 5(32), 147–153. https://doi.org/10.15623/ijret [Google Scholar] [CrossRef]
6. Nasab, M. S. E., Guo, Y., Kim, J. (2022). Seismic retrofit of a soft first-story building using viscoelastic dampers considering inherent uncertainties. Journal of Building Engineering, 47, 1–15. https://doi.org/10.1016/J.JOBE.2021.103866 [Google Scholar] [CrossRef]
7. Nasab, M. S. E., Kim, J. (2022). Fuzzy analysis of a viscoelastic damper in seismic retrofit of structures. Engineering Structures, 250, 1–13. https://doi.org/10.1016/J.ENGSTRUCT.2021.113473 [Google Scholar] [CrossRef]
8. Wang, S., Zhang, Q., Yu, C. (2021). Effectiveness of damaged viscoelastic dampers in seismic protection of structures under main shocks and aftershocks. Engineering Structures, 242, 1–15. https://doi.org/10.1016/J.ENGSTRUCT.2021.112424 [Google Scholar] [CrossRef]
9. Shahriari, A., Birzhandi, M. S., Zafarani, M. M. (2021). Seismic behavior, blast response and progressive collapse of RC structures equipped with viscoelastic dampers. Soil Dynamics and Earthquake Engineering, 143, 1–20. https://doi.org/10.1016/J.SOILDYN.2021.106643 [Google Scholar] [CrossRef]
10. Zhang, C., Huang, W., Zhou, Y., Luo, W. (2021). Experimental and numerical investigation on seismic performance of retrofitted RC frame with sector lead viscoelastic damper. Journal of Building Engineering, 44, 1–12. https://doi.org/10.1016/J.JOBE.2021.103218 [Google Scholar] [CrossRef]
11. Wu, C., Li, D., Deng, X., Yang, C., Xu, X. (2021). Experimental study on precast concrete moment-resisting frame system with sector lead viscoelastic dampers. Structural Control and Health Monitoring, 28, e2746. https://doi.org/10.1002/stc.2746 [Google Scholar] [CrossRef]
12. Ni, Y., Yun, Y., Zhang, Q., Lu, K. (2020). Vibration properties monitoring and uncertainty quantification of precast and cast-in-situ shear wall buildings using a Bayesian framework. Structural Control and Health Monitoring, 27(6), e2537. https://doi.org/10.1002/stc.2537 [Google Scholar] [CrossRef]
13. Shen, S., Pan, P., Miao, Q., Li, W., Gong, R. (2019). Behaviour of wall segments and floor slabs in precast reinforced concrete shear walls assembled using steel shear keys (SSKW). Structural Control and Health Monitoring, 26(10), e2418. https://doi.org/10.1002/stc.2418 [Google Scholar] [CrossRef]
14. Li, D., Wu, C., Zhou, Y., Luo, W., Lie, W. (2021). A precast beam-column connection using metallic damper as connector: Experiment and application. Journal Constructional Steel Research, 181, 106628. https://doi.org/10.1016/j.jcsr.2021.106628 [Google Scholar] [CrossRef]
15. Lin, K., Lu, X., Li, Y., Guan, H. (2018). Experimental study of a novel multi-hazard resistant prefabricated concrete frame structure. Soil Dynamics and Earthquake Engineering, 119, 390–407. https://doi.org/10.1016/j.soildyn.2018.04.011 [Google Scholar] [CrossRef]
16. Valente, M. (2013). Improving the seismic performance of precast buildings using dissipative devices. Procedia Engineering, 54, 795–804. https://doi.org/10.1016/j.proeng.2013.03.073 [Google Scholar] [CrossRef]
17. Liu, W., Yan, M., Yu, W., He, W. (2018). Design method based on displacement damping region for viscoelastic damper-added structures. Journal of Vibration and Shock, 37(13), 35–42. https://doi.org/10.13465/j.cnki.jvs.2018.13.006 [Google Scholar] [CrossRef]
18. Zhou, Y., Shang, C., Zhang, C. (2019). Progress in research and application of energy-dissipated technology. Building Structure, 49(19), 33–48. https://doi.org/10.19701/j.jzjg.2019.19.005 [Google Scholar] [CrossRef]
19. Huang, L., Zhou, Z., Peng, Z., Ma, J. (2020). Experimental investigation of a self-centering precast concrete beam-to-column connection with top and bottom friction energy dissipaters. The Structural Design of Tall Special Buildings, 29(4), e1707. https://doi.org/10.1002/tal.1707 [Google Scholar] [CrossRef]
20. Koshikawa, T. (2017). Moment and energy dissipation capacities of post-tensioned precast concrete connections employing a friction device. Engineering Structures, 138, 170–180. https://doi.org/10.1016/j.engstruct.2017.02.012 [Google Scholar] [CrossRef]
21. Zhang, C., Li, H., Gao, W., Li, C. (2020). Experimental and analytical investigations on new viscoelastic damped joints for seismic mitigation of structures with precast shear walls. Structural Control and Health Monitoring, 27(2), e2485. https://doi.org/10.1002/stc.2485 [Google Scholar] [CrossRef]
22. Addala, M. B., Bhalla, S., Madan, A. (2022). Performance based design of a new hybrid passive energy dissipation device for vibration control of reinforced concrete frames subjected to broad-ranging earthquake ground excitations. Advances in Structural Engineering, 25(4), 895–912. https://doi.org/10.1177/13694332211052350 [Google Scholar] [CrossRef]
23. Zhao, J., Wang, Y., Zhou, H. (2017). Nonlinear seismic damage control of high-rise steel structures based on MR damper. Revista de la Facultad de Ingenieria, 32(4), 471–479. [Google Scholar]
24. Zhou, Y., Gong, S. (2018). Study on nonlinear characteristics and mechanical model of hybrid nonlinear viscoelastic damper. Engineering Mechanics, 35(6), 132–143. https://doi.org/10.6052/j.issn.1000-4750.2017.02.0156 [Google Scholar] [CrossRef]
25. Li, Q., Xu, Z., Dong, Y., He, Z., He, J. et al. (2022). Microstructure-based equivalent visco-hyperelastic model of viscoelastic damper. Journal of Engineering Mechanics, 148(4), 1–15. [Google Scholar]
26. Zhang, M., Pang, H. (2020). Damping performance analysis of frame structure installing viscoelastic damper with support. Chinese Journal of Applied Mechanics, 37(1), 418–426+497–498. https://doi.org/10.11776/cjam.37.01.C075 [Google Scholar] [CrossRef]
27. Huang, W., Shi, F., Zhang, C., Zhou, Y., Li, Z. (2022). Seismic performance of reinforced concrete frame with lead viscoelastic damper under mainshock-aftershock sequences. Structures, 41, 1624–1636. [Google Scholar]
28. Nasab, M. S. E., Javidan, M. M., Chun, S., Kim, J. (2021). Experimental study on seismic retrofit of a RC frame using viscoelastic dampers. Structures, 34, 771–786. https://doi.org/10.1016/j.istruc.2021.08.044 [Google Scholar] [CrossRef]
29. Siami, K. R., Tehrani, P. (2021). Effects of using different arrangements and types of viscous dampers on seismic performance of intermediate steel moment frames in comparison with different passive dampers. Structures, 33, 3382–3396. https://doi.org/10.1016/j.istruc.2021.06.079 [Google Scholar] [CrossRef]
30. Xiao, Y., Zhou, Y., Huang, Z. (2021). Efficient direct displacement-based seismic design approach for structures with viscoelastic dampers. Structures, 29, 1699–1708. https://doi.org/10.1016/j.istruc.2020.12.067 [Google Scholar] [CrossRef]
31. Xie, L., Zhang, L., Pan, C., Zhang, R., Chen, T. (2020). Uniform damping ratio-based design method for seismic retrofitting of elastoplastic RC structures using viscoelastic dampers. Soil Dynamics and Earthquake Engineering, 128, 105866. https://doi.org/10.1016/j.soildyn.2019.105866 [Google Scholar] [CrossRef]
32. Zhang, M., Pang, H. (2020). Analysis of damping performance of frame structure with viscoelastic damper. Engineering Computations, 38(2), 913–928. https://doi.org/10.1108/EC-02-2020-0116 [Google Scholar] [CrossRef]
33. Wang, Y., Zhou, Y., Ding, K. (2006). Recent advances in research and applications of viscoelastically damped structure. Journal of Disaster Prevention and Mitigation Engineering, 26(1), 109–121. [Google Scholar]
34. Abdollahzadeh, G., Shabani, S. (2017). The effect of viscoelastic damper on reducing seismic responses of steel frame structures. Asian Journal of Civil Engineering, 18(6), 945–960. [Google Scholar]
35. GB50010–2010 (2010). Code for design of concrete structures. China: China Construction Industry Press. [Google Scholar]
36. GB50009–2012 (2012). Load code for design of building structures. China: China Construction Industry Press. [Google Scholar]
37. Bergström, J. S., Boyce, M. C. (2001). Constitutive modeling of the time-dependent and cyclic loading of elastomers and application to soft biological tissues. Mechanics of Materials, 33(9), 523–530. https://doi.org/10.1016/S0167-6636(01)00070-9 [Google Scholar] [CrossRef]
38. GB50011–2010 (2010). Code for seismic design of buildings. China: China Construction Industry Press. [Google Scholar]
Cite This Article
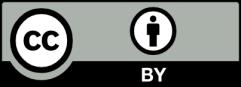
This work is licensed under a Creative Commons Attribution 4.0 International License , which permits unrestricted use, distribution, and reproduction in any medium, provided the original work is properly cited.