Open Access
ARTICLE
Single Point Cutting Tool Fault Diagnosis in Turning Operation Using Reduced Error Pruning Tree Classifier
1 School of Mechanical Engineering (SMEC), VIT University, Chennai, 600127, India
2 Department of Mechanical Engineering, SNS College of Technology, Coimbatore, 641035, India
* Corresponding Author: V. Sugumaran. Email:
Structural Durability & Health Monitoring 2022, 16(3), 255-270. https://doi.org/10.32604/sdhm.2022.0271
Received 23 February 2018; Accepted 02 August 2018; Issue published 18 July 2022
Abstract
Tool wear is inevitable in daily machining process since metal cutting process involves the chip rubbing the tool surface after it has been cut by the tool edge. Tool wear dominantly influences the deterioration of surface finish, geometric and dimensional tolerances of the workpiece. Moreover, for complete utilization of cutting tools and reduction of machine downtime during the machining process, it becomes necessary to understand the development of tool wear and predict its status before happening. In this study, tool condition monitoring system was used to monitor the behavior of a single point cutting tool to predict flank wear. A uniaxial accelerometer was attached to a single point cutting tool under study. The accelerometer acquires vibrational signals during turning operation on a lathe machine. The acquired signals were then used to extract statistical features such as standard error, variance, skewness, etc. The substantial features were recognized to reduce the utilization of computing resources. They were used to classify the signals as good and three different measures of flank wear by a decision tree algorithm. Frequency domain features were also extracted and shown to be less effective in classification in comparison to statistical features. REPTree (Reduced Error Pruning Tree) algorithm was used in this study. REPTree decision tree algorithm achieved a maximum classification accuracy of 72.77% for all signals combined. When spindle speed and feed rate are considered as the variables the accuracy is about 86.25%. When spindle speed is the only variable parameter the accuracy is about 82.71%. When depth of cut, feed rate and speed of the spindle are considered as variable parameters, the accuracy of the decision tree is around 93.51%. This study demonstrates the performance of REPTree classifier in tool condition monitoring. It can be utilized for tool wear identification and thus improve surface finish, dimensional accuracy of the work piece and reduce machine downtime. Any additional research on the work may involve analysis of different classifier algorithms which could potentially predict tool wear with greater accuracy.Keywords
Cite This Article
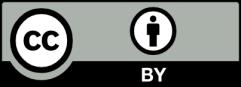
This work is licensed under a Creative Commons Attribution 4.0 International License , which permits unrestricted use, distribution, and reproduction in any medium, provided the original work is properly cited.