Open Access
ARTICLE
Sensor Layout of Hoisting Machinery Vibration Monitoring Based on Harmony Genetic Search Algorithm
1 Jiangsu Key Laboratory of Engineering Mechanics, School of Civil Engineering, Southeast University, Nanjing, 211189, China
2 China Special Equipment Inspection and Research Institute, Beijing, 100029, China
* Corresponding Authors: Keqin Ding. Email: ; Hui Jin. Email:
Structural Durability & Health Monitoring 2022, 16(2), 145-161. https://doi.org/10.32604/sdhm.2022.022241
Received 28 February 2022; Accepted 07 March 2022; Issue published 25 April 2022
Abstract
With the construction of automated docks, health monitoring technology as a parallel safety assurance technology for unmanned hoisting machinery has become a hot spot in the development of the industry. Hoisting machinery has a huge structure and numerous welded joints. The complexity and nonlinearity of the welded structure itself makes the structural failure parts random and difficult to arrange for monitoring sensors. In order to solve the problem of effectiveness and stability of the sensor arrangement method for monitoring the structure of hoisting machinery. Using the global and local search capabilities enhanced by the complementary search mechanism, a structural vibration monitoring sensor placement algorithm based on the harmony genetic algorithm is proposed. Firstly, the model is established for modal analysis to obtain the displacement matrix of each mode. Secondly, the optimal parameter combination is established through parameter comparison, and the random search mechanism is used to quickly search in the modal matrix to obtain the preliminary solution, and then the preliminary solution is genetically summed The mutation operation obtains the optimized solution, and the optimal solution is retained through repeated iterations to realize the decision of the vibration sensor layout of the crane structure monitoring. Combining the comparison test of harmony genetic algorithm, harmony search algorithm and genetic algorithm, the fitness of harmony genetic algorithm in X, Y and Z directions were 0.0045, 0.0084 and 0.0058, respectively, which were all optimal. And the average probability of deviating from the optimal path is 1.10%, 19.34%, and 54.43%, which are also optimal. Harmony genetic algorithm has the advantages of simplicity, fastness and strong global search ability, and can obtain better fitness value and better search stability.Keywords
Cite This Article
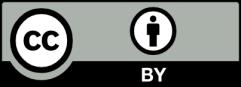
This work is licensed under a Creative Commons Attribution 4.0 International License , which permits unrestricted use, distribution, and reproduction in any medium, provided the original work is properly cited.