Open Access
ARTICLE
A Fatigue Damage Model for FRP Composite Laminate Systems Based on Stiffness Reduction
International Institute for Urban Systems Engineering (IIUSE), Southeast University, Nanjing, China.
Mechanical Engineering Department, California Polytechnic State University, San Luis Obispo, CA 93405, USA.
Mechanical Engineering Department, Faculty of Engineering, Alexandria University, Alexandria, 21544, Egypt.
Department of Civil Engineering, Faculty of Engineering, University of Sistan and Baluchestan, Zahedan, Iran.
*Corresponding Author: Wael A. Altabey. Email: .
Structural Durability & Health Monitoring 2019, 13(1), 85-103. https://doi.org/10.32604/sdhm.2019.04695
Abstract
This paper introduces a stiffness reduction based model developed by the authors to characterize accumulative fatigue damage in unidirectional plies and (0/θ/0) composite laminates in fiber reinforced polymer (FRP) composite laminates. The proposed damage detection model is developed based on a damage evolution mechanism, including crack initiation and crack damage progress in matrix, matrix-fiber interface and fibers. Research result demonstrates that the corresponding stiffness of unidirectional composite laminates is reduced as the number of loading cycles progresses. First, three common models in literatures are presented and compared. Tensile viscosity, Young’s modulus and ultimate tensile stress of composites are incorporated as key factors in this model and are modified in accordance with temperature. Four types of FRP composite property parameters, including Carbon Fiber Reinforced Polymer (CFRP), Aramid Fiber Reinforced Polymer (AFRP), Glass Fiber Reinforced Polymer (GFRP), and Basalt Fiber Reinforced Polymer (BFRP), are considered in this research, and a comparative parameter study of FRP unidirectional composite laminates with different off-angle plies using control variate method are discussed. It is concluded that the relationship between the drop in stiffness and the number of cycles also shows three different regions, following the mechanism of damage of FRP composites and the matrix is the dominant factor determined by temperature, while fiber strength is the dominant factor that determine the reliability of composite.Keywords
Cite This Article
Citations
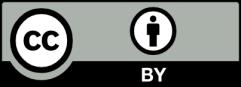
This work is licensed under a Creative Commons Attribution 4.0 International License , which permits unrestricted use, distribution, and reproduction in any medium, provided the original work is properly cited.