Open Access
ARTICLE
The Effects of Different Post-Heat Treatments on Rolling Contact Fatigue Behaviors of Direct Laser Cladding Inconel 625 Coatings
1 School of Materials Science and Engineering, Wuhan University of Technology, Wuhan, 430070, China
2 School of Mechanical and Electronic Engineering, Wuhan University of Technology, Wuhan, 430070, China
3 School of Mechanical Engineering, Xi’an University of Science and Technology, Xi’an, 710054, China
4 State Key Laboratory of Tribology, Tsinghua University, Beijing, 100084, China
5 Shandong Key Laboratory of Corrosion Science, Institute of Oceanology, Chinese Academy of Sciences, Qingdao, 266071, China
* Corresponding Authors: Chen Zhou. Email: ; Xuewu Li. Email:
(This article belongs to the Special Issue: Green Coating and Film for Degeneration Protection)
Journal of Renewable Materials 2021, 9(1), 129-144. https://doi.org/10.32604/jrm.2021.011596
Received 18 May 2020; Accepted 30 June 2020; Issue published 30 November 2020
Abstract
In this paper, the microstructures and rolling contact fatigue behaviors of laser cladding Inconel 625 coatings with or without post-heat treatments were analyzed. The results revealed that the fatigue resistance of the laser cladding coating after any post-heat treatment was worse than that of the as-deposited coating. First, through the finite element analysis, the distribution of stress along the thickness direction of the coating was obtained, and it was concluded that the bonding interface between the coating and the matrix had little effect on the fatigue properties of the coating. Then X-ray diffraction (XRD), scanning electron microscopy (SEM) and energy dispersive spectrometry (EDS) were used to analyze the microstructure and failure morphology. The results revealed that the subsurface failure morphology of the coatings showed a consistent correlation with rolling fatigue property after different heat treatments. The TCP phase and carbides have been shown in the laser cladding coating. The coating after stress relieved annealing exhibited chain-shaped granular carbides on the grain boundaries which could accelerate crack propagation. The aging heat treatment made small amounts of Laves phase dissolved in the coating, while the dispersed phase was precipitated which could result in the formation of pores. And the solution treatment made large amounts of Laves phase dissolved, while the rod-shape brittle phases were generated which was easy to fracture and contribute to crack initiation and spalling.Keywords
Cite This Article
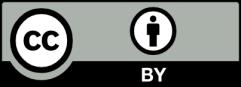
This work is licensed under a Creative Commons Attribution 4.0 International License , which permits unrestricted use, distribution, and reproduction in any medium, provided the original work is properly cited.