Open Access
ARTICLE
3D Printing of Polylactic Acid Bioplastic–Carbon Fibres and Twisted Kevlar Composites Through Coextrusion Using Fused Deposition Modeling
Department of Mechanical and Material Engineering, Lee Kong Chian Faculty of Engineering and Science, Universiti Tunku Abdul Rahman, Jalan Sungai Long, Bandar Sungai Long, Cheras, 43000 Kajang, Selangor, Malaysia
* Corresponding Author: J. Y. Tey. Email:
(This article belongs to the Special Issue: Renewable materials for sustainable development)
Journal of Renewable Materials 2020, 8(12), 1671-1680. https://doi.org/10.32604/jrm.2020.011870
Received 02 June 2020; Accepted 28 August 2020; Issue published 12 November 2020
Abstract
Polylactic acid (PLA) bioplastic is a common material used in Fused Deposition Modeling (FDM) 3D printing. It is biodegradable and environmentally friendly biopolymer which made out of corn. However, it exhibits weak mechanical properties which reduced its usability as a functional prototype in a real-world application. In the present study, two PLA composites are created through coextruded with 3K carbon fibres and twisted Kevlar string (as core fibre) to form a fibre reinforced parts (FRP). The mechanical strength of printed parts was examined using ASTM D638 standard with a strain rate of 1 mm/min. It has been demonstrated that the FRPs coextruded with 3K carbon fibres had achieved significant improvement in Young’s modulus (+180.6%, 9.205 GPa), ultimate tensile strength (+175.3%, 103 MPa) and maximum tensile strain (+21.6%, 1.833%). Although the Young’s modulus of Kevlar FRP was found to be similar to as compared to unreinforced PLA (~3.29 GPa), it has gained significant increment in terms of maximum tensile strain (+179.7%, 104.64 MPa), and maximum tensile strain (+257%, 5.384%). Thus, this study revealed two unique composite materials, in which the 3K carbon FRP can offer stiff and high strength structure while Kevlar FRP offers similar strength but at a higher elasticity.Keywords
Cite This Article
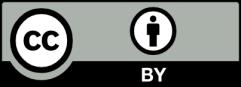
This work is licensed under a Creative Commons Attribution 4.0 International License , which permits unrestricted use, distribution, and reproduction in any medium, provided the original work is properly cited.