Open Access
ARTICLE
Structural and Mechanical Properties of Bio-Sourced Thermoplastic Materials from Flax and Fatty Acids
1 LERMAB, INRAE, Université de Lorraine, Nancy, 54000, France
2 Research Center for Biomass and Bioproducts, National Research and Innovation Agency (BRIN), Bogor, 16911, Indonesia
3 PLASTINNOV, IUT de Moselle-Est, Université de Lorraine, Saint-Avold, 57500, France
* Corresponding Authors: Firmin Obounou Akong. Email: ; Philippe Gérardin. Email:
(This article belongs to the Special Issue: Valorization of Lignocellulosic Biomass for Functional Materials)
Journal of Renewable Materials 2025, 13(3), 539-552. https://doi.org/10.32604/jrm.2024.056813
Received 31 July 2024; Accepted 25 October 2024; Issue published 20 March 2025
Abstract
Bio-based thermoplastic film from flax fiber and fatty acid (FA) was obtained using trifluoroacetic anhydride (TFAA) as an impelling agent. Different quantities of TFAA/FA, size of flax fiber, and fatty acids were applied to investigate chemical structure in relation to the mechanical properties. Decreasing the quantity of TFAA/FA by almost half from 1:4 to 1:2.5 (flax to TFAA/FA) only reduces by 22% the weight percent gain (WPG) and ester content and reducing flax fiber size slightly increases the WPG and ester content. All the treatments showed significant chemical structure modification, observed by FTIR and solid CP/MAS 13C NMR, confirming the presence of carbonyl ester groups and alkyl chains, in relatively similar intensities. The crystallinity index (CrI) of esterified flax was evaluated by comparing the signal of solid CP/MAS 13C NMR in crystalline and amorphous regions and CrI was higher in esterified flax using a lower quantity of reagent and longer fatty acid. Esterified flax in a high quantity of reagent showed ductile or flexible behavior. Decreasing the reagent to 1:2.5 significantly increases the tensile strength and Young’s modulus, and decreases the elongation at break, presenting more brittle and stiff material. Using flax fiber in the original size results in slightly higher tensile strength and Young’s modulus and slightly lower elongation than milled flax. The tensile strength and Young’s modulus of stearic acid esterified flax obtained in this research were higher than myristic acid and comparable to the polyethylene plastics-LDPE and HDPE.Graphic Abstract
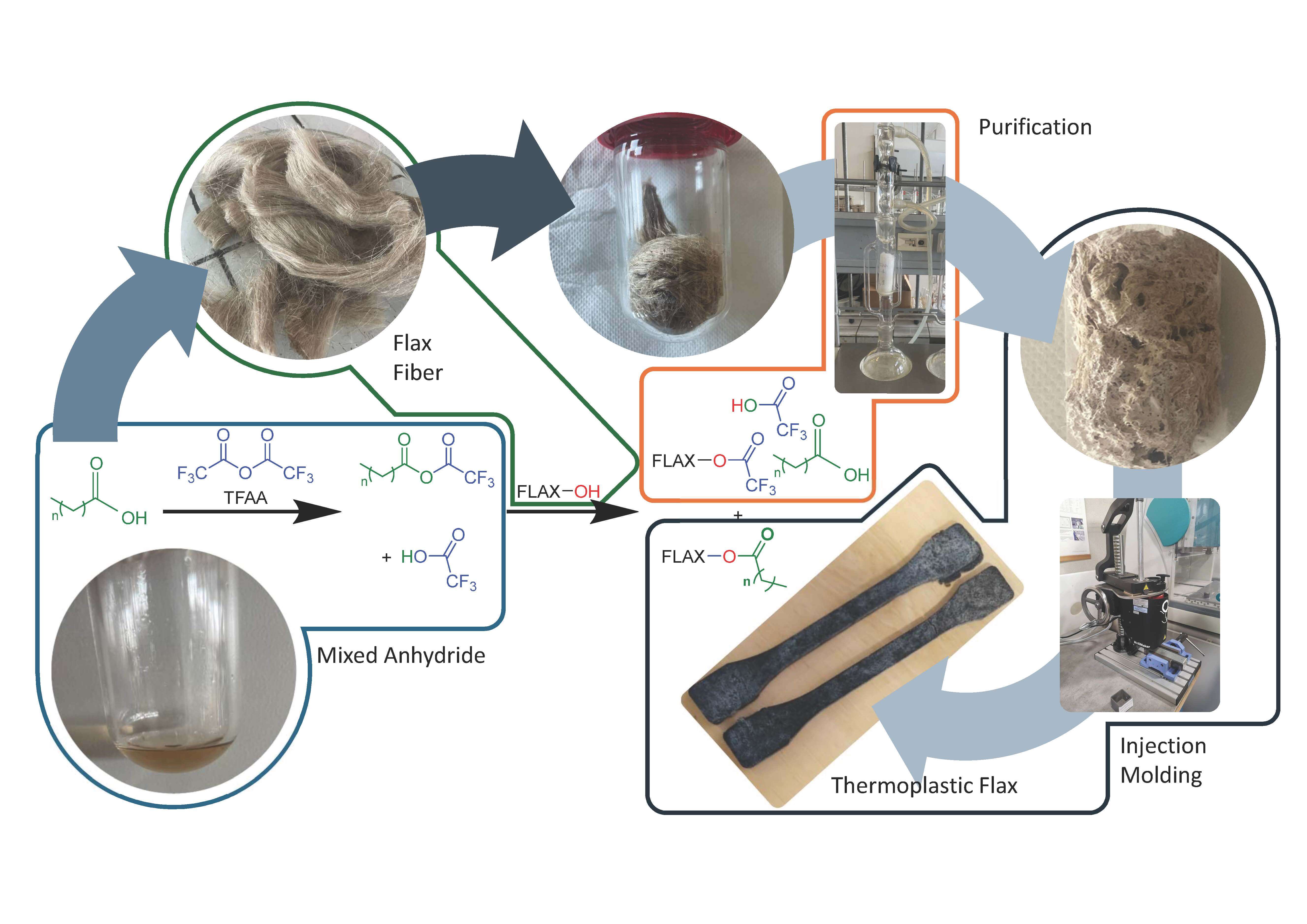
Keywords
Plastics have become an important component in human daily life due to their lightness of weight and low bulk density, high durability, ease of processing, good mechanical properties and barrier properties, and low production costs [1]. The excessive use of this material brings the issue of (micro)nano plastic pollution which continues to be a concern along with the negative impact on ecosystems and human health [2]. The use of naturally sourced alternatives or bioplastics is the future of thermoplastic materials to be one of the solutions to these problems. However, to date, bioplastics only account for less than 2% of all plastics on the market [3]. In this context, cellulose-based natural fibers are promising candidates and have occupied a substantial place in the field of material research because of their availability, sustainability, carbon dioxide neutrality emissions, inexpensive price, and good specific strength properties [4,5]. Although the application of bioplastics is not as widespread as conventional plastics due to low mechanical properties [6], bioplastics have an important role in packaging applications (about 60%), followed by applications in the textile, automotive, and construction industries [7–9]. Lignocellulose-derived bioplastics also have an essential role in biomedical applications due to their non-toxicity and biocompatibility [10].
Flax fiber (Linum usitatissimum) is one of the most widely used bio-fibers because of its cost-effectiveness and its specific mechanical properties, comparable to glass fibers, which is why flax fiber is considered to be the most important fiber in the bast family for composites [11]. Composites are defined as custom made materials in which the properties can be adjusted by differing reinforcement and matrix phases [12]. Flax itself plays the role of filler and reinforcement in composites while thermoplastic and thermoset polymers, such as polyethylene, polypropylene, polystyrene, and epoxy which can be processed below 200°C, were used as matrix due to the low degradation temperature of lignocellulosic fiber [13,14]. Due to the poor compatibility and weak interface bonding between fiber and thermoplastic polymer, some fiber surface treatments have been applied such as alkali, silane, benzoylation, peroxide treatment, or esterification using reactive moieties [13,15]. Significant mechanical properties improvement was reported for composites with 40% flax fiber in different orientations, particularly in the parallel orientation of fiber [16]. John et al. [17] reported that increasing flax weight fraction increased composite stiffness (tensile strength and modulus), but decreased impact strength when it reached 40% weight fraction. Most of the recent studies reported significant improvement of tensile and flexural strength achieved with less than 30% of flax fiber used in composites [18–20], while adding flax in a proportion further than 40% reduced interfacial adhesion between fiber and thermoplastic polymer and reduced mechanical properties [21]. The high degree of crystallinity of flax may account for the lack of thermoplastic properties of flax although it can increase the stiffness of the composite, so it is necessary to add high amounts of thermoplastic polymers, and this causes the resulting composite material to be only partially biodegradable.
Instead of combining natural fibers and thermoplastic polymer to form a reinforced composite, a material with thermoplastic properties could be achieved by chemical modification of natural fiber, by destroying cellulose crystallinity or involving reactions of hydroxyl groups with small molecules. Bilo et al. [22] obtained good mechanical properties and a biodegradable thermoplastic material by solubilizing extracted rice straw in large amounts of trifluoroacetic acid (TFA). Functionalization of hydroxyl groups could be performed by etherification using benzyl chloride of kenaf [23] and bamboo [24] or acrylonitrile [25] of bagasse, both preceded by NaOH pre-treatment. Thermoplastic material could also be obtained by the combination of both action decrystallization of cellulose using ionic liquid and in the same time functionalization of hydroxyl groups using esterifying agents such as phthalic anhydride [26], vinyl esters [27], or short/long chain acyl groups [28,29]. These approaches were applied to cellulose to obtain thermoplastic materials [30–33].
In contrast to commonly practiced methods that involve large amounts of toxic chemicals and vigorous reaction conditions, thermoplastic material could be obtained using relatively small amount of trifluoroacetic anhydride (TFAA) and fatty acid in a one pot reaction at room temperature. Mixed anhydride and TFA liberated during the reaction play an important role by disrupting the cellulose crystallinity and giving higher reactivity to the hydroxyl groups to be substituted with acyl chains [34,35]. The reactivity of TFAA and fatty acids of various natural fibers to have thermoplastic properties have been reported in our previous article through the evaluation of thermal properties by TGA, DSC, and TMA and surface properties by SEM and contact angle measurement [36,37]. The mechanism of this reaction was also studied by esterification of separated lignocellulose components [38]. However, most of the reactions used large quantities of reagent to obtain maximum ester content and the mechanical properties of the resulting materials were not measured. In this present research, a series of esterification reactions of flax fiber using TFAA as an impelling agent and fatty acid as an esterifying agent was performed to evaluate its mechanical properties in relation to the chemical structure.
2.1 Materials and Sample Preparations
Flax fiber was supplied by IN’Bô, Vosges, France. The size of the particle was divided into two groups, original size and milled into a small size of 60 mesh. Carboxylic acids used were myristic acid (C14:0, 99% purity) and stearic acid (C18:0, 97% purity) purchased from Alfa Aesar (Kandel, Germany) and Sigma-Aldrich (Steinheim, Germany) and the trifluoroacetic anhydride (TFAA, purity ≥ 99%) was purchased from Sigma-Aldrich (Saint-Quentin-Fallavier, France).
Chemical modification was conducted according to the acylation method reported in our previous study [35]. Solution of equimolar quantities of fatty acids and TFAA was prepared and left 30 min to form mixed anhydride. A different quantity of oven dried flax (m0) than the TFAA used (1:4 and 1:2.5, m/m) was then added to the mixed anhydride for 4 h at room temperature in a glass flask bottle. Acylated samples were successively washed with ethanol and water followed by Soxhlet with mixture of ethanol and water (2/1, v/v) for 24 h. The sample was then dried at 103°C for 24 h (m1). The weight percent gain (WPG) was calculated as follows Eq. (1):
WPG (%)= (m1− m0)m0 ×100 (1)
Ester content was calculated from the mass of reactant grafted on the hydroxyl groups per gram of flax divided by the molecular mass of fatty acid used for esterification (M) minus 18 corresponding to the molecular mass of water released during esterification using the equation as follows Eq. (2):
Ester content =(m1− m0)m0/(m1− m0)m0(M−18)(M−18)×1000 (2)
2.3 Manufacturing Testing Specimen
Esterified flax was firstly processed in a Brabender WETH 50 twin screw measuring mixer (Brabender, Germany) in controlled temperature and constant rotation speed (160°C for 30 min under speed of 50 rpm) to transform esterified flax fiber to plastic. After plasticizing, the material was passed through a grinder to form flakes or granules. Then, the granules samples were injection molded using an open-source desktop injection machine (Holipress, Holimaker, France) with melt temperature between 180°C and 250°C to form a series of samples with a density of 0.98 g/cm3. The mold chosen for specimen injection corresponds to a mold used to produce a standard tensile specimen for mechanical tensile testing complies with ISO 527-2 type 1B.
FTIR spectroscopy in ATR mode on an ATR Perkin Elmer Spectrum 2000 (Perkin Elmer Ltd., Beaconsfield, UK) equipped with a diamond cell was used to determine the appearance or disappearance of new organic functions, and thus to confirm whether the esterification reaction was successful or not. The spectra (transmittance, T) of the flax before and after acylation were measured in the range of 4000–650 cm−1 at a resolution of 4 cm−1 and then were baseline corrected and normalized by means of the dedicated Spectrum 10 software (Perkin Elmer Ltd., Beaconsfield, UK).
Cross-polarization/magic angle spinning solid state nuclear magnetic resonance (CP/MAS 13C NMR) spectra were recorded on a Bruker MSL300 spectrometer (Bruker, Spectrospin, Germany) at a frequency of 75.47 MHz. Acquisition time was 0.026 s with a number of transients of about 1200. All the spectra were run at a relaxation delay of 5 s, CP time of 1 ms, and spectral width of 20.000 Hz. Spinning rates were 5 kHz. Interferograms were processed with Top Spin 3.6.2 using an apodization value of 21 Hz. Chemical shifts were expressed in parts per million (ppm). The crystallinity index (CrI) as a percentage was measured by the calculation of the integral of the crystalline cellulose C4 in the 86–92 ppm range (a) compared to the sum of an integral of the crystalline cellulose C4 and integral of the amorphous cellulose C4 in the 79–86 ppm range (b) [39].
CrI (100) =aa+b ×100 (3)
The mechanical properties of the samples were determined using a Zwick Roell Z100 (Zwick, Ulm, Germany). Investigations of tensile properties were measured according to ISO 527-2 and sample size according to type 1B under ambient conditions, with a load cell of 100 N at a rate of grip separation of 10 mm/min, and 5 consecutive measurements were made for each sample.
3.1 Weight Percent Gain and Ester Content
Esterification was conducted through functionalization of the hydroxyl groups of flax by a reactive acyl group of mixed anhydride formed between fatty acids and trifluoroacetic anhydride (TFAA) as presented in Fig. 1 [37]. During the reaction, trifluoroacetic acid (TFA) equivalents were produced simultaneously as byproducts that are important to disturb the crystallinity of the cellulose and to facilitate the accessibility of more hydroxyl functions due to its polarity [35]. This reaction is not only observed in the cellulose, but also in the hemicelluloses and lignin, each with different reactivities [38]. In the end of the reaction, most of the hydroxyl of flax will have reacted with acyl groups due to its stability and will be considered as esterified material. Small amounts of hydroxyl groups of fiber reacted to form trifluoroacetatyl groups. Due to the miscibility of TFA with many organic solvents and water, this group is then eliminated using water Soxhlet. Most of the TFAA used in this reaction will be transformed to TFA and should be handled with caution and may present challenges for new process development, especially regarding atom economy and waste management. Additionally, TFA is a low boiling point organic acid, which can be recovered by distillation. It can be dehydrated to trifluoroacetic anhydride or converted into high-value compounds such as isopropyl trifluoroacetate (IPTFA) [40]. The weight percent gain (WPG %) and ester content (mmol/g) were determined after esterification as the first indication of the extent of chemical modification in flax fiber.
Figure 1: Chemical reaction of fiber esterification prepared from fatty acids and TFAA
Fig. 2A shows the relationship between WPG and the ester content of myristic acid esterified flax in different sizes of particles and quantities of reagent. A maximum capacity of flax fiber hydroxyl groups available to be esterified was reported at the proportion of flax to TFAA/fatty acid of 1:8, although translucent films could be achieved using a lower proportion of 1:4 for esterified flax fiber [37]. In this research, we proposed a lower proportion of fiber to TFAA/fatty acid of 1:2.5 and 1:4. Using almost half of the reagent (1:2.5), only reduces by 22% the WPG and ester content compared to a proportion of 1:4 from about 280% to 220%. Using smaller size particles slightly increases the WPG due to the higher contact surface between lignocellulose materials and the fatty acid chain. Esterification of flax fiber in original fiber size was further investigated with different fatty acids as presented in Fig. 2B. Stearic acid esterified flax fiber presented higher WPG and slightly higher ester content comprised between 11.72 and 14.38 mmol/g compared to myristic acid esterified flax that comprised between 10.47 and 13.57 mmol/g. These results are consistent with previous studies that due to the uniformity of esterification reactivity using mixed anhydrides and TFA, the WPG of the esterified material increased linearly with the length of fatty acids used and led to similar ester content especially in fatty acids of more than 6 carbons [35,37].
Figure 2: WPG and ester content of flax in different fiber sizes (O: original, M: milled) and quantity of reagent (flax: TFAA/FA) esterified with C14:0 (A) and WPG of flax fiber esterified with C14:0 and C18:0 (B)
Chemical structure changes as a result of fatty acid esterification were established using Fourier transform infrared spectroscopy (FTIR in ATR mode) and cross-polarization/magic angle spinning solid state nuclear magnetic resonance (CP/MAS 13C NMR). The FTIR spectra in Fig. 3 demonstrates that a significant decrease of the O-H stretching band at about 3000–3500 cm−1 in non-modified flax fiber. The strong intensity of the peak at 1740 cm−1 is attributed to C=O carbonyl ester groups. The bands at 2850 cm−1 and 2920 cm−1 belonging to the symmetric and asymmetric aliphatic chains (CH, CH2, CH3), while the 720 cm−1 band is assigned to at least four linearly methylene (–CH2–) [41–44]. The substitution of free hydroxyl groups with these new peaks revealed the successful esterification of acyl groups by fatty acid confirming the structure of the modified flax proposed in Fig. 1. Different WPG between the proportion of fiber to TFAA/fatty acid of 1/2.5 and 1/4 showed similar intensities of C=O carbonyl ester at 1740 cm−1, while smaller amount of reagent presents slightly lower decrease of O-H stretching intensities which correspond to the lower WPG. There were no significant differences between myristic and stearic acid esterified flax in the FTIR spectra as they presented a similar chemical structure pattern.
Figure 3: FTIR spectra of esterified flax with various quantities of reagent (A) and with various fatty acids (B)
Solid state 13C NMR spectra in Fig. 4 confirmed the structure changes of esterified flax according to the various carbon atoms of the different carbohydrates in flax fiber. Non-modified flax showed dominant signals characteristic of polysaccharides as cellulose is the main constituent of flax fiber in the region between 50 and 110 ppm [45–47]. The signal at 105 ppm is assigned for the C1 hemi acetic carbon atom of the cellulose and hemicellulose. In the esterification at low quantity of reagent (proportion flax to fatty acid 1:2.5), the signal of C1 duplicated at 102 and 105 ppm and at higher quantity of reagent (proportion flax to fatty acid 1:4) both for myristic and stearic acid, the signal of C1 hemi acetic carbon were shifted to lower signal about 102 ppm attributed to anomeric carbon of non-reducing unit [48]. The signal of C4 carbon of non-modified flax that appears between 79 and 92 ppm was duplicated owing to the presence of amorphous cellulose (83–85 ppm) and crystalline cellulose (88–89 ppm). This duplicate signal was broadened in the sample of low quantity of reagent and was not observed in high a quantity of reagent. The signals of C2/C3/C5 carbon in esterified flax were observed in lower intensity than in non-modified flax between 70–80 ppm. The signal of C6 carbon was also duplicated owing to the characteristic of disordered cellulose at 63 ppm and ordered cellulose at 65 ppm. After esterification, the signal C6 carbon was broadened and shifted to 64 ppm.
Figure 4: CP/MAS 13C NMR spectra of esterified flax in various quantities of reagent (A) and various fatty acids (B)
The appearance of several new signals corroborated the success of fatty acid esterification such as the peak at 172 ppm assigned to carbonyl ester groups (C=O) of myristate and stearate acyl group [45,46,49]. The signal between 15–35 ppm was assigned to the methylene groups (–CH2–) due to the presence of aliphatic chains in esterified flax fiber [34,35,43,50]. Unlike native wood that presents aromatic carbons between 120–160 ppm, non-modified flax does not present any signal in this region and is similar to the wood cellulose solid NMR spectra, confirming the low quantity of lignin in non-modified flax fiber [38,51].
Determination of the crystallinity index (CrI) is known to be correlated with certain intensities of NMR spectra as well as other approaches such as XRD, Raman, and FTIR. These different techniques can give results with different absolute values but the general trends between samples and their relative values are consistent [52]. In this case, the crystallinity index of flax fiber was estimated by comparing the integral of the crystalline cellulose C4 with the sum of the integral of the crystalline and integral of the amorphous C4 cellulose. The CrI is about 50% when the peaks of amorphous and crystalline are roughly equal in size. The amorphous and crystalline peaks of non-modified flax are of similar size which results in CrI of 42.9%. As presented in Fig. 4A, esterification of myristic acid in lower quantities decreases the CrI to 29.8% and esterification of myristic acid in higher quantities resulted in a remarkable decrease in CrI to 4.5%. Fig. 4B shows the influence of fatty acid length esterification on the CrI. Stearic acid esterified flax presented slightly lower CrI than non-modified flax. A small decrease in the esterified flax can be attributed to the esterification process, where long fatty acid chains attach to the hydroxyl groups within the flax structure. This process loosens the flax texture, increasing the crystallinity of cellulose and creating a new crystalline region from the aliphatic side chain [53]. This phenomenon was reported in long fatty acid esterified wood observation using XRD, which shows a diffraction peak in a low angle region and increases the crystallinity of esterified wood [35].
Mechanical properties evaluation of thermoplastic film was performed by tensile test depicted in Fig. 5, comprising the maximum tensile strength, elongation at break, and Young’s modulus in different quantities of reagent, different sizes of flax particles and different fatty acid. The tensile strength of the high quantity of reagent (1:4) esterification of original flax and milled flax was 7.36 and 6.12 MPa, respectively. Decreasing by almost half the quantity of reagent (1:2.5) improved by 50%–70% the tensile strength to 12.47 and 9.05 MPa of original flax and milled flax, respectively. Young’s modulus of myristic acid esterified flax also increased by a factor of three from 219 MPa to 656 MPa and doubled from 158 MPa to 324 MPa for original flax and milled flax, respectively when reducing the quantity of TFAA and myristic acid in the reaction (Fig. 5A). These results were in accordance with previously reported results for thermoplastic paramylon using lauric and myristic acid [54]. The highest tensile strength and Young’s modulus of esterified flax were observed in stearic acid esterified flax of 14.3–14.5 MPa and 605–1227 MPa, respectively for proportions 1:2.5 and 1:4, flax to TFAA/FA (Fig. 5B). Tensile strength and Young’s modulus of stearic acid esterified flax obtained in this research were higher than stearic acid esterified microcrystalline cellulose [55] and unsaturated fatty acids esterified cellulose [56], LDPE [57,58] and HDPE (Young’s modulus) [59]. Elongation at break indicates how much the sample lengthens permanently when experiencing tensile force before breaking. We noticed a drastic increase of elongation from about 5% to 20% when the amount of fatty acid increased in the reaction. Generally, utilization of flax in original size results in slightly higher tensile strength and Young’s modulus and slightly lower elongation at break than milled flax.
Figure 5: Mechanical properties of C14:0 esterified flax in different quantities of reagent and size of particle (A) and esterified flax in different quantities of reagent and fatty acids (B)
Fig. 6 presented the stress-strain curves of each sample for a better understanding of the mechanical properties of esterified flax. Myristic acid esterified flax in a high quantity of reagent showed ductile or flexible behavior of materials than low quantity or low ester content. This behavior could be related to the extended plasticizing effect due to alkyl chains in esterified materials as ester content increased [44]. A higher value of elongation at break was also reported for the higher molar ratio of the esterifying agent to the substrate [60]. On the other hand, stearic acid esterified flax was the least ductile or brittle behavior than the other sample. This is possibly ascribed to the high crystallinity of stearic acid esterified flax fiber. Decreasing the size of the flax particles also increases the ductility of the film. Lignocellulose fiber has an important role in increasing the mechanical properties of esterified flax film. High tensile strength of the esterified flax was achieved in sufficient ester content for thermoplasticity, maximum ester content led to ductile and flexible thermoplastic materials.
Figure 6: Stress-strain diagrams of esterified flax in several conditions (A), a mechanical test sample of esterified flax with C14:0 (B) and 18:0 (C)
A study of chemical structure and mechanical properties of thermoplastic flax fiber through solvent free esterification was investigated. Utilization of the proportion of flax to TFAA/FA of 1:2.5 only reduces 22% of WPG than the proportion of 1:4 from about 280% to 220%. Using this amount of acyl introduced to the flax hydroxyl groups, the FTIR results confirmed the success of flax fiber chemical modification by the appearance of carbonyl ester and aliphatic chain for both the 1:4 and 1:2.5 treatments in similarly high intensity, residual hydroxyl stretch indicated a small amount of free hydroxyl groups were unesterified. Solid state 13C NMR analysis complemented chemical structure change and allowed estimation of the crystallinity index (CrI) of esterified flax. Increasing ester content decreased CrI for myristic acid esterification. Using the same proportion of flax and TFAA/FA, stearic acid esterified flax showed higher CrI than myristic acid due to the crystallization of long fatty acid chains to the hydroxyl groups within the fiber structure. Having higher crystallinity, stearic acid esterified flax resulted in higher tensile strength and Young’s modulus than myristic acid esterified flax. Generally, fatty acid esterified flax showed ductile behavior particularly in material with higher ester content. High tensile strength and Young’s modulus were achieved for the esterified flax with sufficient ester content for thermoplasticity.
Acknowledgement: The authors gratefully acknowledge the Région GrandEst region and Lorraine University for the doctoral fellowship granted to the first author. The authors also acknowledge PLASTINNOV for technical support during mechanical analysis.
Funding Statement: UR 4370 LERMAB is supported by a grant overseen by the French National Research Agency (ANR) as part of the “Investissements d’Avenir” program (ANR-11-LABX-0002-01, Lab of Excellence ARBRE) in the frame of the project “Woodstic”. The authors also thank ICEEL for the financial in the frame of the project “BoisPlast” (CARN 0013 01).
Author Contributions: The authors confirm contribution to the paper as follows: study conception and design: Firmin Obounou Akong, Frédéric Fradet, Philippe Gérardin; data collection: Prabu Satria Sejati, Jennifer Afrim. Alexandre Maenhaut, Julie Maillet; analysis and interpretation of results: Prabu Satria Sejati, Luke Froment, Alexandre Maenhaut, Julie Maillet, Firmin Obounou Akong, Frédéric Fradet, Philippe Gérardin; draft manuscript preparation: Prabu Satria Sejati, Adrien Magne, Firmin Obounou Akong, Philippe Gérardin. All authors reviewed the results and approved the final version of the manuscript.
Availability of Data and Materials: Not applicable.
Ethics Approval: Not applicable.
Conflicts of Interest: The authors declare no conflicts of interest to report regarding the present study.
References
1. Fredi G, Dorigato A. Recycling of bioplastic waste: a review. Adv Ind Eng Polym Res. 2021;4(3):159–77. doi:10.1016/j.aiepr.2021.06.006. [Google Scholar] [CrossRef]
2. Walker TR, Fequet L. Current trends of unsustainable plastic production and micro(nano)plastic pollution. TrAC-Trends Anal Chem. 2023;160(6510):116984. doi:10.1016/j.trac.2023.116984. [Google Scholar] [CrossRef]
3. PlasticEurope. Plastics—The Facts 2022. Brussel, Belgium; 2022. Available from: https://plasticseurope.org/fr/knowledge-hub/plastics-the-facts-2022/ [Accessed 2024]. [Google Scholar]
4. Moudood A, Rahman A, Öchsner A, Islam M, Francucci G. Flax fiber and its composites: an overview of water and moisture absorption impact on their performance. J Reinf Plast Compos. 2019;38(7):323–39. doi:10.1177/0731684418818893. [Google Scholar] [CrossRef]
5. Tsegaye B, Ström A, Hedenqvist MS. Thermoplastic lignocellulose materials: a review on recent advancement and utilities. Carbohydr Polym Technol Appl. 2023;5(3):100319. doi:10.1016/j.carpta.2023.100319. [Google Scholar] [CrossRef]
6. Yang J, Ching YC, Chuah CH. Applications of lignocellulosic fibers and lignin in. Polymers. 2019;11:1–26. [Google Scholar]
7. Zhao X, Cornish K, Vodovotz Y. Narrowing the gap for bioplastic use in food packaging: an update. Environ Sci Technol. 2020;54(8):4712–32. doi:10.1021/acs.est.9b03755. [Google Scholar] [PubMed] [CrossRef]
8. Cinar SO, Chong ZK, Kucuker MA, Wieczorek N, Cengiz U, Kuchta K. Bioplastic production from microalgae: a review. Int J Environ Res Public Health. 2020;17(11):1–21. doi:10.3390/ijerph17113842. [Google Scholar] [PubMed] [CrossRef]
9. Ahmed MJ, Ashfaq J, Sohail Z, Channa IA, Sánchez-Ferrer A, Ali SN, et al. Lignocellulosic bioplastics in sustainable packaging—recent developments in materials design and processing: a comprehensive review. Sustain Mater Technol. 2024;41(4):e01077. doi:10.1016/j.susmat.2024.e01077. [Google Scholar] [CrossRef]
10. Reshmy R, Thomas D, Philip E, Paul SA, Madhavan A, Sindhu R, et al. Bioplastic production from renewable lignocellulosic feedstocks: a review. Rev Environ Sci Biotechnol. 2021;20(1):167–87. doi:10.1007/s11157-021-09565-1. [Google Scholar] [CrossRef]
11. Yan L, Chouw N, Jayaraman K. Flax fibre and its composites—a review. Compos Part B Eng. 2014;56(6):296–317. doi:10.1016/j.compositesb.2013.08.014. [Google Scholar] [CrossRef]
12. Bledzki AK, Gassan J. Composites reinforced with cellulose. Prog Polym Sci. 1999;24(2):221–74. doi:10.1016/S0079-6700(98)00018-5. [Google Scholar] [CrossRef]
13. Wang B, Tabil L, Panigrahi S. Effects of chemical treatments on mechanical and physical properties of flax fiber-reinforced composites. Sci Eng Compos Mater. 2008;15(1):43–57. doi:10.1515/SECM.2008.15.1.43. [Google Scholar] [CrossRef]
14. Islam MZ, Ulven CA. Effect of loading frequency on the high cycle fatigue strength of flax fiber reinforced polymer matrix composites. J Renew Mater. 2022;10(5):1185–200. doi:10.32604/jrm.2022.018018. [Google Scholar] [CrossRef]
15. Zhu J, Zhu H, Njuguna J, Abhyankar H. Recent development of flax fibres and their reinforced composites based on different polymeric matrices. Materials. 2013;6(11):5171–98. doi:10.3390/ma6115171. [Google Scholar] [PubMed] [CrossRef]
16. Kannan TG, Wu CM, Cheng KB, Wang CY. Effect of reinforcement on the mechanical and thermal properties of flax/polypropylene interwoven fabric composites. J Ind Text. 2013;42(4):417–33. doi:10.1177/1528083712442695. [Google Scholar] [CrossRef]
17. John MJ, Anandjiwala RD. Chemical modification of flax reinforced polypropylene composites. Compos Part A Appl Sci Manuf. 2009;40(4):442–8. doi:10.1016/j.compositesa.2009.01.007. [Google Scholar] [CrossRef]
18. Li X, Tabil LG, Panigrahi S, Crerar WJ. The influence of fiber content on properties of injection molded flax fiber-HDPE biocomposites 2013. In: CSBE/SCGAB 2006 Annual Conference, 2006 Jul 16–19; Edmonton Alberta. doi:10.13031/2013.22101. [Google Scholar] [CrossRef]
19. Makhlouf A, Belaadi A, Amroune S, Bourchak M, Satha H. Elaboration and characterization of flax fiber reinforced high density polyethylene biocomposite: effect of the heating rate on thermo-mechanical properties. J Nat Fibers. 2022;19(10):3928–41. doi:10.1080/15440478.2020.1848737. [Google Scholar] [CrossRef]
20. Zhang J, Wang H, Ou R, Wang Q. The properties of flax fiber reinforced wood flour/high density polyethylene composites. J For Res. 2018;29(2):533–40. doi:10.1007/s11676-017-0461-0. [Google Scholar] [CrossRef]
21. Niu H, Jiao X, Wang R, Zhou H. Direct manufacturing of flax fibers reinforced low melting point PET composites from nonwoven mats. Fibers Polym. 2010;11(2):218–22. doi:10.1007/s12221-010-0218-2. [Google Scholar] [CrossRef]
22. Bilo F, Pandini S, Sartore L, Depero LE, Gargiulo G, Bonassi A, et al. A sustainable bioplastic obtained from rice straw. J Clean Prod. 2018;200(114105):357–68. doi:10.1016/j.jclepro.2018.07.252. [Google Scholar] [CrossRef]
23. Chen C, Cho M, Kim B-W, Nam J-D, Lee Y. Thermo plasticization and characterization of kenaf fiber by benzylation. J Ind Eng Chem. 2012;18(3):1107–11. doi:10.1016/j.jiec.2011.12.012. [Google Scholar] [CrossRef]
24. Sun E, Sun F, Zhang Z, Dong Y. Interface morphology and thermoplasticization behavior of bamboo fibers benzylated with benzyl chloride. Surf Interface Anal. 2016;48(2):64–72. doi:10.1002/sia.5889. [Google Scholar] [CrossRef]
25. Hassan ML, El-Wakil NA, Sefain MZ. Thermoplasticization of bagasse by cyanoethylation. J Appl Polym Sci. 2001;79:1965–78. doi:10.1002/(ISSN)1097-4628. [Google Scholar] [CrossRef]
26. Chen MJ, Shi QS. Transforming sugarcane bagasse into bioplastics via homogeneous modification with phthalic anhydride in ionic liquid. ACS Sustain Chem Eng. 2015;3(10):2510–5. doi:10.1021/acssuschemeng.5b00685. [Google Scholar] [CrossRef]
27. Chen MJ, Li RM, Zhang XQ, Feng J, Feng J, Liu CF, et al. Homogeneous transesterification of sugar cane bagasse toward sustainable plastics. ACS Sustain Chem Eng. 2017;5(1):360–6. doi:10.1021/acssuschemeng.6b01735. [Google Scholar] [CrossRef]
28. Suzuki S, Hikita H, Hernandez SC, Wada N, Takahashi K. Direct conversion of sugarcane bagasse into an injection-moldable cellulose-based thermoplastic via homogeneous esterification with mixed acyl groups. ACS Sustain Chem Eng. 2021;9(17):5933–41. doi:10.1021/acssuschemeng.1c00306. [Google Scholar] [CrossRef]
29. Suzuki S, Hamano Y, Hernandez SC, Wada N, Takahashi K. Green conversion of total lignocellulosic components of sugarcane bagasse to thermoplastics through transesterification using ionic liquid. ACS Sustain Chem Eng. 2021;9(45):15249–57. doi:10.1021/acssuschemeng.1c05281. [Google Scholar] [CrossRef]
30. Gao X, Liu H, Shuai J, Zhao J, Zhou G, Huang Q, et al. Rapid transesterification of cellulose in a novel DBU-derived ionic liquid: efficient synthesis of highly substituted cellulose acetate. Int J Biol Macromol. 2023;242:125133. doi:10.1016/j.ijbiomac.2023.125133. [Google Scholar] [PubMed] [CrossRef]
31. Todorov AR, King AWT, Kilpeläinen I. Transesterification of cellulose with unactivated esters in superbase-acid conjugate ionic liquids. RSC Adv. 2023;13(9):5983–92. doi:10.1039/d2ra08186e. [Google Scholar] [PubMed] [CrossRef]
32. Yoshizawa A, Maruyama C, Kusuma SBW, Wada N, Kuroda K, Hirose D, et al. Aryloxy ionic liquid-catalyzed homogenous esterification of cellulose with low-reactive acyl donors. Polymers. 2023;15(2):419. doi:10.3390/polym15020419. [Google Scholar] [PubMed] [CrossRef]
33. Tarasova E, Savale N, Krasnou I, Kudrjašova M, Rjabovs V, Reile I, et al. Preparation of thermoplastic cellulose esters in [mTBNH][OAC] ionic liquid by transesterification reaction. Polymers. 2023;15(19):3979. doi:10.3390/polym15193979. [Google Scholar] [PubMed] [CrossRef]
34. Sejati PS, Obounou Akong F, Torloting C, Fradet F, Gérardin P. Fully wood based novel translucent and thermoplastic materials by solvent-free esterification. RSC Adv. 2022;12(54):35206–14. doi:10.1039/d2ra06555j. [Google Scholar] [PubMed] [CrossRef]
35. Sejati PS, Obounou F, Torloting C, Philippe G. Thermoplastic translucent film from wood and fatty acids by solvent free esterification: influence of fatty acid chain length. Eur Polym J. 2023;196:112276. doi:10.1016/j.eurpolymj.2023.112276. [Google Scholar] [CrossRef]
36. Sejati PS, Obounou Akong F, Fradet F, Gérardin P. Wood esterification by fatty acids using trifluoroacetic anhydride as an impelling agent and its application for the synthesis of a new bioplastic. Materials. 2023;16(21):6830. doi:10.3390/ma16216830. [Google Scholar] [PubMed] [CrossRef]
37. Sejati PS, Roche L, Afrim J, Mariani V, Akong FO, Fradet F, et al. Thermoplastic film from natural fibers and fatty acids by a single esterification reaction. Cellulose. 2024;31(7):4263–76. doi:10.1007/s10570-024-05865-1. [Google Scholar] [CrossRef]
38. Sejati PS, Obounou Akong F, Fradet F, Gérardin P. Understanding the thermoplasticization mechanism of wood via esterification with fatty acids: a comparative study of the reactivity of cellulose, hemicelluloses and lignin. Carbohydr Polym. 2024;324:121542. doi:10.1016/j.carbpol.2023.121542. [Google Scholar] [PubMed] [CrossRef]
39. Salem KS, Kasera NK, Rahman MA, Jameel H, Habibi Y, Eichhorn SJ, et al. Comparison and assessment of methods for cellulose crystallinity determination. Chem Soc Rev. 2023;52(18):6417–46. doi:10.1039/d2cs00569g. [Google Scholar] [PubMed] [CrossRef]
40. Bayer IS, Guzman-Puyol S, Heredia-Guerrero JA, Ceseracciu L, Pignatelli F, Ruffilli R, et al. Direct transformation of edible vegetable waste into bioplastics. Macromolecules. 2014;47(15):5135–43. doi:10.1021/ma5008557. [Google Scholar] [CrossRef]
41. Hou DF, Li ML, Yan C, Zhou L, Liu ZY, Yang W, et al. Mechanochemical preparation of thermoplastic cellulose oleate by ball milling. Green Chem. 2021;23(5):2069–78. doi:10.1039/d0gc03853a. [Google Scholar] [CrossRef]
42. Hanabusa H, Izgorodina EI, Suzuki S, Takeoka Y, Rikukawa M, Yoshizawa-Fujita M. Cellulose-dissolving protic ionic liquids as low cost catalysts for direct transesterification reactions of cellulose. Green Chem. 2018;20(6):1412–22. doi:10.1039/C7GC03603E. [Google Scholar] [CrossRef]
43. Pei M, Peng X, Shen Y, Yang Y, Guo Y, Zheng Q, et al. Synthesis of water-soluble, fully biobased cellulose levulinate esters through the reaction of cellulose and alpha-angelica lactone in a DBU/CO2/DMSO solvent system. Green Chem. 2020;22(3):707–17. doi:10.1039/C9GC03149A. [Google Scholar] [CrossRef]
44. Duchatel-Crépy L, Joly N, Martin P, Marin A, Tahon JF, Lefebvre JM, et al. Substitution degree and fatty chain length influence on structure and properties of fatty acid cellulose esters. Carbohydr Polym. 2020;234(11):115912. doi:10.1016/j.carbpol.2020.115912. [Google Scholar] [PubMed] [CrossRef]
45. Kostryukov SG, Petrov PS, Tezikova VS, Masterova YY, Idris TJ, Kostryukov NS. Determination of wood composition using solid-state 13C NMR spectroscopy. Cellul Chem Technol. 2021;55(5–6):461–8. doi:10.35812/CelluloseChemTechnol.2021.55.42. [Google Scholar] [CrossRef]
46. Popescu CM, Larsson PT, Vasile C. Carbon-13 CP/MAS solid state NMR and X-ray diffraction spectroscopy studies on lime wood decayed by Chaetomium globosum. Carbohydr Polym. 2011;83(2):808–12. doi:10.1016/j.carbpol.2010.08.049. [Google Scholar] [CrossRef]
47. Wooten JB, Seeman JI, Hajaligol MR. Observation and characterization of cellulose pyrolysis intermediates by 13C CPMAS NMR. A new mechanistic model. Energy Fuels. 2004;18(1):1–15. doi:10.1021/ef0300601. [Google Scholar] [CrossRef]
48. Willför S, Sjöholm R, Laine C, Roslund M, Hemming J, Holmbom B. Characterisation of water-soluble galactoglucomannans from Norway spruce wood and thermomechanical pulp. Carbohydr Polym. 2003;52(2):175–87. doi:10.1016/S0144-8617(02)00288-6. [Google Scholar] [CrossRef]
49. Wei L, McDonald AG, Freitag C, Morrell JJ. Effects of wood fiber esterification on properties, weatherability and biodurability of wood plastic composites. Polym Degrad Stab. 2013;98(7):1348–61. doi:10.1016/j.polymdegradstab.2013.03.027. [Google Scholar] [CrossRef]
50. Xie Y, Fu Q, Wang Q, Xiao Z, Militz H. Effects of chemical modification on the mechanical properties of wood. Eur J Wood Wood Prod. 2013;71(4):401–16. doi:10.1007/s00107-013-0693-4. [Google Scholar] [CrossRef]
51. Inari GN, Mounguengui S, Dumarçay S, Pétrissans M, Gérardin P. Evidence of char formation during wood heat treatment by mild pyrolysis. Polym Degrad Stab. 2007;92(6):997–1002. doi:10.1016/j.polymdegradstab.2007.03.003. [Google Scholar] [CrossRef]
52. Lee C, Dazen K, Kafle K, Moore A, Johnson DK, Park S, et al. Correlations of apparent cellulose crystallinity determined by XRD, NMR, IR, Raman, and SFG methods. In: Rojas OJ, editor. Cellulose chemistry and properties: Fibers, nanocelluloses and advanced materials. Advances in polymer science. Cham: Springer International Publishing; 2016. p. 115–31. doi: 10.1007/12_2015_320. [Google Scholar] [CrossRef]
53. Ratanakamnuan U, Atong D, Aht-Ong D. Cellulose esters from waste cotton fabric via conventional and microwave heating. Carbohydr Polym. 2012;87(1):84–94. doi:10.1016/j.carbpol.2011.07.016. [Google Scholar] [PubMed] [CrossRef]
54. Shibakami M, Sohama M. Effects of long-chain acyl substituents on the thermoplasticity and mechanical properties of paramylon mixed esters. J Polym Environ. 2020;28(8):2263–76. doi:10.1007/s10924-020-01763-2. [Google Scholar] [CrossRef]
55. Li ML, Hou DF, Li PY, Feng ZW, Huang YH, Wang F, et al. One-step solvent-free strategy to efficiently synthesize high-substitution cellulose esters. ACS Sustain Chem Eng. 2024;12(26):9669–81. doi:10.1021/acssuschemeng.4c00953. [Google Scholar] [CrossRef]
56. Kulomaa T, Matikainen J, Karhunen P, Heikkilä M, Fiskari J, Kilpeläinen I. Cellulose fatty acid esters as sustainable film materials-effect of side chain structure on barrier and mechanical properties. RSC Adv. 2015;5(98):80702–8. doi:10.1039/C5RA12671A. [Google Scholar] [CrossRef]
57. Djellali S, Haddaoui N, Sadoun T, Bergeret A, Grohens Y. Structural, morphological and mechanical characteristics of polyethylene, poly(lactic acid) and poly(ethylene-co-glycidyl methacrylate) blends. Iran Polym J. 2013;22(4):245–57. doi:10.1007/s13726-013-0126-6. [Google Scholar] [CrossRef]
58. Szlachetka O, Witkowska-Dobrev J, Baryła A, Dohojda M. Low-density polyethylene (LDPE) building films—tensile properties and surface morphology. J Build Eng. 2021;44:103386. doi:10.1016/j.jobe.2021.103386. [Google Scholar] [CrossRef]
59. Kakroodi AR, Bainier J, Rodrigue D. Mechanical and morphological properties of flax fiber reinforced high density polyethylene/recycled rubber composites. Int Polym Process. 2012;27(2):196–204. doi:10.3139/217.2473. [Google Scholar] [CrossRef]
60. Hou DF, Li ML, Li PY, Zhou L, Zhang K, Liu ZY, et al. Efficient conversion of cellulose to thermoplastics by mechanochemical esterification. ACS Sustain Chem Eng. 2023;11(20):7655–63. doi:10.1021/acssuschemeng.2c07364. [Google Scholar] [CrossRef]
Cite This Article
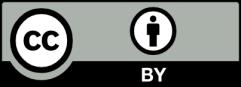
This work is licensed under a Creative Commons Attribution 4.0 International License , which permits unrestricted use, distribution, and reproduction in any medium, provided the original work is properly cited.