Open Access
ARTICLE
Charcoal Briquette Manufactured from Indonesian Sugar Palm Bunches (Arenga longipes Mogea) as Biomass-Based New Renewable Energy
1 Laboratory of Forest Product Technology, Faculty of Forestry, Universitas Sumatera Utara, Deli Serdang, 20353, Indonesia
2 Research Center for Applied Botany, National Research and Innovation Agency, Cibinong, 16911, Indonesia
3 Department of Forest Biomaterials Engineering, College of Forest and Environmental Sciences, Kangwon National University, Chuncheon, 24341, Republic of Korea
4 Faculty of Forest Industry, University of Forestry, Sofia, 1797, Bulgaria
5 Department of Furniture Design, Faculty of Forestry and Wood Technology, Poznan University of Life Sciences, Poznan, 60627, Poland
6 Department of Wood Industry, Faculty of Applied Sciences, Universiti Teknologi MARA (UiTM), Cawangan Pahang Kampus Jengka, Kuantan, 26400, Malaysia
7 Department of Bio and Natural Resource, Faculty of Bioengineering and Technology, Universiti Malaysia Kelantan, Jeli, 17600, Malaysia
8 Department of Environmental Science and Engineering, School of Engineering and Sciences, SRM University-AP, Amaravati, 522240, India
9 Research Center for Biomass and Bioproduct, National Research and Innovation Agency, Cibinong, 16911, Indonesia
* Corresponding Authors: Luthfi Hakim. Email: ; Apri Heri Iswanto. Email:
(This article belongs to the Special Issue: Recent Advances on Renewable Materials)
Journal of Renewable Materials 2025, 13(3), 637-650. https://doi.org/10.32604/jrm.2025.056365
Received 21 July 2024; Accepted 17 January 2025; Issue published 20 March 2025
Abstract
The utilisation of sugar palm bunches-charcoal briquettes (SPB-CB) represents a significant advancement in biomass energy. This study aimed to analyse the properties of charcoal briquettes produced from SPB (Arenga longipes). The experiment involved categorising the dimensions of charcoal powder into three specific particle sizes: 20–40 mesh, 40–60 mesh, and particles that could pass through a 60-mesh screen. The charcoal powder will be combined with tapioca as a binding agent at three specific concentrations: 11%, 13%, and 15%. The research findings indicate that the samples underwent 60 mesh passes achieved the maximum briquette density, with an average value of 0.58 g/cm3. The highest attainable compressive strength sample value was 27.52 kgf/cm2, which was attained by employing 60 mesh size and 15% adhesive concentration. The calorimetric investigation showed that SPB-charcoal had the highest calorific value of 25.88 MJ/kg, while the SPB-CB had a little lower caloric value of 24.64 MJ/kg. The ash content and volatile matter values showed that the briquettes with the lowest ash content had values of 10.49% and 32.65%, respectively. Furthermore, the carbon fixation values varied between 16.65% and 52.36%. Thermogravimetric analysis indicates that charcoal derived from SPB exhibits superior thermal characteristics compared to charcoal briquettes. However, thermal properties of SPB charcoal do not show significant differences when compared to charcoal briquettes that have been processed with a mesh size of 20–40 and include 11% adhesive. According to this research, it may be inferred that charcoal briquettes made from sugar palm bunches meet the requirements specified in SNI 01-6235-2000.Keywords
The present and anticipated shortage of energy has indicated an asymmetry between the demand for energy and its availability. The persistent scarcity and upward trajectory of oil prices will persist as a result of its finite and non-renewable characteristics. In order to address this issue, it is imperative to promptly counterbalance it by offering renewable energy sources that are both plentiful and cost-effective, ensuring their accessibility to a broader population [1,2].
The global energy consumption has been steadily rising over the years, primarily driven by the growing world population. The purpose of potential resources is to mitigate concerns regarding fossil fuels, namely their significant carbon dioxide emissions and the resulting negative impact on global warming. Consequently, alternative energy has garnered significant interest in numerous countries. Various policies and strategies are utilized to encourage and facilitate research in the field of renewable energy, specifically focusing on alternative sources such as biomass, solar energy, wind energy, and hydropower [3]. According to the World Bioenergy Association, fossil fuels continue to be the primary source of energy worldwide. As of 2020, fossil fuels accounted for 80% of the global energy demand, while nuclear power contributed 5%, and renewable energy technologies fulfilled approximately 15% [4]. Researchers face the challenge and duty of discovering viable and enduring options for renewable energy. Biomass is a viable alternative source of renewable energy. Briquettes, a biomass-based energy source, can replace petroleum and other fossil fuels. Several researchers have studied ways to make biomass-based briquette; some of them found that the rice straw briquette has lower emissions than the CO, NO, and SO emitted from burning chopped rice straw [5], said that the biomass briquette from sorghum panicles-pearl better fuel properties than pongamia-tamarind shell [6], studied the characteristics of charcoal briquette from the Sungkai sawdust and found that all parameters (except for the volatile matter) of the briquette comply with the Indonesian National Standard of briquette products [7].
Indonesia possesses a substantial biomass potential; nevertheless, its exploitation as an energy source is currently suboptimal [8]. An underutilized source of biomass is the sugar palm tree. Sugar palm tree is a widely recognized and extensively employed palm species in Indonesia [9,10]. In addition, sugar palm trunks can serve as excellent raw materials for producing parquet flooring due to their exceptional hardness characteristics [11]. Furthermore, apart from sap and fibers, the community also makes use of the sugar palm fruit as a snack food, including sweets and traditional beverages. The sugar palm fruit is located in the unharvested upper section of the bunch. The sugar palm bunches (SPB) have not been fully exploited throughout the sugar palm fruit harvesting procedure. Several indigenous communities employ sugar palm bunches as a source of firewood for the purpose of boiling sap into palm sugar [12,13].
Until recently, there have been no previous findings on the characteristics of charcoal briquettes derived from the SPB of Indonesian sugar palm plants (Arenga longipes Mogea). The researchers discovered that the Indonesian sugar palm possesses chemical, physical, and mechanical characteristics that render it appropriate for utilization as a solid fuel [14]. The analysis is based on the scarce information available on the technological feasibility of producing charcoal briquettes from SPB. Knowledge on the characteristics of charcoal briquettes can be valuable for utilizing them as a potential source of biomass energy in local communities, as part of the development of suitable technologies. The objective of this study was to assess the suitability of SPB as a primary material for producing charcoal briquettes, serving as a viable alternative for new sustainable energy sources.
2.1 Raw Materials Preparation and Carbonization
The sugar palm bunches (SPB) were collected from the tree at the point of ripeness of the individual fruit. Once the SPB are removed from the fruit, SPBs dried in the sun for a week. Additionally, the SPB is segmented into pieces measuring around 10–15 cm in length and then subjected to oven drying until the moisture content drops below 15%. The SPB is subsequently subjected to carbonization in an oxygen-free environment at a temperature of 350°C for 4 h which resulted in charcoal yield approximately of 30%. After undergoing carbonization, the charcoal was conditioning with the room temperature and subsequently pulverized into various sizes (Fig. 1).
Figure 1: An illustration manufacturing of SPB-charcoal briquette. (a) sugar palm bunch; (b) SPB-charcoal; (c) SPB-charcoal powder; (d) SPB-charcoal briquette
2.2 Manufacturing of Charcoal Briquette
The SPB-charcoal powder underwent screening and was subsequently divided into distinct particle sizes, specifically 20–40 mesh, 40–60 mesh, and greater than 60 mesh. Tapioca flour was used as an adhesive to combine with each particle size. Tapioca starch is one of the components commonly utilized as an adhesive for producing charcoal briquettes. The adhesive level was considered from previous studies [15,16] that used adhesive levels ranging from 10%–20% w/w. The tapioca flour adhesive was composed of three distinct concentrations: 11%, 13%, and 15% of the weight of SPB-charcoal powder (w/w).
The dimension of briquette was manufactured of 2.5 cm diameter and 3 cm length with target density of 0.6 g/cm3 for 10 min pressing time and 8-min conditioning time. To facilitate the bonding of SPB powders a solution was prepared by combining SPB-charcoal powder and tapioca flour. This was achieved by adding 50 mL of water to the mixture. This treatment was conducted using 5 replicates. The process for manufacturing SPB-charcoal briquettes is outlined in Table 1.
2.3 Physical and Mechanical Properties of SPB-Charcoal Briquette
The physical and mechanical properties of the SPB-charcoal briquette were assessed, namely in terms of density and radial compression strength. The apparent density was determined as the ratio between the mass of the briquette at room temperature (+25°C) and 65% relative humidity. The dimensions of the briquettes were measured using a calliper ruler with an accuracy of 0.01 mm for determined the briquette volume. The compression strength of the briquettes was determined using a Universal Testing Machine (Tensilon, RTF 1350, A&D Company, Tokyo, Japan). The briquettes were squeezed at a constant rate of 3.5 mm/min until they failed. Five repetitions were performed to ascertain each test property.
2.4 Proximate Analysis of SPB-Charcoal Briquette
The proximate analysis of SPB charcoal briquettes involved the examination of several parameters, including moisture content according to ASTM D 3173-03 [17], ash content according to ASTM D 3174-02 [18], volatile matter according to ASTM D3175-05 [19], and fixed carbon content according to ASTM D 3172-89 [20]. The caloric value was determined by calorimeter bomb (IKA, Bomb Calorimeter, Version C2000, Königswinter, Germany).
2.5 Thermal Properties by Thermogravimetry Analysis (TGA)
A thermogravimetric study was performed using an Ekstar SIII-Type 7300 instrument (Hitachi, Tokyo, Japan) to measure the rate of mass change and thermal stability of the SPB-charcoal and SPB-charcoal briquette samples at different temperatures. In this examination, samples weighing approximately 10 mg were subjected to heating in an alumina crucible. The temperature was increased from room temperature to 750°C at a rate of 10°C per minute. Throughout the process, the apparatus was continuously flushed with nitrogen at a flow rate of 30 mL per minute.
2.6 Quality of SPB-Charcoal Briquette Based on Indonesian National Standard
The quality of SPB-charcoal briquette is assessed by comparing it to the standards set by SNI 01-6235-2000 [21], which serves as a benchmark for charcoal briquette quality. The quality of charcoal briquettes, as specified by the Indonesian National Standard (SNI), is presented in the following Table 2.
Factorial completely randomized design was used to analyse interaction between particle size level (20–40 mesh; 40–60 mesh, and >60 mesh) and adhesive level (11%, 13%, and 15%). The Duncan’s Multiple Range Test (DMRT) was employed for conducting additional testing, with a significance level of 5%, while a statistical analysis was performed using R-Studio software Version 4.0.0.
3.1 Physical and Mechanical Properties of SPB-Charcoal Briquette
The density of the briquette made from sugar palm bunch charcoal has been determined and the corresponding measurement is presented in Fig. 2a. The research findings indicate that the density of the manufactured charcoal briquette falls within the range of 0.42–0.60 g/cm3. As the particle size decreases and the adhesive content increases, the density value increases. The density value obtained aligns with the findings of Rohman et al. [22] in their study on sugar frond raw materials, specifically 0.68 g/cm3. The density of a substance is affected by the size of its particles. Specifically, when the particle size decreases, the surface area of the particles increases, resulting in more contact between surfaces. This increased contact leads to an increase in density. Similarly, increasing the amount of tapioca adhesive will result in a larger density of the briquette. The density of charcoal briquettes is affected by the uniformity of the adhesive mixture with charcoal particles. When the stirring is more even, the resulting briquettes become stronger, as the charcoal particles are evenly distributed. Briquettes possessing higher density will exhibit a prolonged combustion rate compared to briquettes with lesser density [23,24]. All briquettes generated in this study have successfully complied with the Indonesian National Standard for density, which requires a minimum of 0.44 g/cm3. The correlation between the size of particles and the amount of adhesive present has a notable impact on the density of the charcoal briquettes that are produced. Nevertheless, the density of this substance is lower compared to charcoal briquettes made from oil palm fronds and tapioca glue, which have a density range of 0.84–0.99 g/cm3 [25].
Figure 2: a: Density histogram of SPB-charcoal briquette; b: Compression strength histogram of SPB-charcoal briquette
Fig. 2b displays the findings of the compressive strength test conducted on charcoal briquettes made from empty bunches of sugar palm (Arenga longipes Mogea). Compressive strength test is a mechanical test measuring the maximum amount of compressive load a briquette can bear before fracturing. Compressive strength is one of the most significant qualities of a briquette, determining its stability and durability. According to Okot et al. [26], the compressive strength test is used to evaluate the compressive stress caused by the weight of the top briquettes on the bottom briquettes during storage, transportation, and handling. The compressive strength values of the charcoal briquettes generated varied between 4.96 and 27.52 kgf/cm2. The charcoal briquettes with a particle size of 40 mesh and an adhesive percentage of 11% exhibited the lowest compressive strength, whereas the charcoal briquettes with a particle size of 60 in mesh and adhesive concentration of 15% shown the maximum compressive strength. The statistical analysis showed that the combination of particle size and adhesive content did not have a significant impact on the compressive strength value of charcoal briquettes. However, both parameters individually influenced the compressive strength value, with particle size having a particularly strong effect. Decreasing the size of the particles leads to an increase in the compressive strength of the charcoal briquettes. Consistent with other research, decreasing the particle size will result in an increased compressive strength measurement [27,28]. Adding adhesive level didn’t significantly increase the compression strength in the charcoal briquette with the lowest particle size; the particle size caused it. According to prior study [16], the particle size of charcoal briquettes influences the compressive strength value; the smaller the particle size and the lower the moisture content, the higher the compressive strength. On the other hand, the addition of adhesives has an effect on moisture content (Fig. 3b), so the possibility of moisture content affecting compressive strength does not increase significantly.
Figure 3: a: Caloric value histogram of SPB-charcoal briquette; b: Moisture content histogram of SPB-charcoal briquette; c: Ash content histogram of SPB-charcoal briquette; d: Volatile matter histogram of SPB-charcoal briquette; e: Fixed carbon histogram of SPB-charcoal briquette
The compressive strength obtained in this investigation was inferior than that reported in a prior work conducted by Rohman et al. [22], where charcoal briquettes were generated from sugar palm fronds, yielding a compressive strength value of 97.7 kgf/cm2. According to Lestari et al. [29], charcoal briquettes that have a high density will exhibit superior mechanical strength. The significant compressive strength value suggests a robust cohesive force between particles in sugar palm bunch charcoal briquettes. This could be attributed to the presence of high molecular weight organic compounds that create water bridges between neighbouring particles. Additionally, the uniform surface of the charcoal briquettes contributes to the solidification of particle bonds [30].
3.2 Proximate Analysis of SPB-Charcoal Briquette
Fig. 3a displays the calorific value of charcoal briquettes under different conditions, including particle size treatment and adhesive concentration. The graph also includes untreated charcoal as a control. The graph indicates that there is an inverse relationship between particle size and adhesive concentration with calorific value. Specifically, larger particle sizes and higher adhesive concentrations are associated with lower calorific values. The 60-mesh particle treatment with an adhesive concentration of 15% had the lowest calorific value, measuring 21.74 MJ/kg. On the other hand, the 20-mesh particle treatment with an adhesive concentration of 11% had the highest calorific value. However, the calorific value of charcoal briquettes was still lower than that of untreated charcoal, which was 22.88 MJ/kg. The calorific value of the charcoal briquettes generated exceeded the findings of Rohman et al. [22], who utilised sugar palm fronds as raw materials and reported a calorific value of 24.46 MJ/kg. The high calorific value of a substance is determined by its low water and ash content, as well as its high bound carbon. Additionally, the type of raw material used to make briquettes plays a significant role in the production of bound carbon, with varied material features having an impact. Furthermore, particle size also affects the level of heat content, the smaller the particle size, the higher the heat value because it is related to the low water content and the wider surface area of the particles [31].
According to the available literature (Table 3), the caloric values of SPB charcoal were marginally lower compared to charcoal derived from teakwood sawdust [32], rice husk charcoal briquette [33], and coconut shell charcoal briquette [34]. Nevertheless, the caloric values of SPB-charcoal briquette exceeded those of coconut shell briquette and bamboo charcoal briquette [34], as well as charcoal briquette created from organic waste [35], and charcoal briquette made from coconut shell with pine resin [36]. The findings of this study demonstrate that the calorific value of the SPB-charcoal briquettes generated is comparable to that of charcoal briquette products made from different types of raw materials, including both wood and non-wood sources.
The moisture content of the charcoal briquette made from sugar palm bunch is quantified and the outcome is presented in Fig. 3b. The graphic illustrates that the water content of the charcoal briquette varies between 3.92% and 14.58%. Incorporating adhesive material into the charcoal briquette results in an elevation of the briquette’s moisture content. On the other hand, when the particle size of the charcoal decreases, the moisture content of the resulting charcoal briquette decreases as well. The moisture content of the charcoal briquette, produced by treating particles of size 40 and 60 mesh with adhesive contents of 11% and 13%, respectively, complies with the SNI norm of ≤8%. The water content value of the charcoal briquette created is significantly greater than the water content value of the charcoal briquette derived from the sugar palm fronds, as determined by Rohman et al. [22], which is 4.17%. Similarly, the water content of the charcoal briquette made from a combination of oil palm fronds and palm shells, as determined by Simatupang et al. [25] ranges from 1.3% to 1.6%. The statistical analysis shows that the relationship between the particle size and the adhesive level used does not have an impact on the moisture content of the charcoal briquettes produced. The results indicate that the moisture content of charcoal briquettes is affected by the charcoal particle size, adhesive content, type of raw material, and carbonisation process [24,31,38]. According to Muraina et al. [39], charcoal briquettes with smaller particle sizes will have a faster drying time compared to charcoal briquettes with bigger particle sizes. The use of adhesive material in charcoal briquettes also impacts the moisture content generated, as a result of the incorporation of water into the adhesive substance employed [40].
Fig. 3c demonstrates that the ash concentration of the manufactured charcoal briquettes varies between 10.49% and 20.39%. The charcoal briquettes with a particle size of 60 mesh and 13% adhesive have the highest ash content value, specifically 20.39%. On the other hand, the charcoal briquettes with a particle size of 20 mesh, 40 mesh retained, and 13% adhesive have the lowest ash content value, which is 10.49%. These findings suggest a positive correlation between particle size and ash content, indicating that smaller particle sizes are associated with higher ash concentration. The presence of a significant amount of ash in charcoal briquettes indicates that the combustion residue produced by the briquettes is substantial, but the energy value of the briquettes is relatively low [41]. The ash concentration in briquettes can be affected by the presence of inorganic components in biomass waste and the amount of glue used during the briquette manufacturing process [42]. Prior research also identified elevated ash concentration levels exceeding 20% [43]. Compared with SNI, although the ash content of SPB-CB has not met the standard requirements set, the moisture content of SPB-CB is still relatively low compared to previous research.
Fig. 3d shows that the coconut palm bunch charcoal briquette product (Arenga longipes) has a volatile matter content ranging from 32.65% to 63.97%, as indicated by the test findings. The charcoal briquettes with a particle size of 20 passes, 40 holds, and 15% adhesive have the highest volatile matter content value, which is 63.97%. On the other hand, the charcoal briquettes with a particle size of 40 passes, 60 holds, and 11% adhesive have the lowest volatile matter content value, which is 32.65%. Imperfect carbonisation process might lead to a high volatile matter content. Furthermore, the volatile matter content is also affected by temperature and the duration of carbonisation. As the temperature during carbonisation increases, the amount of volatile materials decreases. It is evident that an increase in sticky content corresponds to an increase in volatile matter content. The reason for this is because tapioca includes carbohydrates (amylase and protein) that are not metabolised during the combustion process, resulting in the production of a significant amount of volatile chemicals [24]. Briquettes with a high volatile percentage will generate a significant amount of smoke and are more prone to ignition. On the other hand, briquettes with a lower volatile content are slightly more challenging to ignite but will burn consistently [44]. Consequently, charcoal briquettes are anticipated to possess the lowest feasible volatile content in order to minimise the amount of smoke generated. Based on the SNI 01-6235-2000 standard, a good briquette should have a maximum material loss of 15% when heated to 950°C. However, none of the treatments for SPB-CB matched the quality standards, as indicated by the test data.
The proportion of carbon that can be combusted in charcoal briquettes is determined by the fixed carbon content of the fuel. Fig. 3e demonstrates a negative correlation between adhesive content and particle size with the bound carbon value. Specifically, when the adhesive content increases and the particle size decreases, the bound carbon value decreases. The charcoal briquettes, which have a particle size smaller than 60 mesh and include 15% adhesive, have the lowest bound carbon value of 16.65%. The upper and lower limits of carbon levels represent the calorific value of the briquettes [41]. The bound carbon value is affected by the moisture content, volatile matter content, and ash content. In general, the presence of high levels of water and ash in briquettes leads to a decrease in the carbon content, making them challenging to burn due to the excess water and resulting in irregular combustion (low fixed carbon). Additionally, the high ash content leads to more frequent disposal of combustion residue [45].
Fixed carbon refers to the quantity of charcoal that remains after the devolatilization stage, which is the process of biomass combustion until all the volatile components in the charcoal have evaporated. Significant amounts of fixed carbon are indicative of high-quality charcoal. Charcoal quality improves as the fixed carbon percentage increases. High-quality charcoal is characterized by a high concentration of fixed carbon, as the combustion process relies on carbon reacting with oxygen to generate heat. The study found that charcoal briquettes with a particle size of 40 mesh and an adhesive content of 11% had the maximum fixed carbon content, making them the best charcoal briquettes.
3.3 Thermogravimetry Analysis (TGA)
Fig. 4a shows the thermogravimetry (TG) graph illustrating the reduction in weight of the SPB-charcoal briquette. Generally, thermal stabilization decreases with the particle size and adhesive concentration treatment. The SPB-charcoal briquette with small size particle (>60 mesh) showed a faster degradation rate, compared to the SPB-charcoal briquette subjected with a particle size of 40–60 mesh and 20–40 mesh, respectively. This low thermal resistance occurs because the small particle size accelerates the combustion process. As the particle size decreases, the particle’s surface area increases, leading to an accelerated combustion process on the particle’s surface [46].
Figure 4: a: Thermogravimetry graph of SPB-charcoal briquette; b: Derivatives thermogravimetry graph of SPB-charcoal briquette; c: Differential thermal analysis graph of SPB-charcoal briquette
Based on the curves, three distinct zones were identified. These zones correlate to the beginning and end points of the derivatives thermogravimetry (DTG) curve (as shown in Fig. 4b), which reflect the thermal degradation of organic substances and volatile compounds. The initial temperature range spans from 30°C to 270°C, and this is attributed to the evaporation of moisture in all the samples. The second zone, which spans from 300°C to 450°C, is where the highest amount of weight loss occurred in all the samples. In the third zone, the temperature range spans from 450°C–750°C, and this is attributed to the stabilize weight loss occurred in the samples and occurs char oxidation due to removal of residual volatiles in the samples [47]. This weight loss can be attributed to oxidation and the elimination of volatile substances, as indicated in Table 3. The highest weight loss exhibited by the SPB-charcoal briquette was because of the size of the particle >60 mesh with tapioca adhesive of 15% (w/w). Table 4 shows the complete degradation process of the SPB-charcoal and SPB-charcoal briquette. According to Table 4, the small particle size (>60 mesh) degraded more rapidly from the lower to the higher temperature. It can be inferred that the thermal degradation process in charcoal briquettes is influenced by the size of the particles.
Fig. 4c shows the differential thermal analysis (DTA) results for the all samples. The endothermic reactions in the water immersion and modification treatments occurred between 30°C and 270°C, which indicated the presence of water molecules in the all sample. In addition, exothermic reactions occurred within a temperature range of 270°C to 750°C. Exothermic peaks visible beyond 510°C indicate the removal of residual volatiles and ash content in the samples [48]. In the SPB-charcoal briquette, the exothermic peak was first reached at a temperature of approximately 390°C, while the size particle of >60 mesh counterpart was reached at a temperature of approximately 750°C. This difference in enthalpy indicated the particle size and under various adhesive treatment makes the thermal instability of the SPB-charcoal briquette.
Achievements have been achieved in the study of charcoal briquettes derived from sugar palm bunches (SPB). The SPB-charcoal briquettes exhibit excellent quality and meets Indonesian National Standard (SNI) requirements, especially characterized by a density range of 0.42–0.60 g/cm3, a compressive strength of 4.96–27.52 kgf/cm2, and moisture content of 3.92%–14.98%, as well as the calorific value varies between 21.74–24.64 MJ/kg. However, the parameters of ash content ranges from 11.07%–20.39%, whereas the volatile matter content ranges from 32.65%–63.97%, as well as the fixed carbon ranges from 16.65%–52.36% did not meet SNI requirement. According to the SNI and considering the optimal amount of adhesive used as well as the ease of particle production, the SPB-charcoal briquettes have the highest quality when formulated with a 20–40 mesh sieve particle size and a tapioca adhesive concentration of 11%. These briquettes have a calorific value of 24.64 MJ/kg, water content of 11.22%, ash content of 15.74%, volatile matter of 38.50%, fixed carbon of 34.55%, and compressive strength of 11.05 kgf/cm2. Thermogravimetry analysis indicates that SPB-charcoal briquettes have excellent thermal stability. The combustion and ignition of the briquettes endure a lengthy duration and are fully decomposed at a temperature exceeding 750°C. This demonstrates the viability of SPB-charcoal briquettes as a sustainable and renewable energy alternative.
Acknowledgement: The authors are grateful to Directorate General Higher Education, Research, and Technology, Ministry of Education, Culture, Research, and Technology for funding this research through the Regular Fundamental Research grant. The authors would also like acknowledge Laboratory of Forest Product Technology, Faculty of Forestry, Universitas Sumatera Utara and Advanced Characterization Laboratories Bandung, and Serpong, National Research and Innovation Agency through E-Layanan Sains, Badan Riset dan Inovasi Nasional.
Funding Statement: This study was funded by the Regular Fundamental Research Grant of the Directorate of Research, Technology, and Community Service, Ministry of Education, Culture, Research, and Technology, Republic of Indonesia No. 093/E5/PG.02.00.PL/2024 and Research Institution of Universitas Sumatera Utara No. 1/UN5.4.10S/PPM/KPDRTPM/2024. This research was also supported by the project “Development, Exploitation Properties and Application of Eco-Friendly Wood-Based Composites from Alternative Lignocellulosic Raw Materials”, Project No. HИC-Б-1290/19.10.2023, carried out at the University of Forestry, Sofia, Bulgaria.
Author Contributions: The authors confirm contribution to the paper as follows: study conception and design: Luthfi Hakim; Apri Heri Iswanto; Yunida Syafriani Lubis; data collection: Adam Jagwani Wirawan; Yunida Syafriani Lubis; Ridwanti Batubara; analysis and interpretation of results: Luthfi Hakim; Yunida Syafriani Lubis; Apri Heri Iswanto; draft manuscript preparation: Luthfi Hakim; Yunida Syafriani Lubis; Nam Hum Kim; Petar Antov; Tomasz Rogozinski; Lee Seng Hua; Lum Wei Chen; Rangabhashiyam Selvasembian; Jayusman; Jajang Sutiawan. All authors reviewed the results and approved the final version of the manuscript.
Availability of Data and Materials: The data that support the findings of this study are available from the corresponding author upon reasonable request.
Ethics Approval: Not applicable.
Conflicts of Interest: The authors declare no conflicts of interest to report regarding the present study.
References
1. Mombekova G, Nurgabylov M, Baimbetova A, Keneshbayev B, Izatullayeva B. The relationship between energy consumption, population and economic growth in developing countries. Int J Energy Econ Policy. 2024;14(3):368–74. doi:10.32479/ijeep.15614. [Google Scholar] [CrossRef]
2. Ahmed M, Huan W, Ali N, Shafi A, Ehsan M, Abdelrahman K, et al. The effect of energy consumption, income, and population growth on CO2 emissions: evidence from NARDL and machine learning models. Sustainability. 2023;15(15):11956. doi:10.3390/su151511956. [Google Scholar] [CrossRef]
3. Kongprasert N, Wangphanich P, Jutilarptavorn A. Charcoal briquettes from Madan wood waste as an alternative energy in Thailand. Procedia Manufact. 2019;30:128–35. doi:10.1016/j.promfg.2019.02.019. [Google Scholar] [CrossRef]
4. World Bioenergy Assosiation. Globol bioenergy statistic 2022. Sweden: World Bioenergy Association; 2022. [Google Scholar]
5. Narzary A, Brahma J, Das AK. Utilization of waste rice straw for charcoal briquette production using three different binders. Cleaner Energy Syst. 2023;5:100072. doi:10.1016/j.cles.2023.100072. [Google Scholar] [CrossRef]
6. Velusamy S, Subbaiyan A, Thangam RS. Combustion characteristics of briquette fuels from sorghum panicle-pearl millets using cassava starch binder. Environ Sci Pollut Res. 2021;28:21471–85. doi:10.1007/s11356-020-11790-0. [Google Scholar] [CrossRef]
7. Nugroho A, Istikowati WT. Characteristics and performance of charcoal briquette from the sawdust of Sungkai (Peronema canescens jack). In: IOP Conf Ser: Earth Environ Sci. 2020;473:012098. [Google Scholar]
8. Primadita DS, Kumara INS, Ariastina WG. A review a biomass for electricity generation in Indonesia. J Elect Elect Inform. 2020;4(1):1–9. doi:10.24843/JEEI.2020.v04.i01.p01. [Google Scholar] [CrossRef]
9. Azhar I, Risnasari I, Muhdi, Srena MF, Riswan. The utilization of sugar palm (Arenga pinnata) by the people around Batang Gadis Nasional Park Area. IOP Conf Ser: Earth Environ Sci. 2019;305:012016. doi:10.1088/1755-1315/305/1/012016. [Google Scholar] [CrossRef]
10. Azhar I, Nasution Z, Delvian, Agussabti, Aulin FR, Sembiring FR. Utilization of sugar palm (Arenga pinnata Merr) by the communities around the PT Toba Pulp Lestari. IOP Conf Ser: Earth Environ Sci. 2021;782:032017. doi:10.1088/1755-1315/782/3/032017. [Google Scholar] [CrossRef]
11. Nuryawan A, Tarigan A, Hakim L. The feasibility of sugar palm (Arenga pinnata) trunk for raw material of parquet (Wood Flooring). IOP Conf Ser: Earth Environ Sci. 2017;180:012017. doi:10.1088/1757-899X/180/1/012017. [Google Scholar] [CrossRef]
12. Fadhilla S, Hakim L, Agustian A, Lubis YS, Siregar AW. The diversity of utilizations, tapping flow discharge, and conservation of sugar palm (Arenga longipes Mogea) cultivated in Langkat, North Sumatra, Indonesia. Biodiversitas. 2023;24(1):122–32. doi:10.13057/biodiv/d240116. [Google Scholar] [CrossRef]
13. Mogea JP. Four new species of Arenga (Palmae) from Indonesia. Reinwardtia: J Taxon Bot Plant Sociol Ecol. 2004;12(2):181–9. [Google Scholar]
14. Hakim L, Iswanto AH, Herawati E, Batubara R, Lubis YS, Aini EN. Characterization of Indonesian sugar palm bunch (Arenga longipes Mogea) properties for various utilization purposes. Forests. 2024;15(2):239. doi:10.3390/f15020239. [Google Scholar] [CrossRef]
15. Asmara S, Lanya B, Putri AN, Rahmat A, Mutolib A. The effect of various varieties of cassava stems waste and tapioca adhesive concentrations on the quality of bio-coal briquette. IOP Conf Ser: Earth Environ Sci. 2021;739:012084. doi:10.1088/1755-1315/739/1/012084. [Google Scholar] [CrossRef]
16. Adam SNFS, Aiman JHM, Zainuddin F, Hamdan Y. Processing and characterization of charcoal briquettes made from waste rice straw as a renewable energy alternative. IOP Conf Ser: Earth Environ Sci. 2021;2080:012014. doi:10.1088/1742-6596/2080/1/012014. [Google Scholar] [CrossRef]
17. ASTM D 3173-03. American society for testing and materials in standard test method for moisture in the analysis sample of coal and cokel. West Conshocken, PA. USA: ASTM International; 2008. [Google Scholar]
18. ASTM D 3174-02. American society for testing and materials in standard test method for ash in the analysis sample of coal and coke from coal. West Conshocken, PA. USA: ASTM International; 2002. [Google Scholar]
19. ASTM D 3175-05. American society for testing and materials in standard test method for volatile matter in the analysis sample of coal and coke. West Conshocken, PA. USA: ASTM International; 2005. [Google Scholar]
20. ASTM D 3172-89. American society for testing and materials in standard test method for proximate analysis of coal and coke. West Conshocken, PA. USA: ASTM International; 1989. [Google Scholar]
21. SNI 01-6235-2000. Indonesian National Standard for charcoal briquette. Jakarta, Indonesia: National Standardization Agency; 2000. [Google Scholar]
22. Rohman F, Fahmi AN. The analysis of charcoal briquette quality according to the composition of oil palm (Elais guineensis Jacq) frond charcoal powder and sugar palm (Arenga pinnata Merr) frond charcoal powder. Jurnal Multidisiplin Madani. 2022;2(6):2879–94 (In Indonesia). doi:10.55927/mudima.v2i6.397. [Google Scholar] [CrossRef]
23. Fitri N. Manufacturing of briquette made from coffee bean bark (Coffea arabica) and sawdust with pinus gum (Pinus merkusii) as adhesive [thesis]. Makassar, Indonesia: Faculty of Science and Technology, State Islamic University of Alauddin; 2017 (In Indonesia). [Google Scholar]
24. Thamrin GAR. Quality of bio-briquette from a mixture of palm oil (Arenga pinnata) and water hyacinth (Eichhornia crassipes) with 10 tons press pressure. Russian J Agricul Socio-Econ Sci. 2023;133(1):163–73. doi:10.18551/rjoas.2023-01.20. [Google Scholar] [CrossRef]
25. Simatupang DF, Simbolon M. Fabrication of bio-briquettes from mixture of palm fronds and palm shells with varying binders of tapioca and sago flour. Int J Appl Res Sustain Sci. 2023;1(4):319–30. doi:10.59890/ijarss.v1i4.1062. [Google Scholar] [CrossRef]
26. Okot DK, Bilsborrow PE, Phan AN. Effects of operating parameters on maize COB briquette quality. Biomass Bioene. 2018;112:61–72. doi:10.1016/j.biombioe.2018.02.015. [Google Scholar] [CrossRef]
27. Pang L, Yang Y, Wu L, Wang F, Meng H. Effect of particle sizes on the physical and mechanical properties of briquettes. Energies. 2019;12(19):3618. doi:10.3390/en12193618. [Google Scholar] [CrossRef]
28. Tambunan H, Nuryawan A, Iswanto AH, Risnasari I, Basyuni M, Fatriasari W. Briquettes made of branches wood of three mangrove species bonded by starch adhesive. Materials. 2023;16(15):5266. doi:10.3390/ma16155266. [Google Scholar] [CrossRef]
29. Lestari L, Variani VI, Sudiana IN, Firihu MZ, Raharjo S, Agusu L, et al. Production and characterization of briquette from the activated charcoal of corncob. IOP Conf Ser: Earth Environ Sci. 2019;1153(1):012076. doi:10.1088/1742-6596/1153/1/012076. [Google Scholar] [CrossRef]
30. Wu S, Zhang S, Wang C, Mu C, Huang X. High-strength charcoal briquette preparation from hydrothermal pretreated biomass wastes. Fuel Process Technol. 2018;171:293–300. doi:10.1016/j.fuproc.2017.11.025. [Google Scholar] [CrossRef]
31. Sukarta IN, Sastrawidana I, Suyasa I. Proximate analysis and calorific value of fuel briquettes from wood and coffee skins biomass as a renewable energy source. Ecol Eng Environ Technol. 2023;24(1):1–16. doi:10.12912/27197050/172506. [Google Scholar] [CrossRef]
32. Musabbikhah SB. Optimizing the pyrolysis process and modelling the calorific value of sawdust charcoal as composing materials of quality briquettes. In: Proceedings of the 2nd International Conference on Applied Science, Engineering and Social Sciences (ICASESS 2019); 2020; Setbal, Portugal. p. 263–7. [Google Scholar]
33. Inegbedion F, Ikpoza E. Estimation of the moisture content, volatile matter, ash content, fixed carbon and calorific values of rice husk briquettes. In: Proceedings of the International Conference on Industrial Engineering and Operations Management; 2022; Nsukka, Nigeria. p. 5–7. [Google Scholar]
34. Siharath P, Chanthakhoun M, Kannitha S, Sonemanivong C, Vilaychaleun S, Thammathevo K, et al. The calorific value experiment on coconut shell, bamboo and mixed charcoal briquette. Asian J Sci, Technol, Eng Art. 2024;2(1):83–92. doi:10.58578/ajstea.v2i1.2480. [Google Scholar] [CrossRef]
35. Fikri E, Sartika C. Study on the use and composition of bio-charcoal briquettes made of organic waste. J Ecol Eng. 2018;19(2):81–8. doi:10.12911/22998993/81782. [Google Scholar] [CrossRef]
36. Pari G, Efiyanti L, Darmawan S, Saputra NA, Hendra D, Adam J, et al. Initial ignition time and calorific value enhancement of briquette with added pine resin. J Korean Wood Sci Technol. 2023;51(3):207–21. doi:10.5658/WOOD.2023.51.3.207. [Google Scholar] [CrossRef]
37. Alfian DGC, Tambunan MJ, Paundra F, Silitonga DJ, Syaukani M. The effect of pressure variations on the characteristics of coconut shell based briquettes using tapioca starch adhesive. ROTASI. 2023:25(3);23–32. [Google Scholar]
38. Duangkham S, Thuadaij P. Characterization of charcoal briquettes produced from blending rice straw and banana peel. Heliyon. 2023;9(6):e16305. doi:10.1016/j.heliyon.2023.e16305. [Google Scholar] [CrossRef]
39. Muraina HO, Odusote JK, Adeleke AA. Physical properties of biomass fuel briquette from oil palm residues. J Appl Sci Environ Manag. 2017;21(4):777–82. doi:10.4314/jasem.v21i4.19. [Google Scholar] [CrossRef]
40. Suharto B, dan Sutanhaji AT. Uji Kualitas Briket Kotoran Sapi Pada Variasi Kadar Perekat Tapioka dan Suhu Pengeringan. Jurnal Sumberdaya Alam dan Lingkungan. 2018;3(2):39–44 (In Indonesian). [Google Scholar]
41. Ajimotokan HA, Ehindero AO, Ajao KS, Adeleke AA, Ikubanni PP, Shuaib-Babata YL. Combustion characteristics of fuel briquettes made from charcoal particles and sawdust agglomerates. Scientif African. 2019;6(3):e00202. doi:10.1016/j.sciaf.2019.e00202. [Google Scholar] [CrossRef]
42. Setyono MYP, Purnomo YS. Analisis Kadar Air dan Kadar Abu Briket Lumpur IPAL dan Fly Ash dengan Penambahan Serbuk Gergaji Kayu. INSOLOGI: Jurnal Sains Dan Teknologi. 2022;1(6):696–703 (In Indonesian). doi:10.55123/insologi.v1i6.1047. [Google Scholar] [CrossRef]
43. Mencarelli A, Cavalli R, Greco R. Variability on the energy properties of charcoal and charcoal briquettes for barbecue. Heliyon. 2022;8(8):e10052. doi:10.1016/j.heliyon.2022.e10052. [Google Scholar] [CrossRef]
44. Shiferaw Y, Tedla A, Melese C, Mengistu A, Debay B, Selamawi Y, et al. Preparation and evaluation of clean briquettes from disposed wood wastes. Energy Sour, Part A: Recov, Utiliz Environ Eff. 2017;39(20):2015–24. doi:10.1080/15567036.2017.1399175. [Google Scholar] [CrossRef]
45. Dias Junior AF, Andrade CR, Lana AQ, da Silva ÁM, Brito JO, Milan M. Tips on the variability of BBQ charcoal characteristics to assist consumers in product choice. Eur J Wood Wood Prod. 2021;79(4):1017–26. doi:10.1007/s00107-021-01659-5. [Google Scholar] [CrossRef]
46. Safana AA, Abdullah N, Tasiu Z. A comparative study on the heat release during the combustion of coal and oil palm biomass charcoal briquette via thermogravimetric analysis (TGA). Int J Biomass Renew. 2019;8(2):1–8. [Google Scholar]
47. Kumar TTA, Ramesh SKT. Thermal decomposition kinetics of Prosopis juliflora charcoal briquette using thermogravimetric analysis. Environ Sci Pollut Res. 2023;30:16626–41. doi:10.1007/s11356-022-23399-6. [Google Scholar] [CrossRef]
48. Liu J, Jiang X, Cai H, Gao F. Study of combustion characteristics and kinetics of agriculture briquette using thermogravimetric analysis. ACS Omega. 2021;6(24):15827–33. doi:10.1021/acsomega.1c01249. [Google Scholar] [CrossRef]
Cite This Article
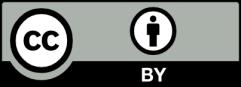
This work is licensed under a Creative Commons Attribution 4.0 International License , which permits unrestricted use, distribution, and reproduction in any medium, provided the original work is properly cited.