Open Access
REVIEW
Biobased Biodegradable Polybutylene Succinate Polymers and Composites: Synthesis, Structure Properties and Applications—A Review
1 Centre for Nanostructures and Advanced Materials (CeNAM), Council for Scientific and Industrial Research (CSIR), Pretoria, 0001, South Africa
2 Department of Chemistry, University of the Western Cape, Bag X17, Robert Sobukwe Drive, Bellville, 7535, South Africa
3 Department of Chemistry, Nelson Mandela University, Port Elizabeth, 6001, South Africa
4 Department of Chemical Sciences, University of Johannesburg, Doornfontein, 2018, South Africa
5 Department of Engineering Metallurgy, Faculty of Engineering and the Built Environment, University of Johannesburg, Johannesburg, 2028, South Africa
* Corresponding Authors: Peter Ramashadi Makgwane. Email: ; Sudhakar Muniyasamy. Email:
(This article belongs to the Special Issue: Bio-based/Degradable Materials towards A Sustainable Future)
Journal of Renewable Materials 2025, 13(3), 449-495. https://doi.org/10.32604/jrm.2025.027523
Received 02 November 2022; Accepted 24 January 2025; Issue published 20 March 2025
Abstract
The materialization of polybutylene succinate (PBS) belongs to the family of polyesters which are degradable and biodegradable, their biodegradability properties have attracted enormous interest for product development towards different polymer-based applications. Besides its biodegradability, PBS can be derived from petroleum and biobased monomers. At the same time, the latter is the driving factor for its growing interest in bioplastics for fully green and sustainable biobased-derived polymer products. The processes and techniques presented herein, are based on the production of biobased succinic acid monomer to PBS. However, the counterpart biobased monomer 1,4-butanediol (1,4-BDO) production has not been commercially demonstrated. This review discusses the progress in state-of-the-art developments in the synthesis strategies of PBS, its copolymers, and composites with the view to improve molecular weight, thermal, and mechanical properties. It further analyzes the different strategies to synthesize modified PBS polymer composites from organic and inorganic nanofillers to enhance their chemical, thermal, stability and mechanical structural properties. Importantly, the review highlights the progress in the applications of PBS copolymers and composites with tailored structure-designed properties for specific sectors such as packaging films, biomedical and drug release, fire retardants, and agricultural products. The structure-functional performance characteristics of these developments in the PBS, copolymers, and composites are highlighted to provide baseline insights for future developments in engineering the specific applications, and structural interface PBS composites with enhanced structure-functional performance properties.Graphic Abstract
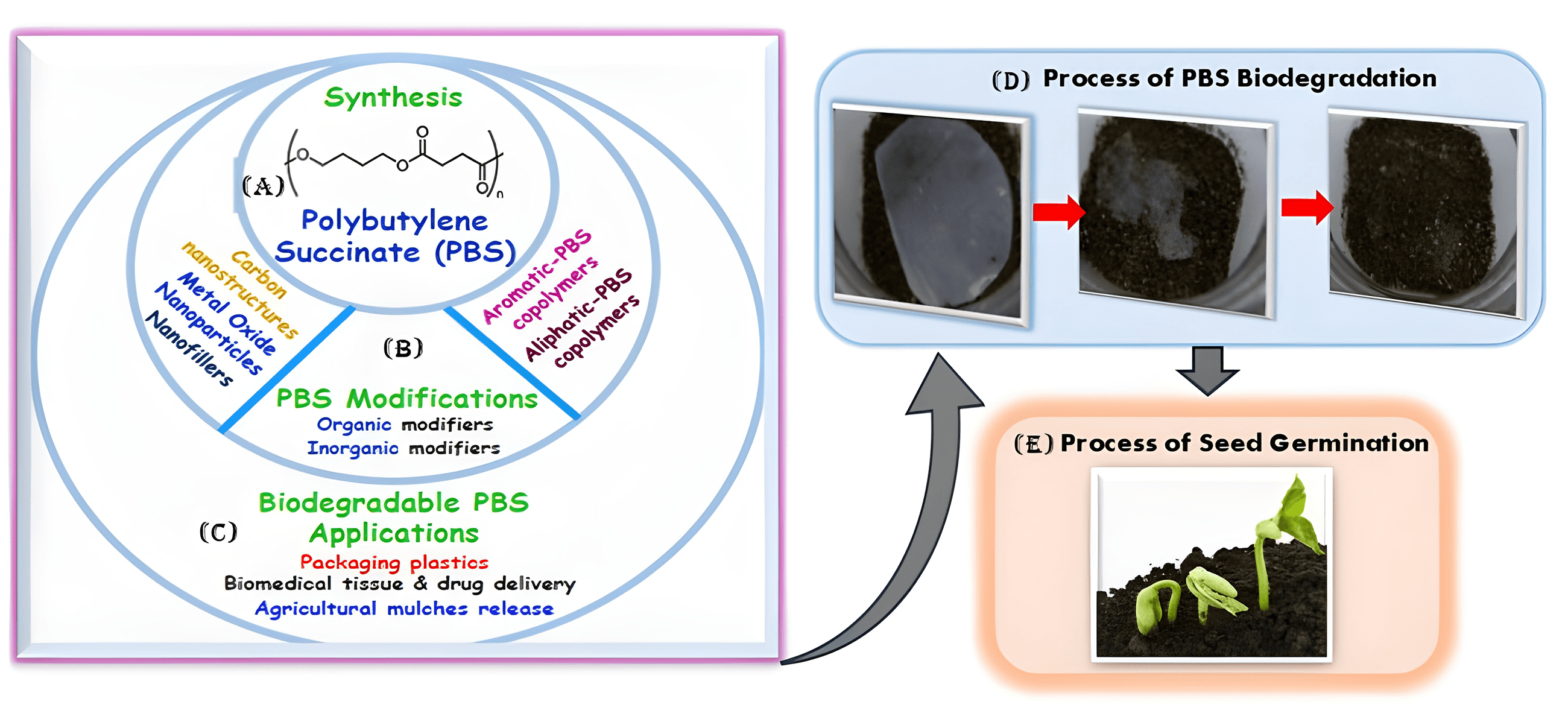
Keywords
With increasing environmental and ecological concerns due to the use of petroleum-based chemicals and products, the synthesis of chemicals and their conversion into functional performance materials from renewable resources like natural biomass has become of great interest around the globe. As a result, there is a growing shift from fossil fuel-derived chemicals [1–5]. Biomass-derived biopolymers have emerged in the past decade as one of the most promising sustainable materials due to their renewability and abundance [1,6–9]. According to a recent market analysis by Nova Institute and European Bioplastics, the global production of bioplastics is estimated to increase from 2.18 million tons (Mt) to 7.43 Mt by 2028 [10,11]. The market share of biodegradable polymers in the bio-based plastic market is currently dominated at about 90%. The forecast suggests that in 2023, large production capacities of bioplastics will occur in Asia (46.3%) and South America (45.1%) followed by Europe (4.9%) and North America (3.5%) [11]. Most synthetic plastics are derived from petrochemicals, are primarily non-biodegradable, and create extensive environmental plastic pollution [12,13]. Most consumer packaging materials greatly depend on petroleum-based polymers like poly(ethylene) derivatives [14–16]. The main concern about using these petroleum-based polymers is due to their attractive properties, including lightweight, high strength, and stiffness [14]. However, their non-degradability in environmental spaces generally results in pollution after disposal [17–21]. As a result, there is a growing drive for developing bioplastics, which may be biodegradable, biobased or both [22–26]. The desire to replace petroleum-based polymers with the biobased polymers with comparable structural mechanical properties is the focus of research development globally with the special interest in green and sustainable bioeconomy realization. Amongst the many biobased polymer materials from the biorefinery that have been explored in the past decade or two, biodegradable polyesters are the most attractive. To date, the most sought and well-known biobased polymers include polyhydroxybutyrate (PHB) [27–29], polyglutamic acid (PGA) [30], polylactic acid (PLA) [31–35], Poly(butylene adipate terephthalate) (PBAT) [36–39], and polybutylene succinate (PBS) [40–43]. These polymers have demonstrated potential for diverse applications in various sectors such as three-dimensional (3D) printing [31], biomedical [44], tissue engineering and drug delivery [45,46], packaging [36,47,48], textile and fabrics [49], and as flame retardants [50,51]. However, this review focuses primarily on PBS, with a substantial global market of about 80,000 tonnes annually [52]. Notably, the biosynthesis route to obtain the BDO from renewable material has not been used commercially or at the industrial level. However, the actual biosynthesis of BDO in E. coli starts with the conversion of glucose into succinic acid via the reductive TCA cycle, involving enzymes such as phosphoenolpyruvate carboxylase (PEPC), malate dehydrogenase (MDH), fumarase (FumC), and fumarate reductase (FRD) (Scheme 1). Succinic acid is then converted into succinyl-CoA by succinyl-CoA synthetase (SucC/SucD), followed by reduction to succinic semialdehyde through succinic semialdehyde dehydrogenase (GabD) and further conversion into 4-hydroxybutyrate (4HB) by succinic semialdehyde reductase (GabT). The 4HB intermediate is then reduced to 4-hydroxybutyraldehyde by 4-hydroxybutyrate dehydrogenase (4HBDH) and finally converted to 1,4-butanediol through aldehyde reductase/alcohol dehydrogenase (YqhD/PuuC) [53,54]. Through metabolic engineering, heterologous expression of key enzymes, and pathway optimizations, E. coli can efficiently convert glucose into BDO as a sustainable alternative to petrochemical processes.
PBS is less prominent than other synthetic biodegradable polymers, especially polybutylene adipate terephthalate (PBAT) and PLA. PBAT is a biodegradable polymer synthesized from 1,4-butane diol, adipic acid, and terephthalic acid, and it has been widely used in PBS blends to improve the toughness for certain packaging and coating applications [48,55,56]. PLA is a compostable polymer sourced from biomass that has exceptional transparency, mechanical strength, low elongation at break, poor crystallization, and low resistance to hydrolysis, which limits its wide industrial applications [57–59]. To address PLA drawbacks, polymers such as PBS are widely used to improve the physical-chemical and thermal properties of PLA for potential industrial applications [58,60]. However, unlike PLA, PBS precursor monomers are equally obtainable from fossil fuels and biomass. In fact, industrial and commercial PBS is made from both sources, with only the relative market prices for crude oil and agrochemicals determining which product is competitive. Hence, PBS dually reflects petroleum-based and biobased polymers. It offers countries with abundant fossil fuel reserves and agro-waste alike the opportunity to take advantage of the growing demand for biodegradable polymers and plastics. Stereoselectivity of the lactic acid monomers is crucial for PLA’s physical and mechanical properties, whereas these properties are somewhat correlated to the molecular weight (Mw) in PBS. Molecular weight control is synthetically more facile than achieving specific enantiomeric ratios in PBS; Table 1 summarizes the thermal and mechanical properties [61,62]. As a result, this review aims to discuss the recent developments in the synthesis and applications of PBS-based polymers and their composite materials. It begins with an introductory overview of biomass as an alternative carbon source for synthesizing biobased chemicals and biodegradable polymers. The discussion further highlights the critical different synthesis strategies to achieve high Mw PBS by using both non-catalyzed and enzymatic reactions by elaborating on the influencing reaction parameters. It further describes the modification strategies to synthesize PBS composite to improve mechanical structure properties, including Mw of PBS, using various types of inorganic and organic fillers. The review also presents the developments in the applications of some of the successfully synthesized PBS-based materials in the packaging, biomedical, agricultural fertilizer release, and fire-retardant components additives. It also presents the overview of developments in biodegradability testing properties of the PBS composite materials under various conditions, highlighting the relationship between the structure of PBS composite and biodegradation rates and time.
2 Synthesis Methods of PBS Polyesters
The synthesis of aromatic or aliphatic polyesters are usually carried out by one of the two melt-polycondensation methods namely, (i) direct esterification of aromatic or aliphatic dicarboxylic acids with a diol (or a hydroxyl-acid) through polycondensation to obtain the polyesters with high molecular weight (Mw), or (ii) transesterification of a diester dicarboxylate with a diol (or a hydroxyl-ester). Usually, both the direct esterification and transesterification reaction rates are somewhat slow at low-temperature operating conditions. Hence, they must be carried out at elevated reaction temperatures and under reduced pressure conditions. The vacuum is applied primarily during the final steps of the reaction to remove by-products, such as unreacted monomers, including water in the direct esterification process and alcohol in the transesterification process. As a result, by-products must be continuously distilled off to condense the reaction mass up to attain high Mw polymers as illustrated in Scheme 2 reaction of SA and 1,4-BDO as monomers for PBS synthesis. The first synthesis of PBS was reported in 1931 by Carothers, using the direct polycondensation reaction of SA and 1,4-BDO monomers [63]. Unfortunately, the obtained PBS material was characterized by low Mw of below 5000 g/mol, weak and brittle, and thus, it could not be used for further applications. Since then, different synthetic methods have been investigated to achieve PBS with improved Mw and good mechanical properties such as enhanced thermal stability and tensile strength. Recently, polyesters with high Mw have been synthesized by the direct esterification and melt polycondensation of dicarboxylic acids and diols in the presence or absence of catalysts and solvents [64]. Accordingly, the synthesis of PBS can be achieved in three different ways, namely, (i) without the catalyst, (ii) with the catalyst, and (iii) by using enzymes.
2.1 Non-Catalyzed Synthesis of PBS Polyester
The non-catalyzed esterification reaction of diacids and diols for the synthesis of polyesters was demonstrated to yield only oligomers with low Mw as predicted by Carothers Law [63]. For example, Agach et al. [65] reported on the single step synthesis of branched poly(glycerol-succinate) from SA and glycerol (GLY). The solventless synthesis reaction was carried out at 190°C for 24 h without using a catalyst. Likewise, Chandure et al. [66] reported on polypropylene (dicarboxylates) esters having low Mw (2500 g/mol), which were synthesized via non-catalyzed reaction process by using equimolar proportions of propane diols and SA or adipic acids. The polymers with the Mw of up to 5000 to 6000 g/mol were obtained, while their dispersity index was determined to be in the range of 2.37–2.94. As a result, these approaches proved to be ineffective for synthesizing polyesters or PBS polyesters with desirable high Mw. The increased Mw of the synthesized polyesters could improve mechanical properties. Recent research has focused on using metal catalysts to synthesize biobased polyesters with enhanced mechanical properties. Table 2 summarizes standard literature available data on metal catalyzed synthesis of PBS polyesters.
2.2 Metal-Catalyzed Synthesis of PBS Polyesters
Several transition metals based alkoxide catalysts have demonstrated effective catalytic activities in the direct esterification and transesterification reactions for the synthesis of PBS polyesters. In addition, these catalysts are more favorable and convenient as they can be used under solvent-free reaction conditions. Furthermore, numerous studies have demonstrated efficient catalytic activities of titanium (IV) based catalysts such as titanium (IV) isopropoxide [67,68], titanium (IV) isobutoxide [69], and titanium (IV) n-butoxide [70], that are commonly used for the synthesis of polyesters with high Mw.
Jin et al. [83] reported on the synthesis of PBS polyesters with Mw in a range of 20,000 and 70,000 g/mol by using 1,4-BDO and SA monomers in the direct melt condensation method. The results showed the formation of PBS polyesters with high Mw in the range of 40,000–70,000 g/mol and improved mechanical properties as summarized in Table 2 [81,83]. In esterification reactions, water is generated, and it causes the deactivation of the metal alkoxide catalysts activity due to the agglomeration of metal species. In the study by Lyoo et al. [84], a PBS polyester was synthesized in the presence of a titanium (IV) isobutoxide (TBT) catalyst via a melt polycondensation using a reaction system capable of continuously removing water before the addition of a catalyst. The obtained PBS possessed enhanced thermal and mechanical properties such as melting temperature (Tm) at 110°C, tensile strength of around 0.71 GPa, tensile modulus of 9.4 GPa, and the maximum drawn with the ratio of 9.8 PBS film. The above-mentioned ratio, tensile strength, and tensile modulus of PBS fiber obtained by melt spinning were 4–12, 0.3–0.9, and 0.9–2.2 GPa, respectively. The obtained specimens exhibited parallel molecular weights (Mw) of 37,000 and 44,000 g/mol [85]. Moreover, other studies have demonstrated rapid synthesis of aliphatic polyesters by using dicarboxylic acids and diols via the process intensification under microwave irradiation in the presence of catalysts.
To prepare aliphatic polyesters via two-step melt polycondensation, titaniumtetraisopropoxide (TTP) and titaniumtetrabutoxide are the most used metal complexes catalysts. Shirahama et al. [86] found that TTP was the best catalyst in terms of molar mass and yield obtained for the synthesis of high molecular weight PBS (Mn = 61,000 g/mol) by using dimethyl succinate (DMS) with 1,4-BDO when compared to the other metal alkoxide catalysts tested. Furthermore, the structural orientation of the catalyst can also influence its catalytic activity [86,87]. Similarly, in some instances, polymerization rates were even influenced by the chemical structure of the monomers and the reaction type (i.e., direct esterification or transesterification). For example, E. Gubbels et al. [87] demonstrated that a tin catalyst was more efficient for obtaining high Mw polyesters by using a mixture of SA and 1,3-butanediol (1,3-BDO) in equimolar proportions via transesterification process than other metal catalysts such as titanium or zirconium compounds. A few studies have described the addition of the catalyst before the esterification stage, but in these instances, adding a second catalyst after the esterification stage was essential. This synthetic route is unfavorable because it uses a large quantity of metal complex catalysts, which may lead to undesirable side reactions. Some studies have also used heat stabilizer co-catalysts or additives such as poly (phosphoric acid) to avoid side reactions [88]. The synthesis of biobased aliphatic homo-polyesters with high glass transition temperatures (Tg) was successfully achieved by Lavilla et al. [89]. The solventless reaction was carried out through the melt polymerization process without the use of dibutyl tin oxide catalysts. The dibutyl tin oxide catalyst performed better than titanium (IV) tetrabutoxide (TTBT) for the synthesis of homopolyesters under mild conditions (below 160°C) and relatively short reaction times [90]. A high Mw homopolyester (>30,000 g/mol) with high dispersity value (2.3) was obtained by using dibutyl tin oxide catalyst. Recently, different strong Lewis’s acid catalysts of rare earth or transition metals, including scandium (scandium triflate, scandium perfluorooctanesulfonate or scandium triflyimide), neodymium, thulium or yttrium were investigated in the synthesis of PBS polyesters [79,90]. For example, scandium triflate (Sc(OTf)3) was use as catalyst for the polycondensation of various alkanediols with methyl succinic acid ((poly(butylene methylsuccinate)) at reaction temperatures below 45°C [79,90]. Unfortunately, low Mw polyesters (Mw < 13,000 g/mol) were formed under these reaction conditions. However, using the same Sc(OTf)3 catalyst Takasu et al. [79] demonstrated the feasibility of the bulk scale synthesis of high Mw PBS (31,000 g/mol) achieved under reduced pressure at 180°C (Scheme 3). The effective efficiency of Sc(OTf)3 ascertains the possibilities for the production of different Mw polyesters under both low temperature (Mn = 0.9 × 104 at 35°C) and high temperature (Mn = 1.13 × 104 at 120°C) conditions. Moreover, the polycondensation of SA and 1,4-BDO using Sc(OTf)3 also demonstrated the formation of high Mw PBS at lower temperature (Mn = 1.13 × 104 at 120°C). Based on these results, for the synthesis of high Mw polymers temperature and kinetics showed to play a significant impact [79,91].
In the other study, Lahcini et al. [92] investigated bismuth-based catalysts for synthesizing PBS using esterification, followed by polycondensation at 240°C under a nitrogen atmosphere. Similarly, the use of bismuth-triflate and lanthanide-triflate as catalysts for polyesterifications of dicarboxylic acids and diols was further studied by Buzin et al. and others [93,94]. The other study by Kircheldorf [90] reported on the synthesis of aliphatic polyesters by using of dimethyl aliphatic esters and diacids with succinic anhydrides or by the direct polycondensation of dicarboxylic acids in the presence of bismuth-based catalysts. Polymers with Mw of up to 31,000 g/mol were achieved when the polymerization was performed at 80°C for over 48 h [92]. Initially, diols and dimethyl succinate were condensed at 240°C in the presence of Bi2O3 and in this approach only low molar mass polyesters were achieved. In the next approach, decalin was used as a solvent under reflux conditions and 1,4-BDO and succinic anhydride were polycondensed by the azeotropic elimination of water in presence of different bismuth metal containing catalysts such as BiBr3, BiI3, BiCL3, and Bi-triflate. The BiCl3 catalyst exhibited the best performance, and the highest molar masses of polyester were obtained with this catalyst [93].
Several researchers have studied bimetallic catalytic systems to enhance the polymerization efficiency, as illustrated in Scheme 4. This approach helps to raise the transesterification reaction efficiency and decrease the duration and temperature of the reaction. For example, Bersot et al. [94] reported on the two-step, melt poly-condensation reaction (esterification and transesterification) in the presence of antimony-based bimetallic catalytic systems that enhanced the polymerization reaction and, to some extent, reduced coloration problems. Likewise, SiO2 was also used with zirconium (IV) n–butoxide (ZBT) or TBT for the polymerization of SA and 1,4-BDO to enhance the transesterification reaction by Jacquel and co-workers [95]. Colloidal silica (12 nm particle size, 200 m2/g surface area), 0.5 wt% gave better results, such as polyesters with high elongation properties (780 units), low glass transition temperature (−31°C) and suitable melting temperature (111°C). Moreover, Li et al. [96] developed a novel catalyst with biogenic guanidine as the primary catalyst and co-catalysts such as tetrabutoxyzirconium, titanium dioxide, and zinc oxides that were used for the synthesis of PBS by using SA and 1,4-BDO as monomers via transesterification and polycondensation methods.
2.3 Enzymatic Synthesis of PBS Polyester
The researchers have demonstrated significant development in synthesizing PBS-based polyesters by enzymes, which are mainly used as catalysts [97–100]. These methods are not only an alternative approach to access reusable green or sustainable catalysts but also to provide desired products without toxic residues (metal free). Secondly, these methods are to decrease or even control the side reactions towards the properties and structures of final products [101,102]. The key benefits of enzymes are associated with the flexibility of catalysts. They afford greater chemo, enantio and regio-selectivity, and are capable to lower the activation energy of chemical reaction to execute at milder reaction conditions and are derived by renewable resources [103]. By varying the temperature of the reaction triggered a different molecular weight PBS namely, 5000 to 10,000 Mw PBS was obtained at 80°C for 5–21 h under 1.8–2.2 mmHg, similarly Mw > 35,000 PBS was achieved at 95°C under similar condition [104]. Likewise, lipase enzyme (Novozym 435) was catalyzed towards the synthesis of high Mw PBS using succinic anhydride, succinic acid, and butane diol. The total procedure was subjected to two steps, step-1 is the atmospheric condensation between the succinic anhydride and butane diol in the presence of succinic acid (absence of catalysts) to afford a PBS oligomer. Moreover, it was noted that after the oligomerization, the polycondensation process must continue in the presence of Novozyme-435 under reduced pressure to achieve a high Mw PBS [104]. As a result of the study, Mw > 36,000 was obtained at 95°C after 6 h, and the Mw > 72,000 PBS was obtained at 95°C after the continuation of the reaction up to 30 h as shown in Scheme 5. In fact, for many years, PBS and PBSA were produced from petrochemical sources by Showa Highpolymer (Shanghai, China), but the important novelty was the production of PBS from renewable resources, for example, sugarcane, cassava, and corn.
3 Synthesis Modifications of PBS Copolymers
The PBS and its co-polymers research have grown interest in academia and industry in recent decades because of their diverse perspective applications [63,103]. To modify the beneficial advantages of PBS structural properties for various applications, the co-monomeric units can be introduced, and the amount incorporated during the PBS copolymer synthesis can be controlled to yield materials that ranges from soft (rubber-like) to stiff and mechanically stable [104]. However, high molecular weights are required to obtain polymeric materials with good mechanical properties. Nevertheless, the synthesis of high-molecular-weight aliphatic polyesters by conventional polycondensation is a challenge due to the simultaneous competing reactions of condensation and degradation. Therefore, to obtain polyesters with improved mechanical properties, side chains with aromatic units and chain extenders must be introduced. This approach will increase the molecular weight or, more frequently, catalysts to accelerate the kinetics. Many articles suggested using diisocyanate such as 1,6-hexamethylene diisocyanate (HDI) as a chain-extending agent could revolutionize the process. Ideally, the chain extender molecule has two functional groups that can react with the terminal –COOH or –OH of PBS and a couple of polymer chains.
Titanium butooxide displayed the most effective activity as a catalyst for this type of PBS copolymers synthesis reactions, including the lipase assisted polymerizations via enzymatic synthesis route [105]. Both aliphatic and aromatic modified copolymers of PBS have been successfully synthesized. The two main synthetic strategies for obtaining PBS-based copolymers are copolycondensation and reactive blending [106]. Copolycondensation allows the synthesis of random copolymers by means of a two-step catalytic reaction while reactive blending method can make it possible to synthesize multiblock copolymers with different block lengths by changing the mixing time. In this context, multiblock PBS copolymer derivatives were successfully obtained by copolymerizing PBS with aliphatic polyesters bearing the ether or thioether-linkages, such as poly(diethylene glycol succinate) [107], poly(butylene thiodiglycolate) [108], poly(triethylene succinate) [109], poly(thiodiethylene succinate) [110], and poly(butylene diglycolate) [111]. In their quest to combine the different properties of the homo-polyesters, namely; high melting point of PBS and higher biodegradability of polybutylene adipate (PBA), Marija and co-workers [112] reported the synthesis and characterization of high Mw aliphatic co-polyesters, poly(butylene succinate-co-butylene adipate)s obtained by transesterification reaction in the bulk from dimethyl esters of adipic acid (AA) and 1,4-BDO and SA in the presence of TBT catalyst. The effect of the copolymer composition on the enzymic degradation as well as physical and thermal properties was investigated using the lipase originating from Candida cylindracea [112]. In the other study, the biodegradable aliphatic poly(butylene succinate-co-ε-carprolactone) (PBSCs) copolymers were synthesized via polycondensation using TTP catalyst, diphenylphosphinic acid (DPPA) and stannous octoate (Sn(Oct)2) as effective co-catalysts [113]. PBS copolymerized with monoacylglycerol was produced from 1,4-BDO, dimethyl succinate (DMS), and various monoacylglycerol such as monostearin, monolaurin, and monoolein [114]. By using 1H NMR analysis, the authors showed that the copolymers obtained using monolaurin indicated the laurate component to be present in the copolymers. When more than 1 mol% monolaurin to DMS was used for copolymerization, gelation occurred, and the copolymers were insoluble in chloroform owing to transesterification of a portion of the laurate component. For copolymers containing 0.3 mol% monoolein or monostearin to DMS, break stress of the copolymers was three times that of the PBS homo-polymer, though the thermal properties and Mn of copolymers were the same. The same authors also reported the synthesis of various aliphatic copolymers of PBS such as, 3-allyloxy-1, 2-propanediol (3a), 3-methoxy-1,2-propanediol (3b) and 3-octadecyloxy-1,2-propanediol (3c) from compositions of DMS, 1,4-BDO and 3-alkoxy-1,2-propanediol as illustrate in Scheme 6 [115]. By using TTP as a catalyst, the PBS copolymers with Mn higher than 60 000 were obtained when a small amount of aliphatic 3-alkoxy-1,2-propanediol substrates were included, but Mw decreased with increasing amount of 3-alkoxy-1,2-propanediol. The PBS copolymers including a small amount of 3-alkoxy-1,2-propanediol had larger break strain than PBS homopolymer [115].
Oishi et al. [116] reported the preparation of PBS copolymers from diglycollic acid (DGA), SA, and 1,4-BDO, in the presence of TTP catalyst and co-catalyst of magnesium hydrogen phosphate trihydrate. The PBS copolymers with a Mn higher than 65,000 were obtained. The compositions of the synthesized PBS copolymers were almost the same as the starting feed compositions. However, the elastic yield stress, modulus, and break stress values decreased. On the other hand, a report describing the synthesis and characterization of high Mw PBS and its copolyesters containing minor amounts of poly(propylene succinate) (PPSu) was presented by Chen and co-workers [117]. The compositions of the copolyesters were determined in three ways from 1H and 13C NMR spectra based on (i) the relative areas of the proton peaks under butylene succinate and PS units, (ii) the carbon peaks α bonded to the ester oxygen, and (iii) the split peaks of carbonyl carbons. The results of these three methods were found to be in good agreement. The window between Tg and Tm was significantly narrowed when PS units were incorporated into PBS copolymer composite while the cold crystallization ability retarded to lower the crystallinity to a considerable extent [117]. Zhang and co-workers [118] reported a new biodegradable copolyester of PBS, poly(butylene succinate-co-butylene malate) P(BS-co-BM), which was preliminarily prepared with optically active centers and lateral hydroxyl functional groups via a four-step synthetic strategy. Firstly, the starting material of (S)-dimethyl malate was used to synthesize pure optically active benzyl-protected dimethyl malate in good yield. Then, copolyester poly(butylene succinate-co-benzyl-protected butylene malate), P(BS-co-BBM), was prepared through a skilled condensation copolymerization of dimethyl succinate, the benzyl-protected dimethyl malate, and 1,4-BDO using TTP catalyst. Finally, the benzyl protection group was removed using a palladium on carbon (Pd/C) catalyzed hydrogenation reaction in a mixed solvents of THF and methanol to attain the targeted copolyester P(BS-co-BM) was attained [118]. The characterization data showed that the lower BBM unit content was in the benzyl-protected optically active P(BS-co-BBM) copolyester, the higher crystallinity, T(m), the broader molecular distribution, and the lower T(g) would be detected. These results may be due to the presence of bulky lateral benzyl moieties. In addition, P(BS-co-55 mol % BM) exhibited thermal stability as high as that of the linear PBS, while a strong BBM unit content dependence of thermal stability was detected for the benzyl-protected copolyester P(BS-co-BBM)s. it was concluded that these new optically active P(BS-co-BM) bearing hydrophilic hydroxyl functional groups have the potential to be used for further chemical modification and construction of a new biomaterials.
The synthesis of segmented copolymers is another effective method using long-chain biobased monomers to produce BS copolymers with enhanced structural properties and greater flexibility. Stȩpień et al. [119] reported the synthesis of various aliphatic bio-copolyesters of poly(butylene succinate-succinate) (PBS-DLS) via the direct two-step polycondensation method using a semi-pilot scale reactor for melt polymerization and a titanium dioxide/silicon dioxide (TiO2/SiO2) coprecipitate as a catalyst. Based on their thermal and mechanical properties, the broad range of melt flow index values and crystallization temperatures indicates that a polyester library with customizable properties was successfully synthesized.
Recently, Gigli et al. [111] described a solvent-free process for the synthesis of high Mw PBS-based copolymers from different compositions containing sub-units monomers of glycol bearing alkyl suspended groups of different length. The synthesized PBS copolymer composites were subjected to thermal, molecular, diffractometric, and mechanical characterization. Further, the barrier performances to oxygen (O2), carbon dioxide (CO2) and nitrogen (N2) gases were analyzed to obtain information suitable for potential application of these PBS based materials in food packaging. The existence of the side alkyl groups on the polymer structure framework showed no change to the thermal stability but significantly decreased the degree of crystallinity, which made the materials more flexible than neat PBS. In addition, the barrier performance properties of some PBS copolymers were comparable or even better to those derived from LDPE, which is popularly used in flexible food packaging. A suitable synthetic method for biodegradable and inexpensive multiblock poly(ester urethane) (PEU) consisting of poly(L-lactic acid) (PLLA) and PBS blocks was developed by Zeng and co-workers [120]. By using toluene-2,4-diisocyanate (TDI) as the chain extender, the synthesis of the copolymer was successfully achieved via the chain-extension reaction of dihydroxyl terminated PLLA (PLLA-OH) and PBS pre-polymers (PBS-OH). According to the characterization data obtained, the PLLA segment was compatible with the PBS segment in the amorphous phase. The PEU crystallization was mainly induced by PBS segment as evidenced by WAXD analysis. The tensile testing data showed that the extensibility of PLLA was improved primarily by incorporating the PBS segment. The authors concluded that based on physical and chemical properties, PEU has the potential to be used as a prominent substitute to some petroleum-derived thermoplastics. A study on the structure-properties relationship of biodegradable and biobased aliphatic copolyesters based on 1,3-PDO, 1,4-BDO, SA and adipic acid (AA) was recently reported [121]. To synthesize the copolymer with high Mw, first the poly(1,3-propylene succinate-co-1,4-butylene succinate) (PPBS) and poly(1,3-propylene adipate-co-1,4-butylene adipate) (PPBA) copolyesters were obtained from polymerization reaction of various 1,3-PDO/1,4-BDO ratios using the transesterification polycondensation from the melt using titanium-based organometallic catalyst. The compositions of the synthesized copolymers were like the feed ones with random distribution of 1,3-PDO and 1,4-BDO segments along chains. Further, the co-polyesters displayed enhanced stability up to the temperature of 275°C, with the degradation performance depending mainly on the diacid structure. The authors also demonstrated that the shortening of the diacid and diol lengths increased Tg. At the same time, the crystallization rate decreased, especially for 1,3-PDO, until having amorphous copolyesters for 1,3-PDO content of 60–100 and 80 mol.% for PPBS and PPBA, respectively. In addition, both PPBS and PPBA copolyesters exhibited an isodimorphic co-crystallization trend characterized by a pseudo-eutectic melting behavior and the presence of mainly single crystalline phase, except for PPBA composing 1,3-PDO content of 50–59 mol.% which were in molten state. The interfaces of these copolymers structures showed the aerobic biodegradation rates in soil to increase relatively with the increase of the diacid length from SA to AA and the diol length from 1,3-PDO to 1,4-BDO. Efforts to synthesize materials with anti-adhesive properties by free radicals copolymerization of carboxymethyl dextran (CMD) and poly(butyl methacrylate) (PBMA), which easily created covalent bonds between hydrophilic and hydrophobic polymers have been well researched. The effects of CMD substitution degrees and CMD/BMA ratio on the copolymerization yields were also investigated. CMDPBMA copolymers characterized by 13C-NMR, ATR-FTIR, and XPS exhibited similar compositions for all conditions with 80%–95% of PBMA. The observed mechanical and low adhesive properties make the CMD-PBMA copolymers attractive candidates for medical devices. By two-step esterification and polycondensation procedure, Guo and co-workers [122] reported the synthesis of poly(butylene succinate-co-butylene 2-methylsuccinate) (P(BS-BMS)) from SA, 2-methylsuccinic acid and 1,4-BDO. These copolymer materials were evaluated for their performance in agricultural pesticides. In their study, a model drug Avermectin (Av) was encapsulated in the uniform P(BS-BMS) microparticles by premix membrane emulsification (PME) method for controlling Av delivery. An improvement in dispersion and utilization of active ingredients was observed. Initially, it showed a burst release, followed by sustained release of Av for an extended period, which had a great potential to be an effective and environmentally friendly pesticide-release vehicle.
The aromatic polyesters with good physical and mechanical properties such as poly(ethylene terephthalate) (PET) and poly(butylene terephthalate) (PBT) have been broadly applied in various areas. Nonetheless, these aromatic polyesters are difficult to degrade in the environment because of their hydrophobic and compact chemical structure properties. Conversely, it has been shown that adequate shortening of the molecular chain and incorporating some hydrophilic groups into the chain can improve the environmental degradability of aromatic polyesters [123]. This strategy of synthesizing degradable aromatic polyesters was demonstrated by Wang and co-workers [124] via the chain-extension reaction of preparing a series of multiblock poly(ester urethane)s (PBESTU) containing poly(butylene succinate) (PBS-OH) and poly(ethylene succinate-co-ethylene terephthalate) (PETS-OH). The authors studied the influence of the multiblock copolymer composition interfaces of PBESTU materials on chemical structure and mechanical and thermal properties. Based on the Tg analyses, the authors concluded that the copolymer segments interface of PETS and PBS were well-compatible, resulting in the amorphous phase. Further, they reported that PETS segments enhanced thermal degradation, while WAXD and DSC demonstrated that the PBS segment greatly contributed to the crystallization of PBESTUs. According to the tensile testing studies, the copolymers possessed excellent mechanical properties. Recently, a series of fully biobased combined aliphatic-aromatic copolyesters composed of poly(butylene furandicarboxylate-co-succinate) were synthesized by ring-opening polymerization (ROP) [125]. In addition, this reaction could be achieved by either enzymatic or chemical routes activated by using Candida antarctica lipase B (CALB) or Sn(Oct)2 catalyst, respectively. According to GPC analysis, the catalyzed ROP reaction produced copolyesters with Mw in the range of 50,000–65,000, while Mw of 15,000–45,000 was achieved for CALB enzyme mediated ROP reaction. This example demonstrates the versatility of the chemical catalyzed method in accessing the controlled synthesis of high Mw PBS copolymers. Importantly, the author demonstrated that the chemical compositions of the copolyesters produced by ROP could be simply controlled by variation of feed ratios. It was also shown that the differences in thermal properties between the two methods (i.e., by enzymatic and chemical catalysis ROP) were marginally small according to their variances in their Mw. Based on these preliminary results, it was concluded that the subsequent work on biodegradability would encourage interest in these copolyesters as fully bio-based materials suitable for potential applications. Further demonstration of the simultaneously combined synthesis of aliphatic-aromatic copolyesters at the pilot scale dedicated to biodegradable film applications was reported by Jacquel and co-workers [95]. This included the use of rigid biobased co-monomers such as isosorbide and 2,5-furandicarboxylic acid (FDCA) together as copolymers of PBS. The biobased PBS copolymers were investigated for their structure properties and compared to copolymers derived from terephthalic acid (TPA) [95]. The analysis of the structures of both PBS-FDCA and PBS-TPA copolyesters showed typical random structures while their crystallinity decreased with the increase in the amount of co-monomer added. Based on their final film properties, a large increase in the elongation at break of 1400% was observed for PBS containing 15 mol% FDCA, which is an interesting feature for film applications [953]. Recently, PBS and salicylic acid were utilized to make biodegradable random copolymers through melt polycondensation [108]. Since a small amount of salicylic acid can promote the growth of plants, they proposed that the introduction of salicylic acid in PBS polymer could improve the rate of plant growth without affecting the overall performance of PBS polymer. As a result, the study was mainly focused on discussing the influence of low salicylic acid content on copolymers and compared to the influence of medium and high salicylic acid content on copolymers. Different characterization techniques, such as TGA, DSC and XRD analysis were used to investigate the properties of copolymers. The obtained data showed that the copolymers with 0.5% SA content exhibited better elastic modulus and tensile strength, and similar thermal decomposition temperature compared to pure PBS. The enzymatic degradation of copolymers was investigated while molecular docking simulation was used to study the molecular chain structures during degradability of copolymers. Lastly, the capacity of copolymers to improve plant growth was also investigated and it was concluded that they could stimulate the growth of green vegetables. Table 3 summarizes the list of other PBS-based copolymers with their water contact angle (WCA), crystallinity data together with their mechanical properties. These include a range of elastic modulus (E), the elongation at break (eb) and the stress at break (rb) as found in various publications.
4 Nanofillers Reinforced PBS Copolymers and Composites
The effect of nanofillers reinforcement in polymer matrix for the development of nanocomposites is greatly attributed to several factors including the type of polymer matrix (random/copolymer) chosen and its chemical structure; and the type of fillers derived from organic or inorganic fillers, and its particles size, ratio, orientation and distribution. Various types of nanoparticles, such as clays [131–133], carbon nanotubes [134–136], graphene [137–141], nanocellulose [142–145], and halloysite [146–149] have been used to obtain nanocomposites with different polymers. Apart from nanofillers reinforcement with polymeric materials, compatibilization is a critical part between the phases in terms of physical or chemical bonds for improving specific required properties for their end use applications. Polymer compatibilization can be achieved by different approaches and techniques, which strongly contribute to many aspects, such as materials performance, cost, processability, renewability, and recyclability, including biodegradation and industrial applications. Many novel approaches have recently emerged in terms of compatibilization strategies, such as adding reactive polymers, block or graft copolymers, low molecular weight compounds, utilization of interchange reactive polymers, and adding cross-linking agents [150,151]. Recently, polymer composite materials have been used as flexible alternatives to conventional materials such as metals, bone fracture implants, wood, and ceramics among various other sorts of materials in the production of consumer end-user products [152]. A variety of polymer-based composites have been reported and grouped according to their type of matrix composition. The most common type of polymer composite is the particle reinforced composite. The materials that can be used in particle-reinforced composites can be anything derived from organic and inorganic fillers. This type of polymer composite is split into two categories, large particle fillers and dispersion strengthened polymer composites. Fillers that contain large particles are generally cheaper than their small-sized particle counterparts. However, the small particles have the greater ability to improve properties [153]. The addition of the filler particles usually minimizes the matrix phase’s movement near the filler particle interface [150]. Unfortunately, filling polymers with large particles comes at a price of loss of optical clearness, surface shine and may lead to an increased weight of the product. This is more severe in cases where higher filler loadings are required (≥20 wt%) [151]. This has led scientists to investigate the second category of polymer composites, the dispersion-strengthened particle reinforced polymers. Here, at least one dimension of the filler used must be in the nanoscale. These materials have been shown to possess superior physical properties compared to pristine polymers, particularly at lower filler loading. In the following sections, the discussions highlight how different types of nanomaterials, based on their geometry, are used as fillers to improve the structural properties of PBS. Herein, the fillers are discussed based on their dimensions, and how they affect the properties of PBS is highlighted.
4.1 Zero-Dimensional (0D) Nanofillers PBS Composites
Nanomaterials, which have 0D structures, have been used as fillers for PBS for various applications with targeted improved physical properties. For example, in instances where the strength of PBS is targeted, Liu et al. [154] modified the surface of tetrapod-shaped-nano ZnO and cubic-nano-ZnO with 3-aminopropyltriethyloxy silane (APS) to reinforce PBS properties. They found that reinforcing PBS with tetrapod-shaped-nano ZnO provides better increased mechanical properties of PBS than cubic-nano-ZnO [154]. They reported that the flexural strength was increased by more than 25% when ZnO was combined at 30 wt% compared to the neat PBS. This study highlighted the necessity of modifying the surface of the nano-fillers so it can be compatible with the host polymer such as PBS. However, modifying the surface of the nanomaterials is not always a prerequisite as was shown when SiO2 NPs were used as fillers for PBS. Here, the authors found that the mechanical performances of polymer nanocomposites hinged on the amount and the spreading of the SiO2 NPs in the PBS matrix. At low SiO2 incorporation, the mechanical properties were increased; nevertheless, the mechanical properties diminished at the higher silica content due to the SiO2 particles agglomerated in the polymer matrix [155]. The surface of SiO2 can be modified to avoid agglomeration, this perhaps could have allowed the authors to use more SiO2 and harvest even superior mechanical properties. Other than modifying the inherent properties of PBS using 0D (NPs), it has been shown that nanofillers can be used to introduce new properties to PBS and other polymers. This field is particularly maturing in food packaging applications for self-disinfecting packages [156]. Active packaging with antimicrobial properties based on 0D NPs and polymers are made by incorporating NPs with antimicrobial properties into polymeric films. These active packages work due of their superior surface to volume ratio and the elevated reactiveness of the surface of the nano-sized antimicrobial NPs enabling them to inactivate microorganisms more efficiently than their bulk state counterparts [151,157,158]. The most used NPs for this function include silver, gold, iron oxide, zinc oxide (ZnO), titanium dioxide (TiO2), and aluminum oxide (Al2O3) [157,159]. An example of an instance where 0D nanofiller was used to introduce antimicrobial properties onto PBS was in 2016. Here, PBS was composited with ZnO NPs and the resulting films were used to kill E.coli and S. aureus as shown in Table 4 [160]. Other 0D nanoparticles have been incorporated into PBS or other biodegradable polymers to make effective films that deactivate E.coli and S. aureus, such as SiO2 and Ag NPs [161,162].
4.2 One-Dimensional (1D) Nanofillers PBS Composites
A 1D nanomaterial is commonly classified as a linear structure material with a diameter less than 100 nm and one dimension outside the nanoscale set range [163,164]. This class encompasses materials such as nanofibers, nanowires, nanotubes, and nanorods. These types of materials have also been used to improve the properties of PBS [165,166]. This field is interesting as it has opened avenues of using natural biobased nanofibers, particularly nanofibrous cellulose [167–171]. Cellulose nanofibers are not only biobased and biodegradable, but they also have exclusive features such as a high surface area to volume ratio, high tensile strength, and Young’s modulus, and also a low coefficient of thermal expansion [97,172–174]. These nanofibers are usually sourced from plant cell walls which are renewable and cheap [172]. The widespread use of cellulose fibers is limited due to the expensive extraction methods, but their biodegradability and renewability makes it worth talking, discussing, and investigating. The following paragraph summarizes some of the literature on the use of cellulose nanofibers as a filler for PBS. Nanofibrous cellulose has been shown to affect the properties of PBS in different ways such that the PBS polymer nano biocomposites can be used for diverse applications. For instance, a study published by Jiajun and co-workers reported on the synthesis of bimodal porous PBS/cellulose nanofibers composite. They noted that the composite had a well-defined open-pore structure consisting of pores ranging between 11 and 70 µm and open porosity of 95% and good biocompatibility. They used this composite as scaffolds for the growth of cells [175]. On the other hand, Platnieks et al. [166] demonstrated that filling PBS with nano-fibrillated cellulose can improve the biodegradation times of PBS under composting conditions. Also, cellulose nanofibers have been used to improve PBS’s physical properties. Kurokawa et al. [171] showed that the alignment of the cellulose nanofibers in the PBS matrix was important for how the filling affects the mechanical properties of PBS. They found that Young’s moduli of the polymer nano biocomposites were higher than Young’s moduli of the polymer nano biocomposites filled with random cellulose nanofibers [171]. Coleman et al. [98] concluded that compositing PBS with nano-cellulosic fibers had a progressive effect on the thermophysical properties of PBS such that the composites can be suitably used in automotive interiors and food packaging. Nanofibrous cellulose might be the most used filler for PBS polymer nano biocomposites, but it is only one of several that have been investigated. Pinho and co-workers reported using chitosan nanofibers for the enhancement of the mechanical properties and biodegradation kinetics [99]. They cited an increase in the surface area-to-volume ratio and water uptake of the composites for the accelerated biodegradation [171]. In another study, it was shown that nano-lignin fibers increased the UV-barrier capability and photostability of poly(butylene adipate-co-terephthalate) (PBAT) Some of the reviews published on the subject of using carbon nanotubes/fibers as fillers for polymers have interesting titles such as “Small but strong: A review of the mechanical properties of carbon nanotube-polymer composites” and “Big returns from small fibers: A review of polymer/carbon nanotube composites”. These types of titles may seem unusual, but they describe just how imperative these materials are in how they influence the properties of polymers. Since their (carbon nanotubes) discovery in 1991 [101], these materials have spawned massive interest in scientific research because of their impressive properties. Few, if any, materials have been shown to have a combination of excellent mechanical, thermal, and electronic properties, such as carbon nanotubes, making them suitable for various applications [176]. Modifications to the surface of these materials are sometimes necessary to be compatible with the polymer matrix (PBS).
In the area of nanofillers for polymers, the properties of carbon nanofibers (conductivity, thermal conductivity, and mechanical stability) make them perfect options as advanced as nanofillers [176]. The Halpin-Tsai model [177] and the rule of mixtures predict that the toughness of the carbon nanomaterials and polymer nanocomposite increases with an increasing high aspect ratio [176]. There are several reports on how the high aspect ratio of carbon nanomaterials increased PBS’s strength, thermal properties, and electrical conduction. For instance, in a study by Song et al. [101] they imaged a single functionalized-multiwalled carbon nanotube (f-MWCNTs) and found that its diameter ranged between 50–70 nm and its length was several microns. Adding high aspect ratio f-MWCNTs as fillers for PBS enhanced the thermal stability of f-MWCNTs-PBS composite by around 10°C relative to virgin PBS [101]. On the other hand, Zeng et al. [176] demonstrate that at low-level filling of PBS with high aspect ratio non-covalently functionalized CNTs, the electrical conductivity of the resulting composite was found to be six orders of magnitude relative to virgin PBS. This shows that the incorporation of CNTs into polymer matrix (PBS) can influence the mechanical properties of the resulting polymer composite.
4.3 Two-Dimensional (2D) Nanofilers of PBS Composites
2D nanomaterials are characterized as materials whose two dimensions are not in the nanoscale and the other dimension is only a single or few atomic layers thick [178,179]. This group of nanomaterials incorporates materials such as graphene, black phosphorus, graphitic carbon nitride, metal dichalcogenides, and boron nitride, among others that had been exfoliated into few or single layers [180]. These types of materials are being extensively researched in fields such as the vehicle, naval, oil, and metallurgy industries [181]. Some of the reports on the use of 2D nanomaterials as fillers for polymers have shown that the resulting polymer nanocomposites usually have better physical properties such as thermal stability, mechanical, dielectric constant, fire retardant, and gas barrier [31,181–183]. Graphene oxide (GO) [176,184,185], and hexagonal boron nitride [185–187] are the most investigated 2-dimensional materials as polymer fillers and their benefits are there to be seen. However, the anticipated enhancements caused by compositing polymers with 2D nanofillers are hindered by the lack of uniformity in how they are distributed in the polymer matrix and the strong interface shear stress between the polymer matrix and the filler [181]. In the case of the interface shear stress, in an instance where the interface is stronger than the host polymer, the polymer matrix will not hold and the bonds at the end of the filler may break and spread along the surface. This necessitates that the surfaces of these 2D nanofillers be engineered such that they can interact with the relevant polymer matrix. Typically, the various kinds of interactions that occur between 2D nanofillers and polymer matrixes are as follows (a) covalent/chemical bonding between the polymer matrix and the 2D nanofillers, (b) non-covalent interactions/Van der Waals force, which occurs between the basal plane of the 2D nanofiller and the polymer matrix, and (c) polymer blending, which refers to the weak π-π interactions that exist between the 2D filler and the polymer matrix. This weak π-π interactions was demonstrated in a study reported by Wang et al. who blended graphene oxide and PBS and observed that there were strong interfacial interactions between graphene and the PBS matrix. These interfacial interactions translated into strong tensile properties relative to virgin PBS but compromised the crystallization of PBS [188]. Zainal Abidin et al. [189] reported that octadecylamine functionalized graphene oxide blended with PBS had superior tensile strength and Young’s modulus. This was attributed to the increased interactions between the two hydrophobic graphitic carbon and low-polar PBS.
4.4 Cellulose Modifier of PBS Composites
The most prevalent renewable polymer material in nature is cellulose, which is a biodegradable and hydrophilic organic compound. Cellulose is a polysaccharide consisting of a linear chain of several hundred to thousands of β(1→4) linked D-glucose units [189–193]. It is an inexpensive material that is frequently thrown away as garbage and contains residue from the farming and forestry sectors. Cellulose structure provides renewability attributes, low density, highly crystalline and amorphous areas, high specific strength, stiffness, and non-toxicity to humans and the environment [194–198]. For the development of polymer composites, cellulose fillers from various sources, such as lignocellulosic fibers, microcrystalline cellulose, and nanocellulose, are generally utilized [199]. Moreover, the advantage and adoption of natural cellulose-reinforced PBS composite material can enable the polymer industry to design biodegradable and sustainable polymer composites to end current plastic pollution across the world. Thus, this will solve the conventional plastic pollution and landfill issues and provide more sustainable polymer composites. Increased mechanical and/or dynamic mechanical properties have been reported in general investigations using MCC filler to develop MMC-filled polymer composites. Nevertheless, durability and performance often decrease over 30 wt% MMC filler loading. The high strength and stiffness of cellulose fibers are attributed to the numerous hydroxyl groups in cellulose molecules, which form hydrogen-bond networks [200]. Unfortunately, the polar nature of cellulose results in weak interactions with a non-polar polymer matrix, causing agglomerations that restrict potential composite improvements, hence cellulose modification is important prior compounding [201]. For example, He et al. [202] reported that the incorporation of modified cellulose into PBS composites gradually improved tensile modulus with increasing modified cellulose, whereas the elongation at fracture decreased. However, 3 wt% modified cellulose loading was noted to be the optimum, thus low cellulose loading is critical for effective property improvement [203].
4.5 Effect of Morphology Structure of 0D, 1D, and 2D, and Cellulose Fillers on PBS
Fullerenes are the first nano-carbonaceous materials to be discovered and reported in 1985 [204,205]. Moreover, other 0D carbonaceous materials, such as carbon nanodots are still the least used nano filler to improve PBS-based materials. Table 5 summarizes the critical synthesis and effects of carbonaceous nanomaterial on the PBS system. One critical study found that adding CNTs into the PBS matrix decreases PBS nucleation due to the better dispersion of CNTs compared to their counterparts, such as fullerenes [206]. Although CNTs outperformed fullerenes, further research is required to explore other nanofillers with morphology configurations of 0D carbonaceous materials like carbon dots and carbon nano onions. The application of nanofillers such as single-walled carbon nanotubes (SWCNTs) has seldom been reported as PBS fillers. This scarcity is probably because of the technical complexities and cost of producing SWCNTs. In one study that focused on improving PBS with SWCNTs functionalized with 3-aminopropyltriethoxysilane, the authors reported that the crystallization rate for filled PBS was an order of magnitude higher than that of virgin PBS. The work done on 1D MWCNTs and 2D graphene as fillers for PBS is more popular. Many of the examples reported in the literature, including the ones summarized in Table 5, the MWCNTs and graphene used require prior functionalization, and the cheapest way is to acid treat the carbonaceous fillers. At the same time, other authors opted to use organic molecules. Advances in the synthesis of MWCNTs have yielded promising results regarding the costs associated with producing them. This means that the exciting improvements observed when compounding PBS with MWCNTs are feasible. Several studies have reported that using carbon nanomaterials as fillers for PBS opted to use blending methods for synthesizing these composites. This is probably because it is cheaper than forming stronger covalent bonds between the matrix and the filler. Overall, using carbon-based nanomaterials to reinforce the PBS composites properties is promising. It is well-known that the durability and performance of the cellulose polymer composite material, which is crucial for cellulose filled-PBS efficiency depend on the adhesion, dispersion of the filler, and filler-matrix interaction [207,208]. Hence, it is essential to modify cellulose fibers before compounding [207]. However, cellulose is generally poorly dispersed in non-polar polymer matrices since it is hydrophilic. In this rationale, a method for the surface modification of cellulose is required to improve their dispersion in the polymer matrix. This method includes an esterification reaction, which can improve polymer and cellulose components interface compatibility to obtain high exploitation and properties of the final composite material. Based on this principle, additives can be used to improve the interfacial adhesion through the compatibilization process and efficient stress transfer across the phase morphology of the polymer matrix and cellulose filler.
Table 5 clearly describes how using carbonaceous nanomaterials such as fullerenes, CNTs, and graphene as nanofillers to PBS yields materials with much superior properties. The literature covered suggests that there is a limit to the concentration of fillers that can be used before the advantages observed begin to diminish. This observation is commonly attributed to high amounts of carbonaceous nanofillers, which tend to agglomerate and result in poor performance. Furthermore, there seems to be no preferable method of synthesis over the others that is better suited for incorporating carbonaceous nanofillers into PBS as all the methods covered in Table 5 showed that they are all advantageous. This is the case with the different types of interactions between the PBS host and the nanofillers.
5 Applications of PBS Copolymers and Its Composites
5.1 PBS Copolymer Composites for Food Packaging Applications
Among numerous biobased polymers that have been exploited to advance biodegradable food packaging materials, PBS has been regarded as one of the appropriate materials. However, issues associated with poor mechanical, thermal, and barrier characteristics are still challenging. Reinforcement with different materials has been established as a common method to improve PBS biopolymer’s mechanical and barrier properties. A multiphase bio-composite material comprising two or more constituents may enhance both PBS mechanical and barrier properties. The multiphase bio-composite material could also offer other food packaging requirements such as antimicrobial agents, oxygen scavengers, etc. Metal-reinforced PBS packaging films are commonly used in the food industry for antimicrobial packaging and to prolong the shelf life [146,217,218]. PBS can be processed via different melt extrusion methods to produce packaging films. To name a few melt extrusion methods, blown films, fiber spinning, blow, and injection molding give PBS the advantage of replacing polyolefin as anticipated [168]. PBS mechanical strength and microbial corrosion shortcomings have been resolved using ZnO nanoparticles (NPs) filler [219]. Incorporating ZnO NPs on PBS provides antimicrobial activity and inhibits unpleasant odors that may result from organic volatiles [220,221]. When investigating the antibacterial activity and properties of PBS-ZnO composite films, it was discovered that the composite was stiffer due to reinforcement effect from ZnO and only 6 wt% ZnO NPs was required to prevent the Escherichia coli and the Staphylococcus eareus growths. Upon performing the release studies, Zn2+ migrated over 15 days, and significant migration was witnessed when acetic acid was used as a food simulant [168]. TiO2 was incorporated into poly(ethylene terephthalate) PET and PBS blends for improved thermal, mechanical, and antibacterial properties [222]. Each component in the composite material delivered its unique property. For example, the presence of PET provided high mechanical properties, whereas TiO2 NPs increased the thermal stability of PET/PBS fusions. For antibacterial activity, PET/PBS blend film with TiO2 NPs presented more activity against both E.coli and S. aureus than the one containing ZnO NPs [222]. Degradable biobased polymers have also been incorporated into PBS packaging films to fine-tune their physical and mechanical properties. In PLA/PBS blend prepared by a twin-screw extruder, the rheological results displayed miscibility between the two polymers and PLA brittleness was reduced by PBS, making the composite a contender for packaging applications [223]. Functionalized chitosan and dicumyl peroxide were also incorporated into PLA/PBS blends through a reactive extrusion blend to improve tensile strength and % elongation break [224]. The processed biocomposite offered improved hydrophobicity and UV-blocking proficiency, which induced the probability for the utilization in the packing of UV sensitive materials [224]. Hydrotalcite-type anionic clays (HTs) is widely used as a food compatible filler. The HT hybrid modified with antibacterial biomolecules were integrated with PBS via in situ polymerization [225]. The compatible MgAl hydrotalcite hosted molecules and a natural non-toxic aromatic hydroxy acid 3-(4-hydroxyphenyl)propionic acid (HPP) [226]. Intercalation of HT hybrid platelets were found to be well dispersed onto PBS polymer while giving chain extension influence. Additionally, these molecules preserved the pristine antibacterial activity when accommodated within HT and in the resulting PBS nanocomposite [226]. The nanocomposite showed chain extension effects and antibacterial activity, specifically for inhibition of 90%–97% of E. coli. Overall, the food packaging material should be in a position of providing appropriate physicochemical conditions to obtain satisfactory shelf life while maintaining food quality and safety.
5.2 PBS Copolymer Composites for Biomedical Applications
Aliphatic biodegradable polymers are steadily replacing other materials such as metals and ceramics for use in biomedical applications due to the versatility that these polymeric materials offer [226]. PBS is well-known to be a biocompatible material as it does not cause cytotoxic effects when degrading [214,227]. In brief, biodegradable polymers such as PBS have demonstrated potential for use in various applications upon polymer blending and incorporation of fillers [215,228]. Moreover, PBS also compares well with widely used biomedical polyesters such as PLA and PGA in terms of processability and the required mechanical properties to act as scaffold material [214]. Scaffolds must also stimulate cell adhesion and proliferation for tissue regeneration. These characteristics are influenced by the material used, the scaffolds’ internal structure, and the scaffolds’ surface properties [229]. Surface properties, including wettability, hydrophilicity, and surface roughness, are key in determining the effectiveness of cell adhesion and other biological processes on the scaffold surfaces [230]. Adjustments to biocompatibility, internal structures, and surface properties can be achieved via selection or tailoring of the preparation techniques used, blending/copolymerization with other compounds (synthetic and/or natural), or via surface treatment to enhance cell adhesion [231]. Various studies have been performed on the use of structures prepared from PBS or copolymers of PBS with other synthetic or natural biodegradable polymers for applications ranging from scaffolds for bone repair [232–235], controlled release capsules and scaffolds [236,237] and repair of soft tissue damage [238–242]. Numerous preparation methods exist to prepare the 3D structures required for different applications, including thin film formation [157,243], electrospinning [230,234,244], extrusion [245], and salt leaching [233]. PBS-based micro- and nano-particulate structures were prepared via emulsion solvent evaporation techniques [108,237], or via nanoprecipitation [246]. PBS and copolymerized PBS particles loaded with different drugs have been prepared for the treatment of Parkinson’s Disease, arthritis as well as cancer therapy [108,236,237,246,247]. The hydrophilicity of PBS scaffold surfaces was improved via functionalization/capping with phosphorylcholine for application in devices where contact with blood is made [130]. Fibrous-type scaffolds are known to encourage cell adhesion and proliferation due to the availability of large surface areas and connectivity between individual fibres [214], with specific fibre orientation of electrospun PBS and PBS-diglycolate scaffolds shown to impact the degree of cell differentiation [234]. Various surface modification techniques, including sodium hydroxide etching, ultraviolet radiation, and grafting, were utilized to alter the properties of knitted fibrous PBS scaffolds, and improved fibroblast cell adhesion was achieved due to increased surface roughness and hydrophilicity of the scaffolds [248]. The porosity of electrospun nano biocomposites of PBS and cellulose nanocrystals was altered via a supercritical CO2 foaming process and retained biocompatibility with fibroblast cells in vitro [185,244]. Blending with natural materials including hydroxyapatite and chitosan is often performed to improve the bio-affinity of pure PBS scaffolds [238,239,245]. Cellulose nanocrystals [244], lignin [249] and thrombin [241] have also been blended with PBS for improved cell proliferation and adhesion as compared to pure PBS scaffolds. Commercially available products based on biodegradable polymer technology are largely confined to soft tissue engineering (resorbable sutures) and bioresorbable implants mainly synthesized from PLA, as produced by companies such as Conmed, DePuy, Arthrex, Linvatec and Inovasive Devices [226]. There is thus an ample opportunity for the development of commercial PBS-based biomedical products that can be tailored via a range of synthesis techniques and copolymerization or composite formation with other compounds for improved mechanical or biochemical characteristics.
5.3 Flame Retardant Applications
PBS occupies 4.3% of the global bioplastics market, with applications in packaging, agriculture, automotive, transportation, building and construction, electrical/electronics, consumer products, furniture, and consumer products. However, its application in transportation, electrical, construction, and packaging is limited primarily due to its flammability; it is auto-extinguishable around ambient temperatures [255,256,259]. In recent years, there has been a growing interest in enhancing the flame-retardant properties of PBS. This is mainly owing to increased demand for biodegradable and biobased polymers to address societal challenges such as climate change and resource depletion [253,257,258,265]. The flame retardancy potential of biobased materials like PBS can be enhanced by the addition of intumescent flame retardants (IFRs) components [256]. Studies that investigated the flame retardancy potential of PBS-IFR composites, that have been modified with reinforcement or synergist agents, are listed in Table 6.
Literature suggests that the compatibility of IFRs and polymers can be enhanced using reinforcement components including graphene, clay-based agents such as organically modified montmorillonite (OMMT) and urea intercalated kaolinite and nanomaterials such as halloysite and sepiolite, and in addition these materials can offer a synergistic effect by also enhancing mechanical properties [253,257,258]. Some of the literature data in this section of the review suggest alternatives to the use of halogen-based IFRs in light of environmental concerns, thus showing potential for completely environmentally friendly PBS flame retardants. This includes using inorganic hydroxides as replacements to halogen-containing IFRs, with magnesium hydroxides highly favorable because they are abundant in nature, low cost, and have a relatively high decomposition temperature [252]. Recently, the potential of entirely biobased IFR PBS composite systems has been explored by replacing the phosphorous and nitrogen-based flame-retardant components with materials derived from renewable sources [259,260]. There has been an increased interest in developing wood-plastic composites (WPCs) when considering that the individual benefits of wood and polymers like PBS can be maximized in the interfaced composites to address environmental concerns [261]. Studies on PBS-WPCs exploring halogen-free IFRs, including hypophosphites (AHP and CaHP) and APP and calcium carbonate for reinforcement as well as the synergistic effect of magnesium hydroxide sulfate whisker (MHSH) on PBS IFRs have been investigated [261–263]. The PBS WPCs were found to be highly effective as flame retardants. A novel multi-layered PBS composite with a dual role of providing both electromagnetic interference (EMI) shielding, and flame retarding properties has been explored [264]. Conducting layers were prepared from a PBS matrix loaded with carbon nanotubes (CNTs) while the flame-retardant layers comprised of polyurethane (TPU) filled with halogen-free IFRs and CNTs. These enhancements of flame-retardant properties of PBS to address the challenges associated with the auto-extinguish ability of PBS will undoubtedly open a window of opportunity for its use in several applications such as electronics, automotive and transportation.
5.4 Agricultural PBS Composite Applications
The global use of plastics in the agricultural sector, which provides multiple benefits for food production, packaging, and others, is significantly growing by 6.5% from 2018 to 2026 [10,11]. Disposal options for agricultural plastics are limited and threaten our ecosystem’s sustainability due to the persistency of residual plastic residues in terrestrial and aquatic environments [266–270]. A sustainable strategy to overcome these risks is using biodegradable technology made of biopolymers in agricultural sectors that contributes to significant savings as landfill removal costs are eliminated and the environmental plastic pollution issues are reduced. The use of biodegradable polymers for agricultural applications is mainly focused on mulch films and controlled release of fertilizer products [271–275]. The agricultural mulch films are applied onto the agricultural soil surface to ensure stable ground temperatures and reduction, or prevention of weed growth, hence, to sustain soil moisture and reduce the runoff of fertilizers [271,276–278]. Controlled and slow-release fertilizers assist in maintaining necessary levels of fertilizer in soil to promote efficient crop growth and reduce negative environmental impacts due to overuse and runoff of excess fertilizer. To address drawbacks associated with the disposal of conventional plastic mulches and controlled release fertilizers, the development of biodegradable alternatives has gained considerable attention [266,279]. Ultimately, for a typical biodegradable plastic, the polymer must undergo molar mass reduction and biological conversion to carbon dioxide and/or methane, and water [266,280–283]. Both synthetic and biobased PBS are used in agricultural mulch film [266,284–286]. Examples of different types of materials investigated for agricultural applications are shown in Table 7.
A novel PBS/abamectin-loaded microcapsule composite film was developed as a potential mulch film with pesticide-controlled release properties [285]. According to the study, a slower and more uniform release of the abamectin from the composite was observed in comparison to the microcapsules alone, and to the blend of PBS and abamectin. Fig. 1 shows the basic control release fertilizer mechanism, which is described by three different phases: lag phase, constant release phase, and decay phase [289].
Figure 1: Mechanism of controlled release. (a) controlled release fertilizer granules. (b) A lag phase. (c) The constant release phase. (d) The decay phase (adapted from Lawrencia et al. [289])
In a lag phase, water molecules penetrate the coating through cracks to the core to dissolve the small amount of fertilizer (Urea, for example) or to establish a steady state. In the constant release phase, water intake continues until the critical water saturation and the osmotic pressure in the core builds up, which then allows the fertilizer to be released gradually through the cracks in the coating layer. Finally, in the decay phase, the concentration gradient and release rate decrease due to most of the fertilizer being dissolved and released [289]. Controlled release fertilizers have been prepared via simple coating of granules, solution blending, and melt mixing via extrusion [287,288,290,291], or membrane emulsification [122]. Copolymers of PBS and other polyesters or natural compounds are used as matrices to fine-tune characteristics such as crystallinity and morphology that affect the release rates of the encased fertilizer compounds [288]. These are important critical factors of the matrix composite to be considered for the controlled release as shown when red pepper and tomato seeds were compromised when PBS and PLA powder were sowed and cultivated in soil [292]. It was discovered that the PBS concentration depressed the growth rate even at lower concentrations for over 80 days. This was attributed to PBS Mw diminishing at a fast rate, thus producing toxic degradation fragments such as SA and 1,4-BDO. In controlling PBS concentration for fertilizer production, grinded lemon basil natural plant was melt-blended with PBS alongside ammonium sulphate content to make a fertilizer composite film [286]. Moisture sorption was significantly enhanced with the increase in lemon basil content. According to soil burial examination, biodegradation of PBS matrix was accelerated by lemon basil because of moisture and microorganism from conditioned soil compared to pristine PBS film [286].
5.5 Biodegradability of PBS and Its Composites
In recent years, there has been a growing interest in developing environmentally friendly materials for addressing the global plastic waste disposal issues. Approximately more than 55% of consumption from the global plastic production, i.e., 359 million tons (Mt), are being widely used in various single-use and short-term applications such as packaging, agriculture, biomedical, electronic, and others [293–297]. Post-consumer plastic waste contributes to severe environmental pollution due to its recalcitrant in nature and harmful effects on terrestrial and aquatic habitats. To overcome the current global plastic pollution, many countries have outlawed banning the single-use plasticsand finding a sustainable solution by moving towards using renewable biobased materials with an emphasis on the adoption of circular economy [298,299]. Biodegradable and compostable polymers offer an alternative to these non-biodegradable conventional plastics since their bioderived undergo complete biodegradation after the end-of-life in compost, landfill, and other natural environmental conditions, in a defined time frame and leaving less or no toxic residues [300–303]. In addition, biodegradable polymeric materials support nature conservation to reduce carbon footprints and greenhouse gas emissions [304–308]. Among various types of biodegradable polymers, PBS based biopolymer and its biocomposites provide unique properties in terms of performance with added advantages of biodegradable and compostability to replace non-biodegradable conventional plastics such as polyethylene (PE), polypropylene (PP) and polystyrene (PS) [309–313]. Because of the growing demand in PBS based composite materials, its effective biodegradability has also become a critical driving factor of its research endeavors. The breakdown of any complex biochemical substance into simpler compound fractions by the action of microorganisms, including bacteria and fungi is referred to as biodegradability [314–316]. The factors that play a significant role in the breakdown of polymers include mobility, molecular weight, crystalline quality, additives or fillers, and different types of functional groups. During the breakdown process of the polymer composites, mineralization takes place where the polymers are broken down into monomers, which further break into water, methane, and carbon dioxide as illustrated schematically in Fig. 2 [300]. The polymer degradation process can occur in different ways, including enzymatic breakdown. In enzymatic breakdown, the substrate is broken into simpler molecules such as monomers, dimers, and oligomers by enzymes secreted by microorganisms. Microorganisms usually secrete enzymes such as proteinase k, lipase, and dehydrogenase, which can break down both synthetic and natural polymers [101,317–320]. As a result, the extracellular enzyme secreted by microorganisms penetrates through the plastic and degrades it into water-soluble species. The breakdown of PBS is usually caused by 39 strains of class proteobacteria and firmicute bacteria such as Pseudomonas chlororaphis [317], Amycolatopsis sp. HT-6 [321], Micrcobispora rosea [321], Schlegelella thermodepolymerans [321], Excellospora japonica [322], E. viridilutea [322] and Caenibacterium thermophilum [322]. A microorganism known as Microbispora roea has been demonstrated to possess the ability to break down the PBS polymer to up to 50% in eight days [323].
Figure 2: Schematic representation of polymer biodegradation. (cited from Muniyasamy et al. [300])
In the study by Hu et al. [324], it has been shown that after 21 days 80% (w/w) of PBS film could be degraded by Fusarium solani compared to Pseudozyma antarctica where the degradation was limited to approximately 60% (w/w) in 42 days. Besides, the cutinase synthesized from A. oryzae has also been reported to show effective PBS degradation activity within 6 h at 80 mg/mL concentration. In the attempts to reduce the degradation time, it has been reported that enzymes react more efficiently with water soluble polymers compared to insoluble [324,325]. Also, the degradation rate is mainly controlled by the polymers’ physical and chemical characteristics as well as the interaction of specific enzymes mediated reactions, which can include an efficient pretreatment process. Initially, the non-crystalline part of the polymer degrades; later, with the increase in time crystalline parts also degrade away. Hence, it is important to understand the degradation mechanism [325–329]. Further studies by Platnieks et al. [166] demonstrated that filling PBS with nano-fibrillated cellulose NFC/MCC reduced the time required for the biodegradation of neat PBS, which was 75 days under compositing conditions to decomposition rate up to 60 days (Fig. 3). These studies show the significant impact of tuning the biodegradability characteristics and the mechanical properties of PBS blended composites as an integrated approach for specific intended applications.
Figure 3: (A) Percentage weight loss (B) Pictures of (PBS and PBS/cellulose composites films during biodegradation studies in soil burial test conducted in composting conditions (adapted from Platnieks et al. [166])
Scheme 1: Synthesis of PBS using renewable material such as glucose
Scheme 2: Synthesis route of PBS via transesterification and polycondensation
Scheme 3: Synthesis of cross-linking polymer of PBS using scandium triflates
Scheme 4: Schematic synthesis of PBS followed by transesterification and polycondensation process in the presence of multi-catalytic system
Scheme 5: Schematic synthesis of PBS followed by atmospheric condensation and lipase catalyzed polycondensation in presence of Novo-435 catalytic system
Scheme 6: Synthesis of various aliphatic copolymers of PBS
Table 8 summarizes some of the achieved results on PBS and its biocomposite materials biodegradability in soil and compost conditions. The PBS composite made from natural polymers such as soymeal, corn gluten meal, and switch grass natural fibres and starch show an increased rate of biodegradation when compared to neat PBS bioplastic [325]. Moreover, when comparing the different natural environments, composting environmental conditions provide high rate of biodegradability for both PBS and its biocomposites as compared to soil and other natural environmental conditions [325,330–332]. Similarly, the different study of polybutylene succinate co-adipate (PBSA) blended with starch composite films exposed to aerobic composting conditions at 25°C showed 96% degradation within 45 days by monitoring the mineralization amount of the CO2 emissions [333]. Ratto et al. [333] studied PBSA/starch films in soil conditions and monitored the mineralization amount of CO2 emissions by varying the concentration of starch content in PBSA blends. The CO2 emissions results showed that the PBSA-based sample containing 15% starch content to undergo effective biodegradation rates reaching above 80% within 90 days. In contrast, the neat PBSA showed slow biodegradation rates to reach a similar 80% amount only after 365 days in natural soil conditions [333]. Overall, the end-of-life options of PBS or PBSA biocomposites provide sustainable biodegradation in a short time and enrich carbon nutrients in the soil as compared to the neat polymer material. This factor of controlling the biodegradation rates of PBS by interfacing with suitable biocomposites not only improves its structural required properties for specific applications but also for end-life biodegradation. The reasonable biodegradation rate of PBS composites provides ample opportunity for further developments in research on PBS biocomposite materials. The research should not be limited to the biodegradation rate or mechanism (examination of end-of-life processes) but should also focus on the types, sizes, and concentrations of biodegradable plastics [334,335]. This approach will pave the way for using biodegradable polymers instead of conventional plastics [336].
The continuing global climate change and gradual depletion of fossil resources are the interplay factors fostering the new developments of alternative renewable carbon materials to produce chemicals and polymers in the modern chemical industry. The shift from fossil-derived chemicals and polymers to biomass-derived ones has gained momentous interest globally due to public pressure on governments and private sectors to innovate sustainable and environmentally friendly solutions. Another aspect driving the green and circular bioeconomy is the increasing demand in bioplastics, which its growth has positively been predicted towards expansion in the diversified biobased polymers derived products with biodegradable properties. Polybutylene succinate (PBS) and its copolymers have emerged as promising biobased degradable and biodegradable functional polymer materials with diverse applications. In the work reviewed herein, the progress in the production of biobased succinic acid, monomer to PBS, is one key area that has been shown to achieve industrial implementation success. In contrast, biobased production of its other counterpart monomer 1,4-butanediol (1,4-BDO), has not been commercially demonstrated. This presents an opportunity for future research to focus on establishing commercial-scale production of 1,4-BDO from succinic acid or other biobased chemicals, which will eventually make the PBS synthesis fully biobased. On the synthesis of neat PBS, the challenge identified is to achieve comprehensively high molecular weight materials with improved chemical, mechanical, and thermal structure properties for specific applications. With the diverse applications anticipated for PBS in biomedical, food packaging and other packaging sectors, agricultural, electronic, there is a need for further studies in the synthesis of PBS with sector-applications tailored structural properties. The application such PBS composite for drug delivery will require the synthesis of PBS without trace amounts of metals, thus the current methodologies using the metal complexes as catalyst is posing the limitations to obtain PBS free of metal contaminants. We believe that the use of solid heterogeneous catalysts and enzymatic catalysis or biocatalysis, whose applications in PBS synthesis are limited, could provide some alternative solutions for synthesizing PBS free of metal traces. The incorporations of inorganic and organic fillers in the PBS matrix structure have demonstrated significant improvements in the chemical, thermal, and mechanical properties of various designed PBS bio-nanocomposites. We envisage that further developments in methodologies to reinforce the chemical and mechanical stability of PBS composite materials with their biodegradability properties maintained could open new avenues for their applications. The initial data results produced on the application of the PBS-based composites have shown that the performance depends on the design and controlled synthesis of specific application-oriented tailored structure properties. Moreover, this could be achieved by strategies such as multiblock PBS copolymers and inorganic-organic PBS reinforcement. The organic modification of PBS using biobased-derived chemicals is also becoming attractive in preparing reinforced PBS composites and its copolymer materials. The biodegradation studies of the PBS and its composites still require further investigations to develop suitable conditions for anaerobic and aerobic degradation to mimic the ideal environmental conditions (compost, landfill, soil, and aqueous media). More importantly, the success of developing a naturally assisted biodegradation process of PBS waste derivatives will be beneficial to society and the environment.
Acknowledgement: None.
Funding Statement: The authors received no specific funding for this study.
Author Contributions: Peter Ramashadi Makgwane: Conceptualization, Validation, Writing—original draft, Writing—review & editing. Lerato Hlekelele: Investigation, Validation, Writing—original draft, Writing—review & editing. Zamani Cele: Investigation, Validation, Writing—original draft, Writing—review & editing. Andri Swanepoel: Investigation, Validation, Writing—original draft, Writing—review & editing. Venkata Satyanarayana Sypu: Investigation, Validation, Writing—original draft, Writing—review & editing. Lindani Mdlalose: Investigation, Validation, Writing—original draft, Writing—review & editing. Saloshnee Naidoo: Investigation, Validation, Writing—original draft, Writing—review & editing. Sudhakar Muniyasamy: Investigation, Validation, Writing—original draft, Writing—review & editing. Arjun Maity: Validation, Writing—review & editing. Mohammed Balogun: Validation, Writing—review & editing, Project administration. Orebotse Joseph Botlhoko: Design and implementation of the major revision and conceived the review of biobased materials research. All authors reviewed the results and approved the final version of the manuscript.
Availability of Data and Materials: The authors confirm that the data supporting the findings of this study are available within the article.
Ethics Approval: Not applicable.
Conflicts of Interest: The authors declare no conflicts of interest to report regarding the present study.
References
1. Schwager P, Decker N, Kaltenegger I. Exploring green chemistry, sustainable chemistry and innovative business models such as chemical leasing in the context of international policy discussions. Curr Opin Green Sustain Chem. 2016;1:18–21. doi:10.1016/j.cogsc.2016.07.005. [Google Scholar] [CrossRef]
2. Yadav VG, Yadav GD, Patankar SC. The production of fuels and chemicals in the new world: critical analysis of the choice between crude oil and biomass vis-a-vis sustainability and the environment. Clean Technol Environ Policy. 2020;22(9):1757–74. doi:10.1007/s10098-020-01945-5. [Google Scholar] [PubMed] [CrossRef]
3. Priya, Deora PS, Verma Y, Muhal RA, Goswami C, Singh T. Biofuels: an alternative to conventional fuel and energy source. Mater Today: Proc. 2022;48:1178–84. doi:10.1016/j.matpr.2021.08.227. [Google Scholar] [CrossRef]
4. Mandree P, Thopil GA, Ramchuran S. Potential opportunities to convert waste to bio-based chemicals at an industrial scale in South Africa. Fermentation. 2023;9(10):908. doi:10.3390/fermentation9100908. [Google Scholar] [CrossRef]
5. Qasim U, Osman AI, Al-Muhtaseb AaH, Farrell C, Al-Abri M, Ali M, et al. Renewable cellulosic nanocomposites for food packaging to avoid fossil fuel plastic pollution: a review. Environ Chem Lett. 2020;19(1):613–41. doi:10.1007/s10311-020-01090-x. [Google Scholar] [CrossRef]
6. Dessbesell L, Paleologou M, Leitch M, Pulkki R, Xu C. Global lignin supply overview and kraft lignin potential as an alternative for petroleum-based polymers. Renew Sustain Energ Rev. 2020;123:109768. doi:10.1016/j.rser.2020.109768. [Google Scholar] [CrossRef]
7. Appiah ES, Dzikunu P, Mahadeen N, Ampong DN, Mensah-Darkwa K, Kumar A, et al. Biopolymers-derived materials for supercapacitors: recent trends, challenges, and future prospects. Molecules. 2022;27(19):6556. doi:10.3390/molecules27196556. [Google Scholar] [PubMed] [CrossRef]
8. Raza S, Zhang J, Ali I, Li X, Liu C. Recent trends in the development of biomass-based polymers from renewable resources and their environmental applications. J Taiwan Inst Chem Eng. 2020;115:293–303. doi:10.1016/j.jtice.2020.10.013. [Google Scholar] [CrossRef]
9. Yadav M, Goel G, Hatton FL, Bhagat M, Mehta SK, Mishra RK, et al. A review on biomass-derived materials and their applications as corrosion inhibitors, catalysts, food and drug delivery agents. Current Res Green Sustain Chem. 2021;4:100153. doi:10.1016/j.crgsc.2021.100153. [Google Scholar] [CrossRef]
10. Europeanbioplastics. Application for bioplastics. 2023 [cite 2025 Jan 23]. Available from: https://www.european-bioplastics.org/market/applications-sectors/. [Google Scholar]
11. Europeanbioplastics. Bioplastics market development update. [cite 2025 Jan 23]. Available from: https://www.european-bioplastics.org/market/. [Google Scholar]
12. Aliotta L, Seggiani M, Lazzeri A, Gigante V, Cinelli P. A brief review of poly (butylene succinate) (PBS) and its main copolymers: synthesis, blends, composites, biodegradability, and applications. Polymers. 2022;14(4):844. doi:10.3390/polym14040844. [Google Scholar] [PubMed] [CrossRef]
13. Singh N, Ogunseitan OA, Wong MH, Tang Y. Sustainable materials alternative to petrochemical plastics pollution: a review analysis. Sustain Horizons. 2022;2:100016. doi:10.1016/j.horiz.2022.100016. [Google Scholar] [CrossRef]
14. Sid S, Mor RS, Kishore A, Sharanagat VS. Bio-sourced polymers as alternatives to conventional food packaging materials: a review. Trends Food Sci Technol. 2021;115:87–104. doi:10.1016/j.tifs.2021.06.026. [Google Scholar] [CrossRef]
15. Atiwesh G, Mikhael A, Parrish CC, Banoub J, Le TT. Environmental impact of bioplastic use: a review. Heliyon. 2021;7(9):e07918. doi:10.1016/j.heliyon.2021.e07918. [Google Scholar] [PubMed] [CrossRef]
16. Sinha S. An overview of biopolymer-derived packaging material. Polym Renew Resour. 2024;15(2):193–209. doi:10.1177/20412479241226884. [Google Scholar] [CrossRef]
17. Teixeira SC, Gomes NO, Oliveira TVd, Fortes-Da-Silva P, Soares NdFF, Raymundo-Pereira PA. Review and perspectives of sustainable, biodegradable, eco-friendly and flexible electronic devices and (bio)sensors. Biosens Bioelectr: X. 2023;14:100371. doi:10.1016/j.biosx.2023.100371. [Google Scholar] [CrossRef]
18. Kasprzak D, Mayorga-Martinez CC, Pumera M. Sustainable and flexible energy storage devices: a review. Energy Fuels. 2022;37(1):74–97. doi:10.1021/acs.energyfuels.2c03217. [Google Scholar] [CrossRef]
19. Taghavi N, Udugama IA, Zhuang WQ, Baroutian S. Challenges in biodegradation of non-degradable thermoplastic waste: from environmental impact to operational readiness. Biotechnol Adv. 2021;49:107731. doi:10.1016/j.biotechadv.2021.107731. [Google Scholar] [PubMed] [CrossRef]
20. Satti SM, Shah AA. Polyester-based biodegradable plastics: an approach towards sustainable development. Lett Appl Microbiol. 2020;70(6):413–30. doi:10.1111/lam.13287. [Google Scholar] [PubMed] [CrossRef]
21. Acharjee SA, Bharali P, Gogoi B, Sorhie V, Walling B, et al. PHA-based bioplastic: a potential alternative to address microplastic pollution. Water Air Soil Pollut. 2023;234(1):21. doi:10.1007/s11270-022-06029-2. [Google Scholar] [PubMed] [CrossRef]
22. Kumari S, Rao A, Kaur M, Dhania G. Petroleum-based plastics versus bio-based plastics: a review. Nature Environ Pollut Technol. 2023;22(3):1111–24. doi:10.46488/NEPT.2023.v22i03.003. [Google Scholar] [CrossRef]
23. Atta OM, Manan S, Shahzad A, Ul-Islam M, Ullah MW, Yang G. Biobased materials for active food packaging: a review. Food Hydrocoll. 2022;125:107419. doi:10.1016/j.foodhyd.2021.107419. [Google Scholar] [CrossRef]
24. Shen M, Song B, Zeng G, Zhang Y, Huang W, Wen X, et al. Are biodegradable plastics a promising solution to solve the global plastic pollution? Environ Pollut. 2020;263(Pt A):114469. doi:10.1016/j.envpol.2020.114469. [Google Scholar] [PubMed] [CrossRef]
25. Ghosh K, Jones BH. Roadmap to biodegradable plastics—current state and research needs. ACS Sustain Chem Eng. 2021;9(18):6170–87. doi:10.1021/acssuschemeng.1c00801. [Google Scholar] [CrossRef]
26. Moshood TD, Nawanir G, Mahmud F, Mohamad F, Ahmad MH, AbdulGhani A, et al. Green product innovation: a means towards achieving global sustainable product within biodegradable plastic industry. J Clean Prod. 2022;363:132506. doi:10.1016/j.jclepro.2022.132506. [Google Scholar] [CrossRef]
27. Adeleye AT, Odoh CK, Enudi OC, Banjoko OO, Osiboye OO, Toluwalope Odediran E, et al. Sustainable synthesis and applications of polyhydroxyalkanoates (PHAs) from biomass. Process Biochem. 2020;96:174–93. doi:10.1016/j.procbio.2020.05.032. [Google Scholar] [CrossRef]
28. Sirohi R, Prakash Pandey J, Kumar Gaur V, Gnansounou E, Sindhu R. Critical overview of biomass feedstocks as sustainable substrates for the production of polyhydroxybutyrate (PHB). Bioresour Technol. 2020;311:123536. doi:10.1016/j.biortech.2020.123536. [Google Scholar] [PubMed] [CrossRef]
29. McAdam B, Brennan Fournet M, McDonald P, Mojicevic M. Production of polyhydroxybutyrate (PHB) and factors impacting its chemical and mechanical characteristics. Polymers. 2020;12(12):2908. doi:10.3390/polym12122908. [Google Scholar] [PubMed] [CrossRef]
30. Bajaj I, Singhal R. Poly (glutamic acid)—an emerging biopolymer of commercial interest. Bioresour Technol. 2011;102(10):5551–61. doi:10.1016/j.biortech.2011.02.047. [Google Scholar] [PubMed] [CrossRef]
31. Botlhoko OJ, Makwakwa D, Muniyasamy S. Design of 3D printable boehmite alumina/thermally exfoliated reduced graphene oxide-based polymeric nanocomposites with high dielectric constant, mechanical and thermomechanical performance. Nano-Struct Nano-Objects. 2024;39:101228. doi:10.1016/j.nanoso.2024.101228. [Google Scholar] [CrossRef]
32. Wu Y, Gao X, Wu J, Zhou T, Nguyen TT, Wang Y. Biodegradable polylactic acid and its composites: characteristics, processing, and sustainable applications in sports. Polymers. 2023;15(14):3096. doi:10.3390/polym15143096. [Google Scholar] [PubMed] [CrossRef]
33. Joseph TM, Kallingal A, Suresh AM, Mahapatra DK, Hasanin MS, Haponiuk J, et al. 3D printing of polylactic acid: recent advances and opportunities. Int J Adv Manuf Technol. 2023;125(3–4):1015–35. doi:10.1007/s00170-022-10795-y. [Google Scholar] [PubMed] [CrossRef]
34. Ebrahimi F, Ramezani Dana H. Poly lactic acid (PLA) polymers: from properties to biomedical applications. Int J Polym Mater Polym Biomater. 2021;71(15):1117–30. doi:10.1080/00914037.2021.1944140. [Google Scholar] [CrossRef]
35. De Luca S, Milanese D, Gallichi-Nottiani D, Cavazza A, Sciancalepore C. Poly(lactic acid) and its blends for packaging application: a review. Clean Technol. 2023;5(4):1304–43. doi:10.3390/cleantechnol5040066. [Google Scholar] [CrossRef]
36. Bandyopadhyay J, Botlhoko OJ, Mphahlele C, Lekalakala R, Muniyasamy S, Ray SS. Reactively processed poly(butylene adipate terephthalate) composite-based multilayered films with improved properties for sustainable packaging applications. Struct Charact Biodegradation Mech Macromol Chem Phy. 2024;225(18):2400067. [Google Scholar]
37. Parodi A, Arpaia V, Samorì C, Mazzocchetti L, Galletti P. Novel strategies for recycling poly(butylene adipate-co-terephthalate)-starch-based plastics: selective solubilization and depolymerization-repolymerization processes. ACS Sustain Chem Eng. 2023;11(39):14518–27. doi:10.1021/acssuschemeng.3c03588. [Google Scholar] [CrossRef]
38. Yu S, Wang H-M, Xiong S-J, Zhou S-J, Wang H-H, Yuan T-Q. Sustainable wood-based poly(butylene adipate-co-terephthalate) biodegradable composite films reinforced by a rapid homogeneous esterification strategy. ACS Sustain Chem Eng. 2022;10(44):14568–78. doi:10.1021/acssuschemeng.2c04332. [Google Scholar] [CrossRef]
39. Ge FF, Tsou CH, Yuan S, De Guzman MR, Zeng CY, Li J, et al. Barrier performance and biodegradability of antibacterial poly(butylene adipate-co-terephthalate) nanocomposites reinforced with a new MWCNT-ZnO nanomaterial. Nanotechnol. 2021;32(48):485706. doi:10.1088/1361-6528/ac1b52. [Google Scholar] [PubMed] [CrossRef]
40. Zarei M, El Fray M. Synthesis of hydrophilic poly(butylene succinate-butylene dilinoleate) (PBS-DLS) copolymers containing poly(Ethylene Glycol) (PEG) of variable molecular weights. Polymers. 2021;13(18):3177. doi:10.3390/polym13183177. [Google Scholar] [PubMed] [CrossRef]
41. Mtibe A, Muniyasamy S, Mokhena TC, Ofosu O, Ojijo V, John M. Recent insight into the biomedical applications of polybutylene succinate and polybutylene succinate-based materials. Express Polym Lett. 2023;17(1):2–28. doi:10.3144/expresspolymlett.2023.2. [Google Scholar] [CrossRef]
42. Taylan O, Abdullah T, Baik S, Yilmaz MT, Alidrisi HM, Qurban RO, et al. Comparative study of evolutionary machine learning approaches to simulate the rheological characteristics of polybutylene succinate (PBS) utilized for fused deposition modeling (FDM). Polym Bull. 2023;81(10):8663–83. doi:10.1007/s00289-023-05106-8. [Google Scholar] [CrossRef]
43. Ingrao C, Platnieks O, Siracusa V, Gaidukova G, Paiano A, Gaidukovs S. Spent-coffee grounds as a zero-burden material blended with bio-based poly(butylene succinate) for production of bio-composites: findings from a Life Cycle Assessment application experience. Environ Impact Assess Rev. 2022;97. doi:10.1016/j.eiar.2022.106919. [Google Scholar] [CrossRef]
44. Elias Guckert F, Cesca K, Sayer C, de Oliveira D, Hermes de Araújo PH, Francisco Oechsler B. Lipase-catalyzed solution polycondensation of 1,4-butanediol and diethyl succinate: effect of diphenyl ether concentration on enzyme stability, reuse and PBS molar mass distribution. Eur Polym J. 2023;187. doi:10.1016/j.eurpolymj.2023.111926. [Google Scholar] [CrossRef]
45. Zhao Y, Zhong W. Recent progress in advanced polyester elastomers for tissue engineering and bioelectronics. Molecules. 2023;28(24). doi:10.3390/molecules28248025. [Google Scholar] [PubMed] [CrossRef]
46. Prabakaran R, Marie JM, Xavier AJM. Biobased Unsaturated polyesters containing castor oil-derived ricinoleic acid and itaconic acid: synthesis, In Vitro antibacterial, and cytocompatibility studies. ACS Appl Bio Mater. 2020;3(9):5708–21. [Google Scholar] [PubMed]
47. Zhao X, Cornish K, Vodovotz Y. Narrowing the gap for bioplastic use in food packaging: an update. Environ Sci Technol. 2020;54(8):4712–32. [Google Scholar] [PubMed]
48. Fei X, Wang J, Zhu J, Wang X, Liu X. Biobased poly(ethylene 2,5-furancoateno longer an alternative, but an irreplaceable polyester in the polymer industry. ACS Sustain Chem Eng. 2020;8(23):8471–85. [Google Scholar]
49. Razzaq S, Shahid S, Nawab Y. Applications and environmental impact of biodegradable polymers in textile industry: a review. Int J Biol Macromol. 2024;282(Pt 3):136791. [Google Scholar] [PubMed]
50. Schwarzer M, Korwitz A, Komber H, Häußler L, Dittrich B, Schartel B, et al. Phosphorus–containing polymer flame retardants for aliphatic polyesters. Macromol Mater Eng. 2017;303(2). doi:10.1002/mame.201700512. [Google Scholar] [CrossRef]
51. Kovacevic Z, Flincec Grgac S, Bischof S. Progress in biodegradable flame retardant nano-biocomposites. Polymers. 2021;13(5). doi:10.3390/polym13050741. [Google Scholar] [PubMed] [CrossRef]
52. Tiso T, Winter B, Wei R, Hee J, de Witt J, Wierckx N, et al. The metabolic potential of plastics as biotechnological carbon sources—review and targets for the future. Metab Eng. 2022;71:77–98. doi:10.1016/j.ymben.2021.12.006. [Google Scholar] [PubMed] [CrossRef]
53. Liu H, Liu S, Ning Y, Zhang R, Deng L, Wang F. Metabolic engineering of Escherichia coli for efficient production of 1,4-butanediol from crude glycerol. J Environ Chem Eng. 2024;12(1):111660. doi:10.1016/j.jece.2023.111660. [Google Scholar] [CrossRef]
54. Yim H, Haselbeck R, Niu W, Pujol-Baxley C, Burgard A, Boldt J, et al. Metabolic engineering of Escherichia coli for direct production of 1,4-butanediol. Nat Chem Biol. 2011;7(7):445–52. doi:10.1038/nchembio.580. [Google Scholar] [PubMed] [CrossRef]
55. de Matos Costa AR, Crocitti A, Hecker de Carvalho LH, Carroccio SC, Cerruti P, Santagata G. Properties of biodegradable films based on poly(butylene Succinate) (PBS) and poly(butylene adipate-co-terephthalate) (PBAT) blends (dagger, double dagger). Polymers. 2020;12(10). doi:10.3390/polym12102317. [Google Scholar] [PubMed] [CrossRef]
56. Jiang Z, Hou F, Chen J, Wang B, Song S, Li J, et al. Synthesis and properties of biodegradable PBAT prepared from PBT chemically recycled resources. Polymer. 2024;307. doi:10.1016/j.polymer.2024.127326. [Google Scholar] [CrossRef]
57. Taib N-AAB, Rahman MR, Huda D, Kuok KK, Hamdan S, Bakri MKB, et al. A review on poly lactic acid (PLA) as a biodegradable polymer. Polym Bull. 2022;80(2):1179–213. doi:10.1007/s00289-022-04160-y. [Google Scholar] [CrossRef]
58. Trivedi AK, Gupta MK, Singh H. PLA based biocomposites for sustainable products: a review. Adv Ind Eng Polym Res. 2023;6(4):382–95. doi:10.1016/j.aiepr.2023.02.002. [Google Scholar] [CrossRef]
59. Raj T, Chandrasekhar K, Naresh Kumar A, Kim S-H. Lignocellulosic biomass as renewable feedstock for biodegradable and recyclable plastics production: a sustainable approach. Renew Sustain Energ Rev. 2022;158. doi:10.1016/j.rser.2022.112130. [Google Scholar] [CrossRef]
60. Tangnorawich B, Magmee A, Roungpaisan N, Toommee S, Parcharoen Y, Pechyen C. Effect of polybutylene succinate additive in polylactic acid blend fibers via a melt-blown process. Molecules. 2023;28(20). doi:10.3390/molecules28207215. [Google Scholar] [PubMed] [CrossRef]
61. Someya Y, Nakazato T, Teramoto N, Shibata M. Thermal and mechanical properties of poly(butylene succinate) nanocomposites with various organo–modified montmorillonites. J Appl Polym Sci. 2003;91(3):1463–75. doi:10.1002/app.13366. [Google Scholar] [CrossRef]
62. Rajgond V, Mohite A, More N, More A. Biodegradable polyester-polybutylene succinate (PBSa review. Polym Bull. 2023;81(7):5703–52. doi:10.1007/s00289-023-04998-w. [Google Scholar] [CrossRef]
63. Xu J, Guo BH. Poly(butylene succinate) and its copolymers: research, development and industrialization. Biotechnol J. 2010;5(11):1149–63. doi:10.1002/biot.201000136. [Google Scholar] [PubMed] [CrossRef]
64. Mochizuki M, Mukai K, Yamada K, Ichise N, Murase S, Iwaya Y. Structural-effects-upon-enzymatic-hydrolysis-of-poly(butylene-succinate-co-ethylene-succinate)s. Macromolecules. 1997;30(24):7403–7. doi:10.1021/ma970036k. [Google Scholar] [CrossRef]
65. Agach M, Delbaere S, Marinkovic S, Estrine B, Nardello-Rataj V. Characterization, stability and ecotoxic properties of readily biodegradable branched oligoesters based on bio-sourced succinic acid and glycerol. Polym Degrad Stab. 2012;97(10):1956–63. doi:10.1016/j.polymdegradstab.2012.03.026. [Google Scholar] [CrossRef]
66. Chandure AS, Umare SS. Synthesis, characterization and biodegradation study of low molecular weight polyesters. Int J Polym Mater Polyme Biomater. 2007;56(3):339–53. doi:10.1080/00914030600865093. [Google Scholar] [CrossRef]
67. Pranamuda H, Tokiwa Y, Tanaka H. Microbial-degradation-of-an-aliphatic-polyester-with-a-high-melting-point-poly(tetramethylene. Appl Environ Microbiol. 1995;61(5):1828–32. doi:10.1128/aem.61.5.1828-1832.1995. [Google Scholar] [PubMed] [CrossRef]
68. Han YK, Kim SR, Kim J. Preparation and characterization of high molecular weight poly(butylene succinate). Macromol Res. 2002;10(2):108–14. doi:10.1007/BF03218299. [Google Scholar] [CrossRef]
69. Lim JS, Hong SM, Kim DK, Im SS. Effect of isocyanate–modified fumed silica on the properties of poly(butylene succinate) nanocomposites. J Appl Polym Sci. 2007;107(6):3598–608. doi:10.1002/app.27532. [Google Scholar] [CrossRef]
70. Bikiaris DN, Papageorgiou GZ, Achilias DS. Synthesis and comparative biodegradability studies of three poly(alkylene succinate)s. Polym Degrad Stab. 2006;91(1):31–43. doi:10.1016/j.polymdegradstab.2005.04.030. [Google Scholar] [CrossRef]
71. Mincheva R, Delangre A, Raquez JM, Narayan R, Dubois P. Biobased polyesters with composition-dependent thermomechanical properties: synthesis and characterization of poly(butylene succinate-co-butylene azelate). Biomacromolecules. 2013;14(3):890–9. doi:10.1021/bm301965h. [Google Scholar] [PubMed] [CrossRef]
72. Bikiaris DN, Achilias DS. Synthesis of poly(alkylene succinate) biodegradable polyesters, Part II: mathematical modelling of the polycondensation reaction. Polymer. 2008;49(17):3677–85. doi:10.1016/j.polymer.2008.06.026. [Google Scholar] [CrossRef]
73. Kint DPR, Alla A, Deloret E, Campos JL, Muñoz-Guerra S. Synthesis, characterization, and properties of poly(ethylene terephthalate)/poly(1,4-butylene succinate) block copolymers. Polymer. 2003;44(5):1321–30. doi:10.1016/S0032-3861(02)00938-2. [Google Scholar] [CrossRef]
74. Jin HJ, Lee BY, Kim MN, Yoon JS. Properties and biodegradation of poly(ethylene adipate) and poly(butylene succinate) containing styrene glycol units. Eur Polym J. 2000;36(12):2693–8. doi:10.1016/S0014-3057(00)00057-4. [Google Scholar] [CrossRef]
75. Tachibana Y, Masuda T, Funabashi M, Kunioka M. Chemical-synthesis-of-fully-biomass-based-poly(butylene-succinate)-from-inedible-biomass-based. Biomacromolecules. 2010;11(10):2760–5. doi:10.1021/bm100820y. [Google Scholar] [PubMed] [CrossRef]
76. Cao A, Okamura T, Nakayama K, Inoue Y, Masuda T. Studies on syntheses and physical properties of biodegradable aliphatic poly(butylene succinate-co-ethylene succinate)s and poly(butylene succinate-co-diethylene glycol succinate)s. Polym Degrad Stab. 2002;78(1):107–17. doi:10.1016/S0141-3910(02)00124-6. [Google Scholar] [CrossRef]
77. Ahn BD, Kim SH, Kim YH, Yang JS. Synthesis and characterization of the biodegradable copolymers from succinic acid and adipic acid with 1,4–butanediol. J Appl Polym Sci. 2001;82(11):2808–26. doi:10.1002/app.2135. [Google Scholar] [CrossRef]
78. Chen GQ. Plastics completely synthesized by bacteria: polyhydroxyalkanoates. In: Chen GQ, editor. Plastics from bacteria. Berlin/Heidelberg: Springer; 2010. Vol. 14, p. 17–37. doi:10.1007/978-3-642-03287-5_2. [Google Scholar] [CrossRef]
79. Takasu A, Oishi Y, Iio Y, Inai Y, Hirabayashi T. Synthesis-of-aliphatic-polyesters-by-direct-polyesterification-of-dicarboxylic-acids-with-diols-under. Macromolecules. 2003;36(6):1772–4. doi:10.1021/ma021462v. [Google Scholar] [CrossRef]
80. Ferreira LP, Moreira AN, Pinto JC, de Souza FG. Synthesis of poly(butylene succinate) using metal catalysts. Polym Eng Sci. 2015;55(8):1889–96. doi:10.1002/pen.24029. [Google Scholar] [CrossRef]
81. Jacquel N, Freyermouth F, Fenouillot F, Rousseau A, Pascault JP, Fuertes P, et al. Synthesis and properties of poly(butylene succinateefficiency of different transesterification catalysts. J Polym Sci Part A: Polym Chem. 2011;49(24):5301–12. doi:10.1002/pola.25009. [Google Scholar] [CrossRef]
82. Luo S, Li F, Yu J, Cao A. Synthesis of poly(butylene succinate–co–butylene terephthalate) (PBST) copolyesters with high molecular weights via direct esterification and polycondensation. J Appl Polym Sci. 2009;115(4):2203–11. doi:10.1002/app.31346. [Google Scholar] [CrossRef]
83. Jin TX, Zhou M, Hu SD, Chen F, Fu Q, Fu Y. Effect of molecular weight on the properties of poly(butylene succinate). Chin J Polym Sci. 2014;32(7):953–60. doi:10.1007/s10118-014-1463-4. [Google Scholar] [CrossRef]
84. Lyoo WS, Kim JH, Yoon WS, Ji BC, Choi JH, Cho J, et al. Effects of polymer concentration and zone drawing on the structure and properties of biodegradable poly(butylene succinate) film. Polymer. 2000;41(26):9055–62. doi:10.1016/S0032-3861(00)00154-3. [Google Scholar] [CrossRef]
85. Salmawy AE, Yamane H, Miyamoto M, Kimura Y. Properties and degradability of melt-spun fibers of poly (butylene succinate) and its copolymer with L-lactic acid. Sen’i Gakkaishi. 1999;55(3):120–6. doi:10.2115/fiber.55.3_120. [Google Scholar] [CrossRef]
86. Shirahama H, Kawaguchi Y, Aludin MS, Yasuda H. Synthesis and enzymatic degradation of high molecular weight aliphatic polyesters. J Appl Polym Sci. 2001;80(3):340–7. doi:10.1002/(ISSN)1097-4628. [Google Scholar] [CrossRef]
87. Gubbels E, Jasinska–Walc L, Koning CE. Synthesis and characterization of novel renewable polyesters based on 2,5–furandicarboxylic acid and 2,3–butanediol. J Polym Sci Part A: Polym Chem. 2012;51(4):890–8. doi:10.1002/pola.26446. [Google Scholar] [CrossRef]
88. Papageorgiou GZ, Bikiaris DN. Crystallization and melting behavior of three biodegradable poly(alkylene succinates). A comparative study. Polymer. 2005;46(26):12081–92. doi:10.1016/j.polymer.2005.10.073. [Google Scholar] [CrossRef]
89. Lavilla C, Alla A, Martinez de Ilarduya A, Munoz-Guerra S. High T(g) bio-based aliphatic polyesters from bicyclic D-mannitol. Biomacromolecules. 2013;14(3):781–93. doi:10.1021/bm301854c. [Google Scholar] [PubMed] [CrossRef]
90. Kricheldorf HR. Syntheses-of-biodegradable-and-biocompatible-polymers-by-means-of-bismuth-catalysts. Chem Rev. 2009;109(11):5579–94. doi:10.1021/cr900029e. [Google Scholar] [PubMed] [CrossRef]
91. Barletta M, Aversa C, Ayyoob M, Gisario A, Hamad K, Mehrpouya M, et al. Poly(butylene succinate) (PBSmaterials, processing, and industrial applications. Prog Polym Sci. 2022;132. doi:10.1016/j.progpolymsci.2022.101579. [Google Scholar] [CrossRef]
92. Lahcini M, Qayouh H, Yashiro T, Simon P, Kricheldorf HR. Syntheses of poly(butylene succinate) by means of non-toxic catalysts. J Macromol Sci, Part A. 2010;47(6):503–9. doi:10.1080/10601321003741875. [Google Scholar] [CrossRef]
93. Buzin P, Lahcini M, Schwarz G, Kricheldorf HR. Aliphatic polyesters by bismuth triflate-catalyzed polycondensations of dicarboxylic acids and aliphatic diols. Macromolecules. 2008;41(22):8491–5. doi:10.1021/ma8017662. [Google Scholar] [CrossRef]
94. Bersot JC, Jacquel N, Saint–Loup R, Fuertes P, Rousseau A, Pascault JP, et al. Efficiency increase of poly(ethylene terephthalate–co–isosorbide terephthalate) synthesis using bimetallic catalytic systems. Macromol Chem Phys. 2011;212(19):2114–20. doi:10.1002/macp.201100146. [Google Scholar] [CrossRef]
95. Jacquel N, Saint-Loup R, Pascault J-P, Rousseau A, Fenouillot F. Bio-based alternatives in the synthesis of aliphatic-aromatic polyesters dedicated to biodegradable film applications. Polymer. 2015;59:234–42. doi:10.1016/j.polymer.2014.12.021. [Google Scholar] [CrossRef]
96. Li H, Zhang Q, Song Y, Sun X, Huang W, Li A. Inventor; Nanjing University, assignee. inventor; Nanjing University, assignee. Method for synthesizing poly(butylene succinate) catalyzed by biogenic guanidinine. United States patent US9688811B2. 2017. [Google Scholar]
97. Pinho ED, Martins A, Araújo JV, Reis RL, Neves NM. Size also matters in biodegradable composite microfiber reinforced by chitosan nanofibers. MRS Proc. 2014;1621:59–69. doi:10.1557/opl.2014.67. [Google Scholar] [CrossRef]
98. Coleman JN, Khan U, Blau WJ, Gun’ko YK. Small but strong: a review of the mechanical properties of carbon nanotube-polymer composites. Carbon. 2006;44(9):1624–52. doi:10.1016/j.carbon.2006.02.038. [Google Scholar] [CrossRef]
99. Affdl JCH, Kardos JL. The halpin–Tsai equations: a review. Polym Eng Sci. 2004;16(5):344–52. doi:10.1002/pen.760160512. [Google Scholar] [CrossRef]
100. Elias Guckert F, Sayer C, de Oliveira D, Hermes de Araújo PH, Francisco Oechsler B. Synthesis of polybutylene succinate via lipase-catalyzed transesterification: enzyme stability, reuse and PBS properties in bulk polycondensations. Eur Polym J. 2022;179. doi:10.1016/j.eurpolymj.2022.111573. [Google Scholar] [CrossRef]
101. Song L, Qiu Z. Crystallization behavior and thermal property of biodegradable poly(butylene succinate)/functional multi-walled carbon nanotubes nanocomposite. Polym Degrad Stab. 2009;94(4):632–7. doi:10.1016/j.polymdegradstab.2009.01.009. [Google Scholar] [CrossRef]
102. Barletta M, Genovesi A, Desole MP, Gisario A. Melt processing of biodegradable poly(butylene succinate) (PBS)—a critical review. Clean Technol Environ Policy. 2024. doi:10.1007/s10098-024-03005-8. [Google Scholar] [CrossRef]
103. Guidotti G, Soccio M, Siracusa V, Gazzano M, Salatelli E, Munari A, et al. Novel Random pbs-based copolymers containing aliphatic side chains for sustainable flexible food packaging. Polymers. 2017;9(12). doi:10.3390/polym9120724. [Google Scholar] [PubMed] [CrossRef]
104. Liverani L, Piegat A, Niemczyk A, El Fray M, Boccaccini AR. Electrospun fibers of poly(butylene succinate–co–dilinoleic succinate) and its blend with poly(glycerol sebacate) for soft tissue engineering applications. Eur Polym J. 2016;81:295–306. doi:10.1016/j.eurpolymj.2016.06.009. [Google Scholar] [CrossRef]
105. Liu J, Jiang Z, Zhang S, Saltzman WM. Poly(omega-pentadecalactone-co-butylene-co-succinate) nanoparticles as biodegradable carriers for camptothecin delivery. Biomaterials. 2009;30(29):5707–19. doi:10.1016/j.biomaterials.2009.06.061. [Google Scholar] [PubMed] [CrossRef]
106. Hwang SY, Yoo ES, Im SS. The synthesis of copolymers, blends and composites based on poly(butylene succinate). Polym J. 2012;44(12):1179–90. doi:10.1038/pj.2012.157. [Google Scholar] [CrossRef]
107. Gualandi C, Soccio M, Govoni M, Valente S, Lotti N, Munari A, et al. Poly(butylene/diethylene glycol succinate) multiblock copolyester as a candidate biomaterial for soft tissue engineering: solid-state properties, degradability, and biocompatibility. J Bioact Compat Polym. 2012;27(3):244–64. doi:10.1177/0883911512440536. [Google Scholar] [CrossRef]
108. Gigli M, Lotti N, Gazzano M, Finelli L, Munari A. Macromolecular design of novel sulfur–containing copolyesters with promising mechanical properties. J Appl Polym Sci. 2012;126(2):686–96. doi:10.1002/app.36856. [Google Scholar] [CrossRef]
109. Gualandi C, Soccio M, Saino E, Focarete ML, Lotti N, Munari A, et al. Easily synthesized novel biodegradable copolyesters with adjustable properties for biomedical applications. Soft Matter. 2012;8(20). doi:10.1039/c2sm25308a. [Google Scholar] [CrossRef]
110. Soccio M, Lotti N, Gazzano M, Govoni M, Giordano E, Munari A. Molecular architecture and solid-state properties of novel biocompatible PBS-based copolyesters containing sulphur atoms. React Funct Polym. 2012;72(11):856–67. doi:10.1016/j.reactfunctpolym.2012.08.002. [Google Scholar] [CrossRef]
111. Gigli M, Lotti N, Gazzano M, Finelli L, Munari A. Synthesis and characterization of novel poly(butylene succinate)–based copolyesters designed as potential candidates for soft tissue engineering. Polym Eng Sci. 2012;53(3):491–501. doi:10.1002/pen.23289. [Google Scholar] [CrossRef]
112. Marija S, Nikolic JD. Synthesis and characterization of biodegradable poly(butylene succinate-co-butylene adipate)s. Polym Degrad Stab. 2001;74(2):263–70. doi:10.1016/S0141-3910(01)00156-2. [Google Scholar] [CrossRef]
113. Cao A, Okamura T, Ishiguro C, Nakayama K, Inoue Y, Masuda T. Studies on syntheses and physical characterization of biodegradable aliphatic poly(butylene succinate-co-ε-caprolactone)s. Polymer. 2002;43(3):671–9. doi:10.1016/S0032-3861(01)00658-9. [Google Scholar] [CrossRef]
114. Taguchi Y, Oishi A, Fujita KI, Ikeda Y, Watanabe K, Masuda T. Preparation of poly(butylene succinate) containing monoacylglycerol unit. J Japan Oil Chem’ Soc. 2000;49(8):825–30. doi:10.5650/jos1996.49.825. [Google Scholar] [CrossRef]
115. Oishi A, Nakano H, Fujita KI, Yuasa M, Taguchi Y. Copolymerization of poly (butylene succinate) with 3-alkoxy-1, 2-propanediols. Polym J. 2002;34(10):742–7. doi:10.1295/polymj.34.742. [Google Scholar] [CrossRef]
116. Oishi A, Zhang M, Nakayama K, Masuda T, Taguchi Y. Synthesis of poly(butylene succinate) and poly(ethylene succinate) including diglycollate moiety. Polym J. 2006;38(7):710–5. doi:10.1295/polymj.PJ2005206. [Google Scholar] [CrossRef]
117. Chen C-H, Peng J-S, Chen M, Lu H-Y, Tsai C-J, Yang C-S. Synthesis and characterization of poly(butylene succinate) and its copolyesters containing minor amounts of propylene succinate. Colloid Polym Sci. 2010;288(7):731–8. doi:10.1007/s00396-010-2187-9. [Google Scholar] [CrossRef]
118. Zhang S, Yang J, Liu X, Chang J, Cao A. Synthesis and characterization of poly(butylene succinate-co-butylene malatea new biodegradable copolyester bearing hydroxyl pendant groups. Biomacromolecules. 2003;4(2):437–45. doi:10.1021/bm0201183. [Google Scholar] [PubMed] [CrossRef]
119. Stȩpień K, Miles C, McClain A, Wiśniewska E, Sobolewski P, Kohn J, et al. Biocopolyesters of poly(butylene succinate) containing long-chain biobased glycol synthesized with heterogeneous titanium dioxide catalyst. ACS Sustain Chem Eng. 2019;7(12):10623–32. doi:10.1021/acssuschemeng.9b01191. [Google Scholar] [CrossRef]
120. Zeng J-B, Li Y-D, Zhu Q-Y, Yang K-K, Wang X-L, Wang Y-Z. A novel biodegradable multiblock poly(ester urethane) containing poly(l-lactic acid) and poly(butylene succinate) blocks. Polymer. 2009;50(5):1178–86. doi:10.1016/j.polymer.2009.01.001. [Google Scholar] [CrossRef]
121. Debuissy T, Sangwan P, Pollet E, Avérous L. Study on the structure-properties relationship of biodegradable and biobased aliphatic copolyesters based on 1,3-propanediol, 1,4-butanediol, succinic and adipic acids. Polymer. 2017;122:105–16. doi:10.1016/j.polymer.2017.06.045. [Google Scholar] [CrossRef]
122. Han J, Shi J, Xie Z, Xu J, Guo B. Synthesis, properties of poly(butylene succinate-co-butylene 2-methylsuccinate) and application for sustainable release. Materials. 2019;12(9). doi:10.3390/ma12091507. [Google Scholar] [PubMed] [CrossRef]
123. Witt lR-JM, 1 U, Deckwer W-D. Evaluation of the biodegradability of copolyesters containing aromatic compounds by investigations of model oligomers. J Environ Polym Degrad. 1996;4(1):9–20. doi:10.1007/BF02083878. [Google Scholar] [CrossRef]
124. Chen H-B, Wang X-L, Zeng J-B, Li L-L, Dong F-X, Wang Y-Z. A novel multiblock poly(ester urethane) based on poly(butylene succinate) and poly(ethylene succinate-co-ethylene terephthalate). Ind Eng Chem Res. 2011;50(4):2065–72. doi:10.1021/ie101798n. [Google Scholar] [CrossRef]
125. Morales-Huerta JC, Ciulik CB, de Ilarduya AM, Muñoz-Guerra S. Fully bio-based aromatic-aliphatic copolyesters: poly(butylene furandicarboxylate-co-succinate)s obtained by ring opening polymerization. Polym Chem. 2017;8(4):748–60. doi:10.1039/c6py01879c. [Google Scholar] [CrossRef]
126. Qin J, Lin L, Wang S, Ye S, Luo W, Xiao M, et al. Multiblock copolymers of PPC with oligomeric PBS: with low brittle-toughness transition temperature. RSC Adv. 2018;8(26):14722–31. doi:10.1039/c8ra01588k. [Google Scholar] [PubMed] [CrossRef]
127. Soccio M, Dominici F, Quattrosoldi S, Luzi F, Munari A, Torre L, et al. PBS-based green copolymer as an efficient compatibilizer in thermoplastic inedible wheat flour/poly(butylene succinate) blends. Biomacromolecules. 2020;21(8):3254–69. doi:10.1021/acs.biomac.0c00701. [Google Scholar] [PubMed] [CrossRef]
128. Han SI, Kang SW, Kim BS, Im SS. A novel polymeric ionomer as a potential biomaterial: crystallization behavior, degradation, and in-vitro cellular interactions. Adv Funct Mater. 2005;15(3):367–74. doi:10.1002/adfm.200400079. [Google Scholar] [CrossRef]
129. Bautista M, De Ilarduya A, Alla A, Muñoz-Guerra S. Poly(butylene succinate) ionomers with enhanced hydrodegradability. Polymers. 2015;7(7):1232–47. doi:10.3390/polym7071232. [Google Scholar] [CrossRef]
130. Hao N, Wang YB, Zhang SP, Shi SQ, Nakashima K, Gong YK. Surface reconstruction and hemocompatibility improvement of a phosphorylcholine end-capped poly(butylene succinate) coating. J Biomed Mater Res A. 2014;102(9):2972–81. doi:10.1002/jbm.a.34967. [Google Scholar] [PubMed] [CrossRef]
131. Taleb K, Saidi-Besbes S, Pillin I, Grohens Y. Biodegradable poly(butylene succinate) nanocomposites based on dimeric surfactant organomodified clays with enhanced water vapor barrier and mechanical properties. ACS Omega. 2022;7(47):43254–64. doi:10.1021/acsomega.2c05964. [Google Scholar] [PubMed] [CrossRef]
132. Gomez-Gamez AB, Yebra-Rodriguez A, Peñas-Sanjuan A, Soriano-Cuadrado B, Jimenez-Millan J. Influence of clay percentage on the technical properties of montmorillonite/polylactic acid nanocomposites. Appl Clay Sci. 2020;198. doi:10.1016/j.clay.2020.105818. [Google Scholar] [CrossRef]
133. Rivas-Rojas PC, Ollier RP, Alvarez VA, Huck-Iriart C. Enhancing the integration of bentonite clay with polycaprolactone by intercalation with a cationic surfactant: effects on clay orientation and composite tensile properties. J Mater Sci. 2021;56(9):5595–608. doi:10.1007/s10853-020-05603-5. [Google Scholar] [CrossRef]
134. Wu B, Huang J, Yu Y, Zhu H, Zhu K, Yang Y, et al. In-depth investigation of how carbon nanofiller dispersion affects microcellular foaming behavior in poly(butylene succinate) nanocomposites. J Supercrit Fluids. 2024;209. doi:10.1016/j.supflu.2024.106252. [Google Scholar] [CrossRef]
135. Vidakis N, Petousis M, Kourinou M, Velidakis E, Mountakis N, Fischer-Griffiths PE, et al. Additive manufacturing of multifunctional polylactic acid (PLA)—multiwalled carbon nanotubes (MWCNTs) nanocomposites. Nanocomposites. 2021;7(1):184–99. doi:10.1080/20550324.2021.2000231. [Google Scholar] [CrossRef]
136. Wang Y, Meng F, Zhu J, Ba Z, Jiang D, Wen X, et al. Synergistic effect of carbon nanotube on improving thermal stability, flame retardancy, and electrical conductivity of poly(butylene succinate)/piperazine pyrophosphate composites. Colloid Polym Sci. 2023;301(12):1529–37. doi:10.1007/s00396-023-05166-2. [Google Scholar] [CrossRef]
137. Platnieks O, Gaidukovs S, Neibolts N, Barkane A, Gaidukova G, Thakur VK. Poly(butylene succinate) and graphene nanoplatelet-based sustainable functional nanocomposite materials: Structure-properties relationship. Mater Today Chem. 2020;18. doi:10.1016/j.mtchem.2020.100351. [Google Scholar] [CrossRef]
138. Cosquer R, Pruvost S, Gouanve F. Improvement of barrier properties of biodegradable polybutylene succinate/graphene nanoplatelets nanocomposites prepared by melt process. Membranes. 2021;11(2). doi:10.3390/membranes11020151. [Google Scholar] [PubMed] [CrossRef]
139. Hasheminejad K, Montazeri A. Enhanced interfacial characteristics in PLA/graphene composites through numerically-designed interface treatment. Appl Surface Sci. 2020;502. doi:10.1016/j.apsusc.2019.144150. [Google Scholar] [CrossRef]
140. Li N, Wang M, Luo H, Tse SD, Gao Y, Zhu Z, et al. Processing and properties of graphene-reinforced polylactic acid nanocomposites for bioelectronic and tissue regenerative functions. Biomater Adv. 2025;167:214113. doi:10.1016/j.bioadv.2024.214113. [Google Scholar] [PubMed] [CrossRef]
141. Anitasari S, Wu CZ, Shen YK. PCL/Graphene scaffolds for the osteogenesis process. Bioengineering. 2023;10(3). doi:10.3390/bioengineering10030305. [Google Scholar] [PubMed] [CrossRef]
142. de Souza AG, de Lima GF, Colombo R, Rosa DS. A new approach for the use of anionic surfactants: nanocellulose modification and development of biodegradable nanocomposites. Cellulose. 2020;27(10):5707–28. doi:10.1007/s10570-020-03160-3. [Google Scholar] [CrossRef]
143. de Souza AG, Barbosa RFS, Rosa DS. Nanocellulose from industrial and agricultural waste for further use in PLA composites. J Polym Environ. 2020;28(7):1851–68. doi:10.1007/s10924-020-01731-w. [Google Scholar] [CrossRef]
144. Albitres GAV, Araujo Junior FP, Freitas DFS, Mariano DM, Tavares MIB, Mendes LC. Nanocellulose: effect on thermal, structural, molecular mobility and rheological characteristics of poly(butylene adipate-co-butylene terephthalate) nanocomposites. Mater Sci Appl. 2022;13(4):249–77. doi:10.4236/msa.2022.134014. [Google Scholar] [CrossRef]
145. Ilyas RA, Azmi A, Nurazzi NM, Atiqah A, Atikah MSN, Ibrahim R, et al. Oxygen permeability properties of nanocellulose reinforced biopolymer nanocomposites. Mater Today: Proc. 2022;52:2414–9. doi:10.1016/j.matpr.2021.10.420. [Google Scholar] [CrossRef]
146. Ucpinar Durmaz B, Ugur Nigiz F, Aytac A. Active packaging films based on poly(butylene succinate) films reinforced with alkaline halloysite nanotubes: production, properties, and fruit packaging applications. Appl Clay Sci. 2024;259. doi:10.1016/j.clay.2024.107517. [Google Scholar] [CrossRef]
147. He X, Zhang M, Zhu M, Zhou H, Wang X, Chen N. Green fabrication of poly (butylene succinate)/halloysite nanotube open-cell foams with ultra-high foaming and adsorption performance. Appl Clay Sci. 2024;261. doi:10.1016/j.clay.2024.107578. [Google Scholar] [CrossRef]
148. Sun Y, Yu B, Liu Y, Yan J, Xu Z, Cheng B, et al. Bio-inspired surface manipulation of halloysite nanotubes for high-performance flame retardant polylactic acid nanocomposites. Nano Res. 2023;17(3):1595–606. doi:10.1007/s12274-023-6050-y. [Google Scholar] [CrossRef]
149. Risyon NP, Othman SH, Basha RK, Talib RA. Characterization of polylactic acid/halloysite nanotubes bionanocomposite films for food packaging. Food Packag Shelf Life. 2020;23. doi:10.1016/j.fpsl.2019.100450. [Google Scholar] [CrossRef]
150. Ahmed S, Jones FR. A review of particulate reinforcement theories for polymer composites. J Mater Sci. 1990;25(12):4933–42. doi:10.1007/BF00580110. [Google Scholar] [CrossRef]
151. Fu S, Sun Z, Huang P, Li Y, Hu N. Some basic aspects of polymer nanocomposites: a critical review. Nano Mater Sci. 2019;1(1):2–30. doi:10.1016/j.nanoms.2019.02.006. [Google Scholar] [CrossRef]
152. Oladele IO, Onuh LN, Siengchin S, Sanjay MR, Adelani SO. Modern applications of polymer composites in structural industries: a review of philosophies, product development, and graphical applications. Appl Sci Eng Progress. 2023. doi:10.14416/j.asep.2023.07.003. [Google Scholar] [CrossRef]
153. Kuciel S, Rusin-Żurek K, Kurańska M. The influence of filler particle size on the strength properties and mechanical energy dissipation capacity of biopoly(ethylene terephthalate) bioPET/eggshell biocomposites. Recycling. 2024;9(5). doi:10.3390/recycling9050088. [Google Scholar] [CrossRef]
154. Liu W-G, Zhang X-C, Li H-Y, Liu Z. Effect of surface modification with 3-aminopropyltriethyloxy silane on mechanical and crystallization performances of ZnO/poly(butylenesuccinate) composites. Compos Part B: Eng. 2012;43(5):2209–16. doi:10.1016/j.compositesb.2012.02.021. [Google Scholar] [CrossRef]
155. Khankrua R, Pivsa-Art S, Hiroyuki H, Suttiruengwong S. Thermal and mechanical properties of biodegradable polyester/silica nanocomposites. Energy Proc. 2013;34:705–13. doi:10.1016/j.egypro.2013.06.803. [Google Scholar] [CrossRef]
156. Sharma SK, Sehgal N, Kumar A. Biomolecules for development of biosensors and their applications. Curr Appl Phys. 2003;3(2–3):307–16. doi:10.1016/S1567-1739(02)00219-5. [Google Scholar] [CrossRef]
157. Sharma R, Jafari SM, Sharma S. Antimicrobial bio-nanocomposites and their potential applications in food packaging. Food Control. 2020;112. doi:10.1016/j.foodcont.2020.107086. [Google Scholar] [CrossRef]
158. Petchwattana N, Covavisaruch S, Wibooranawong S, Naknaen P. Antimicrobial food packaging prepared from poly(butylene succinate) and zinc oxide. Measurement. 2016;93:442–8. doi:10.1016/j.measurement.2016.07.048. [Google Scholar] [CrossRef]
159. Ostheller ME, Abdelgawad AM, Balakrishnan NK, Hassanin AH, Groten R, Seide G. Curcumin and silver doping enhance the spinnability and antibacterial activity of melt-electrospun polybutylene succinate fibers. Nanomater. 2022;12(2). doi:10.3390/nano12020283. [Google Scholar] [PubMed] [CrossRef]
160. Rhim J-W, Park H-M, Ha C-S. Bio-nanocomposites for food packaging applications. Prog Polym Sci. 2013;38(10–11):1629–52. doi:10.1016/j.progpolymsci.2013.05.008. [Google Scholar] [CrossRef]
161. Ma P, Jiang L, Yu M, Dong W, Chen M. Green antibacterial nanocomposites from poly(lactide)/poly(butylene adipate-co-terephthalate)/nanocrystal cellulose-silver nanohybrids. ACS Sustain Chem Eng. 2016;4(12):6417–26. doi:10.1021/acssuschemeng.6b01106. [Google Scholar] [CrossRef]
162. Shankar S, Rhim JW. Preparation of nanocellulose from micro-crystalline cellulose: the effect on the performance and properties of agar-based composite films. Carbohydr Polym. 2016;135:18–26. doi:10.1016/j.carbpol.2015.08.082. [Google Scholar] [PubMed] [CrossRef]
163. Mekuye B, Abera B. Nanomaterials: an overview of synthesis, classification, characterization, and applications. Nano Select. 2023;4(8):486–501. doi:10.1002/nano.202300038. [Google Scholar] [CrossRef]
164. Joudeh N, Linke D. Nanoparticle classification, physicochemical properties, characterization, and applications: a comprehensive review for biologists. J Nanobiotechnol. 2022;20(1):262. doi:10.1186/s12951-022-01477-8. [Google Scholar] [PubMed] [CrossRef]
165. Wang Y, Ying Z, Xie W, Wu D. Cellulose nanofibers reinforced biodegradable polyester blends: ternary biocomposites with balanced mechanical properties. Carbohydr Polym. 2020;233:115845. doi:10.1016/j.carbpol.2020.115845. [Google Scholar] [PubMed] [CrossRef]
166. Platnieks O, Gaidukovs S, Barkane A, Sereda A, Gaidukova G, Grase L, et al. Bio-based poly(butylene succinate)/microcrystalline cellulose/nanofibrillated cellulose-based sustainable polymer composites: thermo-mechanical and biodegradation studies. Polymers. 2020;12(7). doi:10.3390/polym12071472. [Google Scholar] [PubMed] [CrossRef]
167. Zhou M, Fan M, Zhao Y, Jin T, Fu Q. Effect of stretching on the mechanical properties in melt-spun poly(butylene succinate)/microfibrillated cellulose (MFC) nanocomposites. Carbohydr Polym. 2016;140(1):383–92. doi:10.1016/j.carbpol.2015.12.040. [Google Scholar] [PubMed] [CrossRef]
168. Chirayil CJ, Mathew L, Thomas S. Review of recent research in nano cellulose preparation from different lignocellulosic fibers. Reviews Adv Mater Sci. 2014;37:20–8. [Google Scholar]
169. Siró I, Plackett D. Microfibrillated cellulose and new nanocomposite materials: a review. Cellulose. 2010;17(3):459–94. doi:10.1007/s10570-010-9405-y. [Google Scholar] [CrossRef]
170. Oksman K, Aitomäki Y, Mathew AP, Siqueira G, Zhou Q, Butylina S, et al. Review of the recent developments in cellulose nanocomposite processing. Compos Part A: Appl Sci Manufacturing. 2016;83:2–18. doi:10.1016/j.compositesa.2015.10.041. [Google Scholar] [CrossRef]
171. Naruki Kurokawa SK, Atsushi H. Mechanical properties of poly(butylene succinate) composites with aligned cellulose-acetate nanofibers. J Appl Polym Sci. 2018;135(24):45429. doi:10.1002/app.45429. [Google Scholar] [CrossRef]
172. Joy J, Jose C, Yu X, Mathew L, Thomas S, Pilla S. The influence of nanocellulosic fiber, extracted from Helicteres isora, on thermal, wetting and viscoelastic properties of poly(butylene succinate) composites. Cellulose. 2017;24(10):4313–23. doi:10.1007/s10570-017-1439-y. [Google Scholar] [CrossRef]
173. Ju J, Gu Z, Liu X, Zhang S, Peng X, Kuang T. Fabrication of bimodal open-porous poly(butylene succinate)/cellulose nanocrystals composite scaffolds for tissue engineering application. Int J Biol Macromol. 2020;147:1164–73. doi:10.1016/j.ijbiomac.2019.10.085. [Google Scholar] [PubMed] [CrossRef]
174. Yang HB, Yue X, Liu ZX, Guan QF, Yu SH. Emerging sustainable structural materials by assembling cellulose nanofibers. Adv Mater. 2024:e2413564. doi:10.1002/adma.202413564. [Google Scholar] [PubMed] [CrossRef]
175. Iijima S. Helical microtubules of graphitic carbon. Nature. 1991;354(6348):56–8. doi:10.1038/354056a0. [Google Scholar] [CrossRef]
176. Zeng R-T, Hu W, Wang M, Zhang S-D, Zeng J-B. Morphology, rheological and crystallization behavior in non-covalently functionalized carbon nanotube reinforced poly(butylene succinate) nanocomposites with low percolation threshold. Polym Test. 2016;50:182–90. doi:10.1016/j.polymertesting.2016.01.003. [Google Scholar] [CrossRef]
177. Ribeiro H, Trigueiro JPC, Owuor PS, Machado LD, Woellner CF, Pedrotti JJ, et al. Hybrid 2D nanostructures for mechanical reinforcement and thermal conductivity enhancement in polymer composites. Compos Sci Technol. 2018;159:103–10. doi:10.1016/j.compscitech.2018.01.032. [Google Scholar] [CrossRef]
178. Baig N, Kammakakam I, Falath W. Nanomaterials: a review of synthesis methods, properties, recent progress, and challenges. Mater Adv. 2021;2(6):1821–71. doi:10.1039/D0MA00807A. [Google Scholar] [CrossRef]
179. Rastin H, Mansouri N, Tung TT, Hassan K, Mazinani A, Ramezanpour M, et al. Converging 2D nanomaterials and 3D bioprinting technology: state-of-the-art, challenges, and potential outlook in biomedical applications. Adv Healthc Mater. 2021;10(22):e2101439. doi:10.1002/adhm.202101439. [Google Scholar] [PubMed] [CrossRef]
180. Zhao J, Chen Z, Liu S, Li P, Yu S, Ling D, et al. Nano–bio interactions between 2D nanomaterials and mononuclear phagocyte system cells. BMEMat. 2024;2(2). doi:10.1002/bmm2.12066. [Google Scholar] [CrossRef]
181. Rafiee MA, Narayanan TN, Hashim DP, Sakhavand N, Shahsavari R, Vajtai R, et al. Hexagonal boron nitride and graphite oxide reinforced multifunctional porous cement composites. Adv Funct Mater. 2013;23(45):5624–30. doi:10.1002/adfm.201203866. [Google Scholar] [CrossRef]
182. Butler SZ, Hollen SM, Cao L, Cui Y, Gupta JA, Gutiérrez HR, et al. Progress, challenges, and opportunities in two-dimensional materials beyond graphene. ACS Nano. 2013;7(4):2898–926. [Google Scholar] [PubMed]
183. Gonçalves G, Marques PAAP, Barros-Timmons A, Bdkin I, Singh MK, Emami N, et al. Graphene oxide modified with PMMA via ATRP as a reinforcement filler. J Mater Chem. 2010;20(44). doi:10.1039/c0jm01674h. [Google Scholar] [CrossRef]
184. Cao Y, Lai Z, Feng J, Wu P. Graphene oxide sheets covalently functionalized with block copolymers via click chemistry as reinforcing fillers. J Mater Chem. 2011;21(25). doi:10.1039/c1jm10420a. [Google Scholar] [CrossRef]
185. Lin Z, Liu Y, Raghavan S, Moon KS, Sitaraman SK, Wong CP. Magnetic alignment of hexagonal boron nitride platelets in polymer matrix: toward high performance anisotropic polymer composites for electronic encapsulation. ACS Appl Mater Interfaces. 2013;5(15):7633–40. doi:10.1021/am401939z. [Google Scholar] [PubMed] [CrossRef]
186. Kim JY, Kim T, Suk JW, Chou H, Jang JH, Lee JH, et al. Enhanced dielectric performance in polymer composite films with carbon nanotube-reduced graphene oxide hybrid filler. Small. 2014;10(16):3405–11. doi:10.1002/smll.201400363. [Google Scholar] [PubMed] [CrossRef]
187. Wang X, Hu Y, Song L, Yang H, Yu B, Kandola B, et al. Comparative study on the synergistic effect of POSS and graphene with melamine phosphate on the flame retardance of poly(butylene succinate). Thermochim Acta. 2012;543:156–64. doi:10.1016/j.tca.2012.05.017. [Google Scholar] [CrossRef]
188. Abidin ASZ, Yusoh K, Jamari SS, Abdullah AH, Ismail Z. Enhanced performance of alkylated graphene reinforced polybutylene succinate nanocomposite. AIP Conf Proc. 2016;1756(1):040005. doi:10.1063/1.4958766. [Google Scholar] [CrossRef]
189. Zainal Abidin AS, Yusoh K, Jamari SS, Abdullah AH, Ismail Z. Surface functionalization of graphene oxide with octadecylamine for improved thermal and mechanical properties in polybutylene succinate nanocomposite. Polym Bull. 2018;75(8):3499–522. doi:10.1007/s00289-017-2217-6. [Google Scholar] [CrossRef]
190. Aziz T, Farid A, Haq F, Kiran M, Ullah A, Zhang K, et al. A review on the modification of cellulose and its applications. Polymers. 2022;14(15). doi:10.3390/polym14153206. [Google Scholar] [PubMed] [CrossRef]
191. Perera KY, Jaiswal AK, Jaiswal S. Biopolymer-based sustainable food packaging materials: challenges, solutions, and applications. Foods. 2023;12(12). doi:10.3390/foods12122422. [Google Scholar] [PubMed] [CrossRef]
192. Seddiqi H, Oliaei E, Honarkar H, Jin J, Geonzon LC, Bacabac RG, et al. Cellulose and its derivatives: towards biomedical applications. Cellulose. 2021;28(4):1893–931. doi:10.1007/s10570-020-03674-w. [Google Scholar] [CrossRef]
193. Mokhena TC, Sadiku ER, Mochane MJ, Ray SS, John MJ, Mtibe A. Mechanical properties of cellulose nanofibril papers and their bionanocomposites: a review. Carbohydr Polym. 2021;273:118507. doi:10.1016/j.carbpol.2021.118507. [Google Scholar] [PubMed] [CrossRef]
194. Mishra K, Siwal SS, Sithole T, Singh N, Hart P, Thakur VK. Biorenewable materials for water remediation: the central role of cellulose in achieving sustainability. J Bioresour Bioproducts. 2024;9(3):253–82. doi:10.1016/j.jobab.2023.12.002. [Google Scholar] [CrossRef]
195. Tanpichai S, Boonmahitthisud A, Soykeabkaew N, Ongthip L. Review of the recent developments in all-cellulose nanocomposites: properties and applications. Carbohydr Polym. 2022;286:119192. doi:10.1016/j.carbpol.2022.119192. [Google Scholar] [PubMed] [CrossRef]
196. Baghaei B, Skrifvars M. All-cellulose composites: a review of recent studies on structure. Prop Appl Mol. 2020;25(12). doi:10.3390/molecules25122836. [Google Scholar] [PubMed] [CrossRef]
197. Ganapathy V, Muthukumaran G, Sudhagar PE, Rashedi A, Norrrahim MNF, Ilyas RA, et al. Mechanical properties of cellulose–based multiscale composites: a review. Polym Compos. 2022;44(2):734–56. doi:10.1002/pc.27175. [Google Scholar] [CrossRef]
198. Dutta D, Sit N. A comprehensive review on types and properties of biopolymers as sustainable bio–based alternatives for packaging. Food Biomacromolecules. 2024. doi:10.1002/fob2.12019. [Google Scholar] [CrossRef]
199. Omran AAB, Mohammed A, Sapuan SM, Ilyas RA, Asyraf MRM, Rahimian Koloor SS, et al. Micro- and nanocellulose in polymer composite materials: a review. Polymers. 2021;13(2). doi:10.3390/polym13020231. [Google Scholar] [PubMed] [CrossRef]
200. Jakob M, Mahendran AR, Gindl-Altmutter W, Bliem P, Konnerth J, Müller U, et al. The strength and stiffness of oriented wood and cellulose-fibre materials: a review. Prog Mater Sci. 2022;125. doi:10.1016/j.pmatsci.2021.100916. [Google Scholar] [CrossRef]
201. Filizgok S, Kodal M, Ozkoc G. Non–isothermal crystallization kinetics and dynamic mechanical properties of poly(butylene succinate) nanocomposites with different type of carbonaceous nanoparticles. Polym Compos. 2018;39(8):2705–21. doi:10.1002/pc.24261. [Google Scholar] [CrossRef]
202. He Y, Zhu J, Wang W, Ni H. Surface modification of cellulose nanocrystals with different acid anhydrides for improved dispersion in poly(butylene succinate). RSC Adv. 2018;8(67):38305–14. doi:10.1039/C8RA07597B. [Google Scholar] [PubMed] [CrossRef]
203. Li J, Qiu Z. Fully biodegradable poly(butylene succinate-co-1,2-decylene succinate)/cellulose nanocrystals composites with significantly enhanced crystallization and mechanical property. Polymer. 2022;252. doi:10.1016/j.polymer.2022.124946. [Google Scholar] [CrossRef]
204. Pramoda KP, Linh NTT, Zhang C, Liu T. Multiwalled carbon nanotube nucleated crystallization behavior of biodegradable poly(butylene succinate) nanocomposites. J Appl Polym Sci. 2008;111(6):2938–45. doi:10.1002/app.29349. [Google Scholar] [CrossRef]
205. Ghavanloo E, Rafii-Tabar H, Kausar A, Giannopoulos GI, Fazelzadeh SA. Experimental and computational physics of fullerenes and their nanocomposites: synthesis, thermo-mechanical characteristics and nanomedicine applications. Phys Rep. 2023;996:1–116. doi:10.1016/j.physrep.2022.10.003. [Google Scholar] [CrossRef]
206. Shih YF, Chen LS, Jeng RJ. Preparation and properties of biodegradable PBS/multi-walled carbon nanotube nanocomposites. Polymer. 2008;49(21):4602–11. doi:10.1016/j.polymer.2008.08.015. [Google Scholar] [CrossRef]
207. Cichosz S, Masek A, Rylski A. Cellulose modification for improved compatibility with the polymer matrix: mechanical characterization of the composite material. Materials. 2020;13(23). doi:10.3390/ma13235519. [Google Scholar] [PubMed] [CrossRef]
208. Tcherdyntsev VV. Reinforced polymer composites. Polymers. 2021;13(4). doi:10.3390/polym13040564. [Google Scholar] [PubMed] [CrossRef]
209. Jin T-X, Liu C, Zhou M, S-g Chai, Chen F, Fu Q. Crystallization, mechanical performance and hydrolytic degradation of poly(butylene succinate)/graphene oxide nanocomposites obtained via in situ polymerization. Composites Part A: Appl Sci Manufacturing. 2015;68:193–201. doi:10.1016/j.compositesa.2014.09.025. [Google Scholar] [CrossRef]
210. Wan C, Chen B. Reinforcement of biodegradable poly(butylene succinate) with low loadings of graphene oxide. J Appl Polym Sci. 2012;127(6):5094–9. doi:10.1002/app.38136. [Google Scholar] [CrossRef]
211. Li Y-D, Li H, Du A-K, Wang M, Zeng J-B. Morphology and isothermal crystallization of graphene oxide reinforced biodegradable poly(butylene succinate). Polym Test. 2017;59:1–9. doi:10.1016/j.polymertesting.2017.01.014. [Google Scholar] [CrossRef]
212. Wang X, Yang H, Song L, Hu Y, Xing W, Lu H. Morphology, mechanical and thermal properties of graphene-reinforced poly(butylene succinate) nanocomposites. Compos Sci Technol. 2011;72(1):1–6. doi:10.1016/j.compscitech.2011.05.007. [Google Scholar] [CrossRef]
213. Wang XW, Zhang CA, Wang PL, Zhao J, Zhang W, Ji JH, et al. Enhanced performance of biodegradable poly(butylene succinate)/graphene oxide nanocomposites via in situ polymerization. Langmuir. 2012;28(18):7091–5. doi:10.1021/la204894h. [Google Scholar] [PubMed] [CrossRef]
214. Oliveira JT, Correlo VM, Sol PC, Costa-Pinto AR, Malafaya PB, Salgado AJ, et al. Assessment of the suitability of chitosan/polybutylene succinate scaffolds seeded with mouse mesenchymal progenitor cells for a cartilage tissue engineering approach. Tissue Eng Part A. 2008;14(10):1651–61. doi:10.1089/ten.tea.2007.0307. [Google Scholar] [PubMed] [CrossRef]
215. Penas MI, Perez-Camargo RA, Hernandez R, Muller AJ. A review on current strategies for the modulation of thermomechanical, barrier, and biodegradation properties of poly (butylene succinate) (PBS) and its random copolymers. Polymers. 2022;14(5). doi:10.3390/polym14051025. [Google Scholar] [PubMed] [CrossRef]
216. Tan L, Chen Y, Zhou W, Ye S, Wei J. Novel approach toward poly(butylene succinate)/single-walled carbon nanotubes nanocomposites with interfacial-induced crystallization behaviors and mechanical strength. Polymer. 2011;52(16):3587–96. doi:10.1016/j.polymer.2011.06.006. [Google Scholar] [CrossRef]
217. Fadiji T, Rashvand M, Daramola MO, Iwarere SA. A review on antimicrobial packaging for extending the shelf life of food. Processes. 2023;11(2). doi:10.3390/pr11020590. [Google Scholar] [CrossRef]
218. Ge F-F, Yao W-H, Potiyaraj P, Lin J-H, Wu C-S, Meng L, et al. Enhanced PBS nanocomposites with ZnO-Coated MWCNT for extending shelf life in sustainable food packaging applications. J Polym Res. 2024;31(9). doi:10.1007/s10965-024-04125-x. [Google Scholar] [CrossRef]
219. Sawai J. Quantitative evaluation of antibacterial activities of metallic oxide powders (ZnO, MgO and CaO) by conductimetric assay. J Microbiol Methods. 2003;54(2):177–82. doi:10.1016/S0167-7012(03)00037-X. [Google Scholar] [PubMed] [CrossRef]
220. Aydin Sevinc B, Hanley L. Antibacterial activity of dental composites containing zinc oxide nanoparticles. J Biomed Mater Res B Appl Biomater. 2010;94(1):22–31. doi:10.1002/jbm.b.31620. [Google Scholar] [PubMed] [CrossRef]
221. Murariu M, Doumbia A, Bonnaud L, Dechief AL, Paint Y, Ferreira M, et al. High-performance polylactide/ZnO nanocomposites designed for films and fibers with special end-use properties. Biomacromolecules. 2011;12(5):1762–71. doi:10.1021/bm2001445. [Google Scholar] [PubMed] [CrossRef]
222. Threepopnatkul P, Wongnarat C, Intolo W, Suato S, Kulsetthanchalee C. Effect of TiO2 and ZnO on thin film properties of pet/pbs blend for food packaging applications. Energy Proc. 2014;56:102–11. doi:10.1016/j.egypro.2014.07.137. [Google Scholar] [CrossRef]
223. Bhatia A, Gupta R, Bhattacharya S, Choi H. Compatibility of biodegradable poly (lactic acid)(PLA) and poly (butylene succinate)(PBS) blends for packaging application. Korea-Australia Rheol J. 2007;19(3):125–31. [Google Scholar]
224. Monika, Pal AK, Bhasney SM, Bhagabati P, Katiyar V. Effect of dicumyl peroxide on a poly(lactic acid) (PLA)/poly(butylene succinate) (PBS)/functionalized chitosan-based nanobiocomposite for packaging: a reactive extrusion study. ACS Omega. 2018;3(10):13298–312. doi:10.1021/acsomega.8b00907. [Google Scholar] [PubMed] [CrossRef]
225. Totaro G, Sisti L, Celli A, Aloisio I, Di Gioia D, Marek AA, et al. Dual chain extension effect and antibacterial properties of biomolecules interleaved within LDH dispersed into PBS by in situ polymerization. Dalton Trans. 2018;47(9):3155–65. doi:10.1039/c7dt03914j. [Google Scholar] [PubMed] [CrossRef]
226. Song R, Murphy M, Li C, Ting K, Soo C, Zheng Z. Current development of biodegradable polymeric materials for biomedical applications. Drug Des Devel Ther. 2018;12:3117–45. doi:10.2147/dddt.s165440. [Google Scholar] [PubMed] [CrossRef]
227. Li H, Chang J, Cao A, Wang J. In vitro evaluation of biodegradable poly(butylene succinate) as a novel biomaterial. Macromol Biosci. 2005;5(5):433–40. doi:10.1002/mabi.200400183. [Google Scholar] [PubMed] [CrossRef]
228. Mtibe A, Hlekelele L, Kleyi PE, Muniyasamy S, Nomadolo NE, Ofosu O, et al. Fabrication of a polybutylene succinate (PBS)/polybutylene adipate-co-terephthalate (PBAT)-based hybrid system reinforced with lignin and zinc nanoparticles for potential biomedical applications. Polymers. 2022;14(23). doi:10.3390/polym14235065. [Google Scholar] [PubMed] [CrossRef]
229. Ribeiro VP, Ribeiro AS, Silva CJ, Durães NF, Bonifácio G, Correlo VM, editor, et al. Evaluation of novel 3D architectures based on knitting technologies for engineering biological tissues. In: International Conference on Medical Textiles and Healthcare Products; 2013; Raleigh, NC, USA. [Google Scholar]
230. Ranella A, Barberoglou M, Bakogianni S, Fotakis C, Stratakis E. Tuning cell adhesion by controlling the roughness and wettability of 3D micro/nano silicon structures. Acta Biomater. 2010;6(7):2711–20. [Google Scholar] [PubMed]
231. Wang H, Ji J, Zhang W, Zhang Y, Jiang J, Wu Z, et al. Biocompatibility and bioactivity of plasma-treated biodegradable poly(butylene succinate). Acta Biomater. 2009;5(1):279–87. [Google Scholar] [PubMed]
232. Pajoumshariati S, Shirali H, Yavari SK, Sheikholeslami SN, Lotfi G, Mashhadi Abbas F, et al. GBR membrane of novel poly (butylene succinate-co-glycolate) co-polyester co-polymer for periodontal application. Sci Rep. 2018;8(1):7513. doi:10.1038/s41598-018-25952-1. [Google Scholar] [PubMed] [CrossRef]
233. Tang X, Dai J, Sun H, Nabanita S, Petr S, Tang L, et al. Copper-doped nano laponite coating on poly(butylene succinate) scaffold with antibacterial properties and cytocompatibility for biomedical application. J Nanomat. 2018;2018:1–11. doi:10.1155/2018/5470814. [Google Scholar] [CrossRef]
234. Cristofaro F, Gigli M, Bloise N, Chen H, Bruni G, Munari A, et al. Influence of the nanofiber chemistry and orientation of biodegradable poly(butylene succinate)-based scaffolds on osteoblast differentiation for bone tissue regeneration. Nanoscale. 2018;10(18):8689–703. doi:10.1039/C8NR00677F. [Google Scholar] [PubMed] [CrossRef]
235. Ojansivu M, Johansson L, Vanhatupa S, Tamminen I, Hannula M, Hyttinen J, et al. Knitted 3D scaffolds of polybutylene succinate support human mesenchymal stem cell growth and osteogenesis. Stem Cells Int. 2018;2018:5928935. doi:10.1155/2018/5928935. [Google Scholar] [PubMed] [CrossRef]
236. Park SJ, Lee YM, Hong SK. Release behaviors of porous poly(butylene succinate)/poly(epsilon-caprolactone) microcapsules containing indomethacin. Colloids Surf B Biointerfaces. 2006;47(2):211–5. doi:10.1016/j.colsurfb.2005.12.001. [Google Scholar] [PubMed] [CrossRef]
237. Mohanraj K, Sethuraman S, Krishnan UM. Development of poly(butylene succinate) microspheres for delivery of levodopa in the treatment of Parkinson’s disease. J Biomed Mater Res B Appl Biomater. 2013;101(5):840–7. doi:10.1002/jbm.b.32888. [Google Scholar] [PubMed] [CrossRef]
238. Oliveira MB, Queimada AJ, Kontogeorgis GM, Coutinho JAP. Evaluation of the CO2 behavior in binary mixtures with alkanes, alcohols, acids and esters using the Cubic-Plus-Association Equation of State. J Supercrit Fluids. 2011;55(3):876–92. doi:10.1016/j.supflu.2010.09.036. [Google Scholar] [CrossRef]
239. Costa-Pinto AR, Correlo VM, Sol PC, Bhattacharya M, Srouji S, Livne E, et al. Chitosan-poly(butylene succinate) scaffolds and human bone marrow stromal cells induce bone repair in a mouse calvaria model. J Tissue Eng Regen Med. 2012;6(1):21–8. doi:10.1002/term.391. [Google Scholar] [PubMed] [CrossRef]
240. Deepthi S, Viha C, Thitirat C, Furuike T, Tamura H, Jayakumar R. Fabrication of chitin/poly(butylene succinate)/chondroitin sulfate nanoparticles ternary composite hydrogel scaffold for skin tissue engineering. Polymers. 2014;6(12):2974–84. doi:10.3390/polym6122974. [Google Scholar] [CrossRef]
241. Cheng HH, Xiong J, Xie ZN, Zhu YT, Liu YM, Wu ZY, et al. Thrombin–loaded poly(butylene succinate)–based electrospun membranes for rapid hemostatic application. Macromol Mater Eng. 2017;303(2). doi:10.1002/mame.201700395. [Google Scholar] [CrossRef]
242. Sobolewski P, Murthy NS, Kohn J, El Fray M. Adsorption of fibrinogen and fibronectin on elastomeric Poly(butylene succinate) copolyesters. Langmuir. 2019;35(26):8850–9. doi:10.1021/acs.langmuir.9b01119. [Google Scholar] [PubMed] [CrossRef]
243. Zhang S, Wang L, Yang S, Gong Y. Improved biocompatibility of phosphorylcholine end-capped poly(butylene succinate). Sci China Chem. 2012;56(2):174–80. [Google Scholar]
244. Huang A, Peng X, Geng L, Zhang L, Huang K, Chen B, et al. Electrospun poly(butylene succinate)/cellulose nanocrystals bio-nanocomposite scaffolds for tissue engineering: preparation, characterization and in vitro evaluation. Polym Test. 2018;71:101–9. doi:10.1016/j.polymertesting.2018.08.027. [Google Scholar] [CrossRef]
245. Costa-Pinto AR, Martins AM, Castelhano-Carlos MJ, Correlo VM, Sol PC, Longatto-Filho A, et al. In vitro degradation and in vivo biocompatibility of chitosan-poly(butylene succinate) fiber mesh scaffolds. J Bioact Compat Polym. 2014;29(2):137–51. [Google Scholar]
246. Jäger A, Gromadzki D, Jäger E, Giacomelli FC, Kozlowska A, Kobera L, et al. Novel soft biodegradable nanoparticles prepared from aliphatic based monomers as a potential drug delivery system. Soft Matter. 2012;8(16). doi:10.1039/c2sm07247e. [Google Scholar] [CrossRef]
247. Jager E, Jager A, Chytil P, Etrych T, Rihova B, Giacomelli FC, et al. Combination chemotherapy using core-shell nanoparticles through the self-assembly of HPMA-based copolymers and degradable polyester. J Control Release. 2013;165(2):153–61. doi:10.1016/j.jconrel.2012.11.009. [Google Scholar] [PubMed] [CrossRef]
248. Ribeiro VP, Almeida LR, Martins AR, Pashkuleva I, Marques AP, Ribeiro AS, et al. Modulating cell adhesion to polybutylene succinate biotextile constructs for tissue engineering applications. J Tissue Eng Regen Med. 2017;11(10):2853–63. doi:10.1002/term.2189. [Google Scholar] [PubMed] [CrossRef]
249. Dominguez-Robles J, Larraneta E, Fong ML, Martin NK, Irwin NJ, Mutje P, et al. Lignin/poly(butylene succinate) composites with antioxidant and antibacterial properties for potential biomedical applications. Int J Biol Macromol. 2020;145:92–9. doi:10.1016/j.ijbiomac.2019.12.146. [Google Scholar] [PubMed] [CrossRef]
250. Wang X, Song L, Yang H, Lu H, Hu Y. Synergistic effect of graphene on antidripping and fire resistance of intumescent flame retardant poly(butylene succinate)composites. Ind Eng Chem Res. 2011;50(9):5376–83. doi:10.1021/ie102566y. [Google Scholar] [CrossRef]
251. Liu YJ, Mao L, Sh Fan. Preparation and study of intumescent flame retardant poly(butylene succinate) using MgAlZnFe–CO3 layered double hydroxide as a synergistic agent. J Appl Polym Sci. 2014;131(17). doi:10.1002/app.40736. [Google Scholar] [CrossRef]
252. Chen H, Wen X, Guan Y, Min J, Wen Y, Yang H, et al. Effect of particle size on the flame retardancy of poly(butylene succinate)/Mg(OH)2 composites. Fire Mater. 2016;40(8):1090–6. doi:10.1002/fam.2355. [Google Scholar] [CrossRef]
253. Wang Y, Zhang S, Wu X, Lu C, Cai Y, Ma L, et al. Effect of montmorillonite on the flame-resistant and mechanical properties of intumescent flame-retardant poly(butylene succinate) composites. J Therm Anal Calorim. 2017;128(3):1417–27. doi:10.1007/s10973-017-6092-z. [Google Scholar] [CrossRef]
254. Gu L, Zhang S, Li H, Sun J, Tang W, Zhao L, et al. Preparation of intumescent flame retardant poly(butylene succinate) using urea intercalated kaolinite as synergistic agent. Fibers Polym. 2019;20(8):1631–40. doi:10.1007/s12221-019-7999-8. [Google Scholar] [CrossRef]
255. Zhou X, Wu T. Synthesis, characterization of phosphorus-containing copolyester and its application as flame retardants for poly(butylene succinate) (PBS). Chemosphere. 2019;235:163–8. doi:10.1016/j.chemosphere.2019.06.151. [Google Scholar] [PubMed] [CrossRef]
256. Dumazert L, Rasselet D, Pang B, Gallard B, Kennouche S, Lopez–Cuesta JM. Thermal stability and fire reaction of poly(butylene succinate) nanocomposites using natural clays and FR additives. Polym Adv Technol. 2018;29(1):69–83. doi:10.1002/pat.4090. [Google Scholar] [CrossRef]
257. Wang Y, Liu C, Shi X, Liang J, Jia Z, Shi G. Synergistic effect of halloysite nanotubes on flame resistance of intumescent flame retardant poly(butylene succinate) composites. Polym Compos. 2017;40(1):202–9. doi:10.1002/pc.24629. [Google Scholar] [CrossRef]
258. Wang Y, Liu C, Lai J, Lu C, Wu X, Cai Y, et al. Soy protein and halloysite nanotubes-assisted preparation of environmentally friendly intumescent flame retardant for poly(butylene succinate). Polym Test. 2020;81. doi:10.1016/j.polymertesting.2019.106174. [Google Scholar] [CrossRef]
259. Chen S, Wu F, Hu Y, Lin S, Yu C, Zhu F, et al. A fully bio-based intumescent flame retardant for poly(butylene succinate). Mater Chem Phys. 2020;252. doi:10.1016/j.matchemphys.2020.123222. [Google Scholar] [CrossRef]
260. Hu C, Bourbigot S, Delaunay T, Collinet M, Marcille S, Fontaine G. Poly(isosorbide carbonatea ‘green’ char forming agent in polybutylene succinate intumescent formulation. Compos Part B: Eng. 2020;184:107675. doi:10.1016/j.compositesb.2019.107675. [Google Scholar] [CrossRef]
261. Jiang S, Yang Y, Ge S, Zhang Z, Peng W. Preparation and properties of novel flame-retardant PBS wood-plastic composites. Arab J Chem. 2018;11(6):844–57. doi:10.1016/j.arabjc.2017.12.023. [Google Scholar] [CrossRef]
262. Yue X, Li J, Liu P, Pu W, Lin Y. Investigation of flame-retarded poly(butylene succinate) composites using MHSH as synergistic and reinforced agent. J Mater Sci. 2017;53(7):5004–15. doi:10.1007/s10853-017-1915-7. [Google Scholar] [CrossRef]
263. Liu P, Yue X, He G, Zhang X, Sun Y. Influence of modified fiber-MHSH hybrids on fire hazards, combustion dynamics, and mechanical properties of flame–retarded poly(butylene succinate) composites. J Appl Polym Sci. 2019;137(12). doi:10.1002/app.48490. [Google Scholar] [CrossRef]
264. He L, Shi Y, Wang Q, Chen D, Shen J, Guo S. Strategy for constructing electromagnetic interference shielding and flame retarding synergistic network in poly (butylene succinate) and thermoplastic polyurethane multilayered composites. Compos Sci Technol. 2020;199. doi:10.1016/j.compscitech.2020.108324. [Google Scholar] [CrossRef]
265. Rashid M, Chetehouna K, Cablé A, Gascoin N. Analysing flammability characteristics of green biocomposites: an overview. Fire Technol. 2020;57(1):31–67. doi:10.1007/s10694-020-01001-0. [Google Scholar] [CrossRef]
266. Brodhagen M, Peyron M, Miles C, Inglis DA. Biodegradable plastic agricultural mulches and key features of microbial degradation. Appl Microbiol Biotechnol. 2015;99(3):1039–56. doi:10.1007/s00253-014-6267-5. [Google Scholar] [PubMed] [CrossRef]
267. Kumar R, Verma A, Shome A, Sinha R, Sinha S, Jha PK, et al. Impacts of plastic pollution on ecosystem services, sustainable development goals, and need to focus on circular economy and policy interventions. Sustainability. 2021;13(17). doi:10.3390/su13179963. [Google Scholar] [CrossRef]
268. Ali SS, Elsamahy T, Koutra E, Kornaros M, El-Sheekh M, Abdelkarim EA, et al. Degradation of conventional plastic wastes in the environment: a review on current status of knowledge and future perspectives of disposal. Sci Total Environ. 2021;771:144719. doi:10.1016/j.scitotenv.2020.144719. [Google Scholar] [PubMed] [CrossRef]
269. King CD, Stephens CG, Lynch JP, Jordan SN. Farmers’ attitudes towards agricultural plastics—management and disposal, awareness and perceptions of the environmental impacts. Sci Total Environ. 2023;864:160955. doi:10.1016/j.scitotenv.2022.160955. [Google Scholar] [PubMed] [CrossRef]
270. Koul B, Yakoob M, Shah MP. Agricultural waste management strategies for environmental sustainability. Environ Res. 2022;206:112285. doi:10.1016/j.envres.2021.112285. [Google Scholar] [PubMed] [CrossRef]
271. Mansoor Z, Tchuenbou-Magaia F, Kowalczuk M, Adamus G, Manning G, Parati M, et al. Polymers use as mulch films in agriculture-A review of history, problems and current trends. Polymers. 2022;14(23). doi:10.3390/polym14235062. [Google Scholar] [PubMed] [CrossRef]
272. Salimi M, Channab BE, El Idrissi A, Zahouily M, Motamedi E. A comprehensive review on starch: structure, modification, and applications in slow/controlled-release fertilizers in agriculture. Carbohydr Polym. 2023;322:121326. doi:10.1016/j.carbpol.2023.121326. [Google Scholar] [PubMed] [CrossRef]
273. Jariwala H, Santos RM, Lauzon JD, Dutta A, Wai Chiang Y. Controlled release fertilizers (CRFs) for climate-smart agriculture practices: a comprehensive review on release mechanism, materials, methods of preparation, and effect on environmental parameters. Environ Sci Pollut Res Int. 2022;29(36):53967–95. doi:10.1007/s11356-022-20890-y. [Google Scholar] [PubMed] [CrossRef]
274. Serrano-Ruiz H, Martin-Closas L, Pelacho AM. Biodegradable plastic mulches: impact on the agricultural biotic environment. Sci Total Environ. 2021;750:141228. doi:10.1016/j.scitotenv.2020.141228. [Google Scholar] [PubMed] [CrossRef]
275. Salimi M, El Idrissi A, Channab B-E, Essamlali Y, Firouzabadi AG, Beygi M, et al. Cellulose-based controlled release fertilizers for sustainable agriculture: Recent trends and future perspectives. Cellulose. 2024;31(18):10679–726. doi:10.1007/s10570-024-06273-1. [Google Scholar] [CrossRef]
276. Iqbal R, Raza MAS, Valipour M, Saleem MF, Zaheer MS, Ahmad S, et al. Potential agricultural and environmental benefits of mulches—a review. Bulletin National Res Centre. 2020;44(1). doi:10.1186/s42269-020-00290-3. [Google Scholar] [CrossRef]
277. Madin M, Nelson K, Fatema K, Schoengold K, Dalal A, Onyekwelu I, et al. Synthesis of current evidence on factors influencing the suitability of synthetic biodegradable mulches for agricultural applications: a systematic review. J Agric Food Res. 2024;16. doi:10.1016/j.jafr.2024.101095. [Google Scholar] [CrossRef]
278. Song Z, Zhao L, Bi J, Tang Q, Wang G, Li Y. Classification of degradable mulch films and their promotional effects and limitations on agricultural production. Agriculture. 2024;14(8). doi:10.3390/agriculture14081235. [Google Scholar] [CrossRef]
279. Menossi M, Cisneros M, Alvarez VA, Casalongué C. Current and emerging biodegradable mulch films based on polysaccharide bio-composites. A review. Agron Sustain Dev. 2021;41(4). doi:10.1007/s13593-021-00685-0. [Google Scholar] [CrossRef]
280. Paul V, Muniyasamy S, Kanny K, Joseph Botlhoko O, Sivakumar PM, Mostafa K. Improving the performance and biodegradability of biocomposites made from banana sap and banana fibres. J Chem. 2024;2024(1). doi:10.1155/2024/8503770. [Google Scholar] [CrossRef]
281. Kabir E, Kaur R, Lee J, Kim K-H, Kwon EE. Prospects of biopolymer technology as an alternative option for non-degradable plastics and sustainable management of plastic wastes. J Clean Prod. 2020;258. doi:10.1016/j.jclepro.2020.120536. [Google Scholar] [CrossRef]
282. Polman EMN, Gruter GM, Parsons JR, Tietema A. Comparison of the aerobic biodegradation of biopolymers and the corresponding bioplastics: a review. Sci Total Environ. 2021;753:141953. doi:10.1016/j.scitotenv.2020.141953. [Google Scholar] [PubMed] [CrossRef]
283. Dintcheva NT. Overview of polymers and biopolymers degradation and stabilization towards sustainability and materials circularity. Polymer. 2024;306. doi:10.1016/j.polymer.2024.127136. [Google Scholar] [CrossRef]
284. Ayu RS, Khalina A, Harmaen AS, Zaman K, Jawaid M, Lee CH. Effect of modified tapioca starch on mechanical, thermal, and morphological properties of PBS blends for food packaging. Polymers. 2018;10(11). doi:10.3390/polym10111187. [Google Scholar] [PubMed] [CrossRef]
285. Munteanu SB, Vasile C. Vegetable additives in food packaging polymeric materials. Polymers. 2019;12(1). doi:10.3390/polym12010028. [Google Scholar] [PubMed] [CrossRef]
286. Hongsriphan N, Pinpueng A. Properties of agricultural films prepared from biodegradable poly(butylene succinate) adding natural sorbent and fertilizer. J Polym Environ. 2019;27(2):434–43. doi:10.1007/s10924-018-1358-5. [Google Scholar] [CrossRef]
287. Bi S, Barinelli V, Sobkowicz MJ. Degradable controlled release fertilizer composite prepared via extrusion: fabrication, characterization, and release mechanisms. Polymers. 2020;12(2). doi:10.3390/polym12020301. [Google Scholar] [PubMed] [CrossRef]
288. Baldanza VAR, Souza FG, Filho ST, Franco HA, Oliveira GE, Caetano RMJ, et al. Controlled–release fertilizer based on poly(butylene succinate)/urea/clay and its effect on lettuce growth. J Appl Polym Sci. 2018;135(47). doi:10.1002/app.46858. [Google Scholar] [CrossRef]
289. Lawrencia D, Wong SK, Low DYS, Goh BH, Goh JK, Ruktanonchai UR, et al. Controlled release fertilizers: a review on coating materials and mechanism of release. Plants. 2021;10(2):1. doi:10.3390/plants10020238. [Google Scholar] [PubMed] [CrossRef]
290. Li Y, Zhang M, Weng Y, Wang L, Song J. Effects of microencapsulated abamectin on the mechanical, cross-linking, and release properties of PBS. Colloids Surf B Biointerfaces. 2020;196:111290. doi:10.1016/j.colsurfb.2020.111290. [Google Scholar] [PubMed] [CrossRef]
291. Ye H-M, Li H-F, Wang C-S, Yang J, Huang G, Meng X, et al. Degradable polyester/urea inclusion complex applied as a facile and environment-friendly strategy for slow-release fertilizer: performance and mechanism. Chem Eng J. 2020;381. doi:10.1016/j.cej.2019.122704. [Google Scholar] [CrossRef]
292. Kim MN, Shin JH, Im SS. Effect of poly(l-lactide) and poly(butylene succinate) on the growth of red pepper and tomato. J Polym Environ. 2003;11(3):101–5. doi:10.1023/A:1024683014153. [Google Scholar] [CrossRef]
293. Jiao H, Ali SS, Alsharbaty MHM, Elsamahy T, Abdelkarim E, Schagerl M, et al. A critical review on plastic waste life cycle assessment and management: challenges, research gaps, and future perspectives. Ecotoxicol Environ Saf. 2024;271:115942. doi:10.1016/j.ecoenv.2024.115942. [Google Scholar] [PubMed] [CrossRef]
294. Roy P, Mohanty AK, Misra M. Microplastics in ecosystems: their implications and mitigation pathways. Environ Sci: Adv. 2022;1(1):9–29. doi:10.1039/D1VA00012H. [Google Scholar] [CrossRef]
295. Mihai F-C, Gündoğdu S, Markley LA, Olivelli A, Khan FR, Gwinnett C, et al. Plastic pollution, waste management issues, and circular economy opportunities in rural communities. Sustainability. 2021;14(1). doi:10.3390/su14010020. [Google Scholar] [CrossRef]
296. Kong U, Mohammad Rawi NF, Tay GS. The potential applications of reinforced bioplastics in various industries: a review. Polymers. 2023;15(10). doi:10.3390/polym15102399. [Google Scholar] [PubMed] [CrossRef]
297. Lakhiar IA, Yan H, Zhang J, Wang G, Deng S, Bao R, et al. Plastic pollution in agriculture as a threat to food security, the ecosystem, and the environment: an overview. Agronomy. 2024;14(3). doi:10.3390/agronomy14030548. [Google Scholar] [CrossRef]
298. Nøklebye E, Adam HN, Roy-Basu A, Bharat GK, Steindal EH. Plastic bans in India—addressing the socio-economic and environmental complexities. Environ Sci Policy. 2023;139:219–27. doi:10.1016/j.envsci.2022.11.005. [Google Scholar] [CrossRef]
299. Rizan C, Mortimer F, Stancliffe R, Bhutta MF. Plastics in healthcare: time for a re-evaluation. J R Soc Med. 2020;113(2):49–53. doi:10.1177/0141076819890554. [Google Scholar] [PubMed] [CrossRef]
300. Muniyasamy S, Anstey A, Reddy MM, Misra M, Mohanty A. Biodegradability and compostability of lignocellulosic based composite materials. J Renew Mater. 2013;1(4):253–72. doi:10.7569/JRM.2013.634117. [Google Scholar] [CrossRef]
301. Bhagwat G, Gray K, Wilson SP, Muniyasamy S, Vincent SGT, Bush R, et al. Benchmarking bioplastics: a natural step towards a sustainable future. J Polym Environ. 2020;28(12):3055–75. doi:10.1007/s10924-020-01830-8. [Google Scholar] [CrossRef]
302. Islam M, Xayachak T, Haque N, Lau D, Bhuiyan M, Pramanik BK. Impact of bioplastics on environment from its production to end-of-life. Process Saf Environ Prot. 2024;188:151–66. doi:10.1016/j.psep.2024.05.113. [Google Scholar] [CrossRef]
303. Pooja N, Chakraborty I, Rahman MH, Mazumder N. An insight on sources and biodegradation of bioplastics: a review. 3 Biotech. 2023;13(7):220. doi:10.1007/s13205-023-03638-4. [Google Scholar] [PubMed] [CrossRef]
304. Amulya K, Katakojwala R, Ramakrishna S, Venkata Mohan S. Low carbon biodegradable polymer matrices for sustainable future. Compos Part C: Open Access. 2021;4. doi:10.1016/j.jcomc.2021.100111. [Google Scholar] [CrossRef]
305. Benavides PT, Lee U, Zarè-Mehrjerdi O. Life cycle greenhouse gas emissions and energy use of polylactic acid, bio-derived polyethylene, and fossil-derived polyethylene. J Clean Prod. 2020;277. doi:10.1016/j.jclepro.2020.124010. [Google Scholar] [CrossRef]
306. Mosomi EK, Olanrewaju OA, Adeosun SO. Pivotal role of polylactide in carbon emission reduction: a comprehensive review. Eng Rep. 2024;6(8). doi:10.1002/eng2.12909. [Google Scholar] [CrossRef]
307. Chen Q, Hu N, Zhang Q, Sun H, Zhu L. Effects of biodegradable plastic film mulching on the global warming potential, carbon footprint, and economic benefits of garlic production. Agronomy. 2024;14(3). doi:10.3390/agronomy14030504. [Google Scholar] [CrossRef]
308. Zhu J, Wang C. Biodegradable plastics: green hope or greenwashing? Mar Pollut Bull. 2020;161(Pt B):111774. doi:10.1016/j.marpolbul.2020.111774. [Google Scholar] [PubMed] [CrossRef]
309. Ghasemlou M, Barrow CJ, Adhikari B. The future of bioplastics in food packaging: an industrial perspective. Food Packag Shelf Life. 2024;43. doi:10.1016/j.fpsl.2024.101279. [Google Scholar] [CrossRef]
310. Al-Khairy D, Fu W, Alzahmi AS, Twizere JC, Amin SA, Salehi-Ashtiani K, et al. Closing the gap between bio-based and petroleum-based plastic through bioengineering. Microorganisms. 2022;10(12). doi:10.3390/microorganisms10122320. [Google Scholar] [PubMed] [CrossRef]
311. Himantha Kelaniyagama S, Gannoruwa A, Renuka Nilmini AHL. Synthesize and applications of biodegradable plastics as a solution for environmental pollution due to non-biodegradable plastics, a review. Sustain Poly Energy. 2024;2(4):10011. doi:10.70322/spe.2024.10011. [Google Scholar] [CrossRef]
312. Kumar A, Mishra RK, Verma K, Aldosari SM, Maity CK, Verma S, et al. A comprehensive review of various biopolymer composites and their applications: from biocompatibility to self-healing. Mater Today Sustain. 2023;23. doi:10.1016/j.mtsust.2023.100431. [Google Scholar] [CrossRef]
313. Narancic T, Cerrone F, Beagan N, O’Connor KE. Recent advances in bioplastics: application and biodegradation. Polymers. 2020;12(4). doi:10.3390/polym12040920. [Google Scholar] [PubMed] [CrossRef]
314. Silva RRA, Marques CS, Arruda TR, Teixeira SC, de Oliveira TV. Biodegradation of polymers: stages, measurement, standards and prospects. Macromol. 2023;3(2):371–99. doi:10.3390/macromol3020023. [Google Scholar] [CrossRef]
315. Mastropetros SG, Pispas K, Zagklis D, Ali SS, Kornaros M. Biopolymers production from microalgae and cyanobacteria cultivated in wastewater: recent advances. Biotechnol Adv. 2022;60:107999. doi:10.1016/j.biotechadv.2022.107999. [Google Scholar] [PubMed] [CrossRef]
316. Srikanth M, Sandeep T, Sucharitha K, Godi S. Biodegradation of plastic polymers by fungi: a brief review. Bioresour Bioprocess. 2022;9(1):42. doi:10.1186/s40643-022-00532-4. [Google Scholar] [PubMed] [CrossRef]
317. Mohee R, Unmar G. Determining biodegradability of plastic materials under controlled and natural composting environments. Waste Manag. 2007;27(11):1486–93. doi:10.1016/j.wasman.2006.07.023. [Google Scholar] [PubMed] [CrossRef]
318. Mohanan N, Montazer Z, Sharma PK, Levin DB. Microbial and enzymatic degradation of synthetic plastics. Front Microbiol. 2020;11:580709. doi:10.3389/fmicb.2020.580709. [Google Scholar] [PubMed] [CrossRef]
319. Okal EJ, Heng G, Magige EA, Khan S, Wu S, Ge Z, et al. Insights into the mechanisms involved in the fungal degradation of plastics. Ecotoxicol Environ Saf. 2023;262:115202. doi:10.1016/j.ecoenv.2023.115202. [Google Scholar] [PubMed] [CrossRef]
320. Chow J, Perez-Garcia P, Dierkes R, Streit WR. Microbial enzymes will offer limited solutions to the global plastic pollution crisis. Microb Biotechnol. 2023;16(2):195–217. doi:10.1111/1751-7915.14135. [Google Scholar] [PubMed] [CrossRef]
321. Zheng Y, Yanful EK, Bassi AS. A review of plastic waste biodegradation. Crit Rev Biotechnol. 2005;25(4):243–50. doi:10.1080/07388550500346359. [Google Scholar] [PubMed] [CrossRef]
322. Bahl S, Dolma J, Jyot Singh J, Sehgal S. Biodegradation of plastics: a state of the art review. Mater Today: Proc. 2021;39:31–4. doi:10.1016/j.matpr.2020.06.096. [Google Scholar] [CrossRef]
323. Shah AA, Hasan F, Hameed A, Ahmed S. Biological degradation of plastics: a comprehensive review. Biotechnol Adv. 2008;26(3):246–65. doi:10.1016/j.biotechadv.2007.12.005. [Google Scholar] [PubMed] [CrossRef]
324. Hu X, Gao Z, Wang Z, Su T, Yang L, Li P. Enzymatic degradation of poly(butylene succinate) by cutinase cloned from Fusarium solani. Polym Degrad Stab. 2016;134:211–9. doi:10.1016/j.polymdegradstab.2016.10.012. [Google Scholar] [CrossRef]
325. Anstey A, Muniyasamy S, Reddy MM, Misra M, Mohanty A. Processability and biodegradability evaluation of composites from poly(butylene succinate) (PBS) bioplastic and biofuel co-products from Ontario. J Polym Environ. 2014;22(2):209–18. doi:10.1007/s10924-013-0633-8. [Google Scholar] [CrossRef]
326. Ciuffi B, Fratini E, Rosi L. Plastic pretreatment: the key for efficient enzymatic and biodegradation processes. Polym Degrad Stab. 2024;222. doi:10.1016/j.polymdegradstab.2024.110698. [Google Scholar] [CrossRef]
327. Cai Z, Li M, Zhu Z, Wang X, Huang Y, Li T, et al. Biological degradation of plastics and microplastics: a recent perspective on associated mechanisms and influencing factors. Microorganisms. 2023;11(7). doi:10.3390/microorganisms11071661. [Google Scholar] [PubMed] [CrossRef]
328. Huang C, Liao Y, Zou Z, Chen Y, Jin M, Zhu J, et al. Novel strategy to interpret the degradation behaviors and mechanisms of bio- and non-degradable plastics. J Clean Prod. 2022;355. doi:10.1016/j.jclepro.2022.131757. [Google Scholar] [CrossRef]
329. Agarwal S. Biodegradable polymers: present opportunities and challenges in providing a microplastic–free environment. Macromol Chem Phys. 2020;221(6). doi:10.1002/macp.202000017. [Google Scholar] [CrossRef]
330. Adhikari D, Mukai M, Kubota K, Kai T, Kaneko N, Araki KS, et al. Degradation of bioplastics in soil and their degradation effects on environmental microorganisms. J Agric Chem Environ. 2016;5(1):23–34. doi:10.4236/jacen.2016.51003. [Google Scholar] [CrossRef]
331. Sasimowski E, Majewski L, Grochowicz M. Study on the biodegradation of poly(butylene succinate)/wheat bran biocomposites. Materials. 2023;16(21). doi:10.3390/ma16216843. [Google Scholar] [PubMed] [CrossRef]
332. Folino A, Pangallo D, Calabrò PS. Assessing bioplastics biodegradability by standard and research methods: current trends and open issues. J Environ Chem Eng. 2023;11(2). doi:10.1016/j.jece.2023.109424. [Google Scholar] [CrossRef]
333. Ratto JA, Stenhouse PJ, Auerbach M, Mitchell J, Farrell R. Processing, performance and biodegradability of a thermoplastic aliphatic polyester/starch system. Polymer. 1999;40(24):6777–88. doi:10.1016/S0032-3861(99)00014-2. [Google Scholar] [CrossRef]
334. Fan P, Yu H, Xi B, Tan W. A review on the occurrence and influence of biodegradable microplastics in soil ecosystems: are biodegradable plastics substitute or threat? Environ Int. 2022;163:107244. doi:10.1016/j.envint.2022.107244. [Google Scholar] [PubMed] [CrossRef]
335. Samir A, Ashour FH, Hakim AAA, Bassyouni M. Recent advances in biodegradable polymers for sustainable applications. npj Mater Degrad. 2022;6(1). doi:10.1038/s41529-022-00277-7. [Google Scholar] [CrossRef]
336. Nelson TF, Baumgartner R, Jaggi M, Bernasconi SM, Battagliarin G, Sinkel C, et al. Biodegradation of poly(butylene succinate) in soil laboratory incubations assessed by stable carbon isotope labelling. Nat Commun. 2022;13(1):5691. doi:10.1038/s41467-022-33064-8. [Google Scholar] [PubMed] [CrossRef]
Cite This Article
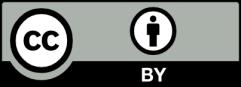
This work is licensed under a Creative Commons Attribution 4.0 International License , which permits unrestricted use, distribution, and reproduction in any medium, provided the original work is properly cited.