Open Access
ARTICLE
Polymer Resins Synthesized via the Michael 1,4-addition from Tall Oil Fatty Acids Using Various Epoxidation Techniques
Latvian State Institute of Wood Chemistry, Riga, LV-1047, Latvia
* Corresponding Author: Aiga Ivdre. Email:
(This article belongs to the Special Issue: Advances in Biorefinery Technologies and Products – 2024)
Journal of Renewable Materials 2025, 13(2), 349-361. https://doi.org/10.32604/jrm.2024.056820
Received 31 July 2024; Accepted 23 October 2024; Issue published 20 February 2025
Abstract
Studies on the use of renewable materials for various applications, including polymers, have gained momentum due to global climate change and the push towards a circular economy. In this study, polymer resins were developed through Michael 1,4-addition. The precursors were synthesized from tall oil-based acetoacetates derived from epoxidized tall oil fatty acids or their methyl esters. Two different epoxidation methods were employed: enzymatic epoxidation of tall oil fatty acids and ion-exchange resin epoxidation of tall oil fatty acid methyl esters. Following oxirane opening and transesterification with trimethylolpropane, further esterification or transesterification was carried out to obtain the acetoacetates. These synthesized acetoacetates were then reacted with acrylates of various functionalities to obtain polymer resins with differing degrees of crosslinking. The developed polymer resins were characterized using differential scanning calorimetry, dynamic mechanical analysis, and thermogravimetric analysis. The results indicated that the glass transition temperature and storage modulus of the polymer resins were significantly influenced by both the functionality of the acrylates used and the epoxidation technique employed. Higher acrylate functionality resulted in increased stiffness, while enzymatic epoxidation enhanced the polymer’s mechanical properties, nearly doubling the storage modulus, achieving approximately 470 MPa, compared to the ion-exchange resin technique. Therefore, selecting the appropriate acrylate functionality and epoxidation method could tailor the mechanical properties of the polymer resins.Keywords
Nomenclature
DMA | Dynamic mechanical analysis |
DSC | Differential scanning calorimetry |
DTG | Derivative thermogravimetry |
EETOFA | Epoxidized tall oil fatty acids via enzymatic epoxidation |
EETOFA_TMP | Polyol synthesized from EETOFA through oxirane ring-opening, followed by transesterification with trimethylolpropane |
EETOFA_TMP_AA | Acetoaceate obtained from EETOFA_TMP, subsequently reacted with tert-butyl acetoacetate |
EIRTOFA | Epoxidized tall oil fatty acids with ion-exchange resin |
EIRTOFAME_TMP | Polyol synthesized from EIRTOFA through oxirane ring-opening, followed by transesterification with trimethylolpropane |
EIRTOFAME_TMP_AA | Acetoacetate obtained from EIRTOFAME_TMP reacted with tert-butyl acetoacetate |
HDODA | Hexanediol diacrylate |
PETA | Pentaerythritol tetraacrylate |
TGA | Thermal gravimetry analysis |
Tmax1 | The first maximum of DTG peaks |
Tmax2 | The second maximum of DTG peaks |
TMG | 1,1,3,3-tetramethylguanidine |
TMP | Trimethylolpropane |
TMPTA | Trimethylolpropane triacrylate |
Tm5% | Temperature at a weight loss of 5% |
Tm10% | Temperature at a weight loss of 10% |
TOFA | Tall oil fatty acids |
TOFAME | Tall oil fatty acids methyl ester |
Tonset | Onset temperature |
The increasing environmental challenges of climate change and resource depletion have underscored the urgency for sustainable development practices. Renewable materials have emerged as a critical component in this paradigm shift, offering a viable alternative to traditional, fossil-based resources. The concept of a circular economy, which emphasizes resource efficiency, waste reduction, and the continual use of resources, has gained significant traction globally [1,2]. In Europe, stringent directives and regulations, such as the European Green Deal and the Circular Economy Action Plan, drive the transition towards sustainable materials and processes [3]. Developing and utilizing renewable materials, including those used to produce polymers, are integral to achieving these ambitious environmental goals and fostering a resilient and sustainable future [4].
Renewable sources have evolved significantly, starting from the first generation, which competes with the food industry, to the fourth generation, which includes genetically modified resources [5]. Tall oil, a byproduct of the Kraft pulping process in the paper industry, stands out as a promising second-generation bio-based material. Unlike first-generation bio-based materials that compete with food resources, tall oil derives from waste streams, making it a more sustainable option. Rich in fatty and resin acids, tall oil can be refined into valuable chemicals and materials [6,7], including adhesives [8,9], coatings [10], surfactants [11,12], rigid foams [13,14], and various types of films and resins [15,16] such as polyesters, polyethers, polyurethanes, polyamides, epoxy resins, alkyd resins [6], polyacrylates [17] and resins obtained via Michael 1,4-addition [18].
Polymer resins derived from tall oil fatty acids (TOFA) exhibit a wide range of thermal and mechanical properties. The glass transition temperature of polyester urethane films from TOFA has been reported at around 60°C, which is lower than that of poly (urethane amides) at approximately 65°C. The modulus of elasticity for these materials varies between 0.5 and 1.0 GPa, and they remain thermally stable up to 225°C [16]. TOFA-based alkyd resins and alkyd–acrylate copolymers have a glass transition temperature of around 40°C [15]. Hyperbranched alkyd resins from TOFA, as reported by Murillo et al., display a glass transition temperature ranging from −50°C to −5°C and a thermal decomposition temperature between 253°C and 296°C [19]. Rodriguez-Tobias et al. studied poly(acrylate)s synthesized from fatty acid-based methacrylate monomers, including TOFA. The resulting acrylic paints and coatings, demonstrated excellent drying times. However, their mechanical performance—particularly in terms of flexion, impact resistance, and adhesion—was moderate to poor. The glass transition temperatures of these coatings ranged from ~53°C to ~69°C [17]. TOFA-based polymer resins obtained via Michael 1,4-addition have shown glass transition temperatures between 21°C and 63°C, Young’s modulus ranging from 8 MPa to 2.7 GPa, and thermal stability up to 300°C [18]. In the realm of sustainable polymers, resins produced via Michael 1,4-addition represent a notable advancement. This chemical process involves the reaction between an electron-deficient olefin and a nucleophile, typically an amine or thiol, resulting in a robust network of cross-linked polymers [20]. TOFA can be employed as precursors to obtain polyols after epoxidation and esterification. Further acetoacetylation gives acetoacetates as Michael donor. Reacted with various acrylates, cross-linked polymers can be obtained. The versatility of Michael 1,4-addition allows for the incorporation of various bio-based monomers, enhancing the material properties and expanding their application range [21]. By leveraging bio-based inputs and innovative chemical processes, the development of sustainable polymers continues to progress, offering significant potential for reducing environmental impact and advancing green chemistry.
In the chemical route for Michael donor and/or acceptor synthesis from TOFA, epoxidation is required. This process can be achieved through various techniques. Enzymatic epoxidation utilizes specific enzymes to catalyze the reaction, providing a mild and environmentally friendly approach [22]. Ion exchange resin epoxidation employs ion exchange resins to facilitate the process, offering a reusable and efficient method [23]. Traditional chemical epoxidation methods, such as using peracids or hydrogen peroxide, are also widely used. Additionally, a methylation step can be introduced before epoxidation to enhance the process. Each technique presents distinct advantages, allowing for selection based on the desired efficiency, environmental impact, and application requirements [24,25].
This study aimed to develop polymer resins via Michael 1,4-addition using TOFA, which were modified through two distinct chemical routes. The first route involved the enzymatic epoxidation of TOFA, followed by oxirane ring opening and esterification with trimethylolpropane (TMP). The second route started with the methylation of TOFA, followed by the epoxidation of the resulting TOFA methyl esters (TOFAME) using ion exchange resin, and subsequent oxirane ring opening and transesterification with TMP. A comprehensive comparison of these methods was conducted, focusing on the resulting polyols and polymer resins. The study discussed the efficiency, environmental impact, and evaluated material properties of the polyols and resins obtained from each method, providing insights into how various epoxidation techniques influence the production of sustainable polymer resins from TOFA.
The primary bio-based raw material for acetoacetate synthesis was TOFA, with an acid value of 198 mg KOH/g and an iodine value of 155 g I2/100 g. Sourced from Forchem Oyj (Rauma, Finland), it comprised over 96% fatty acids, with less than 2% rosin and unsaponifiables. TOFA consists mainly of oleic and linoleic acids with small amounts of other fatty acids [6,26]. Key reagents included Candida antarctica lipase B (Novozym® 435, Novozymes A/S, Bagsvaerd, Denmark) used for enzymatic epoxidation, and methanol (≥99.8%) from Riedel-de Haen (Seelze, Germany) for methylation reactions. The choice of Novozym® 435 for TOFA epoxidation was driven by its excellent selectivity in catalyzing epoxidation reactions. It efficiently targets the double bonds in fatty acids, converting them into epoxides with minimal side reactions. Additionally, its effectiveness under mild conditions and its alignment with green chemistry principles made it the preferred choice for this process [27,28].
Additional materials, including hydrogen peroxide, sulfuric acid, trimethylolpropane (TMP), Amberlite® IRC120 H, tert-butyl acetoacetate (98%), were purchased from Sigma-Aldrich, and tetrafluoroboric acid solution was obtained from Alfa Aesar (Kandel, Germany).
Polymer resins were developed from the synthesized acetoacetates using difunctional hexanediol diacrylate (HDODA), trifunctional trimethylolpropane triacrylate (TMPTA), and tetrafunctional pentaerythritol tetraacrylate (PETA) in the presence of catalyst 1,1,3,3-tetramethylguanidine (TMG), all received from Sigma-Aldrich without further purification.
2.2 Synthesis of Michael Donors
Acetoacetates were prepared using two distinct routes. In the first approach, TOFA was epoxidized enzymatically using Novozym® 435, followed by oxirane ring-opening with TMP. The resultant polyol was further acetoacetylated with tert-butyl acetoacetate. The synthesis pathway for acetoacetate via enzymatic epoxidation is presented in Fig. 1.
Figure 1: Synthesis pathway for acetoacetate via enzymatic epoxidation of TOFA
The second route involved methylating TOFA, epoxidizing the methyl ester using ion-exchange resin, and completing the transesterification with TMP before acetoacetylation. A schematic representation of this synthesis pathway can be found in Fig. 2.
Figure 2: Synthesis pathway for acetoacetates via ion-exchange epoxidation
Details on enzymatic epoxidation can be found in the study by Abolins et al. [29], and for a more comprehensive description of the methylation of TOFA and ion-resin epoxidation refer to the study by Polaczek et al. [30]. EETOFA or EIRTOFAME was subjected to a reaction with TMP in the presence of tetra-fluoroboric acid solution as a catalyst. Oxirane ring-opening occurred at 120°C, while for esterification/transesterification, the temperature was elevated to 200°C. A full description of synthesis is given in the work by Abolins et al. [29]. Obtained polyols (EETOFA_TMP and EIRTOFAME_TMP) were further reacted with tert-butyl acetoacetate at 120°C temperature for 4 h to yield acetoacetates, abbreviated EETOFA_TMP_AA and EIRTOFAME_TMP. For additional details, refer to the study by Pomilovskis et al. [31].
Synthesized acetoacetates EETOFAME_TMP_AA or EIRTOFAME_TMP_AA served as Michael Donors, while acrylates (HDODA, TMPTA, and PETA) with varying functionalities acted as Michael Acceptors. A total of six polymer resin samples were produced and subsequently characterized. Polymerization was carried out with a 1:2 molar ratio of acetoacetate to acrylate groups, employing 1% (by total mixture mass) of TMG as a catalyst. After mixing, the solution was centrifuged for 1 min to remove any air bubbles, ensuring a homogeneous polymer monolith formation.
The acid value of polyols was determined following the ISO 2114:2000 standard [32], while hydroxyl value was assessed according to the ISO 4629-2:2016 standard [33]. Moisture content was evaluated using Karl Fischer titration. Polymer resin characterization involved differential scanning calorimetry (DSC), dynamic mechanical analysis (DMA) in compression oscillation mode, and thermogravimetric analysis (TGA). Detailed descriptions of the characterization methods are provided in Table 1. The glass transition temperature was derived from DSC data, in compliance with ISO 11357-2 [34]. All data analysis was performed using OriginPro 2022b (version 9.9.5.171).
3.1 Polyols and Corresponding Acetoacetates
Two bio-based polyols were synthesized from TOFA via distinct pathways: the first involved enzymatic epoxidation followed by oxirane opening and esterification, while the second pathway employed methylation followed by ion-exchange epoxidation, and subsequent oxirane opening and transesterification. An alternative epoxidation method could involve direct TOFA epoxidation with an ion-exchange resin. In this study, methylation of TOFA was chosen due to the possibility of reducing the formation of dimers and trimers during the synthesis process, as no free acid groups are available for dimerization and trimerization reactions [30]. However, a disadvantage of this approach is the additional methylation step in the synthesis process and the use of acetic acid. Acetic acid as a low-molecular organic acid opens oxirane rings and esters are formed. In contrast, enzymatic epoxidation reduces the formation of low-molecular-weight by-products but enzymes cost more. The chemical structures of the raw materials, polyols, and the subsequently synthesized acetoacetates are shown in Fig. 3.
Figure 3: Synthesis pathways of polyols and acetoacetates from TOFA with chemical structures
Table 2 compares the characteristics of synthesized polyols and their corresponding acetoacetates. It reveals that the polyol synthesized via the enzymatic epoxidation method (EETOFA_TMP) has a higher hydroxyl value than the polyol synthesized through ion-resin epoxidation (EIRTOFAME_TMP). Both polyols have similar acid values and water content. Both were effective in reacting with tert-butyl acetoacetate to form acetoacetates. Due to the higher hydroxyl value of the enzymatically derived polyol, the resulting acetoacetate exhibits a higher acetoacetate group content.
The acetoacetates obtained were used as Michael donors and reacted with acrylates (HDODA, TMPTA, and PETA) to produce six different polymer resins. The corresponding Michael acceptors and Michael donors, along with the designations of the polymer resin samples, are presented in Table 3.
The schematic chemical structure of the obtained polymers is shown in Fig. 4. R1 and R2 correspond to the respective Michael acceptor and Michael donor listed in Table 2, thus generating six unique polymer resin structures.
Figure 4: Schematic representation of the polymer backbone with R1 and R2 moieties corresponding to Michael donors and acceptors
DSC, DMA, and TGA were employed to characterize the thermal and mechanical properties of obtained polymer resins. The DSC results, presented in Fig. 5, indicate that the glass transition temperature increases with the functionality of the acrylate used in the polymer resin synthesis. For samples where enzymatic epoxidation was used in synthesis pathways, glass transition varied from 26°C to 72°C. In the case of samples derived from ion-exhange resin epoxidation technique—glass transition temperature increased from −5°C to 62°C. It can be seen that EETOFA samples (Fig. 5a) show higher glass transition than EIRTOFAME samples (Fig. 5b).
Figure 5: DSC curves and glass transition temperatures of polymer resins: a—polymer resin samples obtained from EETOFA, b—polymer resin samples obtained from EIRTOFAME
The glass transition temperatures identified from the tan δ curves presented in Fig. 6 are higher than those determined by DSC, but they exhibit the same trend.
Figure 6: Tan δ curves from DMA analysis and corresponding glass transition temperatures: a—polymer resin samples obtained from EETOFA, b—polymer resin samples obtained from EIRTOFAME
Curves of storage modulus (E’) are shown in Fig. 7. Storage modulus increases with the functionality of the acrylate used in the polymer resin synthesis. Higher functionality of acrylate leads to a denser crosslinked network in the polymer. This denser network enhances the rigidity and mechanical strength, thereby increasing the storage modulus. When comparing different epoxidation techniques, the enzymatic epoxidation method results in polymer resins with significantly higher storage modulus, nearly double, compared to ion-exchange resin method. This can be attributed to the more efficient and controlled formation of epoxy groups, leading to better crosslinking and, consequently, a stiffer polymer network. The ion-resin method might produce polymers with some degree of irregularity in epoxy group distribution, leading to less optimal crosslinking and lower storage modulus and glass transition temperature.
Figure 7: Storage modulus curves from DMA analysis, including storage modulus values at 20°C temperature: a—EETOFA samples, b—EIRTOFAME samples
Thermal stability was assessed using TGA, with TGA and derivative thermogravimetry (DTG) curves shown in Fig. 8. Characteristics of thermal stability-onset temperature (Tonset), the temperature at a weight loss of 5% and 10% (Tm5% and Tm10%), the weight of the solid residue remaining at 700°C (residue), and maximums of DTG peaks (Tmax)—are presented in Table 4.
Figure 8: TGA and DTG results: a—EETOFA samples, b—EIRTOFAME samples
Thermal degradation of developed polymer resins occurs in one main step in the temperature range from 300°C to 500°C. EIRTOFAME_HDODA shows an additional peak at 180°C in the DTG curve. The differences in thermal stability are minimal, with the polymer resins synthesized with HDODA showing a slightly lower Tonset and a lower Tmax1 in the DTG curve. Additionally, the polymer resin obtained with HDODA exhibits an additional peak shoulder at approximately 445°C (for EETOFA-HDODA) and 455°C (for EIRTOFAME-HDODA) in the DTG curve. For the other samples, a single main degradation peak is observed at approximately 370°C–378°C, corresponding to the degradation of the polymer network. The residue at the final temperature (700°C) increases as the functionality of the acrylate used in the synthesis increases. The thermal degradation pattern of developed resins is similar to the degradation behavior observed in other polymer resins synthesized via 1,4-Michael addition [18,21]. Additionally, these resins exhibit higher thermal stability than pure epoxy resins (Tonset < 360°C [35,36]), conventional polyurethanes (Tonset < 215°C [37,38]), and poly(methyl methacrylate) films (Tonset < 245°C [39,40]), demonstrating superior thermal stability properties.
Six polymer resins were synthesized from tall oil fatty acids-based acetoacetate and acrylates with varying functionalities. For the polyol synthesis necessary for acetoacetate synthesis, two epoxidation techniques were employed: enzymatic epoxidation and ion-exchange resin epoxidation. Polymerization was carried out via the Michael 1,4-addition at room temperature. The obtained polymer resins were characterized using DSC, DMA, and TGA.
The glass transition temperature and storage modulus of the polymer resins were significantly influenced by both the functionality of the acrylates used and the epoxidation technique employed. Higher acrylate functionality resulted in increased stiffness, while enzymatic epoxidation enhanced the polymer’s mechanical properties by nearly doubling the storage modulus compared to the ion-exchange resin technique. Thermal stability was similar across all six samples, although the polymer resin obtained with HDODA exhibited slightly lower thermal stability.
Depending on the application, selecting the appropriate acrylate functionality and epoxidation method can tailor the mechanical properties of the polymer. For instance, applications requiring high stiffness and mechanical strength would benefit from high-functionality acrylates and enzymatic epoxidation techniques.
Acknowledgement: Not applicable.
Funding Statement: This research was funded by the Latvian State Institute of Wood Chemistry Bioeconomic grant no. 04-24 “Development of Composites from Polymer Resin Synthesized from Tall Oil Fatty Acids and Reinforced with Various Fillers” (FiTeCo).
Author Contributions: The authors confirm contribution to the paper as follows: study conception and design: Ralfs Pomilovskis, Arnis Abolins; data collection: Ralfs Pomilovskis, Arnis Abolins; analysis and interpretation of results: Ralfs Pomilovskis, Arnis Abolins, Aiga Ivdre; draft manuscript preparation: Aiga Ivdre, Ralfs Pomilovskis, Arnis Abolins. All authors reviewed the results and approved the final version of the manuscript.
Availability of Data and Materials: The data that support the findings of this study are available from the corresponding author, Aiga Ivdre, upon reasonable request.
Ethics Approval: Not applicable.
Conflicts of Interest: The authors declare no conflicts of interest to report regarding the present study.
References
1. Orejuela-Escobar LM, Landázuri AC, Goodell B. Second generation biorefining in Ecuador: circular bioeconomy, zero waste technology, environment and sustainable development: the nexus. J Bioresour Bioprod. 2021;6:83–107. [Google Scholar]
2. Kumar S, Darshna A, Ranjan D. A review of literature on the integration of green energy and circular economy. Heliyon. 2023;9:e21091. [Google Scholar] [PubMed]
3. Vela Almeida D, Kolinjivadi V, Ferrando T, Roy B, Herrera H, Vecchione Gonçalves M, et al. The greening of empire: the European green deal as the EU first agenda. Polit Geogr. 2023;105(5):102925. doi:10.1016/j.polgeo.2023.102925. [Google Scholar] [CrossRef]
4. Xie Y, Gao S, Zhang D, Wang C, Chu F. Bio-based polymeric materials synthesized from renewable resources: a mini-review. Resour Chem Mater. 2023;2:223–30. [Google Scholar]
5. Cabulis U, Ivdre A. Recent developments in the sustainability of the production of polyurethane foams from polyols based on the first-to the fourth-generation of biomass feedstock. Curr Opin Green Sustain Chem. 2023;44:100866. doi:10.1016/j.cogsc.2023.100866. [Google Scholar] [CrossRef]
6. Vevere L, Fridrihsone A, Kirpluks M, Cabulis U. A review of wood biomass-based fatty acids and rosin acids use in polymeric materials. Polymers. 2020;12:1–17. doi:10.3390/polym12112706. [Google Scholar] [PubMed] [CrossRef]
7. Churchill JGB, Borugadda VB, Dalai AK. A review on the production and application of tall oil with a focus on sustainable fuels. Renew Sustain Energy Rev. 2024;191:114098. doi:10.1016/j.rser.2023.114098. [Google Scholar] [CrossRef]
8. Yeşilçiçek H, Oruç Ş, Gülfer Bozdemir M. Characterization and rheological properties of asphalt binder with a novel tall oil-based boron additive to enhance asphalt performance. Constr Build Mater. 2022;359(9–10):129510. doi:10.1016/j.conbuildmat.2022.129510. [Google Scholar] [CrossRef]
9. Bearsley SR, Haverkamp RG. Adhesive Properties of tall oil pitch modified bitumen. Road Mater Pavement Des. 2007;8(3):449–65. doi:10.1080/14680629.2007.9690083. [Google Scholar] [CrossRef]
10. Yakushin V, Misane M, Bikovens O, Vilsone D, Sevastyanova I. Synthesis of trimethylolpropane esters of tall oil fatty acids and properties of polyurethane coatings on their basis. J Coatings Technol Res. 2016;13:317–24. doi:10.1007/s11998-015-9747-3. [Google Scholar] [CrossRef]
11. Hedman B, Piispanen P, Alami EO, Norin T. Synthesis and characterization of surfactants via epoxidation of tall oil fatty acid. J Surfactants Deterg. 2003;6:47–53. doi:10.1007/s11743-003-0247-4. [Google Scholar] [CrossRef]
12. Wang S-F, Furuno T, Cheng Z. Synthesis of new betaine-type amphoteric surfactants from tall oil fatty acid. J Wood Sci. 2002;48(5):419–24. doi:10.1007/BF00770703. [Google Scholar] [CrossRef]
13. Kirpluks M, Ivdre A, Fridrihsone A, Cabulis U. Tall oil based rigid polyurethane foams thermal insulation filled with nanofibrillated cellulose. Polimery. 2020;65(10):719–27. doi:10.14314/polimery.2020.10.7. [Google Scholar] [CrossRef]
14. Kirpluks M, Vanags E, Abolins A, Michalowski S, Fridrihsone A, Cabulis U. High functionality bio-polyols from tall oil and rigid polyurethane foams formulated solely using bio-polyols. Materials. 2020;13(8):38–53. doi:10.3390/ma13081985. [Google Scholar] [PubMed] [CrossRef]
15. Uschanov P, Heiskanen N, Mononen P, Maunu SL, Koskimies S. Synthesis and characterization of tall oil fatty acids-based alkyd resins and alkyd-acrylate copolymers. Prog Org Coatings. 2008;63:92–9. doi:10.1016/j.porgcoat.2008.04.011. [Google Scholar] [CrossRef]
16. Yakushin V, Stirna U, Bikovens O, Misane M, Sevastyanova I, Vilsone D. Synthesis and characterization of novel polyurethanes based on tall oil. Mater Sci. 2013;19(4):112–9. doi:10.5755/j01.ms.19.4.2666. [Google Scholar] [CrossRef]
17. Rodríguez-Tobías H, Uzcátegui-Flores J, Enríquez-Medrano FJ, Morales G, Martínez-Arellano AG. Further investigation on fatty acids-based methacrylate monomers: high temperature radical polymerization for obtaining copolymers and their blends with medium-oil alkyd resin for coatings. Prog Org Coatings. 2024;186:107962. doi:10.1016/j.porgcoat.2023.107962. [Google Scholar] [CrossRef]
18. Pomilovskis R, Mierina I, Fridrihsone A, Kirpluks M. Bio-based polymer developments from tall oil fatty acids by exploiting michael addition. Polymers. 2022;14(19):4068. doi:10.3390/polym14194068. [Google Scholar] [PubMed] [CrossRef]
19. Murillo EA, Vallejo PP, López BL. Effect of tall oil fatty acids content on the properties of novel hyperbranched alkyd resins. J Appl Polym Sci. 2011;120(6):3151–8. doi:10.1002/app.33502. [Google Scholar] [CrossRef]
20. Mather BD, Viswanathan K, Miller KM, Long TE. Michael addition reactions in macromolecular design for emerging technologies. Prog Polym Sci. 2006;31:487–531. [Google Scholar]
21. Pomilovskis R, Kaulina E, Mierina I, Abolins A, Kockova O, Fridrihsone A, et al. Wood pulp industry by-product valorization for acrylate synthesis and bio-based polymer development via Michael addition reaction. J Bioresour Bioprod. 2023;8(3):265–79. doi:10.1016/j.jobab.2023.06.001. [Google Scholar] [CrossRef]
22. Salmi T, Aguilera AF, Lindroos P, Kanerva L. Mathematical modelling of oleic acid epoxidation via a chemo-enzymatic route—From reaction mechanisms to reactor model. Chem Eng Sci. 2022;247(4):117047. doi:10.1016/j.ces.2021.117047. [Google Scholar] [CrossRef]
23. Freites Aguilera A, Rahkila J, Hemming J, Nurmi M, Torres G, Razat T, et al. Epoxidation of tall oil catalyzed by an ion exchange resin under conventional heating and microwave irradiation. Ind Eng Chem Res. 2020;59(22):10397–406. doi:10.1021/acs.iecr.0c01288. [Google Scholar] [CrossRef]
24. Danov SM, Kazantsev OA, Esipovich AL, Belousov AS, Rogozhin AE, Kanakov EA. Recent advances in the field of selective epoxidation of vegetable oils and their derivatives: a review and perspective. Catal Sci Technol. 2017;7:3659–75. [Google Scholar]
25. Saurabh T, Patnaik M, Bhagst SL, Renge V. Epoxidation of vegetable oils: a review. Int J Adv Eng Technol E. 2011;2:459–501. [Google Scholar]
26. Sture B, Kirpluks M, Gaidukovs S, Vanags E. Synthesis of photoactive compounds from tall oil fatty acids. J Renew Mater. 2020;8(9):1077–89. doi:10.32604/jrm.2020.09294. [Google Scholar] [CrossRef]
27. Aguilera AF, Tolvanen P, Oger A, Eränen K, Leveneur S, Mikkola JP, et al. Screening of ion exchange resin catalysts for epoxidation of oleic acid under the influence of conventional and microwave heating. J Chem Technol Biotechnol. 2019;94(9):3020–31. doi:10.1002/jctb.6112. [Google Scholar] [CrossRef]
28. Törnvall U, Orellana-Coca C, Hatti-Kaul R, Adlercreutz D. Stability of immobilized Candida Antarctica lipase B during chemo-enzymatic epoxidation of fatty acids. Enzyme Microb Technol. 2007;40(3):447–51. doi:10.1016/j.enzmictec.2006.07.019. [Google Scholar] [CrossRef]
29. Abolins A, Pomilovskis R, Vanags E, Mierina I, Michalowski S, Fridrihsone A, et al. Impact of different epoxidation approaches of tall oil fatty acids on rigid polyurethane foam thermal insulation. Materials. 2021;14(4):1–17. doi:10.3390/ma14040894. [Google Scholar] [PubMed] [CrossRef]
30. Polaczek K, Kaulina E, Pomilovskis R, Fridrihsone A, Kirpluks M. Epoxidation of tall oil fatty acids and tall oil fatty acids methyl esters using the SpinChem® rotating bed reactor. J Polym Environ. 2022;30(11):4774–86. doi:10.1007/s10924-022-02556-5. [Google Scholar] [CrossRef]
31. Pomilovskis R, Mierina I, Beneš H, Trhlíková O, Abolins A, Fridrihsone A, et al. The synthesis of bio-based michael donors from tall oil fatty acids for polymer development. Polymers. 2022;14(19):4107. doi:10.3390/polym14194107. [Google Scholar] [PubMed] [CrossRef]
32. ISO 2114:2000; Plastics (polyester resins) and paints and varnishes (binders)—Determination of partial acid value and total acid value. Geneva, Switzerland: International Organization for Standardization. 2000. [Google Scholar]
33. ISO 4629-2:2016; Binders for paints and varnishes—Determination of hydroxyl value—Part 2: Titrimetric method using a catalyst. Geneva, Switzerland: International Organization for Standardization. 2016. [Google Scholar]
34. ISO 11357-2:2020; Plastics—Differential scanning calorimetry (DSC) Part 2: Determination of glass transition temperature and step height. Geneva, Switzerland: International Organization for Standardization. 2020. [Google Scholar]
35. Zhi M, Liu Q, Chen H, Chen X, Feng S, He Y. Thermal stability and flame retardancy properties of epoxy resin modified with functionalized graphene oxide containing phosphorus and silicon elements. ACS Omega. 2019;4(6):10975–84. doi:10.1021/acsomega.9b00852. [Google Scholar] [PubMed] [CrossRef]
36. Zhao H, Liang X, Gao Y. Organic-inorganic hybrid epoxy resin coating with high thermal stability and hydrophobicity for corrosion protection prepared by (3-aminopropyl) triethoxysilane as a bridging agent. Mater Today Commun. 2024;39(5):108950. doi:10.1016/j.mtcomm.2024.108950. [Google Scholar] [CrossRef]
37. Ivdre A, Kirpluks M, Abolins A, Vevere L, Sture B, Paze A, et al. Rigid polyurethane foams’ development and optimization from polyols based on depolymerized suberin and tall oil fatty acids. Polymers. 2024;16(7):942. doi:10.3390/polym16070942. [Google Scholar] [PubMed] [CrossRef]
38. Ni X, Wu L. Enhanced flame retardancy and thermal stability in flexible polyurethane foam through synergistic core-shell structured DBDPE@PMA particles. Arab J Chem. 2024;17(4):105684. doi:10.1016/j.arabjc.2024.105684. [Google Scholar] [CrossRef]
39. Gałka P, Kowalonek J, Kaczmarek H. Thermogravimetric analysis of thermal stability of poly(methyl methacrylate) films modified with photoinitiators. J Therm Anal Calorim. 2014;115(2):1387–94. doi:10.1007/s10973-013-3446-z. [Google Scholar] [CrossRef]
40. Wang H, Xu P, Zhong W, Shen L, Du Q. Transparent poly(methyl methacrylate)/silica/zirconia nanocomposites with excellent thermal stabilities. Polym Degrad Stab. 2005;87:319–27. doi:10.1016/j.polymdegradstab.2004.08.015. [Google Scholar] [CrossRef]
Cite This Article
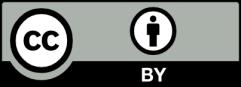
This work is licensed under a Creative Commons Attribution 4.0 International License , which permits unrestricted use, distribution, and reproduction in any medium, provided the original work is properly cited.