Open Access
ARTICLE
Preparation of Flaxseed Meal Protein Renewable Bioadhesive by Using Small Proportions of Trimethylolpropane Trigglycidyl Ether and Ethylenediamine
1 Key Laboratory of Bio-Based Materials and Energy Ministry of Education, South China Agricultural University, Guangzhou, 510642, China
2 Guangxi Key Laboratory of Chemistry and Engineering of Forest Products, Guangxi Collaborative Innovation Center for Chemistry and Engineering of Forest Products, Guangxi University for Nationalities, Nanning, 530006, China
* Corresponding Author: Xianfeng Hou. Email:
Journal of Renewable Materials 2025, 13(2), 297-310. https://doi.org/10.32604/jrm.2024.049534
Received 10 January 2024; Accepted 17 May 2024; Issue published 20 February 2025
Abstract
The main raw material utilized in wood adhesives comes from petrochemical extractives. However, due to the excessive dependence on petrochemical resources and the adverse impact on the ecosystem and human well-being, there is an increasing trend to develop byproduct protein-based adhesives in the current global food safety context. In this research, flaxseed meal was subjected to pretreatment, and trimethylolpropane triglycidyl ether (TTE) and ethylenediamine (EN) were utilized as crosslinkers to establish a more compact adhesive layer and to prevent water intrusion. The pretreatment decreased the FM/UB viscosity by 60% compared to FM. The combination of CD analysis indicated that the Urea-NaOH pretreatment effectively stretched the flaxseed meal protein. According to Fourier transform infrared (FTIR) spectroscopy, X-ray diffraction (XRD), and differential scanning calorimetry (DSC) were used to analyze the resulting adhesive’s reaction mechanism and thermal response. Furthermore, the physical properties of the adhesive were characterized using wet shear strength testing and SEM observation. Remarkably, the dry bond strength increased from 0.72 to 2.12 MPa, representing a 194.4% increase. The wet bonding strength of the adhesive was improved from 0.22 to 1.21 MPa, representing a 550% increase compared to the original flaxseed protein-based adhesive, which far exceeded the minimum requirement for plywood of Type II (≥0.7 MPa, by GB/T 9846-2015). This study demonstrated an eco-friendly and sustainable method for the development of protein adhesives as viable substitutes for petrochemical resins.Graphic Abstract
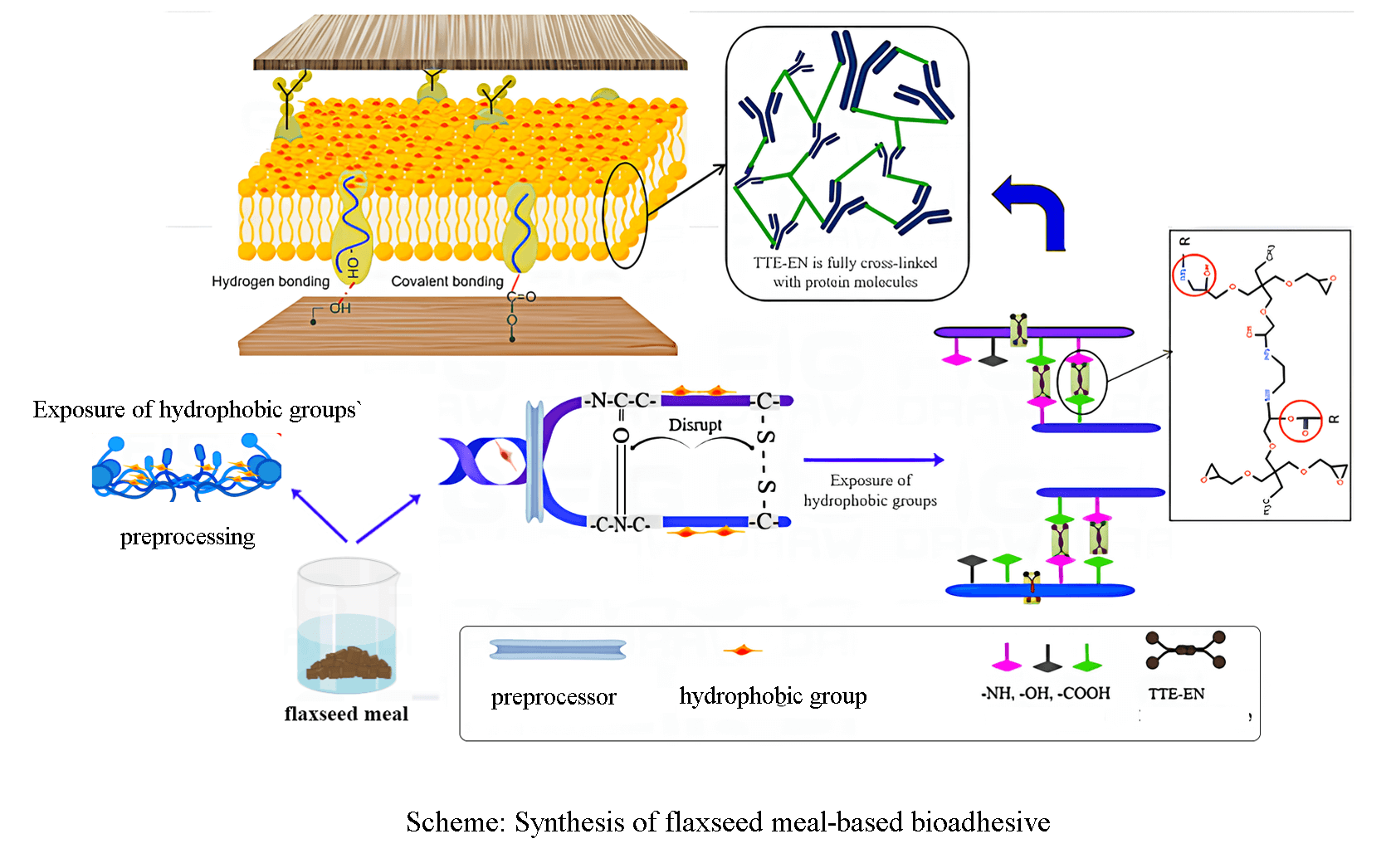
Keywords
Supplementary Material
Supplementary Material FileFormaldehyde-based adhesives, sourced from restricted and non-replenishable fossil resources, are extensively utilized in plywood manufacturing attributable to their exceptional physical properties, specifically water resistance [1,2]. However, these adhesives emit hazardous substances during preparation and use, causing adverse effects on the environment and human health [3–5]. Therefore, there is a growing focus on developing sustainable and eco-friendly adhesives sourced from renewable bioresources. Biodegradable biomass adhesives have gained significant attention due to their availability, sustainability, and potential to replace formaldehyde-based adhesives, addressing the oil crisis, and reducing ecological burdens simultaneously [6].
Protein-based adhesives are an important category of biomass adhesives, but their widespread use is limited by inferior water resistance [7,8]. To tackle this problem, different physical [9,10], chemical [11–13], and biological modification [14] devices have been investigated to enrich the hydrophobicity of proteins. Protein molecules contain numerous reactive groups within their peptide chains [15], which can form stable chemical bonds with highly reactive groups such as aldehyde, epoxy, and isocyanate groups through chemical reactions, thus increasing the crosslinking density of adhesives and ultimately enhancing bonding strength. According to the current international context of food safety, a significant trend is the advancement of protein-based adhesives derived from food by-products. The raw materials of protein-based adhesives are mostly plant or animal proteins, of which soy protein occupies an important position, and industrialized production has been realized in plywood manufacturing [16]. However, the dependence on soy protein as a food resource should be reduced in the context of food security. In recent years, the development of protein-based adhesives using food by-products has become a trend. Related research has used papyrus leaf forestry waste protein, cottonseed meal protein, peanut meal protein, etc., as raw materials [17–19]. The preparation of environmentally friendly protein-based adhesive offers excellent performance and low cost.
Flaxseed, as an important oilseed crop, contains 18%–30% protein, 20%–35% polysaccharides, 30%–41% fat, and 3%–4% ash. Its main components are similar to soybean protein [20,21]. Flaxseed meal is the solid residue remaining after the oil extraction process, which is rich in 32%~49% proteins and contains more groups (e.g, -OH, -COOH, -NH2, etc.), which have the potential for development in the field of biomass-based adhesives.
This study to flaxseed meal protein as the main raw material, through urea and NaOH pretreatment of flaxseed meal crude protein, stretching the protein structure; the use of trimethylolpropane triglycidyl ether and ethylenediamine to build a cross-linking network, combined with cross-linking agent to improve the degree of cross-linking of pre-treated protein molecules, to enhance the polymer cohesion, to produce excellent performance and low-cost environmentally friendly adhesive. It provides a new idea for the preparation of green and high-performance adhesives.
The flaxseed meal (Protein content of 35%) was provided by Liaoning Sanmark Corporation, Liaoning, China. Phosphate Buffered Saline (Application to circular dichroic spectroscopy) was purchased from China Aladdin Biochemical Co., Shanghai, China. TTE (Trimethylolpropane triglycidyl ether) was supplied by Aladdin Biochem Co., Ltd., Shanghai, China. Ethylenediamine (EN) was provided by Tianjin InnoChem New Materials Technology Co., Ltd., Tianjin, China. Sodium hydroxide and urea were provided by Beijing Chemical Plant, Beijing, China. Eucalyptus veneer: size 30 cm × 30 cm × 2.2 mm (length × width × thickness), with a moisture content between 10% and 13%, was purchased.
2.2 Sample Preparation of Adhesives
The synthetic route of TTE-EN is shown in Scheme 1. Pretreatment formulations are shown in Table 1. Crosslinking modification formulations are shown in Table 2.
Scheme 1: The synthesis and chemical structure of TTE-EN
FM adhesive: Mix 20 g of flaxseed powder with 120 g of deionized water in a water bath at 30°C for 60 min at high speed.
FM/UB adhesive: Urea (2.5 g) and NaOH (2.5 g) were mixed with deionized water (120 g) and stirred for 5 min, then completely dissolved in a water bath at 70°C. Eventually, add 20 g of flaxseed powder and mix well to make an FM/UB adhesive.
FM/UB/TTE adhesive: TTE (7 wt%) is added to FM/UB and reacted in a water bath at 70°C with high-speed stirring for 10 min.
FM/UB/TTE-EN adhesive: TTE-EN (7 wt%) is added to FM/UB and reacted in a water bath at 70°C with high-speed stirring for 10 min.
TTE-EN crosslinker: obtained by mixing EN with TTE at a mass ratio of 0.1, pH 11, and reacting in a water bath at 50°C with high-speed stirring for 20 min.
The plywood consists of three pieces of eucalyptus wood with 260 g/m2 of adhesive applied to each veneer of the middle eucalyptus board. The veneer was then hot-pressed at a precise temperature of 140°C and a pressure of 1.0 MPa for 8 min, ensuring successful plywood manufacturing. Standardized plywood specimens were obtained by cutting the produced plywood to maintain consistency.
2.4 Characterization of TTE-EN and Adhesives Samples
To assess the viscosity of various adhesives, the NDJ-79 rotary viscometer was employed. The test temperature was maintained at 25°C throughout the experiment. Revised: Selection of the right rotor for the viscosity range. The selected rotor was vertically immersed into the adhesive sample, and three measurements were conducted to ensure reliability and precision. Reason: Added a period after “viscosity range” for clarity and separated the sentence for improved readability. By calculating the average viscosity value from these measurements, accurate viscosity data was obtained for further analysis and comparison.
2.4.2 Circular Dichroic Spectroscopy (CD) Test
The samples to be tested were concentrated at 0.01 g/mL in a phosphate buffer, and the temperature was maintained at 25°C under specific operating parameters to ensure the consistency of results. Samples were analyzed using a Chirascan circular dichroism spectrophotometer. Measurements were carried out using quartz cuvettes with a thickness of 0.1 cm. The analytical wavelengths range from 190 to 260 nm, providing a comprehensive view of the sample properties. Scanning speeds of 50 nm/min and 1 nm steps enable detailed and accurate data acquisition.
2.4.3 Tensile Shear Strength Measurement
Based on the standard GB/T 9846-2015, plywood must be conditioned in a standardized environment for continuous 24 h before dimensioning. Standard-sized plywood is then submerged at 63 ± 3°C for 3 h to evaluate its mean tensile resilience, which should meet or exceed 0.7 MPa to meet the standard requirements.
2.4.4 Fourier Transform Infrared (FTIR) Spectroscopy
The adhesive specimens underwent careful preparation before FTIR analysis using the Spectrum 100 spectrometer. Revised 2: First, the specimens were dried in an oven at precisely 120 ± 3°C and then ground to a 200 mesh particle size for consistency. Reason 2: Corrected the formatting and added the degree symbol for Celsius. Transparent flakes were created by compressing the specimens with KBr powder at a proportion of 1:100 for accurate FTIR analysis. The scanning range was set from 4000 to 500 cm−1, providing ample spectral range for comprehensive analysis, while 4 cm−1 resolution maintained a balance between spectral detail and measurement speed for precise results.
To examine the alterations in the crystalline structure of different crosslinkers based on flaxseed meal proteins, X-ray diffraction spectra were acquired at ambient temperature using an XRD-6100 X-ray diffractometer. XRD radiation was produced using a Cu-Kα source. The recorded data spanned from 5 to 60° with a precise step size of 0.2°. Operating conditions involved a test voltage of 40 kV and a current of 30 mA.
The main purpose of performing the DSC analysis was to investigate the curing characteristics of the adhesive. Before testing, the samples were freeze-dried in a vacuum lyophilizer for 72 h. Careful weighing and loading of approximately 6~8 mg of each sample was loaded into a differential scanning calorimeter for accurate analysis. The DSC analysis was conducted using the continuous heating mode, with a temperature range of 30°C~220°C and a heating rate of 10°C/min.
2.4.7 Scanning Electron Microscopy (SEM)
The protein adhesive and control samples were both dried for 12 h in an oven maintained at 120°C. To enable observation of the microstructure of the samples, they were affixed to a base using conductive adhesive and then gold-coated. Scanning electron microscopy (SEM) S-570 was employed for microstructural observation.
Fig. 1A shows the initial viscosity of the U and NaOH modified flaxseed meal protein-based adhesive, and Fig. 1B shows the results after modification with different pretreatments. High viscosity leads to poor flow and uneven distribution, reducing the contact area between the flaxseed protein and the crosslinker, and resulting in inadequate bonding. NaOH can break the hydrogen, disulfide, and ionic bonds of the higher structure of proteins [22,23].
Figure 1: Initial viscosity of the adhesive samples. (A) The initial viscosity of U and NaOH modified flaxseed meal protein-based adhesives. (B) Effect of different pretreatment on protein viscosity of flaxseed meal protein
Due to the limited breaking ability, the viscosity converges to 6040 mPa·s at concentrations greater than 0.6 mol/L. The 53.2% decrease in viscosity urea can break the hydrogen bond, leading to the relaxation of the protein molecular structure and causing protein denaturation [24]. As the concentration of urea increased, the apparent viscosity of the modified flaxseed protein solution continued to decrease. Revised 2: When the level of urea reached 0.3 mol/L, the viscosity recorded was 7840 mPa·s, exhibiting a decrease of 39.2% compared to the initial viscosity. Reason 2: N/A combined urea-based modification improves the ability to disperse proteins, with a 60% reduction in viscosity to 5240 mPa·s. According to Fig. 2, the structure of the flaxseed protein changed significantly before and after pretreatment with urea alkali modification, which shows that urea alkali modification can greatly disperse the flaxseed protein and release more of the protein’s secondary structure.
Figure 2: The CD patterns of the flaxseed meal protein-based adhesive before and after modification
The secondary structure content of proteins before and after flaxseed protein pretreatment is shown in Fig. 2. Before the pretreatment of flaxseed protein, the α-helix structure at 192 nm was a positive band, and the wavelength was close to negative values in the range of 200~225 nm. β-sheet stacked structure at 216 nm was a band close to negative values, and there was a band close to positive values in the range of 190~200 nm.
The standard assessment of various protein structures reveals that the pretreated α-helix structure exhibited a significant increase compared to the untreated α-helix structure. Similarly, the β-sheet structure demonstrated a similar trend. However, the random coil structure displayed an opposite pattern. This opposing trend can be attributed to the destructive influence of Urea-NaOH modification on the protein’s random coil structure [21] and the release of more protein secondary structures [25].
3.3 Tensile Shear Strength Analysis
Fig. 3 demonstrates the wet shear strength of plywood produced using various adhesives. The plywood bonded with adhesive A displayed a wet shear strength of merely 0.22 MPa, falling well below the lowest stipulated level of 0.7 MPa for indoor plywood stated in the standard (GB/T 9846-2015). Introducing urea and NaOH into adhesive B increased the wet shear strength of the plywood, reaching 0.32 MPa. This can be ascribed to the utilization of the combination of urea and strong alkali modification to greatly extend the structure of flaxseed protein, thereby revealing more hydrophobic groups. In addition, the inclusion of TTE in adhesive B significantly elevated the wet shear strength of the plywood to 0.75 MPa, satisfying the specified threshold for plywood used in indoor applications (≥0.7 MPa). The enhanced waterproofing of adhesive C is ascribed to cross-linking between the epoxy groups in the TTE and the reactive groups on the flaxseed protein molecule.
Figure 3: The shear strength of the plywood specimens bonded by: (A) the FM adhesive, (B) the FM/UB adhesive, (C) the FM/UB/TTE adhesive, (D) the FM/UB/TTE-EN adhesive
Upon mixing TTE-EN into adhesive B, the plywood’s wet shear strength was observed to improve by 505% to 1.21 MPa (Figs. S1 and S2), which surpassed the minimum requirement of 0.7 MPa for industrial application. The dry bond strength also increased from 0.72 to 2.12 MPa, an increase of 294.4%. This improvement is likely due to two primary factors: first, the higher number of epoxy groups in TTE-EN molecules when compared to TTE, as illustrated in Scheme 1, may have led to an enhanced level of cross-linking and a more compact network structure during adhesive curing; second, the reaction between TTE and EN resulted in the formation of a long chain structure that could combine with flaxseed protein molecules, thus creating a complex cross-linked network (Scheme 2) that further enhances waterproofing of adhesives.
Scheme 2: Cross-linked network structure between the TTE-EN and FM molecules
The gluing mechanism is analyzed in Fig. 4.
Figure 4: (A) FTIR spectra of different experimental groups; (B) FTIR spectra of different experimental groups with different peak intensities; (C) corresponding XRD spectra of different experimental groups; (D) corresponding DSC spectra of different experimental groups
Based on FTIR spectra (Fig. 4A) and Scheme 1, the primary amine groups were identified by a distinct absorption doublet in TTE, TTE-EN, and TTE/U represented by symmetric and asymmetric stretching vibration bands, located within the range of 3300–3500 cm−1 and almost disappears. At 3394 cm−1, the peak intensity of TTE-EN and TTE/U increases significantly, and the characteristic epoxy group peak decreases significantly at 910 cm−1 after the incorporation of EN and U, indicating the characteristic absorption band of secondary amines. The results indicate that EN and U can react with TTE, increasing the chain length and the amount of epoxy groups per single molecule, thus enhancing the crosslinking density.
Fig. 4B presents the FTIR spectrum of the adhesives derived from flaxseed meal protein. The spectrum reveals characteristic peaks at specific wavenumbers: 1663 cm−1 (C=O stretch, amide I), 1536 cm−1 (N-H bend, amide II), and 1249 cm−1 (C-N stretch, amide III) [26]. Following the introduction of TTE or TTE-EN, an observed decrease in the intensity of the epoxy group peak at 910 cm−1 showed the presence of crosslinking between TTE and flaxseed meal protein. Additionally, stretching peaks were witnessed at 2800–3000 cm−1 for C-H, 1663 cm−1 for C=O, 1497 cm−1 for N-H, 1428 cm−1 for -COOH, and 3300–3500 cm−1 for N-H/O-H stretching groups [27]. The peak at 2800–3000 cm−1 in FM/UB is enhanced compared to FM due to protein denaturation by urea and NaOH [24,25]. This denaturation exposes more nonpolar hydrophobic groups, leading to an increase in water resistance strength. Compared with FM, the carboxyl group peak intensity decreased, while the ester bond increased at 1745 cm−1 in FM/UB/TTE and FM/UB/TTE-EN samples. The N-H and OH characteristic peaks were further reduced, signifying that the carboxyl groups of flaxseed protein crosslinked with peptide chains to form a more compact, crosslinked structure.
It can be observed that the FM and FM/UB groups exhibit strong IR absorption peaks at 3300–3500 cm−1 (O-H of polysaccharides) and 1105 cm−1 (related to the C-O stretching vibration of the sugar groups in carbohydrates) [28]. However, the C-O absorption peaks at the FM/UB/TTE and FM/UB/TTE-EN positions of the saccharide groups were weakened and shifted to 1110 cm−1. Additionally, the peaks at 3300–3500 cm−1 (O-H peaks of the polysaccharides) were also weakened. This suggests that the addition of cross-linking agents can cause the hydroxyl groups of the polysaccharides to undergo a ring-opening reaction with the epoxy groups, forming an interpenetrating network [29–31]. This process ultimately enhances the bonding performance. As a result, the crosslinked network structure became well distributed and robust, leading to an improvement in the reliability of the flaxseed meal protein-based adhesive. It is noteworthy that the crosslinking mechanism revealed in this study is of great significance for the optimization of flaxseed meal protein-based adhesive design and performance enhancement.
To explore the inherent interactions of various adhesive samples based on flaxseed meal protein, alterations in the crystalline structure were analyzed via XRD spectroscopy. The corresponding crystallinity was estimated, and the consequences are presented in Table 3, with the XRD spectra displayed in Fig. 4C. The X-ray reflection pattern of proteins exhibits distinct peaks at approximately 9.4° and 20° for the α-helix and β-sheet structures, respectively [32,33].
The XRD patterns of the various adhesive samples based on flaxseed meal protein revealed only a prominent peak at 20° (2θ), indicating the potential for electrostatic interaction as a result of the presence of covalent bonds [34]. The distinctive peak (β-sheet) of the FM adhesive sample shifted from 20° to 19° upon binding to TTE or TTE-EN. According to the FTIR plots (Fig. 4B), the characteristic epoxy group was weakened at 910 cm−1 after doping with TTE or TTE-EN. Suggesting a possible partial denaturation of the protein crystalline structure resulting from the development of covalent bonds amid the epoxy groups and the peptide chains of the flaxseed protein side chains [35], caused a reduction in crystallinity, with the original value of 18.41% dropping to either 13.3% or 12.2%.
Fig. 4D illustrates the DSC test results obtained from a variety of adhesive samples formulated using flaxseed meal protein. The curing characteristics of the FM/UB/TTE-EN adhesives were investigated through DSC analysis, and the enthalpy data are presented in Table 4. The DSC studies revealed that the FM adhesive exhibited a significant exothermic broad peak at 82°C, attributed to β-conglycinin globulin (7S) and glycinin globulin (11S). In addition, under alkaline conditions, proteins can convert to 2 or 7S [36]. High concentrations of urea can cause a significant increase in protein denaturation [2,24], raising the glass transition temperature. The reason for this is that after the addition of TTE or TTE-EN, some of the epoxy groups reacted exothermically with the protein groups of flaxseed. This increased the exothermic broad peak to 93°C and 102°C, respectively. The enthalpy for FM/UB/TTE-EN was measured at 59.63 J/g.
The DSC analysis indicated that FM/UB/TTE and FM/UB/TTE-EN exhibited a heat absorption transition peak at 152°C, with an enthalpy of −4.83 J/g. The most probable reason for this peak is the condensation reaction between the carboxyl and amino groups of FM, a process that involves heat absorption [37]. The DSC curves of FM/UB/TTE and FM/UB/TTE-EN adhesives revealed a distinct exothermic peak around 180°C, with an enthalpy of 19.43 J/g, which is noteworthy. This peak indicates that the TTE and TTE-EN adhesives underwent additional reactions with flaxseed meal protein under high-temperature conditions. Moreover, the FTIR plots in Fig. 3B indicate a significant reduction in the epoxy group, suggesting that the reaction between the epoxy group and flaxseed meal protein was primarily exothermic.
The surface appearance of the ruptured adhesives formulated under different conditions was examined using scanning electron microscopy (SEM), as shown in Fig. 4. Analysis of adhesive A revealed the presence of holes and non-stretchable proteins on the ruptured surface (Fig. 5A). These holes were most likely formed due to the evaporation of water within the adhesive when exposed to high temperatures and pressure. Consequently, moisture could easily penetrate these empty spaces within the cured adhesive layer, leading to a decrease in cohesive strength and reduced wet shear strength [13]. For adhesive B, SEM imaging showed a reduction in pores on the fractured surface and a more uniform surface after modification with the Urea-NaOH (Fig. 5B).
Figure 5: The fracture surface appearance of various formulated adhesives: (A) the FM adhesive, (B) the FM/UB adhesive, (C) the FM/UB/TTE adhesive, (D) the FM/UB/TTE-EN adhesive
According to Fig. 2, it can be seen that the flaxseed protein’s secondary structure changed significantly before and after the treatment, which was attributed to the fact that the urea-base modification disrupted the hydrogen bonds within the protein [38,39], making the flaxseed protein more stretchy, but due to the disruption of the protein spherical structure disrupted, allowing cracks to develop after curing. In comparison to adhesive B, the cured adhesive C was observed to have a film wrapped around its surface (Fig. 5C). As depicted in Scheme 2, the addition of the TTE crosslinker after urea base pretreatment promoted the attachment of amino and carboxyl groups to TTE on small molecule proteins with incidental hydrophobic groups. The unreacted hydrophobic groups were then wrapped outside to form a hydrophobic layer. In contrast, the fracture surface of adhesive D with the addition of TTE-EN demonstrated a smoother and more uniform texture compared to adhesive C (Fig. 5D). This indicates that the supplement of EN-TTE advanced the crosslinking to a greater extent of the cured adhesive. The adhesive properties are significantly influenced bythe quantity of epoxy groups within an individual molecule of the cross-linking agent. A higher concentration of epoxy groups leads to a more intricate cross-linking network and consequently results in improved adhesion performance.
The combined pretreatment with urea-strong base was found to significantly reduce the initial viscosity of flaxseed protein, with a reduction of 60% to 5240 mPa·s from the original 12,900 mPa·s. This reduction not only improved the ability to disperse the protein but also provided a more adequate reaction area for the cross-linking reaction.
TTE and EN reacted together to form a polymer chain with epoxy groups. This resulted in the cross-linking of flaxseed protein molecules and the forming of a more compacted cured adhesive layer that combined with the flaxseed protein molecules to form a complex reticulation of interconnections.
Following the oligomerization of TTE-EN, the cured adhesive layer exhibited a high degree of cross-linking resulting in a smooth cross-sectional appearance. Moreover, the post-cure process facilitated water resistance improvement. Adhesive laminates comprising FM/UB/TTE-EN were found to exhibit a wet shear strength of 1.21 MPa, highlighting their potential use in industrial plywood applications.
Acknowledgement: We would like to extend our appreciation for the financial assistance provided by Guangxi Key Laboratory of Chemistry and Engineering of Forest Products, Guangxi Collaborative Innovation Center for Chemistry and Engineering of Forest Products, Guangxi University for Nationalities and 2021 University Teacher Characteristic Innovation Research Project (Foshan Education Bureau).
Funding Statement: The authors received no specific funding for this study.
Author Contributions: The authors confirm contribution to the paper as follows: study conception and design: Chenglong Zhong, Xianfeng Hou, Qiaofang Zhou, Shijing Yan; data collection: Chenglong Zhong; analysis and interpretation of results: Chenglong Zhong, Xianfeng Hou, Shuai Peng, Zhenzhong Gao; draft manuscript preparation: Chenglong Zhong, Xianfeng Hou. All authors reviewed the results and approved the final version of the manuscript.
Availability of Data and Materials: The data that support the findings of this study are available from the corresponding author upon reasonable request.
Ethics Approval: Not applicable.
Conflicts of Interest: The authors declare no conflicts of interest to report regarding the present study.
Supplementary Materials: The supplementary material is available online at https://doi.org/10.32604/jrm.2024.049534.
References
1. Pizzi A. Synthetic adhesives for wood fibers and composites chemistry. In: Belgacem N, Pizzi A, editors. Lignocellulosic fibers and wood handbook. Beverly, MA, USA: Scrivener Publishing LLC; 2016. p. 247–76.
2. Li Z, Zhao S, Wang Z, Zhang S, Li J. Biomimetic water-in-oil water/pMDI emulsion as an excellent ecofriendly adhesive for bonding wood-based composites. J Hazard Mater. 2020;396:122722. doi:10.1016/j.jhazmat.2020.122722.
3. Chen NR, Zeng QZ, Rao JP, Lin QJ. Effect of preparation conditions on bonding strength of soy-based adhesives via viscozyme l action on soy flour slurry. BioResources. 2014;9(4):7444–53. doi:10.15376/biores.9.4.7444-7453.
4. Xu C, Xu Y, Chen M, Zhang Y, Li J, Gao Q, et al. Soy protein adhesive with bio-based epoxidized daidzein for high strength and mildew resistance. Chem Eng J. 2020;390:124622. doi:10.1016/j.cej.2020.124622.
5. Huang X, Chen Y, Li J, Li J, Gao Q, Mao A. Development of a strong soy protein-based adhesive with excellent antibacterial and antimildew properties via biomineralized silver nanoparticles. Ind Crop Prod. 2022;188(49):115567. doi:10.1016/j.indcrop.2022.115567.
6. Tian W, Wang XY, Ye YH, Wu WJ, Wang YL, Jiang SH, et al. Recent progress of biomass in conventional wood adhesives: a review. Green Chem. 2023;25(24):10304–37. doi:10.1039/D3GC03441K.
7. Zeng Y, Yang W, Xu P, Cai X, Dong W, Chen M, et al. The bonding strength, water resistance and flame retardancy of soy protein-based adhesive by incorporating tailor-made core-shell nanohybrid compounds. Chem Eng J. 2022;428(14):132390. doi:10.1016/j.cej.2021.132390.
8. Vnučec D, Gorsek A, Kutnar A, Mikuljan M. Thermal modification of soy proteins in the vacuum chamber and wood adhesion. Wood Sci Technol. 2015;49(2):225–39. doi:10.1007/s00226-014-0685-5.
9. Li Y, Cai L, Chen H, Liu Z, Zhang X, Li J, et al. Preparation of a high bonding performance soybean protein-based adhesive with low crosslinker addition via microwave chemistry. Int J Biol Macromol. 2022;208(9):45–55. doi:10.1016/j.ijbiomac.2022.03.059.
10. Yue L, Shi R, Yi Z, Shi SQ, Gao Q, Li J, et al. A high-performance soybean meal-based plywood adhesive prepared via an ultrasonic process and using significantly lower amounts of chemical additives. J Clean Prod. 2020;274(5):123017. doi:10.1016/j.jclepro.2020.123017.
11. Zhu X, Wang D, Sun XS. Carbodiimide stabilizes the ultrasound-pretreated camelina protein structure with improved water resistance. Ind Crop Prod. 2017;97:196–200. doi:10.1016/j.indcrop.2016.11.001.
12. Yue C, Xu J, Yao M, He G, Yin Y, Cui Y, et al. Characterization and properties of plywood bioadhesive derived from cottonseed protein and sawdust cellulose. Cellulose. 2022;29(10):5869–81. doi:10.1007/s10570-022-04611-9.
13. Li H, Li C, Gao Q, Zhang S, Li J. Properties of soybean-flour-based adhesives enhanced by attapulgite and glycerol polyglycidyl ether. Ind Crop Prod. 2014;59:35–40. doi:10.1016/j.indcrop.2014.04.041.
14. Xu Y, Han Y, Shi SQ, Gao J. Preparation of a moderate viscosity, high performance and adequately-stabilized soy protein-based adhesive via recombination of protein molecules. J Clean Prod. 2020;255(6):120303. doi:10.1016/j.jclepro.2020.120303.
15. Lin Q, Chen N, Bian L, Fan M. Development and mechanism characterization of high performance soy-based bio-adhesives. Int J Adhes Adhes. 2012;34(1–3):11–6. doi:10.1016/j.ijadhadh.2012.01.005.
16. Luo J, Li X, Zhang H, Gao Q, Li J. Properties of a soybean meal-based plywood adhesive modified by a commercial epoxy resin. Int J Adhes Adhes. 2016;71:99–104. doi:10.1016/j.ijadhadh.2016.09.002.
17. Li C, Tang Y, Wang Y, Yuan X, Zhang B, Wu Z, et al. A novel environment-friendly adhesive based on recycling of Broussonetia papyrifera leaf forestry waste protein. Forests. 2022;13(2):291. doi:10.3390/f13020291.
18. Qu Y, Li T, Huang X, Liang M, Qin J, Guo Q, et al. Developing multifunctional and environmental-friendly hot-pressed peanut meal protein adhesive based on peanut waste. Chem Eng J. 2023;144207.
19. Yao J, Chen Z, Xu C, Chen Y, Guo J, Yue H. Cottonseed protein bioadhesive with high adhesion performance achieved by a synergistic dual-crosslinking strategy. Int J Adhes Adhes. 2023;127:103514. doi:10.1016/j.ijadhadh.2023.103514.
20. Li KY, Ye JT, Yang J, Shao JQ, Jin WP, Zheng C, et al. Co-extraction of flaxseed protein and polysaccharide with a high emulsifying and foaming property: enrichment through the sequence extraction approach. Foods. 2023;12(6):1256. doi:10.3390/foods12061256.
21. Yoshie-Stark Y, Müller K, Kawarada H, Futagawa K, Nakada R, Tashiro Y. Functional properties of linseed meal fractions: application as nutraceutical ingredient. Food Sci Technol Res. 2011;17(4):301–10. doi:10.3136/fstr.17.301.
22. Averina E, Konnerth J, D’Amico S, van Herwijnen HWG. Protein adhesives: alkaline hydrolysis of different crop proteins as modification for improved wood bonding performance. Ind Crops Prod. 2021;161:113187. doi:10.1016/j.indcrop.2020.113187.
23. Tang Q, Roos YH, Miao S. Plant protein versus dairy proteins: a pH-dependency investigation on their structure and functional properties. Foods. Jan 12;12(2):368.
24. Chen C, Du Y, Chen FS. Effect of urea concentration on properties of peanut protein isolate, arachin and conarachin-based adhesives during urea-epichlorohydrin modification. Royal Soci Open Sci. 2021;8(3):202227. doi:10.1098/rsos.202227.
25. Viseu MI, Melo EP, Carvalho TI, Correia RF, Sílvia MBC. Unfolding kinetics of -lactoglobulin induced by surfactant and denaturant: a stopped-flow/fluorescence study. Biophys J. 2007;93(10):3601–12. doi:10.1529/biophysj.106.101667.
26. Zhao S, Wang Z, Li Z, Li L, Li J, Zhang S. Core-shell nanohybrid elastomer based on Co-deposition strategy to improve performance of soy protein adhesive. ACS Appl Mater Interfaces. 2019;11(35):32414–22. doi:10.1021/acsami.9b11385.
27. Chen MS, Luo J, Shi RQ, Zhang JZ, Gao Q, Li J. Improved adhesion performance of soy protein-based adhesives with a larch tannin-based resin. Polymers. 2017;9(9):408. doi:10.3390/polym9090408.
28. Luo L, Wu Y, Liu C, Huang L, Zou Y, Shen Y, et al. Designing soluble soybean polysaccharides-based nanoparticles to improve sustained antimicrobial activity of nisin. Carbohydr Polym. 2019;225:115251. doi:10.1016/j.carbpol.2019.115251.
29. Mi Y, Sun Z, Gao D, Bai Y, Gao Z. Positive impact of carbohydrate on the crosslinking, performance, and potential applications of defatted soybean flour-based adhesive. Int J Adhes. 2021;106:102811. doi:10.1016/j.ijadhadh.2021.102811.
30. Fusteş-Dămoc I, Măluţan T, Mija A. Chitosan as a polyfunctional crosslinker for a renewable-based resorcinol diglycidyl ether. ACS Sustain Chem Eng. 2023;11(19):7605–16. doi:10.1021/acssuschemeng.3c01429.
31. Zhang Y, Chen M, Zhang J, Li J, Shi SQ, Gao Q. A high-performance bio-adhesive using hyperbranched aminated soybean polysaccharide and bio-based epoxide. Adv Mater Interfaces. 2020;7(9):2000148. doi:10.1002/admi.v7.9.
32. Fekri MH, Mohamareh SI, Hosseini M, Mehr MR. Green synthesis of activated carbon/Fe3O4 nanocomposite from flaxseed and its application as adsorbent and antibacterial agent. Chem Pap. 2022;76:6767–82. doi:10.1007/s11696-022-02278-x.
33. Ren X, He H, Li T. Variations in the structural and functional properties of flaxseed gum from six different flaxseed cultivars. Food Sci Nutrit. 2021;9(11):6131–8. doi:10.1002/fsn3.2566.
34. Hasanvand E, Rafe A. Characterization of flaxseed gum/rice bran protein complex coacervates. Food Biophys. 2018;13(4):387–95. doi:10.1007/s11483-018-9544-5.
35. Pang H, Zhao S, Wang Z, Zhang W, Zhang S, Li J. Development of soy proteinbased adhesive with high water resistance and bonding strength by waterborne epoxy crosslinking strategy. Int J Adhes Adhes. 2020;100(25):102600. doi:10.1016/j.ijadhadh.2020.102600.
36. Lakemond CMM, de Jongh HHJ, Hessing M, Gruppen H, Voragen AGJ. Soy glycinin: influence of pH and ionic strength on solubility and molecular structure at ambient temperatures. J Agric Food Chem. 2000;48(6):1985–90. doi:10.1021/jf9908695.
37. Zhang QJ, Wu JQ, Gao L, Liu T, Zhong WH, Sui G, et al. Dispersion stability of functionalized MWCNT in the epoxy-amine system and its effect on mechanical and interfacial properties of carbon fiber composites. Mater Des. 2016;94:392–402. doi:10.1016/j.matdes.2016.01.062.
38. Zhang L, Zhang B, Fan B, Gao Z, Shi J. Liquefaction of soybean protein and its effects on the properties of soybean protein adhesive. Pigment Resin Technol. 2017;46(5):399–407. doi:10.1108/PRT-07-2016-0074.
39. Huang W, Sun X. Adhesive properties of soy proteins modified by sodium dodecyl sulfate and sodium dodecylbenzene sulfonate. J Am Oil Chem Soc. 2000;77(7):705–8. doi:10.1007/s11746-000-0113-6.
Cite This Article
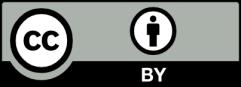
This work is licensed under a Creative Commons Attribution 4.0 International License , which permits unrestricted use, distribution, and reproduction in any medium, provided the original work is properly cited.