Open Access
ARTICLE
Evaluating the Potential of Birch Bark Suberinic Acids for Solid Wood Impregnation
1 Latvian State Institute of Wood Chemistry, Biorefinery Laboratory, Riga, LV-1006, Latvia
2 Norwegian Institute of Bioeconomy Research, Department Wood Technology, Høgskoleveien 8, Ås, 1433, Norway
* Corresponding Author: Daniela Godina. Email:
(This article belongs to the Special Issue: Advances in Biorefinery Technologies and Products – 2024)
Journal of Renewable Materials 2025, 13(1), 147-161. https://doi.org/10.32604/jrm.2024.056822
Received 31 July 2024; Accepted 24 September 2024; Issue published 20 January 2025
Abstract
Instead of the traditional linear model of taking, making, and disposing, the circular bio-economy promotes a regenerative approach. Although there is potential to create valuable products like betulin, lupeol, and suberinic acids (SA) from outer birch bark, many industries, such as plywood and pulp, often choose to incinerate substantial amounts of leftover birch bark to meet their energy needs. This highlights the importance of obtaining valuable products from wood. The objective of this study was to examine various fractions of SA and assess their potential for wood impregnation. The fractions included SA potassium salts in ethanol (SAK-EtOH) and water (SAK-H2O), SA suspension in water (SAS-H2O) and dried SA, which was subsequently diluted in ethanol (DSA-EtOH). There is significant potential for utilizing SA in wood treatment formulations as a sustainable alternative to harmful petroleum-derived chemicals. This approach not only addresses environmental concerns but also enhances the functionality of wood in construction applications, such as improving impregnation for moisture and fungal protection. Among the solutions tested, the ethanol solution of SA, specifically DSA-EtOH, showed the highest weight percent gain (WPG) and the greatest leaching resistance. GPC analysis showed that SA salts in ethanol (SAK-EtOH) and water (SAK-H2O) predominantly consist of low molecular fractions and each process (acidification and drying) reduces the low molecular content in the sample. This suggests that SA polymerizes after drying, making it necessary to dissolve it in ethanol to meet the requirements for impregnation. Further optimization, including adjustments in the concentration of the SA ethanol solution and the curing temperature, is essential to identify the optimal conditions for more in-depth impregnation studies.Graphic Abstract
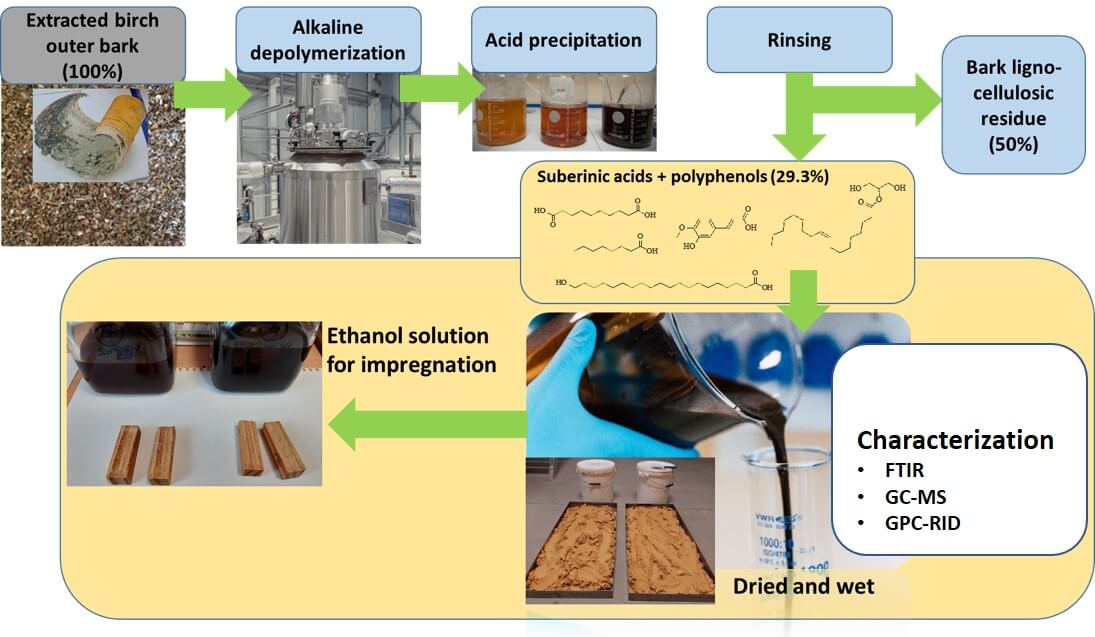
Keywords
Nomenclature
DSA | Dried suberinic acids |
FTIR | Fourier-transform infrared spectroscopy |
GC-MS | Gas chromatography-mass spectrometry |
GPC | Gel permeation chromatography |
SA | Suberinic acids |
SAK | Suberinic acids potassium salts |
SAS | Suberinic acid suspension |
WPG | Weight percent gain |
Suberin is a group of lipophilic (hydrophobic) macromolecules found in the cell walls of the outer layers of many plants [1]. It protects plant cells from environmental conditions, aids in recovery from mechanical damage, shields them from pests and pathogens, prevents excessive water loss, and assists in nutrient transport within the plant [2]. In plant roots, suberin acts as a diffusion barrier, influencing the absorption of minerals into plant cells [1,2]. Thanks to these properties, suberin has attracted significant attention in the field of circular bioeconomy [3]. The quantity of suberin in plant cell walls varies depending on the plant and the location of the cells (above ground or in the roots). Both the quantitative and qualitative content of suberin varies between different plant species [4]. For instance, the suberin content in the thick bark of cork oak (Quercus suber) ranges from 30% to 50%, while in the peels of carrots, beets, and potatoes, it ranges from 20% to 50% [1,2,4,5]. Birch bark is composed of two layers: the outer bark and the inner phloem. The outer bark contains approximately 50% suberin and 30% extractives [5].
Suberinic acids (SA) extracted from birch bark can be used in water-repellent coatings [6]. By applying depolymerized SA to cellulose-coated films and thermally treating them, researchers have found that the suberin coating enhances water resistance and promotes water repellency [7]. These water-repellent properties are highly valued in industries such as wood material impregnation [8]. Therefore, creating such coatings from renewable resources like suberin could provide an opportunity to replace coatings derived from fossil resources [9]. Another application for SA is their use as a binder in various board materials [10]. Our previous studies have found applications for by-products from the plywood manufacturing process, such as birch shavings and bark [10]. There, we described how to hot-press particleboards with a SA binder. By obtaining the SA mixture in an alkaline-water environment from birch outer bark and using it as a binder in particleboard pressing [11], the resulting wood panels achieved a bending strength of 17.1 N/mm2 [5]. These promising properties led us to test several SA solutions into bulk wood impregnation.
To extract SA from plant cells, suberin macromolecules must be depolymerized or broken down [9]. In the past, methods for SA depolymerization were not well-studied, which limited the potential applications of suberin. With various suberin depolymerization methods now appearing in the literature, numerous applications for suberin have also emerged [12]. Depolymerization methods are mainly divided into two types: chemical and enzymatic depolymerization [4]. The yield of the obtained SA can vary not only depending on the source of the suberin but also on the depolymerization method used [13].
Chemical methods include acid or base methanolysis [12], as well as acid or base hydrolysis [4]. To obtain the purest possible SA, an extraction of birch outer bark with organic solvents is necessary before depolymerization, thus removing extractives and waxes present in the plant’s protective layer [14]. Enzymatic depolymerization of suberin can be performed using various enzymes, such as lipase, esterase, and cutinase [13,15]. These enzymes are obtained from different yeasts and bacteria, which can act as pathogens and cause plant infections [16]. For impregnation application, we chose depolymerization in the ethanol environment using KOH as an alkaline agent based on our previous research [5].
After depolymerization, the composition of suberin monomers or oligomers primarily includes fatty acids, hydroxy fatty acids, dicarboxylic acids, aliphatic alcohols, epoxy derivatives, and aromatic acids, depending on the plant material [17] (Fig. 1). Hydroxy fatty acids are the most commonly found group of SA monomers [18].
Figure 1: The main derivatives of saturated fatty acids obtained by depolymerizing birch bark in an alkaline environment are: epoxy derivatives (A), dicarboxylic acids (B), and hydroxy fatty acids (C)
In wood protection, there is a growing trend toward creating hydrophobic structures to improve water repellency, increase dimensional stability, and extend the service life of wood products [19]. A novel and simple method for preparing highly hydrophobic wood, with a 30% improvement in dimensional stability, has been reported [8,20]. The long alkyl chains were chemically bonded (grafted) onto the cell walls via a reaction between the hydroxyl groups in the wood and the isocyanate groups of octadecyl isocyanate, thus forming a stable bulk hydrophobic structure [21]. These excellent hydrophobic properties were achieved throughout the entire wood sample, not just on the surface but also within the core [22]. Another approach is to use chemically modified wood using different molecular with phenol formaldehyde resins with different chain length fatty acid chlorides [21]. It was concluded that using a longer chain fatty acid chloride (C16–C18) compared to C12–C14 resulted in higher maximum surface hydrophobicity [23]. However, these methods often involve non-sustainable substances. Considering that SA contains long fatty acids and tends to cure at higher temperatures, there is a potential that bark-derived chemicals such as SA could improve wood’s functionality in construction [24]. SA-based cell wall modifications could reduce moisture content and enhance dimensional stability in treated wood [25]. However, these compounds should enhance properties related to wood protection, including decay resistance.
The primary goal of this work was to examine the chemical composition of various solutions of SA obtained in the ethanol-alkaline solution and assess their potential for wood impregnation. Our study aimed to identify sustainable alternatives to harmful petroleum-derived chemicals by utilizing SA in wood treatment formulations. This involved evaluating different SA fractions—specifically, SA potassium salts in ethanol (SAK-EtOH) and water (SAK-H2O), SA suspension in H2O (SAS-H2O), and dried SA diluted in ethanol (DSA-EtOH) to determine their effectiveness in enhancing the functionality of wood, particularly for moisture and wood protection. The research focused on selecting the most suitable SA solutions for wood impregnation to optimize performance in terms of weight percent gain (WPG) and leaching resistance.
2.1 Raw Material—Birch Outer Bark
A sample industrial waste was chosen from the fractionated and isolated birch outer bark of the AS Latvijas Finieris plywood industry (Latvia). Samples of birch outer bark (moisture content: 4%–5%) were dried at room temperature and ground in an SM 100 cutting mill (Retsch GmbH, Haan, Germany) so that they could pass through a sieve with 4 mm square holes. An AS 200 Basic vibrating sieve shaker (Retsch GmbH, Haan, Germany) was used to separate milled birch outer bark, and a fraction of 1–3.15 mm was recovered. Ethanol was used twice to remove fractionated birch outer bark, following Makars et al.’s protocol [26]. Birch outer bark with a moisture level of roughly 5%–6% was ground to pass through in order to increase the production and quality of SA [10] after extraction.
For each impregnation 10 radiata Pine wood samples (25 mm × 15 mm × 50 mm) were chosen with the closest density. Oven-dried weights were determined after drying at 103 ± 2°C for 24 h.
2.2 Other Materials and Reagents
Ethanol (96.3% v/v) was supplied by SIA Kalsnavas elevators (Jaunkalsnava, Latvia). Tetrahydrofuran (THF), anhydrous, ≥99.9%, inhibitor-free; pyridine (Py), suitable for HPLC, ≥99.9%; Silylating mixture III, for gas chromatography (GC) derivatization; potassium hydroxide (KOH), puriss., ≥85%; nitric acid (HNO3), for analysis, 69%; 1.8-octanediol, puriss ≥98%; myristic acid, Sigma Grade, ≥99%; 2-hydroxyoctanoic acid, puriss, ≥98%; dodecanedioic acid, puriss, ≥99%; betulin, puriss, ≥98%; ferulic acid, puriss, ≥99%.
2.3 Obtaining SA and Solutions for Impregnation
About 2000 g of dry extracted birch outer bark was depolymerized in potassium hydroxide (670 g) 90 Vol% ethanol–water solution (20 L) for 60 min at 80°C. Following depolymerization, the mixture was filtered and chilled to 25°C. The first sample was obtained from the reaction mixture (SA potassium salts in ethanol, or SAK-EtOH), and the filtrate was evaporated until 70% of the ethanol-water solvent was recovered. The remaining mixed mass was further diluted with 4 L of water, and SA potassium salts in water, or SAK-H2O, was extracted for the second sample. The resulting mixture was split into two equal portions and acidified to a pH of 1. The third sample consisted of one portion, which was the SA suspension in water, or SAS-H2O. The fourth sample was diluted in ethanol, or DSA-EtOH, after being dried at 80°C. Because the initial SAK-EtOH sample had such a solid content, the solid content of all SA impregnation solutions was kept constant at 7%. By adding ethanol (DSA-EtOH) or deionized water (SAK-H2O and SAS-H2O), the remaining samples were adjusted to the same solid content. In Fig. 2, the sample preparation scheme is displayed.
Figure 2: Scheme of the SA solution liquid product obtaining
2.4 Impregnation of Wood Blocks
Oven-dried specimens were impregnated with SA solutions in a laboratory glass reactor via a two-step impregnation method (impregnation scheme is shown in Fig. 3). The vacuum step was used (for 1 h at 2 kPa) to ensure the ejection of air from the specimens. To ensure the diffusion of the SA oligomers into the wood cell walls, the specimens were submersed (for 2 h at 100 kPa) in the solutions (the second step). After impregnation, the specimens were oven-dried, and the WPG was calculated to assess the amount of SA in the wood. To avoid crack formation during drying, the temperature was increased gradually. The SA-treated wood samples were cured at 100°C for 2 h. The average WPG was calculated for each treatment according to Eq. (1):
WPG (%)=((M1−M2)/M2)×100 (1)
where M1 is the oven-dried mass after impregnation, and M2 is the oven-dried mass before impregnation. Theoretical WPG was calculated when M1 was the mass of the theoretically possible amount of impregnation liquid uptake multiplied with the solid content of the solution. While the practical WPG was calculated when the M1 was the mass of the practically weighed samples after impregnation and drying procedure. WPG after leaching was calculated when the M1 was the mass of the dried impregnated samples after leaching procedure described in the next section.
Figure 3: Scheme of the wood block impregnation process
2.5 Leaching of Impregnated Wood Blocks
Leaching was performed over 14 days according to EN 84 (2021)-Accelerated aging of treated wood to verify the chemical fixation of SA in the wood. After 14 days, the excess water was blotted off, and the specimens were dried in an oven with a stepwise temperature increase. The dry weight after the test was determined and the amount of leached SA solution was calculated.
2.6 FTIR Analysis of SA Preparation Products
Thermo Fisher Scientific, MA, US Nicolet iS50 spectrometer data with a resolution of 0.2 cm−1, 32 scans were used to examine the SA structure. The attenuated total reflectance method using a diamond crystal prism was used to gather the FTIR data.
2.7 GC-MS Analysis of SA Preparation Products
SA samples were converted into the corresponding trimethylsilyl (TMS) derivatives and analyzed quantitatively by GC-MS, allowing the identification of monomeric structures present in the mixture. SA samples (approximately 50–100 mg) were reacted with 100 µL of Py, 200 µL silylating mixture III (1-(trimethylsilyl) imidazole/BSTFA/TMCS 3/3/2 (v/v/v)) for 20 min at 70°C. After derivatization, the sample (1 μL) was injected into a Thermo Scientific TRACE 1300 gas chromatograph with a Thermo Scientific ISQ quadrupole mass detector. A Thermo Scientific TG-5MS (30 m × 0.25 mm × 0.25 µm) column was used. Injector temperature: 250°C. In spitless mode, carrier gas (helium) flow 1.20 mL/min. Oven temperature program: isothermally held at 150°C for 5 min, then increased at 10°C/min and held for 1 min, before being finally increased at 2°C/min and passed at 300°C for 15 min. The total time of analysis was 60 min. The transition line temperature of the mass detector was 250°C, and the ion source temperature was 200°C. Mass range 45–700 Da. In order to quantitatively determine the compounds in SA samples, we choose several standard substances covering different groups of compounds:
1) Diols (1.8-octanediol),
2) Fatty acids and their esters (myristic acid),
3) Hydroxy acids and their esters (2-hydroxyoctanoic acid),
4) Diacids and their esters (dodecanedioic acid),
5) Extractives (betulin and lupeol),
6) Aromatics (ferulic acid),
7) Carbohydrates (D-glucouronic acid),
8) Other.
2.8 GPC Analysis of Impregnation Liquids
An Agilent 1260 Infinity HPLC system with an isocratic pump, degasser, and autosampler was used to analyze the SA samples. For separation we used PLgel MIXED-E 300 × 8 mm column at 40°C. For detection, Optilab®’s Refractive Index Detector was employed. The RI detector’s thermostat was set at 40°C. Tetrahydrofuran (THF) was the mobile phase, and its flow rate was 1.0 mL·min−1. SA samples were prepared as THF solutions with 5 mg·mL−1 mass concentration and filtered through nylon syringe filters to remove undissolved solids (0.22 µm). There was a 100 µL injection volume. The polystyrene standards (with molar mass 500, 850, 1000, 2500, 3000, 5000, 9000, 17,500, and 20,000 Da) were used in the computations for the data acquired by GPC-RID.
3.1 SA Preparation Product Characteristics–FTIR Analysis
To understand the distribution of functional groups of the dried SA samples FTIR analysis was carried out. The FTIR spectra (Fig. 4) revealed distinct differences in the hydroxyl group content (3350 cm−1), aliphatic chain length (3000–2800 cm−1), indicating longer fatty acid chains and higher molecular masses. Additionally, significant variations in C = O group content were observed at 1710 cm−1. FTIR data for the SA potassium salts in ethanol (SAK-EtOH) and water (SAK-H2O) showed that there is a higher OH to CH2 signal ratio, indicating that these samples have a high content of hydroxyl groups. This is also evidenced by the signal at 1100 cm−1. Logically, these samples exhibit a strong COO− salt signal at 1570 cm−1. Overall, this suggests that these samples are highly polar with a high content of functional groups.
Figure 4: FTIR spectra of the SA preparation products
A very strong peak at 1710 cm−1, representing carboxylic acid groups, in samples SAS-H2O and DSA-EtOH, indicating more free fatty acid content. A small shoulder of this peak also appeared at ~1730 cm−1 as the SA samples contained some esters, with a more extended shoulder for the DSA-EtOH sample. This could be attributed to the formation of additional ethyl esters during the drying and ethanol dilution process. The symmetric and asymmetric stretching vibrations of -O-NO2 at 1270 cm−1 and 1625 cm−1 can be seen in the spectra for samples SAS-H2O and DSA-EtOH. This indicates that SA sample contains a noticeable residue of HNO3 left over after the acidification procedure. Additionally, the broad absorption peak between 3600 and 3100 cm−1 of spectra of all obtained SA samples was identified as characteristic stretching vibrations of the -O-H group.
3.2 Suberin Monomers of SA Preparation Products
To determine suberin monomeric compounds, we employed our developed GC-MS method [18]. In most studies on suberin composition, the quantification of individual suberin monomers is performed using the peak areas of MS or FID signals [27]. However, variations in response factors and electron-impact fragmentation of the analyzed monomers can introduce significant inaccuracies in the quantification data. Therefore, we used standard calibrations for monomer quantification. As outlined in Section 2.4, we used several standard substances covering different groups of compounds: diols (1), fatty acids (2), hydroxy acids and their esters (3), diacids and their esters (4), extractives (5), aromatics (6), carbohydrates (7) and others (8).
Suberin monomeric constituents were determined by direct sample silylation. Fig. 5 shows the gas chromatogram of the methyl ester TMS ether derivatives of suberin samples. Table 1 shows the identified suberin monomers and the molecular weight of the corresponding silyl derivatives. In addition, identified compounds were sorted into corresponding group.
Figure 5: GC-MS chromatograms of the SA preparation products
After cooking birch bark suberin in a KOH ethanol solution, filtering, and drying, the SA remained in their salt form (SAK-EtOH), constituting approximately 33%. These primarily comprised dicarboxylic acids, with the remaining SA existing in smaller quantities as a mixture of various substances. The remaining SA were present in smaller amounts, which was a mixture of various substances. Considering that depolymerization was carried out in an ethanol medium, the solution contained a large excess of triterpene extractives—total 38.81%. Additionally, there was a polyphenolic compound (ferulic acid), which is logical since polyphenolic compounds in birch bark are in the form of tannins and they also depolymerize in an alkaline environment and dissolve in ethanol [26]. Overall, 74% of the compounds in the SAK-EtOH sample were identified, suggesting that the remaining 26% consists of high molecular weight compounds (oligomers) or potassium salts that persisted after chromatographic separation of potassium suberinates.
After evaporating the SAK-EtOH sample and diluting it with water, a mixture of potassium SA salts were obtained in an aqueous medium. In this mixture, where the SA was still in its salt form, there were slightly more fatty acid derivatives than in the SAK-EtOH sample—approximately 45% consisted of SA and their derivatives. Some compounds precipitated after ethanol evaporation and water dilution, and this precipitate was not included in the analysis, resulting in a reduced triterpene content of 8.37%. This reduction is logical, considering that lupeol exhibits better solubility [28]. It is possible that in the ethanol-water solution, which resulted from not fully evaporating all the ethanol and then diluting with water, betulin precipitated. Consequently, a higher proportion of SA is shown here compared to the SAK-EtOH sample. Overall, 68% of the compounds have been identified, indicating that 32% consist of high molecular weight compounds (oligomers) or potassium salts remaining after the destruction of potassium suberinates in chromatography. However, it appears that due to the precipitation of triterpenes, a larger proportion of SA was present in this sample.
After diluting the SAK-EtOH sample with water and acidifying it to pH = 1, a SA suspension in an aqueous medium (SAS-H2O) was obtained. Upon filtration and drying of this suspension, the resulting mixture contained approximately 49% fatty acids, comprising SA and their derivatives, primarily C22 dicarboxylic acid dimethyl docosanedioate, consistent with our previous research findings [18]. The content of C10 dicarboxylic acid (sebacic acid) had significantly decreased, which could indicate that it has copolymerized with other compounds, possibly ferulic acid, which no longer appeared in this sample. As a result of copolymerization, the formed oligomer had such a high molecular weight that it did not reach the GC-MS detectors. In the SAS-H2O sample, the triterpene content had increased again (50.79%). This can be explained by the fact that the acidification of the SAK-H2O sample was carried out with all the precipitates included, and possibly, the triterpene agglomerate has mixed with SA. This suggests that the triterpene content in the SA is elevated unless it is separated in step 2 by filtering the precipitates. This is a significant challenge because filtering alkaline reaction masses is difficult as they form clay-like thick layers that block any porous systems, preventing the solution from passing through [29]. Nevertheless, triterpenes can also participate in the impregnation process, eliminating the need for their separation. Notably, this sample did not contain the polyphenolic compound ferulic acid. This absence could be due to SA precipitation while ferulic acid remained in solution, or ferulic acid may have participated in copolymerization, forming molecules too large for detection by GC-MS.
After the SAS-H2O sample was filtered and dried, it was then redissolved in ethanol for further use in the impregnation. For analysis, this ethanol solution of SA was dried again, resulting in a mixture (DSA-EtOH) where the fatty acid content, as determined by GC-MS, was approximately 26%. This content consists of SA and its derivatives, the majority of which is C22 dicarboxylic acid dimethyl docosanedioate. This dicarboxylic acid appeared in the case of ethanol salts (SAK-EtOH) but decreased in the case of water salts (SAK-H2O), which was explained by the presence of precipitates. After acidifying the entire mixture, when the sample was collected with all precipitates (SAS-H2O), this dicarboxylic acid became dominant again. It seems that after drying, the content of this dicarboxylic acid decreased—possibly because it underwent copolymerization reactions, resulting in molecules too large to be detected by GC-MS [18]. In the previous sample, SAS-H2O, the triterpene content was increased (50.79%), and the same trend was observed in the DSA-EtOH sample, which showed an even higher triterpene content—totaling 59.64%. This can be explained by the fact that the previous sample already had an increased triterpene content, and during the processes of drying, dissolving, and re-drying, it likely promoted the copolymerization of SA. As a result, the relative triterpene content increases because the high molecular weight compounds simply do not reach the GC-MS detector. This sample also showed no content of the polyphenolic compound ferulic acid. This was logical since the previous sample also did not contain free ferulic acid.
Among the SA, C10 diacid Sebacic acid (19), C22 diacid dimethyl docosanedioate, fatty acid ester ethyl stearate were the most prominent. Considering that the depolymerization was carried out in an ethanol medium, there was a large predominance of triterpene extractives in the solution, which should be taken into account in future studies and processes.
3.3 Molar Mass Distribution in SA Impregnation Liquids
Samples without monomeric fraction also contained a significant amount of the polymeric suberin fraction, which could not be seen by GC-MS without hydrolysis. That’s why we also performed GPC-RID analysis for all samples (Fig. 6). Table 2 summarizes the relative area percentage of each molar mass range determined with GPC-RID. The calculations were done using polystyrene standards (with molar mass 500, 850, 1000, 2500, 3000, 5000, 9000, 17,500, 20,000 Da).
Figure 6: GPC-RID chromatograms of analyzed SA impregnation liquids
GPC analysis revealed that SA salts in ethanol (SAK-EtOH) and water (SAK-H2O) have only low molecular fractions and each additional process (acidification and drying) decreased the low molecular fraction content in the sample. This suggests that SA tends to polymerize after drying, underscoring the necessity to dissolve them in ethanol for impregnation purposes.
The differences in molecular weights between GC-MS and GPC can be explained by the fact that GPC provides more informational value. This is because a polystyrene standard was used for calibration, which definitely did not correspond to suberin salt or acid mixtures. Additionally, each peak in GPC corresponds to a range of molecules rather than a specific molecule. However, it was informative as it allowed for the distinction between low molecular weight and high molecular weight fractions.
3.4 Impregnation of SA Solutions
The degree of treatment was assessed directly as the WPG of the SA-treated wood. The average WPG of pine wood blocks after impregnation and curing at 100°C is shown in Fig. 7. The theoretical WPG was attributed to the nature of the solution than for the SA substance. However, this value showed the solution properties–by how much it was impregnated in the wood structure.
Figure 7: WPG of the SA solution treated pine wood specimens
As can be seen in Fig. 7, the highest WPG after leaching was obtained for DSA-EtOH solution at 5.18% in comparison with 6.18% of practical WPG. This means that 83.8% of SA was fixed in the sample. Slight mass loss could be explained by the reaction of SA with wood and fixation during drying. Salts of SA (SAK-Et-OH and SAK-H2O) were leached out from the sample, due to the solubility of the salts. SAS-H2O solution showed a different uptake mechanism from other solutions. Based on visual observation, the wood blocks appeared darker after treatment, suggesting that some material had been impregnated into the samples (Fig. 8). However, considering the solution uptake (Fig. 9) and WPG value difference between theoretical and practical ones, it can be concluded that the SA from the solution was distributed only on the surface. While all the water from the solution was impregnated in the wood. It can be explained that SA oligomers in the suspension are agglomerated and thus they are too large to migrate into the wood cell structure. Still, these results show that SAS-H2O could be useful as a potential coating substance.
Figure 8: Visual appearance of the impregnated samples after leaching and drying
Figure 9: Solution uptake of the SA solutions treated pine wood specimens
The solution uptake in Fig. 9 showed that SAS-H2O solution had the highest value.
This could be explained by the fact that SAS was not suitable solution for impregnation–mostly water from the solution impregnated in the wood block as it can be seen in the results of WPG practically or after leaching (Fig. 7). Overall, the discrepancy between the theoretical and practical WPG indicated the presence of large molecules or agglomerates in the solution, which do not homogenously impregnate the wood. GPC data support the presence of these large molecules in all SA impregnation solutions. While initial results of the DSA-EtOH solution show promise, further optimization of solution concentration and curing temperature is necessary. Additional measurements on bulking tests should also be conducted to gain a more comprehensive understanding of impregnation depth and dimensional stability [30]. Ultimately, it’s crucial to examine the resistance of treated wood samples against deteriorating organisms. This will provide more insight into the protective efficacy of the SA treatment.
There is potential for SA to be used for wood treatment formulations that substitute harmful and petroleum-derived chemicals, and simultaneously extend the functionality of wood in building and construction end-uses, for example, impregnation to protect from moisture and fungal exposure. The key findings supporting this potential are as follows:
• SA salts in ethanol (SAK-EtOH) and water (SAK-H2O) have mostly low molecular fractions, and each additional process (acidification and drying) decreases the low molecular content in the sample.
• Despite the presence of lower molecule fractions SA salts do not fixate in the wood cells, and the highest WPG and leaching resistance showed the ethanol solution of SA–DSA-EtOH.
• Optimization of concentration and curing temperature as well as fungal tests should be carried out to optimize SA solutions for wood protective purposes.
Acknowledgement: We express our gratitude to AS Latvijas Finieris for delivering the raw material for extraction and depolymerization.
Funding Statement: This research was funded by BarkBuild–Tree Bark as a Renewable Source of Wood Protection Materials for Building Applications (ES RTD/2022/14 within ERA-NET Cofund Action “ForestValue–Innovating the Forest-Based Bioeconomy”). Project BarkBuild is supported under the umbrella of ERA-NET Cofund ForestValue by Valsts izglītības attīstības aģentūra (Latvia), Vinnova (Sweden), Ministry of Education, Science and Sport (MIZS) (Slovenia), Academy of Finland, The Research Council of Norway, and National Science Centre, Poland. ForestValue has received funding from the European Union’s Horizon 2020 research and innovation programme under grant agreement No. 773324. This work was supported according to contract No. 5.1.1.2.i.0/1/22/A/CFLA/007 between “Forest Sector Competence Centre of Latvia” Ltd., and the Central Finance and Contracting Agency which dated 20th January of 2023.
Author Contributions: The authors confirm their contribution to the paper as follows: study conception and design: Janis Rizikovs, Aigars Paze, Andreas Treu; data collection: Daniela Godina, Guntis Sosins, Janis Rizikovs, Raimonds Makars.; analysis and interpretation of results: Daniela Godina, Janis Rizikovs, Aigars Paze, Andreas Treu, Raimonds Makars; draft manuscript preparation: Daniela Godina, Janis Rizikovs, Aigars Paze, Guntis Sosins. All authors reviewed the results and approved the final version of the manuscript.
Availability of Data and Materials: The data presented in this study are available on request from the corresponding authors.
Ethics Approval: Not applicable.
Conflicts of Interest: The authors declare that they have no conflicts of interest to report regarding the present study.
References
1. Graça J. Suberin: the biopolyester at the frontier of plants. Front Chem. 2015;3. doi:10.3389/fchem.2015.00062. [Google Scholar] [PubMed] [CrossRef]
2. Harman-Ware AE, Sparks S, Addison B, Kalluri UC. Importance of suberin biopolymer in plant function, contributions to soil organic carbon and in the production of bio-derived energy and materials. Biotechnol Biofuels. 2021;14:75. doi:10.1186/s13068-021-01892-3. [Google Scholar] [PubMed] [CrossRef]
3. Pinales-Márquez CD, Rodríguez-Jasso RM, Araújo RG, Loredo-Treviño A, Nabarlatz D, Gullón B, et al. Circular bioeconomy and integrated biorefinery in the production of xylooligosaccharides from lignocellulosic biomass: a review. Ind Crops Prod. 2021;162:113274. doi:10.1016/j.indcrop.2021.113274. [Google Scholar] [CrossRef]
4. Woolfson KN, Esfandiari M, Bernards MA. Suberin biosynthesis, assembly, and regulation. Plants. 2022;11:555. doi:10.3390/plants11040555. [Google Scholar] [PubMed] [CrossRef]
5. Rizikovs J, Paze A, Godina D, Makars R, Sosins G, Abolins A. Suberinic acids as adhesive in wood bio-based composites and polymer constituents. In: Proceedings of the European Biomass Conference and Exhibition Proceedings, 2023 Jun 5–8; Bologna: ETA-Florenc Renewable Energies; p. 1027–32. [Google Scholar]
6. Kumar A, Korpinen R, Möttönen V, Verkasalo E. Suberin fatty acid hydrolysates from outer birch bark for hydrophobic coating on aspen wood surface. Polymers. 2022;14:832. doi:10.3390/polym14040832. [Google Scholar] [PubMed] [CrossRef]
7. Garcia H, Ferreira R, Martins C, Sousa AF, Freire CSR, Silvestre AJD, et al. Ex situ reconstitution of the plant biopolyester suberin as a film. Biomacromolecules. 2014;15:1806–13. doi:10.1021/bm500201s. [Google Scholar] [PubMed] [CrossRef]
8. Chen J, Wang Y, Cao J, Wang W. Improved water repellency and dimensional stability of wood via impregnation with an epoxidized linseed oil and carnauba wax complex emulsion. Forests. 2020;11:271. doi:10.3390/f11030271. [Google Scholar] [CrossRef]
9. Negi A, Kataria R. Suberin–a potential source of renewable chemicals for industrial applications. Res J Biotechnol. 2022;17(3):182–91. doi:10.25303/1703rjbt182191. [Google Scholar] [CrossRef]
10. Makars R, Rizikovs J, Godina D, Paze A, Merijs-Meri R. Utilization of suberinic acids containing residue as an adhesive for particle boards. Polymers. 2022;14:2304. doi:10.3390/polym14112304. [Google Scholar] [PubMed] [CrossRef]
11. Ferreira AM, Pereira J, Almeida M, Ferra J, Paiva N, Martins J, et al. Low-cost natural binder for particleboards production: study of manufacture conditions and stability. Int J Adhes Adhes. 2019;93:102325. doi:10.1016/j.ijadhadh.2019.01.019. [Google Scholar] [CrossRef]
12. Lecart B, Baumsteiger C, Monie F, Di Maria A, Detrembleur C, Richel A, et al. Towards green chemicals and edible coatings from barks and peels with near critical extraction of suberin. Green Chem. 2023;25:9282–91. doi:10.1039/D3GC02552G. [Google Scholar] [CrossRef]
13. Järvinen R, Silvestre AJD, Holopainen U, Kaimainen M, Nyyssölä A, Gil AM, et al. Suberin of potato (Solanum tuberosum Var. Nikolacomparison of the effect of cutinase CcCut1 with chemical depolymerization. J Agric Food Chem. 2009;57:9016–27. doi:10.1021/jf9008907. [Google Scholar] [PubMed] [CrossRef]
14. De Oliveira H, Yoon B, Michaud V, Nam J-D, Suhr J. All natural cork composites with suberin-based polyester and lignocellulosic residue. Ind Crops Prod. 2017;109:843–9. doi:10.1016/j.indcrop.2017.09.044. [Google Scholar] [CrossRef]
15. Ofong AU, Pearce RB. Suberin degradation by Rosellinia desmazieresii. Eur J For Pathol. 1994;24:316–22. doi:10.1111/j.1439-0329.1994.tb00825.x. [Google Scholar] [CrossRef]
16. Gururaj P, Khushbu S, Monisha B, Selvakumar N, Chakravarthy M, Gautam P, et al. Production, purification and application of Cutinase in enzymatic scouring of cotton fabric isolated from Acinetobacter baumannii AU10. Prep Biochem Biotechnol. 2021;51:550–61. doi:10.1080/10826068.2020.1836655. [Google Scholar] [PubMed] [CrossRef]
17. Nomberg G, Marinov O, Arya GC, Manasherova E, Cohen H. The key enzymes in the suberin biosynthetic pathway in plants: an update. Plants. 2022;11:392. doi:10.3390/plants11030392. [Google Scholar] [PubMed] [CrossRef]
18. Godina D, Makars R, Paze A, Rizhikovs J. Analytical method cluster development for comprehensive characterisation of suberinic acids derived from birch outer bark. Molecules. 2023;28:2227. doi:10.3390/molecules28052227. [Google Scholar] [PubMed] [CrossRef]
19. Pędzik M, Auriga R, Kristak L, Antov P, Rogoziński T. Physical and mechanical properties of particleboard produced with addition of walnut (Juglans regia L.) wood residues. Materials. 2022;15:1280. doi:10.3390/ma15041280. [Google Scholar] [PubMed] [CrossRef]
20. Janesch J, Arminger B, Gindl-Altmutter W, Hansmann C. Superhydrophobic coatings on wood made of plant oil and natural wax. Prog Org Coatings. 2020;148:105891. doi:10.1016/j.porgcoat.2020.105891. [Google Scholar] [CrossRef]
21. Grinins J, Iesalnieks M, Biziks V, Gritane I, Sosins G. Birch wood surface characterization after treatment with modified phenol-formaldehyde oligomers. Polymers. 2022;14:671. doi:10.3390/polym14040671. [Google Scholar] [PubMed] [CrossRef]
22. Herrera R, Poohphajai F, Sandak A, Gordobil O. Simultaneous improvement of surface wettability and UV resistance of wood with lignin-based treatments. Polymers. 2023;15:3409. doi:10.3390/polym15163409. [Google Scholar] [PubMed] [CrossRef]
23. Rodríguez-Fabià S, Torstensen J, Johansson L, Syverud K. Hydrophobization of lignocellulosic materials part III: modification with polymers. Cellulose. 2022;29:5943–77. doi:10.1007/s10570-022-04660-0. [Google Scholar] [CrossRef]
24. Deng W, Feng Y, Fu J, Guo H, Guo Y, Han B, et al. Catalytic conversion of lignocellulosic biomass into chemicals and fuels. Green Energy Environ. 2023;8:10–114. doi:10.1016/j.gee.2022.07.003. [Google Scholar] [CrossRef]
25. Mandraveli E, Mitani A, Terzopoulou P, Koutsianitis D. Oil heat treatment of wood—a comprehensive analysis of physical, chemical, and mechanical modifications. Materials. 2024;17:2394. doi:10.3390/ma17102394. [Google Scholar] [PubMed] [CrossRef]
26. Makars R, Paze A, Rizikovs J, Berzins R, Godiņa D, Puke M, et al. Changes in composition of birch outer bark extractives after recrystallization with C2–C5 alkanols. Key Eng Mater. 2020;850:3–8. doi:10.4028/www.scientific.net/KEM.850.3. [Google Scholar] [CrossRef]
27. Tahoun M, Gee CT, McCoy VE, Stoneman M, Raicu V, Engeser M, et al. Suberin, the hallmark constituent of bark, identified in a 45-million-year-old monkeyhair tree (Coumoxylon hartigii) from Geiseltal, Germany. Sci Rep. 2024;14:118. doi:10.1038/s41598-023-50402-y. [Google Scholar] [PubMed] [CrossRef]
28. Liu K, Zhang X, Xie L, Deng M, Chen H, Song J, et al. Lupeol and its derivatives as anticancer and anti-inflammatory agents: molecular mechanisms and therapeutic efficacy. Pharmacol Res. 2021;164:105373. doi:10.1016/j.phrs.2020.105373. [Google Scholar] [PubMed] [CrossRef]
29. Cescon A, Jiang J-Q. Filtration process and alternative filter media material in water treatment. Water. 2020;12:3377. doi:10.3390/w12123377. [Google Scholar] [CrossRef]
30. Zelinka SL, Altgen M, Emmerich L, Guigo N, Keplinger T, Kymäläinen M, et al. Review of wood modification and wood functionalization technologies. Forests. 2022;13:1004. doi:10.3390/f13071004. [Google Scholar] [CrossRef]
Cite This Article
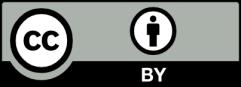
This work is licensed under a Creative Commons Attribution 4.0 International License , which permits unrestricted use, distribution, and reproduction in any medium, provided the original work is properly cited.