Open Access
ARTICLE
The Effect of Uncaria gambir on Optical Properties and Thermal Stability of CNF/PVA Biocomposite Films
1 Mechanical Engineering Department, Universitas Negeri Padang, Padang, 25173, Indonesia
2 Centre for Energy and Power Electronics Research, Universitas Negeri Padang, Padang, 25173, Indonesia
3 Department of Mechanical Engineering, National Cheng Kung University (NCKU), Tainan, 70101, Taiwan
4 Mechanical Engineering Department, Universitas Indonesia, Depok, 16424, Indonesia
5 Mechanical Engineering Department, Universitas Andalas, Padang, 25163, Indonesia
* Corresponding Author: Anna Niska Fauza. Email:
Journal of Renewable Materials 2024, 12(9), 1593-1603. https://doi.org/10.32604/jrm.2024.053651
Received 07 May 2024; Accepted 06 August 2024; Issue published 25 September 2024
Abstract
Cellulose-based film has gained popularity as an alternative to synthetic polymers due to its outstanding properties. Among all types of cellulose materials available, cellulose nanofiber (CNF) has great potential to be utilized in a diverse range of applications, including as a film material. In this study, CNF biocomposite film was prepared by using polyvinyl alcohol (PVA) as a matrix and Uncaria gambir extract as a filler. This study aims to investigate the effect of Uncaria gambir extract on the optical properties and thermal stability of the produced film. The formation of the CNF biocomposite films was confirmed using Fourier Transform Infrared Spectroscopy, their transmittance characteristics were measured using UV-Vis spectroscopy and a transmittance meter, while their reflectance was determined using a reflectance meter. The results revealed that the addition of Uncaria gambir extract to the CNF biocomposite film improved its UV-shielding properties, as indicated by the lower percentage of transmittance in the visible region, 10%–70%. In addition, its reflectance increased to 10.6% compared to the CNF film without the addition of Uncaria gambir extract. Furthermore, the thermal stability of the CNF biocomposite film with the addition of Uncaria gambir extract improved to around 400°C–500°C. In conclusion, the results showed that CNF biocomposite film prepared by adding Uncaria gambir extract can be a promising candidate for optical and thermal management materials.Keywords
Plastic products that are commonly made from synthetic polymers have been widely used in numerous applications, especially as single-use or disposable products. The convenience and practicality of plastic products have made their usage of plastic products increasingly popular in recent decades. However, the high consumption of these non-sustainable plastic products has resulted in an increase in waste produced, which is projected to rise further by around 53 million metric tons in 2030 [1]. Therefore, various remediation strategies have been proposed to overcome the negative impacts of plastic waste pollution which has caused damage to the environment and human health [2,3]. One of the most well-known solutions to this problem is the use of natural polymers that are biodegradable, abundant, and inexpensive [4], whose potential as alternative materials to synthetic polymers has been examined in several studies [5,6].
Cellulose is one of the most extensively developed natural polymers [7–9]. As it can be extracted from wide variety types of plants, this homopolymer consisting of β-D-glucopyranose units is considered the most abundant natural resource [10,11]. Owing to its high number of hydrogen bonds, cellulose is typically found as a load-bearing component in plant cell [12]. Cellulose materials have outstanding properties, such as biodegradable, renewable, sustainable [13], biocompatible and non-toxic [14], as well as having high mechanical properties [15], and tune-able optical characteristics [16], making them applicable for various usages.
Among its diverse utilizations, the use of cellulose in film production has attracted special attention in the past decades. Cellulose films can be used for different types of products, for instance, food packaging [13], coating [17,18], optoelectronics [16], flexible electronics [19], thermoelectric material, conductive film [20], and water treatment [21]. Previous studies have also shown the potential of cellulose as a promising material for an environmentally-friendly film in thermal management applications, especially to address the issues concerning plastic waste [22,23]. Nevertheless, a comprehensive investigation into this matter still needs to be explored. Previous studies have reported the use of cellulose from various resources and derivatives, either pure or combined with other materials, for the production of film. Different types of filler or additives have also been used to enhance the optical and thermal characteristics of the produced cellulose film [10]. For example, Sayed et al. utilized alkali-cellulose by adding clove essential oil to make films and reported an improved antimicrobial activity [24]. Films prepared by adding linseed oil, lemon oil, and Fe3O4 have also been proven to exhibit excellent antibacterial and antioxidant properties [13,21]. In addition, carboxymethyl cellulose (CMC) was also used in previous studies. The CMC film showed a great potential with outstanding UV-shielding characteristics [25]. While, Widyaningrum et al. explored the utilization of cellulose nanofiber (CNF) to produce films by adding silver nanowires, which successfully improved the thermal stability and conductivity of the produced films [19]. However, studies on the use of sustainable and renewable fillers for cellulose film production remain very limited. Therefore, this study aims to analyze the use of Uncaria gambir extract as a natural filler for CNF-based films.
Numerous prior studies have shown that CNF has a uniform fiber dispersion within the matrix material during the preparation of the films [26,27]. This is most likely due to the nanoscale dimensions of the CNF material that produce a high degree of crystallinity. As a result, it favored the optical and thermal characteristics of the produced film, and making it suitable for thermal management applications. In this study, CNF was prepared as a biocomposite film by using polyvinyl alcohol (PVA), which has been considered the most effective and widely used polymer matrix for the production of cellulose biocomposite films [24,28]. The Uncaria gambir extract used as a natural filler in this study consists of approximately 92% catechin, a phenolic type compound that is expected to improve the UV-light shielding characteristics and anti-bacterial activity of the produced CNF biocomposite film [29]. Therefore, the effect of adding Uncaria gambir extract to the CNF biocomposite film on its optical and thermal characteristics was investigated in this study. The presence of phenolic compound in Uncaria Gambir is expected to improve the characteristics of the produced CNF biocomposite film, especially as an alternative material for optical and thermal management applications.
Cellulose nanofiber (CNF) powder with a diameter of 10–20 nm and a length of 2–3 µm was purchased from Nanografi Nano Technology (Çankaya, Turkey). Polyvinyl Alcohol (Fully Hydrolyzed PVA, 70–100 kDa) was obtained from Sigma-Aldrich (Saint Louis, MO, USA). 95% purified Uncaria gambir powder composed of 92% catechins, 8.1% water, and 0.1% ash was purchased from FitoPure (Padang, Indonesia).
2.2 Preparation of CNF Biocomposite Films
CNF suspension, PVA solution, and Uncaria gambir (G) were prepared separately. First, 2 wt% CNF powder was dissolved in demineralized water using a magnetic stirrer at 50°C for 30 min. Then, 5 wt% PVA solution was also prepared by dissolving solid PVA in demineralized water using a magnetic stirrer at 80°C for 30 min and allowing it to cool at room temperature. Meanwhile, 1 wt% Uncaria gambir solution was prepared by dissolving the powder in demineralized water an ultrasonic processor at room temperature for 15 min and letting it sit for 2 h to remove undissolved particles (ash component) prior to the blending process.
The CNF biocomposite films were prepared using the solution casting method with a weight ratio of 10:40:10 (CNF:PVA:G). The solution was mixed using an ultrasonic processor until all components became well dispersed for approximately 45 min at room temperature. Lastly, the mixed solution was poured into a petri dish mold and dried using an oven at 80°C for 24 h.
2.3 Characterization of CNF Biocomposite Films
To confirm the formation of biocomposite films, FTIR spectroscopy (PerkinElmer, Waltham, USA) was employed to examine the functional groups of the materials used. Biocomposite film samples were prepared in a size of 1 cm × 1 cm were subsequently put into a sample holder and exposed to infrared radiation in the range of 4000–600 cm−1.
The transmittance of the biocomposite films was determined using UV-Vis spectroscopy (Shimadzu, Kyoto, Japan). For this purpose, the samples were cut into a size of 1 cm × 3 cm and placed in a sample holder. Then, the samples were subjected to wavelengths in the range of 200–800 nm. In addition, the transmittance percentage of CNF biocomposite films was also confirmed using an LH-220 optical transmittance meter (Shenzhen Lianhuicheng Technology Co., Ltd., Shenzhen, China). Biocomposite film samples were prepared in a size of 3 cm × 3 cm, placed in the test slot, and then exposed to visible light in the range of 380–760 nm.
Furthermore, reflectance percentage of the CNF biocomposite films was measured using the RM-206 digital reflectance meter (Landtek, Guangzhou, China). For this measurement, biocomposite film samples in the size of 3 cm × 3 cm were prepared and then exposed to visible light.
Lastly, the thermal stability of the CNF biocomposite films was examined using the TA-WS 60 Thermogravimetric Analyzer (Shimadzu, Kyoto, Japan). 10 mg of biocomposite film samples were prepared and then placed on an aluminum plate. Then, the measurement was carried out under an argon gas atmosphere in the range of 25°C–800°C.
3.1 Formation of CNF Biocomposite Films
Films were successfully prepared using the solution casting method with three different compositions, namely pure PVA, PVA-CNF, and PVA-CNF-G. All samples showed similar thicknesses of around 0.2–0.3 mm and varying grammages of 221.67, 281.67, and 304.17 g/m2 for PVA, PVA-CNF, and PVA-CNF-G films, respectively. In addition, among all samples, PVA film displayed the highest transparency. The addition of CNF to PVA slightly reduced the transparency of the produced film, whereas the addition of Uncaria gambir extract completely changed the visual appearance of the film to a yellowish color. The visual comparison of all samples can be seen in Fig. 1.
Figure 1: (A) PVA (5 wt%), (B) PVA-CNF (5:2 wt%), and (C) PVA-CNF-G (5:2:1 wt%) biocomposite films
The formation of the produced biocomposite films was confirmed by the FTIR spectrometry characterization to identify the functional groups of the used materials within the films. The spectra of PVA and PVA-CNF biocomposite films showed similar patterns with several peaks indicating the chemical composition of each material (as can be seen in Fig. 2), where two samples displayed high peaks at 3268 and 2920 cm−1 which were assigned as O-H stretching of intramolecular and intermolecular within the hydroxyl groups, respectively. This finding confirms previous studies which also reported that the addition of CNF to PVA did not affect the chemical structure of the film [19,30]. Moreover, the peaks of around 1650, 1082, and 840 cm−1 indicated the C=O stretching, C-O stretching functional groups, and C-H vibration, respectively [31].
Figure 2: FTIR spectra of PVA and PVA-CNF biocomposite films
On the other hand, according to the FTIR spectrum of PVA-CNF-G showed in Fig. 3A, the sample with the addition of Uncaria gambir extract experienced one significant peak at 1602 cm−1 signifying the presence of the C=C stretching in phenolic rings of the catechin structure which is the composition of the Uncaria gambir extract that has antioxidant and anti-microbial properties. This is confirmed by the FTIR spectrum of Uncaria gambir extract in Fig. 3B. Furthermore, by introducing Uncaria Gambir to the biocomposite film, there was a decrease in the band intensity at 3268 and 2920 cm−1 compared to the PVA and PVA-CNF samples. This indicates that the number of O-H stretching vibrations decreased due to an increase in the degree of crosslinking that is formed between CNF and Uncaria Gambir structure [32,33]. Overall, the FTIR spectra seen in this study are similar to those in previous studies [34–36].
Figure 3: (A) FTIR spectra of PVA, PVA-CNF, and PVA-CNF-G films and (B) FTIR spectrum of Uncaria gambir extract
3.2 Optical Properties of CNF Biocomposite Films
The optical properties of the produced films were characterized using UV-Vis spectroscopy. As seen in Fig. 4A, PVA and PVA-CNF biocomposite films displayed similar results with high transmittance of around 85%–90% in range of visible light, indicating that the CNF particles were evenly dispersed within the PVA matrix and did not affect the optical properties of the produced films. The finding is in line with the previous study which reported a transmittance of around 90% for both PVA and PVA-CNF films [37]. However, the addition of Uncaria gambir extract to the film slightly reduced its transmittance percentage to around 70%–80% in the visible region. Meanwhile, within the UV region, the spectrum of the film changed dramatically with the absorption of UV light due to the presence of chromophores or phenolic rings in the Uncaria gambir extract. The biocomposite film can block 100% of UV-B rays (280–320 nm) and almost 98% of UV-A rays (320–400 nm). The result indicates that the produced biocomposite film has a good UV-shielding characteristics, especially for thermal management applications [38,39].
Figure 4: Transmittance of PVA, PVA-CNF, and PVA-CNF-G films measured using (A) UV-Vis spectroscopy and (B) a digital transmittance meter
Furthermore, the transmittance of the produced films in the visible region was also measured using a digital transmittance meter. The results showed that the transmittance percentages of PVA and PVA-CNF films were in accordance with the results obtained from the UV-Vis spectroscopy, as presented in Fig. 4B, where PVA and PVA-CNF biocomposite films had transmittance percentages of 91.88% and 89.14%, respectively. The current study showed that CNF/PVA biocomposite film had a better transmittance value compared to the other report, such as cellulose nanocrystals/polyacrylamide-based film only had 75% of transmittance at 550 nm [40]. Meanwhile, the addition of Uncaria gambir extract to the CNF biocomposite films decreased its transmittance percentage to 25.52%, indicating that the presence of catechin compounds absorbed most light in the UV region. Furthermore, based on the results of the reflectance measurement, both PVA and PVA-CNF biocomposite films possessed a low reflectance percentage of 0.74% and 1.02%, respectively. Meanwhile, introducing Uncaria gambir extract to the film increased the reflectance percentage to more than 10%, as shown in Fig. 5.
Figure 5: Reflectance of PVA, PVA-CNF, and PVA-CNF-G biocomposite films
3.3 Thermal Stability of CNF Biocomposite Films
The thermal stability of the produced films was observed using TGA curves, as shown in Fig. 6.
Figure 6: TGA curves of PVA, PVA-CNF, and PVA-CNF-G biocomposite films
The results showed that the addition of CNF and Uncaria gambir extract to the produced films influenced the thermal stability characteristic. In general, all films undergo two stages of decomposition. The film samples experienced small weight loss in the range of 83%–90% in the first stage, which is attributed to the decomposition of moisture and other volatile components [41]. The results of this observation showed that the addition of CNF and Uncaria gambir extract enhanced the thermal stability of each film, where PVA-CNF and PVA-CNF-G films experienced initial weight loss at 279°C and 286°C, respectively.
Furthermore, the second decomposition stage showed similar results, where all biocomposite films experienced a significant weight loss at temperatures around 400°C–500°C. However, the PVA-CNF-G biocomposite film exhibited better thermal stability at the maximum decomposition temperature with slightly less weight loss than the other films. This is possibly due to the presence of phenolic compounds in Uncaria gambir extract, which requires higher energy to decompose the film. In addition, the char residues of PVA and PVA-CNF films at high temperatures were 1.5% and 0.3%, respectively, whereas the PVA-CNF-G biocomposite film displayed a higher char residue of less than 10% at 800°C. Overall, these measurements showed comparable results to the previous studies [37].
In this study, CNF biocomposite films have been successfully prepared using the solution casting method by using PVA as a matrix and Uncaria gambir extract as a filler. The addition of Uncaria gambir extract was proven to affect the optical properties of the produced film. The addition of Uncaria gambir extract decreased the transmittance percentage of the biocomposite film by around 10%–70% in the visible light region. In addition, it also increased the reflectance percentage of the biocomposite film up to 10.6%. The presence of Uncaria gambir extract improved the thermal stability of biocomposite film at high temperatures. These findings imply that the CNF biocomposite film prepared with Uncaria gambir extract has the potential to be used in UV-shielding coating applications.
Acknowledgement: None.
Funding Statement: This research was funded by the Institute for Research and Community Service (LPPM) Universitas Negeri Padang, Indonesia, with a Contract Number: 1529/UN35.15/LT/2023.
Author Contributions: The authors confirm contribution to the paper as follows: study conception and design: Anna Niska Fauza, Remon Lapisa, Dieter Rahmadiawan; data collection: Anna Niska Fauza, Remon Lapisa; analysis and interpretation of results: Krismadinata, Dori Yuvenda, Randi Purnama Putra, Waskito; draft manuscript preparation: Anna Niska Fauza; writing and reviewing: Nandy Putra, Hairul Abral. All authors reviewed the results and approved the final version of the manuscript.
Availability of Data and Materials: Data available on request from the authors. The data that support the findings of this study are available from the corresponding author upon reasonable request.
Ethics Approval: Not applicable.
Conflicts of Interest: The authors declare that they have no conflicts of interest to report regarding the present study.
References
1. Walker TR, Fequet L. Current trends of unsustainable plastic production and micro(nano)plastic pollution. TrAC-Trends Anal Chem. 2023;160:116984. doi:10.1016/j.trac.2023.116984. [Google Scholar]
2. Cook CR, Halden RU. Ecological and health issues of plastic waste. In: Letcher TM, editor. Plastic waste and recycling. Cambridge, USA: Elsevier Inc.; 2020. p. 513–27. [Google Scholar]
3. Fauza AN, Qalbina F, Nurdin H, Ambiyar A, Refdinal R. The influence of processing temperature on the mechanical properties of recycled PET fibers. Teknomekanik. 2023 Jun 1;6(1):21–8. doi:10.24036/teknomekanik.v6i1.21472. [Google Scholar] [CrossRef]
4. Jain B, Mallya R, Nayak SY, Heckadka SS, Prabhu S, Mahesha GT, et al. Influence of alkali and silane treatment on the physico-mechanical properties of Grewia serrulata fibres. J Korean Wood Sci Technol. 2022 Sep;50(5):325–37. doi:10.5658/WOOD.2022.50.5.325. [Google Scholar] [CrossRef]
5. Kosior E, Mitchell J. Current industry position on plastic production and recycling. In: Letcher TM, editor. Plastic waste and recycling. Cambridge, USA: Elsevier Inc.; 2020. p. 133–62. [Google Scholar]
6. Rahmadiawan D, Fuadi Z, Kurniawan R, Abral H, Ilhamsyah F, Arafat A, et al. Tribological properties of aqueous carboxymethyl cellulose/Uncaria gambir extract as novel anti-corrosion water-based lubricant. Tribol Ind. 2022 Dec 15;44(4):584–91. doi:10.24874/ti. [Google Scholar] [CrossRef]
7. Sathishkumar TP, Navaneethakrishnan P, Shivaram SV, Kanna SS, Rajeshkumar L, Rajeshkumar G. Characterization of new cellulose fiber extracted from Pithecellobium dulce tree. Appl Sci Eng Prog. 2023 May 1;16(3):6845. [Google Scholar]
8. Sukprom T, Chanklang S, Roddecha S, Niamnuy C, Prapainainar P, Seubsai A. Lead ions removal using pineapple leaf-based modified celluloses. Appl Sci Eng Prog. 2022 May 31;16(2):6002. [Google Scholar]
9. Rahmadiawan D, Shi SC, Fuadi Z, Abral H, Putra N, Irwansyah R, et al. Experimental investigation on stability, tribological, viscosity, and thermal conductivity of MXene/carboxymethyl cellulose (CMC) water-based nanofluid lubricant. J Tribol. 2023;39:36–50. [Google Scholar]
10. Baseer RA, Dacrory S, El Gendy MAM, Ewies EF, Kamel S. A biodegradable film based on cellulose and thiazolidine bearing UV shielding property. Sci Rep. 2022 May 12;12(1):7887. doi:10.1038/s41598-022-11457-5. [Google Scholar] [PubMed] [CrossRef]
11. Zendrato HM, Devi YS, Masruchin N, Wistara NJ. Soda pulping of torch ginger stem: promising source of nonwood-based cellulose. J Korean Wood Sci Technol. 2021 Jul 25;49(4):287–98. doi:10.5658/WOOD.2021.49.4.287. [Google Scholar] [CrossRef]
12. Zugenmaier P. Introduction. In: Crystalline cellulose and cellulose derivatives: characterization and structures. Berlin, Germany: Springer-Verlag Berlin Heidelberg GmbH & Co. K.; 2008. [Google Scholar]
13. Arun R, Shruthy R, Preetha R, Sreejit V. Biodegradable nano composite reinforced with cellulose nano fiber from coconut industry waste for replacing synthetic plastic food packaging. Chemosphere. 2022;291:132786. doi:10.1016/j.chemosphere.2021.132786. [Google Scholar] [PubMed] [CrossRef]
14. Azadi S, Peng S, Moshizi SA, Asadnia M, Xu J, Park I, et al. Biocompatible and highly stretchable PVA/AgNWs hydrogel strain sensors for human motion detection. Adv Mater Technol. 2020;5(11):1–12. [Google Scholar]
15. Samiee S, Ahmadzadeh H, Hosseini M, Lyon S. Algae as a source of microcrystalline cellulose. In: Hosseini M, editor. Advanced bioprocessing for alternative fuels, biobased chemicals, and bioproducts. Duxford: Woodhead Publishing; 2019. p. 331–50. [Google Scholar]
16. Badry R, El-Nahass MM, Nada N, Elhaes H, Ibrahim MA. Structural and UV-blocking properties of carboxymethyl cellulose sodium/CuO nanocomposite films. Sci Rep. 2023;13(1):1–18. [Google Scholar]
17. Huang S, Wang X, Zhang Y, Meng Y, Hua F, Xia X. Cellulose nanofibers/polyvinyl alcohol blends as an efficient coating to improve the hydrophobic and oleophobic properties of paper. Sci Rep. 2022;12(1):1–10. [Google Scholar]
18. Shi SC, Tsai XN. Cellulose derivative as protection coating: effect of nanoparticle additives on load capacity. Teknomekanik. 2022 Dec 15;5(2):90–6. doi:10.24036/teknomekanik.v5i2.16372. [Google Scholar] [CrossRef]
19. Widyaningrum BA, Amanda P, Pramasari DA, Ningrum RS, Kusumaningrum WB, Kurniawan YD, et al. Preparation of a conductive cellulose nanofiber-reinforced PVA composite film with silver nanowires loading. Nano-Struct Nano-Objects. 2022;31:100904. doi:10.1016/j.nanoso.2022.100904. [Google Scholar] [CrossRef]
20. Long Q, Jiang G, Zhou J, Zhao D, Jia P, Nie S. Cellulose ionic gel and its sustainable thermoelectric devices–design, applications and prospects. Nano Energy. 2024 Feb;120:109130. doi:10.1016/j.nanoen.2023.109130. [Google Scholar] [CrossRef]
21. Luo H, Jiang YZ, Tan L. Positively-charged microcrystalline cellulose microparticles: rapid killing effect on bacteria, trapping behavior and excellent elimination efficiency of biofilm matrix from water environment. J Hazard Mater. 2022;424:127299. doi:10.1016/j.jhazmat.2021.127299. [Google Scholar] [PubMed] [CrossRef]
22. Sato K, Tominaga Y, Imai Y. Nanocelluloses and related materials applicable in thermal management of electronic devices: a review. Nanomater. 2020;10(3):1–13. [Google Scholar]
23. Guo Y, An X, Qian X. Biodegradable and reprocessable cellulose-based polyurethane films for bonding and heat dissipation in transparent electronic devices. Ind Crops Prod. 2023;193:116247. doi:10.1016/j.indcrop.2023.116247. [Google Scholar] [CrossRef]
24. Sayed A, Safwat G, Abdel-raouf M, Mahmoud GA. Alkali-cellulose/polyvinyl alcohol biofilms fabricated with essential clove oil as a novel scented antimicrobial packaging material. Carbohydr Polym Technol Appl. 2023;5:100273. [Google Scholar]
25. Dhineshbabu NR, Vettumperumal R, Kokila R. A study of linear optical properties of ternary blends PVA/CMC/aloe vera biofilm for UV shielding. Appl Nanosci. 2021;11(2):669–78. doi:10.1007/s13204-020-01629-y. [Google Scholar] [CrossRef]
26. Wang Z, Qiao X, Sun K. Rice straw cellulose nanofibrils reinforced poly(vinyl alcohol) composite films. Carbohydr Polym. 2018;197:442–50. doi:10.1016/j.carbpol.2018.06.025. [Google Scholar] [PubMed] [CrossRef]
27. Ratnawati, Amanda Septevani A, Nurul A, Arifin Y, Handayani Handayani AS. Synthesis and characterization of cellulose nanofiber/poly-vinyl alcohol (CNF/PVA) nanocomposites for gas barrier applications in paper packaging. Mater Today: Proc. 2023. doi:10.1016/j.matpr.2023.04.248. [Google Scholar] [CrossRef]
28. Sudri NM, Handayani AS, Septevani AA, Puspita ME, Husnil YA, Arifin Y, et al. Blending process of cellulose nanofiber/polyvinyl alcohol (NFC/PVA) for paper coating application. Jurnal Sains dan Materi Indonesia. 2023;24(2):105–16. doi:10.55981/jsmi.v24i2. [Google Scholar] [CrossRef]
29. Miksusanti, Fithri AN, Herlina, Wijaya DP, Taher T. Optimization of chitosan-tapioca starch composite as polymer in the formulation of gingival mucoadhesive patch film for delivery of gambier (Uncaria gambir Roxb) leaf extract. Int J Biol Macromol. 2020 Feb;144:289–95. doi:10.1016/j.ijbiomac.2019.12.086. [Google Scholar] [PubMed] [CrossRef]
30. Ji X, Guo J, Guan F, Liu Y, Yang Q, Zhang X, et al. Preparation of electrospun polyvinyl alcohol/nanocellulose composite film and evaluation of its biomedical performance. Gels. 2021 Nov 19;7(4):223. doi:10.3390/gels7040223. [Google Scholar] [PubMed] [CrossRef]
31. Pal N, Banerjee S, Roy P, Pal K. Cellulose nanocrystals-silver nanoparticles-reduced graphene oxide based hybrid PVA nanocomposites and its antimicrobial properties. Int J Biol Macromol. 2021 Nov;191:445–56. doi:10.1016/j.ijbiomac.2021.08.237. [Google Scholar] [PubMed] [CrossRef]
32. Rahmadiawan D, Abral H, Shi SC, Huang TT, Zainul R, Ambiyar A, et al. Tribological properties of polyvinyl alcohol/Uncaria gambir extract composite as potential green protective film. Tribol Ind. 2023 Jun 15;45(1):367–274. doi:10.24874/ti. [Google Scholar] [CrossRef]
33. Aliabadi M, Chee BS, Matos M, Cortese YJ, Nugent MJD, de Lima TAM, et al. Microfibrillated cellulose films containing chitosan and tannic acid for wound healing applications. J Mater Sci Mater Med. 2021 Jun 12;32(6):67. doi:10.1007/s10856-021-06536-4. [Google Scholar] [PubMed] [CrossRef]
34. Abral H, Kurniawan A, Rahmadiawan D, Handayani D, Sugiarti E, Muslimin AN. Highly antimicrobial and strong cellulose-based biocomposite film prepared with bacterial cellulose powders, Uncaria gambir, and ultrasonication treatment. Int J Biol Macromol. 2022 May;208:88–96. doi:10.1016/j.ijbiomac.2022.02.154. [Google Scholar] [PubMed] [CrossRef]
35. da Cruz JA, da Silva AB, Ramin BBS, Souza PR, Popat KC, Zola RS, et al. Poly(vinyl alcohol)/cationic tannin blend films with antioxidant and antimicrobial activities. Mater Sci Eng C. 2020 Feb;107:110357. doi:10.1016/j.msec.2019.110357. [Google Scholar] [PubMed] [CrossRef]
36. Munggari IP, Kurnia D, Deawati Y, Julaeha E. Current research of phytochemical, medicinal and non-medicinal uses of Uncaria gambir Roxb.: a review. Molecules. 2022 Oct 3;27(19):6551. doi:10.3390/molecules27196551. [Google Scholar] [PubMed] [CrossRef]
37. Pan Y, Liu L, Song L, Hu Y, Jiang S, Zhao H. Reinforcement of layer-by-layer self-assembly coating modified cellulose nanofibers to reduce the flammability of polyvinyl alcohol. Cellulose. 2019 Mar 4;26(5):3183–92. doi:10.1007/s10570-019-02298-z. [Google Scholar] [CrossRef]
38. Li X, Li J, Shen X, Cao M, Wang Y, Zhang W, et al. Transparent cellulose/lignin composite films with adjustable haze and UV-blocking performance for light management. ACS Sustain Chem Eng. 2024 Apr 8;12(14):5427–35. doi:10.1021/acssuschemeng.3c07076. [Google Scholar] [CrossRef]
39. Sun H, Liu Y, Guo X, Zeng K, Kanti Mondal A, Li J, et al. Strong, robust cellulose composite film for efficient light management in energy efficient building. Chem Eng J. 2021;425:131469. doi:10.1016/j.cej.2021.131469. [Google Scholar] [CrossRef]
40. Zhang Y, Li D, Yang C, Xiong Z, Tohti M, Zhang Y, et al. Polymerization strategy for cellulose nanocrystals-based photonic crystal films with water resisting property. Int J Biol Macromol. 2024 Apr;265:130793. doi:10.1016/j.ijbiomac.2024.130793. [Google Scholar] [PubMed] [CrossRef]
41. Zhang Q, Lu W, Wu M, Qi G, Yuan Y, Li J, et al. Preparation and properties of cellulosenanofiber (CNF)/polyvinyl alcohol (PVA)/graphene oxide (GO): application of CO2 absorption capacity and molecular dynamics simulation. J Environ Manage. 2022 Jan;302:114044. doi:10.1016/j.jenvman.2021.114044. [Google Scholar] [PubMed] [CrossRef]
Cite This Article
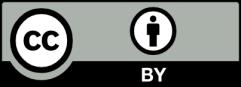
This work is licensed under a Creative Commons Attribution 4.0 International License , which permits unrestricted use, distribution, and reproduction in any medium, provided the original work is properly cited.