Open Access
ARTICLE
Phosphoric Acid Pretreatment and Saccharification of Paper Sludge as a Renewable Material for Cellulosic Fibers
1 Chemical Engineering and Pilot Plant Department, National Research Centre, Dokki, Giza, 12622, Egypt
2 Cellulose and Paper Department, National Research Centre, Dokki, Giza, 12622, Egypt
* Corresponding Author: Mohammad Hassan. Email:
Journal of Renewable Materials 2024, 12(9), 1573-1591. https://doi.org/10.32604/jrm.2024.053589
Received 05 May 2024; Accepted 31 July 2024; Issue published 25 September 2024
Abstract
Recycling of paper sludge waste is crucial for establishing a sustainable green industry. This waste contains valuable sugars that can be converted into important chemicals such as ethanol, poly hydroxybutyrate, and lactic acid. However, the main challenge in obtaining sugars in high yield from paper sludge is the high crystallinity of cellulose, which hinders hydrolysis. To address this, pretreatment using phosphoric acid was optimized using response surface methodology to facilitate cellulose hydrolysis with minimal energy and chemicals. The created prediction model using the response surface method considered factors such as acid concentration (ranging from 60% to 85%), consistency (ranging from 4% to 10%), temperature (ranging from 25°C to 80°C), and time (ranging from 0.5 to 4 h). The results revealed that the model’s significant factors affecting the yield were acid concentration, reaction time, temperature, and the product of acid concentration and temperature, while the model’s significant factors affecting the crystallinity were the consistency, the temperature, and their product. The results showed that the optimum conditions for pretreatment were using an acid concentration of 64%, temperature of 25°C, consistency of 10%, and time of 30 min. The hydrolysis of the conditionally pretreated paper sludge resulted in a weight loss of 42%, compared to only 18% weight loss in non-pretreated paper sludge. Furthermore, the optimized conditions led to low levels of furfurals and acetic acid, which are undesirable by-products that can interfere with sugar fermentation. The total sugar obtained under the optimized conditions was 0.43 g glucose/g sample (10.46 g/L), while the contents of methyl furfural, furfural, and acetic acid were 21.65, 235.7, and 4.57 mg/L, respectively. This study demonstrates the potential of phosphoric acid for pretreatment and hydrolysis of paper sludge, enabling efficient saccharification and the production of sugars with minimal undesired by-products.Graphic Abstract
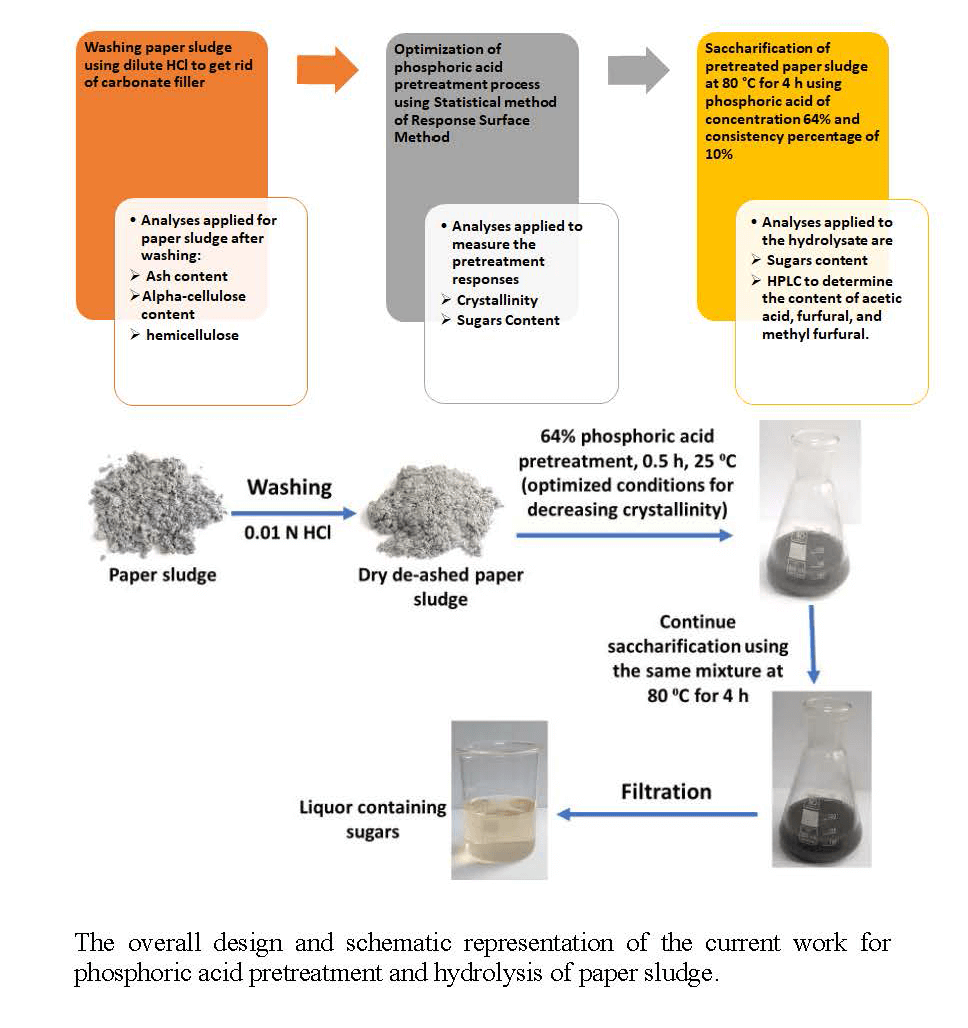
Keywords
Zero-waste industries are based on recycling any by-products into useful products, either in the same or in another process. In a recent statistical study, about 400 million tons of paper products have been consumed worldwide [1]. After papermaking, especially from recycled paper, huge amounts of waste known as paper sludge are produced in all paper mills around the world. There are different kinds of paper sludge wastes produced from papermaking [2]. Production of one ton of paper generates about 50 kg of paper sludge waste [3]. Paper sludge is an organic solid waste derived from wastewater treatment in the pulp and paper industry. The main components of paper sludge are mineral matter and organic materials, which are mainly short cellulose fibers [4,5]. The mineral matter of the sludge (up to 35% based on dry weight) is usually fillers used in the paper industry such as calcium carbonate, talc, kaolin, as well as alum (the double salt of aluminum sulfate) used in sizing of paper [6]. To utilize the huge amounts of paper sludge and reduce its negative impact on the environment, different routes are available for its recycling such as soil amendment, incineration, anaerobic digestion, filler in construction materials, and the production of carbon materials and bio-based chemicals [7–11]. The rationale for using paper sludge in producing bio-based chemicals is that it is rich in polysaccharides that exist in pulp fibers, namely, cellulose and hemicelluloses [12–15]. A key step toward that is the hydrolysis of cellulose and hemicelluloses into simple sugars at the maximum possible yield and minimum side-products that may affect the processing of sugars into the final bio-based chemicals [16]. The overall cost of the process is important to commercialize the final product.
The breakdown of cellulose and hemicelluloses in paper sludge using mineral acids, particularly sulfuric acid, remains the most economical, rapid, and high-yielding method. Some drawbacks, such as the corrosive nature of acids, acid recovery, and separation of sugars from acids, have been addressed by using organic, metal, and ceramics-coated anti-corrosive vessels [17], and developing efficient methods for acid recovery and acid/sugars separation [18]. This has renewed interest in using mineral acid hydrolysis, especially with concentrated acids to achieve a high sugar yield at moderate temperatures and reaction time [19]. While almost complete hydrolysis of hemicelluloses into sugars could be easily achieved due to their highly amorphous nature [19], complete hydrolysis of cellulose is difficult to attain due to its semi-crystalline nature resulting from the formation of three-dimensional hydrogen-bonded networks [20]. Increasing temperature, acid concentration, and reaction time can enhance the hydrolysis of cellulose and hemicelluloses, but this also leads to the formation of undesirable by-products of the reaction, mainly furfural and hydroxymethyl furfural which negatively affect the subsequent fermentation processes to the sugars into biofuels and bio-based chemicals [21]. Therefore, optimizing hydrolysis conditions and using adequate pretreatment are crucial for producing sugars for subsequent fermentation into bio-based chemicals such as bio-fuel and organic acids (such as succinic acid, hydroxybutyric acid, levulinic acid, and lactic acid).
Phosphoric acid has been studied to a lesser extent than sulfuric acid for the direct hydrolysis of lignocellulosic materials into simple sugars with high yields as performed by Idrees et al. [22] who studied the hydrolysis of water hyacinth, Gámez et al. [23] and Aguilar et al. [24] who studied the hydrolysis of sugar cane bagasse, and Israilides et al. [25] who studied the hydrolysis of rice straw. Using phosphoric acid for hydrolysis of lignocellulosic materials has the advantage of possibility to neutralize the residual acid in the hydrolyzate with sodium hydroxide into sodium phosphate, which can be used as a nutrient by microorganisms during the subsequent monosaccharide fermentation step, i.e., no acid recovery is needed [23]. The lower corrosive property of phosphoric acid than that of other mineral acids is another advantage in addition to its easier recovery.
Phosphoric acid was also used for pretreatment of different lignocellulosic materials to facilitate their subsequent hydrolysis into sugars. The pretreatment aimed to remove lignin and hemicelluloses from the lignocellulosic materials to make cellulose more accessible to acid hydrolysis. These studies include the use of phosphoric acid alone [26–30] or in combination with other chemicals and technologies such as microwave-assisted phosphoric acid hydrolysis [31], phosphoric acid/steam explosion [32], N-methylmorpholine N-oxide/phosphoric acid [33], ferric chloride/phosphoric acid [34], sulfomethylation-aided phosphoric acid [35], phosphoric acid/hydrogen peroxide [36–39], phosphoric acid/sodium hydroxide [40], ethanol/phosphoric acid [41], acetone/phosphoric acid [42], and milling/disc refining/phosphoric acid pretreatments [43].
Despite the previous studies pointing out the utilization of phosphoric acid as a pretreatment for subsequent saccharification or direct saccharification of various lignocellulosic materials, its use for hydrolysis or pretreatment of paper sludge is quite rare. To the extent of our knowledge, the only published work was that of Yamashita et al. [44] and Pečar et al. [45]. Yamashita et al. [44] studied enzymatic saccharification of paper sludge after pretreatment with phosphoric acid and ball milling. In that study, phosphoric acid pretreatment was carried out using 85% phosphoric acid at mass to liquor ratio 1:20, at 4°C, for 1 h. No characterization for the paper sludge was carried out. On the other hand, Pečar et al. [45] studied the pretreatment of paper sludge before enzymatic saccharification using ~80% phosphoric acid at a liquor ratio of 1:3.5 at 50°C for 2 h.
The current study focused on optimizing the pretreatment of paper sludge waste using phosphoric acid, considering factors like concentration, reaction time, temperature, and consistency (sludge-to-acid ratio). The goal was to minimize cellulose crystallinity, maximize sugar yield during subsequent acid hydrolysis using phosphoric acid, and minimize the side products (such as furfural and acetic acid). Response surface methodology was employed to perform simultaneous parameters study via designing the experiments to decrease the number of experiments and to create a prediction model to perform the optimization [46,47]. The derived models were analyzed using ANOVA analysis to verify the models’ terms and the models’ accuracy. After pretreatment, paper sludge held the potential as a valuable resource for sustainable and circular economy industries [48,49].
Interstate Paper Industries, Sadat City, Egypt kindly supplied paper sludge; the moisture content of the sludge was 70%. The paper sludge was generated from the recycling process of white writing and printing paper used in tissue paper manufacture. The paper sludge was dried in an oven with air circulation at 40°C for 12 h; the moisture content after drying was 9.41% based on the weight before drying. Before being used in the experiments, the dry paper sludge was treated with dilute hydrochloric (0.01 N) at 25°C and liquor ratio 1:10 for 1 h with stirring to remove the acid-soluble ash [50]. Phosphoric acid (85%), sulfuric acid (98%), phenol (crystals), absolute ethanol (95%), sodium hydroxide (analytical grade), glacial acetic acid, and toluene were purchased from Fisher Scientific and used as received.
2.2 Characterization of Paper Sludge
For chemical analyses, ash content was determined using a muffle furnace at 900°C for 45 min (TAPPI T 413) and 525°C (TAPPI T 211). Acid non-hydrolyzable material in the sludge was determined by hydrolysis of the sample using 72% sulfuric acid according to TAPPI standard method (TAPPI T 222); after hydrolysis, the residues were filtered on ashless filter paper, washed thoroughly with distilled water till neutral pH, dried and weighed. α-cellulose content was determined using the TAPPI standard method (TAPPI T 429), and hemicelluloses were estimated from the difference in weight due to the treatment of the paper sludge by 17.5% NaOH.
2.3 Phosphoric Acid Pretreatment
Dried paper sludge (10 g) was mixed with phosphoric acid at the measuring values of consistency, acid concentrations, time, and temperature illustrated in Table 1. These values are defined based on the experimental design. At the end of pretreatment, 50 mL of distilled water was added to the mixture (paper sludge and phosphoric acid solution) and stirred for 30 min. Then, residual paper sludge was removed from the hydrolyzate by centrifugation at 6000 rpm for 20 min, washed several times using vacuum filtration until neutral pH, and dried in an oven with circulating air at 45°C for 18 h. The experiments were carried out in duplicates and the results averaged.
The residual weight of the sludge (Yield, Y) after the acid pretreatment was determined gravimetrically from the weight of the paper sludge before and after treatment as in Eq. (1).
where X1 is the weight of the sludge before acid treatment and X2 is the weight of the sludge after acid treatment.
2.4 Experimental Design Used for Pretreatment of Sludge
For the pretreatment of paper sludge, the selected factors affecting the pretreatment process using phosphoric acid were the consistency (A) which represents the weight % of the dried sludge to the amount of acid used, the acid concentration in weight % (B), the time used for the process (C), and the temperature used for the pretreatment (D). The design of the experimental schedule was prepared by Response Surface Methodology using Design Expert software version 6.0.8 in the trial version. These four numeric factors are arranged in 26 experiments.
The selected ranges of the four parameters were 4% to 10% for factor A, 60% to 85% for factor B, 0.5 h to 4 h for factor C, and 25°C to 80°C for factor D. The range of each parameter is based on previous research that addressed the pretreatment of cellulosic material before hydrolysis [26–30]. However, the prior research studied one or more parameters individually, whereas their simultaneous effect on the process yield was not recorded before. Therefore, simultaneous optimization of these parameters within the model’s navigation area is essential to obtain the optimum conditions for the pretreatment process. In the experimental design schedule, illustrated in Table 1, each numeric factor is varied over five levels which are ± the axial points, ± the factorial point itself, and the center point. The axial points were designed to be face-centered to widen the model’s navigation area. The center composite technique enhances the model fitting in case of curvature. The theoretical equation of the model is illustrated in Eq. (2). Meanwhile, the application of the Design Expert program software derives the model prediction, fitting, and verifying using the simultaneous ANOVA analysis of the significant parameters and the results.
where Y is the response; a0 is the intercept regression constant; ai, aii,…, ain are regression coefficients, and Xi, and Xin are the independent variables investigated.
2.5 Saccharification of Pretreated Paper Sludge
The pretreatment process, which was carried out using 64% phosphoric acid and 10% consistency at 25°C for 30 min, was directly followed by hydrolysis at 80°C for 4 h. After the hydrolysis, 50 mL of distilled water was added to the mixture and stirred for 30 min. Then, residual paper sludge was removed from the hydrolyzate by centrifugation at 6000 rpm for 20 min, washed several times using vacuum filtration until neutral pH, and dried in an oven with circulating air at 45°C for 18 h. The yield of the paper sludge was determined as mentioned above in Section 2.3. The hydrolyzate was collected and used for determination of sugars, furfurals, and acetic acid as mentioned in Section 2.6.
2.6.1 Crystallinity of Paper Sludge
Crystallinity (X) of the paper sludge before and after pretreatment with phosphoric acid was calculated from XRD diffraction patterns recorded using a D8 advance Empyrean X-ray diffractometer (Panalytical, Malvern, UK) equipped with Cu Kα radiation (λ = 1.5406 Å) at 40 kV and 40 mA. The diffractograms were recorded from 2θ angle of 10° to 80° with scanning steps of 0.02° and an exposure of 4 s per step. The measurements were carried out at ambient conditions (25°C). The crystallinity was calculated according to Eq. (3) [51].
where I200 is the intensity of the diffraction peak at 2θ ~ 22.7° (the position of 002 peaks) and Iam is the intensity at about 2θ = 18°.
Total hydrolyzed sugars in the hydrolyzate were determined using the standard phenol/sulfuric acid hydrolysis method either after the pretreatment or saccharification [52]. In addition, high-performance HPLC analysis was carried out on the hydrolyzed sugars using Agilent Technologies 1100 series liquid chromatography (Agilent Technologies, Ratingen, Germany) equipped with an autosampler and a refractive index detector. The analytical column was a Shim-pack SCR-101N with 7.9 mm × 300 mm internal diameter by length and the column temperature was 40°C. The mobile phase consisted of ultrapure water. The flow rate was kept at 0.7 mL/min for a total run time of 20 min with isocratic elution.
2.6.3 Determination of Acetic Acid and Furfurals
Acetic acid, furfural, and methyl furfural were determined using an Agilent 1260 Infinity HPLC instrument (Agilent Technologies, Ratingen, Germany) equipped with a DAD detector at wavelength 230 nm. The analytical column was an Agilent Hi-Plex H, 7.7 mm × 300 mm, 8 μm (p/n PL1170-6830). The mobile phase was 100%, 0.01 M H2SO4, the flow rate of 0.6 mL/min, and the column temperature of 50°C. The total run time was 25 min.
3.1 Characterization of Paper Sludge
Paper sludge received in a wet form (70% moisture content) was dried first. The sludge had high ash content due to the presence of fillers such as calcium carbonate (ash content at 900°C was 33.45% based on the oven-dry weight of the paper sludge). The dried paper sludge was washed with a dilute hydrochloric acid solution before pretreatment with phosphoric acid. As a result of washing with the hydrochloric acid, calcium carbonate was removed from the sludge and the ash content at 525°C and 900°C was 11.87% and 10.60%, respectively. The ash content values at these temperatures indicate almost complete removal of calcium carbonate by the acid washing. The residual ash could be attributed to other acid-resistant fillers such as kaolin. The dilute acid washing process followed by washing with water till neutrality not only removes the calcium carbonate which can react with phosphoric acid in the next step, but also removes other residual chemicals used during the recycling and bleaching of pulp. The bleaching process was carried out in the paper mill using two-stage hydrogen peroxide/sodium dithionite bleaching. The composition of the sludge after the hydrochloric acid washing was 21.9% acid non-hydrolysable carbon-based materials, 42.1% α-cellulose content, and 24.13% hemicelluloses, in addition to the ash. The total sugars in the sludge sample were 0.893 g per gram of the sample (0.635 g/g glucose, 0.192 g/g xylose, 0.042 g/g arabinose, and 0.0025 g/g galactose) as determined by the HPLC.
3.2 Pretreatment of Paper Sludge with Phosphoric Acid
Two prediction models were created using the Design Expert program software version 6.0.8. The first model was derived to optimize the yield and the second model was derived to optimize the crystallinity. These prediction models were derived according to the experimental design scheduled in Table 1. The simultaneous effect of the parameters A, B, C, and D on the pretreatment process are represented as the yield of paper sludge after pretreatment (Y) and the crystallinity of paper sludge after pretreatment (X) responses. These results are summarized in Table 1 and analyzed using ANOVA.
3.2.1 Prediction Model for Yield Optimization
The model of the yield response is the Reduced Two-Factor Interaction model (2FI) expressed in Eq. (4), which shows a simultaneous effect of parameters B and D on the sludge yield represented by the product term in Eq. (4) (B × D). This simultaneous effect is plotted as shown in Fig. 1. The ANOVA analysis for the model is applied for probability function p = 0.05, and the F-value test is calculated as illustrated in Table 2. The results of these tests revealed that the significant parameters are B, C, and D. Meanwhile, the parameter A is excluded from the model equation as it is non-significant for p > 0.05. In Table 2, the regression coefficient R2 of the model curve is 0.86 which is in reasonable agreement with the adjusted R2 which equals 0.83, and the predicted R2 which equals 0.8. The adequate precision is greater than 4 which denotes a tolerable signal-to-noise ratio to fit the model, also the coefficient of variance is greater than one which stipulates the normal probability of the model. The ANOVA results elucidate the fitting of the model to navigate the design space.
Figure 1: 3-D model of the simultaneous effect of acid concentration and temperature on yield percentage
where Y represents the yield of the paper sludge after pretreatment, B represents the acid concentration percentage, C represents the pretreatment time, and D represents the temperature.
Regarding Fig. 1, parameter C is inversely correlated with the yield as elucidated in runs 1 & 5, runs 2 & 6, runs 3 & 7, runs 4 & 8, and runs 9 & 13, as well as parameter B in runs 1 & 3. At the maximum value of parameter D, the yield is inversely proportional to the value of D as observed in runs 13 & 15 and 14 & 16. However, increasing the value of parameter B does not affect the yield percentage at the axial points of runs 19 & 20. At the axial points of runs 21 & 22, the yield percentage decreased by 4.5% when parameter C was increased to 4 h, while the yield percentage decreased by 15% when the value of parameter D was increased to 80°C as shown in runs 23 & 24.
The 3-D graph of the model (Fig. 1) represents the simultaneous effect of parameters B and D at the maximum value of parameter A and the minimum value of parameter C. The conditions of maximum consistency and minimum time were chosen as industrial requirements to maximize the paper sludge consumption during the minimum time.
3.2.2 Prediction Model for Crystallinity Optimization
The main aim of the pretreatment stage with phosphoric acid was to decrease the crystallinity of cellulose fibers in paper sludge in order to facilitate their subsequent hydrolysis to produce the maximum possible yield of sugars. The crystallinity percentage of the control sample without pretreatment was 83.7%. Experimentally, all samples treated with 85% phosphoric acid at all temperatures, mass-to-liquor ratios, and times (runs 3, 4, 7, 8, 11, 12, 15, 16) suffered from charring and their X-ray diffraction pattern didn’t show crystallinity pattern of cellulose, i.e., diffraction pattern with peaks due to diffraction from (110), (200), and (004) planes [53] (Fig. A1). Therefore, crystallinity (X) could not be measured for these samples. The rest of the experimental runs were modeled regarding their crystallinity and verified using the Response Surface Reduced 2FI model. The analysis of variance ANOVA is elucidated in Table 3, while the model equation is displayed in Eq. (5).
where X represents the percentage of crystallinity, A represents the consistency, and D represents the temperature.
ANOVA analyses are applied with a significance level of p =0.05. Non-significant parameters are eliminated from the model’s equation and analysis of variance in Table 3, as removing non-significant parameters improves the model’s fitting. The model and the model’s terms illustrated in Table 2 are significant according to the F-value test where the probability <0.05 while the lack of fit is non-significant as its probability function >0.05. The regression coefficient R2 of the model curve is 0.83, and the predicted R2 which equals 0.74 is in reasonable agreement with the adjusted R2 which equals 0.79. The adequate precision is greater than 4 which denotes a tolerable signal-to-noise ratio to fit the model, also the coefficient of variance is greater than one which stipulates the normal probability of the model. The ANOVA results elucidate the fitting of the model to navigate the design space.
Parameter C has no significant effect on the crystallinity of cellulose as appeared in runs 1 & 5 and 2 & 6. On the other hand, factors A and D affect the cellulose crystallinity, showing an inverse relationship until the center point of temperature (52.5°C) as shown in runs 1 & 6, runs 4 & 10, and runs 17 & 18. However, at 80°C factor A has no effect on the crystallinity in runs 9 & 10. The 3-D graph of the model (Fig. 2) represents the simultaneous effect of parameters A and D. The deterioration of cellulosic fibers occurs due to the harsh conditions of low consistency using 85% acid concentration at high temperatures. This deterioration can be observed in the contour of the 3-D graph, where non-continuous contour lines appear at low values of parameter A and high values of parameter D. Therefore, it is recommended to use an acid concentration not exceeding 64% at 25°C for pretreatment of paper sludge with 10% consistency to achieve minimal crystallinity without causing charring of the fibers.
Figure 2: The 3-D model of the simultaneous effect of consistency percentage and temperature on crystallinity percentage
Regarding the effect of phosphoric acid on paper sludge, phosphoric acid can degrade and dissolve the hemicelluloses part of the fibers in the sludge due to their amorphous and short chains nature by cleaving the glycosidic bonds between the constituent sugars’ units [30]. The same is also possible, but to a lower extent, in the case of cellulose fibers due to their semi-crystalline nature [27,30]. In addition to the degradation of cellulose chains by acid hydrolysis, phosphoric acid is known to cause swelling of the crystalline parts of cellulose under a specific range of conditions of acid concentration, time, and temperature [54]. This swelling can ultimately lead to the dissolution of cellulose due to protonation and phosphorylation by phosphoric acid. Therefore, the net effect of the different pretreatment conditions on the crystallinity of the paper sludge is complex since swelling causes a decrease in crystallinity while hydrolysis of hemicelluloses and amorphous cellulose causes an increase in crystallinity. Phosphoric acid pretreatment at lower temperatures enhances swelling of cellulose, i.e., decrease crystallinity [54–57] while higher temperatures and longer pretreatment times result in more hydrolysis of the amorphous hemicelluloses and cellulose in the amorphous region, i.e., increase the overall crystallinity.
It should be noted that the crystallinity of pretreated paper sludge was determined on dry samples, where rearrangement of cellulose chains could occur to some extent upon drying after their swelling by the action of phosphoric acid in the wet state. This means that when samples are wetted with phosphoric acid, the measured crystallinity could be lower than the determined crystallinity after drying.
In continuation of the ANOVA analysis, the normal probability of studentized residuals plot for the two models for optimization is performed to verify them. The scatter plot shown in Fig. 3 represents the predicted percentiles of the probability vs. the actual residuals which are formatted into studentized residuals to consider the standard deviation. The observed plot of each model is normally distributed around the line, which indicates that each model is fitted normally.
Figure 3: (A) Normal plot of studentized residuals of the error terms of yield model, (B) normal plot of studentized residuals of the error terms of crystallinity model
The optimization results for the four parameters (acid concentration of acid, the pretreatment temperature and time, and consistency) to maximize the paper sludge yield and minimize the crystallinity revealed that the optimum conditions are consistency of 10%, temperature 25°C, and acid concentration not more than 64% for half an hour. The predicted optimum conditions are statistically examined at a confidence interval (CI) of 95% and a predicted interval (PI) of 95% and are experimentally verified as elucidated in Table 4. The predicted vs. the experimental results for yield and crystallinity are shown in Fig. 4.
Figure 4: (A) The predicted results vs. the actual results for the yield model, (B) the predicted results vs. the actual results for the crystallinity model
3.3 Saccharification of Phosphoric Acid-Pretreated Paper Sludge
Based on the experimental design results shown in Table 1, the weight loss of paper sludge after phosphoric acid treatment is illustrated in Fig. 5, which elucidates a significant simultaneous effect of acid concentration and temperature on weight loss (Fig. 5A). The maximum weight loss percentage is observed at 80°C using an acid concentration of 85%. The consistency percentage has no significant effect on weight loss as shown in Fig. 5B,C. The maximum weight loss was achieved at maximum acid concentration and highest temperature. Fig. 5D indicates a significant relationship between process temperature and the reaction time, with the maximum weight loss observed at the highest temperature and longest time.
Figure 5: (A) The simultaneous effect of acid concentration percent and temperature at maximum consistency and maximum time, (B) the simultaneous effect of acid conc percent and consistency percent at maximum temperature and maximum time, (C) the simultaneous effect of consistency percent and temperature at maximum acid concentration percent and maximum time, (D) the simultaneous effect of process time and temperature at maximum consistency and maximum acid concentration
The maximum weight loss is achieved using an acid concentration of 85%, a temperature of 80°C, and a consistency of 10% for 4 h. However, using lower values of acid concentration decreases the formation of undesirable byproducts such as furfurals and acetic acid, while also saving the used chemicals. Therefore, the pretreatment process was directly followed by the saccharification process in the same reactor without changing the acid or washing, i.e., using the conditions of 64% acid concentration, 80°C, and consistency of 10% for 4 h.
The results of the hydrolysis experiment by the above-mentioned conditions (64% phosphoric acid, 10% consistency, at 80°C for 4 h) showed that the paper sludge yield was approximately 58%, i.e., weight loss of 42% of the sludge due to hydrolysis. This yield is significantly lower than that obtained without pretreatment under the same conditions, where the paper sludge yield was about 81%, resulting in a weight loss of 18%. This indicates that the pretreatment before the saccharification step significantly reduced the crystallinity of the paper sludge, making the hydrolysis of cellulose chains much easier. Such a positive effect of phosphoric pretreatment of paper sludge on hydrolysis of paper sludge into sugars was found before but in the case of using enzymatic saccharification [44,45].
In the case of using the highest acid concentration (85% phosphoric acid) under the same temperature, time duration, and consistency, where the minimum yield of paper sludge (43%) was obtained, the resulting supernatant containing sugars was very dark due to side products formed as a result of the high concentration of acid used.
Considering the ash content of the pretreated sample used in the hydrolysis step (~11.5%), and the presence of residual acid non-hydrolyzable carbon-based materials exist in the paper sludge sample (21.90%), which means that the maximum theoretical hydrolyzable cellulosic material in the sample is approximately 67% of its weight, assuming that all cellulosic material is accessible for hydrolysis into simple sugars. Based on that, phosphoric acid hydrolysis of paper sludge under the chosen conditions (64% acid concentration, 4 h, 10% consistency, and 80°C) could hydrolyze approximately 63% of the sample (42% weight loss out of the maximum theoretical weight loss of 67%). The lower total sugars content obtained than the theoretical value, i.e., all cellulose is hydrolyzed by the acid, which means that there are still crystalline regions of cellulose in the pulp that could not be accessed by phosphoric acid to hydrolyze.
The total sugars in the hydrolyzate determined by the phenol/sulfuric acid method and expressed as glucose were 0.43 g glucose/g sample (10.46 g/L). Comparing the pretreatment and saccharification of paper sludge in the current study to previous work that used phosphoric acid pretreatment but saccharification with enzymes [44], the yield of sugars after phosphoric acid pretreatment using 80% acid at 4°C for 1 h followed by enzyme saccharification for 12 h was 0.45 g/g of paper sludge, while in case of pretreatment of phosphoric acid 85% at 50°C for 2 h, followed by enzymatic pretreatment for 24 h the total sugars obtained was 0.365 g/g of paper sludge [45]. In both of the previous studies, dried paper sludge was ball milled before phosphoric acid pretreatment. The comparison shows the effectiveness of using phosphoric acid pretreatment and saccharification of paper sludge under the conditions used in the current work.
To determine the composition of sugars obtained by phosphoric acid hydrolysis in the current study, HPLC analysis was carried out on the crude hydrolyzate. Glucose, xylose, arabinose, and galactose sugars represent 72.07%, 23.95%, 2.48%, and 1.51% of the total sugars, respectively. The total sugars in the hydrolyzate determined by HPLC was 0.36 g/g of paper sludge sample (0.258 g/g glucose, 0.086 g/g xylose, 0.0089 g/g arabinose, and 0.0054 g/g galactose).
Regarding the formation of methyl furfural and furfural as byproducts, which have a negative effect on the subsequent use of sugars for fermentation, HPLC results showed the presence of 21.65 and 235.7 mg/L of methyl furfural and furfural, respectively. In addition, acetic acid concentration in the crude hydrolysate was 4.57 mg/L. These concentrations are considered low in terms of their inhibitory effect on the fermentation of sugars such as xylose and glucose. For example, a concentration of 1 g/L for both furfural and methyl furfural, and a concentration of 500 mg/L for the acetic acid could significantly inhibit the fermentation of xylose to xylitol [58]. In the case of the fermentation of glucose into ethanol, concentrations of furfural (1 g/L), and methyl furfural (1 g/L) negatively affected the fermentation process [59].
It is important to mention here regarding the high phosphoric acid concentration (64%) used in the pretreatment and saccharification that using of the high acids’ concentration is not unusual with cellulose and lignocellulosic materials. For example, ~85% phosphoric acid is used for dissolution and regeneration of cellulose [54–57]. In the area of lignocellulosic saccharification with mineral acids, both concentrated and dilute acid hydrolysis approaches have been investigated. Each approach has its own advantages and disadvantages. Using of high acid concentrations has the advantages of achieving near-theoretical yield of sugars in a shorter reaction time with fewer side degradation products (furfural-type components) than in case of using dilute acids since much lower temperature is used in the former case. In addition, concentrated mineral acids effectively de-crystallize the cellulose, making the hydrolysis reaction more homogeneous and thus less labile to sugars degradation before complete hydrolysis is obtained [60,61]. For example, ~72% sulfuric acid was used for de-crystallization and hydrolysis of wood residues [60]. A 2-stage process was used in that work where the milled wood was first treated with 72% sulfuric acid at 1:15 solid to acid ratio at low temperature (~27–40), then the mixture was diluted with water to 20% acid concentration and refluxed at 100°C for 3 h. In another study [61], 95% sulfuric acid and t-butyl alcohol mixture was used saccharification of wood (ratio of the 95% acid to wood was ~1:10).
Paper sludge waste could be successfully hydrolyzed in a good yield of sugars (0.43 g glucose/g of sludge) and low levels of inhibitory side products using consecutive one-pot 64% phosphoric acid pretreatment and hydrolysis. The factors that affect the pretreatment process simultaneously (temperature, time, acid concentration, and liquor ratio) were studied using response surface methodology and an optimization model. The goal was to maximize the sugar content and minimize the crystallinity. This model could predict the optimum conditions for the pretreatment process to decrease the crystallinity of cellulose of the paper sludge, and to get the maximum hydrolysis. The optimum conditions for minimizing the crystallinity of paper sludge were: acid concentration of 64%, consistency of 10%, pretreatment time 0.5 h, and temperature 25°C. Decreasing the crystallinity of cellulose in the sludge by phosphoric acid pretreatment was proved to be very efficient in increasing the hydrolysis of paper sludge at a lower cost since a lower concentration of the acid (64% at 10% consistency and 80°C for 4 h) could be used as compared to carrying out the hydrolysis without the pretreatment. Using lower acid concentrations will also reduce the cost of the acid recovery. The overall approach used in the current work, pretreatment of paper sludge with phosphoric acid at a low temperature followed by hydrolysis of the same mixture at a higher temperature, could have a potential contribution to attain a sustainable paper recycling industry, where the cost and energy reduction should be at the top of its priorities. Using of phosphoric acid for hydrolysis has an advantage over the use of other mineral acids, such as the industrially used sulfuric acid which is more corrosive than phosphoric acid. Using phosphoric acid instead of sulfuric acid for hydrolysis prevents formation of sulfur-containing compounds that may be inhibitory to the action of enzymes during fermentation of sugars. In addition, using the same concentrated phosphoric acid (64%) for both pretreatment and hydrolysis in consecutive steps is another advantage over the use of concentrated sulfuric acid where the process involves two separate steps to avoid formation of significant amounts of inhibitory side products. Moreover, the use of 64% phosphoric acid pretreatment and saccharification approach in the current work is superior to previous studies which used phosphoric acid and the costly enzymes to get comparable yield of sugars from paper sludge.
Last, but not least, the cost estimation of the energy needed for the recovery of phosphoric acid and the detailed process for that is an important challenge that should be considered in further studies.
Acknowledgement: The authors acknowledge the support of National Research Centre (NRC) in Egypt by submitting facilities required for completing the different experiments of the current work. The authors also acknowledge the support of Interstate Paper Industries, Sadat City, Egypt for kindly providing the paper sludge and phosphoric acid used in the study.
Funding Statement: The authors acknowledge funding of the current work by the Science, Technology, and Innovation Funding Authority (STDF), Egypt, Project No. 46104: Recycling of Sludge Wastes from Paper Industry via Green Technologies.
Author Contributions: The authors confirm their contribution to the paper as follows: Funding acquisition: Mohammad Hassan; Study conception and design: Mohammad Hassan, Samar El-Mekkawi, Enas Hassan, Shaimaa Fadel, Wafaa Abou Elseoud; Methodology, analysis and interpretation of results: Mohammad Hassan, Samar El-Mekkawi, Enas Hassan, Shaimaa Fadel, Wafaa Abou Elseoud; Project administration: Mohammad Hassan; Supervision: Mohammad Hassan; Writing original draft: Mohammad Hassan, Samar El-Mekkawi; Writing, review and editing final manuscript: Mohammad Hassan, Samar El-Mekkawi, Enas Hassan, Shaimaa Fadel, Wafaa Abou Elseoud. All authors reviewed the results and approved the final version of the manuscript.
Availability of Data and Materials: All data generated or analyzed during this study are included in this published article.
Ethics Approval: Not applicable.
Conflicts of Interest: The authors declare that they have no conflicts of interest to report regarding the present study.
References
1. Tiseo. Paper consumption worldwide from 2020 to 2030. Available from: https://www.statista.com/statistics/1089078/demand-paper-globally-until-2030/. [Accessed 2021]. [Google Scholar]
2. De Azevedo ARG, Alexandre J, Pessanha LSP, Manhães RDST, de Brito J, Marvila MT. Characterizing the paper industry sludge for environmentally-safe disposal. Waste Manag. 2019;95(10):43–52. doi:10.1016/j.wasman.2019.06.001. [Google Scholar] [PubMed] [CrossRef]
3. Bajpa P. Generation of waste in pulp and paper mills. In: Bajpei P, editor. Management of pulp and paper mill waste. Cham: Springer; 2015. p. 9–15. [Google Scholar]
4. Singh R, Patel M, Sohal KS. The potential use of waste paper sludge for sustainable production of concrete—a review. Lect Notes Civ Eng. 2022;172:365–74. doi:10.1007/978-981-16-4396-5. [Google Scholar] [CrossRef]
5. Yin Y, Yin H, Yuan Z, Wu Z, Zhang W, Tian H, et al. Study on the pyrolysis characteristics, kinetics, and mineral transformation of paper sludge. Bioenergy Res. 2021;14(4):1289–99. doi:10.1007/s12155-021-10248-6. [Google Scholar] [CrossRef]
6. Logeswaran V, Ramakrishna G. Waste paper sludge ash—state of art. Int J Innov Technol Explor Eng. 2019;8(9):2333–8. doi:10.35940/ijitee.I8572.078919. [Google Scholar] [CrossRef]
7. Hurst G, Ahmed A, Taylor S, Tedesco S. Anaerobic digestion of recycled paper crumb and effects of digestate on concrete performance. Renew Energy. 2023;208:577–82. doi:10.1016/j.renene.2023.03.061. [Google Scholar] [CrossRef]
8. Kusumarini N, Putranto AW, Agustina C, Wahab AA. The potential of paper industry sludge potency as organic soil amendment. Jurnal Tanah dan Sumberdaya Lahan. 2022;9:147–51. doi:10.21776/ub.jtsl. [Google Scholar] [CrossRef]
9. Liu BB, Chen X, Wu L, Chen M, Zhou KB, Peng LX. The reuse of pulp and paper mill sludge: as a soil amendment. In: Proceedings of 2015 International Forum on Energy, Environment Science and Materials (IFEESM 2015); 2015 Sep 25–26; Shenzhen, China: Atlantis Press. p. 1231–7. doi:10.2991/ifeesm-15.2015.226. [Google Scholar] [CrossRef]
10. Lee SY, Sankaran R, Chew KW, Tan CH, Krishnamoorthy R, Chu DT, et al. Waste to bioenergy: a review on the recent conversion technologies. BMC Energy. 2019;1:4. doi:10.1186/s42500-019-0004-7. [Google Scholar] [CrossRef]
11. Wang YH, Bayatpour S, Qian X, Frigo-Vaz B, Wang P. Activated carbon fibers via reductive carbonization of cellulosic biomass for adsorption of nonpolar volatile organic compounds. Colloid Surfaces A. 2021;612:125908. doi:10.1016/j.colsurfa.2020.125908. [Google Scholar] [CrossRef]
12. Duncan SM, Alkasrawi M, Gurram R, Almomani F, Wiberley-Bradford AE, Singsaas E. Paper mill sludge as a source of sugars for use in the production of bioethanol and isoprene. Energies. 2020;13:4662. doi:10.3390/en13184662. [Google Scholar] [CrossRef]
13. Glińska K, Stüber F, Fabregat A, Giralt J, Font J, Mateo-Sanz JM, et al. Moving municipal WWTP towards circular economy: cellulose recovery from primary sludge with ionic liquid. Resourc Conserv Recycl. 2020;154:104626. doi:10.1016/j.resconrec.2019.104626. [Google Scholar] [CrossRef]
14. Alkasrawi M, Rajangam AS, Tawalbeh M, Kafiah F, Al-Othman A, Al-Asheh S, et al. Techno-economic analysis and a novel assessment technique of paper mill sludge conversion to bioethanol toward sustainable energy production. Int J Energy Res. 2020;44:12602. doi:10.1002/er.v44.15. [Google Scholar] [CrossRef]
15. Ioannidou SM, Pateraki C, Ladakis D, Papapostolou H, Tsakona M, Vlysidis A, et al. Sustainable production of bio-based chemicals and polymers via integrated biomass refining and bioprocessing in a circular bioeconomy context. Bioresour Technol. 2020;307:123093. doi:10.1016/j.biortech.2020.123093. [Google Scholar] [PubMed] [CrossRef]
16. Tareen AK, Punsuvon V, Parakulsuksatid P. Conversion of steam exploded hydrolyzate of oil palm trunk to furfural by using sulfuric acid, solid acid, and base catalysts in one pot. Energ Source Part A. 2020. doi:10.1080/15567036.2020.1741733. [Google Scholar] [CrossRef]
17. Møller VB, Dam-Johansen K, Frankær SM, Kiil S. Acid-resistant organic coatings for the chemical industry: a review. J Coating Technol Res. 2017;14:279–306. doi:10.1007/s11998-016-9905-2. [Google Scholar] [CrossRef]
18. Wolfaardt FJ, Leite Fernandes LG, Cangussu Oliveira SK, Duret X, Görgens JF, Lavoie J-M. Recovery approaches for sulfuric acid from the concentrated acid hydrolysis of lignocellulosic feedstocks: a mini-review. Energy Convers Manag. 2021;10:100074. [Google Scholar]
19. Gnanasekaran L, Priya AK, Thanigaivel S, Hoang TK, Soto-Moscoso M. The conversion of biomass to fuels via cutting-edge technologies: explorations from natural utilization systems. Fuel. 2023;331:125668. doi:10.1016/j.fuel.2022.125668. [Google Scholar] [CrossRef]
20. Jarvis M. Chemistry: cellulose stacks up. Nature. 2023;426:611–2. [Google Scholar]
21. Morales-delaRosa S, Campos-Martin JM, Fierro JLG. Optimization of the process of chemical hydrolysis of cellulose to glucose. Cellulose. 2014;21:2397–407. doi:10.1007/s10570-014-0280-9. [Google Scholar] [CrossRef]
22. Idrees M, Adnan A, Sheikh S, Qureshi FA. Optimization of dilute acid pretreatment of water hyacinth biomass for enzymatic hydrolysis and ethanol production. EXCLI J. 2013;12:30–40. [Google Scholar] [PubMed]
23. Gámez S, González-Cabriales JJ, Ramírez JA, Garrote G, Vázquez M. Study of the hydrolysis of sugar cane bagasse using phosphoric acid. J Food Eng. 2006;74:78–88. doi:10.1016/j.jfoodeng.2005.02.005. [Google Scholar] [CrossRef]
24. Aguilar R, Ramírez JA, Garrote G, Vázquez M. Kinetic study of the acid hydrolysis of sugar cane bagasse. J Food Eng. 2002;55(4):309–18. doi:10.1016/S0260-8774(02)00106-1. [Google Scholar] [CrossRef]
25. Israilides CJ, Grant GA, Han YW. Sugar level, fermentability, and acceptability of straw treated with different acids. Appl Environ Microbiol. 1978;36(1):43–6. doi:10.1128/aem.36.1.43-46.1978. [Google Scholar] [PubMed] [CrossRef]
26. Kendrick EG, Bhatia R, Barbosa FC, Goldbeck R, Gallagher JA, Leak DJ. Enzymatic generation of short-chain cello-oligosaccharides from Miscanthus using different pretreatments. Bioresour Technol. 2022;358(4):127399. doi:10.1016/j.biortech.2022.127399. [Google Scholar] [PubMed] [CrossRef]
27. Majumdar S, Naha A, Bhattacharyya DK, Bhowal J. Effective delignification and decrystallization of cauliflower wastes by using dilute phosphoric acid for efficient enzymatic digestibility to produce fermentable sugars. Biomass Bioenergy. 2019;125(10):169–79. doi:10.1016/j.biombioe.2019.04.017. [Google Scholar] [CrossRef]
28. Rojas-Chamorro JA, Cara C, Romero I, Ruiz E, Romero-García JM, Mussatto SI, et al. Ethanol production from Brewers’ spent grain pretreated by dilute phosphoric acid. Energy Fuels. 2018;32(4):5226–33. doi:10.1021/acs.energyfuels.8b00343. [Google Scholar] [CrossRef]
29. Wu W, Rondon V, Weeks K, Pullammanappallil P, Ingram LO, Shanmugam KT. Phosphoric acid-based pretreatment of switchgrass and fermentation of entire slurry to ethanol using a simplified process. Bioresour Technol. 2018;251(2):171–80. doi:10.1016/j.biortech.2017.12.041. [Google Scholar] [PubMed] [CrossRef]
30. Wang Q, Shen F, Yang G, Zhang Y, Deng S, Hu Y, et al. Pretreating luffa sponge (Luffa cylindrica L.) with concentrated phosphoric acid and subsequent enzymatic saccharification. BioResources. 2016;11:899–912. [Google Scholar]
31. Hermiati E, Laksana RPB, Fatriasari W, Kholida LN, Yopi TA, Arnieyanto DR, et al. Microwave-assisted acid pretreatment for enhancing enzymatic saccharification of sugarcane trash. Biomass Convert Biorefinery. 2022;12(8):3037–54. doi:10.1007/s13399-020-00971-z. [Google Scholar] [CrossRef]
32. Tong D, Zhan P, Zhang W, Zhou Y, Huang Y, Qing Y, et al. Surfactant-assisted dilute phosphoric acid plus steam explosion of poplar for fermentable sugar production. ChemistrySelect. 2022;7(17):e202200423. doi:10.1002/slct.202200423. [Google Scholar] [CrossRef]
33. Molaverdi M, Mirmohamadsadeghi S, Karimi K, Aghbashlo M, Tabatabaei M. Efficient ethanol production from rice straw through cellulose restructuring and high solids loading fermentation by Mucor indicus. J Clean Prod. 2022;339:130702. doi:10.1016/j.jclepro.2022.130702. [Google Scholar] [CrossRef]
34. Kumar B, Bhardwaj N, Verma P. Pretreatment of rice straw using microwave assisted FeCl3-H3PO4 system for ethanol and oligosaccharides generation. Bioresour Technol Rep. 2019;7:100295. doi:10.1016/j.biteb.2019.100295. [Google Scholar] [CrossRef]
35. Jin Y, Liu J, Yang H, Shi Z, Zhao P, Yang J. Improving enzymatic saccharification and ethanol production of bamboo residues with sulfomethylation-aided phosphoric acid pretreatment. Ind Crops Prod. 2021;170:113733. doi:10.1016/j.indcrop.2021.113733. [Google Scholar] [CrossRef]
36. Ajayo PC, Wang Q, Huang M, Zhao L, Tian D, He J, et al. High bioethanol titer and yield from phosphoric acid plus hydrogen peroxide pretreated paper mulberry wood through optimization of simultaneous saccharification and fermentation. Bioresour Technol. 2023;374:128759. doi:10.1016/j.biortech.2023.128759. [Google Scholar] [PubMed] [CrossRef]
37. Zhao J, Tian D, Shen F, Hu J, Zeng Y, Huang C. Valorizing waste lignocellulose-based furniture boards by phosphoric acid and hydrogen peroxide (PHP) pretreatment for bioethanol production and high-value lignin recovery. Sustainability. 2019;11:6175. doi:10.3390/su11216175. [Google Scholar] [CrossRef]
38. Qiu J, Tian D, Shen F, Hu J, Zeng Y, Yang G, et al. Bioethanol production from wheat straw by phosphoric acid plus hydrogen peroxide (PHP) pretreatment via simultaneous saccharification and fermentation (SSF) at high solid loadings. Bioresour Technol. 2018;268:355–62. doi:10.1016/j.biortech.2018.08.009. [Google Scholar] [PubMed] [CrossRef]
39. Qiu J, Wang Q, Shen F, Yang G, Zhang Y, Deng S, et al. Optimizing phosphoric acid plus hydrogen peroxide (PHP) pretreatment on wheat straw by response surface method for enzymatic saccharification. Appl Biochem Biotechnol. 2017;181:1123–39. doi:10.1007/s12010-016-2273-7. [Google Scholar] [PubMed] [CrossRef]
40. Mund NK, Dash D, Barik CR, Goud VV, Sahoo L, Mishra P, et al. Evaluation of efficient glucose release using sodium hydroxide and phosphoric acid as pretreating agents from the biomass of Sesbania grandiflora (L.) Pers.: a fast growing tree legume. Bioresour Technol. 2017;236:97–105. doi:10.1016/j.biortech.2017.03.177. [Google Scholar] [PubMed] [CrossRef]
41. Chen W, Xu L, Chen K. Effects of ethanol-phosphoric acid pretreatment on enzymatic saccharification of rice straw. Nongye Gongcheng Xuebao Trans Chin Soc Agric Eng. 2011;27:268–72 (In Chinese). [Google Scholar]
42. Li H, Kim N-J, Jiang M, Kang JW, Chang HN. Simultaneous saccharification and fermentation of lignocellulosic residues pretreated with phosphoric acid-acetone for bioethanol production. Bioresour Technol. 2009;100:3245–51. doi:10.1016/j.biortech.2009.01.021. [Google Scholar] [PubMed] [CrossRef]
43. Du X, Lucia LA, Ghiladi RA. Development of a highly efficient pretreatment sequence for the enzymatic saccharification of loblolly pine wood. ACS Sustain Chem Eng. 2016;4:3669–78. doi:10.1021/acssuschemeng.6b00198. [Google Scholar] [CrossRef]
44. Yamashita Y, Sasaki C, Nakamura Y. Development of efficient system for ethanol production from paper sludge pretreated by ball milling and phosphoric acid. Carbohydr Polymer. 2010;79:250. doi:10.1016/j.carbpol.2009.07.054. [Google Scholar] [CrossRef]
45. Pečar D, Goršek A. Enzymatic treatment of paper sludge. Chem Eng Trans. 2015;43:631–6. [Google Scholar]
46. Riswanto FDO, Rohman A, Pramono S, Martono S. Application of response surface methodology as mathematical and statistical tools in natural product research. J Appl Pharm Sci. 2019;9:125–33. doi:10.7324/JAPS.2019.91018. [Google Scholar] [CrossRef]
47. Chelladurai SJS, Murugan K, Ray AP, Upadhyaya M, Narasimharaj V, Gnanasekaran S. Optimization of process parameters using response surface methodology: a review. Mater Today: Proc. 2021;37:1301–4. [Google Scholar]
48. Mou J, Li C, Yang X, Kaur G, Sze Ki Lin C. Overview of waste valorisation concepts from a circular economy perspective. In: Lin CSKL, Kaur G, Li C, Yang X, editors. Waste valorisation: waste streams in a circular economy. New Jersy: John Wiley & Sons Ltd.; 2021. p. 1–10. [Google Scholar]
49. Naicker JE, Govinden R, Lekha P, Sithole B. Transformation of pulp and paper mill sludge (PPMS) into a glucose-rich hydrolysate using green chemistry: assessing pretreatment methods for enhanced hydrolysis. J Environ Manag. 2020;270:110914. doi:10.1016/j.jenvman.2020.110914. [Google Scholar] [PubMed] [CrossRef]
50. Mendes CVT, Rocha JMS, Carvalho MGVS. Valorization of residual streams from pulp and paper mills: pretreatment and bioconversion of primary sludge to bioethanol. Ind Eng Chem Res. 2014;53:19398–404. doi:10.1021/ie503021y. [Google Scholar] [CrossRef]
51. Segal L, Creely JJ, Martin AE, Conrad CM. An empirical method for estimating the degree of crystallinity of native cellulose using the X-ray diffractometer. Text Res J. 1959;29:786–94. doi:10.1177/004051755902901003. [Google Scholar] [CrossRef]
52. Nielsen SS. Phenol-sulfuric acid method for total carbohydrates. In: Nielsen SS, editor. Food analysis laboratory manual. Food science texts series. Boston: Springer; 2010. p. 47–52. [Google Scholar]
53. French AD. Idealized powder diffraction patterns for cellulose polymorphs. Cellulose. 2014;21:885–96. doi:10.1007/s10570-013-0030-4. [Google Scholar] [CrossRef]
54. Percival Zhang Y-H, Cui J, Lynd LR, Kuang LR. A transition from cellulose swelling to cellulose dissolution by o-phosphoric acid: evidence from enzymatic hydrolysis and supramolecular structure. Biomacromolecules. 2006;7:644–8. doi:10.1021/bm050799c. [Google Scholar] [PubMed] [CrossRef]
55. Zhang J, Zhang J, Lin L, Chen T, Zhang J, Liu S, et al. Dissolution of microcrystalline cellulose in phosphoric acid-molecular changes and kinetics. Molecules. 2009;14:5027. doi:10.3390/molecules14125027. [Google Scholar] [PubMed] [CrossRef]
56. Kang P, Qin W, Zheng Z-M, Dong C-Q, Yang Y-P. Theoretical study on the mechanisms of cellulose dissolution and precipitation in the phosphoric acid-acetone process. Carbohydr Polym. 2012;90:1771–8. doi:10.1016/j.carbpol.2012.07.068. [Google Scholar] [PubMed] [CrossRef]
57. Su H, Wang B, Sun Z, Wang S, Feng X, Mao Z, et al. High-tensile regenerated cellulose films enabled by unexpected enhancement of cellulose dissolution in cryogenic aqueous phosphoric acid. Carbohydr Polym. 2022;277:118878. doi:10.1016/j.carbpol.2021.118878. [Google Scholar] [PubMed] [CrossRef]
58. Banuvalli B, Mudliar S, Bokade V, Debnath S. Evaluation of inhibition kinetics of furfural, 5-hydroxymethylfurfural and acetic acid on xylitol fermentation by Pichia stipitis NCIM 3497. Biomass Convers Biorefin. 2024;14:4909–23. doi:10.1007/s13399-022-02758-w. [Google Scholar] [CrossRef]
59. Fu S, Hu J, Liu H. Inhibitory effects of biomass degradation products on ethanol fermentation and a strategy to overcome them. BioResources. 2014;9:4323–35. [Google Scholar]
60. Moe ST, Janga KK, Hertzberg T, Hägg M-B, Øyaas K, Dyrset N. Saccharification of lignocellulosic biomass for biofuel and biorefinery applications A renaissance for the concentrated acid hydrolysis? Energy Proc. 2012;20:50–8. doi:10.1016/j.egypro.2012.03.007. [Google Scholar] [CrossRef]
61. Shiraki Y, Goto T, Nonaka H. Concentrated sulfuric acid hydrolysis of softwood with t-butyl alcohol. Biomass Convers Biorefin. 2021;11(3):937–41. doi:10.1007/s13399-019-00594-z. [Google Scholar] [CrossRef]
Appendix A
Figure A1: XRD patterns of Sample # 2 pretreated paper sludge (pretreatment conditions: acid concentration 60%, treatment time 0.5 h, 10% consistency, temperature 25°C), and Sample # 4 pretreated paper sludge (pretreatment conditions: acid concentration 85%, treatment time 0.5 h, 10% consistency, temperature 25°C)
Cite This Article
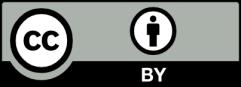
This work is licensed under a Creative Commons Attribution 4.0 International License , which permits unrestricted use, distribution, and reproduction in any medium, provided the original work is properly cited.