Open Access
ARTICLE
Reduction Discoloration of Reactive Dyed Cotton Waste and Chemical Recycling via Ionic Liquid
Department of Textile Engineering, Federal University of Santa Catarina, Blumenau, 89036-256, Brazil
* Corresponding Author: Andrea Cristiane Krause Bierhalz. Email:
Journal of Renewable Materials 2024, 12(9), 1557-1571. https://doi.org/10.32604/jrm.2024.052963
Received 20 April 2024; Accepted 08 July 2024; Issue published 25 September 2024
Abstract
The textile industry generates large volumes of waste throughout its production process. Most of this waste is colored, therefore, discoloration is an important step toward recycling and reusing this waste. This study focused on the chemical reductive discoloration of textile waste composed of cotton dyed with reactive dye. The experimental design demonstrated the significant influence of the concentration of reducing agent and time of reaction on the degree of whiteness of the cotton fibers. The concentration of the alkaline agent was not significant in the process. The optimization of the reaction conditions lead to Berger degree of 50.5 ± 3.5. The discolored cotton was chemically recycled through dissolution in ionic liquid 1-ethyl-3-methylimidazolium chloride and regeneration in film form in water. The microstructure of the regenerated cellulose films was evaluated by Scanning Electron Microscopy (SEM) indicating complete dissolution and uniform regeneration. The discoloration process reduced the polymerization degree and crystallinity index of the cotton fibers but retained the cellulose I structure. The dissolution and cellulose regeneration process results in transparent films with an amorphous structure. The thermal behavior, evaluated by thermogravimetric analysis, indicated that residues and regenerated film presented a main decomposition step. The maximum decomposition rate temperature of the regenerated films was approximately 40°C lower than the cotton fibers, which correlates well with the reduction in polymerization degree and amorphous structure. In general, the study demonstrated that textile cotton waste dyed with reactive dyes can be chemically discolored to form transparent and amorphous films, contributing to the development of sustainable strategies for the textile industry.Graphic Abstract

Keywords
Cotton is the most used natural fiber in the textile industry, representing 30% of total fiber production in the world [1]. The various stages of industrial cotton processing, such as spinning, weaving, and brushing, generate a large amount of solid waste. Most of these solid wastes are dyed by reactive dyes, which form a covalent bond with the cellulose in the fiber, imparting excellent fastness properties with relative ease of application [2]. These wastes have low added value and can be incinerated to generate heat or electricity energy. However, in the case of dyed waste, harmful gases can be released during incineration. If landfilled, the release of dye components during the degradation of the textile substrate can contaminate soil and water [2,3]. This is considered the least favored waste management method [4].
A promising alternative for reusing dyed cotton waste, which is mostly composed of cellulose, is the production of regenerated cellulose through chemical recycling. The dissolution of cellulose in ionic liquids, especially imidazole types, has gained prominence due to its dissolution efficiency and the possibility of recovering the solvent, resulting in a more sustainable and less harmful process to the environment [5,6]. As waste can have different colors, standardization can be done with a color removal procedure for more efficient use. Although some studies have used pre-and post-consumer cotton waste to obtain regenerated cellulose fibers or films using ionic liquids [1,7], the influence of color removal on physicochemical properties is poorly understood.
Discoloration of colored cotton fabric residues dyed with reactive dyes can be achieved through alkaline reduction [7]. A traditionally alkaline agent is sodium hydroxide, which breaks the covalent bond between the dye and cotton fiber via hydrolysis. The sodium hydrosulfite, in contrast, is responsible for the reduction reaction that will destroy the chromophore [8,9]. Although reduction reaction is well established in the textile field, literature is scarce regarding the single or joint effect of the time and concentration of reagents (reducing and alkaline agents) on the discoloration result. Optimization studies of reductive discoloration can lead to low reaction times and smaller amounts of reagents, which implies milder process conditions, reduced costs, and effluents with lower chemical loads, which is relevant for the textile sector.
In this work, reductive discoloration of dyed cotton waste from the textile brushing process was evaluated using an experimental design varying the reagents concentration and time of reaction. From the best discoloration condition, chemical recycling was performed by dissolving discolored cotton in ionic liquid and regeneration in transparent films. In addition to optimizing reaction conditions, the novelty of this study lies in the use of discolored waste to obtain regenerated cellulose via ionic liquid and to evaluate the effect of discoloration on crucial properties such as degree of polymerization, crystallinity, and thermal behavior.
A green-colored cotton waste from the textile brushing process was donated by a company located in Apiúna (Brazil). The choice of pure cotton waste to be discolored is justified by its high cellulose content, which is relevant for efficient subsequent chemical recycling. The trichrome of the green dye is presented in Table 1.
Commercial cotton fiber (Cremer®, hydrophilic, H2O2 bleached, free of any optical brightener) was used as a white standard. The reagents used in the reductive decolorization were sodium hydroxide P.A. (Ciacco) and sodium hydrosulfite P.A (Exodus Científica). The ionic liquid 1-ethyl-3-methylimidazolium chloride ([EMIM]Cl) (Sigma-Aldrich) was used for the dissolution of the cellulose and an aqueous solution of cuproethylenediamine 1 M (CUEN) (Sigma-Aldrich) was used for the determination of the degree of polymerization.
2.2 Chemical Treatment Discoloration
The chemical discoloration of the cotton waste was performed based on the NBR 13538 standard [10].
Samples of cotton waste (0.2 g), previously dried for 30 min at 60°C in an air renewal and circulation oven (New Lab, NL 82-81), were inserted in a 200 mL solution composed of sodium hydroxide (NaOH) and sodium hydrosulfite (Na2S2O4) at specific concentrations. The experiments were conducted under constant magnetic stirring, in a glycerin bath at 85°C. After the discoloration procedure, the samples were dried at 60°C for 30 min.
A full factorial experimental design 23 was conducted with repetition at the central point and axial points, to develop a statistical model to determine the conditions of the process that maximize the color removal and, consequently, achieve a higher degree of whiteness (Berger degree). Through this experimental design, the effects of the following factors on the Berger degree were evaluated: concentration of Na2S2O4 (x1) and NaOH (x2), as well as discoloration time (x3), according to the levels presented in Table 2.
The relevance of these reagents as variables was highlighted in the recent study by Wang et al. [9], who evaluated the individual use of NaOH, dithionite, and the two reagents combined in the decolorization of cotton with different chromophores. The authors set the reaction time at 80 min and the temperature at boiling or 80°C. In the present study, the temperature was set at 85°C, a condition usually used in industry and presents energy savings compared to the boiling temperature. Therefore, all discolorations were carried out with both reagents and the isolated and interaction effects of the variables were statistically evaluated. The experimental design generated in this study and the statistical analysis of the results obtained were performed using the Statistica® 12.0 software, with a significance level (α) of 5% and a confidence interval of 95%.
The degree of whiteness of the discolored fibers was measured in terms of Berger degree in a reflectance spectrophotometer (DATACOLOR 500) using illuminant UV D65/10 and 9 mm opening. The commercial cotton fiber sample was used as a white standard. The measurements were performed at four different points of the samples.
2.4 Dissolution and Regeneration of Cellulose
For dissolution, a sample of 0.09 g cotton from the best condition of the reducing discoloration was added to 3 g of ionic liquid [EMIM]Cl. The mixture was heated at 110°C in a glycerin bath and stirred for 2.5 h [11]. Then, the cellulose solution was poured into a 5 cm diameter Petri dish and spread evenly to form a homogeneously thick film. The coagulation of the cellulose occurred after 15 mL of deionized water was added to the solution and remained for 15 min. The solidified cellulose film was washed several times with deionized water until the ionic liquid was completely removed and then dried at 60°C for 30 min.
2.5 Scanning Electron Microscopy (SEM)
The morphology of the surface and cross-section of the regenerated film was evaluated by Scanning Electron Microscopy (SEM). The SEM images were performed using a scanning electron microscope JEOL (model JSM-6390LV). The samples were placed on carbon disks with gold coating before obtaining the images.
2.6 Degree of Polymerization (DP)
The degree of polymerization of the cotton fibers and the regenerated films was evaluated following the ASTM D1795-13/2021 standard. The previously dried samples of fibers or films (0.018 g) were added to 17.5 mL of deionized water and 17.5 mL of 1 M of copper (II) ethylene-diamine solution (CUEN) in an Erlenmeyer-containing sphere glass. The system was stirred in an orbital shaker (NL-343-01, New Lab) under a nitrogen atmosphere for 3 h at 150 rpm and a temperature of 25°C. After this period, 7 mL of the mixture was transferred to the viscometer Cannon-Fenske n° 75 and kept in a water bath at 25°C to measure the flow time. The DP was obtained by Eq. (1).
where (η) is the intrinsic viscosity, calculated from Eq. (2).
In Eq. (2), ηsp is the specific viscosity, c is the polymer concentration (g/dL), and k is Martin’s constant.
The specific viscosity is determined from the relative viscosity (ηrel), which correlates the outflow time of the CUEN-cellulose solution (t) and the outflow time of the CUEN solution (t0), as Eq. (3).
XRD studies of the samples were carried out using an X-ray diffractometer (MiniFlex600 model, Rigaku) operating at 45 kV and 40 mA. The diffraction intensity was measured in the reflection mode at a rate of 0.1°/min for 2 (θ) = 5 – 90° [12]. The crystallinity index was calculated by Segal’s method using Eq. (4).
where I200 is the height intensity of the crystal plane (at 22.6° of 2θ for cellulose I, and 20.2° of 2θ for cellulose II), and the Iam refers to the minimum intensity of diffraction attributed to amorphous cellulose between planar reflections (110)/(200) and (1–10)/(110) for celluloses I and II, respectively [13].
2.8 Fourier Transform Infrared Spectroscopy (FTIR)
The identification of functional groups in the structure of cotton fibers and regenerated films was performed by FTIR in Attenuated Total Reflection (ATR) mode in Cary 660 FTIR equipment (Agilent Technologies, Denver, CO, USA), in the range of 4000–400 cm−1 and resolution of 4 cm−1.
2.9 Thermogravimetric Analysis (TGA)
The thermal stability of the cotton samples and regenerated films was evaluated using a STA 449-F3 Jupiter (Netzsch, Selb, Germany). Samples with approximately 10 mg were heated from room temperature to 600°C, at a rate of 10°C.min−1, under a nitrogen atmosphere with a flow rate of 60 mL.min−1.
3.1 Chemical Treatment Discoloration
According to the experimental design, reducing discolorations were performed using sodium hydrosulfite and sodium hydroxide at different concentrations and times of reaction. Table 3 shows the results of the measurements of Berger degree using commercial cotton fiber as a standard.
The highest Berger degree was obtained for the treatment 13 (35.96 Berger degrees), which indicated that the conditions used in this discoloration reaction (48 g/L Na2S2O4, 16 g/L NaOH and 60 min) resulted in cotton fibers with a degree of whiteness closest to the standard.
The effect of the dependent variables (concentrations and time of reaction) on reducing discoloration is shown in Table 4. The linear variables that presented an isolated effect were time, with the greatest effect, and Na2S2O4 concentration. The other variables, linear and quadratic and interaction, did not show significant effects.
The reaction time had a positive effect on the Berger degree, indicating that more time is needed to remove the color. This may be related to the difficulty of accessing dyes covalently linked to cellulose since the morphology of the cotton fiber is complex and arranged in layers in the structure of the cotton fiber [14]. However, increasing the reaction time can also compromise the fiber, reducing the degree of polymerization.
On the other hand, Na2S2O4 concentration had a significant negative effect. This means that increasing the concentration results in a lower degree of reduction in discoloration, possibly due to over-reduction, excessive damage to the material, or the formation of unwanted by-products.
Under the conditions studied, the NaOH concentration was insignificant for the color removal reaction. This result indicates that the lowest level of NaOH concentration studied (10 g/L) is sufficient for the reduction reaction. This explanation is corroborated by the negative sign of the effects of this variable, which despite not being significant, are both negative. Despite being a component that must be present in the cotton discoloration process, lower concentrations of NaOH reduce the risk of cellulose degradation and favor a better resistance of the cellulose material obtained in the subsequent dissolution process.
The analysis of the response surface of the interaction between time and sodium hydrosulfite, shown in Fig. 1, indicates that, regardless of the test time employed, the concentration of Na2S2O4 exhibits a beneficial effect by increasing the concentration until it reaches 48 g/L. However, the Berger degree declines for higher values, indicating that Na2S2O4 becomes detrimental to the process, as demonstrated by the negative significant effect value. In addition, the interaction surface confirms the positive effect of time, revealing that longer test times are associated with greater discoloration.
Figure 1: Graph of variable interactions between Na2S2O4 and time
The ANOVA analysis (Table 5) proves that the isolated linear effects of time and Na2S2O4 concentration have a statistically significant interference in the degree of whiteness, based on the 95% confidence level. This means that these variables have an important impact on the response studied. The ANOVA analysis resulted in a coefficient of determination (R2) of 0.85287, indicating that about 85% of the variability in the degree of whiteness can be explained by the variation of the proposed factors (time of reaction, NaOH concentration and Na2S2O4 concentration), with low external interference and good reproducibility to green reactive dye. This information is relevant because a high R² value indicates that the factors considered in the model can explain a large part of the variability observed in the response studied. The values obtained in the analysis of the curvature of the quadratic predictive model (Eq. (5)) demonstrated a good fit for the observed data. Thus, it can be considered that the model allows predicting values of discoloration of reactive green dye-cotton for several intermediate values of the studied factor, under conditions imposed by the independent variables (x1, x2, and x3). The 15% difference between the experimental data and the predicted values (R2) can be adjusted by choosing the dye color without color deviation in the final product. Furthermore, analyzing the residual variance, the lack of fit test was not significant (p-value > 0.05) for the prediction model, implying that the experimental data were well adjusted.
The simplified regression predictive model (coded variables) was obtained by excluding non-significant regression coefficients for predicting the Berger degree (Eq. (5)).
where x1 represents the encoded sodium hydrosulfite concentration and x2 represents the encoded time.
Desirability is a statistical technique often used in process optimization, aiming to find the optimal combination of independent variables that simultaneously satisfy the desired criteria for the dependent variables. It allows different criteria to be considered and combined into a single desirability function, making it easier to find the optimal operating point [15]. In the context of chemical decolorization, desirability was employed to optimize the process, i.e., to find the ideal concentrations of the independent variables (Na2S2O4, NaOH, and reaction time) that provide the best possible Berger degree. The optimum point, determined by desirability analysis (Fig. 2), corresponds to concentrations of 42.6 g/L of Na2S2O4, 22 g/L of NaOH, and a time of 90 min.
Figure 2: Application of desirability to optimize the Berger degree
The experiment was repeated in duplicate, resulting in a Berger degree of 50.5 ± 3.5, validating these reaction conditions. Fig. 3 shows a comparative image between the original residue (a) and the discolored residue under optimal conditions, providing visual evidence of the success achieved in discoloration. Therefore, 42.6 g/L of Na2S2O4, 22 g/L of NaOH, and 90 min of reaction were selected to study the recycling of discolored waste by regenerating cellulose into films after dissolution in ionic liquid. Using the optimized sample in recycling is relevant considering the application of cellulose regenerated films since the greater whiteness degree tends to result in greater transparency.
Figure 3: Green residue (a) discolored green residue (b) and regenerated film of the discolored green residue (c)
Li et al. [2] decolorized cotton fabric waste dyed with dark blue reactive dyes and achieved a decolorization efficiency of 90.9% after 90 min of treatment using 25 g/L of Na2S2O4, but at a temperature of 90°C. Bigambo et al. [16] discolored fabrics dyed with reactive dyes and post-consumer denim fabric, using 30 g/L of Na2S2O4, and 40 g/L of NaOH at a temperature of 80°C for 1 h. This treatment removed part of the dyes reactive agents (Black 5, Blue 19, and Red 228) of dyed fabrics. To obtain a more efficient decolorization, these authors employed a combined treatment involving H2SO4/Na2S2O4/H2O, resulting in the production of white regenerated fibers through the Lyocell/NMMO process.
It is noteworthy that the chromophore groups and active groups of the reactive dyes influence the discoloration process, as pointed out by Wang et al. [9]. Therefore, the obtained conditions are optimized for green reactive dye, which has more than one chromophore group. Substrates with other colors and containing a single chromophore group may require milder conditions.
3.2 Dissolution and Regeneration of Cellulose
After the dissolution of the discolored waste in ionic liquid, the cellulose was regenerated using water as an antisolvent and formed a transparent and macroscopically homogeneous film (Fig. 3).
The morphology of the regenerated films from discolored cotton was investigated by SEM and the results (Fig. 4) show a predominantly regular, dense, and homogeneous microstructure, with no evidence of pores and undissolved fibers.
Figure 4: SEM images of cellulose films at (a) Surface morphology at 100× magnification, (b) Surface morphology at 1000× magnification, (c) transverse morphology at 100× magnification, and (d) transverse morphology at 1000× magnification
3.3 Degree of Polymerization (DP)
The DP values of the green residue, discolored residue, and its regenerated film are shown in Fig. 5.
Figure 5: Degree of polymerization (DP) of green and discolored waste samples and their regenerated film
The results indicate that the DP of discolored waste was significantly (p < 0.05) lower than green waste. This means that the discoloration process affected the cellulose molecular chain, leading to depolymerization and compromising the structural integrity of the cellulose-containing material.
The regenerated film also presented a significant reduction in DP compared to the discolored waste, which was the cellulose raw material. This phenomenon occurs due to the interaction between the ionic liquid and the cellulose molecular chains during the dissolution stage. This interaction leads to the breaking of hydrogen bonds, both intramolecular and intermolecular [17,18]. During the regeneration process, changes involve the rearrangement of molecular chains into smaller structures, the formation of amorphous molecular structures, and the degradation of cellulose, resulting in a reduced DP [19,20].
The results are consistent with the literature [21]. For example, Li et al. [2] investigated the discoloration of cotton waste dyed with reactive dyes, which presented a DP of 1327. For the regenerated films, the values observed corroborate the DPs demonstrated by De Silva et al. [1], who used textile waste as a source of cellulose and 1-allyl-3-methylimidazolium chloride, [AMIM]Cl, for the dissolution process at 100°C. The DP obtained for the regenerated film in this study was 550.
The XRD profiles revealed distinct characteristics for the residues and the regenerated cellulose film, as illustrated in Fig. 6. The green residue and the discolored residue exhibited diffraction angles typical of cellulose I (2θ) around 14.8°, 16.6°, 22.4°, and 34.5°, corresponding to the crystallographic planes (1–10), (110), (200) and (004), respectively [22,23]. The green and discolored residue’s crystallinity index (CrI) was 78.0% and 74.5%, respectively. This reduction in CrI of the discolored residue corroborates the lower degree of polymerization obtained for this sample. On the other hand, in the regenerated cellulose film, a broad peak at 2θ = 20.6° was observed in the XRD patterns, indicating an amorphous structure [24] The formation of amorphous films upon dissolution in ionic liquids has been corroborated by previous studies [25,26]. According to Sundberg et al. [26], the rapid regeneration process solidifies the disordered state of cellulose molecules in the ionic liquid solution, preventing recrystallization.
Figure 6: XRD patterns of the green residue, discolored residue samples, and their regenerated film
3.5 Infrared Spectroscopy (FTIR)
The FTIR spectrum of the discolored residue and the regenerated film are shown in Fig. 7. For all samples, a wide absorption band between 3100–3600 cm−1 was identified, corresponding to the elongation vibration of the OH groups, indicating the presence of inter-and intramolecular hydrogen bonds in the cellulose chains [22]. Symmetrical elongation vibration of −CH was observed at 2900 cm−1 [23] and deformation of CH2 groups at 1430 cm−1.
Figure 7: FTIR spectra of the green residue, discolored residue samples, and their regenerated film
The absorption band at 1313 cm−1 in the regenerated film is associated with CH2 shear vibration. These results suggest that intramolecular hydrogen bonds containing O6 have been destroyed [27]. The absorption bands in the range of 1064 cm−1 are related to the vibration of the anhydroglucose ring C-O-C [28]. The strong absorption band at 1027 cm−1 is attributed to the characteristic elongation of the C-O-C bonds. In addition, the band at 894 cm−1 is associated with the amorphous region of cellulose, corresponding to the β bond of cellulose [1].
The absorption bands at 1430, 1162, 1111, and 893 cm−1 are important for the analysis of cellulose crystallinity and the changes that occur during the dissolution process [29]. The characteristic bands of cellulose I at 1430, 1162, and 111 cm−1, present in the residue sample, were not found in the cellulose film sample. On the other hand, the band at 1420 cm−1, present in the film spectrum, is characteristic of cellulose II and amorphous cellulose [23]. In addition, the most significant and well-defined band at 893 cm−1 confirms the absence of cellulose I in the regenerated cellulose film and is also related to amorphous cellulose [29]. Based on these results, it can be stated that the regenerated cellulose film is composed mostly of amorphous cellulose, corroborating the data obtained in the XRD analysis.
3.6 Thermogravimetric Analysis (TGA)
The thermal behavior of the green and discolored waste samples and the regenerated film was investigated by TGA and the weight loss (TG) and weight loss derivative (DTG) results are presented in Fig. 8a,b, respectively.
Figure 8: TG (a) and DTG (b) of the green residue, discolored residue sample and their regenerated film
The first stage of mass loss occurred between 70°C and 170°C in both samples and is attributed to the water desorption process due to the moisture absorbed [23]. The second stage is associated with the depolymerization, dehydration, and decomposition of cellulose [22]. As described in Table 6, the initial temperature (Tonset) of the decomposition process for the green and discolored residue sample was higher than the regenerated film. The maximum decomposition rate temperature (Tmax) occurred at 387°C for the waste samples and 345°C for the regenerated film. Thermal stability is closely linked to crystallinity, as cellulose pyrolysis gradually progresses from the non-crystalline zone to the crystalline zone [1,30]. According to Wang et al. [30], cellulose samples with lower crystallinity start to degrade at lower temperatures due to the formation of a liquid intermediate, reducing activation energies and accelerating dehydration reactions. Therefore, the cellulose in the green and discolored waste sample showed a higher decomposition temperature and greater stability than the regenerated cellulose film, which showed an amorphous structure after the dissolution process. In the main stage of degradation, the mass loss was 77% and 71% for the green and discolored residue, respectively. For the regenerated film, a mass loss of 52% was observed. The reduction in mass loss of the regenerated film can be attributed to the prevalence of amorphous regions in the samples [7]. As shown in Table 6, it is noted that the percentage of residual mass at 600°C in the discolored residue (6%) was lower than that in the green residue (15%). This disparity may be associated with the discoloration process suffered by discolored residue. The carbon residue at 600°C was higher for the regenerated film, which may be linked to the non-crystalline content; in other words, an increase in non-crystalline content could lead to a higher carbon yield [21].
This study evaluated the discoloration of dyed cotton waste using the chemical reductive method. The time of reaction and concentration of the reducing agent have a statistically significant interference in the degree of whiteness. Through optimization, a Berger degree of 50.5 ± 3.5 was achieved after discoloration of the green cotton waste. Compared to the properties of the original residue, the discolored residue showed a lower degree of polymerization and degree of crystallinity but maintained the structure of type I cellulose. Thermal stability was little affected by the discoloring process. The film obtained from the dissolution of discolored cotton in ionic liquid presented transparency, homogeneity, and a smooth surface. SEM images confirmed the complete dissolution of cellulose in the film. The regeneration process resulted in amorphous films and in thermal stability and degree of polymerization lower than the discolored residue, but similar to commercial cellulose products.
These findings are relevant to the advancement of knowledge in the area of textile discoloration, providing valuable information for the development of more efficient and sustainable strategies for treating reactive dye residues on cotton substrates. This approach can pave the way for improvements in the treatment of textile waste and contribute to reducing the environmental impact associated with the inappropriate disposal of reactive dyes.
Acknowledgement: The authors thank to the LINDEN-Metro Laboratory and the Central de Análises at the Federal University of Santa Catarina for their assistance in analysis.
Funding Statement: This work was supported by Fundação de Amparo à Pesquisa e Inovação do Estado de Santa Catarina (FAPESC) (Grant Number 2021TR000327) and by the Coordenação de Aperfeiçoamento de Pessoal de Nível Superior-Brasil (CAPES)-Finance Code 001.
Author Contributions: The authors confirm contribution to the paper as follows: study conception and design: Aline Ferreira Knihs; data collection: Aline Ferreira Knihs, Larissa Klen Aragão; analysis and interpretation of results: Aline Ferreira Knihs, Larissa Klen Aragão, Miguel Angelo Granato, Andrea Cristiane Krause Bierhalz, Rita de Cássia Siqueira Curto Valle; draft manuscript preparation: Aline Ferreira Knihs, Andrea Cristiane Krause Bierhalz, Rita de Cássia Siqueira Curto Valle. All authors reviewed the results and approved the final version of the manuscript.
Availability of Data and Materials: Data is available on request from the authors.
Ethics Approval: Not applicable.
Conflicts of Interest: The authors declare that they have no conflicts of interest to report regarding the present study.
References
1. De Silva R, Byrne N. Utilization of cotton waste for regenerated cellulose fibres: influence of degree of polymerization on mechanical properties. Carbohydr Polym. 2017;174(1):89–94. doi:10.1016/j.carbpol.2017.06.042. [Google Scholar] [PubMed] [CrossRef]
2. Li R, Yang J, Zhang G, Zhu P. Decolorization of dark-colored waste cotton fabric using redox decoloring agents. RSC Adv. 2022;12(28):17689–700. [Google Scholar] [PubMed]
3. Ibrahim1 NA, Eid BM, Khattab TA. Environmentally sound dyeing of cellulose-based textiles. In: Shabbir M, editor. Textiles and clothing. Wiley-Scrivener; 2019. p. 77–99. [Google Scholar]
4. Çifçi DI, Atav R, Güneş Y, Güneş E. Determination of the color removal efficiency of laccase enzyme depending on dye class and chromophore. Water Sci Tech. 2019;80(1):134–43. [Google Scholar]
5. Verma C, Mishra A, Chauhan S, Verma P, Srivastava V, Quraishi MA, et al. Dissolution of cellulose in ionic liquids and their mixed cosolvents: a review. Sustain Chem Pharm. 2019;13:100162. doi:10.1016/j.scp.2019.100162. [Google Scholar] [CrossRef]
6. Ma Y, Nasri-nasrabadi B, You X, Wang X, Rainey TJ. Regenerated cellulose fibers wetspun from different waste cellulose types regenerated cellulose fibers wetspun from different waste. J Nat Fibers. 2021;18(12):2338–50. doi:10.1080/15440478.2020.1726244. [Google Scholar] [CrossRef]
7. Liu H, Fan W, Miao Y, Dou H, Shi Y. Closed-loop recycling of colored regenerated cellulose fibers from the dyed cotton textile waste. Cellulose. 2023;30(4):2597–610. doi:10.1007/s10570-022-05002-w. [Google Scholar] [CrossRef]
8. Saikhao L, Setthayanond J, Karpkird T, Suwanruji P. Comparison of sodium dithionite and glucose as a reducing agent for natural indigo dyeing on cotton fabrics. MATEC Web Conf. 2017;108(1):8–11. doi:10.1051/matecconf/201710803001. [Google Scholar] [CrossRef]
9. Wang W, Xu Z, Yin Y, Wang H, Guo X, Gong Z, et al. Decolorization properties and mechanism of reactive-dyed cotton fabrics with different structures utilized to prepare cotton pulp. Cellulose. 2023 May 1;30(7):4735–48. doi:10.1007/s10570-023-05153-4. [Google Scholar] [CrossRef]
10. Associação Brasileira de Normas Técnicas. NBR 13538 qualitative analysis of textiles–method of test. Rio de Janeiro: ABNT; 1995. p. 1–20 (In Portuguese). [Google Scholar]
11. Ferreira Knihs A, Klen Aragão L, Porto B, Borges Valle JA, Granato MA, Bierhalz ACK, et al. Influence of acid hydrolysis on the degree of polymerization of cellulose from colored cotton substrates. J Text Inst. 2024;6(4):1–7. doi:10.1080/00405000.2024.2354116. [Google Scholar] [CrossRef]
12. Liu Z, Wang H, Li Z, Lu X, Zhang X, Zhang S, et al. Characterization of the regenerated cellulose films in ionic liquids and rheological properties of the solutions. Mater Chem Phys. 2011;128(1–2):220–7. doi:10.1016/j.matchemphys.2011.02.062. [Google Scholar] [CrossRef]
13. French AD. Idealized powder diffraction patterns for cellulose polymorphs. Cellulose. 2014;21(2):885–96. [Google Scholar]
14. Gordon S, Hsieh YL. Cotton: science and technology. England: Woodhead P. Cambridge; 2007. [Google Scholar]
15. Myers RH, Montgomery DC. Response surface methodology: process and product optimization using designed experiments. New York: Wiley; 1995. [Google Scholar]
16. Bigambo P, Carr CM, Sumner M, Rigout M. The effect of the acid/dithionite/peroxide treatments on reactively dyed cotton and indigo dyed denim and the implications for waste cellulosic recycling. J Text Inst. 2020;111(6):785–94. doi:10.1080/00405000.2019.1662874. [Google Scholar] [CrossRef]
17. Sirvio JA. Fabrication of regenerated cellulose nanoparticles by mechanical disintegration of cellulose after dissolution and regeneration from a deep eutectic solvent. J Mater Chem. 2019;7:755–63. [Google Scholar]
18. Uto T, Yamamoto K, Kadokawa JI. Cellulose crystal dissolution in imidazolium-based ionic liquids: a theoretical study. J Phys Chem B. 2018;122(1):258–66. [Google Scholar] [PubMed]
19. De Araújo AM, Braido G, Saska S, Barud HS, Franchi LP, Assunc RMN, et al. Regenerated cellulose scaffolds: preparation, characterization and toxicological evaluation. Carbohydrate Polymers J. 2016;136:892–8. [Google Scholar]
20. Jiang W, Sun L, Hao A, Chen JY. Regenerated cellulose fibers from waste bagasse using ionic liquid. Text Res J. 2011;18(81):1949–58. doi:10.1177/0040517511414974. [Google Scholar] [CrossRef]
21. Liu W, Liu S, Liu TT, Liu TT, Zhang J, Liu H. Eco-friendly post-consumer cotton waste recycling for regenerated cellulose fibers. Carbohydr Polym. 2019;206:141–8. doi:10.1016/j.carbpol.2018.10.046. [Google Scholar] [PubMed] [CrossRef]
22. Tan X, Chen L, Li X, Xie F. Effect of anti-solvents on the characteristics of regenerated cellulose from 1-ethyl-3-methylimidazolium acetate ionic liquid. Int J Biol Macromol. 2019;124:314–20. doi:10.1016/j.ijbiomac.2018.11.138. [Google Scholar] [PubMed] [CrossRef]
23. Pang J, Wu M, Zhang Q, Tan X, Xu F, Zhang X, et al. Comparison of physical properties of regenerated cellulose films fabricated with different cellulose feedstocks in ionic liquid. Carbohydr Polym. 2015;121(3):71–8. doi:10.1016/j.carbpol.2014.11.067. [Google Scholar] [PubMed] [CrossRef]
24. Yao W, Weng Y, Catchmark JM. Improved cellulose X-ray diffraction analysis using Fourier series modeling. Cellulose. 2020 Jul 1;27(10):5563–79. doi:10.1007/s10570-020-03177-8. [Google Scholar] [CrossRef]
25. Zhao Z, Gao H, Zhou L, Wang J, Yuan H, Wei J, et al. Preparation of regenerated cellulose fibers by microfluidic spinning technology using ionic liquids as the solvents. Cellulose. 2023 Aug 1;30(12):7535–49. [Google Scholar]
26. Sundberg J, Toriz G, Gatenholm P. Moisture induced plasticity of amorphous cellulose films from ionic liquid. Polymer. 2013 Nov 14;54(24):6555–60. [Google Scholar]
27. Li X, Li H, Ling Z, Xu D, You T, Wu YY, et al. Room-temperature superbase-derived ionic liquids with facile synthesis and low viscosity: powerful solvents for cellulose dissolution by destroying the cellulose aggregate structure. Macromolecules. 2020;53(9):3284–95. [Google Scholar]
28. Lv F, Wang C, Zhu P, Zhang C. Isolation and recovery of cellulose from waste nylon/cotton blended fabrics by 1-allyl-3-methylimidazolium chloride. Carbohydr Polym. 2015;123:424–31. [Google Scholar] [PubMed]
29. Carrillo F, Colom X, Suñol JJ, Saurina J. Structural FTIR analysis and thermal characterisation of lyocell and viscose-type fibres. Eur Polym J. 2004;40(9):2229–34. [Google Scholar]
30. Wang Z, McDonald AG, Westerhof RJM, Kersten SRA, Cuba-Torres CM, Ha S, et al. Effect of cellulose crystallinity on the formation of a liquid intermediate and on product distribution during pyrolysis. J Anal Appl Pyrolysis. 2013;100(4):56–66. doi:10.1016/j.jaap.2012.11.017. [Google Scholar] [CrossRef]
Cite This Article
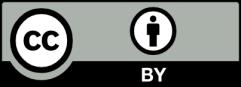
This work is licensed under a Creative Commons Attribution 4.0 International License , which permits unrestricted use, distribution, and reproduction in any medium, provided the original work is properly cited.