Open Access
ARTICLE
Potential of Bamboo Species Guadua trinii and Guadua angustifolia for Nanocellulose Production
1 Círculo de Investigación del Bambú, Universidad Nacional Agraria La Molina (UNALM), Lima, 15026, Perú
2 Instituto de Materiales de Misiones (IMAM), Universidad Nacional de Misiones (UNaM), Consejo Nacional de Investigaciones Científicas y Técnicas (CONICET), Facultad de Ciencias Exactas, Químicas y Naturales (FCEQYN), Programa de Celulosa y Papel (PROCyP), Posadas, 3300, Argentina
3 Instituto de Materiales de Misiones (IMAM), Universidad Nacional de Misiones (UNaM), Consejo Nacional de Investigaciones Científicas y Técnicas (CONICET), Facultad de Ciencias Forestales (FCF), Eldorado, 3380, Argentina
* Corresponding Author: María Evangelina Vallejos. Email:
Journal of Renewable Materials 2024, 12(9), 1541-1555. https://doi.org/10.32604/jrm.2024.052481
Received 03 April 2024; Accepted 05 August 2024; Issue published 25 September 2024
Abstract
Non-traditional lignocellulosic materials are a significant resource for producing high-value products, including nanocellulose. This work studied the nanocellulose obtention from chemical pulps of the two fast-growing bamboo species, Guadua trinii, and Guadua angustifolia. Chemical pulps were produced by soda-anthraquinone (S) pulping from both autohydrolysis-pretreated (H) and unpretreated bamboo chips. Autohydrolysis-pretreated (SHP) and unpretreated soda-anthraquinone (AQ) (SP) pulps were characterized by yield, Kappa number, alpha, beta, and gamma cellulose, degree of polymerization, water retention value, and crystallinity. The nanocellulose was produced by a sequential chemical oxidation treatment (2,2,6,6-tetramethylpiperidine-1-oxyl, TEMPO reagent) and mechanical nanofibrillation. Nanocellulose was characterized by carboxylic group content and viscosity. The results revealed that autohydrolysis pretreatment resulted in a higher hemicelluloses extraction in G. angustifolia. In contrast, the pulping yield of unpretreated samples was higher for G. trinii, and the soda-AQ pulps from this species exhibited better delignification than the autohydrolysis-pretreated pulps. The crystallinity index values of the obtained pulps were high (>80%), and the alpha-cellulose contents were similar. The viscosities of the aqueous nanocellulose suspensions were higher for the nanocellulose solutions obtained from the unpretreated soda-AQ pulps. Besides, nanocellulose from G. trinii unpretreated soda-AQ pulps had a higher rate of carboxylic groups. The results of this work are significant in assessing the potential of both bamboo species as a source of high-value products within the biorefinery framework because the viscosities of the aqueous nanocellulose suspensions depend on the size and shape of nanofibrils. It has significant importance for industrial unit operations and potential applications.Graphic Abstract
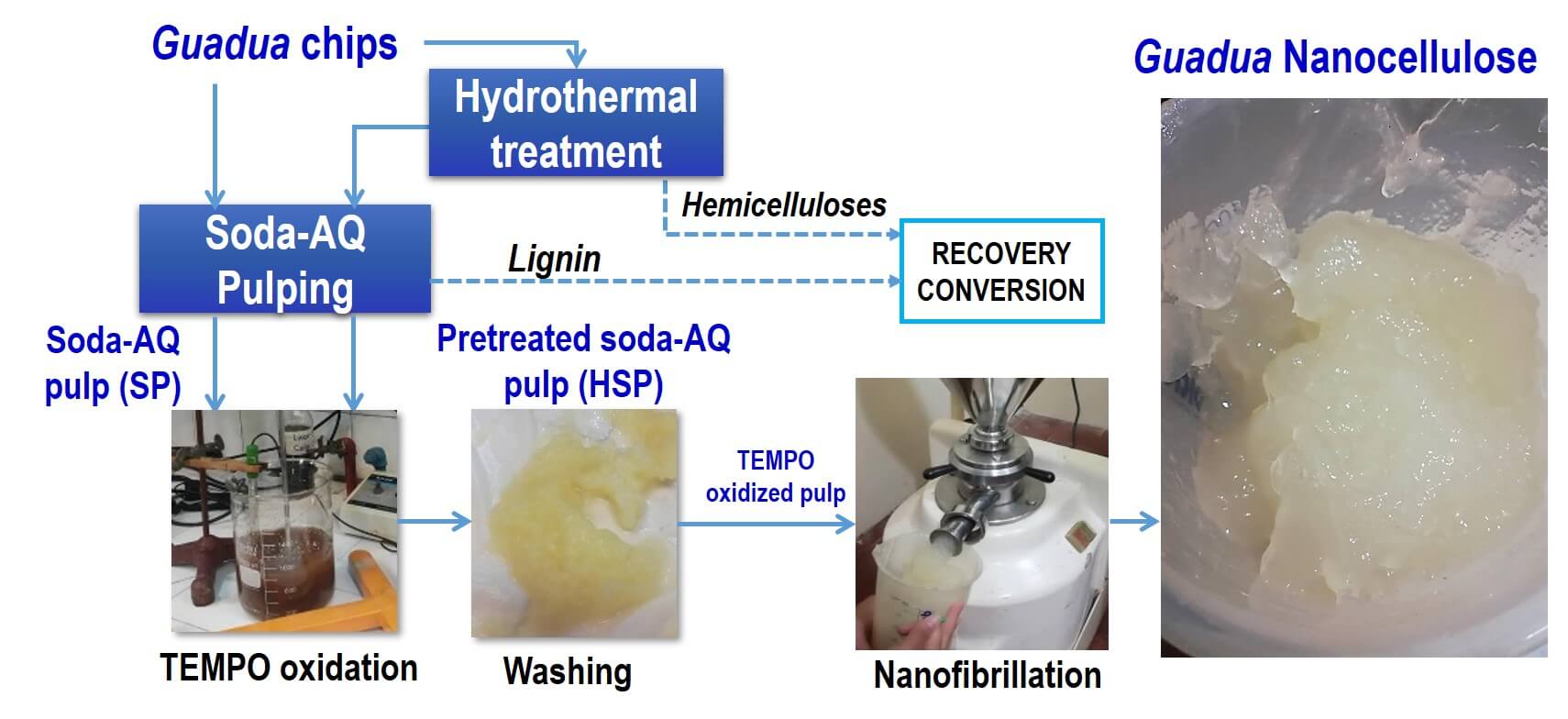
Keywords
Inexpensive and widely available nonwood biomass includes agricultural and forest byproducts, native fibrous plants, and annual plants, which grow and can be harvested quickly. The cellulosic fibers from these sources are excellent substitutes for raw materials, especially given the global decline in wood resources. As a result, research into alternative renewable raw materials for the energy, chemical, pharmaceutical, and biomaterials industries has increased significantly [1,2]. Lignocellulosic material has become the most relevant future biomass source due to its moderate costs and minimal competition with food production [3,4]. Due to recent advancements, cellulose, and paper producers in tropical and subtropical regions can now use technologies that have increased their production capacities while reducing raw material and labor costs. These improvements have helped these producers remain competitive in a constantly changing market. Additionally, these regions boast a variety of annual crops (such as sisal and bamboo) and agroforestry residues (including sugar cane bagasse, wood sawdust, and cereal straw) with significant potential as fibrous resources because of their rapid growth, low cost, and renewability [5,6].
Projections indicate that the prices of forest products may keep falling due to global market competition. So, forest producers have implemented innovative strategies to boost their income by producing bioenergy and biomaterials alongside wood, pulp, and paper to counter this. One such strategy is adopting the biorefinery concept, which leverages the high concentration of raw materials in the forestry industry [2].
A biorefinery is a facility that produces fuel, energy, and chemical products from biomass. It emerged from the need to protect the environment using closed-cycle, eco-friendly processes. Initially, biorefineries aimed to produce ethanol from lignocellulosic residues due to oil shortages. Recently, however, it has been discovered that biorefineries can generate various chemical products from biomass besides biofuels [1]. The lignocellulosic feedstock biorefinery encompasses the refining of lignocellulosic biomass (wood, straw, others) into intermediate outputs (cellulose, hemicellulose, lignin) for producing a spectrum of products and bioenergy. The products from the biorefinery serve to incorporate biomass in the development and formulation of energy strategies in the short, medium, and long term; the analysis of technical, economic, ecological, environmental, and social impacts; and contribute to the sustainable management of natural resources for the production of raw materials for the production of bioenergy [4]. The biorefinery concept presents a significant opportunity for this industry, as it can enhance companies’ profitability. This potential has led to increased research into lignocellulosic materials as alternative renewable raw materials for the energy sector, chemical production, pharmaceuticals, and biomaterials manufacturing [2].
The bamboo market is still emerging and complex. Due to its rapid growth, high strength, surface hardness, and ease of machining, its traditional use is in construction and handicrafts. Its production is scattered, and its market is highly interconnected, involving merchants, producers, transporters, and regulatory authorities. Guadua angustifolia, a high-strength fibrous material, has a basic density of 700 kg/m3. In 2016, a Bamboo Research Circle (CIB) of Perú was established at the La Molina Agrarian University (UNALM) with some institutional partners. UNALM promotes research on bamboo in three fields: taxonomy and ethnobotany, technology for its transformation, and value chain and markets [7]. In Paraguay and NE of Argentina, a similar species called Guadua chacoensis (tacuara cane) grows wild. Guadua trinii can be found in southern Brazil, Uruguay, and Argentina. In Argentina, this species lives in Buenos Aires, Corrientes, Entre Ríos, and Misiones. This species grows in the Misiones Jungle, forming dense, impenetrable thickets [8]. It is used to construct ranch walls, with the mud adhering well to its thorns and rough edges [9,10]. Additionally, it has been tested for use in paper manufacturing [11].
Guadua is harvested after four years and has a woody structure that is simpler than wood. Its diameter can reach 17 cm, with a hollow interior and a stem thickness of 15–18 mm. The stem can grow up to 25 m tall, depending on the region [7]. Recent research has focused on its use in structural and semi-structural applications, such as reinforcing fiber in composite materials or polymer matrix composites [12]. These studies have demonstrated that bamboo fiber can reinforce composite materials due to its excellent mechanical properties. Some research indicates that the tensile strength and modulus of elasticity of bamboo fibers are nearly twice those of pine fibers and significantly higher than other softwood fibers, attributed to the unique structure of their cellular walls [13]. However, the differences among bamboo species and the limited research available to clarify their structural, morphological, chemical, and physical distinctions, just as the size distribution of their fibers, have restricted their use as a fibrous resource with industrial significance.
Alkaline pulping (kraft, soda, sulfite, and organosolv) is the most widely used delignification technology for nonwood raw materials such as bamboo. Soda and soda-anthraquinone (AQ) pulping are the standard methods for processing nonwood raw materials. The required NaOH load, typically between 15% and 20%, depends on the species’ chemical composition, while the pulping process operates at temperatures ranging from 140°C–170°C. Adding Anthraquinone (1% to 5%) improves pulping efficiency by speeding up the delignification process and protecting the carbohydrates [14,15].
Cellulose, composed of β-D-glucose units linked in a linear polymer chain, with cellobiose as the repeating unit, is the main polysaccharide in the cell walls of lignocellulosic biomass. These cellulose chains form elementary fibrils through hydrogen bonding, which aggregate into microfibrils [16]. These microfibrils provide strength and rigidity to plant cell walls, contributing to the structural integrity of materials like wood. The organized structure of cellulose within microfibrils, along with additional components like lignin and hemicellulose, adds to the complexity and diversity of the chemical composition of lignocellulosic biomass [17]. When isolated from the cell wall, these nanofiber structures, due to their unique supramolecular structure and nanoscale properties, can be used as reinforcing elements to create advanced composite materials with exceptional performance [18,19].
Cellulose nanofibrils (CNF) generally range from 10 to 50 nm in diameter and extend several micrometers in length [20,21]. These composite materials show significant potential in diverse fields, including optoelectronic devices, packaging, and pharmaceuticals [22,23]. Various lignocellulosic resources are sources of CNF [24]; while wood was initially used, other fibrous materials are now being explored [25–28].
Cellulosic nanoparticles or nanocelluloses have a distinctive structure suitable for reinforcing materials, offering enhanced performance and novel functionalities. Their properties depend on the extraction method from trees, plants, or other cellulose-containing sources [29]. CNFs can be produced through mechanical, chemical, or a combination of these methods. Mechanical treatments applied to pretreated material are homogenization, microfluidization, cryocrushing, and microgrinding, yielding nano-and microfibrillated cellulose. Chemical or enzymatic pretreatments, such as 2,2,6,6-tetramethylpiperidine-1-oxyl (TEMPO) oxidation and carboxymethylation, are often used to enhance the degree of nanofibrillation and reduce the energy required for the mechanical processing [30].
Research has combined various pretreatment methods with mechanical fibrillation techniques [26,31–34]. Chemical modifications (such as adding negatively charged groups to the microfibril surface) have garnered significant interest, including carboxymethylation [35] and TEMPO-mediated oxidation [36,37]. These approaches are expected to produce nanocellulose fibril (NFC) systems with smaller particle size distributions due to their high loadings compared to other pretreatment processes [38,39]. Recently, ultrasonic techniques have also been employed to extract cellulose nanofibers, focusing on their effects on breaking polysaccharide bonds [40,41]. Nanocellulose fibers (NCFs) are long bundles of cellulose chains held together laterally by hydrogen bonds between adjacent polymers. Their production and use have attracted growing industrial interest due to their high specific strength and stiffness, biodegradability, reproducibility, and biocompatibility [42,43].
The objective of this study was the preparation and characterization of pulp from “tacuara” (G. trinii) and bamboo (G. angustifolia) and the manufacture and characterization of a high-value product in the framework of the biorefinery, such as nanocellulose. The findings of this study are crucial for evaluating the potential of both bamboo species as sources of high-value products within a biorefinery framework. The viscosity of nanocellulose aqueous suspensions partially depends on nanofibrils’ size and shape, which affects their preparation, processing, and blending with other materials, having substantial implications for industrial operations and potential applications.
Two different four-year-old Guadua species were used as raw material in this study: G. trinii and G. angustifolia. G. trinii was locally collected and provided by IMAM-FCF (Eldorado, Argentina), whereas G. angustifolia was supplied by the Círculo del Bambú (UNALM, Perú). Both bamboo species were chipped and screened by size.
2.2 Hydrothermal Treatment and Soda-AQ Pulping
Previous work [44,45] details the chemical characterization of Guadua species. Fig. 1 shows the schematic process for obtaining autohydrolysis-pretreated (SHP) pulp, unpretreated soda-AQ (SP) pulp, and nanocellulose from both species.
Figure 1: The schematic process for nanocelluose production. SP: pulps obtained by conventional soda-AQ pulping; HSP: pulps obtained by hydrothermal pretreatment followed by soda-AQ pulping (ods: on oven-dry Guadua sample, odp: on oven-dry pulp). T: temperature, t: time, C: consistency, L/S ratio: liquid/solid ratio
Guadua soda-AQ pulps were obtained by (i) a conventional soda-AQ pulping (SP) and (ii) a sequential fractionation based on the biorefinery concept by hydrothermal pretreatment, to extract the hemicelluloses, followed by soda-AQ pulping (HSP). A discontinuous digester of 7 liters of capacity (MK type) with automatic programmable time, temperature controller, and indirect heating was used to perform both treatments. The solid-liquid ratios for the pretreated and unpretreated chips were 1:4 and 1:3, respectively. The SP y HSP yields (%, g dry pulp/g dry Guadua) were obtained considering the involved treatments and reject (shives and large particles from the screening of pulp suspensions, Somerville screen, slots: 0.15 mm).
The production of nanocellulose was carried out with a chemical pretreatment (oxidation by TEMPO reagent). TEMPO oxidation pretreatment was performed with 10 grams of dry pulp, 5 moles of NaClO (167 mL, NaClO ≈ 33.4 g L−1), 10% NaBr, and 1.6% TEMPO. This treatment was carried out at 1% consistency in an agitated medium at 25°C with the previous dispersing of the NaBr and TEMPO reagents in distilled water, then pulp was added. NaOH was used as a medium for the reaction to be maintained at a pH between 10 and 10.5. The TEMPO-oxidized pulp was washed three times with two liters of water. Each pulp sample was passed 10 times through the colloid mill (CMX-65 Model, CRYMA-Metalúrgica Pardo, Buenos Aires, Argentina) of 25 L maximum capacity with a recirculation system, at 3.000 rpm (50 Hz), which is shown in Fig. 2.
Figure 2: Colloid mill (CMX-65 model, CRYMA) used for nanofibrillation treatment
2.4 Characterization of Pulp and Nanocellulose
WRV test was carried out according to SCAN-C 62:00, with a centrifugation at 4000 rpm, at room temperature for 15 min. The average fiber length was determined using the Bauer McNett fiber classifier with sieves of 30, 50, 100, and 200 mesh (TAPPI T233 cm-15). The chemical characterization of the pulps involved the following analytical techniques: α, β, and γ cellulose content (TAPPI T203 cm-99). The kappa number was used to measure the residual lignin content (TAPPI T236). HPLC liquid chromatography was used to determine structural carbohydrates, using an AMINEX-HPX87H (BIO-RAD) column with refractive index detectors and diode array based on “Determination of Structural Carbohydrates and Lignin in Biomass” NREL/TP-510-42618. Intrinsic viscosity and viscosimetric average degree of polymerization (DPV) in cupriethylenediamine were determined according to ISO 5351/1–1981 “Cellulose in dilute solutions–Determination of limiting viscosity number–Part 1: Methods in cupri-ethylene-diamine (CED) solution”. The dynamic viscosity was obtained using the TAPPI T230 om-94, and the intrinsic viscosity following the ISO 5351/1-1981. The crystallinity of pulps was examined by X-ray diffraction (DRX) in a PANalytical Empyrean X-ray diffractometer at 40 kV, 45 mA (range 2θ = 0–100°). The crystallinity index (IC) was calculated using the Segal method [44].
Carboxyl group content in nanocellulose samples was determined using the conductometric titration method with 0.01 N NaOH (Carboxyl content of pulp, TAPPI-T237 cm-22). The viscosity was measured with a digital vane viscometer with a temperature sensor at 25°C. 100 mL of suspension at 0.3% consistency was prepared for each species with and without hydrothermal treatment. Each sample was shaken for 60 min at 500 revolutions to homogenize. Each measurement was performed in duplicate [45].
The chemical composition of Guadua species was determined in previous work [46,47]. The chemical composition of G. trinii was 65.6% of carbohydrate (40.9% of glucans, 21.1% of xylans, 0.63% of arabinans, 3.03% of acetyl groups), 23.9% of lignin, 8.67% of extractives, and 4.58% of ashes. G. angustifolia contained 63.8% of carbohydrates (41.3% of glucans, 19.6% of xylans, 0.74% of arabinans, 2.14% of acetyl groups), 25.2% of lignin, 8.55% of extractives, and 4.05% of ashes. These percentages are based on oven-dry materials.
The chemical composition of G. trinii was 65.6% of carbohydrate (40.9% of glucans, 21.1% of xylans, 0.63% of arabinans, 3.03% of acetyl groups), 23.9% of lignin, 8.67% of extractives, and 4.58% of ashes. G. angustifolia contained 63.8% of carbohydrates (41.3% of glucans, 19.6% of xylans, 0.74% of arabinans, 2.14% of acetyl groups), 25.2% of lignin, 8.55% of extractives, and 4.05% of ashes. These percentages are based on oven-dry materials.
The yield and Kappa number of SP and HSP are presented in Table 1. Under the same pulping conditions, G. trinii reached a higher degree of delignification. These differences could be attributed to its slightly lower lignin content, although other factors should also be considered, such as the difference between species, age, and growth factors, among others. The screened yields of the hydrothermal-soda-AQ pulping were similar for both species.
Pulps fiber length distribution (% by weight) was carried out using Bauer McNett equipment and is presented in Table 2. In all cases, the highest percentage of fiber retention occurred in 30 mesh and the lowest in 200 mesh. SP pulp of G. trinii shows the highest percentage of fines (percentage by weight that passed through the 200 mesh), whereas HSP pulp of G. angustifolia presents the lower one. For G. angustifolia, the increase in the fraction retained in the 30 mesh of the SP pulps can be attributed to its higher reject content and Kappa number.
The water retention value (WRV) of the pulps is presented in Table 3. The differences in the WRV values of the pulps with and without pretreatment of both species were not significant.
The contents of α, β, and γ cellulose for both species are also presented in Table 3. The α-cellulose content of the pulp is the undegraded fraction, which is associated with the highest molecular weight. The SP and HSP pulps of both species presented similar α-cellulose contents. However, α-cellulose contents were slightly higher in HSP pulps.
The degraded fraction, β-cellulose, was also similar between pulps, although this content was relatively high in pulps without pretreatment. The γ-cellulose content, a fraction composed mainly of hemicelluloses, was low and similar for all the pulps, varying between 1.12% and 1.66%.
The alpha, beta, and gamma cellulose content of the soda-AQ pulps without pretreatment of both species was similar to that of commercial Eucalyptus ECF kraft pulps. The pretreated soda-AQ pulps presented higher proportions of alpha and beta cellulose, complying with the requirements for dissolving pulps [48]. However, the lignin contents were high, so a purification treatment is needed to remove the residual lignin to achieve the quality specifications for these pulps.
The polymerization degree presented in Table 3 is determined through the intrinsic viscosities of the pulps [49]. The higher DP values for pretreated pulps can be attributed to the low hemicelluloses content because of their relatively short polymer chains. These results indicate that G. trinii pulps, without or with pretreatment, contain longer cellulosic chains than G. angustifolia, which sometimes represents a benefit.
The crystallinity index values of all pulps (shown in Table 3) are high in all samples (>80%). The higher crystallinity index of the pretreated pulps is attributed to the pulps’ low amorphous hemicelluloses content. Therefore, the contribution of cellulose to the crystallinity index is more significant.
Fig. 3 shows the characteristic diffractograms for the pulps of both species with and without pretreatment, representing a typical semi-crystalline material. The peaks were almost identical in all the analyzed samples (22.65°–23.15°).
Figure 3: X-ray diffraction of SP and HSP pulps from (a) G. angustifolia and (b) G. trinii
There is an indirect proportional relationship between pulp yield and cellulose crystallinity [50,51], which is only fulfilled by G. angustifolia. For example, water/ethanol bamboo pulps produced have crystallinity indexes of 52.7% for one hour, 79.4% for two hours, and 80.5% for three hours cooking [49]. The high crystallinity and α-cellulose content of these pulps (with and without pretreatment) demonstrate their potential as raw material for the production of nanocellulose.
3.2 Nanocelulose Characterization
The conditions adopted for nanocellulose production were those already used in the PROCyP to obtain nanofibers from other raw materials (bagasse, eucalyptus, moringa, pine) [45]. All samples were pretreated by TEMPO-mediated oxidation [52], and subsequently, they were nanofibrillated by mechanical treatment in a colloid mill. The obtained nanocelluloses were characterized by the carboxylic group content and the rheology of nanocelluloses aqueous suspensions. In this study, the determination of acid-insoluble lignin or Klason lignin method by TAPPI T222 om-83 of TEMPO-oxidized pulps was not carried out because it is a standardized procedure only applicable to wood and all grades of unbleached pulps (lignin content >1%). Two fundamental considerations restrict the range of applicability of this method in TEMPO-oxidized chemical pulps. (i) Residual lignin has been significantly modified (severe TEMPO-oxidation followed by strongly acidic hydrolysis) to such a degree that its characteristic properties totally or partially disappear. However, it is still capable of yielding a residue after being treated with 72% H2SO4 according to the standardized procedure; this material could have the structural features and reactivity generally recognized as unique to lignin [53]. (ii) “Pseudo-lignin” could be formed from polysaccharides degradation (furfural and 5-hydroxymethylfurfural), which increases with treatment severity. Different studies revealed this new lignin-like structure [54] is detected as lignin in the Klason lignin determination.
The carboxylic group rate of the cellulose nanofiber per gram of dry pulp was obtained by conductometric titration and indicates the TEMPO treatment degree of oxidation [45]. G. angustifolia and G. trinii without hydrothermal treatment have an average carboxylic group rate of 1162.7 and 1293.6 μEq/g, respectively. The same species but without treatment have 895.7 and 978.7 μEq/g, respectively, showing that G. trinii has a higher rate of carboxylic groups than G. angustifolia in both cases. Similarly, in both species, a higher rate of carboxylic groups is obtained in the samples without pretreatment, which shows its negative influence on the carboxylic group rate.
The rheological properties of aqueous suspensions obtained with the TEMPO pretreatment usually depend on the nanofibers interactions and degree of interlacing, which are determined by structural properties such as diameter, length, and aspect ratio (length/width). Shear rate measurements of dilute nanocellulose suspensions are a method to assess aspect ratio. The changes in the specific viscosity as a function of its concentration show two regions: one linear in the diluted regime and the other described by the power law used to explain the non-Newtonian behavior of some fluids (viscosity~concentration) above the critical concentration [55]. The intrinsic viscosity of diluted nanocellulose suspensions can be expressed only as a function of the aspect ratio of the nanofibrils. As the aspect ratio of a nanocellulose increases, it becomes more flexible, and the dispersion has a higher viscosity. In this work, the type of species and the pulping process effect on the “aspect ratio” of the cellulose nanofibers were analyzed by the viscosity of aqueous solutions of soda-AQ pulp TEMPO nanocellulose with and without pretreatment of both Guadua species diluted to 0.3% consistency, in function of the rotation speed (rpm), as shown in Table 4.
Fig. 4 shows that the viscosities were higher for the TEMPO nanocellulose solutions obtained from the soda-AQ pulps without pretreatment for both species, which could indicate that the aspect ratio of the nanofibrils obtained from pretreated pulps, with low hemicelluloses content, was lower. Similar results were observed by other authors [56], who pointed out that the pulps with higher hemicelluloses content showed higher nanofibrillation yields and better aptitude for microfibrils individualization. Although the fibers of G. angustifolia have thinner wall thicknesses than G. trinii [47], which would favor nanofibrillation [56], the viscosity values were lower, possibly due to the higher residual lignin content in pulps.
Figure 4: Viscosity of nanocellulose suspension as a function of the cutting speed for G. angustifolia and G. trinii pulps with and without hydrothermal treatment
Fig. 5 shows the trend line of the correlation between the carboxylic group content generated in the TEMPO oxidation and the nanocellulose suspension viscosity. This correlation is significant and positive (R2 = 97%), which indicates that both samples without pretreatment have better nanofibrillation behavior.
Figure 5: Correlation between carboxylic group rate (µEq/g) and viscosity of nanocellulose suspension in water (mPa.s). The standard deviation is in parentheses
Recent studies showed that the rheological behavior of nanocellulose aqueous suspension depends on the aspect ratio, surface area, and surface hydroxyl and carboxyl group contents. It is reported that high carboxyl group contents significantly affect the suspension properties in terms of viscosity. The fibers-nanofibrils interaction leads to entanglement and adhesive interactions, increasing the viscosity of the suspension [39]. The gel structure of nanocellulose is related to the level of carboxylation. The gel and viscosity behaviors depended on the interaction of nanocellulose due to the entanglement and aggregation greater than electrostatic repulsion. The gel structure and rheological behaviors could be tunable by adjusting the level of carboxylation [57]. The optical aspect of nanocellulose gels and films regarding transparency are shown in Fig. 6.
Figure 6: Optical aspect of nanocellulose gels: HSP (a) and SP (c) pulps from G. angustifolia, and HSP (b) and SP (d) pulps from G. trinii. Optical aspect of films in terms of transparency: HSP (e) and SP (f) pulps from G. angustifolia, and HSP (g) and SP (h) pulps from G. trinii
In nanocellulose suspensions, the nanofibrils form networks at specific concentrations, increasing the viscosity. The carboxyl groups on the TEMPO-oxidized nanocellulose surface facilitate stable colloidal suspensions and gel formation, leading to unique rheological properties. These properties could be suitable for food applications such as thickening, stabilizing, and gelling agents [39]. Its rheological properties are being studied extensively; however, the comparison of viscosity with other studies is complex due to the differences in the surface properties of the nanofibers, and the lack of a complete understanding of the relationship between rheological properties and nanostructure for nanocellulose suspensions [57].
Based on the Kappa number, G. trinii showed better soda-AQ pulping delignification and was less affected by pretreatment. The soda-AQ pulps without pretreatment of both species presented similar α-cellulose contents, higher in pretreated pulps. The crystallinity index of all pulps was high (>80%). In pretreated pulps, it is attributed to their low hemicelluloses content. It is possible to obtain nanocellulose (TEMPO) with all obtained pulps; the effect of the species type and pretreatment on the nanofiber’s thickness distribution is to be analyzed. G. trinii without pretreatment has the highest carboxylic group rate per gram of dry sample. The soda-AQ pulps without pretreatment generated TEMPO nanocellulose suspensions with higher viscosities, indicating a lower aspect ratio of the nanofibrils obtained from low hemicelluloses pulps.
Acknowledgement: The authors thank Círculo de Investigación del Bambú (UNALM), and Programa de Celulosa y Papel (PROCyP-IMAM (UNaM, CONICET).
Funding Statement: The authors received no specific funding for this study.
Author Contributions: The authors confirm contribution to the paper as follows: study conception and design: Agatha E. R. Prado Gárate, María Evangelina Vallejos; data collection: Agatha E. R. Prado Gárate, Fernando E. Felissia; analysis and interpretation of results: Agatha E. R. Prado Gárate, Fernando E. Felissia, María Evangelina Vallejos, María Cristina Area, Teresa Suirezs; draft manuscript preparation: Agatha E. R. Prado Gárate, María Evangelina Vallejos. All authors reviewed the results and approved the final version of the manuscript.
Availability of Data and Materials: Data is available on request from the authors. The data that support this study are available from the corresponding author.
Ethics Approval: Not applicable.
Conflicts of Interest: The authors declare that they have no conflicts of interest to report regarding the present study.
References
1. Area MC, Vallejos ME. Biorrefinerias a partir de recursos lignocelulosicos. 1st ed. Saarbrücken, Alemania: Editorial Académica Española; 2012 (In Spanish). [Google Scholar]
2. Trigo EJ, Mentaberry A, Cap EJ, Zelada A, Villarreal F. El potencial de la bioeconomía y las biorrefinerías en la argentina. Buenos Aires (AR): Ministerio de Ciencia, Tecnología, e Innovación Productiva; 2011. p. 39 (In Spanish). [Google Scholar]
3. Kamm B, Grubber PR, Kamm M. Biorefineries–industrial processes and products. In: Ullmann’s encyclopedia of industrial chemistry. Weinheim, Germany: Wiley; 2007. p. 2006. [Google Scholar]
4. FAO. Análisis del balance de energía derivada de biomasa en argentina-WISDOM argentina. Buenos Aires (AR): Food and Agriculture Organization; 2009. p. 118 (In Spanish). [Google Scholar]
5. Kumar R, Kumar G. Nanocellulose: fascinating and sustainable nanomaterial for papermaking. In: Bhat R, Kumar A, Nguyen T, Sharma S, editors. Nanotechnology in paper and wood engineering. Amsterdam: Elsevier; 2022. p. 389–407. [Google Scholar]
6. Wang Y, Wang Z, Lin Y, Qin Y, He R, Wang M, et al. Nanocellulose from agro-industrial wastes: a review on sources, production, applications, and current challenges. Food Res Int. 2024;192:114741. [Google Scholar] [PubMed]
7. UNALM. Universidad Nacional Agraria La Molina. Internal Reports of the Bamboo Research Circle; 2016 (In Spanish). [Google Scholar]
8. Parodi L. Las Bambúseas Indígenas en la Mesopotamia Argentina. Rev Argent Agron. 1936;3:229–305 (In Spanish). [Google Scholar]
9. Burkart A. Gramíneas : La familia botánica de los pastos In: Flora ilustrada de Entre Ríos. Buenos Aires: INTA; 1969. vol. 2 (In Spanish). [Google Scholar]
10. Nicora E, Rúgolo de Agrasar Z. Los géneros de Gramíneas de América Austral: Argentina, Chile, Uruguay y áreas limítrofes de Bolivia, Paraguay y Brasil. 1st ed. Buenos Aires: Hemisferio Sur; 1987 (In Spanish). Available from: https://unlz.opac.com.ar/pergamo/documento.php?ui=1&recno=39084&id=UNLZ.1.39084. [Accessed 2024]. [Google Scholar]
11. Smith L, Wasshaussen D, Klein R. Gramíneas. In: Reitz R, editor. Flora ilustrada catarinense. Santa Catarina: Herbário “Barbosa Rodrigues” (HBR); 1981. p. 1–435 (In Spanish). [Google Scholar]
12. Kelkar BU, Shukla SR, Nagraik P, Paul BN. Structural bamboo composites: a review of processing, factors affecting properties and recent advances. Adv Bamboo Sci. 2023;3:100026. [Google Scholar]
13. Yu Y, Wang HK, Lu F. Bamboo fibers for composite applications: a mechanical and morphological investigation. J Mater Sci. 2014;6:2559–66. [Google Scholar]
14. Liu Z, Wang H, Hui L. Pulping and papermaking of non-wood fibers. In: Kazi SN, editor. Pulp and paper processes. London: InTech; 2018. [Google Scholar]
15. Abd El-Sayed ES, El-Sakhawy M, El-Sakhawy MA-M. Non-wood fibers as raw material for pulp and paper industry. Nord Pulp Pap Res J. 2020;35:215–30. [Google Scholar]
16. Sjöström E. The structure of wood. In: Sjöström E, editor. Wood chemistry. 2nd ed. San Diego: Academic Press Inc.; 1993. p. 1–20. [Google Scholar]
17. Sjöström E. Chapter 3: wood polysaccharides. In: Sjöström E, editor. Wood chemistry. San Diego: Academic Press Inc; 1993. p. 51–70. [Google Scholar]
18. Mai C, Zhang K. Wood chemistry. In: Mai C, Zhang K, editors. Handbook of wood science and technology. Cham: Springer Handbooks; 2023. p. 179–279. [Google Scholar]
19. Liu M, Hoffmann KG, Geiger T, Nyström G. Production of microfibrillated cellulose fibers and their application in polymeric composites. In: Nanotechnology in paper and wood engineering. Amsterdam: Elsevier; 2022. p. 197–229. [Google Scholar]
20. Channab B-E, El Idrissi A, Essamlali Y, Zahouily M. Nanocellulose: structure, modification, biodegradation and applications in agriculture as slow/controlled release fertilizer, superabsorbent, and crop protection: a review. J Environ Manage. 2024;352:119928. [Google Scholar] [PubMed]
21. Barhoum A, Rastogi VK, Mahur BK, Rastogi A, Abdel-Haleem FM, Samyn P. Nanocelluloses as new generation materials: natural resources, structure-related properties, engineering nanostructures, and technical challenges. Mater Today Chem. 2022;26:101247. [Google Scholar]
22. Kumar S, Ngasainao MR, Sharma D, Sengar M, Gahlot APS, Shukla S, et al. Contemporary nanocellulose-composites: a new paradigm for sensing applications. Carbohydr Polym. 2022;298:120052. [Google Scholar] [PubMed]
23. Norrrahim MNF, Jenol MA, Nurazzi NM, Janudin N, Yasim-Anuar TAT, Ishak KA, et al. Performance evaluation of nanocellulose-reinforced biopolymer composites. In: Synthesizer nature nanofillers polymer composite. Sawston: Elsevier; 2023. p. 273–87. [Google Scholar]
24. Das R, Lindström T, Khan M, Rezaei M, Hsiao BS. Nanocellulose preparation from diverse plant feedstocks, processes, and chemical treatments: a review emphasizing non-woods. BioResources. 2023;19(1):1865–924. [Google Scholar]
25. Palanisamy S, Murugesan TM, Palaniappan M, Santulli C, Ayrilmis N, Alavudeen A. Selection and processing of natural fibers and nanocellulose for biocomposite applications: a brief review. BioResources. 2023;19(1):1789–813. [Google Scholar]
26. Pradhan D, Jaiswal AK, Jaiswal S. Emerging technologies for the production of nanocellulose from lignocellulosic biomass. Carbohydr Polym. 2022;285:119258. [Google Scholar] [PubMed]
27. Ai Y, Zhang L, Cui M, Huang R, Qi W, He Z, et al. Toward cleaner production of nanocellulose: a review and evaluation. Green Chem. 2022;24:6406–34. [Google Scholar]
28. Kong Y, Abitbol T, Yang X. Preparation and properties of nanocellulose. In: Surface modifications of nanocellulose. Amsterdam: Elsevier; 2024. p. 1–42. [Google Scholar]
29. Khalid MY, Al Rashid A, Arif ZU, Ahmed W, Arshad H. Recent advances in nanocellulose-based different biomaterials: types, properties, and emerging applications. J Mater Res Technol. 2021;14:2601–23. [Google Scholar]
30. Clauser NM, Felissia FF, Area MC, Vallejos ME. Technological and economic barriers of industrial-scale production of nanocellulose. In: Green nanomaterials for industrial applications. Amsterdam: Elsevier; 2022. p. 21–39. [Google Scholar]
31. Noremylia MB, Hassan MZ, Ismail Z. Recent advancement in isolation, processing, characterization and applications of emerging nanocellulose: a review. Int J Biol Macromol. 2022;206:954–76. [Google Scholar] [PubMed]
32. Ansari MM, Heo Y, Do K, Ghosh M, Son Y-O. Nanocellulose derived from agricultural biowaste by-products-sustainable synthesis, biocompatibility, biomedical applications, and future perspectives: a review. Carbohydr Polym Technol Appl. 2024;8:100529. [Google Scholar]
33. Azka MA, Adam A, Ridzuan SM, Sapuan SM, Habib A. A review on the enhancement of circular economy aspects focusing on nanocellulose composites. Int J Biol Macromol. 2024;269:132052. [Google Scholar] [PubMed]
34. Hu M, Lv X, Wang Y, Ma L, Zhang Y, Dai H. Recent advance on lignin-containing nanocelluloses: the key role of lignin. Carbohydr Polym. 2024;343:122460. [Google Scholar] [PubMed]
35. Wang J, Wang C, Wang W, Li W, Lou J. Carboxymethylated nanocellulose-based gel polymer electrolyte with a high lithium ion transfer number for flexible lithium-ion batteries application. Chem Eng J. 2022;428:132604. [Google Scholar]
36. Hassan SH, Velayutham TS, Chen YW, Lee HV. TEMPO-oxidized nanocellulose films derived from coconut residues: physicochemical, mechanical and electrical properties. Int J Biol Macromol. 2021;180:392–402. [Google Scholar] [PubMed]
37. Thi Thanh Hop T, Thi Mai D, Duc Cong T, Thi YNT, Duc Loi V, Thi Mai Huong N, et al. A comprehensive study on preparation of nanocellulose from bleached wood pulps by TEMPO-mediated oxidation. Results Chem. 2022;4:100540. [Google Scholar]
38. Masruchin N, Amanda P, Kusumaningrum WB, Suryanegara L, Nuryawan A. Particle size distribution and yield analysis of different charged cellulose nanofibrils obtained by TEMPO-mediated oxidation. IOP Conf Ser Earth Environ Sci. 2020;572:12045. [Google Scholar]
39. Levanič J, Šenk VP, Nadrah P, Poljanšek I, Oven P, Haapala A. Analyzing TEMPO-oxidized cellulose fiber morphology: new insights into optimization of the oxidation process and nanocellulose dispersion quality. ACS Sustain Chem Eng. 2020;8:17752–62. [Google Scholar]
40. Tanaka, Seppanen A, Houni V, Sneck J, Pirkonen A, Biorefinery P. Nanocellulose characterization with mechanical fractionation. Nord Pulp Pap Res J. 2012;27:689–94. [Google Scholar]
41. Zhang QB, Oliveira Vigier MD, Barrault K, Jégou J, Philippe G, Jérome MF. Pretreatment of microcrystalline cellulose by ultrasounds: effect of particle size in the heterogeneously-catalyzed hydrolysis of cellulose to glucose. Green Chemestry. 2013;15:963–9. [Google Scholar]
42. Qi Y, Guo Y, Liza AA, Yang G, Sipponen MH, Guo J, et al. Nanocellulose: a review on preparation routes and applications in functional materials. Cellulose. 2023;30:4115–47. [Google Scholar]
43. Solhi L, Guccini V, Heise K, Solala I, Niinivaara E, Xu W, et al. Understanding nanocellulose-water interactions: turning a detriment into an asset. Chem Rev. 2023;123:1925–2015. [Google Scholar] [PubMed]
44. Segal LC, Martin JA. An empirical method for estimating the degree of crystallinity of native cellulose using the X-ray diffractometer. Text Res J. 1959;29:786–94. [Google Scholar]
45. Ehman N. Nanocelulosa a partir de residuos agro y forestoindustriales. Posadas: Universidad Nacional de Misiones; 2019 (In Spanish). Available from: https://ri.conicet.gov.ar/bitstream/handle/11336/80941/CONICET_Digital_Nro.29e13ccb-f7f1-40cb-aef2-41f29c4000f4_B.pdf?sequence=5&isAllowed=yDoctoraldissertation. [Accessed 2024]. [Google Scholar]
46. Prado Gárate A. Tacuara (Guadua trinii) y Bambú (Guadua angustifolia) como recurso lignocelulósico no tradicional para la obtención de nanocelulosa (Master’s Thesis). Universidad Nacional de Misiones; 2019 (In Spanish). [Google Scholar]
47. Prado Gárate AF, Area F, Suirezs MCT, Vallejo M. Physical, chemical and morphological characterictics of bamboo species Guadua Trinii and Guadua angustifolia and their potential to produce high-value products. Cellul Chem Technol. 2021;55:951–9. [Google Scholar]
48. Batalha L, Colodette J, Gomide J, Barbosa L, Maltha C, Borges F. Dissolving pulp production from bamboo. BioResources. 2012;7:640–51. [Google Scholar]
49. Marx-Figinni M. Significance of the intrinsic viscosity ratio of unsubstituted and nitrated cellulose in different solvents. Die Angew Makromol Chemie. 1978;72:161–71. [Google Scholar]
50. Evans RN, Roick R, Suckling U, Wallis IA. Changes in cellulose crystallinity during kraft pulping. Comparison of infrared, X-ray diffraction and solid state NMR results. Holzforschung. 1995;49:498–504. doi:10.1515/hfsg.1995.49.6.498. [Google Scholar] [CrossRef]
51. Gümüskaya E, Mustafa U, Hüseyin K. The effects of various pulping conditions on crystalline structure of cellulose in cotton linters. Polym Degrad Stab. 2003;81:559–64. doi:10.1016/S0141-3910(03)00157-5. [Google Scholar] [CrossRef]
52. Isogai A, Saito TFH. TEMPO-oxidized cellulose nanofibers. Nanoscale. 2019;3:71–85. doi:10.1039/C0NR00583E. [Google Scholar] [PubMed] [CrossRef]
53. Dence CW. The determination of lignin. In: Lin SY, Dence CW, editors. Methods lignin chem. Berlin, Heidelberg: Springer; 1992. p. 33–61. [Google Scholar]
54. Shinde SD, Meng X, Kumar R, Ragauskas AJ. Recent advances in understanding the pseudo-lignin formation in a lignocellulosic biorefinery. Green Chem. 2018;20:2192–205. doi:10.1039/C8GC00353J. [Google Scholar] [CrossRef]
55. Albornoz G, Andrade A, Pereira M. Study of the relationship between intrinsic viscosity and aspect ratio of cellulose nanofibers suspensions. In: Proceedings of the ABTCP-CIADICYP, 2018; São Paulo, Brazil, ABTCP. p. 2–9. [Google Scholar]
56. Chaker A, Alila S, Mutjé P, Vilar M, Boufi S. Key role of the hemicellulose content and the cell morphology on the nanofibrillation effectiveness of cellulose pulps. Cellulose. 2013;20:2863–75. doi:10.1007/s10570-013-0036-y. [Google Scholar] [CrossRef]
57. Qu R, Wang Y, Li D, Wang L. The study of rheological properties and microstructure of carboxylated nanocellulose as influenced by level of carboxylation. Food Hydrocoll. 2021;121:106985. doi:10.1016/j.foodhyd.2021.106985. [Google Scholar] [CrossRef]
Cite This Article
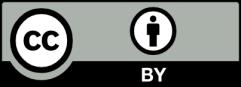
This work is licensed under a Creative Commons Attribution 4.0 International License , which permits unrestricted use, distribution, and reproduction in any medium, provided the original work is properly cited.