Open Access
ARTICLE
Vanillin Based Polymers: VI. Poly(hydrovanilloin-furfural) and Poly(hydrovanilloin-5-hydroxymethylfurfural)
1 Department of Chemistry, Prairie View A&M University, 700 University Drive, Prairie View, TX 77446, USA
2 Center for Energy & Environmental Sustainability, Prairie View A&M University, 700 University Drive, Prairie View, TX 77446, USA
3 Department of Civil and Environmental Engineering, Prairie View A&M University, 700 University Drive, Prairie View, TX 77446, USA
* Corresponding Author: Ananda S. Amarasekara. Email:
(This article belongs to the Special Issue: Recent Advances on Renewable Materials)
Journal of Renewable Materials 2024, 12(9), 1495-1506. https://doi.org/10.32604/jrm.2024.052373
Received 31 March 2024; Accepted 30 July 2024; Issue published 25 September 2024
Abstract
Renewable resources based polymers provides a sustainable alternative to petroleum derived polymeric materials. As a part of our series on synthesis of vanillin based renewable polymers, we report the synthesis of poly(hydrovanilloin-furfural) [poly(HVL-Fur)] and poly(hydrovanilloin–5-hydromethylfurfural) [poly(HVL-5-HMF)]. Vanillin was dimerized to a mixtures of meso/DL-hydrovanilloins with 94% meso product by electrochemical reductive coupling in aqueous sodium hydroxide using lead electrodes in quantitative yield. Then sodium hydroxide catalyzed condensation of hydrovanilloin with furfural in water at 80°C for 72 h was used to synthesize poly(HVL-Fur) with Mw = 8600 g mol−1, PDI = 1.28 in 78% yield. Similarly, condensation of hydrovanilloin with 5-hydroxymethylfurfural at 80°C for 48 h produced poly(HVL-5-HMF) with Mw = 12,100 g mol−1, PDI = 1.27 in 68% yield. poly(HVL-Fur) and poly(HVL-5-HMF) showed similar Tg values of 59°C and 60°C, respectively; whereas melting behaviors are dissimilar with Tm 171°C–173°C and 148°C–182°C, respectively.Graphic Abstract

Keywords
The synthesis of new polymeric materials from renewable resources based monomers is a contemporary research interest with the potential to replace or substitute currently used petrochemical resources based polymers and plastics [1–3]. A wide range of bio-based feedstock chemicals or monomers are under experimentation in this grand scheme and which includes triglycerides or fatty acids from vegetable oils [4,5] cellulose and hemicellulose derived feedstocks such as furfural [6], 5-hydroxymethylfurfural [7], 2,5-furandicarboxylic acid or its derivatives [8,9], levulinic acid [10], 1,3-propanediol [11], fermentation products like lactic acid [12], as well as lignin derived phenolic compounds. Lignin derived phenolics are a relatively less explored class among these new generation of chemicals in comparison to other bio-based feedstocks. The lignin fraction in lignocellulosic biomass can be depolymerized by enzymatic as well as chemical methods to a mixture of phenolic compounds [13,14]. Some of the major lignin derived aromatic feedstocks are vanillin, eugenol, p-coumaryl alcohol, ferulic acid, syringyl alcohol and coniferyl alcohol [15,16]. Among many aromatics and phenols derived from lignin, vanillin (1, Fig. 1) has drawn the most attention due to its abundance among other lignin degradation products as well as the presence of active phenol and aldehyde functional groups in a 1,4-arrangement.
Figure 1: Synthesis of poly(HVL-Fur) (4a) and poly(HVL-5-HMF) (4b). a: electrolysis in 1.25 M aqueous NaOH, 0.164 M vanillin, Pb electrodes, 7.5 V, 3 h, 25°C., b: NaOH, 80°C, 24–72 h
Several research groups have used lignin derived sustainable feedstocks for the preparation of novel polymeric materials [17,18]. Some of the notable lignin based polymer synthesis includes the preparation of thermosetting resins and plastics [19], hydrogels [20], bis(cyanate) ester based polymers [21], vanillic acid polyesters [22,23], and vanillin-oxime derived terpolymer resins [24]. In another example, Mialon and co workers have used dihydroferulic acid synthesized from vanillin for the preparation of polyesters [25]. In this study, Perkin reaction of vanillin with acetic anhydride followed by hydrogenation was used to prepare acetyldihydroferulic acid; then polymerized to poly(dihydroferulic acid), which exhibits thermal properties similar to those of polyethylene terephthalate (PET) [25]. Vanillin can be dimerized by reductive coupling in the aldehyde group to give hydrovanilloin [1,2-bis-(4-hydroxy-3-methoxy-phenyl)-ethane-1,2-diol, 2, Fig. 1] or by oxidative coupling at the 6 position to produce divanillin. The hydrovanilloin synthesis can be carried out by electrochemical reduction discovered by Pearl in 1952 [26] or by a low-valent titanium coupling using TiCl4-Mn [27]. Hydrovanilloin (2) with a symmetrical structure containing reactive alcohol and phenol functional group is an attractive monomer and a potential renewable resource based replacement for toxic bis-phenols and petroleum-derived compounds. In fact, several research groups have seen the potential of this sustainable bis-phenol and reported the use in synthesis of some new generation sustainable polymers [18].
Furfural (3a) and 5-hydroxymethylfurfural (5-HMF, 3b) in Fig. 2 are two well-known biomass derived furan aldehydes that can be prepared by dehydration of monosaccharides obtained in the depolymerization of hemicellulose and cellulose fractions of biomass [28–30]. Catalytic upgrading of these biofurans to chemical feedstocks or monomers and polymerization to produce sustainable polymers is an extensively studied subject [31,32]. However, only a few research groups have studied the potential use of furfural as an alternative to formaldehyde in the synthesis of phenol or lignin formaldehyde resins as well as melamine formaldehyde resins in attempts to avoid the use of formaldehyde due to harmful health effects due to exposure to this volatile chemical [33–35]. Furthermore, the potential health hazards in the use of formaldehyde derived resins as adhesives in wood-based panels in indoor environments have caught attention in recent years promoting the urgent need to develop alternative bio-based phenol resins for limiting volatile organic compounds in the environments [36]. In an effort to find substitutes, Liu et al. have recently reported the synthesis of a resorcinol–furfural thermosetting resin with relatively fast gel formation speed and a curing temperature of about 149°C [35]. In another example, Dongre and co-workers reported the synthesis lignin-furfural resin adhesives from sugar maple wood lignin [37]. In another recent study, Yang and co workers showed methods for the production of renewable phenolic resins from lignin-derived monomers without using formaldehyde as a coupling agent [38]. In this instance the lignin derived vanillin, methyl vanillate, syringaldehyde were first reduced to vanillyl alcohol and syringic alcohol using lithium aluminum hydride. Next, these alcohols were polymerized with furfural using oxalic acid as the catalyst [38]. Furthermore, the authors have reported that these new lignin-derived monomer-furfural resins exhibit excellent adhesion strengths of about 6 MPa and Tg values in the range 107°C–115°C with good thermal stabilities [38].
Figure 2: FT-IR spectra of poly(HVL-Fur) (4a) and poly(HVL-5-HMF) (4b)
Our interest in the development of synthetic methods for new renewable polymeric materials has led us to study the potential of a number of lignocellulosic biomass derived feedstocks. Under this program we have shown that poly(vanillin) can be prepared by electrochemical polymerization of divanillin in aqueous sodium hydroxide solution, where the divanillin was synthesized by a horseradish peroxidase catalyzed dimerization of vanillin [39]. In another example, base catalyzed condensation of hydrovanilloin with aqueous formaldehyde was used to prepare a linear polymer with Mn~10,000 g mol−1, in 91% yield [40]. Furthermore, recently we have shown that hydrovanilloin can be used to prepare poly(hydrovanilloin–urethane)s in two different methods [41]. In the first method, a mixture of hydrovanilloin and diisocyanate was polymerized in DMF using 1,4-diazabicyclo[2,2,2]octane as the catalyst at 60°C. Whereas in the second method diisocyanates were first reacted with polyethylene glycol-400 to give pre-polymers and next reacted with hydrovanilloin at 60°C to produce poly(hydrovanilloin-ethylene glycol-urethane)s. Additionally, we have noted that poly(hydrovanilloin-ethylene glycol-urethane)s from the first method exhibited better thermal stabilities than polymers without polyethylene glycol units [41]. In continuation of these efforts, we have noted that as many researchers have identified the importance of replacing formaldehyde in polymers by less volatile monomers such as furfural due to the toxicity of formaldehyde; nevertheless, most of the furfural-phenol resins reported are prepared using lignin fractions with no well defined structures and this may result in quality control issues during the scaling up due to the lack of standardized physical and chemical properties of lignin. In an attempt to address this concern and to expand the polyphenol-furfural polymer synthesis methods, we have studied the polymerization of furan aldehydes with vanillin derived hydrovanilloin. In this publication we present the synthesis, characterization and relevant physical properties of two new and fully renewable carbon based polymers 4a and 4b prepared from the condensation of furfural (3a) and 5-hydroxymethylfurfural (3b) with hydrovanilloin (2) as shown in Fig. 1.
2.1 Materials and Instrumentation
Vanillin (>97%), 2-furaldehyde (99%), HPLC grade N,N-dimethylformamide (>99.9%). Hydrochloric acid (97%), sodium hydroxide (>99%) and deuterated dimethyl sulfoxide (DMSO-d6, 99.9 atom % D) were purchased from Sigma Aldrich, USA. 5-Hydroxymethylfurfural (>98%) was purchased from Accela ChemBio, Inc., USA. 2-Furaldehyde was distilled before use and all other reagents were used as received. Infrared spectra were recorded on a Thermo Nicolet FT-IR 200 at 1.0 cm−1 resolution. Gel Permeation Chromatography (GPC) of poly(HVL-Fur) (4a) and poly(HVL-5-HMF) (4b) were carried out using EcoSEC Elite HLC-8420 GPC instrument from Tosoh Corporation, Japan. Columns: 2X TSKgel SuperHM-N 6.0 mm I.D. X 15 cm, 3 μm; temperature: 40°C; flow rate: 0.35 mL min−1; solvent: DMF; 1 μL samples with concentration of 2 mg/mL were injected and acquisition time was 30 min. TA instruments TGA 2050 system was used for thermogravimetric analysis. An approximately 5 mg samples in Pt crucibles were used. Thermogravimetric analysis were recorded at a heating rate of 10°C min−1 and all samples were heated in air. A Mettler Toledo DSC 3 STAR system was used to carry out DSC analysis. STARE-E software was used to evaluate the transition temperature peaks. The mass of the samples placed in aluminum pan was approximately 5 mg and all experiments were carried out in air at a heating/cooling rate of 10°C min−1. 1H NMR Spectra were recorded in DMSO-d6, 99.9 atom % D on a Bruker Ascend EVO 400 spectrometer operating at 400 MHz and chemical shifts are given in ppm downfield from TMS (δ = 0.00). The hardness of polymers was measured using a D-type Shore Durometer (ASTM 2240).
2.2 Synthesis of Hydrovanilloin (2)
Hydrovanilloin was synthesized by electrochemical coupling of vanillin dissolved in 1.25 M aqueous NaOH in cathode compartment of the electrochemical cell and 1.25 M aqueous NaOH in anode compartment porous cup as described in our previous work [40].
2.3 Synthesis of Poly(hydrovanilloin-furfural) (4a) and Poly(hydrovanilloin-5-hydroxymethylfurfural) (4b)
A mixture of hydrovanilloin (2) (0.918 g, 3.00 mmol), furfural (3a) or 5-HMF (3b) (3 mmol), sodium hydroxide (0.240 g, 6.00 mmol) and 1.50 mL of deionized water was prepared in a glass vial. The closed vial was sonicated for 5 min to a homogenized solution. Then the mixture was heated at constant temperature in an oil bath at 90°C for 24, 48, and 72 h. At the end of the reaction period, the vials were cooled to room temperature and the contents were acidified by adding 1.0 M aqueous hydrochloric acid. The precipitated polymer was repeatedly washed with deionized water (5 × 10 mL) and the solid collected was dried at 60°C for 24 h, weighed and analyzed using FT-IR, TGA, DSC, GPC and 1H NMR for characterization and tested for hardness using a D-type Shore Durometer (ASTM 2240). The reaction conditions, polymer yields (%), GPC Mw (g mol−1) and PDI (Mw/Mn) data in the synthesis of poly(HVL-Fur) (4a) and poly(HVL-5-HMF) (4b) are shown in Table 1. Polymer yields were calculated using the formula:
Polymer yield (%) = number of moles of polymernumber of moles of hydrovanilloin used × 100
FT-IR and TGA data of polymers 4a and 4b are shown in Figs. 2 and 3. Representative DSC data for 4a (entry 3, Table 1) and 4b (entry 5, Table 1) are shown in Table 2. The cooling/heating DSC curves for these samples are in Figs. A1,2. Durometer Type D hardness data for 4a (entry 3, Table 1) and 4b (entry 5, Table 1) are shown in Table 3. The 400 MHz 1H NMR of the representative polymers recorded in DMSO-d6 are shown in Fig. 4.
Figure 3: Thermogravimetric and derivative thermogravimetric (TG-DTG) analysis plots of poly(HVL-Fur) (4a) and poly(HVL-5-HMF) (4b)
Figure 4: 1H NMR of poly(HVL-Fur) (4a, entry 3, Table 1) and poly(HVL-5-HMF) (4b, entry 5, Table 1) in DMSO d6. *DMSO, **H2O
3.1 Synthesis of Hydrovanilloin (2)
Hydrovanilloin was synthesized by reductive coupling of vanillin by electrolysis of an aqueous sodium hydroxide solution at 7.5 V using Pb electrodes as described in our previous work [40].
3.2 Synthesis of Poly(hydrovanilloin-furfural) (4a) and Poly(hydrovanilloin-5-hydroxymethylfurfural) (4b)
The two hydrovanilloin-furan aldehyde polymers 4a and 4b were prepared from vanillin as shown in the reaction scheme in Fig. 1. The polymer yields (%), GPC Mw (g mol−1) and PDI (Mw/Mn) results for the synthesis of two hydrovanilloin-furan aldehyde polymers 4a and 4b under different reaction conditions are shown in Table 1. Initial experiments were carried out using furfural as the aldehyde and heating at 80°C for 24 h. Then increasing reaction times from 24 to 48 h and then to 72 h resulted in a gradual increase in the weight average molecular weight (Mw) of the polymer, determined by GPC, as shown in entries 1–3 in Table 1. The poly(HVL-Fur) (4a) with the highest Mw value Mw = 8600 g mol−1 was obtained in 78% yield with the reaction carried out for 72 h at 80°C and further increase in reaction time failed to produce significant improvements in the molecular weight or the polymer yield. The results from experiments carried out using 5-hydroxymethylfurfural and hydrovanilloin are shown as entries 4–6 in Table 1. In the 5-HMF reactions, the highest molecular weight polymer with Mw = 12,100 g mol−1 and a PDI of 1.27 was obtained in the experiment carried out for 48 h at 80°C, and further increase in the reaction time to 72 h yielded a polymer with a similar molecular weight.
3.3 Characterization of Poly(hydrovanilloin-furfural) (4a) and Poly(hydrovanilloin-5-hydroxymethylfurfural) (4b)
FT-IR and thermogravimetric-derivative thermogravimetric (TG-DTG) analysis of poly(HVL-Fur) (4a, entry 3, Table 1) and poly(HVL-5-HMF) (4b, entry 5, Table 1) are shown in Figs. 2 and 3, respectively. Differential Scanning Calorimetry (DSC) heating, cooling scans of the same set of highest Mw polymer samples are shown in supplementary material as Figs. A1,2, respectively. The 1H NMR spectra of polymer samples are shown in Fig. 4. The FT-IR spectrum of poly(HVL-Fur) (4a, entry 3, Table 1) showed absorptions at 1595.83, 1510.93 and 1462.33 cm−1 due to C-C stretching in the aromatic rings. The absorption at 2936.34 cm−1 is due to aliphatic C-H bonds in the polymer and this peak is relatively small due to fewer aliphatic bonds in the structure. Strong absorptions at 1266.55 and 1120.50 cm−1 can be assigned to methyl ether C-O stretch and in-plane C-H bending in the aromatic rings. The broad absorption centered at 3372.48 cm−1 is assigned to hydroxyl and phenolic -OH groups in the polymer. In addition no carbonyl absorption was observed around 1700 cm−1, indicating the complete reaction of aldehyde function of the furfural monomer used in the polymerization. Similarly, FT-IR spectrum of poly(HVL-5-HMF) (4b) in Fig. 2 shows absorptions at 1595.66, 1510.69 and 1449.34 cm−1 due to C-C stretching in the aromatic rings. As in 4a, absorptions at 1267.27 and 1120.91 cm−1 can be assigned to methyl ether C-O stretch and in-plane C-H bending in the aromatic rings in polymer 4b. The hydroxyl groups and phenolic -OH groups contribute to the broad absorption band centered at 3354.10 cm−1. The weak absorption at 2935.43 cm−1 can be assigned to a small number of aliphatic C-H bonds in polymer 4b. As in furfural based polymer, no carbonyl absorption was observed around 1700 cm−1, confirming the complete reaction of aldehyde carbonyl groups in 5-hydroxymethylfurfural used in the polymerization.
Thermogravimetric analysis curves and derivative thermogravimetric analysis plots of poly(HVL-Fur) (4a) and poly(HVL-5-HMF) (4b) are shown in Fig. 3. Both polymers show similar thermal degradation profiles, confirming the similarity. TGA of poly(HVL-Fur) (4a) showed three broad peaks in its derivative curve at 310°C, 443°C and 620°C, indicating a three step decomposition, whereas the 5-HMF derived polymer poly(HVL-5-HMF) (4b) showed these decompositions at 312°C, 440°C and 616°C, respectively. The representative polymers prepared by using furfural and 5-hydroxymethylfurfural with the highest weight average molecular weights were analyzed by differential scanning calorimetry (DSC). The glass transition temperature (Tg) and melting temperature (Tm) data for poly(HVL-Fur) (4a, entry 3, Table 1) and poly(HVL-5HMF) (4b, entry 5, Table 1) are shown in Table 2. The heating and cooling DSC curves of theses polymers 4a and 4b are in Figs. A1 and A2. The polymers 4a and 4b showed almost identical glass transition temperatures of 59°C and 60°C, respectively, as both polymers have the same backbone in their chemical structure. However, the two polymers showed somewhat different melting behaviors; the furfural based polymer showed a sharper melting point at 171°C–173°C, whereas the 5-hydroxymethylfurfural based polymer showed a very broad meting range from 148°C to 182°C. This is probably due to additional hydrogen bonding of -CH2-OH group of hydroxymethyl furan moiet with other -OH groups in the polymer chain, allowing several packing arrangements between polymer chains.
1H NMR spectra of poly(HVL-Fur) (4a, entry 3, Table 1) and poly(HVL-5-HMF) (4b, entry 5, Table 1), dissolved in DMSO d6 are shown in Fig. 4. The tall peaks in both spectra at 2.5 ppm are due to residual DMSO and whereas the two similar peaks in these spectra at 3.3 ppm are due to residual water together with hydroxyl groups in polymers. Both polymer spectra showed a broad set of peaks at 3.50–3.90 ppm due to -OCH3 groups and -CH-OH hydrogens in the polymeric structure. Similarly, both spectra show a very broad peaks at 6.20–7.10 ppm region due to the presence of 3 and 5 position aromatic ring hydrogens and also furan ring hydrogens. The very broad bumps in the region of 8.5–9.0 ppm in 4a and 8.8–9.2 ppm in 4b spectra are due to the phenolic -OH groups in respective polymers. The additional broad peak found in the poly(HVL-5-HMF) 4b spectrum at 4.10 ppm is assigned to the -CH2-OH methylene hydrogens on the hydroxymethyl furan pendant group in polymer 4b and this peak is absent in the spectrum of 4a since this polymer was prepared using furfural as the aldehyde monomer.
The hardness of the two polymers were measured in four samples each using a type D Shore durometer according to ASTM 2240, and the results are shown in Table 3. poly(HVL-Fur) (4a) showed a hardness of 43.3 ± 1.3, whereas poly(HVL-5-HMF) (4b) showed a significantly higher hardness of 49.0 ± 2.0. This difference in hardness is most likely due to the extra -CH2-OH group present in the hydroxymethyl furan group in 4b in comparison to 4a, which is capable of additional hydrogen bonding type cross-linking the polymer chains making the polymer 4b harder than 4a.
Sodium hydroxide catalyzed condensation of renewable resources based monomer hydrovanilloin with furfural and 5-hydroxymethylfurfural in water at 80°C can be used to prepare moderate molecular weight polymers poly(HVL-Fur) and poly(HVL-5-HMF) in good yields. The new polymers were characterized using FT-IR, 1H NMR, TGA, DSC and GPC. The highest molecular weight samples of poly(HVL-Fur) and poly(HVL-5-HMF) showed Mw values of 8600 and 12,100 g mol−1, respectively. The two polymers displayed similar Tg values of 59°C and 60°C, due to their identical backbone structure. However, the 5-hydroxymethylfurfural based polymer showed a higher hardness value in comparison to the furfural polymer in a D-type Shore Durometer hardness test, and this is most likely due to the additional -CH2OH groups present in the 5-hydroxymethylfurfural based polymer, capable of additional hydrogen bonding between polymer chains. Furthermore, this polymer showed higher Mw values as well. In conclusion, we have presented a simple two step route to prepare all renewable carbon based lignin derived bis-phenol-aldehyde condensation polymers without using toxic formaldehyde as a monomer. In addition, the use of hydrovanilloin as a polyphenol provides a simple approach to producing renewable polymers with better quality control possibilities in comparison to lignin-furfural resins.
Acknowledgement: None.
Funding Statement: This work is funded by United States National Science Foundation (NSF) Grant HRD-1036593, USDA-NIFA Grant 12684238: Award No. 2020-65209-31474 and United States Department of Energy Grant DE-SC0023345.
Author Contributions: Ananda S. Amarasekara: Writing, review, editing, conceptualization and project management. Gabriel Murillo Morales: Designing laboratory experiments, methodology, investigation, formal analysis, data collection, visualization, validation and review of manuscript. Raghava R. Kommalapati: Funding acquisition and project administration. All authors reviewed the results and approved the final version of the manuscript.
Availability of Data and Materials: No data or materials are available.
Ethics Approval: Not applicable.
Conflicts of Interest: The authors declare that they have no conflicts of interest to report regarding the present study.
References
1. Mohanty AK, Wu F, Mincheva R, Hakkarainen M, Raquez J-M, Mielewski DF, et al. Sustainable polymers. Nature Rev Method Prim. 2022;2(1):46. doi:10.1038/s43586-022-00124-8. [Google Scholar] [CrossRef]
2. Getzler YD, Mathers RT. Sustainable polymers: our evolving understanding. Accounts of Chem Res. 2022;55(14):1869–78. doi:10.1021/acs.accounts.2c00194. [Google Scholar] [PubMed] [CrossRef]
3. Thakur VK, Thakur MK. Handbook of sustainable polymers: processing and applications. Boca Raton, FL: CRC Press; 2016. [Google Scholar]
4. Montero De Espinosa L, Meier MAR. Plant oils: the perfect renewable resource for polymer science?! Europ Polym J. 2011;47(5):837–52. doi:10.1016/j.eurpolymj.2010.11.020. [Google Scholar] [CrossRef]
5. Sharma V, Kundu PP. Addition polymers from natural oils—a review. Progress Polym Sc. 2006;31(11):983–1008. doi:10.1016/j.progpolymsci.2006.09.003. [Google Scholar] [CrossRef]
6. Arora PB, Patel HS, Patel SR. Resacetophenone-furfural polymers. Europ Polym J. 1987;23(4):307–9. doi:10.1016/0014-3057(87)90153-4. [Google Scholar] [CrossRef]
7. Jiang Z, Zeng Y, Hu D, Guo R, Yan K, Luque R. Chemical transformations of 5-hydroxymethylfurfural into highly added value products: present and future. Green Chem. 2023;25(3):871–92. doi:10.1039/D2GC03444A. [Google Scholar] [CrossRef]
8. Gandini A. Furans as offspring of sugars and polysaccharides and progenitors of a family of remarkable polymers: a review of recent progress. Polym Chem. 2010;1(3):245–51. doi:10.1039/B9PY00233B. [Google Scholar] [CrossRef]
9. Amarasekara AS, Nguyen HL, Okorie NC, Jamal MS. A two-step efficient preparation of a renewable dicarboxylic acid monomer 5,5′-[oxybis(methylene)]bis[2-furancarboxylic acid] from d-fructose and its application in polyester synthesis. Green Chem. 2017;19(6):1570–5. doi:10.1039/C6GC03314H. [Google Scholar] [CrossRef]
10. Amarasekara AS, Wiredu B, Grady TL, Obregon RG, Margetić D. Solid acid catalyzed aldol dimerization of levulinic acid for the preparation of C10 renewable fuel and chemical feedstocks. Catal Commun. 2019;124:6–11. doi:10.1016/j.catcom.2019.02.022. [Google Scholar] [CrossRef]
11. Umare SS, Chandure AS, Pandey RA. Synthesis, characterization and biodegradable studies of 1,3-propanediol based polyesters. Polym Degrad Stabil. 2007;92(3):464–79. doi:10.1016/j.polymdegradstab.2006.10.007. [Google Scholar] [CrossRef]
12. Pang X, Zhuang X, Tang Z, Chen X. Polylactic acid (PLA): research, development and industrialization. Biotechnol J. 2010;5(11):1125–36. doi:10.1002/biot.v5.11. [Google Scholar] [CrossRef]
13. Menezes FF, Nascimento VM, Gomes GR, Rocha GJ, Strauss M, Junqueira TL, et al. Depolymerization of enzymatic hydrolysis lignin: review of technologies and opportunities for research. Fuel. 2023;342:127796. doi:10.1016/j.fuel.2023.127796. [Google Scholar] [CrossRef]
14. Jiang L, Wang C-G, Chee PL, Qu C, Fok AZ, Yong FH, et al. Strategies for lignin depolymerization and reconstruction towards functional polymers. Sustain Energ Fuel. 2023;7:2953–73. doi:10.1039/D3SE00173C. [Google Scholar] [CrossRef]
15. Roy R, Rahman MS, Amit TA, Jadhav B. Recent advances in lignin depolymerization techniques: a comparative overview of traditional and greener approaches. Biomass. 2022;2(3):130–54. doi:10.3390/biomass2030009. [Google Scholar] [CrossRef]
16. Sang Y, Chen H, Khalifeh M, Li Y. Catalysis and chemistry of lignin depolymerization in alcohol solvents—a review. Catal Today. 2023;408:168–81. doi:10.1016/j.cattod.2022.06.005. [Google Scholar] [CrossRef]
17. Fache M, Darroman E, Besse V, Auvergne R, Caillol S, Boutevin B. Vanillin, a promising biobased building-block for monomer synthesis. Green Chem. 2014;16(4):1987–98. doi:10.1039/C3GC42613K. [Google Scholar] [CrossRef]
18. Fache M, Boutevin B, Caillol S. Vanillin, a key-intermediate of biobased polymers. Europ Polym J. 2015;68(6):488–502. doi:10.1016/j.eurpolymj.2015.03.050. [Google Scholar] [CrossRef]
19. Harvey BG, Guenthner AJ, Meylemans HA, Haines SRL, Lamison KR, Groshens TJ, et al. Renewable thermosetting resins and thermoplastics from vanillin. Green Chem. 2015;17(2):1249–58. doi:10.1039/C4GC01825G. [Google Scholar] [CrossRef]
20. Mondal AK, Uddin MT, Sujan SMA, Tang Z, Alemu D, Begum HA, et al. Preparation of lignin-based hydrogels, their properties and applications. Int J Biol Macromol. 2023;245(11):125580. doi:10.1016/j.ijbiomac.2023.125580. [Google Scholar] [PubMed] [CrossRef]
21. Meylemans HA, Harvey BG, Reams JT, Guenthner AJ, Cambrea LR, Groshens TJ, et al. Synthesis, characterization, and cure chemistry of renewable bis(cyanate) esters derived from 2-methoxy-4-methylphenol. Biomacromolecules. 2013;14(3):771–80. doi:10.1021/bm3018438. [Google Scholar] [PubMed] [CrossRef]
22. Llevot A, Grau E, Carlotti S, Grelier S, Cramail H. Renewable (semi)aromatic polyesters from symmetrical vanillin-based dimers. Polym Chem. 2015;6(33):6058–66. doi:10.1039/C5PY00824G. [Google Scholar] [CrossRef]
23. Zhang S, Cheng Z, Zeng S, Li G, Xiong J, Ding L, et al. Synthesis and characterization of renewable polyesters based on vanillic acid. J Appl Polym Sci. 2020;137(39):49189. doi:10.1002/app.49189. [Google Scholar] [CrossRef]
24. Chauhana NPS, Jangidb NK, Chaudharyc J, Tomara R, Katariac P. Model-free thermal degradation kinetics of bio-based phenolic resin derived from vanillin oxime. Indian J Chem Sec A-Inorg. 2015;54(2):193–8. [Google Scholar]
25. Mialon L, Pemba AG, Miller SA. Biorenewable polyethylene terephthalate mimics derived from lignin and acetic acid. Green Chem. 2010;12(10):1704–6. doi:10.1039/c0gc00150c. [Google Scholar] [CrossRef]
26. Pearl IA. Reactions of vanillin and its derived compounds. XVI. The synthesis of vanillil. J Am Chem Soc. 1952;74(17):4260–2. doi:10.1021/ja01137a005. [Google Scholar] [CrossRef]
27. Duan XF, Feng JX, Zi GF, Zhang ZB. A convenient synthesis of unsymmetrical pinacols by coupling of structurally similar aromatic aldehydes mediated by low-valent titanium. Synthesis. 2009;2:277–82. [Google Scholar]
28. Zhao Y, Lu K, Xu H, Zhu L, Wang S. A critical review of recent advances in the production of furfural and 5-hydroxymethylfurfural from lignocellulosic biomass through homogeneous catalytic hydrothermal conversion. Renew Sustain Energ Rev. 2021;139:110706. doi:10.1016/j.rser.2021.110706. [Google Scholar] [CrossRef]
29. Kabbour M, Luque R. Furfural as a platform chemical: from production to applications. Biomass, Biofuel Biochem. 2020;283–89. [Google Scholar]
30. Hou Q, Qi X, Zhen M, Qian H, Nie Y, Bai C, et al. Biorefinery roadmap based on catalytic production and upgrading 5-hydroxymethylfurfural. Green Chem. 2021;23(1):119–231. doi:10.1039/D0GC02770G. [Google Scholar] [CrossRef]
31. Xu C, Paone E, Rodríguez-Padrón D, Luque R, Mauriello F. Recent catalytic routes for the preparation and the upgrading of biomass derived furfural and 5-hydroxymethylfurfural. Chem Soc Rev. 2020;49(13):4273–306. doi:10.1039/D0CS00041H. [Google Scholar] [PubMed] [CrossRef]
32. Shen G, Andrioletti B, Queneau Y. Furfural and 5-(hydroxymethyl) furfural: two pivotal intermediates for bio-based chemistry. Curr Opin Green Sustain Chem. 2020;26:100384. doi:10.1016/j.cogsc.2020.100384. [Google Scholar] [CrossRef]
33. Zhang Y, Li N, Chen Z, Ding C, Zheng Q, Xu J, et al. Synthesis of high-water-resistance lignin-phenol resin adhesive with furfural as a crosslinking agent. Polymers. 2020;12(12):2805. doi:10.3390/polym12122805. [Google Scholar] [PubMed] [CrossRef]
34. Koley R, Kasilingam R, Sahoo S, Chattopadhyay S, Bhowmick AK. Synthesis and characterization of phenol furfural resin from Moringa oleifera gum and biophenol and its application in styrene butadiene rubber. Ind Eng Chem Res. 2019;58(40):18519–32. doi:10.1021/acs.iecr.9b03684. [Google Scholar] [CrossRef]
35. Liu J, Xuan D, Chai J, Guo D, Huang Y, Liu S, et al. Synthesis and thermal properties of resorcinol–furfural thermosetting resin. ACS Omega. 2020;5(17):10011–20. doi:10.1021/acsomega.0c00365. [Google Scholar] [PubMed] [CrossRef]
36. Chen Y, Shen J, Wang W, Li L, Zheng D, Qi F, et al. Comparison of the properties of phenolic resin synthesized from different aldehydes and evaluation of the release and health risks of VOCs. Environ Pollut. 2024;344:123419. doi:10.1016/j.envpol.2024.123419. [Google Scholar] [PubMed] [CrossRef]
37. Dongre P, Driscoll M, Amidon T, Bujanovic B. Lignin-furfural based adhesives. Energies. 2015;8(8):7897–914. doi:10.3390/en8087897. [Google Scholar] [CrossRef]
38. Yang W, Jiao L, Wang X, Wu W, Lian H, Dai H. Formaldehyde-free self-polymerization of lignin-derived monomers for synthesis of renewable phenolic resin. Int J Biolog Macromolecul. 2021;166:1312–9. doi:10.1016/j.ijbiomac.2020.11.012. [Google Scholar] [PubMed] [CrossRef]
39. Amarasekara AS, Wiredu B, Razzaq A. Vanillin based polymers: I. An electrochemical route to polyvanillin. Green Chem. 2012;14(9):2395–7. doi:10.1039/c2gc35645g. [Google Scholar] [CrossRef]
40. Amarasekara AS, Hasan MA. Vanillin based polymers: III. Electrochemical dimerization of vanillin revisited and synthesis of hydrovanilloin-formaldehyde polymer. Polym Sci Series B. 2016;58(3):307–12. doi:10.1134/S1560090416030015. [Google Scholar] [CrossRef]
41. Amarasekara AS, Garcia-Obregon R. Vanillin based polymers: V. Poly(hydrovanilloin–urethane). Polym Renew Resour. 2021;12(1–2):35–45. [Google Scholar]
Appendix A.
DSC Heating/Cooling Scans of Poly(hydrovanilloin-furfural) (4a) and Poly(hydrovanilloin-5-hydroxymethylfurfural) (4b).
Figure A1: DSC heating scans of poly(HVL-Fur) (4a, entry 3, Table 1) and poly(HVL-5-HMF) (4b, entry 5, Table 1)
Figure A2: DSC cooling scans of poly(HVL-Fur) (4a, entry 3, Table 1) and poly(HVL-5-HMF) (4b, entry 5, Table 1)
Cite This Article
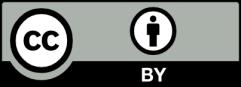
This work is licensed under a Creative Commons Attribution 4.0 International License , which permits unrestricted use, distribution, and reproduction in any medium, provided the original work is properly cited.