Open Access
ARTICLE
Isolation of Microcrystalline Cellulose from Wood and Fabrication of Polylactic Acid (PLA) Based Green Biocomposites
1 Department of Mechanical Engineering, Kalasalingam Academy of Research and Education, Krishnankoil, 626126, India
2 Department of Mechanical Engineering, SSM Institute of Engineering and Technology, Dindigul, 624002, India
3 Department of Engineering, Centre for Engineering Research, School of Physics, Engineering and Computer Science, University of Hertfordshire, Hatfield, AL10 9AB, UK
4 INTI International University, Persiaran Perdana BBN, Nilai, 71800, Malaysia
5 Department of Chemistry, College of Science, King Saud University, P.O. Box 2455, Riyadh, 11451, Kingdom of Saudi Arabia
6 Department of Wood Mechanics and Technology, Faculty of Forestry, Istanbul University–Cerrahpasa, Bahcekoy, Sariyer, Istanbul, 34473, Turkey
* Corresponding Authors: Rajini Nagarajan. Email: ; Nadir Ayrilmis. Email:
(This article belongs to the Special Issue: Environmentally Friendly Wood-Based Composites Based on Sustainable Technologies and Renewable Materials)
Journal of Renewable Materials 2024, 12(8), 1455-1474. https://doi.org/10.32604/jrm.2024.052952
Received 19 April 2024; Accepted 05 July 2024; Issue published 06 September 2024
Abstract
An innovative microcrystalline cellulose (MCC) natural fibre powder-reinforced PLA biocomposite was investigated using the hand lay-up technique. The polymer matrix composite (PMC) samples were prepared by varying the weight percentages (wt.%) of both PLA matrix and MCC reinforcement: pure PLA/100:0, 90:10, 80:20, 70:30, 60:40 and 50:50 wt.%, respectively. From the results obtained, MCC powder, with its impressive aspect ratio, proved to be an ideal reinforcement for the PLA, exhibiting exceptional mechanical properties. It was evident that the 80:20 wt.% biocomposite sample exhibited the maximum improvement in the tensile, flexural, notched impact, compressive strength and hardness by 28.85%, 20.00%, 91.66%, 21.53% and 35.82%, respectively compared to the pure PLA sample. Similarly, during the thermogravimetric analysis (TGA), the same 80:20 wt.% biocomposite sample showed a minimum weight loss of 20% at 400°C, among others. The morphological study using Field Emission Scanning Electron Microscopy (FE-SEM) revealed that the uniform distribution of cellulose reinforcement in the PLA matrix actively improved the mechanical properties of the biocomposites, especially the optimal 80:20 wt.% sample. Importantly, it was evident that the optimal PLA/cellulose biocomposite sample could be a suitable and alternative sustainable, environmentally friendly and biodegradable material for semi/structural applications, replacing synthetic and traditional components.Keywords
Polylactic acid (PLA), a versatile and promising bioplastic, is poised to revolutionize the plastics industry [1]. Its biodegradability, compostability and recyclability under certain conditions make it an environmentally friendly alternative to traditional plastics [2]. While PLA’s versatility is impressive, its low heat threshold, susceptibility to cracking and gas permeability limitations require careful consideration for specific applications [3]. To overcome these limitations, PLA can be blended with additives such as natural fibres to improve its performance and functionality [4]. To overcome these limitations and open up exciting new possibilities for PLA, blending it with additives such as natural fibres can significantly improve its performance and functionality [5]. With dwindling fossil resources and a growing need for sustainability, bio-based polymers derived from renewable resources are becoming a compelling alternative. Both the versatility and sustainability of PLA make it a leading material for diverse applications: packaging, prosthetics, automotive and electronic components, among other innovative materials [6].
PLA has been used as a suitable matrix for several polymer matrix composites (PMCs), especially with cellulose fibres. Fonseca et al. [7] recommended cellulose fibres as a cost-effective and environmentally friendly alternative for reinforcement, improving mechanical properties due to enhanced adhesion with the biodegradable matrix. Crews et al. [8] demonstrated that cellulose improved the thermal stability and mechanical properties of bioplastics. The cellulose was extracted from plant biomass and showed higher thermal stability. Ponsuriyaprakash et al. [9] found that a composite of 20% cellulose fibre and 80% acrylonitrile butadiene styrene (ABS) polymer gave the best properties, with a 37% improvement in tensile behaviour compared to pure ABS. Ponsuriyaprakash et al. [10] suggested that the incorporation of cellulose into ABS composites improved crystallinity, mechanical properties and temperature resistance with a 20% cellulose blend. Ponsuriyaprakash et al. [11] reported that hand layup is widely used in the fabrication of PMCs due to its simplicity. Parameswaranpillai et al. [12] investigated PLA/cellulose nanocomposites which showed significant property improvements over PLA/cellulose fibre composites and the processing techniques tailored the mechanical properties of the nanocomposites.
Liu et al. [13] reported that the incorporation of cellulose nanowhiskers (CNWs) into PLA is expected to provide novel functionalities to electrospun composite nanofibres in the fields of tissue engineering and membranes. Mokhena et al. [14] investigated the potential of cellulose nanomaterials as fillers to stabilise and enhance the behaviour of PLA. PLA is widely used as a replacement for petroleum-based polymers, but its low thermal resistance and heat distortion are relatively low. Yetis et al. [15] found that high lignin microfibrillated cellulose (MFLC) was a cost-effective option for improving the properties of PLA composites, and surface modification of MFLC improved its dispersibility in the PLA matrix. Singh et al. [16] proposed a process for the preparation of biocomposites using PLA and cellulose fibres. Improvements in physicochemical properties and thermal stability were observed. Kasuga et al. [17] investigated PLA composites with hydroxyapatite (HA) fibres for bone plate applications and found that HA fibres improved the modulus of elasticity, which was low in PLA compared to natural bone. Vinyas et al. [18] investigated the use of carbon fibres, nylon glass fibres and a PLA + polyethylene terephthalate glycol (PETG) polymer blend by fused deposition modelling to improve the mechanical behaviour of the PLA composite. Zakaria et al. [19] discussed the potential of PLA to bind with various additives and improve its properties, highlighting its biodegradability and biocompatibility.
A comprehensive review of the intrinsic and functional properties of PLA, including strategies to improve its properties and potential applications, was provided by Farah et al. [20]. Ecker et al. [21] investigated PLA and PLA/wood biocomposites and found that injection moulded samples exhibited higher impact strength after water uptake, while 3D printed samples showed a slight reduction in tensile modulus with higher wood content. Wong et al. [22] reported that the mechanical behaviour of PLA composites was dependent on variations in the physiological state due to the low glass transition temperature. Ruksakulpiwat et al. [23] concluded that injection moulded jute fibre reinforced PLA produced higher modulus and impact strength compared to compression moulded biocomposites. Bahar et al. [24] investigated wood-PLA biocomposites as insulators in the building sector and found that a blend containing 30% wood particles gave good results. Xiang et al. [25] stated that the determination of PLA content in PLA + polybutylene adipate terephthalate (PBAT) blends is challenging due to their overlapping degradation profiles. However, thermogravimetric analysis (TGA) combined with magnesium oxide (MgO) provided a clear solution. Based on the aforementioned literature, it was evident that the present study was an attempt to fill a research gap in green biocomposite technology.
This research focused on an innovative biocomposite material of the PLA polymer reinforced with cellulose fibre powder using a hand lay-up technique. Particularly, the chemical, physical, morphology, mechanical and thermal properties of the cellulose-reinforced PLA composites were extensively investigated by varying the weight percentages (wt.%) of both PLA and cellulose materials in the following respective ratios: 100:0, 90:10, 80:20, 70:30, 60:40 and 50:50 (wt.%). The experiments were carried out by the techniques of chemical analysis, Fourier Transform InfraRed Spectroscopy (FT-IR), X-Ray Diffraction (XRD), Scanning Electron Microscopy (SEM), Tensile, Flexural, Impact, Hardness, Compression tests and Thermogravimetric Analysis (TGA).
This work investigated the properties of materials chosen for biocomposite development. Polylactic acid (PLA) sourced from Green Dot Biopak (City of Gujarat, India) exhibits desirable traits for bio-composites, including low density (1.24 g/cm3), high melting point (170°C), and good mechanical strength (tensile strength: 60 MPa, flexural strength: 108 MPa). FE-SEM analysis confirms a smooth PLA morphology (Fig. 1). Microcrystalline cellulose (MCC), chosen for its potential to enhance bio-composites, is derived from softwood pulp, which was extracted and discussed in detail in the methods part. Dichloromethane, obtained from Sisco Research Laboratory (City of Mumbai, India), acts as a solvent due to its ability to dissolve the PLA and achieve the necessary slurry consistency for composite preparation. In essence, this study lays the groundwork for bio-composite development by characterizing the key materials-PLA, MCC, and dichloromethane. Their properties provide a promising foundation for further research in this area.
Figure 1: Microstructureof PLA
Manufacturing Process of Cellulose
The raw material started as bleached softwood pulp with fluffy white fibres. These fibres are rich in α-cellulose, the desired form for MCC production. The extraction process is shown in Fig. 2a. MCC is a versatile and widely used material with applications in pharmaceuticals, food and cosmetics. It is obtained from wood pulp, mainly from softwoods such as pine, spruce or fir, due to their higher alpha-cellulose content. Furthermore, Fig. 2b shows the microstructure of the cellulose powder analysed by FE-SEM, which appeared with cross-linked fibres. This natural wood-based powder had a unique combination of properties, including a low weight or density of 0.36 g/cm3, a high porosity of 76% and a fine particle size of 109 μm, making it an ideal candidate for reducing the weight and cost of biocomposite materials. It also has a small particle size distribution, which contributed to its ability to improve the thermal and mechanical properties of the biocomposite, exceeding the strength of unfilled polymer matrices [26–28]. Raharjo et al. [29] stated that alterations in molecular weight, crystallinity, distribution, compositions, and temperature during preparation may not affect the mechanical properties of the composite material.
Figure 2: (a) Manufacturing process and (b) microstructure of the cellulose
This section describes the process for creating microcrystalline cellulose (MCC) from wood pulp. It involves several steps: pulping (chemical or mechanical) to isolate cellulose fibers, followed by bleaching for purification. Next, acid hydrolysis refines the cellulose by breaking down amorphous regions and increasing crystallinity [13]. The material is then meticulously washed and neutralized to prevent degradation. Finally, mechanical refining breaks down the cellulose fibers into tiny crystals with a high surface area. The process concludes with drying techniques like spray drying to yield a final product of white, free-flowing MCC powder.
After the chemical composition analysis, the prepared MCC consists 41.7% of α-cellulose, 19.5% of hemicellulose, 17.1% of lignin, 4.3% of wax and 7.3% of ash. The wax contents were removed completely from the fibers after the ethanol-toluene treatment. Cavallo et al. [30] specified that the presence of lignin nanoparticles deliberated the UV-blocking, antioxidant and antibacterial properties to the developed composite material, but it is explicitly at the higher reinforcement percentage composite.
2.3 Fabrication Methodology of PLA/Cellulose Biocomposites
PLA goes through depolymerization while processing, which increments the hydroxyl and carboxyl in PLA. This builds the bond development with cellulose. Additionally, hydrogen bonds between cellulose and PLA further enhance the adhesion, leading to better stress transfer from the matrix to the bio-composite fibers. So, it can potential to be interacted with cellulose’s hydroxyl groups and PLA by shown below in Fig. 3.
Figure 3: Bonding group of PLA and MCC adapted with permission from reference [28]. Copyright ©2020, Springer Publishing
To investigate the effect of varying cellulose content on the PLA bio-composites, as per Fig. 4, the very first step is the conversion of PLA pellets into a slurry form by adding the required amount (based on pouring condition) of dichloromethane solvent. The second step is the addition of developed cellulose powder into PLA slurry by hand lay-up technique (manual mixing) until a visually homogeneous distribution was achieved using stir stick as per different ratios mentioned in Table 1. The third step is the various ratios of blended composites were poured into the respective moulds designed as per ASTM standards (Ponsuriyaprakash et al. [9,10]) and then dried in the room temperature for 24 h.
Figure 4: Fabrication methodology of the PLA/cellulose biocomposite samples
Following ASTM D638 standard (Ponsuriyaprakash et al. [9]), PLA/cellulose biocomposite samples were prepared in specific dimensions (Fig. 5), using a glass mold. The samples were placed on an Instron servo-hydraulic machine for in tensile testing. Precision wedge grips securely held the samples when a controlled load was applied at a constant rate of 5 mm/min. The test continued until the sample fractured, providing valuable data on the ultimate tensile strength of the material. The gauge length was set based on the standard at 150 mm for accuracy.
Figure 5: Tensile test samples with: (a) 0, (b) 10, (c) 20, (d) 30, (e) 40 and (f) 50% reinforcements
PLA/cellulose biocomposite specimens (Fig. 6) were tested using a standardised three-point flexure test was conducted as per ASTM D790 (Ponsuriyaprakash et al. [10]) on a dedicated UTM (Generic Flexure 3PT). The test, conducted at a controlled strain rate of 5 mm/min, provided valuable insight into the ability of the material to withstand flexural forces. The reported average flexural strength and modulus values demonstrated the consistent performance of the biocomposites, highlighting their potential for applications where both strength and flexibility are required.
Figure 6: Flexural test samples with: (a) 0, (b) 10, (c) 20, (d) 30, (e) 40 and (f) 50% reinforcements
To assess the impact strength of the PLA matrix and cellulose-reinforced biocomposites, researchers used an Izod impact test following ASTM D256-07 standard (Ponsuriyaprakash et al. [10]). Six samples (Fig. 7) of standardized dimensions of 63.5 mm × 12.5 mm × 3.0 mm were tested on a dedicated pendulum-type machine (Tinius Olsen Pvt. Ltd., Uttarpradesh, India) at a controlled impact rate of 3.55 m/s, delivering 12.5 J of energy over a distance of 615 mm. The reported average impact strength reflected the consistent performance of the biocomposites under impact conditions, indicating their potential for applications that require resilience to sudden force.
Figure 7: Impact test samples with: (a) 0, (b) 10, (c) 20, (d) 30, (e) 40 and (f) 50% reinforcements
Hardness, a key indicator of resistance of PMCs to deformation, was assessed using Shore D-scale durometer in ASTM D2240 standard (Ponsuriyaprakash et al. [10]). Each biocomposite sample was subjected to five hardness measurements on standardized samples of 30 mm × 30 mm × 6 mm (Fig. 8) at a controlled temperature of 25°C. This approach, employing a reliable durometer (Fasne Test Equipment Pvt. Ltd., Maharastra, India), provided valuable insights for the mechanical behaviors of the biocomposites.
Figure 8: Hardness test samples with: (a) 0, (b) 10, (c) 20, (d) 30, (e) 40 and (f) 50% reinforcements
Another set of the same specimens subjected to compressive loading was evaluated by an ultimate compressive strength (UCS) test in accordance with ASTM D3410 (Ponsuriyaprakash et al. [10]). Six standardised specimens (Fig. 9) were tested on a dedicated UTM (Generic compression) at a predetermined load of 50 kN and a controlled deformation rate of 5 mm/min. The average UCS value demonstrated the remarkable ability of the biocomposites to withstand compressive forces, highlighting their potential for applications requiring structural integrity.
Figure 9: Compression test samples with: (a) 0, (b) 10, (c) 20, (d) 30, (e) 40 and (f) 50% reinforcements
The heat resistivity and weight loss behavior of PLA/cellulose biocomposites were investigated using TGA. Test samples of weights of 10 to 15 mg were examined in platinum TGA pans in the presence of nitrogen. Once dried, the samples were subjected to a heating ramp of 10°C/min from 30°C to 400°C. Subsequently, the test samples were examined with the same heating ramp.
XRD analysis confirmed the successful incorporation of microcrystalline cellulose into the PLA matrix composite. Distinct peaks corresponding to activated carbon were observed in the XRD patterns (Fig. 10). The peak intensity at 2θ = 49° corroborated the presence and homogeneous dispersion of the reinforcement within the PLA matrix. The stronger PLA peak compared to the microcrystalline cellulose peak reflects the relative abundance of each material in the composite.
Figure 10: XRD analysis of PLA/microcrystalline cellulose composites
FT-IR analysis revealed the presence and distribution of cellulose within PLA-MCC composites (0–50 wt.% MCC). Peaks between 1900–3500 cm−1 corresponded to cellulose stretching vibrations, with the characteristic peak at 1650 cm−1 confirming its presence. The intensity of these peaks (including the one at 2950 cm−1) increased with increasing MCC content (Fig. 11), indicating successful dispersion throughout the PLA matrix. Chemical treatment significantly enhanced the peak at 1050 cm−1 and reduced the intensity of cellulose peaks (740, 1050, 1650, 2350, 2950, and 3490 cm−1). This suggests a decrease in detectable cellulose content, potentially improving the mechanical properties of the composite fibers since high cellulose content can be detrimental. Additionally, chemical treatment seems to eliminate these cellulose peaks entirely.
Figure 11: FT-IR analysis of PLA/microcrystalline cellulose composites
The FE-SEM images of low and high presence of cellulose fibres in the PLA matrix is presented in Fig. 12. It was observed that the surface became rougher with increasing wt.% of cellulose, as observed at 10 wt.% compared to 50 wt.% in Fig. 9a,b, respectively. With the highest presence of cellulose, the 50:50 wt.% biocomposite sample, the surface showed an uneven distribution of reinforcement. This phenomenon caused an accumulation of reinforcement, leading to failure. In Fig. 3, the yellow mark indicated the presence and distribution of cellulose reinforcement in the matrix. It also confirmed that the behavior of the presence of cellulose influenced the absorption and deflection of the externally applied load. The different magnification scale values were used in the FE-SEM analysis because it was difficult to identify the location of the bond between matrix and reinforcement in samples with different ratios.
Figure 12: Distribution of cellulose within the samples with (a) 90:10 and (b) 50:50 wt.%
Optimizing the cellulose content was crucial to maximizing the tensile strength of the biocomposites, as shown by the data obtained using a universal testing machine. The strength properties of polymer composites depend on various factors such as the aspect ratio of fillers, the crystallinity degree of the matrix, the optimum filler content and the interfacial bond between the filler and matrix. Fig. 13 shows the remarkable strengthening effect with increasing cellulose content, reaching a maximum at 20 wt.%. However, biocomposite samples above this threshold showed a significant decrease in tensile strength. This may be due to some factors such as low strain, non-uniformity in the structure and potential defects. The above findings provided valuable insights for tailoring cellulose reinforcement strategies to achieve optimal tensile performance in similar biocomposites.
Figure 13: Tensile behavior of neat PLA and PLA/cellulose biocomposite samples
Importantly, the present study on PMCs found that the addition of 20 wt.% cellulose to the PLA matrix significantly increased their tensile strength. This can be associated with improved cellulose-PLA interfacial bonding as observed by microstructural analysis in Fig. 14a–c. FE-SEM images provided visual evidence of this improved bonding and uniform distribution of cellulose fibres within the PLA matrix. When the amount of the MCC was above 20 wt.% in the polymer matrix, the tensile strength gradually decreased. This was mainly attributed to the agglomeration problem of the MCC in the PLA matrix. The results showed that the higher content of the MCC fibres adversely affected the interfacial bond between the filler and PLA matrix. Moreover, a little microvoids were also observed in the morphological analysis (Fig. 14). Similar results were observed in previous studies [26,27].
Figure 14: FE-SEM of post tensile tested biocomposite sample with 80:20 wt.%, depicting: (a) PLA-cellulose bonding interaction, (b) distribution of cellulose and (c) cracked area
The choice of the right cellulose content was crucial to optimise the flexural strength of the PLA/cellulose biocomposites, as shown in Fig. 15. Pure PLA performed relatively poorly in terms of strength and stiffness compared to other biocomposites, except for the sample with the same ratio or highest MCC. It was observed that the addition of MCC significantly increased the flexural strength of the samples compared to the unreinforced or pure PLA sample. The maximum flexural strength was obtained with the biocomposite sample containing 20 wt.% cellulose. However, exceeding this limit can be detrimental as the material became increasingly brittle and its performance under flexural loading was compromised. This implies that design and engineering of PLA-based biocomposites with optimal flexural strength and functionality can be achieved.
Figure 15: Flexural behavior of neat PLA and PLA/cellulose biocomposite samples
From Fig. 16, the microstructural analysis of the optimal biocomposite showed that it had the most improved interfacial bonding among the different samples, which allowed for improved load transfer capability within the biocomposite system. Therefore, this study concluded that the addition of the MCC to PLA played a significant role in enhancing the flexural behaviour of the PMCs. Furthermore, the FE-SEM images showed a clear interfacial bonding reaction and uniform distribution of cellulose within the PLA matrix (Fig. 16).
Figure 16: FE-SEM of post flexural tested PLA/cellulose biocomposite sample with 80:20 wt.%, showing: (a) PLA-cellulose bonding interaction, (b) distribution of cellulose and (c) crack area
The impact strengths of the different biocomposite samples varied significantly with their different reinforcement weight % as shown in Fig. 17. There was a 41.66% increase in impact strength of 17 J/m² for the 10% w/w sample compared to pure PLA. A further increase in cellulose content to 20% gave the highest impact strength of 23 J/m² with a huge significant improvement of 91.66% over pure PLA. This maximum performance can be attributed to the enhanced interfacial bonding together with the uniform distribution of reinforcement, which effectively absorbs energy and prevents crack propagation. However, the addition of more than the threshold of 20 wt.% cellulose resulted in a decrease in impact strength due to the increased brittleness of the biocomposite samples with higher cellulose content.
Figure 17: Impact behavior of neat PLA and PLA/cellulose biocomposite samples
Impact tests revealed a remarkable improvement in load transfer within the PLA/cellulose biocomposites at the optimum 80:20 wt.%, as shown in Fig. 18. This improvement can be attributed to the enhanced bonding between PLA and cellulose as demonstrated by microstructural analysis.
Figure 18: FE-SEM of post impact tested PLA/cellulose biocomposite sample with 80:20 wt.%, depicting: (a) PLA-cellulose bonding interaction, (b) distribution of cellulose and (c) crack path
The hand lay-up process is very important for the production of high-quality biocomposites, as described by the hardness data of cellulose-reinforced PLA biocomposites. Fig. 19 shows that increasing the cellulose content from 10 to 50 wt.% consistently increased the hardness of the materials, unlike other mechanical properties investigated, which later decreased, especially at the same 50:50 wt.% content (Table 1). This remarkable trend not only highlighted the reinforcing effect of cellulose but also established the successful development of biocomposites with minimal pores, voids and uniform fibre distribution, considering their fabrication by hand lay-up process. The 50:50 wt.% biocomposite sample, with its impressive 91 Shore D hardness, showed an increase of 35.82% compared to the pure PLA sample, demonstrating the potential of the hand lay-up method for the production of healthy and high-performance biocomposites.
Figure 19: Hardness behavior of neat PLA and PLA/cellulose biocomposite samples
The compressive strength or bond between cellulose content and PLA of the biocomposites was commendable as shown in Fig. 20. The addition of cellulose up to 20 wt.% indicated its good reinforcing property. This was evident from the 21.54% increase in compressive strength from 65 to 79 MPa compared to pure PLA. This increase supported better interfacial bonding of PLA with cellulose, which promoted efficient load transfer between PLA and cellulose particles. However, the compressive strength of the samples decreased when their cellulose content exceeded the threshold of 20 wt.%, as the stiffness before deformation was compromised.
Figure 20: Compressive strengths of neat PLA and PLA/cellulose biocomposite samples
Overall, the combination of microstructural analysis and FE-SEM imaging from Fig. 21 provided compelling evidence that the incorporation of cellulose in the optimal ratio significantly improved the mechanical properties of the biocomposites. These results can support the development of more efficient and high-performance biomaterials for various applications.
Figure 21: FE-SEM of post compression tested PLA/cellulose biocomposite sample with 80:20 wt.%, showing: (a) PLA-cellulose bonding interaction, (b) distribution of cellulose and (c) crack path
The percentage weight loss for all samples at specific temperatures using TGA is given in Table 2. A key objective of adding cellulose fibre to PLA was to extend the temperature range before significant degradation occurs. The optimum 80:20 wt.% sample showed the lowest weight loss at 400°C (around 20%), indicating an optimum reinforcement content and the strongest PLA-cellulose interactions. The lowest weight loss compared to pure PLA indicated a stabilising effect of cellulose.
Significantly, the higher cellulose content resulted in a faster rate of weight loss. This suggests that the cellulose started to degrade at higher temperatures than the PLA, as shown in Fig. 22. It may have been shielded by the more thermally stable PLA surrounding it. The increased thermal resistance of the 80:20 wt.% sample can be attributed to two factors: (i) the cellulose may have acted as a shield, trapping harmful free radicals generated during PLA degradation and (ii) the fibre network hindered the escape of volatile degradable products.
Figure 22: TGA of neat PLA and PLA/cellulose bio-composite samples
Parameswaranpillai et al. [12] concluded that cellulose nanocomposites reinforced with PLA fabricated using the melt compounding method result in better enhancement in tensile strength, but noted that the processing cost will be higher.
Bhasney et al. [26] determined that commercially available cellulose powder reinforced with PLA and PP using a twin screw extruder blending technique showed improved characterization results in a composite containing 80% PLA, 19.7% PP, and 0.3% MCC. This composite also withstood higher weight loss at a low temperature of 120°C due to its 99.7% polymer content. The present research facilitated comprehension of the overall performance of the extracted and developed MCC fiber powder with PLA composites. Consequently, it was concluded that the overall mechanical and thermal properties of PLA were moderately optimized through the addition of extracted MCC fibre powder.
PLA biocomposite samples reinforced with MCC particles with different wt.% were prepared using the traditional hand lay-up technique and their mechanical (tensile, flexural, notched impact, compression strength and hardness) and thermal (TGA) behaviours were obtained. Microstructural and morphological analyses of the samples were also carried out using FE-SEM. The following conclusions can be drawn from the experimental results obtained:
• XRD and FESEM analyses confirmed a uniform distribution of MCC particles within the PLA matrix and excellent PLA-cellulose interfacial adhesion, especially for the optimum sample.
• FT-IR analysis identified characteristic peaks between 1900 to 3500 cm−1, indicative of cellulose presence within the composite. These peaks were used to assess the impact of chemical treatments on the matrix-fiber interface. Interestingly, the analysis suggests that the chemical reactions not only reduced the matrix and fiber reinforcement materials but also improved their compatibility, potentially hindering cellulose reinforcement separation.
• The optimum PLA/cellulose bio-composite sample with 80:20 wt.% showed maximum mechanical properties. The maximum tensile strength was 67 MPa with an increase of 28.85% compared to neat PLA sample.
• The maximum flexural strength was 102 MPa, with an increase of 20.00% over the neat PLA sample.
• The maximum impact strength was 23 J/m2 with a significant increase of 91.66%. Also, the maximum compressive strength was 79 MPa with 21.53% improvement over the pure PLA sample.
• In general, it was evident that the addition of MCC reinforcement comparatively improved the mechanical strength of the biocomposite samples up to a threshold value of 20 wt.%. However, further addition of MCC, especially at 50 wt.%, decreased the mechanical properties, except for ductility and hardness.
• Therefore, the addition of MCC up to 50 wt.% increased the hardness of the sample from 67 to 91 Shore D with an increase from 5.97% to 35.82%.
• The same biocomposite sample with 80:20 wt.% recorded the lowest weight loss at 400°C (around 20%) during TGA. Therefore, it exhibited most superior thermal stability and degradation properties among the neat PLA and PLA/cellulose biocomposite samples.
• Therefore, the optimal 80:20 wt.% PLA/cellulose biocomposite sample could be used for various engineering applications to benefit from the outstanding properties of the PMC material.
Acknowledgement: We would like to express our gratitude to the Kalasalingam Academy of Research and Education, Krishnankoil, and the SSM Institute of Engineering and Technology, Dindigul, for their technical support. We are also thankful to the technical staff at both research centers for their invaluable assistance.
Funding Statement: The King Saud University authors acknowledge the funding from Researchers Supporting Project Number (RSP2024R355), King Saud University, Riyadh, Saudi Arabia.
Author Contributions: Conception and design: Selwin Maria Sekar, Rajini Nagarajan, Ponsuriyaprakash Selvakumar. Project administration, supervision: Rajini Nagarajan, Selwin Maria Sekar, Faruq Mohammad. Data collection: Selwin Maria Sekar, Rajini Nagarajan. Analysis and interpretation of results: Ponsuriyaprakash Selvakumar, Mohammed Rafi Shaik. Writing: Rajini Nagarajan, Ismail Sikiru Oluwarotimi, Kumar Krishnan, Nadir Ayrilmis. Editing: Faruq Mohammad. All authors reviewed the results and approved the final version of the manuscript.
Availability of Data and Materials: Data available on request from the authors.
Conflicts of Interest: The authors declare that they have no conflicts of interest to report regarding the present study.
References
1. Cuvier DN, Odent J, Delille R, Murariu M, Lauro F, Raquez J, et al. Design of toughened PLA based material for application in structures subjected to severe loading conditions. Part 1. Quasi-static and dynamic tensile tests at ambient temperature. Polym Test. 2014;54:233–43. [Google Scholar]
2. Sujaritjun W, Uawongsuwan P, Pivsa Art W, Hamada H. Mechanical property of surface modified natural fiber reinforced PLA biocomposites. Energy Procedia. 2013;34:664–72. [Google Scholar]
3. Kumar S, Shamprasad MS, Varadarajan YS. Mechanical properties of natural fiber reinforced polylactide composites: a review. IOP Conf Ser: Mater Sci Eng. 2021;1065:12001. [Google Scholar]
4. Kamarudin SH, Abdullah LC, Aung MM, Ratnam CT, Talib ER. A study of mechanical and morphological properties of PLA based biocomposites prepared with EJO vegetable oil-based plasticiser and kenaf fibres. Mater Res Express. 2018;5:085314. [Google Scholar]
5. Kowalczyk M, Piorkowska E, Kulpinski P, Pracella M. Mechanical and thermal properties of PLA composites with cellulose nanofibers and standard size fibers. Compos—A: Appl Sci Manuf. 2011;42:1509–14. [Google Scholar]
6. Graupner N, Mussig J. Cellulose fiber-reinforced PLA versus PP. Int J Polym Sci. 2017;2017:6059183. doi:10.1155/2017/6059183. [Google Scholar] [CrossRef]
7. Fonseca LP, Waldman WR, De Paoli MA. ABS composites with cellulose fibers: towards fiber-matrix adhesion without surface modification. JCOMC. 2021;5:100142. [Google Scholar]
8. Crews K, Huntley C, Cooley D, Phillips B, Curry M. Influence of cellulose on the mechanical and thermal stability of ABS plastic composites. Int J Polym Sci. 2016;2016:9043086. doi:10.1155/2016/9043086. [Google Scholar] [CrossRef]
9. Ponsuriyaprakash S, Udhayakumar P, Pandiyarajan R. Experimental investigation of ABS matrix and cellulose fiber reinforced polymer composite materials. J Nat Fibers. 2022;19:3241–52. [Google Scholar]
10. Ponsuriyaprakash S, Udhayakumar P, Pandiyarajan R. Mechanical characterization and morphological behavior of a novel composite of ABS polymer strengthened by cellulose. J Chin Inst Eng. 2022;45:255–65. [Google Scholar]
11. Ponsuriyaprakash S, Udhayakumar P, Hemalatha A, Sabarish S. Additive manufacturing of customized automotive components using novel cellulose fiber reinforced abs polymer filament. IJIDeM. 2023;17:1869–80. [Google Scholar]
12. Parameswaranpillai J, Siengchin S, Salim NV, George JJ, Poulose A. Polylactic acid-based nanocellulose and cellulose composites. 1st edBoca Raton: CRC Press; 2022. [Google Scholar]
13. Liu W, Dong Y, Liu D, Bai Y, Lu X. Polylactic acid (PLA)/cellulose nanowhiskers (CNWs) composite nanofibers: microstructural and properties analysis. J Compos Sci. 2018;2:4. doi:10.3390/jcs2010004. [Google Scholar] [CrossRef]
14. Mokhena T, Sefadi J, Sadiku E, John M, Mochane M, Mtibe A. Thermoplastic processing of PLA/cellulose nanomaterials composites. Polymers. 2018;10:1363. doi:10.3390/polym10121363. [Google Scholar] [PubMed] [CrossRef]
15. Yetis F, Liu X, Sampson WW, Gong RH. Biodegradation of composites of polylactic acid and microfibrillated lignocellulose. J Polym Environ. 2023;31:698–708. doi:10.1007/s10924-022-02583-2. [Google Scholar] [CrossRef]
16. Singh AA, Genovese ME, Mancini G, Marini L, Athanassiou A. Green processing route for polylactic acid–cellulose fiber biocomposites. Acs Sustain Chem Eng. 2020;8:4128–36. [Google Scholar]
17. Kasuga T, Ota Y, Nogami M, Abe Y. Preparation and mechanical properties of polylactic acid composites containing hydroxyapatite fibers. Biomater. 2000;22:19–23. doi:10.1016/S0142-9612(00)00091-0. [Google Scholar] [PubMed] [CrossRef]
18. Vinyas M, Athul SJ, Harursampath D, Thoi TN. Mechanical characterization of the poly lactic acid (PLA) composites prepared through the fused deposition modelling process. Mater Res Express. 2019;6:105359. doi:10.1088/2053-1591/ab3ff3. [Google Scholar] [CrossRef]
19. Zakaria Z, Islam MS, Hassan A, Haafiz MKM, Arjmandi R, Inuwa IM, et al. Mechanical properties and morphological characterization of pla/chitosan/epoxidized natural rubber composites. Adv Mater Sci Eng. 2013;2013:629092. doi:10.1155/2013/629092. [Google Scholar] [CrossRef]
20. Farah S, Anderson DG, Langer R. Physical and mechanical properties of PLA, and their functions in widespread applications—a comprehensive review. Adv Drug Deliv Rev. 2016;107:367–92. doi:10.1016/j.addr.2016.06.012. [Google Scholar] [PubMed] [CrossRef]
21. Ecker JV, Haider A, Burzic I, Huber A, Eder G, Hild S. Mechanical properties and water absorption behaviour of PLA and PLA/wood composites prepared by 3D printing and injection moulding. Rapid Prototyp J. 2019;25:672–8. doi:10.1108/RPJ-06-2018-0149. [Google Scholar] [CrossRef]
22. Wong S, Wu JS, Leng Y. Mechanical behavior of PLA/HA composite in simulated physiological environment. Key Eng Mater. 2005;288–289:231–6. doi:10.4028/0-87849-967-9. [Google Scholar] [CrossRef]
23. Ruksakulpiwat T, Tonimit P, Kluengsamrong J. Mechanical properties of PLA-jute composites by using natural rubber and epoxidized natural rubber as impact modifiers: effect of molding technique. In: Clean technology. TX: CTSI; 2010. p. 310–3. [Google Scholar]
24. Bahar A, Hamami AE, Benmahiddine F, Belhabib S, Belarbi R, Guessasma S. The thermal and mechanical behaviour of wood-PLA composites processed by additive manufacturing for building insulation. Polymers. 2023;15:3056. [Google Scholar] [PubMed]
25. Xiang S, Feng L, Bian X, Gao L, Chen X. Evaluation of PLA content in PLA/PBAT blends using TGA. Polym Test. 2020;81:106211. [Google Scholar]
26. Bhasney SM, Kumar A, Katiyar V. Microcrystalline cellulose, polylactic acid and polypropylene biocomposites and its morphological, mechanical, thermal and rheological properties. Compos B Eng. 2020;184:107717. [Google Scholar]
27. Ren H, Li S, Gao M, Xing X, Tian Y, Ling Z, et al. Preparation and characterization of microcrystalline cellulose/polylactic acid biocomposite films and its application in Lanzhou lily (Lilium davidii var. unicolor) bulbs preservation. Sustainability. 2023;15:13770. [Google Scholar]
28. Rosli NA, Ahmad I, Anuar FH. Effectiveness of cellulosic Agave angustifolia fibres on the performance of compatibilised poly(lactic acid)-natural rubber blends. Cellulose. 2019;26:3205–18. [Google Scholar]
29. Raharjo WW, Salam R, Ariawan D. The effect of microcrystalline cellulose on the physical, thermal, and mechanical properties of composites based on cantala fiber and recycled high-density polyethylene. J Nat Fibers. 2023;20(2):1. doi:10.1080/15440478.2023.2204454. [Google Scholar] [CrossRef]
30. Cavallo E, He X, Luzi F, Dominici F, Cerrutti P, Bernal C, et al. UV protective, antioxidant, antibacterial and compostable polylactic acid composites containing pristine and chemically modified lignin nanoparticles. Molecules. 2020;26(1):126. doi:10.3390/molecules26010126. [Google Scholar] [PubMed] [CrossRef]
Cite This Article
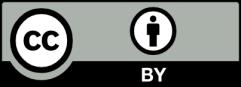
This work is licensed under a Creative Commons Attribution 4.0 International License , which permits unrestricted use, distribution, and reproduction in any medium, provided the original work is properly cited.