Open Access
ARTICLE
Influence of Formulation and Hot-Pressing Conditions on the Performance of Bio-Based Molasses Adhesive for Plywood
1 Research Center for Biomass and Bioproducts, National Research and Innovation Agency, Cibinong, 16911, Indonesia
2 Forest Product Department, Faculty of Forestry and Environment, IPB University, Bogor, 16680, Indonesia
3 Department of Forest Products, Faculty of Forestry, Universitas Sumatera Utara, Medan, 20155, Indonesia
4 Research Collaboration Center for Biomass and Biorefinery, BRIN and Universitas Padjadjaran, Bandung, 40600, Indonesia
5 Department of Agro-Industrial Technology, Universitas Padjadjaran, Bandung, 40600, Indonesia
* Corresponding Authors: Dede Hermawan. Email: ; Muhammad Adly Rahandi Lubis. Email:
Journal of Renewable Materials 2024, 12(8), 1383-1397. https://doi.org/10.32604/jrm.2024.052052
Received 21 March 2024; Accepted 14 June 2024; Issue published 06 September 2024
Abstract
Molasses can serve as a natural adhesive for plywood and particleboard. However, several disadvantages remain, including lower dimensional stability and low bonding strength compared to other adhesives. Therefore, modifications are needed to use molasses as an adhesive for plywood. This research aims to improve bio-based molasses (MO) adhesive for plywood using citric acid (CA) adhesive. In addition, this research aims to analyze the effect of adding citric acid and to investigate the optimum hot-pressing temperature to produce the best quality plywood. In the first stage, the molasses and citric acid were combined in a ratio of 100:0, 75:25, 50:50, 25:75, 0:100 w/w%. Then, the second stage focuses on analyzing the influences of pressing temperature based on an optimum first stage. The research demonstrated that the addition of CA altered the gelation time, solid content, viscosity, and pH of the molasses adhesives. In addition, the thermal properties of molasses adhesives were changed after mixing with citric acid. These phenomena indicate changes in characteristics, such as the curing of adhesive. Overall, the characteristics of plywood showed a steady improvement as the CA ratio increased but revealed a significant decline for the 25:75 MO-CA ratio. By raising the pressing temperature from 180°C to 200°C, the quality of plywood was effectively improved. The plywood that was bonded using adhesives with a 50:50 MO-CA ratio exhibited superior mechanical properties and improved dimensional stability compared to the plywood bonded solely with MO. Furthermore, the optimal mechanical and physical properties resulted in plywood bonded with a 50:50 MO-CA ratio when subjected to a pressing temperature of 200°C. The Thermal and FTIR measurements revealed that CA established ester bonds with both the MO and wood veneers. In conclusion, the mechanical characteristics of plywood were improved, while maintaining its excellent dimensional stability.Graphic Abstract
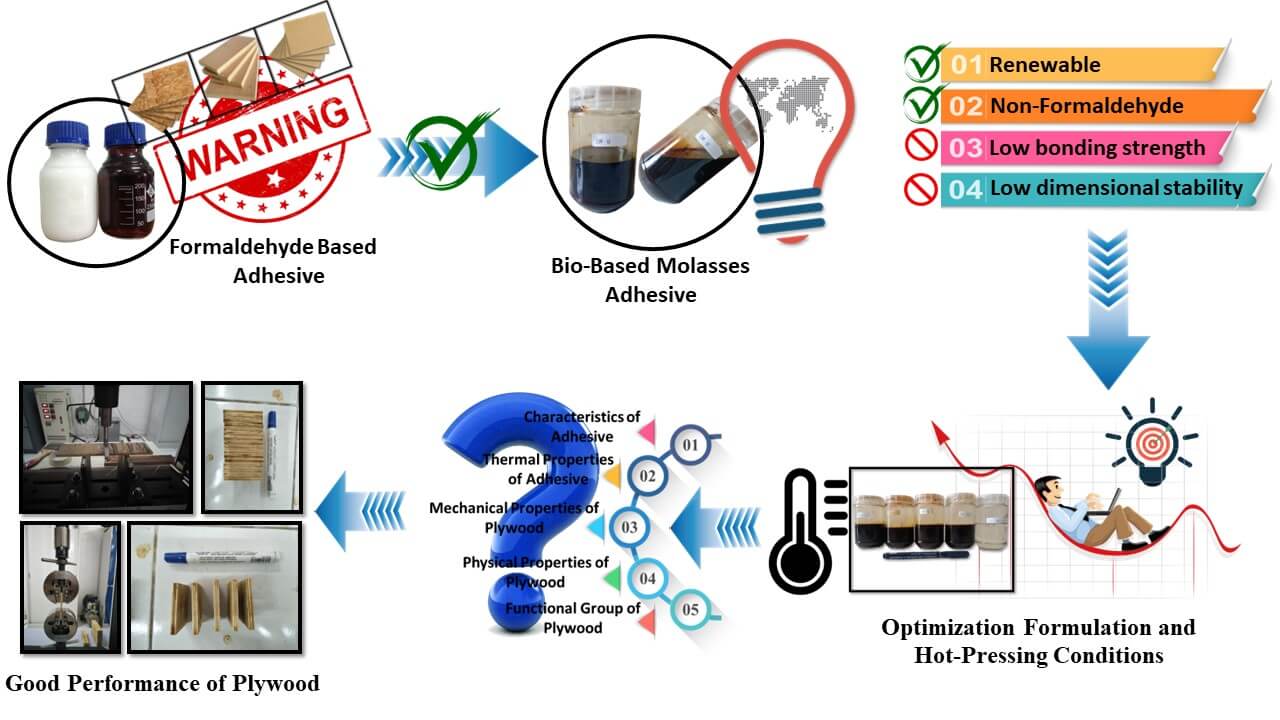
Keywords
Urea Formaldehyde (UF) is an adhesive with several advantages. UF is one of the most economical adhesives [1]. Additionally, UF adhesives have a fast drying time, allowing for an efficient production process [2]. UF also has good adhesion to wood and wood-based materials [3]. UF also produces products with a good appearance compared to other adhesives, making UF widely used in bonding plywood and particleboard [4]. Although UF has many advantages, it also has several disadvantages that must be considered. One of the main disadvantages of UF adhesives is formaldehyde emissions [5]. Increased exposure to formaldehyde can negatively impact human health, causing respiratory problems, eye irritation, and potential cancer if exposed in large amounts [6]. In addition, UF also has lower moisture resistance than several other types of adhesives [7]. UF is also usually unsuitable for outdoor applications where it will be exposed to external weather [8].
To overcome this deficiency, manufacturers and industries often use UF with improved formulations or combine it with certain additional ingredients. In addition, managing formaldehyde emissions is also very important to protect the environment and human health [9]. Adding compounds such as resorcinol or phenol to UF adhesives can improve moisture and heat resistance properties [10]. This results in a UF adhesive that is more suitable for exterior applications or in environments with harsher conditions [11]. In addition, the addition of amines to UF adhesives can improve moisture resistance and reduce formaldehyde emissions [12]. UF adhesives can be modified for outdoor applications by adding UV stabilizers to protect the product from damaging ultraviolet rays [13]. UF adhesives with lower formaldehyde emissions were also developed to meet strict regulations on indoor formaldehyde emissions [14]. Some modifications of UF adhesives typically affect performance properties and cost [15]. Therefore, the modification choice must be according to the particular application’s needs and meet applicable regulatory standards. In some cases, several alternative adhesives, such as natural adhesives based on organic acids, tannins, lignin, chitosan, and polysaccharides, such as molasses, are starting to be developed [16–20].
Molasses is a by-product of the cane sugar production process, which contains sugar, water, minerals, and several organic components [21]. The development of molasses-based adhesives may not be commonplace but could be interesting for certain applications. Molasses as an adhesive has been successfully developed in previous research. Prior investigation has documented that molasses could serve as a natural adhesive for plywood and particleboard [19,22]. However, there are still several disadvantages to developing molasses-based adhesives, such as plywood and particleboard adhesives. These disadvantages include lower dimensional stability and bonding strength compared to other adhesives. Therefore, modifications are needed to use molasses as an adhesive for plywood and particleboard.
Modifications that have the potential to be developed include combining it with citric acid. Previous studies reported that using citric acid improved the quality of particleboard bonded with maltodextrin [23–25]. Previous reports show that citric acid can be used post-modification for low urea formaldehyde adhesive [26]. Citric acid is successfully applied and improves the quality of formaldehyde-free binders based on carbohydrates, lignin, and starch [27–29]. Furthermore, Amirou et al. have demonstrated the feasibility of using citric acid as a natural waterproofing ingredient in wood welding [30]. Therefore, this research combined molasses with citric acid to produce good-quality plywood. This research aims to improve bio-based molasses adhesive for plywood using citric acid adhesive. In addition, this research aims to analyze the effect of adding citric acid and to investigate the optimum hot-pressing temperature to produce the best quality plywood.
A 2 mm thick veneer made from Jabon (Anthocephalus cadamba (Roxb.) Miq) measuring 30 × 30 cm2 was acquired from the Forestry Standardization Center of the Ministry of Environment and Forestry in Bogor, Indonesia. The veneers were dried using an oven at 60°C until they reached less than 5% moisture content. Meanwhile, molasses (MO) and citric acid (CA) were obtained from Limited Liability Company Perkebunan Nusantara and Telaga Sakti Utama, Indonesia. The MO are dissolved in water until they reach a solid content of 59% [19]. Meanwhile, CA was prepared by mixing with water at a temperature of 60°C to reach a concentration of 59% under continuous stirring of 200 rpm for 25 min [31]. The MO and CA were combined in a ratio of 100:0, 75:25, 50:50, 25:75, 0:100 w/w%.
2.2 Characterization of Adhesive
Adhesive solid content testing measures the amount of solids or solid components in an adhesive. Solids content measurement is important in understanding adhesive composition [32]. The test was conducted by drying 2 g of adhesive samples in an oven (Memmert UN55, Berlin, Germany) at 105°C ± 2°C for 3 h.
Adhesive gelatinization testing is used to understand adhesive characteristics during the heating or activation. Gelatination changes an adhesive to cure or melt when exposed to a certain temperature [33] using a gel time meter (Techne GT6, Coleparmer, Washington DC, USA).
Adhesive viscosity testing measures how viscous or fluid an adhesive is at various temperatures or deformation rates. Viscosity measurements are critical in understanding adhesive flow properties and consistency [34]. Adhesive viscosity was analyzed using a Rotational Rheometer (RheolabQC, AntonPaar, Graz, Austria) at 27°C ± 2°C with a shear rate of 500/s.
Adhesive pH testing is important in measuring an adhesive’s acidity or alkalinity level [35]. The test used a pH meter (Orion Star A211, Thermo Scientific, Waltham, MA, USA). The test begins by calibrating using a reference solution with a pH of 4.0, 7.0, and 10.0. After calibration, the pH meter probe is dipped into the adhesive sample, and the results are read on the pH meter screen.
The curing behaviors of adhesives were investigated using thermogravimetric analysis (TGA) (Perkin Elmer Inc., Waltham, MA, USA) and differential scanning calorimetry (DSC) (Perkin Elmer Inc., Waltham, MA, USA). The specimens utilized in the thermal analysis were MO-CA mixed solutions in varied proportions. As previously stated, all specimens were dried at room temperature for one day and pulverized to a mesh size of less than 60. The specimens were freeze-dried for one hour.
TGA is a procedure used to understand the characteristics of adhesives reacting to changes in temperature in the context of weight loss or thermal decomposition. This analysis provides information about the thermal properties and stability of the adhesive under various temperature conditions [36]. TGA (TGA-4000, Perkin Elmer Inc., Waltham, MA, USA) was carried out to determine the thermal stability of the samples. Samples were analyzed at a temperature of 25°C–400°C with a heating rate of 10°C/min under an N2 gas flow of 20 mL/min.
DSC is a method used to understand changes in the thermal properties of adhesives concerning temperature changes [37]. DSC measures the heat capacity, enthalpy, phase transition, and other thermal properties of adhesives. DSC analysis (DSC-4000, Perkin Elmer Inc., Waltham, MA, USA) was carried out to determine the thermal and kinetic processes occurring in the sample. Samples were analyzed at a 25°C–300°C temperature with a heating rate of 10°C/min under an N2 gas flow of 20 mL/min.
The glue spread level and pressing time was determined based on prior research, namely 134 g/m2 and 10 min, respectively [22,31]. The veneers were bonded with adhesives containing various MO:CA ratios (Table 1), and then were dried at 80°C for 12 h to achieve a moisture content of about 10%. Afterward, the veneers were hot-pressed (Shinto, Kyoto, Japan) at different temperatures under 1.3 MPa of hydraulic pressure.
2.4 Determination of Plywood Performance
Following a week of conditioning at room temperature (20°C) and roughly 60% relative humidity, the plywood were evaluated. Using a circular saw, each specimen was cut from the manufactured plywood for testing of its mechanical such as bending characteristics and tensile shear strength (TSS), and physical such as density, moisture content (MC), thickness swelling (TS), and water absorption (WA). The mechanical and physical properties were evaluated according to the Japanese Agricultural Standard No. 233 [38].
Density testing involves measuring the mass of plywood per unit volume, and the results provide information about the density level of the plywood, which is a key factor in determining its strength and stability [39]. Density testing uses samples measuring 7.5 cm × 7.5 cm × 0.6 cm in length, width and thickness. Density determination is expressed as a comparison between the mass and volume of the plywood.
Testing plywood moisture content affects many aspects of plywood performance, including dimensional stability and moisture resistance [40]. Moisture content was tested using samples measuring 7.5 cm × 7.5 cm × 0.6 cm. Moisture content testing was calculated based on the initial and final mass after drying in an oven for 24 h at a temperature of 103°C ± 2°C.
Water absorption testing is important in determining plywood’s resistance to moisture, swelling, and shrinkage [41]. Water absorption was tested using samples of 5 cm × 5 cm × 0.6 cm. Water absorption was obtained from the difference in mass before and after soaking for 24 h.
Plywood thickness swelling testing is performed to understand how much plywood can expand or contract in response to changes in humidity. Thickness swelling testing evaluates the dimensional stability of a plywood product to ensure that the product will maintain dimensions appropriate to a particular application [42]. Thickness swelling was tested using 5 cm × 5 cm × 0.6 cm samples. Thickness swelling is obtained from the difference between the initial thickness before and after soaking for 24 h.
2.4.5 Modulus of Elasticity (MOE) and Rupture (MOR)
Modulus of elasticity (MOE) and rupture (MOR) testing are important tests for measuring the mechanical properties of plywood. MOE measures the stiffness or ability of plywood to return to its original shape after the load is removed. Meanwhile, MOR measures the maximum strength of plywood before it breaks [43]. MOE and MOR tests were carried out using samples measuring 20 cm × 5 cm × 0.6 cm in length, width and thickness. Testing was done using a Universal Testing Machine (UTM, AGS-X series 10 kN, Shimadzu, Tokyo, Japan) with a 10 mm/min loading speed.
2.4.6 Tensile Shear Strength (TSS)
Tensile testing of plywood is an important parameter for evaluating the adhesion between plywood sheets [44]. TSS testing was carried out using samples measuring 7.5 cm × 2.5 cm × 0.6 cm in length, width and thickness. Samples were pulled to maximum load using a Universal Testing Machine (UTM, AGS-X series 10 kN, Shimadzu, Tokyo, Japan) with a 2 mm/min loading speed.
Fourier Transform Infrared Spectroscopy (FTIR) testing of plywood is used to analyze the chemical composition and identify various organic compounds in plywood [45]. The testing process refers to a previous study [31]. The plywood was analyzed for changes in absorption bands at various wave numbers. Analysis was carried out using FTIR (Perkin Elmer Inc., Waltham, MA, USA). Universal Attenuated Total Reflectance (UATR) Accessory sample analysis was performed by placing 2 mg of the sample. All spectra will be recorded at a temperature of 24°C.
Every test’s data was statistically examined. The statistical significance of the variation between components and levels was assessed using the analysis of variance. Duncan’s post hoc test was used to compare the means to determine which groups differed from the others significantly, with a 95% confidence level.
3.1 Characteristics of Adhesive
The research showed that the molasses adhesive’s pH changed after mixing with citric acid (Table 2). The greater the percentage of citric acid added, the lower the pH of the molasses found. The highest pH is found in 100% molasses adhesive (4.40), while the lowest is in 100% citric acid adhesive (0.22). This result was similar to previous studies showing that the citric acid adhesive changes pH after combining with sucrose. Previous study reported the pH of citric acid of 0.9, pH of sucrose of 4.6, and pH 50:50% citric acid and sucrose of 1.2 [46]. Furthermore, molasses adhesive gelatinization changed after mixed with citric acid (Table 2). The greater the percentage of citric acid added, the more the molasses gelatinization will be reduced. The highest gelatinization was found in the 100% citric acid adhesive, while the lowest gelatinization was found in the adhesive with a mixture composition of 50:50% molasses and citric acid.
The viscosity in this study ranged from 11.98–152.69 mPa·s (Table 2). The addition of citric acid reduces the viscosity of molasses. The highest viscosity was found in the 100% molasses adhesive, while the lowest was in the 100% citric acid adhesive. This result was similar to previous studies showing that the citric acid adhesive changes viscosity after combining with sucrose. However, the viscosity in this study was lower [46]. An earlier study reported the viscosity of citric acid of 2 mPa·s, sucrose of 1770 mPa·s, and 50:50% citric acid and sucrose of 1290 mPa·s [46]. In addition, compared to conventional formaldehyde-based adhesives for plywood, like UF resins, which have an average viscosity of 250–400 mPa·s, the average viscosity of adhesive in this study is quite low [47]. In addition, the solids content in this study ranged from 54.93%–58.82% (Table 2). The solids content in this study has the same value as the established solids content target of 59%.
The results of the Thermogravimetric Analysis (TGA) analysis showed that there was a change in weight loss after the molasses was mixed with citric acid. The weight loss of 100% molasses and 100% citric acid at temperatures above 200°C is higher than other mixed compositions (Fig. 1A). This indicates that the mixture of citric acid and molasses mutually influences the thermal degradation of the adhesive and makes the mixture combination more stable. Moreover, Differential Scanning Calorimetry (DSC) analysis of adhesives is very useful in understanding the relationship between the thermal properties of adhesives and the quality of plywood [48]. The DSC results showed a shift in the first endothermic peak after the molasses was mixed with citric acid. The endothermic peak of adhesive with 100% citric acid composition is at 155°C, while the endothermic peak with 100% molasses is at 200°C. After molasses and citric acid were combined, the endothermic peak shifted to a temperature range of 130°C (Fig. 1B). This is, of course, supported by changes in the gelatinization time of the adhesive after molasses is combined with citric acid.
Figure 1: Characteristics thermal of adhesive in this study (A) TGA and (B) DSC
The 50:50 MO-CA ratio types exhibit an endothermic peak at around 130°C, while the MO show an endothermic peak at about 200°C (Fig. 1B). These observations show that adding CA to MO alters the melting point. The melting point of CA is shown by the first endothermic peak, which appears at 150°C, while the decomposition of CA is indicated by the second endothermic peak, which appears at 180°C [49]. Furthermore, the decomposition of MO was indicated by the endothermic peak, which was at about 225°C [19]. Some of the interactions or reactions between MO and CA were anticipated. Consequently, Fig. 1A illustrates how the interaction or reactions between CA and MO, which happened at a low temperature of roughly 130°C to 200°C, led to a more moderate decrease in the weight loss of the specimen of the 50:50 MO-CA ratio types, especially at temperatures higher than 200°C, than the only type.
3.2 Influences Composition of Molasses and Citric Acid
The density and moisture content (MC) of plywood in this study ranged from 0.46–0.53 g/cm3 and 6.76%–7.07%, respectively (Fig. 2A). The highest density was found in 50:50 MO-CA ratio types of plywood. However, the highest MC of plywood was found bonded with MO only, and the lowest was found in plywood bonded with CA only (p > 0.05, Tables 3 and 4). These phenomena are similar to previous studies. The plywood bonded with CA adhesive has good dimensional stability. The carboxyl groups of citric acid reacted with the hydroxyl groups of wood, forming ester linkages and producing dimensional stability [50]. According to Japanese Agricultural Standard No. 233 (JAS 2003), the MC of plywood in this study has met the standard (<12%).
Figure 2: Influence composition of molasses and citric acid on the properties of plywood
Plywood thickness swelling (TS) and water absorption (WA) values with various MO and CA weight ratios are displayed in Fig. 2B. According to the values of the plywood types with a 50:50 MO-CA ratio, the TS and WA values of the plywood declined significantly as the CA ratio increased. However, when the plywood only employed MO, the values sharply increased (p < 0.05, Tables 3 and 4). This indicates that the drop in TS and WA was impacted by adding CA from the intermediate to the high ratio of CA. Otherwise, the plywood varieties with a 50:50 MO-CA ratio exhibited good dimensional stability. The veneer components with hydroxyl groups are pressed at 190°C for 10 min, and CA reacts with them effectively [31]. Furthermore, polysaccharides containing hydroxyl groups, like MO and its thermal derivatives, may react with CA [51]. It is possible that the creation of those chemical bonds prevented the plywood’s TS and WA from developing during the water immersion procedure.
The bending characteristics of plywood at different weight ratios of MO and CA are displayed in Fig. 2C. As the CA ratio increased, the values of the modulus of elasticity (MOE) and modulus of rupture (MOR) increased progressively. The highest MOR and MOE average values (p < 0.05, Tables 3 and 4) were found in plywood with a 50:50 MO-CA ratio, at 60.76 and 6.10 MPa, respectively. These outcomes showed that the bending properties of plywood were significantly enhanced by the addition of CA. In Fig. 2D, the plywood’s tensile shear strength (TSS) values are displayed. Plywood’s TSS strengths grew steadily as the CA ratio increased, reaching a 50:50 MO-CA ratio. Subsequently, they significantly dropped for the plywood just bonded with CA (p < 0.05, Tables 3 and 4). The TSS strength of the 50:50 MO-CA ratio kinds was around twice as high as that of the MO that was employed exclusively with plywood. The binding between veneers was strengthened by the addition of CA. Based on the bending characteristics and TSS findings, as displayed in Fig. 2C,D, plywood variants with a 50:50 MO-CA ratio were found to have exceptional mechanical qualities (0.60 MPa). However, the Japanese Agricultural Standard No. 233 (JAS 2003), which requires a minimum TSS of 0.70 MPa, was not met by the TSS of plywood in this investigation. Thus, the next step in this investigation was to assess the effective pressing time.
3.3 Influences of Pressing Temperatures
The influences of pressing temperature were evaluated using composition 50:50 MO-CA ratio types of adhesives. The plywood density in this study ranged from 0.43–0.53 g/cm3 (Fig. 3A). These density values are not statistically different (p > 0.05, Tables 3 and 4). This result for density is comparable to that of three-layer Jabon plywood bonded with phenol formaldehyde-black liquor (0.47–0.48 g/cm3) [52]. Generally, the pressing temperature affects the density of plywood. Higher pressing temperature results in greater density of plywood due to the thermo-densification effect and curing of the adhesives. This study revealed that plywood with a pressing temperature of 200°C has the highest density (p < 0.05, Tables 5 and 6). The MC of plywood in this study ranged from 5.77%–7.13% (Fig. 3A). The pressing temperature affects the MC of plywood. Plywood with a pressing temperature of 200°C has the lowest MC (p > 0.05, Tables 5 and 6). According to Japanese Agricultural Standard No. 233 (JAS 2003), the MC of plywood in this study has met the standard (<12%).
Figure 3: Influence of pressing temperature on the properties of plywood
The WA of plywood in this study ranged from 58.19%–83.93% (Fig. 3B). The pressing temperature affects the WA of plywood. Plywood with a pressing temperature of 200°C has the lowest WA (p < 0.05, Tables 5 and 6). Furthermore, this WA was less than the plywood bonded with PF adhesive (107.6%) reported in the earlier investigation [52]. The TS of plywood in this research ranges from 4.16%–8.08% (Fig. 3B). The pressing temperature affects the TS of plywood. Plywood with a pressing temperature of 190°C has the lowest TS.
This study’s MOE and MOR of plywood ranged from 5.74–6.80 MPa and 31.17–63.77 MPa, respectively (Fig. 3C). Additionally, the MOR in this investigation was higher than the 43.14 MPa MOR of Jabon LVL bonded with PF resins [53]. The pressing temperature affects the MOE and MOR of plywood. Plywood with a pressing temperature of 200°C has the highest MOE and MOR (p < 0.05, Tables 5 and 6). This study’s TSS of plywood ranged from 0.51–0.79 MPa (Fig. 3D). The pressing temperature affects the TSS of plywood. Plywood with a pressing temperature of 200°C has the highest TSS (p < 0.05, Tables 5 and 6). Furthermore, the plywood in this investigation had a higher TSS than the poplar plywood bonded with citric acid (0.35 MPa) and bonded with sucrose-citric acid 50:50 ratio (0.45 MPa) [46]. However, the TSS result was less than plywood bonded with PF and UF (1.0 MPa) [47,52].
To elucidate the impact of the CA addition on the chemical transformation of plywood, Fourier transform infrared (FTIR) measurements of plywood types with a 50:50 MO-CA ratio were made (Fig. 4). Clear evidence of an absorption peak at about 1727 cm−1 was seen in the plywood types with a 50:50 MO-CA ratio. Because of the carboxyl and C=O ester groups, the peak at 1727 cm−1 was commonly attributed to C=O stretching [54]. There was an extra absorbance intensity peak at 1245 cm−1 in the plywood types with a 50:50 MO-CA ratio. This peak was associated with the ester groups’ C=O stretching vibration band [55].
Figure 4: FTIR spectrum plywood of different composition of molasses and citric acid
The presence of ester groups in the infrared spectra of plywood specimens with a 50:50 MO-CA ratio type suggests that ester linkages were formed by the reaction between the carboxyl groups of CA and the hydroxyl groups of veneer and MO [46]. MO was digested in the mixes of MO-CA solution to yield its corresponding monosaccharides, glucose, and fructose [19]. These monosaccharides are typically found as hydroxyl-group-containing carbohydrates. Essentially, cellulose, hemicellulose, and lignin are the primary sources of hydroxyl groups found in lignocellulose materials [56]. As a result, compared to plywood bonded with MO alone, the plywood glued with the adhesive at a suitable weight ratio of CA to MO seemed to have more ester linkage branches. This resulted from a reaction between the hydroxyl groups of MO and veneers and the carboxyl groups of CA. As a result, ester bonds would form, which would increase the adhesiveness. As a result, applying CA enhanced the plywood’s mechanical and physical qualities.
The research showed that mixing with citric acid changed the molasses adhesive gelation time, pH, solid content, and viscosity. In addition, the thermal properties of molasses adhesives were changed after mixing with citric acid. These phenomena indicate changes in characteristics, such as the curing of adhesive. In general, the properties of plywood increased gradually as the citric acid ratio increased but exceedingly decreased for the 25:75 MO-CA ratio. Meanwhile, the quality of plywood was successfully enhanced by increasing the pressing temperature (180°C to 200°C). The plywood bonded with adhesives at a 50:50 MO-CA ratio had higher mechanical properties and better dimensional stability than those bonded only with MO. In addition, the pressing temperature of 200°C plywood bonded with a 50:50 MO-CA ratio has the best mechanical and physical properties. The Thermal and FTIR analyses demonstrated that CA formed ester linkages with the MO and wood veneers. Ultimately, the mechanical properties of plywood were enhanced, and the plywood still has good dimensional stability.
Acknowledgement: The authors would like to thank National Riset and Innovation Agency for supporting this study.
Funding Statement: This study was funded by Riset dan Inovasi untuk Indonesia Maju (RIIM) National Riset and Innovation Agency (Grant Numbers: 4/IV/KS/05/2023 and 13955/IT3/PT.01.03/P/B/2023) and Research Program by Research Organization of Nanotechnology and Materials, National Research and Innovation Agency (Grant Number 20/III.10/HK/2024).
Author Contributions: Data curation, Jajang Sutiawan, Alifah Syahfitri; methodology, Jajang Sutiawan, Alifah Syahfitri; supervision, Dede Hermawan, Rita Kartika Sari, Sukma Surya Kusumah, Muhammad Adly Rahandi Lubis; writing—original draft, Jajang Sutiawan, Muhammad Adly Rahandi Lubis and Efri Mardawati; writing—review and editing, Jajang Sutiawan, Luthfi Hakim, Muhammad Adly Rahandi Lubis and Efri Mardawati. All authors reviewed the results and approved the final version of the manuscript.
Availability of Data and Materials: The authors confirm that the data supporting the findings of this study are available within the article.
Conflicts of Interest: The authors declare that they have no conflicts of interest to report regarding the present study.
References
1. Khorramabadi LA, Behrooz R, Kazemi S. Effects of nanoclay modification with aminopropyltriethoxysilane (APTES) on the performance of urea-formaldehyde resin adhesives. BioResources. 2023;18(3):5417–34. doi:10.15376/biores.18.3.5417-5434. [Google Scholar] [CrossRef]
2. Duan Z, Hu M, Jiang S, Du G, Zhou X, Li T. Cocuring of epoxidized soybean oil-based wood adhesives and the enhanced bonding performance by plasma treatment of wood surfaces. ACS Sustain Chem Eng. 2022;10(10):3363–72. doi:10.1021/acssuschemeng.2c00130. [Google Scholar] [CrossRef]
3. Bekhta P, Kozak R, Gryc V, Sebera V, Tippner J. Effects of wood particles from deadwood on the properties and formaldehyde emission of particleboards. Polymers. 2022;14(17):3535. doi:10.3390/polym14173535. [Google Scholar] [PubMed] [CrossRef]
4. Park S, Park BD. Crystallinity of low molar ratio urea-formaldehyde resins modified with cellulose nanomaterials. J Korean Wood Sci Technol. 2021;49(2):169–80. doi:10.5658/WOOD.2021.49.2.169. [Google Scholar] [CrossRef]
5. Selakjani PP, Dorieh A, Pizzi A, Shahavi MH, Hasankhah A, Shekarsaraee S, et al. Reducing free formaldehyde emission, improvement of thickness swelling and increasing storage stability of novel medium density fiberboard by urea-formaldehyde adhesive modified by phenol derivatives. Int J Adhes Adhes. 2021;111(5):102962. doi:10.1016/j.ijadhadh.2021.102962. [Google Scholar] [CrossRef]
6. Saito K, Hirabayashi Y, Yamanaka S. Reduction of formaldehyde emission from urea-formaldehyde resin with a small quantity of graphene oxide. RSC Adv. 2021;11(52):32830–36. doi:10.1039/D1RA06717F. [Google Scholar] [PubMed] [CrossRef]
7. Mirski R, Kawaleiczyk J, Dziurka D, Wieruszewski M, Trocinski A. Effects of using bark particles with various dimensions as a filler for urea-formaldehyde resin in plywood. BioResources. 2020;15(1):1692–701. doi:10.15376/biores.15.1.1692-1701. [Google Scholar] [CrossRef]
8. Mahdi HI, Ramlee NN, da Silva Santos DH, Giannakoudakis DA, de Oliveira LH, Selvasembian R, et al. Formaldehyde production using methanol and heterogeneous solid catalysts: a comprehensive review. Mol Catal. 2023;537:112944. doi:10.1016/j.mcat.2023.112944. [Google Scholar] [CrossRef]
9. Liu Y, Zhao A, Sun L, Zhou H, Xia G, Hu Y, et al. Synthesis of microcapsules containing a formaldehyde scavenger for the sustainable control of hazardous chemical release from particleboard. J Hazard Mater. 2023;443(5):130156. doi:10.1016/j.jhazmat.2022.130156. [Google Scholar] [PubMed] [CrossRef]
10. Álvarez-Manuel L, Alegre C, Sebastián D, Eizaguerri A, Napal PF, Lázaro MJ. N-doped carbon xerogels from urea-resorcinol-formaldehyde as carbon matrix for Fe-N-C catalysts for oxygen reduction in fuel cells. Catal Today. 2023;418(5):114067. doi:10.1016/j.cattod.2023.114067. [Google Scholar] [CrossRef]
11. Hogger EM, van Herwijnen HWG, Moser J, Kantner W, Konnerth J. Systematic assessment of wheat extenders in formaldehyde-condensation plywood resins: part II-mechanical properties of plywood panels. J Adhes. 2021;97(14):1404–22. doi:10.1080/00218464.2020.1776123. [Google Scholar] [CrossRef]
12. Kawalerczyk J, Antov P, Dziurka D, Mirski R, Lee SH. The effect of pressing parameters and hardener content on the properties of plywood bonded with propylamine-UF adhesive. Wood Mater Sci Eng. 2023;19(3):710–7. [Google Scholar]
13. Liu C, Li M, Lu B, Huang Y, Zhang Y, Liu P, et al. High-sensitivity crack-based flexible strain sensor with dual hydrogen bond-assisted structure for monitoring tiny human motions and writing behavior. Org Electron. 2021;88:105977. [Google Scholar]
14. Wibowo ES, Park BD, Causin V. Recent advances in urea-formaldehyde resins: cconverting crystalline thermosetting polymers back to amorphous ones. Polym Rev. 2022;62:722–56. [Google Scholar]
15. Yang G, Gong Z, Luo X, Chen L, Shuai L. Bonding wood with uncondensed lignins as adhesives. Nature. 2023;621(7979):511–5. [Google Scholar] [PubMed]
16. Wu S, Cai C, Li F, Tan Z, Dong S. Supramolecular adhesive materials from natural acids and sugars with tough and organic solvent-resistant adhesion. CCS Chem. 2021;3(6):1690–700. [Google Scholar]
17. da Silva Araujo E, Lorenço MS, Zidanes UL, Sousa TB, da Silva Mota G, de Nazaré de Oliveira Reis V, et al. Quantification of the bark Myrcia eximia DC tannins from the amazon rainforest and its application in the formulation of natural adhesives for wood. J Clean Prod. 2021;280(4):124324. doi:10.1016/j.jclepro.2020.124324. [Google Scholar] [CrossRef]
18. Liu J, Li J, Yu F, Zhao XY, Mo MX, Pan JF. In situ forming hydrogel of natural polysaccharides through Schiff base reaction for soft tissue adhesive and hemostasis. Int J Biol Macromol. 2020;147:653–66. doi:10.1016/j.ijbiomac.2020.01.005. [Google Scholar] [PubMed] [CrossRef]
19. Syahfitri A, Hermawan D, Kusumah SS, Ismadi, Lubis MAR, Widyaningrum BA, et al. Conversion of agro-industrial wastes of sorghum bagasse and molasses into lightweight roof tile composite. Biomass Convers Biorefinery. 2024;14(1):1001–15. doi:10.1007/s13399-022-02435-y. [Google Scholar] [CrossRef]
20. Ashori A, Kuzmin A. Effect of chitosan-epoxy ratio in bio-based adhesive on physical and mechanical properties of medium density fiberboards from mixed hardwood fibers. Sci Rep. 2024;14(1):5057. doi:10.1038/s41598-024-55796-x. [Google Scholar] [PubMed] [CrossRef]
21. Mangwanda T, Johnson JB, Mani JS, Jackson S, Chandra S, McKeown T, et al. Processes, challenges and optimisation of rum production from molasses—a contemporary review. Fermentation. 2021;7(1):21. doi:10.3390/fermentation7010021. [Google Scholar] [CrossRef]
22. Sutiawan J, Syahfitri A, Purnomo D, Sudarmanto, Narto, Akbar F, et al. Characterization and application of non-formaldehyde binder based citric acid, maleic acid, and molasses adhesive for plywood composite. Polymers. 2023;15(19):3897. doi:10.3390/polym15193897. [Google Scholar] [PubMed] [CrossRef]
23. Santoso M, Widyorini R, Prayitno TA, Sulistyo J. Bonding performance of maltodextrin and citric acid for particleboard made from nipa fronds. J Korean Wood Sci Technol. 2017;45(4):432–43. [Google Scholar]
24. Castro-Cabado M, Parra-Ruiz FJ, Casado AL, San Román J. Thermal crosslinking of maltodextrin and citric acid. Methodology to control the polycondensation reaction under processing conditions. Polym Polym Compos. 2016;24(8):643–54. [Google Scholar]
25. Widyorini R, Umemura K, Septiano A, Soraya DK, Dewi GK, Nugroho WD. Manufacture and properties of citric acid-bonded composite board made from salacca frond: effects of maltodextrin addition, pressing temperature, and pressing method. BioResources. 2018;13(4):8662–76. [Google Scholar]
26. Kawalerczyk J, Dziurka D, Mirski R, Siuda J. The reduction of adhesive application in plywood manufacturing by using nanocellulose-reinforced urea-formaldehyde resin. J Appl Polym Sci. 2021;138(7):1–9. doi:10.1002/app.49834. [Google Scholar] [CrossRef]
27. Del Menezzi C, Amirou S, Pizzi A, Xi X, Delmotte L. Reactions with wood carbohydrates and lignin of citric acid as a bond promoter of wood veneer panels. Polymers. 2018;10(8):833. doi:10.3390/polym10080833. [Google Scholar] [PubMed] [CrossRef]
28. Li C, Hou D, Lei H, Xi X, Du G, Zhang H, et al. Effective and eco-friendly safe self-antimildew strategy to simultaneously improve the water resistance and bonding strength of starch-based adhesive. Int J Biol Macromol. 2023;248:125889. [Google Scholar] [PubMed]
29. Fehrmann J, Belleville B, Ozarska B, Ismayati M, Dwianto W. Effects of mat composition and pressing time on citric acid-bonded ultra-low-density hemp hurd particleboard. Ind Crops Prod. 2024 Jan 29;210:118070. doi:10.1016/j.indcrop.2024.118070. [Google Scholar] [CrossRef]
30. Amirou S, Pizzi A, Delmotte L. Citric acid as waterproofing additive in butt joints linear wood welding. Eur J Wood Wood Prod. 2017 Jul 1;75(4):651–4. doi:10.1007/s00107-017-1167-x. [Google Scholar] [CrossRef]
31. Sutiawan J, Hermawan D, Massijaya MY, Kusumah SS, Lubis MAR, Marlina R, et al. Influence of different hot-pressing conditions on the performance of eco-friendly jabon plywood bonded with citric acid adhesive. Wood Mater Sci Eng. 2022;17(6):400–9. doi:10.1080/17480272.2021.1884898. [Google Scholar] [CrossRef]
32. Zheng G, Pan A, Xu Y, Zhang X. Preparation of a superior soy protein adhesive with high solid content by enzymatic hydrolysis combined with cross-linking modification. Ind Crops Prod. 2024;213:118446. doi:10.1016/j.indcrop.2024.118446. [Google Scholar] [CrossRef]
33. Hao Y, Yuan C, Deng J, Zheng W, Ji Y, Zhou Q. Injectable self-healing first-aid tissue adhesives with outstanding hemostatic and antibacterial performances for trauma emergency care. ACS Appl Mater Interfaces. 2022;14(14):16006–17. doi:10.1021/acsami.2c00877. [Google Scholar] [PubMed] [CrossRef]
34. Cai L, Chen Y, Lu Z, Wei M, Zhao X, Xie Y, et al. Citric acid/chitosan adhesive with viscosity-controlled for wood bonding through supramolecular self-assembly. Carbohydr Polym. 2024;329(4):121765. doi:10.1016/j.carbpol.2023.121765. [Google Scholar] [PubMed] [CrossRef]
35. He J, Zhang Z, Yang Y, Ren F, Li J, Zhu S, et al. Injectable self-healing adhesive ph-responsive hydrogels accelerate gastric hemostasis and wound healing. Nano-Micro Lett. 2021;13(1):394. doi:10.1007/s40820-020-00585-0. [Google Scholar] [PubMed] [CrossRef]
36. Sudarmanto, Juwono AL, Subyakto, Budiman I, Lubis MAR, Kusumah SS, et al. Effect of cold-water treatment and hydrothermal carbonization of oil-palm-trunk fibers on compatibility with cement for the preparation of cement-bonded particleboard. Wood Mater Sci Eng. 2022;17(6):979–88. doi:10.1080/17480272.2021.1983871. [Google Scholar] [CrossRef]
37. Park BD, Kang EC, Park JY. Differential scanning calorimetry of urea-formaldehyde adhesive resins, synthesized under different pH conditions. J Appl Polym Sci. 2006;100(1):422–27. doi:10.1002/app.23164. [Google Scholar] [CrossRef]
38. Japanese Agricultural Standard. Japanese Agricultural Standard for Plywood. Japanese Agric Stand Plywood. 2008;(233):1–78. [Google Scholar]
39. Bekhta P, Sedliačik J. Environmentally-friendly high-density polyethylene-bonded plywood panels. Polymers. 2019;11(7):1166. doi:10.3390/polym11071166. [Google Scholar] [PubMed] [CrossRef]
40. Wang T, Wang Y, Crocetti R, Wålinder M. Influence of face grain angle, size, and moisture content on the edgewise bending strength and stiffness of birch plywood. Mater Des. 2022;223(4):111227. doi:10.1016/j.matdes.2022.111227. [Google Scholar] [CrossRef]
41. Bekhta P, Pizzi A, Kusniak I, Bekhta N, Chernetskyi O, Nuryawan A. A comparative study of several properties of plywood bonded with virgin and recycled LDPE films. Materials. 2022;15(14):4942. doi:10.3390/ma15144942. [Google Scholar] [PubMed] [CrossRef]
42. Bekhta P, Sedliačik J, Bekhta N. Effect of veneer-drying temperature on selected properties and formaldehyde emission of birch plywood. Polymers 2020;12(3):593. doi:10.3390/polym12030593. [Google Scholar] [PubMed] [CrossRef]
43. Karri R, Lappalainen R, Tomppo L, Yadav R. Bond quality of poplar plywood reinforced with hemp fibers and lignin-phenolic adhesives. Compos Part C: Open Access. 2022;9:100299. [Google Scholar]
44. Younesi-Kordkheili H, Pizzi A. Improving the properties of urea-lignin-glyoxal resin as a wood adhesive by small addition of epoxy. Int J Adhes Adhes. 2020;102:102681. [Google Scholar]
45. Mirski R, Kawalerczyk J, Dziurka D, Siuda J, Wieruszewski M. The application of oak bark powder as a filler for melamine-urea-formaldehyde adhesive in plywood manufacturing. Forests. 2020;11(12):1249. [Google Scholar]
46. Sun S, Zhao Z, Umemura K. Further exploration of sucrose-citric acid adhesive: synthesis and application on plywood. Polymers. 2019;11(11):1875. [Google Scholar] [PubMed]
47. Lubis MAR, Park BD, Hong MK. Tailoring of oxidized starch’s adhesion using crosslinker and adhesion promotor for the recycling of fiberboards. J Appl Polym Sci. 2019;136(38):1–10. doi:10.1002/app.47966. [Google Scholar] [CrossRef]
48. Saražin J, Poljanšek I, Pizzi A, Šernek M. Curing kinetics of tannin and lignin biobased adhesives determined by DSC and ABES. J Renew Mater. 2022;10(8):1–15. [Google Scholar]
49. Chi Y, Maitland E, Pascall MA. The effect of citric acid concentrations on the mechanical, thermal, and structural properties of starch edible films. Int J Food Sci Technol. 2024;59(3):1801–13. [Google Scholar]
50. Gebresas GA, Szabó T, Marossy K. A comparative study of carboxylic acids on the cross-linking potential of corn starch films. J Mol Struct. 2023;1277:134886. [Google Scholar]
51. Santoso M, Widyorini R, Prayitno TA, Sulistyo J, Hamidah N. Effect of pressing temperatures on bonding properties of sucrose-citric acid for nipa palm fronds particleboard. Wood Res. 2020;65(5):747–56. [Google Scholar]
52. Arias A, González-García S, González-Rodríguez S, Feijoo G, Moreira MT. Cradle-to-gate life cycle assessment of bio-adhesives for the wood panel industry. a comparison with petrochemical alternatives. Sci Total Environ. 2020;738(8):140357. doi:10.1016/j.scitotenv.2020.140357. [Google Scholar] [PubMed] [CrossRef]
53. Sutrisno, Alamsyah EM, Sulistyawati E, Suheri A. The potential use of wood waste ash nanofiller for improvement of laminated veneer lumber production made from Jabon (Anthocephalus cadamba). J Indian Acad Wood Sci. 2018;15(2):126–31. doi:10.1007/s13196-018-0217-2. [Google Scholar] [CrossRef]
54. Ando D, Umemura K. Bond structures between wood components and citric acid in wood-based molding. Polymers. 2021;13(1):58. doi:10.3390/polym13010058. [Google Scholar] [PubMed] [CrossRef]
55. Huaxu Z, Hua LS, Tahir PM, Ashaari Z, Al-Edrus SSO, Ibrahim NA, et al. Physico-mechanical and biological durability of citric acid-bonded rubberwood particleboard. Polymers. 2021;13(1):98. doi:10.3390/polym13010098. [Google Scholar] [PubMed] [CrossRef]
56. Elfaleh I, Abbassi F, Habibi M, Ahmad F, Guedri M, Nasri M, et al. A comprehensive review of natural fibers and their composites: an eco-friendly alternative to conventional materials. Results Eng 2023;19:101271. [Google Scholar]
Cite This Article
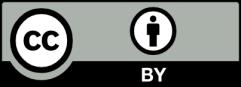
This work is licensed under a Creative Commons Attribution 4.0 International License , which permits unrestricted use, distribution, and reproduction in any medium, provided the original work is properly cited.