Open Access
REVIEW
Overview of the Synthesis, Characterization, and Application of Tannin-Glyoxal Adhesive for Wood-Based Composites
1 Research Center for Biomass and Bioproducts, National Research and Innovation Agency, Cibinong, 16911, Indonesia
2 Department of Forest Products, Faculty of Forestry and Environment, IPB University, Bogor, 16680, Indonesia
3 Department of Agro-Industrial Technology, Universitas Padjadjaran, Bandung, 45363, Indonesia
4 Research Collaboration Center for Biomass and Biorefinery, BRIN and Universitas Padjadjaran, Bandung, 45363, Indonesia
5 School of Life Sciences and Technology, Institut Teknologi Bandung, Bandung, 40132, Indonesia
6 Department of Forest Products Technology, Faculty of Forestry, Universitas Sumatera Utara, Medan, 20355, Indonesia
* Corresponding Author: Muhammad Adly Rahandi Lubis. Email:
(This article belongs to the Special Issue: Environmentally Friendly Wood-Based Composites Based on Sustainable Technologies and Renewable Materials)
Journal of Renewable Materials 2024, 12(7), 1165-1186. https://doi.org/10.32604/jrm.2024.051854
Received 17 March 2024; Accepted 03 July 2024; Issue published 21 August 2024
Abstract
More than a century after its initial synthesis, urea-formaldehyde (UF) resins still have dominant applications as adhesives, paints, and coatings. However, formaldehyde in this industry produces formaldehyde emissions that are dangerous to health. Scientists have spent the last decade replacing formaldehyde and phenol with environmentally friendly substances such as glyoxal and tannin to create bio-based adhesives. This review covers recent advances in synthesizing glyoxal tannin-based resins, especially those made from sustainable raw material substitutes and changes made to synthetic processes to improve mechanical properties. The efficacy of using tannin-glyoxal adhesives in producing wood-based composites has been proven. The glyoxylate reaction forms cross-linked bridges between the aromatic sites of the tannin and glyoxal molecular structures. Glyoxal tannin adhesive with a greater percentage of glyoxal than tannin will produce an adhesive with better characteristics. The gel time reduces as the hardener concentration rises from 7.5% to 15% when glyoxal is used in adhesives. However, excessive amounts of glyoxal will result in a decrease in viscosity values. Glyoxal exhibits faster delivery degradation when it reaches a maximum temperature of approximately 130°C, although it initiates the curing process slightly slower at 110°C. Adding glyoxal to tannin-based adhesives can improve the mechanical properties of composite boards. The wet shear strength of the resulting plywood is increased by 105.4% with the addition of 5-weight percent tannin-based resin with glyoxal as a cross-linker in Soy Protein Adhesive. With glyoxal as a hardener, the panels produced showed good internal bond strengths (>0.35 MPa) and met the international standard specifications for interior-grade panels.Graphic Abstract

Keywords
Particleboard, plywood panels, fiberboard, and other wood composites are constructed using wood adhesives, which are essential parts of the manufacturing process. They ascertain the bonded products′ functionality [1]. The three primary amino resins used in wood-based panel company operations are urea formaldehyde (UF) resin, melamine-formaldehyde (MF), and melamine-urea-formaldehyde resin (MUF). These resins are primarily formaldehyde-based. Adhesives containing formaldehyde are frequently used for bonding, and there is ample evidence of the harmful effects that formaldehyde emissions from panels have on the environment and public health [2]. One of the worst things about wood-based panels is the free formaldehyde emission from conventional fossil-derived synthetic resins like UF, PF, MF, and MUF resins. This also includes the formaldehyde emission from wood-based panels, particularly particleboard, plywood, and medium-density fiberboard (MDF) panels [3].
Formaldehyde (HCHO) is a common indoor contaminant with several negative health effects [4]. Negative health effects on humans, including skin sensitization, nausea, skin and respiratory tract irritation, genotoxicity, nasopharyngeal carcinoma, and leukemia, have been linked to indoor formaldehyde release. In a typical household setting, formaldehyde concentrations range from 0.02 to 0.06 mg/m3 [5]. The formaldehyde content of an interior space is influenced by several factors, including temperature, humidity, ventilation rate, building age, product usage, the presence of flammable materials, and smoking practices [6]. Because of the variations in ultraviolet (UV) light intensity and humidity, it was discovered that the air formaldehyde content was higher in the summer than it was in the winter [7]. For acute exposure (14 days or less), 0.01 ppm is the minimal risk level (MRL) of formaldehyde inhalation exposure (15 to 364 days), while 0.003 ppm is the MRL for chronic exposure (1 year or more) [8]. For the general public, formaldehyde concentrations in indoor air of 0.1 and 0.38 mg/m3 are advised to prevent sensory and eye irritation [9]. According to the World Health Organization, the maximum permissible concentration to safeguard human health against long-term consequences, such as cancer, is 0.21 mg/m3 [10]. Lowering formaldehyde emissions without affecting mechanical quality is one important concern.
The reclassification of formaldehyde as “carcinogenic to humans” in 2004 and the ensuing introduction of more stringent legislation forced resin producers to create a new generation of resins that resulted in a decrease in formaldehyde emissions to levels of natural wood, even though the free formaldehyde levels of these resins have been declining over the previous decades [2,10]. Several approaches have been investigated to decrease the release of formaldehyde, such as directly adding aldehyde to the resin to create better resin formulations [11,12]. Chemical substances or additives known as formaldehyde scavengers are used to lessen or eliminate formaldehyde emissions from various products and the environment [2,13]. Extended exposure to formaldehyde can have adverse health effects, such as allergies, irritation of the respiratory tract, and possibly even cancer. Formaldehyde scavenging agents chemically react with formaldehyde molecules to produce less hazardous or odourless non-volatile compounds. These agents can be added to product formulations or used as surface treatments to lower formaldehyde emissions. Glyoxal is a dialdehyde compound that can react with formaldehyde to form non-volatile compounds, which effectively removes formaldehyde from the environment [14]. Glyoxal is the most likely replacement for formaldehyde when making resin adhesives for wood bonding because of its structural qualities, reactivity, low volatility, non-toxicity, and reasonable cost. Glyoxal is comparatively less volatile and toxic than formaldehyde [15]. Glyoxal has been used extensively in the paper and textile industries as an ideal green environmental agent due to its well-developed production technology, affordable cost, and simple biodegradation [16–19]. Since it has been demonstrated that glyoxalated tannin can be used as an adhesive in particle board manufacturing, tannin synthesis using glyoxal can be an excellent green environmental agent [20–22].
Known by its general name, tannin is a highly water-soluble material that can tan leather and is astringent in water [23]. The fourth most abundant compound in plant vascular tissue, after cellulose, hemicelluloses, and lignin, are tannins, which quantitatively dominate the vast majority of secondary metabolites found in plants [24]. Tannins can make up about 25% of the dry weight of plants, though the amount can vary depending on the environment [25]. Regarding chemistry, tannin combines intricate organic molecules with a phenolic structure [26]. Chemically, tannins are typically categorized into two primary groups: hydrolysable tannins (HTs) and proanthocyanidins, also called condensed tannins (CTs). Phlorotannins (PTs) are being reported in the literature as a third major class of tannins (Fig. 1). By linking a sugar moiety to either gallic acid or hexahydroxydiphenic acid esters, hydrolyzable tannins can be divided into gallotannins and ellagitannins. Proanthocyanidins, also known as condensed tannins, are polymers made up of three-ring flavonols connected by C-C bonds, which are found in many foods and beverages that humans eat, including grape seeds, apples, berries, red wine, chocolate, and cocoa [27]. Compared to HTs, CTs are found in plants in greater abundance and have a more complex structure. Proanthocyanidins are polymers formed by monomeric flavan-3-ols units connected via C-4→C-8 bonds and sometimes through C-4→C-6 linkages [28]. Procyanidins and prodelfinidins are the two types of monomers of CTs [25]. While both might serve as alternatives to phenol-formaldehyde resins, hydrolyzable tannins are a worse choice because of their low phenol substitution and lack of polymeric structure [29].
Figure 1: Structure of tannin [30]. Open Access CC BY-NC-ND 4.0
The tannin oligomers that bark tannin its distinctive dark to black colour typically make up 65–80% of the extract when heated to high temperatures (Table 1); the remaining components include sugars, hydrocolloid gums (3–6%), pectin, hemicellulose, low molar mass (<300 Da) polyphenols, and specific amino and imino acid fractions [31–33]. Tannin extracts are more dense than synthetic resins at the concentrations typically used as adhesives in wood-based panels [34]. High molar mass hydrocolloid gums (carbohydrates) and high molar mass tannins in the extract, as well as hydrogen bonds between the various components, are the causes of the high viscosity even at moderate concentrations of the tannin solutions; this restricts the possibility of increased the possible concentration of the solutions but maintaining viscosities not too high for further processing [35,36].
Glyoxal-based tannin synthesis can be a great green environmental agent since it has been demonstrated that glyoxalated tannin can be used as an adhesive in particleboard manufacturing [16,39,41] and researched tannin-based adhesives that were pretreated with glyoxal and then added to UF resin. Plywood made with UF resin, urea formaldehyde-tannin (UFT), and urea formaldehyde-glyoxal-tannin (UFGT) was then tested for bond strength and formaldehyde on the plywood [16]. Differential Scanning Calorimetry (DSC) results show that adding tannin and glyoxalated tannin reduces the reaction temperature and accelerates the reaction speed. Glyoxalated tannin as a modification material is an excellent way to reduce formaldehyde emissions and increase the binding strength of UF resin. While glutaraldehyde is unsuitable because of its lower reactivity with pine tannins, glyoxal can replace formaldehyde in rigid foams containing pine tannins and furanic acid, offering good insulating properties [42].
2 Characteristics of the Related Literature of Tannin-Glyoxal-Based Adhesives
The interest of researchers in creating adhesives based on tannin is evident from document searches for published papers. A visual map based on the findings of a bibliometric analysis of the keyword’s tannin-based-wood-adhesive is presented in Fig. 2. Indexing provided by keywords in published articles can aid in describing research and facilitate the study of research trends within a scientific discipline [43,44] after conducting a co-occurrence keyword analysis to find terms used together in one or more documents, 59 keywords pertinent to the creation of adhesives based on tannin were found. In the visual map produced, keywords are chosen carefully to remove redundant terms and skewed relationships between them. More articles contain related research, as indicated by the larger circle formed in the bibliometric analysis results via a visual map. Most of the reactions involving tannin-based wood adhesive involve urea and phenol formaldehyde, according to the findings of bibliometric analysis. Research on tannin-based wood adhesives still needs to use glyoxal.
Figure 2: A visual map of keyword co-occurrences within the references considered for the development of this study. Created with VOSviewers 1.6.20
Formaldehyde is used in a lot of tannin-based adhesives as a cross-linker. Alternative aldehyde compounds are necessary because formaldehyde use harms one’s health. Glyoxal is another aldehyde that is substituted for formaldehyde in the synthesis of phenolic resin. With two highly reactive aldehyde groups in its structure, it is a nontoxic aldehyde. The material’s non-volatility, affordability, and effortless biodegradability render it a viable option for replacing formaldehyde in producing phenolic adhesives. It can be made directly from glucose by retro aldol condensation or indirectly by autoxidation from a glycolaldehyde intermediate [45]. After conducting a co-occurrence keyword analysis search to find terms used together in one or more documents, 22 keywords pertinent to the creation of adhesives based on tannin, glyoxal, and wood adhesive were found (Fig. 3). Numerous thermogravimetric analyses, differential scanning calorimetry, and Fourier transform infrared spectrometry tests have been conducted in the context of research on tannin-glyoxal-based adhesives.
Figure 3: A visual map of keyword co-occurrences within the references considered for the development of tannin-glyoxal-wood-based-adhesive. Created with VOSviewers 1.6.20
3 Synthesis of Tannin-Glyoxal-Based Adhesive
Due to their similar structures, tannin has emerged as a new raw material being studied in adhesive research to partially or entirely replace phenol in PF formulation [21,22,46]. Research has revealed that when glyoxal is utilized in biomass-based adhesives rather than formaldehyde, the resulting plywood has superior mechanical qualities since glyoxal increases the reactivity of the biomass materials before the resin’s synthesis [17,47,48]. Fig. 4 shows the possible reaction product of tannin-glyoxal polymers. The glyoxylation reaction is the process by which crosslinked bridges between the aromatic sites of the tannin molecular structure and glyoxal are formed [22]. Glyoxal-cured tannin has a relatively low crosslink density; crosslinking was primarily provided in the proanthocyanidin’s C8 position. As a result, cure at least 90°C was necessary, and the resulting polymers were predominantly elastic [49].
Figure 4: Possible reaction product of tannin-glyoxal polymers [17]. Open Access CC BY-NC-ND 4.0
The second carbonyl group remains unreacted because a portion of the glyoxal that activates the aromatic ring does not crosslink in any way. Only at extended hot press times did the tannin from pine (Pinus radiata) that was cured with glyoxal (an additional amount of 9% at different pH) produce acceptable results [12]. The dialdehyde reacts with the two functional groups in the activated positions of the flavonoid, producing a diabolic crosslink (–CH(OH)–CH(OH)–) or its subsequent enol (–CH=C(OH)–↔–CH2(–C=O)–) [17]. These polymers lacked significant crosslinking, and the activation mostly happened in the proanthocyanidin’s C8 molecule to a lesser extent and with a higher probability. There is no crosslinking of the portion of the glyoxal that activated the aromatic ring, leaving the second carbonyl group unreacted. The glyoxal crosslinking of mimosa tannin is depicted in the following schematic [17].
Fig. 5 shows the responses of larch tannin with glyoxal and resorcinol and crosslinking via dimethylene-ether bridges. The presence of a substitution reaction between phenol and resorcinol or glyoxal indicates the formation of a reactive bi-hydroxyethyl oligomer based on tannin. Large amounts of hydroxyethyl were present in the formed oligomer, which could react with the protein’s –NH2 to form a crosslinking structure and a self-crosslinking structure. The C–O–C stretching vibration was the other peak detected at 1147 cm−1, indicating that this hydroxyethyl reacted with themselves through polycondensation to form ether bonds that link the various tannin molecules [40].
Figure 5: The reaction process of soy protein-based adhesive with a tannin-based resin [40]. Open Access CC BY-NC-ND 4.0
The tannin-glyoxal adhesive was subjected to pyrolysis by Py-GCMS analysis, resulting in the degradation of specific molecular fractions. On the other hand, methyl glyoxal was detected at a retention time of 2.16 min and had a relative abundance of 11.37%. It was established whether tannin-glyoxal adhesive formulations contained benzene compounds. At high temperatures, tannins release benzene triol and carbon dioxide. A byproduct of the tannin structure’s decarboxylation of the outer layer of gallic acid is benzoene triol [40]. Apart from that, there is a butanedione compound formed from the reaction of tannin and glyoxal, which can be seen based on data from the pyrolysis results of the tannin-glyoxal adhesive. This compound functions as a crosslinking agent [16].
4 Characterization of Tannin-Glyoxal-Based Adhesives
4.1 The Physical Properties of Adhesive
The solids content and specific gravity can decrease when the glyoxal percentage is reduced [37]. Generally, higher solids content can contribute to increased adhesive strength. This is because a higher concentration of solid components allows for more effective bonding between surfaces. This could be explained by applying glyoxal at the ideal concentration to react with tannins. Similarly, as the rate of tannin increased, the adhesive’s viscosity value decreased [40]. This indicates that some tannins will remain unreacted when the tannin percentage is higher than the glyoxal percentage because the glyoxal will act as a limiting reagent during the reaction, lowering the viscosity value. Similar findings were made by Zhang et al. in 2023 when he created HUG (hexamethylenediamine-urea-glyoxal) resin for the manufacture of plywood [50]. The viscosity and solids content of HUG3 resin rise when glyoxal from HUG1 resin is added in molarity. This is brought on by the HU and glyoxal polymerization reaction, which raises the reaction product’s molecular weight and the viscosity and solids content.
The solids content will rise during the solids content test because the reaction forming the cross-linked product requires more glyoxal, which will not evaporate. However, the excess glyoxal no longer reacts as the addition of glyoxal increases to HUG4, which dilutes the resin and lowers its viscosity. The excess glyoxal will evaporate during the solids content test, giving the impression that the resin’s solids content is also decreasing [18]. So, some studies use more molar ratios of glyoxal than tannin [20,51]. Research by Santos also shows that the gel time reduces as the hardener concentration rises from 7.5% to 15% when glyoxal is used as a hardener in adhesives [52]. Nevertheless, the gel time increased when the hardener concentration was raised to 20% (Table 2). This is not the same as the CS1 adhesive, which uses paraformaldehyde, tris(hydroxymethyl) nitromethane, and hexamethylenetetramine as hardeners.
Compressing wood composite products, such as plywood, particleboard, and medium-density fiberboard (MDF), is critical in their manufacturing process. Several factors can affect the final product’s pressing process and quality. One of the factors that influences the wood composite pressing process is the adhesive used. The adhesive used in pressing wood composite products is important in glueing wood particles or fibres together to form a sturdy panel. The use of adhesive for particle board is different from adhesive for plywood. Tannin-glyoxal adhesive can be used for particle board applications because it has a low viscosity of <30 mPas [37]. The low viscosity allows for easier distribution of the adhesive while mixing with the particles.
Meanwhile, an adhesive with a higher viscosity is needed for plywood melting applications on the veneer. Chen’s 2017 research on making plywood used Soy Protein-Based Adhesives with a Larch Tannin-Based Resin, which has a viscosity of 970 mPas. Adding the TR molecule (resorcinol and glyoxal were combined with larch tannin to synthesize a tannin-based resin) to the Soy Protein molecule will reduce the intermolecular forces, thereby reducing viscosity [40]. This is in line with the previous explanation stating that adding glyoxal will increase viscosity.
4.2 The Acidity Degree of Tannin-Glyoxal Adhesive
Despite being widely used in wood bonding [53,54], tannin-based adhesives are not as long-lasting as phenol-based resins because of polyflavonoids’ high reactivity and nucleophilicity [55]. In contrast to phenolic resins, tannin-based adhesives’ reactivity exhibits a similar pH dependence [56,57]. The highest reactivity and shortest gel time were found at very high and low pH values [37]. Novolac-type resin is produced by acid catalysis, whereas resol-type resin is produced by base catalysis. Zhang et al.’s research revealed that the addition of glyoxal took one minute longer to gel than formaldehyde when comparing the gelation times of tannin-furfuryl alcohol-formaldehyde (TFF) adhesive and tannin-furfuryl alcohol-glyoxal (TFG) at a temperature of 100°C [51]. Anggini et al. found that the tannin-glyoxal adhesive gelled faster with acid hardener than with alkaline hardener at 135°C (Fig. 6). Generally speaking, NH4Cl is a conventional catalyst that produces acid when it reacts with formaldehyde during the curing process. This acid can hasten the condensation reaction and cause the adhesive to solidify.
Figure 6: Adhesive storage time based on the pH value (a) and adhesive (b) [37]. Open Access CC BY-NC-ND 4.0
The pot-life of the solution is significantly decreased at higher pHs, as indicated by the progressively higher apparent viscosity values, according to Santos, which restricts its use in the formulation of adhesives [52]. The pot life of adhesives and resins can significantly decrease as pH increases, particularly when paraformaldehyde is used as a hardener. Research indicates that at a pH of around 6, the gel time of urea-formaldehyde resins tends to be longer, ensuring a more controlled curing process and minimizing premature hardening [58]. This balance is crucial for maintaining the material’s workability and ensuring consistent performance in various applications. In this instance, Hexamine was chosen as the hardener for tannin-based adhesives, and a lower concentration of 5% allowed for a significant improvement in adhesive pot life. The lower pH allowed for a longer pot life when using glyoxal as a hardener. Fig. 6b shows that even when the adhesive’s pH went acidic, the tannin-glyoxal glue did not harden.
4.3 Thermal Behavior of Tannin-Glyoxal Based Adhesive
The shelf life of the adhesive can also be seen based on the ratio of strain to deflection, known as MOE. Because the curing process tightens the polymer network, lower deflection indicates increased stiffness (MOE). The thermo-mechanical analysis (TMA) instrument applies a constant strain during the temperature rise and records the deflection. Hexamine’s maximum value (2700 MPa) denotes a higher degree of cross-linking due to its increased structural tightness. Glyoxal’s healing rate resulted in high stiffness (MOE = 2300 MPa) [59]. Glyoxal exhibits faster delivery degradation when it reaches a maximum temperature of approximately 130°C, although it initiates the curing process slightly slower at 110°C (Fig. 7). This indicates that glyoxal begins to cure later than hexamine, increasing stiffness like hexamine, but the resulting polymer is more sensitive to higher temperatures than hexamine.
Figure 7: Thermomechanical analysis of the quebracho–crosslinker formulations [59]. Open Access CC BY-NC-ND 4.0
The dynamic mechanical analysis (DMA) technique was used to evaluate the mechanical curing rate, which characterizes the cure in terms of the rate of rigidity development, and the DSC technique assessed the rate and extent of chemical conversion to complete the study of the curing kinetics of the adhesives [60]. Storage modulus (E′), loss modulus (E″), and tan delta all contribute to the explanation of DMA analysis. The storage modulus (E′) curve explains the stiffness properties of adhesive structures [61]. At a given temperature, E first drops to a minimum and then reaches a maximum. The adhesive may have softened initially due to temperature-induced changes in E′. Following that, the adhesive starts to gel, and a molecular network starts to form; as a result, E′ begins to rise towards a maximum.
Furthermore, a high cross-link density in the adhesive is indicated by the gradual decrease of E′ with increasing temperature. This implies the formation of a denser network structure and higher stiffness. Significant changes in E′ have been observed in Anggini et al.’s research when the percentage of glyoxal in tannin-glyoxal adhesives is reduced [37]. The tannin-glyoxal adhesive will soften at a higher temperature if the glyoxal molar ratio is lower (Fig. 8). DMA revealed that adhesives with higher glyoxal content exhibited better elastic properties and mechanical performance, especially when ammonium chloride (NH4Cl) was used as a hardener compared to sodium hydroxide (NaOH).
Figure 8: Storage modulus value of TG adhesive F1 (a), F2 (b), and F3 (c) using different hardeners as a function of temperature [37]. Open Access CC BY-NC-ND 4.0
The tannin-glyoxal adhesive’s loss modulus (E″) trend is comparable to E′. The adhesive softens as the stiffness drops, causing the initial drop in E″ [37]. After reaching a minimum, the adhesive increases (Fig. 9). The E″ value is the viscous response of a material, which measures the energy lost as heat due to deformation [62,63]. The ratio of the storage modulus (tan E′/E′) to the loss modulus (tan delta/tan δ) is known as the damping factor. An analysis of a material’s viscoelastic properties uses the tan delta value. Tan delta values less than or equal to one indicate a material’s tendency toward elasticity, while values greater than or equal to one indicate a material’s tendency toward density [64]. Tan delta increased for all adhesives using tannin-glyoxal-based adhesives as the temperature rose [37]. Compared to F2 (T:G ratio 1:1) and F3 (T:G ratio 2:1) adhesives, F1 (T:G ratio 1:2) adhesive exhibits a lower tan delta value during the rubber transition phase (Fig. 10). According to Goriparthi et al., this suggests a robust configuration of molecular bonds and significant molecular mobility [61]. Increased interaction between the hydroxyl groups produced by tannin and glyoxal may cause this higher tan delta value. This interaction will ultimately lead to a polymerization reaction, raising the ratio E″ to E′s value.
Figure 9: Loss modulus value of TG adhesive F1 (a), F2 (b), and F3 (c) using different hardeners as a function of temperature [37]. Open Access CC BY-NC-ND 4.0
Figure 10: Tan delta value of TG adhesive F1 (a), F2 (b), and F3 (c) using different hardeners as a function of temperature [37]. Open Access CC BY-NC-ND 4.0
Wood adhesives’ fire resistance and thermomechanical behavior are crucial considerations in various applications, especially in construction and manufacturing, where fire safety and structural integrity are paramount [65–67]. In wood adhesives, fire resistance is significant for the application. In contrast, if the adhesive used for the wood composite application has poor heat resistance, it will affect the construction [68]. Thermomechanical behavior refers to how a material behaves under the combined influence of temperature and mechanical loading [69]. When exposed to high temperatures, wood adhesives can experience changes in mechanical properties such as strength, stiffness, and elongation, which can affect the overall performance of the glued wood product.
The correlation between fire resistance and thermomechanical behavior in wood adhesives lies in understanding how adhesive properties change when exposed to fire or high temperatures. High-quality wood adhesives are formulated to exhibit good fire resistance by maintaining their structural integrity and adhesive strength at high temperatures [70]. Adhesives with higher thermal stability and resistance to degradation at high temperatures tend to retain their mechanical properties better when exposed to fire [71]. Additionally, the adhesive’s ability to resist heat transfer can play a role in reducing the spread of fire in glued wood products. These properties can be determined by applying fire retardant materials based on their thermal behavior.
Tannin-based bio-macromolecules show promising potential for sustainable flame retardancy in various natural and synthetic polymer materials, including textiles, steel, and epoxy resins [72]. Tannic acid, as a bio-based hardener in fire-resistant epoxy resin, effectively captures oxygen radicals and forms a charcoal layer, thereby increasing building safety against the threat of fire [73]. In the study [39], the thermal stability of the adhesive was approximately 200°C after glyoxalate, with 40 tannin resin being the most efficient. This indicates that the tannin-glyoxal adhesive has good fire-resistant properties because it can resist degradation and loss of effectiveness at high temperatures.
The thermal and rheological properties of the adhesive will influence the temperature and pressure used during pressing. Proper temperature and pressure settings are critical to facilitating adhesive flow, curing, and setting while minimizing adhesive degradation or over-curing potential [74,75]. Higher temperatures can reduce the viscosity of the adhesive, making it easier to flow and penetrate the wood particles or fibres [76]. Additionally, longer pressing times typically involve more prolonged exposure to high temperatures, allowing for more thorough adhesive curing and composite material consolidation. However, pressing times that are too long can cause the adhesive to dry too quickly, decrease panel properties, or increase energy consumption.
5 Aplications of Tannin-Glyoxal-Based Adhesives
Several studies regarding the application of composite boards using tannin-glyoxal based adhesives have been carried out. Several of these studies aim to evaluate the effectiveness and performance of tannin-glyoxal adhesives in various conditions. Table 3 contains a summary of several applications of tannin-glyoxal adhesives that have been tested, along with the research results. Tannin-glyoxal-based adhesives were dominantly utilized in the manufacture of plywood and particleboard [37,40,77].
According to research by Pizzi et al. [78] and Garcia et al. [79], good strength in particleboards can be achieved solely by the tannins’ auto-condensation reactions, regardless of the variations in the structure and behavior of various polyflavonoid tannins. In rare circumstances, the auto-condensation response may even be hampered by applying a hardener (co-reactant) [80]. “auto-condensation” refers to the pyran rings opening in both acidic and alkaline environments without needing an external hardener [81]. It has a unique chemical property because tannin stimulates self-polymerization to create a crosslinked polyphenolic network. The chemical makeup of the extraction source affects the tannins’ auto-condensation reaction rates [78]. It is reported that weak Lewis acids such as boric acid, silicates, aluminum chloride, and silica can influence the auto-condensation of various tannins. The issues brought on by tannins’ delayed reaction are resolved when Lewis acid catalyzes the auto condensation of tannin [82]. Additionally, the Lewis-acid-based auto-condensation system offers stronger internal bonds and shows a decrease in pressing temperature and time.
Particleboards made of one layer of wood were pressed using the various tannin-based adhesive formulations investigated. Using glyoxal as a hardener resulted in significantly higher MOE for sumac tannins extracted at 70°C and Aleppo tannins at 100°C. The TMA study also showed that the tannins extraction temperature (70°C or 100°C) and, consequently, the tannins DP (degree of polymerization) had a slight or no effect on the resins performance (Fig. 11). The interflavonoid linkages between C4 and C6 and C4 and C8 were found to be responsible for the higher DP of the tannins extracted at the lower temperature [83,84]. The produced panels met the relevant international standard specifications for interior-grade panels (MOE > 0.35 MPa) and demonstrated good internal bond strengths with glyoxal as hardeners, according to the results [85].
Figure 11: Modulus of elasticity (MOE) of tannin-based particleboard. 70 and 100 refer to the extraction temperature of the tannin [85]. Open Access CC BY-NC-ND 4.0
The use of glyoxal as an adhesive in particleboard production offers several advantages, particularly concerning the modulus of elasticity (MOE). Glyoxal-based adhesives, including glyoxalated tannins and glyoxalated lignin, have shown promising results in enhancing the mechanical properties of particleboards. One significant advantage of using glyoxal adhesives is the improved water resistance and mechanical properties of the particleboards. Studies have shown that particleboards made with glyoxal-based adhesives exhibit higher MOE values compared to traditional adhesives [86]. For instance, research indicates that particleboards manufactured using glyoxalated lignin and oxidized dialdehyde starch crosslinked by urea demonstrate enhanced bonding and stability, resulting in better mechanical performance [87].
The internal bonding (IB), a direct indicator of the adhesives’ effectiveness, was established [88,89]. For the Particle Board, SNI 03-2105-2006 type 8 stipulates that the IB strength must be at least 0.15 MPa. To create PB that satisfies the adhesive firmness requirements, the F1 adhesive formula combined the hardener NH4Cl with NaOH (Fig. 12). As the glyoxal percentage in the TG adhesive ratio decreased, so did the adhesive firmness. However, according to Zhang et al.’s study from 2022, the addition of too much glyoxal may have led to a weakening trend in the synthetic resin’s bonding performance, particularly in plywood’s wet shear strength [1]. This is because aldol condensation from glyoxal can form linear oligomerization with hydrophilic hydroxyl groups, which lowers the resin’s water resistance [90]. Another investigation of tannin-glyoxal adhesives found that these adhesives achieve internal bond strengths above 0.4 MPa, making them competitive with conventional adhesives in terms of performance as well as environmental friendliness [91]. Additionally, research on zero-emission tannin-glyoxal adhesives highlights their potential use in wood panels, emphasizing their non-toxicity and adequate bonding properties.
Figure 12: Internal bonding strength of areca particleboard bonded with different TG adhesive formulations [37]. Open Access CC BY-NC-ND 4.0. The significant effect is indicated by different letters (a, b, bc, c, d)
In comparison to tannin-furfuryl alcohol-formaldehyde (TFF) and phenol-formaldehyde (PF) adhesive, the use of an environmentally friendly furfuryl alcohol-glyoxal (FA-G) resin in tannin-based adhesives improves wet shear strength and water resistance [51]. The hydrophobic characteristics of FA-G resin contribute to the resistance of bonded joints to water and decrease in moisture absorption, enhancing their durability in damp conditions. Fig. 13 illustrates the maximum rupture of plywood glued with 100% Mimosa Tannin, Mimosa Tannin-Glyoxalated Lignin (75%–25%), PF, and UF. Comparative research demonstrates that tannin solution adhesives’ mechanical qualities are enhanced by the addition of lignin glyoxalate. Tensile tests for mimosa tannin and mimosa tannin-glyoxalate lignin adhesives (75%–25%) showed a shift from 2173 N to 2637 N, respectively. Furthermore, the tensile measurements of this adhesive formulation are even higher than UF and very similar to measurements made with commercial adhesives, which are commonly used to glue plywood. In addition, in Xu’s research it was found that the strength of UF-glyoxalated tannin was higher than UF-tannin [92]. This may have been caused by the tannin macromolecule’s low reaction activity and few reaction sites with UF resins, resulting in low shearing strength and UFT curing degree. When UF resin and UFGT resin are compared, the UF resin modified by glyoxylate tannin exhibits a higher bonding strength. Raising to 0.87 MPa was the dry strength. The wet strength rose from 0.22 to 0.79 MPa, satisfying the GB/T 9846-2015, ≥0.70 MPa, Chinese national standard. The addition of glyoxylate tannin impacts the bonding strength of UF resin. The glyoxal pretreatment of the tannins may have contributed to the improvement in hydrolysis resistance because of the high reactivity of the glyoxalated tannin and UF resin, as well as the complex structure and higher curing degree. This may also explain why the bonding strength of UFGT is superior to that of UFT.
Figure 13: Comparison of maximum rupture of commercial and bio-adhesives using for bonding plywood panels [93]. Open Access CC BY-NC-ND 4.0
Formaldehyde can be partially or wholly substituted with glyoxal to prepare and study the structure and reaction mechanism of environmentally friendly urea-based amino resins. This has led to significantly decreased or eliminated formaldehyde emission [94–96]. Formaldehyde emissions of PF were 2.78 mg/L, higher than tannin-glyoxalated lignin resin (1.27 mg/L) (Table 4). It also meets the E1 level requirements (≤1.5 mg/L) of Chinese National Standard GB 18580-2001. Plywood panels bonded with lignin glyoxalated and mimosa tannin showed a reduction in formaldehyde emissions of 24%–67% compared with plywood made with commercial PF resin (for mimosa tannin (100%), respectively) and macerated mimosa tannin-lignin glyoxalated.
The combination of tannin and lignin with glyoxal forms a stable polymer structure with fewer bonds resulting in free formaldehyde [97]. In addition, the reaction between tannin or lignin and glyoxal is more likely to involve the aldehyde group of glyoxal rather than the formation of free formaldehyde so that the resulting formaldehyde emissions are less [98]. Plywood bonded with phenol formaldehyde adhesive can emit formaldehyde due to unreacted formaldehyde present in the adhesive. During the production of phenol formaldehyde adhesives, formaldehyde may not fully react with phenol, leaving free formaldehyde that can be released into the environment over time [99,100]. Emissions are typically highest immediately after manufacturing and decrease gradually.
The solids content and specific gravity of glyoxal tannin adhesive can decrease if the glyoxal percentage is reduced. This shows that some tannins will remain unreacted when the tannin percentage is higher than the glyoxal percentage because glyoxal will act as a limiting reagent during the reaction, which can also reduce the viscosity value. Increasing this percentage also affects the gelatinization time to be faster. A high glyoxal percentage increases the percentage of crystallinity in the adhesive, forming better polymer bonds and improving cohesion and adhesion properties for areca-based particleboard. However, excessive amounts of glyoxal will cause a lot of glyoxal not to react, reducing the adhesive’s viscosity. Excess glyoxal will also evaporate when testing the solids content, giving the impression that the resin solids content is also decreasing. However, adding too much glyoxal may have led to a trend toward weakening the bonding performance of synthetic resins, especially the wet shear strength of plywood. The tannin:glyoxal ratio 1:2 produces adhesive and particle board characteristics that meet standards.
Acknowledgement: This study was supported by integrated Laboratory of Bioproducts, National Research and Innovation Agency, Republic of Indonesia.
Funding Statement: This study was funded by National Research and Innovation Agency, Republic of Indonesia, Research Grant No. 65/II.7/HK/2022, titled Pengembangan Produk Oriented Strand Board Unggul dari Kayu Ringan dan Cepat Tumbuh dalam Rangka Pengembangan Produk Biokomposit Prospektif.
Author Contributions: The authors confirm contribution to the paper as follows: study conception and design: Awanda Wira Anggini, Rita Kartika Sari, and Muhammad Adly Rahandi Lubis; data collection: Awanda Wira Anggini, Rita Kartika Sari, and Muhammad Adly Rahandi Lubis; analysis and interpretation of results: Awanda Wira Anggini, Efri Mardawati, Tati Karliati, and Apri Heri Iswanto; validation: Rita Kartika Sari, Apri Heri Iswanto, and Muhammad Adly Rahandi Lubis; draft manuscript preparation: Awanda Wira Anggini, Rita Kartika Sari, and Muhammad Adly Rahandi Lubis; review and editing of the manuscript: Efri Mardawati, Tati Karliati, and Apri Heri Iswanto. All authors reviewed the results and approved the final version of the manuscript.
Availability of Data and Materials: Not applicable.
Conflicts of Interest: The authors declare that they have no conflicts of interest to report regarding the present study.
References
1. Zhang Q, Xu G, Pizzi A, Lei H, Xi X, Du G. A green resin wood adhesive from synthetic polyamide crosslinking with glyoxal. Polymers. 2022;14(14):2819. doi:10.3390/polym14142819. [Google Scholar] [PubMed] [CrossRef]
2. Maulana MI, Lubis MAR, Febrianto F, Lee SH, Iswanto AH, Antov P, et al. Environmentally friendly starch-based adhesives for bonding high-performance wood composites: a review. Forests. 2022;13(10):1614. doi:10.3390/f13101614. [Google Scholar] [CrossRef]
3. Hong MK, Lubis MAR, Park BD, Sohn CH, Roh JK. Effects of surface laminate type and recycled fiber content on properties of three-layer medium density fiberboard. Wood Mater Sci Eng. 2020;15(3):163–71. doi:10.1080/17480272.2018.1528479. [Google Scholar] [CrossRef]
4. Zhang Y, Yu Y, Zhang C, Song N, Guo Z, Liang M. Highly sensitive and selective detection of formaldehyde via bio-electrocatalysis over aldehyde dehydrogenase. Anal Chem. 2022 Nov 15;94(45):15827–31. doi:10.1021/acs.analchem.2c03632. [Google Scholar] [PubMed] [CrossRef]
5. IARC. Formaldehyde, 2-butoxyethanol and 1-tert-butoxypropan-2-ol. IARC Monogr Eval Carcinog Risks to Humans; 200688:1–478. Available from: https://www.ncbi.nlm.nih.gov/pmc/articles/PMC4781641/. [Accessed 2024]. [Google Scholar]
6. Hult E, Willem H, Price P, Hotchi T, Russell M, Singer B. Formaldehyde and acetaldehyde exposure mitigation in US residences: in-home measurements of ventilation control and source control. Indoor Air. 2014 Sep 1;25:523–35. [Google Scholar]
7. Salthammer T. Formaldehyde sources, formaldehyde concentrations and air exchange rates in European housings. Build Environ. 2019;150:219–32. doi:10.1016/j.buildenv.2018.12.042. [Google Scholar] [CrossRef]
8. Agency USEP. Graphical arrays of chemical-specific health effect reference values for inhalation exposures. EPA. 2009:69–75. [Google Scholar]
9. Ulker OC, Ulker O. Toxicity of formaldehyde, polybrominated diphenyl ethers (PBDEs) and phthalates in engineered wood products (EWPs) from the perspective of the green approach to materials: a review. BioResources. 2019;14(3):7465–93. doi:10.15376/biores. [Google Scholar] [CrossRef]
10. World Health Organization. Formaldehyde, 2-butoxyethanol and 1-tert-butoxypropan-2-ol. In: IARC Monographs on the Evaluation of Carcinogenic Risks to Humans; 2006. Available from: https://publications.iarc.fr/Book-And-Report-Series/Iarc-Monographs-On-The-Identification-Of-Carcinogenic-Hazards-To-Humans/Formaldehyde-2-Butoxyethanol-And-1--Em-Tert-Em--Butoxypropan-2-ol-2006. [Accessed 2024]. [Google Scholar]
11. Li J, Zhu W, Zhang S, Gao Q, Xia C, Zhang W, et al. Depolymerization and characterization of Acacia mangium tannin for the preparation of mussel-inspired fast-curing tannin-based phenolic resins. Chem Eng J. 2019;370:420–31. doi:10.1016/j.cej.2019.03.211. [Google Scholar] [CrossRef]
12. Ballerini A, Despres A, Pizzi A. Non-toxic, zero emission tannin-glyoxal adhesives for wood panels. Holz als Roh-und Werkst. 2005;63(6):477–8. doi:10.1007/s00107-005-0048-x. [Google Scholar] [CrossRef]
13. Selakjani PP, Dorieh A, Pizzi A, Shahavi MH, Hasankhah A, Shekarsaraee S, et al. Reducing free formaldehyde emission, improvement of thickness swelling and increasing storage stability of novel medium density fiberboard by urea-formaldehyde adhesive modified by phenol derivatives. Int J Adhes Adhes. 2021;111:102962. doi:10.1016/j.ijadhadh.2021.102962. [Google Scholar] [CrossRef]
14. Chrobak J, Iłowska J, Chrobok A. Formaldehyde-free resins for the wood-based panel industry: alternatives to formaldehyde and novel hardeners. Molecules. 2022;27(15):4862. doi:10.3390/molecules27154862. [Google Scholar] [PubMed] [CrossRef]
15. Deng S. Synthesis, structure characterization and application of melamine–glyoxal adhesive resins. Eur J Wood Wood Prod. 2018;76(1):283–96. doi:10.1007/s00107-017-1184-9. [Google Scholar] [CrossRef]
16. Xu G, Tian H, Xi X, Song J, Lei H, Du G. Preparation and characterization of urea–formaldehyde adhesives modified with glyoxalated tannin. Eur J Wood Wood Prod. 2022;80(5):1215–23. doi:10.1007/s00107-022-01819-1. [Google Scholar] [CrossRef]
17. Tondi G. Tannin-based copolymer resins: synthesis and characterization by solid state 13C NMR and FT-IR spectroscopy. Polymers. 2017;9(6):223. doi:10.3390/polym9060223. [Google Scholar] [PubMed] [CrossRef]
18. Cao L, Pizzi A, Zhang Q, Tian H, Lei H, Xi X, et al. Preparation and characterization of a novel environment-friendly urea-glyoxal resin of improved bonding performance. Eur Polym J. 2022;162:110915. doi:10.1016/j.eurpolymj.2021.110915. [Google Scholar] [CrossRef]
19. Siahkamari M, Emmanuel S, Hodge DB, Nejad M. Lignin-glyoxal: a fully biobased formaldehyde-free wood adhesive for interior engineered wood products. ACS Sustain Chem Eng. 2022;10(11):3430–41. doi:10.1021/acssuschemeng.1c06843. [Google Scholar] [CrossRef]
20. Ghahri S, Pizzi A. Improving soy-based adhesives for wood particleboard by tannins addition. Wood Sci Technol. 2018 Jan 1;52(1):261–79. doi:10.1007/s00226-017-0957-y. [Google Scholar] [CrossRef]
21. Zhang J, Xi X, Liang J, Pizzi A, Du G, Deng S. Tannin-based adhesive cross-linked by furfuryl alcohol-glyoxal and epoxy resins. Int J Adhes Adhes. 2019;94:47–52. doi:10.1016/j.ijadhadh.2019.04.012. [Google Scholar] [CrossRef]
22. Arias A, González-García S, Feijoo G, Moreira MT. Tannin-based bio-adhesives for the wood panel industry as sustainable alternatives to petrochemical resins. J Ind Ecol. 2022;26(2):627–42. doi:10.1111/jiec.v26.2. [Google Scholar] [CrossRef]
23. Mutiar S, Kasim A, Emriadi, Asben A. Quality of leather using vegetable tannins extract of acacia mangium bark from waste of industrial plantation. IOP Conf Ser Earth Environ Sci. 2019;327(1):1–6. [Google Scholar]
24. Bule M, Khan F, Niaz K. Tannins (hydrolysable tannins, condensed tannins, phlorotannins, flavono-ellagitannins); 2020. Available from: https://www.researchgate.net/profile/Kamal-Niaz-2/publication/339841545_Tannins_hydrolysable_tannins_condensed_tannins_phlorotannins_flavonoellagitannins/links/5e686b894585153fb3d5eda1/Tannins-hydrolysable-tannins-condensed-tannins-phlorotannins-flavonoellagitannins.pdf. [Accessed 2024]. [Google Scholar]
25. Adamczyk B, Simon J, Kitunen V, Adamczyk S, Smolander A. Tannins and their complex interaction with different organic nitrogen compounds and enzymes: old paradigms versus recent advances. ChemistryOpen. 2017;6(5):610–4. doi:10.1002/open.v6.5. [Google Scholar] [CrossRef]
26. Zhang T. Multifunctional tannin extract-based epoxy derived from waste bark as a highly toughening and strengthening agent for epoxy resin. Ind Crops Prod. 2022;176:72–87. [Google Scholar]
27. Cai Y, Zhang J, Chen NG, Shi Z, Qiu J, He C, et al. Recent advances in anticancer activities and drug delivery systems of tannins. Med Res Rev. 2017;37(4):665–701. doi:10.1002/med.2017.37.issue-4. [Google Scholar] [CrossRef]
28. Smeriglio A, Barreca D, Bellocco E, Trombetta D. Proanthocyanidins and hydrolysable tannins: occurrence, dietary intake and pharmacological effects. Br J Pharmacol. 2017;174(11):1244–62. doi:10.1111/bph.v174.11. [Google Scholar] [CrossRef]
29. Pizzi A. Condensed tannins for adhesives. Ind & Eng Chem Prod Res Dev. 1982;21(3):359–69. doi:10.1021/i300007a005. [Google Scholar] [CrossRef]
30. Molnar M, Jakovljevi M. A comprehensive analysis of diversity, structure, biosynthesis and extraction of biologically active tannins from various plant-based materials using deep eutectic solvents. Molecules. 2024;29(11):2615. doi:10.3390/molecules29112615. [Google Scholar] [PubMed] [CrossRef]
31. Das AK, Islam MN, Faruk MO, Ashaduzzaman M, Dungani R. Review on tannins: extraction processes, applications and possibilities. South African J Botany. 2020;135:58–70. doi:10.1016/j.sajb.2020.08.008. [Google Scholar] [CrossRef]
32. Pizzi A. Tannin-based adhesives. J Macromol Sci Macromol Chem. 1980;18(2):247–315. doi:10.1080/00222358008081043. [Google Scholar] [CrossRef]
33. Pizzi A. Aminoresin wood adhesives. Wood Adhes Chem Technol. 1983;1:59–104. [Google Scholar]
34. Dunky M. Natural aldehyde-based thermosetting resins. Biobased Adh: Sources, Charact Appl. 2023;5:167–205. [Google Scholar]
35. Yazaki Y. Utilization of flavonoid compounds from bark and wood: a review. Nat Prod Commun. 2015;10(3):513–20. [Google Scholar] [PubMed]
36. Arasaretnam S, Venujah K. Modification of Tannin extracted from the bark of Acacia auriculiformis for the antibacterial activity and application of metal adsorption. Ruhuna J Sci. 2017;8(2):90. doi:10.4038/rjs.v8i2.30. [Google Scholar] [CrossRef]
37. Anggini AW, Lubis MAR, Sari RK, Papadopoulos AN, Antov P, Iswanto AH, et al. Cohesion and adhesion performance of tannin-glyoxal adhesives at different formulations and hardener types for bonding particleboard made of areca (Areca catechu) leaf sheath. Polymers. 2023;15(16):1–25. [Google Scholar]
38. Vázquez G, Santos J, Freire MS, Antorrena G, González-Álvarez J. DSC and DMA study of chestnut shell tannins for their application as wood adhesives without formaldehyde emission. J Therm Anal Calorim. 2012;108(2):605–11. doi:10.1007/s10973-011-2138-9. [Google Scholar] [CrossRef]
39. Chupin L, Charrier B, Pizzi A, Perdomo A, Charrier-El Bouhtoury F. Study of thermal durability properties of tannin-lignosulfonate adhesives. J Therm Anal Calorim. 2015;119(3):1577–85. doi:10.1007/s10973-014-4331-0. [Google Scholar] [CrossRef]
40. Chen M. Improved adhesion performance of soy protein-based adhesives with a larch tannin-based resin. Polymers. 2017;9(9):1–11. [Google Scholar]
41. Amaral-Labat G, Pizzi A, Gonçalves AR, Celzard A, Rigolet S, Rocha G. Environment-friendly soy flour-based resins without formaldehyde. J Appl Polym Sci. 2008;108:624–32. doi:10.1002/app.v108:1. [Google Scholar] [CrossRef]
42. Lacoste C, Basso MC, Pizzi A, Laborie MP, Garcia D, Celzard A. Bioresourced pine tannin/furanic foams with glyoxal and glutaraldehyde. Ind Crops Prod. 2013;45:401–5. doi:10.1016/j.indcrop.2012.12.032. [Google Scholar] [CrossRef]
43. Zhang L, Geng Y, Zhong Y, Dong H, Liu Z. A bibliometric analysis on waste electrical and electronic equipment research. Environ Sci Pollut Res. 2019;26:21098–108. doi:10.1007/s11356-019-05409-2. [Google Scholar] [PubMed] [CrossRef]
44. Rodriguez-Grau G, Marin-Uribe C, Cortés-Rodriguez P, Montero C, Rosales V, Galarce C. Bibliometric analysis of the green gluing technique (2000–2020trends and perspectives. Forests. 2022;13(10):1714. doi:10.3390/f13101714. [Google Scholar] [CrossRef]
45. Amaya-Farfan J, Rodriguez-Amaya DB. The Maillard reactions. In: Chemical changes during processing and storage of foods. Cambridge, Massachusetts: Elsevier; 2021. p. 215–163. [Google Scholar]
46. Zidanes UL. Preparation and characterization of tannin-based adhesives reinforced with cellulose nanofibrils for wood bonding. Holzforschung. 2021;75(2):159–67. doi:10.1515/hf-2020-0033. [Google Scholar] [CrossRef]
47. Hussin H, Alia Abdul A, Anwar I, Ibrahim MNM, Latif NHA. Development and characterization novel bio-adhesive for wood using kenaf core (Hibiscus cannabinus) lignin and glyoxal. Int J Biol Macromol. 2019;122:713–22. doi:10.1016/j.ijbiomac.2018.11.009. [Google Scholar] [PubMed] [CrossRef]
48. Nieuwenhove I, Renders T, Lauwaert J, De Roo T, De Clercq J, Verberckmoes A. Biobased resins using lignin and glyoxal. ACS Sustain Chem Eng. 2020;8(51):18789–809. doi:10.1021/acssuschemeng.0c07227. [Google Scholar] [CrossRef]
49. Dunky M, Mittal KL. Biobased adhesives: sources, characteristics, and applications. New Jersey: Scrivener Publishing, Wiley; 2023. p. 1–738. [Google Scholar]
50. Zhang Q, Chen S, Cao L, Lei H, Pizzi A, Xi X, et al. Preparation of environmentally friendly urea-hexanediamine-glyoxal (HUG) resin wood adhesive. J Renew Mater. 2023;162(5):110915. [Google Scholar]
51. Vera M, Urbano BF. Tannin polymerization: an overview. Polymer Chem. 2021;12(30):4272–90. doi:10.1039/D1PY00542A. [Google Scholar] [CrossRef]
52. Santos J. Environmentally friendly wood adhesives based on chestnut (Castanea sativa) shell tannins. Eur J Wood Wood Prod. 2017;75(1):89–100. doi:10.1007/s00107-016-1054-x. [Google Scholar] [CrossRef]
53. Liu J, Wang L, Li J, Li C, Zhang S, Gao Q, et al. Degradation mechanism of Acacia mangium tannin in NaOH/urea aqueous solution and application of degradation products in phenolic adhesives. Int J Adhes Adhes. 2020;98:102556. doi:10.1016/j.ijadhadh.2020.102556. [Google Scholar] [CrossRef]
54. Tondi G. Tannin-based foams: The innovative material for insulation purposes. In: Handbook of composites from renewable materials; 2017. vol. 1, p. 93–105. Available from: https://api.elsevier.com/content/abstract/scopus_id/85050947096. [Accessed 2024]. [Google Scholar]
55. Pizzi A. Advanced wood adhesives technology. Boca Raton: CRC Press; 1994. [Google Scholar]
56. Garcia DE, Glasser WG, Pizzi A, Lacoste C, Laborie MP. Polyphenolic resins prepared with maritime pine bark tannin and bulky-aldehydes. Ind Crops Prod. 2014;62:84–93. doi:10.1016/j.indcrop.2014.08.010. [Google Scholar] [CrossRef]
57. Garcia R, Pizzi A. Polycondensation and autocondensation networks in polyflavonoid tannins. I. Final networks. J Appl Polym Sci. 1998;70(6):1083–91. [Google Scholar]
58. Qin Y, Jiang W, Li A, Gao M, Liu H, Gao Y, et al. The combination of paraformaldehyde and glutaraldehyde is a potential fixative for mitochondria. Biomolecules. 2021;11(5):1–14. [Google Scholar]
59. Cesprini E, Sket P, Causin V, Zanetti M, Tondi G. Development of Quebracho (Schinopsis balansae) tannin-based thermoset resins. Polymers. 2021;13(24):4412. doi:10.3390/polym13244412. [Google Scholar] [PubMed] [CrossRef]
60. Vázquez G, López-Suevos F, González-Alvarez J, Antorrena G. Curing process of phenol-urea-formaldehyde-tannin (PUFT) adhesives: kinetic studies by DSC and DMA. J Therm Anal Calorim. 2005;82(1):143–9. doi:10.1007/s10973-005-0855-7. [Google Scholar] [CrossRef]
61. Goriparthi BK, Suman KNS, Nalluri MR. Processing and characterization of jute fiber reinforced hybrid biocomposites based on polylactide/polycaprolactone blends. Polym Compos. 2012 Feb;33(2):237–44. doi:10.1002/pc.v33.2. [Google Scholar] [CrossRef]
62. Jawaid M, Abdul Khalil HPS, Hassan A, Dungani R, Hadiyane A. Effect of jute fibre loading on tensile and dynamic mechanical properties of oil palm epoxy composites. Compos Part B Eng. 2013;45(1):619–24. doi:10.1016/j.compositesb.2012.04.068. [Google Scholar] [CrossRef]
63. Asim M, Jawaid M, Nasir M, Saba N. Effect of fiber loadings and treatment on dynamic mechanical, thermal and flammability properties of pineapple leaf fiber and kenaf phenolic composites. J Renew Mater. 2018;6(4):383–93. doi:10.7569/JRM.2017.634162. [Google Scholar] [CrossRef]
64. Rashid B, Leman Z, Jawaid M, Ghazali MJJ, Ishak MRR. Dynamic mechanical analysis of treated and untreated. Bioresources. 2017;12:3448–62. [Google Scholar]
65. Zang X, Liu W, Wu D, Pan X, Zhang W, Bian H, et al. Contemporary fire safety engineering in timber structures: cchallenges and solutions. Fire. 2024;7(1):2. [Google Scholar]
66. Agnihotri S, Sheikh JN, Singh SP, Behera BK. Flame-retardant textile structural composites for construction application: a review. J Mater Sci. 2024;59(5):1–31. [Google Scholar]
67. Kytka T, Gašparik M, Novák D, Sahula L, Karami E, Das S. Burning properties of combined glued laminated timber. Fire. 2024;7(1):30. doi:10.3390/fire7010030. [Google Scholar] [CrossRef]
68. Chen Y, Rao Y, Liu P, Wu L, Zhang G, Zhang J, et al. High-amylose starch-based gel as green adhesive for plywood: adhesive property, water-resistance, and flame-retardancy. Carbohydr Polym. 2024;339:122247. doi:10.1016/j.carbpol.2024.122247. [Google Scholar] [PubMed] [CrossRef]
69. Yang W, Zhang L, Zhang H, Wang F, Li X. Numerical investigations of the effects of different factors on the displacement of energy pile under the thermo-mechanical loads. Case Stud Therm Eng. 2020;21:100711. doi:10.1016/j.csite.2020.100711. [Google Scholar] [CrossRef]
70. Yang Y, Ren Y, Ge S, Ye H, Shi Y, Xia C, et al. Transformation of Buxus sinica into high-quality biocomposites via an innovative and environmentally-friendly physical approach. Appl Surf Sci. 2022;606:154595. doi:10.1016/j.apsusc.2022.154595. [Google Scholar] [CrossRef]
71. Nguyen-Ha TM, Nguyen TB, Nguyen TA, Pham LH, Nguyen DH, Nguyen DM, et al. Novel high-performance sustainable polyurethane nanocomposite foams: fire resistance, thermal stability, thermal conductivity, and mechanical properties. Chem Eng J. 2023;474:145585. doi:10.1016/j.cej.2023.145585. [Google Scholar] [CrossRef]
72. Basak S, Raja ASM, Saxena S, Patil PG. Tannin based polyphenolic bio-macromolecules: creating a new era towards sustainable flame retardancy of polymers. Polym Degrad Stab. 2021;189:109603. doi:10.1016/j.polymdegradstab.2021.109603. [Google Scholar] [CrossRef]
73. Kim YO, Cho J, Yeo H, Lee BW, Moon BJ, Ha YM, et al. Flame retardant epoxy derived from tannic acid as biobased hardener. ACS Sustain Chem Eng. 2019;7(4):3858–65. doi:10.1021/acssuschemeng.8b04851. [Google Scholar] [CrossRef]
74. Alderucci T, Borsellino C, Di Bella G, Favaloro F. Effect of temperature on curing time of single-lap adhesive joints in marine applications. In: Proceedings of the 1st Corrosion and Materials Degradation Web Conference; 2021 May 17–19; Basel, Switzerland: MDPI. doi:10.3390/CMDWC2021-10002. [Google Scholar] [CrossRef]
75. Kim JK, Lee DG. Effects of applied pressure and temperature during curing operation on the strength of tubular single-lap adhesive joints. J Adhes Sci Technol. 2004;18(1):87–107. doi:10.1163/156856104322747027. [Google Scholar] [CrossRef]
76. Mo X, Zhang X, Fang L, Zhang Y. Research progress of wood-based panels made of thermoplastics as wood adhesives. Polymers. 2021;14(1):98. doi:10.3390/polym14010098. [Google Scholar] [PubMed] [CrossRef]
77. Navarrete P. Characterization of two maritime pine tannins as wood adhesives. J Adhes Sci Technol. 2013;27(22):2462–79. doi:10.1080/01694243.2013.787515. [Google Scholar] [CrossRef]
78. Pizzi A, Meikleham N, Dombo B, Roll W. Autocondensation-based, zero-emission, tannin adhesives for particleboard. Eur J Wood Wood Prod. 1995;53(3):201–4. [Google Scholar]
79. Garcia R, Pizzi A, Merlin A. Ionic polycondensation effects on the radical autocondensation of polyflavonoid tannins: an ESR study. J Appl Polym Sci. 1997;65(13):2623–33. doi:10.1002/(ISSN)1097-4628. [Google Scholar] [CrossRef]
80. Garcia R, Pizzi A. Polycondensation and autocondensation networks in polyflavonoid tannins. II. Polycondensation versus autocondensation. J Appl Polym Sci. 1998;70(6):1093–109. doi:10.1002/(ISSN)1097-4628. [Google Scholar] [CrossRef]
81. Dhawale PV, Vineeth SK, Gadhave RV, Fatima MJJ, Supekar MV, Thakur VK, et al. Tannin as a renewable raw material for adhesive applications: a review. Mater Adv. 2022;3:3365–88. doi:10.1039/D1MA00841B. [Google Scholar] [CrossRef]
82. Meikleham N, Pizzi A, Stephanou A. Induced accelerated autocondensation of polyflavonoid tannins for phenolic polycondensates. I. 13C-NMR, 29Si-NMR, X-ray, and polarimetry studies and mechanism. J Appl Polym Sci. 1994;54(12):1827–45. doi:10.1002/app.07.v54:12. [Google Scholar] [CrossRef]
83. Pizzi A. Recent developments in eco-efficient bio-based adhesives for wood bonding: opportunities and issues. J Adhes Sci Technol. 2006 Jan 1;20(8):829–46. doi:10.1163/156856106777638635. [Google Scholar] [CrossRef]
84. Ping L, Pizzi A, Guo ZD, Brosse N. Condensed tannins extraction from grape pomace: characterization and utilization as wood adhesives for wood particleboard. Ind Crops Prod. 2011;34(1):907–14. doi:10.1016/j.indcrop.2011.02.009. [Google Scholar] [CrossRef]
85. Dababi I. Water extraction of tannins from aleppo pine bark and sumac root for the production of green wood adhesives. Molecules. 2020;25(21):5041. doi:10.3390/molecules25215041. [Google Scholar] [PubMed] [CrossRef]
86. Chen X, Pizzi A, Zhang B, Zhou X, Fredon E, Gerardin C, et al. Particleboard bio-adhesive by glyoxalated lignin and oxidized dialdehyde starch crosslinked by urea. Wood Sci Technol. 2021;56:63–85. [Google Scholar]
87. Alkan ÜB, Kızılcan N, Bengü B. Urea glyoxal and urea melamine glyoxal wood adhesives hardened with acid ionic liquid for particleboard pressing. Eur J Wood Wood Prod. 2022;80(4):961–73. doi:10.1007/s00107-022-01811-9. [Google Scholar] [CrossRef]
88. Sutiawan J, Hadi YS, Nawawi DS, Abdillah IB, Zulfiana D, Lubis MAR, et al. The properties of particleboard composites made from three sorghum (Sorghum bicolor) accessions using maleic acid adhesive. Chemosphere. 2022;290:133163. doi:10.1016/j.chemosphere.2021.133163. [Google Scholar] [PubMed] [CrossRef]
89. Nurdin H, Hasanuddin, Waskito, Kurniawan A. Particle board made from areca fiber with tapioca adhesive. J Phys Conf Ser. 2020;1594(1):1–7. [Google Scholar]
90. Xi X, Pizzi A, Amirou S. Melamine-glyoxal-glutaraldehyde wood panel adhesives without formaldehyde. Polymers. 2018;10(1):1–19. [Google Scholar]
91. Zhao Z, Umemura K. Investigation of a new natural particleboard adhesive composed of tannin and sucrose. J Wood Sci. 2014;60(4):269–77. doi:10.1007/s10086-014-1405-3. [Google Scholar] [CrossRef]
92. Tian W, Wang X, Ye Y, Wu W, Wang Y, Jiang S, et al. Recent progress of biomass in conventional wood adhesives: a review. Green Chem. 2023;25:10304–37. doi:10.1039/D3GC03441K. [Google Scholar] [CrossRef]
93. Rhazi N, Oumam M, Sesbou A, Hannache H, Charrier-El Bouhtoury F. Physico-mechanical properties of plywood bonded with ecological adhesives from Acacia mollissima tannins and lignosulfonates. EPJ Appl Phys. 2017;78(3):1–6. doi:10.1051/epjap/2017170067. [Google Scholar] [CrossRef]
94. Zhang J, Wang X, Zhang S, Gao Q, Li J. Effects of melamine addition stage on the performance and curing behavior of melamine-urea-formaldehyde (MUF) resin. BioResources. 2013;8(4):5500–14. doi:10.15376/biores.8.4.5500-5514. [Google Scholar] [CrossRef]
95. Deng S, Du G, Li X, Xie X. Performance, reaction mechanism, and characterization of glyoxal–monomethylol urea (G–MMU) resin. Ind Eng Chem Res. 2014;53(13):5421–31. doi:10.1021/ie404278d. [Google Scholar] [CrossRef]
96. Younesi-Kordkheili H. Some of physical and mechanical properties of particleboard panels bonded with phenol- lignin-glyoxal resin. J Adhes. 2020;96(16):1385–95. doi:10.1080/00218464.2019.1600405. [Google Scholar] [CrossRef]
97. Emmanuel S. Biobased phenolic adhesive using unmodified lignin and glyoxal. USA: Michigan State University; 2020. p. 1–14. [Google Scholar]
98. Younesi-Kordkheili H, Pizzi A. Acid ionic liquids as a new hardener in urea-glyoxal adhesive resins. Polymers. 2016;8(3):57. doi:10.3390/polym8030057. [Google Scholar] [PubMed] [CrossRef]
99. Gonçalves D. Non-formaldehyde, bio-based adhesives for use in wood-based panel manufacturing industry—a review. Polymers. 2021;13(23):4086. doi:10.3390/polym13234086. [Google Scholar] [PubMed] [CrossRef]
100. Jia L, Chu J, Li J, Ren J, Huang P, Li D. Formaldehyde and VOC emissions from plywood panels bonded with bio-oil phenolic resins. Environ Pollut. 2020;264(3):114819. doi:10.1016/j.envpol.2020.114819. [Google Scholar] [PubMed] [CrossRef]
Cite This Article
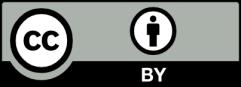
This work is licensed under a Creative Commons Attribution 4.0 International License , which permits unrestricted use, distribution, and reproduction in any medium, provided the original work is properly cited.