Open Access
REVIEW
A Review on the Advancement of Renewable Natural Fiber Hybrid Composites: Prospects, Challenges, and Industrial Applications
1 Center of Excellence Geopolymer & Green Technology (CEGeoGTech), Universiti Malaysia Perlis, Arau, 02600, Malaysia
2 Faculty of Chemical Engineering Technology, Universiti Malaysia Perlis (UniMAP), Arau, 02600, Malaysia
3 Department of Materials Engineering, University of Technology, Baghdad, 10070, Iraq
4 Department of Chemical Materials, University of Bagdad College of Education for Pure Science Ibn-Alhaitham, Baghdad, 10001, Iraq
5 Department of Computer Techniques Engineering, Al-Rafidain University College, Baghdad, 10001, Iraq
6 Faculty of Electronics Engineering Technology, Universiti Malaysia Perlis, Kampus Uniciti Alam Sg. Chuchuh, Perlis, 02100, Malaysia
7 Research Center (NANOCAT), University of Malaya, Kuala Lumpur, 50603, Malaysia
8 Institute of Nano Electronic Engineering, Universiti Malaysia Perlis, Perlis, 01000, Malaysia
9 Center for Global Health Research, Saveetha Medical College & Hospital, Saveetha Institute of Medical and Technical Sciences (SIMATS), Tamil Nadu, 602 105, India
* Corresponding Author: Mohammed Mohammed. Email:
(This article belongs to the Special Issue: Natural Fibre Reinforced Polymer Composites: Processing, Manufacturing, Characterizations and Environmentally Friendly Applications)
Journal of Renewable Materials 2024, 12(7), 1237-1290. https://doi.org/10.32604/jrm.2024.051201
Received 29 February 2024; Accepted 13 June 2024; Issue published 21 August 2024
Abstract
Natural fibre (NFR) reinforced functional polymer composites are quickly becoming an indispensable sustainable material in the transportation industry because of their lightweight, lower cost in manufacture, and adaptability to a wide variety of goods. However, the major difficulties of using these fibres are their existing poor dimensional stability and the extreme hydrophilicity. In assessing the mechanical properties (MP) of composites, the interfacial bonding (IB) happening between the NFR and the polymer matrix (PM) plays an incredibly significant role. When compared to NFR/synthetic fibre hybrid composites, hybrid composites (HC) made up of two separate NFR are less prevalent; yet, these hybrid composites also have the potential to be valuable materials in terms of environmental issues. A new dimension to the flexibility of composites reinforced with NFR is added by the cost-effective manufacture of hybrid composites utilising NFR. The purpose of this study is to offer an overview of the key findings that were presented on hybrid composites. The emphasis was focused on the factors that influence the performance of the natural fiber composites, diverse approaches to enhancing MP, physical, electrical, and thermal characteristics of the HC. HC study in polymer science gains interest for applications in construction and automotive industries.Graphic Abstract
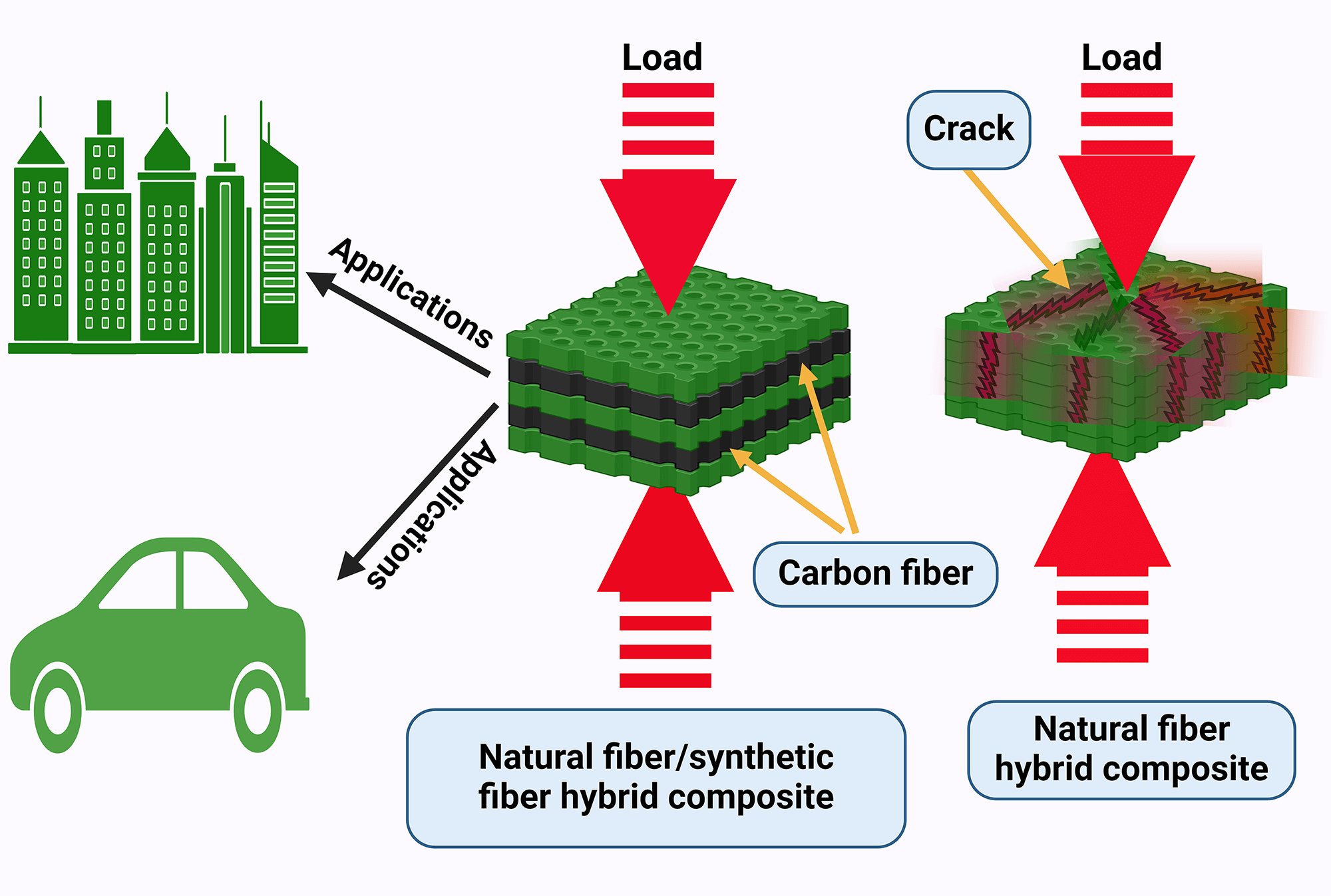
Keywords
Nomenclature
NFR | Natural fibre |
MP | Mechanical properties |
IB | Interfacial bonding |
PM | Polymer matrix |
HC | Hybrid composites |
As per Akter et al.’s [1] research, increasing environmental activism, the imperative to protect natural resources, and the increasing severity of regulations enacted by developing nations have all contributed to the inception and growth of natural materials that emphasize the use of renewable resources. All of these aspects were important contributors to the discovery and advancement of natural materials [2–4]. Companies that manufacture composites need to look for plant-based NFR reinforcements such as flax, hemp, sisal, kenaf, and banana in order to provide an alternative to solid wood as a material that will be used in their products. These are all examples of plant-based natural fibres. The fact that lignocellulosic fibres are made from renewable resources that also have a strong attraction to consumers gives them an edge. NFR reinforced polymer composites have been utilized in a broad variety of uses and purposes, including the automotive and aerospace industries, the sports goods market, and the construction sector. “Recent years” have seen “increased application” of NFR reinforced polymer composites in the construction of bridges and buildings [5,6]. Their popularity stems from the beneficial attributes of these materials, such as their lightweight nature, superior strength, outstanding formability, and strong resistance to corrosion and fatigue.
Cotton, pulp, bark, wood, bagasse, and vegetables are some of the numerous forms of natural fibres that may be distinguished from one another based on their respective sources. Cellulose, hemicelluloses, pectins, lignin, and a trace amount of extractives make up the majority of these natural fibres [7,8]. Fig. 1 is a diagrammatic representation of the structural organisation of the three principal elements of the fibre cell wall. The many types of natural fibres are broken out in Fig. 2. Natural fibers, when compared to synthetic ones, provide several benefits including wide availability, cost-effectiveness, recyclability, renewability, biodegradability, low density, advantageous aspect ratios, and considerable strength [9,10]. Natural fibres also have a desirable aspect ratio and moderate strength. NFR composites have the potential to be a material that is both cost-efficient and environmentally friendly, particularly when it comes to automotive body panels, interior designs, construction and industrial panels, as well as false ceilings [11,12].
Figure 1: Chemical structure of natural fiber. The major components are indicated
Figure 2: Subdivision of natural fibers on the basis of origin. Potential preparations from the parts of plants are shown
Biofibers such as oil palm, kenaf, industrial hemp, flax, jute, wood, and multiple grasses are mixed with polymer matrices sourced from both non-renewable (petroleum-based) and renewable resources to manufacture composite materials. The last 10 years have seen a rise in interest in biocomposites due to their ability to compete well with synthetic composites such as glass-polypropylene and glass-epoxy mixtures. It has been shown that hybrid composites that are reinforced with cellulosic fibres may also display high mechanical characteristics [13,14]. These hybrid composites are quite frequently mixed with synthetic fibres such as glass fibres. Polymer composites with hybrid reinforcement that are purely composed of NFR are not very common; yet, these materials hold promise in tackling environmental issues effectively [15–17].
In addition, Plastics are by far the most popular alternative to wood products among the many different materials that may be manufactured. Plastics are used in almost every industry, ranging from simple household products to intricate engineering components. On the other hand, plastics are non-renewable and non-biodegradable [18]. Because the price of petroleum-based products is always going up and there is a shortage of these resources, it is necessary to find adequate alternatives in order to be ecologically conscious. Concerns like the possibility of biodegradation and recycling play a crucial part in the development of novel materials and goods. Natural fibres, as opposed to synthetic fibres, offer numerous advantages concerning both technological and environmental aspects [19,20]. The differences and similarities between NFR and glass fibres are laid out in Table 1.
Natural-synthetic fiber hybrid composites can provide better thermal, electrical, and acoustic properties in addition to their mechanical and environmental benefits [21]. For example, an HC constructed from NFR and carbon fibers can have excellent thermal conductivity, making it useful in applications where heat dissipation is important. Hybrid composites can also be engineered to have specific electrical properties, making them suitable for use in electronic components. Additionally, hybrid composites (HC) combining natural and synthetic fibers can be tailored to meet specific design requirements. By adjusting the fiber types, orientations, and proportions, it is possible to create materials that have the desired properties for a particular application [22]. This design flexibility makes hybrid composites particularly attractive for use in niche markets, where there may be a need for specialized materials with unique properties. Employing NFR-synthetic fiber HC also holds promise for diminishing the environmental footprint of manufacturing procedures. By substituting traditional materials with eco-friendly composites, it is possible to reduce the amount of waste generated and minimize the use of non-renewable resources. The significance of HC stems from its capability to offer a distinctive set of attributes unattainable with single-fiber composites [23]. They offer improved mechanical performance, reduced costs, and increased sustainability, making them an attractive option for a variety of applications. With ongoing research and development in the field, one can anticipate a growing array of innovative applications for these versatile materials [24].
The primary objective of this study is to provide a synopsis of the information that is currently known about the MP of HC. In the early stages, the discourse will include an examination of morphological attributes, structural components, various approaches to improve mechanical properties, and determinants that impact the properties of composites. Following this, a thorough investigation of the thermal and electrical characteristics of NFR composites and hybrids of these materials was carried out. The last topic is the practical use of NFR-reinforced hybrid composites, followed by a discussion of potential future developments. Table 2, presented below, offers a concise overview of the pros and cons associated with natural fiber composites.
2 Components of Natural Fibre Composites
Natural fibers are integral components of composite materials, functioning as the reinforcing phase that bestows the composite with distinct mechanical, thermodynamic, and environmental characteristics [3]. These fibers, which are obtained from a variety of sources including plants, animals, and minerals, provide a number of beneficial qualities that enhance those of the matrix material. Primarily, natural fibers improve the rigidity, strength, and impact resistance of composites, thereby enhancing their mechanical performance [4]. The intrinsically elevated tensile strength of these materials, specifically in regard to fibers such as flax, hemp, or jute, serves to fortify the composite framework, facilitating the efficient dispersion of strain and enhancing its capacity to sustain loads. Furthermore, the orientation and alignment of natural fibers within the matrix can be modified to maximize mechanical properties, thereby enhancing the composite material’s overall performance. In addition, natural fibers provide environmental advantages, which corresponds to the increasing market demand for sustainable and ecologically conscious materials. Originating from sustainable sources, these textiles possess the advantageous qualities of being biodegradable and recyclable, which positions them favorably among sectors endeavoring to diminish their ecological impact. Additionally, their diminished density aids in the formation of lightweight composite structures, which are highly sought after in sectors such as aerospace and automotive where weight reduction is of the utmost importance [4–6].
When considering the matrix materials utilized in the fabrication of composites, thermosetting and thermoplastic polymers are both extensively utilized. When heated, thermosetting resins (e.g., polyester, phenolic, and epoxy) endure irreversible curing reactions that result in the formation of a crosslinked network [8]. This network imparts the composite with superior mechanical properties and dimensional stability. For applications requiring resistance to high temperatures and superior mechanical performance, these resins are favored. Conversely, thermoplastic polymers, such as polypropylene, polyethylene, and polycarbonate, provide several benefits, including robustness, recyclability, and processing simplicity [9]. By virtue of their resistance to chemical degradation, these materials can be repeatedly transformed and melted, facilitating streamlined production processes and potentially enabling recycling at the conclusion of the product’s life cycle [11]. Numerous factors, including desired mechanical properties, processing specifications, cost considerations, and end-use applications, influence the selection of matrix material [16]. Through meticulous fiber selection and combination with suitable matrix materials, researchers and engineers possess the ability to customize composite materials in order to fulfill particular performance requirements while simultaneously adhering to sustainability objectives.
A composite is a material combination that is typically produced by a synthetic or natural assemblage of two or more components that are unique from one another both physically and chemically. The initial component consists of a specific filler or reinforcing agent, known as the discontinuous phase, while the secondary element is a matrix binder that is compatible with the first component. The purpose of combining these two components is to attain particular qualities and attributes [25]. Various unique types of NFR, matrices, and processing methods are employed in the production of composites.
2.1 Mechanical Properties of Natural Fibres
Natural fibers, which exemplify the resourcefulness of nature, have an inherent appeal that transcends their aesthetic value. These filaments, which have been intricately woven over time by the hand of evolution, contain an abundance of mechanical properties that intrigue both scientists and engineers. Commencing an exploration of the captivating domain of natural fibers unveils a realm where the convergence of durability, adaptability, and strength culminates in a magnificent display of material expertise. At the heart of natural fibers lies an exquisite balance of tensile strength and flexibility, virtues honed over millennia of evolutionary refinement. From the sinewy sinews of flax to the resilient tendrils of hemp, each fiber exhibits a unique blend of mechanical prowess, forged through the crucible of nature’s ceaseless innovation. Furthermore, the natural fibers’ hierarchical structure provides an ideal foundation for an intricate web of mechanical marvels. At the macroscopic level, fibers exhibit exceptional tensile strength, which enables them to withstand tremendous burdens without undergoing deformation. However, a more thorough analysis reveals that they possess an immense amount of resilience due to the intermolecular bonds and crystalline domains that collaborate to reinforce their structural integrity. Moreover, natural fibers exhibit an innate capacity for moisture absorption and thermal regulation, attributes that imbue them with unparalleled versatility in a myriad of applications. Whether reinforcing composite materials or adorning haute couture, natural fibers seamlessly adapt to the demands of their environment, embodying the epitome of sustainable elegance [26–28].
NFR derived from plants are lignocellulosic by their very nature and are constructed of components such as cellulose, hemicelluloses, lignin, pectin, and waxy compounds. Table 3 provides an overview of the structural components that make up fibres. Cellulose is regarded as the principal component of the framework that makes up the fibre structure. It gives the fibre strength and rigidity, which contribute to its structural stability. The chemical structure of cellulose is composed of three hydroxyl (OH) groups. Two of them make hydrogen bonds inside the cellulose macromolecules, which is referred to as an intramolecular hydrogen bond, while the remainder of the group establishes hydrogen bonds with other cellulose molecules, which is referred to as an intermolecular hydrogen link [26]. Hemicellulose primarily exists in the main cell wall and consists of branched polymers with diverse chemical structures incorporating five and six carbon sugars. Lignin is amorphous and features an aromatic structure [27,28]. Pectin is composed of intricate polysaccharides with side chains cross-linked by calcium ions and arabinose sugars. Furthermore, the fiber structure contains minor amounts of organic (extractives) and inorganic (ash) components. The colour, odour, and decay resistance of a fibre may be attributed to organic extractives, whereas the abrasive quality of the fibre can be enhanced by inorganic elements. The concept of the structural arrangement of the three fundamental structural components comprising the cell wall of a natural fiber is illustrated in Fig. 3, which contains micrographs of the fiber’s structure. Fig. 4 is a diagrammatic representation of the NFR. Cellulose microfibrils, which are the building blocks of cellulose, each have their own unique cell shape, which is one of the contributing factors that determine the characteristics of the fibre [29]. The cellulose microfibrils that make up the primary and secondary layers of each fibre cell wall are what make up each fibre cell wall. The main cell wall is responsible for the development of the fibre structure, which is then deposited as the cell wall continues to expand. The secondary wall is composed of three layers, with a protracted sequence of helical cellulose microfibrils situated within each layer [30].
Figure 3: SEM micrographs showing natural fiber composition. Lumen and walls are indicated
Figure 4: Diagrammatic depiction of natural fiber composition. The representative parts are displayed
The percentage of cellulose continuously rises as one move from the primary to the secondary layers, but the proportion of hemicellulose remains relatively constant throughout. Lignin content, on the other hand, drops as you go through this process. The formation of cementing materials for the fibre structure is accomplished by the creation of hydrogen bonds between molecules of hemicellulose and fibrils of cellulose. Pectin and lignin are attached to the cellulose and hemicellulose networks, which gives the network an adhesive characteristic that keeps the molecules together. Because of its adhesive characteristics, the fibre has both a high level of strength and a high level of stiffness. The secondary thick layer, often known as S2, is what defines the fibre’s mechanical characteristics. In general, NFR with a greater cellulose content and a smaller microfibrillar angle (the angle between the fibre axis and cellulose microfibrils) have superior qualities in terms of their tensile strength [31–34]. The distinct modulus and elongation at break of NFR suggest their potential to supplant synthetic fibers in engineering polymer composites. Despite the considerably lower strength characteristics of natural fiber reinforced (NFR) materials compared to synthetic fibers, their potential remains undeniable.
A matrix serves as a binding material that maintains the fibers in place and transfers external forces to internal reinforcements. Thermoset and thermoplastic matrices are widely utilized in NFR reinforced polymer composites for various functions [35,36]. Examples of thermoset matrices include unsaturated polyesters, epoxies, and phenolics, while examples of thermoplastic matrices include polypropylenes, polyethylenes, and elastomers. These matrices each have their own unique chemical structure, and their interactions with the surface molecules of the fibres that make up composites may take a variety of forms. Matrix creates a considerable impact on the MP of composites because it performs a significant part in (a) holding the fibers at its place, (b) fiber protection from the environmental changes, (c) stress transfer among the fibers, (d) orienting the fibers, and (e) providing the texture, color and surface quality [37]. Matrix material should be carefully selected to achieve good interfacial bonds between the matrix and fibers. An adequate number of matrix-fiber interactions results in achieving better mechanical properties. Weak interface results in fiber pull out, fiber breakage, cracks in the matrix materials. Matrix material should be selected based on its compatibility with the fibers. The matrix should be thermally compatible to avoid the formation of residual stresses occurred due to variance in the thermal expansion of matrix and fibers. Good fiber-matrix IB shows the physical compatibility of the matrix material. The differences and similarities between thermoset and thermoplastic matrices are laid forth in Table 4. Fig. 5 shows the classification of composites based on materials.
Figure 5: Categorization of composite materials based on matrix and reinforcement
Production techniques specifically designed for natural fiber composites combine the elegance of conventional handiwork with the accuracy of contemporary engineering. These techniques skillfully utilize the inherent qualities of natural fibers and skillfully incorporate them into intricate structures. These methods, which embrace adaptability and sustainability, open the door to environmentally responsible innovation in materials science. One such process is compression molding, an age-old technology that forms a composite mixture under extreme heat and pressure to create a finished product that is both elaborately patterned and robust. Optimal dispersion within the matrix and improved mechanical qualities are fostered by this approach, which takes use of the pliability and robustness of natural fibers [38].
Natural fiber composites are expertly shaped into a variety of shapes via extrusion, another manufacturing mainstay, from thin profiles to complex geometries. Extrusion carefully regulates temperature and pressure to bring fibers and matrices into a harmonious union, producing products that are remarkably resilient and strong. Utilizing state-of-the-art technology, novel techniques such as vacuum infusion and resin transfer molding (RTM) allow natural fibers to be mixed with resins to create composite structures that are incredibly precise and consistent. By carefully balancing the flow dynamics of resins with the permeability of natural fibers, these techniques produce items that are both aesthetically pleasing and highly engineered. In general, the processing methods for NFR composites are conceptually comparable to the processing methods used for processing synthetic fibres. Reinforcements may be made out of fabrics that are either randomly oriented (short), unidirectional (raw and carded), or woven. These types of fabrics can be utilised in either thermoset or thermoplastic matrices. The kind of reinforcement employed relies on the length of the fibre, its orientation, and the type of fibre. “hand layup” is the term used to describe the fundamental production procedure for thermoset composites [38]. The fibre and the matrix will be mixed together by hand at this step of the process. The level of craftsmanship used in this process determines the degree to which the composite will be homogeneous across the sample with regard to its thickness, the ratio of fibres to matrix, and the amount of empty space.
Pultrusion is an additional process that may be utilised for both thermosets and thermoplastics [39]. In the field of composite production, pultrusion stands out as a superb combination of artistic expression and technical accuracy. This painstaking procedure, well regarded for its adaptability and efficiency, embraces thermosets as well as thermoplastics, offering countless opportunities for material synthesis and structural design. At its core, pultrusion embodies a symphony of controlled forces and meticulous attention to detail. Fibers, meticulously arranged in precise orientations, embark on a transformative journey through a resin bath, where they become ensconced in a matrix of polymers, entrusting their strength and resilience to the alchemy of chemical bonding. Pultrusion, at its essence, comprises a harmonious integration of regulated forces and scrupulous attention to detail. Fibers, which have been arranged in exact orientations with great attention to detail, undergo a profound transformation as they are submerged in a resin bath. Within this matrix of polymers, the fibers place their strength and resilience in the hands of chemical bonding. Moreover, the versatility of pultrusion transcends conventional boundaries, offering a canvas upon which designers and engineers may unleash their creativity with unrestrained fervor. From slender rods to intricate profiles, pultrusion molds the raw essence of materials into captivating shapes and structures, each bearing the indelible imprint of meticulous craftsmanship and technological prowess [39,40]. The production of the composite profile is achieved when the reinforcement is drawn through a heated die and then fused with the matrix. Composite fabrication utilizes both compression molding, which involves merging the reinforcement with the matrix before pressing it with a heated plate, and injection molding, where granules of fiber-resin are loaded into the machine, melted into a liquid mass, and then forcibly injected into the mold under high pressure [40]. These procedures require elevated temperatures (above 200°C) and high pressures (5 MPa) for the accomplish reaction between the NFR and the PM. Fig. 6 depicts the process of pultrusion.
Figure 6: Schematic representation of pultrusion process. The complete steps are shown
Furthermore, the manufacture of natural fiber composites has a fascinating new horizon thanks to additive manufacturing, which has limitless creative potential. Through the meticulous layering of fibers and resins, additive manufacturing surpasses traditional constraints, providing designers with unmatched flexibility to actualize their ideas while reducing waste and optimizing productivity. The production techniques developed specifically for natural fiber composites are, in essence, a harmonious union of tradition and innovation; they combine traditional craftsmanship with state-of-the-art technology to create a future that is both resilient and sustainable. These techniques serve as guiding lights of inventiveness as we make our way through the complex field of materials science, leading us toward a future where form and function coexist peacefully.
3 A Summary of Hybrid Polymer Composites Strengthened with Natural Fibers
A hybrid composite material is defined as the amalgamation of two or more reinforcing components in a single matrix, or a blend of multiple matrices with a single reinforcing component. The physical attributes and MP of HC are impacted by various elements such as the fiber aspect ratio, individual fiber attributes, fiber orientation, individual fiber length, IB between the fiber and the PM, and the stacking order of both fibers [41]. The characteristics of HC comprising two elements can be calculated using the rule of mixtures [42], as demonstrated in Eqs. (1) and (2).
In this case, PH represents the property under examination, while P1 and P2 correspond to the respective characteristics of the first and second elements. V1 and V2 denote the volume fractions of the first and second elements, respectively. Most of the research concerning NFR reinforced HC aims to examine the strength attributes in correlation to factors like fiber loading, fiber length, fiber dispersion, fiber alignment, the sequence of fiber layering, the impact of different chemical modifications on NFR, the application of coupling agents, choice of PM, and the interaction between NFR and PM. These studies aim to improve the understanding of how strength varies based on these factors. Researchers [43] examined the influence of fiber loading, ratio, and chemical modification on the MP of sisal and oil palm fiber reinforced natural rubber hybrid composites. It was determined that the longitudinal direction of the composite had the greatest amount of its mechanical qualities, as opposed to the transverse direction. After the fibres were treated with alkali, it was discovered that the IB strength between the natural fibre and the rubber matrix increased. Therefore, the alkali treated fibres displayed the highest possible tensile strength in comparison to the untreated fibre composites.
The hybrid composites were made by combining three distinct fibres, including sisal, jute, and glass, with an epoxy resin in a weight ratio of 30:70 between the fibres and the matrix [44]. A variety of different combinations of composite materials were manufactured in alignment with the ASTM standard and then subjected to tests to determine their mechanical qualities, such as tensile and impact strengths. In comparison to other combinations, the tensile and impact strengths of the HC made of sisal, glass, and epoxy were determined to be the highest. The MP of silk fabric reinforced epoxy composites have been examined, and a minor quantity of glass fibre has been found to be present. The MP of the silk fibre reinforced composites were significantly enhanced by including a trace amount of glass fabric in the mixture. According to the findings, the improvement in the material’s mechanical characteristics was proportional to the weight fraction of fibre content’s greatest degree of increase. They also discovered that the process of hybridization resulted in a decrease in the composites’ ability to absorb water [45].
As a function of the volume percentage of fibre, the luffa fibre and ground nut reinforced epoxy HC that were made by hand lay-up processes. They discovered that composites with a treated fibre content of 40% displayed greater levels of maximal mechanical characteristics than luffa groundnut polymer composites with fibre percentages of 30% and 50%, respectively. Because there was inadequate wetting between the NFR and the PM, the strength was found to be lowest when the fibre content was 50% [46]. The oil palm empty fruit bunches and jute fibres strengthen epoxy matrix HC have been put through a tensile test. When compared to oil palm empty fruit bunches fibres employed by themselves, the tensile strength and modulus of oil palm empty fruit bunches/jute fibre HC were shown to have significantly improved. During the SEM investigation, the hybrid composites demonstrated superior adherence to the matrix in comparison to the pure oil palm empty fruit bunches fibre composite [47].
The term “hybrid” has its roots in both Greek and Latin, and it is now used in a wide variety of scientific contexts. When it comes to polymer composites, HC are defined as these types of systems in which either one kind of reinforcing material is inserted in a combination of multiple matrices (blends) [48], two or more reinforcing and filling materials are exist within a single matrix [49,50], or both techniques are combined. The production of hybrid composites has been made possible via the combination of two or more kinds of lignocellulosic fibres with a single matrix. The performance of HC may be thought of as the weighted total of the separate components, with the goal being to strike a more advantageous balance between the inherent benefits and drawbacks of each component. When utilizing a HC that consists of two or more different forms of fibre, the benefits of one type of fibre may be able to supplement what are missing in another type of fibre. As a direct result of this, it is possible, with the use of appropriate material design, to strike a balance between cost and performance [51]. The robustness of HC is dependent on several elements including the properties of the fiber, the ratio of fiber content in relation to its aspect, the individual fiber length, direction of fiber alignment, the degree of fiber intertwining, the IB between fiber and PM, and the configuration of both fibers, not forgetting the stress level at which each fiber breaks. The hybrid outcomes are maximised when the fibres are extremely compatible with one another in terms of strain [52].
5 Influential Factors on Composite Characteristics
The cellulose structure of fibers consists of both crystalline and amorphous regions, which can be distinguished from one another. The crystallite region facilitates the formation of numerous strong hydrogen bonds within the molecules, leading to the creation of cellulose blocks that are more resistant to penetration by other chemicals. Conversely, the amorphous region demonstrates a high capacity for absorbing colors and resins. Fig. 7 illustrates the schematic representations of crystalline and amorphous region of cellulose. Water molecules from the surrounding environment mingle with hydrophilic hydroxyl groups that are existing in this region. These water molecules may be stored in a normal condition by substances including hemicellulose, lignin, pectin, and waxy substances. As a result, the fibre develops hydrophilic and polar properties, which lessens its compatibility with the non-polar and hydrophobic matrix [53–55]. In order to obtain the desired results with natural fibre, chemical modification is required. These effects include the enlargement of the crystalline area, the elimination of the hydrophilic hydroxyl groups, and the cleaning of surface impurities (waxy substances). Chemical modifications such as mercerization, acetylation, benzoylation, and coupling agents are frequently employed, either with or without the application of heat, in order to modify the surface of the NFR as well as the structure of the NFR.
Figure 7: Schematic representations of crystalline and amorphous region of cellulose
5.2 Thermal Stability of Fibres
Thermal stability is a crucial property of natural fibers, as it determines their ability to withstand or resist decomposition at elevated temperatures. NFR such as cotton, flax, hemp, jute, sisal, and silk are commonly utilized in various applications, including textiles, automotive, construction, and composite materials. In this scenario, comprehending the thermal stability of these fibers is crucial [56]. In most cases, the temperature at which natural fibre begins to degrade is about 240°C. The structural components of the NFR, such as cellulose, hemicelluloses, and lignin, among other things, are sensitive to a wide range of temperatures. According to some reports, the degradation of lignin begins at a temperature of around 200°C, whereas the degradation of hemicelluloses and cellulosic components occurs at higher temperatures [57]. It is possible to improve the fibre’s thermal stability by eliminating a particular amount of the hemicelluloses and lignin elements of the material using one of many different chemical treatments. Both throughout the production process (curing, extrusion, or injection moulding), as well as when the composites are being used in service, the degradation of NFR might be a significant problem for the progression of composites [58,59]. Fig. 8 demonstrates the degradation steps and their effect on the natural fiber.
Figure 8: The degradation steps and their impact in natural fiber polymer composite
Numerous elements influence the thermal stability of NFR, including their chemical composition, crystallinity, and moisture content.
• Chemical composition: NFR are predominantly composed of cellulose, hemicellulose, lignin, pectin, and waxes. Cellulose contributes to the fiber’s strength and stiffness, while hemicellulose and lignin provide thermal stability. The ratio of these components varies across different natural fibers, thus affecting their thermal stability. Generally, fibers with higher cellulose and lignin content exhibit better thermal stability [60].
• Crystallinity: The degree of crystallinity in natural fibers impacts their thermal stability. Higher crystallinity results in improved thermal stability due to the increased organization of cellulose chains, making it more difficult for them to degrade when exposed to heat. Fibers with a higher degree of crystallinity, such as flax and hemp, exhibit better thermal stability than those with a lower degree of crystallinity, like cotton and jute [61].
Moisture content: Natural fibers tend to absorb moisture from the surrounding environment, which can influence their thermal stability. High moisture content can lead to a lower thermal stability, as the absorbed water can act as a plasticizer and weaken the fiber structure. Hence, it is crucial to take into account the moisture content of NFR when assessing their thermal stability [62].
5.3 Fibre Length, Loading and Orientation
Natural fibers possess unique properties that make them suitable for various applications, particularly in composite materials. Three key aspects that influence their performance are length, loading, and orientation. The length of natural fibers affects their MP, such as tensile strength and stiffness. Longer fibers have better stress transfer and load-bearing capabilities due to the increased aspect ratio, which is the ratio of length to diameter. However, longer fibers can also lead to difficulties in processing and handling. Therefore, an optimal fiber length needs to be determined based on the specific application and composite requirements [63]. In addition, the amount of fibers incorporated into a composite, also known as the fiber loading, significantly impacts the overall mechanical properties [64,65]. Higher fiber loading generally leads to increased stiffness and strength of the composite, since a bigger proportion of the load is carried by the fibres. However, too much fiber can also compromise the material’s durability and workability. Consequently, it is crucial to balance fiber loading to attain the required characteristics without compromising the composite’s performance [66]. Furthermore, the direction and alignment of fibers within the matrix can greatly influence the MP of the composite. Unidirectional fibers, where all fibers are aligned in a single direction, can provide high strength and stiffness along the alignment direction but may lack in other directions. On the other hand, random or multidirectional fiber orientation can offer more balanced properties across all directions, but at the expense of overall strength and stiffness. Designers need to consider the specific application and stress distribution requirements when selecting the appropriate fiber orientation for a composite material [67]. These factors need to be carefully considered and optimized for each specific application to ensure the best possible results [68–70]. Fig. 9 shows classification of composite materials based on type of reinforcement. Fig. 10 shows schematic view of composite reinforcements.
Figure 9: Classification of composite materials based on type of reinforcement
Figure 10: Schematic view of composite reinforcements: (A) unidirectional continuous fibers (B) multidirectional continuous fibers (C) bidirectional continuous fibers (D) aligned short fiber (E) random short fibers (F) particles
The existence of voids in natural fiber polymer composites can substantially impact the MP of these materials. Voids are empty spaces or air pockets that can form within the composite structure during processing or fabrication. These imperfections can arise due to various factors, such as fiber-matrix incompatibility, uneven distribution of NFR, insufficient wetting of NFR by the matrix, or the release of volatile components during curing. The presence of voids can lead to a decline in the overall strength and stiffness of the composite material [71]. Voids interrupt the load-bearing capacity of the NFR and compromise the fiber-matrix IB, which results in decreased stress transfer between the NFR and the PM. This can lead to premature failure of the material under load. Voids function as stress focal points, enhancing the probability of crack beginning and spread in the composite material. This results in a lower fracture toughness, making the composite more susceptible to failure under impact or fatigue loading conditions [72]. Furthermore, the presence of voids can negatively affect the long-term durability and efficiency of NFR composites [73]. Voids can allow the ingress of moisture, leading to fiber swelling, matrix degradation, and increased susceptibility to environmental factors such as UV radiation and temperature fluctuations. This can result in a reduced service life of the composite material. Voids can contribute to an increased coefficient of thermal expansion and reduced dimensional stability of the composite. This can cause problems in applications where tight tolerances and dimensional stability are required. There is a correlation between having a high void content (over 20% by volume) and having a poorer fatigue resistance, a stronger affinity to water diffusion, and an augment in the variance (scatter) in the MP [74,75]. When it comes to composites, a larger fibre content is associated with a greater risk of void formation [75]. Fig. 11 shows pictures taken at a microscopic level of the voids in natural fiber composites. To enhance the MP of NFR hybrid composites and minimize the presence of voids, proper processing techniques and material selection are crucial. For instance, ensuring good fiber-matrix compatibility, using suitable coupling agents or compatibilizers, optimizing fiber loading and distribution, and employing appropriate processing methods can significantly reduce void formation and improve the total effectiveness of NFR polymer hybrid composites.
Figure 11: SEM micrographs of voids in natural fiber composite
5.5 Moisture Absorption of Fibres
NFR, such as sisal, hemp, flax, and jute, have the inclination to absorb moisture from the surrounding atmosphere due to their hydrophilic nature. This moisture absorption can have several implications on the characteristics and performance of NFR-based materials and composites [76]. When NFR absorb moisture, they swell and can cause dimensional changes in the material [77–79]. This swelling can lead to undesirable warping or distortion in composite materials, affecting the dimensional stability and potentially causing problems in applications with strict dimensional tolerances [80,81]. As natural fibers swell, they can generate internal stresses within the composite material [82,83]. These stresses can lead to cracking or delamination in the composite, further affecting its structural integrity and performance [84]. Fig. 12 summarises this process. Moisture absorption can weaken the MP of NFR composites, such as tensile strength, stiffness, and impact resistance. This is due to the hydrolytic degradation of NFR and disruption of the fiber-matrix IB, leading to reduce stress convey between the NFR and the PM. Prolonged exposure to moisture can lead to biological degradation of natural fibers, such as mold growth or rot. This can further compromise the MP and durability of the material. Because of this, one of the most important steps in the process of preparing composites is the removal of moisture from the NFR. It is possible to lessen the amount of moisture that is absorbed by fibres by removing hydrophilic hydroxyl groups from the structure of the fibres using a variety of various chemical treatments [85].
Figure 12: Schematic representation of effect of water on fiber-matrix interface
Natural fibers, derived from plant or animal sources, possess a unique advantage over synthetic fibers due to their biodegradability. This characteristic makes them an eco-friendly option for a wide range of applications, as they can decompose naturally into simpler, environmentally benign components under suitable conditions [86]. A key advantage of employing biodegradable NFR is their diminished environmental footprint. Upon completing their lifespan, materials based on NFR can decompose into benign substances due to the activity of microorganisms like bacteria and fungi. This process helps to minimize waste accumulation in landfills and reduces the overall carbon footprint of the material [87]. The rate and extent of biodegradation of NFR can depend on various factors, including the fiber’s chemical composition, crystallinity, and the presence of lignin or other natural binders. Moreover, environmental circumstances, such as temperature, humidity, and the presence of microorganisms, can also influence the biodegradation process [88]. The terms “biological,” “chemical,” “mechanical,” “thermal,” “photochemical,” and “aqueous” all refer to different types of degradation processes. It is common practise to cite the biodegradability of cellulosic fibre as a positive characteristic that may be used to support the use of these fibres. However, it is required for the composites to remain usable for a number of years in order for them to be used in numerous outdoor applications. Controlling this natural deterioration is crucial in order to lengthen the amount of time they may be used effectively. Modifying the chemical composition of the cell wall is one method that may be used to stop or slow down the natural decomposition process. Thus, potential negative characteristics of cellulosic fibers, such as dimensional instability, flammability, biodegradability, and chemical degradation could be inhibited or decelerated [89,90]. By restricting the accessible OH group on the NFR surface, chemical treatments have the potential to minimise the amount of NFR swelling and biological degradation [91–93]. This is accomplished by lowering the quantity of water that is absorbed by the fibres. While the biodegradability of natural fibers is a desirable trait, it can also be a challenge in certain applications where long-term durability and resistance to environmental factors are required. Therefore, it is crucial to balance the biodegradable nature of natural fibers with their performance, particularly in uses where the material is subjected to humidity, changes in temperature, or other environmental strains. Proper treatments, protective coatings, and the use of HC can help to achieve this balance.
6 Diverse Approaches to Enhancing Mechanical Properties of Natural Fiber Composites
There are a number of different approaches that may be taken in order to augment the MP of NFR polymer composites. These approaches are not yet linear procedures that, if adopted, may result in considerable gains; rather, an active area that is now under development is working to enhance the material features of NFR polymer composites. It is not always the case that mechanical improvement in one application area would immediately provide the same outcome in another particular application. For instance, increasing the hardness of a material may have been ideal for the engineering and manufacturing sectors; however, this may not be essential or desired for medical applications, which may instead choose to increase its adaptability and longevity. Therefore, it will be provided with all possible possibilities, and it will be up to the analysts to pick the best one based on the circumstances. In addition, these strategies may be used in order to have a synergistic impact. The most important aspect that has a part in defining the MP of the NFR reinforced composite is broken down in Table 5.
6.1 Fibers Surface Modification
By using a wide variety of surface modification methods, it is possible to significantly mitigate the drawbacks associated with using natural fibres [94,95]. Surface modification techniques may take the form of either physical or chemical treatments. Examples of the former include plasma, ultrasound, and ultraviolet light, while examples of the latter include silane, alkali, acetylation, and benzoylation, as well as sodium chloride [96–98]. Fig. 13 is a schematic representation of the plasma treatment that is applied in order to remove surface impurities (the cleaning effect). The silane treatment of NFR is depicted pictorially in Fig. 14, which contains a schematic illustration of the process. Stretching, calendaring, and thermal treatment are all examples of physical processes that do not alter the chemical makeup of the NFR, but do modify the surface and structural qualities of the NFR, which in turn affects the way the fibre physically bonds to composites. Altering the fibres chemically, on the other hand, enhances their overall qualities as well as the amount of chemical features, which in turn improves their ability to absorb water when combined with a polymer matrix. In addition to this, it cleans the surface of the fibres, removing any undesired substances such as hemicelluloses, lignin, and pectin, which in turn helps to enhance the matrix adhesion [99–101].
Figure 13: Schematic representation of the plasma surface treatment
Figure 14: Schematic representation of silane treatment
Compatibilizers are additives that lower the surface tension of fibres, making it possible for relatively nonpolar polymer matrices to adhere to the fibres’ shape. Matrix enhancements, which are often accomplished by introducing binding substances and polymer matrix compatibilizers, may in fact lead to increases in the permeability and excitability of polymers. These matrix improvements can be obtained. The increased binding that occurs between the matrix and the reinforcement is mostly the result of the utilized of coupling agents. Gargol et al. [102] highlighted the importance of their work on the MP of NFR-Epoxy HC. The composite specimens that were chosen were then subjected to treatment and additional investigation into their mechanical behaviour. The mechanical characterisation showed that the characteristics had improved as a result of hybridization, with enhanced mechanical interlocking and a boost in mechanical strength standing out as the most significant alterations. The research highlights the significance of alkali treatment as well as the potential for improvement of physico-chemical and MP.
Chandrasekar et al. [103] looked at the mechanical characteristics of NFR composites as well as their ability to absorb water. In this paper, the outcomes of studies on the swelling, moisture resistance, and chemical behaviour of composites are discussed, with a primary focus on the materials’ mechanical characteristics. As a result, tests were conducted to examine the material’s bending strength, tensile strength, compression resistance, and thermal stability. It should also be emphasised that, when exposed to high temperatures, polymer composites exhibited a level of stability that was significantly inferior to that of parent resin matrix composites.
Polymer blends can be described as a fusion of two or more polymers, designed to enhance product attributes while also lowering expenses. Blends of polymers may very literally be utilised in the same way as alloys of polymers are. Therefore, blending refers to the process of combining two or more distinct polymers in such a manner as to produce a new substance with characteristics that are only marginally different from those of the individual polymers that were used. Polymer mixing is a versatile process for the production of new synthetic polymers that have significantly improved properties in comparison to the original polymers [104]. This is a tried-and-true approach to solving new issues that are associated with application development.
Blending is an excellent choice since it enables one to combine existing polymers with new ones that have better properties and are also economically viable. Significant numbers of polymer mixes are recorded in the literature by researchers working in academia and industry [105]. When polymers are mixed together, the resulting blends may be liquid or phase-separate. When miscible blends are mixed, the mixing process eventually reaches a molecular-dimensional scale, and the properties of the present PM mix are more similar to those of a single PM. On the other hand, phase-separated blends often reflect the diverse characteristics of the polymers that are involved [106]. Even though miscibility is not very prevalent in blends, the characteristic profile of miscible blends offers advantages over the property profile of separate-phase blends, notably in terms of mechanical qualities. Because of the weak binding that occurs at the phase interface during blending, the majority of various phase blends have variations in the material properties that they possess. Therefore, researchers have devised a variety of strategies to alleviate the effects of these step separation difficulties. As a result, the composites’ essential features may be included in the construction of the polymer matrix. Blending not only physically alters the matrix but also causes it to take on new chemical characteristics. These new chemical qualities may be purposefully introduced into the matrix in order to facilitate improved interaction between the fibres and the blended PM. Many research works have demonstrated that the robust equilibrium of blends can be substantially boosted by fortifying them with synthetic or NFR [107]. This can be accomplished in either direction. Nonetheless, in recent years, bio-fiber reinforcements have made considerable strides due to the numerous benefits they offer compared to synthetic fibers.
Reddy et al. [108] conducted research on the mixing of epoxy and polyester resin for the production of composite material by reinforcing cordia-dichotoma fibre with granite powder particles. This was done in order to fabricate the composite material. Through testing of the composite material produced, the material’s mechanical and thermal characteristics were examined. Merzah et al. [109] have done research on blended composites made of epoxy and polyester. In this research, the influence of clay in nanodimensions on thermal and morphological qualities was emphasised. It was shown that using 2–3 wt% clay in composites resulted in superior MP than using plain blends. The enhancements featured a 30% growth in tensile strength, a 52% rise in interlaminar shear strength, and a 16% boost in impact strength. Morphological analyses revealed that the material possesses outstanding adhesion and interfacial bonding. Fig. 15 displays a diagrammatic representation of various polymer blending methods, such as physical mixture, block copolymer, and core-shell model. The figure illustrates three primary outcomes of polymer blending: a physical mixture, a block copolymer, and a core-shell structure, using green and black polymers as examples. It highlights the distinct structures resulting from the blending process, from simple mixtures where polymers are mixed but remain separate, to more complex block copolymers with alternating segments, and core-shell structures with one polymer encapsulating the other. These diverse structures are pivotal for advancing material properties and applications in fields like nanotechnology and biomedical engineering, emphasizing the importance of polymer structure manipulation in materials science.
Figure 15: A diagram illustrating various polymer blending techniques, encompassing physical mixture, block copolymer, and core-shell model
Compatibilization is a crucial process in the realm of polymer science, particularly in the creation of polymer blends or composites [110,111]. When two or more immiscible polymers are combined, the goal is to create a stable and homogeneous mixture with improved properties. However, due to the lack of interaction between the different polymer components, achieving this uniformity can be challenging [112]. That is where compatibilization comes into play. Compatibilization involves the use of compatibilizers, which are molecules or additives designed to enhance the compatibility and adhesion between the distinct polymers in a blend. These compatibilizers help improve the interfacial adhesion and reduce the interfacial tension between the immiscible polymers, allowing for better mixing, dispersion, and stability of the final product [113]. There are several methods to achieve compatibilization, such as: Reactive compatibilization, copolymer compatibilization, and polymer surfactant compatibilization. The method of compatibilization is shown here in Fig. 16. The diagram illustrates the role of compatibilizers in polymer blends, comparing blends with and without these molecules. Compatibilizers, depicted as blue structures, enhance interfacial adhesion between the polymers, depicted as yellow and red circles, leading to a more integrated and stable blend. This contrasts with the phase-separated structure observed in blends lacking compatibilizers, where the polymers remain distinct and disconnected. This compatibilization process is crucial for improving the mechanical properties and overall performance of polymer blends, making them suitable for advanced applications in industries like automotive and packaging, where tailored material properties are essential.
Figure 16: Diagrammatic illustration of compatibilization mechanisms
Compatibilization between NFR and the PM is an essential step in the progression of NFR-strengthened polymer composites [114]. The primary aim is to achieve strong adhesion and IB between the NFR and the PM, which can enhance the overall MP, thermal, and physical characteristics of the composite material [115,116]. There are several methods used for compatibilization between NFR and the PM:
• Fiber surface treatment: Chemical or physical modification of NFR surfaces can enhance their compatibility with the polymer matrix. This can include alkali treatment, silane treatment, or acetylation, which can alter the surface properties of NFR, making them more compatible with the polymer matrix [117].
• Matrix modification: The polymer matrix can be modified through the incorporation of functional groups or additives that can react or form hydrogen bonds with the natural fibers. This modification helps enhance the IB between the NFR and the PM, leading to better composite performance [118].
• Coupling agents: These are additives that act as intermediates between the hydrophilic NFR and the hydrophobic PM. Common coupling agents include maleic anhydride grafted polymers, silanes, and isocyanates. They form chemical bonds with both the fibers and the matrix, promoting better interfacial adhesion and compatibility [119].
• Hybrid composites: Incorporating a combination of NFR and synthetic fibers in the PM can improve compatibility and promote better dispersion of fibers within the matrix. This hybridization approach often leads to enhanced MP and physical characteristics in the final composite material [120].
Compatibilization between NFR and the PM is vital to ensure the successful development of NFR-strengthened polymer composites with the desired characteristics for various applications in automotive, construction, and other industries. Fig. 17 is a diagrammatic representation of the chemical interaction processes that occur between the PM and the NFR.
Figure 17: Schematic representation of the chemical interaction mechanisms between the natural fiber and the polymer matrix
6.4 Incorporation of Nanoparticles
There have been several reports of nanoparticles being used in the process of enhancing the characteristics of NFR polymer composites [121–124]. Nanoparticles are defined as “fine particles” that have a volume-to-surface ratio that is very high and in which one or more of their dimensions are smaller than 100 nanometers. The use of these nanoparticles has an effect on the crystallisation process that takes place when the polymer composites are formed, which leads to an improvement in both the thermal and MP of the composites [125–129]. These particles may undergo regulated transformations in order to engage selectively with a certain stage of the composites’ production process. These can be modified to employee as compatibilizers, reacting mainly with the matrix and NFR to create a more robust composite capable of stress transmission. Consequently, this leads to exceptional interplay among the composite’s constituents [130,131].
In order to explore the impact that acid immersion has on the hardness of epoxy-granite composites, Fadhil et al. [132] created composites with varying percentage volumes (5%–20%) of granite powder using the hand lay-up technique. Furthermore, tests of hardness were carried out, which revealed improved hardness with augment in the percentage of granite weight. In addition to this, specimens taken before immersion were found to have a higher hardness than those taken after immersion. The research determined the precise characteristics of granite powder, including its resistance to chemical degradation, its abrasion resistance, and its hardness. The diffusion coefficient fell as the weight percent of granite increased, but it increased at a faster rate as the acidity of the submerged solution became more concentrated. Granite powder and cordia dichotama were both components of the polymer composites that Mugesh Raja et al. [133] studied. Following an investigation into the thermal, mechanical, hygroscopic, and chemical attributes of the newly produced composites, the researchers came to the conclusion that filled composites achieved superior qualities.
Krishnudu et al. [134] conducted a study on CaCO3 filler NFR-reinforced polymer composites. The composites were fabricated using the hand layup method, and their dynamic and thermal properties were examined. The thermal and dynamical mechanical parameters of filler composites were significantly enhanced. In a separate study, the same group of authors investigated the static mechanical and dielectric properties, concluding that filled composites exhibited enhanced dielectric properties along with improved static and dynamic mechanical attributes [135]. This finding stemmed from their analysis of the static MP. Aravindh et al. [136] contributed to a vast and growing collection of literature on the MP of natural fiber polymer hybrid composites. The study examined the impact of various factors, including process parameters and fillers, on the aforementioned properties. The research highlights significant potential for enhancing the MP of NFR composites, in particular with regard to glass fibres. Nanoparticles may be seen in natural fibre nanocomposites, as seen in Fig. 18. Fig. 19 presents a visual representation of hybrid bionanocomposites. The scanning electron microscope (SEM) images (Fig. 18) demonstrate the inclusion of nanoparticles in nano-natural fiber composites, highlighting their varied dispersion and aggregation. The left image shows a dense cluster of irregular nanoparticles, which might suggest a less controlled deposition process, while the right image displays more evenly distributed nanoparticles along fiber structures, indicating a potentially more deliberate placement. This distribution of nanoparticles is crucial as it directly impacts the composite’s properties. For example, a uniform dispersion of nanoparticles can enhance the mechanical strength and durability of the nano-natural fiber composites, improve their functionality in applications such as filtration or reinforcement, and increase their effectiveness in various industrial applications. These images underscore the significant role of nanoparticle integration in optimizing the performance and characteristics of nano-natural fiber composites. An illustrated breakdown of the manufacturing of laminated hybrid bionanocomposites is shown in the Fig. 19, which shows how nanoparticles are selectively integrated with layers of natural and synthetic fibers within a polymer matrix. This in-depth illustration illustrates how a single, layered component becomes a unified, high-performing material. While synthetic fibers improve strength and durability, natural fibers benefit the environment and are lighter. The homogeneous functionality of the composite is ensured by the incorporated nanoparticles, which improve its qualities including mechanical strength and UV resistance. This diagram clearly illustrates how various material types work together, highlighting the promise of composites in sectors like aerospace and automotive where customized, highly durable, and environmentally friendly materials are essential.
Figure 18: SEM micrographs of the presence of nanoparticles in natural fiber nanocomposites
Figure 19: Diagrammatic illustration of the hybrid bionanocomposites
The use of two or more diverse reinforcing forms, shapes, or sizes beneath one composite material is an example of what is meant by the term “hybrid composites.” It has also been said that the qualities of reinforced polymers are dependent on a variety of elements such as: the properties of a single fibre, the strength of the fiber-matrix combination, the fibre surface roughness or resistance, and the degree to which the fibres are intertwined [137]. Lately, investigations into hybrid composites’ properties have focused on combinations of NFR and synthetic fibers, NFR with other NFR, and natural, synthetic, and additive-modified polymeric materials. It is increased owing to the capacity of these composites to change other composites and to grasp features that cannot be reached in produced composites containing single reinforcement that the success of these composites has been achieved. It has been discovered that fiber-reinforced HC exhibit enhanced characteristics in comparison to non-hybrid composites containing only a single reinforcement [138,139]. There have been a number of research investigations that have previously shown that constructing hybrid fibres by incorporating synthetic fibres in varying proportions results in higher-quality composites, especially in addition to MP [140]. It has been noticed that the MP of hybrid NFR/synthetic fibers often improve as the weight percentage of the synthetic fiber increases. This is something that has been seen. In spite of this, the mechanical characteristics of the composites begin to degrade when a specific weight percent of the additional synthetic fibre material has been reached. This can be traced back to weak IB, strong fiber-to-fiber contact, and low wettability. The influence that a variety of different fillers have on the MP of composites was studied by Reddy et al. [141]. The composites were made by independently reinforcing three distinct fillers with prosopis juliflora fibre, and then combining the resulting materials. In their research, the mechanical characteristics of a variety of filled hybrid composites were investigated and analysed.
When producing natural fiber polymer composites, several additional additives or processes are often overlooked but may still influence the final MP and physical characteristics of the material. One example of this is the incorporation of contaminants into the matrix material by means of the inclusion of fibres. These components, as opposed to the nanoparticles, will have an effect on the crystallisation process; however, this is strongly dependent on the chemical structure of the components. It is also important to note that the recrystallization of the composite materials enables the atoms to grow to their full size. This is an important benefit of the recrystallization process. Therefore, the temperatures that are maintained during the annealing process of the materials are really highly crucial to the composite’s ultimate qualities that are achieved. To ensure that the final product has the desired characteristics, extreme caution must be used throughout every stage of production, beginning with the procurement of raw materials and continuing through product packaging.
7 Physical and Mechanical Characteristics of Hybrid Composites
The MP and physical characteristics of HC are largely influenced by several key parameters. These include the proportion and length of the fibres used, which directly impact the composite’s strength and flexibility. Equally important is the orientation of these fibres; their alignment can affect the material’s performance under different stresses. The arrangement of individual fibres also plays a role, with the spatial distribution contributing to the overall structural integrity of the composite [142]. Additionally, the degree to which the fibres intermingle can affect the material’s resilience and durability. This intermingling can create a more uniform structure, leading to improved load distribution when the material is under stress. Lastly, the interfacial adhesion-the bonding strength between the fibre and the matrix-is critical. Strong adhesion can enhance the composite’s resistance to environmental factors, while weak adhesion could lead to premature failure of the material. Therefore, these factors must be carefully controlled during the manufacturing process to optimize the composite’s performance for its intended application [143,144]. Most research on NFR hybrid composites centers around investigating their mechanical properties in relation to factors such as fibre length, fibre quantity, the level of fibre intermingling, the bond strength between fibre and matrix, and the arrangement of both types of fibres. It also examines the impacts of different chemical modifications of fibres and the application of coupling agents. In-depth investigations of this sort have been performed on diverse natural fibre hybrid composites, encompassing materials like carbon fibre, cellulose, hemp, and flax [145].
7.1 Thermoset Hybrid Composites
Researchers create HC by merging fibres with various resins such as epoxy, polyester, phenolic, poly vinyl ester, and poly urethane. Table 6 presents the research conducted on thermoset hybrid composites using both NFR/NFR and NFR/synthetic fibres. The MP of these thermoset biocomposites, as well as the impact of glass hybridization on their mechanical attributes, are discussed in great detail.
7.1.1 Hybrid Composites-Based Epoxy
Alshammari et al. [165–167] conducted a study on the chemical resistance, void content, and MP of HC made from oil palm empty fruit bunches and jute fibres. They found that hybridizing the composites with jute fibres led to enhanced physical characteristics, including water absorption, dimensional stability, and density. The research also examined the impact of fibre bundle loading and modification of bagasse fibre surface on a jute/bagasse hybrid fibre-reinforced epoxy composite. The findings indicated that surface modification significantly enhanced the interaction between the NFR and PM, leading to a considerable enhancement in the MP of the HC [168]. Moreover, this study also offered valuable insights into thermomechanical characteristics and a comprehensive analysis of the interconnected dynamics between fibres and matrix. The primary objective of the research that Sivasankar et al. carried out was to investigate the impact that embedding hemp and abaca fibres in a PM would have on the mechanical characteristics of a composite material. In accordance with the results of the trials, the tensile strength of 30:0 (abaca:hemp fibre) is extraordinarily high, whilst the flexural strength of 40:10 (abaca:hemp fibre) is very high [169].
Ramie, hemp fibres, and coconut shell particle reinforcement with epoxy hybrid composites were subjected to research to determine their mechanical characterisation, which was then presented by Suriyaprakash et al. [170]. The generated samples were subjected to further tests, including tensile testing, impact testing, flexural testing, and water absorption testing, to gain deeper insight into the MP of the material. The hybridization of epoxy composites with hemp and ramie fibres, as the message is given, results in better characteristics of the composites. It was discovered that increasing the percentage composition of hemp fibres in fiber-reinforced composites led to an improvement in the materials’ MP. The water-absorbing and mechanical capabilities of jute and glass fibre reinforced epoxy composites were looked at [171]. The research indicates that the MP of HC fall somewhere in the centre of the spectrum between those of jute composites and those of glass composites. In the context of this research, the researchers are aiming, among other things, to evaluate the effect that water absorption has in a number of different chemical situations, in addition to the effect that boiling water has. It was shown that hybrid composites had a superior water absorption behaviour when compared to jute composite materials and glass composite materials, respectively. The results of this investigation on the loading rate behaviour of jute/glass hybrid reinforced epoxy composites were given [172]. When hybrid composites are exposed to higher loading rates, it has been shown that the hybrid composites are insensitive to the loading rate in terms of the stress at yield, the displacement at yield, and the interlaminar shear strength values [173]. Velu et al. looked into the hybrid composites that were reinforced with carbon, jute, and glass fibres to study their mechanical characteristics [174]. The HC made of carbon, jute, and glass fibre were fabricated with four distinct layers of texture. In preparation for the study, six unique plates were manufactured. The composites were made stronger with the addition of the carbon fibre, which contributed to the improvement. Experimentation also demonstrates that carbon fibre, in comparison to glass fibre and jute fibre, has extremely superior mechanical qualities; nevertheless, the cost of carbon fibre is prohibitively expensive, and the configuration of fibers is crucial in establishing the robustness of the overlay. The hybrid natural fiber/synthetic fibre polymer composites are represented schematically in Fig. 20.
Figure 20: Graphic depiction of hybrid polymer composites composed of natural and synthetic fibers
Through a series of tensile, flexural, and Izod tests, the study [175] that Kudva et al. carried out with the intention of determining the MP of bamboo and carbon fibre reinforced HC was carried out. When compared to bamboo fibre reinforced composites, HC had tensile strengths that were 74.53% higher, flexural strengths that were 41.47% higher, and impact strengths that were 182.24% higher. In comparison to hybrid and bamboo fibre reinforced composites, carbon fibre reinforced composites exhibited improved mechanical capabilities, particularly in terms of tensile and flexural characteristics. According to the findings of the research, composite materials made from a mixture of NFR and synthetic fibres achieve satisfactory levels of mechanical performance. Research was also carried out on the MP of HC crafted from both treated and untreated sisal and glass, reinforced with a blend of epoxy and formaldehyde originating from bisphenol-C [176]. Another study [177] focused on the flexural and compressive attributes of bamboo/glass fibre reinforced epoxy HC. The findings revealed that hybrid bamboo composites utilizing untreated bamboo fibres demonstrated inferior qualities compared to those made with alkali-treated bamboo fibres. This research was aimed at exploring the hybridization of NFR with glass fibres for potential applications in the pipe industry [178]. In a particularly noteworthy project, researchers constructed a passenger car bumper beam using kenaf/glass HC [179]. The findings suggested that the created HC beam possesses MP on par with typical bumper beam material, with the exception of its impact characteristics. The study suggested that kenaf/glass hybrid composites could potentially be employed in the manufacture of automotive structural components.
7.1.2 Hybrid Composites-Based Phenolic Resin
Ramlee et al. undertook a study on the use of oil palm empty fruit bunch (OPEFB) and sugarcane bagasse (SCB) fiber, utilized as filler in varying proportions, to create HC utilizing the hand lay-up method, ensuring a total NFR load of 50 wt% [180]. The study established that the performance and characteristics of these hybrid OPEFB/SCB fiber composites surpass those of pure fiber composites. The results highlighted that the HC with a ratio of 7:3 (OPEFB:SCB) exhibited the highest tensile strength and modulus, measuring 5.56 and 661 MPa, respectively. This study contributes to the understanding of agricultural waste as a potential green material alternative, suitable for use as thermal insulation and heat retention in walls, an application vital to the building and construction industry for its energy-saving capabilities. In this work, the tensile, flexural, and impact mechanical characteristics of novolac-type phenolic composites were studied as a function of fibre orientation and roving/fabric factors [181]. These composites were reinforced with jute/cotton hybrid woven fabrics. According to the results of the study, the characteristics of the roving or fabric, in addition to the orientation of the test, both had a major impact on the composite charateristics. In terms of the composites’ overall mechanical characteristics, the best results were generated by the tests conducted in the direction of the jute roving. Research [182] delved into the hybrid effect of glass fibre and oil palm empty fruit bunches (OPEFB) fibre on the tensile, flexural, and impact response of the phenol-formaldehyde composite. The integration of glass fibres led to an enhancement in the composite’s performance as a whole. However, increasing the volume fraction of OPEFB fibre resulted in a decline in the hybrid composite’s density and impact strength. Similarly, an increment in the volume fraction of OPEFB fibre caused a slight decrease in the hardness of the hybrid composite. Hybrid composites containing a volume fraction of 0.74 of OPEFB fibre demonstrated the greatest impact strength observed. Hybrid composites comprising glass and phenolic outperformed composites made solely of oil palm.
In the research conducted by Feng et al. [183], they used the hand layup method to fabricate hybrid composites, hybridizing treated pineapple leaf fibre (PALF) and kenaf fibre (KF) with the aim of enhancing the MP of untreated HC. They prepared silane treated PALF/KF phenolic HC with varying fibre fractions to assess mechanical properties, comparing them with untreated PALF/KF phenolic HC. It was found that silane treatment of the fibres resulted in better mechanical performance in the hybrid composites, making them suitable for use in the manufacturing of building structures, materials, and automobile components. The hybrid PALF/KF polymer composites are shown in a schematic format in Fig. 21.
Figure 21: Diagrammatic depiction of the hybrid PALF/KF phenolic composites
7.1.3 Hybrid Composites-Based Polyester
Polyester-based NFR hybrid composites are gaining attention due to their improved mechanical properties, cost-effectiveness, and potential for reducing environmental impact. These composites are fabricated by reinforcing polyester resin with different types of NFR, and sometimes in combination with synthetic fibers. This creates a hybrid composite material with improved properties compared to pure polyester or pure natural fiber composites. The main goal of the research conducted by Vivek et al. [184] was to assess the MP of composites reinforced with jute fiber and copper wire in a polyester matrix. They used a hand layup method to investigate the MP of composite samples, conducting a range of tests, including compression, impact, flexural, and tensile tests. Their deduced results indicated that polyester composites reinforced with jute fiber and 5% copper wire yielded 15.38% higher compression strength, 66.67% improved flexural strength, and 34.50% increased tensile strength compared to pure jute fiber composites. The impact test showed a value of 0.7 J for composites with jute and copper, whereas the jute-only composites registered a lower value of 0.4 J. Recent studies have explored the impact behavior of HC composed of glass and oil palm, finding that the impact strength of these composites enhances with the addition of more glass fibre layers and longer fibre lengths [185]. The hybrid impact of glass/oil palm EFB fibre on the tensile, flexural, and impact attributes of polyester composites was studied, with an emphasis on the influence of augmenting loading of both oil palm EFB and glass fibres [186]. The objective was to understand how increasing the load of either oil palm EFB or glass fibres would impact the hybrid effect. It was found that an EFB/glass hybrid polyester composite exhibits superior MP comparison to an EFB/polyester composite. Glass fibre possesses greater strength and modulus compared to EFB fibres, which is the key reason behind the enhanced characteristics of the HC. A different study explored the impact of EFB fibre specimen length and fibre loading on the physical characteristics and MP of oil palm/glass fibre reinforced polyester composites [187]. It was found that shorter EFB fibres exhibited higher water absorption and dimensional change comparison to their longer counterparts. Nevertheless, the flexural strength and density of the composites were not significantly impacted by the length of the EFB fibre specimen. While both flexural strength and density tend to decline with an increase in EFB fibre content, a volume fraction addition of 40%–70% EFB leads to a substantial 350% enhancement in the flexural strength of the polyester resin.
According to a study conducted by researchers [188,189], E-glass/jute/E-glass hybrids demonstrate superior performance under low impact energies (up to 10 J), which do not inflict damage to the laminate core. The research focused on examining the post-impact characteristics of jute/glass HC in relation to the layering arrangement of glass and jute fibres. In contrast, jute/E-glass/jute hybrids excel in their capacity to withstand extensive damage caused by higher impact energy (12.5 and 15 J). This can be attributed to the effective dispersion of impact damage across the structure by these hybrids. The flexural and indentation behavior of pultruded jute/glass and kenaf/glass hybrid polyester composites was observed utilizing acoustic emission, and the findings were juxtaposed with those of kenaf fibre composites [190,191]. Similar research was carried out on polymer matrix composites made from jute/cotton and silk/cotton textiles [192]. It was noted that the tensile attributes improve with the fibre content of the composite, and sisal and cotton HC were slightly more impacted by water than their jute and cotton counterparts. Furthermore, the study examined the tensile behaviours of jute/cotton HC through the lens of three different fabric layouts, each with a distinct jute weight ratio, and five stacking sequences. While cotton fibre didn’t significantly contribute as reinforcing materials, it served as a useful auxiliary fibre that facilitated the fabric production. Sahbaz Karaduman et al. [193] employed natural fibers such as sugar palm, kenaf, and bamboo, combined with synthetic fibers like fibreglass and Kevlar, to examine the MP and water absorption of HC materials. The mechanical strength of these composites was impacted by varying the weight content of the NFR, which were set at 0 (control sample), 15, 45, and 60 wt%. Their findings revealed that a hybrid fibre-reinforced composite, with 45 wt% kenaf fibre, exhibited superior tensile attributes, while a composite with 60 wt% sugar palm fibre demonstrated better performance in the Charpy impact strength test, in comparison to other natural/synthetic hybrid fibre-reinforced composites. Of all the fibres tested, sugar palm fibres showed the highest resistance to water in this study.
Researchers [194] conducted a study on the tensile strength of ramie-cotton hybrid fibre reinforced polyester composites. They found that the tensile behavior was majorly influenced by the volume percentage of ramie fibres aligned in the direction of the test. Neither the fabric type nor the fiber diameter had any effect on the tensile properties. Concurrent research on sisal/glass HC with various stacking sequences demonstrated that appropriate layering of fibre could improve MP [195]. Furthermore, the MP of short, randomly oriented hybrid fibres composed of banana and sisal and reinforced with polyester was examined [196]. The hybrid impact can be demonstrated to exert a positive impact on the flexural strength and flexural modulus of the HC. As the relative volume fraction of the two fibres was altered, an advantageous hybrid effect was noted in the tensile strength of the composites. The HC, which was identified to possess the highest tensile strength, featured a 4:1 ratio of banana to sisal. While an escalation in the volume percentage of sisal contributed to an enhancement in the composites’ impact strength, it inversely affected the materials’ impact properties. Additionally, the researchers investigated short randomly oriented intimately mixed banana and sisal hybrid fibre-reinforced polyester composites with different volume fractions of fibre [197]. These composites were created using compression moulding (CM) and resin transfer moulding (RTM) techniques, maintaining a 1:1 volume ratio of banana and sisal throughout the study. Venkatasudhahar et al. [198] explored the MP of woven fibre from banana and sisal as well as short banana and sisal hybrid fibre reinforced polyester composites.
7.1.4 Hybrid Composites-Based Unsaturated Polyester
Unsaturated polyester resin (UPR) is commonly employed as a matrix in NFR hybrid composites owing to its excellent MP, ease of processing, and good compatibility with NFR. The combination of UPR with NFR can lead to composites with improved tensile strength, flexural strength, and impact strength. In order to produce jute/glass hybrid reinforced unsaturated polyester composites, the hand lay up method, together with the additives and initiator, is used [199]. Hybrid composites with a jute to glass ratio of 1:3 shown considerable increases in mechanical characteristics such as tensile strength (125 percent), tensile modulus (49 percent), bending strength (162 percent), and bending strength (235 percent), in comparison to untreated jute composites. the impact of water on HC that were generated by compressing unsaturated polyester composites before moulding them and then reinforcing them with jute-glass fabric [200] was examined. hybrid composites were made by creating hybrid composites by compressing unsaturated polyester composites before moulding them. During the course of this study, the researchers constructed a mathematical model in order to predict the manner in which mass is transported during the process of water absorption.
The HC were created by combining naturally existing fabrics from the species Ceiba pentandra (also known as kapok) and Agave veracruz (often known as sisal), as well as kapok and glass [201]. In order to create the matrix, an unsaturated polyester resin was used, and the lay-up procedure was done by hand. The chemical resistance of HC made of kapok and glass was much greater when compared to that of HC made of kapok and sisal. A diagrammatic illustration of a hybrid sisal/kapok polymer composite may be seen in Fig. 22. This diagram depicts the hybrid material made of kapok and glass fibre. In addition to that, they evaluated the impact properties of unsaturated polyester HC that were based on kapok [202]. The compression, chemical resistance, and thermal attributes of HC made of kapok/sisal-unsaturated polyester are examined as a function of the fabric/fiber content as well as various volume ratios of textiles [203,204]. The addition of a small number of sisal fibres to kapok-reinforced polymer results in hybrid composites with superior compressive properties. This improvement comes about as a result of the HC being made. Alkali-treated kapok/sisal HC with a volume ratio of 50:50 kapok to sisal shows gains of 8.8% and 10.6% in compression strength and modulus, respectively, as compared to untreated kapok/sisal HC. The compressive attributes of all of the HC that are produced as a consequence are improved, but the improvement is most pronounced in hybrid composites that have a fabric ratio of 1:3. They also researched the MP of kapok/glass hybrid composites and found that these composites had values that were higher than those of unhybridized composites independent of the quantity of fibre loading [203–205]. This was the result of their investigation into the MP of unhybridized composites. After being treated with alkali, it was discovered that both the tensile and the hardness characteristics of these composites saw a considerable rise in their values. In composite materials, an augment in the quantity of glass fibre loading leads to rise in the interlaminar shear strength as well as an increase in the flexural and compressive shear strengths. It was discovered that the flexural and compressive values of HC made with kapok and glass were much higher than those made with sisal and glass and those made with kapok and sisal respectively. The impact of glass fibre loading on the flexural and tensile characteristics of a sisal/glass fibre HC was investigated, and the researchers discovered that the HC displayed lower flexural characteristics and stronger tensile strength than the matrix [206,207]. The flexural and tensile characteristics of the material have been studied to establish how the flexural and tensile attributes of the material are influenced by the treatment of fibres with alkali and trimethoxy silane (a coupling agent). It was discovered that the silane treatment did not considerably impact the flexural characteristics of the sisal–glass HC, but it did greatly increase the tensile strength of the composites. The flexural properties were not altered in any way by the alkaline treatment. After performing research on the chemical resistance attributes of treated and untreated HC constructed of sisal/glass and silk/sisal, the researchers discovered that the developed HC are resistant to all of the tested chemicals with the exception of carbon tetrachloride [208,209]. The researchers also noted that the untreated HC were resistant to carbon tetrachloride. Recent studies [210] examined the flexural and impact mechanical characteristics of a glass/sisal HC with varied quantities of fibre loading and varying volume ratios of sisal to glass fibres. The results of these studies were published in the journal Advanced Materials.
Figure 22: Graphic illustration of hybrid polymer composites made of kapok/glass fiber and kapok/sisal fiber
The tensile, flexural, and compressive strengths, as well as other mechanical parameters, of sisal/silk and coir/silk unsaturated polyester-based HC with various fibre lengths have been examined [211,212]. This research was conducted in order to better understand the properties of these HC. There have been reports of considerable improvements in the tensile, flexural, and compressive strengths of HC consisting of coir and silk that were brought about as a consequence of alkali treatments. Researchers [213] investigated the influence that moisture had on the tensile, flexural, and impact strengths of a hybrid polyester composite consisting of roselle and sisal fibres. The composite was put through a series of tests in both dry and wet conditions to see how the conditions affected the composite’s mechanical properties. An exciting study is now being carried out, the purpose of which is for the researchers to try to examine the impact of alkali and sodium lauryl sulphate (SLS) on the mechanical parameters of banana/kenaf HC and woven HC [214]. The SLS procedure leads in a larger enhancement in the tensile, flexural, and impact strengths of both non-woven and woven HC in comparison to the treatment with alkali. This is the case for all three types of strength.
7.1.5 Hybrid Composites-Based Benzoxazine
Benzoxazine is categorized as a thermosetting resin. Benzoxazine resin polymerizes by ring-opening processes to create a densely interconnected polymer network, resulting in a thermosetting material renowned for its exceptional resistance to heat, stability in size, and mechanical characteristics. Polybenzoxazine resin is a new kind of high-performance phenolic thermoset, which demonstrates improved strength, considerable resilience, high glass transition temperature (Tg), good thermal stability, high flame retardancy, low dielectric properties good toughness, and. It has a low water uptake and good corrosion resistance [215]. It can be polymerized either by heat under pressure or at room temperature with the aid of a curing agent. However, the primary drawbacks of polybenzoxazine matrix are its brittleness and high curing temperature. These drawbacks may be effectively addressed through the incorporation of other thermoplastic and thermosetting polymers into the matrix, or by developing novel linear benzoxazine monomers [216]. The favorable processing characteristics and potential for integrating a greater filler ratio were observed in polybenzoxazine composites reinforced with various fillers, including natural fibers, ceramics, and metals, owing to their wide processing window and low A-stage viscosity. In general, polybenzoxazine systems reinforced with the resulting fibers, particles, or nano-fillers exhibit enhanced mechanical properties, improved heat management capabilities, superior thermal stability, and heightened resistance to corrosion. Polybenzoxazine composites are highly suitable for microelectronics and aerospace applications due to these unique properties [217].
The prominence of fuel depletion issues and heightened environmental consciousness have led to a substantial surge in the development of green composites containing polybenzoxazine over the past decade [218]. Presently, the investigation into the production of polybenzoxazine composites incorporating a variety of renewable raw additives and natural fibers has been concluded in order to fulfill engineering requirements. Furthermore, substantial research effort is devoted to the development of environmentally friendly composites through the use of various natural fibers to reinforce biobased polybenzoxazine thermosets, thereby guaranteeing favorable antimicrobial properties and a significantly diminished processing expense. Nonetheless, the limited accessibility of certain renewable precursors—amines and paraformaldehyde—which are utilized in the synthesis of biobased benzoxazine monomers—basically hampered this strategy. As a result, chemists and industry stakeholders are actively seeking novel synthesis pathways to produce these natural precursors [219].
7.2 Thermoplastic Hybrid Composites
Thermoplastic HC is a material that was developed by a team of researchers that mixed natural rubber, polypropylene, polystyrene, polyethylene (low and high density), poly vinyl chloride, and polycarbonate with polypropylene and polystyrene fibres. This combination resulted in the creation of the material known as thermoplastic hybrid composite. The research that has been conducted on NFR/NFR and NFR/synthetic fibres reinforced thermoplastic HC is outlined in Table 7, which can be found here.
7.2.1 Hybrid Composites-Based Polypropylene (PP)
In order to develop a hybrid composite, oil palm EFB and glass fibres were used as reinforcing agents inside a polypropylene (PP) matrix [224–226]. The oil extraction method of oil palm empty fruit bunches fibre has been proven in a number of studies to have influenced on the flexural and tensile characteristics of composites that have been included with a range of coupling agents. These findings were obtained through the research of a number of different researchers. The removal of oil palm empty fruit bunches fibres has been demonstrated to result in a significant increase in flexural and tensile strength and toughness, as well as a minor rise in flexural and tensile modulus, as well as an increase in elongation at break. A preliminary experiment on oil palm empty fruit bunches/glass HC found that the inclusion of both fibers in the PP matrix led to a decrease in tensile strength and flexural strength of the composites. This discovery was seen in HC made of oil palm empty fruit bunches and glass. The goal of this study is not to investigate the parallels and contrasts between composites made of NFR and those made of glass fibres; rather, the objective is to develop more advanced statistical methods that can be used to analyse the mechanical attributes of these materials [227]. The value that was determined to be predicted for the theoretical elastic modulus was discovered to be pretty comparable to the value that was determined via experimentation. The investigated composite was discovered to have faults in terms of fibre/matrix adhesion as well as voids, which were responsible for the very tiny discrepancy between the measured and predicted values of modulus. This disagreement was caused by the fact that the measured values were slightly higher than the projected values. Fig. 23 shows a diagrammatic representation of a hybrid oil palm empty fruit bunch/glass fiber polypropylene composites.
Figure 23: Diagrammatic depiction of the hybrid oil palm empty fruit bunch/glass fiber polypropylene composites
This study was conducted with the intention of determining the impact that the hybridization of glass fibres would have on the physico-mechanical attributes of composites formed of sisal and polypropylene [228]. The inclusion of glass fibre into sisal polypropylene composites led to a rise in the material’s tensile, flexural, and impact strength without having a discernible influence on the tensile or flexural moduli. This was a significant finding. When glass fibre was coupled with sisal fibre in the manufacturing of the polypropylene, the water absorption of the composites was declined. Additionally, the water absorption of the composites was reduced as the amount of glass fibre in the polypropylene increased. One researcher recently conducted study on the permeability and MP of sisal/glass HC that were created by the procedure of resin transfer moulding [229]. The permeability of the hybrid reinforcement was significantly increased and its MP were markedly enhanced due to the incorporation of sisal fibre mat as a flow medium. We fabricated HC from polypropylene, reinforced with a blend of short banana and glass fibres, utilizing a Haake twin-screw extruder. The process was followed by compression moulding, with or without maleic anhydride grafted polypropylene (MAPP) serving as a coupling agent [230]. Introducing glass fibre and coupling agents into hybrid composites led to a decrease in the material’s water absorption capacity. Blending both types of fibres into the polypropylene matrix caused an increase in tensile, flexural, and impact strength, with fibre content up to 30 wt% and a banana to glass fibre ratio of 15:15 wt%. Furthermore, an inclusion of 2 wt% MAPP led to a strength augment, regardless of the total fibre content within the polypropylene matrix.
Gogoi et al. researched hybrid composites of bamboo/glass fibre reinforced polypropylene (BGRP), utilizing an intermeshing counter-rotating twin screw extruder, subsequently followed by injection moulding [231]. Sergi et al. conducted a detailed study on the hydrothermal ageing and fatigue behavior of a bamboo-glass fibre reinforced polypropylene hybrid composite (BGRP) [232]. This study was quite intriguing. After ageing for 6 months at 25°C, the BGRP samples demonstrated a minimal decrease in tensile strength and elastic modulus. However, there was a significant drop when aged for 3 months at a temperature of 75°C. When MAPP is utilized as a coupling agent in composite systems, it is proven to reduce both moisture absorption and the decline in tensile strength. The innovative approach of combining hard-wearing glass fibre with bamboo fibre effectively enhances the durability of NFR composites against environmental ageing. The research also delved into the impacts of environmental and accelerated ageing on the tensile and flexural properties of bamboo-glass fibre reinforced polypropylene hybrid composite (BGRP). These composites, all of which contained 30% fibre content by weight, were analyzed by immersing the samples in water at 25°C for up to 1600 h and at 75°C for a duration of up to 600 h [233].
The non-absorbent nature of glass fibre means that substituting bamboo with it in the composite results in a decrease in the potential moisture absorption by the material. The mass gain is reduced when aged at 75°C for approximately 600 h, compared to those aged at 25°C, due to the dissolution of bamboo fibre components (such as lignin) and the polypropylene matrix, which can be observed under a scanning electron microscope. Following prolonged water ageing at both 25°C and 75°C, the tensile and flexural strength of BGRP lessened along with its rigidity. The diminution in both strength and stiffness is directly related to the duration of ageing at a specific temperature. In this study, the tensile and flexural characteristics of short bamboo-glass fibre reinforced polypropylene hybrid composites (BGRP) were explored [234]. The study looked into the impact of factors such as fibre content, fibre length, the ratio of bamboo to glass fibre, and the utilize of a coupling agent (MAPP). It also explored the sorption behaviour and the ability of the composites to maintain their mechanical properties post-ageing. The inclusion of up to 20% by mass of glass fibre into the material enhanced the tensile and flexural modulus of BGRP by 12.5% and 10%, respectively. Additionally, the tensile and flexural strength of the material saw improvements of 7% and 25%, respectively. As the fibre length of bamboo increased, the tensile strength reduced slightly, while the tensile modulus showed a minor increase. Composites with longer bamboo fibres exhibited flexural strength and modulus values 25 and 35 percentage points higher than those of composites with shorter fibres, respectively.
Arpitha et al. [235] conducted a study on the flexural behaviour of hand-crafted hybrid laminated composites that had a hemp fibre/polypropylene core and two layers of glass fibres/polypropylene on either side of the specimen. The specimen under study had a thickness of 0.5 centimetres. Compared to polypropylene laminates reinforced with glass fibres, hybrid composites offer distinct enhancements in fatigue strength, along with economical, ecological, and recyclability benefits. The most significant finding was that laminate composites (LC) exhibited an ultimate strength roughly 4% higher than hybrid composites (HLC), whereas hybrid composites (HLC) had a Young’s modulus approximately 3.8% greater. HLC composites showed roughly a 22% point increase in specific flexural strength and flexural stiffness compared to LC laminates. In this specific case, fibre rupture occurs in the region of stress.
Panaitescu et al. [236] investigated the MP, water absorption, and thermal attributes of short hemp/glass fibre-reinforced hybrid polypropylene composites, which were manufactured using injection moulding. The MP of composites created from short hemp fibre can be enhanced by hybridizing them with glass fibre. In another study, researchers developed a HC by integrating flax and glass fibres into a polypropylene matrix [237]. Hybrid composites, with a 30 wt% glass fibre loading, demonstrated superior MP compared to flax fibre bundle/polypropylene. When the hybrid composite was modified with MAPP, it exhibited a higher modulus compared to the untreated HC.
7.2.2 Hybrid Composites Based on Polystyrene
The study performed by Balaji et al. examined the impact of factors such as fibre content, fibre loading, and hybrid impact on the MP of banana/glass hybrid fibre reinforced polystyrene composite, which included tensile strength, Young’s modulus, elongation at break, and flexural characteristics [238]. The role of interface modification on the MP of the HC was also scrutinized, demonstrating that chemical modifications, including alkali treatment, benzoyl chloride, and polystyrene maleic anhydrites, boosted the tensile performance of the composites. This modification led to improved fibre dispersion in the composite, a decrease in the hydrophilicity of the banana fibre, and superior compatibility between the fibre and matrix due to mechanical anchoring, physical bonding, and chemical bonding.
7.2.3 Hybrid Composites Based on Polyethylene (PE)
An attempt was undertaken to investigate the tensile qualities of intimately mixed short sisal/glass hybrid fibre reinforced low density polyethylene (LDPE) as a function of fibre length and various surface chemical changes on both the fibre and the matrix [239]. This was done in order to better understand how these factors affect the tensile characteristics of the material. This study was carried out with the purpose of determining how the tensile characteristics of the material are impacted by the fibre length and surface chemical changes of the material. It is clear that the breaking of the fibres that occurs during the production of the composite takes place more often in the case of glass fibre due to the brittle nature of glass fibre in comparison to the nature of sisal fibre. The results make it clearly clear that the length of the sisal fibre has a major influence on the tensile characteristics of closely mixed sisal/glass hybrid composites. This is shown by the fact that the data make this conclusion abundantly clear. A hybrid sisal fiber/glass fibre low-density polyethylene composite is shown diagrammatically in Fig. 24. Treatments with an extensive variety of agents led to considerable improvements in the tensile attributes of HC. Research has demonstrated that among the many chemical modifications, composites made up of fibres that have been treated with benzyl peroxide have the greatest tensile strength and modulus. Acetylation was shown to be more successful than the other treatments that were employed in this study, according to the findings of an evaluation into the cost-performance ratio that was conducted. Analyses of the MP and physical attributes of composites made from recycled high-density polyethylene (HDPE) and commercial textiles incorporating cotton and flax were conducted [240]. Cotton and flax fibres were added to a recycled high-density polyethylene (HDPE) composite, leading to a surge in the composite’s capacity to absorb water and expand as a consequence of that absorption. The textiles were either treated with maleic anhydride, silane, or enzyme, or they were given maleic anhydride grafted polyethylene (MAA-PE; MDEX 102-1, ExxelorVA 1840), in order to stimulate interactions between the PM and the fibres. This was done in order to facilitate the formation of new bonds between the polymer and the fibres. With the exception of the silane treatment, all of the other treatments led to a reduction in the tensile strength values of the treated denim fabric when compared to the values of the fabric before any treatment was applied.
Figure 24: Diagrammatic depiction of the hybrid sisal fiber/glass fiber low density polyethylene composites
7.2.4 Hybrid Composites-Based Poly Vinyl Chloride (PVC) and Polycarbonate (PC)
The MP of HC consisting of poly (vinyl chloride), wood flour, and glass fibre were explored by researchers [241]. When type L glass fibre was substituted for type S glass fibre, a substantial aufment in both the unnotched and notched impact strength of HC was observed, without any compromise on the flexural properties of the materials. However, there was no equivalent increase elsewhere. The formation of a three-dimensional network glass fibre structure between type L glass fibres and wood flour is believed to be the cause for the significant rise in impact strength displayed by the HC. Composite structures were produced as a result of combining waste silk and cotton with recycled polycarbonate (PC) polymer [242]. When silk content in polycarbonate is increased, yield strength, tensile strength, percentage elongation, and Izod impact strength all decrease, while the material’s hardness, modulus of elasticity, and melt flow index (MFI) all increase. There is no alteration to the heat deflection temperature (HDT) or the Vicat softening values. Conversely, as cotton content in PC increases, the percentage of elongation, Izod impact strength, MFI, HDT, and Vicat softening values all augment. Yield strength, tensile strength, modulus of elasticity, and hardness all decline with the increase in cotton content in PC.
8 Common Characteristics of Natural Fiber Hybrid Composites
8.1 Thermal Properties of Natural Fibre Hybrid Composites
Researchers conducted an investigation into the thermal characteristics of banana/glass hybrid composites. They discovered that MAPP-treated banana/glass hybrid composites (BSGRP) exhibit improved thermal stability when compared to composites consisting of banana fibre reinforced polymer [243]. It is conceivable that this is due to the fact that the SiO groups in glass fibre interlink with the anhydride group in MAPP, which creates a synergistic interaction between glass and banana fibres. After undergoing thermal research, it was discovered that hybrid composites had much higher melting points, temperatures at which they crystallised, and temperatures at which they began to experience thermal deterioration. Similar study using differential scanning calorimetry and thermogravimetric analysis demonstrated that MAPP treatment of banana and glass fibre boosted the cryrstallization temperature as well as the thermal stability of polypropylene [244]. This information emerged as a result of the investigation that was carried out. It was established by Karthik et al. as a result of their study into the thermal characteristics of sisal/glass hybrid PP, that the presence of glass fibre boosted the thermal characteristics of sisal/PP composites [245]. This was discovered as a result of their investigation into the thermal characteristics of sisal/glass hybrid PP. The PP/10sisal/20GF/PP-g-MA composite provided the highest Td5 (temperature at which 5% weight loss) and Td50 (temperature at which 50% weight loss), in contrast to the PP/sisal composite, which delivered the lowest Td5 and Td50 values. The heat distortion temperature (HDT) was identified to be enhanced even more when the glass fibres were added to the sisal–PP composites. According to the results of Kossentini Kallel et al.’s [246] investigation on the thermal attributes of sisal/glass HC, hybrid composites exhibit a better degree of thermal stability than sisal/glass composites do. It was found that the crystallisation temperature [247] of a sisal/glass hybrid that had been treated with 2 weight percent MAPP was greater than that of composites that did not include MAPP. This indicates that the nucleation process is accelerated further when compatibilizer is present.
Differential scanning calorimeter (DSC) and thermo gravimetric analysis (TGA) reveal an increase in the thermal stability of the PM with the insertion of bamboo and glass fibres, which verifies the effects of hybridization and effective fibre matrix interfacial adhesion [248]. In addition to this, it was discovered that the insertion of bamboo fibre, glass fibre, and MAPP did not considerably change the temperature at which the PP matrix melted. This was one of the findings that came about as a result of the research that was conducted. When fibres and MAPP are included in the composition of the matrix, the linear crystallizable sequence of the PP matrix is disturbed, and the degree of crystallisation experienced by the matrix as a whole is lessened as a result. They identified that the thermal stability of PM improves with the introduction of bamboo and glass fibres, and they speculated that this may be attributed to enhanced IB between NFR and PM [249]. They carried out research comparable to this one. Because glass fibre has a greater thermal stability than bamboo fibre, the addition of glass fibres leads in a significant improvement in the thermal stability of both composite systems. This is presumably owing to the fact that glass fibre is more thermally stable than bamboo fibre [250]. In addition to this, the bamboo/glass HC system had the highest amount of charred residue, which is an indication of the systems’ greater level of flame retardancy. Inácio et al. [251] investigated the thermal characteristics of bamboo/glass hybrid composites, including crystallisation, melting behaviour, and thermal stability. The findings from the TGA showed that by incorporating bamboo and glass fibres into the matrix polymer, its thermal stability was enhanced. This affirmed the influence of hybridization and exhibited the efficiency of optimal fibre matrix interfacial adhesion.
The amalgamation of glass fibres into hemp fibre composites enhanced the thermal characteristics of the composites [252]. It was found that merging hemp fibre composite with glass fibre shifted the degradation temperature to a higher value, confirming superior thermal stability in the HC. This can be attributed to the fact that combining hemp fibre composite with glass fibre raises the degradation temperature. An insightful study on the thermal attributes of sisal/oil palm hybrid fibre reinforced natural rubber composites was undertaken by Jacob et al. [253–255]. The team discovered that the thermal stability of the composites improved with the increase in fibre loading and the application of chemical modification. The effect of alkali treatment on the thermal characteristics of kapok/sisal hybrid composites was examined using differential scanning calorimetry [256,257]. The findings indicated that the melting temperature of the treated kapok/sisal hybrid composite demonstrated a slight increase compared to the melting temperature of the untreated HC.
8.2 Electrical Properties of Hybrid Composites
The analysis of the relevant published material makes it abundantly evident that very little investigation into the electrical characteristics of hybrid composites has been documented. Analyses were performed on the electrical characteristics of banana/glass hybrid fibre reinforced composites with a variety of hybrid ratios and stacking patterns [258]. The dielectric properties and volume resistivity of hybrid sisal–oil palm biocomposites were examined by the researchers. Since it has been shown that the dielectric constant improves with increasing fibre loading across all frequencies and that the volume resistivity reduces with increasing frequency as well as increasing fibre loading, this suggests that the conductivity augments with the addition of NFR [259–261]. The chemical modification of the fibers resulted in a decrease in the dielectric constant and an increase in the resistivity of the volume. The rise in the dissipation factor that was observed with increased fibre loading is indicative of the fact that the electrical charges may be maintained for a much-extended length of time. Parsania et al. investigated the impact that jute and glass fibre reinforcement had on the electrical characteristics of epoxy composites [262]. According to the findings, hybrid composites exhibit electrical characteristics that are somewhere in the middle of those of jute composites and glass composites. Patel et al. [263] conducted an analogous investigation on the electrical characteristics of sisal/glass HC that had either been treated or left untreated. The composites had been reinforced with blended epoxy and formaldehyde of bisphenol-C.
This study has examined and contrasted the electrical strength and volume resistivity of jute-biomass HC with jute–bisphenol-C-formaldehyde (BCF) composites. The dielectric breakdown strength of the hybrid composites (1.21–2.11 kV/mm) and BCF–jute composite (1.41 kV/mm) showed no significant disparity. However, the hybrid composites demonstrated an increase in volume resistivity by 197%–437% [264], particularly observed in BCF–jute–wheat husk and BCF–jute–jamun flower husk composites.
In a fascinating research study, researchers explored the electrical attributes like dielectric constant, volume resistivity, and dielectric loss factor of sisal/coir hybrid fibre-reinforced natural rubber composites [265]. These properties were examined in the context of factors such as fibre loading, fibre ratio, frequency, chemical modification of fibres, and the introduction of a bonding agent. The sisal/coir hybrid’s dielectric constant and volume resistivity mimic the patterns previously documented concerning fibre loading and frequency [259–261].
Chemically treated fibres in the composites exhibited reduced dielectric constant values, attributed to the augmented hydrophobicity of the NFR. Furthermore, the inclusion of a two-part dry bonding agent, made up of hexamethylene tetramine and resorcinol, lowered the dielectric constant of the composites. This bonding agent served to improve the IB between the PM and the NFR.
9 Application of Hybrid Composites Reinforced with Natural Fibres
Several scientists [266–269] are exploring the possible uses of composites made from NFR in the automotive sector. Already 8 years ago, Mercedes-Benz began installing door panels made of jute in its A-Class automobiles. NFR composites are used in a variety of settings by almost all of Germany’s main automobile manufacturers (Daimler Chrysler, Mercedes, Volkswagen, Audi Group, BMW, Ford, and Opel) [270]. As a consequence of the legalization of hemp cultivation in Germany, a flax/hemp (50:50) needle felt was developed specifically for high-segment automobiles. Natural fibre composites have more uses in interior panels, linings, and fittings as a result of a historic partnership between the automotive supplier Visteon Automotive system and the biocomposites company Kafus. Ford is the world’s largest vehicle manufacturer. Even though a NFR/PM composite may only be half as strong as a glass composite, it is still feasible to make this technology sufficient.
Polyurethane door trim panels were used in the Audi A2 intermediate automobile, which was introduced in the year 2000 [270]. These panels were reinforced with a mixed flax and sisal mat. A tiny prototype vehicle has been designed, built, and put together by a group of researchers [271]. All of the body panels of the vehicle are constructed from jute fibre reinforced composite and HC. The door panels of some car models were manufactured out of a blend of flax and sisal fibers in an epoxy matrix, which demonstrated an impressive weight reduction of around 20% [272]. It is a significant step towards the goal of improving the performance of HC when used in car applications. It has been stated that at the current time, 27 components of a Mercedes S class are constructed from NFR-based composites with a total weight of 43 kg [273]. According to the end-of-life vehicle (ELV) guideline in Europe, cars will need to be made of 95% recyclable materials by the year 2015, with 85% of those elements being able to be recovered via reuse or by mechanical recycling [274]. The spectre of rising gasoline prices was excellent news for the advancement of hybrid and electric cars, examples of which were abundant at the North American International Auto Show in Detroit, which took place in the United States in 2009.
During composite Europe 2009, the “Composite Poineer award 2009” was presented to the BioConcept-vehicle, the world’s first racing vehicle whose body was built completely of NFR reinforced plastics. This award was given in recognition of the BioConcept-Car’s pioneering contribution in the area of NFR-reinforced plastics. The currently available wood replacement construction materials on the market are unable to meet the requirements set by the industrial sector. Table top laminates, door panels, shutters, roofing materials, and other products like these may all benefit from the utilized of NFR-based hybrid composites, which can offer viable alternatives. Sisal and jute door panels have been constructed and tested according to the specifications of the Indian standard, and the results have been deemed adequate [275]. In the roofing industry, natural fibres are increasingly being considered a viable alternative to asbestos sheeting, which is one of the relevant possibilities. In the not-too-distant future, there will be a rise in the number of possible uses of hybrid composites in the automotive and construction industries.
Researchers face new hurdles when natural fibres are used in commercial applications since it is difficult to get high-quality fibres to utilise as reinforcement in polymer composites. These issues may be overcome, however, by developing appropriate methodologies. In a variety of contexts, the use of synthetic fibres may be supplanted or reduced by the use of hybrid composites, which are economically advantageous, recyclable, and biodegradable. A grasp of the basic structural elements of NFR and how they affect the physical, mechanical, electrical, and thermal characteristics of HC is essential. Nonetheless, several challenges may hinder the integration of these fibres into hybrid composites, which could pose significant issues.
This article attempts to provide a summary of the ongoing research on physical, mechanical, electrical, and thermal attributes of HC composed of NFR/NFR and NFR/synthetic fibers. It appears that extensive work is underway globally, with certain ideas being commonly explored, focusing primarily on the MP and physical characteristics of HC. Nonetheless, studies on the electrical and thermal characteristics of HC are still insufficient. Many researchers have enhanced the IB between fibers and PM in HC by employing coupling agents or chemically altering the fibres, leading to the creation of advanced HC.
The direction of future research on HC should not be confined to their applications in the automotive industry; it should also explore their potential uses in diverse sectors such as aerospace, construction, rural areas, and medicine. In many of the fields highlighted in this review, there is a need for further investigation into the unique characteristics of HC using advanced techniques like the fragmentation test/single fibre composite test, X-ray photoelectron spectroscopy (XPS), atomic force microscopy (AFM), contact angle, zeta potential measurement, and stress relaxation. Despite existing challenges, thorough analytical modelling based on published results is essential. Not only will this facilitate the interpretation of experimental results, but it will also optimize their specific applications across various sectors, such as building construction, structural components in aircraft and cars, and rural development.
Acknowledgement: The writers would like to thank the School of Materials Engineering at Universiti Malaysia Perlis for providing access to the laboratory. Many thanks go out to everyone who helped with this project in any way, whether explicitly or indirectly.
Funding Statement: The authors received no specific funding for this study.
Author Contributions: Mohammed Mohammed: Idea of research stated, Conceived and designed the work, Data collection, Review and editing, Analysed and interpreted the data, wrote the paper; Jawad K. Oleiwi; Bashir O. Betar Aeshah M. Mohammed; Azlin F. Osman: Data collection, Review and editing; Tijjani Adam: Data collection, Review and editing, Analysed and interpreted the data; Anwar Ja’afar Mohamad Jawad: Idea of research stated, Review and editing; Subash C. B. Gopinath: Conceived and designed the work, Data collection, Review and editing. All authors reviewed the results and approved the final version of the manuscript.
Availability of Data and Materials: Available upon request.
Conflicts of Interest: The authors declare that they have no conflicts of interest to report regarding the present study.
References
1. Akter M, Uddin MH, Tania IS. Biocomposites based on natural fibers and polymers: a review on properties and potential applications. J Reinforced Plast Compos. 2022;41(17–18):705–42. [Google Scholar]
2. Aisyah HA, Paridah MT, Sapuan SM, Ilyas RA, Khalina A, Nurazzi NM, et al. Comprehensive review on advanced sustainable woven natural fibre polymer composites. Polymers. 2021;13(3):471. doi:10.3390/polym13030471. [Google Scholar] [PubMed] [CrossRef]
3. Asyraf MRM, Ishak MR, Sapuan SM, Yidris N, Ilyas RA, Rafidah M, et al. Potential application of green composites for cross arm component in transmission tower: a brief review. Int J Polym Sci. 2020;2020:1–5. doi:10.1155/2020/8878300. [Google Scholar] [CrossRef]
4. Bachchan AA, Das PP, Chaudhary V. Effect of moisture absorption on the properties of natural fiber reinforced polymer composites: a review. Mater Today: Proc. 2022;49:3403–8. [Google Scholar]
5. Asyraf MRM, Rafidah M, Ishak MR, Sapuan SM, Yidris N, Ilyas RA, et al. Integration of TRIZ, morphological chart and ANP method for development of FRP composite portable fire extinguisher. Polymer Compos. 2020;41(7):2917–32. doi:10.1002/pc.v41.7. [Google Scholar] [CrossRef]
6. Rajak DK, Wagh PH, Linul E. A review on synthetic fibers for polymer matrix composites: performance, failure modes and applications. Materials. 2022;15(14):4790. doi:10.3390/ma15144790. [Google Scholar] [PubMed] [CrossRef]
7. Hossain S, Jalil MA, Islam T, Rahman MM. A low-density cellulose rich new natural fiber extracted from the bark of jack tree branches and its characterizations. Heliyon. 2022;8(11):E11667. doi:10.1016/j.heliyon.2022.e11667. [Google Scholar] [PubMed] [CrossRef]
8. Chokshi S, Parmar V, Gohil P, Chaudhary V. Chemical composition and mechanical properties of natural fibers. J Nat Fibers. 2022;19(10):3942–53. doi:10.1080/15440478.2020.1848738. [Google Scholar] [CrossRef]
9. Jagadeesh P, Puttegowda M, Thyavihalli Girijappa YG, Rangappa SM, Siengchin S. Effect of natural filler materials on fiber reinforced hybrid polymer composites: an overview. J Nat Fibers. 2022;19(11):4132–47. doi:10.1080/15440478.2020.1854145. [Google Scholar] [CrossRef]
10. Kumar S, Manna A, Dang R. A review on applications of natural fiber-reinforced composites (NFRCs). Mater Today: Proc. 2022;50:1632–6. [Google Scholar]
11. Praveena BA, Buradi A, Santhosh N, Vasu VK, Hatgundi J, Huliya D. Study on characterization of mechanical, thermal properties, machinability and biodegradability of natural fiber reinforced polymer composites and its applications, recent developments and future potentials: a comprehensive review. Mater Today: Proc. 2022;52:1255–9. [Google Scholar]
12. Venkatesh R, Ballal S, Krishnan AM, Prabagaran S, Mohankumar S, Ramaraj E. Effect of fiber layer formation on mechanical and wear properties of natural fiber filled epoxy hybrid composites. Heliyon. 2023;9(5):E15934. doi:10.1016/j.heliyon.2023.e15934. [Google Scholar] [PubMed] [CrossRef]
13. Ramakrishnan M, Ramasubramanian S, Raman S, Chinnapalanichamy J. Evaluation of the physical, mechanical, water absorption, and tribological behavior of pineapple leaf fiber/roselle fiber reinforced vinyl ester hybrid composites for non-structural applications. Polym Compos. 2023;44(8):5284–95. doi:10.1002/pc.v44.8. [Google Scholar] [CrossRef]
14. Thomason J. The influence of fibre cross section shape and fibre surface roughness on composite micromechanics. Micro. 2023;3(1):353–68. doi:10.3390/micro3010024. [Google Scholar] [CrossRef]
15. Nasimudeen NA, Karounamourthy S, Selvarathinam J, Thiagamani SMK, Pulikkalparambil H, Krishnasamy S, et al. Mechanical, absorption and swelling properties of vinyl ester based natural fibre hybrid composites. Appl Sci Eng Prog. 2021;14(4):680–8. [Google Scholar]
16. Chandrasekar M, Siva I, Kumar TSM, Senthilkumar K, Siengchin S, Rajini N. Influence of fibre inter-ply orientation on the mechanical and free vibration properties of banana fibre reinforced polyester composite laminates. J Polym Environ. 2020;28:2789–800. doi:10.1007/s10924-020-01814-8. [Google Scholar] [CrossRef]
17. Asghar MA, Imad A, Nawab Y, Hussain M, Saouab A. Effect of yarn singeing and commingling on the mechanical properties of jute/polypropylene composites. Polym Compos. 2021;42(2):828–41. doi:10.1002/pc.v42.2. [Google Scholar] [CrossRef]
18. Hatti-Kaul R, Nilsson LJ, Zhang B, Rehnberg N, Lundmark S. Designing biobased recyclable polymers for plastics. Trends Biotechnol. 2020;38(1):50–67. doi:10.1016/j.tibtech.2019.04.011. [Google Scholar] [PubMed] [CrossRef]
19. Malviya RK, Singh RK, Purohit R, Sinha R. Natural fibre reinforced composite materials: environmentally better life cycle assessment—a case study. Mater Today: Proc. 2020;26:3157–60. [Google Scholar]
20. Siva R, Kesavaram B, Martin JJ, Mathiselvan G, Navas KB, Sangeetha M. Mechanical behavior of sisal and banana fiber reinforced hybrid epoxy composites. Mater Today: Proc. 2021;44:3692–6. [Google Scholar]
21. Jagadeesh P, Puttegowda M, Girijappa YGT, Rangappa SM, Siengchin S. Carbon fiber reinforced areca/sisal hybrid composites for railway interior applications: mechanical and morphological properties. Polym Compos. 2022;43(1):160–72. doi:10.1002/pc.v43.1. [Google Scholar] [CrossRef]
22. Haris NIN, Hassan MZ, Ilyas RA, Suhot MA, Sapuan SM, Dolah R et al. Dynamic mechanical properties of natural fiber reinforced hybrid polymer composites: a review. J Mater Res Technol. 2022;19:167–82. doi:10.1016/j.jmrt.2022.04.155. [Google Scholar] [CrossRef]
23. Ramasubbu R, Madasamy S. Fabrication of automobile component using hybrid natural fiber reinforced polymer composite. J Nat Fibers. 2022;19(2):736–46. doi:10.1080/15440478.2020.1761927. [Google Scholar] [CrossRef]
24. Mochane MJ, Mokhena TC, Mokhothu TH, Mtibe A, Sadiku ER, Ray, SS, et al. Recent progress on natural fiber hybrid composites for advanced applications: a review. Express Polym Lett. 2019;13(2):159–98. doi:10.3144/expresspolymlett.2019.15. [Google Scholar] [CrossRef]
25. Dasore A, Rajak U, Balijepalli R, Verma TN, Ramakrishna K. An overview of refinements, processing methods and properties of natural fiber composites. Mater Today: Proc. 2022;49:296–300. [Google Scholar]
26. de Souza Castoldi R, de Souza LMS, Souto F, Liebscher M, Mechtcherine V, de Andrade Silva F. Effect of alkali treatment on physical-chemical properties of sisal fibers and adhesion towards cement-based matrices. Constr Build Mater. 2022;345:128363. doi:10.1016/j.conbuildmat.2022.128363. [Google Scholar] [CrossRef]
27. Dawit JB, Regassa Y, Lemu HG. Property characterization of acacia tortilis for natural fiber reinforced polymer composite. Results Mater. 2020;5:100054. doi:10.1016/j.rinma.2019.100054. [Google Scholar] [CrossRef]
28. Karimah A, Ridho MR, Munawar SS, Adi DS, Damayanti R, Subiyanto B, et al. A review on natural fibers for development of eco-friendly bio-composite: characteristics, and utilizations. J Mater Res Technol. 2021;13:2442–58. doi:10.1016/j.jmrt.2021.06.014. [Google Scholar] [CrossRef]
29. Amin MN, Ahmad W, Khan K, Ahmad A. A comprehensive review of types, properties, treatment methods and application of plant fibers in construction and building materials. Materials. 2022;15(12):4362. doi:10.3390/ma15124362. [Google Scholar] [PubMed] [CrossRef]
30. Prem Kumar R, Muthukrishnan M, Felix Sahayaraj A. Effect of hybridization on natural fiber reinforced polymer composite materials—a review. Polym Compos. 2023;44(8):4459–79. doi:10.1002/pc.v44.8. [Google Scholar] [CrossRef]
31. Mahir FI, Keya KN, Sarker B, Nahiun KM, Khan RA. A brief review on natural fiber used as a replacement of synthetic fiber in polymer composites. Mater Eng Res. 2019;1(2):86–97. [Google Scholar]
32. Teke AG, Atik C, Bertoncelj J, Poljanšek I, Oven P. Effects of modified cellulose fiber and nanofibril integration on basic and thermo-mechanical properties of paper. Forests. 2023;14(11):2150. doi:10.3390/f14112150. [Google Scholar] [CrossRef]
33. Jaiswal D, Devnani GL, Rajeshkumar G, Sanjay MR, Siengchin S. Review on extraction, characterization, surface treatment and thermal degradation analysis of new cellulosic fibers as sustainable reinforcement in polymer composites. Curr Res Green Sustain Chem. 2022;5:100271. doi:10.1016/j.crgsc.2022.100271. [Google Scholar] [CrossRef]
34. Belgacem C, Serra-Parareda F, Tarrés Q, Mutjé P, Delgado-Aguilar M, Boufi S. Valorization of date palm waste for plastic reinforcement: macro and micromechanics of flexural strength. Polymers. 2021;13(11):1751. doi:10.3390/polym13111751. [Google Scholar] [PubMed] [CrossRef]
35. Ramesh M, Rangappa SM, Parameswaranpillai J, Siengchin S. Introduction to biodegradable polymers. Biodegradable Polym Blends Compos. 2022;1–18. [Google Scholar]
36. Pickering KL, Li Y, Farrell RL, Lay M. Interfacial modification of hemp fiber reinforced composites using fungal and alkali treatment. J Biobased Mater Bioenergy. 2007;1(1):109–17. doi:10.1166/jbmb.2007.1984. [Google Scholar] [CrossRef]
37. Sreejith M, Rajeev RS. Fiber reinforced composites for aerospace and sports applications. In: Fiber reinforced composites. Woodhead Publishing; 2021. p. 821–59. [Google Scholar]
38. Egbo MK. A fundamental review on composite materials and some of their applications in biomedical engineering. J King Saud Univ-Eng Sci. 2021;33(8):557–68. [Google Scholar]
39. Minchenkov K, Vedernikov A, Safonov A, Akhatov I. Thermoplastic pultrusion: a review. Polymers. 2021;13(2):180. doi:10.3390/polym13020180. [Google Scholar] [PubMed] [CrossRef]
40. Chen T, Su C, Zeng Y, Chen Y, Qiu R, Liu W. Effects of hydrogen bonds on soybean oil-based thermosets and their bamboo fibers composites. Compos Commun. 2022;33:101231. doi:10.1016/j.coco.2022.101231. [Google Scholar] [CrossRef]
41. Rangappa SM, Siengchin S, Parameswaranpillai J, Jawaid M, Ozbakkaloglu T. Lignocellulosic fiber reinforced composites: progress, performance, properties, applications, and future perspectives. Polym Compos. 2022;43(2):645–91. doi:10.1002/pc.v43.2. [Google Scholar] [CrossRef]
42. Muralidaran VM, Natrayan L, Kaliappan S, Patil PP. Grape stalk cellulose toughened plain weaved bamboo fiber-reinforced epoxy composite: load bearing and time-dependent behavior. Biomass Convers Biorefinery. 2023;1–8. [Google Scholar]
43. Surajarusarn B, Hajjar-Garreau S, Schrodj G, Mougin K, Amornsakchai T. Comparative study of pineapple leaf microfiber and aramid fiber reinforced natural rubbers using dynamic mechanical analysis. Polym Test. 2020;82:106289. doi:10.1016/j.polymertesting.2019.106289. [Google Scholar] [CrossRef]
44. Cavalcanti DK, Banea MD, Neto JDSS, Lima RAA. Comparative analysis of the mechanical and thermal properties of polyester and epoxy natural fibre-reinforced hybrid composites. J Compos Mater. 2021;55(12):1683–92. doi:10.1177/0021998320976811. [Google Scholar] [CrossRef]
45. Dhanunjayarao BN, Sanivada UK, Swamy Naidu NV, Fangueiro R. Effect of graphite particulate on mechanical characterization of hybrid polymer composites. J Ind Text. 2022;51(2_suppl):2594S–615S. doi:10.1177/15280837211010670. [Google Scholar] [CrossRef]
46. Jenish I, Sahayaraj AF, Suresh V, Mani Raj J, Appadurai, Irudaya Raj EF, et al. Analysis of the hybrid of mudar/snake grass fiber-reinforced epoxy with nano-silica filler composite for structural application. Adv Mater Sci Eng. 2022;2022:1–10. [Google Scholar]
47. Mohanavel V, Suresh Kumar S, Vairamuthu J, Ganeshan P, NagarajaGanesh B. Influence of stacking sequence and fiber content on the mechanical properties of natural and synthetic fibers reinforced penta-layered hybrid composites. J Nat Fibers. 2022;19(13):5258–70. doi:10.1080/15440478.2021.1875368. [Google Scholar] [CrossRef]
48. Cheng M, Zhong Y, Kureemun U, Cao D, Hu H, Lee HP, et al. Environmental durability of carbon/flax fiber hybrid composites. Compos Struct. 2020;234:111719. doi:10.1016/j.compstruct.2019.111719. [Google Scholar] [CrossRef]
49. Vinod A, Pulikkalparambil H, Jagadeesh P, Rangappa SM, Siengchin S. Recent advancements in lignocellulose biomass-based carbon fiber: synthesis, properties, and applications. Heliyon. 2023;9(3):E13614. doi:10.1016/j.heliyon.2023.e13614. [Google Scholar] [PubMed] [CrossRef]
50. Rashid B, Jawaid M, Fouad H, Saba N, Awad S, Khalaf E, et al. Improving the thermal properties of olive/bamboo fiber-based epoxy hybrid composites. Polym Compos. 2022;43(5):3167–74. doi:10.1002/pc.v43.5. [Google Scholar] [CrossRef]
51. Varshney S, Mishra N, Gupta MK. Progress in nanocellulose and its polymer based composites: a review on processing, characterization, and applications. Polym Compos. 2021;42(8):3660–86. doi:10.1002/pc.v42.8. [Google Scholar] [CrossRef]
52. Sanjeevi S, Shanmugam V, Kumar S, Ganesan V, Sas G, Johnson DJ, et al. Effects of water absorption on the mechanical properties of hybrid natural fibre/phenol formaldehyde composites. Sci Rep. 2021;11(1):13385. doi:10.1038/s41598-021-92457-9. [Google Scholar] [PubMed] [CrossRef]
53. Bichang’a DO, Aramide FO, Oladele IO, Alabi OO. A review on the parameters affecting the mechanical, physical, and thermal properties of natural/synthetic fibre hybrid reinforced polymer composites. Adv Mater Sci Eng. 2022. doi:10.1155/2022/7024099. [Google Scholar] [CrossRef]
54. Patel BY, Patel HK. Retting of banana pseudostem fibre using Bacillus strains to get excellent mechanical properties as biomaterial in textile & fiber industry. Heliyon. 2022;8(9):E10652 doi:10.1016/j.heliyon.2022.e10652. [Google Scholar] [PubMed] [CrossRef]
55. Tanasă F, Zănoagă M, Teacă CA, Nechifor M, Shahzad A. Modified hemp fibers intended for fiber‐reinforced polymer composites used in structural applications—a review. I. Methods of modification. Polym Comp. 2020;41(1):5–31. doi:10.1002/pc.25354. [Google Scholar] [CrossRef]
56. Seki Y, Selli F, Erdoğan ÜH, Atagür M, Seydibeyoğlu MÖ. A review on alternative raw materials for sustainable production: novel plant fibers. Cellulose. 2022;29(9):4877–918. doi:10.1007/s10570-022-04597-4. [Google Scholar] [CrossRef]
57. Chatterjee A, Kumar S, Singh H. Tensile strength and thermal behavior of jute fibre reinforced polypropylene laminate composite. Compos Commun. 2020;22:100483. doi:10.1016/j.coco.2020.100483. [Google Scholar] [CrossRef]
58. Ighalo JO, Adeyanju CA, Ogunniyi S, Adeniyi AG, Abdulkareem SA. An empirical review of the recent advances in treatment of natural fibers for reinforced plastic composites. Compos Interfaces. 2021;28(9):925–60. doi:10.1080/09276440.2020.1826274. [Google Scholar] [CrossRef]
59. Mahmud MA, Abir N, Anannya FR, Khan AN, Rahman AM, Jamine N. Coir fiber as thermal insulator and its performance as reinforcing material in biocomposite production. Heliyon. 2023;9(5):E15597. doi:10.1016/j.heliyon.2023.e15597. [Google Scholar] [PubMed] [CrossRef]
60. Veerasimman A, Shanmugam V, Rajendran S, Johnson DJ, Subbiah A, Koilpichai J, et al. Thermal properties of natural fiber sisal based hybrid composites—a brief review. J Nat Fibers. 2022;19(12):4696–706. doi:10.1080/15440478.2020.1870619. [Google Scholar] [CrossRef]
61. Jena PK, Mohanty JR, Nayak S. Effect of surface modification of vetiver fibers on their physical and thermal properties. J Nat Fibers. 2022;19(1):25–36. doi:10.1080/15440478.2020.1726249. [Google Scholar] [CrossRef]
62. Mohanavel V, Raja T, Yadav A, Ravichandran M, Winczek J. Evaluation of mechanical and thermal properties of jute and ramie reinforced epoxy-based hybrid composites. J Nat Fibers. 2022;19(14):8022–32. doi:10.1080/15440478.2021.1958432. [Google Scholar] [CrossRef]
63. Yun KK, Hossain MS, Han S, Seunghak C. Rheological, mechanical properties, and statistical significance analysis of shotcrete with various natural fibers and mixing ratios. Case Stud Constr Mater. 2022;16(4):e00833. doi:10.1016/j.cscm.2021.e00833. [Google Scholar] [CrossRef]
64. Radzuan NAM, Gunasegran M, Khalid NN. The effect of graphene addition on the young’s modulus and tensile strength of kenaf fibre composites. IOP Conf Series: Mater Sci Eng. 2021 Feb;1078(1):012006. doi:10.1088/1757-899X/1078/1/012006. [Google Scholar] [CrossRef]
65. Setyayunita T, Widyorini R, Marsoem SN, Irawati D. Study on the characteristics of NaCl treated kenaf fiber epoxy composite board. IOP Conf Series: Earth Environ Sci. 2021 Nov;891(1):012006. [Google Scholar]
66. Nurazzi NM, Asyraf MRM, Fatimah Athiyah S, Shazleen SS, Rafiqah SA, Harussani MM, et al. A review on mechanical performance of hybrid natural fiber polymer composites for structural applications. Polymers. 2021;13(13):2170. doi:10.3390/polym13132170. [Google Scholar] [PubMed] [CrossRef]
67. Nurazzi NM, Norrrahim MNF, Sabaruddin FA, Shazleen SS, Ilyas RA, Lee SH, et al. Mechanical performance evaluation of bamboo fibre reinforced polymer composites and its applications: a review. Funct Compos Struct. 2022;4(1):015009. doi:10.1088/2631-6331/ac5b1a. [Google Scholar] [CrossRef]
68. Maurya AK, de Souza FM, Dawsey T, Gupta RK. Biodegradable polymers and composites: recent development and challenges. Polym Compos. 2024;45(4):2896–918. doi:10.1002/pc.v45.4. [Google Scholar] [CrossRef]
69. Sharma AP, Khan SH, Velmurugan R. Effect of through thickness separation of fiber orientation on low velocity impact response of thin composite laminates. Heliyon. 2019;5(10):E02706. doi:10.1016/j.heliyon.2019.e02706. [Google Scholar] [PubMed] [CrossRef]
70. Jagadeesh P, Rangappa SM, Suyambulingam I, Siengchin S, Puttegowda M, Binoj JS, et al. Drilling characteristics and properties analysis of fiber reinforced polymer composites: a comprehensive review. Heliyon. 2023;9(3):E14428. doi:10.1016/j.heliyon.2023.e14428. [Google Scholar] [PubMed] [CrossRef]
71. Akhil UV, Radhika N, Saleh B, Aravind Krishna S, Noble N, Rajeshkumar L. A comprehensive review on plant-based natural fiber reinforced polymer composites: fabrication, properties, and applications. Polym Compos. 2023;44(5):2598–633. doi:10.1002/pc.v44.5. [Google Scholar] [CrossRef]
72. Yu S, Hwang YH, Hwang JY, Hong SH. Analytical study on the 3D-printed structure and mechanical properties of basalt fiber-reinforced PLA composites using X-ray microscopy. Compos Sci Technol. 2019;175:18–27. doi:10.1016/j.compscitech.2019.03.005. [Google Scholar] [CrossRef]
73. Kannan G, Thangaraju R. Recent progress on natural lignocellulosic fiber reinforced polymer composites: a review. J Nat Fibers. 2022;19(13):7100–31. doi:10.1080/15440478.2021.1944425. [Google Scholar] [CrossRef]
74. Yavas D, Zhang Z, Liu Q, Wu D. Interlaminar shear behavior of continuous and short carbon fiber reinforced polymer composites fabricated by additive manufacturing. Compos Part B: Eng. 2021;204:108460. doi:10.1016/j.compositesb.2020.108460. [Google Scholar] [CrossRef]
75. Mehdikhani M, Gorbatikh L, Verpoest I, Lomov SV. Voids in fiber-reinforced polymer composites: a review on their formation, characteristics, and effects on mechanical performance. J Compos Mater. 2019;53(12):1579–669. doi:10.1177/0021998318772152. [Google Scholar] [CrossRef]
76. Kerni L, Singh S, Patnaik A, Kumar N. A review on natural fiber reinforced composites. Mater Today: Proc. 2020;28:1616–21. [Google Scholar]
77. Sultan H, Safri A, Shah M, Majid A. The effects of stacking sequence on dynamic mechanical properties and thermal degradation of kenaf/jute hybrid composites. J Renew Mater. 2021;9(1):73–84. doi:10.32604/jrm.2021.011385. [Google Scholar] [CrossRef]
78. Salim MS, Ariawan D, Ahmad Rasyid MF, Mat Taib R, Ahmad Thirmizir MZ, Mohd Ishak ZA. Accelerated weathering and water absorption behavior of kenaf fiber reinforced acrylic based polyester composites. Front Mater. 2020;7:26. doi:10.3389/fmats.2020.00026. [Google Scholar] [CrossRef]
79. Singh MK, Zafar S, Rangappa SM, Siengchin S. Mechanical performance study of kenaf/HDPE composite for structural applications under wet or outdoor environments. J Nat Fibers. 2022;19(16):14115–30. doi:10.1080/15440478.2022.2116519. [Google Scholar] [CrossRef]
80. Daramola OO, Akinwekomi AD, Adediran AA, Akindote-White O, Sadiku ER. Mechanical performance and water uptake behaviour of treated bamboo fibre-reinforced high-density polyethylene composites. Heliyon. 2019;5(7):e02028. doi:10.1016/j.heliyon.2019.e02028. [Google Scholar] [PubMed] [CrossRef]
81. Husnil Y, Ismojo I, Yuanita E, Novovic AA, Enyta T, Chalid M. The effect of bleaching treatment on the mechanical strength of PP-Kenaf composite. AIP Conf Proc. 2019 Nov;2175(1):020051. [Google Scholar]
82. Hasan A, Rabbi MS, Billah MM, Hasib MA. Effect of chemical treatments on properties of injection molded Nypa fruticans fiber reinforced polypropylene composite. Heliyon. 2022;8(12):e11967. doi:10.1016/j.heliyon.2022.e11967. [Google Scholar] [PubMed] [CrossRef]
83. Joharudin NFM, Mustapa MS, Supawi A, Latif NA, Hussin WNNW, Alias MF, et al. The effect of UV irradiation on tensile strength of polypropylene reinforced Kenaf fiber and peat soil. J Phy: Conf Series. 2021 Nov;2065(1):012003. [Google Scholar]
84. Saeed U, Dawood U, Ali AM. Cellulose triacetate fiber-reinforced polystyrene composite. J Thermoplastic Compos Mater. 2021;34(5):707–21. doi:10.1177/0892705719847249. [Google Scholar] [CrossRef]
85. Ramesh MJPIMS. Flax (Linum usitatissimum L.) fibre reinforced polymer composite materials: a review on preparation, properties and prospects. Prog Mater Sci. 2019;102:109–66. doi:10.1016/j.pmatsci.2018.12.004. [Google Scholar] [CrossRef]
86. Khalid MY, Imran R, Arif ZU, Akram N, Arshad H, Al Rashid A, et al. Developments in chemical treatments, manufacturing techniques and potential applications of natural-fibers-based biodegradable composites. Coatings. 2021;11(3):293. doi:10.3390/coatings11030293. [Google Scholar] [CrossRef]
87. Singh GP, Mangal R. A comprehensive review of natural fiber reinforced composite and their modern application. Mater Today: Proc. 2023;92:542–8. doi:10.1016/j.matpr.2023.03.745. [Google Scholar] [CrossRef]
88. Kakarla AB, Nukala SG. Biodegradable materials. In: Materials for lightweight constructions. CRC Press; 2022. p. 161–90. [Google Scholar]
89. Godara SS. Effect of chemical modification of fiber surface on natural fiber composites: a review. Mater Today: Proc. 2019;18:3428–34. [Google Scholar]
90. Ferreira DP, Cruz J, Fangueiro R. Surface modification of natural fibers in polymer composites. In: Green composites for automotive applications; 2019. p. 3–41. [Google Scholar]
91. Adediran AA, Balogun OA, Akinwande AA, Adesina OS, Olasoju OS. Influence of chemical treatment on the properties of cement-paper hybrid composites for ceiling board application. Heliyon. 2020;6(7):E04512. doi:10.1016/j.heliyon.2020.e04512. [Google Scholar] [PubMed] [CrossRef]
92. Alim MA, Moniruzzaman M, Hossain MM, Repon MR, Hossain I, Jalil MA. Manufacturing and compatibilization of binary blends of superheated steam treated jute and poly (lactic acid) biocomposites by melt-blending technique. Heliyon. 2022;8(8):E09923. doi:10.1016/j.heliyon.2022.e09923. [Google Scholar] [PubMed] [CrossRef]
93. Mohammed M, Rahman R, Mohammed AM, Adam T, Betar BO, Osman AF, et al. Surface treatment to improve water repellence and compatibility of natural fiber with polymer matrix: recent advancement. Polym Test. 2022;115:107707. [Google Scholar]
94. Hassan MN, Mondal MS, Hasan N, Reza MM, Rahman MI, Sarkar J, et al. Evaluation of physico-mechanical properties of naturally dyed betel-nut leaf plate (BLPF)–banana blended fabric. Heliyon. 2023;9(2):E13571. doi:10.1016/j.heliyon.2023.e13571. [Google Scholar] [PubMed] [CrossRef]
95. Verma A, Parashar A, Jain N, Singh VK, Rangappa SM, Siengchin S. Surface modification techniques for the preparation of different novel biofibers for composites. Biofibers Biopolymers Biocompos: Synth Charact Prop. 2020;1–34. [Google Scholar]
96. Hosseini SB, Gaff M, Li H, Hui D. Effect of fiber treatment on physical and mechanical properties of natural fiber-reinforced composites: a review. Rev Adv Mater Sci. 2023;62(1):20230131. doi:10.1515/rams-2023-0131. [Google Scholar] [CrossRef]
97. Pillai RR, Thomas V. Plasma surface engineering of natural and sustainable polymeric derivatives and their potential applications. Polymers. 2023;15(2):400. doi:10.3390/polym15020400. [Google Scholar] [PubMed] [CrossRef]
98. Syduzzaman M, Al Faruque MA, Bilisik K, Naebe M. Plant-based natural fibre reinforced composites: a review on fabrication, properties and applications. Coatings. 2020;10(10):973. doi:10.3390/coatings10100973. [Google Scholar] [CrossRef]
99. Chowdhury H, Rahman MM, Uddin MT. Improvement of mechanical properties of polypropylene composite using filler, modifier and reinforcement. J Phy: Conf Series. 2018 Sep;1086(1):012003. [Google Scholar]
100. Behera S, Gautam RK, Mohan S. Study of mechanical properties of chemically treated kenaf fiber and its composites. In: Advancement in materials processing technology. Singapore: Springer Singapore; 2022. p. 115–23. [Google Scholar]
101. Yosr BM, Mounir J, Foued K, Slah M, Durand B. Characterization and investigation of tensile properties of kenaf fiber reinforced polyester composite material. J Nat Fibers. 2022;19(14):8355–66. doi:10.1080/15440478.2021.1964128. [Google Scholar] [CrossRef]
102. Gargol M, Klepka T, Klapiszewski Ł, Podkościelna B. Synthesis and thermo-mechanical study of epoxy resin-based composites with waste fibers of hemp as an eco-friendly filler. Polymers. 2021;13(4):503. doi:10.3390/polym13040503. [Google Scholar] [PubMed] [CrossRef]
103. Chandrasekar M, Senthilkumar K, Jawaid M, Mahmoud MH, Fouad H, Sain M. Mechanical, morphological and dynamic mechanical analysis of pineapple leaf/washingtonia trunk fibres based biophenolic hybrid composites. J Polym Environ. 2022;30(10):4157–65. doi:10.1007/s10924-022-02482-6. [Google Scholar] [CrossRef]
104. Pirityi DZ, Pölöskei K. Thermomechanical devulcanization of ethylene propylene diene monomer rubber and its application in blends with high-density polyethylene. J Appl Polym Sci. 2021;138(13):50090. doi:10.1002/app.v138.13. [Google Scholar] [CrossRef]
105. Aykanat O, Ermeydan MA. Production of basalt/wood fiber reinforced polylactic acid hybrid biocomposites and investigation of performance features including insulation properties. Polym Compos. 2022;43(6):3519–30. doi:10.1002/pc.26633. [Google Scholar] [CrossRef]
106. Younas M, Noreen A, Sharif A, Majeed A, Hassan A, Tabasum S, et al. A review on versatile applications of blends and composites of CNC with natural and synthetic polymers with mathematical modeling. Int J Biol Macromol. 2019;124(3):591–626. doi:10.1016/j.ijbiomac.2018.11.064. [Google Scholar] [PubMed] [CrossRef]
107. Joy J, George E, Thomas S, Anas S. Effect of filler loading on polymer chain confinement and thermomechanical properties of epoxy/boron nitride (h-BN) nanocomposites. New J Chem. 2020;44(11):4494–503. doi:10.1039/C9NJ05834F. [Google Scholar] [CrossRef]
108. Reddy BM, Reddy RM, Reddy BCM, Reddy PV, Rao HR, Reddy YM. The effect of granite powder on mechanical, structural and water absorption characteristics of alkali treated cordia dichotoma fiber reinforced polyester composite. Polym Test. 2020;91(11):106782. doi:10.1016/j.polymertesting.2020.106782. [Google Scholar] [CrossRef]
109. Merzah ZF, Fakhry S, Allami TG, Yuhana NY, Alamiery A. Enhancement of the properties of hybridizing epoxy and nanoclay for mechanical, industrial, and biomedical applications. Polymers. 2022;14(3):526. doi:10.3390/polym14030526. [Google Scholar] [PubMed] [CrossRef]
110. Muslim RF, Majeed IY, Saleh SE, Saleh MM, Owaid MN, Abbas JA. Preparation, characterization and antibacterial activity of some new oxazolidin-5-one derivatives derived from imine compounds. J Chem Health Risks. 2022;12(4):725–32. [Google Scholar]
111. Fortelný I, Jůza J. Modifications of simple models of polymer blend compatibilization using block copolymer. Colloid Polym Sci. 2023;1–16. [Google Scholar]
112. Yu X, Ren J, He J, Su L, Liu F. Effect of compatibilizer on the structure and property of polycarbonate/polypropylene alloys. J Appl Polym Sci. 2022;139(40):e52957. doi:10.1002/app.v139.40. [Google Scholar] [CrossRef]
113. Abdilla A, D’Ambra CA, Geng Z, Shin JJ, Czuczola M, Goldfeld DJ, et al. Silicone-based polymer blends: enhancing properties through compatibilization. J Polym Sci. 2021;59(19):2114–28. doi:10.1002/pola.v59.19. [Google Scholar] [CrossRef]
114. Sánchez-Safont EL, Aldureid A, Lagarón JM, Cabedo L, Gámez-Pérez J. Study of the compatibilization effect of different reactive agents in PHB/natural fiber-based composites. Polymers. 2020;12(9):1967. doi:10.3390/polym12091967. [Google Scholar] [PubMed] [CrossRef]
115. Rahem Z, Mayouf I, Guessoum M, Delaite C, Douibi A, Lallam A. Compatibilization of biocomposites based on sponge-gourd natural fiber reinforced poly (lactic acid). Polym Compos. 2019;40(12):4489–99. doi:10.1002/pc.v40.12. [Google Scholar] [CrossRef]
116. Mohammed M, Rasidi MSM, Mohammed AM, Rahman R, Osman AF, Adam T, et al. Interfacial bonding mechanisms of natural fibre-matrix composites: an overview. BioResources. 2022;17(4):7031–90. [Google Scholar]
117. Nurazzi NM, Asyraf MRM, Rayung M, Norrrahim MNF, Shazleen SS, Rani MSA, et al. Thermogravimetric analysis properties of cellulosic natural fiber polymer composites: a review on influence of chemical treatments. Polymers. 2021;13(16):2710. doi:10.3390/polym13162710. [Google Scholar] [PubMed] [CrossRef]
118. Gholampour A, Ozbakkaloglu T. A review of natural fiber composites: properties, modification and processing techniques, characterization. Appl J Mater Sci. 2020;55(3):829–92. doi:10.1007/s10853-019-03990-y. [Google Scholar] [CrossRef]
119. Anbupalani MS, Venkatachalam CD, Rathanasamy R. Influence of coupling agent on altering the reinforcing efficiency of natural fibre-incorporated polymers–A review. J Reinforced Plast Compos. 2020;39(13–14):520–44. [Google Scholar]
120. Elfaleh I, Abbassi F, Habibi M, Ahmad F, Guedri M, Nasri M, et al. A comprehensive review of natural fibers and their composites: an eco-friendly alternative to conventional materials. Results Eng. 2023;19:101271. doi:10.1016/j.rineng.2023.101271. [Google Scholar] [CrossRef]
121. Pesaranhajiabbas E, Misra M, Mohanty AK. Recent progress on biodegradable polylactic acid based blends and their biocomposites: a comprehensive review. Int J Biol Macromol. 2023;253:126231. doi:10.1016/j.ijbiomac.2023.126231. [Google Scholar] [PubMed] [CrossRef]
122. Oleiwi JK, Mohammed RA. Comparison of the wear behavior and hardness of vinylester resin reinforced by glass fiber and nano ZrO2 and Fe3O4. Revue des Compos et des Matériaux Avancés. 2021;31(6):325–33. [Google Scholar]
123. Fatalla AA, Tukmachi MS, Jani GH. Assessment of some mechanical properties of PMMA/silica/zirconia nanocomposite as a denture base material. IOP Conf Series: Mater Sci Eng. 2020 Nov;987(1):012031. doi:10.1088/1757-899X/987/1/012031. [Google Scholar] [CrossRef]
124. Owonubi SJ, Mukwevho E, Revaprasadu N. Nanoparticle-based delivery of plant metabolites. In: The therapeutic properties of medicinal plants. Apple Academic Press; 2019. p. 285–316. [Google Scholar]
125. Oleiwi JK, Abass BA. Thermal properties of polymeric composites reinforced by nanoceramic materials. Int J Mech Prod Eng Res Dev. 2018;8(6):517–24. [Google Scholar]
126. Mohammed M, Rahman R, Mohammed AM, Betar BO, Osman AF, Adam T, et al. Improving hydrophobicity and compatibility between kenaf fiber and polymer composite by surface treatment with inorganic nanoparticles. Arab J Chem. 2022;15(11):104233. doi:10.1016/j.arabjc.2022.104233. [Google Scholar] [CrossRef]
127. Mohammed M, Betar BO, Rahman R, Mohammed AM, Osman AF, Jaafar M, et al. Zinc oxide nano particles integrated kenaf/unsaturated polyester biocomposite. J Renew Mater. 2019;7(10):967–82. doi:10.32604/jrm.2019.07562. [Google Scholar] [CrossRef]
128. Adak B, Butola BS, Joshi M. Calcination of UV shielding nanopowder and its effect on weather resistance property of polyurethane nanocomposite films. J Mater Sci. 2019;54(19):12698–712. doi:10.1007/s10853-019-03739-7. [Google Scholar] [CrossRef]
129. Owen MM, Achukwu EO, Romli AZ, Ramlee MH, Abdullah AH, Shuib S, et al. Improved thermal and mechanical properties of kenaf Fiber/ABS polymer composites via resin coating treatment. Pertanika J Sci Technol. 2023;31(S1):39–57. doi:10.47836/pjst. [Google Scholar] [CrossRef]
130. Salih SE, Oleiwi JK, Alaa Mohammed T. Investigation of hardness and flexural properties of pmma nano composites and pmma hybrids nano composites reinforced by different nano particles materials used in dental applications. Eng Technol J. 2016;34(15):2838–53. doi:10.30684/etj.34.15A.6. [Google Scholar] [CrossRef]
131. Younis S, Oleiwi JK, Mohammed RA. Some mechanical properties of polymer matrix composites reinforced by nano silica particles and glass fibers. Eng Technol J. 2018;36(12):1283–9. doi:10.30684/etj.36.12A.10. [Google Scholar] [CrossRef]
132. Fadhil RN, Mahdi SH. Effect of pistachio husk waste powder additive of epoxy composites. Pak J Sci Ind Res Series A: Phys Sci. 2023;66(3):249–54. [Google Scholar]
133. Mugesh Raja V, Sathees Kumar S. Exploration of mechanical attributes, thermal behaviors and atomic force analysis of alkali treated hybrid polyester composites for an engineering application. Fibers Polym. 2021;22(9):2535–42. doi:10.1007/s12221-021-1252-y. [Google Scholar] [CrossRef]
134. Krishnudu DM, Sreeramulu D, Reddy PV. A study of filler content influence on dynamic mechanical and thermal characteristics of coir and luffa cylindrica reinforced hybrid composites. Constr Build Mater. 2020;251:119040. doi:10.1016/j.conbuildmat.2020.119040. [Google Scholar] [CrossRef]
135. Mohammed M, Oleiwi JK, Jawad AJAM, Mohammed AM, Osman AF, Rahman R, et al. Effect of zinc oxide surface treatment concentration and nanofiller loading on the flexural properties of unsaturated polyester/kenaf nanocomposites. Heliyon. 2023;9(9):e20051. doi:10.1016/j.heliyon.2023.e20051. [Google Scholar] [PubMed] [CrossRef]
136. Aravindh M, Sathish S, Ranga Raj R, Karthick A, Mohanavel V, Patil PP, et al. A review on the effect of various chemical treatments on the mechanical properties of renewable fiber-reinforced composites. Adv Mater Sci Eng. 2022;2022(5):1–24. doi:10.1155/2022/2009691. [Google Scholar] [CrossRef]
137. Hazrol MD, Sapuan SM, Ilyas RA, Zainudin ES, Zuhri MYM, Abdul NI. Effect of corn husk fibre loading on thermal and biodegradable properties of kenaf/cornhusk fibre reinforced corn starch-based hybrid composites. Heliyon. 2023;9(4):e15153. doi:10.1016/j.heliyon.2023.e15153. [Google Scholar] [PubMed] [CrossRef]
138. Baigh TA, Nanzeeba F, Hamim HR, Habib MA. A comprehensive study on the effect of hybridization and stacking sequence in fabricating cotton-blended jute and pineapple leaf fibre biocomposites. Heliyon. 2023;9(9):e19792. doi:10.1016/j.heliyon.2023.e19792. [Google Scholar] [PubMed] [CrossRef]
139. Muralidharan ND, Subramanian J, Rajamanickam SK, Gopalan V. An experimental investigation of flame retardancy and thermal stability of treated and untreated kenaf fiber reinforced epoxy composites. J Polym Eng. 2023;43(10):865–74. doi:10.1515/polyeng-2023-0128. [Google Scholar] [CrossRef]
140. Rusdi RAA, Halim NA, Nurazzi NM, Abidin ZHZ, Abdullah N, Ros FC, et al. The effect of layering structures on mechanical and thermal properties of hybrid bacterial cellulose/Kevlar reinforced epoxy composites. Heliyon. 2022;8(6):e09442. doi:10.1016/j.heliyon.2022.e09442. [Google Scholar] [PubMed] [CrossRef]
141. Reddy PV, Prasad PR, Krishnudu DM, Hussain P. Influence of fillers on mechanical properties of prosopis juliflora fiber reinforced hybrid composites. Mater Today: Proc. 2019;19:384–7. [Google Scholar]
142. Bash AM, Oleiwi JK, Othman TT. A review of some characteristics of a composite hybrid socket for prosthetics derived from plant fibers. Key Eng Mater. 2022;937(5):99–106. doi:10.4028/v-fx8n80. [Google Scholar] [CrossRef]
143. Mohammed A, Rao DN. Investigation on mechanical properties of flax fiber/expanded polystyrene waste composites. Heliyon. 2023;9(3):e13310. doi:10.1016/j.heliyon.2023.e13310. [Google Scholar] [PubMed] [CrossRef]
144. Jesthi DK, Nayak RK. Improvement of mechanical properties of hybrid composites through interply rearrangement of glass and carbon woven fabrics for marine application. Compos Part B: Eng. 2019;168:467–75. doi:10.1016/j.compositesb.2019.03.042. [Google Scholar] [CrossRef]
145. Oleiwi JK, Mohammed AA. Assessment of the mechanical properties of hybrid polymer composites for denture applications. J Phys Sci. 2022;33(1):83–95. doi:10.21315/jps. [Google Scholar] [CrossRef]
146. Supian ABM, Jawaid M, Rashid B, Fouad H, Saba N, Dhakal HN, et al. Mechanical and physical performance of date palm/bamboo fibre reinforced epoxy hybrid composites. J Mater Res Technol. 2021;15:1330–41. doi:10.1016/j.jmrt.2021.08.115. [Google Scholar] [CrossRef]
147. Abd El-baky MA, Attia MA, Abdelhaleem MM, Hassan MA. Mechanical characterization of hybrid composites based on flax, basalt and glass fibers. J Compos Mater. 2020;54(27):4185–205. doi:10.1177/0021998320928509. [Google Scholar] [CrossRef]
148. Rout J, Misra M, Tripathy SS, Nayak SK, Mohanty AK. The influence of fibre treatment on the performance of coir-polyester composites. Compos Sci Technol. 2001;61(9):1303–10. doi:10.1016/S0266-3538(01)00021-5. [Google Scholar] [CrossRef]
149. Sumesh KR, Kavimani V, Rajeshkumar G, Indran S, Saikrishnan G. Effect of banana, pineapple and coir fly ash filled with hybrid fiber epoxy based composites for mechanical and morphological study. J Mater Cycles Waste Manag. 2021;23(4):1277–88. doi:10.1007/s10163-021-01196-6. [Google Scholar] [CrossRef]
150. Oliveira Filho EGD, Luz FSD, Fujiyama RT, Silva ACRD, Candido VS, Monteiro SN. Effect of chemical treatment and length of raffia fiber (Raphia vinifera) on mechanical stiffening of polyester composites. Polymers. 2020;12(12):2899. doi:10.3390/polym12122899. [Google Scholar] [PubMed] [CrossRef]
151. Raja AA, Geethan KAV, Kumar SS, Kumar PS. Influence of mechanical attributes, water absorption, heat deflection features and characterization of natural fibers reinforced epoxy hybrid composites for an engineering application. Fibers Polym. 2021;22(12):3444–55. doi:10.1007/s12221-021-0222-8. [Google Scholar] [CrossRef]
152. Boopathi S, Venkatesan G, Anton Savio Lewise K. Mechanical properties analysis of kenaf-grewia–hair fiber-reinforced composite. In: Recent advances in mechanical engineering. Singapore: Springer Nature Singapore; 2022. p. 101–10. [Google Scholar]
153. Jothibasu S, Mohanamurugan S, Vijay R, Lenin Singaravelu D, Vinod A, Sanjay MR. Investigation on the mechanical behavior of areca sheath fibers/jute fibers/glass fabrics reinforced hybrid composite for light weight applications. J Ind Text. 2020;49(8):1036–60. doi:10.1177/1528083718804207. [Google Scholar] [CrossRef]
154. Birniwa AH, Abdullahi SSA, Yakasai MY, Ismaila A. Studies on physico-mechanical behaviour of kenaf/glass fiber reinforced epoxy hybrid composites. Bull Chem Soc Ethiop. 2021;35(1):171–84. doi:10.4314/bcse.v35i1.15. [Google Scholar] [CrossRef]
155. Benkhelladi A, Laouici H, Bouchoucha A. Tensile and flexural properties of polymer composites reinforced by flax, jute and sisal fibres. Int J Adv Manuf Technol. 2020;108:895–916. doi:10.1007/s00170-020-05427-2. [Google Scholar] [CrossRef]
156. Arjmandi R, Yıldırım I, Hatton F, Hassan A, Jefferies C, Mohamad Z, et al. Kenaf fibers reinforced unsaturated polyester composites: a review. J Eng Fibers Fabrics. 2021;16:15589250211040184. [Google Scholar]
157. Baihaqi NN, Khalina A, Nurazzi NM, Aisyah HA, Sapuan SM, Ilyas RA. Effect of fiber content and their hybridization on bending and torsional strength of hybrid epoxy composites reinforced with carbon and sugar palm fibers. Polimery. 2021;66(1):36–43. doi:10.14314/polimery.2021.1.5. [Google Scholar] [CrossRef]
158. Naveen J, Jawaid M, Amuthakkannan P, Chandrasekar M. Mechanical and physical properties of sisal and hybrid sisal fiber-reinforced polymer composites. In: Mechanical and physical testing of biocomposites, fibre-reinforced composites and hybrid composites. Woodhead Publishing; 2019. p. 427–40. [Google Scholar]
159. Afzaluddin A, Jawaid M, Salit MS, Ishak MR. Physical and mechanical properties of sugar palm/glass fiber reinforced thermoplastic polyurethane hybrid composites. J Mater Res Technol. 2019;8(1):950–9. doi:10.1016/j.jmrt.2018.04.024. [Google Scholar] [CrossRef]
160. TG YG, P M, Mavinkere Rangappa S, Siengchin S, Jawaid M. Mechanical and thermal properties of flax/carbon/kevlar based epoxy hybrid composites. Polym Compos. 2022;43(8):5649–62. doi:10.1002/pc.26880. [Google Scholar] [CrossRef]
161. Ismail M, Rejab MRM, Siregar JP, Mohamad Z, Quanjin M, Mohammed AA. Mechanical properties of hybrid glass fiber/rice husk reinforced polymer composite. Mater Today: Proc. 2020;27:1749–55. [Google Scholar]
162. Khalid MY, Nasir MA, Ali A, Al Rashid A, Khan MR. Experimental and numerical characterization of tensile property of jute/carbon fabric reinforced epoxy hybrid composites. SN Appl Sci. 2020;2(4):577. doi:10.1007/s42452-020-2403-2. [Google Scholar] [CrossRef]
163. Pereira AL, Banea MD, Neto JS, Cavalcanti DK. Mechanical and thermal characterization of natural intralaminar hybrid composites based on sisal. Polymers. 2020;12(4):866. doi:10.3390/polym12040866. [Google Scholar] [PubMed] [CrossRef]
164. Pulleti SS, Singh SB. Development and characterization of hemp/carbon and hemp/glass hybrid and novel functionally graded hybrid composites for structural applications. Polym Compos. 2024. doi:10.1002/pc.28540. [Google Scholar] [CrossRef]
165. Alshammari BA, Saba N, Alotaibi MD, Alotibi MF, Jawaid M, Alothman OY. Evaluation of mechanical, physical, and morphological properties of epoxy composites reinforced with different date palm fillers. Materials. 2019;12(13):2145. doi:10.3390/ma12132145. [Google Scholar] [PubMed] [CrossRef]
166. RaviKumar P, Rajeshkumar G, Prakash Maran J, Al-Dhabi NA, Karuppiah P. Evaluation of mechanical and water absorption behaviors of jute/carbon fiber reinforced polyester hybrid composites. J Nat Fibers. 2022;19(13):6521–33. doi:10.1080/15440478.2021.1924339. [Google Scholar] [CrossRef]
167. Manoharan S, Saikrishnan G, Arjun S. Influence of bagasse/sisal fibre stacking sequence on the mechanical characteristics of hybrid-epoxy composites. J Nat Fibers. 2019;17(10):1497–507. [Google Scholar]
168. Sathish T, Jagadeesh P, Rangappa SM, Siengchin S. Studies on mechanical and thermal properties of cellulosic fiber fillers reinforced epoxy composites. Polym Compos. 2022;43(7):4297–305. doi:10.1002/pc.26690. [Google Scholar] [CrossRef]
169. Sivasankar GA, Karthick PA, Boopathi C, Brindha S, Nirmalraj RJT, Benham A. Evaluation and comparison on mechanical properties of abaca and hemp fiber reinforced hybrid epoxy resin composites. Mater Today: Proc. 2023. doi:10.1016/j.matpr.2023.04.400. [Google Scholar] [CrossRef]
170. Suriyaprakash M, Nallusamy M, Shanjai KSR, Akash N, Rohith V. Experimental investigation on mechanical properties of Ramie, Hemp fiber and coconut shell particle hybrid composites with reinforced epoxy resin. Mater Today: Proc. 2023;72:2952–6. [Google Scholar]
171. Jasim KA, Fadhil RN, Shaban AH, Jaafar HI, Maiyaly BK, Aleabi SH, et al. The effects of copper additives on the glass transition temperature and hardness for epoxy resin. Prog Ind Ecol Int J. 2019;13(2):163–72. doi:10.1504/PIE.2019.099357. [Google Scholar] [CrossRef]
172. Mostafa NH. Tensile and fatigue properties of Jute-Glass hybrid fibre reinforced epoxy composites. Mater Res Express. 2019;6(8):085102. doi:10.1088/2053-1591/ab21f9. [Google Scholar] [CrossRef]
173. Perry JI, Walley SM. Measuring the effect of strain rate on deformation and damage in fibre-reinforced composites: a review. J Dyn Behav Mater. 2022;8(2):178–213. doi:10.1007/s40870-022-00331-0. [Google Scholar] [CrossRef]
174. Velu S, Joseph JK, Sivakumar M, Raja VB, Palanikumar K, Lenin N. Experimental investigation on the mechanical properties of carbon-glass-jute fiber reinforced epoxy hybrid composites. Mater Today: Proc. 2021;46:3566–71. [Google Scholar]
175. Kudva A, Kotian A, Mahesha GT, Pai D. Experimental investigation of mechanical properties of bamboo/carbon fiber reinforced hybrid polymer matrix composites. Mater Today: Proc. 2023. doi:10.1016/j.matpr.2023.04.398. [Google Scholar] [CrossRef]
176. Kangokar Mukesh S, Bettagowda N, Praveenkumara J, Thyavihalli Girijappa YG, Puttegowda M, Mavinkere Rangappa S, et al. Influence of stacking sequence on flax/kevlar hybrid epoxy composites: mechanical and morphological studies. Polym Compos. 2022;43(6):3782–93. doi:10.1002/pc.v43.6. [Google Scholar] [CrossRef]
177. Lee SK, Park EY, Park TS, An SK. Mechanical properties of PP/glass fiber/kenaf/bamboo fiber-reinforced hybrid composite. Fibers Polym. 2021;22:1460–5. doi:10.1007/s12221-021-0358-6. [Google Scholar] [CrossRef]
178. Firouzsalari SE, Dizhur D, Jayaraman K, Ingham JM. Bending behaviour of flax fabric-reinforced epoxy pipes. Compos Part A: Appl Sci Manuf. 2021;140:106179. doi:10.1016/j.compositesa.2020.106179. [Google Scholar] [CrossRef]
179. Marichelvam MK, Manimaran P, Verma A, Sanjay MR, Siengchin S, Kandakodeeswaran K, et al. A novel palm sheath and sugarcane bagasse fiber-based hybrid composites for automotive applications: an experimental approach. Polym Compos. 2021;42(1):512–21. doi:10.1002/pc.v42.1. [Google Scholar] [CrossRef]
180. Ramlee NA, Jawaid M, Zainudin ES, Yamani SAK. Tensile, physical and morphological properties of oil palm empty fruit bunch/sugarcane bagasse fibre reinforced phenolic hybrid composites. J Mater Res Technol. 2019;8(4):3466–74. doi:10.1016/j.jmrt.2019.06.016. [Google Scholar] [CrossRef]
181. Aruchamy K, Mylsamy B, Palaniappan SK, Subramani SP, Velayutham T, Rangappa SM, et al. Influence of weave arrangements on mechanical characteristics of cotton and bamboo woven fabric reinforced composite laminates. J Reinforced Plast Compos. 2023;42(15–16):776–89. [Google Scholar]
182. Safri SNA, Sultan MTH, Shah AUM. Characterization of benzoyl treated sugar palm/glass fibre hybrid composites. J Mater Res Technol. 2020;9(5):11563–573. doi:10.1016/j.jmrt.2020.08.057. [Google Scholar] [CrossRef]
183. Feng NL, Malingam SD, Razali N, Subramonian S. Alkali and silane treatments towards exemplary mechanical properties of kenaf and pineapple leaf fibre-reinforced composites. J Bionic Eng. 2020;17(2):380–92. doi:10.1007/s42235-020-0031-6. [Google Scholar] [CrossRef]
184. Vivek VV, Boopathi C, Natarajan N, Pradeesh EL, Pravin MC. Exploration of mechanical properties of jute fiber and copper wire reinforced hybrid polymer composites. Mater Today: Proc. 2022;66:707–11. [Google Scholar]
185. Taghipoor H, Sadeghian A. Experimental investigation of single and hybrid-fiber reinforced concrete under drop weight test. In: Structures, Elsevier; 2022 Sep. vol. 43, p. 1073–83. doi:10.1016/j.istruc.2022.07.030. [Google Scholar] [CrossRef]
186. Mousa S, Alomari AS, Vantadori S, Alhazmi WH, Abd-Elhady AA, Sallam HEDM. Mechanical behavior of epoxy reinforced by hybrid short palm/glass fibers. Sustainability. 2022;14(15):9425. doi:10.3390/su14159425. [Google Scholar] [CrossRef]
187. BA P, Shetty B, HV S, Singh Yadav SP. Mechanical properties and water absorption behaviour of pineapple leaf fibre reinforced polymer composites. Adv Mater Process Technol. 2022;8(2):1336–51. doi:10.1080/2374068X.2020.1860354. [Google Scholar] [CrossRef]
188. Rezasefat M, Da Silva AA, Amico SC, Giglio M, Manes A. Repeated impact behaviour of inter-ply hybrid aramid/S2-glass epoxy laminates. Thin-Walled Struct. 2023;186:110680. doi:10.1016/j.tws.2023.110680. [Google Scholar] [CrossRef]
189. Alia A, Fantozzi G, Godin N, Osmani H, Reynaud P. Mechanical behaviour of jute fibre-reinforced polyester composite: characterization of damage mechanisms using acoustic emission and microstructural observations. J Compos Mater. 2019;53(24):3377–94. doi:10.1177/0021998318822128. [Google Scholar] [CrossRef]
190. Jayababu A, Arumugam V, Rajesh B, Suresh Kumar C. Investigation of indentation damage resistance on normal and inclined plane of glass/epoxy composite laminates using acoustic emission monitoring. J Compos Mater. 2020;54(21):2953–64. doi:10.1177/0021998320906864. [Google Scholar] [CrossRef]
191. Kamble Z, Behera BK. Mechanical properties and water absorption characteristics of composites reinforced with cotton fibres recovered from textile waste. J Eng Fibers Fabrics. 2020;15:1558925020901530. [Google Scholar]
192. Saravanan K, Sampath Kumar SK, Prakash C, Sivamani S, Prakash Maran J, Rajeshkumar G. Influence of processing variables on tensile strength and water absorption of natural fibers hybrid composites. J Nat Fibers. 2022;19(15):10846–57. doi:10.1080/15440478.2021.2002774. [Google Scholar] [CrossRef]
193. Sahbaz Karaduman N, Karaduman Y. Effect of stacking sequence on the mechanical properties of non-interlaced multiaxial jute yarn/epoxy composites. J Compos Mater. 2022;56(13):2083–94. doi:10.1177/00219983221090580. [Google Scholar] [CrossRef]
194. Stanciu MD, Teodorescu Draghicescu H, Tamas F, Terciu OM. Mechanical and rheological behaviour of composites reinforced with natural fibres. Polymers. 2020;12(6):1402. doi:10.3390/polym12061402. [Google Scholar] [PubMed] [CrossRef]
195. Attia MA, El-baky MAA, Abdelhaleem MM, Hassan MA. Hybrid composite laminates reinforced with flax-basalt-glass woven fabrics for lightweight load bearing structures. J Ind Text. 2022;51(3_suppl):4622S–64S. doi:10.1177/1528083720960743. [Google Scholar] [CrossRef]
196. Santhosh N, Praveena BA, Srikanth HV, Angadi S, Gunge A, Rudra Naik M, et al. Experimental investigations on static, dynamic, and morphological characteristics of bamboo fiber-reinforced polyester composites. Int J Polym Sci. 2022;1–11. doi:10.1155/2022/1916877. [Google Scholar] [CrossRef]
197. Haque MR, Sajib KH, Haque MM, Zahura FT, Hasan MA, Ahmed SSU, et al. Mechanical characterization of banana-nylon fibre reinforced vinyl ester composites. Adv Mater Process Technol. 2023;1–20. doi:10.1080/2374068X.2023.2264573. [Google Scholar] [CrossRef]
198. Venkatasudhahar M, Kishorekumar P, Dilip Raja N. Influence of stacking sequence and fiber treatment on mechanical properties of carbon-jute-banana reinforced epoxy hybrid composites. Int J Polym Anal Charact. 2020;25(4):238–51. doi:10.1080/1023666X.2020.1781481. [Google Scholar] [CrossRef]
199. Mahmud SH, Das SC, Mollah MZI, Ul-Hoque MM, Al-Mugren KS, Faruque MRI, et al. Thermoset-polymer matrix composite materials of jute and glass fibre reinforcements: radiation effects determination. J Mater Res Technol. 2023;26:6623–35. doi:10.1016/j.jmrt.2023.08.298. [Google Scholar] [CrossRef]
200. Aranha Rá, Filho MAA, de Lima Santos C, Fonseca VM, Rivera JL, de Lima AG, et al. Water sorption in hybrid polyester/glass/jute composites processed via compression molding and vacuum-assisted resin transfer molding. Polymers. 2023;15(22):4438. doi:10.3390/polym15224438. [Google Scholar] [PubMed] [CrossRef]
201. Ariawan D, Asfar MF, Surojo E. Study of dimensional changes on alkali treated zallaca fibre reinforced unsaturated polyester composites under different aqueous environments. In: Materials science forum, Trans Tech Publications Ltd.; 2019 Sep. vol. 961, p. 3–9. doi:10.4028/www.scientific.net/MSF.961. [Google Scholar] [CrossRef]
202. Bhambure SS, Rao AS, Senthilkumar T. Analysis of mechanical properties of kenaf and kapok fiber reinforced hybrid polyester composite. J Nat Fibers. 2023;20(1):2156964. doi:10.1080/15440478.2022.2156964. [Google Scholar] [CrossRef]
203. Mbeche SM, Omara T. Effects of alkali treatment on the mechanical and thermal properties of sisal/cattail polyester commingled composites. PeerJ Mater Sci. 2020;2:e5. doi:10.7717/peerj-matsci.5. [Google Scholar] [CrossRef]
204. Atmakuri A, Palevicius A, Kolli L, Vilkauskas A, Janusas G. Development and analysis of mechanical properties of caryota and sisal natural fibers reinforced epoxy hybrid composites. Polymers. 2021;13(6):864. doi:10.3390/polym13060864. [Google Scholar] [PubMed] [CrossRef]
205. Gunturu B, Vemulapalli C, Malkapuram R, Konduru N. Investigation on mechanical, thermal and water absorption properties of banana/coir reinforced polypropylene hybrid composites. Revue des Composites et des MatériauxAvancés. 2020;30(3–4):123–31. doi:10.18280/rcma.303-402. [Google Scholar] [CrossRef]
206. Adugna Ayalew A, Fenta Wodag A. Characterization of chemically treated sisal fiber/polyester composites. J Eng. 2022;2022. doi:10.1155/2022/8583213. [Google Scholar] [CrossRef]
207. Sosiati H, Yuniar NDM, Saputra D, Hamdan S. The influence of carbon fiber content on the tensile, flexural, and thermal properties of the sisal/pmma composites. Japan: Kyushu University; 2022. [Google Scholar]
208. Anand AV, Velmurugan P, Singh RA, Jayalakshmi S, Rao KS, Kumar PS, et al. Macro mechanical and water absorption properties of composite laminates with novolac resin and e-glass/sisal fibers. AIP Conf Proc. 2022;2446(1):040012. [Google Scholar]
209. Gupta MK, Singh R. PLA-coated sisal fibre-reinforced polyester composite: water absorption, static and dynamic mechanical properties. J Compos Mater. 2019;53(1):65–72. doi:10.1177/0021998318780227. [Google Scholar] [CrossRef]
210. Takagi H. Review of functional properties of natural fiber-reinforced polymer composites: thermal insulation, biodegradation and vibration damping properties. Adv Compos Mater. 2019;28(5):525–43. doi:10.1080/09243046.2019.1617093. [Google Scholar] [CrossRef]
211. Chowdary MS, Raghavendra G, Kumar MN, Ojha S, Boggarapu V. Influence of nano-silica on enhancing the mechanical properties of sisal/kevlar fiber reinforced polyester hybrid composites. Silicon. 2022;1–8. [Google Scholar]
212. Nagarjun J, Kanchana J, Rajesh Kumar G. Improvement of mechanical properties of coir/epoxy composites through hybridization with sisal and palmyra palm fibers. J Nat Fibers. 2022;19(2):475–84. doi:10.1080/15440478.2020.1745126. [Google Scholar] [CrossRef]
213. Binu Kumar VJ, Bensam Raj J, Karuppasamy R, Thanigaivelan R. Influence of chemical treatment and moisture absorption on tensile behavior of neem/banana fibers reinforced hybrid composites: an experimental investigation. J Nat Fibers. 2022;19(8):3051–62. doi:10.1080/15440478.2020.1838995. [Google Scholar] [CrossRef]
214. Nguyen TA, Nguyen TH. Study on mechanical properties of banana fiber-reinforced materials poly (lactic acid) composites. Int J Chem Eng. 2022;2022. doi:10.1155/2022/8485038. [Google Scholar] [CrossRef]
215. Lyu Y, Ishida H. Natural-sourced benzoxazine resins, homopolymers, blends and composites: a review of their synthesis, manufacturing and applications. Prog Polym Sci. 2019;99:101168. doi:10.1016/j.progpolymsci.2019.101168. [Google Scholar] [CrossRef]
216. Mukherjee S, Amarnath N, Lochab B. Oxazine ring-substituted 4th generation benzoxazine monomers & polymers: stereoelectronic effect of phenyl substituents on thermal properties. Macromolecules. 2021;54(21):10001–16. doi:10.1021/acs.macromol.1c01582. [Google Scholar] [CrossRef]
217. Hao B, Han L, Liu Y, Zhang K. An apigenin-based bio-benzoxazine with three polymerizable functionalities: sustainable synthesis, thermal latent polymerization, and excellent thermal properties of its thermosets. Polym Chem. 2020;11(36):5800–9. doi:10.1039/D0PY00983K. [Google Scholar] [CrossRef]
218. Lu Y, Zhang K. Synthesis and properties of biobased mono-benzoxazine resins from natural renewable pterostilbene. Eur Polym J. 2021;156:110607. doi:10.1016/j.eurpolymj.2021.110607. [Google Scholar] [CrossRef]
219. Qian Z, Lou Y, Li Q, Wang L, Fu F, Liu X. Novel combination of vinyl benzoxazine and its copolymerizable diluent with outstanding processability for preparing a bio-based thermoset. ACS Sustain Chem Eng. 2021;9(32):10929–38. doi:10.1021/acssuschemeng.1c03581. [Google Scholar] [CrossRef]
220. Njom AE, Mewoli A, Ndengue MJ, Ebanda FB, Nitidem AD, Otiti SB, et al. Hybrid composite based on natural rubber reinforced with short fibers of the Triumfetta cordifolia/Saccharum officinarum L.: performance evaluation. J Miner Mater Char Eng. 2022;10(5):385–99. doi:10.4236/jmmce.2022.105027. [Google Scholar] [CrossRef]
221. Neto J, Queiroz H, Aguiar R, Lima R, Cavalcanti D, Banea MD. A review of recent advances in hybrid natural fiber reinforced polymer composites. J Renew Mater. 2022;10(3):561–89. doi:10.32604/jrm.2022.017434. [Google Scholar] [CrossRef]
222. Abdelsalam AA, Araby S, El-Sabbagh SH, Abdelmoneim A, Hassan MA. Effect of carbon black loading on mechanical and rheological properties of natural rubber/styrene-butadiene rubber/nitrile butadiene rubber blends. J Thermoplastic Compos Mater. 2021;34(4):490–507. doi:10.1177/0892705719844556. [Google Scholar] [CrossRef]
223. TG YG, P M, Kushvaha V, MR S, Siengchin S. A new study on flax-basalt-carbon fiber reinforced epoxy/bioepoxy hybrid composites. Polym Compos. 2021;42(4):1891–900. doi:10.1002/pc.25944. [Google Scholar] [CrossRef]
224. Noah AS. Oil palm empty fruit bunches (OPEFB)–alternative fibre source for papermaking. Elaeis Guineensis. 2022. doi:10.5772/intechopen.98256. [Google Scholar] [CrossRef]
225. Mustapha SNH, Norizan CW, C.W.N. F, Roslan R, Mustapha R. Effect of kenaf/empty fruit bunch (EFB) hybridization and weight fractions in palm oil blend polyester composite. J Nat Fibers. 2022;19(5):1885–98. doi:10.1080/15440478.2020.1788686. [Google Scholar] [CrossRef]
226. Sayeed MA, Sayem ASM, Haider J, Akter S, Habib MM, Rahman H, et al. Assessing mechanical properties of jute, kenaf, and pineapple leaf fiber-reinforced polypropylene composites: experiment and modelling. Polymers. 2023;15(4):830. doi:10.3390/polym15040830. [Google Scholar] [PubMed] [CrossRef]
227. Agrawal SA, Umbarkar AM, Sherie NP, Dharme AM, Dhabliya D. WITHDRAWN: Statistical study of mechanical properties for corn fiber with reinforced of polypropylene fiber matrix composite. Mater Today: Proc. 2021. doi:10.1016/j.matpr.2020.12.1072. [Google Scholar] [CrossRef]
228. Sun Z, Mingming W. Effects of sol-gel modification on the interfacial and mechanical properties of sisal fiber reinforced polypropylene composites. Ind Crops Prod. 2019;137:89–97. doi:10.1016/j.indcrop.2019.05.021. [Google Scholar] [CrossRef]
229. Monticeli FM, da Silva Monte Vidal DC, Shiino MY, Voorwald HJC, Cioffi MOH. Hybrid-permeability model evaluation through concepts of tortuosity and resistance rate: properties of manufactured hybrid laminate. Polymer Eng Sci. 2019;59(6):1215–22. doi:10.1002/pen.v59.6. [Google Scholar] [CrossRef]
230. Mukhtar II, Leman Z, Zainudin ES, Ishak MR. Hybrid and nonhybrid laminate composites of sugar palm and glass fibre-reinforced polypropylene: effect of alkali and sodium bicarbonate treatments. Int J Polym Sci. 2019. doi:10.1155/2019/1230592. [Google Scholar] [CrossRef]
231. Gogoi R, Kumar N, Mireja S, Ravindranath SS, Manik G, Sinha S. Effect of hollow glass microspheres on the morphology, rheology and crystallinity of short bamboo fiber-reinforced hybrid polypropylene composite. Jom. 2019;71(2):548–58. doi:10.1007/s11837-018-3268-3. [Google Scholar] [CrossRef]
232. Sergi C, Tirillò J, Seghini MC, Sarasini F, Fiore V, Scalici T. Durability of basalt/hemp hybrid thermoplastic composites. Polymers. 2019;11(4):603. doi:10.3390/polym11040603. [Google Scholar] [PubMed] [CrossRef]
233. Fajardo Cabrera de Lima LDP, Santana RMC, Chamorro Rodriguez CD. Influence of coupling agent in mechanical, physical and thermal properties of polypropylene/bamboo fiber composites: under natural outdoor aging. Polymers. 2020;12(4):929. doi:10.3390/polym12040929. [Google Scholar] [PubMed] [CrossRef]
234. Drouhet Q, Touchard F, Chocinski-Arnault L. Influence of hygrothermal aging on mechanical properties and damage mechanisms of hemp-reinforced biocomposites. J Nat Fibers. 2022;19(17):15404–21. doi:10.1080/15440478.2022.2126424. [Google Scholar] [CrossRef]
235. Arpitha GR, Verma A, Sanjay MR, Siengchin S. Preparation and experimental investigation on mechanical and tribological performance of hemp-glass fiber reinforced laminated composites for lightweight applications. Adv Civil Eng Mater. 2021;10(1):427–39. doi:10.1520/ACEM20200187. [Google Scholar] [CrossRef]
236. Panaitescu DM, Fierascu RC, Gabor AR, Nicolae CA. Effect of hemp fiber length on the mechanical and thermal properties of polypropylene/SEBS/hemp fiber composites. J Mater Res Technol. 2020;9(5):10768–81. doi:10.1016/j.jmrt.2020.07.084. [Google Scholar] [CrossRef]
237. More AP. Flax fiber-based polymer composites: a review. Adv Compos Hybrid Mater. 2022;5(1):1–20. doi:10.1007/s42114-021-00246-9. [Google Scholar] [CrossRef]
238. Balaji A, Sivaramakrishnan K, Karthikeyan B, Purushothaman R, Swaminathan J, Kannan S, et al. Study on mechanical and morphological properties of sisal/banana/coir fiber-reinforced hybrid polymer composites. J Braz Soc Mech Sci Eng. 2019;41(9):1–10. doi:10.1007/s40430-019-1881-x. [Google Scholar] [CrossRef]
239. Ferreira BT, da Silva LJ, Panzera TH, Santos JC, Freire RTS, Scarpa F. Sisal-glass hybrid composites reinforced with silica microparticles. Polym Test. 2019;74(4):57–62. doi:10.1016/j.polymertesting.2018.12.026. [Google Scholar] [CrossRef]
240. Möhl C, Weimer T, Caliskan M, Hager T, Baz S, Bauder HJ, et al. Flax fibre yarn coated with lignin from renewable sources for composites. Polymers. 2022;14(19):4060. doi:10.3390/polym14194060. [Google Scholar] [PubMed] [CrossRef]
241. Zong G, Hao X, Hao J, Tang W, Fang Y, Ou R, et al. High-strength, lightweight, co-extruded wood flour-polyvinyl chloride/lumber composites: effects of wood content in shell layer on mechanical properties, creep resistance, and dimensional stability. J Clean Prod. 2020;244:118860. doi:10.1016/j.jclepro.2019.118860. [Google Scholar] [CrossRef]
242. Faezipour M, Shamsi R, Ashori A, Abdulkhani A, Kargarfard A. Hybrid composite using recycled polycarbonate/waste silk fibers and wood flour. Polym Compos. 2016;37(6):1667–73. doi:10.1002/pc.v37.6. [Google Scholar] [CrossRef]
243. Jahan E, Akter M, Hasan M. Effect of fibre ratio and chemical treatment on the properties of pineapple leaf and betel nut husk fibre-reinforced hybrid polypropylene composites. Adv Mater Process Technol. 2020;6(3):637–46. [Google Scholar]
244. Mahesh D, Kowshigha KR, Raju NV, Aggarwal PK. Characterization of banana fiber-reinforced polypropylene composites. J Indian Acad Wood Sci. 2020;17:1–8. doi:10.1007/s13196-019-00244-x. [Google Scholar] [CrossRef]
245. Karthik S, Arunachalam VP. Investigation on the tensile and flexural behavior of coconut inflorescence fiber reinforced unsaturated polyester resin composites. Mater Res Express. 2020;7(1):015345. doi:10.1088/2053-1591/ab6c9d. [Google Scholar] [CrossRef]
246. Kossentini Kallel T, Taktak R, Guermazi N, Mnif N. Mechanical and structural properties of glass fiber-reinforced polypropylene (PPGF) composites. Polym Compos. 2018;39(10):3497–508. doi:10.1002/pc.24369. [Google Scholar] [CrossRef]
247. Baştürk B. Effect of fiber orientation on the mechanical properties of glass fiber reinforced polymer (GFRP)/PVC sandwich composites. Karaelmas Fen ve Mühendislik Dergisi. 2023;13(1):52–61. [Google Scholar]
248. H. HA, Nawab Y, Anjang A, Akil HM, Abidin MSZ. Mechanical properties of continuous natural fibres (jute, hemp, flax) reinforced polypropylene composites modified with hollow glass microspheres. Fibers Polym. 2020;21(9):2076–83. doi:10.1007/s12221-020-2260-z. [Google Scholar] [CrossRef]
249. Mubarak YA. Tensile and impact properties of microcrystalline cellulose nanoclay polypropylene composites. Int J Polym Sci. 2018;2018(3):1–13. doi:10.1155/2018/1708695. [Google Scholar] [CrossRef]
250. Fang X, Li Y, Zhao J, Xu J, Li C, Liu J, et al. Improved interfacial performance of bamboo fibers/polylactic acid composites enabled by a self-supplied bio-coupling agent strategy. J Clean Prod. 2022;380:134719. doi:10.1016/j.jclepro.2022.134719. [Google Scholar] [CrossRef]
251. Inácio AL, Nonato RC, Bonse BC. Mechanical and thermal behavior of aged composites of recycled PP/EPDM/talc reinforced with bamboo fiber. Polym Test. 2018;72:357–63. doi:10.1016/j.polymertesting.2018.10.035. [Google Scholar] [CrossRef]
252. Stelea L, Filip I, Lisa G, Ichim M, Drobotă M, Sava C, et al. Characterisation of hemp fibres reinforced composites using thermoplastic polymers as matrices. Polymers. 2022;14(3):481. doi:10.3390/polym14030481. [Google Scholar] [PubMed] [CrossRef]
253. Jacob M, Francis B, Thomas S, Varughese KT. Dynamical mechanical analysis of sisal/oil palm hybrid fiber-reinforced natural rubber composites. Polym Compos. 2006;27(6):671–80. doi:10.1002/(ISSN)1548-0569. [Google Scholar] [CrossRef]
254. Jacob M, Jose S, Thomas S, Varughese KT. Stress relaxation and thermal analysis of hybrid biofiber reinforced rubber biocomposites. J Reinforced Plast Compos. 2006;25(18):1903–17. doi:10.1177/0731684406069919. [Google Scholar] [CrossRef]
255. Jacob M, Varughese KT, Thomas S. Dielectric characteristics of sisal-oil palm hybrid biofibre reinforced natural rubber biocomposites. J Mater Sci. 2006;41(17):5538–47. doi:10.1007/s10853-006-0298-y. [Google Scholar] [CrossRef]
256. Pathak G, Dubey OP, Manoharan PK. Mechanical properties of sisal/glass fiber reinforced hybrid composites: a review. Int J Stud' Res Technol Manag. 2018;6(2):70–6. doi:10.18510/ijsrtm.2018.6210. [Google Scholar] [CrossRef]
257. Mbeche SM, Wambua PM, Githinji DN. Mechanical properties of sisal/cattail hybrid-reinforced polyester composites. Adv Mater Sci Eng. 2020;2020(2):1–9. doi:10.1155/2020/6290480. [Google Scholar] [CrossRef]
258. Omri MA, Triki A, Ben Hassen M, Sanjay MR, Arous M, Kallel A. Effect of alfa fiber mechanical separation on dielectric properties of hybrid unsaturated polyester composites. Polym Compos. 2019;40(5):1774–85. doi:10.1002/pc.v40.5. [Google Scholar] [CrossRef]
259. Sivasubramanian P, Mayandi K, Santulli C, Alavudeen A, Rajini N. Effect of fiber length on curing and mechanical behavior of pineapple leaf fiber (PALF) reinforced natural rubber composites. J Nat Fibers. 2022;19(11):4326–37. doi:10.1080/15440478.2020.1856281. [Google Scholar] [CrossRef]
260. Abdellah MY, Seleem AEHA, Marzok WW, Hashem AM, Backer AH. Tensile and imp act properties of hybrid date palm fibre composite structures embedded with chopped rubber. Int J Eng Res Appl. 2022;12:54–66. [Google Scholar]
261. Fares O, AL-Oqla FM, Hayajneh MT. Dielectric relaxation of mediterranean lignocellulosic fibers for sustainable functional biomaterials. Mater Chem Phys. 2019;229:174–82. doi:10.1016/j.matchemphys.2019.02.095. [Google Scholar] [CrossRef]
262. Parsania PH, Patel JP. Fabrication and physicochemical properties of glass fabric-multifunctional epoxy resin composite. Polym Bull. 2020;77:1667–79. doi:10.1007/s00289-019-02809-9. [Google Scholar] [CrossRef]
263. Parsania PH, Patel JV, Patel JP. Synthesis and physicochemical study of bisphenol-C epoxy cinnamate resin and its glass/jute and jute-natural fiber-reinforced composites. Polym Bull. 2024;81(4):3191–207. doi:10.1007/s00289-023-04831-4. [Google Scholar] [CrossRef]
264. Yadav A, Gupta MK. Development and characterization of jute composites for sustainable product: effect of chemical treatments and polymer coating. Mater Res Express. 2019;7(1):015306. [Google Scholar]
265. Agrebi F, Hammami H, Asim M, Jawaid M, Kallel A. Impact of silane treatment on the dielectric properties of pineapple leaf/kenaf fiber reinforced phenolic composites. J Compos Mater. 2020;54(7):937–46. doi:10.1177/0021998319871351. [Google Scholar] [CrossRef]
266. Sanjay MR, Siengchin S. Editorial corner-a personal view Exploring the applicability of natural fibers for the development of biocomposites. Express Polym Lett. 2021;15(3):193. doi:10.3144/expresspolymlett.2021.17. [Google Scholar] [CrossRef]
267. Sreenivas HT, Krishnamurthy N, Arpitha GR. A comprehensive review on light weight kenaf fiber for automobiles. Int J Lightweight Mater Manuf. 2020;3(4):328–37. doi:10.1016/j.ijlmm.2020.05.003. [Google Scholar] [CrossRef]
268. Coppola G, Gaudio MT, Lopresto CG, Calabro V, Curcio S, Chakraborty S. Bioplastic from renewable biomass: a facile solution for a greener environment. Earth Syst Environ. 2021;5(2):231–51. doi:10.1007/s41748-021-00208-7. [Google Scholar] [CrossRef]
269. Peças P, Carvalho H, Salman H, Leite M. Natural fibre composites and their applications: a review. J compos sci. 2018;2(4):66. doi:10.3390/jcs2040066. [Google Scholar] [CrossRef]
270. Naik V, Kumar M. A review on natural fiber composite material in automotive applications. Eng Sci. 2021;18:1–10. doi:10.30919/es8d589. [Google Scholar] [CrossRef]
271. Shelar PB, Narendra Kumar U. A short review on jute fiber reinforced composites. In: Materials science forum. Trans Tech Publications Ltd.; 2021 Feb. p. 32–43. [Google Scholar]
272. Sivanur K, Umananda KV, Pai D. Advanced materials used in automotive industry—a review. AIP Conf Proc. 2021 Feb;2317(1):020032. [Google Scholar]
273. Chandgude S, Salunkhe S. In state of art: mechanical behavior of natural fiber-based hybrid polymeric composites for application of automobile components. Polym Compos. 2021;42(6):2678–703. doi:10.1002/pc.v42.6. [Google Scholar] [CrossRef]
274. Verma D, Senal I. Natural fiber-reinforced polymer composites: feasibiliy study for sustainable automotive industries. In: Biomass, biopolymer-based materials, and bioenergy. Woodhead Publishing; 2019. p. 103–22 [Google Scholar]
275. Njoku CE, Alaneme KK, Omotoyinbo JA, Daramola MO. Natural fibers as viable sources for the development of structural, semi-structural, and technological materials—a review. Adv Mater Lett. 2019;10(10):682–94. doi:10.5185/amlett.2019.9907. [Google Scholar] [CrossRef]
Cite This Article
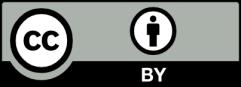
This work is licensed under a Creative Commons Attribution 4.0 International License , which permits unrestricted use, distribution, and reproduction in any medium, provided the original work is properly cited.