Open Access
REVIEW
Valorization of Tree Bark-Derived Suberin in Applications for the Bio-Based Composites Industry–A Recent Review
Institute of Wood Sciences and Furniture, SGGW, Nowoursynowska St. 159, Warsaw, 02-776, Poland
* Corresponding Author: Aleksandra Jeżo. Email:
(This article belongs to the Special Issue: Environmentally Friendly Wood-Based Composites Based on Sustainable Technologies and Renewable Materials)
Journal of Renewable Materials 2024, 12(6), 1029-1042. https://doi.org/10.32604/jrm.2024.051330
Received 02 March 2024; Accepted 26 April 2024; Issue published 02 August 2024
Abstract
Bark extracts are sustainable sources of biopolymers and hold great promise for replacing fossil fuel-based polymers, for example, in wood-based composites. In addition to primary and secondary metabolites, tree bark also contains suberin, which plays a major role in protecting the tree from environmental conditions. Suberin is a natural aliphatic-aromatic cross-linked polyester present in the cell walls of both normal and damaged external tissues, the main component of which are long-chain aliphatic acids. Its main role as a plant ingredient is to protect against microbiological factors and water loss. One of the most important suberin monomers are suberin fatty acids, known for their hydrophobic and barrier properties. Therefore, due to the diverse chemical composition of suberin, it is an attractive alternative to hydrocarbon-based materials. Although its potential is recognized, it is not widely used in biocomposites technology, including wood-based composites and the polymer industry. The article will discuss the current knowledge about the potential of suberin and its components in biocomposites technology, which will include surface finishes, composite adhesives and polymer blends.Keywords
Suberin is a structural lipophilic polyester and it consists of fatty acids, glycerin and aromatic compounds [1,2]. It can be found in the cell walls of various plant tissues, including phellem, endoderm, exoderm, wound tissues, abscission zones or bundle sheath. Its deposition serves as a hydrophobic layer located between the primary cell wall, which is composed of lignocellulosic material and the plasma membrane [3]. Suberin plays a key role in providing high levels of protection against biotic and abiotic stresses. Additionally, it shows high developmental flexibility, and its chemical resistance may contribute to the sequestration of atmospheric carbon by plants [4,5].
Depolymerization of in situ suberin and its simultaneous isolation from the plant composite is traditionally a laborious process requiring chemical processes [3]. These processes involve extensive ester bond cleavage, normally attained through alkaline methanolysis with sodium methoxide [6,7] or alkaline hydrolysis. The last few decades have seen an exponential increase in interest in ionic liquids–a different class of chemical substances consisting of ions that are liquid at temperatures below conventionally defined as 100°C. Fig. 1 shows the extraction and processing of cork or birch outer bark suberin. In a simplified suberin extraction procedure, the ionic liquid is combined with powdered cork in specific proportions and mixed for a specific time at an elevated temperature. After extraction, dimethyl sulfoxide (DMSO) can be added to reduce the viscosity of the mixture, aiding the filtration process through a special membrane. The insoluble residue is thoroughly washed and dried until constant weight is obtained. The resulting filtrate, consisting of the ionic liquid, extracted material, DMSO and rinsing water, is subjected to a cooling process leading to the precipitation of suberin. This material is recovered by centrifugation, washed repeatedly to remove any remaining ionic liquid, and dried to constant weight [8]. To further extract the suberin to obtain valuable suberinic acids [9–14], also known as suberinic fatty acids (SA), the resulting alkaline suspension is treated with HNO3. After acidification, the obtained SA are suspended in water, and then filtered again to reduce water content [15]. By esterification of dried SA, among other products, polyols can be obtained [16,17].
Figure 1: Depolymerization of cork or birch outer bark suberin (own elaboration)
The most important factors affecting the amount of suberin monomers are the isolation method and the tree species [3,18–21]. Suberin content in tree bark depends on proportion of cork tissue in the periderm, as suberin is found in phellem cells and its content is particularly high in hardwood barks, particularly in Quercus suber (37.0%–60.0%) [22–24] and Betula pendula (32.2%–58.6%) [24–26]. However, poplar (3.0%) and willow (1.8%) contain less suberin [27]. In Table 1, selected species and the percentage of suberin in their bark have been presented.
This paper aims to investigate the current state of knowledge about suberin utilization in biocomposites industry, with regard on the valuable properties of this component.
2 Suberin Resources Potential and Utilization in Biocomposites Applications
The percentage share of suberin in the bark of trees varies depending on the species, but it is worth examining the significance and prevalence of this component, commonly utilized from the bark as forest waste. Betula can be used here as an example of a specific species. In the vast landscapes of the Northern Hemisphere, silver birch (Betula pendula Roth.) and downy birch (Betula pubescens Ehrh.) are the main birch species, and their importance goes beyond the sphere of simple arboreal presence [30]. Widely recognized as a key player in the production of pulp [31] and plywood, these birches play a key role in shaping the industrial landscape. Interestingly, birch bark, constituting approximately 12.5% of the tree’s mass, appears as a valuable by-product, with the outer bark of birch logs accounting for 2.0%–3.4% (by weight) of their total composition [10].
Birch’s influence extends further, as the Birch Kraft pulp mill, with an annual production of 400,000 tons, and a plywood mill with an annual production of 252.000 m3, contribute significantly to the by-product stream. Specifically, these facilities produce approximately 28,000 and 16,000 tons of outer bark, respectively. It is worth noting that the calorific value of this outer bark exceeds 30 MJ/kg, making it a strong energy source. In addition to other residual materials such as veneer chips, wood chips, and sawdust, outer bark is used in power plants of pulp and plywood factories [31], where it is burned efficiently.
While the research has extensively focused on suberin and its applications, particularly sourced from Quercus suber [1], main interests focus on the role of suberin, suberinic acids-not only as by-products, but also as transforming factors, therefore this article provides insight into the potential of this valuable component of outer bark.
2.1 Suberin Derivates Utilization in Polymer Industry
In recent years, composites consisting of polymers and cellulosic materials have garnered research interest. This heightened focus is driven by the recognition of the unique properties and sustainable characteristics offered by the combination of polymers with ligno-cellulosic elements, derived from renewable sources such as forestry and agricultural residues [32]. In polymer industries, suberin monomers are used as macromolecular materials either as additives or inactive starting monomeric form. Some reports show that novel synthetic macromolecules or polymers could be prepared using suberin monomers [33,34]. Suberin monomers have –COOH and –OH functional groups at their terminal side that make them reactive during polymerization reactions while their dual thermoplastic and thermoset characteristics result from the variable −OH groups in suberin macromonomers [35,36]. The aliphatic fragments of suberin arising from cleavage of its ester group proved to be suited to polymerization by classical polycondensation processes to give polyesters which properties were alike those of model counterparts [33].
Composite structures incorporating low-density polyethylene (LDPE), cork powder, and suberin as coupling agents were developed to bust adhesion between cork and the polymeric phase. Utilizing reactive extrusion and compression molding for compounding, morphological analysis revealed robust adhesion. Mechanical testing revealed that suberin significantly heightened strength, yielding composites with improved strain properties by increased flexibility and enhanced dispersion of the cork phase within the matrix [37]. Enhancement of mechanical properties has also been reported by de Oliveira et al. [38] after incorporating ligno-cellulosic residues obtained from natural cork into suberin-based polyester to fabricate all cork-based composite materials. Almost 900% and 185% increase in Young’s modulus and tensile strength, respectively, were obtained from the baseline of pristine suberin-based polyesters by adding 40 wt% of ligno-cellulosic residue particles. Oh et al. [39] conducted a study where the extracted suberin has been added to the thermoplastic polyurethane (TPU) matrix as an eco-friendly filler for improving vibration damping property. As a result, when 10 wt% of suberin was added into thermoplastic polyurethane the existing trade-off relationship was overcome. And it is attained the elastic modulus and damping factor at room temperature improving 92% and 59%, respectively, compared to the original matrix, resulting from the interaction between the microstructure of TPU and suberin. SA were used by Cho et al. [40] for the synthesis of an ecofriendly biopolyester syntactic foam along with expandable microspheres (EMs). The specific compressive modulus of this syntactic foam was raised up to 66% when EMs were filled from 20% to 30 wt%. It has been also proven by Sousa et al. [33] that aliphatic suberin components, derived from ester group cleavage, are conducive to polymerization through traditional processes, yielding polyesters with properties similar to models. The experiments conducted by Menager et al. [41] highlight that cross-linked epoxidized linseed oil/suberin films have a wide relaxation temperature range and a tunable glass transition temperature (Tg) between 57°C and 66°C depending of the suberin ratio in the reaction medium.
Moreover, also acids derived from suberin have been investigated regarding their utilization in polymer engineering. Therefore, SA were regarded as lubricants in a recycled polypropylene/polylactic acid (rPP/PLA) composite filled with alkali-treated milled birch shaving microparticles. The addition of SA as a lubricant enhanced composite processing by reducing rotor torque and injection pressure, since the chemical composition of SA, featuring covalently bound aromatic structures, allows them to act as coupling agents at optimal levels, improving mechanical properties and lowering wettability in the composite [15]. SA can be also utilized when creating fibrous materials with excellent water repellent properties. The larger amounts of SA resulted in globular structures on the fiber surfaces further enhancing the hydrophobicity. The SA curing agent treatment improved tensile strength, an important property for packaging materials [42]. In Table 2, suberin utilization in the polymer industry on some examples has been presented.
2.2 Surface Finishing Coatings Containing Suberin Derivates
Suberin performs a key physiological function by providing a water-impermeable diffusion barrier in the dermal tissues of most underground plant organs and the periderm of above-ground tissues, by creating a hydrophobic, protective and antibacterial barrier [45]. Based on that knowledge, it has been attempted to increase the hydrophobicity as well as barrier properties of materials via addition of suberin derivates.
Suberin-derived SA monomers enable to enhance the moisture barrier properties of finishing coatings. In Table 3, the examples of suberin derivates’ moisture barrier properties have been presented with the comparison to the untreated surfaces. In a recent study by Kumar et al. [46], the applicability of SA hydrolysate extracted from the outer bark of silver birch (Betula pendula Roth.) was explored for coating aspen wood (Populus tremula L.). A noteworthy improvement in the hydrophobicity of the wood surface across all coating combinations involving SA has been reported. The authors posit that the extraction process of SA from birch bark could potentially influence the quality of bio-based polyesters. Additionally, Heinämäki et al. [34] demonstrated that even at low concentrations, the incorporation of SA significantly enhances the water vapor barrier properties of hydroxypropyl methylcellulose (HPMC) films. The incorporation of SA in aqueous HPMC films provides an avenue for modifying film properties and performance, since it enhances water vapor barrier properties and influences mechanical parameters. Further insights into the adsorption of suberin and SA on cellulose were explored by Handiso et al. [47], who treated filter paper with solutions of suberin and SA. This study implies that suberin and SA possess the potential for modifying the surface of cellulose, suggesting their utility in enhancing the interfacial properties of cellulose fiber-reinforced composites. The collective findings underscore the multifaceted applications of suberin and SA, pointing towards their role in advancing the performance and properties of various materials. Furthermore, Garcia et al. [44] reported the ex situ reconstitution of the biopolyester suberin as a waterproof and antimicrobial material (Fig. 2). Without any chemical additives or purification, the suberin composing macromolecules underwent self-association on the casting surface forming a film. Suberin films obtained showed barrier properties similar to those of the suberin barrier in plants, including a potentially broad bactericidal effect.
Figure 2: A simplified scheme of preparing of the suberin-film (own elaboration). Adapted with permission from [44]. Copyright © 2014, American Chemical Society
Another potential of introducing suberin to the surface of the material is fire resistance. Although considerable progress has been made in developing applications for suberin through trial and error, there is scope for theoretical development. The following hypothesis has been proposed: chemical intermediates released during the decomposition of suberin have favorable reactive and viscoelastic properties that may lead to the formation of a hard, adherent char layer. In principle, the chemical nature of the byproducts of heated suberin can be assessed, which will enable the discovery of important chemical mechanisms of char formation [48].
There is also known an attempt to incorporate residues from suberic acids extraction (SAR–suberinic acids residues) as an additive in biopolymeric finishing films. Coatings in the form of a film by combining a biopolymer with SAR were made. The addition of carbon-rich SAR significantly improves gas barrier properties of the PLA- and polycaprolactone-PCL-based surface finishing materials. The relative hardness and scratch resistance also increased with rising SAR content [43].
2.3 Adhesives with Incorporation of Suberin Derivates
Suberin, known for its molecular structure and interactions at the molecular level, performs promising adhesion properties. This has inspired a series of studies examining how materials incorporating suberin exhibit adhesion. In a particular study, biocomposites crafted from grey alder (Alnus incana) sawdust employed a blend of SA derived from birch outer bark as a binder [49]. Preliminary observations showed a subtle increase in board density and bending strength when the pressing temperature was raised from 160°C to 200°C at a pressure of 3.5 MPa. A closer examination of the chemical structure, as identified by Lang et al. [50], explains a composition with a high betulin content partially esterified with suberinic compounds. The esterification of betulin plays a crucial role in diminishing intermolecular attractive forces, thereby enhancing wettability. Simultaneously, the remaining hydroxyl groups of betulin and SA contribute to heightened adhesion.
In assessing four different SA-based adhesives obtained in distinct solvents (methanol, ethanol, isopropanol, 1-butanol), a study compared their chemical and thermal properties, as well as their performance in particleboard bonding [11]. The study determined that ethanol, with its highest epoxy content, proved to be the most suitable depolymerization medium for obtaining adhesives. Compared to untreated particleboards, those with 5 wt% SA exhibited the most significant improvement in MOE and MOR [12]. However, it is worth noting that the acidic nature of SA-based adhesives can catalyze the formation of furfural (FUR) from xylenes in wood particles, which, as a volatile organic compound, can have harmful effects on humans. Addressing this concern, the use of an SA-based adhesive with a pH of 6 at a hot-pressing temperature of 230°C, without glycerol added, enabled the production of particleboards meeting the requirements of EN 312 [51] P2 for interior fitments. These boards exhibited a FUR yield more than six times lower than those pressed at 230°C with a wet adhesive pH value of 3 [13]. Further advancements in wood-composites binders have been presented by Janis et al. [52], aiming to establish an energy and resource-efficient method for obtaining a binder from birch outer bark. The objective was to create more efficient binders as adhesives in plywood and wood particleboards, aligning with the requirements set by EN 314 [53] for plywood designed for exterior use.
Another approach regarded incorporation of SA along with betulin-based extractives into conventional phenol-formaldehyde resin. The goal was to select the optimal share of such fillers in the resin. As a result of the study, 30 wt% of the industrial resin has been found to be successfully replaceable with bark components, resulting in blends with no loss in bending strength and moisture resistance properties of produced plywood [54]. The SA-bonded particleboards exhibited up to five times lower total Volatile Organic Compounds (VOC) emissions than the binderless boards with a similar density and thickness and was comparable with the commercially produced particleboard [55].
Since SA itself constitutes a good binder for wood-based composites, as shown above, Jeżo et al. [56] decided to investigate whether the same satisfactory properties would be obtained when using post-extraction residues. The authors showed that when using SAR at 10% and 20% resination level, the requirements of the EN 312:2010 standard were met only in the case of the MOE of boards made of the coarse fraction of wood particles. Research was also carried out on SAR, adapting this material as a bifunctional component of binding mixtures in the production of plywood [57]. The results showed that the curing time of a binder mixture based on commercial urea-formaldehyde (UF) resin could be reduced to approximately 38% and 10% for hot and cold curing, respectively, compared to the initial curing time at the lowest SAR content. A positive effect of the resin impregnation limiter on SAR acting as a filler was found. Moreover, in the case of hot-pressed boards, a higher density of connection lines containing SAR was achieved. A comparison of the mechanical characteristics of SA-based adhesives with conventional solutions and other exemplary ecological adhesives is presented in Table 4.
2.4 Suberinic Acids in Insulation Biomaterials
The process of obtaining polyols from SA has been presented on Fig. 1. Attempts have been made to add SA to polyols in order to improve the properties of the obtained polyurethanes. The addition of SA resulted in a number of benefits, including: improved flexibility, increased mechanical strength, better thermal stability, and increased resistance to chemicals and hydrolysis [17,35,36]. It has been proven that SA also react well with other polyols, so they can be combined to obtain the desired properties of polyurethanes. SA work well as polyols in the synthesis of polyurethanes due to the presence of −OH groups and other chemical properties, thanks to which the obtained PU foams have a higher crosslink density of the polymer matrix. Importantly, after isolating SA, it is necessary to purify them before using them as bio-polyol, because SA themselves have unfavorable features for further synthesis [9,14], such as: high viscosity, high acidity, very thick and sticky form, which makes further application difficult. Attempts were made to bypass the thermal drying step, which causes partial copolymerization of SA and high weight and viscosity. The idea to solve this problem by eliminating the need for heat treatment was lyophilization [14], but unfortunately, this method was not very successful.
Materials with insulating properties employing SA in rigid PUR foams were investigated by [16], through the addition of SA to conventional polyols. It has been shown that the addition of SA up to 20 wt% allows to obtain a material with competitive thermal insulation properties (~0.019 W/(m * K)) and satisfactory strength parameters. The authors claim the need for further studies on overcoming the difficulties resulting from high viscosity of SA [17].
In Table 5, there has been illustrated a comparison of different lignin-based polyols in polyurethane foams and their thermal conductivity. Based on the information in the table it can be concluded that SA-based polyols resulted in the lowest thermal conductivity of PUR foams, indicating the best thermal insulation properties. As the reference, Elastospray 1622/6 as a commercial system based on petroleum polyol, has been chosen.
2.5 Wood Modification via Suberin Derivates Utilization
Suberin shows promising applications in wood modification, where suberin monomers (SM) occupy the cell lumen in a complex manner. This not only blocks the wooden vessels, but also reduces the interaction between the wood and water. In addition, SM penetrates the wood cell wall, increasing its volume and mitigating swelling. After heat treatment, the distribution of SM becomes more uniform, which is accompanied by partial degradation of hemicelluloses. The resulting modified wood is characterized by increased dimensional stability. Under experimental conditions, SM-impregnated poplar (Populus cathayana) wood samples were heat treated at 180°C for two hours, which led to a noticeable improvement in dimensional stability. The synergistic effect of SM use for modification and heat treatment further enhanced this improvement [71]. The heat treatment process of wood by SM has been illustrated on Fig. 3.
Figure 3: Process of the wood surface modification with SM (own elaboration). Adapted with permission from [71]. Creative Commons Attribution-NonCommercial 4.0 International
2.6 Valorization of Antibacterial Properties of Suberin for Biocomposites
Suberin plays a crucial role in protecting the plant from biotical attacks, what explains why it exhibits good antimicrobial and antifungal properties [72], among others against Euglena gracilis [73], Pectobacterium carotovorum [74], Escherichia coli [44], Staphylococcus aureus [44,75], Pseudomonas aeruginosa [76], or Candida albicans [76].
This knowledge has been successfully applied to the development of suberin biopolyester as a waterproof and antibacterial material. Without any chemical additives or purification, the macromolecules forming suberin self-associated on the casting surface, forming a film. The authors claim that the obtained suberin films exhibited barrier properties similar to the suberin barrier of plants, including a potentially broad bactericidal effect [44]. The making process of the film has been presented in the Fig. 3.
The author did not find more studies examining the antifungal and antibacterial effects of suberin and its products in biocomposite technology. However, Fernandes et al. tested the antibacterial effect of the LDPE/cork composite, where, as the authors mentioned, suberin constitutes on average as much as 43% of the cork composition [77]. The author of this review believes that in the future, it would be worth developing research and knowledge on how suberin and its depolymerization products perform antibacterial/antifungal properties.
The article presents the current state of knowledge on the potential use of suberin and its derivatives, including SA, as well as by-products resulting from the extraction of suberinic acids, in the biocomposites industry. In the light of the research carried out on suberin derivates, it can be seen that it is promising in polymer technology, acting as a coupling agent in polymer composites, contributing to the production of polyesters, acting as an additive in polymer composites and as a lubricant in polymer blends. In the field of finishing coating technology, suberin derivates provide, among others, increased resistance to hydrolysis and has the potential to improve fire resistance. Numerous studies have examined the adhesive properties of SA, emphasizing their potential use as a binder in wood-based composite technology. Attempts have also been made to modify wood with suberin derivates. Despite the significant potential illustrated by the examples, suberin remains an underestimated raw material in biocomposite technology. The author is convinced that systematizing the current knowledge about the use of suberin products in bio-based composites technology will allow for inspiration for further research and improvements in this area. Increasing researchers’ awareness of the potential in suberin is a practical goal of this review.
Acknowledgement: The mentioned research is conducted with the support of the Student Furniture Scientific Group (Koło Naukowe Meblarstwa), Faculty of Wood Technology, Warsaw University of Life Sciences–SGGW.
Funding Statement: The research presented is a part of Project BarkBuild that is funded under the ERA-NET Cofund Forest Value Program through Vinnova (Sweden), Valsts izglītības attīstības aģentūra (Latvia), Ministry of Education, Science and Sport (JIA) (Slovenia), Academy of Finland, The Research Council of Norway, and the National Science Centre, Poland (Agreement No. 2021/03/Y/NZ9/00038). The Forest Value Program received funding from the Horizon 2020 Research and Innovation Program of the European Union under Grant Agreement No. 773324.
Author Contributions: The author confirms contribution to the paper as follows: study conception and design: A.J.; data collection: A.J.; analysis and interpretation of results: A.J.; draft manuscript preparation: A.J. The author reviewed the results and approved the final version of the manuscript.
Availability of Data and Materials: Not applicable.
Conflicts of Interest: The author declares that they have no conflicts of interest to report regarding the present study.
References
1. Makars R, Rizikovs J, Paze A, Godina D, Berzins R. Birch outer bark characterisation after extraction and its potential for obtaining suberin fatty acids. Eur Biomass Conf Exhibit Proc. 2023;1113–6. doi:10.5071/31stEUBCE2023-6CV.7.14. [Google Scholar] [CrossRef]
2. Godina D, Makars R, Paze A, Rizhikovs J. Analytical method cluster development for comprehensive characterisation of suberinic acids derived from birch outer bark. Molecules. 2023;28:1–18. doi:10.3390/molecules28052227. [Google Scholar] [PubMed] [CrossRef]
3. Gandini A, Pascoal Neto C, Silvestre AJD. Suberin: a Promising renewable resource for novel macromolecular materials. Progress Polym Sci. 2006;31:878–92. doi:10.1016/j.progpolymsci.2006.07.004. [Google Scholar] [CrossRef]
4. Olga S, Niko G. The making of suberin. New Phytologist. 2022;235(3):848–66. doi:10.1111/nph.18202. [Google Scholar] [PubMed] [CrossRef]
5. Graça J. Suberin: the biopolyester at the frontier of plants. Front Chem. 2015;3:1–11. doi:10.3389/fchem.2015.00062. [Google Scholar] [PubMed] [CrossRef]
6. Helga G, Rui F, Marija P, Fergusson Jamie L, Leitao Maria C, Nimal GHQ, et al. Dissolution of cork biopolymers in biocompatible ionic liquids. Green Chemistry. 2010;12:367–9. doi:10.1039/B922553F. [Google Scholar] [CrossRef]
7. Lopes MH, Gil AM, Silvestre AJD, Neto CP. Composition of suberin extracted upon gradual alkaline methanolysis of Quercus suber L. cork. J Agric Food Chem. 2000;48:383–91. doi:10.1021/jf9909398. [Google Scholar] [PubMed] [CrossRef]
8. Ferreira R, Garcia H, Sousa AF, Petkovic M, Lamosa P, Freire CSR, et al. Suberin isolation from cork using ionic liquids: characterisation of ensuing products. New J Chem. 2012;36:2014–24. doi:10.1039/c2nj40433h. [Google Scholar] [CrossRef]
9. Rizikovs J, Godina D, Makars R, Paze A, Abolins A, Fridrihsone A, et al. Suberinic acids as a potential feedstock for polyol synthesis: separation and characterization. Polymers. 2021;13(24):4380. doi:10.3390/polym13244380. [Google Scholar] [PubMed] [CrossRef]
10. Rižikovs J, Zandersons J, Paže A, Tardenaka A, Spince B. Isolation of suberinic acids from extracted outer birch bark depending on the application purposes. Balt For. 2014;20:98–105. [Google Scholar]
11. Makars R, Rizikovs J, Godina D, Paze A. Utilization of suberinic acids containing residue as an adhesive for particle boards. Polymers. 2022;14(11):2304. doi:10.3390/polym14112304. [Google Scholar] [PubMed] [CrossRef]
12. Makars R, Rizikovs J, Paze A. Study of catalysts for suberinic acid-based adhesive polymerization. Mater Sci Forum. 2022;1071:182–8. doi:10.4028/p-gxs1x9. [Google Scholar] [CrossRef]
13. Makars R, Godina D, Rizhikovs J, Paze A, Tupciauskas R, Berzins R. Investigation of furfural formation and mechanical properties of suberinic acids-bonded particleboards depending on their preparation parameters. Key Eng Mater. 2021;903:235–40. doi:10.4028/www.scientific.net/KEM.903.235. [Google Scholar] [CrossRef]
14. Godina D, Makars R, Abolins A, Paze A, Kirpluks M, Rizikovs J. Suberinic acid isolation from birch outer bark and their characterization. Mater Sci Forum. 2022;1071:166–73. doi:10.4028/p-75i7vl. [Google Scholar] [CrossRef]
15. Shulga G, Rizhikovs J, Neiberte B, Verovkins A, Vitolina S, Betkers T, et al. Processing and properties of woodlastic composite containing alkali-treated birch wood shavings and bioadditive obtained by biorefinery of birch bark. Forests. 2023;14(9):1906. doi:10.3390/f14091906. [Google Scholar] [CrossRef]
16. Ivdre A, Abolins A, Volkovs N, Vevere L, Paze A, Makars R, et al. Rigid polyurethane foams as thermal insulation material from novel suberinic acid-based polyols. Polymers. 2023;15(14):3124. doi:10.3390/polym15143124. [Google Scholar] [PubMed] [CrossRef]
17. Abolins A, Ivdre A, Volkovs N, Makars R, Vevere L, Paze A, et al. Synthesis and characterization of bio-polyols synthesized from various treated depolymerized suberin for rigid polyurethane foams. Eur Biomass Conf Exhibit Proc. 2023;1085–88. doi:10.5071/31stEUBCE2023-6BV.2.32. [Google Scholar] [CrossRef]
18. Pollard M, Beisson F, Li Y, Ohlrogge JB. Building lipid barriers: biosynthesis of cutin and suberin. Trends Plant Sci. 2008;13:236–46. doi:10.1016/j.tplants.2008.03.003. [Google Scholar] [PubMed] [CrossRef]
19. Bernards MA, Lewis NG. The macromolecular aromatic domain in suberized tissue: a changing paradigm. Phytochemistry. 1998;47:915–33. doi:10.1016/S0031-9422(98)80052-6. [Google Scholar] [PubMed] [CrossRef]
20. Pásztory Z, Mohácsiné IR, Gorbacheva G, Börcsök Z. The utilization of tree bark. BioResources. 2016;11:7859–88. doi:10.15376/biores.11.3.Pasztory. [Google Scholar] [CrossRef]
21. Kolattukudy PE. Polyesters in higher plants. Adv Biochem Eng Biotechnol. 2001;71:1–49. doi:10.1007/3-540-40021-4_1. [Google Scholar] [PubMed] [CrossRef]
22. Graça J, Pereira H. Methanolysis of bark suberins: analysis of glycerol and acid monomers. Phytochem Anal. 2000;11:45–51. doi:10.1002/(SICI)1099-1565(200001/02)11:1<45::AID-PCA481>3.0.CO;2-8. [Google Scholar] [CrossRef]
23. Cordeiro N, Belgacem MN, Silvestre AJD, Pascoal Neto C, Gandini A. Cork suberin as a new source of chemicals. 1. Isolation and chemical characterization of its composition. Int J Biol Macromol. 1998;22:71–80. doi:10.1016/S0141-8130(97)00090-1. [Google Scholar] [PubMed] [CrossRef]
24. Holloway PJ. Some variations in the composition of suberin from the cork layers of higher plants. Phytochemistry. 1983;22:495–502. doi:10.1016/0031-9422(83)83033-7. [Google Scholar] [CrossRef]
25. Ekman C, Eckerman R. Aliphatic carboxylic acids from suberin in birch bark by hydrolysis, methanolysis, and alkali fusion, vol. A2. Lab For Prod Chem, Åbo Akademi; 1985. [Google Scholar]
26. Holloway PJ, Brown Deas AH. Epoxyoctadecanoic acids in plant cutins and suberins. Phytochemistry. 1973;12:1721–35. doi:10.1016/0031-9422(73)80393-0. [Google Scholar] [CrossRef]
27. Vangeel T, Neiva DM, Quilhó T, Costa RA, Sousa V, Sels BF, et al. Tree bark characterization envisioning an integrated use in a biorefinery. Biomass Convers Biorefin. 2023;13:2029–43. doi:10.1007/s13399-021-01362-8. [Google Scholar] [CrossRef]
28. Nunes E, Teresa Quilho HP. Anatomy and chemical composition of Pinus pinaster bark. IAWA J. 1996;17:141–9. [Google Scholar]
29. Nunes E, Quilh T, Pereira H, Nunes E, Quilh T, Nunes E, et al. Anatomy and chemical composition of Pinus pinea L. bark. Ann For Sci. 1999;56:479–84. [Google Scholar]
30. Bergelin E, Holmbom B. Reactions and distribution of birch extractives in kraft pulp oxygen delignification. J Wood Chem Technol. 2008;28:261–9. doi:10.1080/02773810802452600. [Google Scholar] [CrossRef]
31. Pinto PCRO, Sousa AF, Silvestre AJD, Neto CP, Gandini A, Eckerman C, et al. Quercus suber and betula pendula outer barks as renewable sources of oleochemicals: a comparative study. Ind Crops Prod. 2009;29:126–32. doi:10.1016/j.indcrop.2008.04.015. [Google Scholar] [CrossRef]
32. Nukala SG, Kong I, Kakarla AB, Tshai KY, Kong W. Preparation and characterisation of wood polymer composites using sustainable raw materials. Polymers. 2022;14(15):3183. doi:10.3390/polym14153183. [Google Scholar] [PubMed] [CrossRef]
33. Sousa AF, Gandini A, Silvestre AJD, Pascoal Neto C. Synthesis and characterization of novel biopolyesters from suberin and model comonomers. ChemSusChem. 2008;1:1020–5. doi:10.1002/cssc.200800178. [Google Scholar] [PubMed] [CrossRef]
34. Heinämäki J, Halenius A, Paavo M, Alakurtti S, Pitkänen P, Pirttimaa M, et al. Suberin fatty acids isolated from outer birch bark improve moisture barrier properties of cellulose ether films intended for tablet coatings. Int J Pharm. 2015;489:91–9. doi:10.1016/j.ijpharm.2015.04.066. [Google Scholar] [PubMed] [CrossRef]
35. Cordeiro N, Belgacem MN, Gandini A, Pascoal Neto C. Urethanes and polyurethanes from suberin 2: synthesis and characterization. Ind Crops Prod. 1999;10:1–10. doi:10.1016/S0926-6690(98)00029-6. [Google Scholar] [CrossRef]
36. Cordeiro N, Belgacem MN, Gandini A, Neto CP. Urethanes and polyurethanes from suberin: 1. Kinetic study. Ind Crops Prod. 1997;6:163–7. doi:10.1016/S0926-6690(96)00212-9. [Google Scholar] [CrossRef]
37. Fernandes EM, Aroso I, Pires RA, Correlo VM, Pitkänen P, Koskimies S, et al. Improvement on the mechanical properties of cork composites using suberin as coupling agent through a reactive extrusion process. In: 69th Annual Technical Conference of the Society of Plastics Engineers; 2011; Boston, MA, USA; 2011. p. 611–615. [Google Scholar]
38. de Oliveira H, Yoon B, Michaud V, Nam JDo, Suhr J. All natural cork composites with suberin-based polyester and lignocellulosic residue. Ind Crops Prod. 2017;109:843–9. doi:10.1016/j.indcrop.2017.09.044. [Google Scholar] [CrossRef]
39. Oh T, Cho S, Yoon B, Yoon H, Suhr J. Effect of cork extract on the mechanical property of thermoplastic polyurethane. Composites Reasearch. 2023;36:86–91. [Google Scholar]
40. Cho SH, Yoon B, Lee SK, Nam J, Suhr J. Natural cork suberin-originated ecofriendly biopolyester syntactic foam. ACS Sustain Chem & Eng. 2022;10:7508–14. doi:10.1021/acssuschemeng.2c00278. [Google Scholar] [CrossRef]
41. Menager C, Nathanaël G, Luc Vincent NS. Suberin from cork as a tough cross-linker in bioepoxy resins. ACS Appl Polym Mater. 2021;3:6090–101. doi:10.1021/acsapm.1c00927. [Google Scholar] [CrossRef]
42. Korpinen RI, Kilpeläinen P, Sarjala T, Nurmi M, Saloranta P, Holmbom T, et al. The hydrophobicity of lignocellulosic fiber network can be enhanced with suberin fatty acids. Molecules. 2019;24:1–14. doi:10.3390/molecules24234391. [Google Scholar] [PubMed] [CrossRef]
43. Jeżo A, Kowaluk G. Carbon capture and storage through upcycling of suberinic acid residues in wood composites finishing. C. 2023;9(3):80. doi:10.3390/c9030080. [Google Scholar] [CrossRef]
44. Garcia H, Ferreira R, Martins C, Sousa AF, Freire CSR, Silvestre AJD, et al. Ex situ reconstitution of the plant biopolyester suberin as a film. Biomacromolecules. 2014;15:1806–13. doi:10.1021/bm500201s. [Google Scholar] [PubMed] [CrossRef]
45. Bernards MA, Lopez ML, Zajicek J, Lewis NG. Hydroxycinnamic acid-derived polymers constitute the polyaromatic domain of suberin. J Biol Chem. 1995;270:7382–6. doi:10.1074/jbc.270.13.7382. [Google Scholar] [PubMed] [CrossRef]
46. Kumar A, Korpinen R, Möttönen V, Verkasalo E. Suberin fatty acid hydrolysates from outer birch bark for hydrophobic coating on aspen wood surface. Polymers. 2022;14:1–14. doi:10.3390/polym14040832. [Google Scholar] [PubMed] [CrossRef]
47. Handiso B, Valle-Delgado JJ, Johansson LS, Hughes M. The physicochemical properties of cellulose surfaces modified with (Depolymerised) suberin and suberin fatty acid. Ind Crops Prod. 2021;159:113070. doi:10.1016/j.indcrop.2020.113070. [Google Scholar] [CrossRef]
48. Trovagunta R, Hubbe MA. Suberin as a bio-based flame-retardant? BioResources. 2023;18:4388–91. doi:10.15376/biores.18.3.4388-4391. [Google Scholar] [CrossRef]
49. Paze A, Rizhikovs J, Brazdausks P, Puke M, Grinins J, Tupciauskas R, et al. Processing possibilities of birch outer bark into green bio-composites. Vide Tehnologija Resursi-Envir, Technol, Res. 2017;3:249–53. doi:10.17770/etr2017vol3.2577. [Google Scholar] [CrossRef]
50. Lang J, Dörrstein J, Zollfrank C. Archaeo-inspired material synthesis: sustainable tackifiers and adhesives from birch bark. Green Mater. 2018;6:157–64. doi:10.1680/jgrma.18.00042. [Google Scholar] [CrossRef]
51. European Committee for Standarization, Brussels B. EN 312:2010 particleboards-specifications. 2010. [Google Scholar]
52. Janis R, Aigars P, Raimonds M, Ramanas T. EP3807341-A method for obtaining thermoreactive binders for a production of wood composite materials from birch outer bark. 2021. Available from: https://patentscope.wipo.int/search/en/detail.jsf?docId=WO2021024152. [Accessed 2024]. [Google Scholar]
53. European Committee for Standarization, Brussels B. EN 314:2004 plywood-bonding quality–part 1: test methods. 2004. [Google Scholar]
54. Paze A, Rizhikovs J, Godiņa D, Rudolfs Berzins RM. Development of plywood binder by partial replacement of phenol-formaldehyde resins with birch outer bark components. Key Eng Mater. 2021;903:229–34. doi:10.4028/www.scientific.net/KEM.903.229. [Google Scholar] [CrossRef]
55. Tupciauskas R, Meile K, Godina D, Rizhikovs J, Syrpas M, Venskutonis PR. Qualitative differences and emission persistence of volatile organic compounds from bio-based particleboards. Materials. 2022;15:1–13. doi:10.3390/ma15155278. [Google Scholar] [PubMed] [CrossRef]
56. Jeżo A, Wronka A. Post-extraction birch bark residues as a potential binder in particleboards. Ann WULS, For Wood Technol. 2022;118:35–47. doi:10.5604/01.3001.0016.0490. [Google Scholar] [CrossRef]
57. Jeżo A, Wronka A, Dębiński A, Kristak L, Reh R, Rizhikovs J, et al. Influence of upcycled post-treatment bark biomass addition to the binder on produced plywood properties. Forests. 2023;14(1):1–14. doi:10.3390/f14010110. [Google Scholar] [CrossRef]
58. Hassan EB, Moon Kim HW. Phenol formaldehyde-type resins made from phenol-liquefied wood for the Bonding.Pdf. J Appl Polym Sci. 2009;112:1097–862. [Google Scholar]
59. Paul GB, Timar MC, Zeleniuc O, Lunguleasa A, Coşereanu C. Mechanical properties and formaldehyde release of particleboard made with lignin-based adhesives. Appl Sci. 2021;11(18):8720. doi:10.3390/app11188720. [Google Scholar] [CrossRef]
60. Sedliačik J, Bekhta P, Potapova O. Technology of low-temperature production of plywood bonded with modified phenol-formaldehyde resin. Wood Research. 2010;55:123–30. [Google Scholar]
61. Lubis MAR, Falah F, Harini D, Sudarmanto AK, Tjahyono B, Fatriasari W, et al. Enhancing the performance of natural rubber latex with polymeric isocyanate as cold-pressing and formaldehyde free adhesive for plywood. J Adhes. 2023;1:58–73. doi:10.1080/00218464.2021.1999233. [Google Scholar] [CrossRef]
62. Sutiawan J, Hermawan D, Massijaya MY, Kusumah SS, Lubis MAR, Marlina R, et al. Influence of different hot-pressing conditions on the performance of eco-friendly jabon plywood bonded with citric acid adhesive. Wood Mater Sci Eng. 2022;17:400–9. doi:10.1080/17480272.2021.1884898. [Google Scholar] [CrossRef]
63. BASF. BASF safety data sheet according to UN GHS 4th Rev. In: Elastospray* 1622/6 Polyol Component. 2022. p. 1–14. [Google Scholar]
64. Duval A, Vidal D, Sarbu A, René W, Avérous L. Scalable single-step synthesis of lignin-based liquid polyols with ethylene carbonate for polyurethane foams. Mater Today Chem. 2022:24. doi:10.1016/j.mtchem.2022.100793. [Google Scholar] [CrossRef]
65. Cateto CA, Barreiro MF, Ottati C, Lopretti M, Rodrigues AE, Belgacem MN. Lignin-based rigid polyurethane foams with improved biodegradation. J Cell Plast. 2014;50:81–95. doi:10.1177/0021955X13504774. [Google Scholar] [CrossRef]
66. Čuk N, Fabjan E, Grželj P, Kunaver M. Water-blown polyurethane/polyisocyanurate foams made from recycled polyethylene terephthalate and liquefied wood-based polyester polyol. J Appl Polym Sci. 2015;132:1–7. doi:10.1002/app.41522. [Google Scholar] [CrossRef]
67. Hu S, Li Y. Two-step sequential liquefaction of lignocellulosic biomass by crude glycerol for the production of polyols and polyurethane foams. Bioresour Technol. 2014;161:410–5. doi:10.1016/j.biortech.2014.03.072. [Google Scholar] [PubMed] [CrossRef]
68. Ma X, Chen J, Zhu J, Yan N. Lignin-based polyurethane: recent advances and future perspectives. Macromol Rapid Commun. 2021;42:1–13. doi:10.1002/marc.202000492. [Google Scholar] [PubMed] [CrossRef]
69. Li Y, Luo X, Hu S. Bio-based polyols and polyurethanes. Switzerland: Springer Cham; 2015. [Google Scholar]
70. Zhang HR, Pang H, Zhang L, Chen X, Liao B. Biodegradability of polyurethane foam from liquefied wood based polyols. J Polym Environ. 2013;21:329–34. doi:10.1007/s10924-012-0542-2. [Google Scholar] [CrossRef]
71. Zhang R, Ma E. Improving dimensional stability of Populus cathayana wood by suberin monomers with heat treatment. iForest. 2021;14:313–9. doi:10.3832/ifor3684-014. [Google Scholar] [CrossRef]
72. Gee CT, Mccoy VE, Stoneman M, Müller CE. Suberin, the hallmark constituent of bark, identified in a 45-million-year-old monkeyhair tree from Geiseltal, Germany. Res Sq. 2023. doi:10.21203/rs.3.rs-3486066/v1. [Google Scholar] [CrossRef]
73. Križková L, Lopes MH, Polónyi J, Belicová A, Dobias J, Ebringer L. Antimutagenicity of a suberin extract from Quercus suber cork. Mutat Res Genet Toxicol Environ Mutagen. 1999;446:225–30. doi:10.1016/S1383-5718(99)00190-4. [Google Scholar] [PubMed] [CrossRef]
74. Kligman A, Dastmalchi K, Smith S, George John RES. Building blocks of the protective suberin plant polymer self-assemble into lamellar structures with antibacterial potential. ACS Omega. 2022;7:3978–89. doi:10.1021/acsomega.1c04709. [Google Scholar] [PubMed] [CrossRef]
75. Dönmez İE, Önem E. Chemical composition and in vitro antibacterial activity of bark extractives and suberin monomers from Pinus brutia and Pinus nigra. Eur J Wood Prod. 2024;82:231–40. doi:10.1007/s00107-023-02004-8. [Google Scholar] [CrossRef]
76. Liakos IL, Menager C, Guigo N, Holban AM, Iordache F, Pignatelli F, et al. Trans-cinnamaldehyde oil nanoparticles with antimicrobial activity and anticancer properties when loaded with paclitaxel. ACS Appl Bio Mater. 2019;2:3484–97. doi:10.1021/acsabm.9b00408. [Google Scholar] [CrossRef]
77. Fernandes EM, Lobo FCM, Faria SI, Gomes LC, Silva TH, Mergulhão FJM, et al. Development of cork biocomposites enriched with chitosan targeting antibacterial and antifouling properties. Molecules. 2023;28:1–20. doi:10.3390/molecules28030990. [Google Scholar] [PubMed] [CrossRef]
Cite This Article
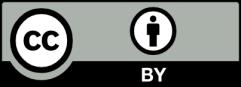
This work is licensed under a Creative Commons Attribution 4.0 International License , which permits unrestricted use, distribution, and reproduction in any medium, provided the original work is properly cited.