Open Access
ARTICLE
Optimization and Characterization of Combined Degumming Process of Typha angustata L. Stem Fibers
Laboratory of Textile Engineering (LGTex), University of Monastir, Ksar Hellal, 5070, Tunisia
* Corresponding Author: Sana Rezig. Email:
(This article belongs to the Special Issue: Recent Advances in Lignocellulosic Fiber-Polymer)
Journal of Renewable Materials 2024, 12(6), 1071-1086. https://doi.org/10.32604/jrm.2024.049935
Received 23 January 2024; Accepted 12 April 2024; Issue published 02 August 2024
Abstract
Plant derived natural fibers have been widely investigated as alternatives to synthetic fibers in reinforcing polymers. Researchers over the years have explored many plant fibers using different extraction processes to study their physical, chemical, and mechanical properties. In this context, the present study relates to the extraction, characterization, and optimization of Typha angustata L. stem fibers. For this purpose, desirability functions and response surface methodology were applied to simultaneously optimize the diameter (D), linear density (LD); yield (Y), lignin fraction (L), and tenacity (T) of Typha stem fibers. Typha stems have been subjected to both alkali (NaOH) and enzymatic (pectinex ultra-SPL) treatments. Three levels of process variables including enzyme concentration (10, 15, and 20 ml/L) and treatment duration (10, 15, and 20 days) were used to design the experiments according to the factorial design. Experimental results were examined by analysis of variance and fitted to second order polynomial model using multiple regression analysis. The Derringer’s desirability function released that the values of process variables generating optimized diameter, linear density, yield, lignin ratio and tenacity are 20 ml/L and 20 days for concentration of pectinex ultra-SPL enzyme and treatment duration, respectively. Confirmation was performed and high degree of correlation was found between the experimental and statistical values. Moreover, the morphological structure has been investigated by the scanning electron microscope, showing a crenelated structure of ultimate fiber bundles of cellulose composing the Typha fiber. Compared to Typha stem non-treated fibers (TSNTF), Typha stem combined treated fibers (TSCTF), brings to improve mechanical properties. This change in mechanical properties is affected by modifying the fiber structure showing alpha cellulose of (66.86%) and lignin ratio of (10.83%) with a crystallinity index of (58.47%).Graphic Abstract
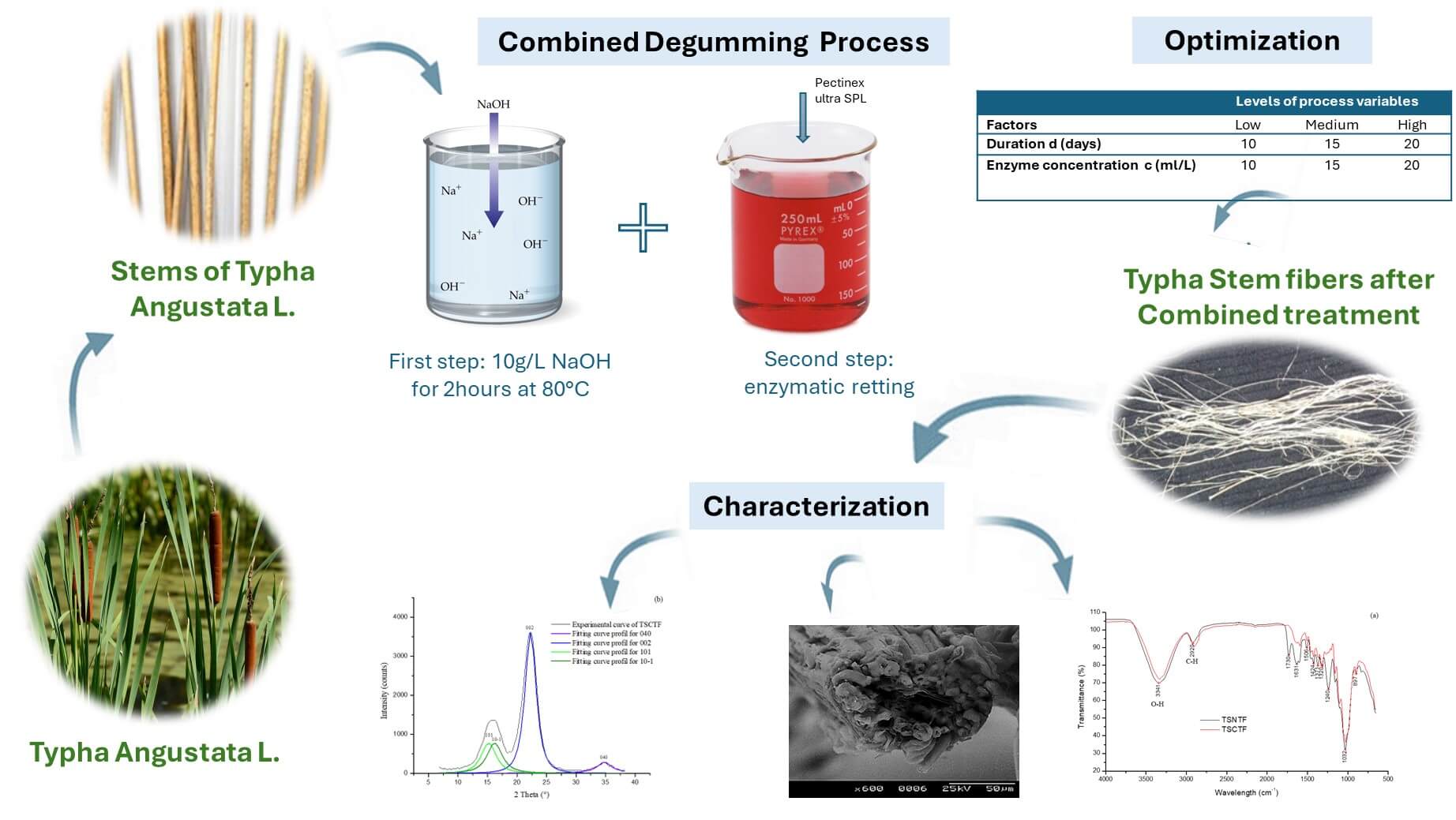
Keywords
The optimization of processes is an essential step to get the best operating parameters in all industries. Especially for the textile industry, having better results while saving costs and production time is very important. The population increment and the higher living standards increase the worldwide use of textiles [1]. However, the average growth of textile industries is covering many problems such as environmental pollution regarding synthetic fiber production [2].
The textile industry’s development is growing quickly. For that, a lot of researchers are developing their research in the textile field related to the development of natural fibers. In addition, the demand for alternative materials with cheap production cost, low density, good thermal properties, and eco-friendly and better mechanical properties encourages investigating and valorizing other sources of natural fibers [3]. Vegetable fibers are the most widely distributed natural fibers on earth [4].
Several non-conventional plant fibers have been available all over the world, with potential textile applications but unexplored. For example, the wetland plants were considered as a novel source of natural fibers. Typha plant is being considered as one of them. In addition, the Typha leaf fiber was found to be very similar to jute fiber which is used for textile applications [5].
Typha angustata L. Fig. 1a, a variety from Tunisia, is an aquatic plant that can be found in numerous wetlands around the world. It is commonly considered a wetland indicator plant because it is widely distributed across margins, rivers, and contaminated reservoirs. As shown in Fig. 1a, the Typha plant is composed of thick leaves with spongy sections, around the stem which ends with a brown flower [6]. Properties of fibers extracted from different varieties of Typha leaves and provided by different extraction processes were characterized. Extracted from different varieties and regions of the world, Typha leaf fibers revealed a lignocellulosic structure compared to other natural fibers such as jute, kenaf, agave, and hemp [7].
Figure 1: (a) Typha angustata L. plant, (b) Typha stems, (c) Typha fibers
The extraction of Typha fibers from its leaves as a source of reinforcement in composite materials or making papers has been widely discussed. In contrast, there is no relative investigation on the extraction of Typha fibers from its stems (Fig. 1b) and their applications. In addition, as a first study, a recent paper dealing with the extraction of Typha stem fibers and their valorization for polyester reinforcement materials has been reported [8]. In this investigation, NaOH treatment was used to extract fibers from Typha angustata L. stems. The alkali treatment using caustic soda was frequently used for the extraction of technical fibers due to its effectiveness and simplicity with less impact on the environment [9,10].
Another treatment was used to extract vegetable fibers: Enzymatic retting. Researchers have used enzymes such as viscozyme L, pectinex ultra-SPL, xylanase, and laccase to extract plant fibers [11]. One of the principal parameters in the enzymatic treatment is the immersion time because it attacks the fiber surface which can modify the mechanical properties. Researchers have investigated the effect of pectinex immersion duration on the mechanical properties of kenaf fibers using two variables 1% and 2% enzyme concentrations and duration treatment of 10, 15, and 20 days. Also, a comparison between the enzymatic and NaOH treatments was investigated. The outcome of this research revealed that the best mechanical properties of kenaf fibers were obtained within 2% of the enzyme for 20 days of soaking time. Pectinex ultra-SPL destroyed non-cellulosic materials on the surface of kenaf fibers without damaging them [12]. Pectinex ultra-SPL, a highly active preparation of pectolytic enzymes produced by a selected strain of Aspergillus aculeatus. This enzyme preparation contains the pectolytic enzyme and a range of hemicellulosic activities. It could break down plant cell walls.
Recent research carried out on Typha latifolia L. plant using enzyme pectinase from Aspergillus aculeatus, shows that 3% of the enzyme at room temperature does not affect the Typha plant for up to 3 months. After treatment, the sheets of the Typha plant were like virgin plants [13]. This investigation confirms that the Typha plant is considered a highly water-tolerant plant [7].
Among studies devoted to fiber extraction from the Typha plant, a very limited research effort has been observed in the optimization of different extraction methods. Previous studies show the optimization process using an alkali treatment for fibers extracted from both leaves [14] and stem of Typha angustata L [15]. Results show that the optimum conditions for the Typha angustata L. leaf extraction process were found to be 20 g/L of NaOH at 100°C for 3 h. At these parameters, we obtained an extraction yield of 37.82%, an average diameter of 303.86 µm, a lignin fraction of 13.65, an average linear density of 22.47 tex and a tenacity of 12.41 cN/tex [14]. In another paper dealing with the same topic, authors determined the optimization process conditions of Typha stems which are 30 g/L of soda concentration at 120°C for 4 h. Obtained fibers in the indicated conditions, show an average diameter of 208.12 µm, a lignin fraction of 22.05%, an extraction yield of 39.68%, a linear density of 29.65 tex and a tenacity of about 9.42 cN/tex [15].
Another research paper was carried out on the optimization of fiber yield from the Typha latifolia L. variety. Typha leaves were subjected to 3% of alkali (LiOH and KOH) treatments at 80°C and 95°C for different time duration (2, 4, 6, and 8 h). Results show that the yield of fiber extraction extended between 30% and 50% controlled by alkali treatment duration and temperature. The most significant result was equal to 43.24%. It was obtained after 2 h of alkali treatment [13].
For this purpose, the objective is to optimize a novel treatment combining NaOH and pectinex ultra-SPL enzyme. Thus, this investigation used RSM optimization and desirability functions to study the correlation between input parameters and responses. A factorial design method was used to determine the influence of two variables, duration (d) and enzyme concentration (c) on yield ratio (Y), lignin ratio (L), diameter (D), tenacity (T), and linear density (LD) of obtained fibers. In the second part, characterizations of the untreated (TSNTF) and optimized fibers (TSCTF) were evaluated in terms of morphological, physical, chemical, and mechanical characteristics. In addition, most characteristics of vegetable fibers are dependent on the extraction process which affects the choice of the appropriate applications [16].
Typha angustata L. plants were harvested from a local river in the region of Moknine-Monastir (Tunisia). Stems were decorticated and exposed to solar radiation to dry them for about one week. After that, stems of Typha plants were introduced in a hot air oven at a temperature equal to 105°C for dehydration until a dry constant weight. Finally, assembled stems were dried at room temperature for 48 h and cut to 10–12 cm in length before extraction treatment.
2.2.1 Extraction of Typha Stem Fibers
Many preliminary tests were carried out to extract Typha stem fibers (TSF) using only Pectinex Ultra SPL enzyme. As a result, using 20 ml/L of pectinex ultra-SPL for more than 90 days did not attack the Typha stems and there was no appearance of Typha fibers [13]. Since it was not possible to obtain good results using enzyme extraction, we thought about preparing the material before treating it with the enzyme. This method was frequently used when extracting other fibers such as alfa [17]. The combination of two or more additional treatments was sometimes necessary to obtain better-quality fibers [18].
The extraction process consisted primarily of treating TSF in a 10 g/L solution of sodium hydroxide at a temperature of 80°C for 2 h, conditions determined after several preliminary tests [15]. Secondly, the fibers were treated in an aqueous solution of enzymes. This enzyme was provided for this study by Novozymes.
Enzyme solutions were developed by putting 0.05 M of sodium acetate with 50 mM of ethylene diamine tetraacetic acid (EDTA). EDTA was added as a chelating agent for the extraction of Typha fibers, as it has already been tested for nettle and flax [19].
Based on the research carried out on other plant fibers, several tests were manipulated to optimize the conditions of extraction of Typha fibers. Duration of less than 10 days and the use of less than 10 ml/L of the enzyme do not affect the stems of Typha. For that reason, we have chosen 10 days and 10 ml/L of pectinex ultra-SPL as low conditions. The experimental conditions were resumed in Table 1.
The treated fibers were carefully washed in cold water and dried under ambient climatic conditions. Typha stem fibers (TSCTF) obtained after combined treatment were presented in Fig. 1c.
2.2.2 Characterization of Extracted Typha Stem Fibers
The diameter of Typha samples was measured following the standard NF G07-004. The tests were carried out on random material with 300 replicates for each sample using an optic microscope model Leica.
The linear density was also measured following the standard ISO 1973. Samples of Typha with known lengths were weighted and the linear density of each sample was determined using the gravimetric procedure. Results were reported as the mean value of 50 sample repetitions.
The tensile test of derived fibers was investigated using the dynamometer LLOYD. The tests were processed following the NF G07-002. The obtained results were presented as the mean value of 50 sample repetitions.
The yield of obtained fibers was calculated by applying the gravimetric method following standard NF G08-001. The yield was estimated by the percentage of the fraction between the mass of Typha stem fibers after and before the combined process.
The morphological examination of the obtained fibers was performed using a Hitachi S-2360N, scanning electron microscopy. Before observation, fibers were metalized. Longitudinal and cross-section images were taken at an acceleration voltage ranging between 8 to 25 Kv.
The chemical composition (alpha-cellulose and lignin faction) of Typha samples was quantified using the TAPPI standard methods: T 203 cm-09 and T 222 om-11.
The X-ray diffraction (XRD, PANalytical (X’PERT Pro model (1967),) measurements were carried out by using Cu Kα radiation in a range 2θ = 5°–50° to investigate the crystalline structure of the Typha samples. The degree of crystallinity was calculated using the Hindeleh and Johnson formula. Curve fitting of the different peaks of each spectrum was undertaken using the «Origin 6.0» processing software to determine the amorphous and crystalline regions [8].
Also, each peak profile was defined referring to the Pearson VII function. Once deconvolution was completed, crystallinity Cr (%) was quantified by the ratio between the sum of the area of crystalline peaks (AC) and the total area (AT) presented by the Eq. (1):
Cr(%)=ACAT×100 (1)
Finally, ATR-FTIR spectrometer was applied to define the functional groups present in TSNTF and TSCTF between 400 and 4000 cm−1.
Considering the Typha stem combined Treatment fibers (TSCTF), we have implemented a complete factorial experiment plan. In this study, all statistical analysis was tracked by applying the statistical software «Minitab 17». A set of tests was developed by modifying Typha fiber extraction parameters. For that, 2 input parameters were fixed: extraction duration in the number of days (d) and the enzyme concentration in ml/L (c). The out puts variables are extraction yield (Y), diameter (D), linear density (LD), tenacity (T) and lignin content (L). Experimental data were fitted to the following second-order polynomial equation [20]:
Yi=a0+a1Xc+a2Xd+a11X2c+a22X2d+a12XcXd (2)
With:
• Yi presented the response of processing parameters which were yield (YY), diameter (YD), linear density (YLD), tenacity (YT), and lignin ratio (YL).
• Xd and Xc were the standardized values of duration (d) and concentration (c), correspondingly.
• a0, ai, and aij were unknown appropriate variables evaluated from the test data.
To make an easy comparison, the independent parameters were standardized to values from 1 to 3. For that, this experiential design could be appropriate to optimize the extraction conditions of Typha samples (TSCTF), and to determine the suitable conditions procedure (c and d) that decreases D, LD, and L and increases Y and T. Two desirability purposes [21] noted “di” were selected in the current research: desirability function to maximize and to minimize [14,15].
So, using these functions, individual desirability di for each measured characteristic could be performed. Then, the global desirability could be calculated by the Derringer and Suich method presented in the following equation:
dg=w√(dDwD×dLDwLD×dLwL×dYwY×dTwT) (3)
With:
“w” presents the sum of wi and wi (i = D, LD, L, Y and T) presents the correlative weight indicating the property’s (Yi) significance in the “dg” desirability purpose. So, the agreement between obtained characteristics was more accepted if “dg” improved. Besides, it was becoming “ideal” when “dg” grew to 1. As a consequence, the satisfaction degree “di” of the property Yi was identical to 0, the response had a value outer of tolerance and the desirability purpose “dg” was identical to 0 and the agreement was declined [21]. As a consequence, the optimum values of concentration and duration were those making “dg” near to 1.
Therefore, to intensify a property “Yi”, in particular Tenacity (YT), the desirability function must be utilized, where the single desirability (dT) was estimated using the following equations:
dT= 0 if YT≤YTmin (4)
dT=(YT−YTminYTtarget−YTmin)s if YTmin≤YT≤YTtarget (5)
dT=1 if YT≥YT target (6)
Besides, to minimize a property “Yi”, such as the Lignin ratio (YL), the desirability purpose must be involved, where the single desirability (dL) was performed using the following equations:
dL=1 if YL≤YLtarget (7)
dL=(YL−Y LmaxY Ltarget−Y Lmax)s if YL target≤YL≤YLmax (8)
dL=0 if YL≥YLmax (9)
3.1 Development of Extracting Fibers Procedure
Statistics of measured properties are reported in Table 2. A multiple linear regression analysis according to Eq. (2) was calculated using the Minitab 17 software. Table 2 shows that the coefficient of variation for every dependent variable was adjusted and the findings were between 2% and 38.35%. These variations were related to environmental influences and inter-plant variability of natural fibers [22].
A mathematical model was constructed to relate the response variable with the factor effects to evaluate the experimental designs. Using Minitab 17 software, the equations are exposed to non-linear designing to find out the best operating conditions. Table 3 shows the terms of the related equations associated with their equivalent Pearson linear coefficient of determination R square and the p-value at a 95% confidence interval. It also presents statistic parameters related to the different responses for YLD, YD, YY, YT and YL. The p-value determines the significance of each model. In fact, when the p-value is low, the related coefficients will be more efficient. From this study, findings show that the p-value for each property was less than 0.05 and the model is significant. The R square for every second-order multivariate analysis was presented in the following table:
So, from this Table, results show that the second-order polynomial equation employed is pertinent, convincing, and suitable to confer the correspondence between the response and the controlled factors. To optimize the extraction parameters, the desirability purpose was used [23]. In addition, it presents the most recommended tool for optimization using the second-order model [24].
With this method, each property was converted to an individual desirability. Table 4 shows the most favorable conditions and the related standardized factors for the independent elements. The best proportions of the measured elements for the extraction process required operating in medium to high enzyme concentration and duration, taking into consideration that:
• Best results for diameter, yield, tenacity, and linear density are obtained by applying high soaking time and pectinex ultra-SPL concentration.
• The greatest lignin ratio is acquired using moderately high enzyme concentration and duration.
The functional setting for the output values as shown in Table 4 was utilized to determine the expected amounts of characteristics of extracted fibers and the divergence from the most favorable conditions (Table 5).
The obtained outcomes from Table 4 could indicate that good quality in terms of resistance, yield, and fineness was obtained using high enzyme concentration (20 ml/L) and soaking time (20 days). Considering these conditions, TSCTF properties deceased just (0%–6%) from the best conditions (Table 5). To optimize the extraction process, it is not possible to optimize each response separately. In addition, an overall solution should be included in an optimal region to find a compromise to maximize tenacity, yield ratio, and fineness measurement.
Since 1980, Derringer et al. established the desirability functions which present one of the most used solutions to optimize multiple responses [25]. The concept of this method was founded on the principle that the quality of a procedure that possesses numerous responses is wholly «rejected” when even one of the responses is outer of the desirable “limit”. The objective was to define the executing setting making sure that all responses approve the criterion all together to get the favorable conditions in the advantageous common response. For that, the desirability approach involves converting the multiple responses into a single one. The first step was to create an individual desirability function (di) for each response using the developed model.
The desirability function takes a value between 0 and 1. In addition, when this function is equal to 0, it means that we have an undesirable response, whereas, when it is equal to 1, we have an ideal response. For every test, we obtain the single desirability purpose for every property that reveals if the response is satisfying or not [25].
Also, utilizing the Derringer and Suich method, we give a global desirability function presenting the global satisfaction of all properties, for the extraction process by giving the relative weight “wi”.
After choosing the significant objective for every response, we get the best curve presenting the greatest conditions and measures of TSCTF such as the linear density equal to 32.79 tex, the diameter equal to 181 µm, the Lignin ratio equal to 11.53%, the tenacity of about 8.36 cN/tex and the Yield ratio of about 66.51%.
The optimal properties are reached only under optimal conditions of enzyme concentration (20 ml/L) and soaking time (20 days). The global desirability acquired is set up to 95.12% which is meaningful. Data investigation presents the best parameters allowing minimizing soaking time and enzyme which are the high values of the treatment conditions.
3.2 Performance of Typha Stem Samples
To verify the optimized findings from the response surface modeling and the desirability purpose (statistical method), another extraction process was carried out in the indicated conditions (c = 20 ml/l and d = 20 days), and the obtained fibers (experimental method) were characterized. Table 6 shows that TSCTF resulting from the experimental method matches well those obtained from the statistical method. As a result, the sample was validated, and the 2nd order model was appropriate to investigate the optimum values of the dependent parameters.
From Table 6, the experimental method (TSCTF) presents better properties than NaOH-treated leaf and stem fibers in terms of diameter, yield, and lignin ratio.
From the longitudinal micrograph in Fig. 2a, manual fibers extracted from stems of Typha (TSNTF) have a smooth surface with some impurities like wax and gummy substances. This structure contains fats, lignin, pectin, and other non-cellulosic materials. This view has longitudinal ridges characteristic of many vegetable-origin fibers, such as agave Americana L. fiber [26], Sambucus ebulus L. stem fiber, [27] and alfa fiber [28].
Figure 2: SEM of longitudinal views of (a) TSNTF and (b) TSCTF
After combined treatment, Fig. 2b shows a modification in the surface of TSCTF presenting the appearance of ultimate fibers from the technical fiber which is visible due to the removal of lignin, pectin, and other foreign materials. Besides, the longitudinal view of TSCTF presents a “crenelated” structure characterized by rectangular indentation. These findings confirmed results obtained by SEM micrographs of Typha latifolia L. treated fibers [13].
The cross-section micrograph in Fig. 3a reveals that TSNTF and TSCTF are technical fibers or composite fibers like many vegetable fibers. The structure of technical fibers of Typha is composed of ultimate fibers having different numbers and sizes and associated together by non-cellulosic and gummy substances. These results are confirmed with those found by other researchers in the analysis of Typha fibers [29].
Figure 3: SEM of cross-sectional views of (a) TSNTF and (b) TSCTF
After combined treatment, there is a partial removal of the binding material, and thus bundles of individual cell elements begin to show. As a consequence, fine fibers are obtained (Fig. 3b). The cross-section view demonstrates that a Typha fiber was formed by several ultimate fibers separated by the presence of “canals”. Besides, these ultimate fibers are characterized by the presence of lumen of different dimensions, which allows the Typha fiber to have good thermal insulation power [30].
Using high magnification, a view of an ultimate fiber has been detected in Fig. 4 showing a smooth surface with a cylindrical form and a diameter of about 10 µm, which can prove that a great portion of inter lamellar pectin was removed using pectinex ultra-SPL.
Figure 4: SEM of ultimate fiber from TSCTF
Table 7 shows that the lignin ratio of TSNTF seems to be very high 30.4% compared to other plant fibers like flax (2.5%), abaca (5.1%), sisal (7.3%), hemp (4%), whereas, it is similar to jute (12%–33%) and wood (19%–26%) fibers [31]. This investigation can explain the high resistance of Typha stems to enzymatic extraction and the need to treat the stem of Typha with NaOH before the enzymatic retting. So, lignin provides a protection barrier. After the combined degumming process, there is a decrease in lignin fraction to reach 10.83%. This finding confirms the results given by morphological studies. Besides, alpha-cellulose (αc) increases and it reaches 66.86% which is similar to other vegetable fibers like hemp (67%), flax (65%–70%), and ramie (68.2%) [31].
Changes in fineness measurement are shown in Table 8. The untreated Typha fibers TSNTF present a high value of diameter (D) compared with TSCTF (520 µm) and high linear density (LD) of about 41.86 Tex. In addition, this bigger diameter and linear density of TSNTF is well related to the presence of pectin, lignin, and other foreign materials. Also, we noticed that Typha fiber was not single but a technical fiber presenting different numbers of ultimate fibers as revealed by SEM. After combined treatment, TSCTF become thin with about 177 µm of diameter and 33.7 tex of linear density which confirms the reduction of non-cellulosic materials between fiber bundles.
Physical characterizations indicated the tenacity (T) of samples (8.2 cN/tex) with soda and enzymatic treatments due to the removal of impurities and the arrangement of the cellulosic chain; the fiber becomes more homogenous through micro-void elimination. The stress transfer between ultimate cells improves.
The addition of aqueous sodium hydroxide (NaOH) to natural fiber promotes the ionization of the hydroxyl group to the alkoxide. The following reaction takes place because of alkali treatment [32]:
Fiber − OH + NaOH −−−−> Fiber − O − Na + H2O (10)
As a consequence, hydroxyl groups in the unit cells favor the swelling of the cellulose chains which promotes the chain alignment. So, this alignment with the fiber axis increases the tensile strength of fibers [33]. Moreover, pectinex ultra-SP-L in the enzymatic process attacks gums and waxy materials, especially pectin. The addition of EDTA to the pectinase enzyme facilitates the disturbance of the internal ripe plant cell and increases the efficiency of the wheel and the quality of the fiber [19]. So, results of morphological and physical properties explain the difference in fine structure, physical and mechanical properties of Typha fibers.
To better characterize Typha fibers, a crystallographic study was performed. In our study, we are interested in the diffraction of cellulosic compounds; any other crystalline diffraction peak due to non-cellulosic materials will not be considered in the subsequent calculations. Fig. 5 shows the experimental diffractograms of TSNTF and TSCTF indicating the shape of native cellulose presenting 4 diffraction peaks detected at 2θ = 15.2°, 16.2°, 22.2°, and 34.7° which show angles of diffraction of the Miller indices planes (101), (10-1), (002) and (040), respectively, characteristic of cellulose I. The obtained diffraction patterns have an overlapping of the different peaks. To obtain the different peaks and reliable results, deconvolution of these curves has been conducted using the “Origin 6.0” reporting the fitting curve for each plane.
Figure 5: XRD patterns of experimental curves and deconvoluted peaks for TSNTF (a) and TSCTF (b)
Combined treatment denotes a great effect on the crystallinity index (Cr (%)) of Typha stem fibers (Table 8). It reaches 58.47% after NaOH and enzymatic treatments, which is comparable to other varieties of Iranian Typha fibers (60%–65%) [29].
A similar result was concluded by other researchers; Pickering et al. [34] reported that combined enzyme and alkali treatment increased the crystallinity index of hemp fibers due to lignin removal. This increase could be attributed first to the action of alkali treatment and to the removal of amorphous non-cellulosic or amorphous cellulose compounds by enzyme treatment, which would allow better packing of the cellulose chains [35]. Sinha et al. [36] found also that the jute fibers treated with 5% NaOH at 30°C for 2, 4, and 8 h show an improvement in the degree of crystallinity, resulting in improving the mechanical strength of the fibers.
So, gum, pectin, lignin, and other non-cellulosic material removal may change the molecular structure by increasing crystallinity or changing the arrangement of crystallites, in Typha fibers, as is the case for ramie [37]. Therefore, it is indispensable to investigate the lignin content, residual gum, and crystallinity index of Typha fibers to understand the relationship between processing and fiber quality.
ATR-FTIR spectra of TSCTF and TSNTF were presented in Fig. 6 showing the characteristics of most vegetables’ fibers. In addition, the obtained spectra were divided into two regions: the first part of the spectra was similar for both TSNTF and TSCTF, composed of two main bands at the wavelength of 3341 and 2920 cm−1 related to OH stretching vibration of cellulose and the stretching vibration between CH in cellulose, respectively (Fig. 6a). The second part located at wavelength ranging between 800 and 1800 cm−1 was characterized by the presence of numerous bands with different amplifications related to the treatment fiber. Fig. 6b reveals the peaks presented in the second region. In fact, after the combined extraction process, there is either a reduction or absence of some bands which can be explained by the modification of the fiber composition. The missing band at the wavelength of 1730 cm−1 was attributed to the C=O stretching vibration related to hemicellulose. Also, the degradation band at a wavelength of 1631 cm−1 showed the reduction in lignin and hemicellulose amount associated with the OH stretching vibration. The bands at around 1424 and 1371 cm−1 were attributed to C-H bending in-plane deformation related to lignin. The missing band at 1240 cm−1 indicated the elimination of the lignin fraction related to the C-O and C-C stretching vibrations. The band at 1156 cm−1 was also attributed to C-O vibration related to ester carbonyl. Moreover, the band at 1032 cm−1 indicated the presence of C-O, C=C, and C-C-O stretching related to cellulose, hemicellulose, and lignin. Finally, the presence of the band at 897 cm−1 for both TSNTF and TSCTF was related to C-OH stretching indicating the existence of cellulose compounds. These findings underline the modification of the chemical structure especially the reduction of the lignin compound which modifies the fiber structure and properties [8].
Figure 6: (a) ATR-FTIR spectra of TSNTF and TSCTF at wavelength between 500 to 4000 cm−1 (b) ATR-FTIR spectra of TSNTF and TSCTF at wavelength between 800 to 1800 cm−1
As a result, the combined treatment: NaOH and pectinex leads to the loss of lignin and hemicelluloses fractions on the surface of TSCTF. The decreased amount of lignin generates the nonpolar amount to decline and makes stronger the interfacial adhesion of TSCTF and polymers for making composite materials.
Using a combined treatment, Fibers from stems of Typha angustata L. variety have been successfully extracted and the best parameters are those of the extreme limits of the factorial design with high duration and enzyme concentration (20 ml/l pectinex ultra-SPL for 20 days immersion). Extracting Typha stem fibers in these conditions, presents a diameter equal to 177.06 µm, a linear density equal to 33.7 tex, an extraction yield equal to 66.78%, a tenacity of 8.2 cN/tex, and a lignin ratio of 10.83%. These values were found to be in good agreement with the predicted ones. FTIR-ATR and X-ray diffraction confirmed that TSCTF is rich in alpha cellulose content of about 66.86%, with a crystallinity index of 58.47%. Moreover, SEM micrographs revealed that TSCTF provides technical fiber presenting a composite structure containing various numbers of ultimate fibers showing a lumen inside. To valorize these fibers, it will be important to complete this work by performing thermogravimetric analysis to study the thermal stability of the obtained fibers and their applications.
So, Typha stem fibers after combined treatment will be considered as a novel plant fiber providing high crystallinity and thinner diameter with rough surface which make it a good source for textile application especially for reinforcing composite materials.
Acknowledgement: The authors would like to thank everyone who has provided a lot of support in completing this research.
Funding Statement: The authors received no financial support for this research.
Author Contributions: The corresponding author has carried out the extraction process, characterized the obtained fibers and drafted the initial copy, and the rest of the authors provide insightful comments with recommendations while obtaining data, analyzing results, and creating the final text.
Availability of Data and Materials: The corresponding author will provide the datasets created during the current investigation upon reasonable request.
Conflicts of Interest: The authors declare that they have no conflicts of interest to report regarding the present study.
References
1. Wang Y. Recycling in textiles. England: Woodhead Publishing; 2006. [Google Scholar]
2. Sumesh KR, Kavimani V, Rajeshkumar G, Indran S, Saikrishnan G. Effect of banana, pineapple and coir fly ash filled with hybrid fiber epoxy based composites for mechanical and morphological study. J Mater Cycles Waste Manag. 2021;23(4):1277–88. doi:10.1007/s10163-021-01196-6. [Google Scholar] [CrossRef]
3. Babatunde EO, Gurav R, Hwang S. Recent advances in invasive aquatic plant biomass pretreatments for value addition. Waste Biomass Valori. 2023;14:3503–27. doi:10.1007/s12649-023-02186-5. [Google Scholar] [CrossRef]
4. Raharjo WP, Ariawan D, Diharjo K, Raharjo WW, Kusharjanta B. Effect of alkaline treatment time of fibers and microcrystalline cellulose addition on mechanical properties of unsaturated polyester composites reinforced by cantala fibers. Rev Adv Mater Sci. 2023;62(1):2023–0103. doi:10.1515/rams-2023-0103. [Google Scholar] [CrossRef]
5. Haq UN, Huraira A, Uddin MA. Physical characteristics of Typha elephantina Roxb. fiber (Hogla) for textile application. J Tex Inst. 2022;113(11):2328–34. doi:10.1080/00405000.2021.1981020. [Google Scholar] [CrossRef]
6. Sana R, Mounir J, Slah M. Study of structure and properties of Tunisian Typha leaf fibers. Int J Eng Res Technol. 2014;3(3):2278. [Google Scholar]
7. Rezig S, Jaouadi M, Bessghaier AEO, Msahli S. Physical properties, morphology and crystallinity of Typha leaf fibers processed by different extraction treatments. J Tex Inst. 2024. doi:10.1080/00405000.2024.2314261. [Google Scholar] [CrossRef]
8. Sana R, Mounir J, Foued K, Asma E, Msahli S, Bernard D. Effect of alkali-treatment on physico-chemical properties of Typha angustata stem fiber and its composites. J Nat Fibers. 2022;19(17):15948–62. doi:10.1080/15440478.2022.2140327. [Google Scholar] [CrossRef]
9. Werchefani M, Lacoste C, Belguith H, Bradai C. Alfa fibers for Cereplast bio-composites reinforcement: effects of chemical and biological treatments on the mechanical properties. Polym Polym Compos. 2021;29(9):441–9. doi:10.1177/09673911211006067. [Google Scholar] [CrossRef]
10. Durai PN, Viswalingam K, Senthilkumar B, Divakaran D, Siengchin S. Effect of alkalization on physical, chemical, thermal, tensile, and surface morphological properties of Musa acuminata peduncles fiber. Biomass Convers Biorefin. 2023. doi:10.1007/s13399-023-04202-z. [Google Scholar] [CrossRef]
11. Subash MC, Perumalsamy M. Identification of efficient bioprocessing of banana pseudostem waste biomass for sustainable fibers in the textile industry. Waste Biomass Valori. 2023;14:631–44. doi:10.1007/s12649-022-01944-1. [Google Scholar] [CrossRef]
12. Ben Mlik Y, Jaouadi M, Khoffi F, Slah M, Durand B. Study the effect of chemical and enzymatic extraction methods on the kenaf fibers properties. J Nat Fibers. 2022;19(3):1168–77. doi:10.1080/15440478.2020.1837327. [Google Scholar] [CrossRef]
13. Rahman M, Cicek N, Chakma K. The optimum parameters for fibre yield (%) and characterization of Typha latifolia L. fibres for textle applications. Fibers Polym. 2021;22(6):1543–55. doi:10.1007/s12221-021-0194-8. [Google Scholar] [CrossRef]
14. Sana R, Mounir J, Foued K, Slah M, Bernard D. Optimization of extraction process of typha leaf fibres. Indian J Fibre Tex Res. 2016;41(3):242–8. [Google Scholar]
15. Sana R, Mounir J, Foued K, Slah M, Bernard D. Optimization of processing parameters for extraction of typha stem fibers. Int J Appl Res Tex. 2016;4(2):53–64. [Google Scholar]
16. Sana R, Foued K, Yosser BM, Mounir J, Slah M, Bernard D. Flexural properties of typha natural fiber-reinforced polyester composites. Fibers Polym. 2015;16(11):2451–7. doi:10.1007/s12221-015-5306-x. [Google Scholar] [CrossRef]
17. Mohamed D. Evaluation du potentiel textile des fibres d’Alfa (Stipa Tenacissima L.) : Caractérisation physico-chimique de la fibre au fil (Ph.D. Thesis). University of Upper Alsace: Mulhouse, France; 2012 (In French). [Google Scholar]
18. Rogge E. Extraction and study of the physical and mechanical properties of Esparto grass fibres in order to find textile applications (Master Thesis). University of Upper Alsace: France; 2009 (In French). [Google Scholar]
19. Bacci L, Lonardo SD, Albanese L, Mastromei G, Perito B. Effect of different extraction methods on fiber quality of nettle (Urtica dioica L.). Tex Res J. 2010 Dec;81(8):827–37. doi:10.1177/0040517510391698. [Google Scholar] [CrossRef]
20. Ngomade SBL, Rawat N, Ngueteu MLT, Anensong CSD, Bopda A, Nche GNA, et al. Optimization of the oil extraction process by response surface methodology from Podocarpus falcatus seed as a low-grade substitute feedstock for biodiesel applications. Biomass Convers Biorefin. 2023. doi:10.1007/s13399-023-05122-8. [Google Scholar] [CrossRef]
21. Hasan M, Rahman M, Chen Y, Cicek N. Optimization of Typha fibre extraction and properties for bio-composite applications using desirability function analysis. Polymers. 2022;14:1685. doi:10.3390/polym14091685. [Google Scholar] [PubMed] [CrossRef]
22. Msahli S, Ae O, Sakly F, Drean JY. Study of the “interplant” variability in agave Americana L. fiber properties. Int J Appl Res Tex. 2015 Dec;3(2):1–14. [Google Scholar]
23. Boateng ID. Application of graphical optimization, desirability, and multiple response functions in the extraction of food bioactive compounds. Food Eng Rev. 2023;15:309–28. doi:10.1007/s12393-023-09339-1. [Google Scholar] [CrossRef]
24. Bezerra MA, Ferreira SLC, Novaes CG, dos Santos AMP, Valasques GS, da Mata Cerqueira UMF, et al. Simultaneous optimization of multiple responses and its application in analytical chemistry—a review. Talanta. 2019;194:941–59. [Google Scholar] [PubMed]
25. Derringer G, Suich R. Simultaneous optimization of several response variables. J Qual Technol. 1980;12(4):214–9. [Google Scholar]
26. MSahli S. Etude de potentiel textile des fibres d’agaves Americana L. (Ph.D. Thesis). University of Upper Alsace: Mulhouse, France; 2002 (In French). [Google Scholar]
27. Eyupoglu S, Eyupoglu C, Merdan N. Physico‐chemical characterization of Sambucus ebulus L. plant stem fiber. Biomass Convers Biorefin. 2023. doi:10.1007/s13399-023-04054-7. [Google Scholar] [CrossRef]
28. Imed BM. Caractérisation et modification des fibres d’alfa en vue de leur utilisation en application textile (Ph.D. Thesis). University of Monastir: Monastir, Tunisia; 2010 (In French). [Google Scholar]
29. Majid MS, M.Kamali M. An analysis of structure and properties of a natural cellulosic fiber (Leafiran). Fibers Polym. 2010;11(6):877–82. doi:10.1007/s12221-010-0877-z. [Google Scholar] [CrossRef]
30. Barrera BMM, Salas Ruíz A, Galbis Morales R. Mechanical and physical characterisation of Typha domingensis-based thermal insulation boards for developing areas such as Nigeria. Waste Biomass Valori. 2021;12:5795–806. doi:10.1007/s12649-021-01410-4. [Google Scholar] [CrossRef]
31. Richard N, Saidjo S, Annie W, Pagore D, Martin T, Etienne M. Extraction, applications and characterization of plant fibers. In: Jeon HY, editor. Natural fibers. South Korea: IntechOpen; 2022. p. 1–33. [Google Scholar]
32. Hashim MY, Roslan MN, Amin AM, Zaidi AMA, Ariffin S. Mercerization treatment parameter effect on natural fiber reinforced polymer matrix composite: a brief review. Int J Materi Metallurgi Engi. 2012;6(8):784–90. [Google Scholar]
33. Mushtaq B, Ahmad F, Nawab Y, Ahmad S. Optimization of the novel jute retting process to enhance the fiber quality for textile applications. Heliyon. 2023;9(11):1–14. doi:10.1016/j.heliyon.2023.e21513. [Google Scholar] [PubMed] [CrossRef]
34. Pickering KL, Li Y, Farrell RL, Lay M. Interfacial modification of hemp fibre reinforced composites using fungal and alkali treatment. J Biobased Mater Bio. 2007;1(1):109–17. doi:10.1166/jbmb.2007.1984. [Google Scholar] [CrossRef]
35. Cao Y, Chan F, Chui YH, Xiao H. Characterization of flax fibres modified by alkaline, enzyme, and steam-heat treatments. BioResources. 2012;7(3):4109–21. doi:10.15376/biores.7.3.4109-4121. [Google Scholar] [CrossRef]
36. E. R, Sinha S. Influence of fibre-surface treatment on structural, thermal and mechanical properties of jute. J Mater Sci. 2008;43:2590–601. doi:10.1007/s12034-009-0010-3. [Google Scholar] [CrossRef]
37. Ramaswamy GN, Ruff CG, Boyd CR. Effect of bacterial and chemical retting on kenaf fiber quality. Tex Res J. 1994;64:305–8. doi:10.1177/004051759406400507. [Google Scholar] [CrossRef]
Cite This Article
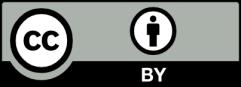
This work is licensed under a Creative Commons Attribution 4.0 International License , which permits unrestricted use, distribution, and reproduction in any medium, provided the original work is properly cited.