Open Access
ARTICLE
Isolation and Characterization of Cellulose Nanofiber (CNF) from Kenaf (Hibiscus cannabinus) Bast through the Chemo-Mechanical Process
1 School of Life Sciences and Technology, Institut Teknologi Bandung, Bandung, 40132, Indonesia
2 Research Center for Biomass and Bioproducts, National Research and Innovation Agency (BRIN), Cibinong, 16911, Indonesia
* Corresponding Authors: Rudi Dungani. Email: ; Widya Fatriasari. Email:
(This article belongs to the Special Issue: Special Issue in Celebration of JRM 10 Years)
Journal of Renewable Materials 2024, 12(6), 1057-1069. https://doi.org/10.32604/jrm.2024.049342
Received 03 January 2024; Accepted 07 March 2024; Issue published 02 August 2024
Abstract
The present work emphasizes the isolation of cellulose nanofiber (CNF) from the kenaf (Hibiscus cannabinus) bast through a chemo-mechanical process. In order to develop high CNF yield with superior properties of CNF for improving compatibility in varied applications this method is proposed. The fiber purification involved pulping and bleaching treatments, whereas mechanical treatment was performed by grinding and high-pressure treatments. The kraft pulping as a delignification method followed by bleaching has successfully removed almost 99% lignin in the fiber with high pulp yield and delignification selectivity. The morphology of the fibers was characterized by scanning electron microscopy, which showed a smooth surface, fiber bundles, gel-shaped nanofiber, and an average size of 94.05 nm with 69% of CNF in 34–100 nm size. The chemo-mechanical process exhibited a more crystalline nature in CNF than pulp kenaf. The low zeta potential values exhibit the distribution of fibrils and colloidal suspension stability without any further agglomeration. A lower concentration of CNF is less stable exhibiting the product agglomeration. Therefore, the chemo-mechanical process for the isolation of CNF (Hibiscus cannabinus) from kenaf involves sustainable, low-cost, non-toxic, and cheap alternatives than other traditional methods.Graphic Abstract
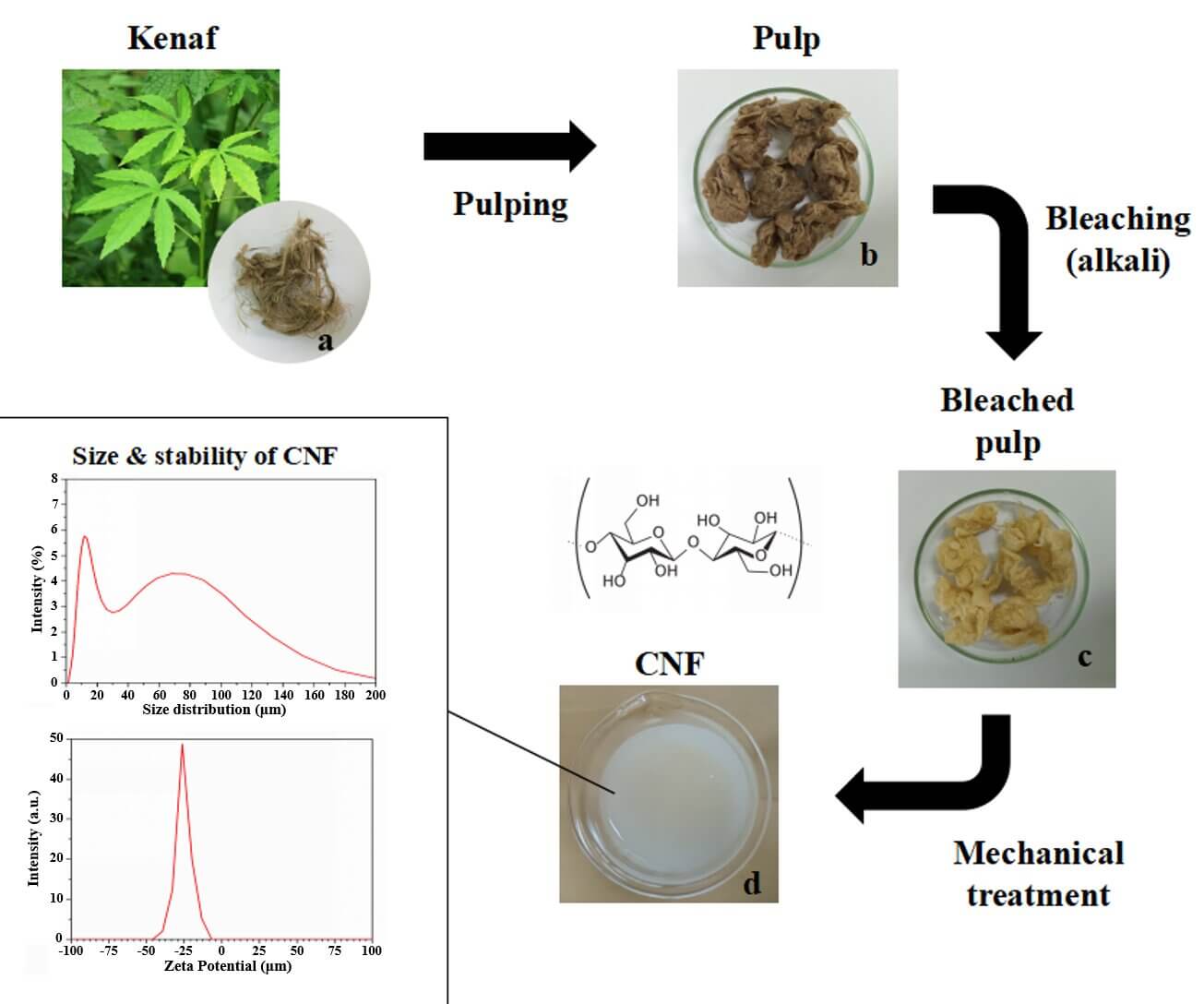
Keywords
Kenaf plant (Malvaceae) is a non-wood lignocellulosic and 1.5–3.5 m tall annual/biennial plant with a stem consisting of two basic parts, i.e., the bast and core. The kenaf fiber is used as a reinforcing agent in the polymer matrixes and production of economic items. The cell wall of lignocellulosic biomass forms an important raw material for the pulp and paper industry consisting of lignin, hemicellulose, cellulose, other extractives, and minor proportions of pectin [1]. It is the most abundant renewable natural resource rich in chemical compounds that can be harnessed to meet the daily needs and demands of the market. Cellulose is a linear homopolysaccharide consisting of unbranched β-(1,4)-D-glucose units connected by β-1-4-linkages [2]. In cellulose, every single monomer unit comprises three hydroxyl groups responsible for cellulose’s bonding and characteristic properties. Different types of methods have been reported to isolate the Cellulose Nano Fiber (CNF) from lignocellulosic materials, which include acid hydrolysis (yellow thatching grass) [3], high-pressure homogenization, ball milling, and grinding [4], catalytic oxidation (e.g., Oryza sativa) [5], ultrasonication [1] and enzymatic technique [6], respectively.
Chemo-mechanical treatment increases the interfacial bonding strength by making the CNF surface available for further modification through hydrogen bonding during the preparation of CNF-based nanocomposites and potential mechanical interlocking between the CNF surface and base matrix of polymer nanocomposite [7]. Further, this paper reports the isolation of CNF from the kenaf bast fiber using chemo-mechanical treatment as the product is obtained in high yield, possesses more crystallinity, purity and is free from non-cellulosic impurities (e.g., lignin, hemicellulose, wax, etc). Instead of depending on synthetic fibers, the natural CNF obtained from kenaf exhibits superior mechanical properties. Chemo-mechanical isolation helps to improve biocompatibility, hydrophilicity, resistance to high shear force, and interaction with surface modifiers for varied applications [8].
To overcome the drawbacks in the pristine polymer materials, the CNF can be used as an efficient reinforcement filler to develop low-cost, hydrophobic, and improved polymeric composite materials with higher thermal stability and lower decomposition behaviour. Heidarian et al. prepared CNF from bagasse by using the modified sulphur-free approach with a high degree of fibrillation, a diameter of 11 nm, and increased crystallinity [9]. Sanchez et al. isolated CNF from different wheat straw pulp using soda and organosolv processes where the organosolv process exhibited higher parameters like surface area, yield, average diameter of 14 nm, and good fibrillation than the soda process [10]. Zhu et al. isolated CNF from Doughlas fir using hot water extraction treatment and ultrasonication with good thermal stability, good fibrillation, and crystallinity [1]. Ravindran et al. prepared CNF from pineapple leaf fibers through the green method using lime juice for acid hydrolysis and ball milling for defibrillation with a size of 50 nm [11]. Syafri et al. prepared ramie CNF through a chemical ultrasonication process and then reinforced cassava starch hybrid composite which exhibited higher tensile strength, moisture absorption, crystallinity index, and thermal stability [12]. Sulaiman et al. prepared CNF from kenaf bast fiber using an ultrasonication technique by decreasing the size of CNF and increasing the cellulose content as potential support for enzyme immobilization [13]. Pengiran et al. investigated the CNF as a potential larvicide nanocarrier and its ecotoxicity against Daphnia magna (planktonic crustacean) and Dania rerio (freshwater fish) where CNF did not cause any mortality, immobilization, or abnormality in any species [14]. Moreover, the CNF has also been isolated from bananas, oil palm trunks [15], cotton stalks [16], Macaranga hypoleuca [17], and Jute bast fiber [18], respectively.
Further, the CNF isolated in the present study reports the isolation of CNF from kenaf bast through chemo-mechanical treatment via kraft delignification, bleaching, and mechanical treatment. To the best of our knowledge, this approach has not been reported previously for producing CNF of kenaf bast fiber with excellent crystallinity, morphology, colloidal dispersibility, and delignification. The nominal value of the zeta potential of isolated CNF is attributed to the bursting of microfibrils to nanofibrils indicating colloidal stability with uniform dispersion. Due to easy availability, cheap, excellent crystalline nature, high mechanical properties, good surface area, environmentally friendly, and low coefficient of thermal expansion, the CNF finds its highest potential in various applications such as electronics, medicine, reinforcement of automobiles, cosmetics, and polymer nanocomposite fields, respectively.
Dried kenaf stem fiber used in this research was procured from National Fiber Council Indonesia (DSN), Banten, Indonesia. Analytical grade Hydrogen peroxide (H2O2, mol. wt. 34.01 g/mol), sodium bromide (NaBr, mol. wt. 150.89 g/mol), sodium chlorite (NaClO2, mol. wt. 90.44 g/mol), hydrochloric acid (HCl, mol. wt. 36.46 g/mol), and ethanol (C2H5OH, mol. wt. 46.06 g/mol) were purchased from Sigma Aldrich (Darmstadt, German). Technical grades of chemicals including sodium hydroxide (NaOH) and sodium sulfide (Na2S) purchased from CV Sarana Global Sejahtera, Bogor, Indonesia were used for kraft pulping of kenaf fibers. For other analyses such as Kappa number, chemicals for titration were directly used without any purifications.
2.2.1 Preparation of Cellulose Fiber from Kenaf Stem
The isolation of CNF from kenaf bast fiber (KBF) from kenaf stem was carried out in two steps, which are discussed under (i) delignification (kraft pulping) and (ii) bleaching as reported in the Indonesian registered patent in 2023 (No. P00202306957). First KBF was cut to a length of 1–2 cm and collected in a tray before soaking it in water thrice and oven dried at 60°C (12 h). After that, the delignification was done using optimized kraft pulping conditions: NaOH (w/v, 22%), Na2S (w/v, 25%), 170°C and kept in a rotary digester for 2 h with liquor to fiber ratio of 20:1. The pulp was cleaned with water to remove the excess chemicals, impurities before starting the next bleaching step. To remove the residual lignin, hydrogen peroxide (w/v, 10%) was used prior to bleaching. Further, the pulp was bleached with MgSO4 (0.039 M), H2O2 (W/V, 35%), and NaOH (30%), maintaining the pH of the slurry at 10.5. The slurry was transferred and kept in a water bath for 120 min at a temperature of 80°C until separate white pulp and cooking liquor were obtained (Indonesian Patent No. P00202306957). The samples were washed until neutral pH, and thereafter, the mechanical treatment was performed on the bleached pulp. After pulping, the pulp yield for evaluating the effectivity of delignification to preserve carbohydrates was determined as follows TAPPI T210 cm-93). Besides that, the Kappa number of kenaf kraft pulp and bleached pulp was then determined by titration technique as reported in TAPPI (TAPPI T236 cm-85).
2.2.2 Preparation of Kenaf Cellulose Nanofiber-CNF
As reported in our registered Indonesian Patent (No. P00202306957), the bleached slurry (10 g) was hydrolyzed in distilled water (w/v, 1%). The slurry was ground using an ultrafine grinder with a double cycle until gel was formed, which is CNF. Further, centrifugation followed by homogenization was carried out on CNF suspension to decrease the fiber’s size. The gel was centrifuged twice at 7000 rpm for 15 min, and the precipitate was collected. The precipitate was re-suspended in distilled water and stirred under strong mechanical intense agitation, and the process was repeated until neutral pH. To obtain the CNF the suspension was further passed through an ultrafine friction grinding machine (super grinder) at 8000 rpm for 4 h with a time gap of 10 min between 4 times.
Various properties of extracted CNF were evaluated by Scanning Electron Microscopy (SEM), FT-IR (Fourier-Transform Infrared Spectroscopy), X-ray diffraction (XRD), Particle Size Analyzer (PSA), Dynamic Light Scattering (DLS) and Zeta potential (ζ-potential). equipped with a capillary cell 1070. The particle size distribution and zeta potential of kenaf CNF suspended in water (0.25% wt.) were determined by laser Doppler electrophoresis technique according to the zeta potential value measured with a zeta sizer instrument (Horiba SZ-100). and Horiba Partica LA-960, respectively.
Scanning Electron Microscopy (SEM) images were taken on a (JSM, IT 200) instrument, and the samples were coated with a thin layer of carbon (around 20 nm) before imaging with micrographs taken at 5 kV. ATR-FTIR (Frontier, Perkin Elmer Inc., Waltham, MA, USA) spectra were used at a resolution of 4 cm−1 with a range of 400–4000 cm−1 wavelengths for functional group identification. XRD analyses were performed using an X-ray diffractometer (Shimadzu, XRD-7000, Japan), using a CuKα radiation source (wavelength (λ) of 0.15406 nm) at 40 kV, 30 mA electrical current with diffractograms of 2θ range 10–60° at a speed of 2°/min). Crystallinity percentage (Xc) was calculated based using the Lorentz fitting curve with Origin Pro 8.5.1 software (Origin Lab Corporation, Northampton, MA, USA). The following Eq. (1):
3.1 Effectivity Delignification and Bleaching of Kenaf Fiber
The isolation of CNF passes through different stages of delignification by kraft pulping and bleaching which was performed through chemo-mechanical treatment. Different parameters like NaOH and Na2S loading, temperature, processing time, and concentration of various solutions are used to influence the fibrillar nature, structure, purity, and morphology. It is a necessary step in the pulping process for the lignin to break down into smaller fragments that could wash out of the fiber [19]. Rich lignin concentration in kraft black liquor is another benefit of effective delignification processes like kraft pulping, which can be utilized to create chemicals and functional materials [20]. Further, the delignified products are mostly lignin involving hydrosulfide (HS) and sulfide ions that are selective to preserve more cellulose than only NaOH (soda pulping). The chemo-mechanical method accelerates delignification by attacking β aryl ether bonds and thus preserving the pulp yield [21,22]. Pulp yield is an important parameter to evaluate the pulping quality. Compared to the previous kraft pulp yield of A. melanoxylon (47%–58.2%) [23] and sorghum bagasse (40%–55%) [24], Agave gigantea (48.3%) [25], Punica granatum (30%–35%) [26] the pulp yield of this study (53.61%) is comparable. The different sources of fiber and pulping conditions might contribute to the variation in pulp yield.
The bleaching process using peracetic acid, and hydrogen peroxide (H2O2) in the bleaching also plays an important role in the removal of residual units and degradation of non-cellulosic segments such as hemicellulose, waxes, chromophores, etc., from the reaction mixture [27]. As a result of an oxidative reaction during the bleaching process, the hydroxyl groups undergo displacement reaction and form soluble derivatives which are leached off during washing. The lignin was mostly removed in the kraft pulping step, while further continued by bleaching but not too much with an extent of about 32.4% (Table 1).
The mechanical treatment by ultrafine grinding makes defibrillation bleached pulp into CNF and is beneficial for utilization in different processes. The effectivity of the lignin-extraction phase of pulping and bleaching was evaluated by the Kappa number that represents lignin content in residual pulp. It closely relates to the pulp’s remaining lignin content. Table 1 shows the kraft pulping and bleaching treatment indicating the removal of lignin and other impurities. It is in agreement with the previous statement that residual lignin is still present after bleaching and other procedures, but excessive lignin removal is needless considering redundant paper bleaching, unnecessary contaminating agent consumption, and preventing pollution to the environment [28]. Up to 99% lignin has been successfully removed from kenaf fiber with a Kappa number below 10 on the unbleached and bleached pulp. Delignification selectivity (DS) can be used to describe the effectivity of the pulping process in which high DS represents higher lignin removal than carbohydrate degradation (cellulose degradation). Preserving cellulose with a low Kappa number value can be achieved by the kraft process, as previously stated [29]. Thus, in this study, kraft pulping was chosen for the delignification of kenaf fiber to produce CNF.
3.2 Functional Group Identification by FTIR
The FTIR spectroscopic technique was used to analyze the chemical compounds in the kenaf, unbleached pulp, bleached pulp, and CNF in the crystalline phase (Fig. 1). The absorption peaks at 1735, 1633, and 1242 cm−1 indicate the presence of hemicellulose and lignin were absent in the chemo-mechanically treated fibers, whereas the presence of peaks at 1327 cm−1 indicates the presence of lignin [30]. The characteristic peaks at 3330 cm−1 correspond to OH vibrations, 2900 cm−1 to aliphatic saturated C-H unit. The peaks at 1620–1595 cm−1 arise due to the lignin’s aromatic ring, and the peak at 1250 cm−1 is due to the C-O stretching of the ether linkage. The peaks from 1055–1032 cm−1 appear due to C-O (C2, C3, C6) and the peak for anomeric carbon (C1) at 900 cm−1 and C-O-C at 1158 cm−1, respectively [31]. Moreover, the absorption peak at 1035 cm−1 is attributed to stretching -OH and -CH groups, whereas the peak at 828 cm−1 is assigned to the presence of β-glycosidic bond [30,32]. Based on FTIR, the non-cellulosic parts were effectively removed during the chemical-mechanical treatment.
Figure 1: FTIR spectra of kenaf, unbleached pulp, bleached pulp, and CNF
3.3 The Crystallinity Analysis by XRD
The crystalline behavior of CNF was measured by XRD analysis. Fig. 2 illustrates the X-ray diffractogram of unbleached, bleached pulp, and CNF from kenaf. The isolated cellulose contains both crystalline and amorphous segments due to the presence of glycosidic units. This indicates the presence of H-bonding in the crystalline unit and its absence in the amorphous unit [7]. From the XRD results, the peaks at around 2θ = 16° and 22.7° are attributed to the typical pristine cellulose crystalline structure [33], suggesting that the crystal integrity was maintained during chemo-mechanical treatment.
Figure 2: X-ray diffractograms of unbleached pulp, bleached pulp, and CNF
The crystallinity of CNF was determined at every stage of chemo-mechanical treatment. The observation affected crystallinity at each process, with the highest percentage observed at the final process (59%). During the dissolution at each stage, the amorphousness decreases with the increase in crystallinity and removal of non-cellulosic components (lignin, hemicellulose) and other impurities [34]. The crystallinity values for unbleached, bleached pulp, and CNF were 56.1%, 58.34%, and 59.32%, respectively. Thus, pure CNF is isolated with higher crystalline units, which will be used for diversified applications, respectively.
3.4 Morphological Analysis by SEM
To better understand the morphology of the kenaf, unbleached, bleached pulp and cellulose nanofiber, SEM images (Figs. 3a `–3d `) were taken at different magnifications in Fig. 3, for interfacial bonding, polymer composite treatment involving a chemical process helps the uneven surface of the pristine fiber to be actively assisted for higher molecular interaction. The soda pulping and alkaline peroxide bleaching chemical treatment on the pristine fiber removes the coverings from the fiber, like lignin, hemicellulose, wax, etc. [35,36].
Figure 3: SEM micrograph of (a `) raw kenaf (b `) kraft pulping-treated (c `) bleached (d `) CNF
The chemical treatment makes the fibers smooth and removes the impurities besides separating the fiber bundles, with an excellent aspect ratio. After the alkaline treatment, the fiber bundles open (defibrillation) with a low diameter which can be chemically tuned for strong interactions and cross-linking at the interface. However, the alkaline treatment with varying NaOH concentrations, acid-to-fiber ratio, and immersion times affects the fiber’s morphology (Fig. 3d `), fiber texture, size, fibrillar tension, and surface roughness [37]. As a result, 5% alkali solution (3 h) and 17.5:1 acid to fiber ratio (2 h) are the optimum conditions for kenaf fiber treatment (Fig. 3c `) compared to higher concentrations, for obtaining crystalline CNF, respectively.
Dynamic Light Scattering (DLS) was used to determine the particle size of kenaf CNF. This method measures the average hydrodynamic particle size, which indicates how the CNF particle diffuses in a fluid. CNF particles suspended in a fluid are in constant Brownian motion with a size in the nanometer range [36,38]. This motion is the result of interaction with the molecules of the suspending fluid of known temperature and viscosity [39]. The success of the chemo-mechanical method of making CNF was evaluated by characterizing the morphology and size of the nanofiber prepared from the kenaf bast substrate using particle size analysis. This method succeeded in producing smaller nano-size CNF which were compared to kraft pulp and bleached pulp (11839.54 and 7867.19 nm) (Table 2). Based on the morphological characterization of CNF in the form of gel-shaped nanofibers with an average size of 94.05 nm which is dominated by 34–100 nm size as much as 69% and ≥100 nm size as much as 31% of CNF, this method is proven to produce CNF from kenaf bast fiber which has a higher percentage of nano-size.
However different evaluation with PSA, Fig. 4 shows that the majority of the particle sizes were in the range of 1 to 200 μm with the mean size distribution at 35.15 μm. The CNF structures are still in the micrometer range. According to Sofla et al. [40], some particles are still in the micrometer range or longer fibers due to breakage and growth of a fibrous layer on the grinding media that decreased the effectiveness of the impact force of the media on the particles. In order to make kenaf CNF into nano size, the process of grinding may take a longer period of time. Improving the mechanical treatment in the experiment will lead to the breakdown of weaker interactions between the crystalline region and the amorphous region of CNFs, forming CNFs with smaller sizes [41].
Figure 4: Particle size distribution of kenaf cellulose nanofibril
3.6 Zeta Potential (ζ-potential)
Zeta potential evaluates the stability and dispersion of fibers/extracted solids in an aqueous solution. Zeta potential (estimated as surface charge) can be measured by tracking the rising rate of negatively or positively charged particles across an electric field [42]. Fig. 5 shows a negative zeta potential value of kenaf CNF which was −25.3 mV. This is a clear indicator of the negative electrostatic repulsion achieved by the presence of carboxylic groups on the CNF surface [43]. The force of repulsion between the individual fibers leads to a uniform and stable dispersion in aqueous media. The carboxylic group is present due to the oxidation of cellulose [44].
Figure 5: Zeta potential of kenaf-based CNF
Based on the result of zeta potential analysis, the particle stability behavior of kenaf CNF was considered incipient instability with heterogenicity of particle size distribution. Hence, kenaf CNF is anticipated to agglomerate over time due to interparticle interaction such as van der Waals and hydrophilic interaction [14,45].
3.7 CNF Condition during Storage
A thorough evaluation of the kenaf CNF shelf life was carried out following a 40-day storage period. Kenaf CNFs were diluted in 3 different concentrations: 1%, 5%, and 10%. From Table 3, we can see that all CNF dispersions started to settle from day 1, and for each concentration completely settled on day 1 for 1% (v/v), day 10 for 5% (v/v), and day 40 for 10% (v/v). Cellulose nanofibrils settle to a certain degree, as shown by distinct turbidity variations along the cell height [46]. This indicates that CNFs with lower concentrations tend to be more prone to agglomeration.
The stability behavior of kenaf CNFs in this experiment was also seen as less stable. There are several factors that affect the stability of kenaf CNF. The first factor is likely due to the CNF being slightly coarser and having a broad size distribution. The mechanical disintegration of the pulp fiber fibrils is much less intense, resulting in a lower viscosity and a wider size distribution of the fibrils formed, which affects the overall colloidal stability. The second factor is influenced by the total charge of the CNF, evaluated by zeta potential measurement, which is −25.3 mV (Fig. 5), regardless of the pH or ionic strength [47,48]. These values indicate that the electrostatic contribution to the stability is low, and relatively small changes will interfere with the stability in the absence of other stabilizing mechanisms [49].
The isolation of CNF from kenaf using chemo-mechanical treatment was carried out successfully. The kraft pulping following bleaching treatment has been successful in removing lignin with preserving carbohydrates, as indicated by low Kappa number and high pulp yield of kraft pulping by 53.61%, including effective kraft pulping of biomass of 45%–55%. The majority of lignin removal is in the pulping process while the bleaching step only reduces the lignin content of unbleached pulp by 31%. Based on morphological observation, the CNF is a gel-shaped nanofiber with an average size of 94.05 nm and a yield of 69%. The characteristics of CNF indicate that CNF has a higher crystallinity degree with strong interfacial interactions after treatment. However, the zeta potential values indicate that the electrostatic contribution of CNF to stability is low, which can be overcome during organo-polymeric reactions. Evaluation of the stability behavior of CNF in various concentrations by storage time indicates that lower concentration tends to be more agglomerated and less stable. The chemo-mechanical process of isolation suggests that the CNF has a prospect as a reinforced material for polymer nanocomposites.
Acknowledgement: The authors are grateful for the Post-Doctoral Program of the National Research and Innovation Agency-BRIN (Grant Number: 86/II/HK/2023) for Dr. Mohammad Irfan Bakhsi. The authors also would like to thank the scientific and technical support provided by the Integrated Laboratory of Bioproducts (iLaB) BRIN through E-Layanan Sains BRIN, Indonesia.
Funding Statement: We also thank the Ministry of Education, Culture, Research and Technology (KEMENDIKBUDRISTEK), Republic of Indonesia, for providing the Research Grant “Basic Research Scheme” No. 110/E5/PG.02.00.PL/2023.
Author Contributions: Study conception and design: Rudi Dungani, Widya Fatriasari. Data collection: Tsabita Zahra Hanifa, Widya Fatriasari. Analysis and interpretation of results: Tsabita Zahra Hanifa, Rudi Dungani, Widya Fatriasari, Muhammad Irfan Bakhsi. Draft manuscript preparation: Mohammad Irfan Bakhsi, Tsabita Zahra Hanifa, Firda A. Syamani, Mustika Dewi, Melbi Mahardika, Widya Fatriasari, Rudi Dungani. Writing—review, and editing: Rudi Dungani, Widya Fatriasari, Mohammad Irfan Bakshi. Supervision: Rudi Dungani, Widya Fatriasari. All authors have read, critically reviewed the draft, edited, and finalized the manuscript with amendments and corrections, and agreed to the published version of the manuscript.
Availability of Data and Materials: Data will be made available on request.
Conflicts of Interest: The authors declare that they have no conflicts of interest to report regarding the present study.
References
1. Zhu R, Yadama V. Isolation and characterization of cellulose micro/nanofibrils from Douglas Fir. J Polym Environ. 2018;26(3):1012–23. doi:10.1007/s10924-017-1013-6. [Google Scholar] [CrossRef]
2. Wulandari WT, Rochliadi A, Arcana IM. Nanocellulose prepared by acid hydrolysis of isolated cellulose from sugarcane bagasse. IOP Conf Series: Mater Sci Eng. 2016;107(1):012045. doi:10.1088/1757-899X/107/1/012045. [Google Scholar] [CrossRef]
3. Ndwandwa N, Ayaa F, Iwarere SA, Daramola MO, Kirabira JB. Extraction and characterization of cellulose nanofibers from yellow thatching grass (Hyparrhenia filipendula) straws via acid hydrolysis. Waste Biomass Valor. 2023;14(8):2599–608. doi:10.21203/rs.3.rs-1819436/v1. [Google Scholar] [CrossRef]
4. Zeng J, Hu F, Cheng Z, Wang B, Chen K. Isolation and rheological characterization of cellulose nanofibrils (CNFs) produced by microfluidic homogenization, ball-milling, grinding and refining. Cellulose. 2021;28(6):3389–408. doi:10.1007/s10570-021-03702-3. [Google Scholar] [CrossRef]
5. Madivoli ES, Kareru PG, Gachanja AN, Mugo SM, Sujee DM, Fromm KM. Isolation of Cellulose nanofibers from oryza sativa residues via TEMPO mediated oxidation. J Nat Fibers. 2022;19(4):1310–22. doi:10.1080/15440478.2020.1764454. [Google Scholar] [CrossRef]
6. Wang J, Song Y, Cui F, Wu W, Zhu H, Li X, et al. Preparation and characterization of nanocellulose fiber (CNF) by biological enzymatic method. J Thermoplast Compos Mater. 2023;37(3):1223–41. doi:10.1177/089270572311804. [Google Scholar] [CrossRef]
7. Chavez BK, Garces-Porras K, Parada DC, Flores E. Thermochemical isolation and characterization of nanofibrillated cellulose from Stipa obtusa fibers. Carbohydr Polym Technol Appl. 2023;6:100344. doi:10.1016/j.carpta.2023.100344. [Google Scholar] [CrossRef]
8. Jamaluddin N, Kanno T, Asoh T-A, Uyama H. Surface modification of cellulose nanofiber using acid anhydride for poly(lactic acid) reinforcement. Mater Today Commun. 2019;21:100587. doi:10.1016/j.mtcomm.2019.100587. [Google Scholar] [CrossRef]
9. Heidarian P, Behzad T, Karimi K. Isolation and characterization of bagasse cellulose nanofibrils by optimized sulfur-free chemical delignification. Wood Sci Technol. 2016;50(5):1071–88. doi:10.1007/s00226-016-0820-6. [Google Scholar] [CrossRef]
10. Sánchez R, Espinosa E, Domínguez-Robles J, Loaiza JM, Rodríguez A. Isolation and characterization of lignocellulose nanofibers from different wheat straw pulps. Int J Biol Macromol. 2016;92:1025–33. doi:10.1016/j.ijbiomac.2016.08.019. [Google Scholar] [PubMed] [CrossRef]
11. Ravindran L, Sreekala MS, Thomas S. Novel processing parameters for the extraction of cellulose nanofibres (CNF) from environmentally benign pineapple leaf fibres (PALFstructure-property relationships. Int J Biol Macromol. 2019;131:858–70. doi:10.1016/j.ijbiomac.2019.03.134. [Google Scholar] [PubMed] [CrossRef]
12. Syafri E, Kasim A, Abral H, Sudirman, Sulungbudi GT, Sanjay MR. Synthesis and characterization of cellulose nanofibers (CNF) ramie reinforced cassava starch hybrid composites. Int J Biol Macromol. 2018;120:578–86. doi:10.1016/j.ijbiomac.2018.08.134. [Google Scholar] [PubMed] [CrossRef]
13. Sulaiman S, Mokhtar M, Naim MN, Baharuddin A, Salleh A, Sulaiman A. Study on the preparation of cellulose nanofibre (CNF) from kenaf bast fibre for enzyme immobilization application. Sains Malays. 2015;44:1541–50. [Google Scholar]
14. Pengiran H, Kamaldin J, Fen LB, Yusob SAA. Properties of kenaf cellulose nanofiber (CNF) as potential larvicide nanocarrier and its acute ecotoxicity against Daphnia Magna and Dania rerio. J Nat Fibers. 2022;19(13):6756–69. doi:10.1080/15440478.2021.1932673. [Google Scholar] [CrossRef]
15. Abdul Razab MKA, Mohd Ghani RS, Mohd Zin FA, Nik Yusoff NAA, Mohamed Noor AA. Isolation and characterization of cellulose nanofibrils from banana pseudostem, oil palm trunk, and kenaf bast fibers using chemicals and high-intensity ultrasonication. J Nat Fibers. 2022;19(13):5537–50. doi:10.1080/15440478.2021.1881021. [Google Scholar] [CrossRef]
16. Soni B, Hassan EB, Mahmoud B. Chemical isolation and characterization of different cellulose nanofibers from cotton stalks. Carbohydr Polym. 2015;134:581–9. doi:10.1016/j.carbpol.2015.08.031. [Google Scholar] [PubMed] [CrossRef]
17. Sutrisno E, Tanpichai S, Chuangchote S. Isolation and characterization of cellulose nanofibers (CNFs) from Macaranga hypoleuca. IOP Conf Series: Earth Environ Sci. 2020;415(1):012003. doi:10.1088/1755-1315/415/1/012003. [Google Scholar] [CrossRef]
18. Dhali K, Daver F, Cass P, Adhikari B. Isolation and characterization of cellulose nanomaterials from jute bast fibers. J Environ Chem Eng. 2021;9(6):106447. doi:10.1016/j.jece.2021.106447. [Google Scholar] [CrossRef]
19. Holtzapple MT. Hemicelluloses. In: Caballero B, editor. Encyclopedia of food sciences and nutrition. 2nd edOxford: Academic Press; 2003. p. 3060–71. [Google Scholar]
20. Sipponen MH, Farooq M, Koivisto J, Pellis A, Seitsonen J, Österberg M. Spatially confined lignin nanospheres for biocatalytic ester synthesis in aqueous media. Nat Commun. 2018;9(1):2300. doi:10.1038/s41467-018-04715-6. [Google Scholar] [PubMed] [CrossRef]
21. Fengel D, Wegener G,editors. Wood: chemistry, ultrastructure, reactions. Berlin and New York: Walter de Gruyter; 1983. doi:10.1515/9783110839654. [Google Scholar] [CrossRef]
22. Sjöström Eeditor. Wood chemistry: fundamentals and applications. San Diego, New York, Boston, London, Sydney, Tokyo, Toronto: Academic Press, Inc.; 1981. [Google Scholar]
23. Santos A, Anjos O, Amaral ME, Gil N, Pereira H, Simões R. Influence on pulping yield and pulp properties of wood density of Acacia melanoxylon. J Wood Sci. 2012;58(6):479–86. doi:10.1007/s10086-012-1286-2. [Google Scholar] [CrossRef]
24. Fatriasari W, Supriyanto S, Iswanto AH. The kraft pulp and paper properties of sweet sorghum bagasse (Sorghum bicolor L Moench). J Eng Technol Sci. 2015;47:149–59. doi:10.5614/j.eng.technol.sci.2015.47.2.4. [Google Scholar] [CrossRef]
25. Syafri E, Jamaluddin, Sari NH, Mahardika M, Amanda P, Ilyas RA. Isolation and characterization of cellulose nanofibers from Agave gigantea by chemical-mechanical treatment. Int J Biol Macromol. 2022;200:25–33. doi:10.1016/j.ijbiomac.2021.12.111. [Google Scholar] [PubMed] [CrossRef]
26. Siddiqui VU, Almehjani TM, Sapuan SM, Jamal T, Ilyas RA, Eldin SM, et al. Isolation and characterization of cellulose from pomegranate (Punica granatum) peel. J Nat Fibers. 2024;21(1):2299943. doi:10.1080/15440478.2023.2299943. [Google Scholar] [CrossRef]
27. Gedik G, Avinc O. Bleaching of hemp (Cannabis Sativa L.) fibers with peracetic acid for textiles industry purposes. Fibers Polym. 2018;19(1):82–93. doi:10.1007/s12221-018-7165-0. [Google Scholar] [CrossRef]
28. Gao W, Zhou L, Guan Y, Gao H, Liu S. Monitoring the kappa number of bleached pulps based on FT-Raman spectroscopy. Cellulose. 2022;29(2):1069–80. doi:10.1007/s10570-021-04333-4. [Google Scholar] [CrossRef]
29. Karimah A, Solihat NN, Hastuti N, Ismayati M, Ermawar RA, Sohail A, et al. The effect of active alkali and sulfidity loading on the kraft pulp properties of sweet sorghum bagasse. Sugar Tech. 2023;25(5):1196–210. doi:10.1007/s12355-023-01291-y. [Google Scholar] [CrossRef]
30. Supian MAF, Amin KNM, Jamari SS, Mohamad S. Production of cellulose nanofiber (CNF) from empty fruit bunch (EFB) via mechanical method. J Environ Chem Eng. 2020;8(1):103024. doi:10.1016/j.jece.2019.103024. [Google Scholar] [CrossRef]
31. Gapsari F, Putri TM, Rukmana W, Juliano H, Sulaiman AM, Dewi FGU, et al. Isolation and characterization of Muntingia calabura cellulose nanofibers. J Nat Fibers. 2023;20(1):2156018. doi:10.1080/15440478.2022.2156018. [Google Scholar] [CrossRef]
32. Espinosa E, Sánchez R, Otero R, Domínguez-Robles J, Rodríguez A. A comparative study of the suitability of different cereal straws for lignocellulose nanofibers isolation. Int J Biol Macromol. 2017;103:990–9. doi:10.1016/j.ijbiomac.2017.05.156. [Google Scholar] [PubMed] [CrossRef]
33. Kim HJ, Roy S, Rhim JW. Effects of various types of cellulose nanofibers on the physical properties of the CNF-based films. J Environ Chem Eng. 2021;9:106043. doi:10.1016/j.jece.2021.106043. [Google Scholar] [CrossRef]
34. He W, Tian J, Li J, Jin H, Li Y. Characterization and properties of cellulose nanofiber/polyaniline film composites synthesized through in situ polymerization. BioResources. 2016;11(4):118535–47. doi:10.15376/biores.11.4.8535-8547. [Google Scholar] [CrossRef]
35. Malucelli L, Matos M, Jordao C, Lomonaco D, Lacerda L, Carvalho MA, et al. Influence of cellulose chemical pretreatment on energy consumption and viscosity of produced cellulose nanofibers (CNF) and mechanical properties of nanopaper. Cellulose. 2019;26:1667–81. doi:10.1007/s10570-018-2161-0. [Google Scholar] [CrossRef]
36. Onyianta AJ, Dorris M, Williams RL. Aqueous morpholine pre-treatment in cellulose nanofibril (CNF) production: comparison with carboxymethylation and TEMPO oxidisation pre-treatment methods. Cellulose. 2018;25(2):1047–64. doi:10.1007/s10570-017-1631-0. [Google Scholar] [CrossRef]
37. Uetani K, Yano H. Nanofibrillation of wood pulp using a high-speed blender. Biomacromolecules. 2011;12:348–53. doi:10.1021/bm101103p. [Google Scholar] [PubMed] [CrossRef]
38. Gamelas J, Pedrosa J, Lourenço A, Mutjé P, González I, Chinga Carrasco G, et al. On the morphology of cellulose nanofibrils obtained by TEMPO-mediated oxidation and mechanical treatment. Micron. 2015;72:28–33. doi:10.1016/j.micron.2015.02.003. [Google Scholar] [PubMed] [CrossRef]
39. Tarrés Q, Aguado R, Zoppe JO, Mutjé P, Fiol N, Delgado-Aguilar M. Dynamic light scattering plus scanning electron microscopy: usefulness and limitations of a simplified estimation of nanocellulose dimensions. Nanomater. 2022;12(23):4288. doi:10.3390/nano12234288. [Google Scholar] [PubMed] [CrossRef]
40. Sofla MRK, Brown RJ, Tsuzuki T, Rainey TJ. A comparison of cellulose nanocrystals and cellulose nanofibres extracted from bagasse using acid and ball milling methods. ANSN. 2016;7(3):035004. doi:10.1088/2043-6262/7/3/035004. [Google Scholar] [CrossRef]
41. Amanda P, Nabila S, Qonita N, Ningrum RS, Ismadi, Masruchin N. The properties of OPEFB cellulose nanofibrils produced by a different mode of ultrafine grinding. IOP Conf. Series: Earth Environ Sci. 2021;891(1):012016. doi:10.1088/1755-1315/891/1/012016. [Google Scholar] [CrossRef]
42. Radakisnin R, Abdul Majid MS, Jamir MRM, Jawaid M, Sultan MTH, Mat Tahir MF. Structural, morphological and thermal properties of cellulose nanofibers from napier fiber (Pennisetum purpureum). Materials. 2020;13(18):4125. doi:10.3390/ma13184125. [Google Scholar] [PubMed] [CrossRef]
43. Sato Y, Kusaka Y, Kobayashi M. Charging and aggregation behavior of cellulose nanofibers in aqueous solution. Langmuir. 2017;33(44):12660–9. doi:10.1021/acs.langmuir.7b02742. [Google Scholar] [PubMed] [CrossRef]
44. Forti ES, El Awad Azrak SM, Ng XY, Cho W, Schueneman GT, Moon RJ, et al. Mechanical enhancement of cellulose nanofibril (CNF) films through the addition of water-soluble polymers. Cellulose. 2021;28(10):6449–65. doi:10.21203/rs.3.rs-162652/v1. [Google Scholar] [CrossRef]
45. Atiqah MSN, Gopakumar DA, F. ATO, Pottathara YB, Rizal S, Aprilia NAS, et al. Extraction of cellulose nanofibers via eco-friendly supercritical carbon dioxide treatment followed by mild acid hydrolysis and the fabrication of cellulose nanopapers. Polymers. 2019;11(11):1813. doi:10.3390/polym11111813. [Google Scholar] [PubMed] [CrossRef]
46. Palacios Hinestroza H, Hernández J, Diaz H, Esquivel M, Toriz G, Rojas O, et al. Isolation and characterization of nanofibrillar cellulose from Agave tequilana weber bagasse. Adv Mater Sci Eng. 2019;7:1–7. doi:10.1155/2019/1342547. [Google Scholar] [CrossRef]
47. Chen C, Li P, Wang T, Wang S, Zhang M. S-Doped carbon fibers uniformly embedded with ultrasmall TiO2 for Na+/Li+ storage with high capacity and long-time stability. Small. 2019;15:1902201. doi:10.1002/smll.201902201. [Google Scholar] [PubMed] [CrossRef]
48. Aaen R, Brodin FW, Simon S, Heggset EB, Syverud K. Oil-in-water emulsions stabilized by cellulose nanofibrils–the effects of ionic strength and pH. Nanomaterials. 2019;9(2):259. doi:10.3390/nano9020259. [Google Scholar] [PubMed] [CrossRef]
49. Tenhunen TM, Pöhler T, Kokko A, Orelma H, Schenker M, Gane P, et al. Enhancing the stability of aqueous dispersions and foams comprising cellulose nanofibrils (CNF) with CaCO3 particles. Nanomater. 2018;8(9):651. doi:10.3390/nano8090651. [Google Scholar] [PubMed] [CrossRef]
Cite This Article
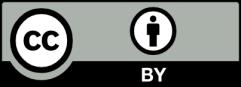
This work is licensed under a Creative Commons Attribution 4.0 International License , which permits unrestricted use, distribution, and reproduction in any medium, provided the original work is properly cited.