Open Access
ARTICLE
Abaca Fiber as a Potential Reinforcer for Acoustic Absorption Material at Middle-High Frequencies
Department of Physics, Faculty of Science and Data Analytics, Institut Teknologi Sepuluh Nopember, Surabaya, 60111, Indonesia
* Corresponding Authors: Susilo Indrawati. Email: ; Darminto. Email:
(This article belongs to the Special Issue: Special Issue in Celebration of JRM 10 Years)
Journal of Renewable Materials 2024, 12(5), 909-921. https://doi.org/10.32604/jrm.2024.048452
Received 08 December 2023; Accepted 14 March 2024; Issue published 17 July 2024
Abstract
Recently, abaca fibers have become the focus of specialized research due to their intriguing characteristics, with their outstanding mechanical properties being a particularly notable. In the conducted study, the abaca fibers underwent a preliminary treatment process involving an alkaline solution, which was composed of 0.5% sodium hydroxide (NaOH) and 50% acetic acid (CHCOOH). This process entailed immersing each fiber in the solution for a period of one hour. This treatment led to a 52.36% reduction in lignin content compared to the levels before treatment, resulting in a dramatic decrease in the full width at half maximum (FWHM) in the XRD spectra from 1.13 to 0.13. This change indicates that the fibers became more crystalline following the treatment. The abaca fibers were also characterized using BET (Brunauer Emmett Teller) measurements, which revealed that the average pore length ranged from 33–49 nm and the surface area was between 13–28 m·g. The morphology of the abaca fiber after alkali an hydrolisis treatment (AFAH) appeared rougher and more uniform. DMA measurements revealed a significant rise in the storage modulus of the single fiber post-treatment, with dependencies on both frequency and temperature. AFAH exhibited an optimal absorption coefficient of α = 0.9 for frequencies above 2500 Hz. The combined effect of alkalization and hydrolyzation treatments, while resulting in an enhancement in the mechanical properties of the fibers, also reduced high-intensity noise produced by sources such as machinery, aircraft takeoffs and landings, etc., across a broader working frequency range.Graphic Abstract
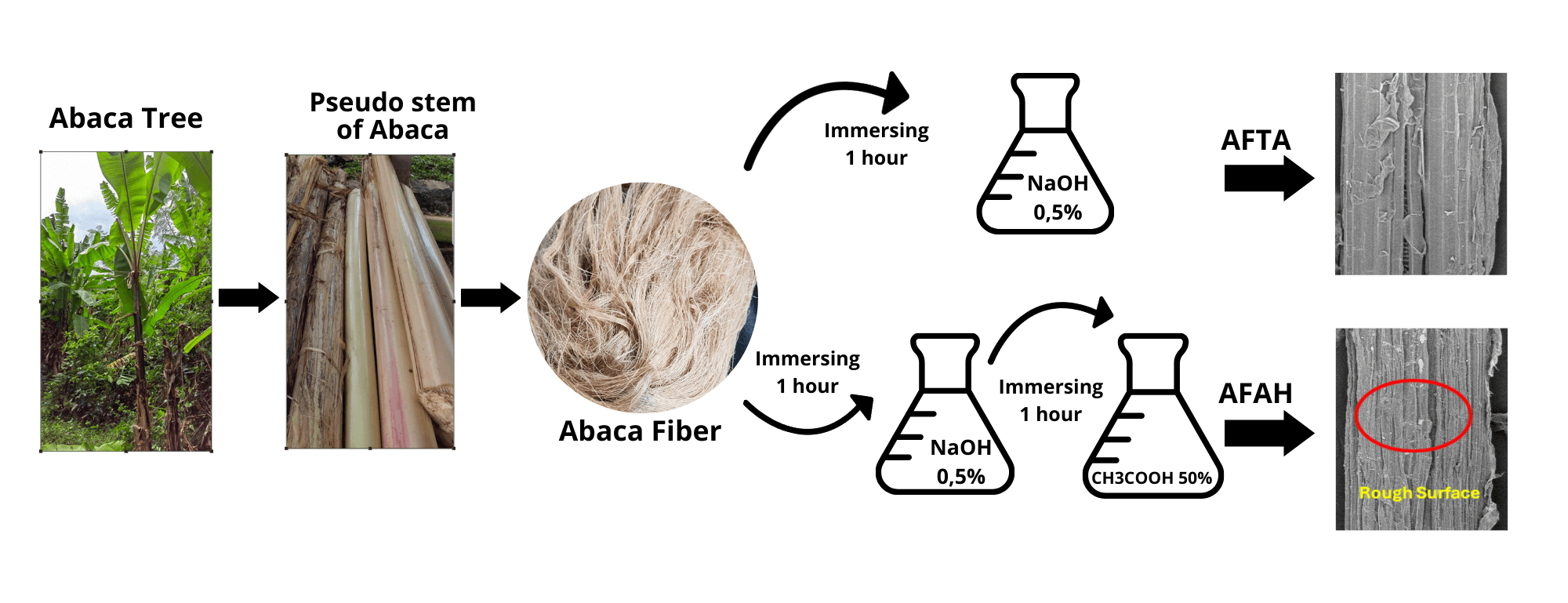
Keywords
High and intense noise can have a detrimental impact on both the environment and people’s quality of life, and it must therefore be controlled [1–3]. Absorbers, which are porous materials, can control noise and reduce echoes in indoor spaces. This capability arises from their ability to absorb sound energy waves and convert them into heat energy [4,5]. Absorbers are typically made from natural minerals and synthetic fibers, such as rockwool, glass wool, and foam materials. The Agency for Toxic Substances and Disease Registry reported that exposure to rockwool and synthetic materials can cause acute irritation to the skin, eyes, and respiratory tract and studies on the long-term negative effects of rockwool are still being conducted frequently [6–8]. The eco-friendliness and effectiveness in the sustainability of natural fibers contribute to their preference for high-quality and environmentally conscious sound absorption. There is a broad range of research focused on the use of natural fibers as sound absorbing materials. For instance, coir fiber has an absorption coefficient (α) of 0.84 at 500 Hz [9]; sugarcane bagasse has an α of 0.75 at frequencies ranging from 500 to 4000 Hz [10]; banana pseudostem fiber has an α of 0.89 at 6300 Hz [11]; areca nut leaf has a Noise Reduction Coefficient (NRC) of 0.74 [12]; kapok and coir fiber [13]; nettle fibers have an NRC of up to 0.72 [14]. Unfortunately, these natural fibers lack mechanical properties. Abaca fiber, which has high mechanical properties [15–18], is one example of a natural fiber. Research on abaca fiber as an application in acoustics is a relatively new field of interest, exploring this natural fiber as a sustainable and environmentally friendly alternative for acoustic materials.
Abaca (Musa Textilis Nee) is a unique natural fiber produced from the stem of the plant, as shown in Fig. 1. This plant is exclusively grown in tropical areas, like the Philippines. This plant is exclusively grown in tropical areas, like the Philippines, Ecuador in South America, and some Southeast Asian countries like Indonesia [19]. According to the Food and Agriculture Organization of the United Nations (FAO, 2018) [20], the Philippines leads abaca production with 60%, followed by Ecuador with 35%, while Costa Rica and Indonesia each supply 1%, contributing about 570–600 tons annually. Research on abaca is currently evolving. The chemical components of abaca fiber include cellulose (56%–66%), hemicellulose (20%–25%), and lignin (7%–13%) [21,22]. The mechanical properties of abaca fibers are impressive, featuring a tensile strength of 400–980 MPa, an elasticity modulus of 6.2–20 GPa, and an elongation of 1%–10% [22–25]. Cellulose, a natural organic polymer, exhibits the most crystalline structure among these components, which leads to the enhanced mechanical characteristics of abaca fibers [21,22,26].
Figure 1: Manufacture of abaca fiber (a) Abaca tree (b) Stem and (c) Abaca fiber
The enhancement of the mechanical properties of natural fibers through alkali processing [26–30] has been conducted on abaca fibers. Alkali treatment assists not only in removing impurities from the fibers but also in reducing the content of lignin and hemicellulose [25,31–34]. The decrease in lignin and an increase in cellulose can enhance tensile strength, Young’s modulus, and flexural strength [28,33]. By eliminating oil, wax, and other contaminants, the surface of the fibers undergoes a transformation to a rougher and more uniform [29,32], which increases surface roughness and facilitates the formation of physical interlocking between the fibers and the matrix. This process enhances the mechanical strength of the composite [35–38]. It substantially enhances the compatibility of the fibers with the polymer matrix in the composite, making them more effective for use in a wide range of applications, from technical textiles to automotive and construction components. Proper treatment of abaca fibers results in good fiber strength and flexibility, allowing and the material to be used for bulletproof vests alongside Kevlar [39–42]. Based on previous research, Abaca fibers are natural fibers with high mechanical properties that serve as reinforcements in composite materials. This highlights the interest in conducting further research on the application of treatments and the composition of composite materials to maximize the performance of abaca fibers.
The purpose of this paper is to further explore further the additional uses of abaca fibers. The abaca fibers to be characterized will undergo preliminary treatment, involving alkali addition and acid hydrolysis, specifically using 0.5% wt NaOH and 50% CH3COOH, in reference to prior research [15]. This study will report on the characterization of both treated an untreated abaca fibers, encompassing their morphology, structure, physical and chemical properties, surface area analysis, and mechanical characteristics. Furthermore, this research will assess the acoustic properties of abaca fibers, an aspect that is particularly innovative, as research on the acoustic properties of abaca fibers is rare and has not been extensively explored. The acoustic properties will be evaluated in accordance with ASTM E1050-12 and ISO 10534-2 standards using an impedance tube to determine their sound absorption capabilities. Hopefully, abaca fibers can be viably applied as sound absorbers according to its high mechanical properties.
2 Materials and Characterization Methods
The abaca fibers utilized in this research originated from Medan, Indonesia. The process of producing market-ready abaca fibers is depicted in Fig. 1c. The initial step in processing abaca fibers involved drying them in an oven at temperatures ranging from 100°C–150°C for 0.5–1 h to reduce moisture content. The next step was the application of a 0.5% NaOH alkali treatment, immersing the fibers for one hour [31], followed by thorough washing with running water. The final step involved a 50% CH3COOH hydrolysis treatment for 1 h [32,43], as depicted in Fig. 2, after which the fibers were again washed clean with running water. Both treatments aimed to reduce the lignin content with the objective of improving the mechanical properties of the abaca fibers. The stages of the alkalization and hydrolyzation process are shown in Fig. 2.
Figure 2: Alkalization and hydrolyzation process
Each fiber was then dried in an oven at temperatures ranging from 100°C–150°C for 1–2 h until no further shrinkage occurred. To simplify sample identification, we categorized the fibers into three types: untreated abaca fiber (AFUT), alkali-treated (AFTA) and alkali and hydrolysis-treated (AFAH) fibers. Each type of fiber was then stored in an airtight container with silica gel to prevent environmental effects. Subsequently, these fibers were further characterized as described in Section 2.2.
The XRD (Philips XPERT-PRO) was utilized to characterize fibers (AFUT, AFTA, and AFAH) using Cu-Kα specifications (40 kV and 30 mA) in the 2θ between 10° to 30°. The gravimetric method was utilized to measure the content of lignin, cellulose, and hemicellulose components in each fiber. A densimeter (BK-DME300D) was used to obtain the fiber density value. The specific surface area and pore size distribution of the fiber were examined using BET (Brunaur, Emmett, and Teller) analysis, while the SEM (Scanning Electron Microscope) of the Phenom Pro X was used to identify the geometry and dimensions of the fibers. Furthermore, the DMA (Dynamic Mechanical Analyzer) was implemented for the assessment of mechanical characteristics, including the storage modulus, as a function of temperature and frequency within the fibers. The sound-absorbing qualities of the fibers, exemplified by the sound absorption coefficient, were determined through the use of an impedance tube (ASTM E-1050, B&K 4206 type 03008) within a frequency span of 500 to 6000 Hz.
The test samples were adjusted according to the type of fiber characterization required. For XRD, BET, and Gravimetric characterizations, the fibers were cut into small pieces resembling powder. Meanwhile, for DMA testing, single fibers of 20–30 mm in length were used. In the absorption coefficient tests for each type of fiber (AFUT, AFTA, and AFAH), the samples had identical dimensions with a thickness of 20 mm, a mass of 7.61 g, and a diameter of 30 mm.
The main chemical components of abaca fibers are cellulose, hemicellulose, and lignin [25,31,32,34,44]. The effects of alkalization and hydrolyzation treatments impact the fiber’s chemical components, which can be identified through gravimetric analytical chemistry testing methods. The results of these measurements, including the content of cellulose, hemicellulose, and lignin, are presented in Table 1.
Alkali treatment has an effect on increasing the chemical content of cellulose, hemicellulose, and lignin. This increase is attributed to the removal of impurities (pectin, fats, proteins) in the fiber as a result of the alkali treatment [31,34,44]. This is also evident from the reduction in the diameter of AFTA and the decrease in surface area. However, a more significant change occurs when acid hydrolysis treatment is applied; the lignin content decreases from 9.63% to 4.14%. Acid hydrolysis can break down ether bonds and other chemical bonds in the structure of lignin, leading to its degradation and dissolution [53–55]. Higher cellulose components (>70%) and the reduction in lignin content contribute to the enhancement of the mechanical characteristics of the fibers [32]. Therefore, based on several previous studies, abaca is considered a good composite reinforcement [24,25].
Table 1 displays the effects of alkalization and hydrolysis treatments on the surface area, pore volume, and pore size. Based on these measurements, the surface area values of AFUT, AFTA, and AFAH decreased to 28.629, 16.983, and 13.721 m²g−1, respectively. Such a decrease in the surface area of the fibers indicates the loss of chemical components, such as impurities including pectin, protein, and lignin [56,57]. In this section, gravimetric measurements confirmed the reduction in lignin content.
XRD characterization was utilized to determine the level of crystallization of fibers before and after alkalization and acetic acid hydrolyzation treatment. Fig. 3 shows that the three fibers (AFAH, AFTA, and AFUT) exhibit there 2θ peaks at 15°, 22.5°, and 35.5°, with respective Miller indexes of [1 1 0], [0 0 2], and [0 0 4]. The XRD pattern results obtained from this study are consistent with the XRD pattern of cellulose [52]. This aligns with previous gravimetric testing results, indicating that the main content of abaca fibers (over 70%) is cellulose.
Figure 3: The degree of crystallization the three fibers (AFAH, AFTA, and AFUT)
The FWHM (Full Width at Half Maximum) value can be obtained by analyzing XRD characterization and is inversely proportional to crystal size. The narrower the FWHM, the higher the level of crystallization; this is in accordance with the Debye-Scherrer equation [58], resulting in values of 1.1364, 1.0361, and 0.1337, respectively, for AFUT, AFTA, and AFAH fibers. This indicates that the mechanical properties of the fibers are enhanced through alkalization and hydrolysis treatments. A significant decrease in FWHM in AFAH, showing a reduction of 88% from 1.0361 to 0.1337, demonstrates that alkalization and hydrolyzation treatments increase the crystallization level, which is associated with the improvement of mechanical properties [22,59–61].
The surface morphology of AFUT, AFTA, and AFAH, as revealed in Fig. 4, indicates fiber erosion. Characterization using SEM demonstrates that alkali treatment successfully reduces contaminants. This is evident in Fig. 4a, where AFUT has a larger diameter (230 µm) and displays a shiny white color, indicating the presence of contaminants and lignin [25]. In Fig. 4b, it is observed that the contaminants have disappeared, which corresponds with the reduction in fiber diameter to 210 µm and is accompanied by an increase in the content of cellulose, hemicellulose, and lignin as explained in the previous subsection. Acid hydrolysis treatment on AFAH fibers results in a rougher and more uniform fiber surface [29,32,55,62,63]. This increased roughness is advantageous as it helps to form an interlock between the fibers and the matrix, thereby enhancing the mechanical strength of the composite material [25,34–36].
Figure 4: SEM micrographs of Abaca fibers (a) AFUT, (b) AFTA, (c) AFAH
3.2 Mechanical Properties of Fibers
Abaca fibers have been scientifically proven to possess high mechanical properties [22–24]. These fibers can be applied as reinforcements in polymer matrices [17,32,52,64]. Table 2 shows that the effects of alkali treatment and acid hydrolysis advancement the mechanical properties of AFAH fibers, with a significant rise in tensile strength by 250%, and a rise in Young’s Modulus by 212% [15]. This improvement is due to the reduction in lignin content in AFAH, which in turn increases the hemicellulose content. According to XRD characterization, this treatment results in a rise in the crystallinity of the fibers.
The storage modulus (E′) of AFAH fibers significantly increases at temperatures above 35°C. As the temperature escalates, E′ correspondingly ascends as shown in Fig. 5a. This trend in the storage modulus curve resembles the heat capacity of solids and the mechanical energy in crystal lattice vibrations, which correlate with quantized mechanical energy in the form of phonons [68]. This indicates that E′ increases with temperature due to the presence of phonons, with higher temperatures leading to more quantized phonons. The E′ trends for AFUT, AFTA, and AFAH fibers suggest that the number of phonons reaches a saturation point at specific temperatures: 64°C, 70°C, and 90°C, respectively. Specifically for AFAH, E′ continues to rise with temperature and remains constant at 90°C, reaching a value of 4.45 × 104 MPa. This increase is attributed to the shedding of lignin, as indicated by a reduction in lignin content and increased in crystallinity confirmed by XRD characterization. The crystalline nature of the fibers makes them more rigid, with a higher E′ value reflecting greater rigidity and load-bearing capacity [69].
Figure 5: Storage modulus (E′) and damping factor (tan ) from abaca fibers [AFUT, AFTA & AFAH] as function of (a) Storage modulus in relation to temperature (b) Storage modulus in relation to frequency (c) Damping Factor in relation to temperature (d) Damping factor in relation to Frequency
The storage modulus of AFAH fibers appears to increase, as depicted in Fig. 5b, and this increase is referred to as the phenomenon of strain hardening [70]. This phenomenon is made possible by structural changes at the atomic level, specifically involving dislocations, which are imperfections in the crystal structure. The accumulation of these dislocations impedes their movement, thereby enhancing the strength and hardness of AFAH fibers. Consequently, the fibers become more resistant to deformation. It is also evident that AFAH fibers exhibit a higher degree of crystallinity compared to the other fibers. Resonant peaks are observed in AFAH fibers after undergoing alkalization and hydrolysis treatment; these peaks are produced due to the presence of voids and pores within the fibers. Furthermore, a smaller number of such peaks indicates higher elasticity and greater load-bearing capacity [50,69]. Fig. 5b demonstrates that the storage modulus in AFAH displays more resonant peaks, signifying that the fibers still retain some pores after treatment, as most of the lignin on the fiber surface is lost. This finding aligns with BET testing results, which reveal that the pore size in AFAH fibers increases due to the erosion of lignin levels.
The damping factor values for AFTA and AFAH fibers are observed to decrease, whereas for AFUT fibers, they increase Fig. 5c. The damping factor is indicative of the ratio between the loss modulus and the storage modulus, indicating how efficiently a material converts mechanical energy into heat energy. AFUT fibers exhibit greater energy absorption due to their high lignin content. A higher lignin content indicates a complex polymer that causes stiffness and resistance to biological attacks on the fibers. In DMA testing, lignin displays unique damping characteristics due to its complex and heterogeneous structure. Lignin tends to have a higher damping factor value at low temperatures compared to cellulose and hemicellulose, owing to its more aromatic and rigid nature. This parameter provides crucial role for determining the acoustic performance of fibers, characterized by their ability to absorb sound energy. Fibers absorb more energy when the damping factor value is greater than one [71]. Fig. 5d shows that the tan δ of AFAH and AFUT fibers is greater than one at several frequency peaks, leading to the conclusion that all fibers have good potential as sound energy-absorbing materials [72]. The damping factor stabilizes upon the temperature reaching 70°C, due to increased molecular mobility and more systematic movement. Conversely, at lower temperatures, the volume of intermolecular space within the fibers is greater, leading to reduced speed of molecular movement.
3.3 Acoustic Properties of Fibers
The challenge of using natural fibers as sound absorbers lies in their organic nature, which tends to be less durable compared to synthetic fibers and also possesses lower mechanical properties. Alkali processing and acid hydrolysis have been found to improve the mechanical properties of these fibers. According to the characterization conducted, such treatments lead to physical and chemical changes in the fibers, including alterations in pore size, surface area, density, fiber diameter, surface roughness, and fiber stiffness, as shown in Table 1.
This research exhibits an initial characterization of the sound absorption capabilities of abaca fibers before and after treatment. The samples used in this study, namely AFUT, AFTA, and AFAH, were chosen due to the effect of the treatment and have the same mass, thickness, and fiber diameter. The amount and size of the pores affect the sound energy within the fibers, and sound absorption decreases if the pores are fewer and smaller. Porous materials exhibit an optimal absorption coefficient at high frequencies [73–75]. Fig. 6 shows that the fibers (AFUT and AFTA) exhibit the same trend curve, which is optimal at the frequency range of 2000–3500 Hz with near-perfect absorption. This indicates that the alkali treatment could not impact the performance of pure abaca fibers (AFUT). However, for AFAH, the frequency range for sound absorption shifts to the right and has a wider range compared to the other fibers (AFUT and AFTA), namely 3400–6400 Hz. This correlates with a significant decrease in lignin content. The significant reduction in lignin makes the fibers stiffer. Furthermore, it can be stated that the stiffness of the fibers affects the absorption coefficient at high frequencies.
Figure 6: Sound absorption performance of fiber AFTA,
AFAH,
AFUT,
coir fibers,
Banana Pseudo stem
When compared to coir fiber, as indicated by the magenta curve, it is evident that coir exhibits a trend curve similar to that of abaca fibers (AFUT, AFTA, and AFAH), but its capability is still lower than that of abaca fibers [76]. Meanwhile, banana fiber, represented by the green curve, optimally absorbs sound at a frequency of 6000 Hz with a coefficient α = 0.8 [11]. Below 6000 Hz, the sound absorption coefficient decreases as the frequency decreases. Based on this research, AFAH fiber surpasses both coir and banana fibers in sound absorption. In addition to its capability to absorb sound energy, its effective frequency range is broader (2000–6000 Hz), which falls within the human hearing sensitivity range and matches the noise frequencies of factory machines and airplanes during takeoff and landing. Therefore, these fibers can be integrated with sound barrier materials and construction techniques to minimize sound transmission, serving as a method for reducing machine noise and decreasing the risk of damage to the organ of Corti [77,78].
Improvements in the mechanical and acoustic properties of abaca fibers were achieved through alkali treatment and acid hydrolysis. The impact of alkali processing on mechanical properties showed improvement, as indicated by the decrease in the FWHM value, suggesting that AFTA is more crystalline compared to the untreated AFUT. This was also evident in the increase in storage modulus, which varied with changes in temperature and frequency. This improvement is supported by structural and morphological changes, including a reduction in diameter caused by the removal of impurities, and a rise in the chemical content of AFTA, including cellulose, hemicellulose, and lignin. However, the acoustic properties of AFTA did not show significant changes.
The hydrolysis treatment significantly altered the mechanical properties. The hydrolyzed AFAH fibers were more crystalline, evidenced by an 88% reduction in FWHM value compared to AFUT. This was also observed in DMA testing, where AFAH showed a significant increase in storage modulus in response to both temperature and frequency. This increase occurred because the acid hydrolysis treatment reduced the lignin content by 57% compared to AFTA. The reduction in lignin made AFAH stiffer than both AFTA and AFUT, leading to minor changes in acoustic characterization, including a shift in the curve and a wider frequency bandwidth at high frequencies. The stiffness of the fibers caused AFAH to tend towards higher sound absorption, with the abaca fibers (AFUT, AFTA, and AFAH) achieving α of up to 0.9 at frequencies ranging from 2500 to 5500 Hz.
Acknowledgement: None.
Funding Statement: The authors received no specific funding for this study.
Author Contributions: Susilo Indrawati: Conceptualization, Methodology, Writing-Original Draft; Suyatno: Investigation; Mochamad Zainuri: Writing-Reviewing and Editing; Lila Yuwana: Writing-Reviewing; Darminto: Supervision.
Availability of Data and Materials: Data available within the article.
Conflicts of Interest: We submit a manuscript to the Journal of Renewable Materials on behalf of myself and my co-authors. However, we feel it is necessary to disclose a potential conflict of interest that may arise from our submission. All of my co-authors are currently the lecturers of Institut Teknologi Sepuluh Nopember, located in Surabaya, Indonesia. We are in the same department and we have made every effort to maintain objectivity in this research and analysis. We wish to assure you that the data presented in this manuscript is accurate, and we have taken great care to ensure that it is presented in an unbiased and fair manner. To address this potential conflict of interest, all co-authors have recused themselves from any decisions related to the publication of this manuscript. They will not be involved in the review or editing process and will not have access to any confidential information regarding this submission. We understand that it is ultimately up to the editorial team to decide whether this potential conflict of interest will impact the publication of this manuscript. However, we want to be transparent about this issue and provide the necessary information to make an informed decision.
References
1. Brown L. Burden of disease from environmental noise. Quantification of healthy life years lost in Europe; 2011, Available from: https://www.researchgate.net/publication/265414152_Burden_of_Disease_from_Environmental_Noise_Quantification_of_Healthy_Life_Years_Lost_in_Europe#:∼:text=These%20results%20indicate%20that%20at,main%20burden%20of%20environmental%20noise. [Accessed 2023]. [Google Scholar]
2. Lu X, Kang J, Zhu P, Cai J, Guo F, Zhang Y. Influence of urban road characteristics on traffic noise. Transp Res Part D Transp Environ. 2019;75:136–55. doi:10.1016/j.trd.2019.08.026. [Google Scholar] [CrossRef]
3. Rey Gozalo G, Gomez Escobar V. Uncertainty evaluation of road traffic noise models in two Ibero-American cities. Appl Acoust. 2021;180:108134. doi:10.1016/j.apacoust.2021.108134. [Google Scholar] [CrossRef]
4. Kuczmarski MA, Johnston JC. Acoustic absorption in porous materials. Glenn Research Center. Available from: https://ntrs.nasa.gov/citations/20110011143. [Accessed 2020]. [Google Scholar]
5. Yang M, Sheng P. Sound absorption structures: from porous media to acoustic metamaterials. Annu Rev Mater Res. 2017;47:83–114. doi:10.1146/annurev-matsci-070616-124032. [Google Scholar] [CrossRef]
6. Kudo Y, Aizawa Y. Behavior of rock wool in lungs after exposure by nasal inhalation in rats. 2009;226–34. doi:10.1007/s12199-009-0082-0. [Google Scholar] [PubMed] [CrossRef]
7. Lipworth L, La Vecchia C, Bosetti C, McLaughlin JK. Occupational exposure to rock wool and glass wool and risk of cancers of the lung and the head and neck: a systematic review and meta-analysis. J Occup Environ Med. 2009;51:1075–87. doi:10.1097/JOM.0b013e3181b35125. [Google Scholar] [PubMed] [CrossRef]
8. Kudo Y, Kotani M, Tomita M, Aizawa Y. Effects of rock wool on the lungs evaluated by magnetometry and biopersistence test. J Occup Med Toxicol. 2009;4:1–7. doi:10.1186/1745-6673-4-5. [Google Scholar] [PubMed] [CrossRef]
9. Sekar V, Fouladi MH, Namasivayam SN, Sivanesan S. Additive manufacturing: aa novel method for developing an acoustic panel made of natural fiber-reinforced composites with enhanced mechanical and acoustical properties. J Eng. 2019;2019:4546863. doi:10.1155/2019/4546863. [Google Scholar] [CrossRef]
10. Othmani C, Taktak M, Zein A, Hentati T, Elnady T, Fakhfakh T, et al. Experimental and theoretical investigation of the acoustic performance of sugarcane wastes based material. Appl Acoust. 2016. doi:10.1016/j.apacoust.2016.02.005. [Google Scholar] [CrossRef]
11. Mendes COB, de Araújo Nunes MA. Acoustic performance of the banana pseudostem fiber. Appl Acoust. 2022;191:108657. doi:10.1016/j.apacoust.2022.108657. [Google Scholar] [CrossRef]
12. Raj M, Fatima S, Tandon N. A study of areca nut leaf sheath fibers as a green sound-absorbing material. Appl Acoust. 2020;169:107490. doi:10.1016/j.apacoust.2020.107490. [Google Scholar] [CrossRef]
13. Kassim DH, Putra A, Ramlan R. Enhancement of sound absorption of coir fiber using thin layer of kapok fibers. J Nat Fibers. 2023;20(1). doi:10.1080/15440478.2022.2164103. [Google Scholar] [CrossRef]
14. Raj M, Fatima S, Tandon N. An experimental and theoretical study on environment-friendly sound absorber sourced from nettle fibers. J Build Eng. 2020;31:101395. doi:10.1016/j.jobe.2020.101395. [Google Scholar] [CrossRef]
15. Indrawati S, Maligi A, Zainuri M, Darminto. Development of natural fibers from banana’s stem as composite reinforcer. AIP Conf Proc. 2023;2604:020011. doi:10.1063/5.0115270. [Google Scholar] [CrossRef]
16. Dancel RR. Abaca fiber as a retrofitting material. In: Proceedings of Research International Conference, 2018; Manila, Philippines. p. 1–5. Available from: https://www.researchgate.net/publication/328900481. [Accessed 2019]. [Google Scholar]
17. Tampi R, Parung H, Djamaluddin R, Amiruddin AA. Reinforced concrete mixture using abaca fiber. In: IOP Conference Series: Earth and Environmental Science, 2020; Bali, Indonesia. p. 419. doi:10.1088/1755-1315/419/1/012060. [Google Scholar] [CrossRef]
18. Saragih SW, Wirjosentono B, Eddiyanto, Meliana Y. Influence of crosslinking agent on the morphology, chemical, crystallinity and thermal properties of cellulose nanofiber using steam explosion. Case Stud Therm Eng. 2020;22:100740. doi:10.1016/j.csite.2020.100740. [Google Scholar] [CrossRef]
19. Department of Agriculture. Philippine abaca industry roadmap 2018–2022—executive summary. 2018. Available from: https://www.da.gov.ph/wp-content/uploads/2019/06/Philippine-Abaca-Industry-Roadmap-2018-2022.pdf. [Accessed 2019]. [Google Scholar]
20. Food and Agriculture Organization of the United Nations. Abaca. 2018. Available from: https://www.fao.org/economic/futurefibres/fibres/abaca0/en/. [Accessed 2019]. [Google Scholar]
21. Simbana EA, Ordóñez PE, Ordóñez YF, Guerrero VH, Mera MC, Carvajal EA. Abaca: cultivation, obtaining fibre and potential uses. Handb Nat Fibres Second Ed. 2020;1:197–218. doi:10.1016/B978-0-12-818398-4.00008-6. [Google Scholar] [CrossRef]
22. Saragih SW, Lubis R, Wirjosentono B, Eddyanto. Characteristic of abaca (Musa textilis) fiber from Aceh Timur as bioplastic. AIP Conf Proc. 2018;2049(1):020058. doi:10.1063/1.5082463 [Google Scholar] [CrossRef]
23. Suhelmidawati, Etri. Tensile tests of abaca fiber as one of alternative materials for retrofitting of unreinforced masonry (URM) houses. Rekayasa Sipil. 2016;XIII(2):22–8. [Google Scholar]
24. Punyamurthy R, Sampathkumar D, Bennehalli B, Patel R, Venkateshappa SC. Abaca fiber reinforced epoxy composites: evaluation of impact strength international journal of sciences: abaca fiber reinforced epoxy composites: evaluation of impact strength. Int J Sci Basic Appl Res. 2014;18(2):305–17. Available from: https://gssrr.org/index.php/JournalOfBasicAndApplied/article/view/3203. [Accessed 2019]. [Google Scholar]
25. Cai M, Takagi H, Nakagaito AN, Li Y, Waterhouse GI. Effect of alkali treatment on interfacial bonding in abaca fiber-reinforced composites. Compos Part A Appl Sci Manuf. 2016;90:589–97. doi:10.1016/j.compositesa.2016.08.025. [Google Scholar] [CrossRef]
26. Tamanna TA, Belal SA, Shibly MAH, Khan AN. Characterization of a new natural fiber extracted from Corypha taliera fruit. Sci Rep. 2021;11:1–13. doi:10.1038/s41598-021-87128-8. [Google Scholar] [PubMed] [CrossRef]
27. Rakowska J, Węgrzyn M, Rudnik E. Impact of ionic liquids on absorption behaviour of natural fibers/biopolyethylene biocomposites. Sci Rep. 2021;11:1–12. doi:10.1038/s41598-021-99956-9 [Google Scholar] [CrossRef]
28. Lakshmi Narayana V, Bhaskara Rao L. A brief review on the effect of alkali treatment on mechanical properties of various natural fiber reinforced polymer composites. Mater Today Proc. 2021;44:1988–94. doi:10.1016/j.matpr.2020.12.117. [Google Scholar] [CrossRef]
29. Dewri SP, Gnanamoorthy R. Effect of alkali treatment on the friction coefficient of single coconut fiber. Mater Today Proc. 2023;3–6. doi:10.1016/j.matpr.2023.03.466. [Google Scholar] [CrossRef]
30. Naik TP, Gairola S, Singh I, Sharma AK. Microwave-assisted alkali treatment of sisal fiber for fabricating composite as non-structural building materials. Constr Build Mater. 2024;411:134651. doi:10.1016/j.conbuildmat.2023.134651. [Google Scholar] [CrossRef]
31. Kumar Sinha A, Narang HK, Bhattacharya S. Effect of alkali treatment on surface morphology of abaca fibre. Mater Today Proc. 2017;4(8):8993–6. doi:10.1016/j.matpr.2017.07.251. [Google Scholar] [CrossRef]
32. Yogeshwaran S, Natrayan L, Udhayakumar G, Godwin G, Yuvaraj L. Effect of waste tyre particles reinforcement on mechanical properties of jute and abaca fiber-Epoxy hybrid composites with pre-treatment. Mater Today Proc. 2020;37:1377–80. doi:10.1016/j.matpr.2020.06.584. [Google Scholar] [CrossRef]
33. Valášek P, Müller M, Šleger V, Kolář V, Hromasová M, D’Amato R, et al. Influence of alkali treatment on the microstructure and mechanical properties of coir and abaca fibers. Materials. 2015;14:27–35. doi:10.3390/ma14102636 [Google Scholar] [CrossRef]
34. Kumar Sinha A, Narang HK, Bhattacharya S. Evaluation of bending strength of abaca reinforced polymer composites. Mater Today Proc. 2018;5:7284–8. doi:10.1016/j.matpr.2017.11.396. [Google Scholar] [CrossRef]
35. Girisha L, Kandasamy K, Sivaraman G, Benham A, Ahammad SH. Assessment of mechanical properties on abaca fiber strengthened nano sandstone filler hybrid polymer composite. Mater Today Proc. 2023. doi:10.1016/j.matpr.2023.05.517. [Google Scholar] [CrossRef]
36. Sivasankar GA, Karthick PA, Boopathi C, Brindha S, Nirmalraj RJT, Benham A. Evaluation and comparison on mechanical properties of abaca and hemp fiber reinforced hybrid epoxy resin composites. Mater Today Proc. 2023. doi:10.1016/j.matpr.2023.04.400. [Google Scholar] [CrossRef]
37. Albuja-Sánchez J, Alcívar E, Escobar D, Montero J, Realpe G, Muñoz A, et al. Influence of abaca fiber inclusion on the unconfined compressive strength of reconstituted sandy silts. Fibers. 2022. doi:10.3390/fib10110099. [Google Scholar] [CrossRef]
38. Pranoto Y, Suryono J, Rahman LH. Study of utilizations abaca fibre with kalimantan local material on the concrete compressive and flexural strength. IOP Conf Ser: Earth Environ Sci. 2021;832:012028. doi:10.1088/1755-1315/832/1/012028. [Google Scholar] [CrossRef]
39. Banowati L, Sari P, Hadi BK. Comparison analysis of abaca fiber/polyester and abaca-e-glass/polyester hybrid composites to impact strength and its application to ballistic. IOP Conf Ser: Mater Sci Eng. 2021;1173:012068. doi:10.1088/1757-899X/1173/1/012068. [Google Scholar] [CrossRef]
40. Saefullah L, Harsono H. Ballistic impact simulation on composite of abaca fiber/Hgm/epoxy/carbon fiber as body armor material & desain sporty dan stylish. AIP Conf Proc. 2023;2614:050018. doi:10.1063/5.0126783. [Google Scholar] [CrossRef]
41. Sirot R, Punongbayan AJ, Magdaluyo E. Ballistic performance simulation of abaca fiber-reinforced epoxy matrix composite using finite element analysis. Aip Conf Proc. 2023;2901(1):100014. [Google Scholar]
42. Koundal NK, Kumar S, Mehta V, Grewal JS. Comparative study of Abaca fiber and Kevlar fibers based brake friction composites. Polym Composite. 2022;43(2):730–40. doi:10.1002/pc.26405. [Google Scholar] [CrossRef]
43. Liu K, Zhang X, Takagi H, Yang Z, Wang D. Effect of chemical treatments on transverse thermal conductivity of unidirectional abaca fiber/epoxy composite. Compos Part A Appl Sci Manuf. 2014;66:227–36. doi:10.1016/j.compositesa.2014.07.018. [Google Scholar] [CrossRef]
44. Cagrl Uyanik M, Tamer Erturk A. Recent developments of natural fibres: natural fibre biocomposites, treatments, and characterizations. J Phys Conf Ser. 2023;2549:012001. doi:10.1088/1742-6596/2549/1/012001. [Google Scholar] [CrossRef]
45. Binoj JS, Raj RE, Hassan SA, Mariatti M, Siengchin S, Sanjay MR. Characterization of discarded fruit waste as substitute for harmful synthetic fiber-reinforced polymer composites. J Mater Sci. 2020;55:8513–25. [Google Scholar]
46. Dittenber DB, Gangarao HVS. Critical review of recent publications on use of natural composites in infrastructure. Compos Part A Appl Sci Manuf. 2012;43:1419–29. doi:10.1016/j.compositesa.2011.11.019. [Google Scholar] [CrossRef]
47. Jústiz-Smith NG, Virgo GJ, Buchanan VE. Potential of Jamaican banana, coconut coir and bagasse fibres as composite materials. Mater Charact. 2008;59:1273–8. doi:10.1016/j.matchar.2007.10.011. [Google Scholar] [CrossRef]
48. Mamun AA, Heim HP, Faruk O, Bledzki AK. The use of banana and abaca fibres as reinforcements in composites. In: Biofiber Reinforcements in Composite Materials. 2015. p. 236–72. doi:10.1533/9781782421276.2.236. [Google Scholar] [CrossRef]
49. Indran S, Raj RE. Characterization of new natural cellulosic fiber from Cissus quadrangularis stem. Carbohydr Polym. 2015;117:392–9. doi:10.1016/j.carbpol.2014.09.072. [Google Scholar] [PubMed] [CrossRef]
50. Haris NIN, Hassan MZ, Ilyas RA, Suhot MA, Sapuan SM, Dolah R, et al. Dynamic mechanical properties of natural fiber reinforced hybrid polymer composites: a review. J Mater Res Technol. 2022;19:167–82. [Google Scholar]
51. Gholampour A, Ozbakkaloglu T. A review of natural fiber composites: properties, modification and processing techniques, characterization, applications. J Mater Sci. 2020;55:829–92. doi:10.1007/s10853-019-03990-y. [Google Scholar] [CrossRef]
52. Sinha AK, Bhattacharya S, Narang H. Abaca fibre reinforced polymer composites. J Mater Sci. 2021;56:4569–87. doi:10.1007/s10853-020-05572-9 2021. [Google Scholar] [CrossRef]
53. Sawpan MA, Pickering KL, Fernyhough A. Effect of various chemical treatments on the fibre structure and tensile properties of industrial hemp fibres. Compos Part A Appl Sci Manuf. 2011;42:888–95. doi:10.1016/j.compositesa.2011.03.008. [Google Scholar] [CrossRef]
54. Santiagoo R, Hong TW, Azizan NZN, Andrew AM, Wahab F, Seman NAA, et al. The effect of stearic acid and different loading treated and untreated EFB fiber on the tensile, structural and chemical properties of polypropylene/recycled acrylonitrile butadiene rubber/empty fruit bunch composites. IOP Conf Ser Earth Environ Sci. 2021;765:012037. doi:10.1088/1755-1315/765/1/012037. [Google Scholar] [CrossRef]
55. Seisa K, Chinnasamy V, Ude AU. Surface treatments of natural fibres in fibre reinforced composites: aa review. Fibres Text East Eur. 2022;30:82–9. doi:10.2478/ftee-2022-0011. [Google Scholar] [CrossRef]
56. Zhang B, Huang C, Zhao H, Wang J, Yin C, Zhang L, et al. Efects of cellulose nanocrystals and cellulose nanofibers on the structure and properties of polyhydroxybutyrate nanocomposites. Polymers. 2019;11(12):2063. doi:10.3390/polym11122063. [Google Scholar] [PubMed] [CrossRef]
57. Nindiyasari F, Griesshaber E, Zimmermann T, Manian AP, Randow C, Zehbe R, et al. Characterization and mechanical properties investigation of the cellulose/gypsum composite. J Compos Mater. 2016;50:657–72. doi:10.1177/0021998315580826. [Google Scholar] [CrossRef]
58. Cullity BD, Stock SR. Elements of X-ray diffraction. 3rd ed. The United States of America: Pearson New International; 2014. Available from: https://www.eng.uc.edu/~beaucag/Classes/AdvancedMaterialsThermodynamics/Books/B.D.%20Cullity,%20S.R.%20Stock%20-%20Elements%20of%20X-Ray%20Diffraction-Pearson%20Education%20Limited%20(2014).pdf. [Accessed 2020]. [Google Scholar]
59. Pratapa S, Kiswanti EA, Diana DR, Hariyani Y, Sari LD, Musyarofah M, et al. Synthesis of high-purity ceramic nano-powders using dissolution method. In: Ceramic materials–synthesis, characterization, applications and recycling. 2016. doi:10.5772/intechopen.81983. [Google Scholar] [CrossRef]
60. Rajak DK, Durgesh DP, Pagar DP, Menezes PL, Linul E. Fiber-reinforced polymer composites: manufacturing, properties, and applications. Polymers. 2019;10(11):1667. doi:10.3390/polym11101667. [Google Scholar] [PubMed] [CrossRef]
61. Ramadevi P, Sampathkumar D, Srinivasa CV, Bennehalli B. Effect of alkali treatment on water absorption of single cellulosic abaca fiber. BioResources. 2012;7:3515–24. [Google Scholar]
62. Dinçel Kasapoğlu E, Kahraman S, Tornuk F. Extraction optimization and characterization of cellulose nanocrystals from apricot pomace. Foods. 2023;12(4):1–14. doi:10.3390/foods12040746. [Google Scholar] [PubMed] [CrossRef]
63. Butt MS. Tannic acid treatment of natural fibers and its effect on moisture absorption and mechanical properties of subsequent composites. 2023;1–21. doi:10.21203/rs.3.rs-3248290/v1. [Google Scholar] [CrossRef]
64. Vijaya RB, Manickavasagam VM, Elanchezhian C, Vinodh KC, Karthik S, Saravanan K. Determination of mechanical properties of intra-layer abaca-jute-glass fiber reinforced composite. Mater Des. 2014;60:643–52. doi:10.1016/j.matdes.2014.03.061. [Google Scholar] [CrossRef]
65. Agarwal GS, Bhuptawat HK, Chaudhari S. Biosorption of aqueous chromium(VI) by Tamarindus indica seeds. Bioresour Technol. 2006;97:949–56. doi:10.1016/j.biortech.2005.04.030 [Google Scholar] [CrossRef]
66. Panara K, Cr H, Vj S. Pharmacognostic and Phytochemical evaluation of fruit pulp of Tamarindus Indica linn. Int J Ayurvedic Med. 2014;5:37–42. [Google Scholar]
67. Mahmud S, Hasan KMF, Jahid A, Mohiuddin K. Comprehensive review on plant fiber-reinforced polymeric biocomposites. J Mater Sci. 2021;56:7231–64. doi:10.1007/s10853-021-05774-9. [Google Scholar] [CrossRef]
68. Kittel C. Quantum theory of solid state. 2nd ed. The United States of America: John Wiley & Sons, Inc.; 1987. [Google Scholar]
69. Menard KP. Dynamic mechanical anaylsis. 2nd ed. CRC Press Taylor & Francis Group; 2008. [Google Scholar]
70. Illampas R, Oliveira DV, Lourenço PB. Design of strain-hardening natural TRM composites: current challenges and future research paths. Mater. 2023;16(13):4558. doi:10.3390/ma16134558. [Google Scholar] [PubMed] [CrossRef]
71. Goken J, Fayed S, Schafer H, Enzenauer J. A study on the correlation between wood moisture and the damping behaviour of the tonewood spruce. Acta Phys Pol A. 2018;133:1241–60. doi:10.12693/APhysPolA.133.1241. [Google Scholar] [CrossRef]
72. Manik TN, Nuki SA, Fauziyah NA, Mashuri, Zainuri M, Darminto. Structure, dynamic-mechanical and acoustic properties of oil palm trunk modified by melamine formaldehyde. J Renew Mater. 2021;9(9):1647–60. doi:10.32604/jrm.2021.016089 [Google Scholar] [CrossRef]
73. Berardi U, Iannace G. Acoustic characterization of natural fibers for sound absorption applications. Build Environ. 2015;94:840–52. doi:10.1016/j.buildenv.2015.05.029. [Google Scholar] [CrossRef]
74. Cao L, Fu Q, Si Y, Ding B, Yu J. Porous materials for sound absorption. Compos Commun. 2018;10(1):25–35. doi:10.1016/j.coco.2018.05.001. [Google Scholar] [CrossRef]
75. Hassani P, Soltani P, Ghane M, Zarrebini M. Porous resin-bonded recycled denim composite as an efficient sound-absorbing material. Appl Acoust. 2021;173:107710. doi:10.1016/j.apacoust.2020.107710. [Google Scholar] [CrossRef]
76. Hosseini Fouladi M, Ayub M, Jailani Mohd Nor M. Analysis of coir fiber acoustical characteristics. Appl Acoust. 2011;72:35–42. doi:10.1016/j.apacoust.2010.09.007. [Google Scholar] [CrossRef]
77. Davis RR. Noise-induced hearing loss: scientific advances, springer handbook of auditory research. J Acoust Soc Am. 2014;136(2):946–7. doi:10.1121/1.4887452. [Google Scholar] [CrossRef]
78. Beranek LL. Acoustics. 2nd ed. The Acoustial Society of America, New York: The McGraw-Hill Book Company, Inc.; 1993. [Google Scholar]
Cite This Article
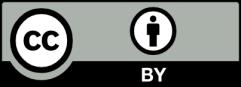
This work is licensed under a Creative Commons Attribution 4.0 International License , which permits unrestricted use, distribution, and reproduction in any medium, provided the original work is properly cited.