Open Access
REVIEW
Wood By-Products as UV Protection: A Consequence Review
Cellulose and Paper Department, National Research Centre, Cairo, 12622, Egypt
* Corresponding Author: Samir Kamel. Email:
(This article belongs to the Special Issue: Special Issue in Celebration of JRM 10 Years)
Journal of Renewable Materials 2024, 12(4), 699-720. https://doi.org/10.32604/jrm.2024.049118
Received 28 December 2023; Accepted 29 February 2024; Issue published 12 June 2024
Abstract
In recent decades, the ozone layer has suffered considerable damage, increasing the entry of ultraviolet (UV) light into the atmosphere and reaching the earth’s surface, negatively affecting life. Accordingly, researchers aimed to solve this problem by synthesizing advanced UV-shielding materials. On the other hand, developing an easy and green strategy to prepare functional materials with outstanding properties based on naturally abundant and environmentally friendly raw materials is highly desirable for sustainable development. Because biomass-derived materials are sustainable and biodegradable, they present a promising substitute for petroleum-based polymers. The three main structural constituents of the plant biomass-based materials that are naturally available are cellulose, hemicellulose, and lignin. This review details current developments using wood-based products such as cellulose, hemicellulose, and lignin in UV-shielding applications. It will start with assembling the structure and chemistry of cellulose, hemicellulose, and lignin, followed by their contributions to preparing UV-shielding materials. Finally, it will briefly discuss the different processing methods for the design of UV-shielding materials. The wood by-products offer additional opportunities to use the whole tree harvest.Graphic Abstract
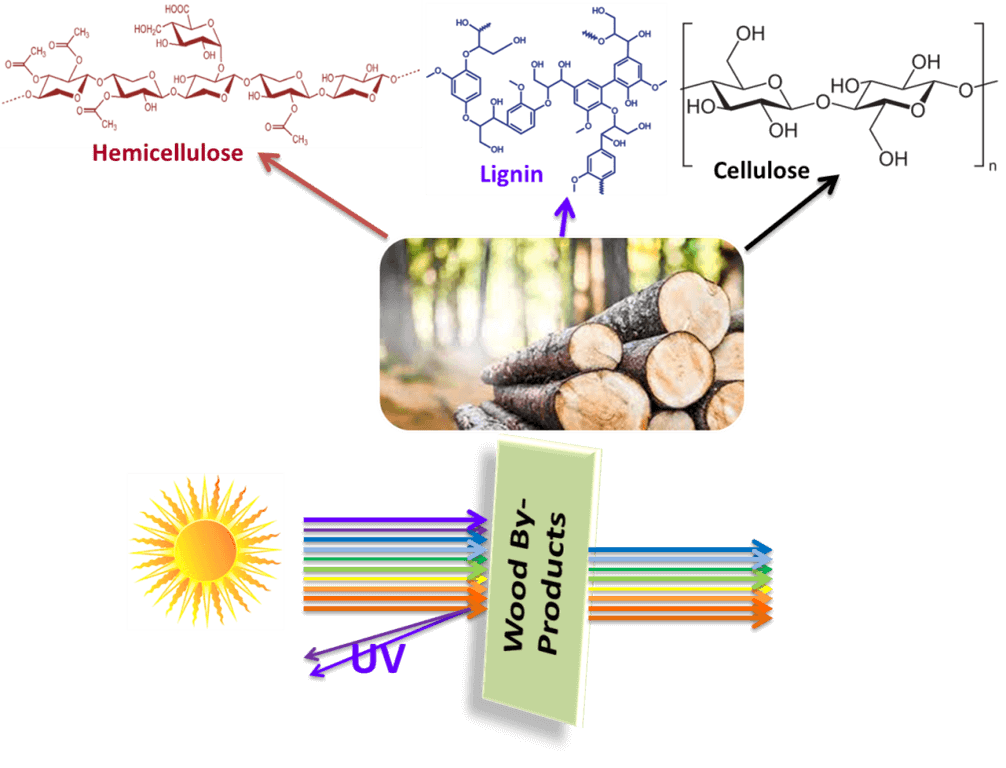
Keywords
People benefit from sunlight in many ways, such as increased synthesis of vitamin D and decreased expression of ß-endorphins [1]. About 10% of solar radiation comprises ultraviolet (UV) light, a high-intensity electromagnetic radiation with a wavelength ranging from 10 to 400 nm (Fig. 1). However, the earth’s atmosphere completely blocks light below 280 nm; in recent decades, most (320–400 nm) and partial (280–320 nm) lights can still reach the earth’s surface, increasing the UV radiation due to the loss of the stratospheric ozone layer, resulting in increasing of negative effects on human’s health such as photoaging, skin burns, skin cancer, and immune system damage [2]. In addition, UV radiation is responsible for the weathering, discoloration of pigments and dyes, loss of mechanical properties (cracking), yellowing of papers and plastics, and other problems. UV absorbers have effectively been used to conserve the material’s properties [3]. Moreover, UV light is produced from different artificial devices, such as mercury-vapor lamps, UV printers, electric arcs, and germicidal cabinets [4]. In general, UV shielding is materials that absorb or block light, and one of their significant applications is their use as sunscreens to protect skin from sun/UV-related damage. Also, UV shielding has been used to protect the hardware of the digital camera, which is sensitive to UV light. From this point, UV skincare products have risen rapidly to protect human skin from sun damage. In the 1900s, the first sunscreen was developed, and plant extracts were used to protect the skin from sunburns in ancient civilizations [5]. According to the capacity of UV filters, they are classified as UV-A (320–400 nm), UV-B (280–320 nm), or broad-spectrum (UV-A & UV-B) UV filters [6,7]. Recently, the development of UV-shielding materials, incredibly transparent UV-protective polymeric films, has attracted increasing attention [8]. There are two traditional UV filters; organic UV absorbers and inorganic UV blockers [9]. Inorganics mainly comprise nanoparticles like CeO2, ZnO, and TiO2, which possess broadband UV absorption. Still, their compatibility with polymeric matrices is poor, and when exposed to UV light, they produce reactive oxygen species, inducing photocatalytic degradation of polymers [10].
Figure 1: UV, visible light, and infrared spectra range
In contrast, organic UV absorbers usually dissipate the energy as heat after absorbing UV light. Although organic UV absorbers show high UV-absorbing efficiency, most are photo-unstable due to their photodegradation or photoisomerization when exposed to UV light. Consequently, they can generate toxic photodegradation products and loss of photoprotective activity [11]. Therefore, natural products and synthetic derivatives using nanotechnology approaches have been investigated over the last two decades to find stable, safe, and high-efficiency UV filters. Recently, studies have documented that polyphenolic polymers and lignin derivatives exhibit better biosafety, stability, dispersion in water, and lower skin permeability. Thus, the methods developed to load small-molecule UV filters into polymers without destroying their UV shielding efficiency have practical value [12]. Accordingly, we aim to provide a short review of wood and its wood by-products followed by a comprehensive review of available studies focusing on utilizing wood by-products in manufacturing UV filters.
Wood has a hierarchical structure from the meter down to the nanoscale to molecular scales corresponding to trunk, fibrils, and cellulose chains [13]. Wood consists mainly of hemicellulose (25%–35%), cellulose (40%–50%), and lignin (18%–35%), and these materials can isolate from various agro-based feedstocks also (Fig. 2). The most abundant plant-based natural polymers are hemicellulose, cellulose, and lignin [14]. Cellulose is the main component of the cell wall; it forms long and highly oriented fibrils. Non-covalent crosslinks hold the highly branched, amorphous hemicellulose to the nearby cellulose filaments. A three-dimensional, unstructured molecule called lignin is bonded to carbohydrates by covalent and hydrogen bonds [15]. Lignocellulose is extensively used in various sectors, including antimicrobial [16,17], biomedical [18], electromagnetic shielding [19], energy storage [20], sensing [21], etc. Currently, lignocellulose may be extracted from various raw materials using different physical and chemical processes, including grinding [22], ultrasonic [23], enzymatic hydrolysis [24], alkali treatment, and acid treatment [25].
Figure 2: Cellulose parts are surrounded by hemicellulose and lignin in the wood cell wall, and their chemical structures (Reprinted from reference [15] with permission from Materials, MDPI, Copyright © [2021])
Before petroleum-derived plastics were widely used, many cellulose polymers that were created commercially were widely used. There are still many cellulose derivatives in use today for specific purposes. Cellulose derivatives are soluble in various industrial solvents. They can be prepared from native cellulose, which is hydrophilic and water-insoluble due to the strong inter and intra-molecular hydrogen bonding within the polymeric chain of cellulose [26]. However, it has promising properties such as high biocompatibility, nontoxicity, high sorption capacity, thermal stabilities, and high mechanical strength. It has three OH groups in glucose residue, which are chemically active sites for modification. These sites can partially or fully react with chemicals to form cellulose derivatives [27]. The solubility of derivatives is advantageous for film development and other processing. The hydrophilic, swelling tendency and hygroscopic nature of cellulose limit its film-forming capability and require an energy-consuming drying process.
The cellulose derivatives can be divided into cellulose ethers, cellulose esters, and oxidized cellulose (Fig. 3). Ether derivatives are produced by replacing the hydrogen atom of OH groups of cellulose with alkyl groups [28]. Both derivatives can be prepared by homogeneous or heterogeneous modification. The properties of derivatives depend on the degree of substitution (average number of hydroxyl groups substituted per anhydroglucose units), degree of polymerization (chain length), and the purity of the cellulose, which is indicated by the relative mass fraction of a-cellulose. The more amorphous means less crystalline, the higher the diffusion rate of different reagents. The hardness, softness, moisture absorption, and biodegradability depend strongly on the degree of substitution; a high degree of substitution lowers the biodegradability.
Figure 3: Cellulose structure and list of its derivatives
Also, the oxidation of cellulose is a promising process for creating new functional groups on the cellulose backbone and new properties. The oxidation process can be selectively achieved with 2,2,6,6-tetramethylpiperidin-1-oxyl (TEMPO) or potassium periodate or non-selective, using hydrogen peroxide, perchloric acid, etc. [29]. Periodate selective oxidation gives C2, C3-dialdehyde cellulose that can be further oxidized to dicarboxylic cellulose by sodium chlorite, while oxidation by TEMPO gives carboxy cellulose (C6) [30]. The combination of common oxidation agents, nitroxyl mediated and periodate, gives 2,3,6-tricarboxy cellulose [31].
Meanwhile, the degree of polymerization effect on the viscosity is associated with mechanical and rheological properties [32]. Cellulose can be further processed to produce cellulose nanocrystals or nanofibers produced by the acid hydrolysis of cellulose fibers. The characteristics of nanocelluloses are determined by the type of acid used, e.g., nanocrystals produced by hydrochloric acid treatment yield inferior colloidal stability. In contrast, those produced by sulfuric acid have good colloidal stability [33].
Hemicellulose is a heteroglycan composed of five and six-carbon sugars, including xylose, arabinose, mannose, galactose, and rhamnose (Fig. 4). It is the main component of lignocellulose and constitutes plant cells with cellulose and lignin, characterized by low polymerization and high branching. Its polymers include xylan, arabinoxylan, glucomannan, glucuronoxylan, and xyloglucan (Fig. 4) [34]. Hemicellulose has good biocompatibility [35], low cost, and comprehensive sources; consequently, it has attracted much attention in biomedical [36,37], sensors [38–40], and environmental applications [41,42,34]. It is rich in groups that have oxygen, such as hydroxyl, carboxyl, acetyl groups, etc. So, it can be modified by esterification [43,44], etherification [45,46], graft copolymerization [47,48], and others [49].
Figure 4: Monomer sugars found in hemicellulose and example of polymers in hemicellulose
Lignin is the second most abundant carbon source after cellulose, and it is amorphous and branched in structure. Approximately 50 million tons of lignin are produced worldwide annually as a by-product of pulp and paper industries and bio-refining operations. It is the main ingredient of black liquor produced from the kraft process in the pulp and paper industries [50]. In the plant, lignin helps to weld cells together and provides resistance against bending that occurs by wind. Also, it acts against fungal and bacterial pathogens. It comprises crosslinked, branched aromatic monomers linked together by ether (about 60%–70%) or C=C bonds (about 30%–40%) [51]: coniferyl alcohol, p-coumaryl alcohol, and sinapyl alcohol (Fig. 5). In softwoods, the predominant monomer is coniferyl alcohol; in hardwoods, coniferyl and sinapyl alcohols are the building blocks, while p-coumaryl alcohol is a minor component of grass and forage-type lignin (Table 1) [52]. Lignin contains many functional groups behind ketone, phenolic unit, and chromophores: UV radiation absorbing groups. The presence of these groups acquired the lignin UV blocking, antioxidant, and radical scavenging properties. Recently, it has been used as a reinforcement antioxidant, a thermostat, and a compatibilizer in polymer composites [53].
Figure 5: Schematic representation for lignin structure (red, blue, and green colors are sinapyl, guaiacyl, and p-coumaryl alcohols, respectively) (Reprinted from reference [55] with permission from Sustainability, MDPI, Copyright © [2020])
Moreover, several different materials can produce from lignin, Such as alkanes (cyclohexane), aliphatic acids (polyesters), simple aromatics (biphenyls, benzene, xylenes), hydroxylated aromatics (phenol, catechol, propylphenol), aromatic aldehydes (vanillin, syringaldehyde), and aromatic acids and diacids (vanillic acid). Also, high molecular weight compounds can be produced from lignin, such as polyelectrolytes, fillers for polymers, thermoplastic polymers, carbon fibers, and resins for wood adhesives and preservatives [51]. According to raw materials, lignin separation can be divided into separation from raw materials, pulp, or pulp waste liquid. Based on the separation principle, the dissolution of cellulose and hemicellulose leaves the insoluble lignin, dissolving the lignin and recovering lignin from the solution [54]. In the following sections, various strategies used in developing wood by-products as UV filters will be discussed.
3 Applications of Wood By-Products in UV Protection
Cellulose has no UV shielding efficiency but can be modified or coupled with other materials to accept this property. Dialdehyde cellulose was coupled with E-3-amino-5-(phenyldiazenyl)-2-thioxothiazolidin-4-one via Schiff base reaction and incorporated onto tricarboxy cellulose to get UV-shielding films (Fig. 6). The studies found that the film with 10% Dialdehyde cellulose-E-3-amino-5-(phenyldiazenyl)-2-thioxothiazolidin-4-one has 99.99%, 99.88%, and 96.19% UV-A, UV-B, and ultraviolet protection factor (UPF), respectively [56].
Figure 6: Plausible mechanism of the reaction of dialdehyde cellulose with E-3-amino-5-(phenyldiazenyl)-2-thioxothiazolidin-4-one and formation of films and their UV protection (Reproduced from reference [56] with permission from Scientific Reports, Springer Nature, Copyright © [2022])
Cellulose is highly suitable as the host biomaterial of inorganic nanoparticles because it can improve stability, control growth, and retain the nanoparticle’s morphology. Also, it can preserve the excellent optical properties of inorganic nanoparticles and has a lot of hydroxyl groups. It can interact with transition-metal cations and acts as nanoreactors for in situ metal nanoparticle synthesis [57]. According to this fact, cellulosic materials with photo-functionality such as UV absorption, optoelectrical, light-diffusing, photoluminescent, and visible-light-induced photocatalytic properties have been prepared by introducing different functional inorganic nanoparticles such as metallic nanoparticles and quantum dots [58,59]. Cellulose can be used as a matrix for loading a UV blocker; regenerated cellulose/CeO2 nanocomposite films were prepared. Films exhibited UV shielding, high transmittance, a certain degree of hydrophobicity, and moderate thermal stability. Film with 2.95 wt% CeO2 had high UV shielding and >75% light transmittance (550 nm). CeO2 showed a strong absorption peak in the UV range with no absorption band >500 nm due to the wide band gap. In general, regenerated cellulose/CeO2 films showed good absorption in the UV-B region means that the organic–inorganic composites reserved the inherent optical properties of the CeO2 (Fig. 7) [60].
Figure 7: UV absorption, transmittance, and digital pictures of regenerated cellulose (RC)/CeO2 and RC/CeO2 nanocomposite films (Abbreviations; RC = Regenerated cellulose) (Reprinted from reference [60] with permission from Polymers, MDPI, Copyright © [2019])
Modified cellulose can be loaded with UV-shielding to suit a specific application. For example, one potential of UV prevention is wearing clothes with UV protection, and the most used textile is cotton, which is natural cellulosic fiber. Unfortunately, it does not provide significant UV-shielding; this property can be improved by loading UV-shielding onto cotton fibers like nanoparticles [61]. Spherical, multi-petal, and rod ZnO-loaded cotton fabric were reported. The fiber coated by spherical and multi-petals-shaped ZnO shows excellent UV-shielding properties and good antibacterial activity, but the ZnO shape shows no considerable effect on antibacterial properties [62]. In another trial, Gorjanc et al. prepared cellulosic fibers with high UV protection by treating cellulosic fibers with moist CF4 plasma and functionalization with nano-ZnO. The prolonged plasma treatment agglomerated the ZnO nanoparticles and reduced the blocking effect. The optimum blocking with good distribution was obtained with plasma treatment for 10 s, with very high protection factor values (50+) [63]. In addition, graphene oxide (GO) was incorporated into cellulose to develop films with UV shielding, GO is capable of absorbing UV radiation due to its conjugated aromatic and planar structures. It was found that increasing the GO concentration increased the UV-shielding and decreased the transparency of visible-light. The films with 2 wt% GO possessed outstanding absorbance and showed complete UV-shielding (~99%) in both the UV-A and UV-B regions [64].
One imported cellulose form is the cellulose nanocrystals; the influence of cellulose nanocrystals on the physicochemical properties of sustainable chitosan biodegradable film was studied by Yadav et al. [65]. They found that the light absorption increased with increasing cellulose nanocrystals due to their 3D structure. Furthermore, cellulose nanocrystals blocked UV light, creating films resistant to UV wavelengths. The UV/visible light transmittance decreased from 94.62% to 61.17% with increasing cellulose nanocrystals from 0–8 wt% due to their agglomeration in the chitosan matrix. The results of the shielding effect at UV-B (280–320 nm), UV-A (320–400 nm), and visible regions (380–700 nm) showed that the cellulose nanocrystal conferred chitosan high barrier properties, resulting in enhanced UV light resistance (Fig. 8).
Figure 8: (A) UV transmittance curve with digital image of fabricated films, (B) blocking effect of UV at different wavelengths for films (Abbreviations; CNC = Cellulose nanocrystal) (Reprinted from reference [65] with permission from Polymers, MDPI, Copyright © [2020])
Chemical modification of cellulose nanocrystals can also improve their UV-shielding efficiency, Mendoza et al. grafted cellulose nanocrystals with phenolic esters such as diethyl ferulate via a click-type copper-catalyzed azide/alkyne cycloaddition reaction and added to a poly(vinyl alcohol) to form excellent photostability and UV-shielding films (Fig. 9). Films with 20 wt% grafted cellulose nanocrystals exhibited complete UV-shielding, 70%–90% transmittance in the visible region, and increased the modulus and tensile strength by 150% and 91%, respectively, relative to neat poly(vinyl) alcohol. As authors reported, the grafted cellulose nanocrystals pointedly aid the dispersion of the phenolic diester in the aqueous poly(vinyl) alcohol, which was not achieved with diethyl ferulate [66]. Poly(cinnamoyloxy ethyl methacrylate) was grafted on cellulose nanocrystals via the surface-initiated atom transfer radical polymerization technique and incorporated into poly(vinyl chloride) giving transparent and UV-shielding films. Adding grafted cellulose nanocrystals enhanced the films’ mechanical properties and their thermal stability. Even after UV radiation, films demonstrated exceptional UV-shielding characteristics (Fig. 10) [67].
Figure 9: Schematic representation of the UV blocking and reinforcing effect of grafted cellulose nanocrystals by diethyl ferulate (20 wt%) in poly(vinyl) alcohol (Abbreviations, poly (vinyl) alcohol = PVA, diethyl ferulate = DEF, and cellulose nanocrystals = CNC) (Reprinted from reference [66] with permission from ACS Sustainable Chemistry & Engineering, American Chemical Society, Copyright © [2021])
Figure 10: Schematic representation depicting the UV-filtering and reinforcing effect of grafted cellulose nanocrystals in poly(vinyl chloride) before and after heat annealing (Abbreviations, poly(vinyl chloride) = PVC, poly(cinnamoyloxy ethyl methacrylate) = PCEM, and cellulose nanocrystals = CNC) (Reprinted from reference [67] with permission from ACS Applied Nano Materials, American Chemical Society, Copyright © [2018])
Also cellulose nanocrystals were esterified with cinnamoyl chloride and displayed film with high transmittance of visible light and a substantial absorption of UV radiation. Accordingly, cinnamoyl cellulose nanocrystals can be used as reinforcing nanofillers and UV-shielding in hydrophobic and hydrophilic polymer matrices. So, by incorporating cinnamoyl cellulose nanocrystals into poly(vinyl) alcohol and polystyrene films, they displayed excellent UV-shielding and enhanced their Young’s moduli [68]. In another trial, naringin blended with microcrystalline cellulose gave UV-shielding, especially UV-B and transparent bioplastics films behind, antibacterial and antioxidant properties. UV-blocking was ~77%–88% and ~99.8%–100% in the UV-A and UV-B regions, respectively (Fig. 11). These can be explained as related to the naringin aromatic structure that can absorb UV radiation and prevent UV transmission from the outside [69].
Figure 11: UV radiation blocking as a function of naringin content
Carboxymethyl cellulose/polydopamine-modified palygorskite nanocomposite films were prepared by Huang et al. These films blocked the UV below 300 nm and retained their relatively high transparency in the visible spectrum. Also, the strong interfacial interaction between polydopamine-modified palygorskite and carboxymethyl cellulose enhanced the water resistance and mechanical properties. However, increasing the dopamine during the modification weakened the water resistance and mechanical properties due to the adhering of the individual fibrous crystals and forming a small bundle through the excessive polydopamine [70]. Loading of nanoparticles onto carboxymethyl cellulose enhanced its UV-shielding efficiency, as loading of CuO nanoparticles onto carboxymethyl cellulose films reduced the light transmittance in both the UV and visible light bands; thus, they can be used as UV-shielding. This can be referred to the reduction of the optical bandgap of the host matrix by CuO nanoparticles [71]. Badry et al. reported that adding CuO@ZnO core/shell nanoparticles loaded carboxy methyl cellulose onto sunblock showed a high blocking capacity for UV radiation. Adding 4 wt% CuO@ZnO core/shell to the carboxymethyl cellulose matrix significantly decreased transmittance in both the UV and visible regions, with approximately 100% of UV light being absorbed (Table 2) [72].
Owing to the excellent optical transparency of cellulose acetate, which is a thermoplastic biodegradable polymer, transparent and UV-shielding composite films based on GO and cellulose acetate were prepared by Moraes et al. Smooth and homogeneous films with well-dispersed GO throughout the cellulose acetate matrix appeared. Films with 0.5 wt% GO displayed 57% and 79% UV-shielding capacity and optical transparency under visible light, respectively, leading to potential applications as transparent UV-protective coatings in different applications [73].
Yu et al. mixed xylan and konjac glucomannan separately or simultaneously with TEMPO-oxidized cellulose nanofibers to form nanocomposite films. It was found that konjac glucomannan enhanced the mechanical properties of films, while Xylan increased the UV-blocking of the film. Therefore, adding mixed Xylan and konjac glucomannan onto cellulose nanofibers improved mechanical and UV-shielding properties. The transmittance of cellulose nanofibers and composite films was 86% at 600 nm and 52% at 325 nm, respectively, confirming the UV-shielding properties of composite film [74].
As packaging materials, hemicellulose and its derivatives have garnered much interest. It underwent carboxymethylation modification before combining with poly(vinyl) alcohol to create a composite film, 30 μm thick, using the solution casting technique. To give the film antibacterial properties, more potassium cinnamonate was added [75]. The composite films’ elongation at break was noticeably better than the poly(vinyl) alcohol film, demonstrating that interactions between polymers increased intermolecular forces. In the visible region, the light transmittance of pure poly(vinyl) alcohol film was about 90% and declined after the addition of carboxymethylation hemicellulose. With the addition of potassium cinnamate the light transmittance in the region of 200–300 nm was nearly zero this; can be referred to as the ability of phenolic compounds to absorb UV. Since UV–vis light could cause food oxidation, this high UV–vis resistance [76,77].
A thermoplastic flexible and UV-shielding hemicellulose films were prepared by esterification of hemicellulose with vinyl benzoate and reinforced with poly(vinyl) alcohol and ZnO-nano. The esterification process increased the solubility of hemicellulose in dimethyl formamide and dimethyl sulfoxide and transformed it to a crystalline nature. The film with 1% ZnO exhibited good flexibility, moderate tensile strength, and excellent UV-shielding with blocking of UV-A and UV-B by 99.34% and 99.99%, respectively. The film network structure, referred to as the driving force of the film component miscibility resulting from the hydrogen bonding interactions in the components, facilitates the uniform insertion of ZnO-nano in the matrix [78].
Xylan, as the major component of hemicellulose, was used for the preparation of hydrogels with superior UV-shielding (~99.96%), excellent mechanical properties such as stretchability >4000% and compressibility, and good adhesion underwater and in air prepared by Chang et al. [38]. These hydrogels were fabricated through radical polymerization of poly(acrylic acid) (-COO), quaternized xylan (-N+(CH3)3), and tannic acid (catechol group), which resembled amino acids with negative and positive charges endowed the underwater adhesion. This adhesion is due to the synergistic interactions of hydrogen bonding, catechol, and electrostatic interaction, which could stick to various substrates. These hydrogels can be used as a wearable sensor to monitor human and even subtle motions. Also, a low-cost, green self-catalyst sulfonated lignin, and Fe3+ system was used to fabricate UV-shielding (99%), transparent (85.37%), elastic, and conductive hydrogel. This hydrogel was prepared by graft polymerization of polyacrylamide on the carboxymethyl xylan at room temperature without removing oxygen in 5 min. Potassium persulfate was used as an initiator, and Fe3+ as a physical cross-linker, which can form coordination bonds with carboxymethyl xylan. The double network structure formed between Fe3+ and carboxymethyl xylan leads to high tensile stress (23 kPa) and charming extension ratio [79] (460%).
Different forms (molecular weight, lignin content, and substitution of loblolly pine hemicellulose-poly(vinyl) alcohol composite films were investigated as UV-shielding by Pan et al. [80]. The results found that hemicelluloses with high substitution, molecular weight, and lignin content enhanced the compatibility with the poly(vinyl) alcohol and improved the film’s mechanical properties. The highly substituted branched hemicellulose increased the film’s density and thermal stability. In addition, the shielding ability increased with highly branched and lignin-content hemicellulose.
The unsaturated functional groups of lignin, such as carbon-carbon double bonds, conjugated carbonyl, and aromatic rings, are the main light absorbers of lignin, making its color brownish to black. Fig. 12 shows different chromophore groups’ UV and visible light absorption with their wavelength absorptions [81]. By chromophore functional groups of lignin, it can absorb UV light in the range of 250–400 nm. Consequently, it is used in modified and non-modified forms to enhance UV-shielding, such as cream, paints, transparent film, and varnishes. Blending lignin with other UV-shielding indicated synergic effects and increased final UV-shielding potential. However, the challenge is the brownish color, its complex structure, impurities, and polydispersity in molecular weight. Accordingly, more research is required to determine an ideal natural UV-shielding [82].
Figure 12: UV and visible light absorption by different chromophore groups (Reprinted from reference [82] with permission from Polymers, MDPI, Copyright © [2020])
Excellent antimicrobial and mechanical properties with a sun protection factor of up to 45 lignin films were reported. Adding 0.5 to 1.5 wt% lignin in a gelatin matrix increased the sun protection factor from 7 (zero lignin) to 39.0–44.6. These films were prepared using a bio-based ionic liquid, choline citrate, which stabilized homogeneous gelatin–lignin [83]. The preparation of biodegradable composite films from agar and alkali lignin has also been reported. Incorporating lignin increased the UV-shielding, thermostability, and tensile strength properties, while the moisture content and swelling ratio decreased with increasing lignin content [84]. Also, lignin can be stabilized by crosslinking with polyvinyl alcohol so that it will be stable in an aqueous media; alkali lignin with poly(vinyl) alcohol as electro-spun fibers and have excellent UV-shielding and antimicrobial properties were reported [85]. Lignin was blended with a polyvinyl alcohol without dramatically affecting its transparency. Lignin increased the UV-shielding performance and enhanced the films’ mechanical, thermal, and barrier properties [86]. To avoid the agglomeration of lignin in the host matrix, Huang et al. prepared lignin nanospheres. They incorporated them into polyvinyl alcohol via mechanical blending to prepare excellent UV-shielding and visible-transparent films. The well-distributed nanospheres in the matrix are due to the formation of hydrogen bonds between lignin and the host matrix. Also, adding lignin nanospheres enhanced the thermal stability and tensile strength. The UV-B (320–275 nm) and UV-C (275–200 nm) were wholly shielded, while UV-A (400–320 nm) was shielded with 4 wt% lignin [87]. Also, lignin surface modification improves its distribution in the host matrix. For example, Cao et al. functionalized lignin with polyhedral oligomeric silsesquioxanes to improve its dispersion in a polylactide matrix. With 5 wt% lignin-silsesquioxanes, the composite film absorbed all UV-spectrum [11]. Monodisperse lignin nanoparticle (diameter = 204 nm) was synthesized by acoustic irradiation of aqueous alkali lignin and incorporated into poly(vinyl) alcohol, resulting in thin and flexible nanocomposite films. Its 2.5 wt% improved the film’s mechanical properties and sun protection factor up to 26 relative to 0 of neat poly(vinyl) alcohol with visible light transmission above 75% [88].
A composite film of citric acid-modified lignin and poly(vinyl) alcohol was reported with lignin content from 0.5 to 10 wt%. The films had higher than 97.5% UV-shielding with excellent transparency. Also, films with modified lignin outperformed films with unmodified lignin in transparency and antioxidant properties [40]. Acetylated lignin/poly(lactic acid) film was prepared with transparent UV-shielding films (76% visual transmittance and over 40 UV protection factors) with balanced mechanical and optical properties. The acetylation of lignin compatibilizes the requirement of poly(lactic acid) [89]. Lignin grafted poly(lactic acid) was dispersed in poly(lactic acid), enhancing UV absorption and reducing brittleness without a sacrifice in the modulus of elasticity [90]. Lignin has been incorporated into poly(methyl methacrylate) and given a UV-shielding film, while the transparency was decreased by 26%. At 400 nm wavelength, the film with 1% lignin showed 60% UV-shielding capacity (40% transparency) [91]. This can be attributed to converting of phenolic hydroxyl groups into phenoxyl radicals and quinones under UV radiation. These quinones are oxidized into aliphatic acid structures, leading to the bleaching of lignin [92]. Liao et al. reported that dynamic vulcanization is a powerful tool for making lignin-polypropylene blends more compatible. The films presented high UV-shielding performance [93].
Loading of TiO2 nanoparticles onto lignin composite films was reported as TiO2 decorated lignin, which was prepared by hydrothermal method, was added to poly(propylene carbonate). The prepared films show a uniform dispersion of TiO2@lignin in the matrix with good miscibility and a high UV-shielding effect. Film containing 5 wt% TiO2@lignin absorbed about 90% of UV light in the broad UV spectrum (200–400 nm) [94]. Lignin-based epoxy/titanium dioxide multifunctional bio-based films were synthesized from moso bamboo-derived lignin via liquid deposition. It was found that films had UV absorption, antibacterial activates, a stable topological surface structure, homogeneity, and good dispersion [95].
This section will give examples of using cellulosic derivatives with lignin as UV-shielding materials. Rukmanikrishnan et al. prepared a sustainable composite that is flexible and translucent with a slight brown film by mixing gellan gum, 2-hydroxyethyl cellulose, and lignin. The prepared films showed high UV protection, with almost 100% and 90% protection against UV-B (280–320 nm) and UV-A (320–400 nm), respectively. The surface hydrophobicity of the composite films increased with the addition of lignin. Also, they found that incorporating of lignin improved the films’ thermal, mechanical, and hydrophobic properties [96]. Also, UV-shielding, semitransparent, and flexible films were prepared from Azide-modified cellulose with lignin by the Cu(I)-catalyzed 1,3-dipolar cycloaddition reaction. The film with 2% lignin showed around 100% and 90% UV-B (280−320 nm) and UV-A (320−400 nm) protection, respectively, with stability against elevated temperature at 120°C (Fig. 13) [97].
Figure 13: Synthesis route of cellulose-lignin conjugate. (Abbreviations, Azid Cellulose = MCC_Az and Propargylated lignin = Lignin-Pr) (Reprinted from reference [97] with permission from ACS Sustainable Chemistry & Engineering, American Chemical Society, Copyright © [2017])
Parit et al. incorporated alkaline and softwood kraft lignin onto cellulose nanocrystals (1–10 wt%) to produce homogenous, transparent, and UV-shielding films. From Fig. 14a, it is clear that the UV-shielding effect of softwood kraft lignin was higher than that of alkaline lignin, with 1 wt% lignin content, the film with softwood kraft lignin wholly blocked, whereas with alkaline lignin partially blocked UV-C (200–280 nm) spectrum. Using 10 wt%, both lignins provided films with complete UV-shielding, but the visible light transmittance of the film with alkali lignin was slightly higher than that of the film with softwood kraft lignin. Acetylation of lignin reduced lignin color, improving transmittance without significant effect of UV- shielding (Fig. 14b) [98].
Figure 14: UV–vis transmission spectra of films with various lignin concentrations (a) and 10 wt% softwood kraft lignin and acetylated lignin (b) (Abbreviations; cellulose nanocrystals = CNC, softwood kraft lignin = SKL, acetylated lignin = Ac-SKL) (Reprinted from reference [98] with permission from ACS Omega, American Chemical Society, Copyright © [2018])
UV-shielding, flexible, and intense film was prepared from wood cellulose skeleton, lignin nanoparticles, and poly(vinyl) alcohol. Incorporating lignin improved the thermal stability, decreased the water absorption by 30%, and blocked over 98% of UV light [99]. At 500 nm, the polyvinyl alcohol and polyvinyl alcohol/ cellulose films exhibited high light transmittance such as 72.6% and 37.5%, respectively. With increasing lignin content, the light transmittance in the visible region (400–800 nm) was decreased due to the lignin color, and with >4 wt%, the light transmittance was lower than 20%. This is consistent with Huang et al., that a film of cellulose nanocrystal with 10% lignin nanoparticles blocked 91.5% and 99.9% of UV-A and UV-B light, respectively [100]. Also, lignin was incorporated into the carboxymethyl cellulose, and lignin was found to enhance the UV-A blocking. With 0.2% (w/v) lignin, a complete UV-A and UV-B blocking were observed, reducing the transparency [101]. The film of cellulose nanofiber with 20% wt% of lignin using epichlorohydrin as a crosslinker blocked > 99% of UV-A and UV-B with a water contact angle of 110.38° [102].
There are different processing techniques for designing UV-shielding materials as follows: the 1st one is solution casting which is an easy technique for fabricating thin film for UV-shielding applications by dissolving the polymer composite in a volatile solvent. After the evaporation of the solvent, a thin film is obtained [103]. The 2nd is Spin coating, another method for fabricating UV-shielding thin film in the micro- to nanometer range. The film thickness depends on the evaporation rate of the solvent and outward fluid flow [104]. The 3rd is the electrospinning technique for fabricating composite fibers with micro- to nano-diameters for UV-shielding. The polymer solution is prepared by dissolving it in a solvent and electrospunting it at an optimized flow rate, voltage, and spinneret tip-collector distance. Upon the application of an electric field, the solvent evaporates, and electrospun fibers are formed [105]. The 4th is the covalent and noncovalent interactions, as the composite can be tuned by noncovalent or covalent modification of the nanofillers. The self-assembly of lignin nanospheres via π–π interactions resulted in an improved UV-shielding effect [106]. Finally, in melt processing, the solution casting technique improves the filler dispersion in the polymer matrix, but using toxic solvents limits its application. In this case, melt processing is preferred for fabricating UV-shielding materials [107].
UV-shielding films are frequently used in many industries, including packaging, electronics, construction, and automobiles. Their main uses include UV-shielding, weather resistance, chemical resistance, and durability. The UV industrial film industry’s market analysis indicates an optimistic growth forecast. The market is expanding due to growing consumer demand from end-use sectors, including electronics and automobiles, as well as increasing awareness of the damaging effects of UV radiation on materials and people. Furthermore, the market is anticipated to increase due to the expanding trend of environmentally and energy-friendly materials. There is fierce competition among the major competitors in the UV-shielding industrial film market, who all provide cutting-edge products. In the upcoming years, the market for UV-shielding film will continue to rise due to the growing need for UV-shielding and the expansion of its applications in various industries. The worldwide market for UV-shielding was estimated at USD 1.5 billion in 2022 and is expected to reach approximately USD 2.72 billion by 2032.
There are many factors for growing the market of UV-shielding films, such as:
• Growing end-use industries: To improve product durability and aesthetics, the construction, automotive, agricultural, and packaging industries drive the market’s expansion. These industries have a growing need for UV-shielding materials.
• Environmental restrictions: As environmental awareness and UV-shielding increase, research into sustainable formulas and eco-friendly alternatives is sparked, opening up new avenues for innovation.
• UV-shielding packaging: The requirement to preserve product quality during storage and transit has accelerated the trend toward UV-shielding packaging materials, particularly in the food and beverage industry.
• Nano-additives: Better UV-shielding is provided by the use of nanotechnology in the development of very effective UV-shielding, which also increases their efficacy and adaptability.
• Renewable energy: The market for UV-shielding has benefited from the growing demand for renewable energy sources, such as solar panels, which drives the requirement for UV-shielding materials to resist extended exposure to sunshine.
• Eco-friendly solutions: Products that adhere to strict environmental laws, bio-based substitutes, and sustainable UV-shielding are becoming increasingly prevalent in the sector.
• Emerging markets: The demand for UV-shielding is driven by the quick industrialization of these nations and the growing appeal of outdoor gear.
• Innovation: Businesses that innovate and create cutting-edge UV-shielding with better performance and less environmental impact have a lot of opportunities.
• Global expansion: Due to the expansion of numerous end-use sectors, UV-shielding is becoming more widely available globally, creating opportunities for joint ventures and market growth.
• Eco-friendly products: Companies can reach ecologically sensitive market groups by concentrating on sustainable and eco-friendly UV-shielding formulas.
• Technological developments: By providing better solutions for various applications, ongoing developments in UV-shielding technology, such as increased efficiency and performance, propel market expansion.
6 Conclusion, Limitations and Future Perspectives
• Humans benefit from sunlight in many ways, including increased vitamin D production and expression of β-endorphins, enhancing well-being. On the other hand, photoaging, solar sunburn, hyperpigmentation, skin photosensitization, and skin cancer are all caused by overexposure to sunlight. Sunscreens contain ultraviolet filters to shield the skin from the damaging effects of ultraviolet light. With the drawbacks mentioned above in mind, scientists have directed their efforts toward developing novel UV filters. Creating polymeric materials that can be used in harsh UV radiation conditions requires careful consideration of selected materials.
• Wood is the ideal material to take into consideration for the circular economy because it is a naturally occurring resource that is readily available in massive amounts and is simple to create. Its significance has grown significantly in the last several years. Alongside this rise, new research is being developed, creating new opportunities in wood by-products. This review discussed using wood by-products for UV-shielding agents to protect humans from UV rays. Various topics include the wood structure and its constituents and the UV-shielding effect of various. However, the valorization of wood by-products is still a big challenge, and commercialization will only be accessible if price competitiveness is overcome. But as society increasingly realizes that the environment must come before material values, it is currently working toward the goals of sustainable development and carbon neutrality. While price competition with current UV-shielding agents presents considerable challenges, the recent shift in consumer awareness points to a promising outcome. Even with their higher price tags, more and more customers are choosing eco-friendly and human-friendly items as their quality of life increases. Furthermore, a social climate that considers the product’s inherent value in addition to social and environmental considerations would make it very evident how we should proceed.
• Lignin can be used as a natural ingredient UV-shielding in modified and non-modified forms. It enhances the UV-shielding of commercial products with less than a 10% blend with other materials. In mixed with synthetic UV blockers, it increases the final UV-shielding potential and indicates synergic effects. Due to the complex structure, brownish color, polydispersity in molecular weight, and lignin impurities, more research is required to make it an ideal bio-based UV-shielding.
• Inorganic nanomaterials have excellent UV-shielding properties. However, their disadvantages are their agglomeration of unmodified polymer matrix, poor visible light transparency of composites containing GO, their photocatalytic effect, and potential photocarcinogenic effects.
Acknowledgement: The authors appreciate the National Research Center, Egypt for the financial support of this research activity.
Funding Statement: This research received no external funding.
Author Contributions: Authors have the same contribution in conceptualization, draft preparation, writing, and editing. All authors have read and agreed to the published version of the manuscript.
Availability of Data and Materials: Not applicable.
Conflicts of Interest: The authors declare no conflict of interest to report regarding the present study.
References
1. Matsumura Y, Ananthaswamy HN. Toxic effects of ultraviolet radiation on the skin. Toxicol Appl Pharm. 2004;195(3):298–308. [Google Scholar]
2. Owens DM, Watt FM. Contribution of stem cells and differentiated cells to epidermal tumours. Nat Rev Cancer. 2003;3(6):444–51 [Google Scholar] [PubMed]
3. Gerlock J, Kucherov A, Smith C. Determination of active HALS in automotive paint systems II: HALS distribution in weathered clearcoat/basecoat paint systems. Polym Degrad Stabil. 2001;73(2):201–10. [Google Scholar]
4. Chen H, Li R, Xu X, Zhao P, Wong DS, Chen X, et al. Citrate-based fluorophores in polymeric matrix by easy and green in situ synthesis for full-band UV shielding and emissive transparent display. J Mater Sci. 2019;54(2):1236–47. [Google Scholar]
5. Hashim A, Hamad Z. Lower cost and higher UV-absorption of polyvinyl alcohol/silica nanocomposites for potential applications. Egypt J Chem. 2020;63(2):461–70. [Google Scholar]
6. Hattori H, Ide Y, Sano T. Microporous titanate nanofibers for highly efficient UV-protective transparent coating. J Mater Chem A. 2014;2(39):16381–8. [Google Scholar]
7. He H, Li A, Li S, Tang J, Li L, Xiong L. Natural components in sunscreens: topical formulations with sun protection factor (SPF). Biomed Pharmacother = Biomedecine & Pharmacotherapie. 2020;134:111161. [Google Scholar]
8. Liu X, Li T, Hu C, Wang Y, Li G, Dong W, et al. Using novel polymer microspheres as an efficient UV filter and blue light converter for constructing multifunctional transparent polyvinyl alcohol films. Colloids Surf A: Physicochem Eng Asp. 2023;666:131236. [Google Scholar]
9. Serpone N, Dondi D, Albini A. Inorganic and organic UV filters: their role and efficacy in sunscreens and suncare products. Inorg Chim Acta. 2007;360(3):794–802. [Google Scholar]
10. Schneider SL, Lim HW. A review of inorganic UV filters zinc oxide and titanium dioxide. Photodermatol Photo. 2019;35(6):442–6. [Google Scholar]
11. Cao X, Huang J, He Y, Hu C, Zhang Q, Yin X, et al. Biodegradable and renewable UV-shielding polylactide composites containing hierarchical structured POSS functionalized lignin. Int J Biol Macromol. 2021;188:323–32 [Google Scholar] [PubMed]
12. Zeng Y, He X, Ma Z, Gou Y, Wei Y, Pan S, et al. Coral-friendly and non-transdermal polymeric UV filter via the Biginelli reaction for in vivo UV protection. Cell Rep Phys Sci. 2023;4(3):101308. [Google Scholar]
13. Zhu S, Biswas SK, Qiu Z, Yue Y, Fu Q, Jiang F, et al. Transparent wood-based functional materials via a top-down approach. Prog Mater Sci. 2023;132:101025. [Google Scholar]
14. Lievonen M, Valle-Delgado JJ, Mattinen ML, Hult EL, Lintinen K, Kostiainen MA, et al. A simple process for lignin nanoparticle preparation. Green Chem. 2016;18(5):1416–22. [Google Scholar]
15. Hu W, Xiang R, Lin J, Cheng Y, Lu C. Lignocellulosic biomass-derived carbon electrodes for flexible supercapacitors: an overview. Mater. 2021;14(16):4571. [Google Scholar]
16. Lobo FCM, Franco AR, Fernandes EM, Reis RL. An overview of the antimicrobial properties of lignocellulosic materials. Molecules. 2021;26(6):1749 [Google Scholar] [PubMed]
17. Cruz JM, Domínguez JM, Domínguez H, Parajó JC. Antioxidant and antimicrobial effects of extracts from hydrolysates of lignocellulosic materials. J Agr Food Chem. 2001;49(5):2459–64. [Google Scholar]
18. Li W, Cheng G, Wang S, Jiang Y, Liu X, Huang Q. Bifunctional lignocellulose nanofiber hydrogel possessing intriguing pH-responsiveness and self-healing capability towards wound healing applications. Int J Biol Macromol. 2024;260(1):129398 [Google Scholar] [PubMed]
19. Cai S, Han H, Lou Z, Yan H, Wang Q, Li R, et al. Preparation of a biomass-derived electromagnetic wave absorber with potential EM shielding application in interior decoration surface coating. Appl Surf Sci. 2023;607:155037. [Google Scholar]
20. Dacrory S, Kamel S, Turky G. Development of dielectric film based on cellulose loaded nano-silver and carbon for potential energy storage. ECS J Solid State Sci Technol. 2021;10(12):123004. [Google Scholar]
21. Kamel S, Khattab TA. Recent advances in cellulose-based biosensors for medical diagnosis. Biosensors. 2020;10(6):67 [Google Scholar] [PubMed]
22. Asada C, Yoshida Y, Nakamura Y. Efficient conversion of moso bamboo components into glucose, lignocellulose nanofiber, and low-molecular-weight lignin through deep eutectic solvent treatment. Biomass Convers Biorefin. 2023;13(9):7713–24. [Google Scholar]
23. Sabaruddin FA, Megashah LN, Shazleen SS, Ariffin H. Emerging trends in the appliance of ultrasonic technology for valorization of agricultural residue into versatile products. Ultrason Sonochem. 2023;99:106572 [Google Scholar] [PubMed]
24. Zhou M, Lv M, Cai S, Tian X. Effects of enzymatic hydrolysis and physicochemical properties of lignocellulose waste through different choline based deep eutectic solvents (DESs) pretreatment. Ind Crop Prod. 2023;195:116435. [Google Scholar]
25. Asem M, Jimat DN, Jafri NHS, Nawawi WMFW, Azmin NFM, Abd Wahab MF. Entangled cellulose nanofibers produced from sugarcane bagasse via alkaline treatment, mild acid hydrolysis assisted with ultrasonication. J King Saud Univ Eng Sci. 2023;35(1):24–31. [Google Scholar]
26. Chahal S, Kumar A, Hussian FSJ. Development of biomimetic electrospun polymeric biomaterials for bone tissue engineering. A review. J Biomater Sci Polym Ed. 2019;30(14):1308–55 [Google Scholar] [PubMed]
27. Roy D, Semsarilar M, Guthrie JT, Perrier S. Cellulose modification by polymer grafting: a review. Chem Soc Rev. 2009;38(7):2046–64 [Google Scholar] [PubMed]
28. Qiu X, Hu S. “Smart” materials based on cellulose: a review of the preparations, properties, and applications. Mater. 2013;6(3):738–81. [Google Scholar]
29. Toshikj E, Tarbuk A, Grgić K, Mangovska B, Jordanov I. Influence of different oxidizing systems on cellulose oxidation level: introduced groups versus degradation model. Cellul. 2019;26:777–94. [Google Scholar]
30. Abou-Zeid RE, Dacrory S, Ali KA, Kamel S. Novel method of preparation of tricarboxylic cellulose nanofiber for efficient removal of heavy metal ions from aqueous solution. Int J Biol Macromol. 2018;119:207–14 [Google Scholar] [PubMed]
31. Coseri S, Biliuta G, Zemljič LF, Srndovic JS, Larsson PT, Strnad S, et al. One-shot carboxylation of microcrystalline cellulose in the presence of nitroxyl radicals and sodium periodate. RSC Adv. 2015;5(104):85889–97. [Google Scholar]
32. Andersson C. New ways to enhance the functionality of paperboard by surface treatment—a review. Packag Technol Sci Int J. 2008;21(6):339–73. [Google Scholar]
33. Grishkewich N, Mohammed N, Tang J, Tam KC. Recent advances in the application of cellulose nanocrystals. Curr Opin Colloid Interface Sci. 2017;29:32–45. [Google Scholar]
34. Vickers NJ. Animal communication: when i’m calling you, will you answer too? Curr Biol. 2017;27(14):R713–5 [Google Scholar] [PubMed]
35. Elkihel A, Christie C, Vernisse C, Ouk TS, Lucas R, Chaleix V, et al. Xylan-based cross-linked hydrogel for photodynamic antimicrobial chemotherapy. ACS Appl Bio Mater. 2021;4(9):7204–12 [Google Scholar] [PubMed]
36. Ai J, Li K, Li J, Yu F, Ma J. Super flexible, fatigue resistant, self-healing PVA/xylan/borax hydrogel with dual-crosslinked network. Int J Biol Macromol. 2021;172:66–73 [Google Scholar] [PubMed]
37. Wang Q, Xu W, Koppolu R, van Bochove B, Seppälä J, Hupa L, et al. Injectable thiol-ene hydrogel of galactoglucomannan and cellulose nanocrystals in delivery of therapeutic inorganic ions with embedded bioactive glass nanoparticles. Carbohyd Polym. 2022;276:118780 [Google Scholar] [PubMed]
38. Chang M, Liu X, Lin Q, Li W, Wang X, Ren J. A highly stretchable, UV resistant and underwater adhesive hydrogel based on xylan derivative for sensing. Int J Biol Macromol. 2022;220:1084–94 [Google Scholar] [PubMed]
39. Gong X, Fu C, Alam N, Ni Y, Chen L, Huang L, et al. Tannic acid modified hemicellulose nanoparticle reinforced ionic hydrogels with multi-functions for human motion strain sensor applications. Ind Crop Prod. 2022;176:114412. [Google Scholar]
40. He X, Luzi F, Hao X, Yang W, Torre L, Xiao Z, et al. Thermal, antioxidant and swelling behaviour of transparent polyvinyl (alcohol) films in presence of hydrophobic citric acid-modified lignin nanoparticles. Int J Biol Macromol. 2019;127:665–76 [Google Scholar] [PubMed]
41. Hu N, Chen D, Guan Q, Peng L, Zhang J, He L, et al. Preparation of hemicellulose-based hydrogels from biomass refining industrial effluent for effective removal of methylene blue dye. Environ Technol. 2022;43(4):489–99 [Google Scholar] [PubMed]
42. Sun XF, Xie Y, Shan S, Li W, Sun L. Chemically-crosslinked xylan/graphene oxide composite hydrogel for copper ions removal. J Polym Environ. 2022;30(9):3999–4013. [Google Scholar]
43. Sun R, Fang JM, Tomkinson J. Characterization and esterification of hemicelluloses from rye straw. J Agr Food Chem. 2000;48(4):1247–52. [Google Scholar]
44. Sun R, Fang J, Tomkinson J, Geng Z, Liu J. Fractional isolation, physico-chemical characterization and homogeneous esterification of hemicelluloses from fast-growing poplar wood. Carbohyd Polym. 2001;44(1):29–39. [Google Scholar]
45. Nypelö T, Laine C, Aoki M, Tammelin T, Henniges U. Etherification of wood-based hemicelluloses for interfacial activity. Biomacromolecules. 2016;17(5):1894–901. [Google Scholar]
46. Ren JL, Sun RC, Liu CF. Etherification of hemicelluloses from sugarcane bagasse. J Appl Polym Sci. 2007;105(6):3301–8. [Google Scholar]
47. Dong L, Hu H, Yang S, Cheng F. Grafted copolymerization modification of hemicellulose directly in the alkaline peroxide mechanical pulping (APMP) effluent and its surface sizing effects on corrugated paper. Ind Eng Chem Res. 2014;53(14):6221–9. [Google Scholar]
48. Farhat W, Venditti R, Ayoub A, Prochazka F, Fernández-de-Alba C, Mignard N, et al. Towards thermoplastic hemicellulose: chemistry and characteristics of poly-(ε-caprolactone) grafting onto hemicellulose backbones. Mater Design. 2018;153:298–307. [Google Scholar]
49. Xu Y, Liu K, Yang Y, Kim MS, Lee CH, Zhang R, et al. Hemicellulose-based hydrogels for advanced applications. Front Bioeng Biotechnol. 2023;10:1110004 [Google Scholar] [PubMed]
50. Vishtal A, Kraslawski A. Challenges in industrial applications of technical lignins. BioResources. 2011;6(3):3547–68. [Google Scholar]
51. Ma C, Kim TH, Liu K, Ma MG, Choi SE, Si C. Multifunctional lignin-based composite materials for emerging applications. Front Bioeng Biotechnol. 2021;9:708976 [Google Scholar] [PubMed]
52. Beaucamp A, Wang Y, Culebras M, Collins MN. Carbon fibres from renewable resources: the role of the lignin molecular structure in its blendability with biobased poly(ethylene terephthalate). Green Chem. 2019;21(18):5063–72. [Google Scholar]
53. Culebras M, Geaney H, Beaucamp A, Upadhyaya P, Dalton E, Ryan KM, et al. Bio-derived carbon nanofibres from lignin as high-performance Li-Ion anode materials. ChemSusChem. 2019;12(19):4516–21 [Google Scholar] [PubMed]
54. Qu R, Zhang W, Liu N, Zhang Q, Liu Y, Li X, et al. Antioil Ag3PO4 nanoparticle/polydopamine/Al2O3 sandwich structure for complex wastewater treatment: dynamic catalysis under natural light. ACS Sustain Chem Eng. 2018;6(6):8019–28. [Google Scholar]
55. Karunarathna MS, Smith RC. Valorization of lignin as a sustainable component of structural materials and composites: advances from 2011 to 2019. Sustainability. 2020;12(2):734. [Google Scholar]
56. Baseer RA, Dacrory S, El Gendy MA, Ewies EF, Kamel S. A biodegradable film based on cellulose and thiazolidine bearing UV shielding property. Sci Rep. 2022;12(1):7887 [Google Scholar] [PubMed]
57. Kamel S. Recent development of cellulose/TiO2 composite in water treatment. Egypt J Chem. 2022;65(131):601–12. [Google Scholar]
58. Feng X, Zhao Y, Jiang Y, Miao M, Cao S, Fang J. Use of carbon dots to enhance UV-blocking of transparent nanocellulose films. Carbohyd Polym. 2017;161:253–60 [Google Scholar] [PubMed]
59. Tu K, Wang Q, Lu A, Zhang L. Portable visible-light photocatalysts constructed from Cu2O nanoparticles and graphene oxide in cellulose matrix. J Phys Chem C. 2014;118(13):7202–10. [Google Scholar]
60. Wang W, Zhang B, Jiang S, Bai H, Zhang S. Use of CeO2 nanoparticles to enhance UV-shielding of transparent regenerated cellulose films. Polym. 2019;11(3):458. [Google Scholar]
61. Montazer M, Maali Amiri M. ZnO nano reactor on textiles and polymers: ex situ and in situ synthesis, application, and characterization. J Phys Chem B. 2014;118(6):1453–70 [Google Scholar] [PubMed]
62. Sricharussin W, Threepopnatkul P, Neamjan N. Effect of various shapes of zinc oxide nanoparticles on cotton fabric for UV-blocking and anti-bacterial properties. Fiber Polym. 2011;12:1037–41. [Google Scholar]
63. Gorjanc M, Jazbec K, Šala M, Zaplotnik R, Vesel A, Mozetič M. Creating cellulose fibres with excellent UV protective properties using moist CF4 plasma and ZnO nanoparticles. Cellul. 2014;21:3007–21. [Google Scholar]
64. Ahmed A, Adak B, Bansala T, Mukhopadhyay S. Green solvent processed cellulose/graphene oxide nanocomposite films with superior mechanical, thermal, and ultraviolet shielding properties. ACS Appl Mater Inter. 2019;12(1):1687–97. [Google Scholar]
65. Yadav M, Behera K, Chang YH, Chiu FC. Cellulose nanocrystal reinforced chitosan based UV barrier composite films for sustainable packaging. Polym. 2020;12(1):202. [Google Scholar]
66. Mendoza DJ, Browne C, Raghuwanshi VS, Mouterde LM, Simon GP, Allais F, et al. Phenolic ester-decorated cellulose nanocrystals as UV-absorbing nanoreinforcements in polyvinyl alcohol films. ACS Sustain Chem Eng. 2021;9(18):6427–37. [Google Scholar]
67. Zhang Z, Sèbe G, Wang X, Tam KC. UV-absorbing cellulose nanocrystals as functional reinforcing fillers in poly(vinyl chloride) films. ACS Appl Nano Mater. 2018;1(2):632–41. [Google Scholar]
68. Zhang Z, Zhang B, Grishkewich N, Berry R, Tam KC. Cinnamate-functionalized cellulose nanocrystals as UV-shielding nanofillers in sunscreen and transparent polymer films. Adv Sustain Syst. 2019;3(4):1800156. [Google Scholar]
69. Guzman-Puyol S, Hierrezuelo J, Benítez JJ, Tedeschi G, Porras-Vázquez JM, Heredia A, et al. Transparent, UV-blocking, and high barrier cellulose-based bioplastics with naringin as active food packaging materials. Int J Biol Macromol. 2022;209:1985–94 [Google Scholar] [PubMed]
70. Huang D, Zheng Y, Quan Q. Enhanced mechanical properties and UV shield of carboxymethyl cellulose films with polydopamine-modified natural fibre-like palygorskite. Appl Clay Sci. 2019;183:105314. [Google Scholar]
71. Badry R, El-Nahass MM, Nada N, Elhaes H, Ibrahim MA. Structural and UV-blocking properties of carboxymethyl cellulose sodium/CuO nanocomposite films. Sci Rep. 2023;13(1):1123 [Google Scholar] [PubMed]
72. Badry R, El-Nahass MM, Nada N, Elhaes H, Ibrahim MA. UV filters and high refractive index materials based on carboxymethyl cellulose sodium and CuO@ ZnO core/shell nanoparticles. Sci Rep. 2023;13(1):21159 [Google Scholar] [PubMed]
73. de Moraes ACM, Andrade PF, de Faria AF, Simões MB, Salomão FCCS, Barros EB, et al. Fabrication of transparent and ultraviolet shielding composite films based on graphene oxide and cellulose acetate. Carbohyd Polym. 2015;123:217–27 [Google Scholar] [PubMed]
74. Yu J, Zhu Y, Ma H, Liu L, Hu Y, Xu J, et al. Contribution of hemicellulose to cellulose nanofiber-based nanocomposite films with enhanced strength, flexibility and UV-blocking properties. Cellul. 2019;26:6023–34. [Google Scholar]
75. Abd El-All AS, Osman SA, Roaiah HM, Abdalla MM, Abd El Aty AA, AbdEl-Hady WH. Potent anticancer and antimicrobial activities of pyrazole, oxazole and pyridine derivatives containing 1,2,4-triazine moiety. Med Chem Res. 2015;24:4093–104. [Google Scholar]
76. Wang X, Yong H, Gao L, Li L, Jin M, Liu J. Preparation and characterization of antioxidant and pH-sensitive films based on chitosan and black soybean seed coat extract. Food Hydrocoll. 2019;89:56–66. [Google Scholar]
77. Yong H, Wang X, Bai R, Miao Z, Zhang X, Liu J. Development of antioxidant and intelligent pH-sensing packaging films by incorporating purple-fleshed sweet potato extract into chitosan matrix. Food Hydrocoll. 2019;90:216–24. [Google Scholar]
78. Zhang X, Luo W, Xiao N, Chen M, Liu C. Construction of functional composite films originating from hemicellulose reinforced with poly(vinyl alcohol) and nano-ZnO. Cellul. 2020;27:1341–55. [Google Scholar]
79. Li N, Sun D, Su Z, Hao X, Li M, Ren J, et al. Rapid fabrication of xylan-based hydrogel by graft polymerization via a dynamic lignin-Fe3+ plant catechol system. Carbohyd Polym. 2021;269:118306 [Google Scholar] [PubMed]
80. Pan H, Zheng B, Yang H, Guan Y, Zhang L, Xu X, et al. Effect of loblolly pine (Pinus taeda L.) hemicellulose structure on the properties of hemicellulose-polyvinyl alcohol composite film. Molecules. 2022;28(1):46 [Google Scholar] [PubMed]
81. Paulsson M, Parkås J. Light-induced yellowing of lignocellulosic pulps-mechanisms and preventive methods. BioResources. 2012;7(4):5995–6040. [Google Scholar]
82. Sadeghifar H, Ragauskas A. Lignin as a UV light blocker—a review. Polym. 2020;12(5):1134. [Google Scholar]
83. Mehta MJ, Kumar A. Ionic liquid stabilized Gelatin-Lignin films: a potential UV-shielding material with excellent mechanical and antimicrobial properties. Chem–Eur J. 2019;25(5):1269–74 [Google Scholar] [PubMed]
84. Shankar S, Reddy JP, Rhim JW. Effect of lignin on water vapor barrier, mechanical, and structural properties of agar/lignin composite films. Int J Biol Macromol. 2015;81:267–73 [Google Scholar] [PubMed]
85. Lee E, Song Y, Lee S. Crosslinking of lignin/poly(vinyl alcohol) nanocomposite fiber webs and their antimicrobial and ultraviolet-protective properties. Text Res J. 2019;89(1):3–12. [Google Scholar]
86. Shikinaka K, Nakamura M, Otsuka Y. Strong UV absorption by nanoparticulated lignin in polymer films with reinforcement of mechanical properties. Polym. 2020;190:122254. [Google Scholar]
87. Huang J, Guo Q, Zhu R, Liu Y, Xu F, Zhang X. Facile fabrication of transparent lignin sphere/PVA nanocomposite films with excellent UV-shielding and high strength performance. Int J Biol Macromol. 2021;189:635–40 [Google Scholar] [PubMed]
88. Edmundson DD, Gustafson RR, Dichiara AB. Sonochemical synthesis of lignin nanoparticles and their applications in poly(vinyl) alcohol composites. Int J Biol Macromol. 2024;254:127487 [Google Scholar] [PubMed]
89. Kim Y, Suhr J, Seo HW, Sun H, Kim S, Park IK, et al. All biomass and UV protective composite composed of compatibilized lignin and poly(lactic-acid). Sci Rep. 2017;7(1):43596. [Google Scholar]
90. Chung YL, Olsson JV, Li RJ, Frank CW, Waymouth RM, Billington SL, et al. A renewable lignin-lactide copolymer and application in biobased composites. ACS Sustain Chem Eng. 2013;1(10):1231–8. [Google Scholar]
91. Avelino F, de Oliveira DR, Mazzetto SE, Lomonaco D. Poly(methyl methacrylate) films reinforced with coconut shell lignin fractions to enhance their UV-blocking, antioxidant and thermo-mechanical properties. Int J Biol Macromol. 2019;125:171–80 [Google Scholar] [PubMed]
92. Lou H, Lai H, Wang M, Pang Y, Yang D, Qiu X, et al. Preparation of lignin-based superplasticizer by graft sulfonation and investigation of the dispersive performance and mechanism in a cementitious system. Ind Eng Chem Res. 2013;52(46):16101–9. [Google Scholar]
93. Liao J, Brosse N, Pizzi A, Hoppe S, Xi X, Zhou X. Polypropylene blend with polyphenols through dynamic vulcanization: mechanical, rheological, crystalline, thermal, and UV protective property. Polym. 2019;11(7):1108. [Google Scholar]
94. Wu W, Liu T, Deng X, Sun Q, Cao X, Feng Y, et al. Ecofriendly UV-protective films based on poly(propylene carbonate) biocomposites filled with TiO2 decorated lignin. Int J Biol Macromol. 2019;126:1030–6 [Google Scholar] [PubMed]
95. Yang J, Dai J, Liu X, Fu S, Zong E, Song P. A lignin-based epoxy/TiO2 hybrid nanoparticle for multifunctional bio-based epoxy with improved mechanical, UV absorption and antibacterial properties. Int J Biol Macromol. 2022;210:85–93 [Google Scholar] [PubMed]
96. Rukmanikrishnan B, Ramalingam S, Rajasekharan SK, Lee J, Lee J. Binary and ternary sustainable composites of gellan gum, hydroxyethyl cellulose and lignin for food packaging applications: biocompatibility, antioxidant activity, UV and water barrier properties. Int J Biol Macromol. 2020;153:55–62 [Google Scholar] [PubMed]
97. Sadeghifar H, Venditti R, Jur J, Gorga RE, Pawlak JJ. Cellulose-lignin biodegradable and flexible UV protection film. ACS Sustain Chem Eng. 2017;5(1):625–31. [Google Scholar]
98. Parit M, Saha P, Davis VA, Jiang Z. Transparent and homogenous cellulose nanocrystal/lignin UV-protection films. ACS Omega. 2018;3(9):10679–91 [Google Scholar] [PubMed]
99. Zhou Y, Han Y, Xu J, Han W, Gu F, Sun K, et al. Strong, flexible and UV-shielding composite polyvinyl alcohol films with wood cellulose skeleton and lignin nanoparticles. Int J Biol Macromol. 2023;232:123105 [Google Scholar] [PubMed]
100. Huang C, Dong H, Zhang Z, Bian H, Yong Q. Procuring the nano-scale lignin in prehydrolyzate as ingredient to prepare cellulose nanofibril composite film with multiple functions. Cellul. 2020;27:9355–70. [Google Scholar]
101. Haqiqi MT, Bankeeree W, Lotrakul P, Pattananuwat P, Punnapayak H, Ramadhan R, et al. Antioxidant and UV-blocking properties of a carboxymethyl cellulose-lignin composite film produced from oil palm empty fruit bunch. ACS Omega. 2021;6(14):9653–66 [Google Scholar] [PubMed]
102. Ma L, Zhu Y, Huang Y, Zhang L, Wang Z. Strong water-resistant, UV-blocking cellulose/glucomannan/lignin composite films inspired by natural LCC bonds. Carbohyd Polym. 2022;281:119083 [Google Scholar] [PubMed]
103. Wang Y, Su J, Li T, Ma P, Bai H, Xie Y, et al. A novel UV-shielding and transparent polymer film: when bioinspired dopamine-melanin hollow nanoparticles join polymers. ACS Appl Mater Inter. 2017;9(41):36281–9. [Google Scholar]
104. Xing J, Yuan D, Xie H, Wang N, Liu H, Yang L, et al. Preparation of efficient ultraviolet-protective transparent coating by using a titanium-containing hybrid oligomer. ACS Appl Mater Inter. 2021;13(4):5592–601. [Google Scholar]
105. Huang ZM, Zhang YZ, Kotaki M, Ramakrishna S. A review on polymer nanofibers by electrospinning and their applications in nanocomposites. Compos Sci Technol. 2003;63:2223–53. [Google Scholar]
106. Xiong F, Han Y, Wang S, Li G, Qin T, Chen Y, et al. Preparation and formation mechanism of size-controlled lignin nanospheres by self-assembly. Ind Crop Prod. 2017;100:146–52. [Google Scholar]
107. Yang W, Rallini M, Wang DY, Gao D, Dominici F, Torre L, et al. Role of lignin nanoparticles in UV resistance, thermal and mechanical performance of PMMA nanocomposites prepared by a combined free-radical graft polymerization/masterbatch procedure. Compos A: Appl Sci Manuf. 2018;107:61–9. [Google Scholar]
Cite This Article
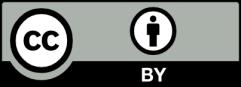
This work is licensed under a Creative Commons Attribution 4.0 International License , which permits unrestricted use, distribution, and reproduction in any medium, provided the original work is properly cited.