Open Access
REVIEW
New Problems of Boiler Corrosion after Coupling Combustion of Coal and Biomass and Anti-Corrosion Technologies
1 National Institute of Clean-and-Low-Carbon Energy, Beijing, 102211, China
2 Key Laboratory of Energy Thermal Conversion and Control of Ministry of Education, School of Energy & Environment, Southeast University, Nanjing, 210096, China
* Corresponding Author: Ziran Ma. Email:
Journal of Renewable Materials 2024, 12(4), 799-814. https://doi.org/10.32604/jrm.2024.047343
Received 02 November 2023; Accepted 13 February 2024; Issue published 12 June 2024
Abstract
This study explores the corrosion issues arising from the coupled combustion of coal and biomass and proposes potential solutions. Biomass, as a renewable energy source, offers advantages in energy-saving and carbon reduction. However, the corrosive effects of alkali metal compounds, sulfur (S) and chlorine (Cl) elements in the ash after combustion cannot be underestimated due to the high volatile content of biomass fuels. We investigate the corrosion mechanisms, as well as the transfer of Cl and alkali metal elements during this process. Comparative corrosion analyses are conducted among coal-fired boilers, pure biomass boilers and boilers with coupled combustion. Various biomass types in co-firing are studied to understand different corrosion outcomes. The main factors influencing corrosion include the physicochemical properties of biomass feedstock, furnace temperature and heating surface materials, with the chemical composition and ash content of biomass playing a dominant role. Currently, the methods used for anti-corrosion include water washing pretreatment of biomass feedstock, application of novel alloys and coatings and the development of additives to inhibit fouling, ash deposition and corrosion. Efficient inhibitors are economical and easy to produce. Additionally, biomass can be converted into biomass gasification gas, although challenges related to tar still need to be addressed.Keywords
In 2021, China’s coal production reached a record high of 4.13 billion tons, but there has been a significant shift in the energy production structure, with non-fossil energy surpassing coal in terms of installed capacity for power generation. Coal’s share in energy consumption has decreased by 12.5 percentage points since 2012, accounting for 56% [1]. Despite the goal of carbon neutrality, coal remains a pillar of economic development and it is projected that coal consumption will decrease to 3.5 billion tons per year from 2031 to 2050 [2]. Currently, although the proportion of coal has significantly declined, it still accounts for over half of the energy structure. Therefore, coupled combustion of biomass holds practical significance. Especially during the “14th Five-Year Plan” period, which is crucial for achieving peak carbon emissions, co-firing biomass and other renewable fuels is a powerful measure to reduce carbon emissions and achieve dual carbon goals.
Biomass fuel, as a renewable fuel, has characteristics such as high volatility, low heating value, low fixed carbon content and low ash content. However, the alkali metal elements in the ash after the combustion of biomass fuels not only promote combustion reactions but also cause corrosion in boilers [3,4]. China is a traditional agricultural country and biomass fuels mainly consist of crop residues such as wheat straw, corn stalks and rice straw. China has abundant biomass resources and as of 2020, the estimated collectible amount of crop residues was about 694 million tons, with only 88.215 million tons utilized as fuel, leaving approximately 87.3% unused [5]. It is projected that the annual production of crop residues alone will exceed 1 billion tons [6]. Therefore, there is still enormous potential for the combustion utilization of biomass.
Compared to coal-fired boilers, coal coupled with biomass combustion can effectively reduce CO2 emissions. It also has lower costs for co-generation and can benefit from carbon trading, resulting in higher cost-profit ratios and both economic and environmental benefits [7]. Wang et al. conducted numerical simulations on a 660 MW ultra-supercritical pulverized coal boiler in a power plant to explore the adaptability of biomass-coal co-firing under different loads [8]. The results showed that co-combustion had no significant impact on combustion under low co-firing ratios (7% and 9%) and could meet the requirements for flexible operation of power generation units, further demonstrating the feasibility of biomass co-firing. Coupled combustion can make use of the existing equipment in power plants and due to the low nitrogen and sulfur content in biomass fuels, the emissions of pollutants such as nitrogen oxides and sulfides are correspondingly reduced after combustion.
In the 1970s, small-scale coal-fired power plants in Europe began co-firing biomass. Research on biomass-coal co-firing technology in foreign countries can be traced back to the 1990s, with boiler capacities ranging from 50 to 500 MW used for experiments and commercial applications [9]. In 2002, the Drax power plant in the UK, representing the retrofitting of large-capacity coal-fired units with biomass co-firing, underwent practical transformations. It started with a single unit co-firing 5% of BMCR (maximum continuous rating) heat, then progressed to all units co-firing 10% and eventually achieved 100% biomass co-firing for Units 1 to 4. This demonstrated the gradual development of coal coupled with biomass combustion towards large-capacity units and high co-firing ratios [10]. In Canada, most biomass co-firing power plants had co-firing ratios between 5% and 10% during commercial operation, but they have been abandoned due to the “coal phase-out” policy [11]. The United States has a developed biomass energy industry and its biomass power generation technology is at the forefront globally. In recent years, the total installed capacity of biomass power generation has exceeded 13 million kilowatts, with over 450 biomass power plants built. Among them, the co-firing mode of coal and biomass accounts for a significant proportion [6].
Compared to direct combustion for power generation, biomass co-firing can better utilize the economies of scale in power plants. As the size of the power plant increases, the cost of electricity generation gradually decreases, which is the opposite of direct combustion. In addition, the marginal abatement cost of co-firing power generation increases at a smaller rate as the scale expands compared to direct combustion [7]. Coupled combustion can be retrofitted on the existing facilities with low retrofitting costs and has advantages such as flexible load adjustment and safe operation [12]. Despite these advantages, biomass co-firing still faces the following challenges. First, the supply and pre-treatment of biomass feedstock have not formed a complete process. Second, mature technologies for high proportion co-firing are lacking. Third, there are issues of slagging and corrosion on the heat transfer surfaces after co-firing.
Compared to pure biomass combustion, co-firing biomass with coal can reduce the content of alkali metals and chlorine elements in biomass fuel, effectively alleviating a series of slagging and corrosion phenomena caused by pure combustion [13]. Priyanto et al. conducted co-firing of a high proportion of woody biomass in a 150 MW pulverized coal boiler and found that compared to coal combustion, co-firing resulted in twice the amount of sulfates (mainly Na2SO4) in the deposits formed on the furnace walls and higher corrosion rates on the tube walls at 500°C [14]. The formation of fouling and corrosion reduces the heat transfer capacity of water-cooled walls [15], affecting the stable operation of the boiler. In addition, under the action of high-temperature flue gas, ash deposits can corrode the wall surfaces, leading to equipment damage and other adverse effects.
Addressing the corrosion challenges in large power plants, especially those involving high co-firing rates of biomass and coal, is a complex issue that varies by region and technology. The U.S. has focused on advanced material research to enhance the corrosion resistance of boiler components. Research efforts like those at the Energy & Environmental Research Center (EERC) at the University of North Dakota have explored the use of corrosion-resistant alloys and protective coatings. Furthermore, operational strategies like optimizing the fuel blend and combustion conditions have been employed to reduce corrosion risks [16]. Germany, with its significant investment in renewable energy, has pioneered in the field of biomass co-firing. German researchers have conducted extensive studies on the impacts of different biomass types on boiler corrosion. They have employed advanced monitoring techniques, such as online corrosion sensors, to provide real-time corrosion rate data, enabling better control and maintenance strategies [17]. Denmark’s focus has been on optimizing boiler design to mitigate corrosion. This includes the development of boilers with enhanced temperature and combustion control to reduce the formation of corrosive compounds. The Technical University of Denmark (DTU) has conducted several studies on the effects of fuel composition on corrosion [18]. In conclusion, while each country has its unique approach, common strategies include developing corrosion-resistant materials, optimizing combustion conditions, using fuel additives, and implementing real-time corrosion monitoring systems. These efforts are crucial for the successful integration of biomass co-firing in large power plants and for ensuring the longevity and efficiency of these systems.
This article provides an overview of the corrosion mechanisms in boilers after co-firing with biomass fuel, with a focus on Cl and alkali metal elements. It compares the differences in corrosion between coal-fired boilers, pure biomass boilers and co-firing boilers. The article also investigates the influence of different types of co-fired biomass and different biomass growth cycles on boiler corrosion, aiming to provide feasible and effective corrosion prevention measures for biomass co-firing technology.
2 Corrosion Mechanism after Coupled Combustion
During the combustion of biomass in the furnace, elements such as alkali metals (K, Na), chlorine (Cl) and sulfur (S) in the ash undergo complex chemical transformations and are released in gaseous form. These compounds include Cl2, SOx, MClx, Mx(SO4)y and other compounds [19]. At high temperatures (500°C), these compounds in the flue gas react with the heated metal surfaces, leading to the formation of metal compounds and causing corrosion.
In traditional boilers, slagging refers to the deposits formed on the radiation heat transfer surfaces such as water-cooled walls. It can be divided into two main stages, one is the formation of an initial slagging layer and the other is the viscous growth and dynamic equilibrium of the initial slagging layer [20]. The alkali metal chlorides and sulfates deposited in the slagging and ash can also react with the metal surfaces, exacerbating corrosion.
Wang et al. [21] simulated the combustion of biomass and the formation process of ash char on the heating surface in a drop tube furnace and proposed the mechanism of deposition and slagging on the heating surface during biomass combustion. It is believed that sulfate aerosol nanoparticles with low melting point play an important role in the deposition process of wheat straw ash samples, as shown in Fig. 1.
Figure 1: Mechanism of slagging formation on the heated surface during biomass combustion. Reprinted with permission from [21], Copyright© (2013), Journal of Engineering Thermophysics
The corrosion after coupled biomass combustion can be roughly divided into three categories, including chemical corrosion, electrochemical corrosion and chloride corrosion [22]. Chemical corrosion mechanism involves the transfer of iron ions to the precipitate through chemical reactions, leading to the destruction of the originally dense Fe2O3 protective film on the heating surface. Electrochemical corrosion refers to the reaction between chloride in the precipitate and Fe in the tube wall, continuously generating FeCl3. Subsequently, FeCl3 is reduced and reacts with Fe, increasing the concentration of FeCl3 and causing cyclic corrosion. Chloride corrosion mainly occurs when HCl and Cl2 oxidize the Fe ions on the metal surface, leading to the corrosion of the furnace wall [23].
Severe corrosion phenomena are mostly associated with ash deposition. Metal chlorides evaporate and diffuse to the surface of the oxide film on high-temperature heating surfaces. They are then oxidized into solid metal chlorides, which deposit and form a loose, non-protective oxide layer. Additionally, the molten substances generated from the chemical reaction of KCl and some low-melting eutectics can quickly combine with fly ash and deposit on the heating surfaces [24]. These deposits can rapidly cover the metal surface. The sulfate deposits formed from their reaction with SO2 or SO3 in the flue gas generate HCl gas, leading to boiler corrosion [25]. The reaction can be represented as follows:
2KCl(s)+SO2(g)+12O2+H2O(g)→K2SO4(s)+2HCl (1)
2KCl(s)+SO2(g)+O2+H2O(g)→K2SO4(s)+Cl2(g) (2)
As a large agricultural country, China’s agricultural waste is mostly rice straw, corn stalk, wheat straw and cotton stalk. Compared with wood fuel, these crop residues, known as straw biomass fuels, have a higher chlorine content, making them more prone to corrosion phenomena.
Research has also indicated that chlorine elements play a role similar to catalysts in the corrosion process, accelerating the corrosion rate and reducing the equipment’s service life [26]. Substances gradually forming a deposition layer adhered to the pipe surface at high temperatures play a crucial role in corrosion.
Chlorine gas can diffuse into the pores of metal after oxidation, penetrate through dense oxide layers and react with the surface of metal alloys to form metal chlorides, ultimately causing severe corrosion. Therefore, to enhance the corrosion resistance of metals, materials such as Cr and Si are often added to alloys. The protective chromium oxide layer formed in an oxidizing atmosphere can prevent the corrosion of metals by chlorine gas [27]. However, the protective Cr2O3 layer reacts with KCl vapor and Cr to generate Cl2 and repeating this process can lead to the depletion of the Cr2O3 layer, resulting in more severe corrosion of the metal material.
During the combustion process, the gaseous compounds formed by alkali metal elements mainly include KCl, NaCl, KOH, NaOH, K2SO4 and Na2SO4. Among them, KCl and NaCl are the major products and their formation is positively correlated with temperature. The production amount of KCl generated is much higher than that of NaCl, approximately ten times higher [28].
For severe slagging caused by chlorides and sulfates, the slagging layer is usually composed of KCl and K2SO4 [29]. The presence of these two compounds will cause serious corrosion to the boiler and due to the high partial pressure of chloride in the deposition layer, the potential reactions are as follows:
Cr2O3(s)+4KCl+52O2(g)→2K2CrO4(s,l)+2Cl2(g) (3)
Cr2O3(s)+4NaCl+52O2(g)→2Na2CrO4(s,l)+2Cl2(g) (4)
Fe2O3(s)+2KCl+12O2(g)→2KFeO2(s,l)+Cl2(g) (5)
Fe2O3(s)+2NaCl+12O2(g)→2NaFeO2(s,l)+Cl2(g) (6)
Míguez et al. proposed the slagging, fouling and corrosion mechanism of specific biomass fuels in the combustion process [30], as shown in Fig. 2.
Figure 2: Mechanisms of slagging, ash accumulation and corrosion formation during combustion of biomass fuels. Reprinted with permission from [30], Copyright© (2021), Elsevier
In summary, compared to traditional boiler, the corrosion issue is more pronounced when biomass is co-combusted. This is attributed to the intensified corrosion caused by the chlorine and alkali metal elements abundant in biomass. The deposition process of ash is accelerated by the low-melting-point nanoscale sulfate aerosol particles. At elevated temperatures, chlorine and alkali metals diffuse into the dense metal protective layer, forming a porous oxide layer. Chlorine elements are also considered as “catalysts” in this process, expediting corrosion. Furthermore, with increasing temperature, the degree of corrosion shows a significant positive correlation, especially for potassium elements, whose generation quantity is ten times that of sodium, playing a crucial role in the corrosion process.
3 Comparative Analysis of Corrosion Characteristics in Three Kinds of Boilers
The main corrosion problem in traditional coal-fired boilers during the coal combustion process is high-temperature corrosion of water-cooled walls. The influencing factors of high-temperature corrosion can be summarized as follows: sulfur content in coal, reducing atmosphere in the corrosion area, near-wall combustion of pulverized coal, temperature conditions of water-cooled wall and fineness of pulverized coal [31]. Under high-temperature conditions, the oxide film on the substrate surface reacts with corrosive gases (such as H2S) or low-melting-point compound alkaline sulfates in the attachment layer, leading to further corrosion of the pipes. Several studies in the literature found that the concentrations of CO and H2S in the atmosphere of water-cooled wall are key factors affecting water-cooled wall corrosion. Yuan et al. proposed a prediction model for H2S corrosion. The theoretical and experimental results remain consistent, while H2S concentration is positively correlated with the degree of corrosion [32]. Operating oxygen, coal particle fineness, coal mill combination and coal mill output mode are the main factors influencing the concentrations. The researchers further explored the optimization and adjustment of parameters such as the perimeter air opening of the burner, secondary auxiliary air opening, over-fire air (OFA) opening, operational oxygen level and selective over-fire air (SOFA) opening. This effectively reduced the concentrations and alleviated high-temperature corrosion. Ma et al. investigated the air classification technology, and based on this, designed a porous wall air coupling with air staged (PW & AS) furnace, which can simultaneously achieve protection against high temperature corrosion, high combustion efficiency and low NOx emissions [33]. Corrosion of water-cooled walls can lead to decreased heat transfer efficiency and studies have shown that heat transfer capacity can be reduced by about 50% [34]. In severe cases, it can lead to safety accidents such as tube bursting. Experts and scholars in the industry have conducted comprehensive analyses and investigations on the corrosion issues of traditional boilers and corresponding corrosion prevention measures have been implemented in production [35–37].
The technology of pure biomass boilers in China has become relatively mature and their application is widespread. The development of biomass combustion boilers is also advancing. However, there is still ample room and prospects for discussion regarding fouling, corrosion, slagging and pollutant emissions [38]. Due to the high chlorine and alkali metal content in biomass fuels, severe corrosion can occur on the heating surfaces of boilers in an oxidizing atmosphere. Corrosion in biomass boilers mainly occurs in the high-temperature corrosion of the superheater and the low-temperature corrosion of the cold section of the air preheater [39]. At high temperatures, the ash deposits formed due to the agglomeration characteristics of alkali metal chlorides react with sulfides and chlorides in the flue gas, leading to corrosion. In the cold air inlet section of the air preheater, the low temperature causes the condensation of acidic gases in the flue gas, resulting in corrosion by acidic liquids on the heating surfaces. Deposits on the low-temperature heating surface tubes can be divided into corrosion layers, coupling layers and ash deposits, mainly composed of NH4Cl, SiO2, CaCl2 and small amounts of sulfates. NH4Cl is generated by the reaction of NH3 produced from biomass pyrolysis with HCl in the flue gas and its subsequent deposition on the outer surface of the tubes [40]. The formation of biomass slag can reduce the heat transfer capacity of the boiler. The decrease in heat absorption by the heating surfaces in the furnace will cause an increase in flue gas temperature, leading to increased heat loss in the flue gas and a decrease in boiler thermal efficiency.
Coupled combustion biomass boilers are one of the effective approaches to achieving the carbon peaking and carbon neutrality goals. In order to transform and upgrade China’s energy structure and achieve the goal of non-fossil energy accounting for no less than 50% of the total power generation by 2030, the vigorous development of coal-fired power generation coupled with biomass will become inevitable. The general process of corrosion after coupled combustion is as follows [41]: in the initial stage of corrosion, the surface layer elements of the metal (mainly Fe and Cr) form thin metal oxides under the action of O2 and CO2, providing a protective effect. When the metal temperature reaches 600°C, new phases (such as CrxCy and FexC) will precipitate between metal particles, causing depletion of a certain element composition in the grain boundary region. At this time, a corrosion cell will form between the depleted grain boundary region and the grain body, leading to intergranular corrosion. The low-temperature molten salt formed during the reaction acts as a liquid electrolyte, exacerbating electrochemical corrosion. The metal carbides precipitated on the metal surface can undergo oxidation-reduction reactions with corrosive gases in the flue gas, transferring carbon elements from the metal surface to the oxide corrosion film, reducing the carbon content in the metal and altering the metal’s microstructure. The oxidation-reduction reactions of metal carbides at grain boundaries result in longitudinal extension of corrosion along the grain boundaries, leading to severe decarburization corrosion. The SO2 emitted from coal combustion can also sulfurize the main corrosive substance KCl in biomass, releasing compounds containing chlorine and causing further oxidative corrosion. Coupled co-firing reduces the chlorine content in fly ash and increases the ash fusion point, which plays a critical role in reducing corrosion on the heating surfaces. High-temperature corrosion is inevitably reduced, especially effectively addressing the high-temperature corrosion of solid-phase alkali metal chlorides [42]. At the same time, it mitigates a series of slagging and corrosion phenomena associated with pure biomass boilers.
Temperature, HCl and KCl concentrations, biomass type and blending ratio play an important role in controlling the extent of corrosion, particularly in industrial applications. When the co-firing ratio is below 10%, the concentration of KCI does not increase significantly with the increase in co-firing ratio. However, the ash fusion temperature significantly rises, leading to a noticeable reduction in corrosion severity. Additionally, maintaining a temperature below 700°C can effectively mitigate corrosion. It is also advisable to control the wall temperature of the low-temperature heated surface of the coal-fired industrial boiler above 70°C, in order to minimize the viscous ash accumulation and dew-point corrosion caused by acid condensation. Co-firing coal with biomass has the advantage of energy saving and emission reduction. The emissions of NOx can be reduced by around 10%. However, the emissions of NOx and SO2 pollutants increase due to the addition of biomass fuel, so it is still necessary to pay attention to the treatment of subsequent nitrogen and sulfur pollutants.
Comparing three types of boilers based on the content of chlorine and alkali metal elements in ash, ranging from low to high in coal-fired boilers, co-firing boilers and pure biomass boilers, the corrosion situation increases accordingly. Conventional boiler corrosion products are primarily oxides and sulfides, while co-firing boilers produce oxides, chlorides, and alkali metal compounds. The corrosion process is influenced by factors such as the type and proportion of biomass added. The higher the proportion of biomass, the more severe the corrosion. Additionally, co-combustion introduces a complex interplay of ash constituents, creating a unique corrosion environment.
4 The Effect of Biomass Fuel Types on Corrosion
The ash composition of biomass is a major factor affecting boiler corrosion. The alkali metals (Na2O, K2O), alkaline earth metals (CaO, MgO) and SiO2 contained in different biomass types play a crucial role in determining the severity of corrosion.
The ash content in wood and forestry processing residues is generally between 1%–5%, which is significantly lower compared to traditional coal, with low levels of alkali metals and SiO2 and high levels of alkaline earth metals. This generally results in a high ash melting point and reduced slagging tendency. Herbaceous plants, on the other hand, have high levels of alkali metals and SiO2 and low levels of alkaline earth metals, leading to a lower ash melting point and a higher propensity for slagging. Agricultural processing residues, such as sugarcane bagasse, olive shells and pine nut shells, have high levels of SiO2, alkali metals and alkaline earth metals in their ash content. Therefore, this type of biomass has a lower ash melting point and is more prone to slagging [43].
According to the basic national conditions in China, agricultural waste mainly composed of straw has the following characteristics [44]: (1) high volatile matter content, with rapid release of volatile matter during combustion; (2) low ash content in biomass fuel, but with a high amount of impurities such as stones and soil; (3) low ash melting point, making it prone to slagging; (4) influenced by soil and water conditions, biomass may accumulate a certain amount of chlorine, which can lead to corrosion after combustion.
Liao et al. studied the chemical element characteristics of 63 samples of straw agricultural biomass such as rice and forestry biomass such as poplar and pine in China [45]. It was found that biomass fuel was composed of very uneven components and the element composition content of different groups of the same organism was very different. Agricultural biomass contains more ash and trace elements (such as K, Si) than most forestry biomass. It has been found that algae biomass can affect the degree of ash aggregation and is easier to adhere than wood biomass through the co-combustion of Henan bituminous coal with seagrass and peach wood. Lignocellulosic biomass can effectively inhibit the formation of low-temperature eutectics due to its elements such as Ca and Fe [46]. Zhou et al. investigated the slagging tendency of seven typical biomasses in Northeast China and developed an index J to measure the slagging risk as shown in Table 1 [47]. In contrast, the softening temperature of corn cob and sweet potato vine is lower (<900°C), the content of alkali metal salt is positively correlated with the slagging trend of biomass boiler and the high content of alkali metal will reduce the melting temperature of biomass ash.
In addition to common biomass fuels such as wood and straw, dried sludge can also participate in co-combustion. Karlsson et al. conducted sampling and analysis of the blades and ash content of the induced draft fan in a 12 MW circulating fluidized bed boiler co-firing solid waste fuel. No sulfur (S) element was found and the cause of corrosion was determined to be the chlorine (Cl) element from the solid waste and sludge [48]. In the case of direct co-firing of biomass, the co-firing of pine wood and sawdust can reduce the ash content flow rate, while the co-firing of sludge can increase the emission of ash, thereby increasing the risk of slagging and corrosion [49]. Yang et al. conducted grouped tests on a supercritical variable-pressure pulverized coal boiler in a power plant. Under co-firing ratios of 20%, 40%, 60% and 80%, the NOX generation at the economizer outlet decreased with the increase of sludge co-firing ratio, while the reducing gas in the wall region showed an increasing trend [50]. Gao et al. used numerical simulation and other tools to analyze the problem of ash accumulation and slagging [51]. It was concluded that the risk of ash accumulation and slagging in boilers is generally controllable when co-firing sawdust at a mixing ratio of less than or equal to 30%.
5.1 Corrosion Influencing Factors
The main factors influencing corrosion are the physicochemical properties of biomass feedstock, furnace temperature and heating surface materials, with a particular emphasis on the chemical composition and ash content of the biomass.
Furnace temperature may be an important influencing factor for high-temperature corrosion. Grabke et al. observed the corrosion behavior of Cr-Mo metal surfaces by adding NaCl under different temperature conditions [52]. They found that the corrosion was mild at temperatures below 450°C, but severe corrosion occurred when the temperature reached 600°C. On the other hand, improving the quality of the heating surface material can reduce the degree of corrosion. Zhang et al. compared two commonly used grades of boiler special steel (TP347H, HR3C) and found that the corrosion resistance of the steel is positively correlated with the Cr content within a certain range [23,53]. The oxide film formed on the metal surface containing Cr is the main barrier against KCl corrosion. For low-temperature corrosion in air preheaters, corrosion-resistant materials such as enamel can be chosen.
The composition of biomass remains a key factor in corrosion issues. The presence of alkali metals and chlorine elements in biomass fuels is the direct cause of corrosion on boiler heating surfaces [54]. Yang et al. conducted a study on corn stalks, rice stalks and bamboo flour at 1000°C, 1100°C, 1200°C and 1300°C and found that corn stalk combustion caused more severe corrosion to the boiler [55]. This is mainly due to the higher potassium (K) content in corn stalks compared to the others. Meanwhile, K has a promoting effect on Pb release. Therefore, it is important to consider the differences in biomass fuels when selecting them to avoid corrosion issues.
Currently, there are several methods used for corrosion prevention, including water washing pretreatment of biomass feedstock, application of new alloys and coatings and the development of additives to inhibit fouling, ash deposition and corrosion. Among these methods, efficient additives are cost-effective and easy to produce. Biomass has a low heating value and low energy density, but it can be converted into biomass gas through biomass gasification. However, tar formation can be a problem in biomass gasification processes.
In typical straw types in China, such as wheat straw and rice straw, the alkali content can be as high as 36% and 30%, respectively, with the alkali metal element potassium (K) primarily present in the form of KCl, which can lead to severe ash deposition. Hu et al. confirmed the optimal washing temperature for these two types of straw [56]. Acid washing at a temperature of 70°C effectively removes alkali metals from the ash, reducing the K2O content to 5.31%. Pre-treatment of biomass before combustion is feasible for mitigating corrosion issues.
The use of new alloys is a direction for practitioners to explore. Nickel-based alloys exhibit good resistance to sulfate corrosion, while cobalt-based alloys and iron-based alloys have poorer protective effects in sulfate environments. A comparison of different spray techniques commonly used in alloy coating and their effectiveness is shown in Table 2.
In the high-temperature chlorine corrosion environment of biomass boilers, a high Cr content in alloys is not conducive to improving the protective performance against chlorine corrosion [59]. He et al. used high-velocity flame spraying to prepare FeCoCrNiAlTix high-entropy alloy coatings on a Q235 substrate [60]. The addition of Ti can reduce the porosity of the coating and the coating exhibits good resistance to thermal shock and high-temperature chlorine corrosion. In the Nässjö biomass power plant in Sweden, Stellite 6 (CoCrWC) coatings were used in both low-temperature and high-temperature biomass-coal co-firing boiler superheaters. Due to their high microhardness and corrosion resistance, these coatings performed well even after 1630 h of operation, demonstrating excellent corrosion-erosion resistance [61]. Since biomass-coal co-firing boilers started relatively late, research on corresponding coatings is still ongoing and it will be a key development direction in the field of boiler protection in the future.
Additives have become another effective means of corrosion prevention due to their ease of operation, good adaptability and consideration of economic costs. The use of additives on the flue gas side can promote fuel blending and ensure complete combustion of the fuel in the furnace. Currently, the most commonly used additive is sulfur-containing compounds. Taking liquid catalysts containing ammonium sulfate as an example, the liquid ammonium sulfate reacts with KCl in the flue gas to generate stable potassium sulfate, reducing the chlorine content in the flue gas and achieving the effect of mitigating corrosion [62]. Wang et al. simulated the ash melting characteristics after the combustion of coal with high alkali metal and alkaline earth metal contents [63]. The experiments showed that the addition of CaO and MgO can inhibit the formation of molten liquid slag in the ash at high temperatures and reduce ash accumulation. Yu et al. added Al2O3 as an additive to corn stalk ash, effectively reducing the content of KCl in the deposited ash and significantly weakening the corrosiveness of the ash [55]. Zhou et al. found that adding a small amount of Fe2O3 and CaO additives in boilers can increase the ash melting temperature and alleviate the phenomenon of molten slag formation [47]. The impact of additives on biomass ash melting are summarized, as shown in Table 3.
However, the additives used in the above experiments are simple aluminum, iron and calcium-based additives. In practical industrial applications, it may be worth considering industrial waste materials containing relevant elements that are easily obtainable and have low cost, taking into account both practicality and economic feasibility.
Biomass gasification may also be a new approach to corrosion prevention. Gasification transforms organic materials into syngas and solid product, called char. The resulting syngas can be separated into a gas phase and a condensable phase known as tar, composed of multiple organic compounds that resemble bituminous oil when condensed. The general approach is to treat the tar compounds as a certain number of lumped classes and to define a reaction path for a single compound, which is considered as representative of the total amount of the classes [67]. For different biomasses, the tar composition varies. Butnaru et al. studied forestry residues (silver fir including cones, needles, and bark) to determine the different compounds present in the condensable products due to the different types of lignin and found that a combination of torrefaction and pyrolysis resulted in a more uniform distribution [68]. Narobe et al. theoretically proposed a pyrolysis model to predict the decomposition time of mono-gasification of plastics and co-gasification of biomass (wood pellets) at 850°C and 900°C by means of an avidity analysis and modeling theory, and later verified the consistency by experiments in a 100 kW pilot experiment [69]. The first 20 MW coal-biomass co-gasification power generation demonstration project in China has been implemented in Tangshan, which can save about 47,000 tons of standard coal per year. It not only achieves energy conservation and emission reduction but also reduces pollutant emissions and has minimal impact on boiler efficiency [70]. In recent years, many scholars have conducted researches on the ratio, type, operating conditions and boiler load of blended biomass gas. Chen et al. simulated a new biomass air-steam circulating fluidized bed gasification co-combustion system based on waste heat and flue gas water recovery using Aspen Plus software and compared it with the original system [71]. The results showed that the new system model improved the overall performance of the co-combustion system, and the syngas was more energy efficient than the air gasification co-combustion system. When the ratio of co-combustion was 40%, the N2 content in syngas was reduced by 12.22%, and the emissions of air pollutants such as carbon dioxide (CO2), sulfur oxides (SOx), and nitrogen oxides (NOx) were also reduced. Furthermore, gasification of solid feedstock can increase the energy density of biomass fuel and improve boiler corrosion issues. Currently, the cost of biomass gasification is higher than coal. However, significant cost reductions can be achieved through the implementation of a carbon credit market, scaling up of waste incineration plant equipment and experience gained [72].
There are many scholars who have studied torrefaction, pyrolysis and gasification, and there is a lot of literature that has experimented and evaluated various aspects such as different biomass types, process conditions, and has pushed the field of gasification forward [73,74].
However, there are still corresponding issues after biomass gasification and tar is the biggest obstacle to the utilization of gasification gas. Tar can condense on boiler surfaces, leading to fouling and corrosion. The chemical composition of tar and its interaction with the boiler materials can accelerate corrosion. The challenges come from three aspects: corrosion, efficiency loss and environmental impact. Firstly, Tars can contribute to the corrosion and erosion of boiler components, reducing their operational lifespan. Tar can block pipelines, preventing proper operation of power generation and gas supply and it can also cause secondary pollution [75]. Second, Tar buildup can decrease boiler efficiency by reducing heat transfer efficiency and increasing the need for maintenance. Last but not least, uncontrolled tar emissions can have environmental implications, contributing to air pollution. Ziad et al. have proposed methods for tar removal and purification using chemical processes, and how to develop catalysts with high activity based on natural zeolites to improve the efficiency of biomass gasification [76]. In summary, the conversion of biomass to gasification gas in co-fired boilers presents both challenges and opportunities. Addressing tar-related problems is crucial for optimizing efficiency, minimizing corrosion, and ensuring the environmental sustainability of co-firing practices. Ongoing research and technological innovations play a key role in advancing the viability of biomass co-firing as a cleaner energy solution.
The biomass-coal co-combustion is a key technology for carbon reduction in the future due to its environmental and economic benefits. However, it also faces significant challenges in terms of corrosion issues. To address these challenges, explore emerging technologies and research innovations are needed for improved corrosion control.
Biomass-coal co-combustion boilers have advantages in mitigating wall slagging and corrosion compared to traditional boilers, but the corrosion situation on the heating surfaces differs due to the alkali metals and Cl elements present in biomass. Different types of biomass fuels have varying levels of corrosiveness corresponding to the elemental content in the ash after combustion. The migration of alkali metals and elements such as K and Cl in biomass is crucial and gaining a clearer understanding of their migration patterns is of great significance for the corresponding anti-corrosion measures in boilers after co-combustion. In biomass-coal co-firing systems, when the co-firing ratio remains below 10%, the concentration of KCl does not exhibit a significant increase with the rise in co-firing ratio. However, it is observed that the ash fusion temperature notably increases, resulting in a considerable reduction in corrosion severity. Furthermore, it has been found that maintaining a temperature below 700°C can effectively mitigate corrosion in such systems.
Common research directions to mitigate corrosion include water washing pretreatment of biomass feedstock, application of new alloys and coatings and the development of additives to inhibit slagging, ash deposition and corrosion. The development of coatings is an important branch for the future. However, considering the high cost associated with doping metallic elements and their limited application in the field of coupled combustion, coating technology is still in its early stages. Additives, on the other hand, are widely used in practical production due to their cost-effectiveness and ease of operation. In addition, biomass gasification is also a promising avenue to explore for corrosion prevention.
Acknowledgement: Authors acknowledge the Key Laboratory of Energy Thermal Conversion and Control of Ministry of Education for their continued support.
Funding Statement: The authors received no specific funding for this study.
Author Contributions: The authors confirm contribution to the paper as follows: study conception and design: L. Wang, Z. Ma; data collection: L. Wang; analysis and interpretation of results: L. Wang, Z. Ma, C. Zhao, J. Zhou, H. Wang, G. Li, N. Zhou; draft manuscript preparation: L. Wang, Z. Ma, C. Zhao, J. Zhou, H. Wang, G. Li, N. Zhou. All authors reviewed the results and approved the final version of the manuscript.
Availability of Data and Materials: The articles surveyed in this paper can be found in mainstream indexing databases. The list of reviewed papers and relevant analysis data can be made available by the authors upon request.
Conflicts of Interest: The authors declare that they have no conflicts of interest to report regarding the present study.
References
1. Zheng JJ, Dang YJ, Assad U. Household energy consumption, energy efficiency, and household income-evidence from China. Appl Energ. 2024;353:122074. [Google Scholar]
2. Chen JD, Li ZD, Song ML, Wang YZ, Wu YY, Li K. Economic and intensity effects of coal consumption in China. J Environ Manage. 2022;301:113912 [Google Scholar] [PubMed]
3. Canabarro N, Soarea JF, Anchieta CG, Kelling CS, Mazutti MA. Thermochemical processes for biofuels production from biomass. Sustain Chem Process. 2013;1:1–10. [Google Scholar]
4. Lv Y, Xu L, Niu YQ, Wang GY, Lei Y, Huang HY, et al. Investigation on ash deposition formation during co-firing of coal with wheat straw. J Energy Inst. 2022;100:148–59. [Google Scholar]
5. Lang LX, Chen YB, Liu Y, Wu JX, Yu YK, Wang Y, et al. Changes in spatial patterns of biomass energy potential from biowaste in China from 2000 to 2020. Frontiers in Energy Research. 2023;11:1109530. [Google Scholar]
6. Fan ZQ. Nanomaterials for food and agriculture in economic valuation of the technology harvesting maize straw for biogas production in China. J Nanomater. 2022;2022:1. [Google Scholar]
7. Joshi VV, Swaminathan G, Prabhakaran SPS. Life cycle assessment of the co-combustion system of single-use plastic waste and lignite coal to promote circular economy. J Clean Prod. 2021;329:129579. [Google Scholar]
8. Wang XL, Liu P, Chu W, Zhang C, Wu GQ, Zhang CQ, et al. Numerical simulation study on load adaptability under co-firing of biomass gas and coal. Electr Power Technol Environ Prot. 2022;38(2):87–94 (In Chinese). [Google Scholar]
9. Hughes EE, Tillman DA. Biomass co-firing: status and prospects 1996. Fuel Process Technol. 1998;54(1–3):127–42. [Google Scholar]
10. Henry EE. As price worries grow, UK asks Drax to extend coal power plant operation. Platts Coal Trader Int. 2022;22(80):11–2. [Google Scholar]
11. Agbor E, Zhang XL, Kumar A. A review of biomass co-firing in North America. Renew Sustain Energy Rev. 2014;40:930–43. [Google Scholar]
12. Miroslav V, Augustín V, Miroslav R, Ján J, Ján K, Ladislav L, et al. Advances in biomass co-combustion with fossil fuels in the European context: a review. Process. 2021;9(100):100. [Google Scholar]
13. Roni MS, Chowdhury S, Mamun S, Marufuzzaman M, Lein W, Johnson S. Biomass co-firing technology with policies, challenges and opportunities: a global review. Renew Sustain Energy Rev. 2017;78:1089–101. [Google Scholar]
14. Priyanto DE, Matsunaga Y, Ueno S, Kasai H, Tanoue T, Mae K, et al. Co-firing high ratio of woody biomass with coal in a 150-MW class pulverized coal boiler: properties of the initial deposits and their effect on tube corrosion. Fuel. 2017;208:714–21. [Google Scholar]
15. Tan ZX, Lagerkvist A. Phosphorus recovery from the biomass ash: a review. Renew Sustain Energy Rev. 2011;15(8):3588–3602. [Google Scholar]
16. Kopf J. Advances in boiler construction and design. Fuel Oil News. 2016;81(3):38–9. [Google Scholar]
17. Lee M, Lin YL, Chiueh PT, Den W. Environmental and energy assessment of biomass residues to biochar as fuel: a brief review with recommendations for future bioenergy systems. J Clean Prod. 2020;251:119714. [Google Scholar]
18. Antunes RA, de Oliveira MCL. Corrosion in biomass combustion: a materials selection analysis and its interaction with corrosion mechanisms and mitigation strategies. Corros Sci. 2013;76:6–26. [Google Scholar]
19. Qi XB, Song GL, Song WJ, Yang SB, Lu QG. Combustion performance and slagging characteristics during co-combustion of Zhundong coal and sludge. J Energy Inst. 2018;91(3):397–410. [Google Scholar]
20. Yao XW, Zhao ZC, Li JS, Zhang BH, Zhou HD, Xu KL. Experimental investigation of physicochemical and slagging characteristics of inorganic constituents in ash residues from gasification of different herbaceous biomass. Energy. 2020;198:117367. [Google Scholar]
21. Wang XB, Zhang LM, Wang XM, Tan HZ, Xu TM. Study on the mechanism of slagging on the heating surface of biomass combustion equipment. J Eng Thermophys. 2013;34(11):2189–93 (In Chinese). [Google Scholar]
22. Kunmi JA, Suriati S, Mohammad Y, Ahmad HJ, Bernard CE, Hesam K, et al. A review of biomass ash related problems: mechanism, solution, and outlook. J Energy Inst. 2024;112:101490. [Google Scholar]
23. Feri K, Adi P, Nandang S, Arif D, Hariana H, Djarot BD, et al. Investigation of austenitic stainless steel corrosion resistance against ash deposits from co-combustion coal and biomass waste. Eng Fail Anal. 2023;150:107368. [Google Scholar]
24. Dengler JE, Doroodlan A, Rieger B. Protic metal-containing ionic liquids as catalysts: cooperative effects between anion and caution. J Organomet Chem. 2011;696(24):3831–5. [Google Scholar]
25. Paul S, Harvey MDF. Corrosion testing of Ni alloy HVOF coatings in high temperature environments for biomass applications. J Therm Spray Technol. 2013;22(2–3):316–27. [Google Scholar]
26. Riedl R, Dahl J, Obernberger I, Narodoslawsky M. Corrosion in fire tube boilers of biomass combustion plants. Proc China Int Corros Control Conf, 1999; Beijing, China. [Google Scholar]
27. Ma HT, Zhou CH, Wang L. High temperature corrosion of pure Fe, Cr and Fe-Cr binary alloys in O2 containing trace KCl vapour at 750°C. Corros Sci. 2009;51(8):1861–7. [Google Scholar]
28. Leiser S, Cieplik MK, Smit R. Slagging behavior of straw and corn stover and the fate of potassium under entrained-flow gasification conditions. Energy Fuels. 2013;27(1):318–26. [Google Scholar]
29. Niu YQ, Tan HZ, Ma L, Pourkashanian M, Liu ZN, Liu Y, et al. Slagging characteristics on the superheaters of a 12 MW biomass-fired boiler. Energy Fuel. 2010;24(11):6220. [Google Scholar]
30. Míguez JL, Porteiro J, Behrendt F, Blanco D, Patiño D, Dieguez-Alonso A. Review of the use of additives to mitigate operational problems associated with the combustion of biomass with high content in ash-forming species. Renew Sustain Energy Rev. 2021;141:110502. [Google Scholar]
31. Kyo S, Nakamori M, Kurokawa K, Narita T. Analysis of high temperature corrosion and wear damage on furnace water wall in pulverized coal firing boiler. Corros Eng. 2010;59(12):456–63. [Google Scholar]
32. Yuan MB, Deng L, Zhang JK, Jiang JH, Liang Y, Liu H, et al. Prediction of H2S corrosion depth for water-cooled wall in lower furnace of utility boiler. Fuel. 2022;329:125466. [Google Scholar]
33. Ma HH, Zhou L, Ma SX, Du HJ. Design of porous wall air coupling with air staged furnace for preventing high temperature corrosion and reducing NOx emissions. Appl Therm Eng. 2017;124(1):865–70. [Google Scholar]
34. Mohammed I. Effect of corrosion on heat transfer through boiler tube and estimating overheating. Int J Adv Mech Eng. 2014;4(6):629–38. [Google Scholar]
35. Zhu YM, Niu YQ, Tan HZ, Wang XB. Short review on the origin and countermeasure of biomass slagging in grate furnace. J Energy. 2014;18(2):78–94. [Google Scholar]
36. Alar K. Investigation of fouling and corrosion of low-temperature reheater in a CFBC boiler. Fuel. 2023;338:127373. [Google Scholar]
37. Vijay JJC, Lawrence A, Arthanareeswaran G. Analytical tool for analysing slagging characteristic of high ash coals in utility boilers. Int J Mech Eng Technol. 2019;8(3):185–96. [Google Scholar]
38. Chen TQ, Sun L, Li Q, Liu C, Liu ZY, Cheng XQ, et al. Comprehensive analysis of corrosion failure of blast furnace gas pipeline in a steel plant. Eng Fail Anal. 2023;154:107651. [Google Scholar]
39. Shrutika S, Mayank S, Deepa M. Adoption of strategies for clean combustion of biomass in boilers. Corros Rev. 2021;39(5):387–408. [Google Scholar]
40. Agata MM, Aneta M, Izabela KR, Wojciech N. The influence of potassium-rich biomass ashes on steel corrosion above 550°C. Energy Convers Manage. 2019;187:15–28. [Google Scholar]
41. Yuan JZ, Peter A, Anker DJ. Ash transformation during co-firing coal and straw. Fuel. 2007;86:1008–20. [Google Scholar]
42. Schreiner M, Kampichler G, Krzack S, Meyer B. Thermodynamic modelling of co-firing coal and biomass pyrolysis gas in a power plant. Fuel Process Technol. 2011;92(4):787–92. [Google Scholar]
43. Chen CX, Bi YX, Huang YT, Huang HZ. Review on slagging evaluation methods of biomass fuel combustion. J Anal Appl Pyrolysis. 2021;155:105082. [Google Scholar]
44. Wang SR, Lu Q, Zhang HY, Yuan HR, Yang HP, Wang CG, et al. Virtual special issue of recent research advances in China: thermochemical processing of biomass and solid wastes. Energy Fuels. 2021;35(3):1885–9. [Google Scholar]
45. Liao CP, Wu CZ, Yan YJ, Huang HT. Chemical elemental characteristics of biomass fuels in China. Biomass Bioenergy. 2004;27(2):119–30. [Google Scholar]
46. Suyatno S, Hariana H, Adi P, Hanafi PP, Nimas MSS, Arif D, et al. Assessment of potential tropical woody biomass for coal co-firing on slagging and fouling aspects. Therm Sci Eng Prog. 2023;44:102046. [Google Scholar]
47. Zhou WJ, Pan PY, Zhang NQ. Experimental study on the melting and slagging characteristics of herbaceous biomass ash in Northeast China. Therm Power Gener. 2022;51(3):60–9 (In Chinese). [Google Scholar]
48. Karlsson S, Amand LE, Liske J. Reducing high-temperature corrosion on high-alloyed stainless steel superheaters by co-combustion of municipal sewage sludge in a fluidised bed boiler. Fuel. 2015;139(1):482–93. [Google Scholar]
49. Bi YX, Chen CX, Huang XD, Wang HK, Wei GS. Discrimination method of biomass slagging tendency based on particle swarm optimization deep neural network (DNN). Energy. 2023;262:12536. [Google Scholar]
50. Yang RL, Ma C, Chen GY, Cheng ZJ, Yan BB, Mansour M. Study on NOx emission during corn straw/sewage sludge co-combustion: experiments and modelling. Fuel. 2021;285(1):119208. [Google Scholar]
51. Gao RD, Yin SY, Song T, Lu P. Numerical simulation of co-combustion of pulverized coal and biomass in TTF precalciner. Fuel. 2023;334:126515. [Google Scholar]
52. Grabke HJ, Reese E, Spiegel M. The effects of chlorides, hydrogen-chloride and sulfur-dioxide in the oxidation of steel below deposits. Corros Sci. 1995;37(7):1023–43. [Google Scholar]
53. Zhang JY, Rahman ZU, Wang XB, Wang Z, Li P, Wang YB, et al. Hot corrosion behaviors of TP347H and HR3C stainless steel with KCl deposit in oxy-biomass combustion. J Environ Manage. 2020;263:110411 [Google Scholar] [PubMed]
54. Back SK, Yoo HM, Jang HNa, Joung HT, Seo YC. Effects of alkali metals and chlorine on corrosion of super heater tube in biomass circulating fluidized bed boiler. Appl Chem Eng. 2017;28(1):29–34. [Google Scholar]
55. Yang XY, Song GC, Li ZW, Song Q. Effect of biomass-coal blending combustion on Pb transformation. J Hazard Mater. 2024;461:132697 [Google Scholar] [PubMed]
56. Hu ZC, Wang XHH, Yang HP, Shao JA, Chen HP. Effect of two-stage pretreatment combined acid-washing with aqueous portion of pyrolysis oil and torrefaction on pyrolysis characteristics of corn stalk. Trans Chinese Soc Agric Eng. 2017;33(12):224–9. [Google Scholar]
57. Zhang XJ, Liu H, Chen TZ, Wang GY, Li HY, Hu HY, et al. Application of coatings to alleviate fireside corrosion on heat transfer tubes during the combustion of low-grade solid fuels: a review. Energy Fuel. 2020;34(10):11752–70. [Google Scholar]
58. Davis JR. Handbook of thermal spray technology. Materials Park, OH: ASM Internationa; 2004. p. 54. [Google Scholar]
59. Wang XY. Chlorine-induced high-temperature corrosion characteristics of Ni-Cr alloy cladding layer and Ni-Cr-Mo alloy cladding layer. Corros Sci. 2023;216:111102. [Google Scholar]
60. He B, Zhang NN, Lin DY, Zhang Y, Dong FY, Li DY. The phase evolution and property of FeCoCrNiAlTix high-entropy alloying coatings on Q253 via laser cladding. Coatings. 2017;7(10):157. [Google Scholar]
61. Chi HT, Pans MA, Bai MW, Sun CG, Hussain T, Sun W, et al. Experimental investigations on the chlorine-induced corrosion of HVOF thermal sprayed Stellite-6 and NiAl coatings with fluidised bed biomass/anthracite combustion systems. Fuel. 2021;288:119607. [Google Scholar]
62. Lariot SCA, Rivas-Gutierrez A, Rodríguez-Machín L, Rubio-González A, Iturria-Quintero PJ. Impact of alkalis and chlorides from sugarcane agriculture residues on high temperature corrosion: a review. Oxid Met. 2022;97:451–75. [Google Scholar]
63. Wang H, Cheng LH, Pu JL. Melting characteristics of coal ash and properties of fly ash to understand the slag formation in the shell gasifier. ACS Omega. 2021;6(24):16066–75 [Google Scholar] [PubMed]
64. Ja’baz I, Chen J, Etschmann B, Ninomiya Y, Zhang L. Effect of silica additive on the high-temperature fireside tube corrosion during the air-firing and oxy-firing of lignite (Xinjiang coal)—characteristics of bulk and cross-sectional surfaces for the tubes. Fuel. 2017;187:68–83. [Google Scholar]
65. Zhang Z, Xie JS, Zhang JH, Dong H, Liu SJ, Zhang XB, et al. Simultaneously improving mechanical and anti-corrosion properties of extruded Mg-Al dilute alloy via trace Er addition. J Mater Sci Technol. 2023;150:49–64. [Google Scholar]
66. Vlček J, Ovčačíková H, Velička M, Topinková M, Burda J, Matějková P. The corrosion effect of fly ash from biomass combustion on andalusite refractory materials. Minerals. 2023;13(3):357. [Google Scholar]
67. Molino A, Chianese S, Musmarra D. Biomass gasification technology: the state of the art overview. J Energy Chem. 2016;25(1):10–25. [Google Scholar]
68. Butnaru E, Brebu M. The thermochemical conversion of forestry residues from silver fir (Abies alba Mill.) by torrefaction and pyrolysis. Energies. 2022;15:3483. [Google Scholar]
69. Narobe M, Golob J, Klinar D, Francetič V, Likozar B. Co-gasification of biomass and plastics: pyrolysis kinetics studies, experiments on 100 kW dual fluidized bed pilot plant and development of thermodynamic equilibrium model and balances. Bioresource Technol. 2014;162:21–9. [Google Scholar]
70. Jiang W, Tao JL, Zhong XD, Ye YY, Kang JX, Tang Q, et al. Co-gasification of rural solid waste and biomass in rural areas: simulation and plant-scale process. Environ Res. 2023;235:116684 [Google Scholar] [PubMed]
71. Chen X, Zhang CX, Chen XL, Peng ZK, Gao HT, Gong X. Performance analysis of a novel biomass gasification system coupled to a coal-fired power plant based on heat and water recovery. Energy Convers Manage. 2024;299:117822. [Google Scholar]
72. Niu YQ, Lv Y, Lei Y, Liu SQ, Liang Y, Wang DH, et al. Biomass torrefaction: properties, applications, challenges, and economy. Renew Sustain Energy Rev. 2019;115:109395. [Google Scholar]
73. Czerski G. Pyrolysis and gasification of biomass and waste. Energies. 2022;15:7299. [Google Scholar]
74. Lapidus AL, Shumovskii AV, Gorlov EG. Gasification of coal and biomass mixtures. Solid Fuel Chem. 2023;57:373–80. [Google Scholar]
75. Zhou TX, Zhang WW, Ren DD. Progress in the change of ash melting behavior and slagging characteristics of co-gasification of biomass and coal: a review. J Energy Inst. 2023;111:101414. [Google Scholar]
76. Ziad A, El Dina H, Iman A, Abdullah N, Muhammad N. Natural zeolite catalyst for tar removal in biomass gasification systems: kinetics and effectiveness evaluation. Fuel. 2023;346:128393. [Google Scholar]
Cite This Article
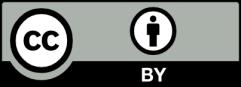
This work is licensed under a Creative Commons Attribution 4.0 International License , which permits unrestricted use, distribution, and reproduction in any medium, provided the original work is properly cited.