Open Access
ARTICLE
Properties of Bark Particleboard Bonded with Demethylated Lignin Adhesives Derived from Leucaena leucocephala Bark
1 Wood Testing Laboratory, Faculty of Tropical Forestry, University of Malaysia Sabah, Kota Kinabalu, Sabah, 88400, Malaysia
2 Industrial Chemistry Program, Faculty of Science and Natural Resources, University of Malaysia Sabah, Kota Kinabalu, Sabah, 88400, Malaysia
* Corresponding Author: Rafidah Md Salim. Email:
Journal of Renewable Materials 2024, 12(4), 737-769. https://doi.org/10.32604/jrm.2024.045695
Received 05 September 2023; Accepted 08 January 2024; Issue published 12 June 2024
Abstract
Lignin extraction from bark can maximize the utilization of biomass waste, offer cost-effectiveness, and promote environmental friendliness when employed as an adhesive material in bark particleboard production. Particles of fine (0.2 to 1.0 mm), medium (1.0 to 2.5 mm), and coarse (2.5 to 12.0 mm) sizes, derived from the bark of Leucaena leucocephala, were hot-pressed using a heating plate at 175°C for 7 min to create single-layer particleboards measuring 320 mm × 320 mm × 10 mm, targeting a density of 700 kg/m. Subsequently, the samples were trimmed and conditioned at 20°C and 65% relative humidity. In this study, we compared bark particleboard bonded with urea formaldehyde (UF) adhesive to fine-sized particleboard bonded with demethylated lignin adhesive. The results indicated that bark particleboards utilizing demethylated lignin and UF adhesives exhibited similar qualities. Coarse particleboard showed differences in modulus of elasticity (MOE) and modulus of rupture (MOR), while medium-sized particles exhibited significant variations in moisture content (MC) and water absorption (WA). Furthermore, the thickness swelling of coarse and medium-sized particles under wet and oven-dried conditions exhibited notable distinctions. Overall, the demethylated lignin adhesive extracted from L. leucocephala bark demonstrated similar quality to UF adhesive, with particle size correlating inversely to the strength of the bark particleboard.Graphic Abstract
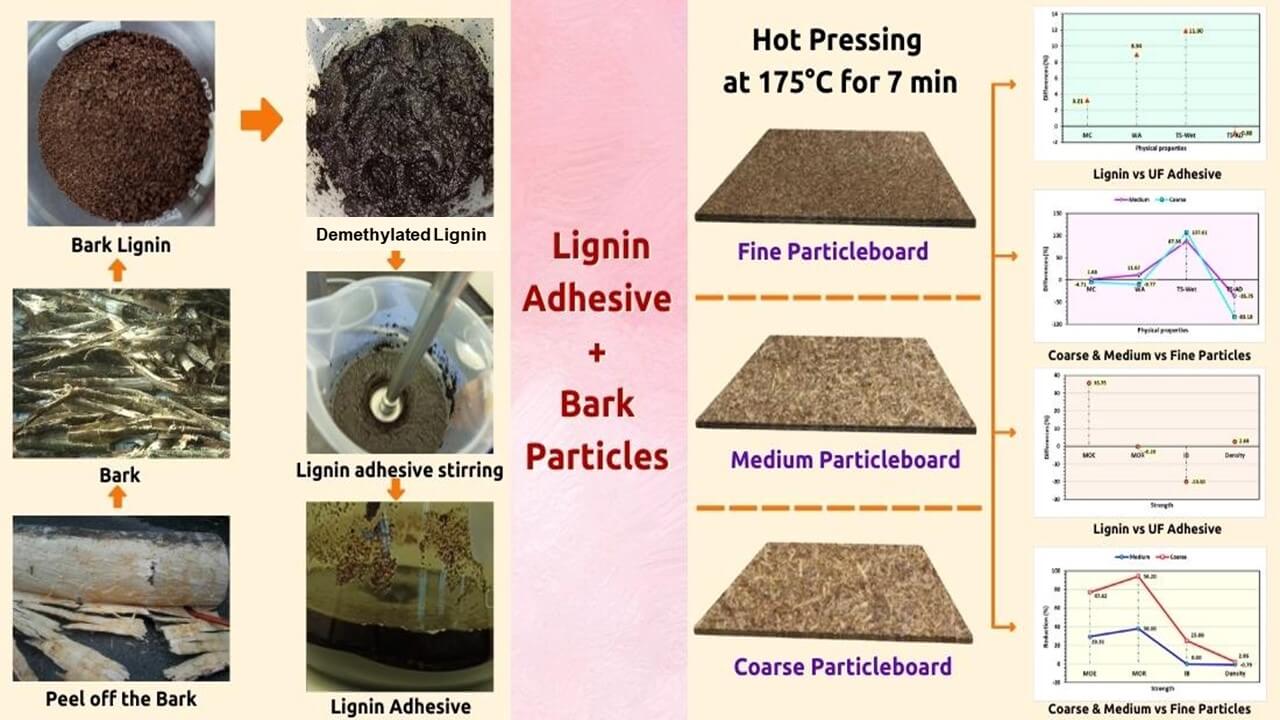
Keywords
Nomenclature
UF | Urea formaldehyde |
MOE | Modulus of elasticity |
MOR | Modulus of rupture |
MC | Moisture content |
TS | Thickness swelling |
TS-Wet | Thickness swelling from wet to oven dry conditions. |
TS-AD | Thickness swelling from air-dry to oven dry conditions. |
IB | Internal bonding |
N | Newton |
MPa | Megapascal |
ρ | Density |
µm | Micrometer |
cps | Centipoise |
Bark, a waste product in the timber industry, holds the potential for conversion into valuable materials, promoting resource efficiency and waste reduction [1,2]. The use of lignocellulosic materials, such as bark particles, as a source for engineered wood products aligns with the growing interest in eco-friendly alternatives and sustainable materials [3]. The development of these materials is driven by the need to address environmental concerns and reduce reliance on fossil-based composites [4]. Through the utilization of bark and other lignocellulosic materials, the timber industry can contribute to a circular economy by transforming waste into high-value-added products [5]. This approach is in line with the goals of the Waste Framework Directive, which aims to promote recycling and shift linear economic processes towards circular ones. The utilization of bark as a raw material for engineered wood products offers a promising solution for improving resource efficiency and reducing waste in the timber industry.
Bark particleboard is a type of composite material made from particles or fibers derived from bark, which is a byproduct in the lumber industry that involves extracting small particles or fibers from various types of bark [6]. These particles are then combined with an adhesive to bind them together. The mixture is subjected to heat and pressure in a hot press to fuse the particles and create a solid board [7]. After hot pressing, the particleboard is cooled and may undergo additional finishing processes [8]. Bark particleboard offers advantages such as sustainability and cost-effectiveness [9]. However, there are challenges in achieving strong adhesion between bark particles and ensuring consistent processing. The properties of bark particleboard can be influenced by factors such as the type of bark, adhesive formulation, and manufacturing process. Researchers and manufacturers can explore different formulations and techniques to optimize the properties of bark particleboard for specific applications. Environmental considerations are vital in bark particleboard manufacturing to ensure sustainability and eco-friendliness. Bark particleboard utilizes bark as a raw material, reducing waste and maximizing resource use [10]. Adhesive selection should prioritize environmentally friendly options with low formaldehyde emissions or formaldehyde-free formulations [11].
Traditional particleboard adhesives have limitations that can affect performance, environmental impact, and health considerations. These limitations include formaldehyde emissions, health concerns, environmental impact, volatile organic compounds (VOCs), moisture sensitivity, energy intensity, global warming potential, adhesion challenges, recyclability challenges, and cost considerations. To address these limitations, there is a growing interest in developing and adopting alternative adhesives, such as bio-based adhesives and lignin-based adhesives, to create particleboard with improved sustainability and performance characteristics [12,13].
Lignin is a complex, amorphous polymer found in plant cell walls, and its structure can vary depending on the plant source. It consists of three main types of phenolic compounds: p-Hydroxyphenyl (H) units, guaiacyl (G) units, and syringyl (S) units. These units are connected by various chemical bonds, including ether linkages and carbon-carbon bonds, forming a complex three-dimensional network [14]. The macromolecular structure of lignin is illustrated in Fig. 1. The arrangement of these units can vary, resulting in different properties and applications of lignin-based materials [15].
Figure 1: Lignin’s macromolecular structure is shown schematically (Major monolignol units are colored as sinapyl alcohol-red, guaiacyl alcohol-blue, p-coumaryl alcohol-green) [16]
Lignin can be extracted from lignocellulosic biomass through various methods, such as physical, chemical, and biological processes. The depolymerization of lignin into value-added chemicals and fuels is a challenging process due to its complex structure [17]. However, there is ongoing research on the conversion of lignin into monomeric aromatic derivatives, which can serve as building blocks for various applications, including chemical synthesis, biomaterials, and bio-oils [18]. The use of bark as a particleboard and adhesive can maximize the utilization of wood resources and minimize waste [19–21]. Bark contains a higher amount of lignin compared to wood, which imparts self-adhesive properties [22]. The structure of lignin extracted from extracted-free bark is illustrated in Fig. 2.
Figure 2: The structure of lignin extracted from extracted-free bark [23]
The main distinction between lignin found in wood flour and bark powder is in their respective lignin compositions and structures. Bark lignin’s composition might vary from that of wood lignin; it frequently has a higher concentration of extractives and a larger percentage of certain phenolic chemicals [24]. However, the lignin found in wood flour normally originates from the plant’s woody portion, and the composition of this substance varies depending on the type of wood [25]. Bark frequently has higher concentrations of extractives than wood grain, such as tannins and resins [26]. Furthermore, differences in the arrangement of phenolic chemicals and links within the chemical structure of lignin in bark may have an impact on the reactivity and characteristics of this material [27]. Bark powder and wood flour can also have different physical properties. Bark powder is usually rougher in texture and contains a mixture of inner and outer bark layers, while wood flour is usually finer in texture and made up of pulverized wood particles [28]. The content, structure, and physical qualities of lignin differ between wood flour and bark powder, which influences the lignin’s properties and possible uses. However, the low molecular weight of lignin from bark can result in weak internal hydrogen bonds [29]. To strengthen the internal bond of bark particleboards, NaOH can be used to bleach methyl compounds and methylene groups in the bark, thereby enhancing the adhesive properties.
Demethylated lignin, derived from the bark particles of Leucaena leucocephala, is a promising alternative with attractive adhesive properties due to its ability to form cross-linkages between lignocellulosic surfaces. Lignin is a natural polymer found in plant cell walls and is a renewable resource [30]. Lignin can be obtained through various processes, such as organosolv extraction, enzymatic depolymerization, and chemical modification [31,32]. These methods allow for the conversion of lignin into high-value materials, including bio-based products, specialty chemicals, and biomaterials [33]. The combination of lignin with biopolymers, such as starch, polylactic acid, and plant proteins, has been explored to enhance the properties of biopolymeric materials. The use of lignin in agriculture as agrochemicals, such as fertilizers, pesticides, and soil improvers, has also gained attention. Demethylated lignin offers a renewable and eco-friendly alternative with potential applications in various industries, including adhesives, materials, agriculture, and biofuels.
Methylation of lignin involves the introduction of methyl (CH3) groups into the lignin structure, modifying its chemical properties. This process is commonly used to make lignin more soluble and reactive for various industrial applications. Lignin can be isolated from lignocellulosic biomass, such as wood, agricultural residues, and pulp mill by-products [34]. A methylating agent, such as dimethyl sulfate (DMS), methyl iodide, or dimethyl carbonate (DMC), is selected for the methylation reaction [35]. The reaction is typically conducted in the presence of a base, such as sodium hydroxide (NaOH), under controlled temperature and pressure conditions [36]. During the reaction, the methylating agent replaces hydrogen atoms in the lignin molecules with methyl groups, which can occur at various positions within the lignin structure [37]. Quenching the reaction with an acid or base is necessary to stop further methylations, and purification techniques, such as filtration or precipitation, are employed to remove impurities and by-products [38]. Methylation of lignin can increase its solubility, reactivity, and compatibility for applications in adhesives, coatings, and composite materials.
The lignin demethylation reaction as observed by Li et al. [39] is shown in Fig. 3. The free hydroxyl -group’s reactivity was hampered because one or two -OCH3 groups were replaced in the ortho positions of the aromatic hydroxyl in the nine-carbon unit of lignin. The demethylated lignin compounds would have much more free phenolic groups, and their reactivity would be greatly enhanced if the -OCH3 groups could be eliminated [40]. Some studies suggest that when attacked by nucleophiles like SO32−, S, and HS−, lignin’s -OCH3 groups will be removed by a nucleophilic substitution reaction, resulting in demethylated lignin that has a higher concentration of phenolic-OH groups and fewer -OCH3 groups [40,41].
Figure 3: Lignin demethylation reaction
Demethylated lignin adhesives have a lower environmental impact compared to synthetic adhesives and are often biodegradable, aligning with eco-friendly practices [42]. The demethylation process improves the adhesive properties of lignin, making it suitable for bonding various materials in composite production. These adhesives exhibit good compatibility with other bio-based materials, enhancing the sustainability of composite materials [43]. They also contribute to the enhancement of mechanical properties in composites, such as strength and stiffness [44]. Demethylated lignin adhesives offer versatility in formulation, allowing for adjustments to meet specific application requirements. They may have lower formaldehyde emissions compared to traditional adhesives, making them suitable for applications where formaldehyde emissions are a concern. Depending on sourcing and processing methods, demethylated lignin adhesives can be cost-competitive, contributing to potential cost savings. These adhesives support the development of innovative and sustainable products, aligning with the demand for environmentally friendly materials and sustainable manufacturing practices.
Leucaena leucocephala bark possesses unique properties that make it suitable for various applications, including composite material production like bark particleboard. The fiber composition of the bark, including characteristics such as length, diameter, and flexibility, contributes to the overall properties of materials derived from it. The lignin content in Leucaena leucocephala bark can influence its adhesive properties, making it potentially suitable for the development of adhesives used in composite material production. The chemical composition of the bark, including the presence of secondary metabolites, can contribute to its unique properties, such as durability and resistance to decay. The bark is likely to be biodegradable due to the presence of organic materials. Leucaena leucocephala is known for its fast growth and adaptability, making the bark readily available and sustainable. The bark may contain natural extractives with antimicrobial or antioxidant properties, enhancing its resistance to biological degradation. Understanding the bark’s moisture absorption, dimensional stability, color, aesthetics, resistance to pests and decay, and specific mechanical properties is crucial for optimizing its use in various applications, including bark particleboard production [45–47].
The separation of fine, medium, and coarse particle sizes is effective in improving the quality of particleboards. The size of particles and press time are important factors in the manufacturing of particleboards, with different combinations yielding varying levels of flexural strength, modulus of elasticity, and water absorption [48]. Previous studies have shown that the separation of fine, medium, and coarse bark particle sizes can effectively improve the quality of particleboards. Fine-sized particles have been found to produce good physical quality of bark particleboards, while coarse bark particles have been shown to produce better mechanical quality compared to medium and fine particles [49].
In this study, lignin was extracted from the bark of L. leucocephala and underwent a methylation process before being modified into an adhesive in fine (0.2 to 1.0 mm), medium (1.0 to 2.5 mm), and coarse (2.5 to 12.0 mm) sized bark particleboards from the same bark species. The main objective is to compare the physical and mechanical quality of L. leucocephala bark particleboard using lignin and urea formaldehyde (UF) adhesives. A comparison was also made on lignin adhesive particleboard using particles of different sizes (fine, medium, and coarse).
There are three phases in this research project. In phase one (collection of bark), the bark was collected, and extractives were removed before bark lignin extraction was conducted in the second phase. Particleboard manufacturing was carried out in the third phase. All the processes were conducted in the field, at the mill, in wood chemistry and wood testing laboratories.
Eleven-year-old Leucaena leucocephala bark was used in this study. The tree was harvested from UMS, Kota Kinabalu, Sabah, Malaysia. The location of this tree was surrounded by a forest area within the UMS campus. The trunk of the tree was manually peeled, and only bark from the stem of the tree was taken and identified by botanist experts from the Forestry Division, UMS. All the samples were transferred to a mill for further processing.
2.2 Preparation of Bark Particles
The bark was gently washed in tap water to remove dirt before being air-dried in the laboratory at room temperature (25 ± 2°C) for 2–3 weeks, protected from direct heat or sunlight. When dried, the stem was chipped, flaked, and pulverized into a coarse powder using a laboratory grinder. The powder was then passed through a BS 500-µm mesh sieve and retained on a 250-µm mesh sieve for lignin extraction.
For particleboard preparation, the dried bark was crushed in a four-shaft drum chipper and flaked before the particles were separated with a multiscreen separator. Using filter sieves, coarse (2.5 to 12.0 mm), medium (1.0 to 2.5 mm), and fine (0.2 to 1.0 mm) particles were collected. The particles were dried to a moisture level of 12 percent. Fig. 4 shows the preparation of bark particles from the peeling process to the separation of particle sizes using a vibrating sieve machine.
Figure 4: Preparation of bark particles into fine, medium, and coarse sizes
2.3 Preparation of Extractive-Free Bark Particles
Approximately 40 g of bark in a thimble (Whatman) was placed in a Soxhlet extraction flask. Extraction was performed with 150 ml of an ethanol solution. A total of 427 ml of toluene was added to reach a final volume of 1 L with the addition of ethanol. The solvent was mixed well. The extraction was conducted for 6 h. Subsequently, the flask was evaporated and dried in an oven at 103 ± 2°C for 1 h before being cooled and weighed [50]. Air-dried extractive-free bark was placed in a thimble (Whatman) and used for bark lignin extraction.
Approximately 35 g of air-dried extractive-free bark powder was accurately weighed and transferred to a 500-ml tall beaker. Three hundred sixteen milliliters of 72% sulfuric acid were carefully added with a pipette, and the mixture was stirred with a small glass rod (which was left in the beaker). The beaker was placed in a cold-water bath at 20°C for 2 h while stirring every 10 min. At the end of the period, the mixture was transferred to a 1 L Erlenmeyer flask containing 560 ml of hot distilled water [51]. A condenser reflux was connected to the Erlenmeyer flask, and the sample was boiled on a hot plate for 4 h.
When refluxing was completed, the insoluble lignin was recovered by filtration through a crucible with a known weight (porosity 4). The residue was rinsed with 500 ml of hot water and dried in an oven at 103 ± 2°C for 24 h before being cooled and weighed. The lignin content was then ready for adhesive preparation.
Approximately 29.5 g of lignin powder (96% solid) was slowly added to 47.6 g of water. Then, 14 g of 30% sodium hydroxide was added intermittently to maintain the pH of the solution between 12 and 12.5 for better dissolution of the lignin powder, which was also facilitated by vigorous stirring with an overhead stirrer.
The solution was transferred to a 1 L flat-bottom flask equipped with a condenser, thermometer, and magnetic stirrer. It was heated to 58°C. Subsequently, 8.75 g of sodium sulfite (40% in water) was added to the lignin solution and continuously stirred on a hot plate for 8 h [52]. The solid content of all demethylated lignin was approximately 41.5%.
2.6 Manufacturing of Lignin Adhesive Bark Particleboards
The physical and mechanical properties of fine, medium, and coarse-sized bark particleboards were tested using the JIS A5908 [53] technique with slight modifications. In a spinning drum mixer, the coarse bark particles were combined with the produced lignin adhesive (pH 11–11.5) for five minutes. Prior to mixing with the bark particles, the lignin glue was blended with 1% hardener (Ammonium chloride). The resulting mixture was manually poured onto a frame before being thermos-pressed with a hydraulic press for seven minutes to form a panel. A similar pressure, corresponding to the required pressure, was applied to all boards to close the mold with a fixed internal volume, reaching the target density.
The hydraulic hot press employed two 350 mm × 350 mm heating plates to press 150 single-layer 320 mm × 320 mm × 10 mm particleboards with a target density of 0.700 kg/m3. To achieve uniform thickness, the boards were hard-pressed with a sole daylight press at 140 kg/m2, and ten-millimeter-thick stops were inserted along the mat’s edges. The pressure was applied at a temperature of 175°C. The press closed in 20 s, cured in 300 s, and opened in 60 s, totaling 380 s of press cycles. The medium and fine bark particles were treated in the same way. A total of twelve bark particleboards were produced, consisting of four boards of each size. Fig. 5 depicts the manufacturing process of demethylated lignin obtained from bark and the production of lignin adhesive bark particleboards at various particle sizes, utilizing hot pressure at a temperature of 175°C for 7 min.
Figure 5: Manufacturing process of bark particleboards with lignin adhesive
After production, all particleboards were conditioned at 20°C and 65% relative humidity until they reached equilibrium moisture content. The physical and mechanical qualities of the particleboards were then determined by cutting samples. Physical qualities were assessed by measuring moisture content, water absorption, thickness, and dimensional swelling, while mechanical properties were evaluated using the modulus of elasticity (MOE), modulus of rupture (MOR), and internal bonding (IB). Table 1 provides information on the manufacturing of the particleboards and the dimensions of the samples used for the tests.
2.7 Evaluation of the Bark Particleboard Properties
Table 1 presents information regarding the bark particles and lignin adhesives used in the manufacturing of bark particleboards. Additionally, urea formaldehyde (UF) adhesives, with a pH of 7.7, a solid content of 51.2, and a viscosity of 138 cps, were used as adhesives in bark particleboards for comparison purposes. Each test was conducted with eight (8) replications. The determination of moisture content (MC), water absorption (WA), thickness swelling (TS), modulus of elasticity (MOE), modulus of rupture (MOR), and internal bonding (IB) was performed for the bark particleboards.
2.7.1 Determination of Moisture Content
A total of twenty-four 50 mm × 50 mm × 10 mm samples of particleboard, produced with coarse, medium, and fine particles of L. leucocephala bark, were subjected to moisture content (MC) evaluations. All samples were conditioned in a conditioning room at 25 ± 2°C and 65 ± 2% relative humidity (approximately 12% MC) until they reached a consistent weight. The samples were then weighed and oven-dried at 103 ± 2°C until a consistent weight was obtained. Finally, the oven-dry weights were recorded and used to compute the moisture content of the bark particleboards using Eq. (1).
2.7.2 Determination of Water Absorption
The bark particleboard samples (50 mm × 50 mm × 10 mm) were fully saturated in water for 24 h. Subsequently, the samples were weighed using an analytical scale and then oven-dried at 103 ± 2°C until a consistent weight was achieved. Afterward, the samples were placed in a desiccator. Eq. (1) was also applied to calculate the water absorption percentages of the bark particleboard samples.
Moisture content/water absorption,
where Wi represents the initial weights of the samples in grams and WOD denotes the oven-dried weights of the samples in grams.
2.7.3 Determination of Thickness Swelling
Before and after the samples were oven-dried for 48 h at 103 ± 2°C, measurements were taken (see Eq. (2)).
Thickness swelling,
where Ti is the initial thickness (mm) and To represents the final thickness (mm).
2.7.4 Determination of Density
Twenty-four samples (50 mm × 50 mm × 10 mm) were conditioned in a conditioning room at 25 ± 2°C and 65 ± 2% relative humidity (approximately 12% MC) until a consistent weight was achieved. We then weighed and measured all the conditioned samples. Each sample was measured in three dimensions (length, width, and thickness), with each dimension marked with waterproof ink. Measurements were taken both before and after the samples were oven-dried for 24 h at 103 ± 2°C. Eq. (3) was utilized to determine the density of the bark particleboard samples.
where Wo represents the oven-dry weight in kg and Vg corresponds to the volume in m3 of the samples.
2.7.5 Determination of MOR and MOE
The samples were conditioned at 20°C and 65% relative humidity (equilibrium moisture content at 12%) until a consistent weight was achieved before measuring the MOR and MOE. Particleboard samples with dimensions of 250 mm (length) × 50 mm (width) × 10 mm (thickness) were tested in a testing room using an Instron 1195 Universal Testing Machine connected to a computer. The strength properties of the samples were evaluated according to Eqs. (4) and (5).
where P represents the load at the proportional limit (N), b is the width of the specimens (mm), h denotes the depth of the specimens (mm), L is the span of the samples (210 mm), P′ is the maximum load (N), and d is the deflection at the proportional limit (mm).
The internal bonding strength test demonstrated the quality of particle bonding by measuring the tensile strength perpendicular to the particleboard surface. The test was conducted following the European Standard BS EN 319:1993. Specimens, measuring 10 mm3 × 50 mm3 × 50 mm3 (thickness, width, and length), were subjected to stretching at a constant speed of 2 mm-1 under a static load. Eq. (6) was employed to calculate the tensile strength in the perpendicular direction, IB.
where Pmax is the maximum load in N, b denotes the width of the specimen in mm, and L represents the length of the sample in mm.
To determine the differences between adhesives and particle sizes, a one-way analysis of variance (ANOVA) was conducted, and the average value for each particleboard size was compared using the least significant difference (LSD) assessment. The investigation was carried out using the Statistical Package for the Social Sciences (SPSS) software program.
The results and discussions of this investigation are divided into two parts. In the first stage, tests on the physical and mechanical properties of Leucaena leucocephala bark particleboard were conducted using lignin adhesive compared to urea formaldehyde (UF). In the second stage, a comparison between particle sizes (fine, medium, and coarse) was made for bark particleboard that uses lignin as an adhesive.
Fig. 6 shows the lignin adhesive bark particleboards with (a) fine (0.2 to 1.0 mm), (b) medium (1.0 to 2.5 mm), and (c) coarse (2.5 to 12.0 mm) particle sizes.
Figure 6: Front and back surfaces of lignin adhesive-treated bark particleboard at (a) fine (0.2 to 1.0 mm), (b) medium (1.0 to 2.5 mm), and (c) coarse (2.5 to 12.0 mm) particle sizes
3.1 Physical Properties of Bark Particleboard with Lignin Adhesives
Table 2 displays the mean physical properties of fine (0.2 to 1.0 mm) bark particleboard using lignin adhesives. In this study, UF adhesive was employed as a control for comparison. The percentages of moisture content (MC), water absorption (WA), and thickness swelling (TS) results were calculated from wet to oven-dried and air-dried to oven-dried.
The findings indicate that there was no significant difference at p < 0.05 between lignin and UF adhesives in terms of moisture content, water absorption, and thickness swelling in Leucaena leucocephala bark particleboards (Table 2). This suggests that the adhesive using lignin extracted from L. leucocephala bark exhibits similar physical qualities as UF adhesive. However, a comparison of the average values reveals that the bark particleboard with lignin adhesive has slightly higher percentages of moisture content (12.51%), water absorption (137%), and thickness swelling in wet conditions (32.83%) compared to UF adhesive (12.12%, 125.75%, and 29.32%, respectively). Under air-dried conditions, lignin adhesive shows better stability (thickness swelling of 9.93%) than UF adhesive (10.01%).
Lignin-based adhesives are being considered as potential alternatives to traditional urea-formaldehyde (UF) adhesives due to their comparable properties. Lignin, a complex organic polymer found in plant cell walls, is one of the most abundant renewable resources. These adhesives offer several advantages, including environmental friendliness and sustainability, as they are derived from renewable biomass sources [54]. They also have the potential to enhance the mechanical and physical properties of wood-based composites, such as particleboard panels, when used as binders [21]. Additionally, lignin-based adhesives can exhibit good adhesive properties, strength, and water resistance when modified with various dispersing agents and cross-linkers [55]. The incorporation of lignin into polyurethane elastomers has been shown to enhance their self-healing properties while maintaining mechanical strength [55]. Lignin-based adhesives offer a promising alternative to UF adhesives, providing a more sustainable and environmentally friendly option for the wood products industry.
Leucaena leucocephala bark particleboard using UF adhesive exhibits slightly better water resistance compared to lignin adhesive. However, lignin adhesives demonstrate greater stability in an air-dry environment. Fig. 7 illustrates the differences in physical properties between bark particleboards with lignin adhesive and urea formaldehyde (UF) adhesive.
Figure 7: Physical properties of lignin adhesives in bark particleboard compared to UF adhesive
Bark particleboard with lignin adhesive exhibited 3.21%, 8.94%, and 11.9% higher moisture content, water absorption, and thickness swelling under wet conditions compared to UF adhesive (Fig. 7). This difference may be influenced by the lower internal bonding strength between bark particleboard and lignin adhesives, as UF adhesives were expected to have better internal bonding strength. The reduction of 0.8% in thickness swelling for lignin adhesive compared to UF adhesive suggests that environmental conditions influenced the stability of the particleboards (Fig. 7). It indicates that bark particleboard bonded with lignin adhesive performed excellently in terms of water resistance under air-dried conditions compared to UF particleboard.
Lignin adhesives derived from plant cell walls offer a bio-based alternative to synthetic adhesives in particleboard production. They offer advantages such as lower formaldehyde emissions and renewable, sustainable properties. However, particleboards bonded with lignin adhesives tend to have a slightly higher moisture content, ranging from 5% to 10%, compared to those bonded with synthetic adhesives. This can affect dimensional stability if not properly controlled during manufacturing and usage. Additionally, lignin adhesives may exhibit lower water resistance compared to some synthetic adhesives [54].
Water absorption is directly proportional to thickness swelling, where high water absorption of bark particleboard leads to increased thickness swelling. This phenomenon may be influenced by the chemical properties of L. leucocephala bark, where the high lignin content (38.24%) affects increased solubility in cold water (11.06%) and hot water (14.45%) [56].
Urea formaldehyde (UF) adhesives have traditionally been used in particleboard manufacturing due to their cost-effectiveness and excellent bonding properties [54]. However, they have faced concerns related to formaldehyde emissions and environmental impact [57]. UF-bonded boards generally exhibit lower moisture content, ranging from 3% to 7% [58], compared to lignin adhesive-based boards, resulting in improved dimensional stability [59]. UF adhesives provide excellent bonding strength, leading to high-quality particleboard [60]. However, UF adhesives can emit formaldehyde, posing potential health risks, and are derived from non-renewable resources, making them less environmentally friendly.
The physical properties revealed that lignin-adhesive bark particleboard is comparable to UF-adhesive bark particleboard (Fig. 7). The performance of bark particleboard with lignin adhesive excels in air-dry conditions, exhibiting superior bonding properties, strength, and overall quality [54]. Conversely, bark particleboard with UF adhesive performs better in terms of water resistance in wet conditions, maintaining its adhesive properties and resisting the effects of moisture [21]. The choice between these adhesives depends on the specific application and the environmental conditions the particleboard will be exposed to. Lignin adhesives are often chosen as a natural and eco-friendly alternative, while UF adhesives are commonly selected for their water-resistant properties [61]. Manufacturers make the appropriate adhesive choice based on the intended application and the performance requirements of the final product [62].
3.2 Physical Properties of Bark Particleboard with Various Particle Sizes and Lignin Adhesives
Table 3 presents the mean physical properties of bark particleboard using lignin adhesives with various particle sizes. In this study, fine particles were used as a control for comparison.
The results demonstrate that there were significant differences at p < 0.05 for moisture content and water absorption among the medium particle sizes, while the thickness swelling of bark particleboard with fine, medium, and coarse particles under both conditions was also significant (Table 3). Medium-sized particles had the highest moisture content (12.72%) and water absorption (152.99%), followed by fine-sized particles (12.51% and 137%) and coarse-sized particles (11.92% and 123.61%), respectively. This variation can be attributed to the presence of more empty areas for absorbed water to fill, especially in cell lumens [63]. The increased surface area of the smaller, finer particles provided additional hydroxyl groups for the water to access within the cellulose nanofibrils, resulting in a higher moisture content [64].
Fine particleboard is crafted from small-sized bark particles, typically ranging from dust-like particles up to 1 mm in diameter. It features a smooth surface and a dense structure, making it ideal for applications that demand a smooth and even finish. Common uses include furniture manufacturing, cabinetry, and interior decorations. Medium particleboard, on the other hand, is composed of larger particles than fine particleboard, generally ranging from 1 to 3 mm in diameter. It strikes a balance between cost, surface smoothness, and structural integrity, rendering it suitable for general-purpose applications in furniture making, shelving, and as a substrate for laminates and veneers. Coarse particleboard is crafted from the largest particles among the three types, typically ranging from 3 to 8 mm in diameter. It possesses higher porosity and is less smooth compared to fine and medium particleboard, making it suitable for structural applications where strength and load-bearing capacity are crucial, such as in construction, flooring, and heavy-duty furniture [65–67].
Fine bark particles, which are the smallest particles obtained from bark, possess a larger surface area, leading to faster moisture absorption and evaporation. The moisture content of fine bark particles can vary from approximately 30% to 70% or higher, depending on environmental conditions and the type of bark. Medium bark particles, larger than fine particles but smaller than coarse ones, strike a balance between surface area and size, resulting in a moisture content range of 20% to 60% [68]. Coarse bark particles, the largest among the three categories, have a lower surface area compared to fine and medium particles, making them less susceptible to rapid moisture changes. The moisture content of coarse bark particles can range from about 10% to 40% [69].
Both an increase and a decrease in value are observed in thickness swelling. Fine particle size exhibited the least amount of thickness swelling when wet (32.83%), followed by medium size (61.51%) and coarse size (68.16%) (Table 3). This indicates a linear relationship between the increase in thickness and particle size, as larger particles tend to swell more. In contrast, when the particles are exposed to air-dried conditions, the thickness swelling decreases. Under air-dry conditions, the fine particles showed the largest percentage increase in thickness (9.93%), followed by medium (6.38%) and coarse (1.67%) (Table 3). Fig. 8 illustrates the differences in physical properties between medium and coarse particle sizes compared to fine particles.
Figure 8: Physical properties of lignin adhesive in bark particleboard at different particle sizes compared to fine particles
The moisture content and water absorption of medium-sized particles are 1.68% and 11.67% higher than those of fine particles, respectively. In contrast to coarse particles, which exhibit reduced moisture content and water absorption, there is a notable difference (4.71% and 9.77%) (Fig. 8). Medium-sized particles provide more empty space for water to be absorbed and filled, especially in the cell lumen, due to the lack of particle contact with each other. Larger surface areas of particles allow for better contact among them [70].
The moisture content of coarse bark particles is generally lower than that of fine bark particles due to the difference in surface area-to-volume ratio. Fine bark particles have a higher surface area-to-volume ratio, enabling them to absorb and retain more moisture compared to coarse bark particles [68]. Coarse bark particles, on the other hand, have a smaller surface area but a larger volume, limiting their moisture absorption and retention capabilities [71]. It is important to note that the moisture content of any bark particle can be influenced by various factors, such as environmental conditions, humidity levels, drying methods, and storage conditions [72]. Therefore, the moisture content can vary widely and should be measured using appropriate testing equipment for accurate results [73].
The thickness swelling of coarse particles was 107.61% higher than that of fine particles in wet conditions, primarily due to the high porosity of the coarse bark particleboard compared to that of fine particles (Fig. 8). Similarly, the size of medium particles resulted in an 87.36% higher thickness of swelling compared to fine particles. The results highlight that the larger the particle size, the higher the particle porosity. However, under air-dry conditions, coarse particles are 83.18% more stable than fine particles, with medium particles showing 35.75% lower swelling.
Fine bark particleboard, made from smaller particles with a higher surface area, tends to exhibit higher water absorption rates and more significant thickness swelling when exposed to wet conditions. However, it may also dry more quickly in dry conditions due to its smaller size. Medium bark particleboard, composed of particles of intermediate size, maintains a balanced composition, resulting in moderate water absorption and thickness swelling properties. It also exhibits moderate thermal expansion and contraction rates, making it less susceptible to extreme dimensional changes. Coarse bark particleboard, composed of larger particles with a lower surface area, displays lower water absorption rates and reduced thickness swelling in wet conditions. However, it may have slower drying rates in dry conditions due to its larger size. The manufacturing process, binder type, overall density, raw material quality, adhesive used, and storage/exposure conditions also impact particleboard swelling behavior [74,75].
3.3 Mechanical Properties of Bark Particleboard with Lignin Adhesives
Table 4 presents the mean mechanical properties of fine (0.2 to 1.0 mm) particle bark particleboard bonded with lignin adhesives. UF adhesive was used as a comparison to lignin adhesives.
The results showed that there were no significant differences in MOE, IB, or density at p < 0.05 except for MOR (Table 4). This result demonstrates that the mechanical quality of bark particleboard with lignin adhesives is comparable to UF, with lignin adhesive exhibiting less rupture than UF. On average, the bark particleboard with lignin adhesive showed a higher MOE (522.67 MPa × 103) compared to the UF adhesive (385.03 MPa × 103). This suggests that using lignin as an adhesive in bark particleboard increases its elasticity compared to boards using UF adhesive. However, lignin adhesive is more fragile, with the average MOR value of the lignin adhesive board (5.00 MPa × 103) much lower than UF (5.01 MPa × 103).
UF and lignin adhesives play significant roles in improving the MOE (Modulus of Elasticity) and MOR (Modulus of Rupture) of bark particleboard [76,77]. The use of UF (Urea-Formaldehyde) adhesive in combination with tannin or lignin enhances the mechanical properties of the particleboard, resulting in higher MOE and MOR values [78]. Similarly, the use of lignin-based adhesives, such as glyoxalated lignin and magnesium lignosulfonate, improves the mechanical properties of the particleboard, leading to higher MOE and MOR values. These adhesives provide an alternative to UF adhesives, which are known to emit formaldehyde. Lignin-based adhesives show potential for reducing formaldehyde emissions while maintaining acceptable mechanical properties.
Internal bonding of bark particleboard with lignin adhesive (0.04 MPa) is lower than UF (Table 4). UF is known for its outstanding water resistance and high reactivity, which could impact the bonding strength as it reacts with isocyanate groups in the bark particleboard. However, the high-water absorption of the bark particle lignin adhesive could lead to a loss of bonding between the surface bark particles.
UF and lignin adhesives are significant factors in terms of internal bonding. The addition of sulfonated Kraft lignin to UF resin enhances thermal stability and reduces formaldehyde emissions during degradation [79]. Lignin phenol formaldehyde resins synthesized with lignin modifications, such as glyoxal, phenol, ionic liquid, and maleic anhydride, show improved adhesive properties and mechanical strength in wood particleboard panels [80]. Bioinspired wet adhesives derived from lignosulfonate and polyamidoamine-epichlorohydrin exhibit instant wet adhesion and stable bonding strength under various conditions, including high temperatures and long-term soaking [81]. Melamine-urea-formaldehyde adhesive demonstrates excellent adhesion to different micro-surfaces of wood fibers, while lignin-rich compound middle lamella surfaces show reduced adhesion to one-component polyurethane due to their lower polar character [82]. Intraparticle cross-linking of lignin nanoparticles with bisphenol A diglycidyl ether improves their stability and allows for surface functionalization, enabling their application as waterborne wood adhesives with competitive dry/wet adhesive strength [83].
The target density of Leucaena leucocephala bark particleboard manufacturing is 700 kg/m3. However, after hot pressing, the density of bark particleboard using lignin adhesive (782.79 kg/m3) was higher than that of bark particleboard using UF adhesive (762.39 kg/m3) (Table 4). During hot pressing at a temperature of 175°C, the lignin adhesive acts as a filler that fills the voids in the bark particles, while the lignin in the bark particles becomes thermoplastic and melts. UF adhesives have higher reactivity and are more resistant to water penetration.
Particleboards bonded with UF adhesives tend to have relatively higher densities compared to lignin-bonded particleboards. The high density is mainly due to the strong adhesive properties of UF, which result in better bonding between particles, leading to tighter packing and fewer void spaces within the board [54]. Particleboards bonded with lignin adhesives may have slightly higher densities compared to UF-bonded particleboards. The higher density can be attributed to the inherent properties of lignin, which might not provide the same level of adhesive strength as UF. As a result, there could be a slightly lower presence of voids within the board [60]. The specific density values of particleboards bonded with UF and lignin adhesives can vary depending on factors such as particle size and distribution, pressing conditions, and the proportion of bark particles in the formulation [84]. The choice between UF and lignin adhesives for bonding bark particleboard depends on factors such as desired mechanical properties, formaldehyde emissions regulations, sustainability goals, and cost considerations [57].
Particleboard properties can vary based on the specific formulation of adhesives, bark particle composition, and manufacturing process. UF-bonded particleboard generally has higher modulus of elasticity (MOE) and modulus of rupture (MOR) values compared to lignin-bonded particleboard [85]. UF adhesives provide strong and durable bonds, resulting in better mechanical properties [65]. UF-bonded particleboard also tends to have a higher internal bonding (IB) strength [19]. Density can be similar for both UF and lignin-bonded particleboard, depending on the adhesive amount and compaction [77]. Lignin adhesives are considered more environmentally friendly as they are derived from renewable resources [86]. However, the mechanical properties of particleboard can be influenced by various factors, including adhesive formulation, bark particle composition, pressing conditions, and the curing process.
The 35.75% increase in MOE for the bark particleboard with lignin adhesive is attributed to a 2.68% increase in density compared to the bark particleboard with UF adhesive (Fig. 9). This indicates that L. leucocephala bark particleboard using lignin adhesive has a higher quality than the board using UF adhesive.
Figure 9: Strength properties of lignin adhesive in bark particleboard compared to UF adhesive
Particleboards made with UF adhesive tend to have a relatively higher density compared to those made with lignin-based adhesives [54,57]. UF-bonded particleboards often exhibit higher MOE values, indicating greater stiffness and rigidity [79]. They also tend to have higher MOR values, indicating better resistance to bending and external forces [62]. On the other hand, particleboards bonded with lignin-based adhesives may have lower density, MOE, and MOR values compared to UF-bonded boards [77]. Lignin adhesives offer an eco-friendlier alternative, as they are derived from renewable resources and have lower VOC emissions. However, UF adhesives are widely used in commercial particleboard production due to their excellent bonding properties and superior mechanical properties. The choice between UF and lignin adhesives for bark particleboard production depends on factors such as the intended application and environmental considerations.
Fig. 9 shows the decrement of MOR (0.2%) and IB (20%) in bark particleboard with lignin adhesive compared to UF adhesive. UF adhesives, specifically urea-formaldehyde, are widely used in the wood industry due to their ability to create strong bonds and improve the internal bonding strength of particleboard [54]. On the other hand, lignin-based adhesives, derived from a natural polymer found in wood, are considered eco-friendly alternatives to synthetic adhesives. However, achieving comparable internal bonding strength with lignin-based adhesives might be more challenging compared to UF adhesives [62]. UF-based particleboards tend to exhibit relatively high modulus of rupture (MOR) values, indicating improved load-bearing capacity and bending strength [87]. Lignin adhesives, while providing good compatibility with wood particles, may have slightly lower MOR values compared to UF adhesives [88]. This difference in MOR values can influence the suitability of lignin-based adhesives for certain load-bearing and structural applications [79].
3.4 Mechanical Properties of Bark Particleboard with Various Particle Sizes and Lignin Adhesives
Table 5 displays the mean mechanical properties of bark particleboard using lignin adhesives with various particle sizes. In this study, fine particles were used as a control for comparison.
Table 5 demonstrates that there is a substantial difference at p < 0.05 between the coarse particles in MOE and the fine particles in MOR. The three particle sizes of L. leucocephala bark particleboards did not significantly vary in IB and density.
Fine bark particleboard is made from small bark particles that are finely ground or shredded. It has a smoother and more homogenous surface compared to the other types, making it suitable for applications where a smooth surface finish is required, such as furniture manufacturing and cabinetry [65]. Medium bark particleboard is made from bark particles that are larger than those used in the fine variety but smaller than the coarse one. It strikes a balance between smoothness and structural integrity, making it commonly used in applications where both appearance and strength are important, such as wall paneling and doors [19]. Coarse bark particleboard is made from larger bark particles, resulting in a more textured and rougher surface. It tends to be stronger and is commonly used in load-bearing applications, such as sub-flooring and sheathing [89]. Lignin-based adhesives, derived from renewable sources, are used to bond these particleboards. The bonding process is similar for all three types, but the efficiency may vary slightly due to differences in particle size [90].
Fine particles have the highest values in MOE (523 MPa × 103), MOR (5 MPa × 103) and IB (0.04 MPa), followed by medium (369 MPa × 103), (3.1 MPa × 103), (0.04 MPa), and coarse particles (238 MPa × 103), (2.19 MPa × 103), (0.03 MPa), respectively (Table 5). This clearly shows that the finer the particles used in the manufacture of bark particleboard, the better the strength. Fine particles performed best in MOE, MOR, and IB.
Particleboard made from bark particles of different sizes (fine, medium, and coarse) was evaluated for its modulus of elasticity (MOE) and modulus of rupture (MOR) [91]. The results showed that the mechanical properties of the particleboard decreased with increasing bark content [78]. Particleboard made from 50% black spruce bark showed the highest MOE and MOR values, which were 12% and 37% lower than the control, respectively [92]. Particleboard made from trembling aspen bark showed the lowest thickness swelling (TS) [93]. The MOE and MOR of particleboards made from 50% black spruce and trembling aspen bark met the requirements of the ANSI standard for commercial and underlayment grades [92]. However, the dimensional properties (TS and linear expansion) of all the boards did not fulfill the minimum requirements of the ANSI standard.
Fine bark particleboard, made from small bark particles, tends to have a higher internal bonding strength. The small particle size allows for better contact points between the particles and the adhesive, resulting in a stronger bond [94]. Medium bark particleboard, with particles larger than fine but smaller than coarse, typically has moderate internal bonding strength. The larger particles may not allow the adhesive to penetrate as deeply as in the fine version, leading to slightly reduced internal bonding strength [95]. Coarse bark particleboard, made from larger particles, tends to have the lowest internal bonding strength among the three types. The larger particles provide fewer contact points for the adhesive to bond effectively, resulting in lower internal bonding strength [96]. In summary, the significant difference in internal bonding strength of fine, medium, and coarse bark particleboard is primarily due to the particle size. Fine bark particleboard generally exhibits the highest internal bonding strength, followed by medium bark particleboard, and then coarse bark particleboard [97].
The density shows that medium particles have the highest value (789 kg/mm3), followed by fine particles (783 kg/mm3) and coarse particles (760 kg/mm3) (Table 5). This reveals that medium particles are slightly denser than fine and coarse particles. However, the difference in the density of fine and coarse particles is very small, only 0.8%.
The density of bark particleboard is influenced by the size of the bark particles used in the manufacturing process. Fine bark particleboard, made from small bark particles, has a higher density compared to medium and coarse particleboard [65]. Medium bark particleboard, made from larger bark particles, has a moderate density [57]. Coarse bark particleboard, made from larger bark particles that may include wood chips and flakes, has the lowest density among the three types [98]. The choice of particleboard type should align with the intended application, considering factors such as strength requirements, appearance, and cost considerations [99]. The density of bark particleboard can also be influenced by other factors such as adhesive content, pressing pressure, and the manufacturing process [100]. The type of adhesive used, such as lignin adhesive, can also impact the overall density and mechanical properties of the particleboard. Fig. 10 illustrates the mechanical properties of the particle size of bark particleboard lignin adhesive against fine particles.
Figure 10: Mechanical properties of lignin adhesives in bark particleboard at different particle sizes compared to fine particles
Similar patterns can be seen in the MOE, MOR, and IB strength characteristics. The coarse and medium particle sizes exhibit a noticeable loss in strength compared to the fine particles at the same target density of 700 kg/mm3 after being hot-pressed at 175°C for 7 min. This finding demonstrates that when the particle size increases, the mechanical strength loss likewise increases (Fig. 10).
On MOE, the strength of coarse particles dropped by approximately 47.62%, but the strength of fine particles dropped by 29.31%. Similar findings apply to MOR, where medium particles weaken structure by 38% more than coarse particles (56.2%). In contrast to IB, there was no decrease in the strength of coarse particles and only a 25% decrease in the strength of fine particles.
Bark particleboard’s strength characteristics are impacted by different particle sizes. While the density of coarse particles decreased by 2.86% after heat pressing, medium particles were 0.79% denser than fine particles (Fig. 10). This is due to how differently the particle surfaces interact with one another. The interaction of the bark particles and the lignin adhesive used in the production of particleboards made from Leucaena leucocephala bark could also be the cause of the variations.
The reduction in strength due to the use of smaller particle sizes in bark particleboard adhesives, specifically lignin, refers to the potential decrease in the adhesive’s bonding performance and overall strength when compared to coarser lignin particles. This phenomenon is relevant in the context of particleboard production, where lignin often serves as an adhesive binder to hold the wood particles together. Reasons for this strength reduction may include reduced mechanical interlocking, inadequate penetration, increased void spaces, incompatibility with wood particles, and higher water absorption when finer lignin particles are used. To address this strength reduction, manufacturers may consider using a combination of different lignin particle sizes, incorporating other additives or modifiers, and optimizing the adhesive formulation through testing and experimentation. Regular testing and quality control are essential to ensuring the desired strength and performance of the particleboard [21,101].
When reducing the particle sizes of bark particleboard adhesives, specifically lignin, the modulus of elasticity (MOE) and modulus of rupture (MOR) can be affected. The MOE may decrease due to factors such as reduced mechanical interlocking, increased void spaces, and inadequate penetration [60]. The reduction in lignin particle sizes can also impact the MOR by weakening bonding, increasing water absorption, and making it more vulnerable to defects [102,103]. To mitigate these reductions, particleboard manufacturers can consider using a well-balanced combination of different lignin particle sizes, incorporating other additives or modifiers, and conducting thorough testing and quality control [104,105]. Striking the right balance between lignin particle size, adhesive formulation, and processing conditions is essential to achieving the desired MOE, MOR, and other mechanical properties in bark particleboard.
When reducing the particle size of bark particleboard adhesives, specifically lignin, the internal bonding strength can be affected in several ways. Coarser lignin particles tend to have more surface irregularities, leading to better mechanical interlocking with the wood particles in the bark and resulting in stronger bonds and higher internal bonding strength [106]. On the other hand, finer lignin particles have fewer prominent irregularities, leading to reduced mechanical interlocking and potentially lower internal bonding strength [107]. Additionally, finer lignin particles may have difficulty penetrating the pores and voids between the larger wood particles, resulting in weak bonding and a decrease in internal bonding strength [108]. Furthermore, finer lignin particles can create more void spaces between particles, reducing the effective contact area for bonding and weakening adhesion [109]. Finally, fine lignin particles might not form strong bonds with the wood particles due to their smaller size and surface characteristics, leading to insufficient bond strength and a decrease in internal bonding strength [110]. To address these potential issues, particleboard manufacturers can optimize adhesive formulation, incorporate additives or modifiers, fine-tune processing conditions, and implement quality control and testing.
3.5 Physical and Mechanical Properties of Bark Particleboard Demethylated Lignin Adhesives
Based on the results and discussion, Tables 6 and 7 summarize the comparison of physical and mechanical properties between bark particleboard adhesives using urea formaldehyde (UF) and demethylated lignin at various particle sizes from Leucaena leucocephala bark particles.
The study concludes that utilizing lignin adhesives and Leucaena leucocephala bark for particleboard production is environmentally friendly and optimizes biomass resources. The following conclusions can be drawn:
1. Lignin adhesive particleboard exhibits moisture content, air absorption, and swelling thickness comparable to urea formaldehyde (UF) particleboard, with UF outperforming in terms of water resistance. Lignin adhesive particleboard demonstrates increased stability in an air-dry environment, attributed to the enlarged surface area of fine particles.
2. The mechanical properties of bark particleboard with lignin adhesive are on par with those of UF adhesive, except for higher fracture resistance and lower internal bond strength. UF adhesive is renowned for its water resistance, whereas the high-water absorption of lignin adhesive weakens bonds.
3. Board properties are influenced by particle size, with medium-sized particles being denser compared to coarse and fine ones. The utilization of lignin as an adhesive enhances elasticity but results in boards that are more brittle. Fine particles exhibit superior mechanical properties.
In summary, lignin-adhesive particleboard is both environmentally friendly and comparable to UF particleboard in terms of physical and mechanical properties, with some distinctions in fracture resistance and bond strength, which are influenced by particle size.
Acknowledgement: The authors would like to thank Assoc. Prof. Dr. Liew Kang Chiang, Mdm. Murni Sundang, Mr. Awang Ahmad Mohd Yunus, Mr. Airin Termin, and Mr. Azli Sulid for their valuable and encouraging conversation and support. We acknowledge the facilities and scientific and technical support from the Wood Testing Laboratory, Faculty of Tropical Forestry, University of Malaysia, Sabah, Malaysia.
Funding Statement: The authors gratefully acknowledge the financial support provided by UMS Great (GUG0217-1/2018), which played a crucial role in the completion of this study. Additionally, we would like to express our sincere appreciation for the financial assistance and scholarships generously offered by the University of Malaysia Sabah (UMS) and the Ministry of Higher Education Malaysia (KPT) throughout the research period. These contributions were invaluable in facilitating our research endeavors.
Author Contributions: The authors confirm their contribution to the paper as follows: study conception and design: Jahimin Asik and Mohd Sani Sarjadi; data collection: Rafidah Md Salim; analysis and interpretation of results: Rafidah Md Salim; draft manuscript preparation: Rafidah Md Salim, Jahimin Asik, and Mohd Sani Sarjadi. All authors reviewed the results and approved the final version of the manuscript.
Availability of Data and Materials: Data not available due to commercial restrictions. Due to the nature of this research, participants in this study did not agree for their data to be shared publicly, so supporting data is not available.
Conflicts of Interest: The authors declare that they have no conflicts of interest to report regarding the present study.
References
1. Grondahl J, Karisalmi K, Vapaavuori J. Micro-and nanocelluloses from non-wood waste sources; processes and use in industrial applications. Soft Matter. 2021;17(43):9842–58. doi:10.1039/D1SM00958C [Google Scholar] [PubMed] [CrossRef]
2. Safian MTU, Sekeri SH, Yaqoob AA, Serra A, Jamudin MD, Ibrahim MN. Utilization of lignocellulosic biomass: a practical journey towards the development of emulsifying agent. Talanta. 2022;239:123109. doi:10.1016/j.talanta.2021.123109 [Google Scholar] [PubMed] [CrossRef]
3. Delmas GH, Banoub JH, Delmas M. Lignocellulosic biomass refining: a review promoting a method to produce sustainable hydrogen, fuels, and products. Waste Biomass Valor. 2022;13:2477–91. doi:10.1007/s12649-021-01624-6. [Google Scholar]
4. Oliaei E, Lindström T, Berglund LA. Sustainable development of hot-pressed all-lignocellulose composites—comparing wood fibers and nanofibers. Polymers. 2021;13(16):2747. doi:10.3390/polym13162747 [Google Scholar] [PubMed] [CrossRef]
5. Gil A. Current insights into lignocellulose related waste valorization. Chemical Eng J Adv. 2021;8:100186. doi:10.1016/j.ceja.2021.100186. [Google Scholar] [CrossRef]
6. Jiang W, Adamopoulos S, Hosseinpourpia R, Walther T, Medved S. Properties and emissions of three-layer particleboards manufactured with mixtures of wood chips and partially liquefied bark. Materials. 2023;16(5):1855. doi:10.3390/ma16051855 [Google Scholar] [PubMed] [CrossRef]
7. Krug D, Direske M, Tobisch S, Weber A, Wenderdel C. Particle-based materials. In: Springer handbook of wood science and technology. Springer, Cham: 2023. p. 1409–90. doi:10.1007/978-3-030-81315-4_27. [Google Scholar] [CrossRef]
8. Bandityaruck W, Srichaisiriwaech W, Kongkarat S. Utilization of rubber tree bark as a carbon source for electric arc furnace steelmaking: carbon/slag interaction at 1550°C. J Met, Mater Miner. 2022;32(4):128–33. doi:10.55713/jmmm.v32i4.1539. [Google Scholar] [CrossRef]
9. Auriga R, Pędzik M, Mrozowski R, Rogoziński T. Hemp shives as a raw material for the production of particleboards. Polymers. 2022;14(23):5308. doi:10.3390/polym14235308 [Google Scholar] [PubMed] [CrossRef]
10. Sen U, Esteves B, Pereira H. Pyrolysis and extraction of bark in a biorefineries context: a critical review. Energies. 2023;16(13):4848. doi:10.3390/en16134848. [Google Scholar] [CrossRef]
11. Oktavia O, Lestari D, Rokar RK, Kurniawan WB. Particleboard heat insulation pineapple leaf fiber waste and HVS paper as an alternative to improve indoor environmental quality. Jambura Physics J. 2023;5(1):49–56. doi:10.34312/jpj.v5i1. [Google Scholar] [CrossRef]
12. Zymankowska-Kumon S, Kaczmarska K, Grabowska B, Bobrowski A, Cukrowicz S. Influence of the atmosphere on the type of evolved gases from phenolic binders. Arch Foundry Eng. 2020;20(1):31–6. doi:10.24425/afe.2020.131279. [Google Scholar]
13. Dorn L, Thirion A, Ghorbani M, Olaechea LM, Mayer I. Exploring fully biobased adhesives: sustainable kraft lignin and 5-HMF adhesive for particleboards. Polymers. 2023;15(12):2668. doi:10.3390/polym15122668 [Google Scholar] [PubMed] [CrossRef]
14. Behera S, Mohapatra S, Behera BC, Thatoi H. Recent updates on green synthesis of lignin nanoparticle and its potential applications in modern biotechnology. Crit Rev Biotechnol. 2023;1–21. doi:10.1080/07388551.2023.2229512. [Google Scholar]
15. Huda MM, Rai N. Effect of solvent on the interaction of lignin with a zeolite nanosheet in the condensed phase. J Phys Chem B. 2023;127(30):6767–77. doi:10.1021/acs.jpcb.3c02085 [Google Scholar] [PubMed] [CrossRef]
16. Karunarathna MS, Smith RC. Valorization of lignin as a sustainable component of structural materials and composites: advances from 2011 to 2019. Sustainability. 2020;12(2):734. doi:10.3390/su12020734. [Google Scholar] [CrossRef]
17. Ruwoldt J, Blindheim FH, Chinga-Carrasco G. Functional surfaces, films, and coatings with lignin-a critical review. RSC Adv. 2023;13(18):12529–12553. doi:10.1039/D2RA08179B [Google Scholar] [PubMed] [CrossRef]
18. Martínková L, Grulich M, Pátek M, Křístková B, Winkler M. Bio-based valorization of lignin-derived phenolic compounds: a review. Biomolecules. 2023;13(5):717. [Google Scholar]
19. Izdinsky J, Vidholdova Z, Reinprecht L. Particleboards from recycled thermally modified wood. Forests. 2021;12(11):1462. doi:10.3390/f12111462. [Google Scholar] [CrossRef]
20. Silva VUD, Aquino VBDM, Ruthes HC, Christoforo AL, Lahr FAR. Production of mahogany particleboards using branches and wood residues. Ambient Constr. 2021;22:191–9. [Google Scholar]
21. Rizhikovs J, Brazdausks P, Paze A, Tupciauskas R, Grinins J, Puke M, et al. Characterization of suberinic acids from birch outer bark as bio-based adhesive in wood composites. Int J Adhes Adhes. 2022;112:102989. doi:10.1016/j.ijadhadh.2021.102989. [Google Scholar] [CrossRef]
22. Santos J, Pereira J, Ferreira N, Paiva N, Ferra J, Magalhães FD, et al. Valorisation of non-timber by-products from maritime pine (Pinus pinaster, Ait) for particleboard production. Ind Crops Prod. 2021;168:113581. doi:10.1016/j.indcrop.2021.113581. [Google Scholar] [CrossRef]
23. Neiva DM, Rencoret J, Marques G, Gutiérrez A, Gominho J, Pereira H, et al. Lignin from tree barks: chemical structure and valorization. ChemSusChem. 2020;13(17):4537–47. doi:10.1002/cssc.v13.17. [Google Scholar] [CrossRef]
24. Dou J, Ilina P, Cruz CD, Nurmi D, Vidarte PZ, Rissanen M, et al. Willow bark-derived materials with antibacterial and antibiofilm properties for potential wound dressing applications. J Agric Food Chem. 2023;71(44):16554–67. doi:10.1021/acs.jafc.3c00849 [Google Scholar] [PubMed]
25. Traore M, Martinez Cortizas A. Color and chemical composition of timber woods (Daniellia oliveri, Isoberlinia doka, Khaya senegalensis, and Pterocarpus erinaceus) from different locations in southern mali. Forests. 2023;14(4):767. doi:10.3390/f14040767. [Google Scholar] [CrossRef]
26. Cao D, Zhang J, Nie Y, Wang S, Feng X, Zhu J, et al. Valorization of bark to natural lubrication additives via fractionation based on chemical product engineering concept. Chem Eng Sci. 2023;266:118288. doi:10.1016/j.ces.2022.118288. [Google Scholar] [CrossRef]
27. Frankiewicz KE, Chau JH, Baczyński J, Wdowiak A, Oskolski A. Wood and bark structure in Buddleja: anatomical background of stem morphology. AoB Plants. 2023;15(2):plad003. doi:10.1093/aobpla/plad003 [Google Scholar] [PubMed] [CrossRef]
28. Dinulica F, Savin A, Stanciu MD. Physical and acoustical properties of wavy grain sycamore maple (Acer pseudoplatanus L.) used for musical instruments. Forests. 2023;14(2):197. doi:10.3390/f14020197. [Google Scholar] [CrossRef]
29. Zhou M, Chen X, Gao C, Ni L, Wang X, Zhang W, et al. Catalytic hydrogenolysis of larix bark proanthocyanidins in ionic liquids produces UV blockers with potential for use in cosmetics. RSC Adv. 2021;11(48):30078–30087. doi:10.1039/D1RA03197J [Google Scholar] [PubMed] [CrossRef]
30. Parot M, Rodrigue D, Stevanovic T. High purity softwood lignin obtained by an eco-friendly organosolv process. Bioresour Technol Reports. 2022;17:100880. doi:10.1016/j.biteb.2021.100880. [Google Scholar] [CrossRef]
31. Bilal M, Qamar SA, Yadav V, Cheng H, Khan M, Adil SF, et al. Exploring the potential of ligninolytic armory for lignin valorization–A way forward for sustainable and cleaner production. J Clean Prod. 2021;326:129420. doi:10.1016/j.jclepro.2021.129420. [Google Scholar] [CrossRef]
32. Ahmad UM, Ji N, Li H, Wu Q, Song C, Liu Q, et al. Can lignin be transformed into agrochemicals? Recent advances in the agricultural applications of lignin. Ind Crops Prod. 2021;170:113646. doi:10.1016/j.indcrop.2021.113646. [Google Scholar] [CrossRef]
33. Mariana M, Alfatah T, HPS AK, Yahya EB, Olaiya NG, Nuryawan A, et al. A current advancement on the role of lignin as sustainable reinforcement material in biopolymeric blends. J Mater Res Technol. 2021;15:2287–2316. doi:10.1016/j.jmrt.2021.08.139. [Google Scholar] [CrossRef]
34. Sadeghifar H, Ragauskas A. Technical lignin fractionation: a powerful tool for lignin structure homogenization and its application. In: Lignin-based materials: health care and medical applications. The Royal Society of Chemistry; 2023. p. 59–84. [Google Scholar]
35. Zhang C, Shen X, Jin Y, Cheng J, Cai C, Wang F. Catalytic strategies and mechanism analysis orbiting the center of critical intermediates in lignin depolymerization. Chem Rev. 2023;123(8):4510–4601. doi:10.1021/acs.chemrev.2c00664 [Google Scholar] [PubMed] [CrossRef]
36. Hua Q, Liu LY, Cho M, Karaaslan MA, Zhang H, Kim CS, et al. Functional lignin building blocks: reactive vinyl esters with acrylic acid. Biomacromolecules. 2023;24(2):592–603. doi:10.1021/acs.biomac.2c00806 [Google Scholar] [PubMed] [CrossRef]
37. Tran VT, Le TM, Vu PV, Nguyen HM, Duong YH, Le PK, et al. Depolymerization of rice straw lignin into value-added chemicals in sub-supercritical ethanol. Sci World J. 2022;2022:7872307. doi:10.1155/2022/7872307. [Google Scholar]
38. Zhang L, Peng W, Wang F, Bao H, Zhan P, Chen J, et al. Fractionation and quantitative structural analysis of lignin from a lignocellulosic biorefinery process by gradient acid precipitation. Fuel. 2022;309:122153. doi:10.1016/j.fuel.2021.122153. [Google Scholar] [CrossRef]
39. Li J, Wang W, Zhang S, Gao Q, Zhang W, Li J, et al. Preparation and characterization of lignin demethylated at atmospheric pressure and its application in fast curing biobased phenolic resins. RSC Adv. 2016;6(71):67435–67443. doi:10.1039/C6RA11966B. [Google Scholar] [CrossRef]
40. Hu L, Pan H, Zhou Y, Zhang M. Methods to improve lignin’s reactivity as a phenol substitute and as replacement for other phenolic compounds: a brief review. BioResources. 2011;6(3):3515–25. doi:10.15376/biores. [Google Scholar] [CrossRef]
41. Ferhan M, Yan N, Sain M. A new method for demethylation of lignin from woody biomass using biophysical methods. J Chem Eng Process Technol. 2013;4(5):160. [Google Scholar]
42. Peng Z, Jiang X, Si C, Joao Cárdenas-Oscanoa A, Huang CX. Advances of modified lignin as substitute to develop lignin-based phenol-formaldehyde resin adhesives. ChemSusChem. 2023;e202300174. [Google Scholar]
43. Galdino DS, Kondo MY, de Araujo VA, Ferrufino GLAA, Faustino E, Santos HF, et al. Thermal and gluing properties of phenol-based resin with lignin for potential application in structural composites. Polymers. 2023;15(2):357. doi:10.3390/polym15020357 [Google Scholar] [PubMed] [CrossRef]
44. Jimenez Bartolome M, Padhi SSP, Fichtberger OG, Schwaiger N, Seidl B, Kozich M, et al. Improving properties of starch-based adhesives with carboxylic acids and enzymatically polymerized lignosulfonates. Int J Mol Sci. 2022;23(21):13547. doi:10.3390/ijms232113547 [Google Scholar] [PubMed] [CrossRef]
45. Bera K, Patel M. Development of pharmacognostic profile and preliminary phytochemical study of Pluchea wallichiana DC. Indian J Pharm Edu Res. 2023;57. [Google Scholar]
46. Thakur D, Lal UR, Kapoor DN, Kumar D. Identification and quantification of polyphenolic secondary metabolites in stem bark of ficus religiosa (Moraceae) using UPLC-HRMS and RP-HPLC-PDA. Separations. 2023;10(6):338. doi:10.3390/separations10060338. [Google Scholar] [CrossRef]
47. Dylenova EP, Zhigzhitzhapova SV, Goncharova DB, Tykheev ZA, Chimitov DG, Radnaeva LD. Artemisia jacutica Drob. essential oil as a source of chamazulene: primary introduction and component analysis. Foods Raw Materials. 2023;11(2):243–50. doi:10.21603/2308-4057-2023-1-547. [Google Scholar]
48. Farrokhpayam SR, Valadbeygi T, Sanei E. Thin particleboard quality: effect of particle size on the properties of the panel. J Indian Acad Wood Sci. 2016;13:38–43. doi:10.1007/s13196-016-0163-9. [Google Scholar] [CrossRef]
49. Christy EO, Soemarno S, Soehardjono A. Binderless bark particleboard made from gelam (Melaleuca viridiflora sol. ex gaertn.) bark waste: the effect of the pressing temperature on its mechanical and physical properties. BioResources. 2021;16(2):4171. doi:10.15376/biores.16.2.4171-4199. [Google Scholar] [CrossRef]
50. American Society for Testing and Materials, ASTM D1105. Standard test method for preparation of extractive-free wood D1105-96 (Reapproved 2001annual book of ASTM standards 4.10. p. 177–8. Available from: https://file.yizimg.com/175706/2011120520575465.pdf. [Accessed 2024]. [Google Scholar]
51. American Society for Testing Materials, ASTM D1106. Standard test method for acid-insoluble lignin of wood D1106-96 (Reapproved 2001annual book of ASTM standards 4.10. p. 179–80. Available from: https://file.yizimg.com/175706/2011120520563359.pdf. [Accessed 2024]. [Google Scholar]
52. El Mansouri N, Pizzi A, Salvado J. Lignin-based wood panel adhesives without formaldehyde. Holz Roh Werkst. 2007;65:65–70. doi:10.1007/s00107-006-0130-z. [Google Scholar] [CrossRef]
53. Japanese Industrial Standards, JISA5908. Japanese Standard Association. Particleboards (JIS A5908). 2003. p. 1–15. [Google Scholar]
54. Benhamou AA, Boussetta A, Kassab Z, Nadifiyine M, Sehaqui H, El Achaby M, et al. Application of UF adhesives containing unmodified and phosphate-modified cellulose microfibers in the manufacturing of particleboard composites. Ind Crops Prod. 2022;176:114318. doi:10.1016/j.indcrop.2021.114318. [Google Scholar] [CrossRef]
55. Islam MN, Rahman F, Das AK, Hiziroglu S. An overview of different types and potential of bio-based adhesives used for wood products. Int J Adhes Adhes. 2022;112:102992. doi:10.1016/j.ijadhadh.2021.102992. [Google Scholar] [CrossRef]
56. Salim RM, Asik J, Sarjadi MS, Chiang LK. Chemical composition and potential uses of Leucaena leucocephala stem bark. Wood Res. 2023;68(2):241–56. doi:10.37763/wr.1336-4561/68.2.241256. [Google Scholar] [CrossRef]
57. Dadzie PK, Awotwe-Mensah M, Amoah M. Materials mix ratio and binder type effects on physical and mechanical properties of particleboard from mixed-wood sawdust and Cocos nucifera (Coconut) husks. J Indian Acad Wood Sci. 2021;18:128–40. doi:10.1007/s13196-021-00288-y. [Google Scholar] [CrossRef]
58. Goncalves D, Bordado JM, Marques AC, Galhano dos Santos R. Non-formaldehyde, bio-based adhesives for use in wood-based panel manufacturing industry—a review. Polymers. 2021;13(23):4086. doi:10.3390/polym13234086 [Google Scholar] [PubMed] [CrossRef]
59. Oktay S, Kızılcan N, Bengü B. Development of bio-based cornstarch-Mimosa tannin-sugar adhesive for interior particleboard production. Ind Crops Prod. 2021;170:113689. doi:10.1016/j.indcrop.2021.113689. [Google Scholar] [CrossRef]
60. Selakjani PP, Dorieh A, Pizzi A, Shahavi MH, Hasankhah A, Shekarsaraee S, et al. Reducing free formaldehyde emission, improvement of thickness swelling and increasing storage stability of novel medium density fiberboard by urea-formaldehyde adhesive modified by phenol derivatives. Int J Adhes Adhes. 2021;111:102962. doi:10.1016/j.ijadhadh.2021.102962. [Google Scholar] [CrossRef]
61. Liang J, Wu J, Xu J. Low-formaldehyde emission composite particleboard manufactured from waste chestnut bur. J Wood Sci. 2021;67:1–10. [Google Scholar]
62. Liu B, Li Z, Zhang J, Du M, Fang F, Chen F. An environment-friendly wood adhesive using modified wheat gluten by isophorone diisocyanate. Ind Crops Prod. 2021;173:114125. doi:10.1016/j.indcrop.2021.114125. [Google Scholar] [CrossRef]
63. Bazzetto JTDL, Bortoletto G, Brito FMS. Effect of particle size on bamboo particle board properties. Floresta e ambiente. 2019;26(2):e20170125. doi:10.1590/2179-8087.012517. [Google Scholar] [CrossRef]
64. Leng W, Hunt JF, Tajvidi M. Effects of density, cellulose nanofibrils addition ratio, pressing method, and particle size on the bending properties of wet-formed particleboard. BioResources. 2017;12(3):4986–5000. [Google Scholar]
65. Mirindi D, Onchiri RO, Thuo J. Physico-mechanical properties of particleboards produced from macadamia nutshell and gum arabic. Appl Sci. 2021;11(23):11138. doi:10.3390/app112311138. [Google Scholar] [CrossRef]
66. Tanguay-Rioux F, Héroux M, Legros R. Physical properties of recyclable materials and implications for resource recovery. Waste Manag. 2021;136:195–203. doi:10.1016/j.wasman.2021.10.007 [Google Scholar] [PubMed] [CrossRef]
67. Kminiak R, Kučerka M, Kristak L, Reh R, Antov P, Očkajová A, et al. Granulometric characterization of wood dust emission from CNC machining of natural wood and medium density fiberboard. Forests. 2021;12(8):1039. doi:10.3390/f12081039. [Google Scholar] [CrossRef]
68. Jylha P, Halmemies E, Hellström J, Hujala M, Kilpeläinen P, Brännström H. The effect of thermal drying on the contents of condensed tannins and stilbenes in Norway spruce (Picea abies [L.] Karst.) sawmill bark. Ind Crops Prod. 2021;173:114090. doi:10.1016/j.indcrop.2021.114090. [Google Scholar] [CrossRef]
69. Oka A, Takahashi J, Endoh Y, Seino T. Bark effects on stemflow chemistry in a japanese temperate forest II. the role of bark anatomical features. Front For Glob Change. 2021;4:657850. doi:10.3389/ffgc.2021.657850. [Google Scholar] [CrossRef]
70. Hashim R, Saari N, Sulaiman O, Sugimoto T, Hiziroglu S, Sato M, et al. Effect of particle geometry on the properties of binderless particleboard manufactured from oil palm trunk. Mater Des. 2010;31(9):4251–7. doi:10.1016/j.matdes.2010.04.012. [Google Scholar] [CrossRef]
71. Haidar AA, Rishmany J. Investigation of bulk density and friction coefficient of olive residues and sawdust prior to pelletizing. Biomass Convers Biorefin. 2021;1–13. [Google Scholar]
72. Kalman H. Effect of moisture content on flowability: angle of repose, tilting angle, and Hausner ratio. Powder Technol. 2021;393:582–96. doi:10.1016/j.powtec.2021.08.010. [Google Scholar] [CrossRef]
73. Ilek A, Van Stan JT, Morkisz K, Kucza J. Vertical variability in bark hydrology for two coniferous tree species. Front For Glob Change. 2021;4:687907. doi:10.3389/ffgc.2021.687907. [Google Scholar] [CrossRef]
74. Luo HC, Ren X, Zhang Y, Zhang XY, Zhang XG, Luo C, et al. Mechanical properties of foam-filled hexagonal and re-entrant honeycombs under uniaxial compression. Compos Struct. 2022;280:114922. doi:10.1016/j.compstruct.2021.114922. [Google Scholar] [CrossRef]
75. Kapoor R, Feng H. Characterization of physicochemical, packing, and microstructural properties of beet, blueberry, carrot and cranberry powders: the effect of drying methods. Powder Technol. 2022;395:290–300. doi:10.1016/j.powtec.2021.09.058. [Google Scholar] [CrossRef]
76. Hemmila V, Adamopoulos S, Hosseinpourpia R, Ahmed SA. Ammonium lignosulfonate adhesives for particleboards with pMDI and furfuryl alcohol as crosslinkers. Polymers. 2019;11(10):1633. doi:10.3390/polym11101633 [Google Scholar] [PubMed] [CrossRef]
77. Balea Paul G, Timar MC, Zeleniuc O, Lunguleasa A, Coşereanu C. Mechanical properties and formaldehyde release of particleboard made with lignin-based adhesives. Appl Sci. 2021;11(18):8720. doi:10.3390/app11188720. [Google Scholar] [CrossRef]
78. Nath SK, Islam MN, Rahman KS, Rana MN. Tannin-based adhesive from Ceriops decandra (Griff.) bark for the production of particleboard. J Indian Acad Wood Sci. 2018;15:21–7. doi:10.1007/s13196-017-0203-0. [Google Scholar] [CrossRef]
79. Younesi-Kordkheili H, Pizzi A. A comparison among lignin modification methods on the properties of lignin-phenol–formaldehyde resin as wood adhesive. Polymers. 2021;13(20):3502. doi:10.3390/polym13203502 [Google Scholar] [PubMed] [CrossRef]
80. Wei C, Zhu X, Peng H, Chen J, Zhang F, Zhao Q. Facile preparation of lignin-based underwater adhesives with improved performances. ACS Sustain Chem Eng. 2019;7(4):4508–14. doi:10.1021/acssuschemeng.8b06731. [Google Scholar] [CrossRef]
81. Herzele S, van Herwijnen HW, Edler M, Gindl-Altmutter W, Konnerth J. Cell-layer dependent adhesion differences in wood bonds. Compos. Part A: Appl. Sci. Manuf.. 2018;114:21–9. doi:10.1016/j.compositesa.2018.07.037. [Google Scholar] [CrossRef]
82. Zou T, Sipponen MH, Henn A, Österberg M. Solvent-resistant lignin-epoxy hybrid nanoparticles for covalent surface modification and high-strength particulate adhesives. ACS Nano. 2021;15(3):4811–23. doi:10.1021/acsnano.0c09500 [Google Scholar] [PubMed] [CrossRef]
83. Natarelli CVL, Lemos ACC, de Assis MR, Tonoli GHD, Trugilho PF, Marconcin JM, et al. Sulfonated Kraft lignin addition in urea-formaldehyde resin: thermokinetic analysis. J Therm Anal Calorim. 2019;137:1537–47. doi:10.1007/s10973-019-08075-1. [Google Scholar] [CrossRef]
84. Vitrone F, Ramos D, Ferrando F, Salvadó J. Binderless fiberboards for sustainable construction. Materials, production methods and applications. J Build Eng. 2021;44:102625. doi:10.1016/j.jobe.2021.102625. [Google Scholar] [CrossRef]
85. Bi X, Huang R. Preparation, morphology, FTIR and performance properties of foaming particleboard. J Wood Sci. 2021;67(1):1–12. [Google Scholar]
86. de Oliveira MRR, Brito FMS, Villela LS, Mendes LM, Júnior JBG. Physical-mechanical properties of panels produced with corn cob particles and different types and contents of adhesives. Res, Soc Dev. 2021;10(11):e541101119828-e541101119828. [Google Scholar]
87. Oropeza D, Hart AJ. Reactive binder jet additive manufacturing for microstructural control and dimensional stability of ceramic materials. Addit Manuf. 2021;48:102448. [Google Scholar]
88. Zhao S, Pang H, Li Z, Wang Z, Kang H, Zhang W, et al. Polyurethane as high-functionality crosslinker for constructing thermally driven dual-crosslinking plant protein adhesion system with integrated strength and ductility. Chem Eng J. 2021;422:130152. doi:10.1016/j.cej.2021.130152. [Google Scholar] [CrossRef]
89. Nazarinezhad Giashi A, Gereke T, Mbarek T, Cherif C. Novel dynamic test methods for paperboard composite structures. Exp Tech. 2021;46:849–60. doi:10.1007/s40799-021-00496-8. [Google Scholar]
90. Dislaire C, Seantier B, Muzy M, Grohens Y. Mechanical and hygroscopic properties of molded pulp products using different wood-based cellulose fibers. Polymers. 2021;13(19):3225. doi:10.3390/polym13193225 [Google Scholar] [PubMed] [CrossRef]
91. Asfarizal S, Anwar K, Gunawarman. S. Characteristics of particleboard made from trees pine bark (Jungh. Et De Vr.) and oil palm empty fruit bunches. Int J Sci Technol Res. 2020;9(9):320–7. [Google Scholar]
92. Yemele MCN, Cloutier A, Diouf PN, Koubaa A, Blanchet P, Stefanovi T. Physical and mechanical properties of particleboard made from extracted black spruce and trembling aspen bark. For Prod J. 2008;58(10):38–46. [Google Scholar]
93. de Campos CI, Ferreira BS, Barbosa JC, Morales EAM, Christoforo AL, Rocco Lahr FA. Particleboard manufactured with additions of eucalyptus bark in different percentages in the internal layer. Adv Mater Res. 2014;1025:3–6. [Google Scholar]
94. Ma Y, Yang B, Hu S, Shan H, Geng P, Li Y, et al. Combined strengthening mechanism of solid-state bonding and mechanical interlocking in friction self-piercing riveted AA7075-T6 aluminum alloy joints. J Mater Sci Technol. 2022;105:109–21. doi:10.1016/j.jmst.2021.07.026. [Google Scholar] [CrossRef]
95. Nie MH, Zhang S, Wang ZY, Zhang HF, Zhang CH, Chen HT. Development of a novel method for measuring the interfacial bonding strength of laser cladding coatings. Opt Laser Technol. 2022;148:107699. doi:10.1016/j.optlastec.2021.107699. [Google Scholar] [CrossRef]
96. Padhan M, Marathe U, Bijwe J. Exceptional performance of bi-directionally reinforced composite of PEEK manufactured by commingling technique using poly (p-Phenylene-Benzobisoxazole)(PBO) fibers. Compos Sci Technol. 2022;218:109125. doi:10.1016/j.compscitech.2021.109125. [Google Scholar] [CrossRef]
97. He Y, Zhu X, Chen W, Lu C, Li Y, Xu H, et al. An ultra-high bond strength of the Cf/C composite-TC4 alloy joint brazed using pure Ni and revealing synergetic action of multiple stress-relief mechanisms. Mater Lett. 2022;308:131245. doi:10.1016/j.matlet.2021.131245. [Google Scholar] [CrossRef]
98. Chen X, Li J, Pizzi A, Fredon E, Gerardin C, Zhou X, etal. Tannin-furanic foams modified by soybean protein isolate (SPI) and industrial lignin substituting formaldehyde addition. Ind Crops Prod. 2021;168:113607. doi:10.1016/j.indcrop.2021.113607. [Google Scholar] [CrossRef]
99. Tudor EM, Kristak L, Barbu MC, Gergeľ T, Němec M, Kain G, et al. Acoustic properties of Larch bark panels. Forests. 2021;12(7):887. doi:10.3390/f12070887. [Google Scholar] [CrossRef]
100. Masche M, Puig-Arnavat M, Jensen PA, Holm JK, Clausen S, Ahrenfeldt J, et al. Influence of wood pellets properties on their grinding performance. Biomass Convers Biorefin. 2023;13(4):2985–3000. doi:10.1007/s13399-021-01559-x. [Google Scholar] [CrossRef]
101. de Carvalho DM, Lahtinen MH, Bhattarai M, Lawoko M, Mikkonen KS. Active role of lignin in anchoring wood-based stabilizers to the emulsion interface. Green Chem. 2021;23(22):9084–98. doi:10.1039/D1GC02891J. [Google Scholar] [CrossRef]
102. Fang C, Gong J, Jia M, Nie Z, Li B, Mohammed A, et al. DEM simulation of the shear behaviour of breakable granular materials with various angularities. Adv Powder Technol. 2021;32(11):4058–69. doi:10.1016/j.apt.2021.09.009. [Google Scholar] [CrossRef]
103. Wascher R, Avramidis G, Viöl W. Plywood made from plasma-treated veneers: investigation of performance differences between plasma-pretreated and untreated Beech veneers at comparable melamine resin load. Forests. 2021;12(10):1423. doi:10.3390/f12101423. [Google Scholar] [CrossRef]
104. Zuber SH, Hashikin NAA, Yusof MFM, Aziz MZA, Hashim R. Influence of different percentages of binders on the physico-mechanical properties of Rhizophora spp. particleboard as natural-based tissue-equivalent phantom for radiation dosimetry applications. Polymers. 2021;13(11):1868. doi:10.3390/polym13111868 [Google Scholar] [PubMed] [CrossRef]
105. Faria DL, Eugênio TMC, Lopes DE, Protásio TDP, Mendes LM, Guimarães Junior JB. Particleboards produced with different proportions of Hevea brasiliensis: residual wood valorization in higher value-added products. Ciência e Agrotecnologia. 2021;45. [Google Scholar]
106. Wang J, Minami E, Asmadi M, Kawamoto H. Effect of delignification on thermal degradation reactivities of hemicellulose and cellulose in wood cell walls. J Wood Sci. 2021;67(1):1–11. [Google Scholar]
107. Plotnikov N, Plotnikova G, Vaynshtok N. Possibilities of using hydrolytic lignin in the production of wood-splicing materials. In: XXII International Scientific Conference Energy Management of Municipal Facilities and Sustainable Energy Technologies (EMMFT-2020Voronezh, Russia; 2021; EDP Sciences. vol. 244, 04006. doi:10.1051/e3sconf/202124404006. [Google Scholar]
108. Cencin A, Zanetti M, Urso T, Crivellaro A. Effects of an innovative densification process on mechanical and physical properties of beech and Norway spruce veneers. J Wood Sci. 2021;67(1):1–14. [Google Scholar]
109. Ai X, Feng S, Shui T, Kakkar H, Xu CC. Effects of alcell lignin methylolation and lignin adding stage on lignin-based phenolic adhesives. Mol. 2021;26(22):6762. doi:10.3390/molecules26226762 [Google Scholar] [PubMed] [CrossRef]
110. Musah M, Wang X, Dickinson Y, Ross RJ, Rudnicki M, Xie X. Durability of the adhesive bond in cross-laminated northern hardwoods and softwoods. Constr Build Mater. 2021;307:124267. doi:10.1016/j.conbuildmat.2021.124267. [Google Scholar] [CrossRef]
Cite This Article
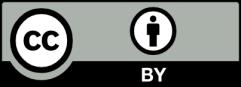
This work is licensed under a Creative Commons Attribution 4.0 International License , which permits unrestricted use, distribution, and reproduction in any medium, provided the original work is properly cited.