Open Access
ARTICLE
A Comprehensive Analysis of the Thermo-Chemical Properties of Sudanese Biomass for Sustainable Applications
1 Institute of Analytical Sciences and Physical-Chemistry for the Environment and Materials-Xylomat, University of Pau and the Adour Region, E2S UPPA, CNRS, IPREM-UMR 5254, Mont de Marsan, 40004, France
2 Institute of Engineering Research and Materials Technology (IERMT), National Center for Research (NCR), Ministry of Higher Education and Scientific Research, Khartoum, 11111, Sudan
3 Faculty of Industries Engineering and Technology, University of Gezira, Gezira State, 21111, Sudan
* Corresponding Author: Bertrand Charrier. Email:
(This article belongs to the Special Issue: Renewable Material from Agricultural Waste and By-Product and Its Applications)
Journal of Renewable Materials 2024, 12(4), 721-736. https://doi.org/10.32604/jrm.2024.031050
Received 11 May 2023; Accepted 11 July 2023; Issue published 12 June 2024
Abstract
The chemical composition and thermal properties of natural fibers are the most critical variables that determine the overall properties of the fibers and influence their processing and use in different sustainable applications, such as their conversion into bioenergy and biocomposites. Their thermal and mechanical properties can be estimated by evaluating the content of cellulose, lignin, and other extractives in the fibers. In this research work, the chemical composition and thermal properties of three fibers, namely bagasse, kenaf bast fibers, and cotton stalks, were evaluated to assess their potential utilization in producing biocomposites and bioenergy materials. The chemical composition analysis followed the Technical Association of the Pulp and Paper Industry Standards (TAPPI) methods. The total phenol content was quantified using the Folin-Ciocalteu method, while Fourier Transform Infrared Spectroscopy (FTIR) was employed to assess the light absorption by the bonds. To evaluate thermal stability and higher heating values, Thermogravimetric Analysis (TGA), Differential Scanning Calorimetry (DSC), and bomb calorimetry were performed. The chemical analysis revealed that bagasse contained 50.6% cellulose and 21.6% lignin, kenaf bast fibers had 58.5% cellulose and 10% lignin, and cotton stalks exhibited 40.3% cellulose and 21.3% lignin. The FTIR curves demonstrated a notable similarity among the fibers. The TGA analysis showed degradation temperatures of 321°C for bagasse, 354°C for kenaf bast fibers, and 289°C for cotton stalks. The DSC analysis revealed glass transition temperatures of 81°C for bagasse, 66.3°C for cotton stalks, and 64.5°C for kenaf bast fibers. The higher heating values were measured as 17.3, 16.6 and 17.1 MJ/kg for bagasse, kenaf bast fibers, and cotton stalks, respectively. The three fibers have a high potential for biocomposites and bioenergy material manufacturing.Keywords
Intensive use of biomass wastes is being promoted due to increasing awareness of environmental protection [1,2]. Renewable sources are essential in the energy sector’s pursuit of decarbonization [3]. This requires a significant reduction in the greenhouse gas emissions that result from the burning of fossil fuels [3–5]. Biomass residues, which include agricultural by-products such as crop residues, straws, husks, and stalks, this resource can be utilized effectively as a sustainable and renewable source [6–8]. Lignocellulosic biomass is made up of three main components: cellulose, hemicellulose, and lignin [3,9]. The precise percentages of these compounds vary based on the specific type and origin of the biomass. According to Mustafa et al. [9], lignocellulosic biomass is made up of approximately 30%–60% cellulose, 14%–40% hemicellulose, and 7%–25% lignin. The plant cell wall is composed of cellulose which is densely packed with hemicellulose and lignin [10]. Lignin is a binding material that holds the cellulose and hemicellulose together in plant cell walls, providing structural support and rigidity. Lignin is an intricate and highly complex aromatic polymer that consists of phenylpropane units that are interconnected by an array of diverse chemical bonds. The depolymerization of lignin can produce different valuable aromatic chemicals, such as vanillin, syringol, and guaiacol, among others [11].
Sugarcane bagasse is a waste product that is generated in significant quantities by the sugar industry. The disposal of bagasse without treatment can cause environmental pollution. Despite this, sugarcane bagasse is primarily used as fuel to power sugar mills, with limited utilization [12]. Kenaf fiber is an exceptional natural fiber that offers a wide range of advantages and is highly recommended for use as reinforcement in composite materials, particularly in polymer composites. Kenaf is a plant that grows rapidly, yields significantly, and exhibits strong stress resistance. Its stem has been grown traditionally as an excellent source of soft fiber [13]. In Sudan, kenaf has been grown in high Savanna areas with heavy rains, such as the Abu-Namaa area and Gezira state Central part of Sudan. Cotton cultivation in Sudan dates back to the 19th century, specifically when it was first introduced and grown in Eastern Sudan’s Tokar area. Cotton stalks are a significant source of biomass. After the cotton is harvested, the remaining stalks and other plant material can be used as feedstock for various processes. Essential quantities of cotton stalks, and bagasse, are burned annually in developing countries because of the lack of suitable and available processing facilities [14].
The widespread use of these fibers is significantly hindered by several constraints, such as the little consistency in the quality of fibers, their thermal instability, their high moisture absorption, and their limited impact strength when used in composites. Fibers are primarily used as an energy source in rural areas. They also provide fuel for small and medium-scale urban and rural industries, predominantly in economically limited regions. To meet the growing energy requirements, it is essential to prioritize efficient production and utilization of biomass. Thermal degradation is highly likely to occur during processing into composite and conversion into energy forms. Understanding the thermal decomposition process of natural fibers is crucial for predicting the behavior of these fibers during composite processing and estimating the resulting composite properties. It will also help to design a better system for their conversion into electricity and different forms of energy. The research on utilizing lignocellulosic material for bioenergy production is expanding at an unprecedented pace, driven by the urgent need to address the depleting reserves of fossil fuels and the catastrophic environmental impact of their extraction [15–17]. It is crucial to understand the individual behaviors of the primary components of plants, namely cellulose, lignin, and hemicelluloses, and as such, most research focuses on precisely that [18,19].
The primary objective of the study was to conduct a comprehensive analysis of the chemical and thermal properties of bagasse, cotton stalks, and kenaf bast fibers, with a focus on their potential applications in sustainable contexts. The chemical analysis involved various essential properties such as moisture content, ash content, solubility in water, extraction with NaOH and organic solvent, total phenols, cellulose, and lignin. Furthermore, Fourier transforms infrared spectroscopy was used to gain insights into the types of chemical bonds in the fibers. The thermal behavior and thermal stability of the fibers were investigated through thermogravimetric analysis and differential scanning calorimetry, while their high heating values were measured using bomb calorimetry. These characterizations provide valuable insights into the potential sustainable applications of the studied fibers.
Three fibers were used in this study: Sugar cane bagasse (Saccharum officinarum), which was provided by the Al-Gunied sugar factory in Gezira state central part of Sudan. Kenaf bast fibers (Hibiscus cannabinus L.) were grown in the demonstration farm of the University of Khartoum, Shambbat, Khartoum-North, Sudan. The Cotton stalks (Gossypium herbaceumL.) were collected from the Gezira project, Gezira State, Sudan.
Bagasse was used without any further processing. Kenaf bast fibers were extracted from Kenaf stalks using water retting process. The cotton stalks and Kenaf fibers were crushed in a laboratory mill to a smaller size range between 2–5 mm. The studied fibers were stabilized in a climatic chamber with a controlled atmosphere (RH = 64% ± 2%) and temperature (T = 20°C ± 2°C).
2.2.1 Chemical Characterization
Representative samples of each of the three fibers (One kilogram of chips) were milled in a laboratory mill (Retsch SK 100). The obtained powder was further fractionated using sieves. The chemical analysis was carried out on the portion retained on a 60-mesh sieve according to the Technical Association of the Pulp and Paper Industry standard (TAPPI 11M-59). The air-dried powder was stored in a plastic jar overnight to homogenize moisture content. The Chemical analysis of raw materials was carried out using the Technical Association of Pulp and Paper Industry (TAPPI) Standard methods, as shown in Table 1.
Ash content was determined by placing 2 g of each sample in porcelain crucibles and heated in an oven at 575°C for 3 h. The ash percentage was then calculated using Eq. (1).
Ash content (%)=weight of ashoven dry weight×100 (1)
The organic matter content and organic carbon content were calculated and given by Eqs. (2) and (3), respectively [20].
OM (%)=100−Ash (2)
OC (%)=0.48×OM (3)
Cellulose content was determined using a mixture of ethanol and nitric acid in a 4:1 ratio. A total of 2 g of each sample was placed in a conical flask, and 25 ml of the ethanol-nitric acid mixture was added. The flask was then placed in a water bath and heated for 15 min. This process was repeated four times, with an additional 15 ml of the mixture added each time. After the sequential extraction, the mixture was filtered, and the residue was placed in an oven for 24 h. The percentage of cellulose was calculated by using Eq. (4):
Cellulose (%)=weight of precipitateoven dry weight×100 (4)
Lignin content in the biomass samples was determined using sulfuric acid with a concentration of 72%. Initially, 5 g of the sample was weighed and placed in a Soxhlet extractor. To this, 15 ml of sulfuric acid was added to a beaker, and then placed in a freezer for 2 h. During this time, the mixture was periodically mixed every 15 min. Subsequently, the mixture was transferred to a conical flask, and 575 ml of distilled water was added. The flask was then heated for 4 h. After heating, the mixture was filtered, and the residue was transferred to an oven. The percentage of lignin was calculated by using Eq. (5):
Lignin (%)=weight of precipitateoven dry weight×100 (5)
The Folin-Ciocalteu method was used to determine the total phenol content, as described previously in the literature [21,22].
The total phenol content was calculated using Eq. (6):
Total Phenols (%)=C × D × V1000 × Mdried×100 (6)
where:
C is the total phenol concentration (ppm)
D is the degree of dilution (10)
V is the volume of starting solution (30 ml)
Mdried is the mass of dry powder.
All the characterizations were carried out in triplicate. The results were expressed as means ± SD.
2.2.2 Fourier Transform Infrared Spectroscopy Analysis (FTIR)
FTIR spectroscopy was used to analyze bagasse, kenaf bast fibers, and cotton stalks. The samples were dried for 24 h at 105°C, and approximately 5 mg of the sample was inserted into the device. The analyses were performed using 64 scans, with a resolution of 4 cm−1 and in the range from 4000 to 600 cm−1.
2.2.3 Thermogravimetric Analysis (TGA)
The thermal degradation was carried out through a thermogravimetric instrument, specifically the TGA Q50 Instrument. For this, around 10 mg of the samples were weighed and placed in a small pan inside the device. The temperature program used a heating rate of 10°C/min, starting from 30°C and going up to 600°C. The measurement was performed under air, using a flux of 60 ml/min. To ensure precision and reproducibility, the experiments were conducted thrice.
2.2.4 Differential Scanning Calorimetry (DSC) Analysis
Measurements were conducted on a DSC (TA Instruments, Q20) equipped with a rapid cooling system. The samples of bagasse, cotton stalks, and kenaf bast fibers were weighed (~5 mg) in standard aluminum pans, and data acquisitions were carried out using the Universal Analysis 2000 program (TA Instruments). The analyses were conducted following a method described by Frances et al. [23], with modification of the temperature range (−50 to 250)°C. All experiments were repeated three times.
2.2.5 Higher Heating Value (HHV)
The higher heating value of bagasse, kenaf bast fibers, and cotton stalk was accurately determined using a bomb calorimeter. ~1 g for each type of fiber was placed on the bomb for this test. Benzoic acid was used to calibrate the device [24]. The experiments were conducted three times, and the results are presented as means ± standard deviation (SD).
The cellulose contents of bagasse, kenaf bast fibers, and cotton stalk are shown in Fig. 1. Among the three fibers studied, the highest % of Cellulose was achieved by the kenaf bast fibers (58.5%), which is similar to the value reported by Hamidon et al. [25]. The bagasse reported a value of (50.6%), which was higher than the value reported by Kanwal et al. [26] (36.9%). The mean amount of cellulose in the cotton stalks (40.3%) was in line with the values in previous studies [27,28]. The differences in these values may be due to various factors such as climatic conditions, soil composition, plant variety, and age [6]. The cellulose, hemicellulose, and lignin contents strongly influence the natural fibers’ mechanical, physical, and thermal properties. Cellulose is the main structural component that contributes to the strength and stability of the plant cell walls and fibers. The high amount of cellulose content in the fibers indicates advanced mechanical properties. Additionally, understanding the impact of cellulose content on the thermal stability of fibers contributes to developing materials with enhanced heat resistance and expands the potential applications in various industries. It has been observed that the amount of cellulose is relatively high in the three fibers, which is suitable for their use in bioenergy and biocomposites as cellulose thermally degrades at about 300°C.
Figure 1: Cellulose and lignin contents of the bagasse, kenaf bast fibers, and cotton stalks
The lignin content of bagasse, kenaf bast fibers, and cotton stalks is presented in Fig. 1, and it was found to be 21.6%, 10%, and 21.3%, respectively. Bagasse had the highest amount of lignin, followed by cotton stalks, while the kenaf bast fibers had the lowest percentage. The measured value of lignin content in bagasse was consistent with the findings of the previous work [29,30]. The value of kenaf bast fibers was the same as that found in the previous study [31]. The lignin content of cotton stalks was lower than that found in the literature [32] and equal to the value reported in the previous study [33].
The results of the total phenol content of bagasse, kenaf bast fibers, and cotton stalks revealed that the fibers with the highest phenols content were the cotton stalks with a value of 6%, followed by bagasse with a value of 1.7%, and kenaf bast fibers with a value of 1.3%. The high amount of phenols in the cotton stalks could be used in various fields and applications. Phenolic compounds have potential applications in producing high-value products such as bio-based tannins adhesives, other chemicals, and pharmaceutical products. The presence of the phenolic compound within these fibers is crucial to defend the biocomposite materials effectively against fungi [34]. Phenolic compounds possess antimicrobial and antifungal properties, making them natural defense mechanisms against biological degradation. This protective role of phenolic compounds is crucial in applications where biocomposite materials are exposed to high humidity, moisture, or outdoor environments, as these conditions are conducive to fungal growth. Furthermore, their presence could also enhance the final adhesive-fibers network if these fibers were targeted for producing biocomposites based on natural matrices such as tannins in future work.
The equilibrium moisture content at 65% relative humidity and 20°C obtained for the bagasse, kenaf bast fibers, and cotton stalks are shown in Table 2. The results revealed 7.8%, 8.5%, and 8.4% for bagasse, kenaf bast fibers, and cotton stalks. The moisture content depends on the atmospheric conditions, type of fiber, age of the plant, soil condition in which the plant was grown, and the method and duration of preservation. These results were lower than previous observations by Spinacé et al. [35], who noticed that the percentage of moisture content of the fibers under normal atmospheric conditions was between 9.1% to 12.1%. It is worth noting that the three fibers understudy were found to be more dried than solid wood particles stored under the same moisture conditions (MC around 11%). This could be due to the dry weather conditions in Sudan during the collection of the fibers, where the temperature was above 40°C. The high moisture content in the fibers is not desirable for many applications, including biocomposites and for producing bioenergy. It would require the addition of water repellent, which may not always be efficient and require advanced technology to reduce its adverse effects [36].
The results of the ash content of bagasse, kenaf bast fibers, and cotton stalks are shown in Table 2. The ash percentage was 8%, 2.5%, and 5.2%, respectively. The bagasse showed the highest value of ash content compared to kenaf bast fibers and cotton stalks and was higher than the value reported in the literature [37]. The ash content of kenaf bast fibers was approximately in line with the value observed by Hamidon et al. [25], which was (2–5)%. The cotton stalks exhibited lower ash content than the previous study [28]. These differences can be attributed to the difference in chemical composition and the nature of the soil in which plants were grown [38,39]. High ash content may affect the mechanical properties of the biocomposites and may add difficulties to their transformation. However, for the production of bioenergy, high heat output and low ash content are recommended [40].
The soluble extractives of the cold and hot water of bagasse, kenaf bast fibers, and cotton stalks are shown in Table 3. The kenaf bast fibers present the lowest % of the extractives compared to bagasse and cotton stalks, while cotton stalks showed the highest extractives % in cold and hot water.
The percentages of the extractive content obtained with 1% sodium hydroxide for bagasse, kenaf bast fibers, and cotton stalks are shown in Table 3. The highest rate was obtained by bagasse (43%), followed by cotton stalks 31.2% and then kenaf bast fibers 16.7%. These values were approximately equal to values reported for non-wood and annual plants [39]. It is worth noting that the bagasse exhibited a high percentage of these extractives due to some sugars on the surface of the fibers.
The ethanol-soluble extractives for the fibers were 9.9%, 10.1%, and 9.5% of bagasse, kenaf bast fibers, and cotton stalks, respectively (Table 3). The value of bagasse was lower than the value reported in previous work [26]. The kenaf bast fibers and Cotton stalks showed higher values than the ones reported by Saba et al. [41] and Zhou et al. [42], respectively.
It was crucial to know the percentages of extractives in the three fibers as they significantly inhibit the reaction between the fibers and the resins used in composite manufacturing. Additionally, the presence of OH groups on the surface of the fibers can hinder water uptake by the resulting panels. Therefore, removing the extractives improved the mechanical and thermal stability of the composites.
3.2 Fourier Transform Infrared Spectroscopy (FTIR) Analysis
The FTIR analysis of the bagasse, kenaf bast fibers, and cotton stalks are shown in Fig. 2. The obtained result for bagasse reveals a pronounced absorbance at 3338 cm−1, signifying the substantial presence of O–H groups in the lignocellulosic structure of bagasse fibers. The absorptions related to groups O–H and C–H stretches are apparent, corresponding to the cellulose and hemicellulose structures and the aromatic and aliphatic chains in the lignin [43]. However, the band at 2891 cm−1 indicates the presence of a C–H group, at 1629 cm−1 of absorbed O–H or carbonyl bands, while the peak at 1423 cm−1 indicates the presence of a −CH2 group, at 1319 cm−1 is corresponding to the bending C–H. The analysis further reveals significant absorptions associated with various groups, including the C–O bond observed at 1030 cm−1, C=O at 1603 cm−1, C=C at 1423 cm−1, and 897 cm−1, indicating the presence of β-glycosidic bonds.
Figure 2: FTIR spectra of bagasse, kenaf bast fibers, and cotton stalk
The FTIR curve of the kenaf bast fibers shows that the band at 3334 cm−1 represents the O–H stretching vibration and hydrogen bond of hydroxyl groups. This is approximately in line with what was achieved in the previous work [44]. The 2916 cm−1 band signifies the C–H stretching vibration of the methyl and methylene groups present in cellulose and hemicelluloses [45]. The band at 1728 cm−1 is attributed to the carbonyl C=O stretching frequency for aldehydes groups in lignin [44,46]. The band observed at 1619 cm−1 is attributed to the C=C stretching of the aromatic ring in lignin. This finding closely aligns with the results reported by Rozyanty et al. [44]. The absorption band appeared at 1423 and 1318 cm−1, corresponding to the C–H bending and C–O stretching frequencies of hemicelluloses [44]. The band at 1237 cm−1 is attributed to the C–O and C=O stretching vibration of the acetyl group in hemicelluloses and lignin [47]. The band at 1155 cm−1 is due to C–O–C asymmetrical stretching in cellulose and hemicelluloses [47,48]. The strong band at 1024 cm−1 is attributed to the C–O and C–C stretching frequencies of xylans. The band is also assigned to the C–O stretching, originating from the C–O–CH3 groups, confirming lignin’s presence [44]. The band at 896 cm−1 is attributed to β-Glycosidic linkage in cellulose [46]. The band at 668 cm−1 is attributed to C–OH out-of-plane bending in cellulose [47].
The FTIR analysis of the cotton stalks showed the following results: The band observed at 3757 cm−1 is likely associated with isolated hydroxyl groups [49]. Isolated hydroxyl groups represent hydroxyl (OH) functional groups that do not bond hydrogen with adjacent molecules or functional groups [50]. The band at 3336 cm−1 is attributed to the hydrogen-bonded O–H stretching vibration [51]. The band at 2920 cm−1 indicates the presence of a C–H group. The band at 1745 cm−1 is attributed to the carbonyl C=O stretching frequency for aldehydes groups in lignin. The bands in the range of ~1607 cm−1 are linked to lignin and C = C of aromatic compounds [28]. The absorption band at 1424 cm−1 is attributed to the C–H bending and C–O stretching frequencies of hemicelluloses. The band at 1234 cm−1 is attributed to the C–O and C=O stretching vibration in hemicelluloses and lignin [52]. The band at 1151 cm−1 is ascribed to the C–O–C asymmetrical stretching in cellulose structure [53]. The band at ~1031 cm−1 shows the presence of C = O and C–C at 599 cm−1, which are attributed to cellulose [54].
The curves of bagasse, kenaf bast fibers, and cotton stalks showed some similarities and congruence between them; for example, the absorption that happened by the O–H groups presented approximately equal values in the amount of absorption, and some differences observed, as occurred in some groups such as the C–O, which was very strong for kenaf bast fibers compared to bagasse and cotton stalks. These differences are due to the chemical structure of the fibers [55].
3.3 Thermogravimetric Analysis (TGA)
The thermogravimetric analysis curves for bagasse, kenaf bast fibers, and cotton stalks exhibited a similar pattern of mass loss concerning temperature. In thermogravimetric Analysis (TGA), two critical curves are typically considered: the thermogravimetry (TG) curve and the derivative thermogravimetry (DTG) curve. The TG curve shows a sample’s mass change when subjected to controlled heating or cooling. The DTG curve, on the other hand, is derived from the TG curve. It represents the rate of change of mass concerning temperature.
The TG and DTG curves analysis revealed that kenaf bast fibers exhibited higher thermal stability than bagasse and cotton stalks. Furthermore, bagasse displayed more excellent thermal stability than cotton stalks, as depicted in Figs. 3 and 4. Based on the TG and DTG curves, it was observed that the temperature range between 30°C and 100°C was associated with removing water from the fibers. No significant mass loss was observed between 100°C and 200°C, indicating that the fibers were thermally stable in this temperature range [38,56]. The weight loss observed for each fiber at 200°C was approximately 7.7% for bagasse, 6.3% for kenaf bast fibers, and 10% for cotton stalks. These values indicate the extent of mass reduction experienced by the fibers when subjected to a temperature of 200°C, suggesting the release of volatile components in the samples. During the temperature range of 200°C to 400°C, the decomposition of the bio-macromolecule chains was observed. Specifically, the degradation of hemicelluloses occurred within the temperature range of 250°C to 315°C, while the degradation of cellulose took place between 315°C and 370°C [57]. Lignin degradation was observed to occur within the temperature range of 280°C to 500°C. This temperature range indicates the thermal breakdown of lignin, a complex and heterogeneous polymer found in plant cell walls. During pyrolysis, lignin breaks down and produces a range of volatile compounds, along with the formation of char residue [58]. In this study, the degradation temperatures for bagasse, kenaf bast fibers, and cotton stalks were approximately 321.5°C, 354°C, and 289.5°C, respectively. These temperatures represent the points at which the fibers undergo significant thermal decomposition and weight loss. By identifying these degradation temperatures, insights into the thermal stability and behavior of the fibers emerge, which are essential considerations for various applications such as biomass utilization and energy production. The thermal degradation of fibers is affected by several factors, such as their chemical composition, crystallinity, and moisture content. Cellulose exhibits remarkable thermal stability as the primary component of natural fibers. The physical properties of natural fibers are largely conditioned by cellulose, which is the major constituent. Furthermore, cellulose plays a significant role in the thermal degradation of these fibers. Fibers with higher cellulose content, such as kenaf bast fibers, tend to show higher degradation temperatures than fibers with lower cellulose content. This is attributed to cellulose’s inherent heat resistance and structural integrity [59]. Indeed, the thermal degradation behavior of fibers can be influenced by factors beyond cellulose content, lignin, and hemicellulose content. As a result, fibers with a higher cellulose content are more resistant to thermal decomposition and can withstand higher temperatures before undergoing significant degradation. This characteristic makes cellulose-rich fibers desirable for various applications that involve exposure to elevated temperatures, such as thermal insulation, fire-resistant materials, and biocomposites. Lignin is a complex polymer known to have higher thermal stability than cellulose. Therefore, fibers with a higher lignin content are generally more resistant to thermal degradation. On the other hand, hemicellulose, a branched polysaccharide, exhibits lower thermal stability than cellulose and lignin. In the temperature range of 400°C to 600°C, the thermal degradation of lignin and other organic components took place. During this phase, the remaining organic matter undergoes decomposition, forming residues with high molecular weight [38]. This thermal degradation process involves several key events, including the carbonization of degraded compounds derived from the three biomacromolecules (cellulose, hemicellulose, and lignin) and the condensation of aromatic rings in the lignin structure. These reactions form charred residues and transform organic compounds into more stable carbonaceous structures. The presence of aromatic rings in lignin promotes condensation reactions, leading to the formation of carbon-rich structures. These thermal events occurring in the temperature range of 400°C to 600°C are crucial for understanding the behavior of biomass materials during high-temperature processes such as pyrolysis and carbonization [57].
Figure 3: TG curves of the bagasse, kenaf bast fibers, and cotton stalks
Figure 4: DTG curves of the bagasse, kenaf bast fibers, and cotton stalks
3.4 Differential Scanning Calorimetry (DSC) Analysis
The DSC analysis of the three fibers is illustrated in Fig. 5. The curves show the glass transition ( Tg ) of the studied fibers, which is an endothermic event, and it represents the softening point of the material, as mentioned by Singh et al. [60]. It is an important parameter influencing the material’s mechanical and thermal properties. The variation in Tg among the different materials may be attributed to differences in their chemical composition, molecular structure, and thermal behavior. Understanding the Tg can provide valuable insights into the behavior and performance of these materials in different applications. The glass transition temperature ( Tg ) was 81°C for bagasse, 66.3°C for cotton stalks, and 64.5°C for kenaf bast fibers. The Tg value of polymeric materials increases with both the molecular weight and the difficulty of molecular rotations [61].
Figure 5: DSC curves for the bagasse, kenaf bast fibers, and cotton stalks
3.5 Higher Heating Value (HHV)
The Bomb calorimetric analysis of bagasse, kenaf bast fibers, and cotton stalks showed that the bagasse fibers had the highest heating value compared to the kenaf bast fibers and cotton stalks, as shown in Fig. 6. Bagasse fibers reported a value of 17.36 MJ/kg, the recorded value was lower than what was mentioned in the literature [62]. The value obtained for kenaf bast fibers was 16.61 MJ/kg, which was approximately equal to the value observed by Yub Harun et al. [63]. The cotton stalks showed a value of 17.08 MJ/kg, slightly lower than the bagasse value. This value was lower than the previous study [64]. These differences can be attributed to the difference in the moisture content of the fibers. The presence of moisture in biomass leads to the evaporation of water during combustion, which absorbs heat and reduces the overall heating value of the biomass. The single most crucial factor that defines the energy potential of any fuel is its calorific value. It is crucial to assess the higher heating value (HHV) of biomass before and after its conversion through techniques such as pyrolysis, gasification, or combustion. This assessment is essential as it indicates the potential of biomass as a reliable and efficient source of energy [65].
Figure 6: High heating values of bagasse, kenaf bast fibers, and cotton stalks
This experimental study of the chemical characterization and thermal behavior of the bagasse, kenaf bast fibers, and cotton stalk has led to determining these fibers’ main properties and behavior to produce biocomposites and bioenergy. The values obtained by the chemical Analysis for the bagasse, kenaf bast fibers, and cotton stalks were comparable to those reported in the literature. The moisture content of bagasse, kenaf bast fibers, and cotton was determined to be 7.8%, 8.5%, and 8.4%, respectively. The ash content of the fibers was found to be 8% for bagasse, 2.5% for kenaf bast fibers, and 5.2% for cotton stalks. In terms of extractive content using 1% sodium hydroxide, bagasse exhibited the highest percentage at 43%, followed by cotton stalks at 31.2% and kenaf bast fibers at 16.7%. The ethanol-soluble extractives for the fibers were measured as 9.9% for bagasse, 10.1% for kenaf bast fibers, and 9.5% for cotton stalks. Cellulose content varied among the fibers, with kenaf bast fibers exhibiting the highest percentage (58.5%), followed by bagasse (50.6%) and cotton stalks (40.3%). Lignin content was highest in bagasse (21.6%), followed by cotton stalks (21.3%), while kenaf bast fibers had the lowest percentage (10%). The abundance of lignin presents potential opportunities for lignin-derived products. Analysis of phenol content revealed that cotton stalks had the highest amount (6%), followed by bagasse (1.7%) and kenaf bast fibers (1.3%). Fourier transforms infrared spectroscopy (FTIR) results aligned with previous studies. The thermogravimetric Analysis demonstrated the fibers’ stability below 200°C, with degradation occurring between 200°C and 400°C. Kenaf bast fibers exhibited excellent stability in this temperature range due to their higher cellulose content. The degradation temperatures were determined as 321°C for bagasse, 354°C for kenaf bast fibers, and 289°C for cotton stalks. These findings have significant implications for the processing of biocomposite materials and understanding the thermal behavior and stability of these fibers in bioenergy production. Differential scanning calorimetry (DSC) analysis revealed the glass transition temperatures, representing the temperature at which the material transitions from a rigid, glassy state to a more flexible, rubbery state. The glass transition temperature ( Tg ) for fibers was measured as 81°C for bagasse, 66.3°C for cotton stalks, and 64.5°C for kenaf bast fibers. Furthermore, the higher heating values were determined as 17.36 MJ/kg for bagasse, 16.61 MJ/kg for kenaf bast fibers, and 17.08 MJ/kg for cotton stalks, aligning with previous studies. These results provide valuable insights into the potential sustainable applications of these fibers, enhancing our understanding of their properties and performance.
Acknowledgement: The authors want to acknowledge the Tenure Track Position “Bois: Biobased materials” part of E2S UPPA supported by the “Investissements d’Avenir” French Program managed by ANR (ANR-16-IDEX-0002).
Funding Statement: This research study has been jointly funded by the Ministry of Higher Education and Scientific Research, Sudan, and the Ministry for Europe and Foreign Affairs, France.
Author Contributions: The authors confirm their contribution to the paper as follows: Dr. Wadah Mohammed, wrote the original draft, responsible for the analysis and experiments, writing, and revising. Professor Zeinab Osman, co-author and supervisor of the project, and responsible for the chemical analysis, writing, and revising. Professor Salah Elarabi, co-supervisor, provision of some materials revising and editing. Professor Bertrand Charrier acted as scientific director and helped with writing and revising.
Availability of Data and Materials: Data is available on request from the authors.
Conflicts of Interest: The authors declare that they have no conflicts of interest to report regarding the present study.
References
1. Malyan SK, Kumar SS, Fagodiya RK, Ghosh P, Kumar A, Singh R,et al. Biochar for environmental sustainability in the energy-water-agroecosystem nexus. Renew Sustain Energ Rev. 2021;149:111379. doi:10.1016/j.rser.2021.111379. [Google Scholar] [CrossRef]
2. Ibrahim MS, Sapuan SM, Faieza AA. Mechanical and thermal properties of composites from unsaturated polyester filled with oil palm. J Mech Eng Sci. 2014;2:133–47. [Google Scholar]
3. Popp J, Kovács S, Oláh J, Divéki Z, Balázs E. Bioeconomy: biomass and biomass-based energy supply and demand. New Biotechnol. 2021;60:76–84. doi:10.1016/j.nbt.2020.10.004 [Google Scholar] [PubMed] [CrossRef]
4. Yu Q, Wang Y, van Le Q, Yang H, Hosseinzadeh-Bandbafha H, Yang Y, et al. An overview on the conversion of forest biomass into bioenergy. Front Energy Res. 2021;9:1–10. [Google Scholar]
5. Abu-Omar MM, Barta K, Beckham GT, Luterbacher JS, Ralph J, Rinaldi R,et al. Guidelines for performing lignin-first biorefining. Energy Environ Sci. 2021;14:262–92. doi:10.1039/D0EE02870C. [Google Scholar] [CrossRef]
6. Guo A, Sun Z, Feng H, Shang H, Sathitsuksanoh N. State-of-the-art review on the use of lignocellulosic biomass in cementitious materials. Sustain Struct. 2023;3(1):000023. [Google Scholar]
7. Kant Bhatia S, Palai AK, Kumar A, Kant Bhatia R, Kumar Patel A,Thakur V, et al. Trends in renewable energy production employing biomass-based biochar. Bioresour Technol. 2021;340:125644. doi:10.1016/j.biortech.2021.125644 [Google Scholar] [PubMed] [CrossRef]
8. Glushkov D, Nyashina G, Shvets A, Pereira A, Ramanathan A. Current status of the pyrolysis and gasification mechanism of biomass. Energies. 2021;14(22):7541. doi:10.3390/en14227541. [Google Scholar] [CrossRef]
9. Mustafa AH, Rashid SS, Rahim MHA, Roslan R, Musa WAM, Sikder BH,et al. Enzymatic pretreatment of lignocellulosic biomass: an overview. J Chem Eng Ind Biotechnol. 2022;8(1):1–7. [Google Scholar]
10. Nargotra P, Sharma V, Lee YC, Tsai YH, Liu YC, Shieh CJ, et al. Microbial lignocellulolytic enzymes for the effective valorization of lignocellulosic biomass: a review. Catalysts. 2023;13(1):1–28. [Google Scholar]
11. Davis K, Moon TS. Tailoring microbes to upgrade lignin. Curr Opin Chem Biol. 2020;59:23–9. doi:10.1016/j.cbpa.2020.04.001 [Google Scholar] [PubMed] [CrossRef]
12. Hua LS, Chen LW, Geng BJ, Kristak L, Antov P, Pędzik M, et al. Particleboard from agricultural biomass and recycled wood waste: a review. J Mater Res Technol. 2022;20:4630–58. doi:10.1016/j.jmrt.2022.08.166. [Google Scholar] [CrossRef]
13. Xu J, Tao A, Qi J, Wang Y. Bast fibers: kenaf. In: Ryszard MK, Maria MT, editors. Hank book of natural fibers. UK: Elsevier Ltd.; 2020. p. 71–92. [Google Scholar]
14. Saeed HAM, Liu Y, Lucia LA, Chen H. Evaluation of sudanese sorghum and bagasse as a pulp and paper feedstock. BioResources. 2017;12(3):5212–22. [Google Scholar]
15. Wang Z, An S, Zhao J, Sun P, Lyu H, Kong WW, et al. Plastic regulates its co-pyrolysis process with biomass: influencing factors, model calculations, and mechanisms. Front Ecol Environ. 2022;10:1–17. [Google Scholar]
16. Dahou T, Defoort F, Khiari B, Labaki M, Dupont C, Jeguirim M. Role of inorganics on the biomass char gasification reactivity: a review involving reaction mechanisms and kinetics models. Renew Sustain Energ Rev. 2021;135. [Google Scholar]
17. Danso-Boateng E, Achaw OW. Bioenergy and biofuel production from biomass using thermochemical conversions technologies—A review. AIMS Energy. 2022;10(4):585–647. doi:10.3934/energy.2022030. [Google Scholar] [CrossRef]
18. Sankaran R, Markandan K, Khoo KS, Cheng CK, Ashokkumar V, Deepanraj B, et al. The expansion of lignocellulose biomass conversion into bioenergy via nanobiotechnology. Front Nanotechnol. 2021;3:793528. doi:10.3389/fnano.2021.793528. [Google Scholar] [CrossRef]
19. Chen D, Cen K, Zhuang X, Gan Z, Zhou J, Zhang Y,et al. Insight into biomass pyrolysis mechanism based on cellulose, hemicellulose, and lignin: evolution of volatiles and kinetics, elucidation of reaction pathways, and characterization of gas, biochar and bio-oil. Combust Flame. 2022;242:112142. doi:10.1016/j.combustflame.2022.112142. [Google Scholar] [CrossRef]
20. Navarro AF, Cegarra J, Roig A, Garcia D. Relationships between organic matter and carbon contents of organic wastes. Bioresour Technol. 1993;44(3):203–7. doi:10.1016/0960-8524(93)90153-3. [Google Scholar] [CrossRef]
21. Martins GR, Monteiro AF, do Amaral FRL, da Silva AS. A validated Folin-Ciocalteu method for total phenolics quantification of condensed tannin-rich açaí (Euterpe oleracea Mart.) seeds extract. J Food Sci Technol. 2021;58(12):4693–702. doi:10.1007/s13197-020-04959-5 [Google Scholar] [PubMed] [CrossRef]
22. Lawag IL, Nolden ES, Schaper AAM, Lim LY, Locher C. A modified folin-ciocalteu assay for the determination of total phenolics content in honey. Appl Sci. 2023;13(4):1–18. [Google Scholar]
23. Frances M, Gardere Y, Duret E, Leroyer L, Cabaret T, Cabaret T, et al. Effect of heat treatment on Pinus pinaster rosin: a study of physico chemical changes and influence on the quality of rosin linseed oil varnish. Ind Crops Prod. 2020;155:112789. doi:10.1016/j.indcrop.2020.112789. [Google Scholar] [CrossRef]
24. Melville J. UC berkeley college of chemistry bomb calorimetry and heat of combustion. USA: Physical Chemistry Laboratory; 2014. [Google Scholar]
25. Hamidon MH, Sultan MTH, Ariffin AH, Shah AUM. Effects of fibre treatment on mechanical properties of kenaf fibre reinforced composites: a review. J Mater Res Technol. 2019;8(3):3327–37. doi:10.1016/j.jmrt.2019.04.012. [Google Scholar] [CrossRef]
26. Kanwal S, Chaudhry N, Munir S, Sana H. Effect of torrefaction conditions on the physicochemical characterization of agricultural waste (sugarcane bagasse). Waste Manag. 2019;88:280–90. doi:10.1016/j.wasman.2019.03.053 [Google Scholar] [PubMed] [CrossRef]
27. Hou X, Sun F, Yan D, Xu H, Dong Z, Li Q, et al. Preparation of lightweight polypropylene composites reinforced by cotton stalk fibers from combined steam flash-explosion and alkaline treatment. J Clean Prod. 2014;83:454–62. doi:10.1016/j.jclepro.2014.07.018. [Google Scholar] [CrossRef]
28. Gupta A, Thengane SK, Mahajani S. Kinetics of pyrolysis and gasification of cotton stalk in the central parts of India. Fuel. 2020;263:116752. doi:10.1016/j.fuel.2019.116752. [Google Scholar] [CrossRef]
29. Ning P, Yang G, Hu L, Sun J, Shi L. Recent advances in the valorization of plant biomass. Biotechnol Biofuels. 2021;14(1):1–22. [Google Scholar]
30. Ferdous T, Quaiyyum MA, Salam A, Jahan MS. Pulping of bagasse (Saccrarum officinarumkash (Saccharum spontaneum) and corn stalks (Zea mays). Curr Res Green Sustain Chem. 2020;3:100017. doi:10.1016/j.crgsc.2020.100017. [Google Scholar] [CrossRef]
31. Guillou J, Lavadiya DN, Munro T, Fronk T, Ban H. From lignocellulose to biocomposite: multilevel modelling and experimental investigation of the thermal properties of kenaf fiber reinforced composites based on constituent materials. Appl Therm Eng. 2018;128:1372–81. doi:10.1016/j.applthermaleng.2017.09.095. [Google Scholar] [CrossRef]
32. Shahzad K, Sohail M, Hamid A. Green ethanol production from cotton stalk. IOP Conf Seri: Earth Environ Sci. 2019;257(1):012025. [Google Scholar]
33. Li G, Wang Y, Yu D, Zhu P, Zhao G, Liu C, et al. Ligninolytic characteristics of Pleurotus ostreatus cultivated in cotton stalk media. Front Microbiol. 2022;13:1035040. doi:10.3389/fmicb.2022.1035040 [Google Scholar] [PubMed] [CrossRef]
34. Broda M. Natural compounds for wood protection against fungi—A review. Molecules. 2020;25(15):1–24. [Google Scholar]
35. Spinacé MAS, Lambert CS, Fermoselli KKG, de Paoli MA. Characterization of lignocellulosic curaua fibres. Carbohydr Polym. 2009;77(1):47–53. doi:10.1016/j.carbpol.2008.12.005. [Google Scholar] [CrossRef]
36. Janis E, Anka ZF. Reinforcing plastics with renewable raw materials less moisture in natural fibers. Fraunhofer; 2018. p. 1–3. [Google Scholar]
37. Edreis EMA, Li X, Xu C, Yao H. Kinetic study and synergistic interactions on catalytic CO2 gasification of Sudanese lower sulphur petroleum coke and sugar cane bagasse. J Mater Res Technol. 2017;6(2):147–57. doi:10.1016/j.jmrt.2016.09.001. [Google Scholar] [CrossRef]
38. Hamza S, Saad H, Charrier B, Ayed N, Charrier-El Bouhtoury F. Physico-chemical characterization of Tunisian plant fibers and its utilization as reinforcement for plaster based composites. Ind Crops Prod. 2013;49:357–65. doi:10.1016/j.indcrop.2013.04.052. [Google Scholar] [CrossRef]
39. Khiari R, Mhenni MF, Belgacem MN, Mauret E. Chemical composition and pulping of date palm rachis and Posidonia oceanica—A comparison with other wood and non-wood fibre sources. Bioresour Technol. 2010;101(2):775–80. doi:10.1016/j.biortech.2009.08.079 [Google Scholar] [PubMed] [CrossRef]
40. Platače R, Adamovičs A. The evaluation of ash content in grass biomass used for energy production. WIT Trans Ecol Environ. 2014;190:1057–65. [Google Scholar]
41. Saba N, Jawaid M, Hakeem KR, Paridah MT, Khalina A, Alothman OY. Potential of bioenergy production from industrial kenaf (Hibiscus cannabinus L.) based on Malaysian perspective. Renew Sustain Energ Rev. 2015;42:446–59. doi:10.1016/j.rser.2014.10.029. [Google Scholar] [CrossRef]
42. Zhou B, Wang L, Ma G, Zhao X, Zhao X. Preparation and properties of bio-geopolymer composites with waste cotton stalk materials. J Clean Prod. 2020;245:118842. doi:10.1016/j.jclepro.2019.118842. [Google Scholar] [CrossRef]
43. Teixeira Cardoso AR, Conrado NM, Krause MC, Bjerk TR, Krause LC, Caramao EB. Chemical characterization of the bio-oil obtained by catalytic pyrolysis of sugarcane bagasse (industrial waste) from the species Erianthus Arundinaceus. J Environ Chem Eng. 2019;7(2):102970. doi:10.1016/j.jece.2019.102970. [Google Scholar] [CrossRef]
44. Rozyanty AR, Zhafer SF, Shayfull Z, Nainggolan I, Musa L, Zheing LT. Effect of water and mechanical retting process on mechanical and physical properties of kenaf bast fiber reinforced unsaturated polyester composites. Compos Struct. 2020;257:113384. [Google Scholar]
45. Saha P, Manna S, Chowdhury SR, Sen R, Roy D, Adhikari B. Enhancement of tensile strength of lignocellulosic jute fibers by alkali-steam treatment. Bioresour Technol. 2010;101(9):3182–7. doi:10.1016/j.biortech.2009.12.010 [Google Scholar] [PubMed] [CrossRef]
46. Karimi S, Tahir PM, Karimi A, Dufresne A, Abdulkhani A. Kenaf bast cellulosic fibers hierarchy: a comprehensive approach from micro to nano. Carbohydr Polym. 2014;101(1):878–85 [Google Scholar] [PubMed]
47. Guo A, Sun Z, Satyavolu J. Impact of chemical treatment on the physiochemical and mechanical properties of kenaf fibers. Ind Crops Prod. 2019;141:111726. doi:10.1016/j.indcrop.2019.111726. [Google Scholar] [CrossRef]
48. Tuerxun D, Pulingam T, Nordin NI, Chen YW, Kamaldin JB, Julkapli NBM, et al. Synthesis, characterization and cytotoxicity studies of nanocrystalline cellulose from the production waste of rubber-wood and kenaf-bast fibers. Eur Polym J. 2018;116:352–60. [Google Scholar]
49. Schramm C. High temperature ATR-FTIR characterization of the interaction of polycarboxylic acids and organotrialkoxysilanes with cellulosic material. Spectrochimica Acta Part A: Mol Biomol Spectrosc. 2020;243:118815. doi:10.1016/j.saa.2020.118815 [Google Scholar] [PubMed] [CrossRef]
50. Lin H, Long J, Gu Q, Zhang W, Ruan R, Li Z, et al. In situ IR study of surface hydroxyl species of dehydrated TiO2: towards understanding pivotal surface processes of TiO2 photocatalytic oxidation of toluene. Phys Chem Chem Phys. 2012;14(26):9468–74. doi:10.1039/c2cp40893g [Google Scholar] [PubMed] [CrossRef]
51. Rahbar Shamskar K, Heidari H, Rashidi A. Preparation and evaluation of nanocrystalline cellulose aerogels from raw cotton and cotton stalk. Ind Crops Prod. 2016;93:203–11. doi:10.1016/j.indcrop.2016.01.044. [Google Scholar] [CrossRef]
52. Gaur R, Soam S, Sharma S, Gupta RP, Bansal VR, Kumar R, et al. Bench scale dilute acid pretreatment optimization for producing fermentable sugars from cotton stalk and physicochemical characterization. Ind Crops Prod. 2016;83:104–12. doi:10.1016/j.indcrop.2015.11.056. [Google Scholar] [CrossRef]
53. Wu H, Liang X, Huang L, Xie Y, Tan S, Cai X. The utilization of cotton stalk bark to reinforce the mechanical and thermal properties of bio-flour plastic composites. Constr Build Mater. 2016;118:337–43. doi:10.1016/j.conbuildmat.2016.02.095. [Google Scholar] [CrossRef]
54. Sasmal S, Goud VV, Mohanty K. Characterization of biomasses available in the region of North-East India for production of biofuels. Biomass Bioenergy. 2012;45:212–20. doi:10.1016/j.biombioe.2012.06.008. [Google Scholar] [CrossRef]
55. Coletti F, Romani M, Ceres G, Zammit U, Guidi MC. Evaluation of microscopy techniques and ATR-FTIR spectroscopy on textile fibers from the Vesuvian area: a pilot study on degradation processes that prevent the characterization of bast fibers. J Archaeol Sci: Rep. 2020;36:102794. [Google Scholar]
56. Corrêa AC, de Teixeira EM, Pessan LA, Mattoso LHC. Cellulose nanofibers from curaua fibers. Cellulose. 2010;17(6):1183–92. doi:10.1007/s10570-010-9453-3. [Google Scholar] [CrossRef]
57. Candido RG, Gonçalves AR. Evaluation of two different applications for cellulose isolated from sugarcane bagasse in a biorefinery concept. Ind Crops Prod. 2019;142:111616. doi:10.1016/j.indcrop.2019.111616. [Google Scholar] [CrossRef]
58. Priharto N, Ronsse F, Yildiz G, Heeres HJ, Deuss PJ, Prins W. Fast pyrolysis with fractional condensation of lignin-rich digested stillage from second-generation bioethanol production. J Anal Appl Pyrolysis. 2020;145:104756. doi:10.1016/j.jaap.2019.104756. [Google Scholar] [CrossRef]
59. Nurazzi NM, Asyraf MRM, Rayung M, Norrrahim MNF, Shazleen SS, Rani MSA, et al. Thermogravimetric analysis properties of cellulosic natural fiber polymer composites: a review on influence of chemical treatments. Polymers. 2021;13(16):2710. doi:10.3390/polym13162710 [Google Scholar] [PubMed] [CrossRef]
60. Singh S, Varanasi P, Singh P, Adams PD, Auer M, Simmons BA. Understanding the impact of ionic liquid pretreatment on cellulose and lignin via thermochemical analysis. Biomass Bioenergy. 2013;54:276–83. doi:10.1016/j.biombioe.2013.02.035. [Google Scholar] [CrossRef]
61. Sai RJ, Sai MV, Kalyan SY, Vineeth KD, Srividya K, Sumanth CHM. TGA and DSC analysis of vinyl ester reinforced by Vetiveria zizanioides, jute and glass fiber. Mater Today: Proc. 2019;26:460–5. [Google Scholar]
62. Boer FD, Valette J, Commandré JM, Fournier M, Thévenon MF. Slow pyrolysis of sugarcane bagasse for the production of char and the potential of its by-product for wood protection. J Renew Mater. 2020;9(1):97–117. doi:10.32604/jrm.2021.013147 [Google Scholar] [CrossRef]
63. Yub Harun N, Jin Han T, Vijayakumar T, Saeed A, Afzal MT. Ash deposition characteristics of industrial biomass waste and agricultural residues. Mater Today: Proc. 2019;19:1712–21. [Google Scholar]
64. Gupta GK, Mondal MK. Bioenergy generation from agricultural wastes and enrichment of end products. India: Elsevier Inc.; 2019. [Google Scholar]
65. Singh M, Singh R, Gill G. Estimating the correlation between the calorific value and elemental components of biomass using regrassion analysis. Int J Electron Electr Eng. 2020;3(9):2347–6982. [Google Scholar]
Cite This Article
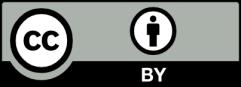
This work is licensed under a Creative Commons Attribution 4.0 International License , which permits unrestricted use, distribution, and reproduction in any medium, provided the original work is properly cited.