Open Access
ARTICLE
Synthesis and Characterization of Phenyl Camellia oleifera Seed Oil Ester Plasticizing PVC
1 College of Chemistry and Chemical Engineering, Zhongkai University of Agriculture and Engineering, Guangzhou, 510225, China
2 College of Chemical Engineering, Zhejiang University of Technology, Hangzhou, 310000, China
3 Key Laboratory of Germplasm Platform and Ornamental Plants, College of Horticulture and Landscape Architecture, Zhongkai University of Agriculture and Engineering, Guangzhou, 510225, China
* Corresponding Authors: Qiaoguang Li. Email: ; Yongquan Li. Email:
# Authors have contributed equally
Journal of Renewable Materials 2024, 12(3), 615-628. https://doi.org/10.32604/jrm.2023.046780
Received 14 October 2023; Accepted 14 December 2023; Issue published 11 April 2024
Abstract
Plasticizers are essential additives in the processing of polyvinyl chloride (PVC), with phthalate plasticizers being widely used. However, these conventional plasticizers have been shown to be harmful to human health and environmentally unfriendly, necessitating the exploration of eco-friendly bio-based alternatives. In this study, Camellia oleifera seed oil, a specialty resource in China, was utilized as a raw material and reacted with 4,4′-Methylenebis(N,N-diglycidylaniline) (AG-80) to synthesize Phenyl Camellia seed Oil Ester (PCSOE). PCSOE was employed as a plasticizer to prepare modified PVC films with varying concentrations, with the conventional plasticizer dioctyl phthalate (DOP) serving as a control. Experimental results demonstrate that PSCOE-plasticized PVC films exhibit enhanced hydrophilicity, tensile strength, and thermal stability compared to DOP-modified PVC films. The contact angle of PSCOE-plasticized PVC films ranges from 66.26° to 78.48°, which is generally lower than the contact angle of DOP-modified PVC films at 78.40°, indicating improved hydrophilicity due to the modification with PCSOE. The tensile strength of PSCOE-plasticized PVC films ranges from 17.73 to 20.17 MPa, all surpassing the value of 16.41 MPa for DOP-modified PVC films. Moreover, the temperatures corresponding to 5%, 10%, and 50% weight loss for PVC samples modified with PCSOE are higher than those for DOP. Hence, PCSOE presents a viable alternative to DOP as a plasticizer for PVC materials.Keywords
Nomenclature
PVC | Polyvinyl chloride |
AG-80 | 4,4′-Methylenebis(N,N-diglycidylaniline) |
PCSOE | Phenyl Camellia seed Oil Ester |
DOP | Dioctyl Phthalate |
RCOSO | Refined Camellia oleifera seed oil |
FT-IR | Fourier Transform Infrared Spectroscopy |
Raman | Raman Spectroscopy |
NMR | Nuclear Magnetic Resonance |
SEM | Scanning Electron Microscopy |
EDS | Energy-Dispersive X-ray Spectroscopy |
AFM | Atomic Force Microscopy |
DSC | Differential Scanning Calorimetry |
TGA | Thermogravimetric Analysis |
DTG | Derivative Thermogravimetric |
Polyvinyl chloride (PVC), as one of the five general purpose synthetic resins, holds a substantial share in the global market [1]. PVC features a unique set of properties due to the introduction of chlorine atoms into its polymer backbone. Its advantages, including high strength, corrosion resistance, and affordability, have led to widespread applications in construction materials, daily goods, and industrial materials [2,3]. However, the inherent brittleness of PVC hinders its practical applications [4].
Plasticizers have become indispensable additives in the industrial production of PVC plastics [5]. When incorporated into the PVC matrix, plasticizers can achieve uniform mixing and compatibility, effectively weakening the intramolecular secondary bonds of the polymer chains. This enhances the material’s plasticity, making it more flexible and malleable while also improving PVC product performance [6,7]. Plasticizers come in various types, at present, the most extensively used plasticizers are phthalate plasticizers, accounting for over 80% of the total plasticizer consumption, primarily as primary plasticizers for PVC [8–10].
Phthalate plasticizers, among them Dioctyl Phthalate (DOP), Dibutyl Phthalate (DBP), Di-(2-ethylhexyl Phthalate) (DEHP), and Diisononyl Phthalate (DINP), are the most common plasticizers in PVC processing [11,12]. Dioctyl Phthalate (DOP) has excellent compatibility with PVC due to its low molecular weight, which allows it to easily insert between PVC molecules and provides high plasticizing efficiency without compromising the electrical insulation and safety properties of the products. Moreover, DOP is inexpensive. As a traditional plasticizer, it is highly popular for modifying PVC materials [13–15]. However, with the widespread application of DOP in industries such as food packaging and pharmaceuticals, increasing research has revealed its potential hazards to human health and the environment [16–18]. Consequently, the development of new plasticizers that are non-toxic, environmentally friendly, safe, cost-effective, and capable of replacing phthalate plasticizers has become an emerging trend [19].
Vegetable oils are widely distributed in nature, typically extracted from plant fruits, seeds, and embryos. Most vegetable oils are rich in unsaturated fatty acids [20]. Camellia oleifera Abel., belonging to genus Camellia of the family Theaceae, is a woody oil crop widely cultivated in Southern China [21,22]. Extracted Camellia oleifera seed oil is abundant in unsaturated fatty acids, mainly oleic acid and linoleic acid, accounting for 90% of the total [22]. Camellia oil is regarded as a precious product with high nutritional value because it is rich in unsaponifiable substances such as polyphenols, phytosterols and other functional ingredients. The physicochemical properties of camellia oil: the acid value, the Iodine value and the saponification value are respectively 0.1–0.5 mg/g, 83.9–86.30 g I2/100 g and 193.28–194.05 mg KOH/g [23]. Unsaturated fatty acids lie oleic acid lack benzene rings in their structure and contain unsaturated double bonds, rendering their derivatives suitable as raw materials for plasticizers in PVC modification due to increased thermal stability.
This study employs camellia seeds as raw materials to produce refined Camellia oleifera seed oil (RCOSO) as a source of carboxylic acids, combined with 4,4′-Methylenebis(N,N-diglycidylaniline) (AG-80) to provide epoxy groups. Through epoxy ring opening and esterification reactions, a novel multi-ester plasticizer, Phenyl Camellia seed Oil Ester (PCSOE), is synthesized [14,20]. Structural analysis using Fourier-transform infrared spectroscopy, Raman spectroscopy, and nuclear magnetic resonance is conducted. By comparing PCSOE with the reference plasticizer DOP, the study investigates the potential of PCSOE as a replacement for DOP in the modification of PVC films. The research on synthesizing bio-based plasticizers using Camellia oleifera seed oil is a promising endeavor, aiming to explore the latent value and reserve technologies for recycling and further processing of waste generated during Camellia oleifera seed oil production. The oil content of tea seeds is 30% to 40%, and the oil yield is about 14% to 27% according to the quality of tea seeds in different places. No matter from press extraction or solvent extraction, waste oil may be produced in the process of preparation, or in the process of application, this technology can be used as a potential conversion deep processing technology [23].
Organic Camellia oleifera seed oil (commercial edible oil, Guangdong Huabao Agricultural Technology Co., Ltd., Guangzhou, China); Potassium hydroxide (Analytical Reagent, Tianjin Damao Chemical Reagent Co., Ltd., Tianjin, China); Hydrochloric acid (Analytical Reagent, Guangzhou Chemical Reagent Factory, Guangzhou, China); Ethanol anhydrous (Analytical Reagent, Shanghai Titan Technology Co., Ltd., Shanghai, China); 4,4′-Methylenebis(N,N-diglycidylaniline) (Analytical Reagent, Shanghai Macklin Biochemical Co., Ltd., Shanghai, China); Benzyltriethylammonium chloride (Analytical Reagent, Shanghai Macklin Biochemical Co., Ltd., Shanghai, China); Tetrahydrofuran (Analytical Reagent, Shanghai Macklin Biochemical Co., Ltd., Shanghai, China); Polyvinyl chloride (Powder, Analytical Reagent, Shanghai Aladdin Bio-Chem Technology Co., Ltd., Shanghai, China); Dioctyl phthalate (Analytical Reagent, Shanghai Aladdin Bio-Chem Technology Co., Ltd., Shanghai, China).
2.2 Preparation of Refined Camellia oleifera Seed Oil (RCOSO)
26.40 g of potassium hydroxide was dissolved in ethanol anhydrous and poured into a conical flask containing 100 g of organic Camellia oleifera seed oil. The mixture was reacted at 60°C for 2 h. Then, 140 mL of 10% hydrochloric acid solution and 100 mL of ethanol anhydrous were added. After allowing the layers to separate, the upper clear liquid was collected. Water and alcohol were removed by rotary evaporation, and the sample was dried at 110°C. The resulting product was sealed, protected from light, and stored for future use.
2.3 Preparation of Phenyl Camellia Seed Oil Ester (PCSOE)
5 g of 4,4′-Methylenebis(N,N-diglycidylaniline), 10.69 g of refined Camellia oleifera seed oil, and 0.27 g of benzyltriethylammonium chloride (TEBAC) catalyst were added to a 250 mL three-necked flask. The mixture was reacted at 115°C for 2 h. After cooling, the obtained sample was sealed and stored away from light. The preparation reaction is depicted in Fig. 1.
Figure 1: Equation for the preparation of PCSOE
2.4 Preparation of Plasticized PVC Films
According to the formulation in Table 1, accurate amounts of PCSOE or DOP, PVC powder, and 50 ml of tetrahydrofuran (THF) were weighed using an analytical balance. The mixture was reacted at 38°C for 20 min. The resulting solution was evenly poured into a clean glass culture dish and placed horizontally in a constant temperature convection drying oven at 40°C. After drying for 24 h, the plasticized PVC film was obtained.
2.5.1 Fourier Transform Infrared Spectroscopy (FT-IR)
FT-IR (Thermo Scientific Nicolet IS10 spectrometer, Nicolet) analysis was performed on PCSOE samples within the infrared wavenumber range of 4000 to 500 cm−1 to determine their structural characteristics.
2.5.2 Raman Spectroscopy (Raman)
PCSOE and various plasticized PVC film samples were subjected to Raman spectroscopy (DXR2, Samufei) to investigate their structural properties.
2.5.3 Nuclear Magnetic Resonance (NMR)
Using deuterated chloroform (CDCl3) as the solvent, 1H NMR and 13C NMR of PCSOE were determined using a 400.13 and 100.61 MHz NMR spectrometer (AV400 spectrometer, Bruker).
2.5.4 Scanning Electron Microscopy (SEM)
Samples were affixed to sample holders using conductive adhesive, coated with gold for 30 s in a vacuum coater, and observed using a scanning electron microscope to study the morphology of various plasticized PVC film samples (EVO 18, ZEISS).
2.5.5 Energy-Dispersive X-Ray Spectroscopy (EDS)
Following the SEM observation of the morphology of different modified PVC film samples, X-ray energy-dispersive spectroscopy (EDS) was employed to determine the elemental composition of the samples using X-ACT energy-dispersive X-ray spectrometry.
2.5.6 Atomic Force Microscopy (AFM)
Atomic force microscopy was employed to study the two-dimensional and three-dimensional morphology of the samples by measuring van der Waals forces between the AFM (Dimension Edge supplied, Bruker) probe and the surface of the plasticized PVC film samples.
2.5.7 Hydrophilicity Measurement
Using ultra-pure water as the testing liquid, appropriately sized plasticized PVC film samples were prepared as sample plates. A volume of 11 μL of ultra-pure water was dropped onto the flat surface of the sample plate, and the contact angle was measured using a contact angle measurement instrument through the sessile drop method and image analysis (Theta, Switzerland).
2.5.8 Differential Scanning Calorimetry (DSC)
DSC (Q200, TA) analysis was conducted on various plasticized PVC film samples using a differential scanning calorimeter under a nitrogen atmosphere. The samples were heated from −10°C to 100°C at a heating rate of 10°C/min, with a nitrogen flow rate of 20 mL/min.
Samples of the plasticized PVC film samples were placed in crucibles and subjected to TG analysis (TG209F1, Netzsch) in a nitrogen atmosphere. The temperature was increased from 30°C to 600°C at a rate of 10°C/min to determine the glass transition temperature of the samples.
2.5.10 Tensile Strength Testing
Mechanical properties were determined using a universal testing machine (UTM6502, Suns) at room temperature. Test samples were cut from the plasticized PVC film samples using a 4 mm × 50 mm dumbbell-shaped cutter. The thickness and length of each test specimen were recorded, and the testing speed was set at 10 mm/min.
DOP has a low molecular weight and contains two long chain groups, which allows it to insert between PVC molecular chains as a lubricant. This increases the mobility of the PVC molecular chains, thereby enhancing its plasticity, flexibility and processability [24].
As shown in Fig. 2, both PCSOE and DOP consist of rigid benzene rings, polar ester groups, and alkyl chains. Compared to DOP, PCSOE possesses four polar ester groups, four hydroxyl groups, two rigid rings, and four long carbon chains. Similar in structure to DOP, PCSOE is tentatively considered suitable for replacing DOP in modifying PVC. This molecular structure with multiple polar ester and hydroxyl groups enhances its interactions with PVC molecules. Additionally, the presence of a rigid benzene ring provides stability and compatibility with PVC molecules.
Figure 2: Structural formula for DOP and PCSOE: (a) DOP; (b) PCSOE
3.1 Structural Characterization of PCSOE
Fig. 3I shows the infrared absorption spectra of refined Camellia oleifera seed oil (RCOSO), 4,4′-Methylenebis(N,N-diglycidylaniline) (AG-80), and Phenyl Camellia seed oil Ester (PCSOE). As depicted in the figure, the AG-80 curve displays a prominent stretching vibration peak of the epoxy group (C-O-C) at 905 cm−1, which is absent in the PCSOE curve. The RCOSO curve exhibits a stretching vibration peak of the carboxyl group (C=O) at 1708 cm−1, whereas the PCSOE curve shows a stretching vibration absorption peak of the ester group (C=O) around 1737 cm−1 and a hydroxyl group (-OH) stretching vibration peak at 3415 cm−1. These peaks indicate the formation of ester groups and hydroxyl groups in PCSOE, suggesting the successful reaction between RCOSO and AG-80 to produce PCSOE.
Figure 3: (I) FT-IR spectra of RCOSO, AG-80, PCSOE; (II) Raman spectra of RCOSO, AG-80, PCSOE; (III) 13C NMR of AG-80, PCSOE; (IV) 1H NMR of AG-80, PCSOE
Fig. 3II reveals the disappearance of characteristic peaks of epoxy groups in the range of 677~932 cm−1 in the AG-80 spectrum when compared to the PCSOE spectrum. This disappearance suggests the opening of epoxy groups in AG-80. Unique peaks in PCSOE, such as the characteristic peak of the C=C group at 1640 cm−1 and the ester group (C=O) characteristic peak at 2897 cm−1, further confirm the successful synthesis of PCSOE through the reaction between RCOSO and AG-80.
In Fig. 3III, the 0 peak corresponds to the deuterated chloroform solvent. In the 13C NMR spectrum of AG-80, the signals at 45 and 51 ppm originate from the carbon atoms of the epoxy groups (C1 and C2). In the 13C NMR spectrum of PCSOE, the signals shift to the range of 60~65 ppm, indicating the disruption of epoxy groups. In the 13C NMR spectrum of PCSOE, the signal at 174 ppm comes from the carbon signal of the ester group, while the signal peak at 130 ppm originates from the carbon-carbon double bond (C=C). These shifts and signals indicate the introduction of Camellia oleifera seed oil and the successful reaction with AG-80, involving the epoxy ring opening in AG-80 and carboxyl esterification with Camellia oleifera seed oil.
Fig. 3IV displays the 1H NMR spectra of AG-80 and PCSOE. In this figure, the 0 peak corresponds to the deuterated chloroform solvent. In the 1H NMR spectrum of AG-80, the proton signals of the epoxy group on the carbon atom C1 range from 2.47 to 2.71 ppm, which shift to 4.1 ppm in PCSOE, indicating the breakage of epoxy groups in AG-80. In the 1H NMR spectrum of PCSOE, the signals at 5.2~5.3 ppm correspond to the proton signals of the C=C group on the long carbon chain (peaks 5 and 6), and the proton signals of the hydroxyl group (-OH) generated by the opening of the epoxy group and carboxyl esterification. This confirms the successful opening of the epoxy group in AG-80 and the formation of new hydroxyl groups in PCSOE.
3.2 Structure Analysis of Plasticized PVC Samples
Fig. 4I depicts the Raman spectra of plasticized PVC film with different formulations. From the graph, it is evident that curves H2, H3, and H4 exhibit a characteristic peak of the C=C functional group at 1655 cm−1, originating from the C=C groups in PCSOE. Curves H1, H2, H3, and H4 all display a characteristic peak at 2940 cm−1, which corresponds to the ester functional group. Based on the above analysis, this Raman spectrum aligns with the expected results and confirms the successful combination of PVC material with different concentrations of PCSOE.
Figure 4: (I) Raman spectra of H1, H2, H3, H4; (II) SEM photographs of H1, H2, H3, H4; (III) EDS photographs of H4, (a) Distribution of C element of H4, (b) Distribution of Cl element of H4, (c) Distribution of O element of H4, (d) Distribution of C, Cl and O elements of H4, (e) Surface micrograph of H4, (f) EDS spectra of H4, (g) Content histogram of C, Cl and O elements
Fig. 4II presents the scanning electron microscope (SEM) images of plasticized PVC film with different formulations. As shown in the figure, the surface of the H1 film is relatively smooth, yet there are some granular particles and strip-like folds present. Compared to H1, films H2, H3, and H4 are smoother, but with increasing PCSOE content, the film surface gradually becomes rougher. A small amount of granular distribution appears on the PVC surface, and the strip-like folds increase with higher PCSOE content. However, the overall appearance of the films remains relatively uniform. While all four formulations of plasticized PVC film exhibit strip-like folds and granular features, the surface remains generally smooth. The compatibility between PCSOE and PVC is greater than that with DOP, aligning with the expected product performance.
Fig. 4III displays the Energy Dispersive X-ray Spectroscopy (EDS) testing results of film H4. From the graph, it is evident that H4 contains Carbon (C), Oxygen (O), and Chlorine (Cl) elements, with mass percentages of 67.63%, 26.23%, and 6.13% respectively. The lower percentage of Oxygen is due to its absence in polyvinyl chloride (PVC) and its presence only in PCSOE. This results in a lower overall Oxygen content in the polymer. This indicates the presence of PCSOE in H4 and good compatibility with PVC. Figures a, b, and c illustrate the even and dense distribution of Carbon and Oxygen elements on the film surface. Chlorine elements slightly aggregate in the central region of the film, as shown in figure d. The distribution in other areas is relatively uniform.
Fig. 5 presents the Atomic Force Microscopy (AFM) two-dimensional and three-dimensional images of plasticized PVC film with different formulations. Due to the varying amounts of PCSOE added, the relative roughness of the PVC samples fluctuates. Among them, films H2 (Ra = 5.888 nm, Rq = 7.748 nm) and H3 (Ra = 5.177 nm, Rq = 7.668 nm) exhibit lower surface roughness and roughness factors compared to H1 (Ra = 6.440 nm, Rq = 9.016 nm). However, the film with the highest amount of added PCSOE, H4 (Ra = 7.342 nm, Rq = 10.273 nm), has higher surface roughness and roughness factors than H1. It can be initially inferred that surface roughness and roughness factors tend to increase with higher concentrations of added PCSOE.
Figure 5: 2D and 3D AFM of plasticized PVC samples. H1 is 2D figure of H1, H2 is 2D figures of H2, H3 is 2D figures of H3, H4 is 2D figures of H4; H1-3D is 3D image H1, H2-3D is 3D image H2, H3-3D is 3D image H3, H4-3D is 3D image H4
3.3 Performance Analysis of Plasticized PVC Samples
Fig. 6I illustrates the contact angle test results of plasticized PVC film with different formulations. The contact angles of H1, H2, H3, and H4 are all less than 90°, indicating hydrophilic characteristics. Among them, the contact angle for H1 is 78.40° ± 2.73, while the contact angles for H2, H3, and H4 are 71.88° ± 3.44, 78.48° ± 3.32, and 66.26° ± 4.55, respectively. The contact angles of PSCOE-plasticized PVC films exhibit a trend of initially increasing and then decreasing as the amount of added PCSOE increases. Except for H3, which has a slightly larger contact angle than H1, this may be related to the surface substrate structure. H3 has relatively small surface roughness and roughness factors, while the other two groups are significantly smaller than H1, making them more prone to wetting by liquids. This indicates that the hydrophilicity of PVC films plasticized with PCSOE is improved, possibly due to the introduction of multiple hydrophilic hydroxyl groups from PCSOE, enhancing the affinity for water [25].
Figure 6: (I) Contact angle of plasticized PVC samples; (II) DSC curves of plasticized PVC samples; (III) TGA curves of plasticized PVC samples; (IV) DTG curves of plasticized PVC samples; (V) Stress-strain curves of plasticized PVC samples
Fig. 6II displays the Differential Scanning Calorimetry (DSC) curves of plasticized PVC film with different formulations. Within the temperature range of −10°C to 100°C, the Tg value is around 70°C and none of the films (H1, H2, H3, H4) exhibit decomposition exothermic peak. Therefore, it can be inferred that the PSCOE-plasticized PVC films exhibit good thermal stability and can be used for extended periods under conditions below 100°C.
Fig. 6III presents the Thermogravimetric Analysis (TGA) curves of plasticized PVC film with various formulations. From the graph, H1’s thermal weight loss can be divided into two temperature regions. The first stage occurs between approximately 170°C and 350°C, in the middle temperature range of the test, where thermal weight loss is generally attributed to the formation of HCl from the breaking of C-Cl bonds in the PVC structure [26]. Concurrently, the formation of double bonds induces further C-Cl bond breakage, leading to the formation of a polyene structure and generating numerous large molecular radicals and Cl atoms [27]. Additionally, plasticizers undergo decomposition, contributing to the continuous degradation of the PVC film, with a mass loss rate of 72.80% [28]. The second stage of thermal weight loss occurs between 350°C and 580°C, in the high-temperature range of the test, with a mass loss rate of 15.47%. This is primarily due to the fact that at high temperatures, the PVC macromolecular chains cannot maintain stability and gradually break down into smaller molecules [29]. The thermal weight loss of H2, H3, and H4 can be divided into three stages. The first stage, between 170°C and 260°C, exhibits mass loss rates of 35.8%, 36.94%, and 35.72%, respectively, in the mid-low temperature range of the test. This is mainly due to the decomposition of plasticizers in the PVC structure. Compared to H1, the mass loss rate of H2, H3 and H4 is much lower. This may be due to the presence of C=C double bonds with good thermal stability in them, which slows down the continuous degradation rate of the PVC films. This may be due to the fact that the epoxy bond absorbs Cl and H ions released from the material during PVC pyrolysis, which prevents the further degradation of the molecular chain, thus delaying further pyrolysis. The second stage occurs in the mid-high temperature range of the test, between 260°C and 420°C, with mass loss rates of 29.68%, 23.28%, and 25.56%, respectively. The final stage covers the temperature range of 420°C to 580°C, corresponding to the high-temperature range of the test, with mass loss rates of 20.92%, 26.32%, and 25.15%, respectively.
Fig. 6IV illustrates the Derivative Thermogravimetric Analysis (DTG) curves of plasticized PVC film with different formulations. From the graph, it can be observed that H1 exhibits relatively large fluctuations in mass decomposition rate. In the temperature ranges of 230°C to 270°C and 410°C to 470°C, H2, H3, and H4 experience significant variations in mass decomposition rate. In the remaining temperature ranges, the mass decomposition rate remains relatively stable. In the temperature ranges of 230°C to 270°C and 350°C to 470°C, the mass loss rates of H2, H3, and H4 are higher than that of H1.
Table 2 provides the thermal weight analysis data for plasticized PVC film with various formulations. From Figs. 6III and 6IV and Table 2, it can be observed that the mass residue rates of H2, H3, and H4 are significantly higher than that of H1, and the values of T5, T10, and T50 are also noticeably higher for H2, H3, and H4 compared to H1. For example, the T5, T10, and T50 of H2 are respectively 235.98°C, 241.22°C and 315.02°C. This indicates that the thermal stability of H2, H3, and H4 is better than that of H1 [30]. This improvement might be due to the presence of C=C double bonds in PCSOE made from Camellia oleifera seed oil, which can remove the radicals produced during the degradation process of PVC during the first thermal decomposition stage. This slows down the continuous degradation of the PVC film and reduces side reactions during polymerization, further enhancing the thermal stability of the polymer. Additionally, C=C double bonds can increase intra-molecular density and cross-linking, enhancing intermolecular forces and ensuring closer molecular packing. This denser arrangement can increase the melting point and glass transition temperature of molecules and prevent reactions like depolymerization or shear fracture at high temperatures.
Fig. 6V depicts the tensile strain curves of plasticized PVC film with different formulations. It can be observed that the films’ elongation at break follows the order from high to low: H1 > H4 > H3 > H2, with values of 341.57%, 118.04%, 108.24%, and 64.10%, respectively. The tensile strength follows the order from high to low: H2 > H3 > H1 > H4, with values of 20.17, 18.57, 17.73, and 16.41 MPa, respectively. The mechanical properties of PVC films plasticized with added PCSOE change as the mass of added PCSOE increases. When more PCSOE is added, the tensile strength of the PVC film decreases, while the elongation at break increases. This implies a decrease in hardness and an improvement in flexibility.
The reason for the decreased hardness and increased flexibility in PVC films modified with added PCSOE is likely due to the relatively large molecular volume of PCSOE, which contains four long-chain groups that can be inserted between PVC molecules. This insertion prevents close packing of PVC molecules, increasing the mobility of PVC molecular chains and reducing the crystallinity of PVC. Consequently, the hardness of PVC decreases, while flexibility and plasticity increase. The ester and hydroxyl groups in PCSOE molecules can form hydrogen bonds with chlorine atoms in PVC molecules, enhancing the strength of PVC [31].
The tensile performance of plasticized PVC films shows a clear pattern with the amount of added PCSOE. As the amount increases, the tensile strength of the film decreases, while the elongation at break increases. Overall, DOP-plasticized PVC films exhibit better flexibility compared to those plasticized with PCSOE. However, PSCOE-plasticized PVC films demonstrate better tensile strength enhancement.
In response to the requirements for plasticized PVC film regarding brittleness, environmental friendliness, and health considerations, traditional plasticizers like DOP can be replaced by bio-based and environmentally friendly plasticizers derived from renewable resources, thus expanding the application scope of PVC and its products. In this experiment, Camellia oleifera seed oil from plants was used as the main raw material. After a series of steps, a bio-based plasticizer was prepared and compared with dioctyl phthalate (DOP) plasticizer. The conclusions were as follows:
(1) AG-80 can react successfully with RCOSO to produce PCSOE with four ester groups. The structure of PCSOE is similar to that of DOP, making it a viable substitute for DOP as a plasticizer in modified PVC.
(2) PCSOE was used as a plasticizer to produce modified PVC films with varying concentrations, with DOP as the control. The films were characterized using Raman spectroscopy, scanning electron microscopy (SEM), X-ray energy dispersive spectroscopy (EDS), and atomic force microscopy (AFM). The results indicated good compatibility between PCSOE and PVC.
(3) After characterization and testing of the PVC films plasticized with both types of plasticizers, the following conclusions were drawn: In terms of mechanical performance, PSCOE-plasticized PVC films exhibited superior tensile strength compared to those plasticized with DOP, although they showed slightly lower elongation at break. In terms of hydrophilicity and thermal stability, the PSCOE-plasticized PVC films outperformed those plasticized with DOP.
Acknowledgement: The authors thank every author for their valuable suggestions, contribution and the fund for its support.
Funding Statement: This work was funded by the Scarce and Quality Economic Forest Engineering Technology Research Center (2022GCZX002) and the Key Lab. of Biomass Energy and Material, Jiangsu Province (Grant No. JSBEM-S-202305).
Author Contributions: Formal analysis, Y. Liu and Y. He; Funding acquisition, Q. Li and Y. Li; Methodology, W. Xiao and Q. Li; Project administration, Q. Li; Writing—original draft, Y. Liu, Y. He, and Q. Li; Writing—review & editing, W. Xiao, Q. Li and Y. Li All authors have read and agreed to the published version of the manuscript.
Availability of Data and Materials: Data will be made available on request.
Conflicts of Interest: The authors declare that they have no known competing financial interests or personal relationships that could have appeared to influence the work reported in this paper.
References
1. He, W., Zhu, G., Gao, Y., Wu, H., Fang, Z. et al. (2020). Green plasticizers derived from epoxidized soybean oil for poly(vinyl chlorideContinuous synthesis and evaluation in PVC films. Chemical Engineering Journal, 380, 122532. [Google Scholar]
2. Ma, Y., Liao, S., Li, Q., Guan, Q., Jia, P. et al. (2020). Physical and chemical modifications of poly(vinyl chloride) materials to prevent plasticizer migration—Still on the run. Reactive and Functional Polymers, 147, 104458. [Google Scholar]
3. Li, W., Qin, J., Wang, S., Han, D., Xiao, M. et al. (2018). Macrodiols derived from CO2-based polycarbonate as an environmentally friendly and sustainable PVC plasticizer: Effect of hydrogen-bond formation. ACS Sustainable Chemistry & Engineering, 6(7), 8476–8484. [Google Scholar]
4. Deng, T., Li, S., Yang, X., Xu, L., Ding, H. et al. (2022). A strategy to prepare internally-plasticized poly(vinyl chloride) by grafting castor oil onto the PVC chain with three different isocyanates as intermediate bridges. RSC Advances, 12(40), 26297–26306. [Google Scholar] [PubMed]
5. Li, M., Li, S., Xia, J., Ding, C., Wang, M. et al. (2017). Tung oil based plasticizer and auxiliary stabilizer for poly(vinyl chloride). Materials & Design, 122, 366–375. [Google Scholar]
6. Zhu, H., Yang, J., Wu, M., Wu, Q., Liu, J. et al. (2021). Vanillic acid as a new skeleton for formulating a biobased plasticizer. ACS Sustainable Chemistry & Engineering, 9(45), 15322–15330. [Google Scholar]
7. Sinisi, A., Degli Esposti, M., Toselli, M., Morselli, D., Fabbri, P. (2019). Biobased ketal-diester additives derived from levulinic acid: Synthesis and effect on the thermal stability and thermo-mechanical properties of poly(vinyl chloride). ACS Sustainable Chemistry & Engineering, 7(16), 13920–13931. [Google Scholar]
8. Feng, G., Hu, L., Ma, Y., Jia, P., Hu, Y. et al. (2018). An efficient bio-based plasticizer for poly(vinyl chloride) from waste cooking oil and citric acid: Synthesis and evaluation in PVC films. Journal of Cleaner Production, 189, 334–343. [Google Scholar]
9. Jia, P., Ma, Y., Song, F., Liu, C., Hu, L. et al. (2021). Renewable atom-efficient dendrimer-like acetate: From toxic tung oil to non-toxic plasticizers. Materials Today Chemistry, 21, 100518. [Google Scholar]
10. Chen, J., Nie, X., Jiang, J. (2020). Synthesis of a novel bio-oil-based hyperbranched ester plasticizer and its effects on poly(vinyl chloride) soft films. ACS Omega, 5(10), 5480–5486. [Google Scholar] [PubMed]
11. Qureshi, M. S., Yusoff, A. R. B. M., Wirzal, M. D. H., Sirajuddin, Barek, J. et al. (2016). Methods for the determination of endocrine-disrupting phthalate esters. Critical Reviews in Analytical Chemistry, 46(2), 146–159. [Google Scholar] [PubMed]
12. Lee, S., Park, M. S., Shin, J., Kim, Y. W. (2018). Effect of the individual and combined use of cardanol-based plasticizers and epoxidized soybean oil on the properties of PVC. Polymer Degradation and Stability, 147, 1–11. [Google Scholar]
13. Song, F., Huang, C., Zhu, X., Liu, C., Zhou, Y. et al. (2021). Synthesis and application of an environmental epoxy plasticizer with phthalate-like structure based on tung oil and cardanol for poly(vinyl chloride). Journal of Applied Polymer Science, 138(33), 50809. [Google Scholar]
14. Pereira, V. A., Fonseca, A. C., Costa, C. S. M. F., Ramalho, A., Coelho, J. F. J. et al. (2020). End-capped biobased saturated polyesters as effective plasticizers for PVC. Polymer Testing, 85, 106406. [Google Scholar]
15. Rajput, C. V., Sastry, N. V., Chikhaliya, N. P. (2023). Phosphorous-containing flame retardant plasticizer based on Cassia fistula seed oil and their application in poly(vinyl chloride) films. Industrial Crops and Products, 203, 117120. [Google Scholar]
16. Tan, J., Zhang, T., Wang, F., Huang, N., Yu, M. et al. (2022). One-pot and industrial manufacturing of cardanol-based polyoxyethylene ether carboxylates as efficient and improved migration resistance plasticizers for PVC. Journal of Cleaner Production, 375, 133943. [Google Scholar]
17. Adjei, J. K., Ofori, A., Megbenu, H. K., Ahenguah, T., Boateng, A. K. et al. (2021). Health risk and source assessment of semi-volatile phenols, p-chloroaniline and plasticizers in plastic packaged (sachet) drinking water. Science of the Total Environment, 797, 149008. [Google Scholar] [PubMed]
18. Bui, T. T., Giovanoulis, G., Cousins, A. P., Magnér, J., Cousins, I. T. et al. (2016). Human exposure, hazard and risk of alternative plasticizers to phthalate esters. Science of the Total Environment, 541, 451–467. [Google Scholar] [PubMed]
19. Feng, S., Zhang, P., Jiang, P., Zhang, Z., Deng, J. et al. (2022). Synthesis and application of high-stability bio-based plasticizer derived from ricinoleic acid. European Polymer Journal, 169, 111125. [Google Scholar]
20. Zhang, Z., Jiang, P., Liu, D., Feng, S., Zhang, P. et al. (2021). Research progress of novel bio-based plasticizers and their applications in poly(vinyl chloride). Journal of Materials Science, 56(17), 10155–10182. [Google Scholar]
21. Gong, H., Chang, Y., Xu, J., Yu, X., Gong, W. et al. (2023). Unilateral cross-incompatibility between Camellia oleifera and C. yuhsienensis provides new insights for hybridization in Camellia spp. Frontiers in Plant Science, 14, 1182745. [Google Scholar] [PubMed]
22. Zhu, G., Liu, H., Xie, Y., Liao, Q., Lin, Y. et al. (2020). Postharvest processing and storage methods for Camellia oleifera seeds. Food Reviews International, 36(4), 319–339. [Google Scholar]
23. Gao, L., Jin, L., Liu, Q., Zhao, K., Lin, L. et al. (2024). Recent advances in the extraction, composition analysis and bioactivity of Camellia (Camellia oleifera Abel.) oil. Trends in Food Science & Technology, 143, 104211. [Google Scholar]
24. Shieh, Y. T., Liu, C. M. (2002). Influences of contents and molecular weights of LDPE on DOP plasticization of PVC. Journal of Applied Polymer Science, 83(12), 2548–2555. [Google Scholar]
25. Cai, H., Wang, Y., Wu, K., Guo, W. (2020). Enhanced hydrophilic and electrophilic properties of polyvinyl chloride (PVC) biofilm carrier. Polymers, 12(6), 1240. [Google Scholar] [PubMed]
26. N., V., Santos, R., Godinho, B., Silva, R., Ferreira, A. (2019). Methyl acetyl ricinoleate as polyvinyl chloride plasticizer. Journal of Polymers and the Environment, 27(4), 703–709. [Google Scholar]
27. Tan, J., Zhang, S., Lu, T., Li, R., Zhong, T. et al. (2019). Design and synthesis of ethoxylated esters derived from waste frying oil as anti-ultraviolet and efficient primary plasticizers for poly(vinyl chloride). Journal of Cleaner Production, 229, 1274–1282. [Google Scholar]
28. Patil, S. S., Jena, H. M. (2021). Performance assessment of polyvinyl chloride films plasticized with Citrullus lanatus seed oil based novel plasticizer. Polymer Testing, 101, 107271. [Google Scholar]
29. Gao, C., Zhang, X., Sun, J., Yuan, Z., Han, S. et al. (2018). Poly(hexane succinate) plasticizer designed for poly(vinyl chloride) with a high efficiency, nontoxicity, and improved migration resistance. Journal of Applied Polymer Science, 135(25), 46388. [Google Scholar]
30. Subramanian, K., Vadivu, K. S., Subramaniyam, L., Kumar, M. D. (2022). Synthesis, characterization, and analysis of bioplasticizer derived from Hibiscus rosa-sinensis leaves and cinnamon bark for poly(vinyl chloride) films. Industrial Crops and Products, 182, 114933. [Google Scholar]
31. Ma, Y., Song, F., Hu, Y., Kong, Q., Liu, C. et al. (2020). Highly branched and nontoxic plasticizers based on natural cashew shell oil by a facile and sustainable way. Journal of Cleaner Production, 252, 119597. [Google Scholar]
Cite This Article
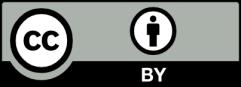
This work is licensed under a Creative Commons Attribution 4.0 International License , which permits unrestricted use, distribution, and reproduction in any medium, provided the original work is properly cited.