Open Access
REVIEW
Overview of Jute Fibre as Thermoplastic Matrix Polymer Reinforcement
1 Faculty of Engineering and Quantity Surveying, INTI International University, Nilai, Negeri Sembilan, 71800, Malaysia
2 Technical Department, Dyna Forming Engineering Technology (DFETECH) SDN. BHD., Seremban, Negeri Sembilan, 70300, Malaysia
3 Faculty of Mechanical and Automotive Engineering Technology, Universiti Malaysia Pahang Al-Sultan Abdullah (UMPSA), Pekan, Pahang, 26600, Malaysia
4 Automotive Engineering Center (AEC), Universiti Malaysia Pahang Al-Sultan Abdullah (UMPSA), Pekan, Pahang, 26600, Malaysia
5 Department of Mechanical Engineering, Universitas Negeri Semarang, Kampus Sekaran, Gunungpati, Semarang, 50229, Indonesia
6 Faculty of Manufacturing and Mechatronic Engineering Technology, Universiti Malaysia Pahang Al-Sultan Abdullah, Pekan, Pahang, 26600, Malaysia
7 Faculty of Health and Life Sciences, INTI International University, Nilai, 71800, Malaysia
8 Faculty of Mechanical and Manufacturing Engineering, Universiti Tun Hussein Onn Malaysia, Parit Raja, Batu Pahat, Johor, 86400, Malaysia
9 Faculty of Engineering, Universitas Tarumanagara, Jakarta Barat, 11440, Indonesia
10 Department of Chemical Engineering, Politeknik Negeri Lhokseumawe, Lhokseumawe, 24301, Indonesia
11 Department of Mechanical Engineering, Faculty of Engineering, Diponegoro University, Semarang, 50275, Indonesia
12 Department of Mathematics Education, Universitas Katolik Indonesia Santu Paulus Ruteng, Nusa Tenggara Timur, 8651, Indonesia
* Corresponding Authors: Tezara Cionita. Email: ; Januar Parlaungan Siregar. Email:
(This article belongs to the Special Issue: Natural Fibre Reinforced Polymer Composites: Processing, Manufacturing, Characterizations and Environmentally Friendly Applications)
Journal of Renewable Materials 2024, 12(3), 457-483. https://doi.org/10.32604/jrm.2024.045814
Received 08 September 2023; Accepted 07 December 2023; Issue published 11 April 2024
Abstract
Recent decades have seen a substantial increase in interest in research on natural fibres that is aligned with sustainable development goals (SDGs). Due to their renewable resources and biodegradability, natural fiber-reinforced composites have been investigated as a sustainable alternative to synthetic materials to reduce the usage of hazardous waste and environmental pollution. Among the natural fibre, jute fibre obtained from a bast plant has an increasing trend in the application, especially as a reinforcement material. Numerous research works have been performed on jute fibre with regard to reinforced thermoset and thermoplastic composites. Nevertheless, current demands on sustainable materials have required new developments in thermoplastic composites. In this paper, the author reviews jute plants as reinforcement materials for thermoplastic matrix polymers. This review provides an overview of the sustainability of jute plants as reinforcement material for thermoplastic matrix polymers. The overview on jute based thermoplastic composites focused on the thermal behavior and mechanical properties. Apart from physical, chemical, and mechanical properties, the study also covers the current and perspectives for future research challenges faced by the researchers on jute fibre reinforced thermoplastic composites.Keywords
Plastic waste is becoming a serious environmental problem [1,2]. The landfill is full and limited in space thus cannot meet the expectation of municipal solid waste that exponentially increases annually in high population areas. The main root of the environmental concerns relates to the over usage of conventional plastic [3,4]. In 2019, the production of plastic was estimated at around 368 million metric tonnes, which includes plastic material from thermoplastic and thermosets [5,6]. Based on the current trend, the world usage of plastic is expected to grow up to 380 million in 2020. The high demand for conventional plastic is due to its light, cheap, and durable features, making it the decisive choice for industrial and consumer products. In general, conventional plastic can be divided into two major groups, which are thermoset and thermoplastic. Current usage of both thermoset and thermoplastic are dominant in fields of agriculture (3.4%), electrical and electronic (4.1%), automotive (6.2%), building and construction (20.4%), packaging (39.6%), and others, specifically consumer and house products, furniture, sports, as well as health and safety (22.8%) [7,8].
The type of polymer can be determined by what happens to the material when it is heated. The ability to change shape is lost when the thermoset material has been cured. This happens because of the strength of the molecular chains in the thermoset material which are strongly bonded to each other. Thermosets have a 3D network that is bound together with covalent bonds and cannot melt through the reheating process [9]. In recent decades, thermoset matrix fibre-reinforced composites have been widely used in various industries such as automotive, aerospace, and renewable energy structures [10]. This happens because the thermoset material has excellent adhesion, good resistance to corrosion and heat. In addition, the thermoset matrix has higher strength and stiffness than metal materials [11,12]. This makes it possible to create lighter components with more efficient operating costs by weight reduction. One of the disadvantages of thermoset materials is that they cannot be recycled and reformed for use in other applications. Thermoplastics are polymeric materials that soften when heated and could harden when cooled. This means that thermoplastic materials can be recycled and reformed for use in other applications. This property is not available in thermoset materials [13–16]. Other differences between thermosets and thermoplastics are shown in Table 1.
Numerous research works aim to develop more advanced thermoset-based composites. Nevertheless, the thermoset plastic undergoes an irreversible process that does not permit it to be reshaped and reprocessed by heat and chemical solvent. Thus, recycling thermoset plastic is more challenging compared to thermoplastic. Also, thermosetting is known for possessing high brittleness and inability to repair [21,22]. Unlike thermoset plastic, thermoplastic polymer provides a better option for reducing plastic waste [23,24]. So far, the consumption of thermoplastic is approximately 90% of the total plastic usage around the globe. Thermoplastic matrix polymer has excellent resistance to impact loading than thermosetting resin. In general, there are many advantages of thermoplastic over thermosets as listed by the previous research work, such as shorter processing time, longer shelf-life and easier to be plasticised, low water absorption, stable glass transition temperature (Tg), high fatigue resistance, low coefficient of friction, high abrasion resistance, and recyclable [25,26].
Moreover, new biodegradable thermoplastic materials, such as soy-based resin, polylactic acid and starch-based resin, are environmental-friendly because they completely degrade after disposal [27–29]. At the same time, it is economical as it minimises energy consumption. However, the biggest challenge to applying the biodegradable factor is the high cost, requiring complicated processing. Biodegradable plastic needs to improve in terms of shelf-life, mechanical performance, and environmental impact due to different manufacturing processes of bioplastic. However, the constant progress on developing biodegradable products improves production techniques, lowering production costs for biodegradable material [30–32].
The introduction of fibre-reinforced material can modify both thermoset and thermoplastic matrix polymers. The role of fibre-reinforced material in a matrix polymer is to give the desired strength and modulus. Synthetic fibres such as glass, carbon and aramid have been used as reinforcement materials for thermosets and thermoplastics in the last decade. Nevertheless, synthetic fibre is notoriously known for causing environmental problems since it is hard to dispose of with no recycling options. Combining natural fibres and thermoplastic matrix polymer produces a material that fulfils a standard for sustainable materials [13,24,33]. At the same time, inexpensive and environmental-friendly plant fibre could hinder the pollution that is at a critical level nowadays. Plant fibre can be categorised based on different plant elements, such as leaf, bast, stem, bark, and seed. Generally, the plant fibres, for instance, jute, kenaf, coconut, bamboo, cotton, flax, abaca, hemp, and sisal, are broadly utilised because they are non-abrasive, renewable, biodegradable, and have high corrosion resistance, high stiffness, low density, and highly disposable recovery [34–36].
Plant fibre is extensively used as a reinforcement material by industries for various applications, especially automobile and construction industries. The demand for natural fibres worldwide increases every year according to the increasing usage of multiple applications [37,38]. In automotive and structural applications, plant fibre is less dense than synthetic fibre, reducing about 10% to 30% of the total weight percent. Furthermore, natural fibre consumes less energy for production, which means that they are environmentally friendly and can become alternative sources for petroleum-based products, minimising dependence on petroleum usage [39–41]. The aim of the paper is to review the most recent advancements in jute-reinforced thermoplastic composites. Jute fibres provide several benefits and interesting prospective uses when used as reinforcing materials for thermoplastic and thermoset polymer matrices. However, several specific difficulties must be researched and resolved to employ jute as reinforcement in matrix polymers, such as problems with moisture absorption, compatibility, and variability in fibre properties. Jute-reinforced composites have a lot of potentials, and future research will focus on how to optimise that potential and contribute to ecologically friendly and sustainable material solutions across a range of industries. The current state of jute-based composites today and their potential for the future are extensively and scientifically reviewed in this research.
The high demand for conventional plastic is due to its light, cheap, and durable features, making it a decisive choice. Jute is a widespread natural fibre used as reinforcement material and is known as the Golden Fibre due to its golden and silky shiny aesthetics. Jute is classified into the Sparrmanniaceae family and commonly cultivated in two species which are Corchorus olitorius (Tossa jute) and Corchorus capsularis (white jute). Jute is the second most important fibre after cotton [42–44].
Jute brings many benefits to mother nature, like ameliorating land fertility and producing large biomass per unit area of land. Jute fibre can be recognised based on several characteristics and features. It has a length in the range of 1.5 to 4.0 m and 20 micrometres in diameter. The inconsistent jute fibre size contributed to the uneven thickness of fibre cell walls, thus altering its strength. Jute fibre is strong against microorganisms but unconvincing counter to the chemical and photochemical attack. It also possesses high abrasion resistance that makes it suitable for machining the composite to produce different components [45–47].
Jute is included under the group of bast fibre. In Bangladesh and India, jute is an essential commodity that finds widespread application in packaging materials, industrial processes, and other commercial sectors [48,49]. Based on the data obtained from Food and Agriculture Organization (FAO), India and Bangladesh covered 98% of the world’s production of jute fibre in 2017 [50]. Bangladesh produced an average of 804,520 tonnes of jute in 2020 [51]. The high availability and simplicity of processing jute fibre are the main factors for the low cost of jute fibre. Jute fibre was obtained from the pith through a process known as retting. Traditionally, jute fibre has been used in many applications such as wall covers, lampshades, curtains, hessian cloth, ropes, gunny, shopping bags, floor mats and other decorative materials. In modern applications, jute fibre is widely used in thermoplastic composite and insulation material [51–53].
In regards to this, jute fibre was selected as a reinforcement material due to its harmless nature to the environment and possessed a biodegradable feature. Low density and high strength make it suitable as a reinforcement material for thermoplastic composite [54–56].
2.1 Chemical and Mechanical Properties of Jute Fibre
The detail of the chemical and mechanical properties of jute fibre is summarised in Table 2. Based on the chemical composition of jute fibre, it can be concluded that jute fibre is composed of α-cellulose, hemicellulose, lignin, and waxes. The chemical content of jute fibre and other natural fibre has various properties primarily influenced by geographic region, climatic harvesting method, soil condition and qualities of retting [57,58]. Jute has high cellulose content, and its cellulose chains are parallel to the fibre’s long axis. The tremendous cellulose content on jute fibre develops hydrophilic properties that initiate poor interface and vulnerable to moisture absorption. The moderate lignin content on jute fibre boosts its susceptibility to weather. Nevertheless, the appearance of moderate lignin on jute fibre promotes a brittle behaviour causing low extension at the break [59–61]. The tensile properties of jute fibre are comparable to other bast fibre types such as ramie, hemp, sisal, and flax. Jute fibre presents some of the special properties of jute-like high stiffness and light in weight [45,47,62]. From Table 2, the density of jute fibre is among the lowest in the group of bast fibre.
Several Sustainable Development Goals (SDGs) are aligned with the increasing incorporation of natural fibres as reinforcements in polymer composite materials, including jute, ramie, kenaf, banana, hemp, flax, sisal, and bamboo. Jute is the most utilized material because it has an incredibly high tensile strength and is the most possible from an economic perspective. Industries can promote SDG 12 (Responsible Consumption and generation) by reducing their environmental effect and waste generation by substituting these natural fibres for conventional ones in composites. Jute production also supports SDG 15 (Life on Land) by preserving soil fertility, stopping land degradation, and protecting biodiversity. It also supports SDG 9 (Industry, Innovation, and Infrastructure) by encouraging composite manufacturing and environmentally friendly infrastructure investment. Because it generates employment opportunities, particularly in rural areas, jute’s economic viability is related to SDG 8 (Decent Work and Economic Growth), which aims to alleviate poverty. Jute is an environmentally friendly alternative that can be used in polymer composites to promote a more just and sustainable world, advance technology, and fulfil the needs of the company [68–70]. The advantages of jute fibre are [71,72]:
• Jute fibre is biodegradable, recyclable, and eco-friendly.
• Jute fibre is the cheapest of the plant fibres because it is procured from the bast or skin of the plant’s stem.
• Jute fibre can grow in 4–6 months with a large amount of cellulose produced from the parenchyma of jute stems.
• Jute fibre has high tensile strength and low extensibility, better breathability of fabrics, and totally free of any element of narcotic or odour.
• Jute fibre has possessed good insulating and anti-static properties as well as low thermal conductivity and a moderate moisture regain.
2.2 Thermal Properties of Jute Fibre
The thermal degradation of jute fibre is one problem to overcome. It was about thermal properties. Without melting, jute straight away burns and chars when exposed to high temperatures. However, most of the thermoplastic processed temperature is about 200°C. Jute fibre will start to ignite at a temperature of 193°C [73]. Thus, the thermal degradation of jute fibre becomes unsafe after exceeding 250°C. This is due to the temperature limit of jute fibre to degrade is between 220°C to 260°C for hemicellulose, where lignin starts to decompose at 160°C and continues to degrade up to 400°C. Thus, it is challenging to maintain jute fibre from degrading when reinforced with the thermoplastic matrix polymer. The decomposition of lignin will cause deterioration in the mechanical properties of the composite drop if jute thermal degradation occurs at the melt processing temperature [74–76]. Nonetheless, based on thermogravimetric analysis (TGA) from previous work, it indicated jute fibre owns distinguished thermal stability than bamboo, kenaf, abaca or wood micro-fibres [77,78]. Jute fibre possesses high thermal stability due to the high content of cellulose and low ranges of lignin, fats, pectins and proteins. Additionally, jute is an excellent thermal insulator as it has a high specific heat capacity. Nevertheless, jute fibre will lose its strength when exposed to too much heat and sunlight [79–81].
2.3 Water Absorption of Jute Fibre
The disadvantages of jute fibre are also manifested by high water absorption, which causes deteriorating strength when wet, dimensional movement and biological degradation [82]. The increased moisture absorption subsequently produces a weak bonding on the composite since most of the thermoplastic matrix polymer such as PP, PE and PVC are non-polar and hydrophobic compounds [83]. As a result, jute fibre and thermoplastic matric polymer are not compatible, which causes several problems such as debonding or void, which can deteriorate the performance of the composite. On the other hand, natural fibre like jute typically has a higher moisture absorption than synthetic fibre. Therefore, jute fibre poses a significant threat when exposed to the environment, especially for outdoor applications. Unlike synthetic fibre, jute fibre contains a high cellulose molecule encompassing hydroxyl groups [84–86]. Functional groups like carbonyl, vinyl, hydroxyl, ketone, and others can be observed via FTIR spectroscopy. FTIR spectroscopy is used to analyse untreated and treated jute fabric and fibres [87]. This allows the changes in chemical compounds before and after chemical treatments to be investigated. Based on the FTIR, the existence of polar hydroxyl groups (-OH) on jute fibre can be determined. Table 3 summarises the transmittance value obtained from the previous study on jute fibre. FTIR confirms the hydroxyl group in jute fibre that causes high sorption, diffusion, and permeability coefficients [88].
3 Trend of Jute Fibre as Reinforcement Material
Jute is utilised predominantly in polymer matrices to enhance the mechanical properties of composites. Many kinds of research were already instigated to reinforce jute with thermoset and thermoplastic. The trend of jute fibre utilisation as reinforcement material is expected to increase in the future. High demand from the automotive industries to acquire low weight structural for fuel efficiency and energy saving urges more research on lingo-cellulose fibre [56,74,91]. Based on the literature survey, jute fibre has been used in various reinforcement forms, divided into the filler, short, long, and textile. The structure of fibre reinforcement is important in deciding the bulk properties of the final product [92]. The researcher investigated different types of support in various testing to determine mechanical and thermal properties. Each of the reinforcement forms influenced the properties of the composite in different ways. Diverse forms of reinforcement were prepared to match the thermoplastic resin characteristic, known to possess very high melting, viscosities and difficulties when performing impregnation [93].
Jute textile fabric is woven, non-woven, braid, knitting, mat, unidirectional and bi-directional. The textile fabric is made up of a long fibre which goes through various conventional textile processes. Among all textile fabrics, jute in woven form is observed at the highest frequency compared to other forms of reinforcement material. Several factors influence woven fabric selection, such as higher mechanical and physical properties, modest processing technique, and inexpensive cost. The woven fabric comprises more balanced properties than another reinforcement textile, such as unidirectional lamina [37,94].
Woven fabric reacted on both directions of longitudinal and horizontal due to the yarn’s appearance in weft and warp. Also, the woven fabric possesses significant mechanical performance in terms of tensile, flexural and impact loading that the non-woven fabric does not. The woven fabric keeps high strength due to the interlocking feature of the fibre’s weaving; different weaving patterns such as plain, twill, and basket influence composite performance [94]. Therefore, the composite made by several layers of woven fabric resulted in outstanding tensile resistance and energy absorption characteristics. The woven jute fabric reinforced with soy-based resin composite performed better than non-woven jute fabric. The mechanical properties of woven fabric reinforced with matrix polymer composite can be enhanced by optimising woven and laminated parameters covering fibre orientation and volume fraction, respectively [37]. The high cost of production has hindered the application of woven fabric since it involves multiple processes such as scotching, hackling, and spinning to turn whole raw fibre into yarn [95].
Nevertheless, the short fibre is more significant in terms of processability and cost. Short yarn is more versatile than long fibre since it can be processed using fabrication methods such as extrusion, injection, and compression without thermal degradation. Moreover, short fibre is known for anisotropy and easy dispersion [96,97]. Mechanical performance of short jute fibre composite depends on several factors such as mechanical and physical properties of jute, type of matrix polymer, aspect ratio, fibre orientation, and volume fraction [98].
To enhance the mechanical properties of short fibre, two important parameters of short fibre composites: dispersion and aspect ratio, are carefully optimised. The aspect ratio plays an important role in determining the properties of the short fibre composite. One of the reasons for altering the aspect ratio is the manufacturing method. The high viscosity of the matrix can cause fibre breakage during the manufacturing as the high shear stresses form the viscous polymer, affecting the final length distribution. Thus, to achieve a high level of stress transfer in the fibre, the fibre length (lf) must be exact to the critical distance (lc) [99,100]. On the other hand, a specific length degradation on fibre occurs due to the high processing temperature of the compounding process. In addition, the strength of short fibre composite is controlled via interfacial adhesion between fibre and matrix polymer while the fibre orientation controls the modulus. The variation of short jute fibre length alters the mechanical properties composite [101–103].
The experiment conducted by Bisaria et al. [104] displayed that the effect of short jute fibre reinforced with epoxy composite using four fibre lengths of 5, 10, 15 and 20 mm. The results showed that the maximum tensile and flexural properties were found for composites with a fibre length of 15 mm, while the maximum impact properties were found for composites with a fibre length of 20 mm.
4 Jute Reinforced Thermoplastic Polymers
Lignin-rich fibres such as jute (5%–26%) are more flexible and have a higher maximum deformation, while the cellulose content (61%–72%) in jute makes it harder, with a higher modulus of elasticity [105,106]. Jute has good mechanical properties that can be transferred to thermoplastic polymers by incorporation in composites. This results in improving the physical, mechanical, and thermal properties of the material while decreasing production costs and being environmentally friendly. Compared with thermosets, composites made of thermoplastic materials usually have a longer shelf life, greater strain to failure, fast consolidation, excellent chemical resistance, better damping characteristics, low noise emission, repairable and recyclable [106,107]. Some advantages associated with the use of jute as reinforcement in thermoplastics are biodegradability and high specific properties. jute is one of the superior natural fibre materials due to its low cost, high level of production, low density, and high specific strength making it suitable as a reinforcement material for thermoplastic composite [108,109].
Jute fibre has been reinforced with many thermoplastic matrix polymers such as poly(butylene succinate) (PBS), polyvinyl chloride (PVC), starch resin, light density polyethene (LDPE), high-density polyethene (HDPE), polyethene terephthalate (PET), polypropylene (PP) soy-based resin and poly-lactic acid (PLA). As shown in Fig. 1, thermoplastic can be divided into two majors: renewable and non-renewable.
Figure 1: Type of thermoplastic
The selection of different types of thermoplastics depended on several criteria:
• Desired application
• Environmental condition
• Budget and economic aspect
• Process of fabrication
Each of the thermoset matrix polymers has identical mechanical, thermal, and physical properties. Table 4 summarises the mechanical and thermal properties of each thermoplastic composite.
Based on the literature, the researcher primarily focuses on the PP and PLA matrix. The PP matrix polymer became the favourite amongst researchers because it has some excellent character for composite fabrication. It also possesses outstanding properties such as low density, good abrasion, good surface hardness, scratch resistance and significant electrical properties [122]. Besides that, the PP is effective regarding price, recycling behaviour and thermal stability [107]. Furthermore, the polypropylene can be blended with another thermoplastic polymer. The high biodegradability of PLA is the main feature since it’s made from plants such as corn and rice. PLA completely degrades when exposed to the environment and only produces H2O and CO2 while degrading, non-toxic and safe for people [123].
From the collected literature, the standard method that has been utilised includes compression moulding, injection moulding and hot press. The selection of the fabrication method highly depended on the reinforcement phase. In most cases, the compression moulding was selected to manufacture jute textile reinforcement with a thermoplastic matrix. In the compression moulding, jute fibre was mixed with matrix and then pressed with a heated plate with a temperature of about 200°C and pressure of 5 MPa [124]. Moreover, the fabrication method also depended on the production scale. The suitable fabrication method for larger-scale production is injection moulding, while other composite fabrication is less appropriate [125,126]. Despite that, the pultrusion can undergo a mass-production scale since it can maintain continuous production of the straight profile with constant cross-sections [127].
In the case of filler and short fibre of jute reinforced thermoplastic composites, most of the fabrication method applied is a melt mixing or solution mixing followed by injection moulding or compression moulding. Fibre the content is usually limited to 40 wt.% in both melt mixing and solution mixing. This is due to the fibre content above 40 wt.% is hard to incorporate and produces a lower mechanical performance of the composite [128,129].
4.1 Jute Reinforced Polypropylene (PP) Composite
PP has some noteworthy properties such as low density, good surface hardness, abrasion resistance, and excellent electric properties [84,86]. The researcher commonly performed jute reinforced PP in previous works to investigate the mechanical properties, thermal behaviour, and effect of surface modification [130,131]. From an earlier study on durability and interfacial evaluation of modified jute-polypropylene (PP) composites using micromechanical test and acoustic emission. Park et al. [130,131] proved that with better interfacial properties of jute fibre and PP polymer, the better the mechanical properties of the composite. A study of creep and dynamic mechanical behaviour of PP–jute composites were investigated by Acha et al. [132], who discovered that creep behaviour decreases when jute content in the composite increases, but only marginal for fibre concentrations more prominent than 25 wt.%. Jute fibre with different weight content has been reinforced with PP composite. In the study by Hassan et al. [133], it was shown that the short jute fibre with 10 wt.% Content achieved high tensile strength in PP composite. Jute fibre content for 20% and 30% decreased the tensile strength of the composite. A similar result was obtained from the experiment conducted by Rahman et al. [134,135]. The optimum fibre content is varied for the different types of jute reinforcement. Dieu et al. [136] performed the mechanical testing of jute cloth reinforced PP composite with 30 wt.%, 40 wt.%, 45 wt.%, 50 wt.%, 60 wt.%, 65 wt.% of jute fibre content. The result indicated jute fibre content is optimum at 45 wt.% content. Table 5 summarises the previous work on the mechanical properties of jute fibre reinforced PP composites.
4.2 Jute Reinforced Polyethylene (PE) Composites
The application of polyethene matrix polymer is limited compared to polypropylene. Polyethene is often classified according to density and branching. The mechanical properties are varied depending on the type of branching, crystal structure, and molecular weight. High-density polyethene (HDPE) is stiff, strong, and has a high melting temperature. It is one of the most widely used plastics in many applications such as bottles, film, and packaging. The preparation of composite polymer by mixing the HDPE with inorganic fillers is very interesting. HDPE is lightweight yet super strong that makes it ideal for packaging and manufacturing products. Plus, HDPE is impact-resistant and weather-resistant, which makes it last longer. It is also safe against insects, rot, and any chemical. HDPE is safe for consumer use since it produces no harmful emissions during production or usage by consumers. Jute fibre has been used as reinforcement in previous works [56,143].
Hossain et al. utilised jute to reinforce recycled HDPE matrix polymer. The weight content of jute fibre used is 0 wt.%, 5 wt.%, 10 wt.%, 15 wt.%, 20 wt.% and 25 wt.%. The result of tensile strength obtained for different weight content of jute from 0–25 wt.% Jute-mat fabric produces a significant reinforcement effect initially in the used HDPE composite. The maximum value of the tensile strength of recycled HDPE/jute-mat composites is found to be 33.12 MPa for 20 wt.%. Jute mat fibre composites. The tensile strength drops when the weight content of jute fibre exceeds 20 wt.% [144]. Unlike HDPE, Low-Density Polyethylene (LDPE) is produced by polymerization of ethylene gas at higher pressure and temperature. The LDPE is essentially low density, impact-resistant, and waterproof, which are similar to HDPE properties. Besides that, the LDPE are relatively cheap, with exceptional electrical insulation properties, a high level of toughness, and high chemical resistance [145]. Nevertheless, the usage of LDPE is safe for the human body, and it does not extract toxic substances in the environment. In addition, the LDPE can stand a temperature of 80°C to 95°C in a short time. However, LDPE is weak against gasses, so that it is ineffective for packing the products sensitive to oxidation. Jahan et al. [146] performed an investigation to compare physical and elastic properties under the condition of increasing weight content and duration of soaking time between jute/LDPE and glass fibre/LDPE composite. Four types of weight content were used to prepare ute/LDPE and glass fibre/LDPE composite, including 35 wt.%, 45 wt.%, 56 wt.%, and 66 wt.%. fibre content. Jute/LDPE composite was reported to decrease than glass fibre/LDPE composite slowly. The finding obtained from the experiment revealed that jute/LDPE had low tensile strength than glass fibre/LDPE composite in all fibre weight content except for 45 wt.%. A similar pattern was observed on the flexural strength of jute/LDPE composite. The tensile and flexural strength of jute/LDPE decreases when fibre weight content increases more than 45 wt.%. Jute/LDPE possesses better young modulus, elongation, and flexural strain than glass fibre/LDPE composite, indicating less stiffness. Unlikely, jute/LDPE composite has a higher percentage of water absorption than the glass fibre/LDPE composite.
4.3 Jute Reinforced Biopolymer
As an alternative to petroleum-based polymers, jute fibre has been reinforced with a biopolymer as matrix. Biopolymer is one type of polymer that mainly consists of several types of carbon-containing repeating units that are used or derived from living organisms. Biopolymers include natural polymers, bio-based polymers, also known as bioplastics, which are extracted from biomass (i.e., natural polymers) or polymerized from bio-based monomers [147,148]. Most biopolymer matrix originated from the biological system or chemically processed using sugar, starch, natural fats, and oils [149]. As it originated from natural resources, the biopolymer degrades when exposed to the sun and air over a short period [150]. The popular type of biopolymer as a matrix of composite is PLA. The usage of PLA can decrease the demand for petroleum-based thermoplastic such as PP, PE, and PVC [151].
PLA originated from renewable and biodegradable agricultural resources. There are two main methods for producing the PLA: through ring-opening of polymerization of lactide and direct polycondensation of lactic acid monomers. The PLA is an interesting matrix polymer since it offers high strength, thermal plasticity, good aesthetics, and bio-compatibility. The weakness of PLA matrix polymer is caused by its brittleness which limits its application [149]. Numerous findings have been proposed by the researcher from the investigation of jute-reinforced PLA composite. Hu et al. [152] indicated that during the ageing process of PLA jute composites, the main factors for defect are complete structure relaxation, microcracks, pores, and delamination. Memon et al. [153] indicated that the range between 185°C–195°C is the optimum compression moulding temperature for jute/PLA unidirectional composite. For PLA jute composite with 40% fibre by weight, the result showed that stiffness and tensile strength are doubled compared to pure PLA. They suggested that the heating temperature should be between 210°C and 220°C to yield optimum results for tensile strength [154].
Another type of biopolymer as matrix also has been selected as a matrix phase for jute fibre, such as thermoplastic starch and soy-based resin. Sharma et al. [155] prepared a composite based on potato starch and jute fibre. The sample was prepared by different parameters such as fibre size, meshing or without meshing and with propane-1,2,3-triol or without propane-1,2,3-triol plasticiser. The result confirms that the composite made by the 5 mm jute with propane-1,2,3-triol have some excellent mechanical properties than the composite without propane-1,2,3-triol. Nevertheless, the starch contains propane-1,2,3-triol combined with thick mesh have a poor surface property compared to the composite made up of the original size of jute fibre. Behera et al. [156] formulated a soy-based resin from a different weight percentage of glyoxal such as 1 wt.%, 5 wt.%, 10 wt.%, 15 wt.% and 20 wt.%. The glyoxal is then combined with 10 wt.% of glycerol to acquire soymilk and stirred for 30 min to obtain soy resin. The optimized soy-based resin is made up of 10 wt.%. Glyoxal and 10% glycerol was selected, then reinforced with jute fibre in the form of non-woven and woven fabric with varying content of 40 wt.%, 50 wt.%, 60 wt.%, 70 wt.%, and 80 wt.% The mechanical properties result showed that non-woven jute reinforced soy-based resin with a content of 60 wt.% owned the highest mechanical properties. Table 6 represents the data for the type of reinforcement and mechanical properties of jute reinforced biopolymer. Some environmental issues, such as waste generation, build-up in disposal, and low reproducibility, dominate when many non-biodegradable polymers are used. The use of biopolymers is one solution to these problems. Compared with the petroleum-based polymer, the bio-based polymer matrix has a good life cycle. The increasing environmental awareness has resulted in increased demand for biopolymers. The global biopolymer market is predicted to spread 2.7 million MT (metric tons) by 2023 [157].
4.4 Jute Reinforced Biodegradable Polymer
A biodegradable polymer is one that degrades due to the action of living organisms such as microbes and fungi. A bioplastic or biopolymer can be defined as a polymer that is manufactured into a commercial product from a natural source or renewable resource. A bioplastic can be biodegradable, but a biodegradable plastic does not mean the material was derived fully or in part from a biological source [162–164]. For example, polymers such as polycaprolactone (PCL) and poly(butylene succinate) (PBS) are biodegradable but petroleum based [165,166]. PBS is a white crystalline biodegradable polymer formed through the polymerisation of succinic acid and butanediol. With a melting point around 90°C–120°C, PBS is feasible for further processing various other products with better capabilities. Therefore, jute fibre and PBS are suitable to form composites for their excellent properties and their processing temperature compatibility [167–169]. Jute fibre reinforced PBS matrix polymer test was performed by Liu et al. [170].
The test was performed to investigate the effect of surface modification on jute fibre on the mechanical properties of the composite. Jute/PBS composite had undergone tensile testing and flexural testing with different jute content of 10 wt.%, 20 wt.% and 30 wt.%. The result obtained showed that the increase in fibre content up to 20 wt.%, increased the mechanical properties but decreased or nearly remain constant when fibre content was more than 20 wt.%. Another experiment conducted by Liu et al. worked on jute reinforced PBS composite biodegradability. A similar weight content was used as in the previous research. The fibre with less weight content, about 10 wt.%, has higher weight loss than the composite with more weight fibre content. The 10 wt.% jute/PBS composite experiment resulted in a weight loss of 62.5% after 180 days [170].
The existing physical properties of PBS were changed slightly due to the addition of other materials such as reinforcement, additive or filler. The physical properties of jute fibre reinforced PBS composites increase water absorption because the fibre content increases. PBS reinforced with jute fibre improved tensile strength, tensile modulus, flexural strength, and flexural modulus by 517.9%, 3529.8%, 302.6%, and 1949.1%, respectively. The mechanical properties of the composite were highest when using jute fibre content up to 50% by weight [166].
5 Perspectives for Future Research
When utilized as reinforcing materials for thermoplastic and thermoset matrix polymers, jute fibers provide several advantages as well as attractive prospects for application. Jute fiber processing and treatment, fiber form and size, and various fabrication procedures may be the subject of future research on jute fiber used as reinforcement for thermoplastic matrix polymers. This is necessary because jute fibers generally have issues with moisture absorption, compatibility, and variability of fiber qualities, which can significantly impact the ultimate properties of the resulting composite material [171].
Based on the literature survey, the jute fiber has been used in a variety of reinforcement form particularly divided into the filler, short, long and textile. The form of fiber reinforcement is important in deciding the bulk properties of the final product. Jute fiber is commercially available in all forms of reinforcement such as filler, short [97,104], long [171,172] and textile [159,173], as it also has been utilized by researcher in previous work. Different types of reinforcement have been investigated by the researcher in various testing to determine mechanical and thermal properties. Each of the reinforcement form influenced the properties of the composite in different ways. Diverse forms of reinforcement were prepared to match the thermoplastic resin characteristic which are known to possess very high melt, viscosities and difficulties when performing impregnation [153]. The textile fabric is made up of a long fiber which goes through a various conventional textile process. Among all textile fabric, the jute in woven form is observed at highest frequency compared to other forms of reinforcement material. Several factors that influence the selection of woven fabric such as higher mechanical and physical properties, modest processing technique, and inexpensive cost [174]. The woven fabric possesses significant mechanical performance in terms of tensile, flexural and impact loading that the non-woven fabric does not. The woven fabric possesses high strength due to the interlocking feature from the weaving of the fiber. Different weaving pattern such as plain, twill, and basket are influencing the composite performance [175].
Therefore, the composite made by several layers of woven fabric resulted in outstanding tensile resistance and energy absorption characteristic. As demonstrated by Behera, the woven jute fabric reinforced with soy-based resin composite performed better than non-woven jute fabric. The mechanical properties of woven fabric reinforced with matrix polymer composite can be enhanced through optimizing woven parameter and laminated parameter that cover fiber orientation and volume fraction, respectively. The application of woven fabric has been hindered by high cost of production since it involves multiple processes such as scotching, hackling and spinning to turn raw whole fiber to yarn [156].
Nevertheless, the short fiber is more significant in terms of processability and cost. Short fiber is more versatile than the long fiber since it can be processed using fabrication method such as extrusion, injection, and compression without thermal degradation. Moreover, short fiber is known for anisotropy and easy dispersion [170]. Mechanical performance of short jute fiber composite, depends on several factors such as mechanical and physical properties of jute, type of matrix polymer, aspect ratio, fiber orientation, and volume fraction [176]. To enhance the mechanical properties of short fiber, two important parameters of short fiber composites which are dispersion and aspect ratio are carefully optimized. The aspect ratio is an important role in determining the properties of the short fiber composite. One of the reasons for altering the aspect ratio is the manufacturing method. High viscous of the matrix can cause fiber breakage during the manufacturing as the high shear stresses developed to form the viscous polymer which affects the final length distribution. Thus, in order to achieve a high level of stress transfer in the fiber, the fiber length (lf) must be considered to be exact to the critical length (lc) [176].
On the other hand, the certain length degradation on fiber takes place due to the high processing temperature of compounding process. In addition, the strength of short fiber composite is controlled via interfacial adhesion between fiber and matrix polymer while the modulus is controlled by the fiber orientation. The variation of short jute fiber length alters the mechanical properties composite [140]. Experiments conducted by Rashed et al. [140] showed that the effect of short hemp fibers reinforced with PP composites using three fiber lengths of 1, 2, and 4 mm. The best results were obtained in specimens with a fiber length of 2 mm. This happens because this specimen has tensile strength compared to other specimens. When the fiber used has a fiber length of less than 2 mm, the tensile strength of the composite is lower due to load transfer inefficiency. The use of jute fibers with a length that exceeds 3 mm also results in a decrease in tensile strength as the fibers become incompatible with the matrix, resulting in improper bonding between the fibers and the matrix. In addition, entanglement occurs which reduces strength [140].
5.2 Jute Fiber Processing and Treatment
The main purpose of surface treatment on jute fiber is to improve or change its mechanical and chemical properties. Jute fiber as well as other natural fibers, they suffer from the hydrophilic nature that contribute to poor adhesion between fiber and polymer matrix. The compatibility issue between fiber and mechanical properties reduced their physical and mechanical properties. There were numerous surface treatments that were applied by researchers in previous works on jute fiber, which were categorized into two groups, namely physical and chemical treatments. Both physical and chemical surface treatments have their own advantages and disadvantages. Physical treatment is a dry method that produces less air, water and land pollution compared to wet chemistry method [117,177,178]. The common chemical treatment used by researcher and industry for natural fiber consisted of alkaline treatment [87,97,179,180], silane coupling agent, permanganate, and peroxide [121]. Meanwhile, the popular physical treatment includes corona discharge, electron beam treatment, thermal treatment Ultra Violet (UV) and oxygen plasma [143]. The mechanical properties of jute fibre that is treated via physical and chemical treatment have mainly depended on the type of treatment and amount of treatment agent [50].
5.3 Fabrication Methods of Jute Fiber Reinforced Composite
To ensure the optimal dispersion, orientation, and aspect ratio of the jute fiber in the composite for the particular application, the fabrication procedure must be carefully determined. The final composite design, size and shape, raw material qualities, process speed, and total cost are all factors to consider when choosing a fabrication method. Moisture, fiber type, fiber content, and fiber orientation are all factors that influence the fabrication of jute fiber-reinforced composite [69,171,181]. A high aspect ratio, as well as a uniform distribution of jute fibers in the polymer matrix, are necessary to generate excellent mechanical properties. Compression molding, resin transfer, injection, extrusion, molding, hand lay-up, pultrusion, spray coating, and filament winding methods are some of the fabrication techniques typically utilized in jute fiber-reinforced composite fabrication. These methods have been developed over years of industry experience and research. Furthermore, researchers have made numerous adjustments to develop cost-effective and defect-free jute fiber-reinforced composites [171,182]. Currently, hot compression and hand lay-up have been the most prevalent methods for producing thermoplastic and thermoset plastic composites [171].
5.4 Application of Jute Fiber Reinforced Thermoplastic Matrix Polymer Composites
Green composites, such as jute fiber-reinforced composites, are widely sought after in the aerospace and automotive sectors. This is mostly owing to its favorable characteristics, including biodegradability, improved strength and stiffness-density ratio, lightweight nature, high dependability and durability, cost-effectiveness, and superior physical features [171,183,184]. The automobile industry has found several applications for jute fiber-reinforced composites, such as the utilization of these composites in door panel components, seatbacks, trunk liners, headliner materials, dashboards, car panels, and the front hood of off-road vehicles, specifically buggies [185,186]. There is a growing interest within certain sectors of the aerospace industry to enhance the utilization of thermoplastics in composite materials, leading to a progressive expansion in the range of applications. Thermoplastics offer a range of significant benefits in comparison to thermosets when employed in composite materials, notably enhanced impact resistance, increased fracture toughness, and elevated operating temperature capabilities. Certain thermoplastics possess the desirable characteristics of transparency, toughness, and impact resistance, rendering them well-suited for application in various components of aircraft such as windows, tails, wings, fuselages, electronics racks for helicopter, aircraft wing boxes, aircraft materials and canopies [69,187]. The utilization of jute fiber-reinforced composites in automobiles and aircraft contributes to weight reduction, hence facilitating a decrease in fuel consumption and enhancement of overall performance [69,187].
The utilization of jute fibers as a reinforcing component in composites featuring a thermoplastic polymer matrix has novel prospects for applications within the realm of structural materials for building and construction materials [188]. Jute composites have the potential to serve as a highly cost-effective material within the building and construction sector. Furthermore, these composite materials exhibit favorable characteristics such as high impact resistance, corrosion resistance, thermal and acoustic insulation properties, making them highly suitable for utilization in the construction industry as perfect building materials. The use of jute fiber-reinforced thermoplastic matrix polymer composites in building materials could result in panels for false ceilings and partitions, as well as walls, floors, window and door frames, roof tiles and prefabricated or mobile buildings that could be utilized in the event of a natural disaster like a hurricane, earthquake, flood, etc. Furthermore, the utilization of jute fiber-reinforced thermoplastic matrix polymer composites extends to several domestic applications, including but not limited to doors, chairs, lampshades, roofing, luggage, tables, and bathtub units. Jute has the potential to serve as a viable alternative to wood in the construction of interior spaces [188].
Numerous research works have been performed on jute fibre with regard to reinforced thermoset and thermoplastic composites. Nevertheless, current demands on sustainable materials have required new developments in thermoplastic composites. This review provides an overview of the sustainable of jute plants as reinforcement material for thermoplastic matrix polymers. The overview on jute based thermoplastic composites focused on the thermal behavior and mechanical properties. Apart from physical, chemical, and mechanical properties, the study also covers the current and perspectives for future research challenges faced by the researchers on jute fibre reinforced thermoplastic composites. The use of jute fibre-reinforced thermoplastic in the filler, short fibre, long fibre, and textile has produced a variety of results. The woven fabric possesses significant mechanical performance in terms of tensile, flexural and impact loading that the non-woven fabric does not. The woven fabric possesses high strength due to the interlocking feature of the weaving of the fiber. The variation of short jute fiber length alters the mechanical properties of the composite. The use of jute fiber with the right length, will improve the mechanical properties of the composite material.
It is clear from the overview that thermoplastics reinforced with jute fibre have excellent mechanical properties, such as high tensile strength, stiffness, and strong resistance to impacts. In a variety of composite products from many industries, including those in automotive, building and construction, aerospace, furniture, and sports equipment, jute fibre can be used for the reinforcement of polymer composites. To put it briefly, it is important to support and conduct thorough research on jute fibre-reinforced composites and hybrids in order to advance the development of numerous existing goods and broaden the uses for jute fibre. Natural fibres like jute have some drawbacks when compared to synthetic fibres, such as poor matrix-fibre adhesion, high water absorption, and a highly polar nature because of the presence of hydroxyl groups (-OH) or hydrophilic groups. Jute fiber processing and treatment, fiber form and size, and various fabrication procedures may be the subject of future research on jute fiber used as reinforcement for thermoplastic matrix polymers. This is necessary because jute fibers generally have issues with moisture absorption, compatibility, and variability of fiber qualities, which can significantly impact the ultimate properties of the resulting composite material.
Acknowledgement: The authors would like to express appreciation to INTI International University for providing financing through the publication grant 2023.
Funding Statement: The authors received no specific funding for this study.
Author Contributions: T.C.: conceptualization, supervision; M.H.M.H.: writing—original draft, data collection; J.P.S.: writing—original draft and data collection; D.F.F.: formal analysis, resource; R.J.: formal analysis, collect data; W.L.S.: writing—review and editing, analysis; J.J.: data curation, writing—review and editing; A.P.I.: data curation, visualization; T.R.: methodology, formal analysis; R.I.: formal analysis, visualization; A.P.B.: visualization, data curation; E.J.: data curation, visualization. All authors have read and agreed to the published version of the manuscript.
Availability of Data and Materials: Data are contained within the article.
Conflicts of Interest: The authors declare that they have no conflicts of interest to report regarding the present study.
References
1. Huang, S., Wang, H., Ahmad, W., Ahmad, A., Ivanovich Vatin, N. et al. (2022). Plastic waste management strategies and their environmental aspects: A scientometric analysis and comprehensive review. International Journal of Environmental Research and Public Health, 19(8), 4556. [Google Scholar] [PubMed]
2. Chen, Z., Wei, W., Ni, B. J., Chen, H. (2022). Plastic wastes derived carbon materials for green energy and sustainable environmental applications. Environmental Functional Materials, 1(1), 34–48. [Google Scholar]
3. Ng, C. H., Mistoh, M. A., Teo, S. H., Galassi, A., Ibrahim, A. et al. (2023). Plastic waste and microplastic issues in Southeast Asia. Frontiers in Environmental Science, 11, 1142071. [Google Scholar]
4. Cubas, A. L. V., Moecke, E. H. S., Provin, A. P., Dutra, A. R. A., Machado, M. M. et al. (2023). The impacts of plastic waste from personal protective equipment used during the COVID-19 pandemic. Polymers, 15(15), 3151. [Google Scholar] [PubMed]
5. Bantu, T. R., Kakara, M., Veeravilli, S., Ginjala, V. R. (2023). Impact of single use plastic on the environment due to COVID-19 pandemic. AIP Conference Proceedings, 2673(1), 050001. [Google Scholar]
6. Chen, X., Wang, Y., Zhang, L. (2021). Recent progress in the chemical upcycling of plastic wastes. ChemSusChem, 14(19), 4137–4151. [Google Scholar] [PubMed]
7. Moshood, T. D., Nawanir, G., Mahmud, F., Mohamad, F., Ahmad, M. H. et al. (2022). Biodegradable plastic applications towards sustainability: A recent innovations in the green product. Cleaner Engineering and Technology, 6, 100404. [Google Scholar]
8. Europe, P. (2020). Plastics-the facts 2020. PlasticEurope, 1, 1–64. [Google Scholar]
9. Rashid, M. A., Liu, W., Wei, Y., Jiang, Q. (2022). Review of intrinsically recyclable biobased epoxy thermosets enabled by dynamic chemical bonds. Polymer-Plastics Technology and Materials, 61(16), 1740–1782. [Google Scholar]
10. Karim, M. A., Abdullah, M. Z., Deifalla, A. F., Azab, M., Waqar, A. (2023). An assessment of the processing parameters and application of fibre-reinforced polymers (FRPs) in the petroleum and natural gas industries: A review. Results in Engineering, 18, 101091. [Google Scholar]
11. Aliyeva, N., Sas, H. S., Okan, B. S. (2021). Recent developments on the overmolding process for the fabrication of thermoset and thermoplastic composites by the integration of nano/micron-scale reinforcements. Composites Part A: Applied Science and Manufacturing, 149, 106525. [Google Scholar]
12. Falzon, B. G., Pierce, R. S. (2020). Thermosetting composite materials in aerostructures. In: Pantelakis, S., Tserpes, K. (Eds.Revolutionizing aircraft materials and processes. Cham: Springer. [Google Scholar]
13. Kazemi, M., Kabir, S. F., Fini, E. H. (2021). State of the art in recycling waste thermoplastics and thermosets and their applications in construction. Resources, Conservation and Recycling, 174, 105776. [Google Scholar]
14. Desidery, L., Lanotte, M. (2022). Polymers and plastics: Types, properties, and manufacturing. In: Plastic waste for sustainable asphalt roads. UK: Elsevier, Woodhead Publishing. [Google Scholar]
15. Grigore, M. E. (2017). Methods of recycling, properties and applications of recycled thermoplastic polymers. Recycling, 2(4), 24. [Google Scholar]
16. Winne, J. M., Leibler, L., Du Prez, F. E. (2019). Dynamic covalent chemistry in polymer networks: A mechanistic perspective. Polymer Chemistry, 10(45), 6091–6108. [Google Scholar]
17. Reis, J. P., de Moura, M., Samborski, S. (2020). Thermoplastic composites and their promising applications in joining and repair composites structures: A review. Materials, 13(24), 5832. [Google Scholar] [PubMed]
18. Sudhin, A. U., Remanan, M., Ajeesh, G., Jayanarayanan, K. (2020). Comparison of properties of carbon fiber reinforced thermoplastic and thermosetting composites for aerospace applications. Materials Today: Proceedings, 24, 453–462. [Google Scholar]
19. Bîrcă, A., Gherasim, O., Grumezescu, V., Grumezescu, A. M. (2019). Introduction in thermoplastic and thermosetting polymers. In: Materials for biomedical engineering, pp. 1–28. UK: Elsevier. [Google Scholar]
20. Radzi, A. M., Zaki, S. A., Hassan, M. Z., Ilyas, R. A., Jamaludin, K. R. et al. (2022). Bamboo-fiber-reinforced thermoset and thermoplastic polymer composites: A review of properties, fabrication, and potential applications. Polymers, 14(7), 1387. [Google Scholar] [PubMed]
21. Wang, S., Shen, Y., Du, G., Jiang, S., Liu, S. et al. (2023). Novel melamine-based engineering thermosets: Facile synthesis, extraordinary thermostability, high strength and toughness. Chemical Engineering Journal, 461, 141886. [Google Scholar]
22. Sarath Kumar, P., Jayanarayanan, K., Balachandran, M. (2022). Performance comparison of carbon fiber reinforced polyaryletherketone and epoxy composites: Mechanical properties, failure modes, cryo-thermal behavior, and finite element analysis. Journal of Applied Polymer Science, 139(29), e52494. [Google Scholar]
23. Evode, N., Qamar, S. A., Bilal, M., Barceló, D., Iqbal, H. M. N. (2021). Plastic waste and its management strategies for environmental sustainability. Case Studies in Chemical and Environmental Engineering, 4, 100142. [Google Scholar]
24. Oladele, I. O., Okoro, C. J., Taiwo, A. S., Onuh, L. N., Agbeboh, N. I. et al. (2023). Modern trends in recycling waste thermoplastics and their prospective applications: A review. Journal of Composites Science, 7(5), 198. [Google Scholar]
25. Chauhan, V., Kärki, T., Varis, J. (2022). Review of natural fiber-reinforced engineering plastic composites, their applications in the transportation sector and processing techniques. Journal of Thermoplastic Composite Materials, 35(8), 1169–1209. [Google Scholar]
26. Samir, A., Ashour, F. H., Hakim, A. A. A., Bassyouni, M. (2022). Recent advances in biodegradable polymers for sustainable applications. npj Materials Degradation, 6(1), 68. [Google Scholar]
27. Abdur Rahman, M., Haque, S., Athikesavan, M. M., Kamaludeen, M. B. (2023). A review of environmental friendly green composites: Production methods, current progresses, and challenges. Environmental Science and Pollution Research, 30(7), 16905–16929. [Google Scholar] [PubMed]
28. Mann, G. S., Singh, L. P., Kumar, P., Singh, S. (2020). Green composites: A review of processing technologies and recent applications. Journal of Thermoplastic Composite Materials, 33(8), 1145–1171. [Google Scholar]
29. Balakrishnan, P., Gopi, S. (2021). Processing of advanced green nanomaterials. In: Advanced green materials, pp. 15–30. UK: Woodhead Publishing. [Google Scholar]
30. Ncube, L. K., Ude, A. U., Ogunmuyiwa, E. N., Zulkifli, R., Beas, I. N. (2020). Environmental impact of food packaging materials: A review of contemporary development from conventional plastics to polylactic acid based materials. Materials, 13(21), 4994. [Google Scholar] [PubMed]
31. Shlush, E., Davidovich-Pinhas, M. (2022). Bioplastics for food packaging. Trends in Food Science & Technology, 125, 66–80. [Google Scholar]
32. Ibrahim, N. I., Shahar, F. S., Sultan, M. T. H., Shah, A. U. M., Safri, S. N. A. et al. (2021). Overview of bioplastic introduction and its applications in product packaging. Coatings, 11(11), 1423. [Google Scholar]
33. Begum, S., Fawzia, S., Hashmi, M. S. J. (2020). Polymer matrix composite with natural and synthetic fibres. Advances in Materials and Processing Technologies, 6(3), 547–564. [Google Scholar]
34. Akhil, U. V., Radhika, N., Saleh, B., Aravind Krishna, S., Noble, N. et al. (2023). A comprehensive review on plant-based natural fiber reinforced polymer composites: Fabrication, properties, and applications. Polymer Composites, 44(5), 2598–2633. [Google Scholar]
35. Jino, L., Prasad, V. D., Eswar, M. A., Manoj, E., Jacob, A. et al. (2023). Review on natural fibre composites reinforced with nanoparticles. Materials Today: Proceedings. https://doi.org/10.1016/j.matpr.2023.01.126 [Google Scholar] [CrossRef]
36. Elfaleh, I., Abbassi, F., Habibi, M., Ahmad, F., Guedri, M. et al. (2023). A comprehensive review of natural fibers and their composites: An eco-friendly alternative to conventional materials. Results in Engineering, 19, 101271. [Google Scholar]
37. Tezara, C., Zalinawati, M., Siregar, J. P., Jaafar, J., Hamdan, M. H. M. et al. (2021). Effect of stacking sequences, fabric orientations, and chemical treatment on the mechanical properties of hybrid woven jute-ramie composites. International Journal of Precision Engineering and Manufacturing-Green Technology, 9, 273–285. [Google Scholar]
38. Kumar, R., Ul Haq, M. I., Raina, A., Anand, A. (2019). Industrial applications of natural fibre-reinforced polymer composites-challenges and opportunities. International Journal of Sustainable Engineering, 12(3), 212–220. [Google Scholar]
39. Nurazzi, N. M., Asyraf, M. R. M., Fatimah Athiyah, S., Shazleen, S. S., Rafiqah, S. A. et al. (2021). A review on mechanical performance of hybrid natural fiber polymer composites for structural applications. Polymers, 13(13), 2170. [Google Scholar] [PubMed]
40. Irawan, A. P., Anggarina, P. T., Utama, D. W., Najid, N., Abdullah, M. Z. et al. (2022). An experimental investigation into mechanical and thermal properties of hybrid woven rattan/glass-fiber-reinforced epoxy composites. Polymers, 14(24), 5562. [Google Scholar] [PubMed]
41. Karim, M. R. A., Tahir, D., Haq, E. U., Hussain, A., Malik, M. S. (2020). Natural fibres as promising environmental-friendly reinforcements for polymer composites. Polymers and Polymer Composites, 29(4), 277–300. [Google Scholar]
42. Zakriya, M., Ramakrishnan, G., Gobi, N., Gobi, N., Palaniswamy, N. K. et al. (2017). Jute-reinforced non-woven composites as a thermal insulator and sound absorber—A review. Journal of Reinforced Plastics and Composites, 36(3), 206–213. [Google Scholar]
43. Sanivada, U. K., Gonzalo, M., Brito, F. P. (2020). PLA composites reinforced with flax and jute fibers-A review of recent trends, processing parameters and mechanical properties. Polymers, 12(10), 2373. [Google Scholar] [PubMed]
44. Kar, G., Blaise, D., Srivastava, T. K., Kar, C. S., Verma, P. et al. (2023). Commercial crops (Jute, Cotton and Sugarcane). In: Trajectory of 75 years of indian agriculture after independence, pp. 331–362. Singapore: Springer. [Google Scholar]
45. Pradeepa, B., Malathi, M., Kiruthika, A. V. (2023). Properties of jute fibre reinforced polymer composites—A review. European Journal of Engineering Science and Technology, 6(1), 10–29. [Google Scholar]
46. Singh, H., Singh, J. I. P., Singh, S., Dhawan, V., Tiwari, S. K. (2018). A brief review of jute fibre and its composites. Materials Today: Proceedings, 5(14), 28427–28437. [Google Scholar]
47. Chandekar, H., Chaudhari, V., Waigaonkar, S. (2020). A review of jute fiber reinforced polymer composites. Materials Today: Proceedings, 26, 2079–2082. [Google Scholar]
48. Mukul, M. M., Akter, N., Islam, M. M., Bhuiyan, M. S. H., Mostofa, M. G. et al. (2021). Morpho-phenetical study of high yielding tossa jute variety BJRI Tossa Pat 7 (MG-1) for bast fibre yield and qualities. Heliyon, 7(10), e08129. [Google Scholar] [PubMed]
49. Townsend, T. (2020). World natural fibre production and employment. In: Handbook of natural fibres, pp. 15–36. UK: Woodhead Publishing. [Google Scholar]
50. Norhidayah, M. H., Ariff, A., bin Yaakob, M. Y., Zolkarnain, M., Taufik et al. (2014). A review of current development in natural fiber composites in automotive applications. Applied Mechanics and Materials, 564, 3–7. [Google Scholar]
51. Rahman, M. S., Yasunaga, N., Inoue, N. (2023). Factors influencing the mindset toward jute revival: The case of an educated generation in Bangladesh. Agricultural Information Research, 31(4), 111–119. [Google Scholar]
52. Talukder, M. S. H., Chowdhury, M. R., Sourav, M. S. U., Al Rakin, A., Shuvo, S. A. et al. (2023). JutePestDetect: An intelligent approach for jute pest identification using fine-tuned transfer learning. Smart Agricultural Technology, 5, 100279. [Google Scholar]
53. Aktar, N., Mannan, E., Kabir, S. M. T., Hasan, R., Hossain, M. S. et al. (2023). Comparative metagenomics and microbial dynamics of jute retting environment. International Microbiology, 27, 113–126. [Google Scholar] [PubMed]
54. Ameer, M. H., Nawab, Y., Ahmad, S., Ali, Z., Abdellatif, I. (2023). Study of fibre to fibre and ply to ply comingling technique for fabrication of natural fibre reinforced thermoplastic composites. The Journal of the Textile Institute, 1–10. https://doi.org/10.1080/00405000.2023.2282219 [Google Scholar] [CrossRef]
55. Khandaker, S., Akter, D., Hasan, M., Saifullah, A., Marwani, H. M. et al. (2023). From industrial jute fibre spinning wastes to biofibre-reinforced plastics. Materials Chemistry and Physics, 313, 128586. [Google Scholar]
56. Sayem, A. S. M., Haider, J., Naveed, B., Sayeed, M. M. A., Sashikumar, S. (2022). Thermoplastic composites reinforced with multi-layer woven jute fabric: A comparative analysis. Advances in Materials and Processing Technologies, 8(1), 355–379. [Google Scholar]
57. Ivanovska, A., Dojcinovic, B., Maletic, S., Pavun, L., Asanovic, K. et al. (2020). Waste jute fabric as a biosorbent for heavy metal ions from aqueous solution. Fibers and Polymers, 21, 1992–2002. [Google Scholar]
58. Jabbar, A. (2017). Sustainable jute-based composite materials: mechanical and thermomechanical behaviour. In: SpringerBriefs in applied sciences and technology. Berlin/Heidelberg, Germany: Springer Cham. [Google Scholar]
59. Bledzki, A. K., Gassan, J. (1999). Composites reinforced with cellulose based fibres. Progress in Polymer Science, 24(2), 221–274. [Google Scholar]
60. Mishra, S., Mohanty, A. K., Drzal, L. T., Misra, M., Hinrichsen, G. (2004). A review on pineapple leaf fibers, sisal fibers and their biocomposites. Macromolecular Materials and Engineering, 289(11), 955–974. [Google Scholar]
61. John, M. J., Thomas, S. (2008). Biofibres and biocomposites. Carbohydrate Polymers, 71(3), 343–364. [Google Scholar]
62. Ekundayo, G., Adejuyigbe, S. (2019). Reviewing the development of natural fiber polymer composite: A case study of sisal and jute. American Journal of Mechanical and Materials Engineering, 3(1), 1–10. [Google Scholar]
63. Yu, C. (2015). Natural textile fibres: Vegetable fibres. In: Textiles and fashion, pp. 29–56. UK: Woodhead Publishing. [Google Scholar]
64. Subramanian, G. K. M., Balasubramanian, M., Jeya Kumar, A. A. (2022). A review on the mechanical properties of natural fiber reinforced compressed earth blocks. Journal of Natural Fibers, 19(14), 7687–7701. [Google Scholar]
65. Chokshi, S., Parmar, V., Gohil, P., Chaudhary, V. (2022). Chemical composition and mechanical properties of natural fibers. Journal of Natural Fibers, 19(10), 3942–3953. [Google Scholar]
66. Lilargem Rocha, D., Tambara Júnior, L. U. D., Marvila, M. T., Pereira, E. C., Souza, D. et al. (2022). A review of the use of natural fibers in cement composites: Concepts, applications and Brazilian history. Polymers, 14(10), 2043. [Google Scholar] [PubMed]
67. Bekele, A. E., Lemu, H. G., Jiru, M. G. (2022). Experimental study of physical, chemical and mechanical properties of enset and sisal fibers. Polymer Testing, 106, 107453. [Google Scholar]
68. Gunesegeran, K., Annamalai, R., Ma’arof, M. I. N., Rahman, N. A., Nadarajan, N. (2022). High-density polyethylene (HDPE) tiles. AIP Conference Proceedings, vol. 2532. AIP Publishing. [Google Scholar]
69. Maiti, S., Islam, M. R., Uddin, M. A., Afroj, S., Eichhorn, S. J. et al. (2022). Sustainable fiber-reinforced composites: A review. Advanced Sustainable Systems, 6(11), 2200258. [Google Scholar]
70. Islam, S. (2023). Composites derived from biodegradable Textile wastes: A pathway to the future. In: Sustainable fibres for fashion and textile manufacturing, pp. 333–351. UK: Woodhead Publishing. [Google Scholar]
71. Sonali, S., Farzana, M., Haque, M. M., Saha, A., Khan, R. A. et al. (2023). Natural fiber reinforced polymer-based composites: Importance of jute fiber. GSC Advanced Research and Reviews, 15(1), 21–29. [Google Scholar]
72. Hadi, A. E., Hamdan, M. H. M., Siregar, J. P., Junid, R., Tezara, C. et al. (2021). Application of micromechanical modelling for the evaluation of elastic moduli of hybrid woven jute-ramie reinforced unsaturated polyester composites. Polymers, 13(15), 2572. [Google Scholar] [PubMed]
73. Gafurov, A., Korabayev, S., Alimov, O. (2022). Morphology and properties jute fibers. Science and Innovation, 1(A8), 129–135. [Google Scholar]
74. Mohanavel, V., Raja, T., Yadav, A., Ravichandran, M., Winczek, J. (2022). Evaluation of mechanical and thermal properties of jute and ramie reinforced epoxy-based hybrid composites. Journal of Natural Fibers, 19(14), 8022–8032. [Google Scholar]
75. Felix Sahayaraj, A., Muthukrishnan, M., Ramesh, M. (2022). Experimental investigation on physical, mechanical, and thermal properties of jute and hemp fibers reinforced hybrid polylactic acid composites. Polymer Composites, 43(5), 2854–2863. [Google Scholar]
76. Rahman, M., Karacan, I. (2022). Improved thermal stability of jute fiber as an eco-friendly precursor for activated carbon fiber processing. Journal of Polymer Research, 29(6), 241. [Google Scholar]
77. Bledzki, A. K., Franciszczak, P., Osman, Z., Elbadawi, M. (2015). Polypropylene biocomposites reinforced with softwood, abaca, jute, and kenaf fibers. Industrial Crops and Products, 70, 91–99. [Google Scholar]
78. Mather, R. R., Wardman, R. H. (2015). The chemistry of textile fibres. Cambridge: The Royal Society of Chemistry. [Google Scholar]
79. Yang, J., Ching, Y. C., Chuah, C. H. (2019). Applications of lignocellulosic fibers and lignin in bioplastics: A review. Polymers, 11(5), 751. [Google Scholar] [PubMed]
80. Samanta, A. K., Mukhopadhyay, A., Ghosh, S. K. (2020). Processing of jute fibres and its applications. In: Handbook of natural fibres Processing and Applications, pp. 49–120. UK: Woodhead Publishing. [Google Scholar]
81. Rahman, M. M., Islam, M. M., Maniruzzaman, M. (2023). Preparation and characterization of biocomposite from modified α-cellulose of Agave cantala leaf fiber by graft copolymerization with 2-hydroxy ethyl methacrylate. Carbohydrate Polymer Technologies and Applications, 6, 100354. [Google Scholar]
82. Hamdan, M. H. M., Siregar, J. P., Cionita, T., Jaafar, J., Efriyohadi, A. et al. (2019). Water absorption behaviour on the mechanical properties of woven hybrid reinforced polyester composites. The International Journal of Advanced Manufacturing Technology, 104, 1075–1086. [Google Scholar]
83. Al-Maharma, A. Y., Al-Huniti, N. (2019). Critical review of the parameters affecting the effectiveness of moisture absorption treatments used for natural composites. Journal of Composites Science, 3(1), 27. [Google Scholar]
84. Balogun, O. A., Daramola, O. O., Adediran, A. A., Akinwande, A. A., Bello, O. S. (2023). Investigation of Jute/Tetracarpidium conophorum reinforced polypropylene composites for automobile application: Mechanical, wear and flow properties. Alexandria Engineering Journal, 65, 327–341. [Google Scholar]
85. Tusnim, J., Jenifar, N. S., Hasan, M. (2022). Effect of chemical treatment of jute fiber on thermo-mechanical properties of jute and sheep wool fiber reinforced hybrid polypropylene composites. Journal of Thermoplastic Composite Materials, 35(11), 1981–1993. [Google Scholar]
86. Margoto, O. H., Prado, K. D. S. D, Mergulhao, R. C., Moris, V. A. D. S., de Paiva, J. M. F., (2022). Mechanical and thermal characterization of jute fabric-reinforced polypropylene composites: Effect of maleic anhydride. Journal of Natural Fibers, 19(5), 1792–1804. [Google Scholar]
87. Jabbar, A., Militký, J., Kale, B. M., Rwawiire, S., Nawab, Y. et al. (2016). Modeling and analysis of the creep behavior of jute/green epoxy composites incorporated with chemically treated pulverized nano/micro jute fibers. Industrial Crops and Products, 84, 230–240. [Google Scholar]
88. Ivanovska, A., Lađarević, J., Pavun, L., Dojčinović, B., Cvijetić, I. et al. (2021). Obtaining jute fabrics with enhanced sorption properties and closing the loop of their lifecycle. Industrial Crops and Products, 171, 113913. [Google Scholar]
89. Syazwani, N. S., Efzan, M. N. E., Kok, C. K., Nurhidayatullaili, M. J. (2022). Analysis on extracted jute cellulose nanofibers by Fourier transform infrared and X-ray diffraction. Journal of Building Engineering, 48, 103744. [Google Scholar]
90. Eddine Kari, D., Benmounah, A., Boumediri, H., Bezazi, A., Toufik Moussai, A. et al. (2020). Evaluation of chemical, thermal properties and statistical analysis of tensile properties of jute fibers yarns. Proceedings of the 4th International Symposium on Materials and Sustainable Development, pp. 140–151. Boumerdes, Algeria, Springer. [Google Scholar]
91. Barbosa, L. C. M., Duque, G. R. V., Ancelotti Junior, A. C. (2020). Temperature-frequency-dependent properties analysis of a bio-composite based on a new liquid thermoplastic resin reinforced with jute fibers. Journal of Thermoplastic Composite Materials, 35(11), 2125–2145. [Google Scholar]
92. Azman, M. A., Asyraf, M. R. M., Khalina, A., Petrů, M., Ruzaidi, C. M. et al. (2021). Natural fiber reinforced composite material for product design: A short review. Polymers, 13(12), 1917. [Google Scholar] [PubMed]
93. Kaczmarek, D., Walczyk, D., Garofalo, J., Sobkowicz-Kline, M. (2021). An investigation of in situ impregnation for additive manufacturing of thermoplastic composites. Journal of Manufacturing Processes, 64, 972–981. [Google Scholar]
94. Aisyah, H. A., Paridah, M. T., Sapuan, S. M., Ilyas, R. A., Khalina, A. et al. (2021). A comprehensive review on advanced sustainable woven natural fibre polymer composites. Polymers, 13(3), 471. [Google Scholar] [PubMed]
95. Perera, Y. S., Muwanwella, R. M. H. W., Fernando, P. R., Fernando, S. K., Jayawardana, T. S. S. (2021). Evolution of 3D weaving and 3D woven fabric structures. Fashion and Textiles, 8(1), 11. [Google Scholar]
96. Saram, M., Yang, J. (2020). Predicting the elastic modulus of jute/polypropylene composites using mathematical modelling techniques. Proceedings of the Canadian Society for Mechanical Engineering International Congress 2020, Charlottetown, PE, Canada. [Google Scholar]
97. Rajesh, G., Prasad, A. V. R. (2014). Tensile properties of successive alkali treated short jute fiber reinforced PLA composites. Procedia Materials Science, 5, 2188–2196. [Google Scholar]
98. Gao, S. L., Mäder, E. (2006). Jute/polypropylene composites I. Effect of matrix modification. Composites Science and Technology, 66(7–8), 952–963. [Google Scholar]
99. Ma, G., Li, Z., Wang, L., Wang, F., Sanjayan, J. (2019). Mechanical anisotropy of aligned fiber reinforced composite for extrusion-based 3D printing. Construction and Building Materials, 202, 770–783. [Google Scholar]
100. Müssig, J., Graupner, N. (2021). Test methods for fibre/matrix adhesion in cellulose fibre-reinforced thermoplastic composite materials: A critical review. Progress in Adhesion and Adhesives, 6, 69–130. [Google Scholar]
101. Ahamed, B., Hasan, M., Azim, A. Y. M. A., Saifullah, A., Alimuzzaman, S. et al. (2022). High performance short jute fibre preforms for thermoset composite applications. Composites Part C: Open Access, 9, 100318. [Google Scholar]
102. Naik, N., Shivamurthy, B., Thimappa, B. H. S., Govil, A., Gupta, P. et al. (2019). Enhancing the mechanical properties of jute fiber reinforced green composites varying cashew nut shell liquid composition and using mercerizing process. Materials Today: Proceedings, 19, 434–439. [Google Scholar]
103. Patel, N., Jain, P. (2021). An investigation on mechanical properties in randomly oriented short natural fiber reinforced composites. Materials Today: Proceedings, 37, 469–479. [Google Scholar]
104. Bisaria, H., Gupta, M. K., Shandilya, P., Srivastava, R. K. (2015). Effect of fibre length on mechanical properties of randomly oriented short jute fibre reinforced epoxy composite. Materials Today: Proceedings, 2(4), 1193–1199. [Google Scholar]
105. Awais, H., Nawab, Y., Amjad, A., Anjang, A., Akil, H. M. et al. (2021). Environmental benign natural fibre reinforced thermoplastic composites: A review. Composites Part C: Open Access, 4, 100082. [Google Scholar]
106. Brebu, M. (2020). Environmental degradation of plastic composites with natural fillers—A review. Polymers, 12(1), 166. [Google Scholar] [PubMed]
107. Saikrishnan, S., Jubinville, D., Tzoganakis, C., Mekonnen, T. H. (2020). Thermo-mechanical degradation of polypropylene (PP) and low-density polyethylene (LDPE) blends exposed to simulated recycling. Polymer Degradation and Stability, 182, 109390. [Google Scholar]
108. Suriani, M. J., Rapi, H. Z., Ilyas, R. A., Petrů, M., Sapuan, S. M. (2021). Delamination and manufacturing defects in natural fiber-reinforced hybrid composite: A review. Polymers, 13(8), 1323. [Google Scholar] [PubMed]
109. Ye, H., Zhang, Y., Yu, Z., Mu, J. (2018). Effects of cellulose, hemicellulose, and lignin on the morphology and mechanical properties of metakaolin-based geopolymer. Construction and Building Materials, 173, 10–16. [Google Scholar]
110. Mohanty, A. K., Misra, M., Drzal, L. T. (2005). Natural fibers, biopolymers, and biocomposites. Boca Raton, FL, USA: CRC Press. [Google Scholar]
111. Sever, K. (2010). The improvement of mechanical properties of jute fiber/LDPE composites by fiber surface treatment. Journal of Reinforced Plastics and Composites, 29(13), 1921–1929. [Google Scholar]
112. Kusuktham, B., Teeranachaideekul, P. (2014). Mechanical properties of high density polyethylene/modified calcium silicate composites. Silicon, 6(3), 179–189. [Google Scholar]
113. Li, Y., Hu, C., Yu, Y. (2008). Interfacial studies of sisal fiber reinforced high density polyethylene (HDPE) composites. Composites Part A: Applied Science and Manufacturing, 39(4), 570–578. [Google Scholar]
114. Doan, T. T. L., Brodowsky, H., Mäder, E. (2007). Jute fibre/polypropylene composites II. Thermal, hydrothermal and dynamic mechanical behaviour. Composites Science and Technology, 67(13), 2707–2714. [Google Scholar]
115. Klein, R. (2011). Material properties of plastics laser welding of plastics: Materials, processes and industrial applications. Germany: John Wiley & Sons. [Google Scholar]
116. Gupta, V. B. (1995). Some developments in poly (ethylene terephthalate) fibre production and structure-property relationships. Indian Journal of Fibre &Textile Research, 20, 43–59. [Google Scholar]
117. Feng, Y., Shen, H., Qu, J., Liu, B., He, H. et al. (2011). Preparation and properties of PBS/sisal-fiber composites. Polymer Engineering & Science, 51(3), 474–481. [Google Scholar]
118. De Graaf, R. A., Karman, A. P., Janssen, L. P. B. M. (2003). Material properties and glass transition temperatures of different thermoplastic starches after extrusion processing. Starch/Staerke, 55(2), 80–86. [Google Scholar]
119. Zhang, Y., Rempel, C., Liu, Q. (2014). Thermoplastic starch processing and characteristics—A review. Critical Reviews in Food Science and Nutrition, 54(10), 1353–1370. [Google Scholar] [PubMed]
120. Choi, H. Y., Lee, J. S. (2012). Effects of surface treatment of ramie fibers in a ramie/poly (lactic acid) composite. Fibers and Polymers, 13, 217–223. [Google Scholar]
121. Goriparthi, B. K., Suman, K. N. S., Rao, N. M. (2012). Effect of fiber surface treatments on mechanical and abrasive wear performance of polylactide/jute composites. Composites Part A: Applied Science and Manufacturing, 43(10), 1800–1808. [Google Scholar]
122. Ayrilmis, N., Akkus, M., Akbulut, T. (2016). Surface quality of wood plastic composites coated with solvent and water based paints. Machines. Technologies. Materials, 10(4), 33–35. [Google Scholar]
123. Surip, S. N., Jaafar, W. (2018). Comparison study of the bio-degradation property of polylactic acid (PLA) green composites reinforced by kenaf fibers. International Journal of Technology, 9(6), 1205–1215. [Google Scholar]
124. Kabir, M. M., Wang, H., Lau, K. T., Cardona, F. (2012). Chemical treatments on plant-based natural fibre reinforced polymer composites: An overview. Composites Part B: Engineering, 43(7), 2883–2892. [Google Scholar]
125. Kim, J., Tuladhar, U., Je, D., Mieremet, M., Baek, J. et al. (2023). A feasibility study on the use of injection molding systems for mass production of 100W class wind turbine blades. Processes, 11(6), 1855. [Google Scholar]
126. Choi, J. Y., Jeon, J. H., Lyu, J. H., Park, J., Kim, G. Y. et al. (2023). Current applications and development of composite manufacturing processes for future mobility. International Journal of Precision Engineering and Manufacturing-Green Technology, 10(1), 269–291. [Google Scholar]
127. Volk, M., Yuksel, O., Baran, I., Hattel, J. H., Spangenberg, J. et al. (2022). Cost-efficient, automated, and sustainable composite profile manufacture: A review of the state of the art, innovations, and future of pultrusion technologies. Composites Part B: Engineering, 242, 110135. [Google Scholar]
128. Maharana, S. M., Samal, P., Dehury, J., Mohanty, P. P. (2020). Effect of fiber content and orientation on mechanical properties of epoxy composites reinforced with jute and Kevlar. Materials Today: Proceedings, 26, 273–277. [Google Scholar]
129. Singh, R., Singh, B., Tarannum, H. (2019). Mechanical properties of jute fiber-reinforced UP/PU hybrid network composites. Polymers and Polymer Composites, 27(9), 546–556. [Google Scholar]
130. Park, J. M., Quang, S. T., Hwang, B. S., DeVries, K. L. (2006). Interfacial evaluation of modified Jute and Hemp fibers/polypropylene (PP)-maleic anhydride polypropylene copolymers (PP-MAPP) composites using micromechanical technique and nondestructive acoustic emission. Composites Science and Technology, 66(15), 2686–2699. [Google Scholar]
131. Park, J. M., Kim, P. G., Jang, J. H., Wang, Z., Hwang, B. S. et al. (2008). Interfacial evaluation and durability of modified Jute fibers/polypropylene (PP) composites using micromechanical test and acoustic emission. Composites Part B: Engineering, 39(6), 1042–1061. [Google Scholar]
132. Acha, B. A., Reboredo, M. M., Marcovich, N. E. (2007). Creep and dynamic mechanical behavior of PP-jute composites: Effect of the interfacial adhesion. Composites Part A: Applied Science and Manufacturing, 38(6), 1507–1516. [Google Scholar]
133. Hassan, M. M., Wagner, M. H., Zaman, H. U., Khan, M. A. (2011). Study on the performance of hybrid jute/betel nut fiber reinforced polypropylene composites. Journal of Adhesion Science and Technology, 25(6–7), 615–626. [Google Scholar]
134. Rahman, M. R., Huque, M. M., Islam, M. N., Hasan, M. (2008). Improvement of physico-mechanical properties of jute fiber reinforced polypropylene composites by post-treatment. Composites Part A: Applied Science and Manufacturing, 39(11), 1739–1747. [Google Scholar]
135. Aggarwal, P. K., Raghu, N., Karmarkar, A., Chuahan, S. (2013). Jute-polypropylene composites using m-TMI-grafted-polypropylene as a coupling agent. Materials & Design, 43, 112–117. [Google Scholar]
136. Dieu, T. V., Phai, L. T., Ngoc, P. M., Tung, N. H., Thao, L. P. et al. (2004). Study on preparation of polymer composites based on polypropylene reinforced by jute fibers. JSME International Journal Series A Solid Mechanics and Material Engineering, 47(4), 547–550. [Google Scholar]
137. Venkatesan, K., Bhaskar, G. B. (2020). Evaluation and comparison of mechanical properties of natural fiber abaca-sisal composite. Fibers and Polymers, 21, 1523–1534. [Google Scholar]
138. Khan, R. A., Haque, M. E., Huq, T., Khan, M. A., Zaman, H. U. et al. (2009). Studies on the relative degradation and interfacial properties between jute/polypropylene and jute/natural rubber composites. Journal of Thermoplastic Composite Materials, 23(5), 665–681. [Google Scholar]
139. Righetti, B., Mello, R., Benedetto, D., Hirayama, D., Andrade, O. D. (2017). Manufacturing and characterization of jute/PP thermoplastic commingled composite. Materials Research, 20, 458–465. [Google Scholar]
140. Rashed, H., Islam, M. A., Rizvi, F. B. (2006). Effects of process parameters on tensile strength of jute fiber reinforced thermoplastic composites. Journal of Naval Architecture and Marine Engineering, 3(1), 1–6. [Google Scholar]
141. Yang, Y., Ota, T., Morii, T., Hamada, H. (2011). Mechanical property and hydrothermal aging of injection molded jute/polypropylene composites. Journal of Materials Science, 46(8), 2678–2684. [Google Scholar]
142. Liu, X. Y., Dai, G. C. (2007). Surface modification and micromechanical properties of jute fiber mat reinforced polypropylene composites. Express Polymer Letters, 1(5), 299–307. [Google Scholar]
143. Sever, K., Erden, S., Gülec, H. A., Seki, Y., Sarikanat, M. (2011). Oxygen plasma treatments of jute fibers in improving the mechanical properties of jute/HDPE composites. Materials Chemistry and Physics, 129(1–2), 275–280. [Google Scholar]
144. Hossain, M. K., Khanom, S., Kabir, M. A., Gafur, M. A., Ahmed, F. et al. (2020). Investigation of fiber loading on physico-mechanical and thermal properties of jute-mat fiber reinforced recycled polymer composite. Evolution in Polymer Technology Journal, 3, 1–12. [Google Scholar]
145. Nuryawan, A., Hutauruk, N. O., Purba, E. Y. S., Masruchin, N., Batubara, R. et al. (2020). Properties of wood composite plastics made from predominant low density polyethylene (LDPE) plastics and their degradability in nature. PLoS One, 15(8), e0236406. [Google Scholar] [PubMed]
146. Jahan, A., Rahman, M. M., Kabir, H., Kabir, M. A., Ahmed, F. et al. (2012). Comparative study of physical and elastic properties of jute and glass fiber reinforced LDPE composites. International Journal of Scientific and Technology Research, 1(10), 68–72. [Google Scholar]
147. Kabasci, S. (2013). Bio-based plastics-introduction. In: Bio-based plastics: Materials and applications, pp. 1–7. USA: Wiley. [Google Scholar]
148. Jha, A., Kumar, A. (2019). Biobased technologies for the efficient extraction of biopolymers from waste biomass. Bioprocess and Biosystems Engineering, 42, 1893–1901. [Google Scholar] [PubMed]
149. Shimpi, N. G. (2018). Biodegradable and biocompatible polymer composites: Processing, properties and applications. UK: Woodhead Publishing. [Google Scholar]
150. Chamas, A., Moon, H., Zheng, J., Qiu, Y., Tabassum, T. et al. (2020). Degradation rates of plastics in the environment. ACS Sustainable Chemistry & Engineering, 8(9), 3494–3511. [Google Scholar]
151. Naser, A. Z., Deiab, I., Darras, B. M. (2021). Poly(lactic acid) (PLA) and polyhydroxyalkanoates (PHAsgreen alternatives to petroleum-based plastics: A review. RSC Advances, 11(28), 17151–17196. [Google Scholar] [PubMed]
152. Hu, R. H., Sun, M., Lim, J. K. (2010). Moisture absorption, tensile strength and microstructure evolution of short jute fiber/polylactide composite in hygrothermal environment. Materials & Design, 31(7), 3167–3173. [Google Scholar]
153. Memon, A., Nakai, A. (2013). Mechanical properties of jute spun yarn/PLA tubular braided composite by pultrusion molding. Energy Procedia, 34, 818–829. [Google Scholar]
154. Plackett, D., Løgstrup Andersen, T., Batsberg Pedersen, W., Nielsen, L. (2003). Biodegradable composites based on l-polylactide and jute fibres. Composites Science and Technology, 63(9), 1287–1296. [Google Scholar]
155. Sharma, M., Manickam, R. (2015). Development and characterization of fibre reinforced material based on potato starch and jute fibre. International Journal of Applied Engineering Research, 10, 10324. [Google Scholar]
156. Behera, A. K., Avancha, S., Basak, R. K., Sen, R., Adhikari, B. (2012). Fabrication and characterizations of biodegradable jute reinforced soy based green composites. Carbohydrate Polymers, 88(1), 329–335. [Google Scholar]
157. Sanivada, U. K., Mármol, G., Brito, F. P., Fangueiro, R. (2020). PLA composites reinforced with flax and jute fibers—A review of recent trends, processing parameters and mechanical properties. Polymers, 12(10), 2373. [Google Scholar] [PubMed]
158. Gibeop, N., Lee, D. W., Prasad, C. V., Toru, F., Kim, B. S. et al. (2013). Effect of plasma treatment on mechanical properties of jute fiber/poly(lactic acid) biodegradable composites. Advanced Composite Materials, 22(6), 389–399. [Google Scholar]
159. Khan, G. M. A., Terano, M., Gafur, M. A., Alam, M. S. (2016). Studies on the mechanical properties of woven jute fabric reinforced poly(l-lactic acid) composites. Journal of King Saud University-Engineering Sciences, 28(1), 69–74. [Google Scholar]
160. Arao, Y., Fujiura, T., Itani, S., Tanaka, T. (2015). Strength improvement in injection-molded jute-fiber-reinforced polylactide green-composites. Composites Part B: Engineering, 68, 200–206. [Google Scholar]
161. Bledzki, A. K., Jaszkiewicz, A. (2010). Mechanical performance of biocomposites based on PLA and PHBV reinforced with natural fibres—A comparative study to PP. Composites Science and Technology, 70(12), 1687–1696. [Google Scholar]
162. Siracusa, V., Rocculi, P., Romani, S., Dalla Rosa, M. (2008). Biodegradable polymers for food packaging: A review. Trends in Food Science & Technology, 19(12), 634–643. [Google Scholar]
163. Kumar, S., Thakur, K. S. (2017). Bioplastics-classification, production and their potential food applications. Journal of Hill Agriculture, 8(2), 118–129. [Google Scholar]
164. Emadian, S. M., Onay, T. T., Demirel, B. (2017). Biodegradation of bioplastics in natural environments. Waste Management, 59, 526–536. [Google Scholar] [PubMed]
165. Sadeghi, A., Mousavi, S. M., Saljoughi, E., Kiani, S. (2021). Biodegradable membrane based on polycaprolactone/polybutylene succinate: Characterization and performance evaluation in wastewater treatment. Journal of Applied Polymer Science, 138(18), 50332. [Google Scholar]
166. Rafiqah, S. A., Khalina, A., Harmaen, A. S., Tawakkal, I. A., Zaman, K. et al. (2021). A review on properties and application of bio-based poly(butylene succinate). Polymers, 13(9), 1436. [Google Scholar] [PubMed]
167. Platnieks, O., Gaidukovs, S., Thakur, V. K., Barkane, A., Beluns, S. (2021). Bio-based poly(butylene succinateRecent progress, challenges and future opportunities. European Polymer Journal, 161, 110855. [Google Scholar]
168. Chen, G. Q., Patel, M. K. (2012). Plastics derived from biological sources: Present and future: A technical and environmental review. Chemical Reviews, 112(4), 2082–2099. [Google Scholar] [PubMed]
169. Storz, H., Vorlop, K. D. (2013). Bio-based plastics: Status, challenges and trends. Applied Agricultural and Forestry Research, 63(4), 321–332. [Google Scholar]
170. Liu, L., Yu, J., Cheng, L., Qu, W. (2009). Mechanical properties of poly(butylene succinate) (PBS) biocomposites reinforced with surface modified jute fibre. Composites Part A: Applied Science and Manufacturing, 40(5), 669–674. [Google Scholar]
171. Shahinur, S., Sayeed, M. M. A., Hasan, M., Sayem, A. S. M., Haider, J. et al. (2022). Current development and future perspective on natural jute fibers and their biocomposites. Polymers, 14(7), 1445. [Google Scholar] [PubMed]
172. Uawongsuwan, P., Yang, Y., Hamada, H. (2015). Long jute fiber-reinforced polypropylene composite: Effects of jute fiber bundle and glass fiber hybridization. Journal of Applied Polymer Science, 132(15), 41819. [Google Scholar]
173. Singh, J. I. P., Singh, S., Dhawan, V. (2020). Effect of alkali treatment on mechanical properties of jute fiber-reinforced partially biodegradable green composites using epoxy resin matrix. Polymers and Polymer Composites, 28(6), 388–397. [Google Scholar]
174. Dan-mallam, Y., Abdullah, M. Z., MegatYusoff, P. S. M. (2012). Predicting the tensile properties of woven kenaf/polyethylene terephthalate (PET) fiber reinforced polyoxymethylene (POM) hybrid laminate composite. IOSR Journal of Mechanical and Civil Engineering, 2(3), 6–13. [Google Scholar]
175. Pothan, L. A., Thomas, S., Groeninckx, G. (2006). The role of fibre/matrix interactions on the dynamic mechanical properties of chemically modified banana fibre/polyester composites. Composites Part A: Applied Science and Manufacturing, 37(9), 1260–1269. [Google Scholar]
176. Sreenivasan, V. S., Ravindran, D., Manikandan, V., Narayanasamy, R. (2011). Mechanical properties of randomly oriented short Sansevieria cylindrica fibre/polyester composites. Materials and Design, 32(4), 2444–2455. [Google Scholar]
177. Yuan, X., Jayaraman, K., Bhattacharyya, D. (2004). Effects of plasma treatment in enhancing the performance of woodfibre-polypropylene composites. Composites Part A: Applied Science and Manufacturing, 35(12), 1363–1374. [Google Scholar]
178. Kim, B. S., Chun, B. H., Lee, W.I., Hwang, B. S. (2009). Effect of plasma treatment on the wood flour for wood flour/PP composites. Journal of Thermoplastic Composite Materials, 22(1), 21–28. [Google Scholar]
179. Barkoula, N. M., Alcock, B., Cabrera, N. O., Peijs, T. (2008). Flame-retardancy properties of intumescent ammonium poly(phosphate) and mineral filler magnesium hydroxide in combination with graphene. Polymers, 6(11), 2875–2895. [Google Scholar]
180. Rodriguez, E. S., Stefani, P. M., Vazquez, A. (2007). Effects of fibers’ alkali treatment on the resin transfer molding processing and mechanical properties of Jute—Vinylester composites. Journal of Composite Materials, 41(14), 1729–1741. [Google Scholar]
181. Rahman, A., Hasib, M. A., Islam, M. A., Alam, I., Chanda, S. (2023). Fabrication and performance investigation of natural-glass fiber hybrid laminated composites at different Sstacking orientations. Journal of Natural Fibers, 20(1), 2143981. [Google Scholar]
182. Ashraf, M. A., Zwawi, M., Taqi Mehran, M., Kanthasamy, R., Bahadar, A. (2019). Jute based bio and hybrid composites and their applications. Fibers, 7(9), 77. [Google Scholar]
183. Farzana, M., Maraz, K. M., Sonali, S. N., Hossain, M. M., Alom, M. Z. et al. (2022). Properties and application of jute fiber reinforced polymer-based composites. GSC Advanced Research and Reviews, 11(1), 084–094. [Google Scholar]
184. Song, H., Liu, J., He, K., Ahmad, W. (2021). A comprehensive overview of jute fiber reinforced cementitious composites. Case Studies in Construction Materials, 15, e00724. [Google Scholar]
185. Huda, M. K., Widiastuti, I. (2021). Natural fiber reinforced polymer in automotive application: A systematic literature review. IOP Conference Series: Earth and Environmental Science, 1808(1), 012015. [Google Scholar]
186. Arya, M., Malmek, E. M., Ecoist, T. K., Pettersson, J., Skrifvars, M. et al. (2023). Enhancing sustainability: Jute fiber-reinforced bio-based sandwich composites for use in battery boxes. Polymers, 15(18), 3842. [Google Scholar] [PubMed]
187. Balakrishnan, P., John, M. J., Pothen, L., Sreekala, M. S., Thomas, S. (2016). Natural fibre and polymer matrix composites and their applications in aerospace engineering. In: Advanced composite materials for aerospace engineering, pp. 365–383. UK: Woodhead Publishing. [Google Scholar]
188. Zakaria, M., Ahmed, M., Hoque, M. M., Islam, S. (2017). Scope of using jute fiber for the reinforcement of concrete material. Textiles and Clothing Sustainability, 2, 1–10. [Google Scholar]
Cite This Article
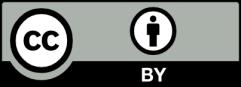
This work is licensed under a Creative Commons Attribution 4.0 International License , which permits unrestricted use, distribution, and reproduction in any medium, provided the original work is properly cited.