Open Access
REVIEW
Sustainable Biocomposites Materials for Automotive Brake Pad Application: An Overview
1 Department of Mechanical Engineering, Covenant University, Ota, Ogun, Nigeria
2 Department of Mechanical and Mechatronics Engineering, AFE Babalola University, Ado, Ekiti, Nigeria
3 Department of Mechanical and Industrial Engineering Technology, University of Johannesburg, Johannesburg, 2028, South Africa
4 School of Chemical and Metallurgical Engineering, University of the Witwatersrand, Johannesburg, South Africa
* Corresponding Authors: Joseph O. Dirisu. Email: ; Imhade P. Okokpujie. Email:
(This article belongs to the Special Issue: Eco-Friendly Waste-Base Materials for Pollution Control Sustainable Technologies)
Journal of Renewable Materials 2024, 12(3), 485-511. https://doi.org/10.32604/jrm.2024.045188
Received 20 August 2023; Accepted 20 October 2023; Issue published 11 April 2024
Abstract
Research into converting waste into viable eco-friendly products has gained global concern. Using natural fibres and pulverized metallic waste becomes necessary to reduce noxious environmental emissions due to indiscriminately occupying the land. This study reviews the literature in the broad area of green composites in search of materials that can be used in automotive brake pads. Materials made by biocomposite, rather than fossil fuels, will be favoured. A database containing the tribo-mechanical performance of numerous potential components for the future green composite was established using the technical details of bio-polymers and natural reinforcements. The development of materials with diverse compositions and varying proportions is now conceivable, and these materials can be permanently connected in fully regulated processes. This explanation demonstrates that all of these variables affect friction coefficient, resistance to wear from friction and high temperatures, and the operating life of brake pads to varying degrees. In this study, renewable materials for the matrix and reinforcement are screened to determine which have sufficient strength, coefficient of friction, wear resistance properties, and reasonable costs, making them a feasible option for a green composite. The most significant, intriguing, and unusual materials used in manufacturing brake pads are gathered in this review, which also analyzes how they affect the tribological characteristics of the pads.Graphic Abstract
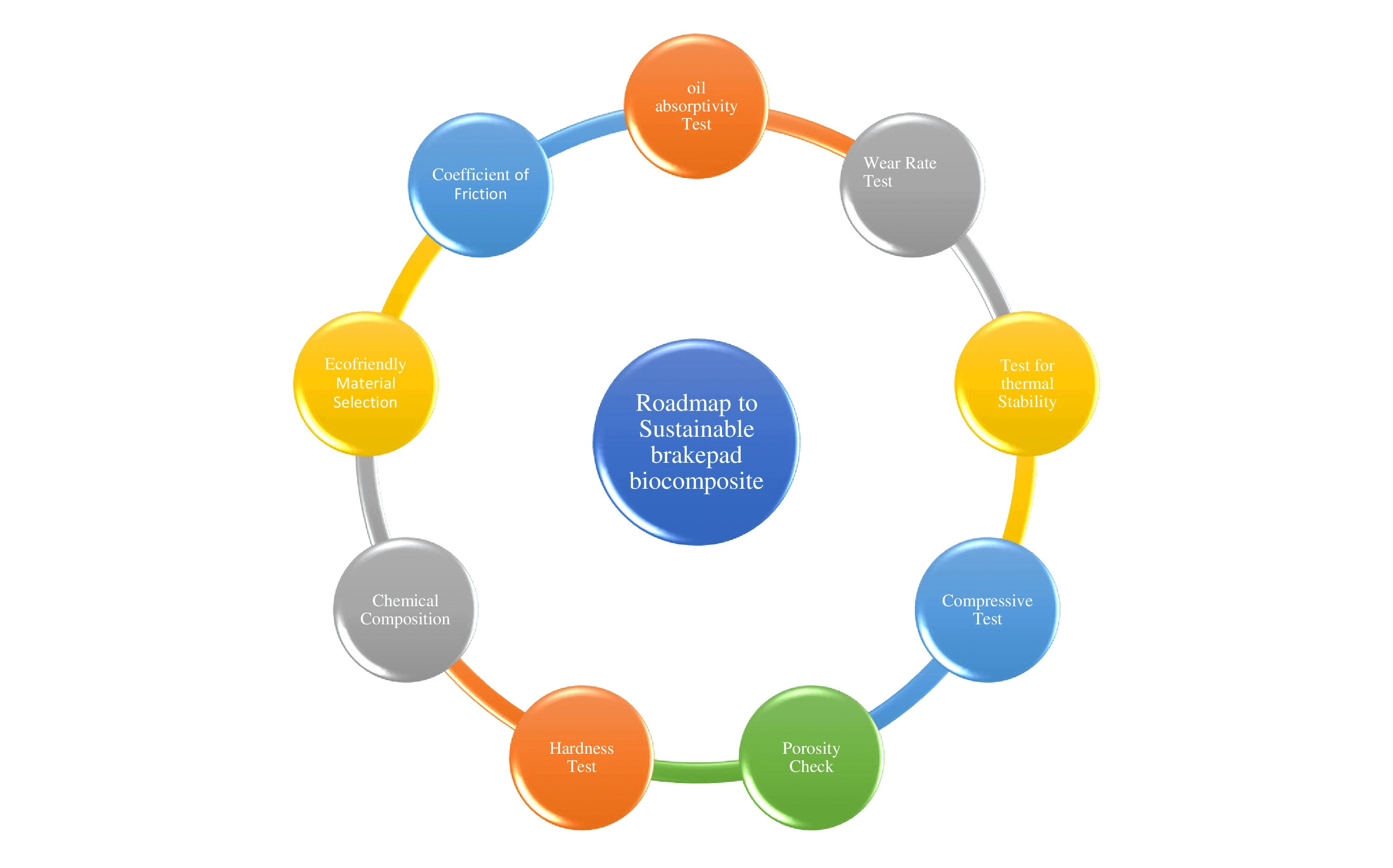
Keywords
The braking system in each vehicle plays a crucial role. Its primary purpose is to stop or reduce the speed of a moving vehicle completely. Brakes are a crucial component of high-performance automobiles that should only receive careful consideration for safety. The brake system is an amalgam of fluid, lines, pedals, levers, connections, and braking devices. Choosing a material that offers strength, durability, performance, and other qualities when designing any system is crucial. Its braking components are essential for a brake system to function safely and effectively. These parts include hydraulic control systems, master cylinders, and brake callipers. Mechanical energy is converted into heat energy by brakes using friction materials. The environment and other brake system components received the heat generated by the friction substance. A car’s brake system consists of a disc brake and a pad, which work together to slow down and accelerate the car. As a result of friction between the surface of the disc and the brake pad, thermal heat is generated during the braking process. The disc and pad should not contact each other at a high temperature [1]. Therefore, the braking system must be dependable, and brake performance must be constant throughout their lives and under varying environmental circumstances [1,2]. The frictional and wear characteristics of the materials used to create brake pads are heavily influenced by their composition. Hence these materials should be stable and consistent. Various natural fibre kinds are available for usage in a variety of applications. The former can exhibit better impact resistance, tensile strength, and stiffness when comparing pure synthetic composites to natural fibre bio-composites. Natural fibres can also help the composites industry in 2050 lessen their negative effects on the environment and carbon footprint. Due to the limited supply of petroleum and asbestos environmental concerns, green composites made from renewable resources have a very bright future in terms of benefits to businesses, the environment, and consumers. The transition to more environmentally friendly building practices in the automotive sector is not just a need for European rules but also a move toward a more economically viable environment. These latter constitute a significant impetus behind the usage of sustainable materials [2].
2 Natural Fibres as Alternatives to Asbestos Brake Pads
Numerous kinds of research have been conducted on viable alternatives to asbestos in friction brake pads. The research considered here is those that employ eco-friendly materials such as natural fibres as alternatives to asbestos. Tensaye et al. [3] postulated that the most vital component of a vehicle is the brakes. He also sought a substitute for asbestos in brake pads due to their carcinogenic nature and focused his research on banana peels. After obtaining the banana peels, they were dried to remove moisture and were pulverized by milling. The banana powder was then sieved and mixed with carbon powder, bronze powder, epoxy resin, and hardener in three different ratios, as shown in Fig. 1.
Figure 1: Mixing ratios for developed brake pads [3]
The best ratio yielded a tensile strength of 2.06 MPa, a bending strength of 30 MPa, a compressive strength of 1.62 MPa, and a wear rate of 0.02 mg/m [3,4]. In contrast with the commercial pad, the developed pad had a better wear rate but worse tensile, compressive, and bending stress [3,5]. The authors concluded that banana peels might be used as a replacement for asbestos in manufacturing brake pads. Ramanathan et al. [4] utilized lemon peel with aluminium oxide, iron oxide, epoxy resin, and hardener to produce asbestos-free brake pads. The peels had moisture extracted from them by drying them at 32°C for 240 h (10 days) and were reduced to a fine particle powdered form. Two samples were produced using hand moulding and were obtained by varying the composition of the stated constituent materials. The binder was epoxy when combined with a hardener in the ratio of 4:1 (epoxy: hardener). Mild steel was used to manufacture the mould, which had a diameter of 30 mm and was 25 mm thick. The tests conducted on the two samples were density, hardness, wear, water absorption, oil absorption, and specific gravity tests. Sample 1 outperformed sample 2 in every testing category, and it had the following composition: 15% graphite, 40% epoxy, 12.5% aluminium oxide (Al2O3), 10% calcium hydroxide, 12.5% iron oxide, and 10% lemon peel powder. Sample 1 had a density of 2.00 g/cm3, an average hardness value (3 tests) of 32, wear loss of 0.5524 g (13.45%), water absorption of 0.96%, and an oil absorption of 0.01%. The authors concluded that lemon peel might substitute asbestos in brake pads [6]. Asotah [7] investigated using corn husks as filler material in brake pads to replace asbestos. They sourced the corn husks from a farm, sun-dried them, and hammered them before turning them to powder using a ball mill. The corn husks were sieved using 100 µm and 200 µm sieve sizes. The corn husks were mixed with silicon carbide (SiC), graphite, resin, and steel dust. Five samples were created where the amount of graphite, resin, and steel was kept constant while alternating the amount of corn husk and silicon carbide. The binder was phenolic resin (phenol-formaldehyde) in combination with hardener, with 64.3% resin and 35.7% hardener. The tests carried out were wear rate, hardness, density, compressive strength, flame resistance, and porosity. The sample produced using corn husk powder from the 100 μm sieve yielded superior compressive strength, hardness, porosity, and wear rate, as seen in Fig. 2. The developed pad was then considered alongside a commercial pad containing asbestos.
Figure 2: Comparison of the results obtained from the brake pad from the 100 µm sieve with commercial brake pad [5]
The authors concluded that the results were desirable, indicating that corn husk can substitute for asbestos in brake pads. Sawdust is usually classified as a by-product of sawmills and has many uses and applications. Lawal et al. [6] utilized sawdust as the base material to manufacture an asbestos-free brake pad. 30 kg of sawdust was acquired from a sawmill; moisture was extracted from the sawdust by placing it under the sun for one week. The dried sawdust was then pulverized using a ball mill. The powdered sawdust was then separated into three categories distinguished by sieve sizes and sieved using 710, 355, and 100 µm. The sawdust was mixed with silicon carbide, graphite, steel dust, epoxy resin, and hardener. The epoxy served as the binder when mixed with the hardener in the appropriate ratio. From Figs. 3 and 4, three samples were created with the same mixing ratios, with the only difference being the particle size of the constituents (710, 355, and 100 µm). The ratio that guided the mixing was 55% sawdust, 15% steel dust, 5% graphite, 10% silicon carbide, and 15% epoxy. The composition was hot pressed after mixing; then, it was cured using an oven before being left to cool at room temperature. The developed brake pad was subjected to various tests and analyses. The data obtained from the tests concluded that the developed pads’ characteristics improved as the particle size decreased.
Figure 3: Results of various properties of developed brake pads [6]
Figure 4: Comparison of properties of the best sawdust-based brake pad (100 µm) with asbestos-based brake pad [6]
Tests were carried out on the commercial asbestos-based brake pads to form a basis for comparison.
It was concluded from the comparison that the developed brake pad is similar to and in the range of the commercial brake pad and can, therefore, be used as a viable alternative. Also, Elakhame et al. [7] studied the use of periwinkle as a replacement for asbestos in brake pads. The periwinkles used were bought from a market, and moisture was extracted from the shells by employing the natural heat source (the sun) followed by the artificial heat provided by an oven set at 105°C for five hours. The shells were then loaded into a cone crusher, which reduced the size to 3–4 mm, then 1–2 mm after reloading. They were then put in a ball mill for two hours and then sieved using 350, 200, and 100 µm sieves with a sieve shaker. The developed brake pad consisted of a periwinkle shell, steel dust, graphite, silicon carbide, and resin. Thirty samples were produced for each of the three seize sizes in varying compositions, as shown in Fig. 5.
Figure 5: Composition of developed brake pads [7]
The produced sample underwent various tests, including compressive strength, density, hardness, wear rate, and oil and water absorptivity. The results showed better values for the tested parameters as the particle size decreased. The results obtained from the smallest particle size (100 µm) were comparable with those obtained from the commercial brake, leading to the conclusion that periwinkle shells can substitute for asbestos in brake pads.
Waste is described as an unwanted by-product of human activities and an inevitable after-effect of human existence and activities. It can also be described as anything of little or no worth regarding money and functionality. Due to the population boom, industrial activities, agricultural activities, and mining and exploratory activities, the quantity of waste produced on the planet has exponentially multiplied [8]. There are various types of waste, but they can be broadly classified into four, namely: municipal solid waste, agricultural waste, hazardous waste, and industrial solid waste [9]. Further explanations are given thus:
i) Municipal Solid waste: this is usually obtained from homes, hotels, schools, shops, offices, and workplaces. It comprises minimal food waste, paper, fabrics, glass, and metal. Some hazardous or toxic waste in minute quantities, such as batteries, pharmaceuticals, etc. Other additions to these vary from place to place. They can include large amounts of ash from wood being burnt for heating during winter in temperate climates, fallen leaves from trees in arboreous areas, vehicles, old furniture, and even faeces in places with poor sewage disposal where they are either bagged and disposed of or bucket latrines are emptied [10].
ii) Industrial Solid waste: this type of waste includes materials involved in manufacturing, mining, production, and several other industries. Such waste includes paper, glass, metal, ceramic, rubber, plastic, wood, leather, solvents, resins, sawdust, sandpaper, straw, etc. Industrial waste differs according to the country’s nature; developed countries tend to have more industrial waste than developing and under-developed countries due to more industries and the preference to manufacture instead of importing. Manufacturing powerhouses like China would have more industrial waste than other countries [11].
iii) Agricultural waste: as humans, there is an inherent need to feed to stay alive, and not all parts of the food we eat are consumable or edible. This produces waste, and as there has been a population boom, there has been an equivalent rise in demand for food, tallying in an increase in agricultural waste. Some sources of these agricultural wastes include rice husks, corn stalks, egg shells, banana peels, husks of various grains, yam peels, sugarcane bagasse, tobacco stalks, coconut husks, and shells, unwanted products from abattoirs (of which cattle husbandry has the highest percentage), animal waste products, palm shells, etc. [12].
iv) Hazardous waste: as advancements are made in agricultural, industrial, and medical sectors and processes, more hazardous or toxic wastes are discovered and produced annually. Hazardous waste is obtained from various places, including hospitals, nuclear power plants, manufacturing industries, workshops, homes, etc. Such waste includes pesticides, insecticides, fertilizer, drugs, detergents, engine oil, paint and paint fumes, exhaust gases from power plants, and petroleum waste products [13].
Improper disposal or handling of waste can adversely affect animal and plant life and the environment. The waste impact can broadly be categorized as the impact on human life, plant and animal life, and the environment [14].
i) Impact on human life-some impacts on human life include: severe and sometimes terminal health conditions; displacement of people from their homes due to uninhabitable environments (as seen after the unfortunate nuclear accident at Chernobyl); loss of lives and properties; people using face masks in cities (such as Beijing) to avoid breathing unclean air; decline in agricultural output due to barren or unfertile lands; deaths resulting from typhoid, diarrhoea, etc. due to unclean or polluted water [15].
ii) Impact on plant and animal life-some impacts on plant and animal life include destruction and, in some cases, extinction of plant and animal species; death or migration of aquatic life due to pollution of their marine habitat [16].
iii) Impact on the environment-some impacts on the environment include: global warming and melting of ice due to the effect of greenhouse gases and other industrial activities; ozone layer depletion; unfertile lands due to chemical spillage, nuclear accidents, or methane from landfills; poisoning of water bodies due to chemical or waste dumping, oil spillage; unclean air due to air pollution [17].
3.2 Handling and Managing Waste
Waste is often undesirable, generated in large quantities, and adversely affects life and the environment when not handled or disposed of appropriately. This means waste needs to be handled and managed correctly to avoid pollution [18]. Waste has to be handled appropriately before it arrives at where it is to be managed to aid ease of management and prevent spillage and accidents. Some of the steps involved in waste handling are:
i. Sorting the waste: various types of waste require different means of disposal. To ease disposal, avoid injuries when handling, contamination of other waste, or formation of harmful by-products, it is best to segregate the waste into several categories, including; paper waste, oil waste, glass waste, plastic waste, metal waste, bio-degradable waste, chemical waste, toxic waste, etc. [19].
ii. Labelling the waste: the various types of waste in the waste collection vessel must be clearly stated to aid in collection, transportation, and disposal. Non-hazardous wastes do not require any specific form of labelling. In contrast, in many nations, toxic waste is often required by law to be labelled in a specific way (often ostentatiously using bright colours and symbols) [20].
iii. Storing the waste: the generated waste must be kept securely after it has been moved from the collection vessels (usually comparatively small in size) and before it is transported to its processing site. The vessels used to house or store the waste must not react with the waste to form by-products, the vessel should be impermeable to fluids, it should not corrode or degrade when placed in contact with the waste, the vessel should have contingencies for leakage such as tank traps to collect leakage and avoid spillage. The storage vessels or facilities should undergo scheduled routine or extensive checks. The vessels should be shielded from the natural elements as much as possible [21].
iv. Transporting the waste entails moving the waste from the point of collection to its final point. Waste can be transported over short distances via automobiles and locomotives or over longer distances (to places that require them or have the facilities to process them) using aircraft, watercraft, and pipelines. For safety, the vessel used for transportation must be routinely checked, and the shortest and safest route should be selected because spillage can still occur while in transit [22].
v. Managing the waste: this encompasses destroying or disposing of the waste and turning waste into a valuable product or using it to do something useful. Some methods and processes employed in disposing of waste include:
vi. Landfill: this is the oldest and most common method of waste disposal. Here waste is kept in huge piles or pits. In the sanitary landfill, the waste is buried [22].
vii. Incineration: this is a form of thermal waste treatment. Here the waste material is burnt and leaves a residue. It is one of the best methods for disposing of biomedical waste. It is practiced on small scales, such as burning combustible materials at home, and on larger scales, such as industrial incineration. It has the advantage of significantly reducing the mass of the waste material and leaving relatively little residue. It has the disadvantage of producing and emitting harmful gases into the atmosphere and large quantities of CO2 [22].
Some methods and processes employed in reusing waste include:
viii. Recycling involves reusing materials that would otherwise be deemed useless, such as empty cans. This benefits the environment as fewer non-biodegradable waste materials, such as plastics, are in the ocean. It boosts the economy as less is spent on obtaining raw materials to create these items and creates new jobs. Some of the most common recycled items are aluminium soda cans, soup cans, PET bottles, glass, and paper [23].
ix. Pyrolysis: This is used to obtain a substitute for conventional fuels from waste materials. The fuel can be in the form of liquid (bio-oil), solid (bio-char), or gas (pyro-gas). Here, the waste materials are heated up without oxygen; hence, combustion is avoided. Due to the high temperatures, the materials decompose to form hydrocarbon gases and, in some cases, solid charcoal. In contrast with incineration, the by-products are less harmful, but pyrolysis of some types of waste can produce harmful gases as by-products [24].
x. Composting involves breaking down organic waste to form compost or humus, which can be added to the soil for increased fertility and improvement. A by-product is methane gas, which can be trapped and used for electricity generation. Composting works by the action of microorganisms, and these organisms need four components to work appropriately: carbon, nitrogen, oxygen, and water. These must be provided in a set ratio that will enable the compost to be heated to the temperature range where the organic waste materials are decomposed [25].
xi. Energy Recovery involves turning non-recyclable materials into energy either in heat or electricity or by converting them into fuels. This can be obtained from various waste management processes such as incineration, pyrolysis, composting, and landfill gas recovery. It provides an alternative to fossil fuels and is a means of renewable energy. It utilizes the methane generated from composting, pyrolysis, etc., for electricity generation instead of being released into the atmosphere [26]. Waste materials can be used to generate many valuable items. They can be remade into the items they were before, they can be used to generate heat and electricity, and more recently, they have been used to form composite materials.
4 Review on Composite Materials
Composite materials are materials composed of two or more different materials that have distinct properties individually and are combined to obtain a unique combination of these characteristics and properties that would not have been otherwise achieved by selecting one of the materials [27]. The difference between composites and mixtures is that in the final structure, the constituent materials remain separate in composites. Composites are anisotropic and heterogeneous, and the constituents are separate at the macroscopic level [28].
4.1 Classification of Composites
Composites comprise a base material (matrix) binder for the filler material (reinforcement). The matrix (polymer, metal, or ceramic) is continuous and envelops the reinforcement, usually in fibre, fragment, or particle form. The matrix contains the reinforcement and gives the composite the required shape, while the reinforcement enhances the mechanical and physical properties of the matrix [29]. The matrix is usually the weaker material and transmits or transports the load, while the reinforcement carries the load and is the more substantial material. Fig. 6 shows the classification of composite materials based on matrix and reinforcement materials. The matrix should have good ductility, thermal conductivity, etc., while the reinforcement should have high strength, stiffness, etc. [30]. Composites can be classified based on the final structure’s constituent materials. This thus yields two classifications, which are based on matrix materials and reinforcement materials.
Figure 6: Classification of composites [31]
4.1.1 Based on Matrix Material
The matrix protects the reinforcement from external influences and keeps the reinforcement bonded. Composites can be broadly classified based on the material the matrix is made of as ceramic matrix composite (CMC), metal matrix composite (MMC), and organic matrix composite (OMC). The OMC can be further categorized as polymer matrix composite (PMC) or carbon matrix composite (also called carbon-carbon composite). Polymer matrix composites are very popular and have the highest application presently [32].
i. Polymer Matrix Composite: a polymer matrix containing a reinforcement such as carbon, metal, ceramic, glass, etc. They are relatively cheap composites due to the easy manufacturing techniques used. The matrix is weak, and the strength of the composite material is obtained from the reinforcement. They can be further classified into thermoset and thermoplastic composites [30,32].
ii. Thermoset Composites: blends of various resins mixed with non-reactive fillers, fibre (used for reinforcing), catalysts, pigments, and other materials to create compounds, which can be moulded by injecting, compressing, or transferring. Curing is achieved via heating, chemical reaction, or pressure to obtain an interlinked and stable molecular structure, which implies that they cannot be melted or reformed [33]. They are the most popular matrix material and have desirable properties such as high corrosion resistance, good surface finish, thermal resistance, good strength, etc. The matrix is prepared by mixing resin with hardener.
iii. Thermoplastic Composites: they also combine fibre, fillers, and other materials. They are formed under heat and solidify as they cool. Thermoplastic can be melted and reformed, giving it an advantage over thermosets. They save more money when compared to the thermoset composite because of non-heated tooling, take less time to produce, and the used-up parts can be recycled to regain the raw material. The polymer matrix and the reinforcements can be recovered using dissolution, thermal degradation, and grinding [34]. Table 1 shows the comparison between thermoset and thermoplastic composites.
Examples of resins are polyester, iso polyester, phenolic, vinyl ester, and epoxy resins.
i. Ceramic Matrix Composite: they are made of fibre reinforcement (usually carbon, aluminium oxide (Al2O3), silicon nitride (SiN), and silicon carbide (SiC)) enclosed in a ceramic matrix. This composite’s advantage over traditional ceramic is ductility, as conventional ceramics are very brittle. Ceramic matrix composites behave differently from other composite materials regarding loading and failure. Here, the matrix is the more robust material and fails first under loading to avoid premature failure of the brittle reinforcement fibres. Ceramics possess good refractory properties, and as such ceramic matrix composites are used in high-temperature applications [30,35].
ii. Metal Matrix Composite: here, the matrix must be a metal (pure metal or alloy), usually magnesium (Mg), aluminium (Al), titanium (Ti), copper (Cu), etc., and the material used as reinforcement may be ceramics (oxides & carbides), carbon or other metals (lead, tungsten, etc.).
The advantage of these composites over metals and their alloys is that they possess higher strength, better stiffness, lower density, better thermal expansion, and better resistance to wear, creep, and fatigue. Composites with aluminium as the matrix material are widely applied in propulsive systems (such as automobile and aerospace systems), braking systems for locomotives and automobiles, gas turbine engines, etc. Reinforcements such as silicon carbide and aluminium oxide can be readily mixed in molten aluminium [35]. Due to increased stiffness, when machining these composite materials using conventional methods, the cutting tool has a higher wear rate (due to the inclusion of hard ceramic or metal particles) than it would have when machining the matrix material alone. Therefore, unconventional machining methods are employed [36].
4.1.2 Based on Reinforcement Material
Fibre Reinforced Composite:here, synthetic fibres (glass, carbon, ceramic, etc.) or natural fibres (coconut, jute, etc.) are dispersed in the matrix. As a result of using fibres as the reinforcement, the material will yield higher strength, stiffness, and better chemical, thermal, and wear resistances application [30,36]. Natural fibers are gaining traction because they provide high impact and fatigue strength and have excellent specific strength and stiffness characteristics. They are also readily sourced and comparatively cheaper than synthetic fibres, offer a means of recycling and waste reduction, and are bio-degradable, hence, eco-friendly. They also weigh less than synthetic fibres [37,38].
Particle Reinforced Composite: these are formed by having the reinforcement in particle form (flake or powder form) embedded in a desired matrix. An example is concrete, where coarse aggregate serves as the reinforcement to offer strength and stiffness, while cement is the matrix that binds and keeps the reinforcement together in shape. Fiber-reinforced composites possess higher strength than particle-reinforced composites. Still, particle-reinforced composites have higher resistance to wear and, as such, are used where more excellent wear resistance is needed. Another benefit of particle reinforcement composite is their relatively low production cost and ease of manufacturing [39].
Sheet Reinforced Composite:high-strength molding composites of long glass fibres and unsaturated resins. They are primarily used in areas where a high strength-to-weight ratio is required (such as substantial structural fixtures) [30,39]. They are subdivided into laminated and sandwich composites. In laminar composites, the composite is a summation of laminas that produces multiple plies. The intended use of the composite determines the stacking and ply orientation which may vary from ply to ply. A resin binds the composite layers, and each layer comprises fibres embedded in a matrix. Sandwich composites contain a light material with good compressive strength sandwiched between two counter-plates with high strength. The resulting composite material has low weight but high stiffness [32,39].
4.1.3 Advantages of Composites
Some of the advantages composite have over traditional materials include:
Lightweight: composites are considerably lighter than traditional materials such as metals while possessing similar or even better structural properties. For example, reinforced carbon fibre is about a fifth of 1020-grade steel in mass but can possess up to five times its strength [30,39]. This property is beneficial in applications with a low weight-to-power ratio, such as propulsion systems or high-velocity vehicles (e.g., rockets, high-performance cars, race cars, race boats, kayaks, etc.), and strength is also required for safety purposes. It also has applications in sports equipment manufacturing (e.g., rackets, bats, helmets, boards, etc.). In particle-based composite materials, the density is a function of the particle size and shape [36,39].
Design Flexibility: they are every designer’s dream as they can be manipulated to form the most complicated and intricate designs. Lower tolerances can be obtained using composites, and shrinkage allowances are significantly reduced compared to metals. Also, densities and other properties can be varied to serve different purposes [27,39].
Lower Cost: it costs much less to produce components using composites than if metals were employed. Much more material would have to be used to achieve the desired design parameters if conventional materials are employed in some products. In contrast, a thinner composite material layer can achieve said parameters for a lesser cost [37,39].
Higher Productivity and Part Consolidation: production time is massively reduced by employing composites because post-moulding machining is often unnecessary. Also, single components can perform assemblies’ functions due to a wide range of properties [29,39].
Corrosion Resistance: the major problem with metals is that they corrode when exposed to specific conditions and environments, limiting the application of certain types of metals to specific conditions. Most composites do not have this issue and can be used in various environments. A significant example is using composites in biomedical engineering for body implants, such as hip replacements [40].
Low Weight-to-Strength Ratio:metals are pretty strong but also very heavy; composites are as strong or stronger than metals while weighing less. This is especially relevant in aeroplanes as they have solid materials but also at the least weight possible. Composites offer the highest strength-to-weight or lowest weight-to-strength ratios among any materials currently being used [29,40].
High Impact Strength:they can be engineered to withstand and contain impacts such as the force of a moving bullet or an explosive blast. This gives them preference when selecting bulletproof vests and armour-plating materials for vehicles, buildings, and aircraft [29,40].
Other advantages composites possess over conventional materials include electric insulation, thermal resistance, durability, high strength, good surface finish, non-magnetic, chemical resistance, damping, flame retardant, radiopacity, acoustic, puncture resistance, wear resistance, etc. [30,40].
4.2 Uses and Application of Composites
Composite materials have various applications in engineering practice due to their vast array of desirable physical and chemical properties and characteristics, which cannot be obtained from a single conventional material. Some of these applications are listed below:
Aerospace: composite materials are used in several aircraft parts, such as the wings, fuselages, bulkheads, etc. It is used here because of its desirable properties such as lightweight, design flexibility, corrosion resistance, thermal resistance, high strength, etc. On aircrafts low weight-to-power ratio is desirable and this is accomplished by using lighter materials [41].
Appliances: composites are used in frames, handles, and panels on various equipment, tools, and appliances such as washing machines, dryers, ovens, refrigerators, etc. [42].
Automobiles: composites are now being used on panels, dashboards, and some furniture as a means of weight-saving on high-performance cars and cost-saving on some economy cars [43].
Racing: composites such as reinforced carbon fibre are now commonplace on race cars where the goal is to go as fast as possible, and this can be achieved by making the car as light as possible coupled with a powerful engine. This is achieved using composites due to their lightweight nature [44]. Also, aerodynamics is as essential as the power produced, and the composites can easily be formed into the desired shapes. Safety is also essential since the vehicle moves at very high velocities, and the composites possess high impact strength to withstand excessive deformation on crashing. Composites are used not just on the panels and the interior but to make the bodywork [45].
Marine: most waterbodies travel in salt water, which is corrosive. This poses a challenge to most watercraft as they are usually made of metals that tend to corrode. Composites offer a solution to this problem because they are corrosion-resistant and have the added benefit of being lightweight, making the vessel travel faster. They possess high impact strength, which enables them to withstand the impact of waves [46].
Corrosive or harsh environments: composites are preferred to metals in corrosive applications due to their corrosion resistance. This includes chemical plants, water treatment plants, pipes, pumps, and refineries [47].
Construction: one of the most popular composite materials is concrete, used in almost all construction activities [48]. Other applications of composite materials in construction include roofing, doors, windows, frames, and other fixtures [49].
Civil: due to their high strength, thermal resistance, and other properties, composite materials can be used for reinforcement and structural purposes on civil projects such as bridges, roads, etc. [40]. Numerous composite materials exist today as engineers aim for improved material selection to yield optimum results and maximize profits. Some examples of these materials include paper-mâché, polyvinyl chloride (PVC) pipes, fibreglass, reinforced carbon fibre, plywood, ceramic matrix composite, metal matrix composite, reinforced concrete, and brake pads [50].
Natural fibres are primarily obtained from plants and animals but can also be obtained from minerals. Examples of plant fibres include cotton, jute, kenaf, coconut, sugarcane bagasse, etc. Examples of animal fibres include wool, silk, angora, mohair, etc. [51].
Natural fibres can reinforce composite materials; these composites containing natural fibres are called biocomposites. Compared with synthetic fibres, they offer the advantages of being less dense (resulting in lighter composites), better thermal insulation, lower costs, lesser skin irritation, and being bio-degradable. Synthetic fibres are more substantial than natural fibres [52].
5.1 Classification of Natural Fibres
Natural fibres can be classified into plant and animal fibres depending on the source from which they are obtained. Fig. 7 shows the classification of natural fibres.
Figure 7: Classification of natural fibres [53]
Plant Fibres: these are fibres obtained from different parts of a plant. They can be further classified according to the part of the plant the fibre is sourced from [54].
Seed Fibre: the fibres are sourced from the seeds of the plants [55]
Leaf Fibre: these are fibres sourced from plant leaves, e.g., pineapple, banana, etc. [56].
Bast Fibre: the fibres are sourced from the outer cell layer of the stem of the plants, e.g., jute, kenaf, flax, etc. [50].
Fruit Fibre: these are fibres sourced from the fruits of trees, e.g., coconut coir, etc. [57]
Stalk fibre: these are fibres sourced from plant stalks, e.g., bamboo, wheat, rice, etc. [58]
Animal Fibres: these are fibres retrieved from animal parts. Animal fibres usually comprise proteins like chitin, collagen, keratin, and fibroin [59].
Hair Fibre: fibres sourced from hairy animals, e.g., sheep wool, goat hair (mohair), horse hair, angora, etc. [60].
Serictery Fibre: fibres obtained from insects’ glands during their cocoon preparation. e.g., silk [60].
When combined with a polymer matrix, plant fibres form the most common type of natural fibre composite. The resin or matrix material determines whether the composite will yield a thermoset or thermoplastic composite [61]. Fig. 8 shows the constituents of a natural fibre composite.
Figure 8: Constituents of a natural fibre composite [62]
The coconut (cocos nucifera) is a plant under the family of arecacaeae (Palm family) and the subfamily cocoideae [63]. The constituents of coconut from the outermost part inwards are; a thin layer of hard skin (exocarp), a thick layer of fibre called the husk (mesocarp), a hard shell (endocarp), the white kernel (solid endosperm/copra) and a cavity filled with a liquid called coconut water/milk (liquid endosperm) [64]. Fig. 9 shows a cross-section of coconut fibre.
Figure 9: Cross section of coconut [64]
5.1.2 Physical and Mechanical Properties of Coconut Fibre
Marimuthu [65] performed a study on a composite material containing glass fibre, coconut fibre, and epoxy in a ratio of 1:3:6. The inclusion of coconut fibre increased the mechanical properties of the composite such as its hardness, impact strength, and flexural strength while also reducing its tensile strength and density.
In a study carried out by Gopinath et al. [66], polyester and epoxy resin served as the matrix, while E-glass, jute fibre, and coconut fibre were used as reinforcement in their respective composite mixtures. Several mechanical and physical tests were carried out on the produced samples. The results showed that the E-glass had better tensile, flexural & and impact strengths, and hardness among the three reinforcements. The coconut fibre had better values for tensile & and impact strengths and hardness than the natural fibers. The synthetic fibre had better overall values, but the cost of the natural fibres made it an attractive alternative. Among the natural fibres, the coconut proved superior from the concluded tests. Somashekhar et al. [67] researched the mechanical properties of a polymer composite material reinforced with coconut shell powder and tamarind shell powder with an epoxy resin matrix. Three different mixing ratios were used, and from the results obtained, the best values were obtained when the ratio was 50% coconut shell, 5% tamarind, and 45% epoxy resin. It was discovered that including coconut shell and tamarind, shell powder increased tensile properties by 50%. Tests carried out include bending tests, tensile strength tests, Rockwell hardness tests, water absorption tests, and flexural strength tests.
Yashas et al. [68] performed research operations on polymer matrix composites that utilized natural fibres as reinforcement materials. The experiment was done on both thermoplastic and thermoset polymers. Among the thermoplastic polymers, when polypropylene was used as the matrix material and coconut fibres were used as reinforcement, it was noted that there was an increase in flexural strength and other properties like tensile and impact strengths increased with the addition of more reinforcement fibres. Optimal values were obtained when the reinforcement was 30% of the total weight. The composite material’s water absorption was reduced due to good adhesion between the matrix and reinforcement. When polyethylene was used as the matrix material, adding coconut fibre as reinforcement for the high-density polyethylene (HDPE) matrix yielded better mechanical properties when compared to the HDPE matrix on its own. The mechanical properties were directly proportional to the amount of coconut fibre reinforcement, as an increase in the amount of coconut fibre yielded a corresponding increase in the mechanical properties of the matrix. Among the thermoset polymers, a polyurethane polymer matrix was used with natural fibre reinforcement. Castor oil resin was the matrix and was combined with coconut and sisal fibres, respectively. The sisal fibres combination yielded better results than its coconut fibre counterpart. An increase in the amount of fibre in the composite yielded an increase in tensile strength, rigidity, and water absorption, as well as a decrease in bending strength [68].
6 Biocomposites: Review of Materials for Automobile Application
For composite, the matrix is constant while the reinforcement varies, dispersed within the matrix in the form of fibrous or particulates. The essence of composite development is to enhance toughness, strength, and stiffness properties. Wood, bone, plastics, etc., are examples of composites. Environmental concerns exist about specific composites that are not biodegradable and recyclable, such as plastics. Thus, several types of research were made to develop composites that contribute to reducing global warming and improving the ecological system [69]. This is by sustainable development goals 7 & 13 and net zero emission target cum global 1.5°C temperature reduction by 2030. Biopolymer composites are considered an option to explore in improving the environment. Biopolymers, bio-fillers, and biocomposites are biodegradable, abundantly available, low in cost, and highly stiff. Biocomposites or green composites are composites that occur naturally or are made of cellulosic materials employed as reinforcement. A biocomposite can be formed from the combination of natural fibres with polymers. There exist various biocomposites such as natural fibres, natural resin, and hybrid reinforcement. Natural fibres are cellulose, protein, and mineral fibres. Food starch, bio waste, and agricultural waste can be utilized as natural fibre. Natural resins are gums, glues, gum Arabic, and hard resin copal amongst others [69]. Hybrid reinforcement is a result of a combination of different fibres into a single matrix to form a hybrid biocomposite. Two hybrid composites can be formed by following the rule of mixture as depicted in the equations:
PH=P1V1+P2V2 (1)
MA=M1V1+M2V2 (2)
where MA is the property under investigation. M1 and M2 are properties of the first and second systems. V1 and V2 are the volume fractions for the systems. The rule of mixture can be applied to simple situations such as composite density. It cannot analyze accurately the mechanical properties but hypothesis elasticity can be used to analyze it as it is more complex than the rule of mixture [69].Let ma=mb+mc (3)
where ma is the total mass of the composite, mb is the mass of the fibre and mc is the mass of the matrix, respectively. The equation is valid irrespective of the void in the composite. The volume of the composite must also be accounted for by considering the volume of the void [69]. Therefore,
va=vb+vc+vd (4)
where the v subscripts are the volumes a, b, c & d represent the volume of total composite, fibre, matrix, and void. By dividing Eq. (3) by ma and Eq. (4) by va, we have
Mb+Mc=1 (5)
and
Vb+Vc+Vd=1 (6)
where Mb, Mc, Vb, Vc, and Vd are the mass fractions of fibre, matrix, and volume fractions, respectively. The composite density, ρ=m/v becomes
ρa=mava= mb+mcva=ρbvb+ρcvcva (7)
where the last term numerator in Eq. (7) is the composite density in terms of volume fraction. ρa , ρb and ρc are densities of the total composite, fibre, and matrix, respectively. We can express ρa with respect to the mass fractions [69]. Therefore,
ρa=mava= mavb+vc+vd=mambρb+mcρc+vd (8)
ρa=1Mbρb+Mcρc+vdρd (9)
Rewriting Eq. (9) to obtain the volume fraction,
ρa=ρaρa(Mbρb+Mcρc)+vd (10)
Making vd the subject of the formula
vd= 1−ρa(Mbρb+Mcρc) (11)
Biocomposite can be developed by utilizing biowaste and biobased polymers that are available and contribute to overall low-cost of production not compromising its excellent mechanical properties. There is research to improve biocomposite to have appreciable load-bearing capacity. The introduction of bio-resin and biopolymer is part of the improvement of biocomposite. The authors recognized the impact of natural fibre on polymer matrix and recommended the discontinuation of materials that pose an ecological risk to humanity. The automobile industry was spotted as the predominant application of biocomposite [69].
In a separate review, the authors reviewed green composite to sort suitable materials for automobile applications. The shift to a more sustainable material did not just stem from cost efficiency or a more viable environment but from EU regulation that wants a more sustainable city and zero emission environment. Natural fibre according to the researchers is lightweight and cost-effective compared to the synthetic fibre and steel used in autobody. The feasibility of mechanically green composite hinges on how fair it is compared with synthetic ones in the market [1,69]. Another author worked on bio epoxy resin as a replacement for matrixes such as polyester, epoxy, and polymer amongst others. The research reveals that biocomposite prepared using resin as a matrix yields 90% impact strength compared with industrial hemp fibres [70]. The authors [71] employed bio-sourced materials to develop resin matrix-based brake pads. The test samples showed comparable mechanical resistance and tolerated severe stresses to commercial brake pads. Their work attested to the possibility of developing a greener auto-brake pad with tunninsfuranic resin binder and abrasive particles dispersed into it. The biobased resin material can replace oil-derived resins or petrochemical resin under extreme conditions [71]. The increment of phenolic resin content in slag waste for braking application resulted in hardness and shear stress upscale. Thermoset phenolic resin performs the function of bonding the materials together and is responsible for determining the tribological characteristics of brake pad material. The combination of fly ash and phenolic resin yielded a high coefficient of friction according to [71] the interaction of water-quenched slag fibre and phenolic-based resin resulting in an enhanced frictional coefficient. The authors reviewed the combination of different natural fibres with polymer reinforcement. The aim was to regulate polyester resin with biocomposite to make products that can be used for different applications. Fillers are to improve manufacturability by partially replacing the overall base materials to reduce the overall cost of production. Fillers are also introduced to improve the mechanical properties of biocomposites [72]. The content of the fibre, the fibre length, the material composition of the filler, and the fibre treatment are factors that improve the properties of biocomposites. Polymer combines with these fibre properties to form a polymer matrix composite material. They are composed of the reinforcement phase and matrix phase. Epoxy resin has been widely used as a matrix element in the makeup of biocomposite [73]. The authors endorsed the use of resin for eco-friendly composite as it possesses results that apply to various industrial demands. biocomposites also known as green composites are good replacements for polymer matrixes in developing composites [74]. Lignin polymers such as soda lignin, sulphuric acid lignin (SAL), and heat-treated SAL were used as frictional materials to substitute phenolic formaldehyde resin [75]. The authors were positive with the view of petrochemicals being replaced with bio-sourced chemicals due to oil price increases [76].
6.1 Materials Used for Brake Pad and Tribo-Mechanical Properties
Due to the interaction of the brake pad with the rotating disc, the brake pad should have the capacity to withstand heat as friction generates heat between the brake pad and the rotating disc. Therefore, materials should possess thermal stability at high temperatures as their decomposition will compromise their performance in service [77]. A high friction coefficient material is sought for in achieving a prolonged service life. Agricultural and industrial wastes are employed to form a brake pad composite which are viable replacement for the carcinogenic asbestos material. Composites that are blended to form brake pads must be composed of filler, reinforced fibre, friction additives, and abrasives. The brake pad is developed from these blended materials in different compositions. The purpose of the reinforcement is to improve the mechanical properties of the composite. The binder is to keep the brake pad structure bonded when undergoing mechanical and thermal stresses. The binder prevents the microstructure from collapsing. Abrasives and lubricants are frictional materials to increase the coefficient of friction and stabilize the COF at elevated temperatures.
Ikpambese et al. [78] developed brake pads using 40% epoxy resin, 10% palm waste, 6% Al2O3, 29% graphite, and 15% CaCO3 were outstanding percentage compositions. Palm kernel fibre composite served as a viable replacement for the commercial asbestos brake pad. Ruzaidi et al. [79] used waste materials such as palm slag, dolomite, and CaCO3 as filler materials. Steel fibre and phenolic resin were used. However, the performance was not impressive compared to palm slag and CaCO3. Palm Slag showed better thermal stability at 50°C–100°C. the authors concluded that phenolic resin cannot be relied upon at high temperatures due to weight loss at 150°C. Ibhadode et al. [80] used PKS, agro waste material, and compared it with other kernel shells such as Hyphaene thebaica kernel shell (HTKS) and deleb PKS (DPKS). Refining PKS according to the authors will improve its wear rate at high vehicle speeds. Banana peel and phenolic resin were combined to develop 25% wt uncarbonized banana peel and 30% wt carbonized banana peel. The latter was seen to provide better performance and recommended as a replacement for the asbestos brake pad type. However, the tribological properties will give more insight into its viability as brake pad material [80]. High coefficients of friction, low wear rates, high heat dissipation rates, good resistance to water swelling, dimensional stability at high temperatures, high tensile, compressive, and shear strengths, low water and oil absorption rates, and low thermal conductivity are important considerations when choosing materials [81]. Manufacturers of brake pads use almost 2,000 different materials, each of which has a different impact on the finished product [81,82]. A typical brake pad contains 10 to 20 different materials. It is challenging to choose the ideal brake pad composition and foresee how it would affect the finished goods. It necessitates extensive research and experience in plenty [83]. The decision must also take into account the operating circumstances and the brake pad’s intended purpose [84]. Production technology, which is typically the best-kept secret of every manufacturer, also influences the brake pad’s final characteristics [85,86]. The tribological characteristics of the brake pad might be 100% better with an efficient production method. Different criteria can be used to classify the materials that are used to make brake pads [86].
The most significant one is the part the composite plays while braking. Binders, additives, fillers, and abrasives are available based on this standard. The flue that holds all of the pad’s components is the binder. This substance must have a high and steady coefficient of friction, be resistant to high and abrupt temperature changes, and have a low bulk (the binder typically makes up 20% of the pad volume). The material must also not react with any other part of the pad as this could modify its general material properties or result in the composite’s delamination, both of which would significantly reduce the braking system’s effectiveness. Typically, epoxy or silicone resin is used as the binder [87]. The reinforcement is a fibrous substance (one or more) that enhances the mechanical properties of the binder (raising its strength). The endurance and resistance of the brake pad are greatly influenced by the various types of reinforcement materials; as a result, the choice cannot be made at random. Asbestos was a superior reinforcing fibre in the past. Finding a substitute, which is now not at all difficult given the wide variety of materials that may be used successfully for this purpose, was necessary due to the material’s detrimental characteristics [81,87]. Abrasives are used to change the coefficient of friction (increase or decrease it). Due to their hardness, additives like steel, cast iron, flame-resistant oxides, silicates, or quartz can increase the coefficient of friction between the brake pad and disc, extending the pad’s useful life. The adherence to the disc material, particularly in the case of metals, also strengthens the effect. Contact zones, which are the primary sites of friction in the two components, are also produced by the substances. Unfortunately, high temperatures are produced because of the friction in the contact areas. This can result in the structure of the pad being destroyed and the separation of its parts. For this reason, lubricants are employed, which typically enhance the pad’s thermal conductivity. The removal of energy from the contact region is enhanced by lubricants, which also keep the friction components from overheating. Graphite and metallic sulfates (such as copper or tin) are the most widely used lubricants. Their lubricity is influenced by the pad’s volume (around 10% of the total volume produces the optimum results) and the size of the lubricant particles [87,88].
Friction materials are often the main component of a brake pad. Brake pads can be divided into the following categories based on the type of friction material they contain metallic, where steel, copper, or another metal serves as the primary friction material; the pad is characterized by high resistance and thermal conductivity; cooperation with a cast iron disc results in deep scratches and cavities in the material (due to adhesion); this can cause unwelcome noise and quickly spreading corrosion. Semi-metallic-the friction material consists of a mix of metals and organic components, offering good friction and strong heat conductivity; similarly, to metallic pads, wear may be quicker, as well as noise during braking and corrosion [89]. Non-asbestos organic or ceramic-the primary component is typically an organic material reinforced with aramid, glass, or ceramic fiber; this design ensures high durability, resistance to high temperatures, low wear rate, lightweight, and quiet operation; however, due to the complexity of the manufacturing process, this type of solutions may be very expensive, and because of the material’s high hardness, it may be brittle [89].
Resins are frequently utilized as binders to create bonds. They must be added in precisely calculated amounts since only then will they fulfil their intended purpose [81,87]. A pad’s durability is decreased if there is insufficient resin, while its hardness is greatly increased if there is too much resin. One of the most crucial materials used in the production of brake pads is resin since it binds all the other parts of the pad and enables them to work together efficiently. When used as a matrix material to hold structural elements, fillers, abrasive friction modifiers, etc. together during the manufacture of brake pads, thermosetting material resins are the most affordable binders and provide good physical and chemical properties [81,89].
However, the quality of the brake pad material may decrease if too much heat is produced during braking. This is connected to resin degradation, which causes a substance’s binding capabilities to disappear. Because of this, the resin may have a significant role in a brake pad’s thermal stability, ability to preserve mechanical qualities, and ability to bind components under harsh braking conditions. Numerous attempts have been to change the composition of resins to enhance their initial mechanical and thermal qualities. The filler that is manufactured the most frequently for friction materials—almost exclusively—is phenol resin. Few additional uses exist for them. From 5% to 35% of the volume, phenol resin makes up the weight fraction of brake pads. Inverse relationships exist between the content amount and the wear rate’s coefficient of friction value. With a 10% decrease in the weight of pad resin, the COF value only changes by a small amount. Due to the resin’s advantageous qualities, including its excellent mechanical resistance and low cost, the automotive sector frequently uses it. Heat expansion is minimal. It also resists solvents, acids, and water better than other resins, and it burns cleaner than other resins. The material is brittle, which is unfortunate. The addition of silicone gum or oil can lessen the likelihood of cracking. Silica resin is created in this way. Other mechanical qualities, however, suffer as a result. For friction at high temperatures, phenol resin is not the optimum material [81,82]. When braking suddenly, the pad’s temperature can quickly rise to 700°C, far above the point at which phenol resin starts to degrade [83,84]. Epoxy resins are frequently utilized in the industry. They are inappropriate as friction materials because of their limited thermal stability (degradation begins at about 260°C). According to the findings of some researchers, weight loss of around 7% is still detectable at 100°C [85]. Volatiles that develop during firing may be responsible for this bulk loss. Carbon was created and oxidized when the temperature was raised over 400°C. Epoxy and phenol resins mixed, however, provide some intriguing outcomes [86,87]. Compared to the two resins, the substance is far more heat resistant and has superior mechanical qualities. Thermoplastic polyamide resin is a substance produced from calcium carbonate and fluoresin [88,89]. It can withstand both high temperatures and wear. Additionally, the production method is simple and economical. Though roughly three times better than phenol resin, the resin is an excellent thermal isolator. Its value in the production of brake pads is therefore quite low [81–89]. Thermal resistance is marginally increased by COPNA resin. It disintegrates at a similar temperature (400°C–500°C), but much less gas is emitted throughout the process. As a result, brake fade danger is decreased. Additionally, the particle and graphite have excellent adhesion because of their similarity. This increases the friction resistance of the pad. Cyanide monomers are used to create cyanate ester resins. Chemically speaking, these resins are inert and exhibit a propensity to dampen vibration. However, resilience to high temperatures is its most crucial quality. According to research, adding ZrB2 to it in a quantity of about 5% makes it more thermally stable and guarantees that its tribological qualities about the COF and wear rate are at their best. Graphite and MoS2 were mixed for experiments as well. In this approach, scientists improved the mechanical qualities and decreased the rate of wear. On the other hand, one of its key negatives is the high cost (coming from a difficult and frequently multi-day production procedure). Because of this, it is hardly used in friction materials. Electronics is where cyanate ester resins are used most frequently [81,89].
It is necessary to use reinforcing (structural) elements to boost mechanical characteristics. There are many different kinds of fibres formed of materials including metals, carbon, synthetic fibre, Kevlar, minerals, ceramics, and natural fibres, among others. The mechanical qualities of the fibre orientation are also good. The performance of the brake pad is enhanced by the good structural reinforcing qualities and high thermal stability of steel wool and fibre glass [81,87]. Palm Kernel Shell is a waste product that is produced, for instance, when margarine-making palm oil is produced [82,83]. West Africa is where palms are primarily grown in plantations. Palm Kernel Shells (PKS), which have an output of 15–18 tons per acre, are a plentiful and affordable resource. It is simple and affordable to transport due to its low density (in comparison to other organic waste) [84,85]. PKS is utilized in brake pads as an alternative to asbestos because of its fibrous texture [86]. Even 40% of the volume of the friction layer can be made up of them [87]. The low hygroscopicity, high rigidity, and high hardness of pulverized particles make them ideal for brake pads. Additionally, they have a cast iron brake disc with a high coefficient of friction of about 0.41 [87,88]. Oxidation accelerated the wear of the pad, which happened much more quickly than with commercial brake pads [89].
Research by Mgbemena et al. [90], revealed that the three phases’ start temperatures were 54.28°C, 237.14°C, and 538.57°C, respectively, and that there were significant weight losses of 6%, 27%, and 42.37%. The results of tests using brake pads designed for “cold” braking, which does not produce temperatures of hundreds of degrees Celsius, were far better. Another crucial factor in the manufacturing of the pad is the PKS particle size. In tests, brake pads with bigger particles displayed superior hygroscopic absorption and wear resistance. Using finely ground PKS allowed for the best mechanical qualities (high hardness, resistance, and low porosity) to be attained [90]. Up to 40% of a fresh banana’s weight is made up of banana peels. Currently, the peels are either thrown away as waste or used as fertilizer. Banana peels can be used safely in a variety of sectors because they are classified as non-toxic for human tissues by the National Cancer Standard Institute. Physical and chemical analyses of banana peels revealed that pectin and antioxidants make up the majority of their composition. Complex polysaccharide mixes known as pectin compounds, which are used to make gels, contain galacturonic acid units as the primary chain. The addition of banana peel powder increases the substance’s potential further. The powder was seen to first become more gelatinous as the temperature rose, before hardening. These characteristics allow banana peels to be used to create unique brake linings that increase the binding resin’s ability to withstand high temperatures. Experimental studies support these assertions. A sufficient amount of binding strength between the powdered banana peels causes a higher coefficient of friction. The material also showed minimal water and oil absorption. However, brake pads with banana peels in them deteriorate more quickly [89,90]. The most unusual material employed in the fabrication of the brake pads is a periwinkle shell. These little animals’ shells are a waste product from the food manufacturing industry [89,90]. It is thought to pose a threat to the environment and human health because of the enormous amount of trash that is produced throughout the process. The usage issue may be somewhat mitigated if asbestos were replaced by shell fragments in the manufacture of brake pads. Nigerian researchers used material that has been ground into particles smaller than 255 microns to examine the mechanical characteristics of the shells.
According to their research, the material is quite heat resistant and has a lower density than asbestos. The onset of heat deterioration was first noted at temperatures above 6000°C. The substance under study was also revealed to be harder than asbestos (around 75 HRC harder). Other researchers, also from Nigeria, went a step further and developed a variety of brake pad prototypes employing different periwinkle shell particle sizes (varying from 100 to 350 µm). The investigations revealed that particles with a diameter of 100 µm offer the optimum properties. They demonstrated the highest hardness, lowest water, and oil absorption, and excellent compression resistance. The parameters are superior to those of commercial brake pads [7,81]. The smallest fractions (125 µm) produced the best abrasive wear resistance results in their study from the study of Elakhame et al. [7,81]. As the periwinkle shell particle size was lowered from 350 to 100 m, there was strong interfacial bonding. As the particle size of the periwinkle shell was reduced from 350 to 100 m, it was shown that the brake pad samples’ compressive strength, hardness, and density increased, while the oil soak, water soak, and wear rate decreased. Periwinkle shell particles at 100 m outperformed industrial braking pads. When making brake pads, periwinkle shell fragments can successfully replace asbestos [90].
Filler materials are affordable and cost-effective, which increases their suitability for manufacture. The spaces between particles are filled with fillers. Based on their compatibility and thermal stability, these are chosen. Here, scientists have more freedom to use natural chemicals and lower the proportion of metallic material used in brake pad application. The brake pad is filled with materials like vermiculite, cashew powder, and barium sulfate, among others, which also control and lessen noise [81,89,90]. Fly ash is a by-product of the burning of coal in power plants and industrial facilities. It takes the shape of fine mineral dust and is mostly made up of silicon, aluminium, and iron. Its colour ranges from light to dark grey or light brown. Fly ash also has a small amount of unburned carbon and several trace elements, just like natural rock. Because of the damaging effects of coal combustion, several governments prioritize waste product management in their environmental policies, particularly regarding industrial waste. Fly ash has varying qualities due to the various types of coal and power boilers, which affect waste management. The inexpensive price of the material led to attempts to employ it as a filler in brake pads. Between a few percent and 55%–60% of the total weight is the mass content. According to research, brake pads with a high ash content have steady coefficients of friction—but only at low initial vehicle speeds. After reaching a limit value (the experiments were based on braking from a starting speed of approximately 100 km/h), some researchers noticed that the coefficient of friction considerably dropped. The use of different materials that are less heat resistant may be the cause of this. It was tried to employ the inexpensive substance as a filler in brake pads. A few percent to between 55 and 60 percent of the total weight make up the mass content. High ash content brake pads exhibit consistent coefficients of friction, but only at low initial vehicle speeds, according to research. Some researchers found that the coefficient of friction dramatically decreased after reaching a limit value (the tests were based on braking from an initial speed of approximately 100 km/h). This might be the effect of employing other materials that are not as heat resistant. For samples with only 4 wt% of the substance under consideration. The results are not clear-cut, so it may be concluded that the choice of the other abrasive material components has a significant impact. The characteristics of fly ash do not alter with temperature. Ash has a beneficial impact on controlling thermal energy. Compared to commercial pads, brake pads with a volume ash content of 55% were more heat resistant. This is caused by fly ash’s low thermal conductivity and high heat capacity (up to 800 kJ/kg K), which allow ash particles to store heat [81,89,90].
Friction modifiers like graphite and zirconium oxide are used to keep the operating coefficient of friction within a certain range. They help stabilize, maintain low temperatures, and reduce wear. Because they don’t work well with binding materials, they are only utilized in small amounts. Controlling interfacial film is another benefit [81,89,90]. Abrasives are accustomed to producing brittle, harsh brake pads. Hardness increase is useful for cleaning rotating elements (such as discs or drums). However, a significant increase in hardness harms the disc or drum. As a result, a lesser number of abrasives are utilized to make brake pads [81,89,90]. Fig. 10 presents the coefficient of friction of various materials for brake pads that compare favourably with asbestos brake pad composite. It also confirms that the best value of COF can sometimes be obtained by combining different materials.
Figure 10: Coefficient of friction of composite materials for brake pad [74,83,85]
7 Future Consideration and Conclusions
As long as green composites function similarly to asbestos fibre types in terms of tribo-mechanical performance, the use of green composites in automotive brake pads appears to be possible. This work outlined the key characteristics of the various materials used in the manufacture of brake pads. The right composition of materials for brake pads and proportions guarantees not only an appropriate and consistent stopping force but also an enhancement in comfort by lowering the rate of abrasive wear and quieting frictional noise.
Brake pads’ environmental impact and the harmful effects on human health caused by the usage of asbestos can both be decreased by using natural fibres as reinforcing agents. The difference in fibres content may have an impact on mechanical and tribological properties, respectively, according to this review research. For instance, by properly incorporating natural fibres, the tribological characteristics of brake pads, such as the coefficient of friction (COF) and wear rate, can be greatly enhanced. It is possible to lessen the amount of environmental pollution caused by automobiles by using natural fibres like banana peels, periwinkle shells, or coconut fragments, which are showing up increasingly frequently in friction materials. The complexity of tribological phenomena that occur in the friction pair must be better understood. Doing so will help researchers and research institutions around the world create new and inventive brake pad production technologies or compositions, like those that use industrial or agro-food waste.
From the research reviewed, the coefficient of friction can be improved upon by combining different reinforcement materials.
The development of materials with diverse compositions and varying proportions is now conceivable, and these materials can be permanently connected in fully regulated processes. This explanation demonstrates that all of these variables affect friction coefficient, resistance to wear from friction and high temperatures, and the operating life of brake pads to varying degrees. The most significant, intriguing, and unusual materials utilized to make brake pads were gathered in this study, and their effects on the tribological characteristics of the pads are described.
Acknowledgement: The authors wish to appreciate the Management of Covenant University for publication support of this manuscript.
Funding Statement: No funding was received for this work. We confirm that we have given due consideration to the protection of intellectual property associated with this work and that there are no impediments to publication, including the timing of publication, with respect to intellectual property.
Author Contributions: The authors confirm their contribution to the paper as follows: Dirisu conceptualization of idea, writing, analyzing and editing. Okokpujie substantive revision of the manuscript. O.O. Joseph substantive revision of the manuscript. S.O. Oyedepo title revision and substantive revision of the manuscript. O. Falodun substantive revision of the manuscript. L.K. Tartibu substantive revision of the manuscript. D.F. Shehu writing, preparing the research agenda, editing and revision of the paper critically for important intellectual content. All other authors reviewed the results and approved the final version of the manuscript.
Availability of Data and Materials: The datasets generated during and/or analyzed during the current study are available from the corresponding author upon reasonable request.
Conflicts of Interest: The authors certify that they have no affiliations with or involvement in any organization or entity with any financial interest (such as honoraria; educational grants; participation in speakers’ bureaus; membership, employment, consultancies, stock ownership, or other equity interest; and expert testimony or patent-licensing arrangements), or non-financial interest (such as personal or professional relationships, affiliations, knowledge or beliefs) in the subject matter or materials discussed in this manuscript.
References
1. Hemanth, M. S. K., Dhas, J. E. R. (2023). Eco-friendly materials for brake pad-ANSYS overview. Materials Today: Proceedings. [Google Scholar]
2. Koronis, G., Silva, A., Fontul, M. (2013). Green composites: A review of adequate materials for automotive applications. Composites Part B: Engineering, 44(1), 120–127. [Google Scholar]
3. Yigrem, M., Fatoba, O., Tensay, S. (2022). Tribological and mechanical properties of banana peel hybrid composite for brake-pad application. Materials Today: Proceedings, 62, 2829–2838. [Google Scholar]
4. Ramanathan, K., Saravanakumar, P., Ramkumar, S., Pravin, K. P., Surender, S. R. (2017). Development of asbestos-free brake pads using lemon peel powder. International Journal of Innovative Research in Science, Engineering and Technology, 6(3), 4449–4455. [Google Scholar]
5. Asotah, W., Adeleke, A. (2017). Development of asbestos-free brake pads using corn husks. Leonardo Electronic Journal of Practices and Technologies, 31, 129–144. [Google Scholar]
6. Lawal, S. S., Bala, K. C., Alegbede, A. T. (2017). Development and production of brake pad from sawdust composite. Leonardo Journal of Sciences, 30, 47–56. [Google Scholar]
7. Elakhame, Z. U., Olotu, O. O., Abiodun, Y. O., Akubueze, E. U., Akinsanya, O. O. et al. (2017). Production of asbestos free brake pad using periwinkle shell as filler material. International Journal of Scientific & Engineering Research, 8(6), 1728–1735. [Google Scholar]
8. Dirisu, J. O., Oyedepo, S. O., Fayomi, O. S. I., Joseph, O. O., Akinlabi, E. T. et al. (2022). Thermal-emission assessment of building ceilings from agro-industrial wastes. Fuel Communications, 10, 100042. [Google Scholar]
9. Abdel-Shafy, H. I., Mansour, M. S. (2018). Solid waste issue: Sources, composition, disposal, recycling, and valorization. Egyptian Journal of Petroleum, 27(4), 1275–1290. [Google Scholar]
10. Singh, A. (2019). Managing the uncertainty problems of municipal solid waste disposal. Journal of Environmental Management, 240, 259–265. [Google Scholar] [PubMed]
11. Krishna, R. S., Mishra, J., Meher, S., Das, S. K., Mustakim, S. M. et al. (2020). Industrial solid waste management through sustainable green technology: Case study insights from steel and mining industry in Keonjhar. India Materials Today: Proceedings, 33, 5243–5249. [Google Scholar]
12. Duque-Acevedo, M., Belmonte-Urena, L. J., Cortés-García, F. J., Camacho-Ferre, F. (2020). Agricultural waste: Review of the evolution, approaches and perspectives on alternative uses. Global Ecology and Conservation, 22, e00902. [Google Scholar]
13. Fazzo, L., Minichilli, F., Santoro, M., Ceccarini, A., Della Seta, M. et al. (2017). Hazardous waste and health impact: A systematic review of the scientific literature. Environmental Health, 16(1), 1–11. [Google Scholar]
14. Nwankwo, C., Gobo, A. E., Israel-Cookey, C., Abere, S. A. (2020). Effects of hazardous waste discharge from the activities of oil and gas companies in Nigeria. Central Asian Journal of Environmental Science and Technology Innovation, 1, 119–129. [Google Scholar]
15. Sajib, S. H. (2021). A study on the effects of environmental pollution on human life in the riverbank area of Barishal City Corporation (Kirtankhola River). https://scholar.google.com/scholar?hl=en&as_sdt=0%2C5&q=study+on+the+effects+of+environmental+pollution+on+human+life+in+the+riverbank+area+of+Barishal+City+Corporation&btnG= (accessed on 20/09/2023). [Google Scholar]
16. Preeti, J. K. R., Thakur, M., Suman, M., Kumar, R. (2018). Consequences of pollution in wildlife: A review. The Pharma Innovation Journal, 7, 94–102. [Google Scholar]
17. Upadhyay, R. K. (2020). Markers for global climate change and its impact on social, biological and ecological systems: A review. American Journal of Climate Change, 9(3), 102270. [Google Scholar]
18. Malav, L. C., Yadav, K. K., Gupta, N., Kumar, S., Sharma, G. K. et al. (2020). A review on municipal solid waste as a renewable source for waste-to-energy project in India: Current practices, challenges, and future opportunities. Journal of Cleaner Production, 277, 123227. [Google Scholar]
19. Lu, H., Sidortsov, R. (2019). Sorting out a problem: A co-production approach to household waste management in Shanghai. China Waste Management, 95, 271–277. [Google Scholar] [PubMed]
20. Persson, L., Karlsson-Vinkhuyzen, S., Lai, A., Persson, Å., Fick, S. (2017). The globally harmonized system of classification and labelling of chemicals—Explaining the legal implementation gap. Sustainability, 9(12), 2176. [Google Scholar]
21. Taufan, H. S., Purwanto, P. (2018). The management of toxic and hazardous waste materials in the food industry. E3S Web of Conferences, vol. 73, 07020. EDP Sciences. [Google Scholar]
22. Tulebayeva, N., Yergobek, D., Pestunova, G., Mottaeva, A., Sapakova, Z. (2020). Green economy: Waste management and recycling methods. E3S Web of Conferences, vol. 159, 01012. EDP Sciences. [Google Scholar]
23. Ayodele, T. R., Alao, M. A., Ogunjuyigbe, A. S. O. (2018). Recyclable resources from municipal solid waste: Assessment of its energy, economic and environmental benefits in Nigeria. Resources, Conservation and Recycling, 134, 165–173. [Google Scholar]
24. Soltes, E. J., Elder, T. J. (2018). Pyrolysis. In: Organic chemicals from biomass, pp. 63–99. Boca Raton: CRC Press. [Google Scholar]
25. Ayilara, M. S., Olanrewaju, O. S., Babalola, O. O., Odeyemi, O. (2020). Waste management through composting: Challenges and potentials. Sustainability, 12(11), 4456. [Google Scholar]
26. Moya, D., Aldás, C., López, G., Kaparaju, P. (2017). Municipal solid waste as a valuable renewable energy resource: A worldwide opportunity of energy recovery by using waste-to-energy technologies. Energy Procedia, 134, 286–295. [Google Scholar]
27. Clyne, T. W., Hull, D. (2019). An introduction to composite materials. Cambridge university press. [Google Scholar]
28. Barile, C., Casavola, C., De Cillis, F. (2019). Mechanical comparison of new composite materials for aerospace applications. Composites Part B: Engineering, 162, 122–128. [Google Scholar]
29. Nagavally, R. R. (2017). Composite materials-history, types, fabrication techniques, advantages, and applications. International Journal of Mechanical and Production Engineering, 5(9), 82–87. [Google Scholar]
30. Rajak, D. K., Pagar, D. D., Kumar, R., Pruncu, C. I. (2019). Recent progress of reinforcement materials: A comprehensive overview of composite materials. Journal of Materials Research and Technology, 8(6), 6354–6374. [Google Scholar]
31. Yang, Y., Boom, R., Irion, B., van Heerden, D. J., Kuiper, P. et al. (2012). Recycling of composite materials. Chemical Engineering and Processing: Process Intensification, 51, 53–68. [Google Scholar]
32. Duarte, J. M. R. M. B. (2018). Composite panels subjected to multi-impacts at different energy levels (Doctoral Dissertation). Universidade de Coimbra. [Google Scholar]
33. Jouyandeh, M., Paran, S. M. R., Jannesari, A., Puglia, D., Saeb, M. R. (2019). Protocol for nonisothermal cure analysis of thermoset composites. Progress in Organic Coatings, 131, 333–339. [Google Scholar]
34. Cousins, D. S., Suzuki, Y., Murray, R. E., Samaniuk, J. R., Stebner, A. P. (2019). Recycling glass fiber thermoplastic composites from wind turbine blades. Journal of Cleaner Production, 209, 1252–1263. [Google Scholar]
35. Gireesh, C. H., Prasad, K. D., Ramji, K., Vinay, P. V. (2018). Mechanical characterization of aluminium metal matrix composite reinforced with aloe vera powder. Materials Today: Proceedings, 5(2), 3289–3297. [Google Scholar]
36. Bai, W., Roy, A., Sun, R., Silberschmidt, V. V. (2019). Enhanced machinability of SiC-reinforced metal-matrix composite with hybrid turning. Journal of Materials Processing Technology, 268, 149–161. [Google Scholar]
37. Koh, R., Madsen, B. (2018). Strength failure criteria analysis for a flax fibre reinforced composite. Mechanics of Materials, 124, 26–32. [Google Scholar]
38. Rangappa, S. M., Siengchin, S. (2019). Lightweight natural fiber composites. Journal of Applied Agricultural Science and Technology, 3(2), 178. [Google Scholar]
39. Sajan, S., Selvaraj, D. P. (2021). A review on polymer matrix composite materials and their applications. Materials Today: Proceedings, vol. 47, pp. 5493–5498. [Google Scholar]
40. Kuzina, E., Cherkas, A., Rimshin, V. (2018). Technical aspects of using composite materials for strengthening constructions. IOP Conference Series: Materials Science and Engineering, vol. 365, no. 3, 032053. IOP Publishing. [Google Scholar]
41. Asim, M., Saba, N., Jawaid, M., Nasir, M. (2018). Potential of natural fiber/biomass filler-reinforced polymer composites in aerospace applications. In: Sustainable composites for aerospace applications, pp. 253–268. Woodhead Publishing. [Google Scholar]
42. Kumar, K., Davim, J. P. (2018). Composites and advanced materials for industrial applications. IGI Global. [Google Scholar]
43. Agarwal, J., Sahoo, S., Mohanty, S., Nayak, S. K. (2020). Progress of novel techniques for lightweight automobile applications through innovative eco-friendly composite materials: A review. Journal of Thermoplastic Composite Materials, 33(7), 978–1013. [Google Scholar]
44. Nickels, L. (2018). Composites driving the auto industry. Reinforced Plastics, 62(1), 38–39. [Google Scholar]
45. Shiva Prasad, U., Babu, AR., Sairaju, B., Amirishetty, S., Deepak, D. (2020). Automotive chassis design material selection for road and race vehicles. Journal of Mechanical Engineering Research and Developments, 43(3), 274–282, ffhal-02519178f. [Google Scholar]
46. Rubino, F., Nisticò, A., Tucci, F., Carlone, P. (2020). Marine application of fiber reinforced composites: A review. Journal of Marine Science and Engineering, 8(1), 26. [Google Scholar]
47. Umoren, S. A., Solomon, M. M. (2019). Protective polymeric films for industrial substrates: A critical review on past and recent applications with conducting polymers and polymer composites/nanocomposites. Progress in Materials Science, 104, 380–450. [Google Scholar]
48. Yuhazri, M. Y., Zulfikar, A. J., Ginting, A. (2020). Fiber reinforced polymer composite as a strengthening of concrete structures: A review. IOP Conference Series: Materials Science and Engineering, vol. 1003, no. 1, 012135. IOP Publishing. [Google Scholar]
49. Subramanian, C. V., Ramachandran, N., Kumar, S. S. (2021). Performance evaluation of the designed solar passive architecture incorporated residence in warm humid climate. Transportation. [Google Scholar]
50. Yi, X. S. (2018). An introduction to composite materials. In: Composite materials engineering, volume 1: Fundamentals of composite materials, pp. 1–61. [Google Scholar]
51. Ramakrishnan, S., Loganayagan, S., Kowshika, G., Ramprakash, C., Aruneshwaran, M. (2021). Adobe blocks reinforced with natural fibres: A review. Materials Today: Proceedings, 45, 6493–6499. [Google Scholar]
52. Sanjay, M. R., Madhu, P., Jawaid, M., Senthamaraikannan, P., Senthil, S. et al. (2018). Characterization and properties of natural fiber polymer composites: A comprehensive review. Journal of Cleaner Production, 172, 566–581. [Google Scholar]
53. Akil, H., Omar, M. F., Mazuki, A. M., Safiee, S. Z. A. M., Ishak, Z. M. et al. (2011). Kenaf fiber reinforced composites: A review. Materials & Design, 32(8–9), 4107–4121. [Google Scholar]
54. Bourmaud, A., Beaugrand, J., Shah, D. U., Placet, V., Baley, C. (2018). Towards the design of high-performance plant fibre composites. Progress in Materials Science, 97, 347–408. [Google Scholar]
55. Stalin, B., Nagaprasad, N., Vignesh, V., Ravichandran, M., Rajini, N. et al. (2020). Evaluation of mechanical, thermal and water absorption behaviors of Polyalthia longifolia seed reinforced vinyl ester composites. Carbohydrate Polymers, 248, 116748. [Google Scholar] [PubMed]
56. Siakeng, R., Jawaid, M., Ariffin, H., Sapuan, S. M. (2019). Mechanical, dynamic, and thermomechanical properties of coir/pineapple leaf fiber reinforced polylactic acid hybrid biocomposites. Polymer Composites, 40(5), 2000–2011. [Google Scholar]
57. Ramlee, N. A., Jawaid, M., Zainudin, E. S., Yamani, S. A. K. (2019). Tensile, physical and morphological properties of oil palm empty fruit bunch/sugarcane bagasse fibre reinforced phenolic hybrid composites. Journal of Materials Research and Technology, 8(4), 3466–3474. [Google Scholar]
58. Liu, Y., Xie, J., Wu, N., Wang, L., Ma, Y. et al. (2019). Influence of silane treatment on the mechanical, tribological and morphological properties of corn stalk fiber reinforced polymer composites. Tribology International, 131, 398–405. [Google Scholar]
59. Nagarajan, S., Radhakrishnan, S., Kalkura, S. N., Balme, S., Miele, P. et al. (2019). Overview of protein-based biopolymers for biomedical application. Macromolecular Chemistry and Physics, 220(14), 1900126. [Google Scholar]
60. Tonk, R. (2021). Natural fibers for sustainable additive manufacturing: A state of the art review. Materials Today: Proceedings, vol. 37, pp. 3087–3090. [Google Scholar]
61. Chauhan, V., Kärki, T., Varis, J. (2019). Review of natural fiber-reinforced engineering plastic composites, their applications in the transportation sector and processing techniques. Journal of Thermoplastic Composite Materials, 0892705719889095. [Google Scholar]
62. Sanjay, M. R., Arpitha, G. R., Yogesha, B. (2015). Study on mechanical properties of natural-glass fibre reinforced polymer hybrid composites: A review. Materials Today: Proceedings, 2(4–5), 2959–2967. [Google Scholar]
63. Xiao, Y., Xu, P., Fan, H., Baudouin, L., Xia, W. et al. (2017). The genome draft of coconut (Cocos nucifera). Gigascience, 6(11), gix095. [Google Scholar]
64. Atoyebi, O. D., Osuolale, O. M., Ibitogbe, E. M. (2019). Strength evaluation of Cocos nucifera fibre reinforced concrete. Journal of Engineering and Applied Sciences, 14(21), 8061–8066. [Google Scholar]
65. Marimuthu, K. P., Kumar, S. M., Kumar, V. R., Govindaraju, H. K. (2019). Characterization of mechanical properties of epoxy reinforced with glass fiber and coconut fiber. Materials Today: Proceedings, 16, 661–667. [Google Scholar]
66. Gopinath, A., Senthilkumar, M., Babu, A. (2018). Evaluation of mechanical properties and microstructure of polyester and epoxy resin matrices reinforced with jute, E-glass and coconut fiber. Materials Today: Proceedings, 5(9), 20092–20103. [Google Scholar]
67. Somashekhar, T. M., Naik, P., Nayak, V., Rahul, S. (2018). Study of mechanical properties of coconut shell powder and tamarind shell powder reinforced with epoxy composites. IOP Conference Series: Materials Science and Engineering, vol. 376, no. 1, 012105. IOP Publishing. [Google Scholar]
68. Yashas Gowda, T. G., Sanjay, M. R., Subrahmanya Bhat, K., Madhu, P., Senthamaraikannan, P. et al. (2018). Polymer matrix-natural fiber composites: An overview. Cogent Engineering, 5(1), 1446667. [Google Scholar]
69. Badamasi, H., Ibrahim, A. (2017). Development and characterization of bio-composite: A review. 2ND International Conference on Green Engineering for Sustainable Development (IC-GESD 2017), Kano, Nigeria, Faculty of Engineering, Bayero University, Kano, Nigeria. [Google Scholar]
70. Johnson, R. D. J., Arumugaprabu, V., Rajasekar, E., Santhosh, G., Saravanakumar, M. (2018). Mechanical property studies on environmental friendly bio epoxy resin. Materials Today: Proceedings, 5(2), 6815–6820. [Google Scholar]
71. Lagel, M. C., Hai, L., Pizzi, A., Basso, M. C., Delmotte, L. et al. (2016). Automotive brake pads made with a bioresin matrix. Industrial Crops and Products, 85, 372–381. [Google Scholar]
72. Rajan, R., Tyagi, Y. K., Pruncu, C. I., Kulshreshtha, S., Ranakoti, L. et al. (2022). Tribological performance evaluation of slag waste filled phenolic composites for automotive braking applications. Polymer Composites, 43(10), 7118–7129. [Google Scholar]
73. Boey, J. Y., Lee, C. K., Tay, G. S. (2022). actors affecting mechanical properties of reinforced bioplastics: A review. Polymers, 14(18), 3737. [Google Scholar] [PubMed]
74. Yashwhanth, S., Mohan, M. M., Anandhan, R., Selvaraj, S. K. (2021). Present knowledge and perspective on the role of natural fibers in the brake pad material. Materials Today: Proceedings, 46, 7329–7337. [Google Scholar]
75. Park, J., Hwang, H., Kim, J. Y., Choi, J. W. (2020). Applicability of lignin polymers for automobile brake pads as binder and filler materials and their performance characteristics. Environmental Technology, 41(4), 488–497. [Google Scholar] [PubMed]
76. Al-Marzouki, F. M., Zahed, A., Pizzi, A., Abdalla, S. M. S. (2017). U.S. Patent No. 9,791,012. Washington DC: U.S. Patent and Trademark Office. [Google Scholar]
77. Rao, R. U., Babji, G. (2015). A review paper on alternate materials for Asbestos brake pads and its characterization. International Research Journal of Engineering and Technology, 2(2), 556–562. [Google Scholar]
78. Ikpambese, K. K., Gundu, D. T., Tuleun, L. T. (2016). Evaluation of palm kernel fibers (PKFs) for production of asbestos-free automotive brake pads. Journal of King Saud University-Engineering Sciences, 28(1), 110–118. [Google Scholar]
79. Ruzaidi, C. M., Kamarudin, H., Shamsul, J. B., M. M., A. (2011). Abdullah comparative study on thermal, compressive, and wear properties of palm slag brake pad composite with other fillers. Advanced Materials Research, 328–330, 1636–1641. [Google Scholar]
80. Ibhadode, A. O. A., Dagwa, I. M. (2008). Development of asbestos-free friction lining material from palm kernel shell. Journal of the Brazilian Society of Mechanical Sciences and Engineering, 30, 166–173. [Google Scholar]
81. Jadhav, S. P., Sawant, S. H. (2019). A review paper: Development of novel friction material for vehicle brake pad application to minimize environmental and health issues. Materials Today: Proceedings, 19, 209–212. [Google Scholar]
82. Ademoh, N. A., Olabisi, A. I. (2015). Development and evaluation of maize husks (asbestos-free) based brake pad. Development, 5(2), 67–80. [Google Scholar]
83. Olabisi, A. I., Adam, A. N., Okechukwu, O. M. (2016). Development and assessment of composite brake pad using pulverized cocoa beans shells filler. International Journal of Materials Science and Applications, 5(2), 66–78. https://doi.org/10.11648/j.ijmsa.20160502.16 [Google Scholar] [CrossRef]
84. Dirisu, J. O., Fayomi, O. S. I., Oyedepo, S. O., Udoye, N. E. (2021). Asbestos-free aluminium dross brake pad: A mini review. IOP Conference Series: Materials Science and Engineering, 1107(1), 012034. [Google Scholar]
85. Aigbodion, V. S., Akadike, U., Hassan, S. B., Asuke, F., Agunsoye, J. O. (2010). Development of asbestos-free brake pad using bagasse. Tribology in Industry, 32(1), 12. [Google Scholar]
86. Idris, U. D., Aigbodion, V. S., Abubakar, I. J., Nwoye, C. I. (2015). Eco-friendly asbestos free brake-pad: Using banana peels. Journal of King Saud University-Engineering Sciences, 27(2), 185–192. [Google Scholar]
87. Singh, T., Rathi, M. K., Patnaik, A., Chauhan, R., Ali, S. et al. (2018). Application of waste tire rubber particles in non-asbestos organic brake friction composite materials. Materials Research Express, 6(3), 035703. [Google Scholar]
88. Afolalu, S. A., Oladipupo, S., Bose, M. E., Abioye, A. A., Adejuyigbe, S. B. et al. (2019). Agro waste a sustainable source for steel reinforcement–review. Journal of Physics: Conference Series, 1378(3), 032032. [Google Scholar]
89. Borawski, A. (2020). Conventional and unconventional materials used in the production of brake pads–review. Science and Engineering of Composite Materials, 27(1), 374–396. [Google Scholar]
90. Mgbemena, C. O., Mgbemena, C. E., Okwu, M. O. (2014). Thermal stability of pulverized palm kernel shell (PKS) based friction lining material locally developed from spent waste. ChemXpress, 5(4), 115–122. [Google Scholar]
Cite This Article
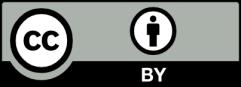
This work is licensed under a Creative Commons Attribution 4.0 International License , which permits unrestricted use, distribution, and reproduction in any medium, provided the original work is properly cited.