Open Access
ARTICLE
Effect of Adhesive Type on the Quality of Coconut Shell Charcoal Briquettes Prepared by the Screw Extruder Machine
1 Department of Mechanical Engineering, Faculty of Engineering, Universitas Negeri Semarang, Gunung pati, Semarang, 50229, Indonesia
2 Arka Tama Indonesia, Co., Ltd., Karawang, West Java, 41382, Indonesia
3 Department of Mechanical Engineering, Dili Institute of Technology, Ai-meti Laran Street, Dili, Timor Leste
* Corresponding Author: Samsudin Anis. Email:
(This article belongs to the Special Issue: Advanced Renewable Mineral and Energy Materials)
Journal of Renewable Materials 2024, 12(2), 381-396. https://doi.org/10.32604/jrm.2023.047128
Received 26 October 2023; Accepted 27 November 2023; Issue published 11 March 2024
Abstract
Indonesia is one of the largest coconut-producing countries in the world. The utilization of coconut shell waste into briquettes will increase the selling value and become a great export opportunity. However, the effect of adhesives on the quality of coconut shell charcoal briquettes made using screw extruder machine has not been widely studied. This study aims to determine the effect of adhesive type on the quality of coconut shell charcoal briquettes. The process of fabricating briquettes in this study included crushing, mixing, blending, pressing, and drying. In the mixing process, 3 types of adhesives were used, namely tapioca flour (Briquette_1), cassava flour (Briquette_2), and modified cassava flour (Briquette_3) with a concentration of 5% of the weight of coconut shell charcoal powders. The quality of the resulting briquettes and commercial briquettes will be evaluated by moisture content, ash content, volatile matter, fixed carbon, calorific value, density, compressive, and drop test testing. The results of this research showed that the type of adhesive had a significant effect on the quality of the briquettes produced. Specimen Briquette_1 had better quality than commercial briquettes (Briquette_4) and other briquette specimens. The test results showed that Briquette_1 produced briquettes with better compressive strength and friability than the other specimens, at 6.95 N/mm2 and 4.44%, respectively. The moisture content, ash content, fixed carbon, and calorific value of Briquette_1 have met the requirements set by the Indonesian National Standard (SNI) number 01-6235-2000. Meanwhile, the volatile matter content and density of Briquette_1 are by the standards of Japan and the United States America (USA).Graphic Abstract
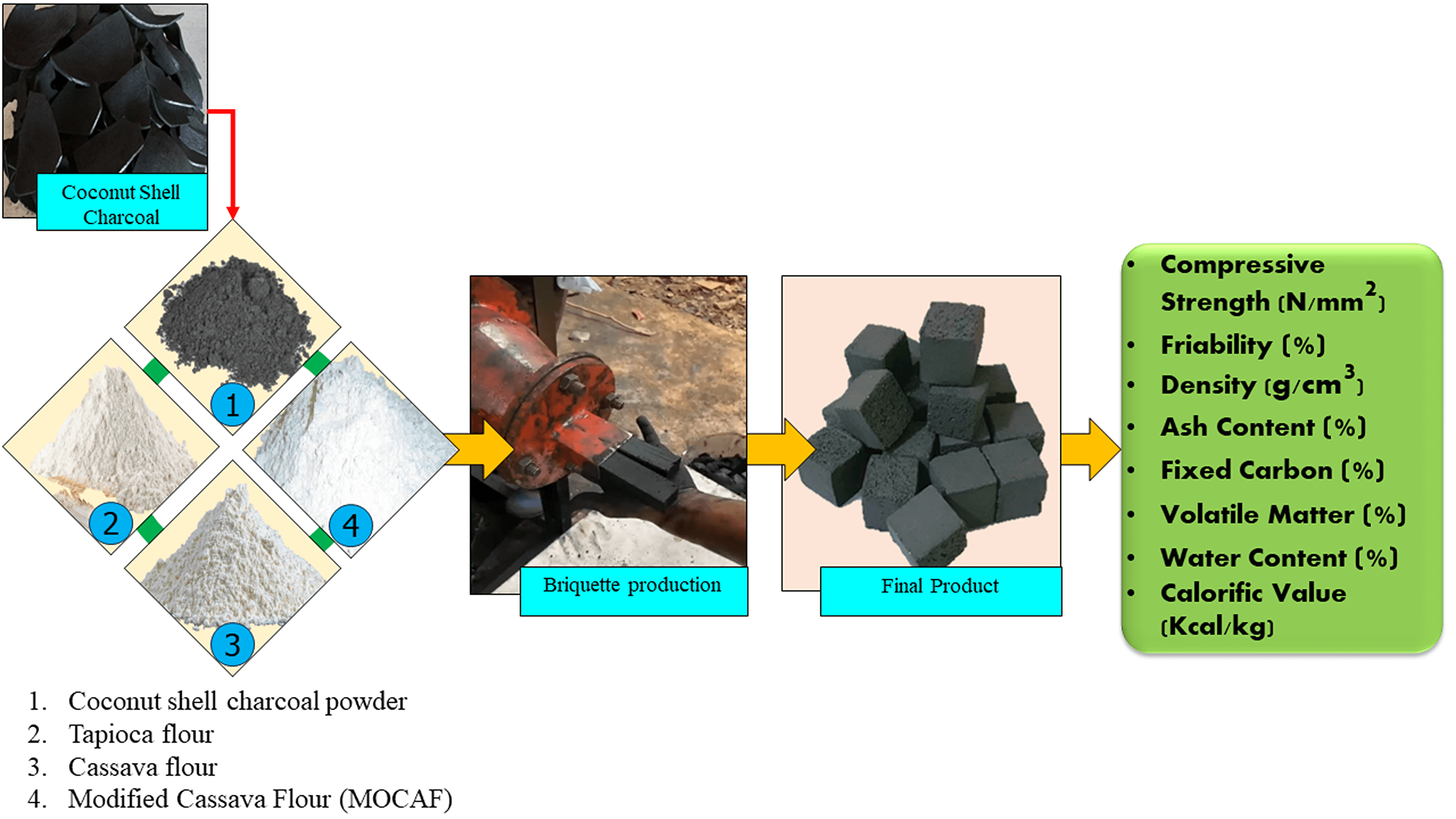
Keywords
Indonesia has the biggest global expanse of coconut farms, encompassing over 3.88 million hectares. The production of coconuts holds significant significance in the national economy of Indonesia, positioning the country as the second-largest global producer of this agricultural commodity [1,2]. Indonesia possesses a cumulative expanse of 3.6 million hectares dedicated to coconut plantations, with around 90 per cent of this land being managed by small-scale farmers [3]. The total land area dedicated to coconut plantations in Indonesia is around 3,343,000 hectares, while the quantity of coconut fruit harvested from small-scale farms amounted to 2,822,000 tonnes [4,5]. According to the cited source, the composition of a coconut fruit includes three main components: meat, coir, and shell.
It is reported that each of these components accounts for 28%, 35%, and 12% of the coconut fruit, respectively [6]. The cumulative quantity of coconut shells generated amounts to 338,640,000 metric tons.
The utilization of coconut shell waste presents opportunities for the production of many commodities, including handicrafts, coconut shell charcoal, and briquettes. This practice might potentially generate supplementary income for farmers. The utilization of coconut shells has promise to enhance farmers’ economic opportunities by means of producing coconut shell charcoal and briquettes. The creation of coconut shell charcoal and briquettes has the potential to make a valuable contribution to both the local and global circular economy. This is achieved through the generation of coconut shell and husk biochar, which can be utilized for economic advancement and environmental enhancement [7–9].
The manufacture of coconut shell charcoal briquettes will improve the appearance of coconut shells so that they have a selling value and become a great export opportunity. Briquettes are fuels made from organic materials in the form of solids or blocks that are made by using pressure so that briquette solids can be formed. Briquettes have advantages, including high heat generation, smokeless, non-toxic, longer flame, and environmentally friendly [8,10] Coconut shell charcoal briquettes produced in Indonesia have been distributed and marketed in several regions, including Europe, America, and the Middle East. Coconut shell charcoal briquette production has emerged as a thriving industry in Indonesia, with its goods being extensively exported to numerous nations across the globe [11].
Coconut shell charcoal briquettes exhibit varying applications across diverse regions of the country. Coconut shell charcoal briquettes are a prevalent fuel source for barbeque purposes across the European region. In the Middle East region, briquettes serve as a primary source of fuel for sissa. The Sissa is a conventional water pipe commonly employed in the Middle Eastern region to smoke flavoured tobacco [12,13] Indonesian coconut shell charcoal briquettes are in high demand due to their high calorific value, which ranges from 6,161 to 7,110 calories per gram [14–16]. The manufacturing process of coconut shell charcoal briquettes includes multiple steps, varying depending on the particular production methodology employed. Briquette production typically involves a series of phases, including carbonation, crushing, mixing, blending, molding, and drying [17,18]. The utilization of tapioca starch as an adhesive in the production of briquettes derived from coconut shell charcoal has been widely conducted [19,20].
Tapioca starch has many advantages as an adhesive in the briquetting procedure, including its ability to biodegrade, classified as a renewable resource, non-toxic characteristics, and cost efficiency. The material has good adhesive properties, produces few combustion by-products, and offers flexibility for formulation modifications [21,22] However, the material’s susceptibility to moisture and its limited ability to withstand high temperatures can be considered a disadvantage. In addition, there may be concerns regarding microbial proliferation, limited compatibility, and inconsistent quality [22–24].
Hence, the present investigation involved the production of briquettes derived from coconut shell charcoal by the utilization of diverse adhesive agents. The adhesives employed in this study encompass tapioca flour, cassava flour, and modified cassava flour. The objective of this study is to investigate the impact of different adhesive types on several attributes of coconut shell charcoal briquettes, encompassing moisture content, ash content, volatile matter, bound carbon, calorific value, density, drop test performance, and compressive strength. Furthermore, the coconut shell charcoal briquettes manufactured by PT Arka Tama Indonesia will undergo testing procedures, and the outcomes of these tests will serve as a benchmark for evaluating the quality of the coconut shell charcoal briquettes produced.
The coconut shell charcoal (Fig. 1) used in this study was obtained from a local charcoal producer located in Tuntang District, Semarang Regency, Central Java, Indonesia. This coconut shell charcoal has an ash content, moisture content, fixed carbon, and calorific value of 3%, 15%, 73%, and 7.744 kcal/kg, respectively.
Figure 1: Coconut shell charcoal
In this study, tapioca flour, cassava flour, and modified cassava flour (mocaf) were used as adhesives in the manufacture of briquettes made from coconut shell charcoal. Tapioca flour consists of approximately 17% amylose, which serves as an effective binding agent through its ability to absorb water and produce a dense gel with high viscosity, thereby increasing water and moisture retention [25]. The pH level, moisture content, amount of carbohydrates, density, and viscosity of tapioca flour were measured to be 4.7–5.3, 10%–13.5%, 86.55%, 0.610 (g/cm3), and 9.77 (cSt), respectively [26–28]. Cassava flour, which is obtained from the roots of the cassava plant through several processing steps, is a highly valuable commodity. Due to its characteristic advantages, such as its transparent visual quality, lack of objectionable taste, and ideal viscosity, it is widely recognized as an essential component in the field of food production. The pH level, moisture content, amount of carbohydrates, density, and viscosity of cassava flour were measured to be 5.5 to 8.5, 6.34%–14.58%, 26%–27%, 0.57–0.79 (g/cm3), and 2697.67–3667.00 (Cp), respectively [29,30]. Modified Cassava Flour (MOCAF) is a cassava flour product processed using the principle of modifying cassava cells by fermentation using LAB (Lactic Acid Bacteria) microbes. Mocaf has a starch content of 85%–87%. The moisture content, amount of carbohydrates, and viscosity of mocaf were measured to be 13.3%–13.8%, 60%, and 70 (Cp), respectively [31,32].
The process of making charcoal briquettes from coconut shells involved several well-organised steps, as shown in Fig. 2. The coconut shells were turned into coconut shell charcoal powder with a size of 40 mesh using a disk mill machine. Next, the coconut shell charcoal powder was mixed with water and adhesive using a mixer machine. In this study, the water and adhesive content used were 25% and 5%, respectively. The specimen codes used in this study are shown in Table 1. The product obtained from the mixer process was blended using a screw extruder machine with a repetition of 3 times. The process of making coconut shell charcoal briquettes used a screw extruder machine at 1650 rpm. The briquettes formed were cut manually with a size of 2.5 cm × 2.5 cm × 2.5 cm. The drying process was carried out using an oven at a temperature of 100°C for 3 h. To determine the effect of the type of adhesive used on the quality of coconut shell charcoal briquettes produced, in this study, proximate testing (moisture content, ash content, volatile matter, and bound carbon), calorific value testing, density, drop test, and compressive testing were carried out. The same tests were also carried out on coconut shell charcoal briquettes made by PT Arka Tama Indonesia.
Figure 2: Experiment setup
In this study, moisture content was tested in briquettes by ASTM D-3173-17. While testing ash content, volatile matter, and fixed carbon is done by ASTM D-3174-12, ASTM D-3175-17, and ASTM D-3172-13. Furthermore, calorific value testing was carried out following ASTM D-240. Density testing on the briquettes produced in this study was carried out following ASTM B-311-17. The drop test was conducted by dropping the coconut shell charcoal briquettes at a height of 1.83 m onto a hard surface. The drop test was conducted to determine the size stability of the briquettes produced. This test refers to ASTM D-440-07 R02. The compressive test is a test conducted to determine the strength capacity of the material against the applied pressure. Compressive testing is carried out by placing the specimen on a universal testing machine and pressing until deformation occurs on the briquette with a constant pressure in the pressure range of 2–4 kg/cm2 per s [33].
The water content of a briquette is the amount of water contained in a briquette [18,34]. A high-water content will affect the calorific value of the briquettes. In addition, high water content in briquettes will result in the appearance of cracks, making the briquettes unstable. This will cause problems when the briquettes are stored and distributed [35,36]. Fig. 3 shows the effect of adhesive type variation on the water content of briquette specimens from coconut shell charcoal. Based on the test results, it can be seen that the water content of each briquette specimen is different. The test results of water content (%) for Briquette_1, Briquette_2, Briquette_3, and Briquette_4 specimens were 6.80, 6.46, 2.96, and 4.97, respectively. The difference in water content results was due to differences in the characteristics of the types of briquette adhesive. The findings of this study are consistent with those of Wahyuni et al.’s study, which found that the type of adhesive used can affect the moisture content of briquettes, indicating that the adhesive eventually controls the moisture content of the briquettes that are formed [33]. The water content of briquettes with tapioca flour adhesive (Briquette_1) was higher than briquettes using cassava flour and mocaf. This is because tapioca flour generally has a higher moisture content than cassava flour and mocaf.
Figure 3: Effect of adhesive type on water content of briquette specimens
Some literature states that good quality tapioca flour, cassava flour, and mocaf should have a maximum moisture content of 10%–13.5% [26], 10.38% [37], and 9.34% [38], respectively. Water content in this range can ensure microbial stability during the storage of tapioca flour, cassava flour, and mocaf. So that flour storage becomes more effective and does not experience damage during storage [37,38]. In addition, tapioca flour is known to have high water absorption compared to cassava flour and mocaf [39,40]. Thus, briquettes with tapioca flour adhesive produced the highest moisture content compared to other specimens. The results of this study indicated that the water content in all coconut shell charcoal briquette specimens had met the criteria of Indonesian National Standard (SNI) number 01-6235-2000 with a standard water content of <8% [41].
The ash content in briquette specimens made from coconut shell charcoal is the residue resulting from combustion during combustion [34,42,43]. Fig. 4 shows the effect of types of adhesives on the ash content of briquette specimens made from coconut shell charcoal.
Figure 4: Effect of adhesive type on ash content of briquette specimens
The type of adhesive used affects the ash content of the briquettes produced [44,45]. The main element of ash is the mineral silica, and it hurts the calorific value produced, so the higher the ash content, the lower the quality of the briquettes [44,45]. The ash content test results for Briquette_1, Briquette_2, Briquette_3, and Briquette_4 specimens were 1.93%, 1.71%, 2.23%, and 1.87%, respectively. This research found that the highest ash content was produced from Briquette_3 with a mocaf adhesive of 2.23%, and the lowest ash content was produced from Briquette_2 with a cassava flour adhesive of 1.71%. The difference in test results was due to the different ash content of each adhesive. Research conducted by Asmoro et al. (2021) stated that the ash content in tapioca flour and cassava flour is relatively the same, namely 1.1%, while the ash content in mocaf is 1.3% [46]. In addition, previous research shows that the ash content in mocaf is 1.54%–2.3% [47]. While in cassava flour, the ash content was found to be 1.01%–2.06% [48]. The results of this study indicate that the ash content in all coconut shell charcoal briquette specimens has met the criteria of Indonesian National Standard (SNI) number 01-6235-2000 with a standard ash content of <8% [41].
Volatile matter is a substance that can evaporate as a result of the decomposition of compounds still present in the briquette, in addition to moisture content, bound carbon, and ash content [49]. Volatile matter is an indicator of the quality of briquettes consisting of hydrogen, carbon monoxide (CO), methane (CH4), CO2, and H2O [50]. Fig. 5 shows the comparison of volatile matter in briquette specimens made using different adhesives. Volatile matter in specimens of Briquette_1, Briquette_2, Briquette_3, and Briquette_4 specimens were 21.78%, 21.53%, 19.03%, and 17.25%, respectively. The results of this study showed that the volatile matter content of briquettes is influenced by the type of adhesive used [36]. Research conducted by Tambunan et al. showed that the type and percentage of adhesive in the manufacture of charcoal briquettes greatly affects the volatile matter content of the briquettes. The high volatile matter will accelerate the combustion of carbon materials so that the carbon content produced is lower and the smoke produced is more during combustion [51]. Furthermore, the high volatile matter concentration indicates that the fuel sample is ready to ignite with a proportionate flame throughout the combustion process [52]. However, volatile matter in all briquette specimens produced in this study does not meet the criteria of Indonesian National Standard (SNI) number 01-6235-2000 which determines the standard of volatile matter in briquettes of <15% [41]. However, the results of this study have met the standards of Japan and United States of America (USA) with volatile matter in the range of 15% to 30% and 19% to 28% [53].
Figure 5: Effect of adhesive type on volatile matter of briquette specimens
Fig. 6 shows the effect of varying types of adhesives on the value of fixed carbon in briquette specimens made from coconut shell charcoal. The results showed that the fixed carbon of the briquette specimens was influenced by the type of adhesive used.
Figure 6: Effect of adhesive type on fixed carbon of briquette specimens
Fixed carbon in Briquette_1, Briquette_2, Briquette_3, and Briquette_4 specimens were 76.75%, 69.18%, 78.74%, and 80.88%, respectively. The highest fixed carbon was found in the commercial briquette (Briquette_4) specimen. While the specimen with the lowest fixed carbon was found in specimen 2. This happened because the commercial briquette specimen had the lowest volatile matter compared to other specimens. While Briquette_2 was the specimen that had the highest volatile matters. The higher the volatile matters, the lower the fixed carbon and conversely [54–57].
Fixed carbon is the carbon remaining in the charcoal briquette after the volatile matter is removed. Therefore, if a charcoal briquette has a higher volatile substance content, it will lose more of its original mass, which results in a lower percentage of fixed carbon in the final product. The increase in fixed carbon content may be due to the increased interlock of the coconut shell charcoal particles and the adhesive during the briquetting process. The higher the fixed carbon content, the higher the briquette quality [50,58]. Fixed carbon produced in all briquette specimens made from coconut shell charcoal has met the criteria of Japanese standards, with fixed carbon in the range of 60% to 80% [53].
Fig. 7 shows the effect of different types of adhesives on the calorific value of briquettes made from coconut shell charcoal. Based on the test results, it can be seen that the calorific value of each briquette specimen is influenced by the type of adhesive used [59,60]. The calorific value (Kcal/kg) of Briquette_1, Briquette_2, Briquette_3, and Briquette_4 specimens were 7,040; 7,003; 7,181; and 7,014, respectively. The results of this study showed that Briquette_3 produced the highest calorific value compared to the other specimens. This happened because Briquette_3 was the specimen with the lowest water content. The lower the water content, the higher the calorific value of the briquette [61]. Water is a material that has a high specific heat capacity. This indicates that water requires a large amount of energy to raise its temperature [62,63]. High water content in briquettes can lead to inefficient combustion as energy is used to vaporize the water and not released as heat. Incomplete combustion can reduce the effective calorific value [64]. Therefore, an increase in the water content of coconut shell charcoal briquettes will decrease their calorific value because some of the energy is spent on evaporating water rather than generating heat and conversely [65]. Handra et al. discovered that the more adhesive applied, the higher the water content of the briquettes. This drastically decreases the calorific value of the briquettes. Because of the high-water content, the briquettes will be difficult to ignite and thus tough to burn. Briquettes with excessive water will need more air to dry, making them hard to burn [65]. The results of this study indicate that the calorific value of all briquette specimens made from coconut shell charcoal has met the criteria of Indonesian National Standard (SNI) number 01-6235-2000, with a standard calorific value of >5000 Kcal/kg [41].
Figure 7: Effect of adhesive type on calorific value of briquette specimens
The results of this study indicated that the density of briquettes produced was influenced by the use of adhesive types (Fig. 8). In general, the use of adhesives in the production of charcoal briquettes was to improve their physical properties. The addition of adhesives can increase the density of the briquettes so that the briquettes become denser and easier to handle. The density (g/cm3) produced in Briquette_1, Briquette_2, Briquette_3, and Briquette_4 specimens were 1.003; 1.010; 0.905, and 0.900, respectively. The highest density was found in Briquette_2. While the lowest density was found in the commercial briquette (Briquette_4) specimen.
Figure 8: Effect of adhesive type on density of briquette specimens
The results of this study showed that the density of all briquette specimens met the minimum density determined by the British standard of 0.48 g/cm3. However, briquette specimens that met Japanese standards were only Briquette_1 and Briquette_2. This was because the density of briquettes based on Japanese standards was in the range of 1 to 2 g/cm3.
In addition, Briquette_1 and Briquette_2 produced in this study also had a density determined by the USA standard of ≥1 g/cm3 [34,53]. Research conducted by Carnaje et al. states that density affects the combustion efficiency and durability of briquettes. In general, consumers prefer briquettes with high density. This is because briquettes with high density facilitate the processes of transportation, distribution, and storage [66].
Fig. 9 shows the effect of adhesive type on the compressive strength of briquettes made from coconut shell charcoal. The results of this study showed that the type of adhesive affects the compressive strength of the briquettes produced. The compressive strength (N/mm2) for Briquette_1, Briquette_2, Briquette_3, and Briquette_4 specimens were 6.95; 3.59; 2.13, and 3.26, respectively. The highest compressive strength was found in Briquette_1. While Briquette_3 had the lowest compressive strength. The results of this study showed that only Briquette_1 had a compressive strength that met Japanese standards, which was 60 to 65 kg/cm2 or 5.88 to 6.37 N/mm2 [67].
Figure 9: Effect of adhesive type on compressive strength of briquette specimens
In another study, it was mentioned that the compressive strength of coal briquettes that is suitable for the industry is 3.8 kg/cm2. Based on this standard, all briquette specimens produced in this study have met the standard for industrial applications. This is because all briquette specimens produced in this study have a compressive strength greater than 3.8 kg/cm2 [68]. The resistance of charcoal briquettes to external pressure, which has the potential to cause fracture or disintegration, is directly dependent on their compressive strength. A greater value of compressive strength signifies a heightened ability to withstand external pressure, consequently reducing the likelihood of the charcoal briquettes being damaged. Furthermore, briquettes exhibiting high compressive strength are characterized by increased hardness and enhanced manageability, facilitating their transportation and storage. Augmenting the compressive strength can also fortify the durability of the briquettes by impeding water absorption capacity, thereby shortening their lifespan [69,70].
In this study, the drop test on briquettes was carried out when the briquettes were unburned and had burned completely or were red. The drop test was used to obtain the level of destruction of briquettes, namely the level of destruction or separation of briquette particles due to impact after being dropped at a height of 1.83 m. The drop test results will obtain the size stability and friability of the coconut shell charcoal briquette specimen. In this study, the drop test was carried out with three repetitions and then calculations were made to determine the average value of size stability (%) and friability (%) of the briquette specimens. Size stability (%) in briquette specimens was obtained by comparing the weight of briquettes after dropping (g) and the weight of briquettes before dropping (g).
Meanwhile, the friability or lost particles (%) in the briquette specimen was obtained from 100% minus the size stability in the briquette specimen. The greater the size stability and the smaller the friability, the less mass was lost during the testing process. This showed that the quality of the briquettes produced was getting better. The results of the drop test on briquette specimens are shown in Table 2.
In the unburned condition, the friability (%) of Briquette_1, Briquette_2, Briquette_3, and Briquette_4 specimens were 0, 0.47, 0.63, and 0.71, respectively. While the size stability (%) in Briquette_1, Briquette_2, Briquette_3, and Briquette_4 specimens were 100, 99.53, 99.37, and 99.29, respectively. The best size stability (%) and friability (%) when the briquettes were not burned were found in Briquette_1. This was because Briquette_1 produces the most stable size and lowest friability compared to the other specimens. Based on the reference, the maximum friability limit on charcoal briquettes is <4% [71]. The results of this study showed that the friability (%) of all coconut shell charcoal briquette specimens before burning was still lower than the maximum friability limit. This showed that all specimens of coconut shell charcoal briquettes before being burned had good friability (%).
Under fully burnt conditions, the friability of Briquette_1, Briquette_2, Briquette_3, and Briquette_4 specimens were 4.44%, 63.98%, 58.7%, and 15.05%, respectively. While the size stability of Briquette_1, Briquette_2, Briquette_3, and Briquette_4 specimens were 95.56%, 36.02%, 41.38%, and 4.95%, respectively. The best size stability (%) and friability (%) when the briquettes were fully burnt were found in Briquette_1. This was because specimen 1 produced the most stable size and lowest friability compared to the other specimens. This happened because when the specimens burned, Briquette_2 and Briquette_3 experienced cracks. Meanwhile, Briquette_1 did not have any cracks appearing when the briquettes were burnt, as seen in Fig. 10.
Figure 10: Briquette specimens (a) Briquette_1, (b) Briquette_2, and (c) Briquette_1 are in the fully burnt condition
The cracks formed in Briquette_2 and Briquette_3 when the briquettes burned completely caused the briquettes to break during the drop test. This resulted in low size stability (%) and high brittleness (%) in specimens 2 and 3. The results of this study showed that the friability (%) of all coconut shell charcoal briquette specimens when burning completely was higher than the maximum friability limit of <4%. However, Briquette_1 produced the friability (%) that was closest to the predetermined maximum friability limit of <4% [71]. Tapioca flour has a higher adhesion than cassava flour and mocaf in the production of coconut shell charcoal briquettes. Due to its chemical composition and physical characteristics, tapioca flour demonstrates a higher adhesion level than cassava flour and mocaf during the production process of coconut shell charcoal briquettes. Tapioca flour possesses a notable abundance of amylose and amylopectin, both of which are extensive chains of glucose molecules that can establish robust connections with other substances. Additionally, tapioca flour exhibits a lower gelatinization temperature, leading to its dissolution and the formation of a sticky paste at temperatures lower than that of cassava flour and mocaf. This favourable attribute facilitates seamless amalgamation with other materials and fosters the formation of a potent interaction. Conversely, cassava flour and mocaf contain a lower amylose content and higher gelatinization temperatures, potentially resulting in diminished adhesion and mechanical strength of the briquettes. This causes the briquettes with tapioca flour to adhere more tightly between the particles. Therefore, the briquettes produced are still strong after the drop test. Briquettes using cassava flour and mocaf adhesives were weaker due to lower adhesion [21,72,16].
The production of coconut shell charcoal briquettes using tapioca flour, cassava flour, and mocaf as an adhesive in this research was successfully carried out using a screw extruder machine. This research investigated the effect of the type of adhesive on the quality of the coconut shell charcoal briquettes produced. The results of this research showed that the type of adhesive used significantly influences the quality of the coconut shell charcoal briquettes produced. The type of adhesive used can affect the various properties of coconut shell charcoal briquettes, including proximate, ultimate, physical, and mechanical characteristics. The results of this research showed that the moisture content, ash content, fixed carbon, and calorific value of all briquette specimens had met the requirements determined by the Indonesian National Standard (SNI) number 01-6235-2000. In addition, the volatile matter and density produced in all coconut shell charcoal briquette specimens had met the criteria determined by Japanese and American standards. All briquette specimens produced in this study had met standards for industrial applications because the compressive strength produced in all specimens exceeded 3.8 kg/cm2. However, only specimen 1 had a compressive strength that met the Japanese standard of 5.88 to 6.37 N/mm2.
The use of tapioca flour in Briquette_1 produced the best size stability (%) and friability (%) compared to other specimens, both in unburned and completely burned conditions. Tapioca flour had greater adhesion than cassava flour and mocaf in the production of coconut shell charcoal briquettes. This caused the briquettes with tapioca flour to adhere more tightly between the particles. Therefore, the briquettes produced were still strong after the drop test. Briquettes using cassava flour and mocaf adhesives were weaker due to lower adhesion. The results of the drop test showed that Briquette_1 produced the friability (%) that was closest to the predetermined maximum friability limit of <4%.
Acknowledgement: The authors would like to thank Universitas Negeri Semarang (UNNES) for allocating funds under the Penelitian Terapan Kepakaran Scheme in 2023 with Contract Number 226.12.4/UN37/PPK.10/2023.
Funding Statement: This study was funded by the Universitas Negeri Semarang (UNNES) with Grant No. 226.12.4/UN37/PPK.10/2023.
Author Contributions: The authors confirm contribution to the paper as follows: study conception and design: Samsudin Anis, Deni Fajar Fitriyana; data collection: Muhammad Choirul Anwar, Arsyad Zanadin Ramadhan, Fajar Chairul Anam; analysis and interpretation of results: Mateus De Sousa Da Silva, Aldias Bahatmaka, Ahmad Jazilussurur Hakim; draft manuscript preparation: Raffanel Adi Permana, Natalino Fonseca Da Silva Guterres. All authors reviewed the results and approved the final version of the manuscript.
Availability of Data and Materials: Data available within the article.
Conflicts of Interest: The authors declare that they have no conflicts of interest to report regarding the present study.
References
1. Alouw, J. C., Wulandari, S. (2020). Present status and outlook of coconut development in Indonesia. IOP Conference Series: Earth Environmental Science, 418, 1–10. https://doi.org/10.1088/1755-1315/418/1/012035 [Google Scholar] [CrossRef]
2. Multi-Spices (2023). The outlook of Indonesia’s coconut plantation. https://www.multispices.com/post/the-outlook-of-indonesia-s-coconut-plantation (accessed on 07/09/2023). [Google Scholar]
3. Coca, N. (2023). Revitalising coconut farming in Southeast Asia. https://chinadialogue.net/en/food/revitalising-coconut-farming-in-southeast-asia/ (accessed on 07/09/2023). [Google Scholar]
4. Statista Research Department (2022). Coconut production in Indonesia 2013–2022. https://www.statista.com/statistics/706968/coconut-production-in-indonesia/ (accessed on 07/09/2023). [Google Scholar]
5. APPERTANI (2023). Policy brief regarding whole coconut exports. https://appertani.org/?p=1482&lang=en (accessed on 07/09/2023). [Google Scholar]
6. Deo, M. M., Mathew, A. C., Manikantan, M. R., Hebbar, K. B. (2020). Performance evaluation of semi-automatic coconut de-husking machine for west coast tall variety of coconut. International Journal of Current Microbiology and Applied Sciences, 9(6), 3187–3194. https://doi.org/10.20546/ijcmas.2020.906.381 [Google Scholar] [CrossRef]
7. Priyanata, I., Broto, B. E., Siregar, N. A. (2022). Utilizing coconut shell waste into a crafts and driving economic income in the COVID pandemic in berangir plantation village. Quantitative Economics and Management Studies, 3(5), 789–794. https://doi.org/10.35877/454RI.qems1016 [Google Scholar] [CrossRef]
8. Ajien, A., Idris, J., Md Sofwan, N., Husen, R., Seli, H. (2023). Coconut Shell and Husk Biochar. A review of production and activation technology, economic, financial aspect and application. Waste Management & Research, 41(1), 37–51. https://doi.org/10.1177/0734242X221127167 [Google Scholar] [PubMed] [CrossRef]
9. Gunawan, S., Nursanni, B., Januariyansah, S., Suprapto, S. (2022). Comparative calorific analyzes of coconut shell and durian fruit peel by using differential scanning calorimetry. Jurnal Rekayasa Mesin, 13(3), 731–739. https://doi.org/10.21776/jrm.v13i3.1110 [Google Scholar] [CrossRef]
10. Arafah, A. D., Harsono, S. (2021). Analysis the effect of coconut shell charcoal mixed doses and adhesive in characteristics jamu dregs briquettes. Berkala Sainstek, 9(4), 179–185. https://doi.org/10.19184/bst.v9i4.27326 [Google Scholar] [CrossRef]
11. Anita, D. C., Wulandari, R., Nugroho, H. S. (2020). Upgrading charcoal briquettes of coconut shell for export. Jurnal Pemberdayaan Masyarakat Madani (JPMM), 4(1), 323–334. https://doi.org/10.21009/JPMM.004.1.02 [Google Scholar] [CrossRef]
12. Sibarani, C. G. G. T. (2022). Wasted of young coconut shell and skins as an alternative polybag and charcoal bricket. Journal of Community Research and Service, 6(1), 1–4. https://doi.org/10.24114/jcrs.v6i1.31058 [Google Scholar] [CrossRef]
13. Osfaldo, D., Rusnadi, I., Fatria, Syarif, A. (2022). Evaluation of the quality of combustion test biobricket coal char gasification with coconut shell charcoal. Jurnal Pendidikan Dan Teknologi Indonesia, 2, 1–11. https://doi.org/10.31764/orbita.v6i2.2645 [Google Scholar] [CrossRef]
14. Tsani, R., Mauluddin, F., Tinambunan, R. C., Maulani, S. (2022). Analysis of the quality of briquette charcoal products on the needs of export markets in the Middle East and Europe of PT. Nudira Sumber Daya Indonesia. Jurnal Ekonomi Dan Bisnis, 11, 1214–1224. https://doi.org/10.34308/eqien.v11i03.1009 [Google Scholar] [CrossRef]
15. Dalimunthe, Y. K., Kasmungin, S., Satiawati, L., Madani, T., Rizky, T. A. (2021). Analysis of the quality of mixed coconut shell waste briquettes with various biomass additives as alternative fuels. Journal of Earth Energy Science, Engineering, and Technology, 4, 1–6. https://doi.org/10.25105/jeeset.v4i2.9118 [Google Scholar] [CrossRef]
16. Rudiyanto, B., Agustina, I., Ulma, Z., Prasetyo, D., Hijriawan, M. et al. (2023). Utilization of cassava peel (Manihot utilissima) waste as an adhesive in the manufacture of coconut shell (Cocos nucifera) charcoal briquettes. International Journal of Renewable Energy Development, 12, 270–276. https://doi.org/10.14710/ijred.2023.48432 [Google Scholar] [CrossRef]
17. Sulistyaningkarti, L., Utami, B. (2017). Making charcoal briquettes from corncobs organic waste using variation of type and percentage of adhesives. Jurnal Kimia Dan Pendidikan Kimia, 2, 1–11. https://doi.org/10.20961/jkpk.v2i1.8518 [Google Scholar] [CrossRef]
18. Hamzah, F., Fajri, A., Harun, N., Pramana, A. F. (2023). Characterization of charcoal briquettes made from rubber rods and coconut shells with tapioca as an adhesive. IOP Conference Series: Earth and Environmental Science, 1182, 1–6. https://doi.org/10.1088/1755-1315/1182/1/012071 [Google Scholar] [CrossRef]
19. Widodo, S., Astriani, A., Asmiani, N. (2019). Utilising of canary shell as the material of bio-briquette. International Journal of Engineering, 6, 31–38. [Google Scholar]
20. Lamido, S. I., Habib, M., Oloboh, S. C. (2023). Application of 2K full factorial on the production of charcoal briquettes made from coconut shell. Global Journal of Engineering and Technology Advances, 16(2), 173–179. https://doi.org/10.30574/gjeta.2023.16.2.0153 [Google Scholar] [CrossRef]
21. Pulungan, M. A., Siahaan, S., Benu, S. M. (2023). Analysis of the effect of tapioca flour adhesive on the characteristics of palm oil empty charcoal briquettes. International Journal of Research in Vocational Studies (IJRVOCAS), 2(4), 8–12. https://doi.org/10.53893/ijrvocas.v2i4.156 [Google Scholar] [CrossRef]
22. Syarief, A., Nugraha, A. B., Ramadhan, M. N., Fitriyadi, Supit, G. G. (2021). The effect of the percentage of alaban waste and rice husk waste with tapioca adhesive on the physical properties. IOP Conference Series: Earth and Environmental Science, 758, 1–9. https://doi.org/10.1088/1755-1315/758/1/012019 [Google Scholar] [CrossRef]
23. Defri, I., Irfansyah, A., Sudarsono, S. N., dan Erwan, A. S. (2021). Review: Sorbitol manufacture technology from tapioca flour using catalytic hydrogenation process. Atmosphere, 2(2), 8–14. https://doi.org/10.36040/atmosphere.v2i2.4314 [Google Scholar] [CrossRef]
24. Anggoro, D. D., Wibawa, M. H. D., Fathoni, M. Z. (2018). Pembuatan briket arang dari campuran tempurung kelapa dan serbuk gergaji kayu sengon. Teknik, 38(2), 76–80. https://doi.org/10.14710/teknik.v38i2.13985 [Google Scholar] [CrossRef]
25. Nimitkeatkai, H., Pasada, K., Jarerat, A. (2022). Incorporation of tapioca starch and wheat flour on physicochemical properties and sensory attributes of meat-based snacks from beef scraps. Foods, 11(7), 1034. https://doi.org/10.3390/foods11071034 [Google Scholar] [PubMed] [CrossRef]
26. Riaz, M. N. (2016). Snack foods: Processing. In: Wrigley, C., Corke, H., Seetharaman, K., Faubion, J. B. T. E. F. G. (Eds.Encyclopedia of food grains (2nd edition), pp. 414–422. Oxford: Academic Press. [Google Scholar]
27. Widati, A. S., Mustakim, M., Widyastuti, E. S., Evanuarini, H., Amertaningtyas, D. et al. (2022). The effect of the use of different types and levels of tapioca flour on the physical quality of rabbit meatballs. Jurnal Ilmu Dan Teknologi Hasil Ternak, 17(1), 27–33. https://doi.org/10.21776/ub.jitek.2022.017.01.4 [Google Scholar] [CrossRef]
28. Nandiyanto, A. B. D., Ragadhita, R., Ana, A., Hammouti, B. (2022). Effect of starch, lipid, and protein components in flour on the physical and mechanical properties of indonesian biji ketapang cookies. International Journal of Technology, 13(2), 432–443. https://doi.org/10.14716/ijtech.v13i2.5208 [Google Scholar] [CrossRef]
29. Verma, R., Chauhan, N., Singh, B. R., Chandra, S., Sengar, R. S. (2022). Evaluation of physicochemical and flow properties of cassava flour. The Pharma Innovation Journal, 11, 190–196. [Google Scholar]
30. Hasmadi, M., Harlina, L., Jau-Shya, L., Mansoor, A. H., Jahurul, M. H. A. et al. (2020). Physicochemical and functional properties of cassava flour grown in different. Food Research, 4(4), 991–999. https://doi.org/10.26656/fr.2017.4(4).405 [Google Scholar] [CrossRef]
31. Sulistyo, J., Nakahara, K. (2014). Physicochemical properties of modified cassava starch prepared by application of mixed microbial starter. International Journal of Research in Agriculture and Food Sciences, 2(7), 1–9. [Google Scholar]
32. Diniyah, N., Subagio, A., Nur Lutfian Sari, R., Gita Vindy, P., Ainur Rofiah, A. (2018). Effect of fermentation time and cassava varieties on water content and the yield of starch from modified cassava flour (MOCAF). Indonesian Journal of Pharmaceutical Science and Technology, 5(2), 71–75. https://doi.org/10.24198/ijpst.v5i2.15094 [Google Scholar] [CrossRef]
33. Wahyuni, H., Aladin, A., Kalla, R., Nouman, M. (2022). Utilization of industrial flour waste as biobriquette adhesive: Application on pyrolysis biobriquette sawdust red teak wood. International Journal of Hydrological and Environmental for Sustainability, 1(2), 54–69. https://doi.org/10.58524/ijhes.v1i2.74 [Google Scholar] [CrossRef]
34. Lestari, L., Variani, V. I., Sudiana, I. N., Sari, D. P., Sitti Ilmawati, W. O. et al. (2017). Characterization of briquette from the corncob charcoal and sago stem alloys. Journal of Physics: Conference Series, 846, 1–7. https://doi.org/10.1088/1742-6596/846/1/012012 [Google Scholar] [CrossRef]
35. Abdel Aal, A. M. K., Ibrahim, O. H. M., Al-Farga, A., El Saeidy, E. A. (2023). Impact of biomass moisture content on the physical properties of briquettes produced from recycled ficus nitida pruning residuals. Sustainability, 15(15), 11762. https://doi.org/10.3390/su151511762 [Google Scholar] [CrossRef]
36. Hasan, E. S., Jahiding, M., Mashuni, M., Ilmawati, W. O. S., Wati, W. et al. (2017). Proximate and the calorific value analysis of brown coal for high-calorie hybrid briquette application. Journal of Physics: Conference Series, 846, 1–7. https://doi.org/10.1088/1742-6596/846/1/012022 [Google Scholar] [CrossRef]
37. Oladunmoye, O. O., Aworh, O. C., Maziya-Dixon, B., Erukainure, O. L., Elemo, G. N. (2014). Chemical and functional properties of cassava starch, durum wheat semolina flour, and their blends. Food Science & Nutrition, 2(2), 132–138. https://doi.org/10.1002/fsn3.83 [Google Scholar] [PubMed] [CrossRef]
38. Hawa, L. C., Ubaidillah, U., Damayanti, R., Hendrawan, Y. (2020). Moisture sorption isotherms of modified cassava flour during drying and storage. Heat and Mass Transfer, 56(8), 2389–2396. https://doi.org/10.1007/s00231-020-02866-1 [Google Scholar] [CrossRef]
39. Dipowaseso, D., Nurwantoro, N., Hintono, A. (2018). Characteristics and smearing ability of sugar palm fruit jam made through pectin substitution with modified cassava flour ( MOCAF ) as thickening agent. Jurnal Teknologi Pangan, 2(1), 1–7. https://doi.org/10.14710/jtp.2018.20680 [Google Scholar] [CrossRef]
40. Violalita, F., Yanti, H. F., Novita, R., Evawati, E., Syahrul, S. et al. (2021). Shelf-life prediction of gluten-free dry noodles made from composite flour (Mocaf, Tapioca, Cornstarch, and Soybeans) using accelerated shelf-life testing (ASLT) method with arrhenius equation approach. IOP Conference Series: Earth and Environmental Science, 757, 1–10. https://doi.org/10.1088/1755-1315/757/1/012057 [Google Scholar] [CrossRef]
41. National Standarization Agency of Indonesia (2020). Indonesian national standard SNI 01-6235-2000 (Charcoal briquette), pp. 1–5. [Google Scholar]
42. Pranowo, D., Savira, T. D., Perdani, C. G., Setyawan, H. Y. (2022). Characteristics of briquette as an alternative fuel made of mixed-biomass waste (Dairy sludge and coconut shell). Proceedings of the International Conference on Innovation and Technology (ICIT 2021), vol. 212, pp. 148–154. https://doi.org/10.2991/aer.k.211221.020 [Google Scholar] [CrossRef]
43. Syafrudin, S., Zaman, B., Indriyani, I., Erga, A. S., Natalia, H. B. (2015). The utilization of bottom ash coal for briquette products by adding teak leaves charcoal, coconut shell charcoal, and rice husk charcoal. Waste Technology, 3(1), 14–21. https://doi.org/10.12777/wastech.3.1.14-21 [Google Scholar] [CrossRef]
44. Rizki, M., Mustaqilla, S., Rinaldi, W., Mukhriza, T. (2022). The effect of adhesive types of damar and pine resin for biobricket manufacturing from sugarcane bagasse. Journal of Applied Technology, 9(1), 35–42. [Google Scholar]
45. Wijianto, W., Sarjito, S., Akhlis, N., Anggono, A. D., Darmawan, A. (2020). The influence of the type of adhesive on the properties of sawdust briquettes. International Journal of Emerging Trends in Engineering Research, 8(9), 5352–5356. https://doi.org/10.30534/ijeter/2020/73892020 [Google Scholar] [CrossRef]
46. Asmoro, N. W. (2021). Review: Characteristics and properties of modified cassava flour (Mocaf) and its benefits in food products. Journal of Food and Agricultural Product, 1(1), 34–43. https://doi.org/10.32585/jfap.v1i1.1755 [Google Scholar] [CrossRef]
47. Andriansyah, R. C. E., Rahman, T., Herminiati, A., Rahman, N., Luthfiyanti, R. (2017). Characteristics of chemical and functional properties of modified cassava flour (Manihot esculenta) by autoclaving-cooling cycles method. IOP Conference Series: Earth and Environmental Science, 101, 012023. https://doi.org/10.1088/1755-1315/101/1/012023 [Google Scholar] [CrossRef]
48. Nilusha, R. A. T., Jayasinghe, J. M. J. K., Perera, O. D. A. N., Perera, P. I. P., Jayasinghe, C. V. L. (2021). Proximate composition, physicochemical, functional, and antioxidant properties of flours from selected cassava (Manihot esculenta Crantz) varieties. International Journal of Food Science, 2021, 6064545. https://doi.org/10.1155/2021/6064545 [Google Scholar] [PubMed] [CrossRef]
49. Yuliah, Y., Suryaningsih, S., Ulfi, K. (2017). Penentuan kadar air hilang dan volatile matter pada bio-briket dari. Campuran Arang, 1(1), 51–57. https://doi.org/10.24198/jiif.v1i01.10902 [Google Scholar] [CrossRef]
50. Kongprasert, N., Wangphanich, P., Jutilarptavorn, A. (2019). Charcoal briquettes from madan wood waste as an alternative energy in Thailand. Procedia Manuf, 30, 128–135. https://doi.org/10.1016/j.promfg.2019.02.019 [Google Scholar] [CrossRef]
51. Tambunan, H., Nuryawan, A., Iswanto, A. H., Risnasari, I., Basyuni, M. et al. (2023). Briquettes made of branches wood of three mangrove species bonded by starch adhesive. Materials, 16(15), 1–22. https://doi.org/10.3390/ma16155266 [Google Scholar] [PubMed] [CrossRef]
52. Ajimotokan, H. A., Ehindero, A. O., Ajao, K. S., Adeleke, A. A., Ikubanni, P. P. et al. (2019). Combustion characteristics of fuel briquettes made from charcoal particles and sawdust agglomerates. Scientific African, 6, e00202. https://doi.org/10.1016/j.sciaf.2019.e00202 [Google Scholar] [CrossRef]
53. Faiz An Nabil, A., Putri, I. E., Ariyanti, D., Saputro, E. A. (2022). Comparison of various methods of processing plastic waste into economical briquettes. Natural Science, 11(1), 30–36. https://doi.org/10.22487/25411969.2022.v11.i1.15812 [Google Scholar] [CrossRef]
54. Tang, J. Y., Chung, B. Y. H., Ang, J. C., Chong, J. W., Tan, R. R. et al. (2023). Prediction model for biochar energy potential based on biomass properties and pyrolysis conditions derived from rough set machine learning. Environmental Technology,1–15. https://doi.org/10.1080/09593330.2023.2192877 [Google Scholar] [PubMed] [CrossRef]
55. Hong, Q. F. (2009). The carbon and hydrogen content of bituminous in fengfeng coal field calculated from the content of volatile matter and fixed carbon. Coal Quality Technology, 1(1), 1–8. [Google Scholar]
56. Yu, S., Kim, H., Park, J., Lee, Y., Park, Y. et al. (2022). Relationship between torrefaction severity, product properties, and pyrolysis characteristics of various biomass. International Journal of Energy Research, 46(6), 8145–8157. https://doi.org/10.1002/er.7716 [Google Scholar] [CrossRef]
57. Aich, S., Behera, D. U., Nandi, B. K., Bhattacharya, S. (2020). Relationship between proximate Analysis parameters and combustion behaviour of high ash Indian coal. International Journal of Coal Science & Technology, 7(4), 766–777. https://doi.org/10.1007/s40789-020-00312-5 [Google Scholar] [CrossRef]
58. Manyuchi, M. M., Mbohwa, C., Muzenda, E. (2018). Value addition of coal fines and sawdust to briquettes using molasses as a binder. South African Journal of Chemical Engineering, 26, 70–73. https://doi.org/10.1016/j.sajce.2018.09.004 [Google Scholar] [CrossRef]
59. Rahmawati, S., Afadil, A., Suherman, S., Santoso, T., Abram, P. H. et al. (2023). The utilization of durian peels (Durio zibethinus) for the manufacturing of charcoal briquettes as alternative fuel. Jurnal Pengelolaan Sumberdaya Alam dan Lingkungan (JPSL), 13(1), 76–87. https://doi.org/10.29244/jpsl.13.1.76-87 [Google Scholar] [CrossRef]
60. Sudding, S., Jamaluddin, P. (2016). The processing of coconut shell based on pyrolysis technology to produce renewable energy sources. International Conference on Mathematics, Science, Technology, Education, and Their Applications, pp. 498–510. Makassar, Indonesia. [Google Scholar]
61. Anasthasia, A., Syaiful, A. Z., Tang, M. (2020). Making charcoal briquettes from coconut shells using the pyrolysis method. Jurnal Saintis, 1, 1–8. [Google Scholar]
62. Dillon, S. R. (2023). Water. https://www.chem.fsu.edu/chemlab/chm1020c/Lecture%205/01.php (accessed on 07/09/2023). [Google Scholar]
63. Brewer, P. G., Peltzer, E. T. (2016). The molecular basis for the heat capacity and thermal expansion of natural waters. Geophysical Research Letters, 46, 13227–13233. https://doi.org/10.1029/2019GL085117 [Google Scholar] [CrossRef]
64. Daham Shyamalee, A. D. U. S., Amarasinghe, N. S. S. (2015). Evaluation of different binding materials in forming biomass briquettes with saw dust. International Journal of Scientific and Research Publications, 5(3), 1–8. [Google Scholar]
65. Handra, N., Abuzar, Perdana, M., Junaidi, Indra, A. (2023). The effect of percentage binder on fiber bio-briquettes EFB on ignition quality. International Conference on Mechanical Engineering for Emerging Technologies (ICOMEET 2021), Padang, Indonesia. https://doi.org/10.1063/5.0118193 [Google Scholar] [CrossRef]
66. Carnaje, N. P., Talagon, R. B., Peralta, J. P., Shah, K., Paz-Ferreiro, J. (2018). Development and characterisation of charcoal briquettes from water hyacinth (Eichhornia crassipes)-molasses blend. PLoS One, 13(11), 1–14. https://doi.org/10.1371/journal.pone.0207135 [Google Scholar] [PubMed] [CrossRef]
67. Rahmat, B., Suhardjadinata, S., Ratna, Y. (2023). Reduction of young coconut waste by pyrolysis to liquid smoke and charcoal briquettes. Proceedings of the 3rd Sriwijaya International Conference on Environmental Issues, pp. 1–8. Palembang, Indonesia. [Google Scholar]
68. Makgobelele, N. W., Mbaya, R. K. K., Bunt, J. R., Leokaoke, N. T., Neomagus, H. W. J. P. (2021). Evaluation of the mechanical properties of wood-derived charcoal briquettes for use as a reductant. Journal of the Southern African Institute of Mining and Metallurgy, 121, 187–192. https://doi.org/10.17159/2411-9717/903/2021 [Google Scholar] [CrossRef]
69. Sen, R., Wiwatpanyaporn, S., Annachhatre, A. (2016). Influence of binders on physical properties of fuel briquettes produced from cassava rhizome waste. International Journal of Environment and Waste Management, 17(2), 158–174. https://doi.org/10.1504/IJEWM.2016.076750 [Google Scholar] [CrossRef]
70. Supriadi, S., Rahmawati, S., Abram, P. H., Afadil, A., Parwati, N. G. A. M. et al. (2022). Characteristics of charcoal briquettes from kepok banana peel waste (Musa paradisiaca F.) as alternative fuel. Rasayan Journal of Chemistry, 15(1), 108–115. https://doi.org/10.31788/RJC.2022.1516607 [Google Scholar] [CrossRef]
71. Waluyo, J., Setianto, M. M., Safitri, N. R., Pranolo, S. H., Susanti, A. D. et al. (2023). Characterization of biochar briquettes from coconut shell with the effect of binder: Molasses, cow manure and horse manure. Evergreen, 10(1), 539–545. [Google Scholar]
72. Nasbey, H., Yahya, L. A., Budi, A. S. (2022). Optimization of the mechanical properties of coconut shell briquettes with a tapioca flour adhesive. Journal of Physics: Conference Series, 2377, 1–6. https://doi.org/10.1088/1742-6596/2377/1/012012 [Google Scholar] [CrossRef]
Cite This Article
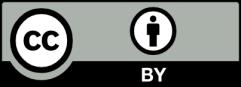
This work is licensed under a Creative Commons Attribution 4.0 International License , which permits unrestricted use, distribution, and reproduction in any medium, provided the original work is properly cited.