Open Access
ARTICLE
Preparation of Environmentally Friendly Urea-Hexanediamine-Glyoxal (HUG) Resin Wood Adhesive
1 Yunnan Key Laboratory of Wood Adhesives and Glue Products, College of Material Science and Engineering, Southwest Forestry University, Kunming, 650224, China
2 International Joint Research Center for Biomass Materials, Southwest Forestry University, Kunming, 650224, China
3 College of Chemical and Materials Engineering, Zhejiang A&F University, Hangzhou, 311300, China
4 LERMAB, University of Lorraine, Epinal, 88000, France
* Corresponding Author: Xuedong Xi. Email:
# These two authors have contributed equally to this work
Journal of Renewable Materials 2024, 12(2), 235-244. https://doi.org/10.32604/jrm.2023.029537
Received 24 February 2023; Accepted 08 May 2023; Issue published 11 March 2024
Abstract
Using non-toxic, low-volatile glyoxal to completely replace formaldehyde for preparing urea-glyoxal (UG) resin adhesive is a hot research topic that could be of great interest for the wood industry. However, urea-glyoxal (UG) resins prepared by just using glyoxal instead of formaldehyde usually yields a lower degree of polymerization. This results in a poorer bonding performance and water resistance of UG resins. A good solution is to pre-react urea to preform polyurea molecules presenting already a certain degree of polymerization, and then to condense these with glyoxal to obtain a novel UG resin. Therefore, in this present work, the urea was reacted with hexamethylene diamine to form a polyurea named HU, and then this was used to react it with different amounts of glyoxal to synthesize hexamethylenediamine-urea-glyoxal (HUG) polycondensation resins, and to use this for bonding plywood. The results show that the glyoxal can well react with HU polyuria via addition and schiff base reaction, and also the HUG resin exhibits excellent bonding strength and water resistance. The shear strength of the plywood bonded with this HUG at 160°C hot press temperature as high as 1.93 MPa, 2.16 MPa and 1.61 MPa, respectively, which meets the requirement of the China national standard GB/T 9846-2015 (≥0.7 MPa), and can be a good choice as a wood adhesive for industrial application.Graphic Abstract
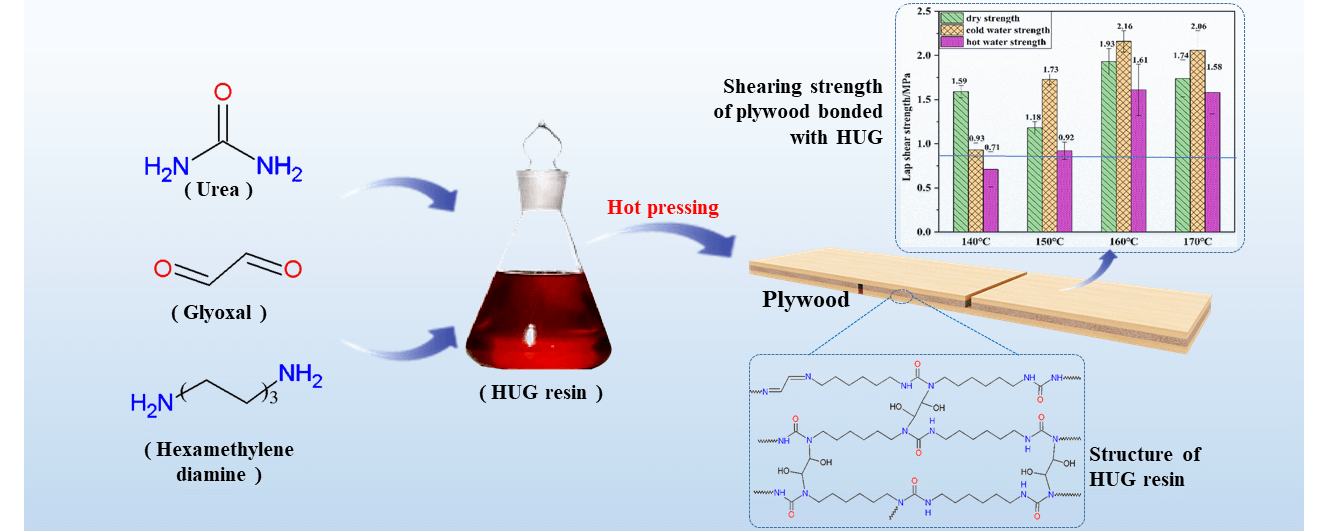
Keywords
Urea-formaldehyde resins, including their modifications, are important raw material to be most widely and currently used as adhesives in the wood composites industry. They constitute more than 90% of the wood adhesives market because of their convenient synthesis and low cost. However, since formaldehyde is used in their synthesis, the formaldehyde emission problem cannot be eliminated in the panels bonded with them, formaldehyde being now classified as toxic and carcinogenic. Therefore, finding a suitable aldehyde with low or even no toxicity to replace formaldehyde has been for some time a hot topic in the field of wood adhesives [1–3]. Up to now, dimethoxy acetaldehyde [4], propionic aldehyde [5], butandialdehyde [6], glutaraldehyde [7], isobutyral [8], dialdehyde starch [9] and others have been reported as substitutes for formaldehyde. Among them, glyoxal has become the focus of attention because of its reasonably high reactivity, low toxicity and volatility [10,11]. Previous research works have already confirmed that glyoxal, as a simple aliphatic binary aldehyde, can react well with urea to form a urea-glyoxal (UG) amino resin. These UG amino resins have similar structures and properties as urea-formaldehyde resins.
In reality, synthetic UG resins are used in common industrial practice at present, in the textile and paper industries to improve the properties of products, but are not used in the wood industry. This is mainly because only UG resins of a low degree polymerization can be obtained by simply replacing formaldehyde with glyoxal in urea resins synthesis. Such low degree of polymerization resins do not adhere sufficiently well on wood surfaces to get a good bonding performance, a finding already confirmed by previous research [12,13]. The main reason for this is that glyoxal has a lower reactivity than formaldehyde, so that the polycondensation degree of UG resins is much lower than that of UF resin, thus showing a poor bonding performance. In order to improve the degree of polymerization on UG resin, some research work has been done such as using a small proportion of formaldehyde to promote the synthesis reaction. This has achieved better results, but the toxic formaldehyde is still used [12]. There are also reports on the utilization of acid ionic liquids as hardeners [10] that obtained a considerable improvement to the point of achieving the same characteristics as UF resins, but ionic liquid are still an expensive commodity. 5-Hydroxymethylfurfural (HMF) and other substances have also been tried to improve the performance of UG resin, and achieved good results [14]. However, all these trials, some successful, still present some drawbacks.
To improve the degree of polymerization of UG resin by more affordable means, two further approaches can be taken. The first is to find suitable catalysts to improve the reactivity of urea with glyoxal [10], and the second is to pre-treat small molecules of urea-based compounds to obtain polyureas with up to a certain degree of polymerization. These can then form with more ease macromolecules to be crosslinked by glyoxal. With this in mind, in this present work, urea and hexamethylenediamine were reacted via deamination to prepare polyureas (HU) [15]. These were then crosslinked by glyoxal to obtain hexamethylenediamine-urea-glyoxal (HUG) resin adhesives, and used for laboratory three layers of plywood bonding. The effects of different amounts of glyoxal on the adhesive physical properties and bonding properties of this synthesized HUG resin were researched to obtain the optimum preparation process. In addition, by pressing plywood at different temperatures and testing their bonding strength, this work also explored the influence of hot pressing temperatures on the performance of HUG resin adhesives. Finally, to prepare a good performance formaldehyde-free hexamethylenediamine-urea-glyoxal (HUG) resin wood adhesive in this work, and it will possess great potential to replace the existing UF resin adhesive in the industrial production of wood composites.
Analytical purity urea (99.0%) and hexamethylene diamine (99.0%) were purchased from Sinopharm Chemical Reagent Co., Ltd., China; The 40% glyoxal solution (Analytical purity) from Shanghai Zhanyun Chemical Co., Ltd., China.
2.1 Synthetic Scheme of HU Polyurea
The synthesis of the HU polyurea was performed in a solvent-free condition, with the hexamethylenediamine (HDM) to urea of molar ratios of 1, and reacted the mixture at 120°C temperature for 4 h to obtain the white solid polyurea [15], then placed this solid in the oven for 6 h at 103°C to release reaction produces ammonia gas, and then crushed it into powder form for easy subsequent utilization.
In the flask with a volume of 250 ml, 15 g HU powder was added into 0.5 mol, 0.75 mol, 1 mol, 1.25 mol glyoxal solution with pH = 4.5, respectively, and mix them for 10 min at temperature 45°C to dissolve well the HU powder, then increase the temperature to 90°C and keep it for 1 h to synthesize the HUG1, HUG2, HUG3, HUG4 resins. The viscosity of synthetic HUG resins was tested by the SNB-2 viscometer from Nyirun Intelligent Technology Co., Ltd. (Shanghai, China).
2.3 Fourier Transform Infrared Spectrometry (FTIR)
Fourier Transform Infra-Red (FTIR) analysis was carried out using a Shimadzu IRAffinity-1 spectrophotometer for exploring the molecular structures of synthetic resins. A blank sample tablet of potassium bromide was prepared for the reference spectrum. A similar tablet was prepared by mixing potassium bromide with 5% w/w of the HUG resins powders for the test. The final spectrum was obtained in transmission measurement of 32 scans times and a resolution of 2.0.
2.4 Dynamic Thermomechanical Analysis (DMA)
HUG resins were tested by NETZSCH DMA-242 equipment for the DMA analysis. All tested samples were prepared in dimensions of 50 mm × 10 mm × 3 mm, and each adhesive was applied between two poplar wood plies to form a sandwiches model and then tested in non-isothermal three-point bending mode at a temperature range between 30°C to 250°C, the heating rate in this work was 10°C/min, the frequency of 10 Hz, strain amplitude of 60 µm, and the dynamic force was 1.5 N. The tested results were analyzed by NETZSCH Proteus software to obtain the DMA curves.
2.5 Differential Scanning Calorimetry (DSC)
Differential scanning calorimetry (DSC) was used to analyze HUG resins here. The Perkin-Elmer DSC spectrometer purchased from Germany with type DSC 204F1 was used to test all synthetic resin adhesives. All samples were freeze-dried before its testing, and the heating rate was 10°C/min, testing temperature range in 30°C–250°C. The PYRISTM Version 4.0 software was used for the data treatment in this work.
2.6 Tests of Mechanical Properties
The bonding performance of the HUG resins was evaluated by the three-layer laboratory poplar plywood, then tested their dry shear strength, and wet strength after 24 h in cold water soaking and after 3 h in 63°C hot water soaking. The glue spread used was of 260 g/m2, and the hot pressing time was of 5 min at the set temperature (140°C, 150°C, 160°C, 170°C) and 1.0 MPa pressure. The pressed plywood samples were stored in ambient condition for two days before their tests. The mechanical properties were tested according to the China National Standard GB/T 14074 (2017) [16] and GB/T 17657 (2013) [17].
3.1 Physical Properties of HUG Resins
The physical properties of the four prepared HUG resins were tested in this work and their results are shown in Table 1. With the increase of the glyoxal addition from the HUG1 to the HUG3 resin, the resin viscosity and solids content increased. This is caused by the polymerization reaction between HU and glyoxal, which results in the molecular weight of the reaction product increasing, thus both solids content and viscosity increase also. As more glyoxal gets involved in the reaction to form cross-linked products, it will also not be evaporated when testing the solids content, resulting in an increase in solids content. However, as the glyoxal addition continued to increase to HUG4, the excess glyoxal did not participate anymore in the reaction, thus exerting a diluting effect on the resin and causing the viscosity of the resin to decrease. When the solids content test is then done, the excess glyoxal evaporates so that the solid content of the resin also appears to decrease.
3.2 Bonding Performance of HUG Resins
Fig. 1 shows the bonding performance of plywood prepared with HUG resins at a pressing temperature of 150°C. Although the dry strength of the HUG1 resin is 1.13 MPa, its wet strength after 3 h soaking in 63°C hot water and 24 h cold water soaking failed to reach the standard requirement (≥0.7 MPa), so it does not conform to the industrial production requirements. Due to the deficiency of glyoxal in the preparation of HUG1 resin HU cannot fully react with glyoxal to form enough branched HUG molecules to ensure a sufficient bonding strength. As the amount of glyoxal increased to 0.75 mol (namely in the HUG2 resin), the dry strength of plywood bonded with it is 1.18 MPa, 24 h cold water soaking strength as high as 1.70 MPa, and its 0.92 MPa warm water strength also comply with the requirements of the national standard (GB/T 9846-2015). This is because sufficient glyoxal can react well with the HU polyurea to form a cross-linked network, which provides good bonding results to the wood surface. This mechanical property of the HUG resin is also obviously better than the UG resin that was reported in the literature [13], and it can be similar to melamine-modified UF resin now used in industrial production, thus it has good application potential [18]. However, with a further increase in the amount of glyoxal to 1 mol (namely HUG3 resin), the bonding strength of the plywood prepared with this adhesive will decrease, especially its hot water strength failed to reach the level required by the relevant standard. Combining the results of the adhesive viscosity in Table 1 and the percentage wood failure of the plywood shear test in Table 2, these may due to the high viscosity of the HUG3 resin resulting in its poor adhesion to, and penetration in, the surface of the panel veneers.
Figure 1: Shear strength of plywood bonded with HUG resins
Moreover, HUG4, prepared with an excess of glyoxal, shows poor shear strength and water resistance of the plywood bonded with it. This is so because the excess of glyoxal can form linear molecules containing hydrophilic hydroxyl groups by aldol condensation, which cannot contribute to the bond strength and will reduce the glue line water resistance. Thus, when the optimal amount of glyoxal is 0.75 mol in preparing the HUG resin, the plywood bonded with it presents the best shear strength and the highest percentage wood failure.
3.3 Influence of Hot Pressing Temperature on the Plywood Bonding Performance
To explore the influence of the hot pressing temperature on the bonding performance of plywood prepared with HUG resins, the HUG2 resin was used to bond plywood at 140°C, 150°C, 160°C, 170°C press temperature. The results of the shear strengths obtained is shown in Fig. 2. First, it can be noticed that the hot water soaking strength of plywood pressed at 140°C just meets the requirements of the standard (≥0.70 MPa), however this is neither stable nor constant, as some of the tested specimens cannot reach the value required by the standard. Thus, the hot pressing temperature of 140°C does not seem to be sufficiently high for a plywood bonded with a HUG resin, even though the dry strength and the wet strength after 24 h cold water soaking, and the respective wood failures are already complying with the requirements. With the increase in the hot pressing temperature, the shear strength of the plywood bonded with a HUG resin improves, especially its wet bonding strength.
Figure 2: Adhesive properties of HUG2 resin at different platen temperatures
At the hot pressing temperature of 160°C and 170°C, the hot water soaking strength of the plywood is far exceeding the standard requirement (≥0.7 MPa) being more than 1.5 MPa. The excellent shear strength and the wood failure of the plywood in Table 3 show that a HUG resin has good bonding performance and water resistance at these pressing temperatures. Therefore, the bonding properties of a HUG resin can be improved by the increase, within limits, of the hot pressing temperature and the best bonding property can also be obtained at 160°C. When the temperature is too high, such as 170°C, this leads to the thermal decomposition of the adhesive, thus resulting in a decline in the bonding performance (as shown in Fig. 2). Thus, 160°C can be used as the best hot pressing temperature for the HUG resins, which is comparable to phenol-formaldehyde (PF) resins [19,20]. However, what should not be ignored is also that the performance of the plywood pressed at the temperature of 150°C can meet the requirements of the standard, and it is good enough compared to industrial UF adhesives.
Infrared spectral analysis can be used to analyze the functional groups in the resin structure, so as to identify the changes occurring in the reaction process. Fig. 3 shows the results of the FTIR spectrum of the four HUG resins prepared in this work. The spectra characteristics of these four resins synthesized by different amounts of glyoxal are basically the same, this meaning that their functional groups are also roughly the same.
Figure 3: FT-IR images of four groups of HUG resins
The wide absorption peak at around 3500 cm−1 belongs to the stretching vibration of hydroxyl and amino groups [21]. This means that the HUG resins contain many hydroxyl or reactive amino groups. And these active functional groups can be well involved in crosslinking reactions in the subsequent hot pressing process to form a network structure, to then ensure excellent bonding performance of the HUG resins. The peaks at 2930 and 2860 cm−1 both are attributed to the C–H deformation [22,23]. C-N linkages will result from the reaction of amino groups and glyoxal, their bending vibration absorption peak being at 1461 cm−1 [24,25]. The peak at 1705 cm−1 is assigned to the C=O group in the HU polyurea chemical compounds, which has no noticeable change, because the reaction between polyurea and glyoxal does not affect the amount of this functional group. The N-H structure appears at 1546 cm−1, it can be clearly seen from the curve in Fig. 4 that HUG1 resin has an obvious absorption peak at this wavelength [15,26,27]. However, with the increase of the amount of glyoxal, this peak has been weakened or even disappeared (such as in the HUG3 and HUG4), which is due to the reaction between glyoxal and HU and leads to the depletion of this functional group. This is also good proof of the crosslinking reaction between HU polyurea and glyoxal occurring. By this analysis, a conceivable reaction mechanism of HUG can be proposed as shown in Fig. 4.
Figure 4: Synthetic reaction mechanism of HUG resin
3.5 Thermal Characteristics Analysis
In order to study the effects of different amounts of glyoxal addition on the curing performance of HUG resins, a DSC analysis was used to analyse the four HUG resins prepared, and the results are shown in Fig. 5. First, from the figure it appears that there is only one exothermic peak in the DSC curves of HUG1 and HUG2, while there are two exothermic peaks in curves of HUG3 and HUG4. This means that there are two curing reaction systems in the HUG3 and HUG4 resins, which may be due to excessive glyoxal in the resin producing an aldol condensation reaction. The HUG2 resin with the optimal bonding performance (cf. Fig. 1) shows a large curing exotherm in the DSC curve, which means that its curing reaction is sufficient, thus ensuring its good bonding strength and water resistance. In addition, the peak curing temperature of HUG2 is 105°C, which is similar to that of UF resins in industrial production [28,29]. Therefore, the HUG2 resin has real potential as a substitute for UF resin.
Figure 5: DSC (a) and DMA (b) results of four groups of HUG resin
In the DMA results of the HUG resins HUG2 and HUG3 present higher peaks of Young’s modulus than HUG1 and HUG4 (Fig. 5b). This means that these two resins may have better mechanical performance [30,31], this being consistent with, and supporting the results in Fig. 1 of plywood shearing strength. Meanwhile, as shown also in Fig. 4, all DMA curves start to increase at a lower temperature (near 70°C), which means that the curing reaction temperature of the HUG resins is low. This is of interest to the wood-based panel industry. More importantly, the DMA peak value of HUG resins appeared near 160°C, which is consistent with the best bonding performance of plywood at the hot pressing temperature of 160°C. Certainly, at temperatures above 160°C, the resin gradually degrades as the temperature rises, which results in a decrease in the bond strength and the modulus value of the DMA curves. This is a rapid decrease, and seems to imply that HUG is not well resistant to heat. It is worth emphasising, however, that wood-based panels are not normally used at such high temperatures in daily life, so this does not affect the prospects of one of the HUG resins synthesised in this work for use in the panel industry.
A glyoxal-based HUG resin with great potential to replace industrial UF resins for wood adhesives was successfully prepared in the present work. Urea was reacted with hexanediamine by deamination to obtain polyureas and then crosslinked with glyoxal. This resin can be considered as an environmentally friendly adhesive, and it has good bonding properties and water resistance, as the plywood bonded with it at 160°C pressing temperature shows that its dry shear strength, wet strength after 24 h cold water immersion and 3 h hot water (63°C) immersion reached 1.93 MPa, 2.16 MPa, 1.61 MPa, respectively. This is higher than the UF resin adhesives commonly used in the wood composite industry today. The HUG resin produced has a low curing temperature of about 105°C, which is similar to UF resin adhesives. This work also confirms that HUG resins will rapidly crack and lose their bonding strength at temperatures above 160°C, but this does not affect their application in wood composites bonding as few wood-based panels are used at such high temperatures.
Acknowledgement: The authors acknowledge the support of the authority of the College of Material Science and Engineering, Southwest Forestry University for providing a conducive atmosphere for this work.
Funding Statement: This work was supported by the Yunnan Provincial Natural Science Foundation (202201AU070222, 202201AT070045, 202101BD070001-074) and Scientific Research Fund Project of Yunnan Provincial Department of Education (2022J0490). This research was also financed by the 111 Project (D21027).
Author Contributions: The authors confirm contribution to the paper as follows: study conception and design: Hong Lei, Guanben Du, Antonio Pizzi, Xuedong Xi; data collection: Qianyu Zhang, Shi Chen, Long Cao; analysis and interpretation of results: Qianyu Zhang, Shi Chen, Long Cao; draft manuscript preparation: Qianyu Zhang, Shi Chen, Long Cao. All authors reviewed the results and approved the final version of the manuscript.
Availability of Data and Materials: Not applicable.
Conflicts of Interest: The authors declare that they have no conflicts of interest to report regarding the present study.
References
1. Pizzi, A., Papadopoulos, A. N., Policardi, F. (2020). Wood composites and their polymer binders. Polymers, 12, 1115. [Google Scholar] [PubMed]
2. Pizzi, A. (2016). Wood products and green chemistry. Annals of Forest Science, 73, 185–203. [Google Scholar]
3. Pizzi, A. (2006). Recent developments in eco-efficient bio-based adhesives for wood bonding: Opportunities and issues. Journal of Adhesion Science and Technology, 20(8), 829–846. [Google Scholar]
4. Despres, A., Pizzi, A., Vu, C., Delmotte, L. (2010). Colourless formaldehyde-free urea resin adhesives for wood panels. European Journal of Wood & Wood Products, 68(1), 13–20. [Google Scholar]
5. Mamiński, M. Ł., Król, M. E., Grabowska, M., Głuszyński, P. (2011). Simple urea-glutaraldehyde mix used as a formaldehyde-free adhesive: Effect of blending with nano-Al2O3. European Journal of Wood & Wood Products, 69(3), 505–506. [Google Scholar]
6. Wang, S., Pizzi, A. (1997). Succinaldehyde induced water resistance improvements of UF wood adhesives. Holz als Roh–und Werkstoff, 55(1), 9–12. [Google Scholar]
7. Maminski, M. L., Borysiuk, P., Parzuchowski, P. G. (2008). Improved water resistance of particleboards bonded with glutaraldehyde-blended UF resin. Holz als Roh–und Werkstoff, 66(5), 381–383. [Google Scholar]
8. Zhang, Y. F., Zeng, X. R., Ren, B. Y. (2009). Synthesis and structural characterization of urea-isobutyraldehyde–formaldehyde resins. Journal of Coatings Technology and Research, 6(3), 337–344. [Google Scholar]
9. Oktay, S., Kızılcan, N., Bengu, B. (2021). Oxidized cornstarch–Urea wood adhesive for interior particleboard production. International Journal of Adhesion and Adhesives, 110, 102947. [Google Scholar]
10. Younesi-Kordkhaili, H., Pizzi, A. (2016). Acid ionic liquids as a new hardener in urea–glyoxal adhesive resins. Polymers, 8(3), 57–71. [Google Scholar]
11. Xi, X., Pizzi, A., Amirou, S. (2018). Melamine-glyoxal–glutaraldehyde wood panel adhesives without formaldehyde. Polymers, 10(1), 22. [Google Scholar]
12. Deng, S. D., Pizzi, A., Du, G. B., Zhang, J. Z. (2014). Synthesis, structure, and characterization of glyoxal-urea-formaldehyde cocondensed resins. Journal of Applied Polymer Science, 131(21), 41009. [Google Scholar]
13. Deng, S., Du, G., Li, X., Pizzi, A. (2014). Performance and reaction mechanism of zero formaldehyde-emission urea-glyoxal (UG) resin. Journal of the Taiwan Institute of Chemical Engineers, 45(4), 2029–2038. [Google Scholar]
14. Xi, X., Liao, J., Pizzi, A., Gerardin, C., Amirou, S. et al. (2020). 5-Hydroxymethyl furfural modified melamine glyoxal resin. The Journal of Adhesion, 96(13), 1167–1185. [Google Scholar]
15. Cao, L., Pizzi, A., Zhang, Q., Tian, H., Lei, H. et al. (2022). Preparation and characterization of a novel environment-friendly urea-glyoxal resin of improved bonding performance. European Polymer Journal, 162, 110915. [Google Scholar]
16. China National Standard GB/T 14074 (2017). Testing methods for wood adhesives and their resins. http://c.gb688.cn/bzgk/gb/showGb?type=online&hcno=6A257A2155A2DC1AC06AD925B0FD54D5 [Google Scholar]
17. China National Standard GB/T 17657 (2013). Test methods for evaluating the properties of wood-based panels and surface decorated wood-based panels. http://c.gb688.cn/bzgk/gb/showGb?type=online&hcno=256095A3CAC6DA7A999AD342F1EE2102 [Google Scholar]
18. Zanetti, M., Pizzi, A. (2003). Low addition of melamine salts for improved melamine-urea-formaldehyde adhesive water resistance. Journal of Applied Polymer Science, 88(2), 287–292. [Google Scholar]
19. Zhang, Y., Zhang, Y., He, L., Zhou, Z. (2007). Cure rate of Phenol-Formaldehyde (PF) resol resins catalyzed with MgO. Journal of Adhesion Science and Technology, 21(9), 833–839. [Google Scholar]
20. Zhao, M., Jing, J., Zhu, Y., Yang, X., Wang, X. et al. (2016). Preparation and performance of lignin-phenol-formaldehyde adhesives. International Journal of Adhesion & Adhesives, 64, 163–167. [Google Scholar]
21. Irman, N., Latif, N., Brosse, N., Gambier, F., Syamani, F. A. et al. (2022). Preparation and characterization of formaldehyde-free wood adhesive from mangrove bark tannin. International Journal of Adhesion and Adhesives, 114, 103094. [Google Scholar]
22. Saražin, J., Pizzi, A., Amirou, S., Schmiedl, D., Šernek, M. (2021). Organosolv lignin for non-isocyanate based polyurethanes (NIPU) as wood adhesive. Journal of Renewable Materials, 9(5), 881–907. [Google Scholar]
23. Song, J., Chen, S., Yi, X., Zhao, X., Liu, B. (2021). Preparation and properties of the urea-formaldehyde res-in/reactive halloysite nanocomposites adhesive with low-formaldehyde emission and good water resistance. Polymers, 13(14), 2224. [Google Scholar] [PubMed]
24. Stern, T. (2020). Side-reactions in diisocyanate-derived bulk polyurea synthesis. Journal of Applied Polymer Science, 137(35), 1–16. [Google Scholar]
25. Gao, Z., Zhang, Y., Fang, B., Zhang, L., Shi, J. (2015). The effects of thermal-acid treatment and crosslinking on the water resistance of soybean protein. Industrial Crops & Products, 74, 122–131. [Google Scholar]
26. Dazmiri, M. K., Kiamahalleh, M. V., Dorieh, A., Pizzi, A. (2019). Effect of the initial F/U molar ratio in urea-formaldehyde resins synthesis and its influence on the performance of medium density fiberboard bonded with them. International Journal of Adhesion and Adhesives, 95(4), 102440. [Google Scholar]
27. Deng, S., Du, G., Li, X., Xie, X. (2014). Performance, reactionmechanism and characterization of glyoxal-monomethylol urea (G-MMU) resin. Industrial & Engineering Chemistry Research, 53(13), 5421–5431. [Google Scholar]
28. Costa, N., Pereira, J., Martins, J., Ferra, J., Cruz, P. et al. (2012). Alternative to latent catalysts for curing UF resins used in the production of low formaldehyde emission wood-based panels. International Journal of Adhesion and Adhesives, 33, 56–60. [Google Scholar]
29. Lu, X., Pizzi, A. (1998). Curing conditions effects on the characteristics of thermosetting adhesives-bonded wood joints. European Journal of Wood and Wood Products, 56(6), 393–401. [Google Scholar]
30. Ghahri, S., Pizzi, A. (2018). Improving soy-based adhesives for wood particleboard by tannins addition. Wood Science and Technology, 52, 261–279. [Google Scholar]
31. Xi, X., Pizzi, A., Gerardin, C., Liao, J., Amirou, S. et al. (2021). Glutaraldehyde-wheat gluten protein adhesives for wood bonding. The Journal of Adhesion, 97(1), 88–100. [Google Scholar]
Cite This Article
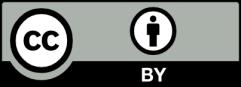
This work is licensed under a Creative Commons Attribution 4.0 International License , which permits unrestricted use, distribution, and reproduction in any medium, provided the original work is properly cited.