Open Access
ARTICLE
Comparison of Various Ion Exchange Resins for the Separation of Phenols in a Wood Pyrolysis-Based Biorefinery
1 Latvian State Institute of Wood Chemistry, Riga, LV-1006, Latvia
2 University of Latvia, Riga, LV-1004, Latvia
3 Nova Pangaea Technologies, Lealholme Building, Wilton International, Wilton, Redcar, TS10 4RG, UK
* Corresponding Author: Kristine Meile. Email:
(This article belongs to the Special Issue: Advances in Biorefinery Technologies and Products – 2024)
Journal of Renewable Materials 2024, 12(12), 2135-2152. https://doi.org/10.32604/jrm.2024.056775
Received 30 July 2024; Accepted 23 September 2024; Issue published 20 December 2024
Abstract
Fast pyrolysis of pre-treated birch wood in a super-heated steam environment produces a condensate rich in anhydrosugars. With the objective to obtain several product streams from this condensate, the possibility of extracting additional chemical species is explored, thus promoting the development of a pyrolysis-based biorefinery. In this work, the extraction and recovery of pyrolytic phenols from birch wood pyrolysis condensate was studied using ion exchange resins. With an aim to achieve effective phenol recovery, while obtaining high purity levoglucosan, basic ion exchange resins, both in OH− and Cl− form, as well as polystyrene-divinyl resins without functional groups were compared. This study characterizes the influence of sorbent matrix type and porosity, functional group and counter ion on the sorption of various aromatic compounds. It was concluded that the counter ion of the ion exchange resins had the most influence on the pyrolytic phenol adsorption, while in the case of unfunctionalized resins smaller pore size improved removal of phenols from the pyrolysis liquids. Of the resins tested, the most effective at the removal and recovery of pyrolytic phenols were strongly basic, macroporous, anion exchange resins in OH− form. The possibility to reuse the sorbents and solvents is explored to make the over-all process more environmentally friendly and economically feasible.Graphic Abstract
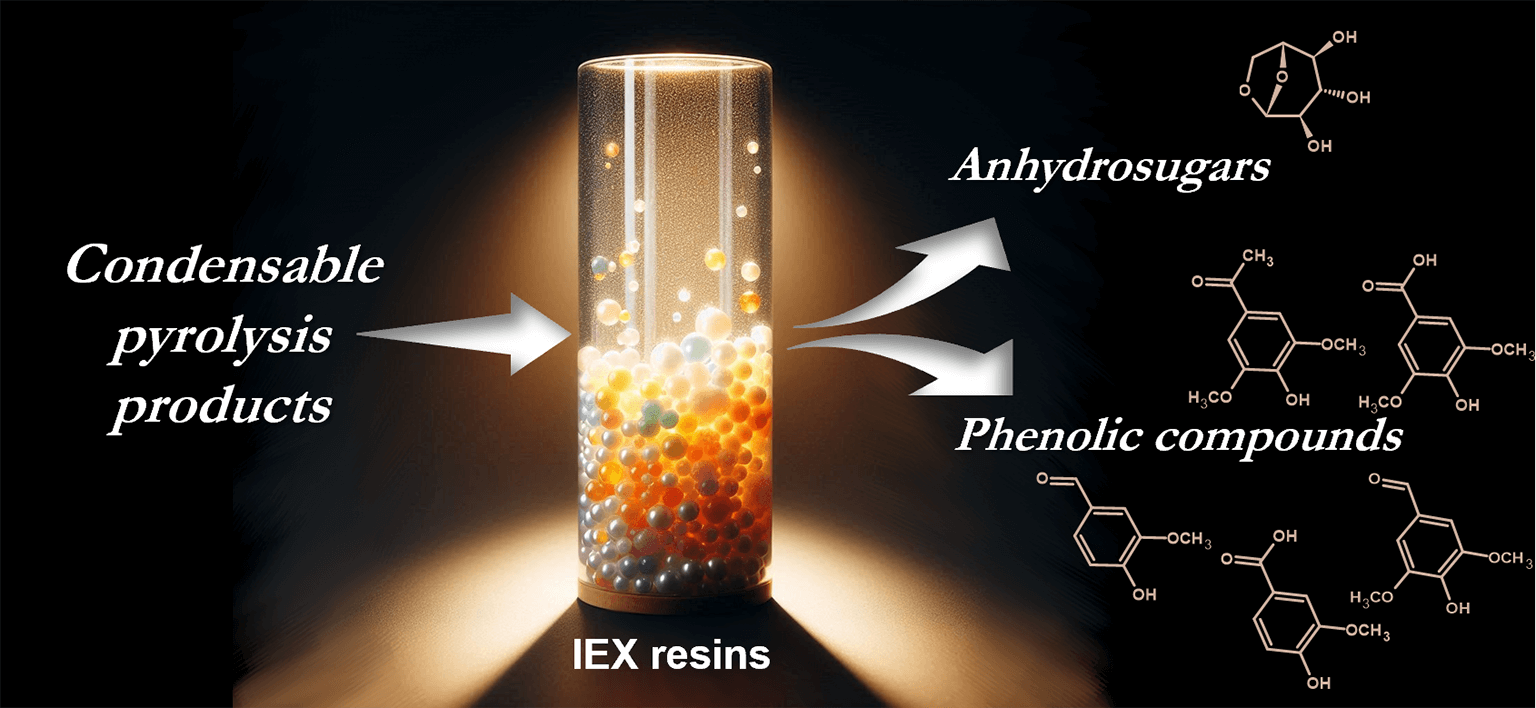
Keywords
Nomenclature
Acr | Acrylic matrix |
C | Concentration |
DVB | Divinylbenzene |
G | Gelular matrix |
IE | Ion exchange |
LG | Levoglucosan |
m | Mass |
Mp | Macroporous matrix |
NREL | National Renewable Energy Laboratory |
SBA | Strongly basic anion |
St | Styrenic matrix |
tR | Retention time |
V | Volume |
WBA | Weakly basic anion |
Among other renewables, biomass is unparalleled for the production of carbon containing products–both materials and chemicals. Ergo, rational processing of biomass is a key factor in replacing the unsustainable use of fossil resources in the chemical industry. Pyrolysis is a key process to transform lignocellulosic biomass, such as wood, into valuable products. It is considered to be a comparatively simple, economically feasible process which can be up-scaled for industrial applications [1,2].
Easily accessible biomass sources include agricultural and forestry wastes, which, from a chemical point of view, consist primarily of three constituents–cellulose, hemicellulose and lignin. All three are natural polymers, but each has its own peculiarities. At first glance, cellulose seems to be the most straightforward structure simply consisting of (1→4) linked glucose units. Despite this, the pyrolysis products of glucose [3], as well as cellulose [4] are numerous, including furan derivatives, anhydrosugars, acetic acid, methanol, volatiles, etc. Furthermore the definitive mechanism of cellulose pyrolysis is still under debate [5]. As stated in the relevant NREL (National Renewable Energy Laboratory) report [6], one of the most abundant and promising pyrolysis products of cellulose–and lignocellulosic biomass as a whole–is levoglucosan (LG) or 1,6-anhydro-β-D-glucopyranose. LG can be used for the synthesis of food additives, polymers, pharmaceuticals and other products [7].
The pyrolysis of hemicellulose–a group of more complex, but unstable polysaccharides–is similarly a source of a wide variety of low molecular weight products [8]. The chemical structure of lignin, on the other hand, is made up mostly of phenylpropane units with different functional groups, which are a source of aromatic pyrolysis products–2-methoxyphenols, 2,6-dimethoxyphenols, catechols, as well as furfural, acetic acid, etc. [9], and oligomers known as pyrolytic lignin [10]. Consequently, liquid product streams from pyrolysis are a mixture of hundreds of chemical compounds [11], with only a few of them being produced in high enough concentrations for commercialization. For now, LG is practically the only chemical, considered for individual isolation from the condensable pyrolysis products [12]. LG is a beautiful illustration of the potential hidden in the chemical composition of pyrolysis condensates. However it must be stressed that to ensure an economic profit from the pyrolysis process, it is necessary to obtain a broader range of products. Therefore, the objective of this study is to examine the process for recovery of phenol derivatives from pyrolysis products, to improve the economic feasibility of the wood pyrolysis-based biorefinery. A successful recovery method should enable high levels of recovery and lead to a pure LG stream.
The isolation of the multiple chemical product groups in pyrolysis condensate is known as fractionation or separation [13–17]. Fractionation of high water bio-oils can be conducted by spontaneous phase separation [14]. However, these bio-oils are targeted for fuel production and are less comparable to sugar-rich fermentation-targeted bio-oil/aqueous pyrolyzate product streams. To minimize energy and material consumption, fractionation would ideally be done at a condensation stage. Staged fractional condensation has been observed in the literature [18]. However, the fast pyrolysis phenol and sugar fractions partially co-condensate, due to their high temperature dew points. This leads to some portion of the phenolic compounds being captured in the later condenser fractions [19]. For complete extraction of the phenolics content, post-processing of a fully condensed stream is preferable. Depending on the condensation method, condensate can be obtained as either a typical bio-oil or an aqueous pyrolyzate [20,21]. “Water washing” of bio-oils, particularly the sugar-rich fraction [22], is often conducted to yield an aqueous stream of anhydrosugars such as LG. Without organic solvent extraction, these sugar rich fractions contain a portion of phenolic compounds. Aqueous pyrolyzate potentially provides a direct route to a similar product stream. These aqueous streams predominantly find applications in fermentation, as opposed to fractionation for the range of products within them.
For the removal and recovery of phenolics, there is a well-established and patented procedure developed by the NREL. This procedure uses solvent extraction (primarily with ethyl acetate) followed by aqueous-organic separation, alkali metal carbonate neutralization, and evaporation to isolate phenolics [23]. This patented ethyl acetate extraction methodology is comparable to the extraction methodologies used to quantify the phenolic fraction in bio-oils, which suggests that it removes a major fraction of phenolics present [24]. However, some phenols do remain in the aqueous solution after this treatment, as literature procedures suggest that a further detoxification step is required before use in fermentation [13]. Washed bio-oil or aqueous pyrolyzate fractions are often detoxified using activated carbon [25] with the aim of removing multiple fermentation inhibitors including phenolics. Activated carbon has been demonstrated to remove phenolic compounds. However, a significant portion of compounds removed by activated carbon are irreversibly adsorbed [26], depending on conditions of adsorption (low solution pH and low activated carbon oxygen content is better for avoiding irreversible sorption) [27]. Developing effective recovery of these removed compounds is an opportunity for diversification of biorefinery products through an adsorption/desorption fractionation.
The widely used NREL extraction method has been highlighted as problematic for sustainability, due to the large volumes of expensive to recover, often fossil derived, solvents it uses [28]. This has led to attempts to develop alternative solvents for the same process [29]. Furthermore, as noted in its patent, this method tends to produce a product which contains other neutral organic compounds. Although heterogeneous adsorbents have a lower uptake capacity when compared to solvent extraction, the identification of re-usable adsorbents could allow for more sustainable and selective separation of phenolic compounds.
Resins–rigid, crosslinked, synthetic polymers–are well known sorbents in the food industry for phenol extraction [30,31] and sugar refining [32]. The resins are characterized by various physical properties, mostly influenced by the crosslinking in the matrix, which defines the pore structure and surface area [33]. The polymer can be functionalized with either basic or acidic groups, which add ion exchange (IE) to the resin’s separation mechanism, by binding oppositely charged ions [34]. The advantages of resin-based separations include adjustable selectivity, stability and long service life, simple operation, and the possibility of up-scaling using a closed circuit [30,31]. The cost of adsorption processes is sometimes controversially mentioned as an advantage by some authors [31], and a disadvantage by others [30], especially, if the regeneration of the resins involves large amounts of wastewaters [32]. This uncertainty demonstrates that the recovery and maintenance of the resins is of high importance to ensure the economic feasibility of the separation process.
Various factors influence the adsorption and desorption mechanisms of phenols [31] on ion exchange resins. This study aims to practically investigate the efficiency of the removal of phenols from pyrolysis liquids, subsequent extraction efficiency for recovering phenols from resin sorbents, and the influence of resin properties on the sorption mechanisms.
The resins used in this study were as follows: Amberlite XAD-2 (purchased from Supelco, Bellefonte, PA, USA), Sepabeads SP850 (Mitsubishi Chemical Group, Tokyo, Japan), and Lewatit S 5228, S 5528, S 5128, S 6368 A (kindly provided by LanXess, Cologne, Germany). Chemicals were purchased from Sigma-Aldrich (Darmstadt, Germany) and used without additional purification.
The pyrolysis liquids were produced using the pilot equipment of Nova Pangaea Technologies Ltd. (Redcar, UK). The feedstock was birch wood, which was first steam exploded with dilute acid as a pre-treatment. The resultant lignocellulose was subjected to fast pyrolysis in a superheated steam reactor. The typical pyrolysis condensate, which initially contained approximately 94% water, was evaporated for more convenient storage. The evaporated sample was a dark, amorphous paste with 10% moisture, according to gravimetric analysis. For the separation experiments, the paste was dissolved in water and filtered through a Whatman 4 filter paper.
2.3 Comparison of the Phenols Removal Efficiency with Different Resins
Six different resins (see Table 1) were tested for their ability to separate phenols from the pyrolysis product sample. 0.5 g (dry weight) of each resin was weighed (±5 mg) into a glass beaker, 10 mL of water was added, and the resin was allowed to swell for 1 h. Then the resins were washed by stirring the resin in a beaker with 5 mL of water for 10 min, before removing the water by a syringe. This washing was conducted two times.
To begin the adsorption tests, the water was replaced with 5 mL of the pyrolysis product solution (12.5 g/L) and the mixture was stirred for 10 min. The solution was then removed with a syringe and the resin was washed with 5 mL of water three times. When testing recovery of phenols, the final wash solution was removed and replaced with 5 mL of a methanol/water/acetic acid mixture (50/40/10 v/v/v), based on a procedure established in our previous work [35], and again stirred for 10 min. The IE resins were also tested in OH− form, which was obtained by including a conditioning step between the swelling and the first washing. The conditioning was done by adding 5 mL of 0.4% NaOH solution to the resin and stirring for 10 min. The solution was replaced with a further 5 mL of 0.4% NaOH solution. The resin was then repeatedly washed with deionized water until a neutral pH was measured with litmus paper (pH 1–14).
To better understand the separation mechanisms, solutions (1 g/L) of syringic acid and syringaldehyde were treated using the same procedure.
UV/Vis-spectrophotometric measurements were used to characterize the pyrolysis products solution, and the recovered resin extraction fractions. UHPLC-UV was used to characterize the selectivity of each resin, by comparing the pyrolysis product solution before and after mixing with the resins. The experiments were carried out in triplicate.
Removal efficiency was calculated to quantitatively compare the separation of phenols from the pyrolysis products with each resin. The percent of removal efficiency was calculated, based on the initial Ci and final Cf concentrations of phenols (as determined by UV/Vis absorption), as follows [36]:
Removal efficiency (%)=100⋅Ci−CfCi (1)
Similarly, the phenol recovery was based on the initial concentration of phenols Ci and the concentration in the extract Ce, which had the same volume, and calculated by the formula:
Phenol recovery (%)=100−100⋅Ci−CeCi (2)
2.4 Regeneration of the Resins
To evaluate the possibility of sorbent regeneration and re-use, the cycle of adsorbing and desorbing phenols from the pyrolysis liquids was repeated five times with each resin type, as described in Section 2.3. The regeneration was characterized by the removal efficiency of phenols (Eq. (1)) after each cycle. Each cycle was conducted in duplicate. Two types of regeneration were compared:
R1–desorption of phenols using 5 mL of the solvent mixture, consisting of methanol/water/acetic acid mixture (50/40/10 v/v/v), followed by washing with water until a neutral pH was achieved;
R2–desorption of phenols with 5 mL of the same solvent mixture, followed by washing with water and additional treatment with 5 mL of 0.4% NaOH solution, and again followed by washing with water until a neutral pH was achieved.
2.5 Levoglucosan Crystallization
The pyrolysis product solution after treatment with the AcrMp-SBA resin was filtered through a paper filter to remove resin particles, then evaporated under vacuum at 60°C to obtain an orange-brown syrup, which partly crystallized upon cooling to room temperature. 10 g of the sugar fraction was dissolved in 20 mL ethanol, by mixing and heating. The solution was cooled down in an ice bath, vacuum filtered and the obtained crystals were washed twice with cold solvent. Additionally, 0.2 g activated carbon (Norit, Fluka, Amersfoort, the Netherlands) was added to the solution as a final polishing step for LG purification. The hot solution was filtered to remove the carbon and then cooled down, filtered and washed as described previously. The melting point (melting point instrument Mettler Toledo MP70, Giessen, Germany) and specific rotation (polarimeter POLAX-2L, Saitama, Japan) of the pure LG product were determined and compared to a 1,6-anhydro-β-D-glucose standard (99%, Sigma-Aldrich, Darmstadt, Germany).
2.6.1 UV/Vis Spectrophotometry
65 µL of the sample solution was diluted up to 2.5 mL in deionized water, and its absorption at 280 nm was measured in a 1 cm quartz cuvette with a Lambda 25 190–900 nm UV/Vis spectrophotometer. Deionized water was used as a blank.
UV/Vis spectrophotometry was used as the most straightforward quantification method of the separated phenol fractions, but due to of the complexity of the pyrolysis product, calibration with any single model chemical would not provide an accurate result to calculate the total phenolic yield. Therefore, gravimetry was used as a complementary method, as described further.
To evaluate the mass yields of the phenolic compounds, a series of desorption samples with a constant mass of loaded resins were prepared, i.e., the AcrG-SBA resin was mixed with an aqueous solution of the pyrolysis products, decanted, washed with water and allowed to dry at ambient conditions. 5 g of the resins were mixed with various volumes (V)–5, 10, 15, 20, 25, 30 mL–of the desorption solvent mixture for 10 min at room temperature. The UV absorption at 280 nm in the solutions was measured, and the decanted solutions were dried at 103°C until a constant dry mass (m), which was used to calculate the mass concentration in the phenol solutions as follows:
Phenol mass concentration (mgmL)=mdry residueVdesorption solution (3)
The correlation of the phenol mass concentration and UV absorption (Fig. 1) with R2 = 0.994 was used to tentatively calculate the phenolic fraction yield in the extracts.
Figure 1: Relationship between pyrolysis-based phenol mass concentration and UV absorption
Gravimetry was also used to determine the solubility of the condensed pyrolysis product as follows. Pyrolysis product solutions at concentration levels from 25 to 300 g/L were prepared by dissolving concentrated pyrolysis product paste of known masses from 0.5 to 6.0 g in 20 mL of deionized water each, by mixing with a magnetic stir bar for 30 min. This was completed in duplicate. The solutions were filtered through a filter paper and two aliquots of each were dried at 103°C till a constant dry mass, and the solubility was calculated:
Solubility (%)=100%⋅mass concentrationdry residueconcentration level (4)
2.6.3 Ultra-High Performance Liquid Chromatography
A Waters Acquity H-Class UPLC system with a PDA detector was used. The column was Waters Acquity BEH C18 (2.1 mm × 50 mm, 1.7 µm) at temperature 30°C. The eluent consisted of water with 0.1% formic acid and acetonitrile at a flow rate of 0.35 mL/min. A gradient elution was conducted, starting with 5% acetonitrile, which was increased to 25% from 0.2 to 2.6 min, and then to 95% from 3.6 to 5.0 min. The eluent mixture was held constant at 95% acetonitrile until 6.0 min, afterwards the system was equilibrated back to 5% acetonitrile. The injection volume was 2 µL, and the sample solutions were filtered with Nylon syringe filters (Kinesis, 25 mm, 0.2 µm). The UV measurements were done at 280 nm wavelength. These analyses were carried out in triplicate and the standard deviation of the retention times was <1% in all cases. Retention times and UV spectra of the detected peaks were compared to 0.2 mg/mL phenol and furan derivative standards (furfural 99%, 5-hydroxymethylfurfural ≥99%, vanillic acid 97%, vanillin 99%, 2,6-dimethoxyphenol 99%, syringaldehyde 98%, syringic acid ≥95%, 3,5-dimethoxy-4-hydroxyacetophenone 97%) obtained from Sigma-Aldrich.
2.6.4 Chemical Analysis of the Pyrolysis Products
The pyrolysis product solution to be used in the resin tests was analyzed with previously reported methods: iodometric titration [37] to determine the content of levoglucosan, potentiometric titration of aldehydes [38], and the Folin-Ciocalteu method [16] for determining the content of phenols as gallic acid equivalents. Additionally, the solubility of the pyrolysis product paste was characterized by gravimetric analysis of the solution filtrate–the filtrate was dried at 103°C until a constant mass was reached.
3.1 Characteristics of the Pyrolysis Liquids
The evaporated pyrolysis product was comparable to low-moisture bio-oil in terms of its overall characteristics (dark viscous mass with a distinct odour [39]), but was rich in levoglucosan. Chemical analysis, as described in Section 2.6.4, showed that the sample contained 525 ± 11 mg/g LG, 294 ± 6 mg/mL aldehydes (as furfural equivalents), and 200 ± 20 mg/g phenols (as gallic acid equivalents determined by the Folin-Ciocalteu method). UHPLC analysis showed the presence of such compounds as vanillic acid, syringic acid, vanillin, syringaldehyde, syringol, acetosyringone, as well as furan derivatives–furfural, 5-hydroxymethylfurfural, and 5-methylfurfural. Pyrolysis liquids are generally complicated samples, which require a combination of various analytical methods to fully understand their chemical composition [40]. The analysis reported in this paper does not aim to completely characterize the composition of the pyrolysis liquid, but serves to highlight the potential of pyrolysis products as a source of a high yield of LG, as well as several aromatic compounds. For example, lignin-based vanillic acid and syringic acid have been recently praised for their bioactivity and potential use in medicine [41], and phenol derivatives in general are viewed as antioxidants [42].
To reduce water consumption in the whole biorefinery system, it would be practical to work with as concentrated solutions as possible, therefore, Fig. 2 illustrates the solubility of the pyrolysis product in water. It was decided to work with up to 20 g/L concentration for the small-scale study for convenience, but for up-scaling higher concentrations (up to 100 g/L) may be considered to save dilution water and energy for evaporation. The results from this study should also be applicable to pyrolysis condensates directly obtained from steam-assisted pyrolysis condenser systems without a dilution step.
Figure 2: Solubility of the pyrolysis product in water depending on the concentration level
3.2 Removal of Phenols from Pyrolysis Liquids with the Various Resins
Nine resin forms were compared in small scale batch experiments to evaluate their phenols removal efficiency for a real pyrolysis product sample (Fig. 3). Two resins were unfunctionalized polystyrene-DVB polymers with different pore sizes (St90Å and St38Å). Another three of the resins were strongly basic anion exchange resins. These three were tested both in their original Cl− form, and also in OH− form. Among these three, one was macroporous polysterene-DVB based (StMp-SBA), another was a macroporous polyacryate-based SBA resin (AcrMp-SBA), and one was a gelular polyacrylate-based SBA resin (AcrG-SBA). One final resin, which was used as received in its free base form, was a weakly basic anion exchange resin with a gelular polyacrylate matrix (AcrG-WBA).
Figure 3: The phenols removal efficiency of six resins when applied to a pyrolysis liquid sample (the grey arrows denote the increase of the phenols removal efficiency based on the replacement of the Cl− ions with OH− ions)
3.2.1 Evaluation of the Phenols Removal Efficiency by UV/Vis Spectrophotometry
Fig. 3 summarizes the removal of phenols from the pyrolysis products, i.e., adsorption efficiency of all the resins when applied to a sample of pyrolysis liquid. In the case of styrenic resins, the pore size made a significant difference in the phenol adsorption. The St38Å resin, with smaller pores, was approximately three times more effective (removal efficiency: 50 ± 1% compared to 15 ± 1%) at adsorbing phenols than the macroporous unfunctionalized resin St90Å. However, the results obtained with the third styrenic resin StMp-SBA showed that even a macroporous resin achieved higher phenols removal efficiency when functionalized with strongly basic groups (61 ± 1% in Cl− form, and 88 ± 2% in OH− form), which indicates that the phenols’ interaction with the functional groups of the resins plays a more significant role that the π-π interactions with the resin matrix.
All the functionalized resins showed comparable phenol removal efficiency, which supports the hypothesis, that resin functional groups had a more significant impact on the adsorption of phenols than the differences in the resin matrix. The SBA resins in their OH− forms showed comparable removal efficiency, with results ranging from 83 ± 2% to 88 ± 3% (within error of one another). The WBA resin in its free base form showed slightly lower removal efficiency with a 74 ± 1% result. The results of the acrylic SBA resins in the Cl− form were also very similar, regardless of pore size (from 41 ± 7% for the AcrG-SBA to 44 ± 2% for the AcrMp-SBA). The styrenic SBA resin in the Cl− form had a higher phenol removal efficiency than the other resins in their Cl− forms (61 ± 1% compared to the 41%–44% range of the acrylic resins), indicating that the phenol π-π attraction with the aromatic rings in the resin matrix may have a complementary impact on the phenol removal from the pyrolysis liquids, even though in other instances acrylic resins have been reported as more efficient for adsorption of hydrophilic compounds [43]. That being said, the overall trend was for the counter-ion to have the greatest effect on the efficiency of the removal of phenols. When their Cl− counter-ions were exchanged with OH− counter-ions, the increase of the phenol removal was by 97%, 105% and 45% for the AcrMp-SBA, AcrG-SBA and StMp-SBA resins, respectively. It has been reported [44] that, in case of natural organic matter removal from water, the Cl− ion is more efficient when the ion exchange mechanism dominates, while the OH− ion provides H-bonding with hydroxyl groups of the sample compounds, which coincides with the effective removal of the pyrolytic phenols, which often contain methyl esters and always contain OH−groups.
3.2.2 Evaluation of the Purity of the Anhydrosugars Fraction after the Removal of the Phenols
To better understand which specific compounds are removed by these resin treatments, the pyrolysis liquid solution was analyzed with UHPLC-UV before and after treatment. Fig. 4 shows the chromatograms of the initial pyrolysis liquids and the purified samples after the removal of phenols. The main components which were identified in the pyrolysis condensate were 5-hydroxymethylfurfural (1–tR 0.87 min), syringic acid (5–tR 2.54 min), vanillin (6–tR 2.91 min), syringic aldehyde (7–tR 3.11 min), acetosyringone (8–tR 3.34 min), and traces of furfural (2–tR 1.21 min) and vanillic acid (4–tR 2.37 min). A significant unidentified peak (3) was detected at 1.35 min, which is likely to be a furan derivative based on its early retention. The chromatograms show that all resins were selective in adsorbing phenols, but not 5-hydroxymethylfurfural. Semi-quantitative observations show that the peak area of 5-hydroxymethylfurfural did not significantly change, while the peak areas of the phenols were reduced (using unfunctionalized resins and the Cl− form ion exchange resins) or completely removed (using OH− form ion exchange resins). The results obtained with the unfunctionalized resins showed that the pore size influenced the resins’ specificity toward acidic and neutral phenols. In case of St90A, phenol removal efficiency was low comparatively for all identified aromatic compounds, while the St38A resin almost completely removed neutral phenols, but only partly removed the acidic ones. This phenomenon was also later confirmed with syringic acid and syringaldehyde standard solutions in Section 3.2.3. Additionally, it must be noted that the SBA resins in OH− form not only efficiently removed all aromatic compounds, but also appear to have caused the formation of furfural (Peak 2), possibly as a product of the conversion of the unknown compound (Peak 3).
Figure 4: UHPLC-UV chromatograms of the pyrolysis liquids as they were (untreated), compared to after the treatment with the different resins: top–unfunctionalized resins; middle–IE resins in Cl− form; bottom–IE resins in OH− form (peaks: 1–5-hydroxymethylfurfural; 2–furfural; 3–unknown; 4–vanillic acid; 5–syringic acid; 6–vanillin; 7–syringic aldehyde; 8–acetosyringone)
UHPLC-UV analysis showed that the pyrolysis liquids after treatment with IE resins could give a purified anhydrosugars fraction. Fig. 5 illustrates the pathway from the dark amorphous pyrolysis product (1) to the anhydrosugars fraction (2) after the removal of phenols by treatment with the AcrMp-SBA resin, all the way to pure LG (3). The yield of the anhydrosugars fraction was 60% of the pyrolysis product mass, and the yield of the white crystalline LG was 20% after crystallization with ethanol. However, the yield of the final product can be significantly increased by a more efficient continuous crystallization procedure for industrial use or by application of more advanced crystallization techniques, such as ultrasonic-assisted crystallization [45]. The purity of the obtained LG was 97.5 ± 0.9%. The melting point of the obtained LG was 180.6 ± 0.3°C, compared to the 191.5 ± 0.4°C of the commercial standard. The optical rotation was −69 ± 2, compared to −65 ± 2 of the standard.
Figure 5: Images of the evaporated pyrolysis product (1), the anhydrosugars fraction after phenol removal (2) and the crystallized levoglucosan (3)
To further discuss the adsorption mechanisms involved in the separation of phenols by the different resins, standard solutions of syringic acid and syringaldehyde were treated with the resins, as described in the next section.
3.2.3 Standard Phenol Derivative Sorption Test with the Various Resins
Fig. 6 shows some trends in the separation of phenol derivatives, specifically syringic acid and syringaldehyde, from standard solutions. The adsorption of both standards with the St90Å resin (9 ± 2 and 10 ± 2%) was of a similar magnitude to the case of the pyrolysis product sample (15 ± 1%). Likewise, the trend of smaller pores improving the phenols removal efficiency from the sample solution was present. However, it was interesting to observe that syringic acid adsorption on the St38Å resin was lower (36 ± 0.3%) compared to that of syringic aldehyde (89 ± 0.4%), which may be explained by electrostatic exclusion from the tighter pores. The H-bonding of the OH− form resins and the hydroxyl group at C4 position in both standards appears to have had the most significant impact on the adsorption, as seen from the complete removal of both standards (approximately 100%) from the solutions for all IE resins in their basic forms. The slight pH differences in the solutions of syringic acid and syringaldehyde are likely to influence the ion exchange mechanism efficiency in the Cl− form of the IE resins.
Figure 6: Adsorption of syringaldehyde and syringic acid from standard solutions with different resins
Adsorption curves in Fig. 7 give a closer look at the syringaldehyde and syringic acid removal from the standard solutions with two SBA resins. The OH− form resins reached maximum phenolic compound removal efficiency at very low resin mass to standard solution volume ratio, i.e., 0.05 g resin to 5 mL solution (1 g/L). In their Cl− forms, both SBA resins could eventually reach adequate syringic acid removal efficiency (around 90%) by increasing the resin mass to solution volume ratio. However, in case of the neutral syringaldehyde solution, the acrylic matrix of the resin had an inhibitory effect on the removal efficiency. Based on results from the pyrolyzate, which were discussed in Section 3.2.1, and model compound adsorption studies, the impact of the various resin (or adsorbate) characteristics on the removal of phenols from aqueous solutions appears to follow the series: chemical structure of the resin matrix < pore size < adsorbate acidity << presence of basic functionality. The OH− counter ion consistently ensured the highest removal efficiency in all cases.
Figure 7: Adsorption curves of syringaldehyde and syringic acid from standard solutions
3.3 Recovery of Phenols from the Various Resins
Since the aim of this study was not to simply remove phenols from the pyrolysis liquid sample, but to recover the phenolic fraction as a source of value-added products, the phenolic desorption efficiency of each resin was further investigated. Comparison of the UV absorption of the initial pyrolysis product solution and the recovered extracts allowed for the recovery of phenols to be quantified for each resin according to Eq. (2) (Fig. 8). The overall trend of the recovery of phenols was similar to the trend in phenolic removal efficiency shown in Fig. 3, with the exception that the acrylic gelular resins provided a lower recovery result than expected. This indicates that larger pores in the IE allow for better phenolic extraction with the solvent mixture. Based on the calibration curve in Fig. 1, the maximum mass yield of phenols with the AcrMp-SBA in OH− form resin was up to 15% of the pyrolysis product.
Figure 8: Recovery of phenols from the resins with four repeated extractions
Further to this, the influence of temperature on the recovery of phenols was tested by carrying out the extraction at room temperature (22 ± 1°C), 40°C, and 60°C. The recovery of phenols from the AcrG-SBA resin at the three temperatures was 29.5 ± 0.1%, 35.2 ± 0.8%, 33.4 ± 1.2%, respectively. The unremarkable increase of the recovery by approximately 15% is unlikely to justify the energy consumption necessary for process heating. However, if a pyrolysis condensate is treated directly from the condenser system in an industrial biorefinery, energy could be saved by reducing cooling duty on condenser systems and adsorbing phenolic compounds at higher temperatures. Further investigations, including a techno-economic assessment, could provide a definitive answer about the most economically feasible extraction method.
3.4 Regeneration and Re-Use of the Resins
The resins were tested in small batch experiments of pyrolysis liquid separation with repeated regeneration of the resins. Each resin was regenerated and used five times. Two regeneration conditions were compared, as shown in Fig. 9: R1–regeneration only by extracting phenols with the desorption solvent, consisting of methanol, water and acetic acid; R2–regeneration by desorption with the mentioned solvent, followed by a solution of NaOH.
Figure 9: Efficiency of phenols removal from the pyrolysis liquids by the resins with two regeneration conditions: R1–regeneration with the solvent mixture (methanol/water/acetic acid); R2–regeneration with the solvent mixture followed by NaOH
Fig. 9 shows the changes in phenols removal efficiency across the various resins during the five regeneration cycles. When assessing trends in these changes, removal efficiency % was the criteria for confirming a successful regeneration.
The trends of reusability for the various resins over several regeneration cycles were as follows. The three functionality types of the resins–unfunctionalized, WBA and SBA–showed different results after regeneration with the two conditions. The unfunctionalized resins had a significant improvement in the adsorption of phenols after the first regeneration with both methods R1 and R2. This increase could be explained by a pore activation induced by treatment with the methanol-containing solvent mixture. This hypothesis was confirmed by an additional experiment, in which phenolic removal efficiency was tested for St90Å, St38Å and AcrG-SBA with an alternative conditioning step before mixing with the pyrolysis product solution. These alternative conditioning tests were done by stirring each resin with either deionized water, methanol, or the desorption solvent mixture consisting of methanol, water and acetic acid. The results in Table 2 illustrate how the phenol removal efficiency improved for both unfunctionalized resins, after having been soaked in methanol or methanol-containing solution, while the SBA resin maintained the same efficiency. It should be noted that the two unfunctionalized resins showed different magnitudes of increase in their phenolic removal efficiency, when comparing water and the solvent mixture. The St90Å resin improved 4.6 times, while the St38Å only had an 8.3% improvement. St90Å resin showed the same improvement in Fig. 9 (improved removal efficiency 4.5 times after the 1st cycle), while the St38Å resin improved 1.9 times.
Fig. 9 shows that the SBA resins lost significant capacity of phenolic adsorption (by 46%–58%) in case of R1, when NaOH solution was not used, because the OH− counter ions were not restored, and the removal capacity of phenols dropped to the level of Cl− form resins as was seen in Fig. 2. This suggests that the adsorption of the phenols on SBA resins is not influenced by the Cl− counter ion at all. In the case of R2 regeneration, when NaOH solution was used, the removal capacity of phenols remained at an overall 80–90 % for the SBA resins. The molar equivalents of NaOH required to induce this regeneration [46] should be further investigated to fully understand regeneration efficiency in this process. Although the StMp-SBA resin showed successful regeneration of its adsorption capacity, it physically degraded after mechanical mixing and could be used through only four cycles. However, with shaking instead of mixing this obstacle could be overcome in batch experiments, while in industrial applications, resins are often applied using packed columns. A resin bed with backwash and regeneration cycles is likely to see less mechanical attritional breaking. This could be included in a further study on the industrial application of this process.
In case of the WBA resin, there was a similar trend of a decreased removal capacity in case of R1 regeneration. The WBA resin also showed a relatively small capacity drop (13%) with the R2 regeneration, indicating that for the regeneration of WBA resin the concentration of the NaOH solution may need to be adjusted for optimal performance. The level of the recovery of phenols was also maintained after the five cycles, proportionate to the efficiency of the removal of phenols for all resin types.
To further adhere to green chemistry principles which state that the recovery and reuse of solvents is a significant step towards better sustainability [47], the reusability of the desorption solvent was tested. When the phenolic extract in the mixture of methanol/water/acetic acid was concentrated by evaporation, the condensed solvent was reused for repeated extraction of phenols. Upon reuse, a decrease of extraction efficiency by 35%–40% was observed. This decrease was determined to be due to acetic acid loss during the evaporation step. However, the acetic acid content can be controlled by simple titration, and the acid loss can be compensated by spiking with respective amounts of acetic acid, which returned functionality to the solvent mixture. This confirms that it is possible to recycle most of the solvents used in the desorption step.
These experiments provide insights into the sorption mechanisms of pyrolytic phenols on various resins. And the results support the hypothesis that SPE is suitable for the separation of LG and phenols from the condensable wood pyrolysis products. SPE using porous resins provides an anhydrosugars rich fraction for the purification of LG, and a phenolic compound fraction as a potential value-added product in a wood pyrolysis-based biorefinery. Based on results from adsorption, recovery and regeneration trials, the adsorption of the pyrolytic phenols on the resins is influenced by various factors in the following ascending order: chemical structure of the resin matrix < pore size < adsorbate acidity << counter ion. The dominance of resin counter ion as a factor to determine the effect of adsorption is evidenced by the significant increases in resin removal efficiency towards phenols when functionalized, particularly OH− form resins are used. The contribution from adsorbate acidity was determined through examination of the specific phenolic compounds that were adsorbed by each resin. Therefore, the most suitable resins of those tested for the removal of phenols from pyrolysis condensates are strongly basic anion exchange resins in OH− form. The results also demonstrate that recovery of phenols is possible by solvent extraction. Recovery of phenols by desorption is more effective in macroporous resins, when compared to gelular. This was demonstrated by the improved recovery of phenols with these resins through solvent extraction. To further advance this method, green chemistry aspects need to be considered for environmental and economic benefits when implementing solid phase extraction for the separation of pyrolysis products. Potential approaches to improving resource efficiency include treating condensate directly or at higher concentrations to save evaporation energy, avoiding energy use from heat transfer by assessing adsorption efficiency vs. pyrolyzate temperature, as well as the reuse of sorbent materials and solvents.
Acknowledgement: The authors are truly grateful to PhD Daniela Godina, and Prof. Dr. Chem. Arturs Viksna for the levoglucosan purity tests carried out at the Department of Chemistry, University of Latvia, and the shared passion for analytical chemistry.
Funding Statement: The study was funded by the Bioeconomy grant at the Latvian State Institute of Wood Chemistry “Transition to Greener Analytical Chemistry for the Analysis of Biorefinery Products With Liquid Chromatography” (No. 03-24).
Author Contributions: The authors confirm contribution to the paper as follows: study conception and design: Kristine Meile, Aivars Zhurinsh; data collection: Martins Romanovskis, Kristine Meile; analysis and interpretation of results: Kristine Meile, Martins Romanovskis, Thomas Nicol, Neil Hindle; draft manuscript preparation: Kristine Meile, Thomas Nicol. All authors reviewed the results and approved the final version of the manuscript.
Availability of Data and Materials: The data that support the findings of this study are available from the corresponding author, Kristine Meile, upon reasonable request.
Ethics Approval: Not applicable.
Conflicts of Interest: The authors declare no conflicts of interest to report regarding the present study.
References
1. Singh R, Krishna BB, Mishra G, Kumar J, Bhaskar T. Strategies for selection of thermo-chemical processes for the valorisation of biomass. Renew Energy. 2016;98:226–37. doi:10.1016/j.renene.2016.03.023. [Google Scholar] [CrossRef]
2. Amenaghawon AN, Anyalewechi CL, Okieimen CO, Kusuma HS. Biomass pyrolysis technologies for value-added products: a state-of-the-art review. Environ Develop Sustain. 2021;23(10):14324–78. doi:10.1007/s10668-021-01276-5. [Google Scholar] [CrossRef]
3. Paine JB, Pithawalla YB, Naworal JD. Carbohydrate pyrolysis mechanisms from isotopic labeling. Part 5. The pyrolysis of D-glucose: the origin of the light gases from the D-glucose molecule. J Anal Appl Pyrol. 2019;138:70–93. doi:10.1016/j.jaap.2018.12.010. [Google Scholar] [CrossRef]
4. Cao J, Liaw SB, Long Y, Yu Y, Wu H. Formation of reaction intermediates and primary volatiles during acid-catalysed fast pyrolysis of cellulose in a wire-mesh reactor. Proc Combust Inst. 2020;38(3):4301–8. [Google Scholar]
5. Yang X, Fu Z, Han D, Zhao Y, Li R, Wu Y. Unveiling the pyrolysis mechanisms of cellulose: experimental and theoretical studies. Renew Energy. 2020;147:1120–30. doi:10.1016/j.renene.2019.09.069. [Google Scholar] [CrossRef]
6. Werpy T, Petersen Geditors. Top value added chemicals from biomass. Volume I—results of screening for potential candidates from sugars and synthesis gas. USA: US Department of Energy; 2004. [Google Scholar]
7. Itabaiana Junior I, Avelar Do Nascimento M, De Souza ROMA, Dufour A, Wojcieszak R. Levoglucosan: a promising platform molecule? Green Chem. 2020;22(18):5859–80. doi:10.1039/D0GC01490G. [Google Scholar] [CrossRef]
8. Gao Z, Li N, Wang Y, Niu W, Yi W. Pyrolysis behavior of xylan-based hemicellulose in a fixed bed reactor. J Anal Appl Pyrolysis. 2020;146:104772. doi:10.1016/j.jaap.2020.104772. [Google Scholar] [CrossRef]
9. Lou R, Wu S, Lyu G. Quantified monophenols in the bio-oil derived from lignin fast pyrolysis. J Anal Appl Pyrol. 2015;111:27–32. doi:10.1016/j.jaap.2014.12.022. [Google Scholar] [CrossRef]
10. Zhu X-F, Lu Q. Production of chemicals from selective fast pyrolysis of biomass. In: Momba MNB, editor. Biomass. Croatia: Sciyo; 2010. [Google Scholar]
11. Zadeh ZE, Abdulkhani A, Aboelazayem O, Saha B. Recent insights into lignocellulosic biomass pyrolysis: a critical review on pretreatment, characterization, and products upgrading. Processes. 2020;8(7):799. doi:10.3390/pr8070799. [Google Scholar] [CrossRef]
12. Rover MR, Aui A, Wright MM, Smith RG, Brown RC. Production and purification of crystallized levoglucosan from pyrolysis of lignocellulosic biomass. Green Chem. 2019;21(21):5980–9. doi:10.1039/C9GC02461A. [Google Scholar] [CrossRef]
13. Lian J, Chen S, Zhou S, Wang Z, O’Fallon J, Li C-Z, et al. Separation, hydrolysis and fermentation of pyrolytic sugars to produce ethanol and lipids. Biores Technol. 2010;101(24):9688–99. doi:10.1016/j.biortech.2010.07.071. [Google Scholar] [PubMed] [CrossRef]
14. Lindfors C, Kuoppala E, Oasmaa A, Solantausta Y, Arpiainen V. Fractionation of bio-oil. Energy Fuels. 2014;28(9):5785–91. doi:10.1021/ef500754d. [Google Scholar] [CrossRef]
15. Meile K, Iljina N, Zhurinsh A. Desorption of phenols from anion exchange resins after the separation of wood pyrolysis products. Key Eng Mater. 2019;800:256–60. doi:10.4028/www.scientific.net/KEM.800.256. [Google Scholar] [CrossRef]
16. Stanford JP, Hall PH, Rover MR, Smith RG, Brown RC. Separation of sugars and phenolics from the heavy fraction of bio-oil using polymeric resin adsorbents. Separat Purif Technol. 2018;194(6):170–80. doi:10.1016/j.seppur.2017.11.040. [Google Scholar] [CrossRef]
17. Yang C, Zhang B, Moen J, Hennessy K, Liu Y, Lin X, et al. Fractionation and characterization of bio-oil from microwave-assisted pyrolysis of corn stover. Int J Agricult Biolog Eng. 2010;3(3):54–61. [Google Scholar]
18. Westerhof RJM, Brilman DWF, Garcia-Perez M, Wang Z, Oudenhoven SRG, van Swaaij WPM, et al. Fractional condensation of biomass pyrolysis vapors. Energy Fuels. 2011;25(4):1817–29. doi:10.1021/ef2000322. [Google Scholar] [CrossRef]
19. Rover MR, Johnston PA, Jin T, Smith RG, Brown RC, Jarboe L. Production of clean pyrolytic sugars for fermentation. ChemSusChem. 2014;7(6):1662–8. doi:10.1002/cssc.201301259. [Google Scholar] [PubMed] [CrossRef]
20. Dalluge DL, Whitmer LE, Polin JP, Choi YS, Shanks BH, Brown RC. Comparison of direct and indirect contact heat exchange to improve recovery of bio-oil. Appl Energy. 2019;251(3):113346. doi:10.1016/j.apenergy.2019.113346. [Google Scholar] [CrossRef]
21. Westerhof RJM, Kuipers NJM, Kersten SRA, van Swaaij WPM. Controlling the water content of biomass fast pyrolysis oil. Indus Eng Chem Res. 2007;46(26):9238–47. doi:10.1021/ie070684k. [Google Scholar] [CrossRef]
22. Ren S, Ye XP. Stability of crude bio-oil and its water-extracted fractions. J Anal Appl Pyrol. 2018;132:151–62. doi:10.1016/j.jaap.2018.03.005. [Google Scholar] [CrossRef]
23. Chum HL, Black SK, Diebold JP, Kreibich RE. Phenolic compounds containing/neutral fractions extract and products derived therefrom from fractionated fast-pyrolysis oils. United States Patent 5223601. Available from: www.nrel.gov/docs/patents/42742.pdf. [Accessed 2024]. [Google Scholar]
24. Rover MR, Brown RC. Quantification of total phenols in bio-oil using the Folin-Ciocalteu method. J Anal Appl Pyrol. 2013;104:366–71. doi:10.1016/j.jaap.2013.06.011. [Google Scholar] [CrossRef]
25. del Campo BGeditor. Production of activated carbon from fast pyrolysis biochar and the detoxification of pyrolytic sugars for ethanol fermentation (Graduate Thesis and Dissertations) Iowa State University: USA; 2015. [Google Scholar]
26. Dąbrowski A, Podkościelny P, Hubicki Z, Barczak M. Adsorption of phenolic compounds by activated carbon—a critical review. Chemosphere. 2005;58(8):1049–70. doi:10.1016/j.chemosphere.2004.09.067. [Google Scholar] [PubMed] [CrossRef]
27. Terzyk AP. Further insights into the role of carbon surface functionalities in the mechanism of phenol adsorption. J Coll Interf Sci. 2003;268(2):301–29. doi:10.1016/S0021-9797(03)00690-8. [Google Scholar] [PubMed] [CrossRef]
28. Sáenz de Miera B, Cañadas R, Santiago R, Díaz I, González-Miquel M, González EJ. A pathway to improve detoxification processes by selective extraction of phenols and sugars from aqueous media using sustainable solvents. Sep Purif Technol. 2022;299:121675. doi:10.1016/j.seppur.2022.121675. [Google Scholar] [CrossRef]
29. Li X, Luque-Moreno LC, Oudenhoven SRG, Rehmann L, Kersten SRA, Schuur B. Aromatics extraction from pyrolytic sugars using ionic liquid to enhance sugar fermentability. Biores Technol. 2016;216(1):12–8. doi:10.1016/j.biortech.2016.05.035. [Google Scholar] [PubMed] [CrossRef]
30. Hu Y, Yan B, Chen Z-S, Wang L, Tang W. Recent technologies for the extraction and separation of polyphenols in different plants: a review. J Renew Mater. 2022;10(6):1471–90. doi:10.32604/jrm.2022.018811. [Google Scholar] [CrossRef]
31. Soto ML, Moure A, Domínguez H, Parajó JC. Recovery, concentration and purification of phenolic compounds by adsorption: a review. J Food Eng. 2011;105(1):1–27. doi:10.1016/j.jfoodeng.2011.02.010. [Google Scholar] [CrossRef]
32. Susanto H, Roihatin A, Widiasa IN. Production of colorless liquid sugar by ultrafiltration coupled with ion exchange. Food Bioprod Process. 2016;98:11–20. doi:10.1016/j.fbp.2015.12.002. [Google Scholar] [CrossRef]
33. dos Santos FKF, de Rezende CM, da Veiga Júnior VF. Macroporous polymeric resins as a tool to obtain bioactive compounds in food and food-waste: a review. J Food Compost Anal. 2022;114:104703. doi:10.1016/j.jfca.2022.104703. [Google Scholar] [CrossRef]
34. Hassan MM, Carr CM. A critical review on recent advancements of the removal of reactive dyes from dyehouse effluent by ion-exchange adsorbents. Chemosphere. 2018;209:201–19. doi:10.1016/j.chemosphere.2018.06.043. [Google Scholar] [PubMed] [CrossRef]
35. Meile K, Jermolajeva A, Volkova E, Zhurinsh A. Solid-phase extraction of the aromatic by-products obtained by fast pyrolysis of pretreated lignocellulose. Chem Eng Technol. 2023;46(6):1212–7. doi:10.1002/ceat.v46.6. [Google Scholar] [CrossRef]
36. Víctor-Ortega MD, Ochando-Pulido JM, Airado-Rodríguez D, Martínez-Ferez A. Comparison between different ion exchange resins combinations for final treatment of olive mill effluent. Separat Purif Technol. 2016;158:374–82. doi:10.1016/j.seppur.2015.12.041. [Google Scholar] [CrossRef]
37. Meile K, Syrpas M, Basinskiene L, Zhurinsh A. Discrimination of levoglucosan and its structural isomer in biomass pyrolysis products by iodometry, liquid chromatography, mass spectrometry. J Anal Appl Pyrolysis. 2022;166:105602. doi:10.1016/j.jaap.2022.105602. [Google Scholar] [CrossRef]
38. Oasmaa A, Meier D. Analysis, characterization and test methods of fast pyrolysis liquids. In: Bridgwater AV, editor. Fast pyrolysis of biomass: a handbook. UK: CPL Press; 2002. p. 23–35. [Google Scholar]
39. Bridgwater AV, Czernik S, Piskorz J. The status of biomass fast pyrolysis. In: Bridgwater AV, editor. Fast pyrolysis of biomass: a handbook. UK: CPL Press; 2002. p. 1–22. [Google Scholar]
40. Choi YS, Johnston PA, Brown RC, Shanks BH, Lee K-H. Detailed characterization of red oak-derived pyrolysis oil: integrated use of GC, HPLC, IC, GPC and Karl-Fischer. J Anal Appl Pyrol. 2014;110:147–54. doi:10.1016/j.jaap.2014.08.016. [Google Scholar] [CrossRef]
41. Mota MIF, Barbosa S, Pinto PCR, Ribeiro AM, Ferreira A, Loureiro JM, et al. Adsorption of vanillic and syringic acids onto a macroporous polymeric resin and recovery with ethanol: water (90:10 %V/V) solution. Separat Purif Technol. 2019;217:108–17. [Google Scholar]
42. Lu X, Jiang J, Sun K, Sun Y, Yang W. Enhanced antioxidant activity of aqueous phase bio-oil by hydrothermal pretreatment and its structure-activity relationship. J Anal Appl Pyrolysis. 2021;153(4):104992. doi:10.1016/j.jaap.2020.104992. [Google Scholar] [CrossRef]
43. Bolto B, Dixon D, Eldridge R, King S, Linge K. Removal of natural organic matter by ion exchange. Water Res. 2002;36(20):5057–65. doi:10.1016/S0043-1354(02)00231-2. [Google Scholar] [PubMed] [CrossRef]
44. Laforce E, Stals I, Cornelissen ER, Vermeir P, De Clercq J. Revealing the effect of anion exchange resin conditioning on the pH and natural organic matter model compounds removal mechanisms. J Environ Chem Eng. 2022;10(5):108315. doi:10.1016/j.jece.2022.108315. [Google Scholar] [CrossRef]
45. Xiang L, Fu M, Wang T, Wang D, Xu H, Miao W, et al. Application and development of ultrasound in industrial crystallization. Ultrason Sonochem. 2024;111(6):107062. doi:10.1016/j.ultsonch.2024.107062. [Google Scholar] [PubMed] [CrossRef]
46. Tamizharasan S, Muralidharan R, Abirami N, Leelavathi H, Siva A, Kumarasamy A, et al. Biomass derived carbon blended ion-exchange resins for the removal of toxic metal ions from waste water. Optik. 2023;283:170930. doi:10.1016/j.ijleo.2023.170930. [Google Scholar] [CrossRef]
47. Aboagye EA, Chea JD, Yenkie KM. Systems level roadmap for solvent recovery and reuse in industries. iScience. 2021;24(10):103114. doi:10.1016/j.isci.2021.103114. [Google Scholar] [PubMed] [CrossRef]
Cite This Article
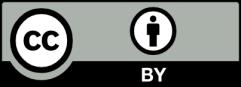
This work is licensed under a Creative Commons Attribution 4.0 International License , which permits unrestricted use, distribution, and reproduction in any medium, provided the original work is properly cited.