Open Access
ARTICLE
Improvement of the Birch Outer Bark Plywood Binder: The Impact of the Bark Fractional Composition and the Binder Preparation Methodology
Latvian State Institute of Wood Chemistry, Riga, LV-1006, Latvia
* Corresponding Author: Rūdolfs Bērziņš. Email:
(This article belongs to the Special Issue: Advances in Biorefinery Technologies and Products – 2024)
Journal of Renewable Materials 2024, 12(12), 2095-2113. https://doi.org/10.32604/jrm.2024.056769
Received 30 July 2024; Accepted 21 October 2024; Issue published 20 December 2024
Abstract
Birch outer bark (BOB) from Betula pendula Roth. is a unique and valuable biomass feedstock that contains suberin. The biopolyester suberin is built from bifunctional fatty acids-suberinic acids (SA)-which can be obtained through a depolymerization process in an alkaline medium and used as a binder due to their adhesive properties. The aim of this study was to develop the SA-containing binder and identify suitable pressing conditions to produce plywood that meets the shear strength requirements of the EN 314-2 standard 3rd moisture resistance class for bonding quality, ensuring durability in unprotected exterior conditions (shear strength ≥ 1 N/mm2). The raw BOB material was modified by extraction, milling, and fractionation, and the depolymerization methodology was enhanced by additional sieving to improve the adhesive properties of the obtained binders. Several analytical methods were used to characterize the feedstock and the binders. Higher heating value was used to assess the pure outer bark content of BOB. GC-MS and GPC were used to describe the monomeric and oligomeric composition of binders. TGA was used to describe the biopolymeric composition and DSC was used to determine the thermal behavior of the binders. As a result, successful modification of feedstock (extracted BOB, milled through 2 mm sieve, 1–2 mm fraction used) and its depolymerization process (implementing the separation of coarse ligno-carbohydrate particles by 1 mm mesh sieve) was employed to obtain a binder for which suitable hot-pressing parameters were determined −200°C for 5 min at 1.8 MPa. Consequently, plywood with shear strength of 1.26 ± 0.18 N/mm2, which adheres to the EN 314-2 standards 3rd moisture resistance class, was obtained.Graphic Abstract
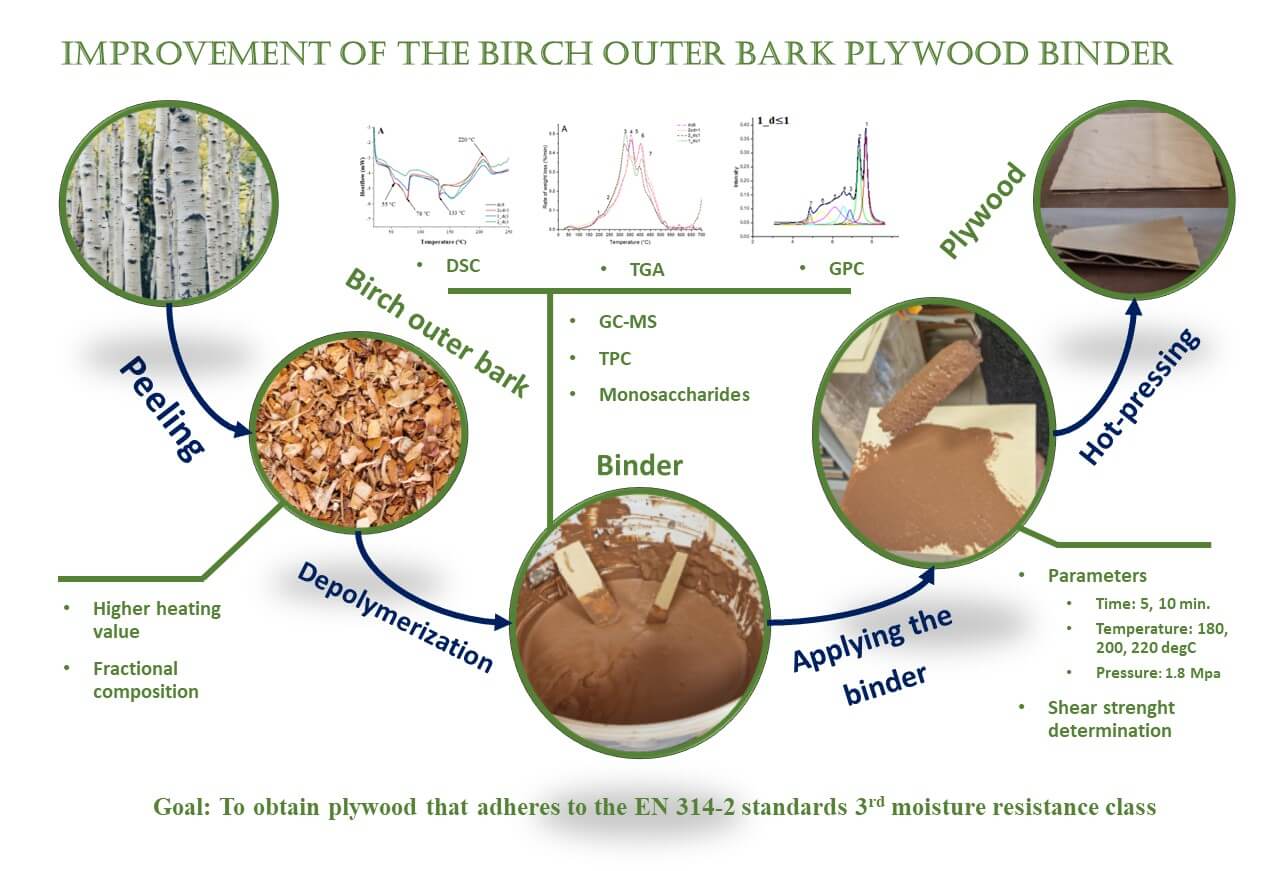
Keywords
Nomenclature
BB | Birch bark |
BOB | Birch outer bark biomass |
EBOB | Extracted birch bark biomass |
d | Particle diameter |
SA | Suberinic acids |
TPC | Total polyphenol content |
GC-MS | Gas chromatography, mass spectrometry |
GPC | Gel permeation chromatography |
TGA | Thermogravimetric analysis |
DSC | Differential scanning calorimetry |
The increasing focus on environmental sustainability has spurred efforts to develop bio-based composite materials as innovative alternatives to traditional, non-renewable synthetic materials. Wood-based composites represent a broad category of products where wood is combined with other wood or non-wood materials. These composites are designed with multiple objectives in mind:
1. Efficiently utilize small-diameter assortments, low-grade timber, and forest residues;
2. Minimize the use of wood or other materials, thereby reducing costs or addressing the limited availability of certain components;
3. Produce end products with superior properties and consistency compared to the individual materials used;
4. Create products tailored to meet specific performance criteria, such as thermal and sound insulation, durability, water resistance, mechanical strength, and bonding [1,2].
Among the various types of wood composites, plywood is a widely used material for both outdoor and indoor applications. Traditionally, plywood is manufactured using formaldehyde-based binders due to their high reactivity, chemical versatility, and cost-effectiveness [3]. However, these binders emit free formaldehyde, a substance classified as carcinogenic [4]. As a result, formaldehyde-containing binders pose a toxicity risk to humans during both the production and use. Therefore, the need for non-toxic plywood, produced from environmentally sustainable materials, drives the development of alternative binders. So far binders from chitosan [5], soy proteins [6] and birch bark [7] have been investigated. Birch bark (BB) has been utilized as a partial substitute for formaldehyde-containing binder. For instance, BB biomass particles have been used as additives to replace 20 wt% of urea-formaldehyde binders in plywood production, successfully reducing free formaldehyde emissions [8]. In another research, BB components have been used as additives to replace 30 wt% of phenol-formaldehyde binder to obtain plywood without significant loss of bending strength and moisture resistance [9]. As described in the patent [10], a successful plywood binder from pure BB biocomponent—birch outer bark (BOB) has been developed. To our knowledge, an adaptation of BOB processing and binder obtaining methodology for industrial feedstock is unprecedented in scientific literature.
BOB is usually produced as a by-product of plywood production after peeling logs of Betula pendula Roth. and Betula pubescens Ehrh., which are common birch tree species in northern Europe [11]. Until now, most of BOB is burned in the factory for heat energy. However, it is a unique and valuable biomass feedstock [12]. Peeled BOB contains outer bark and inner bark biomass components [13], which include suberin, biologically active substances (such as triterpenes and polyphenols), carbohydrates, lignin, and cellulose [14–16]. Pure outer bark can contain up to 45% suberin, while inner bark—up to 25% [17]. Additionally, the inner bark has a higher content of carbohydrates and lignin than the pure outer bark [17]. A common method of processing BOB involves extraction to obtain the biologically active substances [18]. Among these substances, triterpenes like betulin and lupeol have potential applications in pharmaceutical and cosmetic product development [19]. For example, betulin particles can be incorporated into a hydrogel, oleogel or an emulsion matrix [20–23]. Furthermore, the remaining solid residue after extraction—extracted BOB (EBOB)—can still be used to produce other high-value-added products from suberin. Suberin, a biopolyester, can be further processed as a binder [24] or for polyol synthesis [25]. To use suberin as a plywood binder, it must be depolymerized into its monomeric or oligomeric components—suberinic acids (SA) [26]. The depolymerization of suberin can be performed in an alkaline water or organic solvent medium [27], where the obtained SA salts can be precipitated from water as free acids by acidification. The SA composition primarily consists of ω -hydroxy fatty acids, α , ω -dicarboxylic acids, aliphatic alcohols and aromatic acids. To date, a complete degree of depolymerization of suberin from BOB has not been achieved, leading to a mixture of SA oligomers and monomers after depolymerization. Additionally, given the complexity of BOB as a feedstock, it is expected that other biopolymers (such as lignin and carbohydrates) or extractive substances (like betulin) may be present in the SA mixture post-depolymerization. The overall composition of these components depends on the feedstock pretreatment and depolymerization conditions [26].
To assess the moisture resistance quality of obtained plywood, EN 314-2 [28] standard can be utilized, following the methods outlined in the EN 314-1 [29] standard. The EN 314-2 standard defines three classes based on the bonding quality tests that the corresponding plywood samples must meet:
• Class 1: Dry conditions—suitable for interior applications with no risk of wetting.
• Class 2: Humid conditions—appropriate for protected exterior conditions, such as behind cladding or under roof coverings.
• Class 3: Exterior conditions—suitable for exposure to weather over sustained periods or continuous exposure to relatively high humidity.
Class 3 test requires the plywood to withstand 3 cycles of treatment—boiling in water for 4 h, drying for 20 h at 60°C, repeated boiling in water for 4 h and submersion in water for 1 h—after which the shear strength of the plywood glue line must be ≥1 N/mm2 to automatically comply with the 3rd moisture resistance class.
In our previous research we successfully developed the depolymerization process of suberin [26] and obtained SA containing mixture, using it as a binder for particle boards [24]. The aim of this study was to develop a SA-containing binder and identify suitable pressing conditions to produce plywood that meets the shear strength requirements of the EN 314-2 standard for bonding quality in the 3rd moisture resistance class, ensuring durability in unprotected exterior conditions over extended period of time [28].
Isolated and fractionated BOB and EBOB (moisture content 4–5 wt%, d < 6 mm) was kindly supplied by BetulinLab from AS Latvijas Finieris (Riga, Latvia). The feedstock was prepared by milling in an SM 100 cutting mill (Retsch GmbH, Germany) and fractionating by sieving using an AS 200 Basic vibratory sieve shaker (Retsch GmbH, Germany).
Potassium hydroxide (KOH) (Reag. Ph Eur, 85.0%–100.5%) was provided by VWR International (Leuven, Belgium). Nitric acid (HNO3) (≥65%) was obtained from Honeywell (Seelze, Germany). Dimethyl sulfoxide (≥99.9%) and sodium hydroxide (KOH) (≥85%), Folin & Ciocalteu’s phenol reagent, suitable for determination of TPC (1.9–2.1 N) and sodium carbonate (≥99.9%) were purchased from ACS reagent (New York, USA). Tetrahydrofuran (THF), anhydrous (≥99.9%), inhibitor-free; pyridine, suitable for HPLC (≥99.9%), gallic acid, (97.5%–102.5%) (titration) and silylating mixture III, for gas chromatography derivatization were all purchased from Merck Chemicals (Darmstadt, Germany).
The raw BOB or EBOB depolymerization was carried out in a pilot-scale 30 L steel reactor equipped with a steam heating jacket, reflux condenser and a mechanical stirrer. Water solution of 4 wt% KOH was used for depolymerization and the bark was suspended at bark particle:liquid mass ratio—1:10. The depolymerization was carried out at 90°C for 30 min, after that the suspension was cooled to 20°C and acidified with HNO3 to pH = 2. Then the mixture was filtered in a polypropylene filter bag with a fabric mesh size of 100 microns, rinsed with water and filtered again to separate water soluble KNO3 and to obtain SA containing binder; solid content was 20%.
Also, an additional step for the depolymerization process was tested: after the rinsing, most of the remaining coarse particles were separated from the mixture with a metal sieve of 1 mm size.
The fractional composition of raw BOB and EBOB materials was determined with AS 200 basic sieve shaker (Retsch, Germany). The fractions were separated by a particle diameter (d) of d > 4; 4 ≥ d > 2; 2 ≥ d > 1.4; 1.4 ≥ d > 1; d ≤ 1 mm. Additionally, the pure outer/inner bark proportion of the samples was determined from higher heating value results (ISO 18125:2017 [30]) and calculated according to a specially created graph and its calibration curve equation, described in our previous research [17]. Moisture and dry matter content were determined with MLB 50-3 moisture analyzer (KERN, Germany).
2.4 Analysis of the Obtained Binders
For the analysis of the compounds present in the binder, first the binder paste was dried at room temperature to a constant mass. Then the milling was carried out by Cryomill cryogenic mill (Retsch, Germany). Liquid nitrogen was used to maintain a −196°C temperature during the milling (25 Hz for 10 min). As a result, a dry binder powder sample for analysis was obtained.
2.4.2 Determination of the Solid Residue
2 mL of THF was added to approximately 0.2 g of SA sample in a glass tube and left for 24 h at room temperature. The sample solutions were then filtered through preheated and weighed glass filters and heated at 105°C to constant mass.
2.4.3 GC-MS Analysis of SA Samples
For GC-MS analysis SA samples were converted to the corresponding trimethylsilyl (TMS) derivatives and analyzed quantitatively, allowing the identification of monomeric structures present in the mixture. Binder samples (approximately 50–100 mg) were reacted with 100 µL of pyridine, 200 µL silylating mixture III (1-(trimethylsilyl)imidazole/BSTFA/TMCS 3/3/2 (v/v/v)) and 300 µL of THF for 20 min at 70°C.
After derivatization 1 μL of the sample was injected into a Thermo Scientific TRACE 1300 gas chromatograph with a Thermo Scientific ISQ quadrupole mass detector. A Thermo Scientific TG-5MS (30 m × 0.25 mm × 0.25 µm) column was used. Injector temperature: 250°C. In spitless mode, carrier gas (helium) flow was 1.20 mL/min. Oven temperature program: isothermally held at 150°C for 5 min, then increased at 10°C/min and held for 1 min, before being finally increased at 2°C/min and passed at 300°C for 15 min. The transition line temperature of the mass detector was 250°C, and the ion source temperature was 200°C. Mass range 45–700 Da.
2.4.4 GPC (SEC-MALS-RID) Analysis
The SA samples were conducted with Agilent 1260 Infinity HPLC system, equipped with isocratic pump, degasser and autosampler. For separation 1 Plgel Mixed-E 300 × 8 mm column at 40°C was used. Infrared 3 angle light scattering detector DAWN® and refractive index detector Optilab® were used for detection. The thermostat temperature for the RI detector was 40°C. The mobile phase was THF with a flow rate of 1.0 mL/min. SA samples were prepared as THF solutions with 5 mg/mL mass concentration and filtered through nylon syringe filters to remove undissolved solids. The injection volume was 100 µL. Polystyrene standards were used for calibration.
2 mL of THF was added to approximately 0.2 g of the sample and left for 24 h at room temperature. The sample was then filtered through preheated and weighed glass filters and heated at 105°C to constant mass. The filtrate was diluted 10-fold for TPC analyses. For TPC determination, 7.9 mL of deionized water was filled into plastic tubes, 0.1 mL of diluted filtrate and 0.5 mL of Folin Ciocalteu reagent were added. The solutions were incubated in the dark for 8 min. Then, 1.5 mL of 20% sodium carbonate solution was added and after 2 h of incubation in the dark, the absorbance was measured at 756 nm.
0.125 mL of 72% sulfuric acid was added to 10 mg of the sample. After 3 h, the sample was diluted with 3.45 mL of water and placed in a thermostat for 3 h at 101°C. After hydrolysis, the sample was neutralized with 0.32 mL of ammonium hydroxide solution and 0.1 mL of internal standard (methyl-α-D-glucose) was added.
To 0.2 mL of the neutralized solution, 1 mL of a 2% NaBH4 solution in dimethyl sulfoxide was added and heated for 90 min at 40°C. The excess of the reagent was partitioned with 0.1 mL of concentrated acetic acid. After reduction, 2 mL of acetic anhydride and 0.2 mL of 1-methylimidazole were added. After 10 min, the excess of acetic anhydride was partitioned with 5 mL of water. The cooled solution was extracted once with 1 mL of DCM. The lower layer was transferred to a vial with a Pasteur pipette and stored at −20°C until GC-FID analysis. The analysis was conducted using an Agilent 6850 series GC instrument with a 30 m DB-1701 column with an internal diameter of 0.25 mm and a film thickness of 0.25 µm. Oven temperature 150°C, injector temperature 220°C [31,32].
TGA analysis was performed using a Discovery TGA 5500 thermogravimetric analyzer (TA Instruments, US). Mass loss was determined using platinum pans, using nitrogen gas at a flow rate of 50 mL/min, preheating the sample at 30°C, then heating to 700°C at a rate of 10 °C/min.
For DSC analysis DSC822 differential scanning calorimeter (Mettler-Toledo, Greifensee, Switzerland) was used to analyses the thermal behavior of binder samples. The analysis was performed in aluminum pans with pin, using nitrogen atmosphere. The samples were heated from 20°C to 260°C (heating/cooling rate 10 °C/min).
2.5 Obtaining the Plywood and the Shear Strength Determination
2.5.1 Preparation of the Plywood Using SA Binder
Specifically sawn 200 mm × 200 mm size and 1.5 mm thick “S” grade birch veneer sheets were used to obtain the three-layer plywood. The SA binders were applied to the veneer on one side with a 10 cm long polyacrylic fiber roll at a 90 g/m2 coating weight (dry matter basis). The covered veneers were placed under a load in a ventilated drying oven at a temperature of 60°C and dried to a constant mass (Fig. 1). Three layers of veneer were placed perpendicularly to each other by the direction of the wood fibers. Two parallel plywood samples were pressed for each binder at each pressing mode. Hot-pressing was done at constant pressure (1.8 MPa) for curing time of 5 and 10 min, and at temperatures of 180°C, 200°C and 220°C.
Figure 1: The steps for the obtaining of the plywood: 1., 2. Applying the binder, 3. Drying and 4., 5. Hot-pressing
2.5.2 Shear Strength Determination of Plywood Glue Line
The obtained plywood samples were cut into the sizes intended for testing (150 × 25 mm). To determine the shear strength of the binder according to the EN 314-1 standards 3rd highest moisture resistance class, it was necessary to additionally process the samples as can be seen in Fig. 2 and then sample was subjected to processing in 3 cycles (4 h boiling water + 20 h drying at 60°C in an oven + 4 h boiling in water with a further 1 h submersion in cold water). The adhesive shear strength of plywood veneer layers was then tested in Z010 testing machine (Zwick/Roell, Germany). The test results of shear strength are given as the average of the four parallel measurements.
Figure 2: Plywood sample processing example in (A) top and (B) side view for testing according to EN-314-1 standard
3.1 Feedstock Analysis and Modification
Our strategy was to explore ways to potentially increase the yield of the binder obtained from EBOB while simultaneously achieving the highest possible plywood shear strength. We hypothesized that using more finely ground feedstock would result in a higher yield, as the depolymerization reagent would have easier access to the particles throughout the entire volume. On one hand, separating the inner bark from the feedstock could also enhance the adhesion properties of the binder and increase yield, since inner bark contains less suberinic acids (SA) and more lignin and carbohydrates than outer bark. On the other hand, the inclusion of inner bark particles in the binder could act as an additional interphase modifier [26] and serve as an extra source of polyphenolic compounds, which could participate in the cross-linking of suberinic acid compounds during the binding process when hot-pressing the plywood. Therefore, the increased presence of inner bark particles might improve both yield and adhesion properties. Additionally, the presence of betulin could promote cross-linking of the binder at lower temperatures, therefore non-extracted BOB was used as a feedstock as well.
Given the assumptions outlined, we decided to conduct an extensive study and modification of both non-extracted BOB and EBOB to develop binders with varying compositions that could be optimized for improved adhesion. Our industrial supplier provided the BOB by peeling the bark, sorting it from the inner bark, drying it to a moisture content of 4–5 wt%, and then milling it to pass through a 6 mm sieve. To obtain EBOB the supplier did an additional extraction processing to BOB as described in our previous research [18]. To understand the best preparation of the feedstock, we started by determining the fractional composition of BOB and EBOB supplied to us (Fig. 3).
Figure 3: The distribution of (A) BOB and (B) EBOB feedstock fractions
For both BOB and EBOB the highest amount of fraction was in average size 2–4 mm, 55% and 51%, respectively. The main difference can be observed in other fractions—for BOB particles 27% were coarser fractions (d > 4 mm) and 17% were smaller fractions (d < 2 mm), while for EBOB particles only 8% were coarser (d > 4 mm) and 40% were smaller (d < 2 mm). This difference can be explained due to the extraction process when the EBOB was obtained—the extractives were isolated from BOB particle cells, therefore decreasing their size.
Knowing the difference in the inner and outer bark biomass components [17], it was important to determine the outer/inner bark ratio in the feedstocks’ fractions, as seen in Fig. 4.
Figure 4: The outer/inner bark proportion in particles for each separated fraction of (A) BOB and (B) EBOB feedstock
From the results displayed in Figs. 3 and 4, it can be concluded that for both BOB and EBOB feedstocks, the bark particles of average size 4 ≥ d > 2 mm were mainly comprised of outer bark—up to 80%, while in the smaller fractions the inner bark proportion increases in both feedstocks individually. While the outer bark content in BOB is more selectively dependent on the fractional composition, in EBOB, the outer bark content shows an increased presence even in the smaller fractions.
Based on the previous data, the BOB and EBOB feedstocks could be modified by separating the outer bark fractions from inner bark fine fractions. In this study, we will investigate the adhesive properties and yield based on the content of outer bark, which has a higher suberin content, and the admixture of inner bark, whose increased lignin and carbohydrate content could contribute additional effects to the adhesion process as a filler. If the presence of inner bark proves to have a positive impact on adhesive properties, feedstock modification through fractionation could be applicable on an industrial scale.
Moreover, to increase the yield of suberinic acids (SA) in the binder, reducing the particle size should enhance the depolymerization process by increasing the diffusion rate of depolymerized SA salts into the alkaline-water medium. Thus, feedstock modification by reducing particle size could also be feasible on an industrial scale.
To test these hypotheses, four different feedstock modifications were applied to both BOB and EBOB. To obtain finer outer and inner bark fractions, the feedstocks were milled through a 2 mm sieve before separation, thereby minimizing the effects of particle size differences on the results. For a clearer understanding of the feedstock modification process, it is schematically summarized in Fig. 5.
Figure 5: A scheme of all feedstock modifications obtained
For each feedstock following processes were carried out:
1. For reference, the unmodified feedstocks (d ≤ 6) were used as received by the supplier;
2. Feedstock was milled through a 2 mm sieve and 2–1 mm fraction was used for depolymerization (2 ≥ d > 1)—more outer bark finer fraction;
3. Feedstock was milled through a 2 mm sieve and fraction d ≤ 1 mm was used for depolymerization (2_d ≤ 1)—more inner bark fine fraction;
4. Feedstock was milled through a 1 mm sieve and depolymerized without further separation (1_d ≤ 1)—decreased particle size and lower inner bark fraction in comparison with the previous sample.
From the main composition results (Table 1), it can be seen that the outer bark fine fractions (2 ≥ d > 1) still contained 20%–30% of inner bark after milling and fractionation, so it was decided to alter the method of depolymerization for d ≤ 6 and 2 ≥ d > 1 modifications by adding an additional step of separating most of the coarse particles from the suspended binder with a 1 mm mesh sieve. Additionally, we found that the EBOB still contained around 10% of extractive substances, so it was expected that all binders would contain some amount of extractives. Therefore, the chemical composition was more extensively analyzed for the obtained binders.
3.2 Obtained Binder Yields and Analysis
3.2.1 Yield of Obtained Binders
Performing the depolymerization process, there were three forms how the mass of the feedstock can distribute:
1. Part of the barks’ mass was obtained in the binder;
2. If the 1 mm mesh was used, part of barks’ mass, was separated mainly as coarse particles;
3. Part of the barks’ mass were dissolved in the water medium (mainly carbohydrates and polyphenols).
We determined the percentage distribution (yield of the components) of the bark mass after depolymerization for each feedstock modification. As shown in Fig. 6, it can be concluded that to achieve a higher yield of the binder, solid particles should not be separated. However, for the BOB and EBOB modifications with particle sizes of 2 ≥ d > 1 mm and d ≤ 6 mm, the yield of binders correlates with the outer bark proportion, as displayed in Table 1—an increased amount of outer bark results in a higher binder yield.
Figure 6: Distribution of the barks’ mass after the depolymerization process
3.2.2 GC-MS, GPC Analysis and Solubility in THF
We performed GC-MS and GPC analysis to the compounds of the sample soluble in THF to understand the molecular weight distribution, the degree of depolymerization and the proportion of large molecules in the binders. GC-MS analysis gave us an insight of what monomers were present in binders. From triterpene compounds betulin and lupeol were detected in all binders. From SA compounds:
1. Acids such as 11,14-eicosadienoic acid and 10,12-docosadiynedioic acid;
2. Esters such as hexadecanoic acid ethyl ester, ethyl stearate and dimethyl dodecanedioate;
3. Hydroxy acids such as 2-hydroxy sebacic acid and 22-hydroxy decanoic acid;
were detected in all binders.
The molecular mass of SA present in the samples ranges from 210 to 350 Da. It is possible for SA in binders to exist in a dimer structure [24], so the molecular mass of dimers in obtained binders could be in ranges from 420 to 700 Da. However main extractives compound—betulin—has a molecular mass of 456 Da, which could interfere with SA substances results in GPC analysis.
During GPC analysis (Fig. 7) of the soluble substance in THF, different molecular weight fractions were detected, ranging from 453 to 127,869 Da in BOB and from 78 to 125,236 Da in EBOB binders. For EBOB binders peak 1 could correspond to the aromatic compounds (7%), peaks 2 and 3 could be attributed to SA monomers and betulin (10% and 5%); peak 4 could be SA dimers—750 Da (5%), however, the highest share of the sample—peaks 5–11—was composed of oligomeric compounds, that make up around 70% of the samples. For non-extracted BOB binders, triterpenes (mainly betulin) make up around 50% of the samples (peak 1), while other substances (peaks 2–7) could be mainly oligomeric substances. The method and parameters of depolymerization used mostly yields oligomeric substances. This is also represented in number of average molecular weight (Mn), where for BOB binders on average Mn is 5900 Da and for EBOB–12,400 Da. Thus, it will be interesting how the presence of betulin and oligomeric substances in the binders will impact the mechanical properties of the obtained plywood samples.
Figure 7: GPC chromatograms of BOB (right column) and EBOB (left column) binders
To see the difference in binder chemical composition we summarized the chromatography and THF solubility results in Table 2.
The increased presence of extractives, particularly betulin, in the bark feedstock (as shown in Table 1) also led to a higher concentration of triterpenes in the binders. When using a 1 mm mesh for separation, the THF-insoluble substances in the binders decreased, which can be attributed to the removal of coarse particle biopolymers such as lignin, cellulose and suberan [33].
It is hypothesized that during the pressing process, SA monomers undergo cross-linking or wood adhesion reactions via their free acid and hydroxy groups creating ester bonds. During the hot-pressing at high temperatures the double bonds in SA monomers are likely to undergo hydrolysis creating additional hydroxy groups for esterification [34]. So, we propose that the main curing mechanism of obtained SA binders occurs via esterification (Fig. 8). Therefore, considering the highest content of SA, the lowest triterpene levels, and the greatest solubility in THF, the binders produced from EBOB with particle sizes of d ≤ 6 mm and 2 ≥ d > 1 mm show the greatest potential for enhancing plywood adhesive strength.
Figure 8: Proposed mechanism of SA containing binder-wood curing
3.2.3 TPC and Monosaccharide Analysis
We did a TPC analysis to determine which binder samples have an increased amount of polyphenolic compounds, which could potentially participate in the cross-linking of SA compounds during the binding process while hot-pressing the plywood. Additionally, we did monosaccharide analysis as well and the results are summarized in Table 3.
We determined no major difference in the TPC results for all binder modifications. On average 3–5 wt% of BOB binders and around 2 wt% of EBOB binders were polyphenolic compounds. It can be concluded that the used feedstock and depolymerization process modifications did not significantly affect the TPC. As for the monosaccharide analysis, D-arabinose, D-xylose, D-mannose, 2-deoxyglucose and D-galactose were detected in all binders. Non-extracted BOB on average showed an increased monosaccharide content than EBOB. As for the fractional modifications, 1_d ≤ 1 and 2_d ≤ 1 showed an increased monosaccharide content than 2 ≥ d > 1 and d ≤ 6 fractions for BOB and EBOB. This coincides with the THF solubility results, indicating that 1_d ≤ 1 and 2_d ≤ 1 fractions could have an increased carbohydrate content as well.
3.2.4 Thermogravimetric Analysis of Obtained Binders
As seen in the DTGA curves (Fig. 9), all the binder samples showed complex weight loss patterns. Based on [35,36] experimental findings, the compounds of binders can be estimated using a multi-peak fitting technique of the DTGA signals. So, we estimated the biopolymeric and monomeric substance content found in binders using Lorentzian multi-peak fitting.
Figure 9: DTGA curves of obtained (A) BOB and (B) EBOB binders
In general, the thermal decomposition of binders takes place in two stages, which is characteristic of lignocellulose-containing natural materials—the formation of volatile substances due to the thermal decomposition of components (maximum at 320°C) and the formation of charcoal from the most thermally stable components and their final charring (400°C–450°C). In 2_d ≤ 1 and 1_d ≤ 1, which contained more coarse particles, the peaks in the first stage of decomposition at 325°C are much more pronounced than in d ≤ 6 and 2 ≥ d > 1, where the binder contained more SA oligomers, which are more thermally resistant. The approximate distribution of components is shown in Table 4.
Based on [37] experimental findings, betulin decomposes into two stages, where the first stage occurs as melting between 200°C and 300°C, and the second stage occurs as decomposition between 300°C and 400°C with a peak at 370°C. Therefore, the decomposition of betulin affected the ratios of hemicelluloses, cellulose and lignin peak areas. Nevertheless, the results of TGA analysis confirmed that binders obtained from fraction 2_d ≤ 1 and 1_d ≤ 1, with more coarse particles, have an increased lignin and carbohydrate composition. As for SA content, TGA analysis confirmed that a portion of hydroxy- and diacid-SA are present in an oligomeric state (decomposing at 410°C and 445°C). The highest SA composition was present in EBOB d ≤ 6 and 2 ≥ d > 1 binders, which coincides with GC-MS and GPC results.
3.2.5 DSC Analysis of Obtained Binders
The DSC results can be seen at Fig. 10. Most importantly, the results showed the curing and polymerization temperature of binders, which are important to the adhesion process. The heterogeneous nature of the curves showed the complex structure of the binder, where there is a mixture of many components, which was also observed in the TGA analyses.
Figure 10: DSC thermograms of (A) EBOB and (B) BOB binders
All EBOB binders have at least two crystalline phase melting zones, at 55°C, 78°C and a SA melting phase at 133°C. Additionally, for binders 2_d ≤ 1 and 1_d ≤ 1, the peak at 155°C could be explained by the release of water associated with the dehydration of the lignocellulose structure, before the degradation of its macromolecular structure. This could mean that too much admixture of particles containing lignocellulose could slow down the adhesion of the binder to the veneer, because before hardening, dehydration of the lignocellulose structure occurs with the release of additional water. The adhesion and curing process starts at 160°C, peaking at 215°C–220°C.
If compared to the binder samples from EBOB, BOB binder thermograms showed a lower starting temperature of hardening—around 145°C–155°C, reaching their maximum at 205°C–210°C. This decrease in temperature could indicate that increased betulin content not only protects the SA from melting, but also promotes hardening at a slightly lower temperature. Also, it is possible that betulin admixture in binders could inhibit the adhesion of the binder to the veneer by occupying the SA free carboxylic groups. However, the plywood shear strength results will define which feedstock and method modification will result in the highest adhesive strength of the binder.
3.3 Plywood Shear Strength Results after 3 Cycles of Treatment
To assess the quality of the obtained plywood and choose the most suitable binder, determination of the shear strength of the plywood veneer layers in wet outdoor conditions according to the EN 314-1 standard was chosen as the main plywood testing method. After 3 cycle moisture processing, the plywood will automatically adhere to the 3rd moisture resistance class if the shear strength ≥1 N/mm2. Additionally, the pressing parameters were varied to adjust the pressing process for the obtained binders. As concluded from the DSC results, the adhesion and curing process of binders takes place around 200°C–220°C. So, it was decided to test the pressing temperature at 180°C, 200°C and 220°C. The pressure was 1.8 MPa and pressing time was chosen 5 min for approximately 5 mm thick sample, which is 1 min/mm, as it is used for ordinary plywood production. We tested also 10 min because we wanted to test if longer pressing time will allow to use lower pressing temperature. So, for each binder 6 different pressing parameter combinations were tested.
As seen in Table 5, plywood binders obtained from fractions 1_d ≤ 1 and 2_d ≤ 1 have a significant decrease in shear strength than reference feedstock (d ≤ 6) plywood binder, which could be due to increased ligno-carbohydrate complex particle content. Especially when the non-extracted BOB was used as a feedstock. It allows to conclude that increased concentration of betulin and coarse particles in binders performs a negative effect on the adhesion. Possibly, ligno-carbohydrate complex particles react with most of SA molecules via hydrogen-bonding and occupy the reaction sites instead of the hydroxy groups of veneer wood [38–40].
The results of BOB d ≤ 6 and 2 ≥ d > 1 plywood binders showed similar values of shear strength when pressed at 200°C for 10 min (0.73 and 0.70 N/mm2, respectively). At higher pressing temperature (220°C) the higher shear strength values were for the 2 ≥ d > 1 binder achieving 1.06 ± 0.23 N/mm2 at pressing time 10 min, which could be due to betulins’ promotive effect in BOB binders as indicated by DSC results.
Slightly different results were obtained for the plywood binders made from EBOB with particle sizes of d ≤ 6 mm and 2 ≥ d > 1 mm. When pressing was carried out at 180°C and 200°C, the plywood produced from all binders did not meet the requirements for the 3rd moisture resistance class of the EN 314 standard. However, these samples could still be suitable for testing under other moisture resistance classes (indoor or covered exterior). When pressing was performed at 220°C for 10 min, the plywood produced using BOB and EBOB 2 ≥ d > 1 binders showed uncertain adherence to the EN 314-2 standard requirements. The highest shear strength value was achieved when plywood was pressed with the EBOB 2 ≥ d > 1 binder for 5 min at 220°C, resulting in a shear strength of 1.26 ± 0.18 N/mm2. However, increasing the hot-pressing time for the EBOB 2 ≥ d > 1 binder from 5 to 10 min led to a decrease in average shear strength to 1.04 ± 0.07 N/mm2, which suggests either damage to the veneer itself or a decline in the adhesive properties of the binder due to prolonged thermal exposure. The necessity of high hot-pressing temperatures could pose challenges when scaling the binder for industrial use. However, the potential use of various catalysts or crosslinkers could lower the adhesion and curing process temperature for SA binders. These possibilities will be investigated in future research.
From the results, we summarized the following conclusions that will be useful for the adaptation of BOB processing and binder obtaining methodology from industrial feedstock:
1. BOB and EBOB feedstock modifications with higher content of pure outer bark biocomponent (77.53 and 70.60 wt%) yield a binder with a higher plywood shear strength (1.06 ± 0.23 and 1.26 ± 0.18 N/mm2) than other modifications. These binders showed the highest SA monomer and oligomer content and decreased ligno-carbohydrate complex as determined by GC-MS and TGA analysis. So, a successful treatment of feedstock (milled through 2 mm and 1–2 mm fraction used) and depolymerization process (separation of coarse ligno-carbohydrate particles by 1 mm mesh sieve) was employed to obtain a binder that adheres to the EN 314-2 standard: 3rd moisture resistance class. Additionally, successful hot-pressing conditions were determined—pressed at 220°C and 1.8 MPa for 5 min (EBOB) and 10 min (BOB).
2. Decreased particle size of the feedstock has a positive effect on the plywood shear strength, if the coarse particles in the binder are removed as much as possible. The binder obtained from the fraction 2 ≥ d > 1 had an increased shear strength of the plywood after treatment. While decreased particle size (d ≤ 1) without separation gave increased amount of the ligno-carbohydrate complex in the binder, which inhibited the adhesion process during hot pressing. DSC results confirmed that the adhesion inhibition by lignocellulose dehydration results in the release of additional water at 155°C before the curing at 200°C.
3. Non-separated, coarse ligno-carbohydrate complex particles increased the yield of the binders, however, decreased plywood shear strength results. For the binders with isolated ligno-carbohydrate complex the pure outer bark content was elevated, as a result the yield of the binder increased as well.
4. The elevated amount of extractives (mainly triterpene-betulin) in the binders was of mainly neutral effect on the plywood shear strength. The plywood shear strength results indicated a small difference between EBOB and BOB plywood binders when the fraction of feedstock was 2 ≥ d > 1. Additionally, the used feedstock and depolymerization process modifications do not affect the TPC. This is a very positive result because then the feedstock for binder production is not so dependent on the process of extraction.
Acknowledgement: We express our gratitude to AS Latvijas Finieris for the long-term cooperation.
Funding Statement: This work was supported according to contract No. 5.1.1.2.i.0/1/22/A/CFLA/007 between “Forest Sector Competence Centre of Latvia” Ltd., and the Central Finance and Contracting Agency which dated 20th January of 2023.
Author Contributions: Conceptualization, Jānis Rižikovs; methodology, Jānis Rižikovs, Daniela Godiņa; formal analysis, Rūdolfs Bērziņš, Daniela Godiņa, Guntis Sosins, Laima Vēvere; investigation, Rūdolfs Bērziņš, Jānis Rižikovs, Daniela Godiņa, Guntis Sosins; writing—original draft preparation, Rūdolfs Bērziņš; writing—review and editing, Rūdolfs Bērziņš, Jānis Rižikovs, Laima Vēvere, Aigars Pāže, Daniela Godiņa; project administration, Jānis Rižikovs, Aigars Pāže; funding acquisition, Jānis Rižikovs. All authors reviewed the results and approved the final version of the manuscript.
Availability of Data and Materials: Data is available on request from the authors.
Ethics Approval: Not applicable.
Conflicts of Interest: The authors declare no conflicts of interest to report regarding the present study.
References
1. Andrew JJ, Dhakal HN. Sustainable biobased composites for advanced applications: recent trends and future opportunities—a critical review. Coposites. 2021;7(9):1002200. doi:10.1016/j.jcomc.2021.100220. [Google Scholar] [CrossRef]
2. Zanuttini R, Negro F. Wood-based composites: innovation towards a sustainable future. Forest. 2021;12(12):1717. doi:10.3390/f12121717. [Google Scholar] [CrossRef]
3. Dunky M. Adhesives based on formaldehyde condensation resins. In: Macromolecular symposia. UK: John Wiley and Sons Ltd.; 2004. p. 417–30. [Google Scholar]
4. La-Torre G, Vitello T, Cocchiara RA, Della-Rocca C. Relationship between formaldehyde exposure, respiratory irritant effects and cancers: a review of reviews. Public Health. 2023;218(4):186–96. doi:10.1016/j.puhe.2023.03.009. [Google Scholar] [PubMed] [CrossRef]
5. Xi X, Pizzi A, Lei H, Zhang B. Environmentally friendly chitosan adhesives for plywood bonding. Int J Adhes Adhes. 2021;122(2–3):103027. doi:10.1016/j.ijadhadh.2021.103027. [Google Scholar] [CrossRef]
6. Mo X, Sun XS. Soy proteins as plywood adhesives: formulation and characterization. J Adhes Sci Technol. 2013;27(1):8–19. doi:10.1080/01694243.2012.696916. [Google Scholar] [CrossRef]
7. Pāže A, Rižikovs J, Brazdausks P, Puķe M. Processing possibilities of birch outer bark into green bio-composites. In: Environment, technology, resources. Latvia: Rezekne Higher Education Institution; 2017. p. 249–53. doi:10.17770/etr2017vol3.2577. [Google Scholar] [CrossRef]
8. Réh R, Krišťák Ľ, Sedliačik L, Bekhta P, Božiková M, Kunecová D, et al. Utilization of birch bark as an eco-friendly filler in urea-formaldehyde adhesives for plywood manufacturing. Polymers. 2021;13(4):1–21. doi:10.3390/polym13040511. [Google Scholar] [PubMed] [CrossRef]
9. Pāže A, Rižikovs J, Godiņa D, Makars R. Development of plywood binder by partial replacement of phenol-formaldehyde resins with birch outer bark components. In: Key engineering materials. Switzerland: Trans Tech Publications Ltd.; 2021. p. 229–34. doi:10.4028/www.scientific.net/KEM.903.229. [Google Scholar] [CrossRef]
10. Rižikovs J, Pāže A, Makars R, Tupciauskas R. A method for obtaining thermoreactive binders for a production of wood composite materials from birch outer bark. European Patent No. EP 3807341 A1. EP register. 2021. Available from: https://patents.google.com/patent/EP3807341A1/#patentCitations. [Accessed 2024]. [Google Scholar]
11. Beck P, Caudullo D, de Riga D, Tinner W. Betula pendula, Betula pubescens and other birches in Europe: distribution, habitat, usage and threats. In: European atlas of forest tree species. Luxembourg: Publication Office of the European Union; 2016. p. 70–3. [Google Scholar]
12. Krasutsky PA. Birch bark research and development. Nat Prod Rep. 2006;23(6):919–42. doi:10.1039/b606816b. [Google Scholar] [PubMed] [CrossRef]
13. Ferreira JP, Quilho T, Pereira H. Characterization of Betula pendula outer bark regarding cork and phloem components at chemical and structural levels in view of biorefinery integration. J Wood Chem Technol. 2017;37(1):10–25. doi:10.1080/02773813.2016.1224248. [Google Scholar] [CrossRef]
14. Abyshev AZ, Agaev EM, Guseinov AB. Studies of the chemical composition of birch bark extracts (Cortex betula) from the Betulaceae family. Pharm Chem J. 2007;41(8):419–23. doi:10.1007/s11094-007-0091-5. [Google Scholar] [CrossRef]
15. Blondeau D, St-Pierre A, Bordeeau N, Bley J, Lajeunesse A. Antimicrobial activity and chemical composition of white birch (Betula papyrifera Marshall) bark extracts. Microbiol Open. 2020;9(1):1–23. doi:10.1002/mbo3.944. [Google Scholar] [PubMed] [CrossRef]
16. Vedernikov DN, Shabanova N, Roshchin VI. Change in the chemical composition of the crust and inner bark of the Betula pendula Roth. Birch (Betulaceae) with tree height. Russ J Bioorg Chem. 2011;37(7):877–82. doi:10.1134/S1068162011070259. [Google Scholar] [CrossRef]
17. Rižikovs J, Pāže A, Pļaviniece A, Stankus K. A novel method for birch outer bark quality control using higher heating value. In: Environment, technology, resources. Latvia: Rezekne Higher Education Institution; 2017. p. 282–5. doi:10.17770/etr2017vol3.2550. [Google Scholar] [CrossRef]
18. Makars R, Pāže A, Rižikovs J, Bērziņš R. Changes in composition of birch outer bark extractives after recrystallization with C2-C5 alkanols. Key Eng Mater. 2020;850(1):3–8. doi:10.4028/www.scientific.net/KEM.850.3. [Google Scholar] [CrossRef]
19. Muceniece R, Namniece J, Nakurte I, Jēkabsons K, Riekstina U, Jansone B. Pharmacological research on natural substances in Latvia: focus on lunasin, betulin, polyprenol and phlorizin. Pharmacol Res. 2022;113(1):760–70. doi:10.1016/j.phrs.2016.03.040. [Google Scholar] [PubMed] [CrossRef]
20. Pāže A, Vītoliņa S, Bērziņš R, Rižikovs J, Makars R, Godiņa D, et al. The study of betulin particles containing hydrogels prepared by antisolvent precipitation. Key Eng Matter. 2022;933(1):139–46. doi:10.4028/p-rhk0o3. [Google Scholar] [CrossRef]
21. Vitolina S, Bērziņš R, Rižikovs J, Godina D, Horváth ZM, Logviss K, et al. Evaluation of oleogels stabilized by particles of birch outer bark extract through a novel approach. Gels. 2023;9(11):911. doi:10.3390/gels9110911. [Google Scholar] [PubMed] [CrossRef]
22. Andze L, Vītoliņa S, Bērziņš R, Rižikovs J, Godiņa D, Tereško A, et al. Innovative approach to enhance bioavailability of birch bark extracts: novel method of oleogel development contrasted with other dispersed systems. Plants. 2024;13(1):145. doi:10.3390/plants13010145. [Google Scholar] [PubMed] [CrossRef]
23. Berzins R, Pāže A, Rižikovs J, Makas R, Godiņa D, Lauberts M, et al. Influence of solvents on the antioxidant properties of the birch outer bark extract in cosmetic emulsions. Key Eng Mater. 2021;903(1):28–33. doi:10.4028/www.scientific.net/KEM.903.28. [Google Scholar] [CrossRef]
24. Makars R, Rižikovs J, Godiņa D, Pāže A, Merijs-Meri R. Utilization of suberinic acids containing residue as an adhesive for particle boards. Polymers. 2022;14(11):2304. doi:10.3390/polym14112304. [Google Scholar] [PubMed] [CrossRef]
25. Rizikovs J, Godiņa D, Makars R, Pāže A, Āboliņš A, Fridrihsone A, et al. Suberinic acids as a potential feedstock for polyol synthesis: separation and characterization. Polymers. 2021;12(24):4380. doi:10.3390/polym13244380. [Google Scholar] [PubMed] [CrossRef]
26. Rižikovs J, Brazdausks P, Pāže A, Tupciauskas R, Grīniņš J, Puķe M, et al. Characterization of suberinic acids from birch outer bark as bio-based adhesive in wood composites. Int J Adhes Adhes. 2022;112:102989. doi:10.1016/j.ijadhadh.2021.102989. [Google Scholar] [CrossRef]
27. Neiva D, Pereira H, Miranda I, Simões R. Chemical depolymerization of cork suberin with hydrothermal processes. Ind Crops Prod. 2024;208(5):117902. doi:10.1016/j.indcrop.2023.117902. [Google Scholar] [CrossRef]
28. The Engineered Wood Association. Plywood bond quality—requirements. European Patent No. EN 314-2. EP register. 2013. Available from: https://apawood-europe.org/wp-content/uploads/2022/12/APA_WOOD_PDF_Standard-8_BS-EN-314-2.pdf. [Accessed 2024]. [Google Scholar]
29. The Engineered Wood Association. Plywood bond quality—test methods. European Patent No. EN 314-1. EP register. 2014. Available from: https://apawood-europe.org/wp-content/uploads/2022/12/APA_WOOD_PDF_Standard-7_BS-EN-314-1.pdf. [Accessed 2024]. [Google Scholar]
30. International Organization for Standardization. Solid biofuels—determination of calorific value. ISO Patent No. ISO 18125. 2017. Available from: https://www.iso.org/standard/61517.html. [Accessed 2024]. [Google Scholar]
31. Blakeney AB, Harris PJ, Henry RJ, Stone BA. A simple and rapid preparation of alditol acetates for monosaccharide analysis. Carbohydr Res. 1983;113(2):291–9. doi:10.1016/0008-6215(83)88244-5. [Google Scholar] [CrossRef]
32. Pals M, Pētersone L, Ponomarenko J, Lauberts M, Arshanitsa A. Microwave-assisted water extraction of aspen (Populus tremula) and pine (Pinus sylvestris L.) barks as a tool for their valorization. Plants. 2022;11(12):1544. doi:10.3390/plants11121544. [Google Scholar] [PubMed] [CrossRef]
33. Turner JW, Hartman BE, Hatcher PG. Structural characterization of suberan isolated from river birch (Betula nigra) bark. Org Geochem. 2013;57:41–53. doi:10.1016/j.orggeochem.2013.01.004. [Google Scholar] [CrossRef]
34. Charuwat P, Bordman G, Bott C, Novak JT. Thermal degradation of long chain fatty acids. Water Environ Res. 2018;90(3):278–87. doi:10.2175/106143017X15131012152825. [Google Scholar] [PubMed] [CrossRef]
35. Shangguan W, Chen Z, Zhao J, Song X. Thermogravimetric analysis of cork and cork components from Quercus variabilis. Wood Sci Technol. 2018;52(1):181–92. doi:10.1007/s00226-017-0959-9. [Google Scholar] [CrossRef]
36. Şen U, Pereira H. Pyrolysis behavior of alternative cork species. J Therm Anal Calorim. 2022;147(6):4017–25. doi:10.1007/s10973-021-10844-w. [Google Scholar] [CrossRef]
37. Guidoin MF, Yang J, Pichette A, Roy C. Betulin isolation from birch bark by vacuum and atmospheric sublimation. A thermogravimetric study. Thermochim Acta. 2003;398(2):153–66. doi:10.1016/S0040-6031(02)00358-1. [Google Scholar] [CrossRef]
38. Pāže A, Rižikovs J. Study of an appropriate suberinic acids binder for manufacturing of plywood. Key Eng Mater. 2019;800:251–5. doi:10.4028/www.scientific.net/KEM.800.251. [Google Scholar] [CrossRef]
39. Handiso B, Valle-Delgado JJ, Leena-Sisko J, Hughes M. The physicochemical properties of cellulose surfaces modified with (depolymerised) suberin and suberin fatty acid. Ind Crops Prod. 2021;159(2):113070. doi:10.1016/j.indcrop.2020.113070. [Google Scholar] [CrossRef]
40. Sudakova G, Kuznestov BN, Garyntseva NV, Pavlenko NI, Ivanchenko NM. Functional and thermal analysis of suberin isolated from birch outer bark. J Sib Fed Univ Biol. 2008;4:355–62. Available from: http://journal.sfu-kras.ru/en/article/907. [Accessed 2024]. [Google Scholar]
Cite This Article
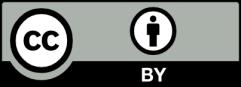
This work is licensed under a Creative Commons Attribution 4.0 International License , which permits unrestricted use, distribution, and reproduction in any medium, provided the original work is properly cited.