Open Access
REVIEW
A Review of Piezoelectric Phenomena as a Key Characteristic of Wood
1 Department of Forest Industrial Engineering, Faculty of Forestry, Bartin, 74100, Turkey
2 Department of Industrial Engineering, Faculty of Engineering and Natural Sciences, Hatay, 31200, Turkey
* Corresponding Authors: Zeynep Eda Özan. Email: ; Deniz Aydemir. Email:
Journal of Renewable Materials 2024, 12(12), 1985-2016. https://doi.org/10.32604/jrm.2024.056000
Received 11 July 2024; Accepted 21 October 2024; Issue published 20 December 2024
Abstract
Piezoelectric materials convert mechanical energy into electrical energy, acting as renewable energy sources. As smart materials, they respond to environmental changes by altering their properties. When pressure is applied, their structure separates positive and negative charge centers, producing opposite charges on crystal surfaces. This generates an electric field and a measurable potential. Wood, a natural material, also exhibits piezoelectric behavior. The piezoelectric effect of wood was first discovered by Russian scientists in 1940–1950. Then, in 1955, Fukada analyzed both the direct and inverse piezoelectric effect of wood and scientifically proved that this natural material has piezoelectric properties. Since then, much research has been done on the piezoelectric effect of wood. Research conducted between the 1960s and 1990s contributed to a deeper understanding of the piezoelectric properties of wood. Since the 2000s, various methods have been developed to enhance wood’s piezoelectric performance using modern research techniques and advanced analysis. These studies improve the understanding of wood’s piezoelectric properties and their potential applications. The research presents a chronological review of scientific studies from the discovery of the piezoelectric effect of wood to the present day. In addition, the piezoelectric and electric potential behavior obtained from planted trees and academic studies on the energy generation purposes of wooden structures are comprehensively examined. Wood’s potential as a natural piezoelectric material is significant, particularly for renewable energy sources and smart material technologies. Optimizing its piezoelectric properties aims to enhance energy harvesting, sensor performance, and other advanced technological applications.Graphic Abstract
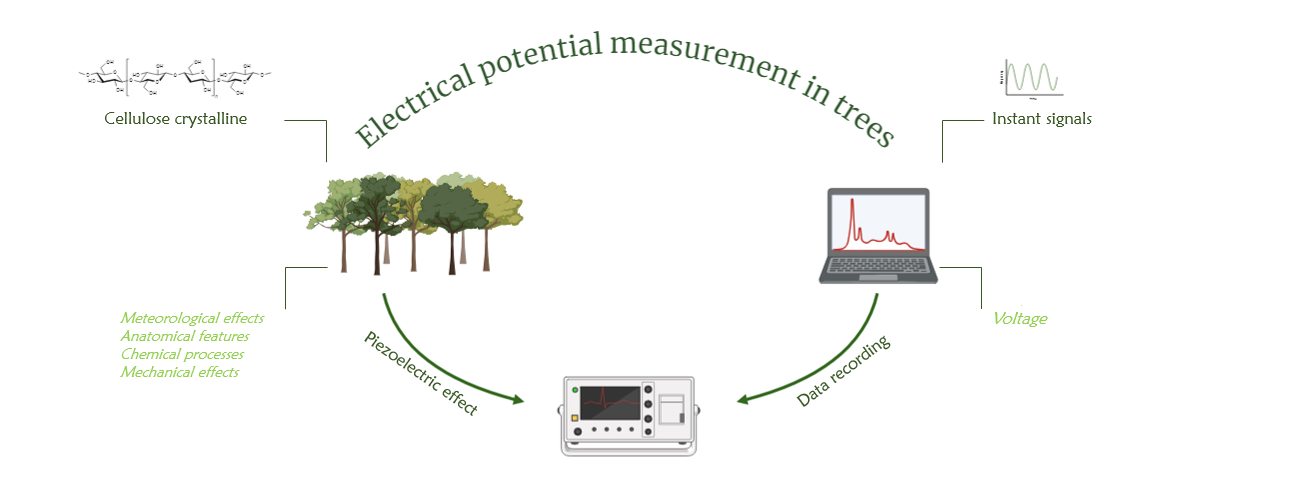
Keywords
Nomenclature
XRD | X-ray diffraction spectroscopy |
EAPap | Electroactive paper |
SEM | Scanning electron microscope spectroscopy |
FTIR | Fourier transform infrared spectroscopy |
ERSAF | Regional Agency for Agriculture and Forestry |
TEMPO | 2,2,6,6-tetramethylpiperidine-1-oxyl |
CNC | Cellulose nanocrystal |
PTFE | Poly(tetrafluoroethylene) |
PDMS | Poly(dimethylsiloxane) |
Wood is a fascinating material, mechanically, physiologically, and biologically. From its unrevealed chemical mysteries in the smallest ultra-structural units to its majestic appearance in mature trees, it offers us interesting directions for scientific research [1]. Exploring the interaction between the unique structural properties of wood and the potential to exploit its piezoelectric capabilities has attracted significant attention as a sustainable and environmentally friendly energy source. They have been found to be widely used in many practical applications ranging from sensor technologies to energy harvesting and storage [2,3]. These materials are examined in two main categories: naturally occurring (natural) and synthetic (inorganic). Among natural materials, crystals such as quartz (SiO2), tourmaline, Rochelle salt (NaKC4H4O6-4H2O), and cellulose stand out [4,5]. Quartz, one of the most well-known crystals in nature, is a complex, crystalline mineral composed of pure silicon dioxide (SiO2) silica arranged periodically and regularly in three dimensions. The anisotropy of quartz crystals, resulting from the regular arrangement of silica atoms, causes quartz’s mechanical, electrical, and optical properties to depend on the axis of the main crystal lattice [6,7]. Quartz, which has a natural piezoelectric effect, behaves similarly to cellulose crystallites found in wood [8]. On the other hand, a significant part of the piezoelectric properties is dominated by inorganic materials such as lead zirconium titanate (PZT), aluminum nitride (AlN), zinc oxide (ZnO), barium titanate (BaTiO3) and lithium niobate (LiNbO3) [9–12]. Also, in the organic class, polyvinylidene fluoride (PVDF) and its copolymers show a direct piezoelectric effect after polarization treatments [13–17].
Bioelectric phenomena at the tissue and organismal level are not well known in trees. The piezoelectricity of wood is due to the piezoelectric properties of cellulose crystallites [18–22]. Wood is one of the primary sources of cellulose materials. Cellulose materials have the advantages of biodegradability, sustainability, and biocompatibility, making the exploration of bio-based sustainable piezoelectric materials very promising [23,24]. The piezoelectric state is not only present in monocrystalline materials such as quartz, Rochelle salt, barium titanate, and lithium sulfate but also occurs in piezoelectric tissues [19]. Cellulose-based materials have textures containing cellulose I or cellulose II crystal forms that exhibit piezoelectric properties. The cellulose chains in these materials are embedded in an amorphous matrix of lignin and hemicelluloses, and in terms of piezoelectric behavior, this mixture of crystalline and amorphous matrix of cellulose chains has been described as a piezoelectric tissue [25]. The asymmetric crystal structure and the inherent dipole moment of crystalline cellulose induce spontaneous polarization when subjected to pressure, and this characteristic of cellulose is the fundamental reason for the piezoelectric properties of wood [26,27]. The highly regular arrangement of cellulose chains in some regions of cellulose fibrils ensures that cellulose has high crystallinity [28]. Due to the existence of a large number of intramolecular and intermolecular hydrogen bonds, cellulose can produce cellulose structures (nanoscale) at different scales. Thanks to the layered structure of wood, the obtained nanoscale cellulose can eliminate most of the defects caused by the macrostructure of wood [29–31]. Cellulose has both a crystalline region where microfibrils are arranged in bundles with dense hydrogen bonds in an orderly manner and an amorphous region with an irregular structure, and although it varies according to the wood species, it generally consists of 60%–70% crystalline and 40%–30% amorphous regions (Fig. 1) [32,33].
Figure 1: Hierarchical structure of cellulose. Adapted with permission from Reference [34], Copyright © 2015, IntechOpen Publishing
The cell wall is a crucial structural component of plant cells, providing mechanical support and protection while also playing a significant role in growth and development (Fig. 2a) [35]. The amounts of cellulose in the primary and secondary walls of the cell wall show significant differences. While the amount of cellulose in the primary wall is quite low, this ratio reaches very high levels in the secondary wall (Fig. 2b,c) [36,37].
Figure 2: Cell wall structure (a), cellulose chains of the primary (b) and secondary cell wall (c). Adapted with permission from References [38,39], Copyright © 2020, Nature and 2015, Elsevier B.V
Due to differences in the arrangement of cellulose microfibrils, the secondary wall is divided into S1, S2, and S3 layers [40–42]. The S2 layer, the most defining region of the cell wall, contains well-oriented cellulose microfibrils with a high degree of crystallinity. Cellulose molecules arranged helically around the cell cavity of the S2 layer are seen as a tissue exhibiting piezoelectric properties [25].
‘Piezo’ is a Greek word that means pressure [43]. Piezoelectricity is the accumulation of charge under mechanical stress [44–46]. Piezoelectric materials are materials that can convert mechanical energy into electrical energy [47,48]. It was first predicted by Coulomb (1736–1806) that electricity could be generated by pressure. However, the studies carried out by Haüy (1743–1822) and Becquerel (1788–1878) to prove the accuracy of this prediction were inconclusive [49]. The real discoverers of the piezoelectric phenomenon are undoubtedly the Curie brothers. The French brothers Pierre and Jacques Curie discovered piezoelectricity in 1880 [50,51].
The solid material in the cellular structure of piezoelectric materials consists of positively and negatively charged particles and these particles are in equilibrium (Fig. 3a). However, when a mechanical force is applied to the material, surface charges are generated [52,53].
Figure 3: Distribution of positive and negative charges in the cellular structure of the piezoelectric material (a), the state after forces is applied to the charges (b), and the resulting electric field (c). Adapted with permission from Reference [54], Copyright © 2014, Vilnius Gediminas Technical University
The observation of piezoelectricity in a crystal depends on the formation of surface charges; however, symmetry properties restrict the conditions for the formation of these charges. Therefore, crystals without a center of symmetry are the most suitable materials for this task. When force is applied to a crystal that is electrically uncharged and has no structural symmetry center (Fig. 3b), the center of positive charges and the center of negative charges are separated from each other due to the effect of pressure (compression, stretching, torsion), causing the emergence of opposite charges on the opposite surfaces of the crystal [52,55–57]. This separation of charges creates an electric field (Fig. 3c). However, a macroscopically measurable electric potential occurs between the crystal surfaces [1,55,58]. Similarly, Werling’s findings confirmed that the non-centrosymmetric crystal structure was the source of the piezoelectric response [59].
Like wood, crystalline materials are anisotropic. Isotropy in crystals is caused by the structure of the crystal lattice [19,60]. Quartz crystal, which shows piezoelectric properties, is composed of silicon (Si) and oxygen (O2) atoms. When force is applied in the direction of the ‘y-axis’, the crystal profile is deformed while the interspace between the charges is maintained. If the crystal is not symmetric along the ‘y-axis’, the displacement of atoms (dx) causes a shift in the charge distribution (Fig. 4). This leads to the piezoelectric effect, an electric field generated by the homogeneous displacement of the crystal atoms [1]. This unique property has led to the exploration of wood as a piezoelectric material for various applications, including energy management, conversion, and sensing [61]. Research into energy harvesting, embedded sensors, smart homes, and wearable devices appears promising [62–65]. Considering the unique advantages of wood, developing these potential applications would yield significant benefits [66].
Figure 4: Compressive stress in the y-direction of the unit cell of α-quartz crystal. Adapted with permission from Reference [25], Copyright © 2009, BOKU-Universität für Bodenkultur Wien
In this study, the historical development of the electrical potential properties of wood as a result of mechanical effects, which were examined under various parameters, was discussed in detail. The research presents a chronological review of the scientific studies carried out from the discovery of the piezoelectric effect of wood to the present day. In this context, a comprehensive analysis of important research on the discovery, development, and applications of the piezoelectric properties of wood and key findings in this field has been made.
3 First Discovery of Piezoelectricity in Wood
The piezoelectric effect of wood was first discovered by Russian scientists between 1940 and 1950. With the discovery, studies began to find a suitable triggering mechanism for use as military equipment, especially for missiles [67,68]. Then, analyzing both the direct and inverse piezoelectric effect of wood, Fukada [18] proved the piezoelectric property of wood. Since then, research has been conducted to explore the relationship between wood and the piezoelectric effect.
4 Effect of Wood on Piezoelectricity
Wood is a natural material that exhibits piezoelectric behavior and produces electrical polarization in response to mechanical stress [25,44]. Fukada [18] characterized the direct piezoelectric effect in wood by applying stress to wood with a 45° angle (Fig. 5), as he believed that the direct piezoelectric effect in wood was due to shear stress.
Figure 5: Measuring apparatus for direct piezoelectric effect. Adapted with permission from Reference [18], Copyright © 1955, The Physical Society of Japan
To detect the presence of the inverse piezoelectric effect, he produced a device with two active parts: a wooden sample with a 45° angle and a Rochelle salt crystal. The mechanical reaction was recorded by the Rochelle salt crystal, which has strong piezoelectric properties. He proved both direct and inverse piezoelectric effects on the piezoelectricity of wood. He found a strong correlation between the current applied to the wood and the output current from the Rochelle salt crystal. Again, in a study conducted by Fukada et al. researchers in 1957 [69], they recorded the change in fracture strength, dynamic Young’s modulus, and piezoelectric modulus (d25) with the age of the wood. They observed the maximum value recorded at the end of three hundred and sixty years. When they analyzed the results, they found that the degree of crystallinity of cellulose increased rather slowly over a period of about three hundred to three hundred and fifty years at room temperature. However, over time, they found that the decomposition of cellulose began to reduce the crystallinity. They found that their XRD studies proved this fact, with sharper diffraction patterns in the three-hundred-and-fifty-year-old samples than in the eight-year-old samples. On the other hand, they found that the pattern of the one thousand three-hundred-year-old wood was very diffuse, which they emphasized as clear evidence of decreasing crystallinity. Bazhenov [19] conducted a comprehensive analysis and quantitative evaluation of wood’s basic and specific piezoelectric properties. He found that the piezoelectric modulus d25 increased with increasing density in pine samples, whereas the modulus d14 decreased. He also found that the piezoelectric modulus is directly related to temperature and increases with increasing temperature. d14 values gradually increase from the core to the bark. For the growth period in the same year, he observed that the piezoelectric modulus values of spring and summer wood were almost equal. As presented in the research of Fukada et al., Li et al. [2], and Hui et al. [3] stated that the piezoelectric effect depends on the degree of crystallinity of the density.
In 1963, Galligan et al. [70] started their work to develop a new approach for the non-destructive testing of adhesive bonds in long wood specimens. They, therefore, constructed an apparatus that caused a shock wave along the length of the specimen by striking the front end of the beam (Fig. 6).
Figure 6: An electrode-forming apparatus that detects the electric field across surfaces. Adapted with permission from Reference [70], Copyright © 1963, Forest Products Society
To detect the electrical signal caused by the piezoelectric effect, they placed an electrode without contacting the surfaces and moved it along the perimeter. They measured the piezoelectric voltage at six points in each direction, twenty-four points in total, slightly away from the point of impact. They found that there was a distinct electrical signal of a few millivolts. They found that there were specific positive and negative charges in the charge distribution. Therefore, they concluded that annual ring deviations (such as knots) could affect the surface polarity or the location of the zero-volt point. They also found that density and wood defects significantly affect the piezoelectric effect.
In 1968, Fukada et al. [71] studied polarization in wood, monoclinic symmetry of the crystalline unit cell of cellulose, tensors, and moduli in detail. They explained the piezoelectric effect in wood, i.e., the occurrence of electrical polarization under mechanical stress and mechanical stress in the electric field, taking into account the uniaxial orientation of cellulose crystallites in the fibers and their monoclinic symmetry. They also studied the variation of temperature on the piezoelectric effect. They found that shear stress in a plane containing the fiber orientation produces electrical polarization perpendicular to it. They found that chemical treatments increase the piezoelectric modulus by changing the crystal structure from cellulose I to II or III. They emphasized that the variation of the phase angle between sinusoidal voltage and polarization with temperature shows a maximum forward phase around room temperature and a maximum delayed phase at about −100°C. They stated that piezoelectric polarization in wood can be used in technical problems such as measuring shock velocity in timber.
Hirai et al. [72] studied wood growth and variations of the piezoelectric modulus on wood quality, degree of crystallinity, and micelle orientation in Japanese pine (Cryptomeria japonica). They emphasized that the piezoelectric constant is highly dependent on the degree of crystallinity.
Pizzi et al. [73], who studied the piezoelectric effect of wood material, aimed to reveal how this phenomenon occurs at the molecular level in cellulose I crystal. In this context, they investigated the forces arising from the piezoelectric effect and applied five different shear deformations to the cellulose I crystal structure. They analyzed the energy changes of van der Waals, hydrogen bonding, and electrostatic interactions in detail. According to the results, it was found that the piezoelectric effect in cellulose I crystal is mainly due to van der Waals interactions. However, they determined that electrostatic and hydrogen bonding interactions do not contribute to the piezoelectric effect. These findings represent an important step in understanding the relationship between molecular forces and the piezoelectric effect.
Knuffel et al. [74] improved their measurements and experimental design by using more sophisticated apparatus and measuring devices in addition to the method of Galligan et al. [70]. In their research, they investigated the piezoelectric effect in wooden beams. They used an impact-induced stress wave to activate the piezoelectric effect in wooden beams and described its detection, demonstration, and measurement. Although the results obtained were in agreement with the findings of Galligan et al. [70], they provided a higher measurement resolution. They noted that in gnarled samples, the zero point can be displaced, and negative charges can be read by the shell and vice versa (Fig. 7). However, they could not clearly state whether they were reading the first peak or another part of the oscilloscope trace.
Figure 7: Direct piezoelectric effect, (a) specimen with knots and (b) specimen without knots. Adapted with permission from Reference [74], Copyright © 1986, Walter de Gruyter GmbH
They stated that they have determined the piezoelectric properties of the wooden beams, and tests are ongoing to correlate this with tensile strength and defect spots.
Knuffel [75] used a pendulum hammer with a cam mechanism to strike wood specimens of 3300 mm × 100 mm × 34 mm in size to induce a shock wave in three different pine species (Fig. 8). He investigated the effect of natural defects in the wood on the piezoelectric effect in structural wood. By measuring the voltage across the surface, the relationship between the piezoelectric effect and the resulting modulus of elasticity and knot formation was discussed.
Figure 8: Piezoelectric effect of the shock wave and the associated formation of wood knots. Adapted with permission from Reference [75], Copyright © 1988, Walter de Gruyter GmbH
As a result of the investigations, when he examined the effect of piezoelectricity at the peak of the first wavelength, he observed that the values increased in the regions close to the knots. However, he noted that the piezoelectric properties observed in wood are more sensitive to defects than to the modulus of elasticity and that these properties are directly related to the strain concentrations of the anatomical structure.
Nakai et al. [76] investigated the possible relationship between the piezoelectric effect and fracture of wood. They investigated the piezoelectric properties of air-dried wood samples under time-varying loads. The results showed that the highest voltage of the piezoelectric signals was obtained when the wood was cut at an angle of 45°. They also found that the effect of the piezoelectric signals on the voltage depends on the magnitude of the load, the wood species, and the annual rings of the tree. These findings provide important contributions toward a better understanding of the piezoelectric response of wood under mechanical load.
Niemz et al. in 1994 [77] aimed to determine moisture content using piezoelectric signals induced by the drying stress of timber. The study examined the effect of moisture content on piezoelectric properties caused by mechanical excitation of the wood. The research findings showed that the piezoelectric signal was significantly reduced by sound. In addition, they observed that the internal stress caused by the drying of wood is associated with piezoelectric signals. These results provide important contributions to understanding the relationship of piezoelectric signals in wood materials with moisture content and internal stresses.
Nakai et al. [78] investigated the relationship between the piezoelectric behavior of baked Sitka spruce (Picea sitchensis Carr.) specimens (5 mm × 10 mm × 60 mm) under pressure and vibration and tracheid deformations by curving the middle parts of the specimens. In the experiments, they placed the observation plane of the specimens on the radial surface and positioned platinum electrodes (5 mm × 20 mm) and copper wires at the centers of the opposite upper and lower surfaces of the specimen to detect piezoelectricity. Piezoelectric voltage measurements were performed using the SEM Selvo Pulser (Fig. 9).
Figure 9: Piezoelectric voltage measurement system with test specimen and load applied to wood. Adapted with permission from Reference [78], Copyright © 1998, SpringerOpen
The results showed that the piezoelectric behavior of wood under compressive and vibrational stresses showed a very small increase in the boundaries of the annual rings and that the specimens fractured only in the 45° direction. For specimens subjected to shear resistance, they found that the piezoelectric voltage increases linearly in the elastic region and gradually decreases after reaching the maximum point. They also observed a linear relationship between the dynamic Young’s modulus and the piezoelectric parameter when stress is taken into account.
Nakai et al. investigated the piezoelectric behavior of wood within the framework of its response to mechanical compression and vibration stress in 2004. For this purpose, they conditioned ten oven-dried specimens of 3 cm × 3 cm × 9 cm in size at a constant temperature of 20°C and 60% constant humidity for six months. The electrodes were glued with double-sided tape to the center and radial sections of the opposite surfaces of the specimens. Lead wires were attached to the electrodes using electrically conductive paint. A sinusoidal load was applied to the samples in static compression. The generated piezoelectric voltage was measured by the electrodes using a current voltmeter (Fig. 10) [79].
Figure 10: Piezoelectric measurement setup. Adapted with permission from Reference [79], Copyright © 2004, SpringerOpen
The findings showed that the measured piezoelectric voltage was quite low. When they examined the behavior of the microfibrils, they found that single cellulose crystals in cellulose microfibrils in unloaded wood deteriorated to some extent, while this deterioration became evident when load was applied. They also observed that the voltage values and Young’s modulus increased with load.
Nakai et al. [80] investigated the piezoelectric effect resulting from the mechanical behavior of the crystalline regions of wood subjected to tensile pressure on Japanese cypress (Chamaecyparis obtusa Endl.). They conditioned the wood materials for six months at a constant temperature of 20°C and a constant humidity of 60%. For X-ray stress analysis, they measured simultaneously at 100 ms intervals using a data acquisition controller that recorded the output of the load cell built into the apparatus and the surface stress on the specimen together with the piezoelectric voltage. The data obtained from the X-ray stress measurements revealed that the crystalline regions of the wood are highly sensitive to mechanical behavior. They also observed that microscopic cracks and tears in the wood reduce the piezoelectric effect.
Cellulose-based EAPap is known as a cheap and environmentally friendly piezoelectric material. Many studies have recommended using EAPap in place of polymer piezoelectric materials [81]. It is generally considered that the piezoelectric effect sources from the ion migration effect in paper-based films (cellulose fibers). Nonetheless, the majority of experts agreed that the primary mechanism underlying EAPap is the piezoelectric effect [82–85]. Kim et al. [82] produced cellulose film from cellulose EAPap. In this process, they formed the cellulose film by preparing cellulose fibers in a solution. They extruded the prepared solution into a sulfuric acid bath. They then dried it and converted it back into pure cellulose. The EAPap was fabricated from cellulose paper with gold electrodes deposited on both surfaces (Fig. 11). X-ray diffraction and thermally induced current measurements were performed to analyze the structural and electrical properties of the cellulose films.
Figure 11: EAPap actuator: (a) water molecules (bound water and free water), (b) cellulose paper with gold electrodes placed on both sides of the EAPap, (c) cellulose microfibril (crystalline regions and amorphous region) and schematic diagram of the force measurement system. Adapted with permission from Reference [82], Copyright © 2006, MDPI (Basel, Switzerland)
In line with the results, the researchers stated that humidity can lead to crystal growth in regenerated cellulose material, and molecular rearrangement can occur due to the absorbed water in this process. Electrical activation is thought to enhance recrystallization. The researchers argued that this crystallization could improve the piezoelectric properties of the EAPap material. By combining the piezoelectric properties of cellulose with ionic transport, they stated that it is possible to use the oriented EAPap material in cheap and lightweight biomimetic actuators and micro-electromechanical system devices.
In their study, Hirai et al. [86] investigated the relationship between d14 and d25 and d31, d32, and d36 moduli in softwood and hardwood. For piezoelectric modulus measurements, they dried the samples in a vacuum chamber for two hours and then kept them completely dry with phosphorus pentoxide for several days. They measured the piezoelectric moduli at four frequencies (13, 26, 52, 104 Hz) using a Rheolographsolid at 20°C. The measurements were carried out twice in the front and back planes of the sample. The results obtained showed that the absolute values of the moduli d31, d32, and d36 were significantly smaller than those of d14 and d25. They stated that the moduli d36 generally showed negative values in softwoods, while they exhibited both positive and negative values in hardwoods. Furthermore, when they examined the d31 and d32 moduli in softwoods and hardwoods, they found that these moduli were a mixture of positive and negative values. The study revealed that cellulose shows crystalline properties in the fiber direction of the wood and that there is electrical polarity in this direction. They emphasized that the d31 and d32 poles are located in the outer part of the tree trunk, where the crystalline properties of cellulose are high and the crystals are aligned parallel to the fiber direction.
In a study by Csoka et al. [87], cellulose nanocrystal films were joined to mica support by using electric field-assisted shear stress. They used an atomic force microscope in contact mode to investigate the connection between these films’ strain mechanics and polarization gradients. The researchers correlated the relationship between the asymmetric crystal structure of the cellulose crystals and the films’ piezoelectric characteristics. They found that the ordered cellulose nanocrystal films’ shear stress piezoelectric constant (d25) had a magnitude of 2.1 Å/V, which is similar to the piezoelectric constant of a piezoelectric metal oxide reference film. This finding indicates that the piezoelectric performance of cellulose nanocrystal films is competitive with certain piezoelectric metal oxides.
Zheng et al. [4] created a new, easy-to-use, affordable, and scalable method for creating flexible piezoelectric nanogenerators with outstanding performance by utilizing a porous cellulose nanofibril CNF/PDMS aerogel film. The resultant flexible porous CNF/PDMS aerogel film-based nanogenerators showed highly stable and high-output piezoelectric signals under periodic external mechanical deformation with an oscillator: an open-circuit voltage of 60.2 V, a short-circuit current of 10.1 μA, and a corresponding power density of 6.3 mW/cm3. These nanogenerators produced enough electricity to charge a capacitor to 3.7 V and directly power 19 blue light-emitting LEDs.
In a study conducted by Islam et al. in 2017 [88], they cut pine trunks into discs to determine localized electrophysiological events in the stems and branches of various herbaceous and woody plants. They glued one surface of these discs with silver epoxy and covered it with aluminum foil to form an electrode (Fig. 12). They then measured the short-circuit current generated using a silver-coated probe and a Keithley 6487 pico-ammeter capable of 1.000 low-current readings per second. With electrodes positioned at precise target positions on every plant sample, they were able to collect system voltages. They then recorded these voltages using a high input impedance digital multimeter.
Figure 12: Cross-section of the plant structure and cross-section of the pine tree disk. Adapted with permission from Reference [88], Copyright © 2017, David Publishing
They observed that when they subdivided the branches of plants, each section produced roughly the same amount of terminal voltage. What is even more remarkable is that even when each branch section was subdivided into smaller pieces, these new and smaller pieces were able to produce almost the same amount of terminal voltage. Furthermore, when they examined silver epoxy-treated samples, they found that the maximum current was in living cells close to the vascular cambium region. They also found electrical activity in secondary xylem and phloem tissues. The research revealed that if the input impedance of the measuring instrument is not high enough, a significant reduction in the amplitude of the measured output voltage will occur.
In a study conducted by Kan et al. in 2017 [89], the feasibility of harvesting energy from wood floor vibration caused by human movement was investigated. They constructed the wooden floor system from nine 40 mm × 225 mm wooden beams with a spacing of 380 mm in the center and a span of 3.65 m in the experimental setup, they used a beam-type piezoelectric generator, an electrical interface that collects energy, a digitizer, and a computer with signal recording software. They utilized human movements as a mechanical energy source and converted the vibration energy generated by these movements into electrical energy through a piezoelectric generator placed on the floor. The generated electricity was regulated by the electrical interface before being stored in a storage system or powering the load (electrical device). The findings of the research demonstrate the potential of piezoelectric generators for energy harvesting on wooden floors. It is emphasized that future research should examine the feasibility of powering electronic systems using multiple piezoelectric generators and multiple excitation sources in in-situ wood floor structures. Such studies can make significant contributions to sustainable energy solutions and improve energy efficiency.
Tuukkanen et al. [90] investigated the significant piezoelectric activity of three different types of nanocellulose films: wood-based cellulose nanofibrils, cellulose nanocrystalline films, and bacterial nanocellulose films. They formed sensors by sandwiching the nanocellulose films between two electrodes (Fig. 13a,b). They fabricated the electrodes for the sensors on a 125-micron thick polyethylene terephthalate substrate using electron beam evaporation. They evaporated a 100 nm thick copper layer through a sieve to create an electrode sample and performed measurements.
Figure 13: (a) Piezoelectric sensor measurement setup: (b) Wood-based cellulose nanofibril film and (c) image of the sensor prepared for measurement. Adapted with permission from Reference [90], Copyright © 2018, IntechOpen Publishing
The results show that nanocellulose is a potential biobased piezoelectric sensor material. These findings represent an important step towards the development of sustainable and environmentally friendly piezoelectric sensors. The research sheds light on future studies by emphasizing the usability of biobased materials in piezoelectric applications.
In 2020, Al-Haik et al. [91] conducted a study in which they collected energy from a macro fiber composite glued to the trunk end of a tree branch. As part of the research, they placed the tree branch in the test section of a wind tunnel with controlled airflow velocity. The macro fiber composite clamped to the end of the trunk collected energy from the vibrating tree branch at ambient wind speed (Fig. 14). The study evaluated the potential of energy harvesting.
Figure 14: Test setup used for piezoelectric measurement in a palm tree. Adapted with permission from Reference [91], Copyright © 2020, IOP Publishing
The study revealed that the power output increased with increasing wind speed. At 7 m/s air flow velocity, they found that a maximum power output of 0.157 mW was achieved, corresponding to a power density of approximately 393 mW/m2. They emphasized that the voltage generated at various flow rates was sufficient to power small sensors.
In preparing cellulose-based materials, improving preparation technology can effectively promote the orientation of cellulose microfibrils and increase piezoelectric dipoles [92]. Chemical modification introduces some functional groups on the surface of cellulose fibers to expand the application range. Chemical modification of cellulose materials changes cellulose’s chemical properties and biodegradability and gives cellulose materials various applications [93,94]. Wood’s piezoelectric behavior has also been linked to its hierarchical structure, with studies focusing on enhancing wood’s piezoelectric properties through treatments like delignification [95]. The anisotropic nature of wood fibers, enhanced by oxidation processes, has been shown to contribute to its piezoelectric characteristics [96]. Sun et al. [97] modified wood through chemical delignification (hydrogen peroxide and acetic acid). They transformed the wood into a mini-generator by making it compressible and separated from lignin and hemicelluloses. By applying a load on the wood material, they generated electrical voltage through the piezoelectric effect (Fig. 15).
Figure 15: Applications of our wood sponge nanogenerator as a proof of concept. (a) Diagrammatic representation showcasing the wearable sensor application. (b) A schematic representation of energy supply applications. (c) Finger tapping is an example of movement sensing. (d) A finger bending as an example of movement sensing. (e) Diagrammatic representation of upscaling using several wood sponges together. (f and g) An example of the resulting piezoelectric timber floor that, when pressed with the foot, may power a commercial LCD screen (inset photographs). Adapted with permission from Reference [97], Copyright © 2020, American Chemical Society
According to the research results, they found that a wood sponge piezoelectric generator (15 mm × 15 mm × 14 mm), produced by a simple delignification process, can generate an instantaneous voltage of up to 0.69 V and a current of 7.1 nA with a low-stress application of 13.3 kPa, with an eighty-five-fold increase in performance compared to natural wood. They were also able to significantly increase the maximum output current (≈205 nA) by connecting thirty wooden sponges in parallel [98]. This study suggests that the modified wood could serve as a biosensor or an energy-generating building material (as a power source in smart buildings).
Natural cellulose leads to poor processing performance due to its low solubility, which limits its use in advanced technologies. Researchers typically use mechanical, chemical, and biological methods to address these limitations and develop new cellulose materials (CNC, CNF, etc.) [99,100]. Wang et al. [5] investigated the piezoelectric properties of CNC films. They used colloidal opal structure fabrication technology to achieve vertical alignment of CNCs. The vertical alignment of CNCs was made easier by the high interface energy between the PTFE surface and the CNC, as well as the shear force. To improve alignment, a DC electric field was applied externally. The outcome was that the CNC films had outstanding piezoelectric performance; their piezoelectric coefficient was determined to be 19.3 ± 2.9 pm/V.
Guan et al. [101] presented a simple and scalable method for producing flexible wood-based piezoresistive pressure sensors by modifying natural wood with reduced graphene oxide. These sensors exhibit high sensitivity (1.85 kPa–1) over a wide linear range and long cyclic stability (10,000 cycles). Additionally, they enable accurate detection of finger movements, acoustic vibrations, and pulse waves. A large-area pressure sensor array was also successfully mounted on a single piece of flexible wood for spatial pressure mapping. Upon examining their results, they stated that this innovative strategy offers a sustainable, low-cost, and simple solution for high-performance flexible pressure sensors, contributing to the development of wearable electronics.
Sun et al. [102] prepared samples with P. chrysosporium and G. adspersum under similar conditions at different times. They then coated the surface of the wood samples (5 mm × 5 mm × 5 mm) with Pt-Pd (80/20) using a sputter coater to produce a coating of about 10 nm to make them conductive. They characterized it by SEM. They were also measured by FTIR spectrometry to see the changes in the chemical composition of the cell wall after fungal treatment. To see the electrical potential, they first glued a 15 mm × 15 mm copper foil to the radial sections of the wood (15 mm × 15 mm × 13.2 mm) and then covered it with an insulating layer. They also provided conduction with conductive wire. Then, to monitor the pressure exerted on the specimens, they attached the specimen to the plate equipped with a loading cell mounted on the rigid frame of the engine. They used a linear motor to apply constant frequency and constant pressure to the samples. They connected the conductive wires to a programmable electrometer and measured the electrical voltage of natural and decayed wood with a Keithley 6514 equipped with MATLAB software. When they analyzed the results, they found that the piezoelectric voltage increased more than fifty-five-fold by increasing the elastic compressibility of the wood sample with fungal decay pretreatment. They found that a single cube of rotten wood produced a maximum voltage of 0.87 V and a current of 13.3 nA under a voltage of 45 kPa. This study aimed to demonstrate the feasibility of using environmentally friendly piezoelectric wood material to meet the challenges of energy and climate change, as well as to generate electricity from renewable sources and reduce the consumption of buildings. It is important to remember that the biodegradation of wood due to the presence of fungal germs will significantly impact the mechanical strength, longevity, and practicality of piezoelectric devices [103]. Chemical or biological techniques, such as the grafting of bio-based polymers, wood carbonization, or the deposition of metal oxide nanoparticles (ZnO, TiO2, Al2O3, and MgO, etc.) on the wood surface, can be used to achieve improvements [104–107]. Miao et al. [108] extensively investigated the piezoelectric load response of CNC films. This study investigated how surface chemistry, particle morphology, ionic strength, and film microstructure affect bulk CNC performance. Their methodology involves a scalable bottom-up approach to fabricate CNC films. They determined that their CNC films maintained a consistent piezoelectric response of approximately 29 pC/N (d33) even after 440 compression cycles. They also found that the piezoelectric response of CNC-polyethylene oxide nanocomposites, which were both flexible and transparent, was approximately 23 pC/N (d33), which was comparable.
Yang et al. [109] also investigated the fabrication of wood-based piezoelectric energy harvesters, highlighting the potential of wood to be used in sustainable energy conversion technologies. Chae et al. [110] described a technique that uses rising bubbles to impart directed shear stress, which causes the bacterial cellulose microfibrils to pack remarkably parallel during the bacterial culture. It has drawn a lot of attention since cellulose-based EAPap has a measured piezoelectric coefficient (d31) of up to 1425 pm/V [111]. Ram and colleagues [112] leveraged the natural hierarchical porous structure of wood to cultivate zinc oxide nanostructures, resulting in high electrical output ideal for harnessing mechanical energy in shoe soles. Nonetheless, the use of zinc oxide, which is a toxic substance, raises concerns regarding its impact on human health and the environment. Similarly, wood materials were used as a template after the delignification process. Periodate oxidation can also enhance the wood/ZnO piezoelectric nanogenerator’s output performance. This is because it increases the porosity of the wood and introduces negative charges, which promote more uniform diffusion of Zn2+ ions in the wood [113]. Li et al. [114] combined rod-shaped cellulose nanocrystals (CNC) with polyethylene glycol (PEG), a soft polymer. With this combination, graphene (GR) was adsorbed as surface electrodes to obtain a CNC-PEG-GR piezoelectric porous material with a 0.096 g/cm³ density. The pore length-to-diameter ratio of the porous material was increased from 1.1 to 3.3 by optimizing the freeze-drying process, and the voltage output reached 0.7 V. As a result, they emphasized that this material can be easily integrated into portable, self-powered sensors used in smart wearable electronic devices. Additionally, Go et al. [115] investigated the feasibility of piezoelectric tiles harvesting energy from human footsteps and pressure. For this purpose, they produced piezoelectric tiles from three different materials: wood, porcelain, and ceramic. Each tile had five piezoelectric plates at the four corners and the center. A voltmeter connected to the piezoelectric tile system to measure the voltage output generated when people stepped on the tiles. The study results showed that the wood tile produced an average voltage of 0.711 V, the porcelain tile produced 0.698 V, and the ceramic tile produced 1.018 V. Jiang et al. [96] investigated the enhancement of piezoelectric properties in wood through TEMPO oxidation and PDMS treatment, emphasizing the role of cellulose crystal orientation in wood fibers in dictating its piezoelectric behavior. They stated that wood electromechanical conversion devices have full potential for energy harvesters and electromechanical sensor fields. The schematic of the piezoelectric behavior in wood via TEMPO oxidation and PDMS treatment is presented in Fig. 16.
Figure 16: Schematic of piezoelectric behavior in wood via TEMPO oxidation and PDMS treatment. Adapted with permission from Reference [96], Copyright © 2023, American Chemical Society
Trellu et al., in their [23] study, evaluated the contribution of macroscopic polarization in cellulose films to their piezoelectric properties. For this purpose, bending tests determined the coefficients of cellulose films with piezoelectric properties in the transverse direction. In the experiments, they prepared five stainless steel/cellulose bilayer films with different morphologies and surface charge levels: two almost neutral cellulose microfibers (CMF) and three (2,2,6,6-tetramethylpiperidin-1-yl) oxyl (TEMPO)-oxidized cellulose microfibers (TCMF) and nanofibers (TCNF) carrying negatively charged groups on the surface. When they examined the results, they observed that unmodified CMF showed a low dielectric constant, while the dielectric properties of TEMPO-oxidized samples increased by up to nine times compared to poly (vinylidene fluoride)-based polymers. This proved that polar groups and surface charge in TEMPO-oxidized cellulose films significantly enhanced the piezoelectric properties. Tang [116] discussed the electromechanical properties of textured Mn-PMN-PZT ceramics under pressure, highlighting the high piezoelectric response exhibited by these materials. This comparison sheds light on the unique characteristics of wood as a piezoelectric material and its potential advantages in certain applications. Voignac et al. [117] used cellulose nanocrystals (CNC) as an excellent matrix for distributing proteins and fabricating robust, transparent thin films with improved dielectric conductivity. These films were obtained by drying a water suspension of CNC and proteins via evaporation-induced self-assembly. The resulting films were characterized in detail in terms of electrical, mechanical, piezoelectric, and optical properties. They designed a simple impact test to evaluate the change in the piezoelectric properties of the CNC film. They also empirically investigated this piezoelectric behavior in one of the CNC-protein films (CNC-BSA) to investigate whether CNC plays a role in improving this behavior. According to the results, the CNC-BSA film produced a higher potential upon impact, indicating that they formed a more sensitive and efficient composite film than the pure CNC. Cellulose-based piezoelectric technologies are widely used in many areas and are essential in medicine. Maity et al. [118] designed a completely three-dimensional (3D) printed pyro-piezoelectric nanogenerator (Py-PNG) manufactured from CNCs, one of the most common and completely biodegradable biopolymers in the world. This study proposed a new NG sensor manufacturing method using 3D geometry. This NG sensor consists of only 3D printed parts and offers superior mechano-thermal energy harvesting performance and sensitivity. The sensor can detect heartbeat and breathing accurately without requiring an external power source or battery. They also introduced an intelligent mask and breath monitoring system that integrates this technology. This innovative solution is an essential step towards real-time cardiorespiratory monitoring, biomedical device development, and human-machine interfaces, providing valuable and exciting information for medical diagnosis.
Moreover, Meng [61] explored the fabrication of a mesoporous all-wood sponge with enhanced compressibility and charge polarization capacity, capable of generating a piezoelectric output voltage of up to 2 V under stress. This study showcases the potential for wood-based materials to serve as efficient piezoelectric generators, offering promising avenues for energy management and conversion applications. Wu et al. [119] have addressed the development of superelastic wood-based nanogenerators that enhance the piezoelectric effect for sustainable energy conversion. The nanogenerators utilize the piezoelectric properties of wood to convert mechanical energy into electrical energy. They have reported that the results are 70 times greater than those of natural wood. The study highlights the potential of wood as a sustainable piezoelectric material. However, In his study, Belashev [120] examined the time series of electrical potential differences along the trunk of a pine tree and the time series of meteorological and geomagnetic parameters recorded between 2017 and 2022, as well as the global geomagnetic activity time series taken from the K-index database. The study’s findings revealed that the electrical potential differences along the trunk of a pine tree varied over time according to seasons and precipitation types. In particular, he found that the daily cycle observed in spring and autumn was associated with transpiration. He stated that precipitation reduced the time course of the potential difference, while precipitation types such as snow and fog increased this difference. He associated the effect of storms on the potential difference of pine trees with previous oscillations, suppression of the daily transpiration peak, changes in meteorological parameters, and the decrease in geomagnetic activity after the storm.
5 Effect of Planted Trees on Piezoelectric and Electrical Potential
In their study, Koppán et al. [121] selected hairy oak (Quercus cerris L.) as the tree species. They placed a total of sixteen non-polarized electrodes at four different levels (0, 2, 4, 6 m) on the tree trunk under the cambium, representing four directions (north, south, east, west) at each level (Fig. 17). Starting in 1997, they recorded electric potential differences for four years. The study revealed that the measured electric potential difference has a characteristic sinusoidal diurnal variation. When they examined the annual fluctuation of the mean daily amplitudes of the daily variations, they found that these values reached a maximum at least twice a year. When they examined the differences in electric potential, they found that there is a relationship between the water potential of the air and the sap flow intensity. However, they emphasized that only snapshots are not sufficient for a complete understanding of the sap situation and that the concentration of elements should be monitored continuously. In their study, Koppán et al. [122] continued their previous research and emphasized that there were significant differences between the channels in the east and west directions of the tree and that these differences were due to the structural inhomogeneity of the tree.
Figure 17: Electrical potential measurement method. Adapted with permission from Reference [122], Copyright © 2005, University of Szeged Publishing
They found that the deviations between elevation levels were small. They found that there was a strong correlation, especially between 0–2 m levels and 4–6 m levels. When they examined the daily curves of electrical potential differences, they found that the maximum values occurred between 06.00–07.00, and the minimum values occurred between 16.00–17.00. With these studies, important data were provided for plant physiology and ecological research by revealing the daily and annual dynamics of electrical potential differences of trees.
Calnan et al. [123] measured the electrical potential between the tree and the soil. They stated that they obtained electricity between 0.8 and 1.2 V from this potential. Between December 2003 and May 2005, Gibert et al. [124] equipped the trunk of a black poplar (Populus nigra L.) tree up to a height of 10.5 m with a vertical line (11 electrodes) and two rings (16 electrodes), totaling twenty-seven electrodes. They measured the electric potential using 6 mm diameter stainless steel electrodes placed 5 mm deep into the sapwood. They used a non-polarized lead/lead chloride ground electrode placed 80 cm deep in the soil. They reported the daily electrical variations in detail (Fig. 18).
Figure 18: Location of the electrodes used for electrical potential measurement on the tree. Adapted with permission from References [124,125], Copyright © 2006, Elsevier B.V and 2010, Elsevier B.V
As a result of the study, they found that the electrical variation was related to sap flow. However, they suggested that electrical potential variations are not solely due to sap flow; various electrochemical effects such as thermoelectric effects, electrokinetic effects, membrane diffusion potentials, and action potentials also play an important role. They found that measurements made during the winter months can show variable amplitudes; however, measurements made during the spring months give stable, consistent results with larger amplitudes and last throughout the summer months.
In 2009 and 2010, Himes et al. [126,127] designed and tested two low-power integrated circuit interconnect ICs for large-leaf maple (Acer macrophyllum) remote sensing networks. The first circuit has 130 nm technology, while the second circuit is a 0.045 Hz oscillator manufactured in 90 nm technology that consumes 2.5 nW during steady-state operation. They stated that these two circuits can provide voltage, timing signals, and wake-up functionality that can be used with remote sensor nodes. Thus, they measured the voltage in the tree. By taking the 20 mV output from the standing tree and connecting custom-made device electrodes to a tree, they produced an output voltage of 1.1 volts, which is sufficient to operate low-power sensors.
In a study conducted by Le Mouël et al. in 2010 [125] between January 2004 and May 2005, they equipped the trunk of a 30 m high black poplar (Populus nigra L.) tree with a total of twenty-seven electrodes forming two rings on a vertical line from 0.5 to 10.5 m in height (Fig. 18). The 6 mm diameter stainless steel electrodes were placed 15 mm deep into the tree trunk. They chose a non-polarized lead-lead chloride ground electrode buried at a depth of 0.7, 5 m from the tree. They measured the potentials at the electrodes using a Keithley 2701 digital multimeter with an input impedance greater than 100 MΩ. When they analyzed the results, they found that the simultaneous signals at all electrodes had the same form, the amplitudes of the trees increased in direct proportion to their height from 10 to 50 mV, and the signals were in a vertical line across the electrodes. They also found that the frequency of the signals did not depend on seasons or time of day.
In a study conducted by McGarry et al. in 2011 [128] on a eucalyptus tree (Eucalyptus sp.), they investigated the amount of energy generated by the crown movement of trees and possible methods of energy harvesting to power wireless sensor nodes. They used a piezoelectric transducer to harvest energy from the tree. They hung a piezoelectric transducer on the trunk of a branch. They allowed the force caused by the attached mass to vibrate, thus generating power to the sensor node. In the study, they found that the 5 kg mass gave an optimum power value of 44 mW. They also found that the free vibrations caused by the movement of the branch alone did not provide enough energy to power the sensor nodes.
Hao et al. [129], in their study of different tree species, placed three iron electrodes (5 mm diameter) into the xylem at different heights of each tree (50, 100, 130 cm). They placed a grounding electrode 15 cm below the soil. They connected fixed-length wires to the electrodes and created a current circuit between the electrode in the tree and the electrode in the soil through the load resistance via the wires. They measured the voltage and current of the load resistor with a multimeter. They also measured the output power, xylem pH, and environmental parameters such as air temperature, air relative humidity, soil temperature, soil moisture, and soil pH of the selected trees. As a result of the study, they observed that there is a constant electrical potential difference and current in forests to power wireless sensor networks. They found that bioelectricity in the xylem is related to soil pH. They also found that air relative humidity, soil temperature, and electrode material affect bioelectricity in the xylem.
In a study by Ying et al. [130] on a eucalyptus tree (Eucalyptus sp.), they nailed several probes to the trunk of the tree and allowed the probes to penetrate the bark without touching the xylem. They connected these probes to the electrode of a capacitor. They connected another electrode of the capacitor to the soil through probes and wires. Due to the electrical potential difference between the tree and the soil, they designed an equivalent circuit model to collect bioenergy. According to the design, when the circuit is switched on, the capacitor will be charged by the tree power. They measured the voltage change between the two electrodes of the capacitor with a voltmeter (Fig. 19).
Figure 19: Electrical potential measurement method from the living tree. Adapted with permission from Reference [130], Copyright © 2015, AIP Publishing
In their study, they proved that there is an electrical potential difference between the phloem of a tree and the surrounding soil. They also found that the shape of the electrodes was the key factor affecting the contact resistance between the electrodes and the phloem in charging efficiency.
In 2015, on a poplar tree (Populus x Canadensis Moench), Hao et al. [131] placed a total of ten electrodes, five each on the trunk of the tree and the surrounding soil. In both sets, the electrodes were arranged as Cu-coated Al, Al, Cu, Fe and Cu-coated Fe. They chose electrodes of the same size (0.6 cm diameter and 8 cm length). They placed the inner end of the electrode 5 cm deep into the trunk and tied the outer end to a wire. They placed the soil electrodes at a depth of 80 cm. They noted that the lines connecting any two adjacent electrodes to the center of the trunk had a 72° angle (Fig. 20a).
Figure 20: Electrical potential measurement method in wood, (a and b) Trunk electrode arrangement. Adapted with permission from References [131,132], Copyright © 2015 PLOS Publishing and 2018 AIP Publishing
They connected the wires between the body electrode and the ground electrode as a load resistor in series, thus creating a current circuit across the load resistor. They measured the voltage across the resistor using a high input impedance voltmeter. They conducted the study during the summer months (June–August 2014) and recorded the measurements at noon. According to the results, they found that the conductivity of the metal electrode significantly affected the contact resistance of the electrode-soil and electrode-body contact surfaces, while the metal reactivity of the electrode had no significant effect on the voltage. However, they found that passivating the electrode materials significantly reduced the voltage. In another study conducted by Hao et al. [132] in different periods and locations between November 2014 and June 2017, they aimed to detect the effect of electrode size on voltage in advance and provide a reference for the best use of such a generator. For this reason, they used different types and sizes of electrodes (Fig. 20b). They connected an external load resistor to the wires between the body electrode and the ground electrodes in such a way that a current circuit is formed through the load resistor. They measured the voltage across the load resistor using a high input impedance voltmeter, a seven-channel voltage measurement system designed for tree-to-ground voltage detection. They applied a median filtering algorithm to remove noise. From the data, they found that the voltage has a logarithmic relationship with the effective surface area of the ground electrode. They observed that as the area of the electrode increased, the voltage increased by approximately 57% compared to the initial value. However, they observed that the growth rate decreased significantly. Therefore, in terms of efficiency, cost, and portability, they found that a larger electrode size is not always better for a generator. In this study, they found that an electrode size of 10 cm × 10 cm × 0.3 cm was optimal.
6 Effect of Planted Trees on Electrical Potential in Buildings
Helder et al. [133,134] conducted a study on obtaining energy from green plants. They realized the project named ‘Plant-e’ on a roof in Wageningen, Netherlands. In this project, they aimed to generate energy using plant roots and bacteria in the soil. In experiments with different designs, they generated electricity by collecting electrons through electrodes placed on plant roots. They stated that the source of the project, which utilizes 70% of the organic matter obtained from the photosynthesis of plants, is the burning of organic matter accumulated in plant roots by bacteria and the production of electricity using the electrons released as a result. They also stated that the electricity produced by the system they tested on a 17 m2 sample has enough power to run a laptop computer, and when considered on a larger scale, rice production can be done together with electricity production, thus combining food and energy production.
Forestami is an urban reforestation project supported by the City of Milan, Lombardy Regional Council, Parco Nord Milano, Parco Agricolo Sud Milano, ERSAF, and Fondazione di Comunità Milano. This project is the result of research carried out by the Polytechnic University of Milan with the support of Falck Renewable Energy and FS Sistemi Urbani. By 2030, the major objective of the project to plant three million new trees in the Metropolitan City was the need to create a real physical, environmental, and cultural change in the city by reconsidering nature as a structural part of urban environments [135,136]. Fig. 21 shows an image of the Forestami project exhibited at the Milan Super Salon.
Figure 21: An image of the Forestami project exhibited in Milan. Adapted with permission from Reference [137], Copyright © 2024 Dezeen. All rights reserved
The project aims to improve the quality of air and green spaces through urban forestry intervention. With the Forestami project, the Metropolitan Municipality of Milan has taken on the challenge of preserving the biodiversity of the woodlands around cities and the continuous tree systems within cities to address global urban warming, energy consumption, and air pollution. Considering the difference in electrical potential of three million trees, the alternative electricity generation and energy savings sound good. The project will support the generation of new ideas and studies for the Forestami project, which will last until 2030 [135,136].
Bosco Verticale is an award-winning landmark in Milan and the world’s first vertical forest (Fig. 22). The project was designed in 2014 by Boeri Studio Architects, led by architects Stefano Boeri, Gianandrea Barreca, and Giovanni La Varra. They are working on alternative vertical urbanization to reduce the destruction caused by urbanization and to find solutions to the city’s oxygen and space problems. The project building consists of two towers, 76 m and 110 m high, with a total of four hundred and eighty trees and three hundred plants [138].
Figure 22: Image of the world’s first vertical forest. Adapted with permission from References [138–140], Copyright © 2022 Iklime Polat Interior Architecture. All rights reserved, 2024 ArchDaily. All rights reserved and 2022 Dezeen. All rights reserved
As a result of the study, the sustainability of such buildings was discussed. The potential to generate alternative electricity and achieve energy savings through the electrical potential obtained from living trees seems inevitable [138].
The studies have provided extensive data on how different types and processing methods of wood affect its electrical potential performance. It sheds light on future research to make the best use of this potential and optimize the piezoelectric properties of wood for various applications.
In this study, the research on the electrical potential properties of wood is discussed in detail, and several important findings are presented. The piezoelectric behavior of wood material has shown that it can generate energy by generating electrical potential under mechanical stress. The piezoelectric properties of planted trees and their effects on the electrical potential have been investigated, and how various factors affect these properties have been emphasized.
In addition, studies investigating the energy generation potential of wooden structures are reviewed, and the following results were obtained:
• The existence of direct and reverse piezoelectric effects in wood is scientifically proven.
• The piezoelectric behavior of wood material has been stated to be able to generate electrical voltage by creating electrical polarization in response to mechanical stress.
• The degree of crystallinity and micelle orientation of the cellulose crystals in the cell wall of the trees were reported to be effective on the piezoelectric modulus.
• It was emphasized that the piezoelectric properties of wood can vary depending on density, temperature, magnitude of load, wood species, age of the wood, annual ring deviations, and wood defects.
• It has been pointed out that it is possible to increase the piezoelectric modulus of wood by chemical treatments (cork pretreatment).
• It has been indicated that it could be important for potential applications in the fields of advanced materials science and nanotechnology.
The results on the electrical potential behavior and piezoelectric effects of planted trees are summarized as follows:
• The electrical potential differences of planted trees were examined and characteristic diurnal variations were identified.
• It is stated that daily variations are effective on annual fluctuations.
• Planted trees are seen to have a certain potential.
• It was determined that the electrical behavior of the tree varies depending on factors such as different periods of the day, seasonal changes, and the height of the tree.
• Factors such as tree sap, electrochemical properties (thermoelectric effects, electrokinetic effects, membrane diffusion potentials, and action potentials), and soil Ph level have been claimed to affect tree potential, but this has not yet been proven.
• It was emphasized that the electrodes used in the measurement (size, effective surface area, etc.) are important.
The effects of planted trees on electrical potential in buildings were determined as follows:
• It has been stated that energy can be produced using plant roots and bacteria in the soil.
• The reasons cited for generating electricity from trees in buildings include preserving the biodiversity of tree systems and addressing global urban warming, energy consumption, and air pollution.
These findings provide important contributions toward a better understanding of the piezoelectric properties of wood materials. The results show that the piezoelectric properties of wood have significant potential for energy harvesting, sensors, and other high-tech applications.
This article reviews the latest scientific research in wood-based energy harvesting with a focus on piezoelectric applications of wood in terms of sustainability, environmentally friendly technologies, and energy efficiency, in chronological order. Advanced engineering techniques such as nanotechnology and chemical modifications used in these studies not only impart superior electrical properties to wood but also open up new horizons for various applications based on natural wood. In the future, the benefits of the piezoelectric properties of wood include energy harvesting, smart materials, and sustainable electronics. Wood-based piezoelectric devices can convert mechanical energy into electrical energy to provide power to small electronic devices or sensors. This will be a great advantage, especially as the importance of energy efficiency and renewable energy sources increases. Additionally, the biodegradable properties of wood have the potential to reduce the amount of electronic waste. The relationship between piezoelectric effects and biochemical reactions in living organisms is a growing interest in biophysics, bioengineering, and forest-based technologies. Piezoelectric effects in biological tissues are linked to biochemical reactions through mechanotransduction, cellular signal transmission, and bioelectric communication. The interdisciplinary work fields have an important potential to understand biological processes and develop new biomedical technologies. While the increasing importance of renewable and sustainable energy sources, the usage of natural materials such as wood or trees in this field has great importance in increasing the diversity of energy resources. Research has shown that the piezoelectric properties of wood are affected by various factors and need to be improved. The future research should focus on better understanding the piezoelectric properties of wood and optimizing these properties to enhance energy efficiency.
1. To better understand the effects of the structural properties and environmental impact assessments on the standing trees’ piezoelectric properties and electrical potential differences, further research is needed.
2. The piezoelectric properties of wood can be a significant alternative for renewable energy sources and smart material technologies, and therefore, wider research on these properties should be encouraged.
3. The effects of fungal decomposition on piezoelectric properties should be examined in more detail, and further research should be conducted in this area.
4. New studies on the piezoelectric effects on wood should be conducted, and the formation of piezoelectric effect formation should be examined at the nano-scale.
In conclusion, although these studies are still in their early stages, they will undoubtedly lead to significant innovations and innovative products in the future. The piezoelectric properties of wood offer great potential in terms of energy efficiency and sustainability, and it is of great importance to continue research in this area.
Acknowledgement: None.
Funding Statement: None.
Author Contributions: Zeynep Eda Özan: Conceptualization, methodology, and preparation of the original draft. Gökhan Gündüz: Conceptualization, methodology, and editing of the original draft. Deniz Aydemir: Conceptualization, methodology, and editing of the original draft. All authors reviewed the results and approved the final version of the manuscript.
Availability of Data and Materials: None.
Ethics Approval: Not applicable.
Conflicts of Interest: The authors declare no conflicts of interest to report regarding the present study.
References
1. Benes E. Piezoelectric materials. Vienna: Institut für allgemeine Physik, Technische Universität Wien; 2009 (In German). [Google Scholar]
2. Li S, Zhao Z, Zhao J, Zhang Z, Li X, Zhang J. Recent advances of ferro-, piezo-, and pyroelectric nanomaterials for catalytic applications. ACS Appl Nano Mater. 2020;3:1063–79. doi:10.1021/acsanm.0c00039. [Google Scholar] [CrossRef]
3. Hui Y, Gomez-Diaz JS, Qian Z, Alu A, Rinaldi M. Plasmonic piezoelectric nanomechanical resonator for spectrally selective infrared sensing. Nat Commun. 2016;7:11249. doi:10.1038/ncomms11249. [Google Scholar] [PubMed] [CrossRef]
4. Zheng Q, Zhang H, Mi H, Cai Z, Ma Z, Gong S. High-performance flexible piezoelectric nanogenerators consisting of porous cellulose nanofibril (CNF)/poly(dimethylsiloxane) (PDMS) aerogel films. Nano Energy. 2016;26:504–12. doi:10.1016/j.nanoen.2016.06.009. [Google Scholar] [CrossRef]
5. Wang J, Carlos C, Zhang Z, Li J, Long Y, Yang F, et al. Piezoelectric nanocellulose thin film with large-scale vertical crystal alignment. ACS Appl Mater Interfaces. 2020;12:26399–404. doi:10.1021/acsami.0c05680. [Google Scholar] [PubMed] [CrossRef]
6. Imseeh WH, Alshibli KA, Moslehy A, Kenesei P, Sharma H. Influence of crystal structure on constitutive anisotropy of silica sand at particle-scale. Comput Geotech. 2020;126:103718. doi:10.1016/j.compgeo.2020.103718. [Google Scholar] [CrossRef]
7. Zhang W, Zhang Z, Yao B, Jing J, Xu Y, Zhao Z, et al. A masterpiece of superior crystals: quartz resonant pressure sensor—a review. IEEE Sens J. 2024;24:9278–98. doi:10.1109/JSEN.2024.3361081. [Google Scholar] [CrossRef]
8. Tozluoğlu A, Çöpür Y, Özyürek Ö, Çıtlak S. Nanoselüloz üretim teknolojisi. Turkish J For | Türkiye Orman Derg. 2015 (In Turkish). doi:10.18182/tjf.09718. [Google Scholar] [CrossRef]
9. Vilarinho PM, Barroca N, Zlotnik S, Félix P, Fernandes MH. Are lithium niobate (LiNbO3) and lithium tantalate (LiTaO3) ferroelectrics bioactive? Mater Sci Eng C. 2014;39:395–402. doi:10.1016/j.msec.2014.03.026. [Google Scholar] [PubMed] [CrossRef]
10. Proto A, Penhaker M, Bibbo D, Vala D, Conforto S, Schmid M. Measurements of generated energy/electrical quantities from locomotion activities using piezoelectric wearable sensors for body motion energy harvesting. Sensors. 2016;16:524. doi:10.3390/s16040524. [Google Scholar] [PubMed] [CrossRef]
11. Pang S, He Y, Zhong R, Guo Z, He P, Zhou C, et al. Multifunctional ZnO/TiO2 nanoarray composite coating with antibacterial activity, cytocompatibility and piezoelectricity. Ceram Int. 2019;45:12663–671. doi:10.1016/j.ceramint.2019.03.076. [Google Scholar] [CrossRef]
12. Shaukat H, Ali A, Bibi S, Altabey WA, Noori M, Kouritem SA. A review of the recent advances in piezoelectric materials, energy harvester structures, and their applications in analytical chemistry. Appl Sci. 2023;13:1300. doi:10.3390/app13031300. [Google Scholar] [CrossRef]
13. Chen X, Zhu Q, Jiang B, Li D, Song X, Huang L, et al. Research progress of wood and lignocellulose in sustainable piezoelectric systems. Nano Energy. 2024;126:109650. doi:10.1016/j.nanoen.2024.109650. [Google Scholar] [CrossRef]
14. Lu L, Ding W, Liu J, Yang B. Flexible PVDF based piezoelectric nanogenerators. Nano Energy. 2020;78:105251. doi:10.1016/j.nanoen.2020.105251. [Google Scholar] [CrossRef]
15. Wu L, Jin Z, Liu Y, Ning H, Liu X, Hu A, et al. Recent advances in the preparation of PVDF-based piezoelectric materials. Nanotechnol Rev. 2022;11:1386–407. doi:10.1515/ntrev-2022-0082. [Google Scholar] [CrossRef]
16. Ponnamma D, Chamakh MM, Alahzm AM, Salim N, Hameed N, AlMaadeed MAA. Core-shell nanofibers of polyvinylidene fluoride-based nanocomposites as piezoelectric nanogenerators. Polymers. 2020;12:2344. doi:10.3390/polym12102344. [Google Scholar] [PubMed] [CrossRef]
17. Liu C, Xu H, Huo B, Wang J, Wang Z, Chen X, et al. Research progress of PVDF based piezoelectric polymer composites in water pollution remediation. J Water Process Eng. 2023;55:104181. doi:10.1016/j.jwpe.2023.104181. [Google Scholar] [CrossRef]
18. Fukada E. Piezoelectricity of wood. J Phys Soc Japan. 1955;10:149–54. doi:10.1143/JPSJ.10.149. [Google Scholar] [CrossRef]
19. Bazhenov VA. Piezoelectric properties of wood. New York: Consultants Bureau; 1961. [Google Scholar]
20. Fukada E. Piezoelectric properties of biological polymers. Q Rev Biophys. 1983;16:59–87. [Google Scholar] [PubMed]
21. Abbasi Moud A. Cellulose nanocrystals examined by atomic force microscopy: applications and fundamentals. ACS Food Sci Technol. 2022;2:1789–818. doi:10.1021/acsfoodscitech.2c00289. [Google Scholar] [CrossRef]
22. Chen C, Kuang Y, Zhu S, Burgert I, Keplinger T, Gong A, et al. Structure-property-function relationships of natural and engineered wood. Nat Rev Mater. 2020;5:642–66. doi:10.1038/s41578-020-0195-z. [Google Scholar] [CrossRef]
23. Trellu H, Le Scornec J, Leray N, Moreau C, Villares A, Cathala B, et al. Flexoelectric and piezoelectric effects in micro- and nanocellulose films. Carbohydr Polym. 2023;321:121305. doi:10.1016/j.carbpol.2023.121305. [Google Scholar] [PubMed] [CrossRef]
24. Carolin CF, Kamalesh T, Kumar PS, Hemavathy RV, Rangasamy G. A critical review on sustainable cellulose materials and its multifaceted applications. Ind Crops Prod. 2023;203:117221. doi:10.1016/j.indcrop.2023.117221. [Google Scholar] [CrossRef]
25. Placner J. The converse piezoelectric effect in wood and cellulosematerials (Master Thesis). Institute of Wood Science and Technology, Department of Material Sciences and Process Engineering, University of Natural Resources and Applied Life Sciences: Austria; 2009. [Google Scholar]
26. Annamalai PK, Nanjundan AK, Dubal DP, Beom Baek J. An overview of cellulose-based nanogenerators. Adv Mater Technol. 2021. doi:10.1002/admt.202001164. [Google Scholar] [CrossRef]
27. Ram F, Garemark J, Li Y, Pettersson T, Berglund LA. Functionalized wood veneers as vibration sensors: exploring wood piezoelectricity and hierarchical structure effects. ACS Nano. 2022;16:15805–13. doi:10.1021/acsnano.2c04668. [Google Scholar] [PubMed] [CrossRef]
28. Moon RJ, Martini A, Nairn J, Simonsen J, Youngblood J. Cellulose nanomaterials review: structure, properties and nanocomposites. Chem Soc Rev. 2011;40:3941. doi:10.1039/C0CS00108B. [Google Scholar] [PubMed] [CrossRef]
29. Tong J, Hu W, Qin Y, Liu Y. Deep eutectic solvent pretreatment for green preparation of nanocellulose. Cellulose. 2023;30:4773–92. doi:10.1007/s10570-023-05154-3. [Google Scholar] [CrossRef]
30. Duan Y, Liu K, Qi J, Li C, Xie H, Du H, et al. Engineering lignocellulose-based composites for advanced structural materials. Ind Crops Prod. 2023;205:117562. doi:10.1016/j.indcrop.2023.117562. [Google Scholar] [CrossRef]
31. Miyashiro D, Hamano R, Umemura K. A review of applications using mixed materials of cellulose, nanocellulose and carbon nanotubes. Nanomater. 2020;10:186. doi:10.3390/nano10020186. [Google Scholar] [PubMed] [CrossRef]
32. Kölln K. Morphologie und mechanische eigenschaften von zellulosefasern untersuchungen mit röntgen-und neutronenstreuung. Albrechts-Universität zu Kiel: Germany; 2004 (In German). Available from: http://macau.uni-kiel.de/servlets/MCRFileNodeServlet/dissertation_derivate_00001173/d1173.pdf. [Accessed 2024]. [Google Scholar]
33. Şahin HT. Suyun kağıt yapısının oluşumuna etkisi üzerine bir inceleme A study on water effects on paper sheet structure formation. SDU Fac For J. 2013;14:152–5 (In Turkish). [Google Scholar]
34. Rojas J, Bedoya M, Ciro Y. Current trends in the production of cellulose nanoparticles and nanocomposites for biomedical applications. In: Cellulose—fundamental aspects and current trends. London: InTech; 2015. doi:10.5772/61334. [Google Scholar] [CrossRef]
35. Geitmann A, Bacic A. Focus on cell walls. Plant Physiol. 2024;194:1–4. doi:10.1093/plphys/kiad537. [Google Scholar] [PubMed] [CrossRef]
36. Müller M, Burghammer M, Sugiyama J. Direct investigation of the structural properties of tension wood cellulose microfibrils using microbeam X-ray fibre diffraction. Holzforschung. 2006;60:474–9. doi:10.1515/HF.2006.078. [Google Scholar] [CrossRef]
37. Mellerowicz E, Sundberg B. Wood cell walls: biosynthesis, developmental dynamics and their implications for wood properties. Curr Opin Plant Biol. 2008;11:293–300. doi:10.1016/j.pbi.2008.03.003. [Google Scholar] [PubMed] [CrossRef]
38. Loqué D, Scheller HV, Pauly M. Engineering of plant cell walls for enhanced biofuel production. Curr Opin Plant Biol. 2015;25:151–61. doi:10.1016/j.pbi.2015.05.018. [Google Scholar] [PubMed] [CrossRef]
39. Jakes JE, Zelinka SL, Hunt CG, Ciesielski P, Frihart CR, Yelle D, et al. Measurement of moisture-dependent ion diffusion constants in wood cell wall layers using time-lapse micro X-ray fluorescence microscopy. Sci Rep. 2020;10(1):9919. doi:10.1038/s41598-020-66916-8. [Google Scholar] [PubMed] [CrossRef]
40. Sjöström E. Wood chemistry fundamentals and applications. 2nd edLondon: Academic Press; 1993. [Google Scholar]
41. Plomion C, Leprovost G, Stokes A. Wood formation in trees. Plant Physiol. 2001;127(4):1513–23. doi:10.1104/pp.010816. [Google Scholar] [CrossRef]
42. Zhong R, Cui D, Ye Z. Secondary cell wall biosynthesis. New Phytol. 2019;221:1703–23. doi:10.1111/nph.15537. [Google Scholar] [PubMed] [CrossRef]
43. Maghsoudi Nia E, Wan Abdullah Zawawi NA, Mahinder Singh BS. Design of a pavement using piezoelectric materials. Materwiss Werksttech. 2019;50:320–8. doi:10.1002/mawe.201900002. [Google Scholar] [CrossRef]
44. Tressler JF, Alkoy S, Newnham RE. Piezoelectric sensors and sensor materials. J Electroceram. 1998;2:257–72. doi:10.1023/A:1009926623551. [Google Scholar] [CrossRef]
45. Chae I, Zu R, Barhoumi Meddeb A, Ogawa Y, Chen Z, Gopalan V, et al. Electric field-induced polarization responses of noncentrosymmetric crystalline biopolymers in different frequency regimes-a case study on unidirectionally aligned β-chitin crystals. Biomacromolecules. 2021;22(5):1901–9. doi:10.1021/acs.biomac.0c01799. [Google Scholar] [PubMed] [CrossRef]
46. De Almeida BV, Pavanello R. Topology optimization of the thickness profile of bimorph piezoelectric energy harvesting devices. J Appl Comput Mech. 2019;5:113–27. doi:10.22055/JACM.2018.25097.1228. [Google Scholar] [CrossRef]
47. Ross RJ, Kan J, Wang X, Blankenburg J, Stockhausen JI, Pellerin RF. Wood and wood-based materials as sensors—a review of the piezoelectric effect in wood. Madison: U.S. Department of Agriculture, Forest Service, Forest Products Laboratory; 2012. [Google Scholar]
48. Wang X, Xiang X, Xie J, Zhao G, Li Z, Sun X. Unleashing the potential: strategies for enhancing performance of electrospun PVDF-based piezoelectric nanofibrous membranes. Fibers Polym. 2024. doi:10.1007/s12221-024-00715-0. [Google Scholar] [CrossRef]
49. Ballato A. Piezoelectricity: history and new thrusts. Proc IEEE Ultrason Symp. 1996;1:575–83. doi:10.1109/ULTSYM.1996.584046. [Google Scholar] [CrossRef]
50. Tichý J, Erhart J, Kittinger E, Privratska J. Fundamentals of piezoelectric sensorics: mechanical, dielectric, and thermodynamical properties of piezoelectric materials. Berlin, Heidelberg: Springer; 2010. doi:10.1007/978-3-540-68427-5. [Google Scholar] [CrossRef]
51. Kumar R, Bera S. Recent approaches in development of bio-based artificial piezoelectric constructs for biomedical applications. Giant. 2024;17:100214. doi:10.1016/j.giant.2023.100214. [Google Scholar] [CrossRef]
52. Şenyurek A, Demetgul M. Kendi enerjisini üretebilen klavye tasarımı. Marmara J Pure Appl Sci. 2015;27(2):42–7 (In Turkish). doi:10.7240/mufbed.28785. [Google Scholar] [CrossRef]
53. Park IW, Kim KW, Hong Y, Yoon HY, Lee Y, Gwak D, et al. Recent developments and prospects of M13- bacteriophage based piezoelectric energy harvesting devices. Nanomater. 2020;10:93. doi:10.3390/nano10010093. [Google Scholar] [PubMed] [CrossRef]
54. Čeponis A, Mažeika D. Piezoelectric systems as an alternative energy source. Mokslas-Lietuvos Ateitis/Sci Future Lithuania. 2014;6(6):676–81. doi:10.3846/mla.2014.775. [Google Scholar] [CrossRef]
55. Ding Y, Pang Z, Lan K, Yao Y, Panzarasa G, Xu L, et al. Emerging engineered wood for building applications. Chem Rev. 2023;123:1843–88. doi:10.1021/acs.chemrev.2c00450. [Google Scholar] [PubMed] [CrossRef]
56. Zhao J, Li F, Wang Z, Dong P, Xia G, Wang K. Flexible PVDF nanogenerator-driven motion sensors for human body motion energy tracking and monitoring. J Mater Sci Mater Electron. 2021;32:14715–27. doi:10.1007/s10854-021-06027-w. [Google Scholar] [CrossRef]
57. Kamel NA. Bio-piezoelectricity: fundamentals and applications in tissue engineering and regenerative medicine. Biophys Rev. 2022;14:717–33. doi:10.1007/s12551-022-00969-z. [Google Scholar] [PubMed] [CrossRef]
58. Saigusa Y. Quartz-based piezoelectric materials. In: Advanced piezoelectric materials (Second Edition). Amsterdam, Holland: Elsevier; 2017. p. 197–233. doi:10.1016/B978-0-08-102135-4.00005-9. [Google Scholar] [CrossRef]
59. Werling KA, Hutchison GR, Lambrecht DS. Piezoelectric effects of applied electric fields on hydrogen-bond interactions: first-principles electronic structure investigation of weak electrostatic interactions. J Phys Chem Lett. 2013;4:1365–70. doi:10.1021/jz400355v. [Google Scholar] [PubMed] [CrossRef]
60. Palma P, Steiger R. Structural health monitoring of timber structures—review of available methods and case studies. Constr Build Mater. 2020;248:118528. doi:10.1016/j.conbuildmat.2020.118528. [Google Scholar] [CrossRef]
61. Meng Z, Liu X, Zhou L, Wang X, Huang Q, Chen G, et al. Versatile mesoporous all-wood sponge enabled by in situ fibrillation toward indoor-outdoor energy management and conversion. ACS Appl Mater Interfaces. 2024;16:6261–73. doi:10.1021/acsami.3c17237. [Google Scholar] [PubMed] [CrossRef]
62. Luo J, Shi X, Chen P, Han K, Li X, Cao X, et al. Strong and flame-retardant wood-based triboelectric nanogenerators toward self-powered building fire protection. Mater Today Phys. 2022;27:100798. [Google Scholar]
63. Chen Z, Zhuo H, Hu Y, Lai H, Liu L, Zhong L, et al. Wood-derived lightweight and elastic carbon aerogel for pressure sensing and energy storage. Adv Funct Mater. 2020 Apr 30. doi:10.1002/adfm.201910292. [Google Scholar] [CrossRef]
64. Luo J, Liu F, Yin A, Qi X, Liu J, Ren Z, et al. Highly sensitive, wide-pressure and low-frequency characterized pressure sensor based on piezoresistive-piezoelectric coupling effects in porous wood. Carbohydr Polym. 2023;315:120983. doi:10.1016/j.carbpol.2023.120983. [Google Scholar] [PubMed] [CrossRef]
65. Rajala S, Siponkoski T, Sarlin E, Mettänen M, Vuoriluoto M, Pammo A, et al. Cellulose nanofibril film as a piezoelectric sensor material. ACS Appl Mater Interfaces. 2016;8:15607–14. doi:10.1021/acsami.6b03597. [Google Scholar] [PubMed] [CrossRef]
66. Song J, Chen C, Zhu S, Zhu M, Dai J, Ray U, et al. Processing bulk natural wood into a high-performance structural material. Nature. 2018;554:224–8. doi:10.1038/nature25476. [Google Scholar] [PubMed] [CrossRef]
67. Shubnikov AV. Piezoelectric textures. Proc Acad Sci Biol Ser. 1946;84:389–92. [Google Scholar]
68. Bazhenov VA, Konstantinova VP. Piezoelectric properties of wood. Chem Abstr. 1950;44:2747. [Google Scholar]
69. Fukada E, Yasuda S, Kohara J, Okamoto H. The dynamic Young’s modulus and the piezoelectric constant of old timbers. Oyo Butsuri. 1957;26(1):25–8 (In Japanese). [Google Scholar]
70. Galligan WL, Bertholf LD. Piezoelectric effect in wood. For Prod J. 1963;13(12):517–21. [Google Scholar]
71. Fukada E. Piezoelectricity as a fundamental property of wood. Wood Sci Technol. 1968;2:299–307. doi:10.1007/BF00350276. [Google Scholar] [CrossRef]
72. Hirai N, Asano I. Studies on piezoelectric effect of [in] wood. III. Tree growth and variations of piezoelectric modulus. J Jpn Wood Res Soc. 1970;16:310–8. [Google Scholar]
73. Pizzi A, Eaton N. Correlation between the molecular forces in the cellulose I crystal and the piezoelectric effect in wood. Holzforsch Holzverw. 1984;36:12–4. [Google Scholar]
74. Knuffel W, Pizzi A. The piezoelectric effect in structural timber. Holzforschung. 1986;40:157–62. doi:10.1515/hfsg.1986.40.3.157. [Google Scholar] [CrossRef]
75. Knuffel WE. The piezoelectric effect in structural timber—part II. The influence of natural defects. Holzforschung. 1988;42:247–52. [Google Scholar]
76. Nakai T, Takemura T. Piezoelectric behaviors of wood during compression tests. Mokuzai Gakkaishi. 1993;39:265–70. [Google Scholar]
77. Niemz P, Emmler R, Pridöhl E, Fröhlich J, Lühmann A. Comparative studies on the use of acoustic emission and piezoelectric effects during wood drying. Holz als Roh-und Werkstoff. 1994;52(3):162–8. doi:10.1007/BF02615213. [Google Scholar] [CrossRef]
78. Nakai T, Igushi N, Ando K. Piezoelectric behavior of wood under combined compression and vibration stresses I: relation between piezoelectric voltage and microscopic deformation of a Sitka spruce (Picea sitchensis Carr.). J Wood Sci. 1998;44:28–34. [Google Scholar]
79. Nakai T, Hamatake M, Nakao T. Relationship between piezoelectric behavior and the stress—strain curve of wood under combined compression and vibration stresses. J Wood Sci. 2004;50:97–9. doi:10.1007/s10086-003-0590-2. [Google Scholar] [CrossRef]
80. Nakai T, Yamamoto H, Nakao T, Hamatake M. Mechanical behavior of the crystalline region of wood and the piezoelectric response of wood in tension tests. Wood Sci Technol. 2005;39(2):163–8. doi:10.1007/s00226-004-0285-x. [Google Scholar] [CrossRef]
81. Kim HS, Li Y, Kim J. Electro-mechanical behavior and direct piezoelectricity of cellulose electro-active paper. Sens Actuators A Phys. 2008;147:304–9. doi:10.1016/j.sna.2008.05.003. [Google Scholar] [CrossRef]
82. Kim J, Yun S, Ounaies Z. Discovery of cellulose as a smart material. Macromol. 2006;39(12):4202–6. doi:10.1021/ma060261e. [Google Scholar] [CrossRef]
83. Kim HS, Kim JH, Zhao LJ, Jang SD, Yun KY, Lee SK. Piezoelectric effect of electro-active paper materials. Key Eng Mater. 2006;326–328:1507–10. doi:10.4028/www.scientific.net/KEM.326-328.1507. [Google Scholar] [CrossRef]
84. Kim J, Seo YB. Electro-active paper actuators. Smart Mater Struct. 2002;11:305. doi:10.1088/0964-1726/11/3/305. [Google Scholar] [CrossRef]
85. Yang C, Kim J-H, Kim J-H, Kim J, Kim HS. Piezoelectricity of wet drawn cellulose electro-active paper. Sens Actuators A Phys. 2009;154:117–22. doi:10.1016/j.sna.2009.07.016. [Google Scholar] [CrossRef]
86. Hirai N, Sobue N, Date M. New piezoelectric moduli of wood: D31 and D32. J Wood Sci. 2011;57:1–6. doi:10.1007/s10086-010-1133-2. [Google Scholar] [CrossRef]
87. Csoka L, Hoeger IC, Rojas OJ, Peszlen I, Pawlak JJ, Peralta PN. Piezoelectric effect of cellulose nanocrystals thin films. ACS Macro Lett. 2012;1(7):867–70. doi:10.1021/mz300234a. [Google Scholar] [PubMed] [CrossRef]
88. Islam M, Janssen D, Chao D, Gu J, Eisen D, Choa FS. Electricity derived from plants. J Energy Power Eng. 2017;11(9):614–9. doi:10.17265/1934-8975/2017.09.007. [Google Scholar] [CrossRef]
89. Kan J, Ross RJ, Wang X, Li W. Energy harvesting from wood floor vibration using a piezoelectric generator. In: Research note, FPL–RN–0347. Madison, WI: US Department of Agriculture, Forest Service, Forest Products Laboratory; 2017. doi:10.2737/FPL-RN-347. [Google Scholar] [CrossRef]
90. Tuukkanen S, Rajala S. Nanocellulose as a piezoelectric material. In: Piezoelectricity—organic and inorganic materials and applications. London: InTech Open; 2018. doi:10.5772/intechopen.77025. [Google Scholar] [CrossRef]
91. Al-Haik MY, Kabir MM, Siddique W, AlNuaimi S, Aldajah S. An experimental study on piezoelectric energy harvesting from palm tree induced by wind. Eng Res Express. 2020;2(2):025044. doi:10.1088/2631-8695/ab9bf1. [Google Scholar] [CrossRef]
92. Sultana A, Alam MM, Pavlopoulou E, Solano E, Berggren M, Crispin X, et al. Toward high-performance green piezoelectric generators based on electrochemically poled nanocellulose. Chem Mater. 2023;35:1568–78. doi:10.1021/acs.chemmater.2c03020. [Google Scholar] [CrossRef]
93. Zhu H, Han Z, Cheng J-H. Da-Wen Sun Modification of cellulose from sugarcane (Saccharum officinarum) bagasse pulp by cold plasma: dissolution, structure and surface chemistry analysis. Food Chem. 2022;374:131675. [Google Scholar] [PubMed]
94. Gopakumar DA, Thomas S, Owolabi FAT, Thomas S, Nzihou A, Rizal S, et al. Nanocellulose based aerogels for varying engineering applications. In: Encyclopedia of renewable and sustainable materials. Elsevier; 2020. vol. 2, p. 155–65. doi:10.1016/B978-0-12-803581-8.10549-1. [Google Scholar] [CrossRef]
95. Yang L, Ma Z, Tian Y, Meng B, Peng Z. Progress on self-powered wearable and implantable systems driven by nanogenerators. Micromachines. 2021;12:666. doi:10.3390/mi12060666. [Google Scholar] [PubMed] [CrossRef]
96. Jiang B, Li M, Cao S, Wang Z, Huang L, Song X, et al. Anisotropic wooden electromechanical transduction devices enhanced by TEMPO oxidization and PDMS. ACS Omega. 2023;8:3945–55. doi:10.1021/acsomega.2c06607. [Google Scholar] [PubMed] [CrossRef]
97. Sun J, Guo H, Ribera J, Wu C, Tu K, Binelli M, et al. Sustainable and biodegradable wood sponge piezoelectric nanogenerator for sensing and energy harvesting applications. ACS Nano. 2020;14(11):14665–74. doi:10.1021/acsnano.0c05493. [Google Scholar] [PubMed] [CrossRef]
98. Sheng H, Zhang X, Liang J, Shao M, Xie E, Yue C, et al. Recent advances of energy solutions for implantable bioelectronics. Adv Healthc Mater. 2021;10(17):2100199. doi:10.1002/adhm.202100199. [Google Scholar] [PubMed] [CrossRef]
99. Chen Q, van Dijken J, Maniar D, Loos K. Aerenchyma tissue of Juncus effusus L.: a novel resource for sustainable natural cellulose foams. Cellulose. 2023;30:9647–67. doi:10.1007/s10570-023-05453-9. [Google Scholar] [CrossRef]
100. Song Y, Shi Z, Hu GH, Xiong C, Isogai A, Yang Q. Recent advances in cellulose-based piezoelectric and triboelectric nanogenerators for energy harvesting: a review. J Mater Chem A. 2021;9:1910–37. doi:10.1039/D0TA08642H. [Google Scholar] [CrossRef]
101. Guan H, Meng J, Cheng Z, Wang X. Processing natural wood into a high-performance flexible pressure sensor. ACS Appl Mater Interfaces. 2020;12:46357–65. doi:10.1021/acsami.0c12561. [Google Scholar] [PubMed] [CrossRef]
102. Sun J, Guo H, Schädli GN, Tu K, Schär S, Schwarze FW, et al. Enhanced mechanical energy conversion with selectively decayed wood. Sci Adv. 2021;7(11). doi:10.1126/sciadv.abd9138. [Google Scholar] [PubMed] [CrossRef]
103. Rajeshkumar L, Kumar PS, Ramesh M, Sanjay MR, Siengchin S. Assessment of biodegradation of lignocellulosic fiber-based composites—a systematic review. Int J Biol Macromol. 2023;253:127237. doi:10.1016/j.ijbiomac.2023.127237. [Google Scholar] [PubMed] [CrossRef]
104. Holy S, Temiz A, Köse Demirel G, Aslan M, Mohamad Amini MH. Physical properties, thermal and fungal resistance of Scots pine wood treated with nano-clay and several metal-oxides nanoparticles. Wood Mater Sci Eng. 2022;17:176–85. doi:10.1080/17480272.2020.1836023. [Google Scholar] [CrossRef]
105. Weththimuni ML, Capsoni D, Malagodi M, Licchelli M. Improving wood resistance to decay by nanostructured ZnO-based treatments. J Nanomater. 2019;2019:1–11. doi:10.1155/2019/6715756. [Google Scholar] [CrossRef]
106. Wang Y, Zhang Z, Fan H, Wang J. Wood carbonization as a protective treatment on resistance to wood destroying fungi. Int Biodeter Biodegr. 2018;129:42–9. doi:10.1016/j.ibiod.2018.01.003. [Google Scholar] [CrossRef]
107. Tomak ED, Can A, Ermeydan MA. Biodegradability of poly (Ɛ-Caprolactone) modified wood by decaying fungi. J Polym Environ. 2023;31:4097–111. doi:10.1007/s10924-023-02839-5. [Google Scholar] [CrossRef]
108. Miao C, Reid L, Hamad WY. Moisture-tunable, ionic strength-controlled piezoelectric effect in cellulose nanocrystal films. Appl Mater Today. 2021;24:101082. doi:10.1016/j.apmt.2021.101082. [Google Scholar] [CrossRef]
109. Yang C, Song S, Chen F, Chen N. Fabrication of PVDF/BaTiO3/CNT piezoelectric energy harvesters with bionic balsa wood structures through 3D printing and supercritical carbon dioxide foaming. ACS Appl Mater Interfaces. 2021;13:41723–34. doi:10.1021/acsami.1c11843. [Google Scholar] [PubMed] [CrossRef]
110. Chae I, Bokhari SMQ, Chen X, Zu R, Liu K, Borhan A, et al. Shear-induced unidirectional deposition of bacterial cellulose microfibrils using rising bubble stream cultivation. Carbohydr Polym. 2021;255:117328. doi:10.1016/j.carbpol.2020.117328. [Google Scholar] [PubMed] [CrossRef]
111. Yun GY, Kim HS, Kim J, Kim K, Yang C. Effect of aligned cellulose film to the performance of electro-active paper actuator. Sens Actuat A Phys. 2008;141:530–5. doi:10.1016/j.sna.2007.10.014. [Google Scholar] [CrossRef]
112. Ram F, Garemark J, Li Y, Berglund L. Scalable, efficient piezoelectric wood nanogenerators enabled by wood/ZnO nanocomposites. Compos Part A Appl Sci Manuf. 2022;160:107057. doi:10.1016/j.compositesa.2022.107057. [Google Scholar] [CrossRef]
113. Gao Y, Ram F, Chen B, Garemark J, Berglund L, Dai H, et al. Scalable hierarchical wood/ZnO nanohybrids for efficient mechanical energy conversion. Mater Des. 2023;226:111665. doi:10.1016/j.matdes.2023.111665. [Google Scholar] [CrossRef]
114. Li S, He Y, Ye X, Fu X, Hou Y, Tian H, et al. Improved piezoelectricity of porous cellulose material via flexible polarization-initiate bridge for self-powered sensor. Carbohydr Polym. 2022;298:120099. doi:10.1016/j.carbpol.2022.120099. [Google Scholar] [PubMed] [CrossRef]
115. Go JCT, Remolino AKA, Sanchez JMP, Paz KE. Harvesting energy through piezoelectric tiles: a comparative study of wood, porcelain, and ceramic tiles. Educ J Sci Math Technol. 2023;10:1–6. doi:10.37134/ejsmt.vol10.1.1.2023. [Google Scholar] [CrossRef]
116. Tang M, Liu X, Ren X, Ren X, Wang Y, Wu Y, et al. Electromechanical properties of [0 0 1]-textured Mn-PMN–PZT ceramics under uniaxial pressure. J Am Ceram Soc. 2024;107:2272–81. doi:10.1111/jace.19544. [Google Scholar] [CrossRef]
117. Voignac D, Belsey S, Wermter E, Paltiel Y, Shoseyov O. Biobased electronics: tunable Dielectric and piezoelectric cellulose nanocrystal—protein films. Nanomater. 2023;13:2258. doi:10.3390/nano13152258. [Google Scholar] [PubMed] [CrossRef]
118. Maity K, Mondal A, Saha MC. Cellulose nanocrystal-based All-3D-printed pyro-piezoelectric nanogenerator for hybrid energy harvesting and self-powered cardiorespiratory monitoring toward the human-machine interface. ACS Appl Mater Interfaces. 2023 Mar 10;15(11):13956–70. doi:10.1021/acsami.2c21680. [Google Scholar] [PubMed] [CrossRef]
119. Wu T, Lu Y, Tao X, Chen P, Zhang Y, Ren B, et al. Superelastic wood-based nanogenerators magnifying the piezoelectric effect for sustainable energy conversion. Carbon Energy. 2024 May 29. doi:10.1002/cey2.561. [Google Scholar] [CrossRef]
120. Belashev B. Monitoring the electrical potential difference of pine tree. BIO Web Conf. 2024;93:01015. doi:10.1051/bioconf/20249301015. [Google Scholar] [CrossRef]
121. Koppán A, Fenyvesi A, Szarka L, Wesztergom V. Measurement of electric potential difference on trees. Acta Biol Szeged. 2002;46(3–4):37–8. [Google Scholar]
122. Koppán A, Szarka L, Wesztergom V. Local variability of electric potential differences on the trunk of Quercus cerris L. Acta Silv Lign Hung. 2005;1:73–81. doi:10.37045/aslh-2005-0006. [Google Scholar] [CrossRef]
123. Calnan C. Plugged in: startup hopes to tap electricity from trees. Mass High Tech: J. New England Technol. 2006. Available from: https://www.bizjournals.com/boston/blog/mass-high-tech/2006/01/plugged-in-startup-hopes-to-tap-electricity.html. [Accessed 2024]. [Google Scholar]
124. Gibert D, Le Mouël JL, Lambs L, Nicollin F, Perrier F. Sap flow and daily electric potential variations in a tree trunk. Plant Sci. 2006;171(5):572–84. doi:10.1016/j.plantsci.2006.06.012. [Google Scholar] [CrossRef]
125. Le Mouël JL, Gibert D, Poirier JP. On transient electric potential variations in a standing tree and atmospheric electricity. CR Geosci. 2010;342(2):95–9. doi:10.1016/j.crte.2009.12.001. [Google Scholar] [CrossRef]
126. Himes C, Carlson E, Ricchiuti RJ, Otis BP, Parviz BA. Ultralow voltage nanoelectronics powered directly, and solely, from a tree. IEEE Trans Nanotechnol. 2009;9(1):2–5. doi:10.1109/TNANO.2009.2032293. [Google Scholar] [CrossRef]
127. Himes C, Carlson E, Ricchiuti RJ, Taylor DW, Otis B, Parviz BA. Using plants for directly powering nanoelectronic circuits. Nanotechnol Percept. 2010;6:29–40. doi:10.4024/N01HI10A.ntp.06.01. [Google Scholar] [CrossRef]
128. McGarry S, Knight C. The potential for harvesting energy from the movement of trees. Sensors. 2011;11:9275–99. doi:10.3390/s111009275. [Google Scholar] [PubMed] [CrossRef]
129. Hao Z, Li W, Kan J, Jiang L, Feng C. Bioelectricity in standing trees-a potential energy for wireless sensor networks. TELKOMNIKA Indonesian J Electr Eng. 2013;11(8):4841–6. doi:10.11591/telkomnika.v11i8.3148. [Google Scholar] [CrossRef]
130. Ying Q, Yuan W, Hu N. Improving the efficiency of harvesting electricity from living trees. J Renew Sustain Energy. 2015;7(6):063108. doi:10.1063/1.4935577. [Google Scholar] [CrossRef]
131. Hao Z, Wang G, Li W, Zhang J, Kan J. Effects of electrode material on the voltage of a tree-based energy generator. PLoS One. 2015;10(8). doi:10.1371/journal.pone.0136639. [Google Scholar] [PubMed] [CrossRef]
132. Hao Z, Liu K, Li W, Zhang J, Kan J, Hao X. Effects of electrode size on the voltage of a tree-based energy generator. J Renew Sustain Energy. 2018;10(4):043101. doi:10.1063/1.5032190. [Google Scholar] [CrossRef]
133. Helder M, Strik DP, Timmers RA, Raes SM, Hamelers HV, Buisman CJ. Resilience of roof-top plant-microbial fuel cells during Dutch winter. Biomass Bioenergy. 2013(a);51:1–7. doi:10.1016/j.biombioe.2012.10.011. [Google Scholar] [CrossRef]
134. Helder M, Chen WS, Van Der Harst EJ, Strik DP, Hamelers HBV, Buisman CJ, et al. Electricity production with living plants on a green roof: environmental performance of the plant-microbial fuel cell. Biofuels, Bioprod Biorefin. 2013b;7(1):52–64. doi:10.1002/bbb.1373. [Google Scholar] [CrossRef]
135. Mussinelli E, Tartaglia A, Castaldo G, Cerati D. Project and evaluation of nature-based solutions for the regeneration of public space. In: Int symp: new metropolitan perspect. Cham: Springer; 2020. p. 1342–51. doi:10.1007/978-3-030-48279-4_125 [Google Scholar] [CrossRef]
136. Boeri S, Pastore MC, Shamir L. Planning and designing NBS toward new coexistence models. In: Nature-based solutions for more sustainable cities—a framework approach for planning and evaluation. Bingley: Emerald Publishing Limited; 2021. p. 87–96. doi:10.1108/978-1-80043-636-720211007. [Google Scholar] [CrossRef]
137. Dezeen. Forestami project. Available from: https://www.dezeen.com/2021/09/24/forestami-project-trees-planted-milan/. [Accessed 2024]. [Google Scholar]
138. Architecture Interior. Bosco verticale, one of Milan’s award-winning landmarks. Available from: https://iklimepolat.com/milanonun-odullu-simge-yapilarindan-bosco-verticale-dikey-orman/. [Accessed 2022]. [Google Scholar]
139. ArchDaily. Bosco verticale, photos of the first vertical forest towers. 2024. Available from: https://www.archdaily.com/777498/bosco-verticale-stefano-boeri-architetti. [Accessed 2024]. [Google Scholar]
140. Dezeen. Bosco verticale, photos of the first vertical forest towers. Available from: https://www.dezeen.com/2022/01/26/stefano-boeri-vertical-forest-skyscraper-china/. [Accessed 2022] [Google Scholar]
Cite This Article
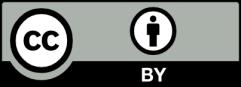
This work is licensed under a Creative Commons Attribution 4.0 International License , which permits unrestricted use, distribution, and reproduction in any medium, provided the original work is properly cited.