Open Access
PERSPECTIVE
The Future of Plasticizers: Biobased and Oligomeric
Center for Applications in Polymer Science, Department of Chemistry and Biochemistry, Central Michigan University, Mt. Pleasant, MI 48859-0001, USA
* Corresponding Author: Bob A. Howell. Email:
(This article belongs to the Special Issue: Renewable Materials and Advanced Technologies for Sustainability)
Journal of Renewable Materials 2024, 12(11), 1857-1861. https://doi.org/10.32604/jrm.2024.056283
Received 18 July 2024; Accepted 09 September 2024; Issue published 22 November 2024
Abstract
The deficiencies of popular phthalate plasticizers (ready migration from a polymer matrix into which they have been incorporated, flammability, environmental pollution, human health risks) have stimulated efforts to develop new effective, nonmigrating, low-cost, nontoxic replacements. In the main, these have been based on readily-available, nontoxic biobased precursors. Some, including those prepared from plant oils, have been generated from biomaterials themselves. However, the more numerous and generally more effective have been generated from discrete compounds produced from various biomaterials. Several structural features of effective plasticizers have been recognized. Polar functionality is required to assure compatibility with a wide range of polymeric materials, including poly(vinyl chloride) (PVC), the most heavily plasticized polymer. A branched structure greatly enhances the effectiveness of compounds used as plasticizers. An oligomeric structure may strongly limit or prevent migration from a polymer matrix. Hyperbranched oligomers of defined structure derived from the readily-available, inexpensive, nontoxic biomonomers, glycerol and adipic acid contain all these features and are excellent plasticizers. They contain ester functionality, are highly branched, and display a large number of end groups, all of which contribute to their effectiveness as plasticizers.Keywords
Plasticizers play an important role in polymer processing. This is particularly true for PVC, which may require 40%–60% plasticizer by weight for processing and use [1]. PVC is a polar polymer and, in the absence of plasticization, is a rigid, brittle material [2]. Traditionally, phthalate esters, most prominently, di(2-ethylhexyl) phthalate [DEHP], have been used as plasticizers. DEHP is produced from two inexpensive precursors, phthalic acid and 2-ethylhexanol. Phthalic acid is obtained from the oxidation of o-xylene, the least useful of the mixed xylenes from the reforming of naphtha [3]. The alcohol, 2-ethylhexanol, is obtained from the hydrogenation of the aldol adduct from butraldehyde, which is a byproduct of the hydroformulation of propylene [3]. Further, DEHP is effective in affording plasticization and workability to a polymer matrix into which it is incorporated. Consequently, it has become the most widely used plasticizer for polymeric materials. Unfortunately, human exposure to DEHP and other phthalates can lead to the development of a wide variety of disease states, most arising from endocrine disruption, but including cardiovascular and respiratory disorders [4]. This has led to the prohibition of the use of phthalate plasticizers in certain key applications [5,6]. The negative properties of phthalate ester plasticizers have stimulated a massive interest in the development of new, effective, nonmigrating, nontoxic and cost-effective plasticizers.
The response to the need for non-phthalate plasticizers that are effective, nonmigrating and nontoxic has focused on the development of plasticizing compounds derived from biomaterials or biobased materials [7–9]. Most often, these have been designed for use in PVC [10–12]. Because of wide availability, lack of toxicity and low cost, crop plant oils have been attractive precursors to new plasticizers [13,14]. Nonedible oils have also been used as plasticizer precursors [15]. A potential drawback to the use of oil-based plasticizers is the somewhat limited compatibility with many polymers. To overcome this, polar functionality has often been introduced into the structure [16,17]. A great variety of other biobased precursors have been used for the generation of plasticizers [18]. Prominently among these have been cardanol [19–21] (a byproduct of cashew nut processing), tartaric acid [22–25] (a byproduct of winemaking) and derivatives of starch, isosorbide [26,27] and the furanics [28–32]. Branching in plasticizer structure is effective for promoting free volume effects in a polymer matrix [33–35]. Branching is most prominent in hyperbranched oligomers, and several have been prepared to function as effective, nonmigrating plasticizers, primarily for PVC [36–38].
Glycerol is a nontoxic, trifunctional biomonomer readily available from biodiesel production and soap making [39]. It represents a valuable starting point for the synthesis of hyperbranched oligomeric plasticizers. Because of the difficulties associated with direct polyesterification of glycerol, materials have often been produced from glycidol [40–42]. Direct polyesterification of glycerol generally leads to a highly crosslinked gelled product. This is useful for the generation of coatings but hampers the generation of discrete, stable oligomers suitable for further transformations. Traditionally, empirical approaches, generally a reaction to low monomer conversion, have been utilized in an attempt to avoid gelation [43,44]. This poses two problems. The desired product must be isolated from a large amount of unchanged reactants. More importantly, the materials generated contain two kinds of end groups, hydroxyl and carboxyl, and will gel on storage. Fortunately, newly developed technology, the Martin-Smith approach for determining initial monomer ratios, permits reaction to high monomer conversion without gelation to produce structures of any desired molecular weight with a single kind of end group, either hydroxyl or carboxyl [45,46]. These materials may be produced in the presence of acidic or enzymatic catalysts or in the absence of catalyst using standard methodology, essentially at one-pot synthesis. The ability to tailor the molecular weight and to control end group identity provides great flexibility for the design of plasticizers for a broad range of polymers. For example, capping the hydroxyl end groups of glycerol/adipic acid hyperbranched oligomer of 1300 molecular weight as esters of varied structure affords excellent, nontoxic, nonmigrating plasticizers for PVC [47–49]. These oligomers prominently contain ester functionality, a high degree of branching, and a large number of end groups. All these features facilitate effective plasticization.
Plasticizers of the future need to be effective, available via a noncomplex process, relatively inexpensive, nonmigrating, and most importantly, non-toxic. Oligomeric materials of optimum molecular weight and structure offer the potential to avoid problems associated with plasticizer migration. Structural branching strongly facilitates plasticization effectiveness. Plasticizer toxicity may be controlled through the use of abundantly available, renewable, biobased precursors for their generation. Most prominently, hyperbranched oligomeric esters derived from the readily available, renewable, nontoxic biomonomers, glycerol and adipic acid, are excellent nonmigrating plasticizers. These materials may be produced in a simple process. Using recently developed technology, these oligomeric plasticizers may be produced in any desired molecular weight without gelation to afford materials of precise structure and a single kind of end group. This greatly facilitates the development of nontoxic, nonmigrating plasticizers for wide use.
To meet the demands of concerns about environmental contamination, sustainability, governmental regulation and human toxicity, plasticizers of the future will need to be biobased and oligomeric.
Acknowledgement: None.
Funding Statement: The author received no specific funding for this study.
Availability of Data and Materials: Not applicable.
Ethics Approval: Not applicable.
Conflicts of Interest: The author declares that they have no conflicts of interest to report regarding the present study.
References
1. Elgharbawy AS. Poly(vinyl chloride) additives and applications—a review. J Risk Anal Crisis Resp. 2022;12:143–51. [Google Scholar]
2. Sarvetnick HA. Poly(vinyl chloride). New York, USA: Van Nostrand Reinhold; 1969. [Google Scholar]
3. Wittcoff HA, Reuben BG, Plotkin JS. Industrial organic chemicals. 3rded. USA: John Wiley & Sons; 2012. [Google Scholar]
4. Eales J, Bethel A, Galloway T, Hopkinson P, Morrissey K, Short RE, et al. Human health impacts of exposure to phthalate plasticizers: an overview of reviews. Environ Int. 2022;258:106903. [Google Scholar]
5. Tickner JA, Schetler T, Guidotti T, McCally M, Rossi M. Health risks posed by use of Di(2-ethylhexyl) phthalate (DEHP) in PVC medical devices: a critical review. Am J Int Med. 2001;38:100–11. [Google Scholar]
6. Kim KY, Chun S, Mohamed FMS, Kim H, Keng D, An J, et al. Phthalate plasticizers in children’s products and estimation of exposure: importance of migration rate. Ind J Environ Res Public Health. 2020;17:8583. [Google Scholar]
7. Jia P, Xia H, Tang K, Zhou Y. Plasticizers derived from biomass resources: a short review. Polymers. 2018;10:1303. doi:10.3390/polym10121303. [Google Scholar] [PubMed] [CrossRef]
8. Kumar S. Recent developments of biobased plasticizers and their effect on mechanical and thermal properties of Poly(vinyl chloridea review. Ind Eng Chem Res. 2019;58:11659–11672. doi:10.1021/acs.iecr.9b02080. [Google Scholar] [CrossRef]
9. Harmon JP, Otter R. Green chemistry and the search for new plasticizers. ACS Sustain Chem. 2018;6:2078–85. doi:10.1021/acssuschemeng.7b03508. [Google Scholar] [CrossRef]
10. Zhang Z, Jiang P-P, Liu D, Feng S, Zhong P, Wang Y, et al. Research progress of novel biobased plasticizers and their applications in poly(vinyl chloride). J Mater Sci. 2021;56:10155–10182. doi:10.1007/s10853-021-05934-x. [Google Scholar] [CrossRef]
11. Lu M, Jiang P, Zhong P, Feng S, Cui Z, Song Q, et al. A highly stable biobased plasticizer constructed from renewable acids for plasticizing and enhancing the optical properties of poly(vinyl chloride). New J Chem. 2023;47:1784. doi:10.1039/D2NJ04972D. [Google Scholar] [CrossRef]
12. Han Y, Weng Y, Zhang C. Development of biobased plasticizers with synergistic effects of plasticization, thermal stabilization, and migration resistance: a review. J Vinyl Addit Technol. 2024;30:26–43. doi:10.1002/vnl.v30.1. [Google Scholar] [CrossRef]
13. Burns K, Ingram IDV, Potgieter JH, Potgieter-Vermaak S. Synthesis and performance evaluation of novel soybean oil-based plasticizers for polyvinyl chloride (PVC). J Appl Polym Sci. 2023;140(45):e54656. doi:10.1002/app.v140.45. [Google Scholar] [CrossRef]
14. Waskiewicz S, Longer E, Tannenberg M, Dziendziol P, Jurczyk S. Synthesis and study of properties of new oligoesters based on soybean oil as potential poly(vinyl chloride) plasticizers. J Appl Polym Sci. 2024;141:e54865. doi:10.1002/app.v141.4. [Google Scholar] [CrossRef]
15. Ma Y, Song F, Kong Q, Li Q, Jia P, Zhou Y. Preparation and performance of biobased polyol ester from one-pot synthesis of caster oil as nontoxic poly(vinyl chloride) plasticizer. J Polym Environ. 2020;28:2101–7. doi:10.1007/s10924-020-01754-3. [Google Scholar] [CrossRef]
16. Zhu H, Yang J, Wu M, Wu Q, Liu J, Zhang J. Effect of ketal group in castor oil acid-based plasticizer on the properties of poly(vinyl chloride). J Appl Polym Sci. 2021;138(43):51274. [Google Scholar]
17. Tan J, Liu B, Fu Q, Wang L, Zhu X. Role of the oxethyl unit in the structure of a vegetable oil-based plasticizer for PVC: an efficiency strategy to enhance compatibility and plasticization. Polymers. 2019;11:779. doi:10.3390/polym11050779. [Google Scholar] [PubMed] [CrossRef]
18. Ledniowsk K, Janik W, Nosal-Kovalenko H, Sabura E, Basiak E, Jaszkiewicez A, et al. Epoxidized esters of succinic acid, oleic acid and propylene glycol as an effective bioplasticizer for PVC: a study of processing conditions on the physico-chemical properties. J Appl Polym Sci. 2024;141:e55218. doi:10.1002/app.v141.15. [Google Scholar] [CrossRef]
19. Lee S, Park MS, Shin S, Kim KW. Effect of the individual and combined use of cardanol-based plasticizers and epoxidized soybean oil on the properties of PVC. Polym Degrad Stab. 2018;147:1–11. doi:10.1016/j.polymdegradstab.2017.11.002. [Google Scholar] [CrossRef]
20. Chen J, Liu Z, Jiang J, Nie X, Zhou Y, Murray RE. A novel biobased plasticizer of epoxidized cardanol glycidyl ether: synthesis and application in soft poly(vinyl chloride) films. RSC Adv. 2015;5:56171. doi:10.1039/C5RA07096A. [Google Scholar] [CrossRef]
21. Greco A, Ferrari F, Del Sole R, Maffezzoli A. Use of cardanol derivatives as plasticizers for PVC. J Vinyl Addit Technol. 2018;24:E62–70. [Google Scholar]
22. Howell BA, Sun W. Biobased plasticizers from tartaric acid, an abundantly available, renewable material. Ind Eng Chem Res. 2018;57:15234–42. [Google Scholar]
23. Zhu H, Yang J, Wu M, Wu Q, Liu J, Zhong J. Biobased plasticizers from tartaric acid: synthesis and effect of alkyl chain length on the properties of poly(vinyl chloride). ACS Omega. 2021;6(20):13161–9. doi:10.1021/acsomega.1c01006. [Google Scholar] [PubMed] [CrossRef]
24. Zawada K, Plichta A, Janezewski D, Hajmowicz H, Florjanezyk Z, Stepien M, et al. A new class of ‘double green’ plasticizers. ACS Sustain Chem Eng. 2017;5:5999–6008. doi:10.1021/acssuschemeng.7b00814. [Google Scholar] [CrossRef]
25. Dong X, Long M, Cai Y, Zhou Z, Xia X. Novel biologically derived tartaric acid plasticizer: synthesis and application. J Appl Polym Sci. 2023;140(47):e54707. [Google Scholar]
26. Yang Y, Xiong Z, Zhang L, Tang Z, Zhang R, Zhu J. Isosorbide dioctoate as a ‘green’ plasticizer for poly(lactic acid). Mater Design. 2016;91:262–8. doi:10.1016/j.matdes.2015.11.065. [Google Scholar] [CrossRef]
27. Yin B, Hakkarainen M. Oligomeric isosorbide esters as alternative renewable resource plasticizers for PVC. J Appl Polym Sci. 2011;119:2400–7. doi:10.1002/app.v119:4. [Google Scholar] [CrossRef]
28. Howell BA, Lazar ST. Biobased plasticizers from carbohydrate-derived 2,5-bis(Hydroxymethyl)furan. Ind Eng Chem Res. 2018;27:1294–1301. [Google Scholar]
29. Howell BA, Lazar ST. Green plasticizers for PVC. Advances in Engineering. 2019. Available from: http://advanceseng.com/green-plasticizers-pvc/. [Accessed 2024]. [Google Scholar]
30. Matos M, Cordeiro RA, Faneca H, Coelho JFJ, Silvestre AJD, Sousa AF. Replacing Di(2-ethylhexyl) Terephthalate by Di(2-ethylhexyl) 2,5-Furandicarboxylate for PVC plasticization: synthesis, materials preparation and characterization. Materials. 2019;12:2336. doi:10.3390/ma12142336. [Google Scholar] [PubMed] [CrossRef]
31. Hao Y, Tian A, Zhu J, Fan J, Yang Y. Synthesis and evaluation of biobased plasticizers from 5-Hydroxymethyl-2-furancarboxylic acid for poly(vinyl chloride). Ind Eng Chem Res. 2020;59:18290–7. doi:10.1021/acs.iecr.0c03356. [Google Scholar] [CrossRef]
32. Nguyen T, Kim YJ, Park S-K, Lee K-Y, Park J-W, Cho JK, et al. Furan-2,5- and Furan-2,3,-dicarboxylate esters derived from marine biomass as plasticizers for poly(vinyl chloride). ACS Omega. 2020;5:197–206. doi:10.1021/acsomega.9b02448. [Google Scholar] [PubMed] [CrossRef]
33. Qian B, Zhang J, Wu M, Liu J, Wu Q. Characterization and performance evaluation of ‘crab’ biobased poly(vinyl chloride) plasticizer based on sustainable lactic acid. Polymer. 2023;283:34126246. [Google Scholar]
34. Huang Y, Yu E, Li Y, Wei Z. Novel branched poly(ε-caprolactone) as a nonmigrating plasticizer in flexible PVC: synthesis and characterization. J Appl Polym Sci. 2018;135(32):46542. [Google Scholar]
35. Choi W, Chung JW, Kwak SY. Unentangled star-shape poly(ε-caprolactone)s as phthalate-free PVC plasticizers designed for nontoxicity and improved migration resistance. ACS Appl Mater Interface. 2014;6:11118–11128. doi:10.1021/am500740v. [Google Scholar] [PubMed] [CrossRef]
36. Chen J, Nie X, Jiang J. Synthesis of a novel bio-oil-based hyperbranched ester plasticizer and its effects on poly(vinyl chloride) soft films. ACS Omega. 2020;5:5480–6. doi:10.1021/acsomega.0c00119. [Google Scholar] [PubMed] [CrossRef]
37. Bei Y, Hu Y, Jia P, Ma Y, Hu F, Xiao T, et al. Biobased hyperbranched ester plasticizers from woody oil based on cohesive energy via a one-pot synthesis reaction. J Polym Environ. 2024;32:1028–38. doi:10.1007/s10924-023-03023-5. [Google Scholar] [CrossRef]
38. Tong H, Hai J. Sustainable synthesis of a biobased hyperbranched ester and its application for preparing soft polyvinyl chloride materials. Polym Ind. 2019;456–63. [Google Scholar]
39. Tan HW, Abdual Aziz AR, Aroua MK. Glycerol production and its applications as a raw material. Renew Sustain Energy Rev. 2013;27:118–27. doi:10.1016/j.rser.2013.06.035. [Google Scholar] [CrossRef]
40. Ciriminna R, Katynick B, Paul S, Dumeignil F, Pagliaro M. Glycerol-derived renewable polyglycerols: a class of versatile chemicals of wide potential application. Org Process Res Dev. 2015;19:748–54. doi:10.1021/op500313x. [Google Scholar] [CrossRef]
41. Lee KW, Chung JW, Kwak S-Y. Synthesis and characterization of biobased alkyl terminal hyperbranched polyglycerols: a Detailed study of their plasticization effect and migration resistance. Green Chem. 2016;18:999–1009. doi:10.1039/C5GC02402A. [Google Scholar] [CrossRef]
42. Lee KW, Chung JW, Kwak S-Y. Highly branched polycaprolactone/glycidol copolymeric green plasticizer by one-pot solvent-free polymerization. ACS Sustain Chem Eng. 2018;6:9006–17. doi:10.1021/acssuschemeng.8b01356. [Google Scholar] [CrossRef]
43. Stumbe J-F, Bruckmann B. Hyperbranched polyesters based on adipic acid and glycerol. Macrol Rapid Commun. 2004;25:921–4. doi:10.1002/marc.v25:9. [Google Scholar] [CrossRef]
44. Valerio O, Misra M, Mohanty AK. Poly(glycerol-co-diacids) polyesters: from glycerol biorefinery to sustainable engineering applications, a review. ACS Sustain Chem Eng. 2018;6:5681–93. doi:10.1021/acssuschemeng.7b04837. [Google Scholar] [CrossRef]
45. Zhang T, Howell BA, Smith PB. Rational synthesis of hyperbranched poly(ester)s. Ind Eng Chem Res. 2017;56:1661–70. doi:10.1021/acs.iecr.6b04435. [Google Scholar] [CrossRef]
46. Zhang T, Howell BA, Dumitrascu A, Martin SJ, Smith PB. Synthesis and characterization of glycerol-adipic acid hyperbranched poly(ester)s. Polymer. 2014;55:5065–72. doi:10.1016/j.polymer.2014.08.036. [Google Scholar] [CrossRef]
47. Howell BA, Lazar ST. Biobased plasticizers from glycerol/adipic acid hyperbranched poly(ester)s. Ind Eng Chem Res. 2019;58:17227–34. doi:10.1021/acs.iecr.9b03869. [Google Scholar] [CrossRef]
48. Howell BA, Lazar ST. Biobased Glycerol hyperbranched poly(ester)s of precise structure as plasticizers for poly(vinyl chloride). Modern Concepts Mat Sci. 2021;4(2). doi:10.33552/MCMS.2021.04.000587. [Google Scholar] [CrossRef]
49. Howell BA. Very effective, nontoxic, inexpensive, nonmigrating biobased oligoeric hyperbranched plasticizers for poly(vinyl chloride) from the biomonomers, glycerol and adipic acid. In: Cheng HN, Gross RA, editors. Sustainable green chemistry in polymer research. Volume 1. Biocatalysis and biobased materials. Washington, DC, USA: American Chemical Society; 2023, p. 237–47. doi:10.1021/symposium. [Google Scholar] [CrossRef]
Cite This Article
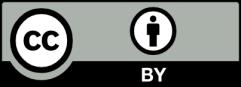
This work is licensed under a Creative Commons Attribution 4.0 International License , which permits unrestricted use, distribution, and reproduction in any medium, provided the original work is properly cited.