Open Access
REVIEW
Research Progress of Biomass-Based Porous Oil-Absorbing Materials
1 School of Chemistry and Chemical Engineering, Yancheng Institute of Technology, Yancheng, 224051, China
2 Jiangsu Co-Innovation Center of Efficient Processing and Utilization of Forest Resources, College of Chemical Engineering, Nanjing Forestry University, Nanjing, 210037, China
3 Department of Technology, Yancheng Tongwei Solar Energy Co., Ltd., Yancheng, 224000, China
* Corresponding Author: Xujuan Huang. Email:
Journal of Renewable Materials 2024, 12(11), 1837-1856. https://doi.org/10.32604/jrm.2024.055933
Received 10 July 2024; Accepted 14 October 2024; Issue published 22 November 2024
Abstract
As oil is now an important resource for the survival and development of mankind, the consumption of oil continues to increase each year, and there have been a number of major oil spills in history, such as the oil spill from the Deepwater Horizon drilling rig. Therefore, oil spills during storage and transportation have become an issue of serious concern. Current methods such as incineration and chemical methods cause secondary environmental pollution and fail to enable resource recovery. The adsorption method by porous materials has attracted worldwide attention due to its simplicity, portability, and efficiency. It has become an important factor to explore how porous adsorption materials can adsorb efficiently and reduce environmental pollution. Biomass resources are abundant, cost-effective, biodegradable, and sustainable, which have been extensively explored for the production of porous materials. Herein, recent advances in cellulose-based, chitosan-based, wood-based and other biomass-based oil-absorbing porous materials are summarized, and cellulose-based porous materials, such as nanocellulose, bacterial cellulose, and regenerated cellulose and their related derivatives, are further expanded. In addition, typical environmentally friendly manufacturing methods and the oil adsorption capacities of various oil-absorbing porous materials are also discussed. Compared with the traditional petrochemical adsorption materials, the development advantages of biomass porous oil absorption materials are analyzed. The reasons hindering the popularization and use of oil-absorbing biomass materials are summarized and the future application fields are prospected.Graphic Abstract
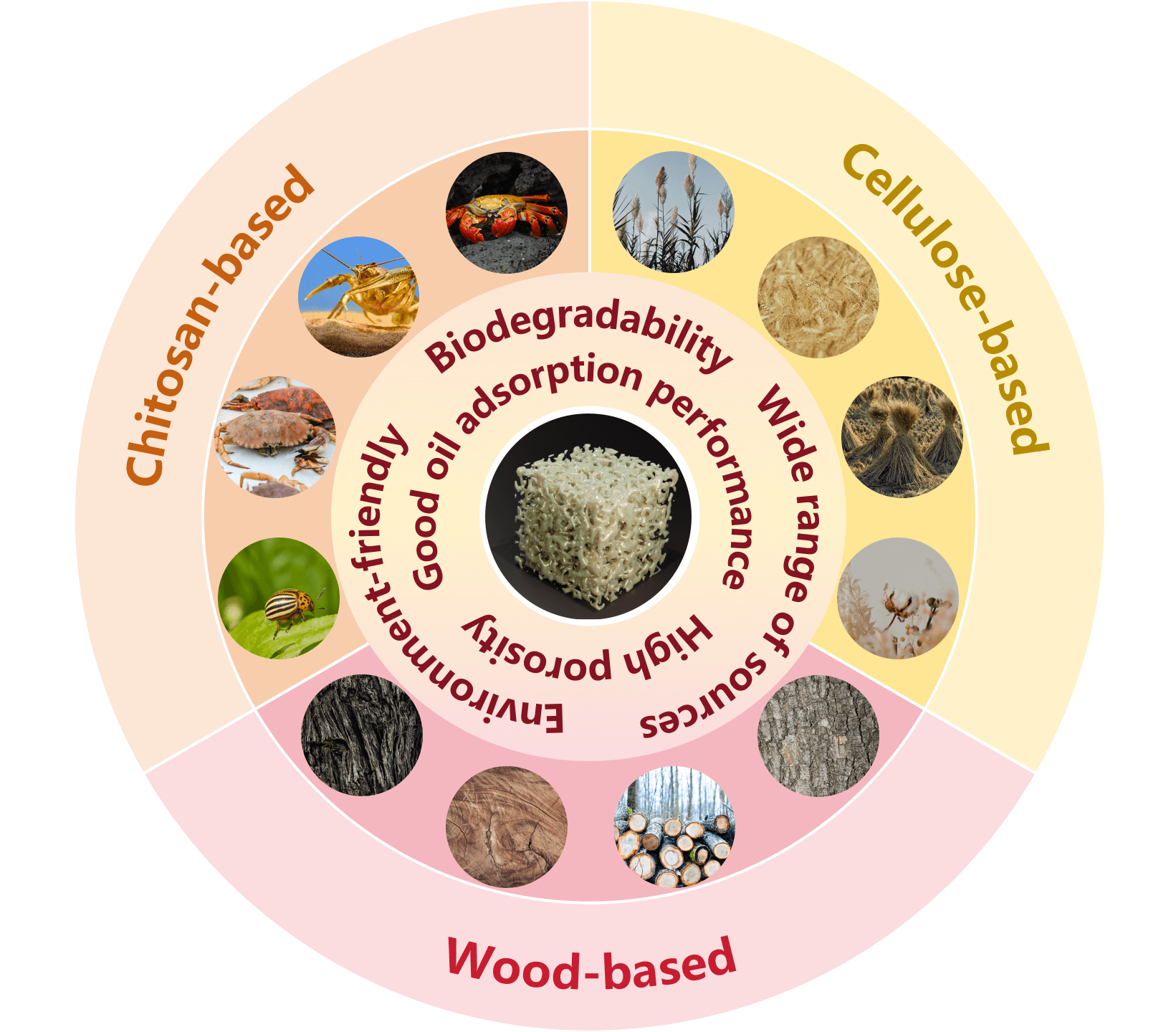
Keywords
Rapid industrialization is having a negative impact on the global environment [1,2], with pollution of marine ecosystems becoming increasingly serious. As global demand for oil and its derivatives grows, the discharges of oil and its by-products [3,4] as well as oil-containg domestic and industrial effluents [5,6] during storage and transportation resulted in irreversible damage to the marine ecology and public health [7–9]. Therefore, the treatment of oily wastewater is an urgent problem that needs to be solved. Generally, the treatment methods to deal with the above incidents generally include incineration [10–12], containment using oil booms to limit spread [13–15], recovery with mechanical skimmers [16–18], and oil dispersion using chemical dispersants [19,20], and others. However, these methods may lead to secondary contamination or wasted resources during incident handling. In contrast, adsorption is a preferred option due to the avoidance of secondary pollution. The unique pore structure of porous materials makes a significantly large specific surface area, which results in the excellent absorption of liquid substances. The structure of oils consists mainly of hydrophobic groups that have non-polar or weak polar properties and have relatively weak intermolecular interactions. The porous materials can be effectively used for oil adsorption through physical adsorption through hydrophobic modification using non-polar monomers. Adsorbent materials are able to adsorb oil and its derivatives from water efficiently and easily, making them a focus of research [21–25].
Industrially produced oil-absorbing materials are mainly derived from petrochemical-based polymers (polyacrylamides, polyurethanes, graphenes, etc.). Bentini et al. [26] mixed powder of polyvinylidene difluoride (PVDF) and expanded graphite (EGr) at a mass ratio of 7:1 to form a homogeneous mixture, which was heated and cooled at room temperature to obtain PVDF/EGr porous material with an average oil absorption capacity of 12 g/g. Visco et al. [27] investigated polyurethane foams filled with different numbers of carbon fibers and found that their selective oil absorption was improved at an optimal filling level of 1 wt% and that their contact angle with water varied with the number of fillings, ranging from 111° to 114°. Nevertheless, most petrochemical-based adsorption materials come from non-renewable resources such as oil and natural gas, and their manufacturing process generates large amounts of wastewater and exhaust gases, resulting in severe environmental pollution. In addition, due to their poor compatibility, these materials are not easily decomposed and degraded, causing serious disposal problems when the upper limit of use is reached. Accordingly, the use of conventional petrochemical-based adsorption materials in conbating oil spills and other oil pollution problems is bound to have adverse effects on the environment.
Compared to petroleum-based materials, porous biomass materials exhibit excellent environmental compatibility and sustainability. In addition, porous biomass materials possess a significant advantage in terms of biodegradability [28,29], which, to a certain extent, can reduce the environmental problems caused by the waste of materials. Therefore, the utilization of biomass resources to develop environmentally friendly oil-absorbing porous materials and reduce dependence on petrochemical products has emerged as a new research focus [30]. Natural polymeric materials such as cellulose, chitosan, and wood derivatives are currently attracting global attention from researchers due to their easy availability, low cost, and excellent performance in oil-water separation. These materials can be used in various applications such as oil absorbents and oil-water separation membranes, providing efficient oil and pollutant removal from water with good adsorption and separation properties. Furthermore, the favorable biocompatibility and degradability of natural polymeric materials result in minimal environmental impact [31,32]. They help reduce waste through natural degradation or recycling, thereby promoting the development of a sustainable circular economic system. Therefore, focusing on the research, development and application of natural polymeric materials is of significant importance, contributing to the protection of the marine ecological environment, human well-being and economic development [33]. Table 1 shows the characteristics, advantages, and disadvantages of the popular oil-absorbing porous materials.
2 Cellulose-Based Oil-Absorbing Porous Materials
Cellulose, a macromolecular polysaccharide composed of glucose with the molecular formula (C6H10O5)n (Fig. 1), is widely available [40] and naturally renewable. There are a variety of cellulose resources worldwide, such as straw, reeds, etc. The porous cellulose-based materials, which can be prepared with nanocellulose, hydroxyethyl cellulose, bacterial cellulose, etc., possess high specific surface area and are easy to modify [41–43] in an environmentally friendly manner. However, its polyhydroxy structure results in poor oil selectivity [44], which requires control of the oil-water selectivity of cellulosic porous materials.
Figure 1: Molecular structure of cellulose
2.1 Nanocellulose-Based Oil-Absorbing Porous Materials
At present, the Technical Association of the Pulp and Paper Industry (TAPPI) and other organizations [45] propose that nanocellulose can be divided into the following three categories: (1) cellulose nanocrystals (CNC), (2) microfibrillated cellulose (MFC), (3) bacterial nanocellulose (BNC). Researchers have shown great interest due to its hydrophilicity, renewability, biocompatibility, and excellent mechanical strength [46–48]. Chatterjee et al. [49] prepared porous materials (CNCA) using the ice template method by combining an aqueous suspension of CNC with polyethyleneimine (PEI) and an epoxy cross-linker. Then, chemically modified graphene sheets (GrEs) were attached to the surface of the porous material by the dip-coating method to obtain a CNC/graphene porous material (GCNCA). GrEs only improved the surface hydrophobicity of the material, without affecting its porosity and elasticity. The absorption of non-polar organic solvents ranged from 25 to 58 g/g, which showed selective oil absorption and maintained good oil absorption even after 100 times of extrusion-expansion. Chen et al. [50] added cellulose nanofibers (CNF) to a mixed bacterial suspension, followed by the addition of sodium alginate for stirring, freezing, and subsequent cross-linking with a Ca2+ solution to produce CNF@aerogel microspheres. An epoxy-acetone solution was configured and sprayed on the surface of CNF@aerogel by a simple spray bonding method to uniformly attach the MHNTs and Fe3O4/MHNTs and obtain a nucleoshell structure with a core-shell structure for the porous biomass material. This material exhibited a hydrophobic angle of up to 134°, which could be used for selective oil adsorption and magnetic recovery. Meanwhile, it showed strong tolerance under different pH and salinity conditions. Gong et al. [51] provided a method to prepare porous hydrophobic aerogels with cellulose nanocrystals (CNC) supported by polyvinyl alcohol (PVA), followed by thermochemical vapor deposition of methyltrichlorosilane on the surface. The maximum contact angle of this material could reach 144.5°, the porosity was more than 97.7%, and the absorption capacity can reach 32.7 times the original weight. Zhang et al. [52] treated kapok fibers with sodium hydroxide (8 wt%) at 100°C for 1 h, then washed them with deionized water to neutrality and drained them at 60°C for 24 h. The obtained kapok fibers were treated in a valley beating machine for 40 min and then homogenized in a high-pressure homogenizer to obtain kapok cellulose nanofibrils (KCN). The aqueous KCN suspension was dispersed and the pH was adjusted to 4. Then 0.2 wt% vinyltrimethoxysilane (VTMO) was added with continuous stirring for 2 h. Finally, the modified porous material was freeze-dried (Fig. 2). The prepared materials possessed superhydrophobicity with a maximum hydrophobicity angle of up to 150.5° and exhibited an excellent oil-absorption capacity in the range of about 126.8 to 320.4 g/g.
Figure 2: Schematic diagram of the preparation process of Kapok cellulose foam. Adapted with permission from Reference [52], Copyright © 2021 Published by Elsevier Ltd.
2.2 Bacterial Cellulose-Based Oil-Absorbing Porous Materials
Bacterial cellulose (BC), a water-soluble polysaccharide produced by bacteria, is mostly ribbon-shaped and has a dense fibrous structure with excellent mechanical properties and inherent biodegradability [53–56]. Compared to plant cellulose, BC is an important environmental protection material [57,58] and offer unique properties such as higher crystallinity and purity. BC is usually synthesized by mechanical crushing and atmospheric drying [59], and the BC prepared by treating vinegar residue hydrolysate with activated carbon exhibits higher fiber density, crystallinity and good thermal stability [60]. Men et al. [61] used the in-situ polymerization method to prepare BC-DMC porous materials by adding only 2-(methacryloyloxy) ethyltrimethyl ammonium chloride (DMC) and AIBN as initiator. The addition of DMC ensured the original porous structure while enhancing the hydrophobicity and antibacterial properties of BC. The maximum oil absorption capacity for various oils exceeded 30 g/g, and after several cycles, an oil absorption capacity of over 20 g/g could still be achieved. He et al. [62] used BC as raw material and 1,2,3,4-butanetetracarboxylic acid (BTCA) as catalyst, which not only acted as a catalyst, but also could undergo esterification reaction with BC.
BC with improved elastic and hydrophobic properties can be prepared by thermochemical vapor precipitation modification. The resulting material can quickly recover after compression and be separated by simple mechanical extrusion after absorbing oil, providing a new way to prepare BC aerogels with high elasticity and hydrophobic ability. This material is easily collected by external magnets, with excellent recyclability, which can be reused at least 10 times and still maintains the highest adsorption capacity (silicone oil has a high value of up to 181 g/g). Yan et al. [63] prepared porous materials with elastic compressibility and high oil absorption by freeze-drying an aqueous suspension with appropriate BC concentration and then performing chemical vapor deposition of methyltrimethoxysilane using ammonia as a catalyst. The maximum contact angle of the modified material could reach 142° and the adsorption capacity of oil was 121.8 to 284.1 g/g, which is a new idea to solve the problem of oil spills in industry. He et al. [64] obtained self-assembled bacterial cellulose aerogels (BCAs) by freeze-drying. Meanwhile, silica sols were prepared by a one-step catalytic process using methyltriethoxysilane (MTES) as a precursor. MTES, H2O, ethanol and acetic acid were mixed at a molar ratio of 1:4:6:0.8, and dilute ammonia was added dropwise to promote gelation. Finally, the freeze-dried BCAs were impregnated in the sol for 30 min and aged in ethanol for 24 h. The BCAs/SAs were obtained by freeze-drying. BCAs/SAs exhibited a remarkable hydrophobicity with a contact angle of 152° and exhibited favorable lipophilicity generated by methyl groups on the surface of the silica gas gel filler. Due to their layered cell structure, BCAs/SAs exhibited good resilience and excellent oil absorption capacity, which makes them promising for various applications in oil absorption, oil production, and oil-water separation (Fig. 3).
Figure 3: (a) Illustration of the whole synthetic steps of BCAs/SA composites: the BCAs obtained by flexible BC nanofibers were impregnated into MTES-derived silica sols under vacuum and finally assembled into BC/SAs after freeze-drying; (b) Schematic of the dehydration reaction between hydroxyl groups on BC fibers and silica aerogels. Adapted with permission from Reference [64], Copyright © 2017 Published by Elsevier B.V.
2.3 Regenerated Cellulose-Based Oil-Absorbing Porous Materials
Materials based on regenerated cellulose are obtained from renewable natural cellulose and are converted into cellulose solution and its derivatives only by changing their physical structure [65,66]. This process primarily involves dissolution-regeneration [67,68] and lead to the production of high-performance, environmentally friendly materials based on regenerated cellulose [69–72]. These materials facilitate the creation of a biodegradable porous adsorption material that provides a new direction for the regeneration and utilization of biomass waste and enables the functional application of porous materials based o regenerated cellulose in the field of water treatment.
Zhang et al. [73] effectively used freeze-drying and hydrophobic modification techniques to obtain new functional regenerated cellulose-based materials through the reaction of discarded cigarette filters and polyvinyl alcohol. The highly porous foam material had a water contact angle range of 91.9° to 126.2° and could be used as an oil adsorbent for wastewater treatment. Du et al. [74] provided a new method for constructing a porous structure of a hydrophobic sponge based on regenerated cellulose. In this method, methyltrichlorosilane was used as a silanizer, and the porosity (up to 87.46%) was regulated by toluenesulfonylhydrazine to achieve the regeneration of cellulose xanthate. After several measurements, the water contact angle was stable at 140°~145°. Xu et al. [75] dissolved pulp cellulose in a solution of tetraethylammonium hydroxide (TEAOH)/urea/H2O and obtained regenerated cellulose microstructures (RCMSs) with a pore size of micro/nanoscale through an emulsion-solidification-drying process, to synthesize microporous materials with high stability and high porosity (Pr, 90%~93%), which could be used for the separation and purification of oily wastewater. Ma et al. [76] prepared natural microfibers/regenerated cellulose (NM/RCA) directly from hardwood pulp by mixing N-methylmorpholine-N-oxide monohydrate (NMMO·H2O) with deep eutectic solvent (DES) to form a co-solvent. The new carbonized microfiber aerogel had a water contact angle of 151.5°. It had excellent properties such as high-temperature resistance, high adsorption rate and high resilience. The recovery rate was 80.5% after several cycles, demonstrating the wide application of new regenerated cellulose-based in the separation and purification of oil/water pollutants (Fig. 4).
Figure 4: (a) Schematic illustration of the fabrication of the natural microfibrils/regenerated cellulose-based carbon aerogel (NM/RCA); (b) The reaction mechanism of NM/RCA. Adapted with permission from Reference [76], Copyright © 2023 Published by Elsevier B.V.
2.4 Oil-Absorbing Porous Materials Based on Other Cellulose
Xu et al. [77] proposed a room temperature cellulose-grafted epoxidized soybean oil (ESO) to efficiently produce natural porous materials based on whole biomass. The cellulose aerogel modified by epoxidized soybean oil has a maximum contact angle with water of 132.6° and good hydrophobic properties. Setyawan et al. [78] prepared hydrophilic cellulose aerogels (~97.5%) with a water contact angle of 137° from low-cost coconut shell fiber by alkali-urea and freeze-drying method. Cellulose aerogels are characterized by low density (ρ = 0.047 g/cm−3), high porosity and high flexibility. The surface is modified by a silanizing agent (TMCS or HMDS), and the hydroxyl group on the surface is replaced by the trimethylsilyl group, which can make the aerogel surface hydrophobic. The modified cellulose aerogel has good elasticity, near-superhydrophobicity, and has great application potential in oil spill recovery. Li et al. [79] successfully prepared a new type of cellulose aerogel by using cellulose oxidation, crosslinking, freeze-drying and cold plasma modification. Its water contact angle was up to 152.8° with excellent oil/water selectivity and high absorption capacity for various oils and organic solvents up to 28.20 g/g, which was expected for use in the field of oil and organic solvent leakage cleaning and oil-water separation. Liu et al. [80] proposed a sol-gel method with freeze-drying and hydrophobic surface modification to prepare bamboo cellulose foam with special wetting properties. The water contact angle of bamboo cellulose foam was 160°. Due to the three-dimensional network structure of the superhydrophobic bamboo cellulose foam and the synergistic effect of its hydrophobic components, it exhibited excellent oil absorption performance of 11.5 to 37.5 g/g and good recyclability for various types of oil. After 10 cycles, the absorption capacity of oil (1,2-dichloroethane) was up to 31.5 g/g, which expanded the possibility of separating oily wastewater by super-wetting interface materials and stimulated the new idea of oil-water separation under harsh conditions, and promoted the development and application of natural bamboo cellulose. Lang et al. [81] dispersed cellulose in a mixed solution of NaOH/urea/H2O (weight ratio 7/12/81), then added MBA (N,N′-methylenebisacrylamide) to the completely dissolved cellulose solution and stirred at room temperature for 5 h, and when the MBA was completely dissolved, a certain amount of tannin was added at a time, and stirring was continued for 1 h. The solution was left for 6 h to form a hydrogel. The obtained solution was kept stationary for 6 h to form a hydrogel, followed by dialysis until the pH of the dialysis medium was neutral, and then freeze-drying was performed to obtain the porous material. Its water contact angle was 163° ± 1°. PCMT exhibited a three-dimensional interpenetrating porous structure and excellent oil absorption capacity with good adaptability in complex environments (Fig. 5).
Figure 5: (a) Illustration of the chemical structure exposed on the PCMT surface; (b) Contact angle of water on the PCMT surface; (c) Absorption of n-hexane in the PCMT; (d) Absorption of dichloromethane in the PCMT under water. Adapted with permission from Reference [81], Copyright © 2024 Published by Springer Nature.
By introducing hydrophobic groups on cellulose molecules or using CVD to treat cellulosic porous materials, the amphiphilicity of cellulosic porous materials can be regulated to give the materials higher oil selectivity and improve oil absorption efficiency. However, the above methods still have a lot of room for improvement in terms of mechanical strength and adsorption efficiency. At the same time, there are also problems such as high costs and difficulties in industrial production.
3 Chitosan-Based Oil-Absorbing Porous Materials
Chitosan is the only alkaline polysaccharide in nature. The molecular weight of the monomer is about 161.2, and the molecular structure is shown in Fig. 6. It is a non-toxic and harmless natural polymer material with good adsorption, biocompatibility, and environmental friendliness, commonly found in exoskeletons of crustaceans and insects [38,82,83].
Figure 6: Molecular structure of chitosan
Li et al. [84] provided a strategy for absorbing highly viscous oils. Essentially, polyaniline and Fe3O4 were used to prepare magnetic and conductive chitosan composite aerogel adsorbent, which can generate heat through an alternating magnetic field. After hydrophobic modification, this absorbent could repeatedly absorb high-viscosity oil with an absorption capacity of 21 g/g. The surface of the modified aerogel changed from hydrophilic to hydrophobic, and the maximum contact angle between the material and water was 121°, which enabled the aerogel to absorb non-polar oil. Si et al. [85] used a metal framework (ZIF-8) with high crystallinity and large surface area to effectively prepared an ultra-light double-mesh cellulose nanofiber/chitosan-based aerogel with high adsorption capacity for oil and organic solvents through physical entanglement and scalable freeze-drying methods. Then, hydrophobic modification was realized by using methyl trimethoxysilane. Its maximum contact angle with water was 132.6°, and the maximum oil absorption capacity could reach 74.55 g/g through the oil absorption capacity test. After several cycles, it still maintained high durability, allowing potential material selection for subsequent engineering applications. Yin et al. [86] constructed a magnetic porous template based on CS, itaconic acid, and Fe3O4 nanoparticles (FeNPs) with electrostatic interaction in water, and then freeze-dried it. The by polydimethylsiloxane (PDMS) modified product exhibited excellent hydrophobicity after freeze-drying, with a maximum contact angle with water of 147.1° and an adsorption capacity of up to 22.38 g/g. Wang et al. [87] mixed CS/acetic acid solution with aminoethyl-β-cyclodextrin-sodium phytate (a-cd-stp) solution to prepare a CTCS sponge, and then immersed it in citric aldehyde/ethanol solution (1%, v/v) to synthesize CCTCS sponge. After drying at room temperature, it was soaked in palmitic acid/ethanol solution at different temperatures and dried to obtain the ACCTCS sponge. The experimental results showed that the modified sponge had ideal mechanical properties and strong hydrophobicity, with a water contact angle of 147.8° and a high organic matter absorption capacity. After 10 times of adsorption-desorption, the oil removal rate could reach >26.2 g/g, which is a new solution for industrial oil-water separation. Su et al. [88] used TPP/citral cross-linking and octadecanethiol to modify chitosan aerogel to obtain a kind of superhydrophobic MCTCS sponge. The highly porous structure and coherent porous structure allowed it to absorb 60 times its weight of oil, enabling continuous and repeated recycling. Yi et al. [89] used directional freezing technology to freeze-dry and silanize chitosan-based aerogels, giving them a highly porous structure and anisotropy. Silane-modified CS aerogels showed a significantly higher water contact angle of 152.3°, and the maximum oil absorption could reach 63 g/g. Kordjazi et al. [90] prepared a high-efficiency water/oil separation filter cotton fabric coated with chitosan/acrylamide hydrogel coated using ammonium persulfate (APS) as a thermal initiator and polyacrylamide monomer (MBA) as a crosslinker. It was tested with a water contact angle of 156° and a porous structure. It had high stability in an alkaline environment (seawater), and could effectively separate water and oil mixtures with a separation efficiency of 98%. Guan et al. [91] dissolved chitosan (CS) in acetic acid (HAc) solution to obtain a homogeneous CS/HAc solution. Cuttlefish ink was added to the above solution and stirred for 30 min to obtain a homogeneous black solution. To this solution, (3-glycidyloxypropyl) trimethoxysilane (40% mass ratio to CS) was added and stirred at 60°C for 1 h to complete the cross-linking process. Directional freezing was then performed for 15 min followed by sublimation in a freeze dryer at −50°C for 48 h to form directional tubular channel structures. Superhydrophobic photothermal PDMS-Ink@CS aerogels were prepared by immersing the obtained Ink@CS aerogels into a mixed PDMS/isopropanol solution for about 10 min, followed by reaction at 80°C for 2 h. PDMS-Ink@CS aerogel had good photothermal conversion and oil adsorption capacity, which could realize the continuous extraction of crude oil on the sea surface. PDMS-Ink@CS aerogel had the best oil absorption rate when the thickness was about 6 mm, and its adsorption capacity for various oils or organic solvents was between 20 and 32 g/g. For the adsorption of highly viscous crude, PDMS-Ink@CS aerogels could adsorb 18 times of their own weight of crude oil under sunlight of 1 kW/m2, and the crude oil could be easily recovered by extrusion (Fig. 7).
Figure 7: Schematic diagram of the preparation for the PDMS-Ink@CS aerogel. Adapted with permission from Reference [91], Copyright © 2023 Published by Elsevier B.V.
The methods mentioned above all utilize chitosan as a raw material to produce oil-absorbing porous materials. Hydrophobic modification treatment improves the adsorption performance and reusability of oil-water mixtures, achieving cost-effective and efficient oil-water separation. This provides a new scheme for the large-scale production of high-performance oil-absorbing porous materials from biomass resources.
4 Wood-Based Oil-Absorbing Porous Materials
Wood has received extensive attention due to its rich hierarchical porous structure and unique anisotropy, adopting a ‘top-down’ or ‘bottom-up’ strategy to precisely regulate the chemical composition, pore structure, and surface wettability of wood [39,92–94]. This not only provides a new perspective for the development of high-performance oil-water separation materials, but also opens a new path for technological innovation and progress in this field.
The polyalkylsiloxane is preferred for the hydrophobic modification of wood-based biomass. Zhu et al. [95] used methyltrimethoxysilane (MTMS) to modify natural renewable balsa mood aerogel. The maximum contact angle of the obtained material with water could reach 151.8°, and the adsorption of CH2Cl2 could reach 25.1 times. However, Zhao et al. [96] proposed a simpler, efficient, and economical strategy for the production of polymethylsiloxane (POMS)-modified wood, so that the three main advantages of superhydrophobicity, porous structure, and intrinsic channels were combined, and the maximum contact angle between the POMS-modified wood and water was 153°, which selectively separated oil-water mixtures. Chen et al. [97] used reduced graphene oxide (GSH) and vinyl-terminated polydimethylsiloxane (V-PDMS) to modify the delignified wood to prepare superhydrophobic PDMS@GSH wood-based porous materials with Joule heat and photothermal effect of superhydrophobic PDMS@GSH wood-based porous materials, that could be separated quickly, were easy to scale, and had a maximum contact angle of up to 156° with water. This material had a wide application prospects in crude oil purification. It could also be hydrophobized by delignified wood coated with TiO2/PDMS with a maximum contact angle of 160°. Due to the photocatalysis achieved by the addition of TiO2, PDMS and petroleum impurities could be degraded, which represents a novel method for the treatment of petroleum impurities [98] (Fig. 8). Wang et al. [99] immersed the prepared wood-based aerogels in a 1 wt% PDMS/toluene solution (10:1 weight ratio of PDMS to curing agent). PDMS was then conveyed into the wood-based aerogel by vacuum, and then cured in an oven at 60°C. Excess PDMS in the cured modified wood-based aerogel was removed by washing with toluene, modified wood-based aerogels have an oil-absorption capacity of up to 20 g/g. The resulting materials could achieve oil/water separation by gravity alone, with a separation efficiency of 99.5%.
Figure 8: (a) PDMS@TiO2 wood based material preparation process; (b) Schematic diagram of photocatalytic degradation. Adapted with permission from Reference [98], Copyright © 2022 Published by Elsevier B.V.
Du et al. [100] sprayed the prepared pH-responsive copolymer onto the compressible wood-based sponge using spraying method. The sponge could realize the surface wettability conversion between hydrophobicity and hydrophilicity at different pH values. The water contact angle of the sponge could reach 155.8° without acid and alkali treatment. After treatment with alkaline solution, the water contact angle was 151.5°. The oil absorption capacity of the wood-based sponge was 12.72 g/g, and it was recyclable. The oil-water separation efficiency was 92% and could be applied to the continuous separation of oily wastewater. Cai et al. [101] coated the surface of porous wood with cross-linked polydivinylbenzene (PDVB), which significantly improved the softness, durability, hydrophobicity, and robustness of the material. The separation efficiency of this PDVB wood film for a surfactant-stabilized water-in-oil emulsion was over 99.98%, and the contact angle with water was up to 160°. After 20 separation cycles, the separation efficiency was 99.98%, achieving high oil/water separation performance and high material recoverys. Ma et al. [102] used the porous structure of natural wood to endow natural wood with the characteristics of fire-proof superhydrophobicity through layer-by-layer construction to deal with the problems of oil leakage and chemical leakage in actual large-scale production. This wood-based material exhibited excellent oil-water separation performance (>97%) and mechanical durability. Its surface and water contact angle was 168°, reflecting superhydrophobic properties.
Zhang et al. [103] developed a wood-based mesoporous Janus membrane, which was based on the unique transpiration microchannel of wood and the synergistic effect of PPy and Ag/AgCl NPs anchored on the wood substrate. In the absence of external input, this wood-based mesoporous Janus membrane enabled highly efficient seawater desalination and switchable separation of oil and water. Meanwhile, the membrane could also adsorb organic substances with an adsorption efficiency of ≥99.51% by increasing the interaction with Ag/AgCl NPs through wood microchanneling. Cheng et al. [104] developed Ag/wood filters that utilize the in-situ precipitation of silver nanoparticles (Ag NPs) in wood. These filters simultaneously achieved the separation of oil and water and the removal of organic dyes from water with a separation efficiency of over 99%, providing a new solution for the treatment of oily wastewater.
All of the above processes use natural renewable wood as raw material to develop new wood adsorption materials for oil-water separation. By retaining the original fibrous skeleton of wood and cross-linking and assembling on its surface, the surface is provided with a high contact angle with water, to obtain wood-based porous materials with hydrophobic and oleophilic properties, which is a new idea for the preparation of new oil-absorbing porous biomass-based materials and realization of the application of natural wood resources in oil-water separation.
5 Other Biomass-Based Oil-Absorbing Porous Materials
In addition to the three biomass materials mentioned above, there are other porous biomass materials that are also suitable for crude oil extraction and oil-water separation. Hu et al. [105] prepared porous-starch/casein K+/carrageenan gel membranes by modifying porous starch, and the cumulative oil absorption could reach 87.5% in 20 min. The material had a high oil absorption capacity and was suitable for quickly extracting oil from crude oil. Jiang et al. [106] used straight-chain starch content control and pre-freezing method to adjust the structure of the starch gel at low-temperature and increase the polyelectrolyte content, thereby improving oil absorption ability of the material. This method was simpleand was intended to be applied in the field of oil-water separation. Wang et al. [107] prepared starch-based superhydrophobic porous materials by rapid impregnation of starch low-temperature gels (SC) in methyltrichlorosilane (MTS) toluene solution, which resulted in the structural formation of micro-and nano-corals from the condensation and hydrolysis of MTS, providing low surface energy. Chen et al. [108] used light-cured soybean oil-based methacrylic acid urethane and low-cost salt porous agent as raw materials to obtain bio-based porous materials through UV curing technology and salt template-assisted process. The material could quickly absorb organic solvents, and the key technologies were all low-cost, which was expected to be utilized on a large scale in the field of oil/water separation. Lu et al. [109] utilized industrial-grade polylactic acid (PA) nonwoven materials as porous membranes and attached PA nanoparticles to the membrane surface to improve the hierarchical roughness of the material surface, and the modified materials had superhydrophobic properties and oil-water separation effects. Zhang et al. [110] added regenerated beeswax and lignin to the cotton surface to achieve superhydrophobicity and superoleophilicity. The beeswax and lignin provided low surface energy and micro/nanostructures to varying degrees, and the addition of lignin further improved the thermal stability of the material and provided good adsorption of thick oil. Li et al. [111] prepared porous templates based on the natural amphiphilic oligomer violet gel secreted by the violet gummy worm, which was converted into a hydrophobic material by self-assembling into a continuous rigid network structure with a hydrophobic core, and air-dried violet aerogels were treated with silane layers. The saturated aerogel could be rapidly degraded in a strong alkaline environment (pH = 14), thus significantly minimizing the impact on the environment. Li et al. [112] prepared micro and nanofiber fabrics by fusion spouting. This material was based on PLA/PBE polymer that used polylactic acid (PLA) and propylene-based elastomers (PBE) as raw materials by mixing thermoplastics. The maximum contact angle between the prepared samples and water was 134°, which had a certain ability to separate water and oil. Aminopropyltrimethoxysilane and vinyltrimethoxysilane could also be polymerized onto PLA by in-situ polymerization to form a semi-interpenetrating silicone network structure, PLA@silicone semi-IPN fiber membranes could absorb up to 83.9 g/g of oil [113], and also exhibit high oil absorption capacity.
In summary, the rich diversity and excellent plasticity of biomass-based porous materials are evident. Different raw materials and preparation methods show different oil absorption properties and oil-water separation effects, thus offering a wider range of possibilities for different application scenarios. In-depth research and development of biomass-based porous materials is expected to provide more sustainable and efficient solutions for environmental management and resource recovery.
The traditional petrochemical-based adsorbent materials are facing the problem of waste disposal, which makes people pay attention to biomass-based porous oil-absorbent materials and highlight them as a new strategy to solve the oil spill accident. The environmental friendliness and sustainability of the preparation process are key factors that must be taken into account when researching new oil-absorbing materials. Through environmentally friendly treatment methods, waste recycling, effective treatment of wastewater, and waste gas, it becomes a more environmentally friendly and sustainable oil-absorbing material.
The research and development of biomass-based porous adsorption materials is not only the theme of green and low-carbon development in today’s world, but also a new oeak for promoting green economic growth. The natural renewability of biomass-based materials relieves the environmental burden caused by dependence on petrochemical materials. At the same time, the modified biomass fiber has higher oil absorption capacity and selectivity. These materials cannot only be applied to the treatment of oil spills at sea, but also play an important role in industrial wastewater treatment, oil transportation pipeline leakage treatment, and other fields. In addition, they can also be used in environmental areas such as soil remediation.
In summary, biomass-based porous oil absorption materials offer numerous advantages, but the properties of the material need to be improved compared to traditional petrochemical products. The reasons may be as follows: (1) The pore structures of bio-based porous materials are complex and uncontrollable, limiting their ability to effectively capture and retain oil. (2) Raw material types and treatment processes, etc., can lead to changes in the surface properties of biomass porous materials, which may further affect the oil-absorption efficiency. (3) Under extreme environmental conditions, such as an atmosphere that is too acidic or alkaline, the structure of the material may be destroyed, thereby affecting the adsorption capacity. In addition, the circulating adsorption capacity of oil-absorbing biomass fiber material is relatively low, which greatly hinders its popularization and use. The oil absorption capacity of chitosan-based porous materials is relatively low, and the adsorption capacity is not as good as that of traditional petrochemical products. The stability of wood oil-absorbing porous materials is poor, and the oil-absorption capacity is lower than that of cellulose-based materials. The preparation process of most materials with high oil absorption capacity is also expensive, which greatly affects their actual production and use. To promote the utilization of porous biomass materials, we will explore novel modification techniques and composite designs to improve their selectivity, stiffness and durability. At the same time, we will also explore methods to improve their properties in extreme environments to extend their durability. In addition, we are committed to the development of low-energy and low-pollution biomass material processing technologies, such as bio-based solvents and supercritical fluid processing technologies, to realize environmentally friendly production and utilization.
Acknowledgement: None.
Funding Statement: This research was supported by Jiangsu Province Biomass Energy and Material Laboratory (JSBEM-S-202201), the National Natural Science Foundation of China (31901257) and School-Level Research Projects of the Yancheng Institute of Technology (xjr2019008).
Author Contributions: The authors confirm contribution to the paper as follows: Conceptualization, Investigation and Writing—original draft: Yifan Sun. Writing—original draft, Investigation: Yuanyuan Zhang and Siying Chen. Writing—original draft: Hailang Liu and Bo Fang. Investigation: Ziyi Tian. Supervision, Writing—review & editing: Xujuan Huang. Writing—review & editing: Zhaosheng Cai. All authors reviewed the results and approved the final version of the manuscript.
Availability of Data and Materials: No data was used for the research described in the article.
Ethics Approval: Not applicable.
Conflicts of Interest: The authors declare that they have no conflicts of interest to report regarding the present study.
References
1. Brkić D, Praks P. Proper use of technical standards in Offshore Petroleum Industry. J Mar Sci Eng. 2020;8:555. doi:10.3390/jmse8080555. [Google Scholar] [CrossRef]
2. Nelson JR, Grubesic TH. Oil spill modeling: risk, spatial vulnerability, and impact assessment. Progress Phys Geograp: Earth Environ. 2018;42:112–27. doi:10.1177/0309133317744737. [Google Scholar] [CrossRef]
3. Qi B, Wang N, Hu X, Cui S, Liu H, He R, et al. Melt-blown fiber felt for efficient all-weather recovery of viscous oil spills by Joule heating and photothermal effect. J Hazard Mater. 2023;460:132523. doi:10.1016/j.jhazmat.2023.132523. [Google Scholar] [PubMed] [CrossRef]
4. Sankaran Rajendran, Aboobacker VM, Vashist OS, Al Khayat JA, Rangel-Buitrago N, Al-Kuwari HA-S, et al. History of a disaster: a baseline assessment of the Wakashio oil spill on the coast of Mauritius, Indian Ocean. Mar Pollut Bull. 2022;175:113330. doi:10.1016/j.marpolbul.2022.113330. [Google Scholar] [PubMed] [CrossRef]
5. Sun Y, Bai J, Wang Z, Li H, Dong H. A hydrophobic/oleophilic silica-cellulose composite aerogel for oil-water separation. J Appl Polym Sci. 2023;140:e54408. doi:10.1002/app.54408. [Google Scholar] [CrossRef]
6. Zhang J, Liu L, Si Y, Yu J, Ding B. Electrospun nanofibrous membranes: an effective arsenal for the purification of emulsified oily wastewater. Adv Funct Mater. 2020;30. doi:10.1002/adfm.202002192. [Google Scholar] [CrossRef]
7. Bruederle A, Hodler R. Effect of oil spills on infant mortality in Nigeria. Proc Nat Acad Sci. 2019;116:5467–71. doi:10.1073/pnas.1818303116. [Google Scholar] [PubMed] [CrossRef]
8. Huynh BQ, Kwong LH, Kiang MV, Chin ET, Mohareb AM, Jumaan AO, et al. Public health impacts of an imminent Red Sea oil spill. Nat Sustain. 2021;4:1084–91. doi:10.1038/s41893-021-00774-8. [Google Scholar] [PubMed] [CrossRef]
9. Pabón REC, de Souza Filho CR, de Oliveira WJ. Reflectance and imaging spectroscopy applied to detection of petroleum hydrocarbon pollution in bare soils. Sci Total Environ. 2019;649:1224–36. doi:10.1016/j.scitotenv.2018.08.231. [Google Scholar] [PubMed] [CrossRef]
10. Tuttle SG, Fisher BT, Kessler DA, Pfützner CJ, Jacob RJ, Skiba AW. Petroleum wellhead burning: a review of the basic science for burn efficiency prediction. Fuel. 2021;303:121279. doi:10.1016/j.fuel.2021.121279. [Google Scholar] [CrossRef]
11. Fritt-Rasmussen J, Wegeberg S, Lassen P, Wilms LB, Renvald L, Larsen MB, et al. Coastline in-situ burning of oil spills, analysis of a Greenland field experiment. J Hazard Mater. 2023;441:129976. doi:10.1016/j.jhazmat.2022.129976. [Google Scholar] [CrossRef]
12. Fritt-Rasmussen J, Jørgensen CJ, Wegeberg S, Lassen P, Møller EF, Gustavson K. PAHs in high Arctic copepods Calanus hyperboreus following exposure of residues from in situ burning of oil spill. Sci Total Environ. 2024;912:169015. doi:10.1016/j.scitotenv.2023.169015. [Google Scholar] [PubMed] [CrossRef]
13. Zhao L, Daskiran C, Mitchell DA, Panetta PD, Boufadel MC, Nedwed TJ. Proof of concept study for in-situ burn application using conventional containment booms–design of Burning Tongue. J Hazard Mater. 2022;439:129403. doi:10.1016/j.jhazmat.2022.129403. [Google Scholar] [PubMed] [CrossRef]
14. Feng X, Zhang B. Applications of bubble curtains in marine oil spill containment: hydrodynamic characteristics, applications, and future perspectives. Mar Pollut Bull. 2023;194:115371. doi:10.1016/j.marpolbul.2023.115371. [Google Scholar] [PubMed] [CrossRef]
15. Liu J, Jiao P, Xu Y. Research on oil boom performance based on Smoothed Particle Hydrodynamics method. PLoS One. 2023;18:e0289276. doi:10.1371/journal.pone.0289276. [Google Scholar] [PubMed] [CrossRef]
16. Etkin DS, Nedwed TJ. Effectiveness of mechanical recovery for large offshore oil spills. Mar Pollut Bull. 2021;163:111848. doi:10.1016/j.marpolbul.2020.111848. [Google Scholar] [PubMed] [CrossRef]
17. Herren B, Saha MC, Altan MC, Liu Y. Funnel-shaped floating vessel oil skimmer with Joule heating sorption functionality. Polymers. 2022;14:2269. doi:10.3390/polym14112269. [Google Scholar] [PubMed] [CrossRef]
18. An W, Zhang Q, Zhao J, Qu L, Liu S, Yang M, et al. Mechanism investigation on a novel oil recovery skimmer coupling free surface vortex and cyclone separation. ACS Omega. 2021;6:20483–91. doi:10.1021/acsomega.1c02506. [Google Scholar] [PubMed] [CrossRef]
19. Cai Q, Zhu Z, Chen B, Lee K, Nedwed TJ, Greer C, et al. A cross-comparison of biosurfactants as marine oil spill dispersants: governing factors, synergetic effects and fates. J Hazard Mater. 2021;416:126122. doi:10.1016/j.jhazmat.2021.126122. [Google Scholar] [PubMed] [CrossRef]
20. Li W, Wang W, Qi Y, Qi Z, Xiong D. Combined effects of chemical dispersant and suspended minerals on the dispersion process of spilled oil. J Environ Manage. 2023;341:118110. doi:10.1016/j.jenvman.2023.118110. [Google Scholar] [PubMed] [CrossRef]
21. Wu X, Li S, Huang J, Chen Z, Cai W, Lai Y. Solar-assisted isotropically thermoconductive sponge for highly viscous crude oil spill remediation. iScience. 2021;24:102665. doi:10.1016/j.isci.2021.102665. [Google Scholar] [PubMed] [CrossRef]
22. Peng M, Zhu Y, Li H, He K, Zeng G, Chen A, et al. Synthesis and application of modified commercial sponges for oil-water separation. Chem Eng J. 2019;373:213–26. doi:10.1016/j.cej.2019.05.013. [Google Scholar] [CrossRef]
23. Hoang AT, Nižetić S, Duong XQ, Rowinski L, Nguyen XP. Advanced super-hydrophobic polymer-based porous absorbents for the treatment of oil-polluted water. Chemosphere. 2021;277(8):130274. doi:10.1016/j.chemosphere.2021.130274. [Google Scholar] [PubMed] [CrossRef]
24. Liu Q, Liu Y, Feng Q, Chen CC, Xu Z. Preparation of antifouling and highly hydrophobic cellulose nanofibers/alginate aerogels by bidirectional freeze-drying for water-oil separation in the ocean environment. J Hazard Mater. 2023;441:129965. doi:10.1016/j.jhazmat.2022.129965. [Google Scholar] [PubMed] [CrossRef]
25. Weng D, Song L, Li W, Yan J, Chen L, Liu Y. Review on synthesis of three-dimensional graphene skeletons and their absorption performance for oily wastewater. Environ Sci Pollut Res. 2021;28:16–34. doi:10.1007/s11356-020-10971-1. [Google Scholar] [PubMed] [CrossRef]
26. Bentini R, Pola A, Rizzi LG, Athanassiou A, Fragouli D. A highly porous solvent free PVDF/expanded graphite foam for oil/water separation. Chem Eng J. 2019;372:1174–82. doi:10.1016/j.cej.2019.04.196. [Google Scholar] [CrossRef]
27. Visco A, Quattrocchi A, Nocita D, Montanini R, Pistone A. Polyurethane foams loaded with carbon nanofibers for oil spill recovery: mechanical properties under fatigue conditions and selective absorption in oil/water mixtures. Nanomater. 2021;11:735. doi:10.3390/nano11030735. [Google Scholar] [PubMed] [CrossRef]
28. Wang F, Xie T, Zhong W, Ou J, Xue M, Li W. A renewable and biodegradable all-biomass material for the separation of oil from water surface. Surf Coat Technol. 2019;372:84–92. doi:10.1016/j.surfcoat.2019.05.002. [Google Scholar] [CrossRef]
29. Jin R, Gong J, Xiang B, Li J. Biomass materials with special wettability: a sustainable solution for efficient oil-water separation. J Mater Chem A. 2024;12:23315–36. doi:10.1039/D4TA04039B. [Google Scholar] [CrossRef]
30. Huang Y, Wu Y, Tao H, Yuan B. Bio-based porous aerogel with bionic structure and hydrophobic polymer coating for efficient absorption of oil/organic liquids. Polymers. 2022;14:4579. doi:10.3390/polym14214579. [Google Scholar] [PubMed] [CrossRef]
31. Nurchi C, Buonvino S, Arciero I, Melino S. Sustainable vegetable oil-based biomaterials: synthesis and biomedical applications. Int J Mol Sci. 2023;24:2153. doi:10.3390/ijms24032153. [Google Scholar] [PubMed] [CrossRef]
32. Zhang S, Lu S, Qian Y, Li Z, Xu X. Developing biomass-modified hydrogel with high mechanical strength by a rosin-based crosslinking agent. Mater Today Commun. 2024;39:108871. doi:10.1016/j.mtcomm.2024.108871. [Google Scholar] [CrossRef]
33. Fouladi M, Heidari MK, Tavakoli O. Development of porous biodegradable sorbents for oil/water separation: a critical review. J Porous Mater. 2023;30:1037–53. doi:10.1007/s10934-022-01385-0. [Google Scholar] [CrossRef]
34. Li Y, Ren S, Yu Q, Wang T, Xu X, He W, et al. High throughput, antibacterial and nonflammable melamine sponges for oil/water separation. J Environ Chem Eng. 2023;11:111127. doi:10.1016/j.jece.2023.111127. [Google Scholar] [CrossRef]
35. Brancato V, Piperopoulos E, Mastronardo E, Calabrese L, Milone C, Proverbio E. Synthesis and characterization of graphite composite foams for oil spill recovery application. J Compos Sci. 2020;4:154. doi:10.3390/jcs4040154. [Google Scholar] [CrossRef]
36. Liu S, Xu Q, Latthe SS, Gurav AB, Xing R. Superhydrophobic/superoleophilic magnetic polyurethane sponge for oil/water separation. RSC Adv. 2015;5:68293–8. doi:10.1039/C5RA12301A. [Google Scholar] [CrossRef]
37. Li A, Huber T, Barker D, Nazmi AR, Zadeh HN. An overview of cellulose aerogels and foams for oil sorption: preparation, modification, and potential of 3D printing. Carbohydr Polym. 2024;343:122432. doi:10.1016/j.carbpol.2024.122432. [Google Scholar] [PubMed] [CrossRef]
38. Umair B, Faizan M, Waheed A. A review on super-wettable porous membranes and materials based on bio-polymeric chitosan for oil-water separation. Adv Coll Interface Sci. 2022;303:102635. doi:10.1016/j.cis.2022.102635. [Google Scholar] [PubMed] [CrossRef]
39. Guan H, Cheng Z, Wang X. Highly compressible wood sponges with a spring-like lamellar structure as effective and reusable oil absorbents. ACS Nano. 2018;12:10365–73. doi:10.1021/acsnano.8b05763. [Google Scholar] [PubMed] [CrossRef]
40. Li T, Chen C, Brozena AH, Zhu JY, Xu L, Driemeier C, et al. Developing fibrillated cellulose as a sustainable technological material. Nature. 2021;590:47–56. doi:10.1038/s41586-020-03167-7. [Google Scholar] [PubMed] [CrossRef]
41. Cheng H, Li LJ, Wang BJ, Feng XL, Mao ZP, Vancso GJ, et al. Multifaceted applications of cellulosic porous materials in environment, energy, and health. Prog Polym Sci. 2020;106:101253. doi:10.1016/j.progpolymsci.2020.101253. [Google Scholar] [CrossRef]
42. Ferreira FV, Souza AG, Ajdary R, de Souza LP, Lopes JH, Correa DS, et al. Nanocellulose-based porous materials: regulation and pathway to commercialization in regenerative medicine. Bioact Mater. 2023;29:151–76. doi:10.1016/j.bioactmat.2023.06.020. [Google Scholar] [PubMed] [CrossRef]
43. Kargarzadeh H, Huang J, Lin N, Ahmad I, Mariano M, Dufresne A, et al. Recent developments in nanocellulose-based biodegradable polymers, thermoplastic polymers, and porous nanocomposites. Prog Polym Sci. 2018;87:197–227. doi:10.1016/j.progpolymsci.2018.07.008. [Google Scholar] [CrossRef]
44. Etale A, Onyianta AJ, Turner SR, Eichhorn SJ. Cellulose: a review of water interactions, applications in composites, and water treatment. Chem Rev. 2023;123:2016–48. doi:10.1021/acs.chemrev.2c00477. [Google Scholar] [PubMed] [CrossRef]
45. Noremylia MB, Hassan MZ, Ismail Z. Recent advancement in isolation, processing, characterization and applications of emerging nanocellulose: a review. Int J Biol Macromol. 2022;206:954–76. doi:10.1016/j.ijbiomac.2022.03.064. [Google Scholar] [PubMed] [CrossRef]
46. Heidarian P, Kaynak A, Paulino M, Zolfagharian A, Varley RJ, Kouzani AZ. Dynamic nanocellulose hydrogels: recent advancements and future outlook. Carbohydr Polym. 2021;270:118357. doi:10.1016/j.carbpol.2021.118357. [Google Scholar] [PubMed] [CrossRef]
47. Chen Y, Duan Y, Zhao H, Liu K, Liu Y, Wu M, et al. Preparation of bio-based foams with a uniform pore structure by Nanocellulose/Nisin/Waterborne-Polyurethane-stabilized pickering emulsion. Polymers. 2022;14:5159. doi:10.3390/polym14235159. [Google Scholar] [PubMed] [CrossRef]
48. Putra BU, Hardiningtyas SD, Hastuti N, Ramadhan W, Uju, Alif Razi M, et al. Alginate hydrogel incorporating cellulose nanofiber from solid waste agar industry for hydrophobic antibiotic delivery: synthesis and characterization. Mater Today Commun. 2024;38:108248. doi:10.1016/j.mtcomm.2024.108248. [Google Scholar] [CrossRef]
49. Chatterjee S, Ke W-T, Liao Y-C. Elastic nanocellulose/graphene aerogel with excellent shape retention and oil absorption selectivity. J Taiwan Inst Chem Eng. 2020;111:261–9. doi:10.1016/j.jtice.2020.04.020. [Google Scholar] [CrossRef]
50. Chen L, Qu N, Lu H, Jiang S, Zhang B, Hasi Q-M, et al. Preparation of a magnetic core-shell bioreactor for oil/water separation and biodegradation. Langmuir. 2023;39:14891–903. doi:10.1021/acs.langmuir.3c01632. [Google Scholar] [PubMed] [CrossRef]
51. Gong X, Wang Y, Zeng H, Betti M, Chen L. Highly porous, hydrophobic, and compressible cellulose nanocrystals/poly(vinyl alcohol) Aerogels as recyclable absorbents for oil-water separation. ACS Sustainable Chem Eng. 2019;7:11118–28. doi:10.1021/acssuschemeng.9b00066. [Google Scholar] [CrossRef]
52. Zhang H, Zhao T, Chen Y, Hu X, Xu Y, Xu G, et al. A sustainable nanocellulose-based superabsorbent from kapok fiber with advanced oil absorption and recyclability. Carbohydr Polym. 2022;278:118948. doi:10.1016/j.carbpol.2021.118948. [Google Scholar] [PubMed] [CrossRef]
53. Zhao X, Shi Y, Niu S, Wei X, Liu T, Yang M, et al. Enhancing wound healing and bactericidal efficacy: a hydrogel membrane of bacterial cellulose and sanxan gel for accelerating the healing of infected wounds. Adv Healthc Mater. 2023;13:e2303216. doi:10.1002/adhm.202303216. [Google Scholar] [PubMed] [CrossRef]
54. Zhao X, Liao Z, Liu T, Cheng W, Gao G, Yang M, et al. Investigation of the transport and metabolic patterns of oil-displacing bacterium FY-07-G in the microcosm model using X-CT technology. J Appl Microbiol. 2023;134:107928. doi:10.1093/jambio/lxad281. [Google Scholar] [PubMed] [CrossRef]
55. Wang R, Fujie T, Itaya H, Wada N, Takahashi K. Force-induced alignment of nanofibrillated bacterial cellulose for the enhancement of cellulose composite macrofibers. Int J Mol Sci. 2024;25:69. doi:10.3390/ijms25010069. [Google Scholar] [PubMed] [CrossRef]
56. Feng Z, Wang S, Huang W, Bai W. A potential bilayer skin substitute based on electrospun silk-elastin-like protein nanofiber membrane covered with bacterial cellulose. Colloids Surf B: Biointerfaces. 2024;234:113677. doi:10.1016/j.colsurfb.2023.113677. [Google Scholar] [PubMed] [CrossRef]
57. Patel A, Patel P, Parmar M, Gosai H. Employing RSM and ANN-based applications for modelling enhanced bacterial cellulose production from pineapple peel waste using Komagateibacter saccharivorans APPK1. Chem Eng J. 2024;480:148057. doi:10.1016/j.cej.2023.148057. [Google Scholar] [CrossRef]
58. Rogova EA, Alashkevich YD, Kozhukhov VA, Lapin IR, Kiselev EG. State and prospects of improving the methods of production and use of bacterial cellulose (a review). Russ J Bioorg Chem. 2023;49:1536–52. doi:10.1134/S1068162023070841. [Google Scholar] [CrossRef]
59. Silviana S, Jannah T. The degradation rate of bio microbeads derived from cellulose and impregnated with moringa leaf flavonoids extract. Mater Sci Forum. 2023;1108:119–40. doi:10.4028/p-1N7dy6. [Google Scholar] [CrossRef]
60. Zhang K, Irmak S, Catchmark JM. Preparation and properties of heteroatom-doped bacterial cellulose-derived carbonaceous materials. Carbohydr Polym Technol Appl. 2023;6:100400. doi:10.1016/j.carpta.2023.100400. [Google Scholar] [CrossRef]
61. Men Y, Yang R, Yang X, Qin Z, Yin X. Preparation and characterization of quaternary bacterial cellulose composites for antimicrobial oil-absorbing materials. J Appl Polym Sci. 2023;141:446. doi:10.1002/app.55022. [Google Scholar] [CrossRef]
62. He X, Chen T, Jiang T, Wang C, Luan Y, Liu P, et al. Preparation and adsorption properties of magnetic hydrophobic cellulose aerogels based on refined fibers. Carbohydr Polym. 2021;260:117790. doi:10.1016/j.carbpol.2021.117790. [Google Scholar] [PubMed] [CrossRef]
63. Yan Z, Zhu K, Li X, Wu X. Recyclable bacterial cellulose aerogel for oil and water separation. J Polym Environ. 2022;30:2774–84. doi:10.1007/s10924-021-02369-y. [Google Scholar] [CrossRef]
64. He J, Zhao H, Li X, Su D, Zhang F, Ji H, et al. Superelastic and superhydrophobic bacterial cellulose/silica aerogels with hierarchical cellular structure for oil absorption and recovery. J Hazard Mater. 2018;346:199–207. doi:10.1016/j.jhazmat.2017.12.045. [Google Scholar] [PubMed] [CrossRef]
65. Li J, Lu S, Liu F, Qiao Q, Na H, Zhu J. Structure and properties of regenerated cellulose fibers based on dissolution of cellulose in a CO2 switchable solvent. ACS Sustainable Chem Eng. 2021;9:4744–54. doi:10.1021/acssuschemeng.0c08907. [Google Scholar] [CrossRef]
66. Chen G, Hong FF, Yuan J, Li L, Fang M, Wei W, et al. Super solvent of cellulose with extra high solubility for tunable cellulose structure with versatile application. Carbohydr Polym. 2022;296:119917. doi:10.1016/j.carbpol.2022.119917. [Google Scholar] [PubMed] [CrossRef]
67. Przypis M, Wawoczny A, Gillner D. Biomass and cellulose dissolution—the important issue in renewable materials treatment. Appl Sci. 2023;13:1055. doi:10.3390/app13021055. [Google Scholar] [CrossRef]
68. Fan W, Wang Y, Liu R, Zou J, Cai W, Cheng J, et al. Weldable and calligraphy programmable humidity-actuated regenerated cellulose film from waste cotton fabric. J Clean Prod. 2024;434:140092. doi:10.1016/j.jclepro.2023.140092. [Google Scholar] [CrossRef]
69. Tu H, Li X, Liu Y, Luo L, Duan B, Zhang R. Recent progress in regenerated cellulose-based fibers from alkali/urea system via spinning process. Carbohydr Polym. 2022;296:119942. doi:10.1016/j.carbpol.2022.119942. [Google Scholar] [PubMed] [CrossRef]
70. Slejko EA, Tuan A, Scuor N. From waste to value: characterization of recycled cellulose acetate for sustainable waste management. Waste Manage Bull. 2024;1:67–73. doi:10.1016/j.wmb.2023.10.001. [Google Scholar] [CrossRef]
71. Vallejos ME, Olmos GV, Taleb MC, Felissia FE, Ehman NV, Peresin MS, et al. Dissolving pulp from eucalyptus sawdust for regenerated cellulose products. Cellulose. 2022;29:4645–59. doi:10.1007/s10570-022-04581-y. [Google Scholar] [CrossRef]
72. He S, Li J, Cao X, Xie F, Yang H, Wang C, et al. Regenerated cellulose/chitosan composite aerogel with highly efficient adsorption for anionic dyes. Int J Biol Macromol. 2023;244:125067. doi:10.1016/j.ijbiomac.2023.125067. [Google Scholar] [PubMed] [CrossRef]
73. Zhang Q, Cheng Y, Fang C, Shi J. Construction of novel regenerated cellulose based foam derived from waste cigarette filters as effective oil adsorbent. J Appl Polym Sci. 2022;139:51900. doi:10.1002/app.51900. [Google Scholar] [CrossRef]
74. Du Q, Yu J, Xu X, Xia L, Zhuang X. High porosity and hydrophobic cellulosic sponges for oil absorption. Fibers Polym. 2023;24:885–92. doi:10.1007/s12221-023-00098-8. [Google Scholar] [CrossRef]
75. Xu F, Cho B-U. Preparation of porous regenerated cellulose microstructures via emulsion-coagulation technique. Cellulose. 2022;29:1527–42. doi:10.1007/s10570-022-04428-6. [Google Scholar] [CrossRef]
76. Ma X, Zhou S, Li J, Xie F, Yang H, Wang C, et al. Natural microfibrils/regenerated cellulose-based carbon aerogel for highly efficient oil/water separation. J Hazard Mater. 2023;454:131397. doi:10.1016/j.jhazmat.2023.131397. [Google Scholar] [PubMed] [CrossRef]
77. Xu X, Dong F, Yang X, Liu H, Guo L, Qian Y, et al. Preparation and characterization of cellulose grafted with epoxidized soybean oil aerogels for oil-absorbing materials. J Agric Food Chem. 2019;67:637–43. doi:10.1021/acs.jafc.8b05161. [Google Scholar] [PubMed] [CrossRef]
78. Setyawan H, Fauziyah M, Tomo HSS, Widiyastuti W, Nurtono T. Fabrication of hydrophobic cellulose aerogels from renewable biomass coir fibers for oil spillage clean-up. J Polym Environ. 2022;30:5228–38. doi:10.1007/s10924-022-02591-2. [Google Scholar] [CrossRef]
79. Li Z, Shao L, Hu W, Zheng T, Lu L, Cao Y, et al. Excellent reusable chitosan/cellulose aerogel as an oil and organic solvent absorbent. Carbohydr Polym. 2018;191:183–90. doi:10.1016/j.carbpol.2018.03.027. [Google Scholar] [PubMed] [CrossRef]
80. Liu C-H, Shang J-P, Su X, Zhao S, Peng Y, Li Y-B. Fabrication of superhydrophobic/superoleophilic bamboo cellulose foam for oil/water separation. Polymers. 2022;14:5162. doi:10.3390/polym14235162. [Google Scholar] [PubMed] [CrossRef]
81. Lang D, Zhang C, Qian Q, Guo C, Wang L, Yang C, et al. Oil absorption stability of modified cellulose porous materials with super compressive strength in the complex environment. Cellulose. 2023;30:7745–62. doi:10.1007/s10570-023-05322-5. [Google Scholar] [CrossRef]
82. Tsurkan MV, Voronkina A, Khrunyk Y, Wysokowski M, Petrenko I, Ehrlich H. Progress in chitin analytics. Carbohydr Polym. 2021;252:117204. doi:10.1016/j.carbpol.2020.117204. [Google Scholar] [PubMed] [CrossRef]
83. Khajavian M, Vatanpour V, Castro-Muñoz R, Grzegorz B. Chitin and derivative chitosan-based structures-Preparation strategies aided by deep eutectic solvents: a review. Carbohydr Polym. 2022;275:118702. doi:10.1016/j.carbpol.2021.118702. [Google Scholar] [PubMed] [CrossRef]
84. Li S-L, Wang Y-T, Liu B-W, Shi H-G, Zhao H-B, Wang Y-Z. Fe3O4@PANI/chitosan composite aerogel with electromagnetic induction heating capacity toward efficient removing viscous oil. Compos Commun. 2022;36:101367. doi:10.1016/j.coco.2022.101367. [Google Scholar] [CrossRef]
85. Si R, Luo H, Zhang T, Pu J. High hydrophobic ZIF-8@cellulose nanofibers/chitosan double network aerogel for oil adsorbent and oil/water separation. Int J Biol Macromol. 2023;238:124008. doi:10.1016/j.ijbiomac.2023.124008. [Google Scholar] [PubMed] [CrossRef]
86. Yin Z, Liu W, Bao M, Li Y. Magnetic chitosan-based aerogel decorated with polydimethylsiloxane: a high-performance scavenger for oil in water. J Appl Polym Sci. 2021;138:50461. doi:10.1002/app.50461. [Google Scholar] [CrossRef]
87. Wang C, Qiu C, Zhan C, McClements DJ, Qin Y, Jiao A, et al. Green preparation of robust hydrophobic β-cyclodextrin/chitosan sponges for efficient removal of oil from water. Langmuir. 2021;37:14380–9. doi:10.1021/acs.langmuir.1c02299. [Google Scholar] [PubMed] [CrossRef]
88. Su C, Yang H, Zhao H, Liu Y, Chen R. Recyclable and biodegradable superhydrophobic and superoleophilic chitosan sponge for the effective removal of oily pollutants from water. Chem Eng J. 2017;330:423–32. doi:10.1016/j.cej.2017.07.157. [Google Scholar] [CrossRef]
89. Yi L, Yang J, Fang X, Xia Y, Zhao L, Wu H, et al. Facile fabrication of wood-inspired aerogel from chitosan for efficient removal of oil from water. J Hazard Mater. 2020;385:121507. doi:10.1016/j.jhazmat.2019.121507. [Google Scholar] [PubMed] [CrossRef]
90. Kordjazi S, Kamyab K, Hemmatinejad N. Super-hydrophilic/oleophobic chitosan/acrylamide hydrogel: an efficient water/oil separation filter. Adv Compos Hybrid Mater. 2020;3:167–76. doi:10.1007/s42114-020-00150-8. [Google Scholar] [CrossRef]
91. Guan Y, Qiao D, Dong L, Chen X, Wang Z, Li Y. Efficient recovery of highly viscous crude oil spill by superhydrophobic ocean biomass-based aerogel assisted with solar energy. Chem Eng J. 2023;467:143532. doi:10.1016/j.cej.2023.143532. [Google Scholar] [CrossRef]
92. Jiang F, Li T, Li Y, Zhang Y, Gong A, Dai J, et al. Wood-based nanotechnologies toward sustainability. Adv Mater Deerfield. 2018;30:1703453. doi:10.1002/adma.201703453. [Google Scholar] [PubMed] [CrossRef]
93. Chen C, Hu L. Nanoscale ion regulation in wood-based structures and their device applications. Adv Mater Deerfield. 2021;33:2002890. doi:10.1002/adma.202002890. [Google Scholar] [PubMed] [CrossRef]
94. Fang Y, Jing C, Li G, Ling S, Wang Z, Lu P, et al. Wood-derived systems for sustainable oil/water separation. Adv Sustain Syst. 2021;5:2100039. doi:10.1002/adsu.202100039. [Google Scholar] [CrossRef]
95. Zhu Y, Li H, Huang W, Lai X, Zeng X. Facile fabrication of superhydrophobic wood aerogel by vapor deposition method for oil-water separation. Surf Interfaces. 2023;37:102746. doi:10.1016/j.surfin.2023.102746. [Google Scholar] [CrossRef]
96. Zhao M, Tao Y, Wang J, He Y. Facile preparation of superhydrophobic porous wood for continuous oil-water separation. J Water Process Eng. 2020;36:101279. doi:10.1016/j.jwpe.2020.101279. [Google Scholar] [CrossRef]
97. Chen Z, Su X, Wu W, Zhou J, Wu T, Wu Y, et al. Superhydrophobic PDMS@GSH wood with Joule heat and photothermal effect for viscous crude oil removal. Carbon. 2023;201:577–86. doi:10.1016/j.carbon.2022.09.014. [Google Scholar] [CrossRef]
98. Chen Z, Su X, Wu W, Chen S, Zhang X, Wu Y, et al. Superhydrophobic PDMS@TiO2 wood for photocatalytic degradation and rapid oil-water separation. Surf Coat Technol. 2022;434:128182. doi:10.1016/j.surfcoat.2022.128182. [Google Scholar] [CrossRef]
99. Wang K, Liu X, Tan Y, Zhang W, Zhang S, Li J. Two-dimensional membrane and three-dimensional bulk aerogel materials via top-down wood nanotechnology for multibehavioral and reusable oil/water separation. Chem Eng J. 2019;371:769–80. doi:10.1016/j.cej.2019.04.108. [Google Scholar] [CrossRef]
100. Du B, Li B, Yang K, Chao Y, Luo R, Zhou S, et al. Superhydrophobic wood sponge with intelligent pH responsiveness for efficient and continuous oil-water separation. Mater Res Express. 2023;10:55101. doi:10.1088/2053-1591/acd5ad. [Google Scholar] [CrossRef]
101. Cai Y, Yu Y, Wu J, Wang K, Dong Y, Qu J, et al. Durable, flexible, and super-hydrophobic wood membrane with nanopore by molecular cross-linking for efficient separation of stabilized water/oil emulsions. EcoMat. 2022;4:e12255. doi:10.1002/eom2.12255. [Google Scholar] [CrossRef]
102. Ma T, Li L, Mei C, Wang Q, Guo C. Construction of sustainable, fireproof and superhydrophobic wood template for efficient oil/water separation. J Mater Sci. 2021;56:5624–36. doi:10.1007/s10853-020-05615-1. [Google Scholar] [CrossRef]
103. Zhang M, Shi L, Du X, Li Z, Shi Y, An C, et al. Janus mesoporous wood-based membrane for simultaneous oil/water separation, aromatic dyes removal, and seawater desalination. Ind Crops Prod. 2022;188:115643. doi:10.1016/j.indcrop.2022.115643. [Google Scholar] [CrossRef]
104. Cheng Z, Guan H, Meng J, Wang X. Dual-functional porous wood filter for simultaneous oil/water separation and organic pollutant removal. ACS Omega. 2020;5:14096–103. doi:10.1021/acsomega.0c01606. [Google Scholar] [PubMed] [CrossRef]
105. Hu D, Zhang Z, Li W, Qin X, Zhang R, Yuan L, et al. Promoting adsorption performance and mechanical strength in composite porous gel film. Int J Biol Macromol. 2022;223:1115–25. doi:10.1016/j.ijbiomac.2022.11.131. [Google Scholar] [PubMed] [CrossRef]
106. Jiang Y, Junejo SA, Jia X, Zhang B, Fu X, Huang Q. Amylose content and pre-freezing regulate the structure and oil absorption of polyelectrolytes-based starch cryogel. Carbohydr Polym. 2023;302:120386. doi:10.1016/j.carbpol.2022.120386. [Google Scholar] [PubMed] [CrossRef]
107. Wang F, Ma R, Tian Y. Superhydrophobic starch-based adsorbent with honeycomb coral-like surface fabricated via facile immersion process for removing oil from water. Int J Biol Macromol. 2022;207:549–58. doi:10.1016/j.ijbiomac.2022.03.045. [Google Scholar] [PubMed] [CrossRef]
108. Chen H, Yang J, Su J, Cui Y. Facile fabrication of biobased porous material via the photocuring technique and a template-assisted approach for oil/water separation. Sep Purif Technol. 2022;303:122239. doi:10.1016/j.seppur.2022.122239. [Google Scholar] [CrossRef]
109. Lu J, Cui C, Yu Q, Su J, Han J. Robustly superhydrophobic polylactic acid nonwoven membranes for efficient oil/water separation. J Porous Mater. 2022;29:241–7. doi:10.1007/s10934-021-01160-7. [Google Scholar] [CrossRef]
110. Zhang Y, Zhang Y, Cao Q, Wang C, Yang C, Li Y, et al. Novel porous oil-water separation material with super-hydrophobicity and super-oleophilicity prepared from beeswax, lignin, and cotton. Sci Total Environ. 2020;706:135807. doi:10.1016/j.scitotenv.2019.135807. [Google Scholar] [PubMed] [CrossRef]
111. Li K, Luo Q, Xu J, Li K, Zhang W, Liu L, et al. A novel freeze-drying-free strategy to fabricate a biobased tough aerogel for separation of oil/water mixtures. J Agric Food Chem. 2020;68:3779–85. doi:10.1021/acs.jafc.9b07629. [Google Scholar] [PubMed] [CrossRef]
112. Li H, Zhang H, Hu J-J, Wang G-F, Cui J-Q, Zhang Y-F, et al. Facile preparation of hydrophobic PLA/PBE micro-nanofiber fabrics via the melt-blown process for high-efficacy oil/water separation. Polymers. 2022;14:1667. doi:10.3390/polym14091667. [Google Scholar] [PubMed] [CrossRef]
113. Mo J, Wang Y, Wang J, Zhao J, Ke Y, Han S, et al. Hydrophobic/oleophilic polylactic acid electrospun fibrous membranes with the silicone semi-interpenetrated networks for oil-water separation. J Mater Sci. 2022;57:16048–63. doi:10.1007/s10853-022-07634-6. [Google Scholar] [CrossRef]
Cite This Article
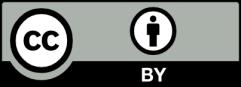
This work is licensed under a Creative Commons Attribution 4.0 International License , which permits unrestricted use, distribution, and reproduction in any medium, provided the original work is properly cited.