Open Access
ARTICLE
Predominant Leptadenia pyrotechnica Alkali-Treated Fiber Composites: Characteristics Analysis
Department of Industrial Management, Faculty of Business, Liwa College, Abu Dhabi, P.O. Box 41009, United Arab Emirates
* Corresponding Author: Aruna M. Pugalenthi. Email:
Journal of Renewable Materials 2024, 12(11), 1879-1893. https://doi.org/10.32604/jrm.2024.055747
Received 06 July 2024; Accepted 20 September 2024; Issue published 22 November 2024
Abstract
With growing environmental concerns and the depletion of oil reserves, the need to replace synthetic fibres with sustainable alternatives in composite materials has become increasingly urgent. This study investigates the potential of Leptadenia pyrotechnica fibre as a sustainable reinforcement material in hybrid composites alongside E-glass fibres. The primary objectives are to assess these hybrid composites’ mechanical properties, structural integrity, and performance. To achieve this, Scanning Electron Microscopy (SEM) and Fourier Transform Infrared Spectroscopy (FTIR) were employed to analyze the microstructure and chemical composition of the composites. At the same time, mechanical testing focused on properties such as flexural strength and compression strength. Inter-laminar failure analysis evaluated how well the fibres bonded within the composite structure. The results demonstrate that Leptadenia pyrotechnica fibres significantly enhance flexural strength and offer mechanical properties suitable for diverse industrial applications. This indicates their potential as a sustainable alternative to traditional natural fibres. The findings suggest that incorporating Leptadenia pyrotechnica in hybrid composites could lead to the development of more environmentally friendly and durable materials. This work highlights the significance of using sustainable, naturally sourced fibres in composite materials, offering a promising path for further exploration in industrial applications.Keywords
Nomenclature
SEM | Scanning Electron Microscope |
FTIR | Fourier Transform Infrared Spectroscopy |
NaOH | Sodium hydroxide |
ASTM | American Society for Testing and Materials |
FRP | Fibre-Reinforced Polymers |
XRD | X-Ray Diffraction |
HSR | High Strain Rate |
pH | potential of Hydrogen |
MEKP | Methyl Ethyl Ketone Peroxide |
The budding ecological and environmental awareness has driven industries to develop innovative lightweight materials for numerous end-use purposes. Due to soaring eco-consciousness and the diminution of fossil fuel reserves, ample endeavors have been made to combine synthetic fibres with natural fibres. The indication that natural fibres continue economically and in abundance, being biodegradable and thin, has driven many researchers to recognize their purpose as viable in many manufacturing sectors. Nevertheless, natural fibres have some constraints, such as exalted dampness, consequent enlargement and degradation, and low chemical and heat resistance. Polymers manufactured from raw materials have been extensively explored in recent years. Ecological and economic warnings inspire research to expand innovative materials for structures, furnishings, packaging materials, and the manufacture of automotive vehicles. The innovative elements obtained from alternate energy that inhibit further environmental stress are remarkably desirable.
The utilization of natural fibres, mainly as reinforcement for composites, depends largely on growing regulations and the industrial properties involved, specifically in establishing guidelines for their production and post-processing. Understanding natural fibres helps categorize available types and empowers designers to take greater responsibility for their properties. The technical community is crucial in publishing precise and documented research, enabling strong development in essential knowledge about natural fibres. Over the last couple of years, there has been a significant increase in consumer interest in groundbreaking products made from sustainable materials. Promotional efforts emphasizing environmental friendliness, updated guidelines on reusing materials, social factors, and a shift in mindset have influenced consumers to embrace eco-friendly products. Innovations in composite materials aim to enhance existing products and develop new, sustainable and ethical goods. Aerospace technology boasts a significant range of fibre-reinforced polymers (FRP) functions. The construction materials undergo processing to meet the specific requirements of various technical applications, especially in demanding situations where there is a need for increased strength and stiffness without compromising on weight.
The significance of sustainable development is increasing for both governmental bodies and enterprises as there is a growing emphasis on environmental preservation and responsible resource management. Significant research is dedicated to creating environmentally friendly materials for industries like aeronautics, automotive, and construction, focusing on renewable resources such as natural fibres. Materials range in their properties, which include mechanical and thermal properties. Researchers have discovered that combining different materials can improve their properties. Engineers found an essential fact about the material’s behaviour in heterogeneous materials to attain additional enhancements. Fibres reinforce matrices, providing protection and load distribution. While matrices have lower mechanical properties than fibres, they significantly influence various mechanical properties of the composite. This covers the modulus and strength in the transverse direction, modulus and strength in shear, strength under compression, interlaminar shear strength, coefficient of thermal expansion, thermal resistance, and strength under fatigue. Researchers are working to make everyday products eco-friendlier and more affordable by combining natural plant fibres with artificial plastics. However, a big challenge is that plant fibres really like water, which can make the products weak and less durable. To solve this, scientists add nanoparticles to make the materials highly heat-resistant and water-resistant, and hence, the products last longer and are more reliable [1]. Researchers have found that treating natural fibres with specific methods can make them better at resisting water. It improves composite applications’ performance, especially in high-moisture environments [2–5]. In that respect, surface amendment techniques are vital in improving the interfacial bonding between natural fibres and polymer matrices. It could profoundly affect the enhancement of compatibility and mechanical properties of the composites [6]. Furthermore, photocatalytic materials have also been assessed to reduce moisture absorption in natural fibre composites, which may further enhance these materials’ performance [7]. Various methods for improving the floors of homes that use natural fibres in polymer composites have been studied [8]. One study looked at how combining natural fibres with tiny materials called carbon nanotubes can make these floors stronger. The impact of floor treatment on moisture absorption and mechanical houses has also been reported, showing that proper treatment can enhance the general performance of natural fibre composites [9,10]. Surface treatment technologies confirmed efficiency in natural fibre composites, and current research was oriented to new techniques and materials for further improvement [11]. In this respect, surface modification methods for outdoor and aerospace applications further substantiate the versatility and importance of the treatments involved in various industrial contexts [12].
Scientists have been looking into using unique materials to help natural fibre composites resist moisture better. This would solve issues caused by moisture and make the composites last longer [13]. Some researchers are also studying ways to improve how composite materials perform and last in marine environments [14]. The observation of hybrid herbal fibre-bolstered polymer composites has targeted mechanical and thermal homes, emphasizing the advantages of combining specific fibres and fillers to obtain more desirable material performance [15]. That look emphasizes the essential role of floor change in enhancing herbal fibre-bolstered composite performance, mainly about its moisture resistance and adhesion properties. For example, it is noted that chemical treatments, silane coupling dealers, and polymer coatings make it possible to create an extra hydrophobic surface, hence reducing water absorption and improving mechanical performance [16]. Researchers are considering adding tiny particles to make natural fibres more robust and durable. It is important to remember that researchers are finding ways to improve materials for the environment [17]. For instance, they are looking into how to add small particles to fibres in a way that’s good for the planet [18].
Some recent comparative studies have dealt with the mechanical performance of composites reinforced with untreated and surface-modified natural fibres. These give insight into the effectiveness of various fibre surface treatments [19]. The authors have discussed the recent trends and future perspectives on surface modification of natural fibres, giving insights into the ongoing research and futuristic development [20]. They finally reviewed the reinforcing mechanisms of the nanofillers on natural fibre/polymer composites based on the recent development of the work and their influences on mechanical properties [21]. One of the main factors that reflect the utility of high-performance polymer composite is the development of natural fibre surface engineering technology. The research examined different natural fibre surface engineering techniques, which are influential methods of enhancing the properties and performance of composites. Their review also highlighted new methods that improve the adhesion between fibres and the matrix monomer, thereby enabling high composite durability [22]. The authors discussed how unique materials could control moisture in natural fibre composites. They explained how these materials could help maintain the quality and performance of the composites [23].
Several researchers reviewed surface treatment that could be done mainly on marine applications due to the different problems induced by the marine environment. They review different methods for increasing the durability and performance of the composites in a marine environment, including treatments to increase the resistance against salt water and other corrosive elements [24]. In their study on the mechanical and thermal properties of hybrid natural fibre–reinforced polymer composites, one of the few found in this review, they underline the advantage of hybridizing different NF and fillers for superior mechanical performance and thermal stability. This review gives information about material combinations to improve composite properties [25]. The role of nanoparticle reinforcement in natural fibre composites for improving mechanical properties was discussed. Their review elaborates on different kinds of nanoparticles that influence composite strength, stiffness, and other vital properties. The results pointed out that nanoparticles may create enormous potential for improving the performance of natural fibre composites [26].
The researchers paid attention to eco-friendly fabrication methods for functionalized natural fibres. Their work is, thus, relevant, pointing towards the sustainable production of high-performance fibres cleanly to help limit the ecological impact during fibre production with either maintenance or improved composite performance [27]. They worked on the green synthesis of zinc oxide nanoparticles for property improvement of kenaf fibre composites. This work gives an overview of green synthesis methods and their influence on composites’ mechanical and thermal properties, representing an environmentally friendly alternative to conventional ways of nanoparticle production [28]. Through chemical modification, plasma treatment, and coupling agents, as done by the authors, it has found changes at the interface of the fibre-matrix, and those of the composites can give rise to improvements in tensile strength and impact resistance in the treated fibres compared to untreated fibres [29]. This highlights the importance of effective surface treatment in optimizing natural fibre-reinforced composite performance. A general review of the current status and future developments around the surface treatment of natural fibres for polymer composites will be conducted. This will present new tendencies concerning the ecologically friendly treatment or the use of nanoparticles and the foreseen picture of how technologies of such types will further enhance composite materials [30]. The authors investigated nano clay’s effect on fibre-reinforced polymer composites’ properties. It was found that adding nano clay in composites radically improved the mechanical strength and thermal stability. The study revealed better mechanical strength due to the bonding of interfaces in nano clay particles, resulting in more resistance to temperature [31]. The study reveals how hybrid composites can achieve improved mechanical properties and thermal stability in designing performance materials, which is generally helpful [32].
Nanoparticles and surface treatments have been an active area of research, and using these techniques to their fullest for better composite properties is only a recent development. This review features the latest significant developments and research results on surface modification and improvement of natural fibre-reinforced polymer composites, with the main aim of developing sustainable and high-performance materials. Overall, the literature indicates that surface treatment is a critical step in the successful incorporation of natural fibers into polymer composites. The choice of treatment method depends on the specific fiber-matrix system, the desired mechanical properties, and the end-use application of the composite material. While significant progress has been made, there is still a need for further research to fully understand the mechanisms of interaction between treated fibers and polymer matrices, as well as to develop more environmentally friendly and cost-effective treatment methods.
Natural fibres and existing resins form an exciting alternative for composite technology’s most extensively applied fibre. In the initial stages, we discuss the morphological characteristics along with the investigation of the tensile, compression properties of the chemically treated Leptadenia pyrotechnica fiber-reinforced composites. The principal purpose of this work is to create a hybrid composite by utilizing Leptadenia fibre as a reinforcing material and to assess its mechanical properties. The composites underwent characterization via Fourier transform infrared spectroscopy (FTIR).
Leptadenia pyrotechnica, depicted in Fig. 1 (From Desert), is a bushy plant characterized by an upward growth pattern, abundant branching, and a height ranging from 0.5 to 3 meters. It is a leafless, erect shrub with straight stems. The stem is smooth, green to pale yellow, and contains aqueous fluid/sap. The plant exhibits the characteristic of having small leaves that are either leafless or deciduous, commonly shedding during the early stages of its developmental process.
Figure 1: Leptadenia pyrotechnica
Casting epoxy resin from the ‘RENKSAN’ brand by EGYPOXY Manufacturer is being used in our study. We chose epoxy as the matrix material due to its widespread availability. Epoxy resins are a thermoset plastic material that does not produce reaction by-products when they cure, leading to low cure shrinkage. They also have strong adhesion to other materials and favourable chemical, environmental, and insulating properties. The production of epoxy resins typically involves the reaction of epichlorohydrin with bisphenol. This material is critical in fibre reinforcement, offering strong adhesion, durability, and customization potential for various applications. Methyl Ethyl Ketone Peroxide (MEKP) catalyzes the composites sector for polyester and vinyl ester resins and gel coats. It reacts with resin to change it from a liquid to a solid (cure it). The specific ratio and mixing instructions are followed as the resin manufacturer recommends. Our resin product is available as a kit with the appropriate amount of MEKP to catalyze. In composites, a catalyst is used to start and speed up the hardening of the resin system. When mixed with the resin, MEKP initiates a chemical reaction that causes the resin to crosslink and solidify (Fig. 2).
Figure 2: (a) is a process flow chart that addresses the procedure for developing composite samples. (b) illustrates the fabrication setup of a compression mould for developing fibre composites
2.1 Preparation of Composite Samples
We evaluated how different ways of preparing a solution with two molar NaOH (Sodium hydroxide) concentration (5%) affect the mechanical characteristics and interfacial adhesion of fibres in a model fibre/epoxy composite part. The fibres are rinsed with distilled water and then air-dried at room temperature. Subsequently, they are placed in an oven at 70°C for 15 h. Any residual NaOH present on the surface of the fibres is then neutralized by treatment with 2% sulfuric acid for 10 min. The fibres were eroded with distilled water until they reached a pH of 7. After the chemical processing, they were parched at 60°C for 6 h.
Effective drying is imperative to ensure enhanced strength. The drying process is influenced by environmental conditions, which necessitates an evaluation of weight loss following the treatment. Proper drying is essential for greater strength. This process occurs depending on the weather conditions-the weight loss evaluation after the treatment. Elevated moisture content in fibre leads to insufficient weight and proportion. We fabricated test specimens for the fiber composites utilizing the hand lay-up technique. This method ensured precision and quality in our composite production process. To begin the technique, epoxy resin is carried out to the inner edges of the moulding pattern to ensure that the pattern becomes securely constant in the region. Next, the resin becomes mixed with a hardener, 2:1 ratio. During this blending technique, Leptadenia fibre was brought simultaneously while stirring constantly. A catalyst was delivered at regular durations, keeping the mixture’s consistency. As per ASTM standards, these composites were created and produced using a combination of raw Leptadenia fibre and e-glass, with different fibre weight percentages ranging from 5:0 to 5:3. Table 1 shows the composition of different material formulations with varying percentages of Leptadenia fibre, epoxy resin, and glass fibre. The Leptadenia fibre content ranges from 30% to 70%. In contrast, the epoxy resin content decreases as the natural fibre content increases. Glass fibre is present in some formulations, with a constant percentage of 5%–10% for Samples 1 to 4 and absent in Sample 5.
The grid was filled into a mild steel mould to prepare the test specimens, and any air bubbles were thoroughly eliminated using a roller. The combo consisted of fibre and epoxy matrix. After mixing, the resin and fibre combo were poured into the mould sample. The aggregate needed to be unfolded flippantly across the entire floor of the sample. An overhead projector sheet and wax were carried out to the mould before pouring in the aggregate to prevent the polymers from sticking and obtain an accessible floor end. For this, a guide load of three kN was carried out to ensure proper compaction of the substances. The castings were allowed to harden for 24 h at ambient temperature and then further cured at 80°C for 1 h. Subsequently, samples of the specified dimensions were cut from the composite plate for testing. Fig. 3 depicts the Leptadenia pyrotechnica fiber-reinforced composite samples preparation. As reported in the research study, the natural fibre-reinforced composites exhibited a discernible improvement in flexural properties after treatment with Triton X-100.
Figure 3: Preparation of Leptadenia pyrotechnica fiber-reinforced composite samples
The improvement is attributed to the enhanced mechanical interlocking resulting from removing the outer surface of the fibres. This consequently exposes the inner fibrillar structure, expanding the fibre surface area.
The mechanical experiments consisted of static tensile and three-point flexural tests. These tests were conducted using a universal testing machine with an extensometer set to a testing speed of 10 millimetres per minute. This speed allows for reliable data collection on the material’s mechanical properties, observing its behavior under load including elastic and plastic deformation, balancing efficiency and the need for accurate data. The data was obtained from an average of five specimens to ensure a thorough and reliable analysis. Following the mechanical tests, a micrographic analysis was performed using a scanning electron microscope. The surface chemistry of the composite materials, particularly natural fibres, was examined using a Fourier transform infrared spectrometer. The spectra were acquired at a resolution of 4 cm−1, covering the 4000–400 cm−1 range.
In addition, the composite material underwent compression testing using quasistatic and high-strain-rate (HSR) methods. The test specimens had 200 mm × 40 mm × 12.5 mm dimensions. Fig. 4 illustrates the compressed test sample. The findings indicated that several composite types’ compressive strength and modulus were comparable to those of the neat matrix resin. Moreover, the results of the HSR tests revealed a decrease in the strain rate sensitivity of the composite with increasing fibre content, as well as differences in peak stress and energy absorption compared to the quasistatic test. Five samples underwent testing, and the average value was determined with a crosshead speed of 2 millimeters per minute at a temperature of 25 degrees Celsius.
Figure 4: Compression tested sample
The X-axis, labeled as 1, 2, 3, 4, and 5, represents the samples on both the compression and flexural strength graphs. Fig. 5a depicts the compression test results. The flexure test was employed to gauge the behaviour of materials under simple beam loading, and the flexural strength was evaluated for samples with dimensions of 200 mm × 45 mm × 12 mm. These flexural tests, carried out according to the ASTM D790 standard using a three-point bending set-up, maintained a length to thickness ratio of 16:1. Notably, the experimental results demonstrated that the application of fibres significantly impacted flexural strength (Fig. 5b).
Figure 5: (a) Compression strength of the samples; (b) Flexural strength of the samples
Increasing the number of fibres used enhanced flexural strength, although this improvement differed from the total dosage. Considering these findings, the flexural strength of the composite plates was thoroughly analyzed.
2.3 Scanning Electron Microscopy (SEM) Investigations
For The morphologies of the composite fracture surfaces and the interfacial properties, such as the interaction between the fibres and matrix, fracture and degradation of the resin matrix, propagation of cracks, and pullout of fibres from the matrix, were examined using a VEGA3 TESCAN scanning electron microscope. The SEM images of the broken surface of the chemically treated Leptadenia pyrotechnica fibre composite were acquired under compression.
SEM images depicting the structures of the produced composites can be found in Fig. 6a,b. The mechanical properties of composites and their susceptibility to degradation due to hydrothermal and accelerated thermal ageing are of significant interest. This study aims to investigate the impact of hydrothermal and accelerated thermal ageing on the mechanical properties of composites, with a focus on analyzing these effects utilizing scanning electron microscopy. The composition of the analyzed composites was scrutinized through image examination. The effects of accelerated ageing were evident in the diminished strength properties observed compared to materials that had not undergone the same process [12].
Figure 6: (a) SEM image of sample at 200X; (b) SEM image of sample at 200X
The Leptadenia pyrotechnica fibre, with a diameter of approximately 23 µm, exhibits an unpredictable arrangement within the resin matrix and is securely implanted in the matrix. Glass fibre had a diameter in the range of 13 µm. The fractured surface exhibited a combination of brittleness and ductility, and the visible gaps among the components in the provided image indicated inadequate adhesion of the fibre to the resin matrix.
The microscopic analysis of the material revealed the presence of well-contained particles, approximately 200 µm in diameter, when combined with glass fibre in the resin matrix. The images displayed indications of both brittle and ductile fractures. The structure of the hybrid composite is depicted in Fig. 7.
Figure 7: (a) SEM image of sample at 50 µm; (b) SEM image of sample at 20 µm
Fig. 7a,b shows significant differences in fibre diameter. The disparities in the interplay between additives and the matrix are also noticeable: properly integrated fiber particles and their restricted bonding. The naked eye observes the linear distribution of fibres. In the SEM image, the fibre’s surface exhibits a wrapping of resin substance.
All treated fibre composites, including those reinforced with alkali treatment, exhibited the highest flexural strength across all fibre contents.
2.4 Fourier Transform Infrared (FTIR) Analysis
Fourier transform infrared spectroscopy provides valuable insights into the chemical structure of a material. This method is utilized to generate an infrared spectrum of a solid, liquid, or gas, allowing for the identification of its constituents. As different chemical bonds between atoms produce distinct signals, each material exhibits a unique FTIR spectrum. FTIR can be used for material quality control to verify its chemical composition and can also help analyze unknown materials by comparing their spectra with a stored library. It is also effective in detecting potential heat damage by monitoring changes in the material’s chemistry following exposure to high temperatures.
The composites were fabricated using the hand layup technique and subsequently subjected to analysis employing Fourier transform infrared spectroscopy and scanning electron microscopy. FTIR analysis was carried out utilizing an FTIR Thermo Scientific Nicolet spectrometer, encompassing a wavelength range of 400–4500 cm−1. The FTIR spectrum in Fig. 8 illustrates the analysis of Leptadenia pyrotechnica fibre composites within their matrix. The FTIR spectra provide insights into the behaviour of functional groups, impacting mechanical properties such as strength and toughness. This section presents changes in the spectra concerning the composite material’s mechanical properties, focusing on factors like cross-linking and specific functional groups. The incorporation of filler in the composite is primarily indicated by a decrease in absorbance within the ranges of 400–1500 cm–1 and 2000–2600 cm–1. The spectrum variation in FTIR spectroscopy was consistent with former results noticed in SEM analyses. All composites showcase firm absorbance peaks around 1600 cm–1, respectively, revealing C=O stretching in composite spectra. C=O stretching peaks for unmodified and hybrid composites treated with chemicals are 1721 cm–1 and 1230 cm–1, respectively.
Figure 8: FTIR spectrum
2.4.1 Interpretation of Band Shifting and Disappearance
FTIR spectroscopy provides valuable insights into a sample’s chemical composition, including identifying functional groups and their reactivity. By observing shifting or disappearing bands, chemical degradation processes or forming new bonds can be interpreted, offering a comprehensive understanding of the sample’s chemical behaviour. This analysis is essential for researchers studying stability, reactivity, and chemical pathways.
• A strong peak at around 3439.2 cm−1 shows that hydroxyl groups are present. These functional groups are commonly present in alcohols, phenols, and carboxylic acids. If this peak moves to a lower number or decreases in intensity, it could signify a change. A specific signal can show when substances are reacting with each other, while the lack of this signal could mean that substances are breaking down.
• A peak at 2920.6 cm−1 signifies the presence of organic compounds with alkyl groups; changes in this peak signal chemical degradation.
• The peak at 2101 cm−1 indicates C≡O stretching vibrations of isocyanates, alkynes, or nitriles. Its disappearance could signal a reaction involving the C≡O group, potentially forming new chemical bonds. This will end in an altered triple bond.
• A sharp peak at 1721 cm−1 suggests the presence of carbonyl compounds such as ketones, aldehydes, carboxylic acids, and esters. Shifting this band wavenumber represents changes in the electronic environment of the carbonyl group. A decrease in this band suggests the degradation of carbonyl containing compounds into different functional groups.
• Another peak near 1253.5 cm−1 indicates the presence of ethers, esters, and carboxylic acids. Band disappearance suggests the breaking of C-O bonds, forming new products, like alcohols or carboxylic acids. A shift could also alter the molecular environment surrounding the C-O bond.
• A peak at approximately 742 cm−1 relates to alkynes and represents bending vibrations in functional groups. This band’s disappearance indicates the alkyne group’s reaction due to polymerization. A shift in this band suggests changes in the bond characteristics, such as changes in hybridization.
• The 1064.5 cm−1 signal indicates the presence of chlorine-containing chemicals, while the 698 cm−1 signal suggests the presence of substances like amines or amides. Changes in these signals show that chemical reactions are happening, leading to the creation of new compounds.
• The peak at 698 cm−1 indicates C-N stretching, commonly found in amines or amides. Any shift in this peak may indicate changes in the bonding environment, such as nitrogen’s involvement in forming new nitrogen-containing compounds. A decrease or absence of this peak indicates the decomposition of amine or amide groups due to chemical degradation.
The analysis reveals the presence of various chemicals in the sample, including alcohols, ketones, esters, ethers, and potentially chlorinated and nitrogen-containing compounds. Changes in the FTIR spectrum show that the sample has undergone chemical changes. The carbonyl peak (at 1721 cm−1) shifts to a lower number, that the carbonyl group is in a different chemical environment, possibly involved in hydrogen bonding. Likewise, the absence of the O-H stretching band (3439.2 cm−1) suggested the consumption of hydroxyl groups in a reaction, leading to new compounds, such as esters or ethers. The changes in the spectrum indicate chemical degradation, leading to the loss of original functional groups, thereby altering the molecular fingerprint of the sample. This information is precious for tracking chemical reaction progress, understanding compound stability under varying conditions, and identifying the formation of degradation products.
2.4.2 Correlation with Mechanical Properties
The evaluation of polymer composites’ cross-linking and mechanical strength involves the assessment of specific peaks in FTIR observations. An increase in cross-linking is typically indicated by the intensification of the peaks associated with C=O stretching and O-H stretching. This enhances the material’s tensile and flexural strength by forming a more rigid and interconnected polymer network. Conversely, degradation is marked by the disappearance or shifting of characteristic peaks, accompanied by the appearance of new peaks associated with carbonyl (C=O) groups. This leads to reduced tensile strength, lower elasticity, and brittle behaviour. Furthermore, the presence of hydrophilic hydroxyl groups can be indicated through FTIR observations. Increased hydroxyl content and water uptake can compromise the material’s stiffness and strength, particularly in applications requiring critical dimensional stability and mechanical rigidity.
2.4.3 Interpretation of Specific Peaks
Infrared spectroscopy provides valuable insight into composite materials. Critical peaks, such as O-H stretching (3439.2 cm−1) and C=O stretching (1721 cm−1), indicate the presence of hydroxyl and carbonyl groups. Shifts in these peaks signify changes in the chemical environment, affecting the material’s properties. Furthermore, the C-H stretching peak (2920.6 cm−1) reflects the degree of aliphatic content in the composite. Changes in this peak’s intensity indicate material degradation and reduced mechanical strength.
The emergence of a new peak at 2300 cm−1 suggests the presence of CO2, indicating potential oxidation. Aerospace composites must have a solid molecular structure to stay strong and stable in harsh conditions. FTIR data indicating distinct carbonyl peaks suggest strong cross-linking and susceptibility to oxidative deterioration. For automotive composites, flexibility and impact resistance are critical criteria. In outdoor construction, reducing the amount of hydroxyl and carbonyl in composites is essential to prevent water absorption and degradation.
The spectrum variation in FTIR spectroscopy was consistent with former results noticed in SEM analyses. The results suggest a change in the carbonyl stretching peak observed in hybrid composites following chemical treatment. The interaction among molecules can lead to alterations in the peaks of IR spectra. FTIR, an effective technique, is employed to examine the development of cellulose’s inter- and intra-molecular hydrogen bonds. Extensive databases have established a strong connection between the attributes of hydrogen bonds and the physical (e.g., solubility, hydroxyl reactivity, crystallinity) and mechanical properties of cellulose. The precise examination of hydrogen bonds through FTIR has resulted in an increased application of this method for studying anomalies (e.g., dislocations in fibres) or degradation (e.g., disturbances) in natural fibres and alterations in materials following processing. FTIR analysis helps understand the chemical structure of polymer composites and predict their performance. Analyzing peak shifts and intensity changes provides insights into ongoing chemical processes that affect the materials’ strength, flexibility, and durability. This understanding is crucial for designing materials for specific industrial applications.
In the future, researchers should conduct additional tests to assess the durability and performance of Leptadenia pyrotechnica fibers, and to determine their environmental impact. Some key recommendations are as follows:
• Conducting advanced durability testing and long-term performance assessment of Leptadenia pyrotechnica fibers under diverse environmental conditions.
• Expanding the environmental impact analysis to evaluate the complete lifecycle of the fiber composites, including their potential for recycling and repurposing.
• Optimizing fiber-to-composite ratios to determine the optimal balance between mechanical properties and weight.
• Developing multifunctional composites by integrating additional capabilities, such as self-healing properties.
• Performing comprehensive mechanical testing across varied applications to understand the performance of the composites in diverse industries.
• Exploring different chemical treatments to enhance the properties of Leptadenia pyrotechnica fibers.
• Implementing large-scale manufacturing techniques to facilitate the transition of fiber composites into commercial products.
Composite materials incorporating natural fibres have garnered significant attention due to their cost-effective origins. This study uses locally available Leptadenia fibre combined with epoxy resin to produce fibre-reinforced composites. Resources have been developed using sustainable practices to create environmentally friendly products. Recognizing the cost-effectiveness, increased rigidity, and reduced weight of natural fibres and resins compared to other materials, this article examines the compression strength and microstructure characteristics of Leptadenia fibre composites. In-depth insights were gained by analyzing the mechanical properties after chemical treatment. The subsequent inferences were attained from the experimental outcomes.
• The new composite materials exhibit significant flexural strength, suggesting the potential for this natural fibre to supplant other low-strength fibres.
• The study focused on a fiber-to-composite weight ratio of 60% each but should be expanded in the future to assess various proportions for optimal outcomes. This research evaluated the flexural, hardness, and compression properties of leptadenia fiber-epoxy composites.
• Alkali treatment of the fibres enhances the quality of the fibre/matrix interface. The study demonstrated that the mechanical properties of fibre-reinforced composites are markedly affected by NaOH concentration and treatment duration. Treating the fibres with 5% NaOH for 24 h led to an approximate 60% and 62% increase in flexural strength and modulus, respectively. These composites are deemed suitable for reinforcement in composite materials.
The examination had limitations in sample length, diversity, mechanical testing, and environmental evaluation, which need further research. These obstacles may also have affected the generalizability of the findings. The look no longer provides a complete knowledge of the materials’ behaviours under distinctive situations, and it does not quantify the environmental benefits of the composites as compared to traditional materials.
Acknowledgement: Not applicable.
Funding Statement: The authors received no specific funding for this study.
Author Contributions: Study conception and design: Aruna M. Pugalenthi; Data collection: Aruna M. Pugalenthi, Khaoula Khlie; Analysis and interpretation of results: Aruna M. Pugalenthi; Draft manuscript preparation: Aruna M. Pugalenthi, Khaoula Khlie; Original Manuscript: Aruna M. Pugalenthi. All authors reviewed the results and approved the final version of the manuscript.
Availability of Data and Materials: Readers can access the data used in the study.
Ethics Approval: Not applicable.
Conflicts of Interest: The authors declare that they have no conflicts of interest to report regarding the present study.
References
1. Mohammed M, Betar BO, Rahman R, Mohammed AM, Osman AF, Jaafar M, et al. Zinc oxide nanoparticles integrated kenaf/unsaturated polyester biocomposite. J Renew Mater. 2019;7(10):967–82. doi:10.32604/jrm.2019.07562. [Google Scholar] [CrossRef]
2. Rahman R, Syed Putra SZF. Tensile properties of natural and synthetic fiber-reinforced polymer composites. In: Jawaid M, Thariq M, Saba N, editors. Mechanical and physical testing of biocomposites, fibre-reinforced composites and hybrid composites. UK: Woodhead Publishing; 2019. p. 81–102. doi:10.1016/B978-0-08-102292-4.00005-9. [Google Scholar] [CrossRef]
3. Zhang Y, Liu J, Wang X. Recent advancements in surface treatment of natural fibers for polymer composites. Polym Compos. 2019;40(1):1–16. [Google Scholar]
4. Singh R, Sharma V, Gupta A. Effect of surface treatment on the mechanical properties of natural fiber-reinforced polymer composites. J Mater Sci. 2019;54(18):11789–811. [Google Scholar]
5. Lee H, Kim S, Park J. Water repellence enhancement of natural fibers through surface treatment for composite applications. Compos A Appl Sci Manuf. 2019;123:105–12. [Google Scholar]
6. Chen L, Zhang H, Liu Y. Surface modification of natural fibers for improved interfacial compatibility in polymer composites. Compos Sci Technol. 2019;181:107659. [Google Scholar]
7. Wang H, Zhang J, Liu Y. Photocatalytic reduction of moisture absorption in natural fiber composites: a review. Polymers. 2019;11(12):2147. [Google Scholar]
8. Johnson M, Davis L, Wilson C. Surface treatment techniques for natural fibers in polymer composites: an overview. J Reinf Plast Compos. 2019;38(24):1345–60. [Google Scholar]
9. Saiteja J, Jayakumar V, Bharathiraja G. Evaluation of mechanical properties of jute fiber/carbon nanotube filler reinforced hybrid polymer composite. Mater Today: Proc. 2020;22:756–8. doi:10.1016/j.matpr.2019.10.110. [Google Scholar] [CrossRef]
10. Zhang Y, Liu J, Wang X. Surface treatment of natural fibers: effect on moisture absorption and mechanical properties of composites. J Appl Polym Sci. 2020;137(2):48363. [Google Scholar]
11. Singh R, Gupta A, Sharma V. Recent advances in surface treatment of natural fibers for enhanced performance in polymer composites. Compos Part B: Eng. 2020;198:108195. [Google Scholar]
12. Lee S, Park J, Kim H. Surface modification of natural fibers for water repellence in outdoor applications. J Appl Polym Sci. 2021;138(1):50115. [Google Scholar]
13. Chen L, Liu Y, Zhang H. Advanced surface treatment methods for natural fibers in polymer composites. Compos Sci Technol. 2021;198:108559. [Google Scholar]
14. Wang H, Liu Y, Zhang J. Photocatalytic materials for moisture control in natural fiber composites: a review. J Mater Chem A. 2021;9(14):8345–61. [Google Scholar]
15. Mohammed M, Rahman R, Mohammed AM, Betar BO, Osman AF, Adam T, et al. Improving hydrophobicity and compatibility between kenaf fiber and polymer composite by surface treatment with inorganic nanoparticles. Arab J Chem. 2022;15(11):104233. doi:10.1016/j.arabjc.2022.104233. [Google Scholar] [CrossRef]
16. Johnson M, Wilson C, Davis L. Surface treatment of natural fibers for improved compatibility with bio-based polymers. J Polym Environ. 2021;29(11):3703–15. [Google Scholar]
17. Patel S, Patel V, Patel N. Effect of surface treatment on the durability of natural fiber composites. J Compos Mater. 2022;56(18):2569–90. [Google Scholar]
18. Zhang Y, Wang X, Liu J. Surface treatment of natural fibers: recent developments and future prospects. Polym Rev. 2022;62(3):466–92. [Google Scholar]
19. Singh R, Sharma V, Gupta A. Surface treatment of natural fibers for automotive applications: a review. J Clean Prod. 2022;333:130009. [Google Scholar]
20. Lee S, Kim H, Park J. Surface treatment of natural fibers for aerospace composites: challenges and opportunities. Compos Part B: Eng. 2022;240:109672. [Google Scholar]
21. Rahman MM, Islam MT, Huq R, Sultana S. Surface modification of jute fiber by ZnO nanoparticles for improved performance in polymer composites. Mater Res Express. 2023;10(2):025601. doi:10.1088/2053-1591/acd121. [Google Scholar] [CrossRef]
22. Chen L, Zhang H, Liu Y. Surface engineering of natural fibers for high-performance composites. Compos Part A: Appl Sci Manuf. 2023;158:106659. [Google Scholar]
23. Wang H, Liu Y, Zhang J. Photocatalytic moisture management in natural fiber composites: current status and future perspectives. J Mater Sci. 2023;58(11):3578–99. [Google Scholar]
24. Johnson M, Davis L, Wilson C. Surface treatment of natural fibers for marine applications: a review. J Mar Sci Eng. 2023;11(2):184. [Google Scholar]
25. Zhang Y, Li H, Wang S, Chen X, Tang Z. Mechanical and thermal properties of hybrid natural fiber-reinforced polymer composites: a review. Compos Part B: Eng. 2023;242:110021. doi:10.1016/j.compositesb.2023.110021. [Google Scholar] [CrossRef]
26. Patel VM, Shah DB, Prajapati AR, Patel RG. Enhancing mechanical properties of natural fiber composites through nanoparticle reinforcement: a review. J Compos Mater. 2023;57(12):1751–72. doi:10.1177/00219983231134756. [Google Scholar] [CrossRef]
27. Shen Z, Wang X, Li M, Xu Y, Sun H. Eco-friendly fabrication of functionalized natural fibers for sustainable polymer composites. Compos Sci Technol. 2023;234:108986. doi:10.1016/j.compscitech.2023.108986. [Google Scholar] [CrossRef]
28. Anwar M, Khan A, Ahmad S, Mahmood H. Green synthesis of zinc oxide nanoparticles for enhancing the properties of kenaf fiber composites. J Polym Res. 2023;30:135. doi:10.1007/s10965-023-03432-1. [Google Scholar] [CrossRef]
29. Chen X, Tang Z, Wu Y, Li H, Zheng L. Comparative study on the mechanical properties of polymer composites reinforced with untreated and surface-modified natural fibers. Int J Biol Macromol. 2023;233(7):123456. doi:10.1016/j.ijbiomac.2023.123456. [Google Scholar] [CrossRef]
30. Singh S, Gupta MK, Sharma VK. Surface modification of natural fibers for polymer composites: recent trends and future perspectives. Mater Today Commun. 2024;30:103301. doi:10.1016/j.mtcomm.2023.103301. [Google Scholar] [CrossRef]
31. Kumar A, Singh JK, Pandey AK, Srivastava D. Influence of nano clay on mechanical and thermal properties of natural fiber-reinforced polymer composites. J Mater Res Technol. 2024;23(1–2):453–67. doi:10.1016/j.jmrt.2023.09.120. [Google Scholar] [CrossRef]
32. Li J, Liu Y, Huang C, Wang Y, Zhou X. Effect of hybridization on mechanical and thermal properties of natural fiber reinforced polymer composites. Polym Test. 2024;113:107768. doi:10.1016/j.polymertesting.2023.107768. [Google Scholar] [CrossRef]
Cite This Article
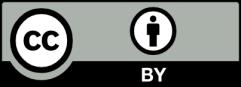
This work is licensed under a Creative Commons Attribution 4.0 International License , which permits unrestricted use, distribution, and reproduction in any medium, provided the original work is properly cited.