Open Access
REVIEW
Oil Palm Fiber Hybrid Composites: A Recent Review
1 Biomass Technology Unit, Engineering and Processing Division, Malaysian Palm Oil Board (MPOB), 6, Persiaran Institusi, Bandar Baru Bangi, Kajang, Selangor, 43000, Malaysia
2 Department of Chemical Engineering, Faculty of Chemical and Energy Engineering, Universiti Teknologi Malaysia, Johor, 81310, Malaysia
* Corresponding Authors: H. A. Aisyah. Email: ; R. A. Ilyas. Email:
Journal of Renewable Materials 2024, 12(10), 1661-1689. https://doi.org/10.32604/jrm.2024.055217
Received 20 June 2024; Accepted 30 August 2024; Issue published 23 October 2024
Abstract
Composite materials from oil palm fiber enhance sustainability by utilizing renewable resources, reducing dependence on non-renewable materials, and lessening environmental impact. Despite their mechanical and dimensional stability limitations, oil palm fiber-based polymer composites offer significant advantages, such as natural abundance, potential weight reduction, and cost-effectiveness due to local availability and renewability. The growing interest in oil palm hybrid composites, made from blending different fibers, is due to their customizable mechanical and physical properties. Hybridization is one of the most effective methods to reinforce and improve the performance of oil palm-derived composite materials. This review investigates the structural qualities of hybrid composites made from oil palm fibers, their suitability for diverse applications, and recent advancements in the field. By focusing on the availability, properties, applications, challenges, and future directions of oil palm fiber hybrid composites, this review highlights the potential of these materials to enhance mechanical and functional properties, thereby contributing to sustainable development and innovation in composite materials.Graphic Abstract
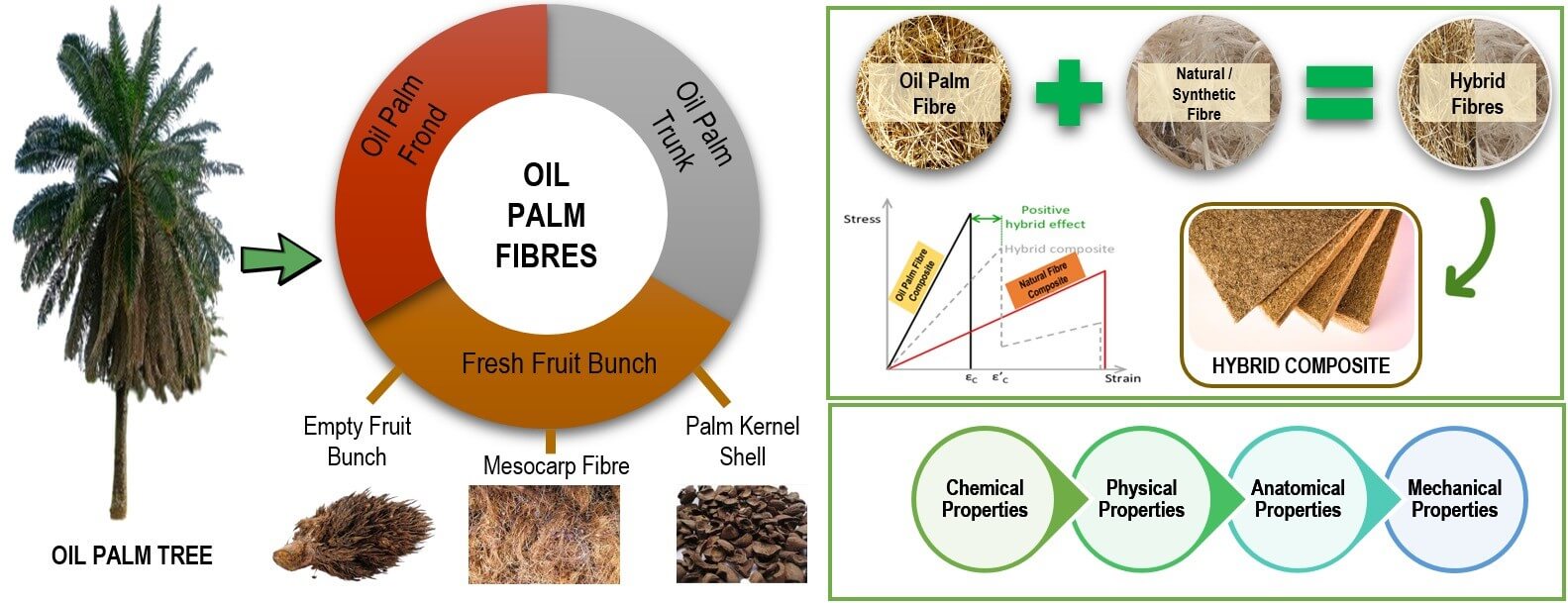
Keywords
Composite materials typically involve the merging of different elements to create a new material with enhanced properties. These composites are composed of a combination of fibers, particles, or other constituents embedded within a matrix material. Biocomposites or natural fiber composites (NFCs) emphasize the incorporation of natural fibers and matrices sourced from renewable materials such as wood, agricultural residues, and biomass sources. These materials produce products that are not only innovative but also sustainable, aligning with the growing global imperative for eco-friendly solutions. Natural fibers come from a variety of sources, including plant fibers like ramie, bamboo, hemp, jute, sisal, kenaf, and flax (Fig. 1). These fibers stand as the most utilized materials in the NFCs industry [1,2]. Natural fibers can also be derived from agricultural by-products, which are materials left over from agricultural processes. These by-products often consist of parts of plants that are not used for food or other primary purposes. Examples of agricultural by-products include bagasse, wheat straw, corn stalks, pineapple leaf (PALF), as well as rice and coconut husks [3].
Figure 1: Plant based natural fibers
The integration of polymeric-based composites, particularly those utilizing natural fibers, aligns closely with the principles of sustainability and cleaner production, supporting several Sustainable Development Goals (SDGs). By incorporating natural fibers into composite formulations, these materials offer an eco-friendly alternative to traditional, petroleum-based composites. This shift not only reduces dependency on non-renewable resources but also mitigates the environmental impact associated with conventional materials. The NFCs influence the inherent properties of these sustainable materials to enhance performance while supporting cleaner manufacturing processes. Advances in the development of NFCs emphasize optimizing fiber-matrix interactions and improving recycling methods, which are crucial for minimizing waste and enhancing the lifecycle sustainability of composite products [4]. The focus on integrating bio-based components and adopting environmentally responsible production techniques highlights the commitment to advancing greener and more sustainable material solutions. Furthermore, there is a need for enhanced stabilization techniques to maintain the long-term performance of these sustainable material.
Oil palm also stands out as another significant source of natural fibers derived from agricultural by-products within the oil palm industry. This sector produces a variety of biomass materials, including empty fruit bunch (EFB), oil palm trunk (OPT), oil palm frond (OPF), mesocarp fiber (MF), palm kernel shell (PKS), and palm kernel cake (PKC). After Indonesia, Malaysia is the second-largest producer of palm oil globally and has a huge oil palm plantation area, covering about 5.65 million hectares, which yields a substantial volume of oil palm biomass [5]. In 2023, the total estimated production of oil palm biomass was at 92.37 million tons based on dry weight basis. This included 7.2 million tons from EFB, 9.83 million tons from OPT, 63.4 million tons from OPF, 7.57 million tons from MF, and 4.47 million tons from PKS as shown in Fig. 2 [5].
Figure 2: Oil palm biomass availability in 2023. Adapted with permission from Reference [5]. Copyright © 2024, MPOB
Considering the availability and abundance of oil palm biomass, leveraging oil palm materials in biocomposites could provide as a useful resource for a various industry, thereby contributing to the creation of a variety of environmentally friendly products. Many research projects have explored the utilization of natural fibers across a range of industrial applications including for furniture, flooring, construction, building materials, doors, packaging, pulp, and paper [6]. Among these, oil palm biomass, sourced from the oil palm tree (Elaeis guineensis), has attracted significant attention. Incorporating oil palm fiber into value-added products represents a crucial step towards sustainability and waste reduction within the palm oil industry. Notably, one promising oil palm fiber variant is EFB fiber, derived as a byproduct from the palm oil industry’s processing of fresh fruit bunches (FFB). Renowned for its lightweight nature, high tensile strength, excellent stiffness, porous structure, and biodegradability, EFB fiber emerges as an exceptional option for reinforcing materials. Its ability to bolster structural integrity without compromising weight renders it particularly advantageous [7].
This paper offers a review of the utilization of oil palm biomass in the biocomposite industry for various applications. Additionally, it provides an up-to-date analysis of developments and research in the field of oil palm fiber-based hybrid composites. The analysis includes a summary of the morphological, mechanical, thermal, and physical characteristics of hybrid composites made from oil palm biomass. The application of oil palm-based composites is also listed and summarized. Furthermore, this paper addresses the limitations, challenges, and future perspectives of using oil palm biomass as a composite material. The information presented in this paper aims to offer researchers and practitioners a comprehensive understanding that supports future innovations in utilizing oil palm biomass, thereby contributing to environmental protection and sustainability efforts.
2 Properties and Applications of Oil Palm Fibers
Oil palm fiber is a versatile natural material that has become increasingly valued across a range of industries, and has gained recognition for its remarkable versatility and diverse applications. Derived from various parts of the tree and categorized by source type such as trunk, frond, shell, EFB, and mesocarp, oil palm fiber offers a multitude of beneficial properties. A schematic representation of the sources of oil palm biomass is illustrated in Fig. 3.
Figure 3: Oil palm biomass generated from the palm oil tree
Generally, the properties of oil palm fibers exhibit irregularity due to variations in their origins. The components of oil palm fibers may differ, influenced by factors such as growth patterns, soil conditions, plant age, climate, different part, and function [8]. The properties of oil palm fibers hold significant importance as they directly influence the performance of the final composite materials. These variations result in differences in fiber length, diameter, density, and chemical composition, impacting their mechanical strength, moisture absorption capacity, thermal conductivity, and other key characteristics. Understanding and optimizing these properties are essential for achieving desired composite performance, ensuring the effectiveness and reliability of products across various applications. Table 1 summarizes the key properties of oil palm fibers, offering valuable information about their characteristics and attributes.
Abundant studies have highlighted the resilient nature of EFB fiber, characterized by its central lacuna contributing to a porous morphology. This unique structure forms a strong mechanical network when blended with matrix resin during composite fabrication [15]. Despite these advantages, EFB fibers may still retain excessive oil and silica bodies on their surfaces [16,17]. In contrast, OPT primarily consists of parenchyma tissue with longitudinal fibrous threads and vascular bundles scattered unevenly throughout, distinguishing it from wood’s anatomical structure [15]. During EFB harvesting, pruning is essential, yielding OPF composed of leaflets, rachis, and petioles primarily utilized for soil protection and nutrient recycling [11,15].
Like various other plant natural fibers, oil palm fibers are the lignocellulosic fiber that is predominantly comprised of cellulose, hemicellulose, and lignin. These components contribute to their structural integrity and versatility as cellulose provides strength, hemicellulose offers flexibility, and lignin acts as a binding matrix, reinforcing the overall fiber structure. The chemical composition of the fibers influences their performance and contributes to the final composite properties. Among the oil palm fibers, EFB has higher cellulose content, followed by OPT [18]. The high cellulose content in EFB makes it valuable for composite production, as it reinforces polymer matrices effectively. Cellulose is composed of long chains of glucose molecules, provides structural reinforcement at the microscopic level, offering high tensile strength and stiffness. It distributes loads effectively, resists deformation, and forms strong interfacial bonds with the polymer matrix [8]. This optimizes the adhesion between the matrix and fibers, efficiently transferring stress and leading to a stronger, more durable composite material. On the other hand, the MF obtained from the mesocarp layer of the oil palm fruit, possesses a cellulose content of 33.9%. The extractives in raw MF were highest, approximately 6%, suggesting the existence of trace amounts of oil and wax in the fibers [19].
On the other hand, OPF fiber exhibits a higher hemicellulose content compared to other oil palm fibers, typically ranging from 34% to 38% [18]. After cellulose, hemicellulose is the second most prevalent polysaccharide polymer in natural fibers, containing polysaccharides that serve as natural binders. These compounds aid in bonding the fibers together, enhancing the cohesion of the composite material. For lignin content, PKS contains highest, i.e., 50% as compared to other oil palm fibers primarily because they serve as protective layers for palm kernels within the fruit [20]. Also, lignin in PKS contributes to its durability and resistance to degradation, allowing it to be used for a variety of purposes such as biomass energy production.
The morphology of fibers, particularly their length, has a vital function in determining the performance of fiber composites. This is because the length-to-diameter ratio, also referred to as the aspect ratio, significantly impacts the properties of the resulting composite materials [21]. Among oil palm fibers, OPT fibers exhibit the longest length and largest diameter, while OPF fibers are characterized by shorter length and greater thickness compared to EFB and OPT fibers. Moreover, oil palm fibers possess potential applications as acoustic materials, serving roles as absorbers due to their soft, porous, and fibrous structures, which effectively dampen sound waves [22]. Additionally, their versatility extends to acting as soundboards, where their unique properties contribute to enhancing acoustic resonance and clarity in various settings such as musical instruments and architectural acoustics.
The mechanical characteristics of oil palm fibers depend on several factors, including their chemical composition, fiber structure, inner structure alignment, and microfibril angle. Among these, OPT fiber notably stands out in Table 1 due to its favorable mechanical properties, particularly in terms of tensile strength and Young’s modulus. This is attributed by the secondary layers’ thick lumen and wide lumen diameter, which provide them rigidity and collapse resistance [13]. Conversely, EFB fibers typically exhibit higher elongation properties due to their more flexible and ductile structure. The distribution and orientation of cellulose within the cell wall contribute to EFB fibers’ ability to elongate under stress [9].
3 Limitation of Oil Palm Fiber
While oil palm fibers offer many advantages, they also come with certain limitations. A common limitation of natural fibers includes their tendency for high moisture absorption, inadequate wettability, and incompatibility with certain polymeric matrices [23,24]. Previous studies have reported limitations associated with EFB and MF, such as their hydrophilic nature, reduced compatibility with non-polar matrix materials, and variability in properties. Additionally, shredded EFB still has 4.5% residual oil, and significant amounts of silica bodies are bound to the EFB fiber surface [25]. The residual oil on fiber surfaces hinders fiber-matrix compatibility, reducing wettability and hindering chemical interactions [16]. Over time, this oil may degrade, further weakening the fiber-matrix interface and compromising composite mechanical properties.
Utilizing oil palm trunk in composite production presents challenges owing to its high moisture content (MC) and variable in density, which can detrimentally impact both fiber quality and composite properties. Managing moisture levels during processing is crucial to mitigate issues such as fiber degradation, reduced mechanical strength, and compromised adhesion between fibers and matrix materials. Additionally, OPT, with its high carbohydrate content in parenchyma cells, serves as a readily consumable substrate for various bio-deteriorating agents. The large and bulky nature of OPT makes transportation and processing into usable fibers difficult. According to Bakar et al. [26], the dimensional instability and high-density variation of OPT, attributed to its radial density gradient, have limited its potential for composite applications. In the case of OPF, its elevated lignin content presents a favorable nutrient source for fungal attacks, particularly by white-rot fungi [27]. This heightened susceptibility to fungal degradation poses a significant challenge in maintaining the integrity and longevity of OPF-based materials. Therefore, proper moisture control and handling strategies are crucial to mitigate problems like mold growth and dimensional instability in the final composite product.
For PKS, several challenges arise in composite production, particularly concerning separation and the high lignin content. The tight adherence of the shells to the kernels is due to structural characteristics such as cell wall composition and adhesion mechanisms [28]. Additionally, the high lignin content in PKS is a result of its function in providing structural support and protection to the palm kernel. While lignin contributes to the strength of the shells, it also presents processing challenges due to its complex chemical structure and interactions with other composite components. Addressing these issues requires innovative approaches in biomass processing and composite formulation to optimize the utilization of PKS in composite production.
To overcome the issues and limitations of oil palm fibers in the composite industry, several strategies can be implemented. Few researchers have stated that fiber surface treatments, fiber modifications, incorporation of filler or coupling agents, and appropriate processing techniques can be applied to address some of the mentioned limitations, particularly to enhance fiber-matrix interfacial adhesion [29]. Hybridizing with another natural or synthetic fibers can also improve fiber-matrix compatibility [30,31]. According to Swolfs et al. [32], the purpose of combining two or more fibers into one composite is to preserve the benefits of each fiber type while minimizing some of the drawbacks. This led to a better balance in the mechanical, chemical, and physical properties of the hybrid composite. Naik et al. [33] also stated that composites in the hybrid form exhibit better properties over single fiber composite due to synergistic effects arising from the combination of different fibers.
Oil palm fiber hybrid composites are advanced materials made by combining oil palm fibers with other types of fibers or matrix materials. These composites utilize the inherent properties of oil palm fibers, which are derived from the oil palm tree, including their natural abundance and renewability. Numerous studies have explored into hybridizing oil palm fiber with both natural and synthetic fibers to improve the compatibility with both thermoset and thermoplastic polymers. These investigations primarily focused on analyzing the composites’ behavior under various parameters such as fiber loading, types, and matrix utilization, while characterizing them for mechanical, physical, electrical, and thermal properties tailored to specific applications. Table 2 provides a summary of these studies, highlighting the various combinations of fibers and the outlining key findings. The discoveries from these studies offer valuable understandings into the potential synergies and benefits of hybridizing oil palm fiber with different types of fibers, contributing to the advancement of composite materials in various applications.
The structure of oil palm fiber hybrid composites typically includes a matrix material that binds the fibers together, resulting in a composite with enhanced properties [34,36]. These composites exhibit improved mechanical strength, durability, and reduced weight compared to traditional materials. The hybrid nature of these composites enables the customization of their properties by varying the types and proportions of fibers used. Oil palm fiber hybrid composites are highly valued for their distinctive advantages across various applications. Their lightweight and high-strength characteristics contribute to improved fuel efficiency and reduced emissions in automotive components, supporting sustainability goals [57]. In construction, they offer superior durability and resistance to environmental degradation, making them ideal for eco-friendly building materials [48,58]. Additionally, their cost-effectiveness and biodegradability present a sustainable alternative to conventional packaging materials, helping to mitigate plastic waste and lessen environmental impact [59,60].
Several techniques are used in the production of oil palm fiber hybrid composites, each with its unique advantages and limitations [61]. Compression molding is known for producing high-quality, consistent composite parts suitable for large and complex shapes but involves long cycle times and high mold costs, making it less efficient for small-scale production [62]. Injection molding excels in precision and repeatability, ideal for complex shapes and high-volume production, though it requires a significant initial investment and careful control to avoid issues such as fiber degradation [8]. Extrusion, as utilized by Sharum et al. [63], is cost-effective for producing long, uniform profiles but may face challenges with complex geometries and fiber alignment. Pultrusion is effective for producing strong, uniform profiles with constant cross-sections but is generally slower and best suited for simpler shapes. However, Balakrishnan et al. [64] assess the suitability of natural fibers for hybridization with glass fibers using this technique and conclude that oil palm fiber is less suitable for pultruded profiles in structural applications. Hand lay-up, used by Hanan et al. [65], involves manually placing reinforcement layers into a mold followed by resin application, offering flexibility for complex shapes and small to medium-scale production but can lead to variability in quality and requires careful handling to ensure uniform resin distribution and minimal voids. In contrast, vacuum infusion, employed by Nik Wan et al. [66] for hybrid OPT epoxy composites, draws resin into a mold through a vacuum, ensuring even distribution and low void content, resulting in high-quality, lightweight composites with enhanced structural integrity.
4.1 Oil Palm Empty Fruit Bunch (EFB) Hybrid Composite
One of the most utilized oil palm fibers is EFB, a primary waste material generated in the oil palm industry during oil production. The process of separating FFB results in EFB, a fibrous residue left behind from oil palm processing, which includes both MF and PKS. Reports indicate that for every ton of palm oil produced, the palm oil industry generates approximately 1.07 tons of EFB [67]. Using EFB is economically advantageous as these waste materials are often abundant and come at minimal cost, thereby reducing expenses, and offering economic benefits. Moreover, their utilization contributes to sustainability by recycling renewable resources, thereby decreasing reliance on natural resources.
In a study by Jawaid et al. [34], EFB and PALF were employed as natural reinforcements in phenolic-based composites for industrial and construction applications. The results demonstrated significant improvements in both tensile and flexural strength, with a notable 173.71% increase in tensile strength upon the addition of 50% EFB. Moreover, Storage and loss moduli improved with the addition of both pure and hybrid composites, although the damping factor was significantly lower in hybrid composites than in pure composites. In the following investigation carried out by Awad et al. [40], alkaline-treated EFB and PALF were employed as reinforcements in bio-phenolic resin. The results indicated that for tensile, modulus, and flexural properties, hybridizing the alkali-treated fibers produced the greatest results. This improvement can be related to the mercerization of EFB and PALF fibers in the composite, which increased the interfacial adhesion between the fiber and matrix.
Ramlee et al. [36] investigated hybrid composites made from EFB and sugarcane bagasse (SCB) fibers reinforced with phenol formaldehyde (PF) at different fiber compositions, as depicted in Fig. 4a. The study found that the higher cellulose content in EFB fibers contributed to improved mechanical strength, while SCB fibers reduced water content and voids, enhancing the overall composite quality. Hybridizing SCB fibers into EFB composites helped mitigate fiber pullout and reduced voids, as seen in micrograph images in Fig. 4b, leading to the highest tensile strength (5.563 MPa) and tensile modulus (661.29 MPa) in the hybrid composite (Fig. 4c) indicating that the balanced fiber distribution significantly improves mechanical properties. In contrast, pure EFB and SCB composites exhibited lower tensile strength due to poor interfacial bonding and lower fiber density. In their study, Ramlee et al. [37] expanded their research by treating both fibers with 2%v/v silane and 4%v/v hydrogen peroxide for insulation material, as illustrated in Fig. 5a. Results indicated that the silane coupling agent yielded superior enhancement across all physical and mechanical properties compared to hydrogen peroxide treatment. This improvement is due to the fiber and matrix adhesion being strengthened, facilitated by silane acting as a fiber-matrix bridge, leading to enhanced tensile, flexural (Fig. 5b), and compression properties, along with improved dimensional stability of the composites.
Figure 4: (a) The pure and hybrid phenolic composite from EFB and SCB fibers, (b) the micrograph image of hybrid EFB and SCB composite, and (c) tensile properties of hybrid composite. Adapted with permission from Reference [36]. Copyright © 2019, Elsevier Ltd.
Figure 5: (a) The production of treated EFB and SCB hybrid composite and (b) the flexural properties of treated EFB and SCB hybrid composite. Adapted with permission from Reference [37]. Copyright © 2021, Elsevier Ltd.
The effect of stacking sequence on the mechanical characteristics of epoxy composites reinforced with kenaf fiber and hybrid EFB was investigated by Mansor et al. [68]. They utilized two types of kenaf fiber, namely short kenaf fiber and woven kenaf mat, and formulated various fiber layering sequences using the hand lay-up method. The findings showed that the strength of the outer layer fibers inside the laminates and the fiber orientation had a substantial impact on the mechanical durability of the hybrid composites. Specifically, layering sequences with a higher proportion of woven kenaf layers demonstrated superior reinforcement of mechanical properties compared to those with kenaf short fibers, attributed to the longer fiber length and orientation. Additionally, greater bending load-bearing capacity of woven kenaf resulted in more uniform stress distribution during tensile loading in the longitudinal and transverse directions as well as more effective stress transmission between the fiber and matrix [69].
Hanan et al. [44] investigated the production of hybrid EFB-kenaf reinforced epoxy composites using EFB mat and woven kenaf fabric, examining the influence of fiber weight ratios on composite properties. The addition of kenaf fiber resulted in higher tensile and flexural properties due to its denser and more compact structure compared to EFB. On the other hand, the hybrid composites’ impact strength increased with an increase in EFB content, which was mainly attributable to the chemical composition of EFB and fiber orientation [70].
In order to improve the fire characteristics of highly combustible kenaf/epoxy composites, researchers investigated the flame retardancy of modified and chemically treated nano EFB fillers [39]. Utilizing non-woven kenaf mats, dried nano fillers, including EFB, montmorillonite (MMT) and organically modified MMT (OMMT), were uniformly dispersed in epoxy resin to fabricate hybrid nanocomposites. Results from the limiting oxygen index (LOI) test demonstrated a significant improvement in flame retardancy in the nano EFB hybrid nanocomposites (Fig. 6). This improvement was credited to a potent synergistic flame-retardant effect in the gaseous phase, facilitated by the interaction between tin and bromine elements. This interaction promoted free radical mechanisms, effectively suppressing combustion.
Figure 6: The enhancement of LOI of hybrid nano EFB/kenaf epoxy composites. Adapted with permission from Reference [39]. Copyright © 2019, Elsevier Ltd.
In a recent work, Anuar et al. [71] explored into the creation of a 3D printed filament by reinforcing polylactic acid (PLA) filament with soda lignin produced from EFB and epoxidized palm oil (EPO). The incorporation of 1 phr lignin and 5 phr EPO resulted in improved mechanical and thermal characteristics, with a greater T0 and more crystallinity. Interestingly, the hybrid PLA/lignin composites with EPO exhibited lower onset temperatures, attributed to enhanced chain mobility. Moreover, the study demonstrated that the inclusion of EFB lignin and EPO influenced polymer crystallization during cooling, indicating good compatibility and an increase in crystallinity. These findings highlight the potential of the hybrid composite as an alternative filament for 3D printing, with the interaction among PLA, lignin, and EPO enhancing mechanical properties and underscoring the importance of EPO in reinforcing the PLA matrix with alkaline lignin powder. In a study by Idris et al. [45], lignin-containing cellulose nanofibrils (LCNF) were derived from EFB through a multi-step bleaching process. The presence of lignin in hybrid EFB hand sheets significantly improved drainage time, tensile index, and tear index. Lignin enhances fiber bonding, reducing water drainage during hand sheet formation, and reinforces the fiber network, preventing delamination and enhancing tear resistance.
Synthetic fibers are extensively used in structural applications due to their specific material properties, allowing for reduced structural weight compared to metallic counterparts. Hybridizing with fibers like carbon and glass has resulted in the creation of advanced composite materials with a range of uses. Muhammad Amir et al. [42] investigated the hybridization potential of EFB and Kevlar with epoxy resin, focusing on dynamic impact response under low velocity impact (LVI) and compression after impact (CAI) tests, both with and without gamma radiation exposure. Results indicated that non-irradiated Kevlar/oil palm EFB hybrids exhibited superior impact resistance compared to irradiated counterparts. However, gamma irradiation improved the compressive residual strength of the hybrids. Overall, the study suggests that Kevlar/EFB hybrid composites could find utility in applications exposed to gamma radiation, such as medical and military contexts.
Suriani et al. [38] studied the utilization of EFB fiber and polyester (PET) yarn in reinforced epoxy polymer materials across varying EFB loading levels. They observed a reduction in both flammability and tensile properties as the volume fraction of EFB fiber increased, with an optimal loading of 20% identified for achieving balanced properties. The horizontal burning test indicated deteriorating flammability properties with higher fiber volume contents, while specimens with lower EFB content (20%) exhibited the highest tensile strength, suggesting challenges in proper fiber-matrix binding at higher fiber volume fractions. The tensile strength decreases as the fiber volume content increases, with the control specimen (0% EFB) exhibiting the highest tensile strength of 10.79 N/mm2 (Fig. 7a). The stress–strain curves in Fig. 7b for specimens with increasing fiber content (20%, 35%, and 50%) show a reduction in tensile strength, with values of 4.29, 3.88, and 3.63 N/mm2, respectively. This decline is attributed to poor adhesion between the EFB fibers and the epoxy matrix, as well as irregular fiber size and potential defects during composite fabrication.
Figure 7: (a) The tensile strength and (b) the stress-strain curve of EFB-PET composite. Adapted with permission from Reference [38]. Copyright © 2021, MDPI
4.2 Oil Palm Trunk (OPT) Hybrid Composite
Trunks utilized in composites are typically processed into veneer, particle, or strand forms. In a study by Nuryawan et al. [46], OPT veneer was combined with EFB mats to create hybrid plywood using PF resin filled with palm oil ash (OPA) nanoparticles (Fig. 8). The dimensions and mechanical qualities of the plywood panels were considerably impacted by the inclusion of OPA nanoparticles, notably improving water absorption and thickness swelling resistance due to the nanoparticles filling voids and porous areas. This effect was attributed to the enhanced impregnation of PF resin into voids by OPA nanoparticles, blocking water molecule ingress and reacting with hydroxyl groups in OPT veneer to reduce water absorption. Additionally, the flexural properties improved with increasing OPA nanoparticle loading, as the nanoparticles increased the bonding surface area between PF resin and OPT, enhancing stress distribution and overall rigidity. Furthermore, the thermal stability of the plywood panels was enhanced by the presence of PF-filled OPA nanoparticles, which dispersed heat and prolonged degradation, thanks to the nanoparticles’ high surface area facilitating heat dissipation [72].
Figure 8: The OPT veneer and EFB mat reinforced with PF resin filled with OPA. Adapted with permission from Reference [46]. Copyright © 2020, MDPI
Mawardi et al. [47] examined the mechanical, physical, and heat conductivity characteristics of bio-insulation materials made of ramie fiber and OPT, with tapioca starch used as a bio-binder. The study assessed the effects of hybridization on the properties of the panels and found that ramie fiber hybridization led to improvements in physical, mechanical, and thermal properties. Hybridization with ramie fiber resulted in a slight reduction in water absorption, attributed to the compatible characteristics of the mixed material, which decreased voids and porosity on the composite surface. This reduction in water absorption was estimated at 3%–5%. In addition, hybridization improved the panels’ bending strength, compensating up for the oil palm wood raw material’s poor mechanical properties. According to thermogravimetric study, hybrid panels showed superior thermal stability because of their increased density, which minimizes gaps that absorb heat and serve as phonon scattering areas, that reduces thermal conductivity [73].
In a different investigation carried out by Mawardi et al. [48], hybrid OPT-ramie composites for thermal insulation were fabricated using different particle sizes of OPT: large (0.42–0.84 mm), medium (0.07–0.42 mm), and small (<0.07 mm). The composite formulation consisted of a ratio of 50:20:30 for OPT, ramie fiber, and tapioca starch, respectively, with PLA utilized to coat the bottom layer of the hybrid composite (Fig. 9). Results revealed that larger particle-sized composites exhibited reduced density and increased porosity, leading to higher water absorption capacity [74]. This increased water intake was attributed to the abundant hydroxyl groups in the parenchyma tissue of OPT, enhancing hydrogen bonding. Moreover, thermal conductivity was found to increase with density, but larger OPT particle sizes decreased thermal conductivity due to the lower composite density, resulting in improved thermal resistance owing to the increased air content within the composite structure [75].
Figure 9: The composition of hybrid OPT and ramie composites with (a) layer pattern; and different OPT particle size (b) large; (c) medium; and (d) small. Adapted with permission from Reference [48]. Copyright © 2022, Elsevier Ltd.
4.3 Oil Palm Frond (OPF) Hybrid Composite
Frond, derived from oil palm pruning and fruit harvesting, has traditionally been utilized as organic fertilizer or animal feed. Momoh et al. [76] explored the use of oil palm broom fiber (OPBF) from oil palm leaflets to reinforce laterite-based roof tiles, enhancing flexural strength by over 120%. In their subsequent study [77], hybrid OPBF strand-reinforced concrete beams were developed, incorporating OPBF, concrete, and steel (Fig. 10). These hybrid beams, with OPBF strands as longitudinal reinforcement and steel stirrups for shear resistance, demonstrated cost and carbon dioxide emission savings of up to 16% and 36% respectively compared to conventional steel-reinforced lintels. The potential for even greater CO2 savings exists if emissions from trans-oceanic steel transportation are considered, particularly for steel-importing countries.
Figure 10: Hybrid concrete beams made from steel and OPBF strands. Adapted with permission from Reference [77]. Copyright © 2024, Elsevier Ltd.
Ademoh et al. [50] developed a safety helmet shell utilizing treated OPF fiber reinforced with male flower bunch stalk fiber. This hybrid composite, combined with unsaturated polyester (PE), exhibited promising mechanical properties, positioning it as a potential alternative to acrylonitrile butadiene styrene (ABS) plastic commonly employed in helmet manufacturing. Notably, the impact strength of the hybrid fiber-reinforced composite approached that of ABS plastic, highlighting its suitability for protective applications. These findings underscore the potential of utilizing natural fibers in composite materials to achieve comparable performance to conventional synthetic materials, offering both mechanical robustness and environmental sustainability in helmet production.
4.4 Palm Kernel Shell (PKS) Hybrid Composite
Oladele et al. [54] investigated the influence of chemically treating PKS fiber and particulate cassava peel (PCP) as hybrid reinforcements on the mechanical properties and wear behavior of epoxy composites reinforced with PKSF/PCP hybrids. The study demonstrated that chemical treatment significantly enhanced interfacial adhesion and reduced porosity, leading to improved mechanical properties. This treatment also increased the stiffness of the composites, resulting in better resistance to deformation under various loads, including Young’s modulus. Surface modification of the fibers likely allowed for higher reinforcement loading and improved properties, particularly by removing lignin and exposing cellulose for a rougher surface. Additionally, the use of these organic agro-based materials contributed to enhanced wear resistance, with the presence of Fe and Ca in the PCP being key factors. Given their biodegradable nature and environmental friendliness, these materials present a promising alternative for low-technology applications.
Padavala et al. [53] studied the strength properties of lightweight concrete incorporating PKS and fly ash (FA) in various proportions of PKS, including 5%, 10%, and 15%. The findings indicated that substituting 25% of cement with FA and 10% of coarse aggregate (CA) with PKS resulted in optimal strength. This substitution improved the composite concrete due to the pozzolanic qualities of PKS, which contributed to its strength and durability. Additionally, incorporating PKS in concrete offers the advantage of reducing the scarcity and high cost of coarse aggregates, thereby enhancing the economic viability of concrete production. Overall, the research shows the possibilities of utilizing PKS as a sustainable alternative in lightweight concrete production, contributing to both strength enhancement and cost reduction.
The PKS also known as oil palm shell (OPS), is the shells of palm kernels, which are waste materials generated during the processing of palm oil. OPS nanoparticles were utilized as fillers in fibers reinforced polyester hybrid composites in a study by Rosamah et al. [56]. These nanoparticles were effectively created by high-energy ball milling of raw OPS, and their effects on the woven kenaf and coconut mat hybrid polyester composites were explored. The findings demonstrated that the inclusion of OPS nanoparticles improved the properties of the hybrid composites, with the most notable enhancements in physical, thermal, morphological, and mechanical characteristics observed at a loading of 3 wt.% OPS nanoparticles. This finding suggests that hybridizing OPS nanoparticles into fibers reinforced hybrid composites increases density, possibly by filling voids in the matrix and enhancing filler-matrix interaction. Additionally, the uniform dispersion of OPS nanoparticles in the matrix contributes to improved mechanical properties, particularly tensile strength, by increasing the composite’s surface area and energy-absorbing capacity while reducing any voids.
Lakshmaiya et al. [55] also utilized OPS as a nanofiller in hybrid composites, incorporating it with flax fibers and epoxy resin. Different proportions of OPS (0, 2, 4, and 6 wt.%) were combined with 40 wt.% of flax fibers to create the composites, which were then subjected to cryogenic conditions to observe their interlaminar shear and dynamic mechanical properties. The study revealed that OPS nanoparticles could serve as natural fillers, and incorporating 4 wt.% OPS nanoparticles resulted in the optimum interlaminar shear and dynamic performance under cryogenic settings. The addition of 4% OPS nanofiller improved both the composite’s loss and storage modulus, attributed to the increased hardness and stiffness provided by the OPS nanoparticles. Furthermore, the damping factor of the hybrid nanocomposite was notably reduced compared to flax/epoxy composites, indicating enhanced adherence between the flax fibers and epoxy resin due to the limitation of epoxy molecular chain mobility by OPS nanofillers.
4.5 Mesocarp Fiber (MF) Based Hybrid Composite
Mesocarp fiber (MF), another prominent type of oil palm fiber, is typically derived from palm-pressed fiber. These fibers are extracted from the biomass residue generated during the oil harvesting process by pressing palm fruit in the manufacture of particleboard from MF, Boonsombuti et al. [52] utilized lignin extracted from PKS as a binder. This extracted lignin served as a replacement for phenol in the synthesis of PF resin, which was subsequently employed in the production of particleboards using MF. The findings revealed that substituting 25% of phenol with lignin in the resin formulation yielded particleboards with comparable bending strength and thickness swelling to those bonded with PF resin alone. This study highlights the potential of utilizing biomass from both palm oil and palm kernel shell to produce particleboard, offering sustainable alternatives in the materials industry such as for furniture, panel, and flooring.
4.6 Comparison of Oil Palm Fiber Hybrid Composites with Other Natural Fiber Composites
Oil palm fiber hybrid composites present a unique set of qualities compared to other natural fiber composites such as jute, kenaf, bamboo, ramie, and coir. However, compared to other fibers, oil palm fibers generally exhibit lower mechanical strength and stiffness. Jute and kenaf fibers are recognized for their superior tensile strength and durability, making them suitable for applications requiring strong performance [78]. Compared to oil palm fiber, bamboo fibers, known for their high strength and stiffness, while ramie offers exceptional strength and durability [79,80]. In terms of mechanical properties, oil palm fiber hybrid composites generally demonstrate significant tensile and flexural strength, particularly when hybridized with fibers like kenaf or jute [36,62]. This hybridization helps to enhance the mechanical performance of oil palm fibers, which are otherwise less strong than other natural fibers like flax and hemp. For example, hybrid composites of oil palm and kenaf fibers have shown improved tensile strength compared to pure oil palm fiber composites [44]. However, oil palm fiber hybrid composites often fall short in impact strength, a critical factor in applications requiring high resistance to sudden forces [70]. On the other hand, fibers such as flax are renowned for their high tensile strength, making them more suitable for structural applications where superior mechanical performance is required [81].
The manufacturing processes for oil palm fiber hybrid composites are tailored to maximize the properties of oil palm fibers in specific applications. Methods such as injection molding, compression molding, and vacuum infusion are not only widely used for other natural fibers but are also well-suited for the manufacturing of oil palm hybrid composites. These techniques provide enhanced control over fiber alignment and distribution, which is crucial for achieving superior mechanical properties in the final composite materials. This process enables the efficient shaping and reinforcement of oil palm fiber hybrid composites, making them suitable for components like crash boxes and interior panels [82]. When considering applications, oil palm fiber hybrid composites are increasingly used in sectors like furniture, automotive and construction. Their lightweight nature and energy absorption capabilities make them ideal for automotive components [82]. However, for more demanding structural components, fibers like flax and hemp are preferred due to their superior mechanical properties and stability. In the construction industry, oil palm fiber hybrid composites are well-suited for non-structural elements like insulation panels and decorative components, where their thermal insulation properties and cost advantages are most beneficial. Conversely, jute and sisal composites are favored in load-bearing construction applications due to their higher strength and durability [83].
While oil palm fiber hybrid composite presents several advantages, particularly in terms of sustainability and cost, they are often outperformed by other natural fiber composites in key areas such as mechanical strength and moisture resistance. Nevertheless, with appropriate treatments and hybridization strategies, oil palm fiber hybrid composite can be optimized for a variety of applications, particularly where their environmental benefits and cost advantages align with the performance requirements. As research continues to address their limitations, oil palm fiber hybrid composite holds the potential to become a more widely adopted solution in sustainable material development.
5 Oil Palm Fiber Reinforced Biopolymer
The environmental impact of petroleum-based polymers has encouraged researchers and manufacturers to seek alternatives to polyolefins. One promising option is the use of bio-based and biodegradable polymers for composite production. The new generation of fully or semi biopolymers, along with their characteristics, supports the production of new bio-products that can enhance various manufacturing processes. These biopolymers are derived from renewable resources and offer properties that make them suitable for a wide range of applications. For instance, thermoplastic starch (TPS), PLA, and polyhydroxyalkanoates (PHA) are prominent examples of biopolymers gaining traction in the market. Their biodegradability, biocompatibility, and mechanical properties make them excellent candidates for replacing conventional polymers in many applications [84]. Recent advancements in the synthesis and processing of these biopolymers have led to the development of novel composites with improved performance and sustainability [85]. However, biodegradable polymers need improvement before they can replace commercial polymers in many applications. Most biopolymers exhibit thermal instability. For example, at high temperatures, the glucose links in starch-based polymers start to break down, and at low temperatures, retrogradation occurs, making the resulting films brittle. PHAs also have a narrow processing window due to their nearly identical melting and degradation temperatures, which complicates their commercial viability. The inherent brittleness and low mechanical strength of biopolymers make it challenging to replace polyolefins in packaging materials. To address these issues, bi-layer or multicomponent films with improved mechanical properties have been developed, making biopolymers more suitable for various applications. Blending biopolymers with lignocellulosic fibers, including oil palm fiber, has garnered significant interest. Additionally, factors like fiber treatment, fiber loading, and manufacturing processes can influence the mechanical properties of biopolymer composites. Most studies indicate that the mechanical properties of biopolymer composites are enhanced compared to neat polymers [85,86]. Table 3 summarizes the mechanical properties of oil palm fiber-reinforced biopolymer composites.
Salim et al. [91] investigated the effect of adding EFB fibers on the mechanical properties of PHA composites, specifically poly(3-hydroxybutyrate-co-3-hydroxyvalerate) (PHBV). Their findings revealed that a composite with 35 wt.% EFB fibers exhibited the highest tensile strength compared to composites with 30 wt.% and 40 wt.% EFB fibers, highlighting the importance of optimizing fiber content for enhanced mechanical performance. Similarly, Jumaidin et al. [92] modified the thermal and mechanical properties of TPS by incorporating coconut fibers at varying concentrations (0–50 wt.%). They observed that a 50 wt.% coconut fiber-TPS composite demonstrated significantly improved thermal stability and mechanical properties, with a tensile strength of 20.7 MPa and a tensile modulus of 2890 MPa. Additionally, the same composite exhibited the highest flexural strength and modulus, reaching 30.3 and 3266.3 MPa, respectively. These enhancements were attributed to the good compatibility and homogeneous structure between the TPS and coconut fibers, as confirmed by Fourier transform infrared spectroscopy (FTIR) and scanning electron microscopy (SEM) analyses.
Adnan et al. [93] explored the mechanical properties of EFB fiber-reinforced TPS films, specifically focusing on the effects of acid hydrolysis treatment on the fibers. The study found that incorporating 4 wt.% acid-hydrolyzed EFB fibers into the TPS matrix significantly improved tensile strength due to the uniform distribution of treated cellulose within the matrix. However, further increases in fiber content led to a decrease in tensile strength, indicating an optimal fiber loading for mechanical performance. In another study, Baskaran et al. [94] examined the impact of steam treatment and the addition of PHA on the properties of particleboards made from oil palm trunks. The inclusion of 10% PHA enhanced the modulus of rupture and internal bond strength of the panels, with the highest values recorded at 8.76 and 1.02 MPa respectively demonstrating the potential of PHA in improving the mechanical properties of bio based composites.
Research on PLA-based composites reinforced with oil palm fibers has also gained attention. Haafiz et al. [95] developed an oil palm fiber-reinforced PLA composite and found that while the incorporation of cellulose from oil palm fibers decreased the tensile strength and elongation at break compared to pure PLA, it significantly increased the Young’s modulus by approximately 30%. This indicates that while interfacial adhesion challenges exist, the stiffness of the composite is enhanced. Additionally, Yee et al. [87] prepared an EFB fiber-reinforced PLA composite incorporating nano silica as a filler to improve thermal stability and mechanical properties. They noted a decrease in tensile strength from 48 MPa in neat PLA to 29 MPa with the addition of 1.5 wt.% EFB fiber, primarily due to the hydrophilic nature of lignin in the EFB fibers. However, the addition of nano silica helped mitigate this decrease, enhancing the composite’s overall tensile strength as fiber content increased.
6 Challenges and Future Directions
Oil palm fibers offer a multitude of beneficial properties and have found applications in various sectors such as composite materials, textiles, paper production, and soil erosion control. However, the utilization of fiber-reinforced hybrid polymer composites presents several challenges and avenues for future research. Firstly, despite their potential benefits, the manufacturing process of these composites remains intricate due to the varied characteristics and interfacial adhesion issues associated with hybrid natural fibers, such as oil palm and jute fibers. Overcoming these challenges will require innovative approaches to optimize manufacturing techniques and enhance interfacial bonding between the fibers and the polymer matrix [30]. Moreover, while recent studies have shown promising improvements in the mechanical properties of hybrid-oil palm fiber-reinforced polymer composites, there is still a need for further investigation into optimizing the composition and processing parameters to achieve superior performance. This includes exploring the effects of different fiber ratios, treatments, and matrix materials on the mechanical and thermal properties of the composites [32,57].
In this context, artificial intelligence (AI) methods offer a promising solution to address these challenges. AI can be utilized to predict the mechanical performance of oil palm fibers and other natural fibers within hybrid composites, allowing for more accurate optimization of material properties and processing parameters [96,97]. AI-driven models, such as artificial neural networks (ANNs), back propagation neural networks (BPNN), spiking neural networks (SNNs), and adaptive neuro-fuzzy inference systems (ANFIS), can analyze complex datasets to predict how different combinations of fibers and matrices will behave under various conditions, thereby predicting the mechanical performance of green fibers in composite materials [98]. These models enhance the reliability of biocomposites by allowing for more accurate predictions of material properties, optimizing the design and development process of sustainable composite materials. This predictive also accelerates the development process by reducing the need for extensive experimental trials [99]. A few researches discusses the use of AI schemes to predict the mechanical performance of lignocellulosic fibers and highlights that AI models can effectively handle unseen data, enhancing the reliability and accuracy of performance predictions for natural fiber composites, thereby improving their applicability in sustainable materials development [100]. The integration of AI in the research and development of oil palm fiber composites could therefore be a crucial step toward overcoming current limitations and unlocking new applications for these materials.
Additionally, as the demand for sustainable materials continues to grow, future research should focus on enhancing the sustainability aspects of these composites. This may involve investigating alternative bio-based matrices and eco-friendly fiber treatments to minimize environmental impact throughout the lifecycle of the composite materials. Furthermore, understanding the long-term durability and environmental stability of hybrid-oil palm fiber-reinforced polymer composites is essential for their widespread adoption in various applications [11]. Future studies should include comprehensive durability testing under various environmental conditions to assess the composites’ resistance to degradation, moisture absorption, and thermal cycling.
Currently, oil palm fiber hybrid composites are utilized across various industries due to their advantageous properties, yet their full potential remains untapped. In the automobile industry, companies like Kejuruteraan Emas Sdn. Bhd. and Polycomposite Sdn. Bhd. have successfully incorporated oil palm fiber in the production of motor vehicle components. In the construction sector, IOI Corporation Bhd. has converted OPT into laminated boards, panels, and kiln-dried palm wood, while Weng Meng Industries Sdn. Bhd. has developed doors using a hybrid of OPT and wood. Additionally, Malaysian micro, small, and medium enterprises (PKMS), in collaboration with Japanese partners, have optimized the production of OPT pellets for use as fuel and in composite products for the Japanese market. In the packaging industry, oil palm fiber composites are being leveraged to create biodegradable trays and containers, providing an eco-friendly alternative to conventional plastics. Verdastro Sdn. Bhd., for example, is at the forefront of commercializing biodegradable OPT drinking straws in Malaysia, demonstrating the potential for these materials in sustainable packaging solutions [101].
Looking forward, the development of these composites could extend to more advanced applications, such as structural components in automobiles, including body panels and impact-resistant parts, which would further enhance vehicle performance and safety while promoting sustainability. Additionally, there is significant potential in the construction industry for innovative architectural elements like decorative facades and modular building systems, leveraging the versatility and environmental benefits of these materials. Expanding the use of oil palm fiber hybrids in the packaging industry for high-performance solutions, such as food-grade containers and protective packaging, could significantly address growing environmental concerns, positioning these materials as key players in the future of sustainable packaging. Furthermore, ongoing research on the development of biodegradable urine collection containers for hospital patients highlights the broader potential of these composites in creating eco-friendly medical disposables.
In terms of performance comparison with conventional materials, oil palm fiber hybrid composites offer significant environmental advantages due to their renewable and biodegradable nature. These composites typically result in a lower carbon footprint and reduced reliance on non-renewable resources, whereas conventional materials, often derived from petrochemical sources, have a higher environmental impact due to extraction processes and long-term waste issues [13]. Regarding scalability, the production of oil palm fiber hybrid composites can be integrated into existing manufacturing processes with necessary adjustments for fiber-specific requirements. Economically, although initial processing and treatment costs may be higher, the use of locally sourced and renewable materials can lead to long-term cost savings. The growing demand for sustainable materials is expected to improve economic feasibility and drive advancements in production efficiency. Furthermore, government initiatives and funding support early-stage technology companies that utilize biomass, fostering the growth of scalable and viable solutions [101]. This additional support enhances the overall viability and sustainability of oil palm fiber composites as an environmentally friendly alternative to conventional materials.
In conclusion, the utilization of composite materials derived from oil palm fibers represents a significant step towards enhancing sustainability and reducing environmental impact. Despite inheret limitations in mechanical and dimensional stability, oil palm fiber-based polymer composites offer a myriad of advantages, including natural abundance, potential weight reduction, and cost-effectiveness. The growing interest in oil palm hybrid composites further underscores their potential, offering customized mechanical, thermal and physical properties for diverse applications. The review of recent advancements in oil palm fiber hybrid composites reveals promising developments in enhancing their structural characteristics and suitability for various industries. Through the combination of different fibers and reinforcing agents, researchers have demonstrated significant improvements in the composite properties. Furthermore, the availability of oil palm biomass presents an abundant and accessible resource for the production of environmentally friendly products. However, challenges remain, particularly in optimizing manufacturing techniques, addressing interfacial adhesion issues, and ensuring long-term durability and environmental stability. Future research efforts should focus on overcoming these challenges, exploring innovative compositions, and processing parameters, and enhancing the sustainability aspects of oil palm-based composites. Overall, this review provides valuable insights and guidance for researchers and industry professionals seeking to advance the utilization of oil palm biomass in composite materials. By leveraging the unique properties of oil palm fibers and exploring hybridization techniques, we can contribute to environmental protection and sustainability efforts while unlocking new opportunities for the development of eco-friendly products across various industries.
Acknowledgement: The authors would like to express their gratitude to the Director General of MPOB for the permission to publish this review paper. Additionally, we extend our thanks to the Biomass Technology Unit and the Economic & Industry Development Division of MPOB for providing valuable data on oil palm biomass.
Funding Statement: The authors received no specific funding for this study.
Author Contributions: The authors confirm contribution to the paper as follows: study conception and design: H. A. Aisyah; data collection: H. A. Aisyah and R. A. Ilyas; analysis and interpretation of results: H. A. Aisyah, E. Hishamuddin, Z. Ibrahim and A. W. Noorshamsiana; draft manuscript preparation: H. A. Aisyah and R. A. Ilyas. All authors reviewed the results and approved the final version of the manuscript.
Availability of Data and Materials: The authors confirm that the data supporting the findings of this study are available within the article.
Ethics Approval: Not applicable.
Conflicts of Interest: The authors declare that they have no conflicts of interest to report regarding the present study.
References
1. Kerni L, Singh S, Patnaik A, Kumar N. A review on natural fiber reinforced composites. Mater Today: Proc. 2020 Jan 1;28:1616–21. [Google Scholar]
2. Karuppiah G, Kuttalam KC, Palaniappan M, Santulli C, Palanisamy S. Multiobjective optimization of fabrication parameters of jute fiber/polyester composites with egg shell powder and nanoclay filler. Molecules. 2020 Nov 27;25(23):5579. doi:10.3390/molecules25235579. [Google Scholar] [PubMed] [CrossRef]
3. Ekpenyong NE, Umoren GP, Udo IE, Yawo OJ. Assessment of thermophysical and mechanical properties of composite panels fabricated from untreated and treated coconut husk particles for structural application. J Brilliant Eng. 2022;2:4547. [Google Scholar]
4. Andrew JJ, Dhakal HN. Sustainable biobased composites for advanced applications: recent trends and future opportunities-a critical review. Compos C: Open Access. 2022 Mar 1;7:100220. [Google Scholar]
5. Malaysian Palm Oil Board (MPOB). Economics and industry development division–statistics; 2024. Available from: https://bepi.mpob.gov.my. [Accessed 2024]. [Google Scholar]
6. Gholampour A, Ozbakkaloglu T. A review of natural fiber composites: properties, modification and processing techniques, characterization, applications. J Mater Sci. 2020 Jan;55(3):829–92. doi:10.1007/s10853-019-03990-y. [Google Scholar] [CrossRef]
7. Jawaid M, Abdul Khalil HP, Bhat AH, Abu Baker A. Impact properties of natural fiber hybrid reinforced epoxy composites. Adv Mater Res. 2011 Jul 21;264:688–93. [Google Scholar]
8. Asyraf MR, Ishak MR, Syamsir A, Nurazzi NM, Sabaruddin FA, Shazleen SS, et al. Mechanical properties of oil palm fiber-reinforced polymer composites: a review. J Mater Res Technol. 2022 Mar 1;17:33–65. doi:10.1016/j.jmrt.2021.12.122. [Google Scholar] [CrossRef]
9. Anuar NI, Zakaria S, Gan S, Chia CH, Wang C, Harun J. Comparison of the morphological and mechanical properties of oil Palm EFB fibers and kenaf fibers in nonwoven reinforced composites. Ind Crops Prod. 2019 Jan 1;127:55–65. doi:10.1016/j.indcrop.2018.09.056. [Google Scholar] [CrossRef]
10. Sreekala MS, Kumaran MG, Thomas S. Oil palm fibers: morphology, chemical composition, surface modification, and mechanical properties. J Appl Polym Sci. 1997 Oct 31;66(5):821–35. doi:10.1002/(ISSN)1097-4628. [Google Scholar] [CrossRef]
11. Wahab R, Rasat MS, Fauzi NM, Sulaiman MS, Samsi HW, Mokhtar N, et al. Processing and properties of oil palm fronds composite boards from Elaeis guineensis. Elaeis Guineensis. 2021 Jun 16;217–48. [Google Scholar]
12. Ahmad Z, Saman HM, Tahir PM. Oil palm trunk fiber as a bio-waste resource for concrete reinforcement. Int J Mech Mater Eng. 2010;5(2):199–207. [Google Scholar]
13. Abdul Khalil HP, Siti Alwani M, Ridzuan R, Kamarudin H, Khairul A. Chemical composition, morphological characteristics, and cell wall structure of Malaysian oil palm fibers. Polym-Plast Technol Eng. 2008 Feb 26;47(3):273–80. doi:10.1080/03602550701866840. [Google Scholar] [CrossRef]
14. Bopda Fokam C, Toumi E, Kenmeugne B, Wiryikfu NC, Mevaa L. Experimental study of the addition of oil palm mesocarp fiber on the physical and mechanical properties of fiber cement mortar composites. SN Appl Sci. 2021 Jan;3(1):1–8. doi:10.1007/s42452-020-04037-7. [Google Scholar] [CrossRef]
15. Osman S, Ibrahim Z, Alias AH, Wahab NA, Ramli R, Hamid FA, et al. Basic properties of oil palm biomass (OPB). Oil Palm Biomass Compos Panels. 2022 Jan;1(2):39–56. doi:10.1016/B978-0-12-823852-3.00007-6. [Google Scholar] [CrossRef]
16. Izani MN, Paridah MT, Anwar UM, Nor MM, H’ng PS. Effects of fiber treatment on morphology, tensile and thermogravimetric analysis of oil palm empty fruit bunches fibers. Compos B: Eng. 2013 Feb 1;45(1):1251–7. doi:10.1016/j.compositesb.2012.07.027. [Google Scholar] [CrossRef]
17. Ibrahim Z, Aziz AA, Ramli R, Jusoff K, Ahmad M, Jamaludin MA. Effect of treatment on the oil content and surface morphology of oil palm (Elaeis guineensis) empty fruit bunches (EFB) fibers. Wood Res. 2015 Jan 1;60(1):157–66. [Google Scholar]
18. Supian MA, Amin KN, Jamari SS, Mohamad S. Production of cellulose nanofiber (CNF) from empty fruit bunch (EFB) via mechanical method. J Environ Chem Eng. 2020 Feb 1;8(1):103024. doi:10.1016/j.jece.2019.103024. [Google Scholar] [CrossRef]
19. Megashah LN, Ariffin H, Zakaria MR, Ando Y. Characteristics of cellulose from oil palm mesocarp fibers extracted by multi-step pretreatment methods. IOP Conf Ser: Materi Sci Eng. 2018;368:012001. doi:10.1088/1757-899X/368/1/012001. [Google Scholar] [CrossRef]
20. Yuliansyah AT, Hirajima T. Efficacy of hydrothermal treatment for production of solid fuel from oil palm wastes. Resour Manag Sustain Agric. 2012 Oct 24;3–20. doi:10.5772/50581. [Google Scholar] [CrossRef]
21. Alkbir MF, Sapuan SM, Nuraini AA, Ishak MR. Fiber properties and crashworthiness parameters of natural fiber-reinforced composite structure: a literature review. Compos Struct. 2016 Jul 15;148:59–73. doi:10.1016/j.compstruct.2016.01.098. [Google Scholar] [CrossRef]
22. Manik TN, Nuki SA, Fauziyah NA, Zainuri M. Structure, dynamic-mechanical and acoustic properties of oil palm trunk modified by melamine formaldehyde. J Renew Mater. 2021;9(9):1647. doi:10.32604/jrm.2021.016089. [Google Scholar] [CrossRef]
23. Hassan A, Salema AA, Ani FN, Bakar AA. A review on oil palm empty fruit bunch fiber-reinforced polymer composite materials. Polym Compos. 2010;31:2079e101. doi:10.1002/pc.21006. [Google Scholar] [CrossRef]
24. Dungani R, Jawaid M, Khalil HPSA, Jasni, Aprilia S, Hakeem KR, et al. A review on quality enhancement of oil palm trunk waste by resin impregnation: future materials. BioResources. 2013;8:3136e56. doi:10.15376/biores.8.2.3136-3156. [Google Scholar] [CrossRef]
25. Bakar AA, Hassan A, Mohd Yusof AF. The effect of oil extraction of the oil palm empty fruit bunch on the processability, impact, and flexural properties of PVC-U composites. Int J Polym Mater. 2006 Sep 1;55(9):627–41. doi:10.1080/00914030500306446. [Google Scholar] [CrossRef]
26. Bakar ES, Lee SH, Lum WC, SaifulAzry SO, Lee CH. Processing of oil palm trunk and lumber. In: Oil palm biomass for composite panels. Amsterdam, The Netherlands: Elsevier; 2022 Jan 1. p. 113–30. [Google Scholar]
27. Rahman MM, Lourenço M, Hassim HA, Baars JJ, Sonnenberg AS, Cone JW, et al. Improving ruminal degradability of oil palm fronds using white rot fungi. Anim Feed Sci Technol. 2011 Nov 3;169(3–4):157–66. doi:10.1016/j.anifeedsci.2011.06.014. [Google Scholar] [CrossRef]
28. Ong HR, Khan MM, Prasad DR, Yousuf A, Chowdhury MN. Palm kernel meal as a melamine urea formaldehyde adhesive filler for plywood applications. Int J Adhes Adhes. 2018 Oct 1;85:8–14. doi:10.1016/j.ijadhadh.2018.05.014. [Google Scholar] [CrossRef]
29. Peças P, Carvalho H, Salman H, Leite M. Natural fiber composites and their applications: a review. J Compos Sci. 2018 Nov 17;2(4):66. doi:10.3390/jcs2040066. [Google Scholar] [CrossRef]
30. Ahmed MM, Dhakal HN, Zhang ZY, Barouni A, Zahari R. Enhancement of impact toughness and damage behaviour of natural fiber reinforced composites and their hybrids through novel improvement techniques: a critical review. Compos Struct. 2021 Mar 1;259(3):113496. doi:10.1016/j.compstruct.2020.113496. [Google Scholar] [CrossRef]
31. Sumesh KR, Ajithram A, Palanisamy S, Kavimani V. Mechanical properties of ramie/flax hybrid natural fiber composites under different conditions. Biomass Convers Biorefin. 2023 Aug 21;1–2. doi:10.1007/s13399-023-04628-5 [Google Scholar] [CrossRef]
32. Swolfs Y, Gorbatikh L, Verpoest I. Fiber hybridisation in polymer composites: a review. Compos A: App Sci Manuf. 2014 Dec 1;67:181–200. doi:10.1016/j.compositesa.2014.08.027. [Google Scholar] [CrossRef]
33. Naik V, Kumar M. A review on natural fiber composite material in automotive applications. Eng Sci. 2021 Dec 7;18:1–10. [Google Scholar]
34. Jawaid M, Awad SA, Asim M, Fouad H, Alothman OY, Santulli C. A comparative evaluation of chemical, mechanical, and thermal properties of oil palm fiber/pineapple fiber reinforced phenolic hybrid composites. Polym Compos. 2021 Dec;42(12):6383–93. doi:10.1002/pc.26305. [Google Scholar] [CrossRef]
35. Hanan F, Khan T, Jawaid M, Sultan MT, Sebaey T, Singh B, et al. Thermal characterization of epoxy bilayer hybrid composites reinforced with kenaf and oil palm fibers. Polym Compos. 2023 Jan;44(1):444–52. doi:10.1002/pc.27108. [Google Scholar] [CrossRef]
36. Ramlee NA, Jawaid M, Zainudin ES, Yamani SA. Tensile, physical and morphological properties of oil palm empty fruit bunch/sugarcane bagasse fiber reinforced phenolic hybrid composites. J Mater Res Technol. 2019 Jul 1;8(4):3466–74. doi:10.1016/j.jmrt.2019.06.016. [Google Scholar] [CrossRef]
37. Ramlee NA, Jawaid M, Yamani SA, Zainudin ES, Alamery S. Effect of surface treatment on mechanical, physical and morphological properties of oil palm/bagasse fiber reinforced phenolic hybrid composites for wall thermal insulation application. Constr Build Mater. 2021 Mar 22;276:122239. doi:10.1016/j.conbuildmat.2020.122239. [Google Scholar] [CrossRef]
38. Suriani MJ, Radzi FS, Ilyas RA, Petrů M, Sapuan SM, Ruzaidi CM. Flammability, tensile, and morphological properties of oil palm empty fruit bunches fiber/pet yarn-reinforced epoxy fire retardant hybrid polymer composites. Polymers. 2021 Apr 14;13(8):1282. doi:10.3390/polym13081282. [Google Scholar] [PubMed] [CrossRef]
39. Saba N, Jawaid M, Alrashed MM, Alothman OY. Oil palm waste based hybrid nanocomposites: fire performance and structural analysis. J Build Eng. 2019 Sep 1;25:100829. doi:10.1016/j.jobe.2019.100829. [Google Scholar] [CrossRef]
40. Awad SA, Jawaid M, Fouad H, Saba N, Dhakal HN, Alothman OY, et al. A comparative assessment of chemical, mechanical, and thermal characteristics of treated oil palm/pineapple fiber/bio phenolic composites. Polym Compos. 2022;43(4):2115–28. doi:10.1002/pc.v43.4. [Google Scholar] [CrossRef]
41. Amir SM, Sultan MT, Jawaid M, Safri SN, Shah AU, Yusof MR, et al. Effects of layering sequence and gamma radiation on mechanical properties and morphology of Kevlar/oil palm EFB/epoxy hybrid composites. J Mater Res Technol. 2019 Nov 1;8(6):5362–73. doi:10.1016/j.jmrt.2019.09.003. [Google Scholar] [CrossRef]
42. Muhammad Amir SM, Hameed Sultan MT, Md Shah AU, Jawaid M, Safri SN, Mohd S, et al. Low velocity impact and compression after impact properties on gamma irradiated kevlar/oil palm empty fruit bunch hybrid composites. Coatings. 2020 Jul 3;10(7):646. doi:10.3390/coatings10070646. [Google Scholar] [CrossRef]
43. Khoshnava SM, Rostami R, Ismail M, Rahmat AR, Ogunbode BE. Woven hybrid Biocomposite: mechanical properties of woven kenaf bast fiber/oil palm empty fruit bunches hybrid reinforced poly hydroxybutyrate biocomposite as non-structural building materials. Constr Build Mater. 2017;154:155–66. doi:10.1016/j.conbuildmat.2017.07.189. [Google Scholar] [CrossRef]
44. Hanan F, Jawaid M, Paridah MT, Naveen J. Characterization of hybrid oil palm empty fruit bunch/woven kenaf fabric-reinforced epoxy composites. Polymers. 2020 Sep 9;12(9):2052. doi:10.3390/polym12092052. [Google Scholar] [PubMed] [CrossRef]
45. Idris FN, Ariffin H, Tahir PM, Ibrahim R. Feasibility of lignin-containing cellulose nanofibrils derived from oil palm empty fruit bunch in enhancing the properties of non-wood handsheets. Ind Crops Prod. 2024 Jun 1;212:118307. doi:10.1016/j.indcrop.2024.118307. [Google Scholar] [CrossRef]
46. Nuryawan A, Abdullah CK, Hazwan CM, Olaiya NG, Yahya EB, Risnasari I, et al. Enhancement of oil palm waste nanoparticles on the properties and characterization of hybrid plywood biocomposites. Polymers. 2020 Apr 27;12(5):1007. doi:10.3390/polym12051007. [Google Scholar] [PubMed] [CrossRef]
47. Mawardi I, Aprilia S, Faisal M, Rizal S. Characterization of thermal bio-insulation materials based on oil palm wood: the effect of hybridization and particle size. Polymers. 2021 Sep 26;13(19):3287. doi:10.3390/polym13193287. [Google Scholar] [PubMed] [CrossRef]
48. Mawardi I, Aprilia S, Faisal M, Rizal S. Investigation of thermal conductivity and physical properties of oil palm trunks/ramie fiber reinforced biopolymer hybrid composites as building bio-insulation. Mater Today: Proc. 2022 Jan 1;60:373–7. [Google Scholar]
49. Niyomukiza JB, Nabitaka KC, Kiwanuka M, Tiboti P, Akampulira J. Enhancing properties of unfired clay bricks using palm fronds and palm seeds. Results Eng. 2022 Dec 1;16:100632. doi:10.1016/j.rineng.2022.100632. [Google Scholar] [CrossRef]
50. Ademoh NA, Olanipekun OC. Hybridizing effect of palm frond fiber on helmet shell cast from elaeis guineensis male flower bunch fiber reinforced biocomposite. Ind Eng Lett. 2015;5(2):89. [Google Scholar]
51. Razak W, Samsi HW, Mohd TM, Mazlan M, Mohd S, Madihan Y. Physical, mechanical and morphological studies on bio-composite mixture of Oil Palm Frond and Kenaf Bast Fibers. J Plant Sci. 2016;11(1/3):22–30. [Google Scholar]
52. Boonsombuti A, Phinichkha N, Supansomboon S, Luengnaruemitchai A. The use of lignin from palm kernel shell (PKS) to fabricate oil palm mesocarp fiber (OPMF) particleboards. Int J Adhes Adhes. 2023 Jul 1;125:103425. doi:10.1016/j.ijadhadh.2023.103425. [Google Scholar] [CrossRef]
53. Padavala SS, Dey S, Veerendra GT, Manoj AV. Experimental study on concrete by partial replacement of cement with fly ash and coarse aggregates with palm kernel shells (PKS) and with addition of hybrid fibers. Chem Inorgan Mater. 2024 Apr 1;2(7):100033. doi:10.1016/j.cinorg.2024.100033. [Google Scholar] [CrossRef]
54. Oladele IO, Ibrahim IO, Adediran AA, Akinwekomi AD, Adetula YV, Olayanju TM. Modified palm kernel shell fiber/particulate cassava peel hybrid reinforced epoxy composites. Results Mater. 2020 Mar 1;5:100053. doi:10.1016/j.rinma.2019.100053. [Google Scholar] [CrossRef]
55. Lakshmaiya N, Kaliappan S, Patil PP, Ganesan V, Dhanraj JA, Sirisamphanwong C, et al. Influence of oil palm nano filler on interlaminar shear and dynamic mechanical properties of flax/epoxy-based hybrid nanocomposites under cryogenic condition. Coatings. 2022 Nov 4;12(11):1675. doi:10.3390/coatings12111675. [Google Scholar] [CrossRef]
56. Rosamah E, Hossain MS, Abdul Khalil HP, Wan Nadirah WO, Dungani R, Nur Amiranajwa AS, et al. Properties enhancement using oil palm shell nanoparticles of fibers reinforced polyester hybrid composites. Adv Compos Mater. 2017 May 4;26(3):259–72. doi:10.1080/09243046.2016.1145875. [Google Scholar] [CrossRef]
57. Suriani MJ, Ilyas RA, Zuhri MY, Khalina A, Sultan MT, Sapuan SM, et al. Critical review of natural fiber reinforced hybrid composites: processing, properties, applications and cost. Polymers. 2021 Oct 13;13(20):3514. doi:10.3390/polym13203514. [Google Scholar] [PubMed] [CrossRef]
58. Poopalam KD, Ismail TN, Hanzah NA, Alias AH, Wahab NA, Ibrahim Z, et al. Utilization of oil palm biomass and Polyurethanes as sustainable construction materials: a review. Dev Built Environ. 2024 Feb 24;17:100380. doi:10.1016/j.dibe.2024.100380 [Google Scholar] [CrossRef]
59. Hermawan D, Hazwan CM, Owolabi FA, Gopakumar DA, Hasan M, Rizal S, et al. Oil palm microfiber-reinforced handsheet-molded thermoplastic green composites for sustainable packaging applications. Prog Rubber, Plast Recycl Technol. 2019 Nov;35(4):173–87. doi:10.1177/1477760619861984. [Google Scholar] [CrossRef]
60. Meekum U, Kingchang P. Compounding oil palm empty fruit bunch/cotton fiber hybrid reinforced poly (lactic acid) biocomposites aiming for high-temperature packaging applications. BioResources. 2017 Aug 1;12(3):4670–89. doi:10.15376/biores.12.3.4670-4689. [Google Scholar] [CrossRef]
61. Asim M, Jawaid M, Saba N, Nasir M, Sultan MT. Processing of hybrid polymer composites—a review. Hybrid Polym Compos Mater. 2017 Jan 1;1–22. doi:10.1016/B978-0-08-100789-1.00001-0. [Google Scholar] [CrossRef]
62. Daramola OO, Balogun OA, Adediran AA, Saka SO, Oladele IO, Akinlabi ET. Tensile, flexural, and morphological properties of jute/oil palm pressed fruit fibers reinforced high density polyethylene hybrid composites. Fibers. 2021 Nov 2;9(11):71. doi:10.3390/fib9110071. [Google Scholar] [CrossRef]
63. Sharum MA, Rajendran TK, Maidin S, Ismail S. Investigation of oil palm fiber reinforced polylactic acid composite extruded filament quality. Eng Res Express. 2024 Jul 11;6(3):035403. doi:10.1088/2631-8695/ad5e5d. [Google Scholar] [CrossRef]
64. Balakrishnan TS, Sultan MT, Naveen J, Shahar FS, Najeeb MI, Shah AU, et al. Selection of natural fibre for pultruded hybrid synthetic/natural fibre reinforced polymer composites using analytical hierarchy process for structural applications. Polymers. 2022 Aug 4;14(15):3178. doi:10.3390/polym14153178. [Google Scholar] [PubMed] [CrossRef]
65. Hanan F, Jawaid M, Tahir PM. Mechanical performance of oil palm/kenaf fiber-reinforced epoxy-based bilayer hybrid composites. J Nat Fibers. 2020 Feb 1;17(2):155–67. doi:10.1080/15440478.2018.1477083. [Google Scholar] [CrossRef]
66. Nik Wanⓐ Wan Senik WNFA, Abu Bakar A, Mat Jusoh S, Mohamed Saat A, Zainal Mukhtar Z, Fitriadhy A, et al. Tensile and morphology analysis of oil palm trunk specimen reinforced epoxy fabricated via vacuum-assisted resin transfer moulding. In: Design in maritime engineering: contributions from the ICMAT 2021. Cham: Springer International Publishing; 2022. p. 217–28. [Google Scholar]
67. Dolah R, Karnik R, Hamdan H. A comprehensive review on biofuels from oil palm empty bunch (EFB): current status, potential, barriers and way forward. Sustainability. 2021 Sep 13;13(18):10210. doi:10.3390/su131810210. [Google Scholar] [CrossRef]
68. Mansor MR, Mustafa Z, Hadi MA, Taufiq MJ, Masripan NA, Ratanawilai T, et al. Effect of layering sequence on mechanical properties of hybrid oil palm empty fruit bunch/kenaf fiber reinforced epoxy composites. J Tribol. 2021 Mar;29:1e10. [Google Scholar]
69. Aisyah HA, Paridah MT, Sapuan SM, Ilyas RA, Khalina A, Nurazzi NM, et al. A comprehensive review on advanced sustainable woven natural fiber polymer composites. Polymers. 2021 Feb 2;13(3):471. doi:10.3390/polym13030471. [Google Scholar] [PubMed] [CrossRef]
70. Jawaid M, Khalil HA, Bakar AA. Mechanical performance of oil palm empty fruit bunches/jute fibers reinforced epoxy hybrid composites. Mate Sci Eng: A. 2010 Nov 15;527(29–30):7944–9. [Google Scholar]
71. Anuar H, Abd Rahman NA, Manshor MR, Alli YA, Alimi OA, Alif F, et al. Novel soda lignin/PLA/EPO biocomposite: a promising and sustainable material for 3D printing filament. Mater Today Commun. 2023 Jun 1;35:106093. doi:10.1016/j.mtcomm.2023.106093. [Google Scholar] [CrossRef]
72. Khankrua R, Pivsa-Art S, Hiroyuki H, Suttiruengwong S. Thermal and mechanical properties of biodegradable polyester/silica nanocomposites. Energy Proc. 2013 Jan 1;34:705–13. doi:10.1016/j.egypro.2013.06.803. [Google Scholar] [CrossRef]
73. Thoemen H, Humphrey PE. Modeling the continuous pressing process for wood-based composites. Wood Fiber Sci. 2003;35(3):456–68. [Google Scholar]
74. Viel M, Collet F, Lanos C. Development and characterization of thermal insulation materials from renewable resources. Constr Build Mater. 2019 Jul 30;214:685–97. doi:10.1016/j.conbuildmat.2019.04.139. [Google Scholar] [CrossRef]
75. Nguyen DM, Grillet AC, Bui QB, Diep TM, Woloszyn M. Building bio-insulation materials based on bamboo powder and bio-binders. Constr Build Mater. 2018 Oct 20;186(3):686–98. doi:10.1016/j.conbuildmat.2018.07.153. [Google Scholar] [CrossRef]
76. Momoh EO, Dahunsi BI. Suitability of oil-palm-broom-fibers as reinforcement for laterite-based roof tiles. Int J Softw Hardw Res Eng. 2017;5(4):27–35. [Google Scholar]
77. Momoh EO, Osofero AI, Menshykov O. Design considerations for eco-friendly palm-strand reinforced concrete for low-cost housing. Case Stud Constr Mater. 2024 Jul 1;20:e02929. doi:10.1016/j.cscm.2024.e02929. [Google Scholar] [CrossRef]
78. Muthalagu R, Srinivasan V, Sathees Kumar S, Krishna VM. Extraction and effects of mechanical characterization and thermal attributes of Jute, Prosopis juliflora bark and Kenaf fibers reinforced bio composites used for engineering applications. Fibers Polym. 2021 Jul;22(7):2018–26. doi:10.1007/s12221-021-1092-9. [Google Scholar] [CrossRef]
79. Liu D, Song J, Anderson DP, Chang PR, Hua Y. Bamboo fiber and its reinforced composites: structure and properties. Cellulose. 2012 Oct;19(5):1449–80. doi:10.1007/s10570-012-9741-1. [Google Scholar] [CrossRef]
80. Cho H, Li G, Zhu J. Ramie fibers, their composites and applications. In: Plant fibers, their composites, and applications. Woodhead Publishing; 2022 Jan 1. p. 363–78. [Google Scholar]
81. Rahman MZ. Mechanical and damping performances of flax fibre composites–a review. Compos C: Open Access. 2021 Mar 1;4(18):100081. doi:10.1016/j.jcomc.2020.100081. [Google Scholar] [CrossRef]
82. Yusof NS, Sapuan SM, Sultan MT, Jawaid M. Conceptual design of oil palm fibre reinforced polymer hybrid composite automotive crash box using integrated approach. J Central South Univ. 2020 Jan;27(1):64–75. doi:10.1007/s11771-020-4278-1. [Google Scholar] [CrossRef]
83. Jacob M, Francis B, Thomas S, Varughese KT. Dynamical mechanical analysis of sisal/oil palm hybrid fiber-reinforced natural rubber composites. Polym Compos. 2006 Dec;27(6):671–80. doi:10.1002/(ISSN)1548-0569. [Google Scholar] [CrossRef]
84. Rababah MM, AL-Oqla FM. Biopolymer composites and sustainability. In: Advanced processing, properties, and applications of starch and other bio-based polymers. Amsterdam, The Netherlands: Elsevier; 2020 Jan 1. p. 1–10. [Google Scholar]
85. RameshKumar S, Shaiju P, O’Connor KE. Bio-based and biodegradable polymers-State-of-the-art, challenges and emerging trends. Curr Opin Green Sustain Chem. 2020 Feb 1;21:75–81. doi:10.1016/j.cogsc.2019.12.005. [Google Scholar] [CrossRef]
86. Prakash SO, Sahu P, Madhan M, Johnson Santhosh A. A review on natural fibre-reinforced biopolymer composites: properties and applications. Int J Polym Sci. 2022;2022(1):7820731. [Google Scholar]
87. Yee YY, Ching YC, Rozali S, Hashim NA, Singh R. Preparation and characterization of poly (lactic acid)-based composite reinforced with oil palm empty fruit bunch fiber and nanosilica. BioResources. 2016 Jan 20;11(1):2269–86. [Google Scholar]
88. Mahmood H, Moniruzzaman M, Yusup S, Akil HM. Particulate composites based on ionic liquid-treated oil palm fiber and thermoplastic starch adhesive. Clean Technol Environ Policy. 2016 Oct;18(7):2217–26. doi:10.1007/s10098-016-1132-0. [Google Scholar] [CrossRef]
89. Campos A, Neto AS, Rodrigues VB, Luchesi BR, Mattoso LH, Marconcini JM. Effect of raw and chemically treated oil palm mesocarp fibers on thermoplastic cassava starch properties. Ind Crops Prod. 2018 Nov 15;124:149–54. doi:10.1016/j.indcrop.2018.07.075. [Google Scholar] [CrossRef]
90. Wu CS, Liao HT, Cai YX. Characterisation, biodegradability and application of palm fibre-reinforced polyhydroxyalkanoate composites. Polym Degrad Stab. 2017 Jun 1;140(6):55–63. doi:10.1016/j.polymdegradstab.2017.04.016. [Google Scholar] [CrossRef]
91. Salim YS, Abdullah AA, Sipaut CS, Nasri M, Ibrahim MN. Biosynthesis of poly(3-hydroxybutyrate-co-3-hydroxyvalerate) and characterisation of its blend with oil palm empty fruit bunch fibers. Bioresour Technol. 2011 Feb 1;102(3):3626–8. doi:10.1016/j.biortech.2010.11.020. [Google Scholar] [PubMed] [CrossRef]
92. Jumaidin R, Shafie S, Ilyas RA. Effect of coconut fiber loading on the morphological, thermal, and mechanical properties of coconut fiber reinforced thermoplastic starch/beeswax composites. Pertanika J Sci Technol. 2023 Aug 2;31:157–73. doi:10.47836/pjst.31.S1.09. [Google Scholar] [CrossRef]
93. Adnan SA, Jayganapatay J, Lai DS, Osman AF, Zaidi NH, Ibrahim I, et al. The effect of acid hydrolysis treatment on the mechanical properties of oil palm empty fruit bunches (OPEFB) fibers/thermoplastic starch. In: AIP Conference Proceedings, 2024 Apr 1; Arau, Perlis, Malaysia: AIP Publishing; vol. 2883, no. 1. [Google Scholar]
94. Baskaran M, Hashim R, Sudesh K, Sulaiman O, Hiziroglu S, Arai T, et al. Influence of steam treatment on the properties of particleboard made from oil palm trunk with addition of polyhydroxyalkanoates. Ind Crops Prod. 2013 Nov 1;51:334–41. doi:10.1016/j.indcrop.2013.09.023. [Google Scholar] [CrossRef]
95. Haafiz MM, Eichhorn SJ, Hassan A, Jawaid M. Isolation and characterization of microcrystalline cellulose from oil palm biomass residue. Carbohydr Polym. 2013 Apr 2;93(2):628–34. doi:10.1016/j.carbpol.2013.01.035. [Google Scholar] [PubMed] [CrossRef]
96. Priyadharshini M, Balaji D, Bhuvaneswari V, Rajeshkumar L, Sanjay MR, Siengchin S. Fiber reinforced composite manufacturing with the aid of artificial intelligence-a state-of-the-art review. Arch Comput Methods Eng. 2022 Nov;29(7):5511–24. doi:10.1007/s11831-022-09775-y. [Google Scholar] [CrossRef]
97. Maruthi Prashanth BH, Gomathi P, Swamy GM, Kandagal ZB, Anne G. Influence of fibre direction on the mechanical properties and artificial intelligence-based performance prediction of hybrid abaca-jute amino composites. Mater Res Express. 2024 Jul 1;11:1–12. [Google Scholar]
98. Thirupathi S, Mallichetty E, Gopalan V, Velu Pitchumani S. Areca fiber reinforced bio-materials: a review on processing, properties and advanced optimization technique. J Nat Fibers. 2024 Dec 31;21(1):2357236. doi:10.1080/15440478.2024.2357236. [Google Scholar] [CrossRef]
99. Al-Jarrah R, AL-Oqla FM. A novel integrated BPNN/SNN artificial neural network for predicting the mechanical performance of green fibers for better composite manufacturing. Compos Struct. 2022 Jun 1;289:115475. doi:10.1016/j.compstruct.2022.115475. [Google Scholar] [CrossRef]
100. Kibrete F, Trzepieciński T, Gebremedhen HS, Woldemichael DE. Artificial intelligence in predicting mechanical properties of composite materials. J Compos Sci. 2023 Sep 1;7(9):364. doi:10.3390/jcs7090364. [Google Scholar] [CrossRef]
101. Ministry of Plantation and Commodities. National biomass action plan 2023–2030. Putrajaya: Ministry of Plantation and Commodities; 2023. Available from: https://www.kpk.gov.my/kpk/. [Accessed 2024]. [Google Scholar]
Cite This Article
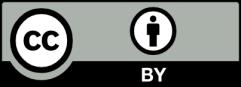
This work is licensed under a Creative Commons Attribution 4.0 International License , which permits unrestricted use, distribution, and reproduction in any medium, provided the original work is properly cited.