Open Access
ARTICLE
Mono Ethanol Amine (MEA) Pulping of Wheat Straw: An Environmentally Friendly Suggestion for the Fluff Pulp Production
1 Wood and Forest Products Division, Research Institute of Forest and Rangelands, Agricultural Research Education and Extension Organization (AREEO), Tehran, 14968-13111, Iran
2 Forest Research Division, Research Institute of Forests and Rangelands, Agricultural Research Education and Extension Organization (AREEO), Tehran, 14968-13111, Iran
3 Department of Wood and Paper Science and Technology, Faculty of Natural Resources, University of Zabol, Zabol, 98613-35856, Iran
4 Department of Wood and Paper Science and Technology, Faculty of Natural Resources, University College of Agriculture & Natural Resources, University of Tehran, Karaj, 77871-31587, Iran
* Corresponding Authors: Saeed Ismaeilimoghadam. Email: ; Mehdi Jonoobi. Email:
(This article belongs to the Special Issue: Recent Advances on Renewable Materials)
Journal of Renewable Materials 2024, 12(10), 1771-1789. https://doi.org/10.32604/jrm.2024.054888
Received 10 June 2024; Accepted 04 September 2024; Issue published 23 October 2024
Abstract
This research aimed to investigate the effect of pulping conditions and refining intensities of wheat straw to be recommended for fluff pulp production. For this purpose, mono ethanol amine (MEA) was selected as a de-lignification agent at three levels of 50:50, 25:75, and 15:85 (MEA/water, W/V %), and soda-AQ 14 W/V % was used as a reference pulping. To investigate the optimal refining intensity, the obtained pulp was passed through a single disk laboratory refiner from 0 to 6 times and in two different consistencies (1.5 and 2.5 W/V %). Total yield, kappa number, ash content, and the Schopper-Riegler (SR°) freeness of the prepared pulps were investigated. Finally, hand sheets with a targeted basic weight of 70 g/m2 were made according to the related standards. The hand sheets were characterized using Fourier transform infrared (FTIR) spectroscopy and a field emission scanning electron microscope (FE-SEM). Sheet density, brightness, and mechanical properties such as burst, tensile, and tear indices were also investigated. The FE-SEM photographs showed that the texture of the hand sheet became denser as the refining intensity increased. External fibrillation on the surface of the fibers was also observed, especially on those refined with 2.5% consistency. The results of the chemical composition of wheat straw indicated that wheat straw containing a high percentage of holocellulose is an excellent candidate for the production of fluff pulp. The total yield and kappa number of MEA pulps increased with the decrease in MEA concentration. FTIR results indicated the presence of a peak related to amino groups in the pulp related to MEA pulp. The results also indicated that the mechanical properties of the papers, except for the tear index, were enhanced as the intensity of refining and the pulp consistency during refining increased.Graphic Abstract
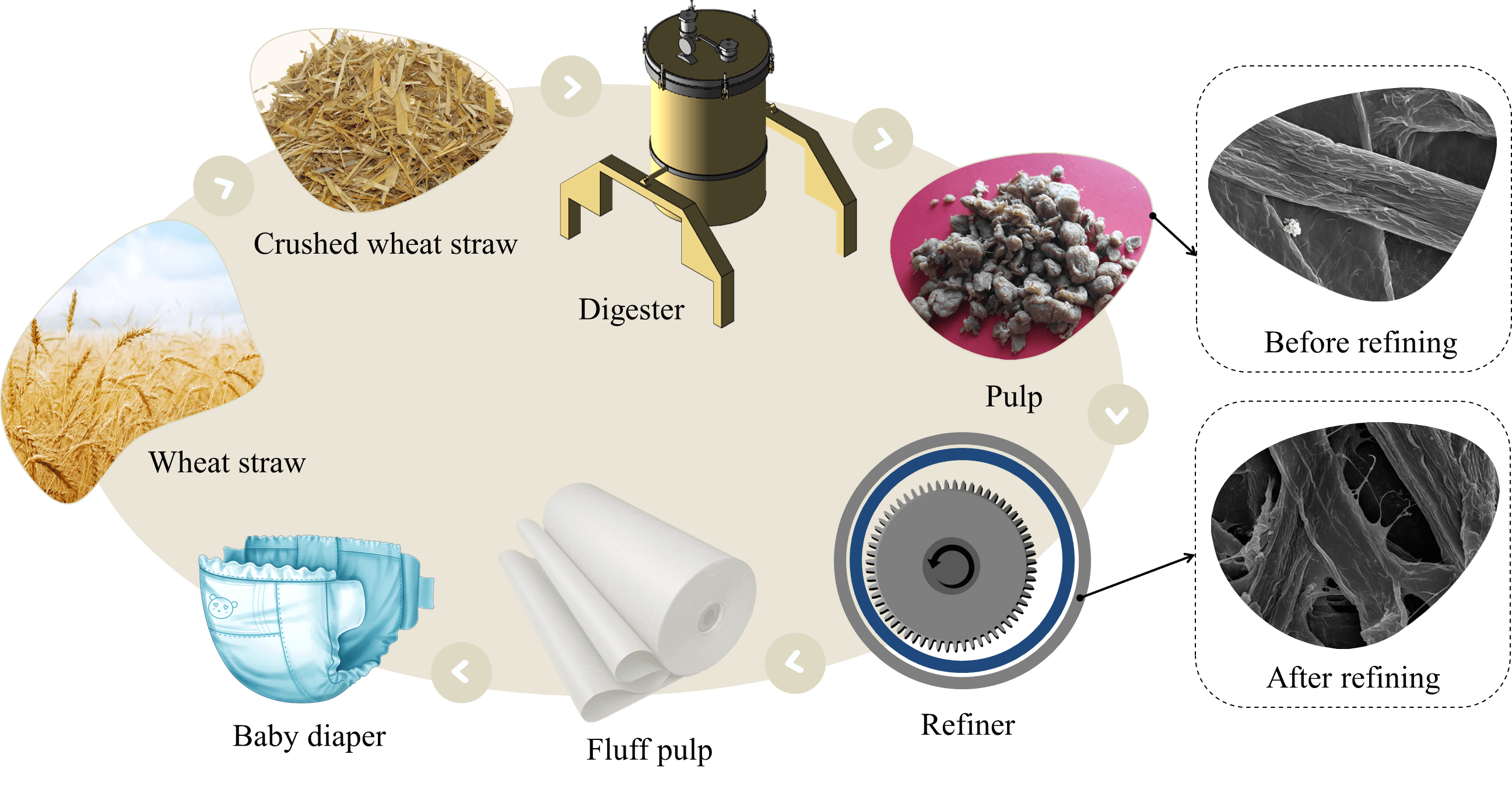
Keywords
Fluff pulp is a high grammage paper intended for the use as part of an absorbent core along with super absorbent polymers (SAPs) in hygienic products like baby diapers [1,2], sanitary napkin [3], and adult incontinence pads [4], after de-fiberization process in a hammer mill [5–7]. In 2021, about 7.8 million tons of fluff pulp were globally consumed, which is about 13% of the total consumption of pulp in the world [8]. With the current population increase and demand for cellulosic products, especially hygienic cellulosic products [9], and the reduction of the area of forests in the world, finding alternative non-wood sources for producing fluff pulp seems necessary. Fluff pulp is usually produced from softwoods; however, in recent years, attempts have been made to produce fluff pulp with hardwoods. The fluff pulp production with non-wood sources has been poorly investigated in the literature. Meanwhile, high holocellulose content lignocellulosic materials, like bagasse, seem to be good candidates for manufacturing fluff pulp. Researchers have reported that adding a small percentage of bagasse pulp to softwood pulps can produce fluff pulp with enhanced hydrophilic properties [7]. Wheat straw, another non-wood agricultural waste with an annual production of 529 million tons worldwide [10] and an excellent characterization [11], is used for paper making in some countries. In countries like Iran, considered one of the poorest countries in the world in terms of wood and forest resources, the production of fluff pulp should inevitably be in the form of a composite and a combination of wood pulp and other non-wood sources [7].
Wheat straw has characteristics that are advantageous and others that are limiting factors in the production of fluff pulp. For example, the hemicellulose of wheat straw can strongly affect the properties of the final fluff pulp [12]. A high percentage of hemicellulose creates many hydrogen bonds, which create problems during fiber separation and increases in the pulp’s knot content (un-fiberized fibers) during dry de-fiberization in hammer mill [12]. On the other hand, non-wood materials with a low percentage of hemicellulose are expected to produce fluff pulp with a high bulk, which results in dust in the hammer mill. From a fiber length point of view, the fiber length of non-wood materials should be within an acceptable range. The longer the fiber length, the more the fibers are tangled, and the resulting paper will not form well. Conversely, very short fibers generate dust during the dry de-fiberization process [6]. Exploring the literature, we found that wheat straw has good characteristics that may be a positive feature for fluff pulp production. For example, the high holocellulose percentage of wheat straw [13] makes it a very good raw material in terms of absorbent properties, especially for absorbing body liquids like urine or menses, one of the most critical features of fluff pulps. Another essential feature of wheat straw is its fiber morphology (acceptable fiber length and appropriate fiber shape), leading to good paper formation and consequently producing a paper with remarkable density and burst index, which specifies the de-fiberization type of the resulting paper in a hammer mill.
In this research, we suggest for the first time that wheat straw be used as a part of the composition of fluff pulp. There are many challenges in using non-wood materials (like wheat straw pulp) in making fluff pulp that do not exist when wood pulps, especially softwood kraft pulps, are used [5,14]. Non-wood sources of long fibers can also be as effective as wood sources of long fibers [15]. This study attempted to solve some of these challenges, including the type of pulping, the best pulping conditions, the optimal level of refining, the optimal density of wheat straw paper, etc. Nowadays, it is general knowledge that the soda pulping method is one of the best procedures to produce paper from agricultural waste [11]. However, using the soda process to produce fluff pulp has its own advantages and disadvantages. The removal of a significant part of minerals and silica during pulping, high initial brightness, and the approximate low kappa number (depending on NaOH concentration) are some of the advantages of the soda pulping process. In contrast, the soda process not only destroys lignin but also decomposes a large percentage of carbohydrates, especially hemicelluloses, during pulping [11]. The presence of hemicelluloses in fluff pulp is necessary because it facilitates the hydrogen bonds between fibers [12]. The hemicellulose also increases total yields and the hydrophilic properties of fluff pulp [12]. Mono ethanol amine (MEA), another type of pulping agent, has also attracted researchers’ attention in recent years [16]. Unlike the soda process, the MEA process (one of the best organic solvents for lignin) does not destroy carbohydrates, which leads to pulping with a higher yield than other conventional chemical processes. While there have been attempts to cook different lignocellulosic materials, i.e., wheat straw [17], fruit bunch of oil palms [18], and sugarcane bagasse [19] with the MEA process, there might be limitations in using this process for non-wood materials with high ash percentages for consumption, such as fluff pulp productions. Preserving hemicelluloses in this process might induce hydrophilic properties in the final product, one of the most important characteristics of fluff pulp [12].
The density of fluff pulp is the most essential feature of this type of pulp [7,20]. The density of the fluff pulp affects almost all of its important properties, such as tensile strength, the way it is defiberized in a hammer mill, and the energy required for the pulp’s de-fiberization [12]. Many factors affect the density of fluff pulp, the most important of which are the coarseness of the fibers [21] and the intensity of refining [22]. As mentioned, due to the increasing demand for cellulosic products as well as the reduction of forest areas in the world, the use of alternative non-wood materials, such as wheat straw, in the production of pulp and paper is inevitable.
Fluff pulp is mainly produced from the softwood kraft process. This research’s innovation is using non-wood resources to produce fluff pulp. As mentioned, the soda process is considered optimal for pulping non-wood sources, and most paper production from non-wood sources uses the soda process for pulping. In this research, we sought to compare the standard soda method with another cooking method called MEA to determine which produces a more suitable pulp for fluff pulp production. Therefore, this research aimed to compare the soda and MEA processes at varying concentrations and investigate the properties of the resulting pulps. This research can be considered environmentally friendly from two points of view: first, a lignocellulosic waste is used to produce fluff pulp, removing the need to cut down trees, and secondly, there is no need to burn the resulting black liquor in a recovery boiler in MEA processes, as the dissolved lignin can be recovered by other processes such as a spray dryer [23]. Another purpose of this study was to investigate the effect of refining intensity on the properties of the obtained pulps. After conducting this research, we should be able to accurately recommend the use of wheat straw in making fluff pulp based on the characteristics required for this kind of pulp. Although out of the scope of this paper, this pulp must be bleached to be used in making fluff pulp, and the bleaching of this pulp needs to be investigated in another study. As far as we know, there is no research investigating the properties of wheat straw pulp and its potential as a partial replacement for wood pulp in fluff pulp production, making this research necessary.
Wheat straw was collected from farms in Hashtgerd, Alborz province (Iran). Chemicals for pulping, fiber analyzing and determination of the chemical composition of wheat straw, i.e., mono ethanol amine (61.08 g.mol−1), sodium hydroxide (40 g.mol−1), anthraquinone (208.21 g.mol−1), sulfuric acid (98.08 g.mol−1), sodium chlorite (90.44 g.mol−1), acetic acid (60.05 g.mol−1), potassium permanganate (158.03 g/mol), Sodium thiosulfate (158.11 g/mol), acetone (58.08 g.mol−1), potassium iodide (166 g/mol) and safranin (350.84 g.mol−1), all were supplied from Sigma Aldrich (St. Louis, MO, USA). Hydrogen peroxide (35%, 34.01 g/mol) is purchased from Dr. Mojalali Company (Tehran, Iran). Cationic starch, for the measuring of kappa number, (pH = 6 in 2 W/V % solution) was obtained from Glucosan Company (Qazvin, Iran).
2.2 Raw Material Characterization
2.2.1 Chemical Composition of Wheat Straw
Measurement of the chemical composition of wheat straw was performed according to the TAPPI standards and references, summarized in Table 1.
2.2.2 Fiber Length Measurements
The fiber length of wheat straw and its resulted pulp was measured using a projectina optical microscope (Heerbrugg, Switzerland) after fiber maceration in acetic acid and H2O2 (50:50 V/V %) by the Franklin [32] procedure. As a summary, a small amount of each materials (pre-dried) were immersed in a Franklin solution for 24 h. The solution was then exchanged with distilled water followed by washing the material several times with distilled water. Then, a few drops of safranin were added to the fiber suspension to color it, and finally, a few drops of the colored suspension were removed and the length of the fibers was measured by an optical microscope.
The wheat straw sample was cleaned and cut into 2–3 cm pieces followed by the physical separation of all impurities and non-lignocellulosic materials from the wheat straw. Pulping conditions of wheat straw can be seen in Table 2. Which was performed in a 10 lit. circulation digester (Haato, Finland). MEA at three ratios (50:50, 25:75 and 15:85) was mixed with water and a soda process (14%) was selected as control pulping. 0.05 w% anthraquinone (AQ) was used in all pulping conditions as a constant factor. Other constant factors are as follows: maximum temperature: 170°C, time to temperature: 40 min, time at temperature: 60 min and liquar/wheat straw (L/W): 8:1. After pulping, the digester was cooled down and the resulted pulp was removed from the digester and washed several times with tap water. In the next step, the shives and uncooked materials were separated from the accepted fibers followed by the disintegration of the resulted pulp in a hand-made laboratory-scale pulper. Finally, the obtained disintegrated pulp was dried to 40% consistency and kept in a polyethylene bag. Pulping yield, ash content and kappa number (T 236 om-99) [33] of the resulted pulp were determined. Fig. 1 shows the schematic image of wheat straw from farm to diaper.
Figure 1: The schematic image of wheat straw from farm to diaper
A single disk laboratory refiner (L&W, Sweden) was used to refine the prepared pulp. The refining gap was set at 0.5 mm and the pulp suspension with two different consistencies (1.5% and 2.5%) that prepared according to TAPPI standard (T 240 om-02) [34], was passed through the refiner from 0 to 6 times. After each pass, a portion of the refined pulp was separated from the initial batch and its freeness was measured (SR°).
To investigate the physical, mechanical and optical properties of the papers, hand-sheets with a basis weight of 70 g/m2 were manufactured according to the TAPPI standard (T 205 sp-02) [35]. For this purpose, a KCL laboratory sheet former, Lorezen & Wettre (L&W, Zurich, Sweden) was used.
2.6 Fourier Transform Infrared (FTIR) Spectroscopy
A FTIR device (VECTOR33, BRUKER Co. (Germany)) was used for exploring functional groups of wheat straw and their changes after pulping with different processes. For this purpose, a small quantity of each materials (pre-dried) were mixed with potassium bromide and then spectrometry was performed on the obtained tablet.
2.7 Field Emission Scanning Electron Microscope (FE-SEM)
To illustrate the morphology and external fibrillation of fibers after refining, a field emission scanning electron microscopy (FE-SEM) was used (MIRA-II TESCAN, (Czech Republic)). For the preparation of samples, a small amount of dried fabricated papers were cut and then sputter-coated with a thin layer of gold. The SEM photography was conducted in two different magnifications of 300x and 4kx, to explore the morphology of sheets and fibers, respectively.
2.8 Physico-Mechanical and Optical Characteristics
Hand-sheets were conditioned in 23°C and 50% humidity for 24 h according to TAPPI standard (T 402 sp-03) [36]. A series of test such as physical properties, i.e., density (T 410 om-02 (grammage) [37], T 411 om-05 (Thickness) [38]), optical properties, i.e., brightness (T 452 om-02) [39] and mechanical properties, i.e., burst index (T 403 om-02) [40], tensile index (T 494 om-01) [41] and tear index (T 414 om-04) [42] were conducted on hand-sheets.
The statistical analysis was conducted using SPSS statistics software (Version 16, Armonk, NY, USA). Univariate analysis was done for analyzing the data. After observing a significant difference between the levels, Duncan’s test was used to group the means at α-value ≥ 0.05 confidence level. Each treatment was tested with five samples.
3.1 Chemical Compositions of Wheat Straw
The chemical compositions of unprocessed wheat straw are summarized in Table 3. As seen, wheat straw with a high percentage of holocellulose and an approximate low amount of lignin is an excellent candidate for the pulp and paper industries. The only limitation is its high ash content, which is expected to be largely removed from the pulp during pulping and bleeping stages.
Medium fiber length is one of the most important characteristics of fluff pulp, and fiber refining keeps many of the critical functional properties of fluff pulp (as discussed below) at an ideal level. Fiber refining should not lead to fiber length reduction. The fiber length measurements of wheat straw and refined and unrefined MEA pulp (50:50) are shown in Fig. 2. As seen, there is no significant difference between the fiber length of wheat straw and unrefined pulp, while a sharp decrease was observed in the fiber length of refined pulps. The fiber length measured in this study is almost in agreement with the results reported by other researchers [43,44].
Figure 2: Fiber length of wheat straw and MEA pulps with different consistency.
Note: A significant difference was observed between treatments, and the letters are related to the Duncan’s grouping, where the letter “a” represents the best treatment, followed by “b”, “c” and so on.
The total yield, kappa number, and ash content of different pulps are presented in Fig. 3. As shown, the total yield, kappa number, and ash content in soda pulp are much less than in the MEA pulp in different concentrations. Results showed that the MEA pulps, total yield, kappa number, and ash content were enhanced as the MEA concentrations decreased. It is worth mentioning that the ash content in soda, MEA 50:50, MEA 25:75, and MEA 15:85 compared to the pure wheat straw decreased by 59.04%, 28.35%, 24.15%, and 16.68%, respectively. In addition, more carbohydrates were retained in the MEA pulp than in the soda pulp. Therefore, the total yield can be expected to be higher in MEA pulp. As the percentage of MEA decreased (from 50% to 15%), the kappa number increased due to the reduction of lignin-attacking substance, which means that more lignin is preserved in the pulp.
Figure 3: Total yield, kappa number and ash content of different pulps
3.4 Field Emission Scanning Electron Microscope (FE-SEM)
FE-SEM images of soda and MEA 50:50 pulps in different refining intensities at low magnifications are given in Fig. 4. As can be seen, the fabricated paper’s texture becomes denser in both soda and MEA pulps as the refining intensity increases. However, this increase in density in MEA pulp is more intense than that of soda pulp. A significant number of vessels can be seen in the pulps resulting from the soda process, while the number of vessels is much less in the MEA process. This is probably due to the softening of the pulp by amine groups of MEA, which leads to thin-walled cells like vessels that are easily crushed by the refiner blades.
Figure 4: FE-SEM images with 300x magnification, soda pulping; without refining (a), soda pulp three passed refiner (b), soda pulp six passed refiner (c), MEA 50:50; without refining (d), MEA 50:50 three passed refiner (e), and MEA 50:50 six passed refiner (f)
Fig. 5 illustrates the FE-SEM images of soda and MEA 50:50 pulps in different refining intensities at high magnifications. As can be seen, with the increase of refining intensity, the fiber surfaces become strongly fibrillated (external fibrillation). At the same level of refining, MEA pulp demonstrated better fibrillation than soda pulp.
Figure 5: FE-SEM images with 4kx magnification, soda pulp; without refining (a), soda pulp three passed refiner (b), soda pulp six passed refiner (c), MEA 50:50 pulp; without refining (d), MEA 50:50 three passed refiner (e) and MEA 50:50 six passed refiner (f)
FE-SEM images of MEA 50:50 pulp refined with different consistencies are exhibited in Fig. 6. As seen, pulp refined with 2.5% consistency (Fig. 6b) is much denser than that refined with 1.5% consistencey (Fig. 6a). Moreover, an extraordinary level of external fibrillation could be observed in pulp refined with 2.5% consistency (Fig. 6d), while in pulp refined with 1.5% consistency (Fig. 6c), the fibrillation level is much lower.
Figure 6: FE-SEM images, MEA 50:50 pulp; refined with 1.5% consistency in low magnification (a), MEA 50:50 pulp refined with 2.5% consistency in low magnification (b), MEA 50:50 pulp refined with 1.5% consistency in high magnification (c) and MEA 50:50 pulp refined with 2.5% consistency in high magnification (d)
FTIR spectroscopy of wheat straw, soda and MEA 50:50 pulps is presented in Fig. 7. The peak around 3400 cm−1 is related to the stretching vibration of the hydroxyl groups in cellulose fibers [45]. The peak near 2900 cm−1 is attributed to C-H stretching vibration [46]. The stretching vibration of carbonyl groups (C=O) in the lignin structure can be seen in 1740 cm−1 [47]. This peak, which associated to the unprocessed wheat straw, has been removed after pulping in both soda and MEA pulps. The peaks around 1600 cm−1 and 1422 cm−1 are attributed to the asymmetric and symmetric stretching vibration [45,48] of carboxyl groups, respectively, which is probably related to the structure of xylene in hemicellulose of wheat straw. The intensity of these peaks in soda and MEA pulps has slightly decreased compared to the pure wheat straw. The peak in 1510 cm−1 is related to the aromatic C-H vibration [49]. This peak is also greatly reduced in soda pulp and completely eliminated in MEA pulp. The decrease in the intensity of this peak in soda pulp is related to the degradation of lignin and its removal from wheat straw, and its removal in MEA pulp is related to the amination reaction of the aromatic part of lignin [49]. The peak in 1044 cm−1 associated to the C-O stretching vibration, which represents the structure of polysaccharides [4]. It is necessary to explain that in the MEA pulp, a new peak was formed in 1375 cm−1, related to the C-N bond, which is caused by the formation of the amine group on the remaining lignin in this pulp [49].
Figure 7: FTIR spectroscopy of wheat straw, soda and MEA 50:50 pulps
Fig. 8 shows the effect of the pulping process and refining intensity on the freeness of pulps. As seen, the highest and lowest freeness are related to MEA 50:50 and MEA 15:85, respectively. The freeness was also enhanced as the refining intensity increased. An increase in water absorption characteristics of pulps is plausible by increasing the percentage of MEA and consequently decreasing the kappa number due to the removal of more lignin. For this reason, as the MEA increased, the freeness increased. Some researchers have reported that in pulps with lower kappa number, the beatability index (time needed to reach SR° freeness 30) increases [50]. However, although the soda pulp in this study had a lower kappa number than MEA 50:50, its freeness was less. This is probably due to the effect of the remaining hydrophilic amine groups on the remaining lignin (FTIR section) in MEA pulp, which caused a slight increase in the freeness compared to soda pulp. By increasing refining intensity, more fibrillation of the fiber surfaces led to an enhancement in freeness because the fiber surfaces also contain hydroxyl groups and can absorb water. Freeness is a very important factor in examining pulp and paper properties [51]. This quantity also seems very important in optimizing fibers for use as fluff pulp. The pulp with a low freeness usually represents little bonding, resulting in easy fiber separation in the hammer mill, but the final pulp may break in the production lines due to the lack of stiffness and tensile strength, leading to the stoppage of the production line. On the contrary, the high freeness of the pulp leads to strong bonding between fibers, making the final pulp difficult to dry-defiberized in a hammer mill. In this situation, undefiberized fibers (knots) can be abundantly seen in the pulp [7].
Figure 8: The effect of pulping process (a) and refining intensity (b) on the SR° freeness of pulps
The effect of pulping types and refining intensity on the density of fabricated papers is demonstrated in Fig. 9. As shown, the highest density is related to MEA 50:50. As the intensity of refining increased the density of papers enhanced. As mentioned, the density of fluff pulp is one of the most important characteristics of this product. The density of fluff pulp depends on many factors, such as the intensity of refining [22,52] and as a result, the freeness [52], the coarseness of the fibers (specific volume of fluff pulp) [21], etc. Like freeness (discussed earlier), density also determines the type of dry-defibration of the pulp in the hammer mill. Pulps with a low density lead to the production of low strength pulp which may break in the production line. On the contrary, pulps with a high density leads to the production of very stiff pulp which spends a lot of energy to separate its fibers in the hammer mill [53]. An increase in the density of papers, with increasing intensity of refining, can be related to more fibrillation of the fibers and their better entanglement [52]. The greater density of MEA 50:50 can be probably related to the greater flexibility of this pulp due to the presence of amine groups on the fiber surfaces compared to other pulps. As mentioned, the density of the papers is strongly related to their fiber coarseness. Unfortunately, there is no research focusing on the relationship between the density of the paper and the fiber’s coarseness to estimate the optimal density suitable for fluff use. However by exploring the sources, a range between 0.5 to 0.6 g/cm3 can be considered for it [7,9] (0.5 g/cm3 for papers fabricated with low fiber coarseness and 0.6 g/cm3 for papers made with high fiber coarseness). MEA 50:50 pulp with a density of about 0.35 g/cm3 has the closest density to the optimum level (0.5 g/cm3, because wheat straw has a low fiber coarseness). Its lack of density can also be compensated by mixing this pulp with softwood pulps that have fibers with higher coarseness.
Figure 9: The effect of pulping process (a) and refining intensity (b) on the density of hand-sheets
Fig. 10 shows the effect of the pulping process and refining intensity on the brightness of the hand sheets. As seen, the highest and lowest brightness were related to soda and MEA 15:85, respectively. An upward trend was observed in the brightness of the pulps as refining intensity increased. The higher brightness of soda pulp compared to other pulps is related to its lower kappa number [54]. By examining the sources, it can be seen that pulps with less than 2.5% remaining lignin (i.e., kappa of about 16 or less) are bleached more easily and with fewer chemicals than pulps with higher kappa numbers [20]. Therefore, soda pulp with a kappa of 11.6 and an initial brightness of about 32, as well as MEA 50:50 with a kappa of 12.6 and an initial brightness of about 27, will be bleached much easier than other pulps (MEA 25:75 and 15:85).
Figure 10: The effect of pulping process (a) and refining intensity (b) on the brightness of hand-sheets
The effect of pulping process and refining intensity on the burst and tensile indices of the hand-sheets is shown in Fig. 11. As shown, the highest and lowest burst and tensile indices are related to soda and MEA 15:85, respectively. On the other hand, the both burst and tensile indices of the hand-sheets enhanced as the refining intensity increased. Burst strength is one of the tests, based on its results, it is possible to find out how the final pulp is dry-defiberized in the hammer mill. According to the sources, pulps with burst index between 1.8 and 2.5 Kpa.m2/g are well dry-defiberized in a hammer mill [5,9,14]. Pulps with lower burst index should be refined to reach the optimum burst strength, but pulps with higher burst strength should be mixed with the other pulps or a de-bonding agent [6] should be used in their manufacturing process to reduce their burst strength. An increase in the burst index with increasing of the intensity of refining, is related to the external fibrillation of fibers, which leads to the bonding improvement [55]. A higher burst strength of soda pulp is related to its lower kappa number. Although soda pulp represented lower density and freeness than MEA 50:50, but the lower kappa number of soda pulp has a greater effect on increasing its burst index than the lower density and freeness on reducing the burst index. Based on the obtained results, even though MEA pulps with concentrations of 25:75 and 15:85, represented a burst index closer to the optimal level required for fluff pulp (1.8–2.5 Kpa.m2/g), but since they are difficult to bleach, they are not good pulps from this point of view. Soda pulp also has the highest burst index. But the MEA 50:50 pulp can be bleached and has a burst index closer to the optimal level, and its excess burst index can be adjusted to the optimal level using a little de-bonding agent or combining it with unrefined softwood pulps. It can be expected that the tensile strength of manufactured papers will increase with the increase of refining intensity and the increase of hydrogen bonds between fibers [51]. The higher tensile index of soda pulp is also related to its lower kappa number. The tensile index is important from the point of view that it shows the strength of the paper roll during the production of baby diapers and other hygienic products.
Figure 11: The effect of pulping process (a and c) and refining intensity (b and d) on the burst (a and b) and tensile (a and d) indices of hand-sheets
The effect of the pulping process and refining intensity on the tear index of the fabricated papers is shown in Fig. 12. As can be seen, the highest tear index is related to the soda process. An initial tear index increase was observed as the refining intensity increased, but with further increases in refining intensity, the tear index of the hand sheets decreased. Among the mechanical properties, the tear index is strongly affected by the fiber length [56]. Since the length of the fibers in the pulps decreased with the increase of the refining intensity, it can be expected that the tear index also decreases with the increase of the refining intensity.
Figure 12: The effect of pulping process (a) and refining intensity (b) on the tear index of hand-sheets
3.11 The Effect of Pulp Consistency during Refining on the Properties of Fabricated Pulp
The effects of the pulp’s consistency during refining on the SR° freeness and density of the fabricated pulp are shown in Fig. 13. Based on this figure, as pulp consistency increased during refining, both the freeness and density of the fabricated pulps increased by 23.53% and 0.26%, respectively. In order to be able to optimize the properties of the fabricated pulp, and since the pulps’ consistency during refining greatly affects the final pulp’s properties [55], the refining operation was carried out at two different consistencies (1.5% and 2.5%). The increase in the freeness and density of the papers due to the increase in consistency during refining can be related to the fibrillation of the pulp fibers [55]. More fibrillation of fibers makes the fibrillated surfaces, which mainly contain hydroxyl groups, able to absorb more water. Moreover, the fibrillation of the fiber surfaces causes more fiber entanglement during the formation of the network and causes the paper to be less thick at a constant weight, which leads to an increase in density [52].
Figure 13: The effect of consistency of pulp during refining on the SR° freeness (a) and density (b) of the fabricated pulp
Fig. 14 shows the effect of pulp consistency during refining on the brightness, burst, tensile, and tear indices of the fabricated pulp. A slight decrease was observed in the brightness when the consistency of pulps increased. On the other hand, the burst index increased by 14.15% as the pulp consistency increased during refining. This increase in burst index is related to more fiber fibrillation (refer to the FE-SEM images) due to refining with higher consistency [55]. The increase in burst index is a negative factor here because it is far from the optimal level required for fluff pulp (1.8–2.5 KPa.m2/g). Additionally, as the consistency of the pulps increased, the tensile index increased by 13.74%, while the tear index decreased by 9.74%.
Figure 14: The effect of pulp consistency during refining on the brightness (a) and burst index (b), tensile index (c) and tear index (d) of hand-sheets
This research presents an environmentally friendly method to produce fluff pulp from wheat straw using mono ethanol amine (MEA) as a delignification agent. The intensity of wheat straw pulp refining was also considered variable. The result of the fiber length analysis showed that intense refining conditions led to a sharp decrease in the fiber length. Pulping yield, kappa number, and ash content decreased with increasing MEA concentrations. FE-SEM photographs showed that fibers became more fibrillated as the refining intensity increased. In MEA processes, an extra peak related to aminated lignin was observed in FTIR spectra, probably related to the remaining aminated groups in the pulp. The results showed that the highest SR° freeness and sheet density was related to the MEA 50:50 pulp. The highest brightness, burst, tensile, and tear indices were related to the control process (Soda). As the refining intensity increased, SR° freeness, sheet density, brightness, tensile, and burst indices also increased while the tear index decreased. This research has highlighted the potential for developing an environmentally friendly fluff pulp based on agricultural waste and organic solvents. The study results show wheat straw pulp resulting from the MEA process with a concentration of 50:50 embodies almost all the features required for fluff pulp manufacturing. The refining intensity of wheat straw pulp should be mild so that the length of the fibers does not significantly decrease, the sheet density should be as close as possible to 0.5 g/cm3, the burst index should be in the range of 1.8 to 2.5 KPa.m2/g, and the freeness of pulp should be within an acceptable range. Not so free (SR° ≤ 20) that the formation of fibers is not good (non-uniform) and not so slow (SR° ≥ 30) that it is difficult to drain water from the slurry on the wire. Therefore, it could be concluded that after the bleaching process, this pulp can be a good option for producing fluff pulp or as an addition to softwood pulps to produce fluff pulp.
Acknowledgement: The authors thank the Iranian National Science Foundation for supporting this research.
Funding Statement: This study was financially supported by Iranian National Science Foundation (project number of 4020345). None external funding entity was involved.
Author Contributions: The authors confirm contribution to the paper as follows: study conception and design: Saeed Ismaeilimoghadam; data collection: Afsaneh Shahraki; analysis and interpretation of results: Saeed Mahdavi, Mehdi Pourhashemi; draft manuscript preparation: Saeed Ismaeilimoghadam, Mehdi Jonoobi. All authors reviewed the results and approved the final version of the manuscript.
Availability of Data and Materials: Not applicable.
Ethics Approval: Not applicable.
Conflicts of Interest: The authors declare that they have no known competing financial interests or personal relationships that could have appeared to influence the work reported in this paper.
References
1. Patino-Maso J, Serra-Parareda F, Tarres Q, Mutje P, Xavier Espinach F, Delgado-Aguilar M. TEMPO-oxidized cellulose nanofibers: a potential bio-based superabsorbent for diaper production. Nanomaterials. 2019;9(9):1271. doi:10.3390/nano9091271. [Google Scholar] [PubMed] [CrossRef]
2. Ismaeilimoghadam S, Jonoobi M, Hamzeh Y, Azimi B, Mezzetta A, Guazzelli L, et al. Development and characterization of sodium alginate-based bio-hybrid super absorbent polymer with high retention capacity suitable for baby diapers. J Polym Environ. 2024;64:3133. doi:10.1007/s10924-024-03297-3. [Google Scholar] [CrossRef]
3. Peng MC, Sethu V, Selvarajoo A. Performance study of chia seeds, chia flour and Mimosa pudica hydrogel as polysaccharide-based superabsorbent polymers for sanitary napkins. Mater Today Commun. 2020;26(6):101712. doi:10.1016/j.mtcomm.2020.101712. [Google Scholar] [CrossRef]
4. Ismaeilimoghadam S, Jonoobi M, Ashori A, Shahraki A, Azimi B, Danti S. Interpenetrating and semi-interpenetrating network superabsorbent hydrogels based on sodium alginate and cellulose nanocrystals: a biodegradable and high-performance solution for adult incontinence pads. Int J Biol Macromol. 2023;253(8):127118. doi:10.1016/j.ijbiomac.2023.127118. [Google Scholar] [PubMed] [CrossRef]
5. Rebola SM, Ferreira J, Evtuguin DV. Potential of bleached eucalyptus kraft pulp for applications in nonwoven fibrous fabrics. J Eng Fibers Fabrics. 2020;15(11):1–13. doi:10.1177/1558925020980146. [Google Scholar] [CrossRef]
6. Xu Shaanxi Y, Ning Shaanxi Y, Zuo L, Sun Shaanxi H. Effects of silane debonder on the properties of fluff pulp and the study of relevant mechanism. J Eng Fibers Fabrics. 2016;11(2):32–9. doi:10.1177/155892501601100205. [Google Scholar] [CrossRef]
7. Ismaeilimoghadam S, Sheikh M, Taheri P, Maleki S, Resalati H, Jonoobi M, et al. Manufacturing of fluff pulp using different pulp sources and bentonite on an industrial scale for absorbent hygienic products. Molecules. 2022;27:5022. doi:10.3390/molecules27155022. [Google Scholar] [PubMed] [CrossRef]
8. https://www.factmr.com/report/1615/fluff-pulp-market. [Accessed 2024]. [Google Scholar]
9. Xu Y, Shi T, Chen X, Liu F, Zhao W. A simple method of simultaneously endowing paper or fluff pulp with both high softness or appropriate fluffing properties and antimicrobial properties. Cellulose. 2021;28:7327–39. doi:10.1007/s10570-021-04025-z. [Google Scholar] [CrossRef]
10. Govumoni SP, Koti S, Kothagouni SY, Venkateshwar S, Linga VR. Evaluation of pretreatment methods for enzymatic saccharification of wheat straw for bioethanol production. Carbohydr Polym. 2013;91:646–50. doi:10.1016/j.carbpol.2012.08.019. [Google Scholar] [PubMed] [CrossRef]
11. Malik S, Rana V, Joshi G, Gupta PK, Sharma A. Valorization of wheat straw for the paper industry: pre-extraction of reducing sugars and its effect on pulping and papermaking properties. ACS Omega. 2020;5:30704–15. doi:10.1021/acsomega.0c04883. [Google Scholar] [PubMed] [CrossRef]
12. Lund K, Sjostrom K, Brelid H. Alkali extraction of kraft pulp fibers: influence on fiber and fluff pulp properties. J Eng Fibers Fabrics. 2012;7(2):30–9. doi:10.1177/155892501200700206. [Google Scholar] [CrossRef]
13. Singh S, Dutt D, Tyagi CH. Complete characterization of wheat straw (Triticum aestivum PBW-343 L. Emend. Fiori & PAOL.)—a renewable source of fibers for pulp and paper making. BioResources. 2011;6(1):154–77. [Google Scholar]
14. Xu Y, Wang J, Qian X, Zua L, Yue X. Effect of supplementary alkali after alkaline peroxide treatment on the properties of bleached kraft pine fluff pulp. BioResources. 2016;11(1):336–53. doi:10.15376/biores.11.1.336-353. [Google Scholar] [CrossRef]
15. Haroen WK. Fluff non-wood for health absorbent. Indo-Iranian J Sci Res. 2019;3(1):10–24. [Google Scholar]
16. Chibudike HO, Mgbachiuzo E, Ndukwe NA, Obi NI, Adeyoju OA, Chibudike C. A study on MEA-pulping of ten (10) Nigerian cultivated agro-based fiber for the production of pulp stock paper. IEEE-SEM. 2020;8(11):112–21. [Google Scholar]
17. Moezzipour B, Hedjazi S, Yousefi H, Ahmadi M. The influence of pulping process and energy consumption on properties of nanofibrillated lignocellulose (NFLC) films isolated from wheat straw. Dravna Ind. 2021;72(4):327–36. [Google Scholar]
18. Chibudike HO, Mgbachiuzo E, Ndukwe NA, Ifeanyi Obi N, Adeyoju OA, Chibudike EC. Monoethanolamine pulping of EFB (Agro-Biomass): effect of operational variables on pulp screen yield. Int J Res Innov Appl Sci. 2021;6(1):10–6. [Google Scholar]
19. Chibudike HO, Ndukwe NA, Chibudike EC, Ifeanyi Obi N, Adeyoju OA. Comparative assessment of the pulping potentials of soda and mea processes for the development of paper-pulp from sugarcane bagasse. World J Adv Res Rev. 2021;12(1):230–42. doi:10.30574/wjarr.2021.12.1.0497. [Google Scholar] [CrossRef]
20. Rebola SM, Azevedo CA, Evtuguin DV. Effect of cooking and bleaching conditions on the properties of eucalyptus kraft fluff pulps. Cellulose. 2021;28(8):4411–26. doi:10.1007/s10570-021-03789-8. [Google Scholar] [CrossRef]
21. Shao J, Liu X, Lu D, Ren S, Wang Z, Li Z, et al. Improving performance of bamboo fluff pulp by liquid hot water pretreatment and combination with longer fibers. Ind Crops Products. 2024;212:118334. doi:10.1016/j.indcrop.2024.118334. [Google Scholar] [CrossRef]
22. Motamedian HR, Halilovic AE, Kulachenko A. Mechanisms of strength and stiffness improvement of paper after PFI refining with a focus on the effect of fines. Cellulose. 2019;26:4099–124. doi:10.1007/s10570-019-02349-5. [Google Scholar] [CrossRef]
23. Wang Y, Yang G, He J, Sun G, Sun Z, Sun Y. Preparation of biochar catalyst from black liquor by spray drying andfluidized bed carbonation for biodiesel synthesis. Process Saf Environ Prot. 2020;141:333–43. doi:10.1016/j.psep.2020.04.050. [Google Scholar] [CrossRef]
24. Technical Association of the Pulp and Paper Industry (TAPPI). Sampling and preparing wood for analysis, T 257 cm-02. 2002. Available from: https://www.tappi.org/content/sarg/t257.pdf. [Accessed 2024]. [Google Scholar]
25. Technical Association of the Pulp and Paper Industry (TAPPI). Preparation of wood for chemical analysis, T 264 cm-97. 1997. Available from: https://imisrise.tappi.org/TAPPI/Products/01/T/0104T264.aspx. [Accessed 2024]. [Google Scholar]
26. Technical Association of the Pulp and Paper Industry (TAPPI). Acid-insoluble lignin in wood and pulp, T 222 om-06. 2002. Available from: https://www.tappi.org/content/SARG/T222.pdf. [Accessed 2024]. [Google Scholar]
27. Rowell RM. Wood chemistry and wood composites. Boca Raton, Florida: CRC Press; 2005. [Google Scholar]
28. Technical Association of the Pulp and Paper Industry (TAPPI). Ash in wood, pulp, paper and paperboard: combustion at 525°C, T 211 om-02. 2002. Available from: https://www.tappi.org/content/sarg/t211.pdf. [Accessed 2024]. [Google Scholar]
29. Technical Association of the Pulp and Paper Industry (TAPPI). Hot water extractable acidity or alkalinity of paper, T 428 om-04. 2004. Available from: https://imisrise.tappi.org/TAPPI/Products/01/T/0104T428.aspx. [Accessed 2024]. [Google Scholar]
30. Technical Association of the Pulp and Paper Industry (TAPPI). Water solubility of wood and pulp, T 207 cm-99. 1999. Available from: https://imisrise.tappi.org/TAPPI/Products/01/T/0104T207.aspx. [Accessed 2024]. [Google Scholar]
31. Technical Association of the Pulp and Paper Industry (TAPPI). Solvent extractives of wood and pulp (Proposed revision of T 204 cm-97), T 204 pm-97. 1979. Available from: https://www.tappi.org/content/sarg/t204.pdf. [Accessed 2024]. [Google Scholar]
32. Franklin GL. A rapid method of softening wood for anatomical analysis. Tropical Woods. 1954;88:35–6. [Google Scholar]
33. Technical Association of the Pulp and Paper Industry (TAPPI). Kappa number of pulp, T 236 om-99. 1999. Available from: https://www.tappi.org/content/SARG/T236.pdf. [Accessed 2024]. [Google Scholar]
34. Technical Association of the Pulp and Paper Industry (TAPPI). Consistency (concentration) of pulp suspensions, T 240 om-02. 2002. Available from: https://www.tappi.org/content/sarg/t240.pdf. [Accessed 2024]. [Google Scholar]
35. Technical Association of the Pulp and Paper Industry (TAPPI). Forming handsheets for physical tests of pulp, T 205 sp-02. 2002. Available from: https://www.tappi.org/content/SARG/T205.pdf. [Accessed 2024]. [Google Scholar]
36. Technical Association of the Pulp and Paper Industry (TAPPI). Standard conditioning and testing atmospheres for paper, board, pulp handsheets, and related products, T 402 sp-03. 2003. Available from: https://www.tappi.org/content/tag/sarg/t402.pdf. [Accessed 2024]. [Google Scholar]
37. Technical Association of the Pulp and Paper Industry (TAPPI). Grammage of paper and paperboard (weight per unit area), T 410 om-02. 2002. Available from: https://www.tappi.org/content/tag/sarg/t410.pdf. [Accessed 2024]. [Google Scholar]
38. Technical Association of the Pulp and Paper Industry (TAPPI). Thickness (caliper) of paper, paperboard, and combined board, T 411 om-05. 2005. Available from: https://www.tappi.org/content/SARG/T411.pdf. [Accessed 2024]. [Google Scholar]
39. Technical Association of the Pulp and Paper Industry (TAPPI). Brightness of pulp, paper, and paperboard (directional reflectance at 457 nm), T 452 om-02. 2002. Available from: https://imisrise.tappi.org/TAPPI/Products/01/T/0104T452.aspx. [Accessed 2024]. [Google Scholar]
40. Technical Association of the Pulp and Paper Industry (TAPPI). Bursting strength of paper, T 403 om-02. 2002. Available from: https://standards.globalspec.com/std/14573216/t-403-om. [Accessed 2024]. [Google Scholar]
41. Technical Association of the Pulp and Paper Industry (TAPPI). Tensile properties of paper and paperboard (using constant rate of elongation apparatus), T 494 om-01. 2001. Available from: https://www.tappi.org/content/SARG/T494.pdf. [Accessed 2024]. [Google Scholar]
42. Technical Association of the Pulp and Paper Industry (TAPPI). Internal tearing resistance of paper (Elmendorf-type method), T 414 om-04. 2004. Available from: https://imisrise.tappi.org/TAPPI/Products/01/T/0104T414.aspx. [Accessed 2024]. [Google Scholar]
43. Urdaneta F, Kumar R, Marquez R, Vera RE, Franco J, Urdaneta I, et al. Evaluating chemi-mechanical pulping processes of agricultural residues: high-yield pulps from wheat straw for fiber-based bioproducts. Indus Crpos Prod. 2024;221(2):119379. doi:10.1016/j.indcrop.2024.119379. [Google Scholar] [CrossRef]
44. Zhang X, Wang Z, Cong L, Nie S, Li J. Effects of fiber content and size on the mechanical properties of wheat straw/recycled polyethylene composites. J Polym Environ. 2020;28(5):1833–40. doi:10.1007/s10924-020-01733-8. [Google Scholar] [CrossRef]
45. Ismaeilimoghadam S, Jonoobi M, Hamzeh Y, Danti S. Effect of nanocellulose types on microporous acrylic acid/sodium alginate super absorbent polymers. J Funct Biomater. 2022;13(4):273. doi:10.3390/jfb13040273. [Google Scholar] [PubMed] [CrossRef]
46. Sepahvand S, Bahmani M, Ashori A, Pirayesh H, Yu Q, Nikkhah Dafchahi M. Preparation and characterizartion of air nanofilters based on cellulose nanofibers. Int J Biol Macromol. 2021;182(14):1392–8. doi:10.1016/j.ijbiomac.2021.05.088. [Google Scholar] [PubMed] [CrossRef]
47. Mohamadinia P, Anarjan N, Jafarizadeh-Malmiri H. Preparation and characterization of sodium alginate/acrylic acid composite hydrogels conjugated to silver nanoparticles as an antibiotic delivery system. Green Process Synth. 2021;10(1):860–73. doi:10.1515/gps-2021-0081. [Google Scholar] [CrossRef]
48. Makhado E, Pandy S, Modibane KD, Kang M, Hato MJ. Sequestration of methylene blue dye using sodium alginate poly(acrylic acid)@ZnO hydrogel nanocomposite: kinetic, Isotherm, and Thermodynamic Investigations. Int J Biol Macromol. 2020;162:60–73. doi:10.1016/j.ijbiomac.2020.06.143. [Google Scholar] [PubMed] [CrossRef]
49. Wang M, Sjöholm E, Li J. Fast and reliable quantification of lignin reactivity via reaction with dimethylamine and formaldehyde (Mannich reaction). Holzforschung. 2017;71(1):27–34. doi:10.1515/hf-2016-0054. [Google Scholar] [CrossRef]
50. Malachowska E, Dubowik M, Lipkiewicz A, Przybysz K, Przybysz P. Analysis of cellulose pulp characteristics and processing parameters for efficient paper production. Sustanability. 2020;12(17):7219. doi:10.3390/su12177219. [Google Scholar] [CrossRef]
51. Mandlez D, Zangl-Jagiello L, Eckhart R, Bauer W. Softwood kraft pulp fines: application and impact on specific refining energy and strength properties. Cellulose. 2020;27(17):10359–67. doi:10.1007/s10570-020-03467-1. [Google Scholar] [CrossRef]
52. Kayhko J, Hiltunen E, Hiltunen Y, Nikolskaya E, Kulmala L, Maloney T. Effect of compression refining on fiber properties. BioResources. 2020;15(4):8696–707. doi:10.15376/biores.15.4.8696-8707. [Google Scholar] [CrossRef]
53. Xu Y, Jiang C, Duan C, Zhang W. In-situ preparation of nano-calcium carbonate/cellulose fiber composite and its application in fluff pulp. J Eng Fibr Fabr. 2017;12(3):48–53. doi:10.1177/155892501701200306. [Google Scholar] [CrossRef]
54. Tofani G, Cornet I, Tavernier S. Estimation of hydrogen peroxide effectivity during bleaching using the kappa number. Chem Pap. 2021;75(11):5749–58. doi:10.1007/s11696-021-01756-y. [Google Scholar] [CrossRef]
55. Nugroho DDP. Low consistency refining of mixtures of softwood & hardwood bleached kraft: effects of refining power. Thailand: Asian Institute of Technology; 2012. [Google Scholar]
56. Ferdous T, Ni Y, Abdul Quaiyyum M, Nashir Uddin M, Jahan MS. Non-wood fibers: relationships of fiber properties with pulp properties. ACS Omega. 2021;6(33):21613–22. doi:10.1021/acsomega.1c02933. [Google Scholar] [PubMed] [CrossRef]
Cite This Article
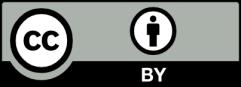
This work is licensed under a Creative Commons Attribution 4.0 International License , which permits unrestricted use, distribution, and reproduction in any medium, provided the original work is properly cited.