Open Access
ARTICLE
Determination of Physical, Mechanical and Fire Retardancy Properties of Innovative Particleboard Made from Corn Stalk (Zea mays L.) Particles
1 School of Agriculture, Food and Ecosystem Sciences, The University of Melbourne, Melbourne, 3121, Australia
2 Research Center for Biomass and Bioproducts, National Research and Innovation Agency, Bogor, 16911, Indonesia
3 Research Institute of Sustainable Humanosphere, Kyoto University, Kyoto, 611-0011, Japan
4 School of Agriculture, Food and Ecosystem Sciences, The University of Melbourne, Creswick, 3363, Australia
5 Faculty of Architecture, Building and Planning, The University of Melbourne, Melbourne, 3010, Australia
* Corresponding Author: Lilik Astari. Email:
(This article belongs to the Special Issue: Valorization of Lignocellulosic Biomass for Functional Materials)
Journal of Renewable Materials 2024, 12(10), 1729-1756. https://doi.org/10.32604/jrm.2024.054786
Received 07 June 2024; Accepted 02 September 2024; Issue published 23 October 2024
Abstract
The demand for particleboard is increasing along with economic and population growth. However, two major barriers to the manufacture of particleboard are a shortage of raw materials (woodchips) and the emission of formaldehyde from conventional adhesives. Agricultural by-products such as corn stalks contain an abundance of renewable lignocellulosic fiber. This study evaluates the effect of citric acid as a natural adhesive and fire retardant addition on the physical, mechanical, and fire retardancy properties of particleboards fabricated from corn stalks. A cost-effective and inorganic salt, calcium carbonate, was tested to enhance the fire retardancy. Ammonium dihydrogen phosphate was also considered as a comparative control. Particleboards with the addition of calcium carbonate was pretreated with sodium chloride. The particleboards were pressed for 10 min at 200°C. Japanese Industrial Standard JIS A 5908:2022 was used as the benchmark for the physical and mechanical tests. Fire retardancy was dynamically tested by simulating a Bushfire Attack Level of 19 kW/m2. The particleboard with 25 wt% citric acid had superior mechanical properties and complied with the JIS A 5908 standard for Type 13 base particleboard. Particleboard with the addition of calcium carbonate (5% and 10%) showed significantly delayed pyrolysis time.Graphic Abstract
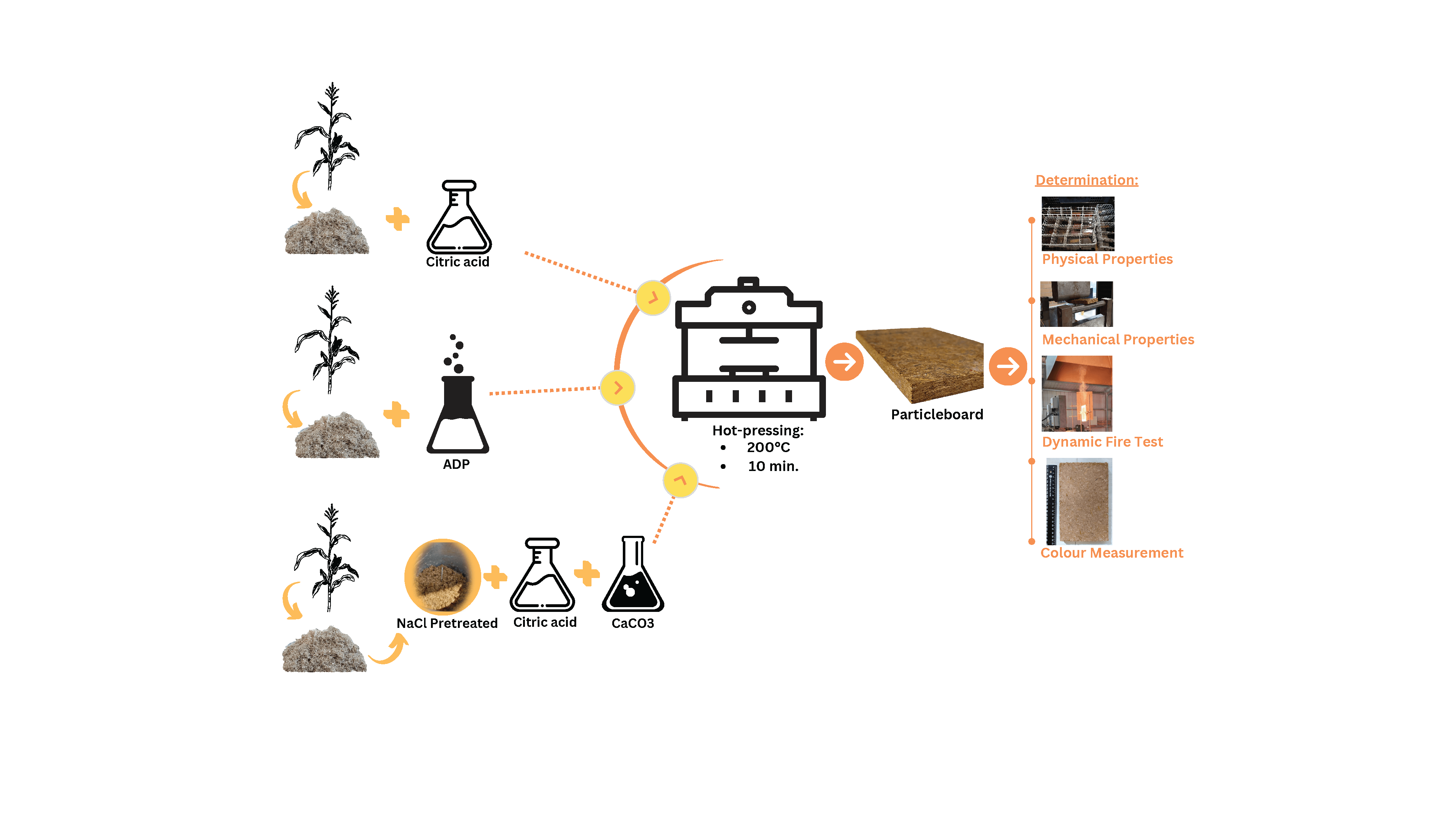
Keywords
The demand for particleboard has led to an increased demand for woodchips. According to the Food and Agricultural Organization, particleboard production has increased by 38.13%, from 76.26 million cubic metres in 2012 to 105.34 million cubic metres in 2022 [1]. However, ongoing deforestation means that wood supplies are declining [2], leading to increasing costs and competition for wood fibre. The identification of renewable non-wood lignocellulosic materials is critical to address this challenge.
Corn (Zea mays L.) is Indonesia’s second-largest food staple after rice. In 2022, Indonesia produced approximately 25.3 million tonnes of corn [3] and 55.67 million tonnes of rice [4]. Corn production generates significant agricultural by-products. According to Pordesimo et al. [5], 54.1% of a mature-age plant is composed of corn residue, comprising 50.9% stalk, 21.0% leaf, 15.2% cob and 12.9% husk. Corn stalk, which is typically burned or buried in landfill, is currently underutilised. Globally, corn residue is the highest contributor (48%) to the open burning of agricultural residues, followed by rice residue (24%), wheat residue (23%) or sugarcane residue (5%) [6]. Open burning releases air pollutants such as polycyclic hydrocarbons, particulate matter and hazardous organic compounds [7,8], negatively affecting air quality and human health.
The incorporation of 25%–50% corn stalk into poplar wood for particleboard (density 0.70 g/cm3) fabrication resulted in meeting the acceptable standard of particleboard according to European standard EN 316:1996 [9]. Ghoncheh et al. [10] found that incorporating 70% corn stalks into commercial wood chips (density of 0.75 g/cm3) using a 12% melamine-urea-formaldehyde resin and pressing for 6 min resulted in a product that met the EN 312 standard. In another study, corn stalk was mixed with oak wood using a urea-formaldehyde resin to produce a medium-density fibreboard (particleboards density 0.70 and 0.80 g/cm3) [11]. While the mechanical properties of the fibreboard became progressively less optimal with an increased proportion of corn stalk, they still complied with the minimum requirements of TS-EN 310 and TS-EN 319 (1999) [11]. Abdulqader [12] examined corn stalk as a partial wood substitute (particleboard density 0.70 g/cm3), finding that the higher the ratio of corn stalk to poplar shavings, the less optimal the physical and mechanical properties of the particleboard. However, the particleboard was still acceptable for interior applications [12]. The above studies investigated the use of corn stalk as a partial substitute for wood particles in the manufacture of particleboard. However, studies on the use of corn stalk to fully replace woodchips for particleboard fabrication are limited.
Prasetiyo et al. [13] and Ye et al. [14] both investigated the full substitution of woodchips with corn stalk for particleboard fabrication. Prasetiyo et al. [13] examined the properties of corn stalk particleboard with urea-formaldehyde and phenol-formaldehyde adhesives, finding that the particleboard with 12% phenol-formaldehyde adhesive fulfilled the Japanese Industrial Standard JIS A 5908:2022 for Type 13 particleboard [15]. These findings suggest that corn stalk may be used as a substitute for woodchips in particleboard fabrication. However, the studies discussed above all employed formaldehyde-based adhesives [16,17]. Despite their low cost and high adhesivity [17], formaldehyde-based adhesives have two main issues. First, they are based on petroleum, a non-renewable resource that is likely to be restricted in the future [18]. Second, they emit formaldehyde, which is a primary pollutant and a Group 1 human carcinogen [19]. Prolonged exposure to formaldehyde emissions by particleboard factory workers and consumers could lead to a deterioration in health. Therefore, alternative adhesives for particleboard fabrication are urgently required.
Ye et al. [14] fabricated corn stalk particleboard using dialdehyde starch as the adhesive, showing that an increase in pressing temperature, board density and dialdehyde starch dosage increased the modulus of rupture (MOR) and modulus of elasticity (MOE) and reduced thickness swelling. The challenge associated with this method is the long and complicated protocol for dialdehyde starch preparation, particularly the need for nitrogen gas and sodium periodate and the adjustment in pH level. Therefore, there is a need for an alternative non-formaldehyde adhesive that is both simple and cost effective.
Researchers have shown that citric acid (CA) can act as an adhesive in particleboard fabrication [20–22]. CA is an organic acid containing three carboxylic acids. It is naturally extracted from citrus fruits and is commonly used in the food and beverages industry [20]. Therefore, the use of CA as an adhesive in particleboard fabricated from corn stalk should be investigated. Kusumah et al. [23] investigated the effect of pre-drying and CA percentage on particleboards fabricated from sorghum bagasse as the raw material and CA as the adhesive. The addition of up to 20 wt% CA improved both the dimensional stability and the mechanical properties of the particleboard. Eterno Teixeria et al. [21] reported that particleboard based on a CA adhesive resulted in higher water resistance, MOR and MOE, meeting the EN 312:2020 standard. Based on the above results, CA may be a suitable natural adhesive for particleboard.
Despite being the most in-demand wood-based panel product, particleboard presents a challenge because of its high flammability, which limits its applications [24–26]. Thus, any comprehensive investigation on particleboard properties should include its ability to resist fire. The flammability of particleboard is mainly related to the presence of organic carbon compounds, particularly lignocellulose [27]. Fire retardants used in particleboard fabrication should ideally be low in cost, non-toxic and easily accessible. Ammonium dihydrogen phosphate (ADP) and calcium carbonate (CaCO3) are two of the preferred fire retardants. CaCO3, a naturally white and odourless powder, is an endothermic material, meaning that it absorbs heat during decomposition. At high temperatures, CaCO3 decomposes into calcium oxide and carbon dioxide (CO2). Its ability to release CO2 is the key mechanism that makes CaCO3 a favourable fire retardant. The decomposition process reduces the temperature of materials and prevents the ignition and spread of fire. The effectiveness of CaCO3 as a fire retardant depends on its proportion in the composition. Moreover, its effectiveness is influenced by other additives. Yusof et al. [28] examined the use of CaCO3 (10 and 20 wt%) as a fire retardant in particleboard, showing that the incorporation of 20% polyvinyl alcohol and 10% CaCO3 resulted in higher fire retardancy. ADP is a phosphorus-based material. Research on particleboard fabricated from hemp fibre and rice husk and exposed to fire showed that the addition of ADP 3–6 wt% resulted in a significant increase in time to ignition and a decrease in total heat release [24]. Suardana et al. [29] also found that the addition of ADP 5 wt% to a biocomposite made from coconut (Cocos nucifera L.) fibre and jute (Corchorus olitorius L.) resulted in reduced temperature and decomposition rate needed for a 5% weight loss. Komariah et al. [30] applied ADP at different percentages to particleboards fabricated with oil palm trunks.
The aim of the present study was to fabricate an eco-friendly, low-flammable using CA as the adhesive and low-cost and non-toxic fire retardant. The specific objectives were to explore:
• The physical and mechanical properties of different particleboards
• The effect of additives on particleboard colour, which can affect its durability and appearance, with darker colours indicating increased thermal degradation [31]
• Fire retardancy, measured using mass loss and pyrolysis time, to indicate the overall safety of different particleboards
• Changes in functional groups and thermal degradation of particleboard, characterised using Fourier-transform infrared (FTIR) and thermogravimetric analysis.
Corn stalks were collected from a traditional farm in the Dramaga district of Bogor Regency, West Java, Indonesia. Corn stalks were cleaned and dried at 80°C for 24 h. The dried stalks were then ground into 6–8 mesh (2.38–3.36 mm). A moisture analyser (Shimadzu MOC63u) was used to ensure that moisture content (MC) was less than 5%.
Anhydrous CA (C6H6O7) (CAS: 77-92-9) with a solid content of 59% was used as the biobased adhesive (gelation time: 4.6 min, pH: 2.3, viscosity: 7.3 mPa.s [32]).
Two fire retardants were considered in the present study, i.e., a cost-effective and inorganic salt, calcium carbonate (CaCO3), and ammonium dihydrogen phosphate (ADP) as a comparative control. Sodium chloride (NaCl) (CAS: 7647-14-5) was used to pretreat the particleboards with CaCO3 added. Either of the following fire retardants was added to different particleboard samples in different amounts:
• CaCO3 powder (CAS: 471-34-1): 5 and 10 wt%.
• ADP (NH4H2PO4) powder (CAS: 7722-76-1): 10, 20, 30 and 40 wt%.
All chemicals were used as received without further purification.
2.2 Preparation and Panel Fabrication
The particleboard panels fabricated in this study were classified as follows (see Table 1):
• Group A: untreated particleboard with the addition of ADP 10, 20, 30 or 40 wt% to identify the optimal percentage of ADP to produce a particleboard that meets the minimum JIS A 5908:2003 requirements. The controls for this group were untreated particleboard without ADP and untreated particleboard with CA 25 wt%. Astari et al. [33] found that CA 25 wt% produced the optimal physical and mechanical particleboard properties.
• Group B: particleboard pretreated with NaCl, with or without the addition of CA 25 wt% and with the addition of CaCO3 5 and 10 wt% [28].
Group A Particleboard Fabrication
Dried particles (MC < 5%) were placed in an enclosed drum mixer apparatus (see Fig. 1). The ADP solution was then sprayed onto the particles using a pneumatic spray gun. The mixed particles were then dried at 80°C for 20 h until MC reached <5%. They were then placed in a mould with metal sheets on the upper and lower surfaces and a 12-mm stop bar attached (see Fig. 2). The mixed particles were then ready for hot pressing.
Figure 1: Drum mixer
Note: (a) tube/drum; (b) spray gun.
Figure 2: The wooden and metal mould
Note: (a) Wooden mould; (b) Metal sheets at the upper and lower surfaces with stop bar attached.
Group B Particleboard Fabrication
Prior to fabricating the Group B particleboards, the particles were pretreated by immersing them in a NaCl 30 wt% solution at 60°C for 24 h to allow thorough penetration of the particles [28]. Aqueous pretreatment is typically performed for flame retardancy purposes [34] because it enables the addition of fire retardants during preparation. Following pretreatment, particles were dried in a dehydrating oven at 100°C for 24 h until MC was <5%. The particles were then mixed with either CA 25 wt%, CA 25 wt% + CaCO3 5 wt% or CA 25 wt% + CaCO3 10 wt% using a drum mixer and spray gun (as for Group A). They were also pre-dried to a target MC of <5% prior to hot pressing.
Particleboards in both groups were subject to hot pressing at 200°C for 10 min. Panel dimensions were 28.2 cm × 20.8 cm × 1.2 cm. The target density of the fabricated particleboards was 0.7 g/cm3, in line with medium-density particleboard commonly used in indoor applications, furniture and packaging [35], thin particleboards [36], and previous studies investigating using agricultural by-products [37,38]. In the present study, three replicates per panel composition were fabricated. A summary of the pressing conditions is presented in Table 2.
The physical properties of the particleboards were tested according to the JIS A 5908:2022. The JIS A 5908:2022 defines five particleboard classes (see Table 3). The physical properties measured were density, MC, thickness swelling and water absorption.
Density and Moisture Content
Particleboard density (g/cm3) was calculated at 12% MC using the following formula:
Density=mV (1)
where m is mass (g), and V is volume (cm3).
Moisture content (MC, %) was calculated as:
MC=m1− m0 m0×100 (2)
where m1 is mass before drying, and m0 is mass after drying.
Thickness Swelling and Water Absorption
Thickness swelling (TS, %) and water absorption (WA, %) were measured after 2 and 24 h immersion in water according to the following equations:
TS =t2−t1t1×100 (3)
where t1 is thickness before immersion, and t2 is thickness after immersion, and:
WA=m2−m1m1×100 (4)
where m1 is mass before immersion, and m2 is mass after immersion.
The mechanical properties of particleboards tested included flexural strength, internal bond strength (IB) and screw-holding power (SHP).
Flexural Strength
Bending strength and stiffness were tested using a universal testing machine (Instron 5569P6422, 50 kN, USA). A three-point test method with a crosshead speed of 8 mm/min was applied. The dimensions of the test sample were 200 mm × 50 mm × 12 mm. Bending strength (MOR, MPa) and stiffness (MOE, MPa) were calculated as follows:
MOR=3PL2bt2 (5)
MOE = σ/ε= ΔPL4ΔYbt3 (6)
where P is maximum load (N), L is sample length (mm), b is sample width (mm), and t is sample thickness (mm). MOE is defined as stress divided by strain, where σ denotes stress (N/m2), and ε denotes strain. ΔP is the difference between the highest and lowest loading limits (N), and ΔY is deflection with respect to ΔP (mm).
Internal Bond Strength
The sample (50 mm × 50 mm) used to test internal bond strength (IB, MPa) was attached to metal blocks with a thermosetting adhesive. Vertical tension load was applied with a loading speed of 2 mm/min [15]. IB was calculated using the following equation:
IB=P′2bL, (7)
where P is maximum load (N), b is sample width (mm), and L is sample length (mm).
Screw-Holding Power
To test SHP, two screws (3.5 mm in diameter and 30 mm in length) were placed vertically on the test sample (50 mm × 10 mm). Pulling out speed was 2 mm/min. SHP was calculated as the mean maximum load required to pull out the screws.
2.5 Thermogravimetric Analysis
TGA was carried out to determine the thermal stability of the fabricated particleboard. 6 mg of each composition were grounded to 100 mesh and placed in a ceramic pan. A thermogravimetric analyser (PerkinElmer, TGA 4000, Waltham, MA, USA) was used to investigate the loss in mass of particleboard with increased temperature. The temperature range was 25°C–750°C at a heating rate of 10°C/min. Nitrogen was applied as the purge gas during pyrolysis. The data obtained from thermogravimetric analysis explained the percentage of mass loss against temperature.
2.6 Fourier-Transform Infrared Analysis
FTIR analysis was conducted to determine the existence of any changes in functional groups in the particleboard samples. Prior to testing, the particleboard samples were immersed in water at 60°C for 4 h, and then oven dried at 60°C for 12 h. The samples were then ground to fine particles, which were further ground to 60 mesh size. A FTIR spectrometer (PerkinElmer, Spectrum Two, Waltham, MA, USA) was used to observe the infrared spectra. The analysis was conducted with a wavenumber range of 400–4000 cm−1 and an average of 16 scans.
Colour measurement was conducted to quantify the appearance of particleboard samples with different additives. The change in surface colour was measured using a spectrophotometer (Spectro-Guide 45/0 Gloss, BYK, Germany) with an observer angle of 10° and an observer diameter of 11 mm. Changes in both brightness (L*) and colour (E*) were measured. Colour coordinates on the green–red (a*) and blue–yellow (b*) axes were measured to calculate the change in colour (ΔE*). The calculations for ΔL* and ΔE* were based on JIS Z 8729:2004 as follows:
ΔL∗= L∗ − L∗0 (8)
Δa∗= a∗ − a∗0 (9)
Δb∗= b∗ − b∗0 (10)
ΔEL∗,a∗,b∗ =√ΔL∗2+ Δa∗2+Δb∗2 (11)
where L0*, a0* and b0* are the values of the particleboard with CA 0 wt%. Nine measures were taken of each particleboard surface (18 measures per board), with means and standard deviations calculated.
Sample Preparation
The particleboard samples used for the fire retardancy test were 20 cm × 12.3 cm × 1.2 cm in size. A calcium silicate thermal insulation board was used to frame the samples, helping to prevent heat loss at the edges, thereby minimising the edge effect. The board was cut into 25 mm-wide pieces, which were glued around the perimeter of the test specimen. A black sodium silicate–based sealer was applied as the adhesive. A 24 h curing time was allowed to ensure the samples were firmly attached to the frame (see Fig. 3).
Figure 3: Sample test preparation
Note: (a) Sample test; (b) calcium silicate board.
Fire Exposure Equipment
A variable heat flux apparatus (see Fig. 4) consisting of a radiative panel with 12 short-wave infrared lamps [39] was used to generate radiant heat flux. The radiative panel was positioned on a 1.5-m linear stage, allowing it to move both forwards and backwards to simulate dynamic fire exposure. The movement also enabled the sample to be exposed to various heat levels. The apparatus was connected to a device that controlled the experimental conditions and recorded the required output data. A programmable controller PCL601USB (Anaheim Automation Inc., Anaheim, CA, USA) was deployed to control the movement speed within a range of 0.001–0.3 m/s. An automatic shutter was placed between the panel and the sample to avoid premature radiation. The radiant heat flux produced by the infrared lamps was controlled using a power control box.
Figure 4: Variable heat flux apparatus
Note: (a) Linear stage; (b) radiative panel; (c) power control box; (d) programmable controller.
The tests were conducted to simulate fire exposure conditions corresponding to a Bushfire Attack Level (BAL) of 19 in the Australian standard AS 1530.8.1: 2018 [40]. BAL-19 represents an exposure to radiant heat of 19 kW/m2. To simulate these conditions, the radiative panel was programmed to move for 30 s (simulating a fire front approaching the sample), remain for 120 s (simulating exposure to a 19 kW/m2 fire), then retreat for 120 s. A water-cooled heat flux sensor (Hukseflux SBG01-100) was used to determine the exposure of samples to radiative heat flux. Prior to testing, the heat flux sensor was placed near the sample, then radiant heat flux measurements were recorded for the duration of the experiment. The samples were placed vertically 30 cm from the radiative panel at its forwardmost position and held by double clamps on both sides (see Fig. 5).
Figure 5: Sample placement
Note: (A) Side view: (i) sample, (ii) clamps; (B) Back view: (i) sample, (ii) clamps, (iii) radiative panel.
The experiments were documented using a digital single-lens reflex camera and an infrared camera (FLIR T1040), which were placed approximately 2 m from the sample. The digital single-lens reflex camera was connected to the control system and operated using Lumix camera software. The infrared camera filmed the rear surfaces of the samples.
Data were analysed using Minitab software to perform one-way analysis of variance at a confidence level of 95% (p ≤ 0.05). Fisher’s exact test was conducted to ascertain significance levels. CA, CaCO3 and ADP were treated as continuous values, while corn stalk particles were treated as discrete values.
Density and Moisture Content
Density and MC are crucial parameters because they determine the appropriate application of the particleboard. Table 4 shows the density and MC of the particleboard samples in this research.
The density of all particleboard samples was within the range 0.4–0.9 g/cm3, meeting the JIS A 5908:2022 requirement for base and decorative particleboards (see Fig. A1). The Group A particleboards showed no significant differences in density, allowing a comparison of particleboard properties. The lowest density was observed in the control sample (0.67 g/cm3), while the highest density (0.75 g/cm3) was observed in the sample with CA 25 wt%.
The Group B samples showed significant differences in density. The densities of pretreated particleboard with and without CA 25 wt% differed from that of the control particleboard, but this difference was nonsignificant. However, the pretreated particleboards with the addition of CA 25 wt% and either CaCO3 5 or 10 wt% had significantly higher densities (0.81 ± 0.06 g/cm3 and 0.80 ± 0.01 g/cm3, respectively) compared with the control samples. This indicates that the addition of CaCO3 significantly increases particleboard density.
Particleboard density is influenced by several factors, including the type and proportion of adhesives and additives, the composition of raw materials and the manufacturing process. The results highlight the effect of different types of adhesives on particleboard properties. Ozyhar [41] also found that adding CaCO3 increased the surface density of particleboard made from industrial wood chips and sawdust. The increase in the density of particleboard may be attributable to the specific gravity of CaCO3, which is higher that of corn stalk particles.
After placing particleboard samples in an oven drier at 103 ± 2°C until they reached a constant mass, MC was evaluated (see Table 4 and Fig. A2). In the Group A samples, MC ranged from 5.55% to 6.44%. The highest MC value was observed in the control sample, while the lowest was observed in the sample with CA 25 wt%. Overall, the addition of ADP decreased MC. The addition of ADP 30 wt% caused MC to dip to 6.02%, while the addition of ADP 40 wt% caused a slight rise in MC to 6.08%. The MC range in the Group A samples met the JIS A 5908:2022 requirements (5%–13%).
The MC of particleboard is affected by board density and particle porosity. Higher density particleboards tend to absorb less moisture, affecting their overall quality and compliance with standards. A lower density enables better accessibility to water vapour [42].
The MC of the Group B samples was variable. The lowest MC was observed in the pretreated samples with no CA or CaCO3 added (3.26%) and with CA 25 wt% and CaCO3 5 wt% added (2.91%). The MC of pretreated particleboards with CA 25 wt% and with CA 25 wt% and CaCO3 10 wt% differed, but the difference was nonsignificant. All pretreated samples (Group B) had an MC below the minimum JIS A 5908:2022 range (5%–13%). A low MC affects the dimensional stability and reliability of particleboard. Guan et al. [43] found that MC significantly affects the mechanical strength of self-bonding particleboard. In this research, NaCl was used as the dehydrating agent. NaCl can permeate cell walls and react with cell components, enhancing the dimension stability of cell walls [44]. Among both groups, the pretreated samples had the lowest MC values because of the addition of NaCl, which prevents water absorption.
Thickness Swelling and Water Absorption
Table 5 shows the change in thickness (thickness swelling) and water absorption after samples were immersed in water for 2 and 24 h.
For Group A, after 24 h immersion in water, the control sample showed the highest thickness swelling (108.4%), while the sample with CA 25 wt% added showed the lowest (10%). The addition of ADP up to 30 wt% also caused thickness swelling to progressively decrease from the control level, but it significantly increased with the addition of ADP 40 wt%, from 47.40% to 62.95%. Only the particleboard with CA 25 wt% met the JIS A 5908:2022 standard for base particleboard thickness swelling (25% maximum thickness swelling for particleboard of up to 12.7 mm in thickness). A similar trend was observed after 2 h immersion in water. The sample with CA 25 wt% had the lowest thickness swelling, while the control sample showed the highest thickness swelling (5.68% and 79.46%, respectively).
The decrease in thickness swelling following the addition of CA was also observed in Group B (see Fig. A3). After 24 h immersion in water, thickness swelling of pretreated particleboard decreased by 93.95% with the addition of CA 25 wt%, from 13.56% to only 0.85%. The addition of CaCO3 5 and 10 wt% resulted in a slight increase in thickness swelling, from 0.85% to 1.36% and 1.13%, respectively. However, this increase was nonsignificant. Overall, the thickness swelling of the Group B samples satisfied the JIS A 5908:2022 requirements for base and decorative particleboards. The high dimensional stability of particleboard with the addition of CA arises from the ester linkages that occur following a reaction between CA and corn stalk particles [20]. Carboxylic groups in the CA react with hydroxylic groups in the corn stalk particles, resulting in improved particleboard properties [45]. Among both groups, pretreated particleboard exhibited the lowest thickness swelling, indicating better dimensional stability.
The significant effect of CA on thickness swelling was repeated in the water absorption test. For the Group A samples, water absorption showed an identical trend to that of thickness swelling. After 24 h immersion, the control sample showed the highest water absorption (176.72%), while the sample with CA 25 wt% showed the lowest water absorption (46.46%). Progressive decreases in water absorption from the control sample level occurred with the addition of ADP 10 wt% (121.3%), ADP 20 wt% (96.00%) and ADP 30 wt% (91.03%). When ADP 40 wt% was added, water absorption slightly increased to 99.09%. However, overall, the higher the ADP percentage, the lower the water absorption. This trend was also observed by Komariah et al. [30], who found that the addition of ADP to particleboard decreased water absorption.
For Group B, following 24 h immersion in water, water absorption ranged from 10.45% (for the pretreated particleboard with the addition of CA 25 wt% and CaCO3 5 wt%) to 176.72% (for the control particleboard). The range of water absorption values was lower in Group B than in Group A.
Overall, Group B particleboards showed the highest water resistance (thickness swelling and water absorption). Group A samples showed a decreasing trend in thickness swelling and water absorption with the addition of CA and various levels of ADP (see Fig. A4). The addition of NaCl in the pretreated samples improved water resistance. NaCl is a hygroscopic substance with a crystalline structure and is thought to be deposited in cells as both small and large crystals. These crystals dissolve in high-humidity environments and recrystallise as humidity decreases. The absorbed and free water in corn particles act as solvents. The entire process of crystallisation and dissolution is reversible [46].
Flexural Strength
Table 6 shows the flexural strength of the particleboard samples with the addition of CA and fire retardants (CaCO3 and ADP). In the Group A particleboards, the addition of either ADP 20–40 wt% or CA 25 wt% increased MOR and MOE from the control sample values (7.34 MPa and 2.46 GPa, respectively). Following the addition of CA 25 wt%, MOR and MOE increased to 14.74 MPa and 6.06 GPa, respectively. This conforms to the JIS A 5908:2022 standard for Type 13 base particleboard (MOR: 13 MPa; MOE: 2.5 GPa). Kusumah et al. [23,47] also observed an increase in flexural strength with the addition of CA 20 wt% to particleboard fabricated from sweet sorghum bagasse. MOR increased from <5.00 MPa in the control sample (CA 0 wt%) to 21.80 MPa, while MOE increased from <1.00 GPa in the control sample to 5.27 GPa. However, the addition of CA 30 wt% slightly decreased the flexural strength of the samples.
In Group A, the lowest flexural strength occurred in samples with ADP 10 wt% (MOR: 6.65 MPa; MOE: 2.24 GPa). However, MOR and MOE significantly increased with the addition of ADP 20 wt% to 9.34 MPa and 3.57 GPa, respectively. There was a slight decrease in both MOR and MOE with the addition of ADP 30 wt%, but they increased again with the addition of ADP 40 wt% (MOR: 12.38 MPa; MOE: 4.06 GPa). The flexural strength of the particleboards with ADP 20–40 wt% met the minimum JIS A 5908:2022 requirements for Type 8 base particleboard (MOR: 8 MPa, MOE: 2.5 GPa). The MOR and MOE values observed in this study were higher than those reported by Komariah et al. [30] for particleboard fabricated with oil palm trunk with the addition of ADP 10–40 wt%. The authors found that the addition of ADP 10 wt% resulted in an MOR of 5.2 MPa and an MOE of 1.17 GPa. Their highest MOR and MOE values were 8.9 MPa and 2.5 GPa, respectively.
All pretreated Group B particleboards had an MOR of <8 MPa (0.72–3.95 MPa) and an MOE of <2.5 GPa (0.12–2.31 GPa). Thus, the flexural strength and stiffness of Group B particleboards were well below the JIS A 5908:2022 standard. The lowest MOR and MOE values were observed in the pretreated particleboard with no CA or CaCO3 added (0.72 MPa and 0.12 GPa, respectively), while the highest were observed in the pretreated particleboard with CA 25 wt% added (3.95 MPa and 2.31 GPa, respectively). Therefore, the addition of CA significantly increased the MOR and MOE of pretreated particleboard. However, a subsequent reduction occurred with the addition of CaCO3 5 wt% (MOR: 2.06 MPa; MOE: 1.21 GPa), followed by an increase with the addition of CaCO3 10 wt% (MOR: 3.60 MPa; MOE: 2.12 GPa). Yusof et al. [28] also observed a low MOR for oil palm trunk particleboard pretreated with NaCl (1.0 MPa) and with CaCO3 10 wt% added (1.6 MPa). The addition of NaCl causes particleboard to become brittle and dry, which is thought to be responsible for poor flexural strength. The addition of CA as an adhesive creates ester linkages between corn stalk particle hydroxyl groups [23,48], leading to high adhesiveness and improved mechanical properties, including flexural strength.
In their study of a wood–plastic composite, Cai et al. [49] also observed an increase in flexural strength following the addition of CaCO3 10 wt%, which helped to fill the tiny gaps in the particleboard. The addition of CaCO3 promoted polymer crystallisation via heterogeneous nucleation, which led to the refinement of spherocrystals. The higher the crystallisation, the better the flexural strength [49]. Thus, while pretreatment with NaCl improves the water resistance of particleboard, it reduces its flexural strength.
Internal Bond Strength
IB refers to the strength of cohesion between particles in the particleboard and determines the durability and overall strength of the board [50]. Table 7 summarises the results for IB, showing significant differences between the two groups.
In the Group A samples, average IB values ranged from 0.013 MPa to 0.183 MPa. IB significantly increased with the introduction of CA 25 wt%. A similar trend was reported by Widyorini et al. [45] in their study of particleboard fabricated from bamboo and CA. The addition of up to 30 wt% ADP resulted in no significant increases in IB. However, the addition of 40 wt% ADP resulted in a considerable increase in IB to 0.09 MPa, the highest IB value for Group A. However, this was still below the minimum standard requirement of 0.15 MPa. The IB values observed in the present study were lower than those observed by Komariah et al. [30], where the addition of ADP 10 wt% to oil palm frond particleboard resulted in an IB of 0.53 MPa. While the addition of ADP 20 wt% reduced IB, the addition of ADP 30 and 40 wt% increased IB. Thus, overall, IB showed a gradual improvement with increased ADP.
The significantly different IB values between the two groups of particleboards indicate that their chemical composition influences the bonding between particles. In Group B, the range of IB values for the pretreated samples (0.002–0.034 MPa) was significantly lower than that for Group A. The pretreated particleboard without CA or CaCO3 had the lowest IB (0.002 MPa), significantly lower than that of any of the other Group B samples. The introduction of CA 25 wt% increased IB to 0.072 MPa, the highest value observed for Group B. The subsequent addition of CaCO3 5 wt% caused a significant drop in IB to 0.030 MPa, while the addition of CaCO3 10 wt% slightly improved IB (0.034 MPa). According to JIS A 5908:2022, the minimum acceptable IB for base particleboard is 0.15 MPa, which is higher than the IB of all Group B samples. A low IB (0.14 MPa) following NaCl pretreatment was also reported by Yusof et al. [28] for particleboard fabricated using oil palm frond, although the overall IB values were higher than those of the present study. However, the authors also reported an improvement in IB following the addition of CA.
The low IB values for the pretreated particleboards indicate the poor bonding between particles as a result of the hygroscopic nature of NaCl, which causes the boards to become dry and brittle. This also demonstrates that maintaining MC at a specific level (<5% in this study) is necessary to enhance particle cohesion. Further, the addition of CaCO3 may affect the bonding between CA and corn stalk particles.
According to Komariah et al. [30], IB and MOR are correlated, which is supported in the present study, where IB and MOR values followed similar trends (see Tables 6 and 7). For example, the particleboards with a low IB also had a low MOR. Low IB indicates that particles are not sufficiently bonded to withstand applied loads. Weak bonding decreases flexural strength.
Screw-Holding Power
The SHP refers to the maximum load required to pull out a screw from a panel. Table 8 shows the SHP of the particleboards in this research. JIS A 5908:2022 requires a minimum SHP of 300 N. In Group A, the only particleboard that met this standard was that with the addition of CA 25 wt% (436.67 N). SHP ranged from 133.3 N to 436.67 N in the Group A particleboards. The addition of CA increased SHP, similar to the other mechanical properties. The addition of ADP, while progressively increasing SHP, did not boost it sufficiently to meet the minimum standard for base particleboard.
The Group B particleboards also showed low SHP values (26.67–135 N). Pretreated particleboard with no adhesive or additives had the lowest SHP (26.67 N). This is attributable to the weak internal bonding between particles following pretreatment with NaCl 30 wt%. Information on the effect of CaCO3 on the mechanical properties of particleboards is limited. Among both groups of particleboards, Group A exhibited superior results for SHP, supporting findings that the addition of CA to particleboard improves its mechanical properties.
The findings on the physical and mechanical properties of particleboards confirm that the use of CA as an adhesive could be considered a replacement for conventional petrochemical adhesives. However, additional research would be required to assess the potential degradation of the lignocellulosic material at the CA and substrate interface over time as a result of excessive acidity (i.e., lower than pH 4) [51,52]. Self-neutralizing systems have shown potential to alleviate such effect. As pointed out by Xi et al. [53], the acidic nature of CA can be counteracted by using hexamine as and acid-based buffer to maintain pH within international standard requirements. Furthermore, the use of buffer has shown to improve IB by 15%–17% as a result of more cross-linking reactions occurring during the pressing process.
3.3 Fourier-Transform Infrared Analysis
In this study, the use of CA as an adhesive and NaCl as a pretreatment led to significant improvements in the physical and mechanical properties of the particleboards. FTIR analysis confirmed the formation of ester linkages in the particleboard samples. Fig. 6 depicts the wavenumbers for each group.
Figure 6: Fourier-transform infrared analysis of particleboards
Note: (a) Group A particleboards before immersion; (b) Group A particleboards after immersion; (c) Group B particleboards before immersion; (d) Group B particleboards after immersion. ADP: ammonium dihydrogen phosphate; CA: citric acid; NaCl: sodium chloride; CaCO3: calcium carbonate.
The FTIR analysis shows that prior to immersion, Group A particleboards had wavenumbers of 1700, 1635, 1400, 1200, 1100 and 530 cm−1. Particleboards were then immersed in water at a temperature of 60°C for 4 h. Fig. 6 shows that transmittance percentage increased with an increase in ADP percentage. This indicates that the number of ester linkages increased with the progressive addition of ADP. The greater the number of ester linkages, the higher the adhesivity of the particleboard, improving its mechanical properties. According to Umemura et al. [20], ADP has a peak absorption at wavenumbers of 1400, 1100, 910 and 530 cm−1, where the peak at 1400 cm−1 is attributed to the presence of ammonium ions, and other peaks are attributed to the presence of phosphate. In the present study, the FTIR analysis of particleboard with ADP added also showed wavenumbers of 1700 and 1200 cm−1. The higher the percentage of ADP, the higher the transmittance percentage. The FTIR analysis for Group B before and after immersion (see Fig. 6a,b) showed the presence of peaks at 3200 and 3500 cm−1, as indicated by the vibration of hydroxyl groups present in lignocellulosic materials. The peak at 2900 cm−1 may be attributed to the stretching of carbon–hydrogen functional groups.
3.4 Thermogravimetric Analysis
TGA analysis showed that particleboard samples underwent two decomposition stages. The first decomposition stage resulted from a loss of moisture and volatile matter where the second was caused by a loss of mass, leading to the formation of carbonaceous char [54]. The degradation of natural particles typically occurs over two main phases: an amorphous phase and a crystalline phase. Amorphous degradation involves a loss of hemicelluloses and lignin, which have less ordered structures, while crystalline degradation mostly involves cellulose, which is more resistant [54].
In this study, the weight loss of particleboards with ADP 20%–40% during stage 1 was between 4.77%–5.80%. In the second Stage, particleboards with ADP 20%–40% showed weight loss between 54.60%–55.60% (see Fig. 7 and Table 9). In Stage 2, the addition of ADP decreased the sample weight loss when comparing to particleboard made using CA 25 wt% (65.27%).
Figure 7: Thermogravimetric analysis of particleboard
Note: CA: citric acid; NaCl: sodium chloride; CaCO3: calcium carbonate; ADP: ammonium dihydrogen phosphate.
In the particleboard made with pretreated particles and the addition of CaCO3, improvements in weight loss were observed in both stages. In Stage 1, the weight loss of particleboard with pretreated NaCl and particleboard with CaCO3 5 and 10 wt% were 0.93%, 2.12%, and 2.97%, respectively. In Stage 2, the weight loss of particleboard with pretreated NaCl and particleboard with CaCO3 5 and 10 wt% were 13.20%, 21.03% and 26.43%. The weight loss of particleboard made with pretreated particles and the addition of CaCO3 was significantly lower compared to particleboard made with CA 25 wt% (65.27%). pretreatment with NaCl eliminates hemicellulose and lignin, resulting in the prevention of heat propagation, which leads to reduced degradation [28].
The presence of CaCO3 improved the thermal resistance of the particleboard because CaCO3 and CA convert to CO2 at increased temperatures. These results indicate that pretreatment with NaCl and the addition of CaCO3 improves the fire retardancy of particleboard.
Fig. 8 and Table 10 show the results for colour measurement. In Group A, the addition of CA 25 wt% and ADP 0–40 wt% led to the darkening of the particleboard surfaces, as indicated by change in colour (∆E*) and brightness (∆L*). The control sample had a ∆E* value of 57.85 ± 4.12 and an L* value of 53.79 ± 3.90, the highest values of all particleboard samples, meaning that it was the brightest. The change in colour and brightness of particleboards with CA 25 wt% and ADP 10–40 wt% significantly differed from that of the control sample (see Fig. 8a and Table 10). Fig. 8a shows that the higher the ADP percentage, the darker the particleboard. The addition of ADP 30 and 40 wt% resulted in the darkest particleboards (L* = 36.75 ± 3.77 and 36.43 ± 1.76, respectively). This was attributed to the increased oxidation of the particleboard with increased ADP.
Figure 8: Changes in colour and brightness of particleboard
Note: Change in colour (ΔE*) in (a) Group A and (c) Group B particleboards. Change in brightness (L*) in (b) Group A and (d) Group B particleboards. CA: citric acid; ADP: ammonium dihydrogen phosphate; NaCl: sodium chloride; CaCO3: calcium carbonate.
The opposite trend occurred with particleboard brightness, which reduced with the addition of CA 25 wt% and ADP 10–40 wt%. The higher the ADP percentage, the lower the brightness. This finding aligns with those of Umemura et al. [55] and Widyorini et al. [45]. The darkening of particleboard from CA is caused by a chemical reaction, particularly thermal degradation during the hot-pressing process.
In Group B, the particleboard pretreated with NaCl with no other additives was significantly brighter than all other samples in the group. The addition of CA significantly darkened the boards, indicating the thermal degradation of hemicellulose and lignin [56]. The addition of CaCO3 resulted in a brighter particleboard compared with the pretreated particleboards with NaCl only and with CA 25 wt%. This increased brightness of particleboard was attributed to the prevention of hemicellulose and lignin degradation with the addition of CaCO3.
Table 11 and Fig. 9 show the total mass loss and pyrolysis time during the dynamic fire test using a BAL of 19 kW/m2. Pyrolysis time was the duration of visible smoke, indicating the start of thermal degradation.
Figure 9: Pyrolysis time of particleboards during dynamic fire testing as a function of particle composition
Note: ADP: ammonium dihydrogen phosphate; CA: citric acid: NaCl: sodium chloride: CaCO3: calcium carbonate.
In the Group A particleboards, mass loss during the fire retardancy test ranged from 11.87 g (± 1.99) to 15.90 g (± 0.27). Mass loss was significantly higher in the particleboard samples with ADP 10–40 wt% compared with the control sample or particleboard with CA 25 wt%, with the highest mass loss (15.9 g) being in the particleboard with ADP 30 wt%. Mass loss from the addition of ADP could be caused by early charring, which occurs during hot pressing. Charring was confirmed by colour measurement—the particleboards with ADP were darker because of higher thermal degradation.
In Group B, the pretreated particleboards lost more mass compared with the control particleboard and the particleboard with CA 25 wt% added, although this difference was nonsignificant. The highest mass loss (15.03 g) occurred in the pretreated particleboard with CA 25 wt%, which may have been caused by charring during the hot-pressing process. This was also confirmed by the colour measurement results, which showed that the pretreated particleboard with CA 25 wt% had the darkest surface.
In Group A, the addition of ADP to particleboards reduced pyrolysis time. Particleboards with ADP 10 wt% and 20 wt% had a significantly shorter pyrolysis time than that of the particleboard with CA 25 wt%. The pyrolysis time of particleboards with ADP 30 and 40 wt% was significantly longer than that of the particleboards with ADP 10 and 20 wt%. The particleboard with CA 25 wt% had the longest pyrolysis time (89.4 s). These findings contradict those of Battegazzore et al. [24], who reported that time to ignition of particleboard fabricated from hemp and rice husk increased with the addition of 0.5 g ADP. Because pyrolysis initiates ignition, the longer the pyrolysis time, the longer the time to ignition. According to Vermesi et al. [57], prior to combustion, solid materials undergo a chemical decomposition while transitioning to a gaseous state. This process is known as pyrolysis. The longer pyrolysis time for the particleboard with CA 25 wt% added indicates its superior fire retardancy properties compared with particleboards with ADP 10–40 wt% added.
In Group B, the particleboard pretreated with NaCl had a longer pyrolysis time compared with the control. The introduction of CA 25 wt% to pretreated particleboard further increased pyrolysis time. The subsequent addition of CaCO3 5 and 10 wt% resulted in significantly longer pyrolysis times compared with all other particleboards in the group (102 and 105 s, respectively). However, these differences were nonsignificant. These results confirm that pretreating corn stalk particleboard with NaCl and adding CA and CaCO3 improves its fire retardancy. Yusof et al. [28] also reported a positive result for CaCO3 as a fire retardant in particleboard fabricated from oil palm trunks. The authors reported that the limited oxygen index for particleboard with CaCO3 was significantly higher (37.17%) than that of the particleboard without CaCO3 (27.55%). The higher limited oxygen index value signifies an increased resistance to combustion. The addition of CaCO3 inhibits thermal degradation by delaying time to ignition and reducing the heat of combustion, thereby increasing fire retardancy [58].
This study showed that the addition of CA 25 wt% to particleboard fabricated from corn stalks results in a product that meets the acceptable mechanical properties for Type 13 base particleboard according to JIS A 5908:2022. Particleboard pretreated with NaCl resulted in poor mechanical properties; however, the addition of CA 25 wt% and CaCO3 improved dimensional stability, fulfilling the requirements of JIS A 5908:2022. Pretreated particleboard with the addition of CA 25 wt% also resulted in a lower ∆E* value (darker appearance) compared with other Group B particleboards. The addition of ADP resulted in a darker colour compared with the control particleboard and particleboards with CA 25 wt%. The dynamic fire test at BAL-19 showed that the addition of addition of CaCO3 (5 and 10 wt%) to the pretreated particleboard slowed pyrolysis time, thus increasing fire retardancy. The addition of ADP resulted in significantly elevated mass loss. Similarly, pretreated particleboards with added CA also had an increased mass loss. Particleboard with added ADP 30 wt% demonstrated a faster pyrolysis time, indicating faster ignition, which is less favourable for fire retardancy properties. The findings demonstrate that corn stalk, a renewable fibre material, and citric acid, as a biobased binder, can be used effectively as a suitable alternative to fabricate particleboard as a base material for laminated (veneered) applications. Future research should focus on addressing the potential risk of lignocellulosic material degradation at the substrate interface due to the acidic nature of CA. Increasing BAL rating in dynamic fire testing and including an investigation of the limited oxygen index (LOI)in addition to static fire testing would also be recommended.
Acknowledgement: The authors acknowledge Surdarmanto, Deni Purnomo, Ismadi, Narto, and Johannes Fehrmann for the technical assistance and test preparations. The authors acknowledge the facilities and scientific and technical support received from the Advance Characterisation Laboratories Cibinong-Integrated Laboratory of Bioproduct, National Research and Innovation Agency through E-Layanan Sains, Badan Riset dan Inovasi Nasional.
Funding Statement: The authors greatly thank the Australian Department of Foreign Affairs and Trade for the Australia Awards Scholarship (Lilik Astari) and the University of Melbourne for the Samuel Francis Pond Trust Round 2 for material purchase (Lilik Astari).
Author Contributions: The authors confirm contribution to the paper as follows: study conception and design: Lilik Astari, Benoit Belleville, Alex Filkov, Kenji Umemura; data collection: Lilik Astari, Benoit Belleville, Alex Filkov; analysis and interpretation: Lilik Astari, Benoit Belleville, Alex Filkov, Kenji Umemura, Barbara Ozarska; draft manuscript preparation: Lilik Astari, Benoit Belleville, Kenji Umemura, Alex Filkov, Barbara Ozarska, Robert H. Crawford. All authors reviewed the results and approved the final version of the manuscript.
Availability of Data and Materials: Data available on request from the authors. The data that support the findings of this study are available from the corresponding author (Lilik Astari), upon request.
Ethics Approval: The authors declare that the present research did not include human or animal subjects.
Conflicts of Interest: The authors declare that they have no conflicts of interest to report regarding the present study.
References
1. FAO. Forestry production and trade. 2023. Available from: https://www.fao.org/faostat/en/#data/FO. [Accessed 2023]. [Google Scholar]
2. FAO. Global deforestation slowing but tropical rainforests remain under threat, key FAO report shows. 2022. Available from: https://www.fao.org/newsroom/detail/global-deforestation-slowing-but-rainforests-under-threat-fao-report-shows-030522/en. [Accessed 2023]. [Google Scholar]
3. Coordinating-Ministry-for-Economic-Affair. Pemerintah dorong peningkatan produksi jagung nasional, melalui intensifikasi dan ekstensifikasi, khususnya perluasan lahan baru, untuk memenuhi kebutuhan nasional dan ekspor. 2022. Available from: https://ekon.go.id/publikasi/detail/4403/pemerintah-dorong-peningkatan-produksi-jagung-nasional-melalui-intensifikasi-dan-ekstensifikasi-khususnya-perluasan-lahan-baru-untuk-memenuhi-kebutuhan-nasional-dan-ekspor. [Accessed 2023]. [Google Scholar]
4. Sutrisno E. Produksi Padi di 2022 Alami Kenaikan. 2022. Available from: https://indonesia.go.id/kategori/editorial/6142/produksi-padi-di-2022-alami-kenaikan?lang=1. [Accessed 2023]. [Google Scholar]
5. Pordesimo LO, Edens WC, Sokhansanj S. Distribution of aboveground biomass in corn stover. Biomass Bioenergy. 2004;26(4):337–43. doi:10.1016/S0961-9534(03)00124-7. [Google Scholar] [CrossRef]
6. Cassou E. The challenge of agricultural pollution: evidence from China, Vietnam, and the Philippines. The World Bank Group. 2017. Available from: https://research.ebsco.com/linkprocessor/plink?id=e220f9cd-83b4-3d83-9c51-23f778e81cd. [Accessed 2024]. [Google Scholar]
7. Sharma G, Sinha B, Pallavi, Hakkim H, Chandra BP, Kumar A, et al. Gridded emissions of CO, NOx, SO2, CO2, NH3, HCl, CH4, PM2.5, PM10, BC, and NMVOC from open municipal waste Burning in India. Environ Sci Technol. 2019;53(9):4765–74. doi:10.1021/acs.est.8b07076. [Google Scholar] [PubMed] [CrossRef]
8. Park YK, Kim W, Jo YM. Release of harmful air pollutants from open burning of domestic municipal solid wastes in a metropolitan area of Korea. Aerosol Air Qual Res. 2013;13(4):1365–72. doi:10.4209/aaqr.2012.10.0272. [Google Scholar] [CrossRef]
9. Abolfazl K. Investigation on utilization of corn stalk in particleboard production. Iran J Wood Paper Sci Res. 2010;24(2):147–56. doi:10.22092/ijwpr.2010.117277. [Google Scholar] [CrossRef]
10. Ghoncheh R, Masoud A, Abolfazl K, Faezeh F. Investigating the possibility of particleboard manufacture using corn (Zea mays) stalks. Iran J Wood Paper Sci Res. 2014;28(4):608–27. doi:10.22092/ijwpr.2014.4428. [Google Scholar] [CrossRef]
11. Akgül M, Guler C, Uner B. Opportunities in utilization of agricultural residues in bio-composite production: corn stalk (Zea mays indurata Sturt) and oak wood (Quercus Robur L.) fiber in medium density fiberboard. Afr J Biotechnol. 2010;9(32):5090–8. [Google Scholar]
12. Abdulqader AA. Efficient utilization of corn stalk and poplar planer shavings in manufacturing particleboard. Maderas: Ciencia y Tecnologia. 2021;23:1–10. doi:10.4067/S0718-221X2021000100449. [Google Scholar] [CrossRef]
13. Prasetiyo KW, Astari L, Syamani FA, Subyakto. Physical and mechanical properties of urea formaldehyde and phenol formaldehyde-bonded particleboards made from corn stalk. IOP Conf Ser: Earth Environ Sci. 2019;374(1):12050. doi:10.1088/1755-1315/374/1/012050. [Google Scholar] [CrossRef]
14. Ye P, An J, Zhang G, Wang L, Wang P, Xie Y. Preparation of particleboard using dialdehyde starch and corn stalk. BioResources. 2018;13(4):8930–42. doi:10.15376/biores.13.4.8930-8942. [Google Scholar] [CrossRef]
15. JSA. Japan Industrial Standard A 5908: Particleboard. Japan: Japan Standard Association; 2022. [Google Scholar]
16. Dorn L, Thirion A, Ghorbani M, Olaechea LM, Mayer I. Exploring fully biobased adhesives: sustainable kraft lignin and 5-HMF adhesive for particleboards. Polymers. 2023;15(12):2668. doi:10.3390/polym15122668. [Google Scholar] [PubMed] [CrossRef]
17. Antov P, Savov V, Krišťák L, Réh R, Mantanis GI. Eco-friendly, high-density fiberboards bonded with urea-formaldehyde and ammonium lignosulfonate. Polymers. 2021;13(220):220. doi:10.3390/polym13020220. [Google Scholar] [PubMed] [CrossRef]
18. Lamaming J, Heng NB, Owodunni AA, Lamaming SZ, Khadir NKA, Hashim R, et al. Characterization of rubberwood particleboard made using carboxymethyl starch mixed with polyvinyl alcohol as adhesive. Compos B. 2020;183(1):107731. doi:10.1016/j.compositesb.2019.107731. [Google Scholar] [CrossRef]
19. Lyon. Formaldehyde, 2-butoxyethanol and 1-tert-butoxypropan-2-ol. IARC Monographs on the Evaluation of Carcinogenic Risks to Humans. 2006. p. 478. Available from: https://pesquisa.bvsalud.org/portal/resource/pt/mis-20789?lang=en. [Accessed 2024]. [Google Scholar]
20. Umemura K, Sugihara O, Kawai S. Investigation of a new natural adhesive composed of citric acid and sucrose for particleboard II: effects of board density and pressing temperature. J Wood Sci. 2013;61(1):40–4. doi:10.1007/s10086-014-1437-8. [Google Scholar] [CrossRef]
21. Eterno Teixeira D, do Carmo Pereira D, Diniz Nakamura AP, Silva Brum S. Adhesivity of bio-based anhydrous citric acid, tannin-citric acid and ricinoleic acid in the properties of formaldehyde-free medium density particleboard (MDP). Drvna Industrija. 2020;71(3):235–42. doi:10.5552/drvind.2020.1917. [Google Scholar] [CrossRef]
22. Kusumah SS, Astari L, Subyakto S, Widyorini R, Zhao Z. The utilization of citric acid as an environmentally friendly of chemical modification agent of the lignocellulosic materials: a review. J Lignocellulose Technol. 2018;2(1):1–7. [Google Scholar]
23. Kusumah SS, Umemura K, Yoshioka K, Miyafuji H, Kanayama K. Utilization of sweet sorghum bagasse and citric acid for manufacturing of particleboard I: effects of pre-drying treatment and citric acid content on the board properties. Ind Crops Products. 2016;84(9):34–42. doi:10.1016/j.indcrop.2016.01.042. [Google Scholar] [CrossRef]
24. Battegazzore D, Alongi J, Duraccio D, Frache A. Reuse and valorisation of hemp fibres and rice husk particles for fire resistant fibreboards and particleboards. J Polym Environ. 2018;26(9):3731–44. doi:10.1007/s10924-018-1250-3. [Google Scholar] [CrossRef]
25. Özdemir F, Serin ZO, Tutuş A. Investigation of the effect of some fire retardant chemicals and mineral materials used in surface coating on combustion performance of particleboard. BioResources. 2017;12(4):8862–9. doi:10.15376/biores.12.4.8862-8869. [Google Scholar] [CrossRef]
26. Özdemir F, Tutuş A. Effects of coating with calcite together with various fire retardants on the fire properties of particleboard. BioResources. 2016;11(3):6407–15. doi:10.15376/biores.11.3.6407-6415. [Google Scholar] [CrossRef]
27. Baskaran M, Hashim R, Leong JY, Ying Ni O, Yhaya MF, Sulaiman O. Flame retardant properties of oil palm trunk particleboard with addition of epoxy resin as a binder and aluminium hydroxide and magnesium hydroxide as additives. Bull Mater Sci. 2019;42(4):1–8. doi:10.1007/s12034-019-1785-5. [Google Scholar] [CrossRef]
28. Yusof M, Lamaming J, Hashim R, Yhaya MF, Sulaiman O, Selamat ME. Flame retardancy of particleboards made from oil palm trunk-poly(vinyl) alcohol with citric acid and calcium carbonate as additives. Constr Build Mater. 2020;263(4):120906. doi:10.1016/j.conbuildmat.2020.120906. [Google Scholar] [CrossRef]
29. Suardana NPG, Ku MS, Lim JK. Effects of diammonium phosphate on the flammability and mechanical properties of bio-composites. Mater Design. 2011;32(4):1990–9. doi:10.1016/j.matdes.2010.11.069. [Google Scholar] [CrossRef]
30. Komariah RN, Miyamoto T, Tanaka S, Prasetiyo KW, Syamani FA, Subyakto, et al. High-performance binderless particleboard from the inner part of oil palm trunk by addition of ammonium dihydrogen phosphate. Ind Crops Products. 2019;141(3):111761. doi:10.1016/j.indcrop.2019.111761. [Google Scholar] [CrossRef]
31. Moya R, Camacho D, Mata J, Fallas RS. Fungal decay, coating, burning properties and change of color of particleboards manufactured with woody biomass, agricultural wastes and tetra pak residues. J Biomater Nanobiotechnol. 2013;4(4):334–42. doi:10.4236/jbnb.2013.44042. [Google Scholar] [CrossRef]
32. Sutiawan J, Syahfitri A, Purnomo D, Sudarmanto, Narto F, Akbar D, et al. Characterization and application of non-formaldehyde binder based citric acid, maleic acid, and molasses adhesive for plywood composite. Polymers. 2023;15(19):3897. doi:10.3390/polym15193897. [Google Scholar] [PubMed] [CrossRef]
33. Astari L, Belleville B, Ozarska B, Umemura K, Crawford R, Ismayati M, et al. Performance of self-binding engineered panels made from sweet corn stalks (Zea mays L.) for furniture applications. Bioresour Technol Rep. 2024;25(4):101802. doi:10.1016/j.biteb.2024.101802. [Google Scholar] [CrossRef]
34. Lazko J, Landercy N, Laoutid F, Dangreau L, Huguet MH, Talon O. Flame retardant treatments of insulating agro-materials from flax short fibres. Polym Degrad Stab. 2013;98(5):1043–51. doi:10.1016/j.polymdegradstab.2013.02.002. [Google Scholar] [CrossRef]
35. Santos J, Fernandes RA, Ferreira N, Ferreira I, Vieira C, Magalhaes FD, et al. New particleboards for food-packaging from poplar peeling by-products using a circular economy approach. Int J Adhes Adhes. 2024;129(6):103563. doi:10.1016/j.ijadhadh.2023.103563. [Google Scholar] [CrossRef]
36. EWPAA. Facts about particleboard and MDF. Australian Wood Panels Association Incorporated Queensland, Australia. 2008. Available from: https://www.australiantimbers.com.au/wp-content/uploads/2018/04/ewpaa_facts_about_pb_and_mdf.pdf.pdf. [Accessed 2024]. [Google Scholar]
37. Luo P, Yang CM, Li MY, Wang YQ. Manufacture of thin rice straw particleboards bonded with various polymeric methane diphenyl diisocyanate/urea formaldehyde resin mixtures. BioResources. 2020;15(1):935–44. doi:10.15376/biores.15.1.935-944. [Google Scholar] [CrossRef]
38. Zakia H, Taha A, Mervat K, Adel B, Samir A, Jutta H, et al. Rice straw and flax fiber particleboards as a product of agricultural waste: an evaluation of technical properties. Appl Sci. 2019;9(18):3878. doi:10.3390/app9183878. [Google Scholar] [CrossRef]
39. Miller TS, Filkov AI, Penman TD. Improved laboratory method to test flammability metrics of live plants under dynamic conditions and future implications. Int J Wildland Fire. 2022;32((2 )):277–95. doi:10.1071/WF21172. [Google Scholar] [CrossRef]
40. Standards Australia. AS 1530.8.1: methods for fire tests on building materials, components and structures. Part 8.1: test on element construction for buildings exposed to simulated bushfire attack-Radiant heat and small flaming sources. Australian Standard. Sydney, Australia. 2018. Available from: https://www.saiglobal.com/pdftemp/previews/osh/as/as1000/1500/1530.8.1-2007.pdf. [Accessed 2023]. [Google Scholar]
41. Ozyhar T. Application of mineral filler in surface layer of three-layer particleboard and its effect on material properties as a function of filler content. Int Wood Prod J. 2020;11(3):109–14. doi:10.1080/20426445.2020.1735753. [Google Scholar] [CrossRef]
42. Apri Heri I, Febrianto F, Hadi Y, Ruhendi S, Hermawan D. The effect of pressing temperature and time on the quality of particleboard made from jatropha fruit hulls treated in acidic condition. Makara J Technol. 2013;17(3):145–51. doi:10.7454/mst.v17i3.2930. [Google Scholar] [CrossRef]
43. Guan M, Bai L, Fu R, Han YL, Liang H. Effects of the type of lactic acid bacteria, hot-pressing temperature, and moisture content of fermented bamboo residue on the properties of self-bonding common particleboards. BioResources. 2023;18(2):3295–307. doi:10.15376/biores.18.2.3295-3307. [Google Scholar] [CrossRef]
44. Jiang J, Li J, Gao Q. Effect of flame retardant treatment on dimensional stability and thermal degradation of wood. Constr Build Mater. 2015;75:74–81. doi:10.1016/j.conbuildmat.2014.10.037. [Google Scholar] [CrossRef]
45. Widyorini R, Umemura K, Isnan R, Putra DR, Awaludin A, Prayitno TA. Manufacture and properties of citric acid-bonded particleboard made from bamboo materials. Eur J Wood Wood Prod. 2015;74(1):57–65. doi:10.1007/s00107-015-0967-0. [Google Scholar] [CrossRef]
46. Pařil P, Dejmal A. Moisture absorption and dimensional stability of poplar wood impregnated with sucrose and sodium chloride. Maderas: Ciencia y Tecnología. 2014;16(3):299–312. doi:10.4067/S0718-221X2014005000023. [Google Scholar] [CrossRef]
47. Kusumah SS, Umemura K, Guswenrivo I, Yoshimura T, Kanayama K. Utilization of sweet sorghum bagasse and citric acid for manufacturing of particleboard II: influences of pressing temperature and time on particleboard properties. J Wood Sci. 2017;63(2):161–72. doi:10.1007/s10086-016-1605-0. [Google Scholar] [CrossRef]
48. Widyorini R, Nugraha PA, Arief Rahman MZ, Prayitno TA. Bonding ability of a new adhesive composed of citric acid-sucrose for particleboard. BioResources. 2016;11(2):4526–35. doi:10.15376/biores.11.2.4526-4535. [Google Scholar] [CrossRef]
49. Cai H, Yang K, Yi W. Effects of calcium carbonate on preparation and mechanical properties of wood/plastic composite. Int J Agric Biol Eng. 2017;10(1):184–90. doi:10.3965/j.ijabe.20171001.2707. [Google Scholar] [CrossRef]
50. Ferdosian F, Pan Z, Guchuhan G, Boxin Z. Bio-based adhesives and evaluation for wood composites application. Polymers. 2017;9(2):70. doi:10.3390/polym9020070. [Google Scholar] [PubMed] [CrossRef]
51. Plath E. Studien über Phenolharzleime.—Zweite Mitteilung: die Prüfung von PF-Harzen auf Säureschädigungen. Holz als Roh-und Werkstoff. 1953;11(12):466–71 (In German). doi:10.1007/bf02606973. [Google Scholar] [CrossRef]
52. Sodhi JS. Über die Säure-Schädigung von Holz bei der Verleimung mit Phenolharzleimen. Holz als Roh-und Werkstoff: Holz als Roh-und Werkstoff. 1957;15(6):261–3 (In German). doi:10.1007/bf02609442. [Google Scholar] [CrossRef]
53. Xi X, Zhou X, Du G, Pizzi A, Lei H. Self-neutralizing melamine-urea–formaldehyde-citric acid resins for wood panel adhesives. Polymers. 2024;16(13):1819. doi:10.3390/polym16131819. [Google Scholar] [PubMed] [CrossRef]
54. Ergun ME, Özlüsoylu İ., İstek A, Can A. Analysis and impact of activated carbon incorporation into urea-formaldehyde adhesive on the properties of particleboard. Coatings. 2023;13(9):1476. doi:10.3390/coatings13091476. [Google Scholar] [CrossRef]
55. Umemura K, Sugihara O, Kawai S. Investigation of a new natural adhesive composed of citric acid and sucrose for particleboard. J Wood Sci. 2013;59(3):203–8. doi:10.1007/s10086-013-1326-6. [Google Scholar] [CrossRef]
56. Hon DN-S, Shiraishi N. Wood and cellulosic chemistry/edited by David N-S. Hon, Nobuo Shiraish. New York, USA: Marcel Dekker Inc.; 2001. [Google Scholar]
57. Vermesi I, Roenner N, Pironi P, Hadden RM, Rein G. Pyrolysis and ignition of a polymer by transient irradiation. Combustion Flame. 2016;163(12):31–41. doi:10.1016/j.combustflame.2015.08.006. [Google Scholar] [CrossRef]
58. Schirp A, Su S. Effectiveness of pre-treated wood particles and halogen-free flame retardants used in wood-plastic composites. Polym Degrad Stab. 2016;126(2):81–92. doi:10.1016/j.polymdegradstab.2016.01.016. [Google Scholar] [CrossRef]
Appendix A
Figure A1: Density of particleboards by composition
Note: ADP: ammonium dihydrogen phosphate; CA: citric acid: NaCl: sodium chloride; CaCO3: calcium carbonate. Dotted lines indicate minimum and maximum density requirements according to JIS A 5908:2022.
Figure A2: Moisture content of particleboards by composition
Note: ADP: ammonium dihydrogen phosphate; CA: citric acid: NaCl: sodium chloride; CaCO3: calcium carbonate. Dotted lines indicate minimum and maximum density requirements according to JIS A 5908:2022.
Figure A3: Thickness swelling of particleboards after 2- and 24-h immersion in water
Note: ADP: ammonium dihydrogen phosphate; CA: citric acid: NaCl: sodium chloride; CaCO3: calcium carbonate.
Figure A4: Water absorption of particleboards after 2- and 24-h immersion in water
Note: ADP: ammonium dihydrogen phosphate; CA: citric acid: NaCl: sodium chloride; CaCO3: calcium carbonate.
Cite This Article
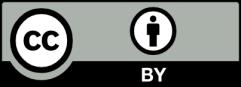
This work is licensed under a Creative Commons Attribution 4.0 International License , which permits unrestricted use, distribution, and reproduction in any medium, provided the original work is properly cited.