Open Access
ARTICLE
Chemically Modified Sugarcane Bagasse for Innovative Bio-Composites. Part One: Production and Physico-Mechanical Properties
1 Department of Wood and Paper Science and Technology, Faculty of Natural Resources, University College of Agriculture and Natural Resources, University of Tehran, Karaj, 3158777871, Iran
2 CIRAD, UPR BioWooEB, Montpellier, F-34398, France
3 BioWooEB, University of Montpellier, CIRAD, Montpellier, F-34398, France
* Corresponding Authors: Peyman Ahmadi. Email: ; Davood Efhamisisi. Email:
Journal of Renewable Materials 2024, 12(10), 1715-1728. https://doi.org/10.32604/jrm.2024.054076
Received 18 May 2024; Accepted 21 August 2024; Issue published 23 October 2024
Abstract
Sugarcane bagasse is an agro-waste that could replace timber resources for the production of bio-composites. Composite boards such as particleboard offer an issue for the use and recycling of poor quality timber, and these engineered products can overcome some solid wood limitations such as heterogeneity and dimension. Bagasse offers an alternative to wood chips for particleboard production but present some disadvantages as well, such as poor physico-mechanical properties. To address these issues, bagasse fibers were treated with an innovative natural resin formulated with tannin and furfural. Impregnated particles with different concentrations of resin (5%, 10%, and 15% m/m) were exposed to temperatures of 40°C, 60°C, 80°C, and 100°C for resin curing. Various types of tannin-based adhesives, including tannin formaldehyde, tannin/formaldehyde-furfural, and tannin hexamine, were utilized for bonding the treated bagasse particles. The resultant panels were assessed for their physical and mechanical properties and compared to those produced using Melamine-Urea-Formaldehyde (MUF) adhesive. The density of the panels varied from 650 to 730 kg/m3 depending on the resin concentration. The values for both modulus of elasticity and modulus of rupture increased as the resin concentration increased. The internal bonding values exhibited an increase with resin concentration up to a critical point, after which a decreasing trend was observed. The water absorption and thickness swelling were significantly reduced with an increase in resin concentration. However, the panels produced using MUF adhesive yielded the most favorable physico-mechanical properties. Additionally, the panels made with tannin-based adhesives met the minimum requirements specified in the standard EN 312 (specifications for uncoated resin-bonded particleboards) for application in dry conditions. The analysis of formaldehyde emissions indicated that panels produced with tannin-based adhesives exhibited significantly lower emissions compared to those made with MUF. The tannin/furfural resin showed great potential for improving the quality of bagasse particleboard using tannin-based adhesives.Graphic Abstract
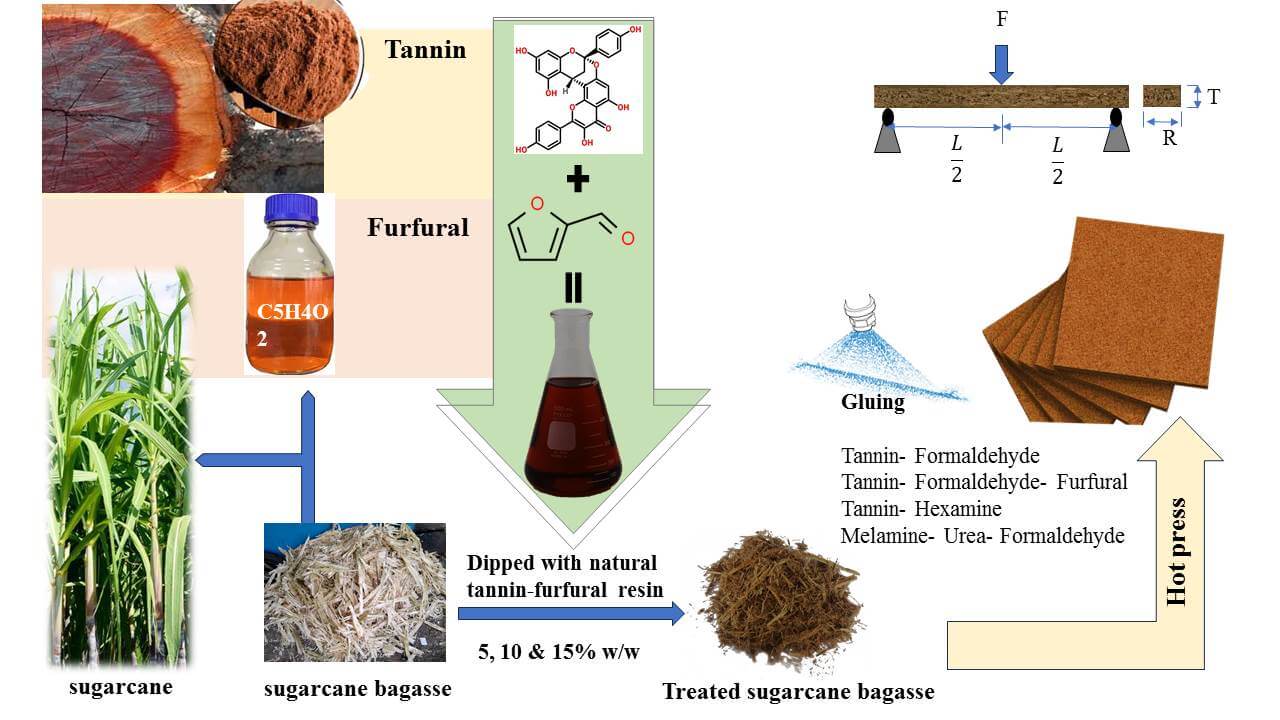
Keywords
Nomenclature
FE | Formaldehyde Emission |
IB | Internal Bonding |
m/m | Mass Percentage |
MC | Moisture Content |
MOE | Modulus of Elasticity |
MOR | Modulus of Rupture |
MUF | Melamine-Urea-Formaldehyde |
PF | Phenol Formaldehyde |
RH | Relative Humidity |
TF | Tannin-Formaldehyde |
TFFu | Tannin-Formaldehyde-Furfural |
TH | Tannin Hexamine |
TS | Thickness Swelling |
v/v | Volume Percentage |
WA | Water Absorption |
WPG | Weight Percentage Gain |
Wood-based composites are common substitutes for solid wood in today’s building structures, furniture, and other applications due to their advantages over solid wood [1]. Due to its nature, structure and lignocellulosic composition, wood is of limited dimensions, hygroscopic, can be dimensionally unstable in uncontrolled environments and is also prone to degradation to different extents by various biotic and abiotic agents depending on its service condition [2]. To address this challenges and promote the use and upcycling of low-quality timber, various wood-based composites can be manufactured in desirable sizes with increased dimensional stability and homogeneous properties [3]. Among the diverse range of composites, the demand for particleboard panels is growing [4]. However, the challenge of supplying enough woody raw materials for particleboard production has led manufacturers to seek alternative sources, especially in countries with limited wood supplies but abundant other lignocellulosic biomasses [5].
In Iran, limited access to wooden raw materials, due to (i) a ban on supply from natural forests, (ii) a shortage of plantation wood, (iii) limited imports, is one of the main challenges facing the wood industry [6]. Consequently, agricultural wastes could provide a renewable and environmentally friendly alternative to meet the domestic demand [7]. Sugarcane bagasse, a pulpy fibrous material, is one of the world’s largest agricultural residues, with 513 million tons produced each year and is widely available in Iran [8]. Bagasse remains after the sugarcane crushing process and has various uses, including in paper and panelboard manufacturing, animal feed, fertilizer, and the production of chemicals like furfural [9–12]. However, most of this waste is either burned as fuel or landfilled without further valorization [13–15].
Sugarcane bagasse, a mix of fibers and smooth parenchymatous tissue, is mainly constituted of polysaccharides (cellulose, hemicelluloses) but also contain limited amounts of lignin, wax, and residual sugars. Utilizing bagasse as a raw material for panelboard production is an effective way to repurpose this agro-residue. However, due to the nature, composition and hygroscopicity of bagasse, manufactured panelboards present serious limitations: poor dimensional stability and mechanical resistance, vulnerability to fungal and insect degradation [16–19].
Numerous studies have attempted to improve the physico-mechanical properties of panelboards made from bagasse. Different pretreatments, such as acetylation [20], wax-sizing [21], heat treatment [16,18,22], and soaking in diluted NaOH solution [23], have been applied to achieve favorable results. Impregnation with different natural [24] or synthetic resins [25] is another approach to improve the mechanical properties of wood-based panels while enhancing dimensional stability. In recent years, the use of tannin-based resins with different hardeners to improve the durability and physico-mechanical properties of wood has been extensively studied [26,27]. The potential of an innovative tannin/furfural resin for the impregnation of poplar wood to improve its physical characteristics was evaluated by Ahmadi et al. [28]. It was demonstrated that natural tannin-furfural resin with appropriate viscosity could easily impregnate wood and be transformed into a highly water-resistant polymer.
The purpose of this study is to promote the use of sugarcane bagasse, tannin and furfural, all renewable materials (furfural being itself produced from sugarcane bagasse), to produce long-lasting bagasse particleboards with enhanced physico-mechanical properties. Two different approaches were considered for achieving this objective: the raw bagasse particles were impregnated with natural tannin/furfural resins, and various tannin-based adhesives were employed for the gluing process. The different composites obtained were assessed for their physical properties, and especially their water-related behavior, as well as their mechanical resistance in order to find out the best option process.
The bio-based materials utilized for this study were sugarcane bagasse, quebracho tannin, and furfural. Sugarcane bagasse was purchased from Pars Paper Industrial Group (Karaj, Alborz, Iran). Commercial condensed tannins extracted from quebracho (Schinopsis balansae) wood were acquired from Silvateam Co. (Buenos Aires, Argentina). Furfural, prepared from the acid hydrolysis of bagasse, was obtained from Behran Oil Company (Tehran, Iran). The bagasse was air-dried for 14 days and finely ground by Pallmann Maschinenfabrik (Zweibrücken, Rhineland-Palatinate, Germany). Bagasse particles that passed through a 40-mesh sieve and remained on a 60-mesh sieve were used for further processing. Hexamethylenetetramine (hexamine), sodium hydroxide, sodium sulfite, sulfuric acid, and formaldehyde were also supplied by Sigma-Aldrich (St. Louis, MS, USA). The commercial Melamine-Urea-Formaldehyde (MUF) adhesive was purchased from Samed Co. (Mashhad, Razavi Khorasan, Iran).
Depolymerization pretreatment of tannin was performed to facilitate easier access to the functional groups of tannin macromolecules and the opening of pyran rings before adding them to the reaction system with furfural [29,30]. Dry tannin powder was dissolved in a 10% w/w NaOH solution to obtain a 20% w/w tannin solution. The tannin solution was heated to 80°C for 30 min, then 8% w/w sodium sulfite (based on the dry tannin powder weight) was added to the solution and kept at 80°C for another 30 min. The pH of the solution was adjusted to 8 using NaOH (33% w/w) to prevent polycondensation reactions between tannin monomers.
2.2.2 Acid Pretreatment of Furfural
The acid-catalyzed opening of the furan ring was performed by adding 5% v/v sulfuric acid (at 20% v/v) to the furfural and stirring for 20 min at 20°C ± 3°C [31].
The previously obtained tannin aqueous solutions (20% m/m) were prepared under vigorous stirring to add furfural. Subsequently, 50% of furfural (based on the tannin dry weight) was added to the solution. The resin pH was adjusted to 4.5 with NaOH (33% m/m) according to Ahmadi et al. [28].
2.3 Dipping of Bagasse Particles
The prepared tannin/furfural resin at three different concentrations, 5%, 10%, and 15% (m/m based on the dry weight of the resin), was used to treat anhydrous bagasse particles previously oven-dried at 103°C. The bagasse particles were soaked in a bath of resin at atmospheric pressure and room temperature for 12 h. Afterwards, they were air-dried under ambient conditions before being exposed to increasing temperatures for resin curing. For resin curing, the treated bagasse particles were exposed to the following temperature sequence: 40°C, 60°C, 80°C, and 120°C, with each step being held for 24 h. After curing the resin inside the bagasse particles, they were dried at a temperature of 103°C until a constant weight (W2) was reached. The weight percentage gain (WPG) of the bagasse particles was calculated using Eq. (1):
WPG (%)=W2−W1W1×100 (1)
where W1 is the oven-dried weight of the bagasse before dipping, and W2 is the oven-dried weight of the bagasse after dipping and curing. The experiment was conducted with three batches for each resin type.
Three different tannin-based adhesives were used for gluing bagasse particles: tannin-formaldehyde (TF), modified tannin-formaldehyde by furfural (TFFu), and tannin hexamine (TH). To compare the performance of bio-adhesives, MUF was also used as a synthetic adhesive. Tannin was first depolymerized before being used in the adhesive system according to the method described in Section 2.2.1. An aqueous tannin solution (40% m/m) was prepared, and different amounts of hardeners were added as follows:
TF: Formaldehyde with the same molar ratio as tannin
TFFu: Formaldehyde (70% v/v) and pretreated furfural (30% v/v) with the same molar ratio as tannin
TH: 6.5% on tannin extract solids of hexamine (40% m/m aqueous solution) added as a hardener
The solutions were then stirred at 80°C for 30 min. Afterwards, the adhesives were rapidly cooled to room temperature, and the pH was adjusted to 8 with NaOH (33% m/m) solution.
2.5 Particleboard Manufacturing
Particleboards were prepared to the final dimensions of 400 × 400 × 10 mm3 and a target density of 650 kg/m3 (Fig. 1). Each set of particle types (including untreated bagasse as control) and different adhesives (12% w/w based on dry particle weight) were blended using a rotary blender. The blended bagasse particles with adhesive were hot-pressed at 160°C for MUF (8 min) and 190°C for all tannin-based adhesives (12 min), with a pressure of 40 kg/cm². Three boards were produced for each experimental condition (48 boards in total).
Figure 1: Particleboards manufactured using tannin-based adhesive
2.6 Mechanical and Physical Experiments
Particleboards were conditioned at 20°C and 65% Relative Humidity (RH) for 10 days after cutting and sampling. Density and moisture content (MC) tests were performed using samples with dimensions of 5 × 5 × 1 cm3. The MC test was calculated based on the initial and final mass after oven drying for 24 h at 103°C ± 2°C. MC and Density were evaluated using Eqs. (2) and (3), according to EN 323 [32].
MC (%)=M1−M0M0×100 (2)
Density (g/cm3)=M1V1 (3)
where M1 and V1 are the conditioned weight and volume at 20°C, 65% RH; M0 is the anhydrous weight of the samples (at 103°C). The tests were conducted with six repetitions for each panel.
Water absorption (WA) and thickness swelling (TS) after 2 and 24 h of soaking in water were determined based on EN 317 [33]. The bending properties, modulus of rupture (MOR), and modulus of elasticity (MOE) were investigated according to EN 310 [34] by conducting a three-point bending test. The internal bonding (IB) strength was investigated under dry and wet conditions according to EN 319 [35] and EN 312 [36]. The experiments were conducted with twelve replicates for each treatment.
The formaldehyde emissions from particleboards were measured using the desiccator method according to JIS A 1460 [37]. Particleboard specimens with dimensions of 150 mm (length) × 50 mm (width) × thickness were placed in a desiccator for 24 h at a temperature of 20°C. A Petri dish containing 30 mL of distilled water was also placed inside the desiccator. The formaldehyde emitted from the specimens was absorbed in the water, and its content was determined by a photometric method using the acetylacetone approach [38]. In this method, formaldehyde absorption was measured at 412 nm using a spectrophotometer (VWR® UV-6300PC). This test was repeated three times for each panel type, and the average result was reported.
Data analysis was performed using a two-way ANOVA in IBM SPSS v. 29 software with a completely randomized design. The independent effects of the resin concentrations and the adhesive type, as well as their interaction, were investigated on the studied features.
3.1 Bagasse Treatment with Different Resins
For each bagasse treatment type, the values of weight percentage gain (WPG) increased along with the resin concentration (Fig. 2), this being due to the loading of resin with more solid content within the bagasse particles. Similarly, Yang et al. [25] found that the WPG values increased linearly with the phenol formaldehyde (PF) resin concentration when they immersed wood chips in a PF water-soluble resin with concentrations between 4.5% and 10% (m/m). Lin et al. [39] reported that the WPG values of the treated wood strands with PF resin ranged from 7.8% to 37.4% with changes in resin concentration.
Figure 2: Average weight percentage gain (WPG) values of bagasse particles after dipping with tannin/furfural resin
3.2 Moisture Content and Density
The increase in resin concentration resulted in a higher board density and a decrease in its equilibrium moisture content (MC%) (Table 1). However, these differences were not statistically significant (Table 2).
The panels made from treated particles with 5% resin solution had the maximum density value. The treatment of bagasse particles with 10% and 15% resin solutions resulted in panels with lower density than the control panels. This could be due to the much lower bulk density of the bagasse particles treated with 10% and 15% resin solutions, resulting in less compaction of the particles during hot pressing. On the other hand, it seems that the low compression of the particles caused a slight springback in thickness after the hot pressing (Fig. 3). Similarly, Bavaneghi et al. [40] found that particleboards made from acetylated particles developed springback after hot pressing. The density of particleboards at a given process condition is affected by several parameters, particularly the density of the lignocellulosic material [9,41]. Boruszewski et al. [42] found that higher panel mat compaction could be achieved with lower density material by regulating the pressing time and heat transfer.
Figure 3: Thickness profile of bagasse particleboard: (A) control panels (untreated particles); (B–D) panels made from particles treated with 5%, 10%, and 15% tannin/furfural resin, respectively
3.3 Flexural Properties and Internal Bonding
The results demonstrated that the impregnation of bagasse particles had a significant increasing effect on the Modulus of Rupture (MOR) and Modulus of Elasticity (MOE) values of bagasse particleboards (Tables 1 and 2). This can be explained by the increase in density of bagasse particles as a result of saturation with the tannin/furfural resin. Indeed, the resin serves as a filler agent in the interstitial spaces within the bagasse particles, subsequently enhancing the structural integrity and mechanical performance of the resulting particleboards. The rigidity effect of the cured resin on the bagasse fibers could be another reason. The highest value of MOE (5322 MPa) was observed in boards produced with the bagasse particles saturated with a 15% concentration of resin and bonded with MUF adhesive. The lowest values of MOE (1023 MPa) were observed in boards produced with untreated bagasse using TF adhesive. A similar improving trend was also observed for the values of MOR. Under the same conditions, MOR and MOE in boards made with MUF adhesives had better mechanical performance than those made using tannin-based adhesives. This stark contrast in MOE and MOR values emphasizes the importance of proper resin treatment and adhesive selection on the mechanical properties of the resulting panels. In a similar study, Yang et al. [25] investigated the production of water-resistant particleboard for applications in humid interior and outdoor use classes with recycled wood wastes of several tree species. The particles were immersed in water-soluble phenol formaldehyde (PF) resin solutions. The bending strength of the boards made from PF-impregnated particles was higher than those prepared with untreated ones [25].
The treatment of bagasse particles with tannin/furfural resin at a 5% concentration increased the internal bonding (IB) values (Table 1). The particles treated with more concentrated resins (10% and 15%) decreased IB values of the resulting panels compared to the control. The lowest IB value was found in the boards made from treated bagasse particles with 15% resin and TF adhesive (0.22 MPa), while it was highest for the boards made from treated particles with 5% resin (0.33 MPa). Kajita et al. [43] showed that the treatment of particles with PF resin considerably increased IB strength of panels with an increase in resin concentration up to a critical point. An excessive increase in resin concentration diminished the IB values. The mat of the panels (before press) made from the treated bagasse had less thickness, which resulted in less compaction during the hot press stage (Fig. 3). High-density raw materials often reduce the IB values of the particleboards [44,45]. The results indicated that the IB values in the wet condition do not meet the minimum standard allowance for type-P2 panels (IB > 0.4 MPa) with either tannin-based adhesive or MUF. However, some of the produced panels meet the requirements of EN 312 [1] standard for type-P1 panels for interior dry applications (IB > 0.28 MPa: type-P1).
The analysis of variance test showed that the treatment of bagasse particles had a significant effect on the IB of the boards. However, the interaction of resin concentration and adhesive type was not significant (Table 2).
Tannin-based adhesives with different formulas and synthesis processes have been successfully used for the production of interior and exterior grade particleboards [46]. Cesprini et al. [47] used industrial quebracho tannin powder and furfural as a bio-sourced hardener to prepare laboratory-scale single-layer particleboard. The values obtained for IB and MOE met the required standards for P1 panels according to EN 312 [1], but the MOR did not satisfy the requirements. In contrast to the favorable flexural properties observed, the IB values of the panels were found to be unsatisfactory and often fell below the stipulated values for both P1 and P2 panels. Pizzi [48] reviewed the advancement of tannin-based resins and the strategies for their successful commercialization in industry. He emphasized the substantial disparity between creating an adhesive formulation in a controlled laboratory setting and its practical implementation in industrial uses. The mechanical properties of particleboards are influenced not only by the type of adhesive used but also by various other parameters. Raw material density plays a crucial role in determining mechanical resistance [49]. Brito et al. [19] investigated the properties of particleboards made from sugarcane bagasse particles and their results showed that the values of MOR, MOE, and IB reached 692.58, 13.50, and 0.22 MPa, respectively. The values obtained in our research were much higher in terms of MOE and IB, but the values of MOR were observed to be the same [19].
Fig. 4 illustrates the thickness swelling (TS) of different panels after soaking in water for 2 and 24 h. The results showed that as the soaking period increased, the thickness swelling also increased. By increasing the concentration of the resin solution, the TS values statistically decreased for all adhesive types (Table 2). The primary cause of the reduction in TS is the limited access of water molecules to the hydroxyl groups on the cell walls of bagasse particles that have undergone treatment with tannin/furfural polymer. On the other hand, the tannin/furfural resin is a polar solution capable of entering the micropores in the cell wall and forming covalent bonds with hydroxyl groups, effectively obstructing their interaction with water on a permanent basis [28,50]. The effect of modification of wood particles or fibers on the swelling behavior of panelboard through acetylation with different types of anhydrides has been previously studied [51–53]. According to Fig. 4, the effect of the used adhesive was also significant on the values of TS. The panels with MUF adhesive had higher dimensional stability than those with tannin-based adhesives. The bond quality and the water resistance of the adhesive are the most effective factors on the TS of particleboard [54]. Although the independent effects of adhesive type and resin concentration were significant on TS, their simultaneous effects were not significant (Table 2).
Figure 4: Thickness swelling of different bagasse panels
The water absorption (WA) values exhibited an increasing trend as the soaking time was prolonged (Fig. 5). Notably, the panels fabricated using treated bagasse particles demonstrated lower WA values in comparison to those prepared with untreated particles, especially after 24 h of soaking. Higher resin concentrations led to a more pronounced reduction in WA, likely due to the formation of a solid tannin/furfural polymer within the bagasse particle interstices. The WA values for panels using untreated bagasse aligned with those reported by Fiorelli et al. [55] for bagasse panels made with castor oil polyurethane adhesive. Moreover, Mendes et al. [56] concluded that adhesive content, rather than type, primarily influenced WA rates. Statistical analysis indicated that both adhesive types and resin concentration significantly affected WA values after 24 h of water soaking (Table 2).
Figure 5: Water absorption (WA) of different bagasse panels
Fig. 6 illustrates the formaldehyde emission (FE) from bagasse boards manufactured using untreated bagasse and various adhesives. Significant differences in FE levels were observed depending on the adhesive type. Panels bonded with tannin-based adhesives exhibited markedly lower FE compared to those bonded with MUF adhesive. In the case of TFFU, FE was substantially reduced due to a lower formaldehyde ratio, without adversely affecting panel properties. Tannin is often incorporated into amino adhesives as a formaldehyde scavenger to diminish FE, owing to its high reactivity with formaldehyde [57–60]. The panels with the highest and lowest FE values were those bonded with MUF and TH adhesives, respectively. Hexamine, a non-aldehyde hardener, forms –CH2–NH–CH2– bridges between tannin units [61], contributing to the development of panels with negligible formaldehyde emissions [62,63]. Panels bonded with TH adhesive were classified as super zero FE (super E0) according to the formaldehyde emission ranges specified in the JIS A 1460 [37] standard.
Figure 6: Formaldehyde emission from panels produced with different adhesives
The aim of this research was to develop particleboards made from bagasse treated with innovative resins formulated based on the complex of tannin and furfural. The treated bagasse particles were bonded using various tannin-based adhesives and compared with those produced using the widely used MUF commercial adhesive. An increase in resin concentration was correlated with improvements in MOE and MOR, and reductions in WA and TS values. However, it was observed that IB values exhibited an optimal improvement trend up to a critical resin concentration of 5%, beyond which performance decreased. The IB values of panels manufactured using tannin-based adhesives were generally inferior to those produced with MUF. Some panels met the minimum standard requirement for indoor general applications according to the IB values. This area warrants further research. Future studies should evaluate the impact of resin content, target board density, and pressing conditions (for higher compaction) on internal quality performance of panels. The use of tannin-based adhesives significantly reduced FE in the panels. These results highlight the potential of tannin-based adhesives in reducing FE, aligning with the growing focus on sustainable and eco-friendly construction materials. In summary, this study provides valuable insights for further research and development in utilizing agricultural residues to produce high-quality, sustainable wood-based panel products.
Acknowledgement: This work was supported by the University of Tehran and the Center for International Scientific Studies and Collaboration (CISSC), as well as Campus France (Paris, France) through the Gundishapur project–Development of Smart Bio-Composites with Innovative Coatings, and CIRAD through specific action for overseas doctoral students.
Funding Statement: This work was supported by the office of vice-president for research and technology, University of Tehran, Gundishapur project 1584/45227SG, and Campus France.
Author Contributions: The authors confirm their contributions to the paper as follows: study conception and design: Peyman Ahmadi, Marie-France Thévenon, Davood Efhamisisi; data collection: Peyman Ahmadi; analysis and interpretation of results: Marie-France Thévenon, Davood Efhamisisi, Peyman Ahmadi, Hamid Zarea Hosseinabadi, Jean Gerard; draft manuscript preparation: Davood Efhamisisi, Peyman Ahmadi, Reza Oladi. All authors reviewed the results and approved the final version of the manuscript.
Availability of Data and Materials: The data that support the findings of this study are available on request from the corresponding authors.
Ethics Approval: This article does not contain any studies involving human or animal participants performed by any of the authors.
Conflicts of Interest: The authors declare that they have no conflicts of interest to report regarding the present study.
References
1. Papadopoulos AN. Advances in wood composites. Polymers. 2019;12(1):48. doi:10.3390/polym12010048. [Google Scholar] [PubMed] [CrossRef]
2. Reinprecht L. Wood deterioration, protection and maintenance. Oxford, UK: John Wiley & Sons; 2016. p. 145–217. [Google Scholar]
3. Zanuttini R, Negro F. Wood-based composites: innovation towards a sustainable future. Forests. 2021;12(12):1717. doi:10.3390/f12121717. [Google Scholar] [CrossRef]
4. Krumins JA, Vamza I, Dzalbs A, Blumberga D. Particle boards from forest residues and bio-based adhesive. Buildings. 2024;14(2):462. doi:10.3390/buildings14020462. [Google Scholar] [CrossRef]
5. Mantanis G, Berns J. Strawboards bonded with urea-formaldehyde resins. In: 35th International Particleboard/Composite Material Symposium, 2001; Pullman, WA, USA: Washington State University. [Google Scholar]
6. Arian A, Vlosky RP. An overview of the wood products sector in Iran: 2007–2022. J For Bus Res. 2023 Nov 27;2(2):146–69. doi:10.62320/jfbr.v2i2.40. [Google Scholar] [CrossRef]
7. Jafarinia M, Almodares A, Khorvash M. Using sweet sorghum bagasse in silo. In: Proceeding of the 2nd Congress of Using Renewable Sources and Agriculture, 2005; Isfahan, Iran: Khorasgan Azade University. [Google Scholar]
8. Miranda NT, Motta IL, Maciel Filho R, Maciel MRW. Sugarcane bagasse pyrolysis: a review of operating conditions and products properties. Renew Sustain Energ Rev. 2021;149(2):111394. doi:10.1016/j.rser.2021.111394. [Google Scholar] [CrossRef]
9. Baharuddin MNM, Zain NM, Harun WSW, Roslin EN, Ghazali FA. Development and performance of particleboard from various types of organic waste and adhesives: a review. Int J Adhes Adhes. 2023;124:103378. doi:10.1016/j.ijadhadh.2023.103378. [Google Scholar] [CrossRef]
10. Chantit F, El Abbassi FE, Kchikach A. Investigation on the reuse of the sugar co-products (Bagasse, Molasses, and Ash) as industrial wastes in the production of compressed earth blocks. Mater Today: Proc. 2022;58(5):1530–4. doi:10.1016/j.matpr.2022.03.295. [Google Scholar] [CrossRef]
11. Nyonje EO, Njogu P, Kinyua R. Assessment of the potential for utilization of sugarcane derived press mud for biogas generation in South Nyanza sugarcane zones. Kenya J Sustain Res Eng. 2014;1(4):30–3. [Google Scholar]
12. Yu N, Tan L, Sun ZY, Nishimura H, Takei S. Bioethanol from sugarcane bagasse: focused on optimum of lignin content and reduction of enzyme addition. Waste Manag. 2018;76:404–13. [Google Scholar] [PubMed]
13. Boer FD, Valette J, Commandré JM, Fournier M, Thévenon MF. Slow pyrolysis of sugarcane bagasse for the production of char and the potential of its by-product for wood protection. J Renew Mater. 2021;9(1):97–117. doi:10.32604/jrm.2021.013147. [Google Scholar] [CrossRef]
14. Han G, Wu Q. Comparative properties of sugarcane rind and wood strands for structural composite manufacturing. For Prod J. 2004;54(12):283–8. [Google Scholar]
15. Kanwal S, Chaudhry N, Munir S, Sana H. Effect of torrefaction conditions on the physicochemical characterization of agricultural waste (sugarcane bagasse). Waste Manag. 2019;88(2):280–90. doi:10.1016/j.wasman.2019.03.053. [Google Scholar] [PubMed] [CrossRef]
16. Ribeiro DP, Vilela AP, Silva DW, Napoli A, Mendes RF. Effect of heat treatment on the properties of sugarcane bagasse medium density particleboard (MDP) panels. Waste Biomass Valorization. 2020;11(11):6429–41. doi:10.1007/s12649-019-00882-9. [Google Scholar] [CrossRef]
17. Mendes RF, Mendes LM, Oliveira SL, Freire TP. Use of sugarcane bagasse for particleboard production. Key Eng Mater. 2015;634:163–71. doi:10.4028/www.scientific.net/KEM.634.163. [Google Scholar] [CrossRef]
18. Milagres EG, Barbosa RAGS, Caiafa KF, Gomes GSL, Castro TAC, Vital BR. Properties of particleboard panels made of sugarcane particles with and without heat treatment. Revista Árvore. 2019;43(5):e430502. doi:10.1590/1806-90882019000500002. [Google Scholar] [CrossRef]
19. Brito FMS, Bortoletto Junior G, Paes JB. Biological resistance and wettability of particleboard produced with sugarcane waste. Sci For. 2021;49(129):e3356–12. doi:10.18671/scifor.v49n129.07. [Google Scholar] [CrossRef]
20. Jonoubi M, Saraeyan AR, Mastery FM. Dimensional stability and mechanical properties of particleboard made from acetylated bagasse. J Wood Forest Sci Technol. 2010;17(3):125–36. [Google Scholar]
21. Xu X, Yao F, Wu Q, Zhou D. The influence of wax-sizing on dimension stability and mechanical properties of bagasse particleboard. Ind Crops Prod. 2009;29(1):80–5. doi:10.1016/j.indcrop.2008.04.008. [Google Scholar] [CrossRef]
22. Carvalho AG, Mendes RF, Oliveira SL, Mendes LM. Effect of post-production heat treatment on particleboard from sugarcane bagasse. Mater Res. 2015;18(1):78–84. doi:10.1590/1516-1439.270814. [Google Scholar] [CrossRef]
23. Magzoub R, Osman Z, Tahir P, Nasroon TH, Kantner W. Comparative evaluation of mechanical and physical properties of particleboard made from bagasse fibers and improved by using different methods. Cell Chem Technol. 2015;49(5–6):537–42. [Google Scholar]
24. Efhamisisi D, Thevenon M-F, Hamzeh Y, Pizzi A, Karimi A, Pourtahmasi K. Tannin-boron complex as a preservative for 3-ply beech plywoods designed for humid conditions. Holzforschung. 2017;71(3):249–58. doi:10.1515/hf-2016-0130. [Google Scholar] [CrossRef]
25. Yang TH, Lin CJ, Wang SY, Tsai MJ. Characteristics of particleboard made from recycled wood-waste chips impregnated with phenol formaldehyde resin. Build Environ. 2007;42(1):189–95. doi:10.1016/j.buildenv.2005.08.028. [Google Scholar] [CrossRef]
26. Tondi G, Hu J, Rizzo F, Buh J, Medved S, Petutschnigg A, et al. Tannin-caprolactam and Tannin-PEG formulations as outdoor wood preservatives: weathering properties. Ann For Sci. 2017;74(1):1–12. doi:10.1007/s13595-016-0605-y. [Google Scholar] [CrossRef]
27. EN 312. Particleboards–Specifications, AFNOR. 2010. Available from: https://www.en-standard.eu/bs-en-312-2010-particleboards-specifications. [Accessed 2024]. [Google Scholar]
28. Ahmadi P, Efhamisisi D, Thevenon MF, Zare Hosseinabadi H, Oladi R, Gerard J. The properties of natural tannin-furfural resin applied to poplar wood modification. J Wood Forest Sci Technol. 2022;29(2):1–20. [Google Scholar]
29. Shirmohammadli Y, Efhamisisi D, Pizzi A. Tannins as a sustainable raw material for green chemistry: a review. Ind Crops Prod. 2018;126:316–32. [Google Scholar]
30. Liu J, Wang L, Li J, Li C, Zhang S, Gao Q, et al. Degradation mechanism of Acacia mangium tannin in NaOH/urea aqueous solution and application of degradation products in phenolic adhesives. Int J Adhes Adhes. 2020;98:102556. [Google Scholar]
31. Zhang A, Li J, Zhang S, Mu Y, Zhang W, Li J. Characterization and acid-catalysed depolymerization of condensed tannins derived from larch bark. RSC Adv. 2017;7(56):35135–46. [Google Scholar]
32. Yi Z, Wang W, Zhang W, Li J. Preparation of tannin-formaldehyde–furfural resin with pretreatment of depolymerization of condensed tannin and ring opening of furfural. J Adhes Sci Technol. 2016;30(9):947–59. [Google Scholar]
33. EN 323. Wood-based panels; determination of density, AFNOR. 1993. Available from: https://www.en-standard.eu/bs-en-323-1993-wood-based-panels-determination-of-density. [Accessed 2024]. [Google Scholar]
34. EN 317. Particleboards and fibreboards. Determination of swelling in thickness after immersion in water, AFNOR. 1993. [Google Scholar]
35. EN 310. Wood-based panels-Determination of modulus of elasticity in bending and of bending strength, AFNOR. 1993. Available from: https://www.en-standard.eu/din-en-310-wood-based-panels-determination-of-modulus-of-elasticity-inbending-and-of-bending-strength-german-version-en-310-1993. [Accessed 2024]. [Google Scholar]
36. EN 319. Particleboards and fibreboards. Determination of tensile strength perpendicular to the plane of the board, AFNOR. 1993. Available from: https://www.en-standard.eu/bs-en-319-1993-particleboards-and-fibreboards-determination-oftensile-strength-perpendicular-to-the-plane-of-the-board. [Accessed 2024]. [Google Scholar]
37. JIS A 1460. Building boards determination of formaldehyde emission-Desiccator method Japanese industrial standard (Tokyo). 2001. [Google Scholar]
38. Martins JM, Coelho C, Pereira J, Ferra JM, Carvalho L. 8. Strategies to reduce formaldehyde emissions from wood-based panels: Impact on physicomechanical properties and machinability. In: J. Paulo Davim and Alfredo Aguilera. Berlin, Boston: De Gruyter; 2017. p. 165–206. [Google Scholar]
39. Lin CH, Yang TH, Lai WJ, Lin FC. Anisotropic physical and mechanical performance of PF-impregnated oriented strand board. BioResources. 2013 Jan 1;8(2):1933–45. doi:10.15376/biores.8.2.1933-1945. [Google Scholar] [CrossRef]
40. Bavaneghi F, Ghorbani M. Mechanical behavior and springback of acetylated particleboard made in different press times. Wood Mater Sci Eng. 2016 Jan 1;11(1):57–61. doi:10.1080/17480272.2015.1006249. [Google Scholar] [CrossRef]
41. Iswanto AH, Fatriasari W, Susilowati A. Effect of particle treatment and adhesive type on physical, mechanical, and durability properties of particleboard made from Sorghum Bagasse. IOP Conf Ser.: Earth Environ Sci. 2018 Mar 1;126(1):012016. doi:10.1088/1755-1315/126/1/012016. [Google Scholar] [CrossRef]
42. Boruszewski P, Borysiuk P, Mamiński M, Czechowska J. Mat compression measurements during low-density particleboard manufacturing. BioResources. 2016 Aug 1;11(3):6909–19. doi:10.15376/biores.11.3.6909-6919. [Google Scholar] [CrossRef]
43. Kajita H, Imamura Y. Improvement of physical and biological properties of particleboards by impregnation with phenolic resin. Wood Sci Technol. 1991 Nov;26(1):63–70. doi:10.1007/BF00225692. [Google Scholar] [CrossRef]
44. Lee S, Kim S, Na Y. Comparative analysis of energy related performance and construction cost of the external walls in high-rise residential buildings. Energy Build. 2015 Jul 15;99:67–74. [Google Scholar]
45. Rofii MN, Yumigeta S, Kojima Y, Suzuki S. Effect of furnish type and high-density raw material from mill residues on properties of particleboard panels. J Wood Sci. 2013;59:402–9. [Google Scholar]
46. Zhou X, Du G. Applications of tannin resin adhesives in the wood industry. In: Aires A, editor. Tannins-structural properties, biological properties and current knowledge. London, UK: IntechOpen; 2020. p. 97–103. [Google Scholar]
47. Cesprini E, Causin V, De Iseppi A, Zanetti M, Marangon M, Barbu MC, et al. Renewable tannin-based adhesive from quebracho extract and furfural for particleboards. Forests. 2022;13(11):1781. doi:10.3390/f13111781. [Google Scholar] [CrossRef]
48. Pizzi A. Little secrets for the successful industrial use of tannin adhesives: a Review. J Renew Mater. 2023;11(9):3403–15. doi:10.32604/jrm.2023.030930. [Google Scholar] [CrossRef]
49. Sieranc A, Pastuch-Gawołek G, Zdanowicz D, Osiak K. Sestec adhesive based on animal proteins for the production of particleboards. J Adhes Sci Technol. 2024 Jan 17;38(2):203–24. doi:10.1080/01694243.2023.2224620. [Google Scholar] [CrossRef]
50. Sommerauer L, Thevenon MF, Petutschnigg A, Tondi G. Effect of hardening parameters of wood preservatives based on tannin copolymers. Holzforschung. 2019 May 27;73(5):457–67. doi:10.1515/hf-2018-0130. [Google Scholar] [CrossRef]
51. Kwon JH, Ayrilmis N. Combined effect of acetylation and wax emulsion on physical and mechanical properties of particleboard. Eur J Wood Wood Prod. 2015 Nov;73(6):845–7. doi:10.1007/s00107-015-0957-2. [Google Scholar] [CrossRef]
52. Mai C, Direske M, Varel D, Weber A. Light medium-density fibreboards (MDFs): does acetylation improve the physico-mechanical properties? Eur J Wood Wood Prod. 2017 Sep;75(5):739–45. doi:10.1007/s00107-016-1147-6. [Google Scholar] [CrossRef]
53. Sandberg D, Kutnar A, Karlsson O, Jones D. Wood modification technologies: principles, sustainability, and the need for innovation. Boca Raton: CRC Press; 2021 Jul 14. doi:10.1201/9781351028226 [Google Scholar] [CrossRef]
54. Sugahara ES, da Silva SAM, Buzo ALSC, de Campos CI, Morales EAM, Ferreira BS, et al. High-density particleboard made from agro-industrial waste and different adhesives. BioResources. 2019;14(3):5162–70. doi:10.15376/biores.14.3.5162-5170. [Google Scholar] [CrossRef]
55. Fiorelli J, Sartori DD, Cravo JC, Savastano Junior H, Rossignolo JA, Nascimento MF, et al. Sugarcane bagasse and castor oil polyurethane adhesive-based particulate composite. Mater Res. 2013;16(2):439–46. doi:10.1590/S1516-14392013005000004. [Google Scholar] [CrossRef]
56. Mendes RF, Mendes LM, JÚNIoR JB, dos Santos RC, Bufalino L. The adhesive effect on the properties of particleboards made from sugar cane bagasse generated in the distiller. Revista de Ciências Agrárias. 2009;32(2):209–18. doi:10.19084/rca.15739. [Google Scholar] [CrossRef]
57. Barbu MC, Lohninger Y, Hofmann S, Kain G, Petutschnigg A, Tudor EM. Larch bark as a formaldehyde scavenger in thermal insulation panels. Polymers. 2020 Nov 10;12(11):2632. doi:10.3390/polym12112632. [Google Scholar] [PubMed] [CrossRef]
58. Bekhta P, Sedliačik J, Noshchenko G, Kačík F, Bekhta N. Characteristics of beech bark and its effect on properties of UF adhesive and on bonding strength and formaldehyde emission of plywood panels. Eur J Wood Wood Prod. 2021 Mar;79:423–33. [Google Scholar]
59. Peng J, Chen X, Zhang J, Essawy H, Du G, Zhou X. Characterization on the copolymerization resin between bayberry (Myrica rubra) tannin and pre-polymers of conventional urea-formaldehyde resin. Forests. 2022 Apr 16;13(4):624. doi:10.3390/f13040624. [Google Scholar] [CrossRef]
60. Ghaffari R, Doost Hosseini K, Abdolkhani A, Mirshakraei S, Faezipour M. Modification of urea formaldehyde adhesive with furfural to reduce the release of formaldehyde from particle board. J For Wood Prod. 2014;67(3):475–87. [Google Scholar]
61. Tondi G, Thévenon MF, Mies B, Standfest G, Petutschnigg A, Wieland S. Impregnation of Scots pine and beech with tannin solutions: effect of viscosity and wood anatomy in wood infiltration. Wood Sci Technol. 2013 May;47(3):615–26. doi:10.1007/s00226-012-0524-5. [Google Scholar] [PubMed] [CrossRef]
62. Arias Calvo A, González García S, Moreira Vilar MT, Feijoo Costa G. Tannin-based bio-adhesives for the wood panel industry as sustainable alternatives to petrochemical resins. J Ind Ecol. 2021;26(2):627–42. doi:10.1111/jiec.13210. [Google Scholar] [CrossRef]
63. Dhawale PV, Vineeth SK, Gadhave RV, MJ JF, Supekar MV, Thakur VK, et al. Tannin as a renewable raw material for adhesive applications: a review. Mater Adv. 2022;3(8):3365–88. doi:10.1039/D1MA00841B. [Google Scholar] [CrossRef]
Cite This Article
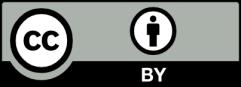
This work is licensed under a Creative Commons Attribution 4.0 International License , which permits unrestricted use, distribution, and reproduction in any medium, provided the original work is properly cited.